Nordson Pro-Meter A2K D2K H2K Parts list manual

1
Nordson Corporation
OPERATOR’S CARD
7443491
Pro−MeterRA2K D2K H2K
Safety
WARNING: Allow only qualified personnel to
perform the following tasks. Follow the safety
instructions in this document and all other
related documentation.
SSafety glasses are to be worn at all times while
installing, servicing, operating, or observing
equipment. The sudden release of air or fluid can
cause damage to eyes.
SRelieve system air pressure, material pressure,
and disconnect power prior to servicing
Pro−Meter A2K D2K H2K components.
SClean any material that has spilled. Be sure to
follow all applicable safety and environmental
guidelines when cleaning spilled material.
SAny material injected into flesh can cause severe
injury or death. Keep body parts away from
material discharge ports. If injection occurs, seek
medical attention immediately.
WARNING: Operating faulty electrostatic
equipment is hazardous and can cause
electrocution, fire, or explosion. Make
resistance checks part of your periodic
maintenance program. If you receive even a
slight electrical shock or notice static
sparking or arching, shut down all electrical
or electrostatic equipment immediately.
CAUTION: Relieve air and material pressure
when equipment is not in use for prolonged
periods of time. Do not allow pressure to
remain static when equipment is idle as this
may cause material to pack and harden.

2
Preparation For Maintenance And Service
Air Pressure Relief
1. Relieve material pressure. Refer to Material
Pressure Relief for material pressure relief
procedure.
2. Turn OFF main air supply.
3. Disconnect air lines from air manifold and/or
inlet/outlet valves.
Material Pressure Relief
1. Proceed to Main Menu HMI Control Panel
Screen.
2. Select Setup Login push button to proceed to
Setup Login HMI Control Panel Screen.
3. Log into the HMI Control Panel using the default
user name and password. The default user name
is ‘S’. The default password is ‘2’.
NOTE: To change default password, proceed as
follows:
SProceed to Main Menu HMI Control Panel
Screen.
SSelect Setup Login to proceed to Setup Login
HMI Control Panel Screen.
SSelect Level 2 Setup to proceed to Level 2 Setup
Menu HMI Control Panel Screen.
4. Proceed to Level 2 Setup Menu HMI Control
Panel Screen.
5. Select the Level 1 Setup push button to proceed
to the Level 1 Setup Menu HMI Control Panel
Screen.
6. Select the Valve Setup push button to proceed to
the Valve Setup HMI Control Panel Screen.
7. Close the inlet valves by selecting the High Vol
Inlet and Low Vol Inlet push buttons.
NOTE: The High Vol Inlet and Low Vol Inlet push
buttons should not be illuminated.
8. Ensure the outlet valves are open.
NOTE: The H/L Vol Outlets push button should be
illuminated.
9. Select the Level 1 Setup push button to proceed
to the Level 1 Setup Menu HMI Control Panel
Screen.
10. Select the Setup Login push button to proceed to
the Setup Login HMI Control Panel Screen.
11. Select the Logout push button to log out.
12. Select the Main Menu push button to proceed to
the Main Menu HMI Control Panel Screen.
13. Select the Cycle Control push button to proceed
to the Cycle Control HMI Control Panel Screen.
14. Enable the Manual Shot push button and then
select the Manual Dispense push button to
dispense material.
WARNING: Utilize a suitable container to
collect material dispensed.
15. Dispense material until the system pressure
reflects 0 psi (0 bar) on the Material Pressure HMI
Control Panel Screen and the gauge plumbed in−
line with the seal cartridge assembly.
Power Disconnect
Lock out system electrical power before proceeding
with maintenance and service.

3
Initial Start−up And Material Bleed Procedure
1. Fill the seal cartridge assembly packing nuts with
Throat Seal Lubricant until they are ¾full. Do not
overfill.
2. Supply electrical power to Pro−Meter A2K D2K
H2K. Refer to the Electrical Circuit Drawing for
additional information.
3. Supply at least 80−100 psi (5.516−6.895 bar) of
clean shop air to the air manifold ports. Refer to
the Pneumatic Circuit Drawing and Customer
Product Manual for additional information.
CAUTION: Utilize a desiccant, or equivalent
drier, to ensure shop air is free of moisture.
4. Connect dispense system material supply lines to
inlet/outlet valves. Refer to the Fluid Circuit
Drawing and Customer Product Manual for
additional information.
5. Ensure the bleed valves attached to seal
cartridge assemblies are closed.
6. Proceed to Main Menu HMI Control Panel
Screen.
7. Select Setup Login push button to proceed to
Setup Login HMI Control Panel Screen.
8. Log into the HMI Control Panel using the default
user name and password. The default user name
is ‘S’. the default password is ‘2’.
NOTE: To change default password, proceed as
follows:
SProceed to Main Menu HMI Control Panel
Screen.
SSelect Setup Login to proceed to Setup Login
HMI Control Panel Screen.
SSelect Level 2 Setup to proceed to Level 2 Setup
HMI Menu Control Panel Screen.
9. Proceed to Level 2 Setup Menu HMI Control
Panel Screen.
10. Select the Level 1 Setup push button to proceed
to the Level 1 Setup Menu HMI Control Panel
Screen.
11. Select the Valve Setup push button to proceed to
the Valve Setup HMI Control Panel Screen.
12. Open the inlet valves by enabling the High Vol
Inlet and Low Vol Inlet push buttons.
13. Ensure the outlet valves are closed. The H/L Vol
Outlets push button should not be selected on the
Valve Setup HMI Control Panel Screen.
14. Connect clear tubing to bleed valve ports.
CAUTION: Utilize 0.25 inch (6.35 mm)
diameter tubing.
15. Open bleed valves and allow them to remain
open until air free material emerges.
WARNING: Utilize a suitable container to
collect material bled from bleed valves.
16. Close bleed valves.
17. Select the H/L Vol Outlets push button on the
Valve Setup HMI Control Panel Screen to open
the outlet valves.
18. Select the Level 1 Setup push button to proceed
to the Level 1 Setup Menu HMI Control Panel
Screen.
19. Select the Setup Login push button to proceed to
the Setup Login HMI Control Panel Screen.
20. Select the Logout push button to log out.
21. Select the Main Menu push button to proceed to
the Main Menu HMI Control Panel Screen.
22. Select the Cycle Control push button to proceed
to the Cycle Control HMI Control Panel Screen.
23. Enable the Manual Shot push button and then
select the Manual Dispense push button to
dispense material.
WARNING: Utilize a suitable container to
collect material dispensed.
24. Repeat steps 4 through 22 (as necessary) until
material is air free.

4
Dispense Mode Descriptions
The dispense command is a signal which instructs
the Pro−Meter A2K D2K H2K to dispense material
based on the mode selected. The Pro−Meter A2K
D2K H2K can dispense material in three distinct
modes (Auto Flow Mode, Manual Flow Mode, and
Manual Shot Mode).
Auto Flow Mode
Auto Flow Mode relies on an external device
(example: robot) to provide all dispense and reload
commands through the machine interlock. The
system will continue to dispense and reload as long
as a signal is received from the external source.
Manual Flow Mode
Manual Flow Mode allows for the continuous
engagement of the dispense command. The system
will continue to dispense as long as the trigger is
engaged. If the trigger is released and depressed
again, system operation resumes from the last
position. There is no automatic reload.
Manual Shot Mode
Manual Shot Mode allows momentary engagement of
the dispense command which completes one
dispense shot and reload as dictated by setup
parameters.
Operation
This section provides a basic overview of how to
initiate a dispense cycle. Refer to HMI Screen
Description Manual for additional information
regarding HMI Control Panel Screens.
Dispense Overview
1. Establish system control parameters. Refer to
Control Parameters for additional information
regarding the setup of system control parameters.
2. Bleed material from Pro−Meter A2K, D2K, H2K.
Refer to Initial Start−Up and Material Bleed
Procedure for material bleed procedure.
3. Ensure the Pro−Meter A2K, D2K, H2K has been
calibrated. Refer to the Pro−Meter A2K, D2K,
H2K Quick Start Guide for system calibration
information.
4. Proceed to the Cycle Control HMI Control Panel
Screen to enable the Pro−Meter A2K, D2K, H2K
to dispense in Auto Shot mode, Manual Shot
mode, or Manual Flow mode.
NOTE:
SAfter powering ON the HMI interface, the Cycle
Control Screen is the first screen that appears.
No password is required to engage the functions
of the Cycle Control HMI Control Panel Screen.
5. Select the Auto Startup push button to ensure the
Pro−Meter A2K, D2K, H2K is ready to dispense.
NOTE:
SIf the system is ready to dispense, the Dispense
Ready and Reload Complete indicators will both
be illuminated.
SIf these indicators are not illuminated after
selecting the Auto Startup push button, faults
and/or warnings may exist. Refer to
Troubleshooting to resolve system faults and
warnings.
6. If the Dispense Ready and Reload Complete
indicators both illuminate after selecting the Auto
Startup push button, elect the desired dispense
mode. The Pro−Meter A2K, D2K, H2K is now
ready to dispense. Refer to Dispense Mode
Descriptions for a description of the Auto Shot,
Manual Shot, and Manual Flow dispense modes.
NOTE: Enable Auto Shot,Manual Shot, or Manual
Flow mode by selecting the applicable push button.
Once enabled, the push button will illuminate.
7. Select the Manual Dispense push button on the
Cycle Control HMI Control Panel Screen to
dispense material.
NOTE: An manual trigger such as a foot switch can
also be utilized to dispense material.

5
Control Parameters
1. Proceed to Main Menu HMI Control Panel
Screen.
2. Select Setup Login push button to proceed to
Setup Login HMI Control Panel Screen.
3. Log into the HMI Control Panel using the default
user name and password. The default user name
is ‘S’. the default password is ‘2’.
NOTE: To change default password, proceed as
follows:
SProceed to Main Menu HMI Control Panel
Screen.
SSelect Setup Login to proceed to Setup Login
HMI Control Panel Screen.
SSelect Level 2 Setup to proceed to Level 2 Setup
Menu HMI Control Panel Screen.
4. Proceed to the the Level 1 Setup Menu HMI
Control Panel Screen to establish parameters
associated with the screens listed below.
SMiscellaneous Pressure Setup HMI Control Panel
Screen
SMiscellaneous Setup HMI Control Panel Screen
SPosition Setup HMI Control Panel Screen
SPressure Limits Setup Control Panel Screen
SProcess Data Setup Control Panel Screen
SPurge Setup Control Panel Screen
SShot Profile Setup Control Panel Screen
SShot Sequence Setup Control Panel Screen
SSpeed Setup Control Panel Screen
5. Proceed to the Level 2 Setup Menu HMI Control
Panel Screen to establish parameters associated
with the screens listed below.
SMeter Setup HMI Control Panel Screen.
SSystem Setup HMI Control Panel Screen.
6. To log out, proceed as follows:
SProceed to Main Menu HMI Control Panel
Screen.
SSelect Setup Login push button to proceed to
Setup Login HMI Control Panel Screen.
SSelect the Logout push button.

6
Preventative Maintenance Schedule
NOTE:
SThe frequencies listed are only guidelines. It’s
recommended to inspect components weekly. It
may be necessary to adjust frequencies due to
the facility environment, process parameters,
material being applied, or experience.
SAlways listen for air leaks, keep your work area
clean of material, and check with the material
supplier for specific cleaning procedures for the
material being utilized.
Component Task Completion Time
Air fittings and tubing Inspect for air leaks. Inspect: 5 Min.
Replace: 10−15 Min.
Air−over−oil cylinder Inspect for air leaks. Inspect air−
over−oil cylinder rod for damage.
Inspect: 30−60 Min.
Replace: 30−60 Min.
Inlet/outlet valves Inspect for leakage at weep holes. Inspect: 10−15 Min.
Replace: 30−60 Min.
Linear servo actuator
Inspect for loose connections. In-
spect linear servo actuator rod for
damage.
Inspect: 30−60 Min.
Replace: 30−60 Min.
Material fittings and hoses Inspect for material leaks. Inspect: 5 Min.
Replace: Up to 2 hours
Metering rod Inspect for damage to surface of rod. Inspect: 5 Min.
Replace: 2−3 Hrs.
Rupture disc and pressure sensor Inspect for material leaks. Inspect: 5 Min.
Replace: Up to 30 Min.
Seal cartridge assembly
Inspect for leakage. Add Seal Sav’r
oil (Throat Seal Lubricant) to packing
nut (as necessary) to prevent dam-
age to system components.
Ensure seal cartridge packing nut is
secure. Hand tighten packing nut un-
til it is snug. Tighten packing nut an
additional ¼turn.
Inspect: 5 Min.
Replace: 30−60 Min.

7
Troubleshooting
These troubleshooting procedures cover only the
most common problems. If you cannot solve a
problem with the information given here, contact your
local NordsonRrepresentative for help.
Problem Possible Cause Corrective Action
Meter will not cycle
Blocked material path Ensure material is passing through all hoses.
Dispense valve not opening
Ensure air is on. Inspect dispense valve for binding.
Inspect dispense valve piston for binding. Inspect
dispense valve piston O-ring for wear or damage.
Ensure there is sufficient air pressure. Ensure dispense
valve solenoid is functioning properly.
Inlet/outlet valve not opening
Inspect valve for needle/ball binding. Inspect dispense
valve piston for binding. Inspect dispense valve piston
O−ring for wear or damage. Ensure there is sufficient air
pressure. Ensure solenoid valve is functioning properly.
Linear servo actuator not
cycling
Inspect the power and controller connections are
properly fastened. Be sure there is sufficient power to
cycle the linear servo actuator shaft. Reference the
linear servo actuator equipment literature provided with
this manual.
Pressure sensor reading low
pressure
Inspect pressure sensor calibration. Inspect position of
the pressure sensor to ensure the to ensure the part
was installed properly. Ensure the pressure sensor is
properly functioning. Be sure there are no leaks from the
seal cartridge assembly.
Seal cartridge assembly
malfunction
Inspect for sufficient supply pressure. Inspect metering
rod for binding. Inspect bearing for binding. Inspect
metering rod for wear and debris.
Supply equipment not cycling Ensure there is sufficient air pressure. Reference supply
equipment literature.
Meter Leakage
Loose fitting Isolate leak and tighten fitting.
Material metering portion
failure
Ensure all fittings and gauges are properly tightened.
Pump seal failure Tighten packing nut on pump. Ensure there is sufficient
lubricant in the wet cup. Replace seal(s), if necessary.
Valve seal failure
Replace seal (s). Replace or repair scored or damaged
needle, if necessary. Replace or repair scored or
damaged sealing face, if necessary.

8
Issued 06/17
Original copyright date 2017. Nordson and the Nordson logo are registered trademarks of Nordson Corporation.
is a registered trademark of Nordson Corporation.
All other trademarks are the property of their respective owners.
Table of contents
Other Nordson Measuring Instrument manuals
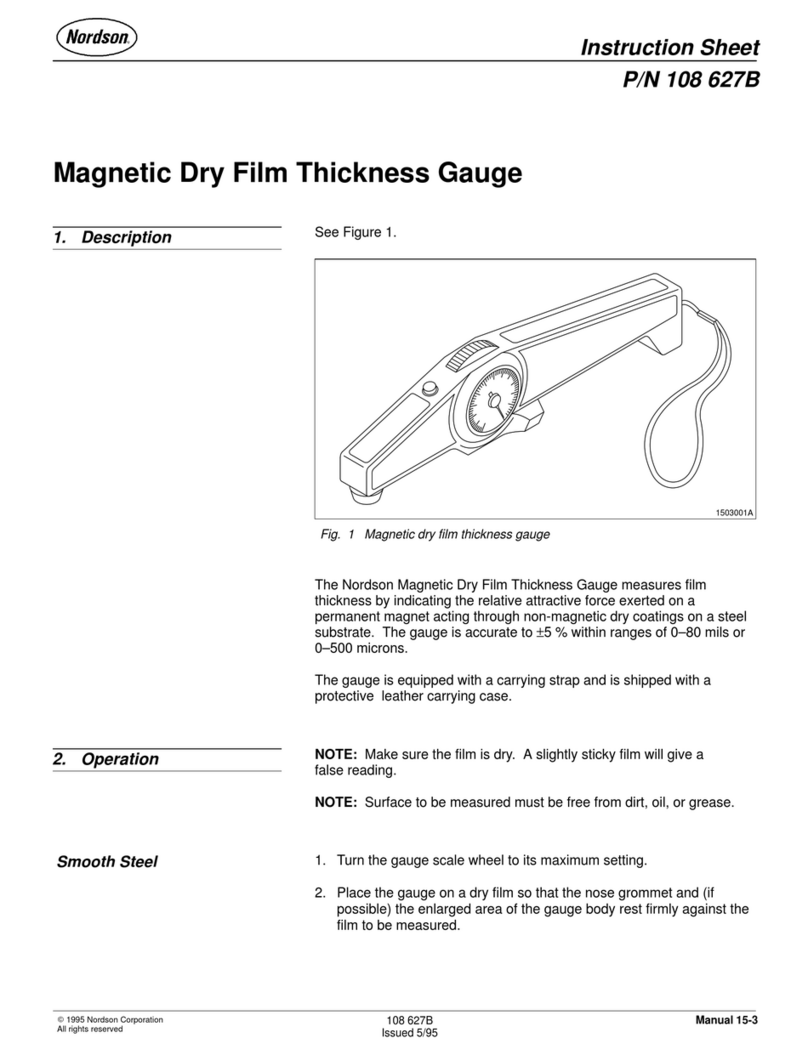
Nordson
Nordson 108 627B User manual
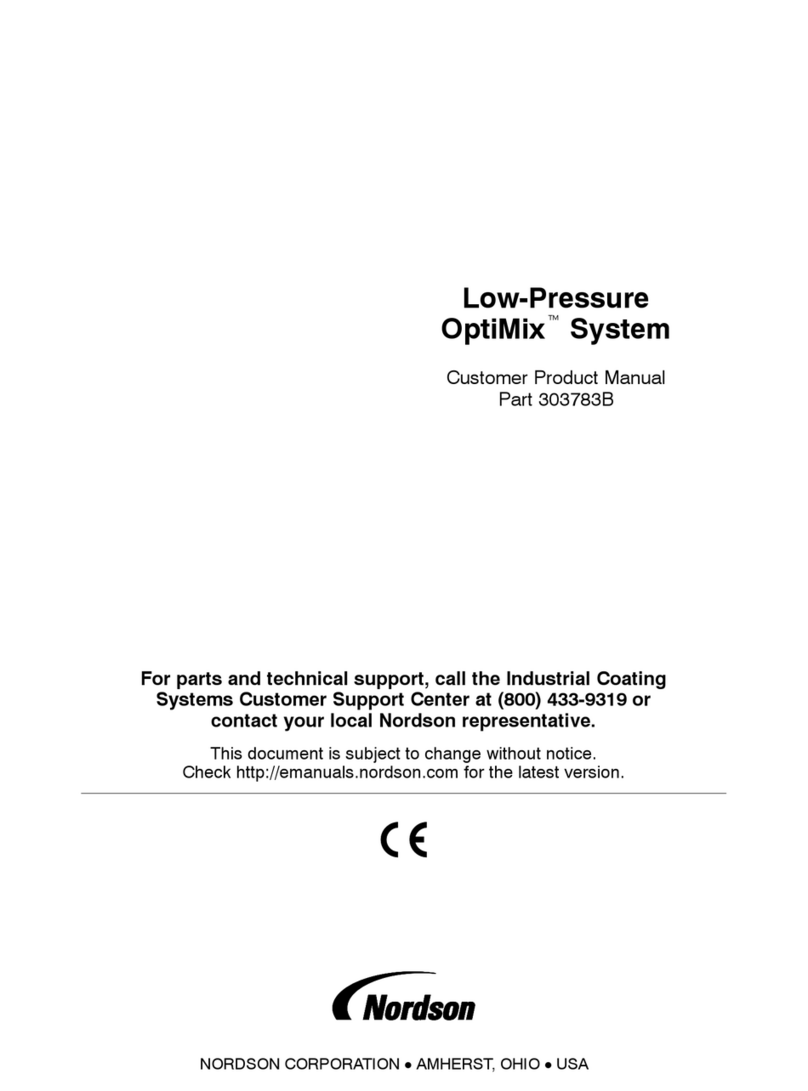
Nordson
Nordson OptiMix Reference guide

Nordson
Nordson BM 200 User manual
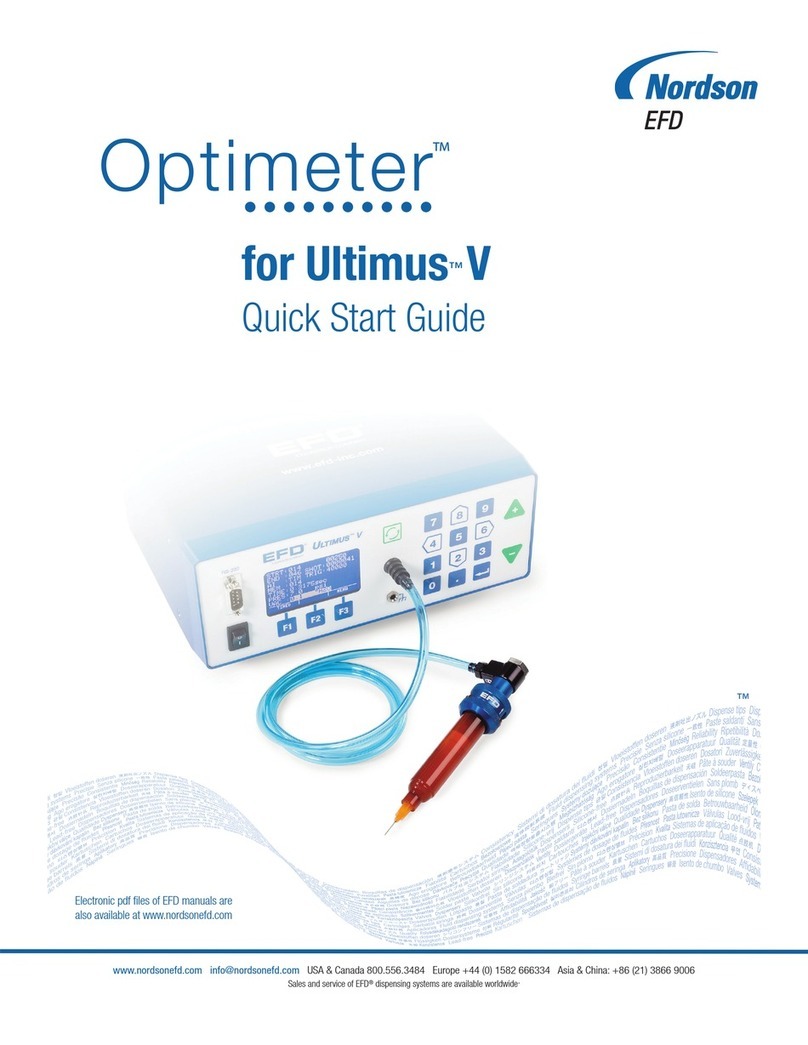
Nordson
Nordson Optimeter User manual
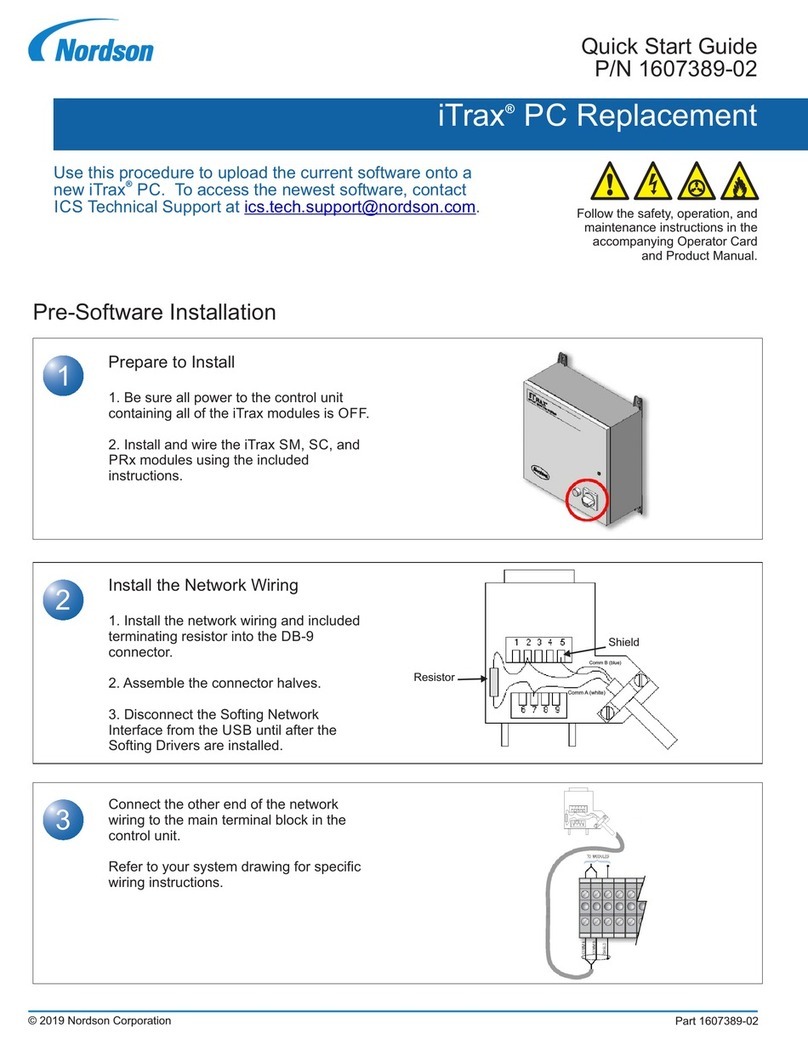
Nordson
Nordson iTrax User manual

Nordson
Nordson DAGE XD7600NT User manual
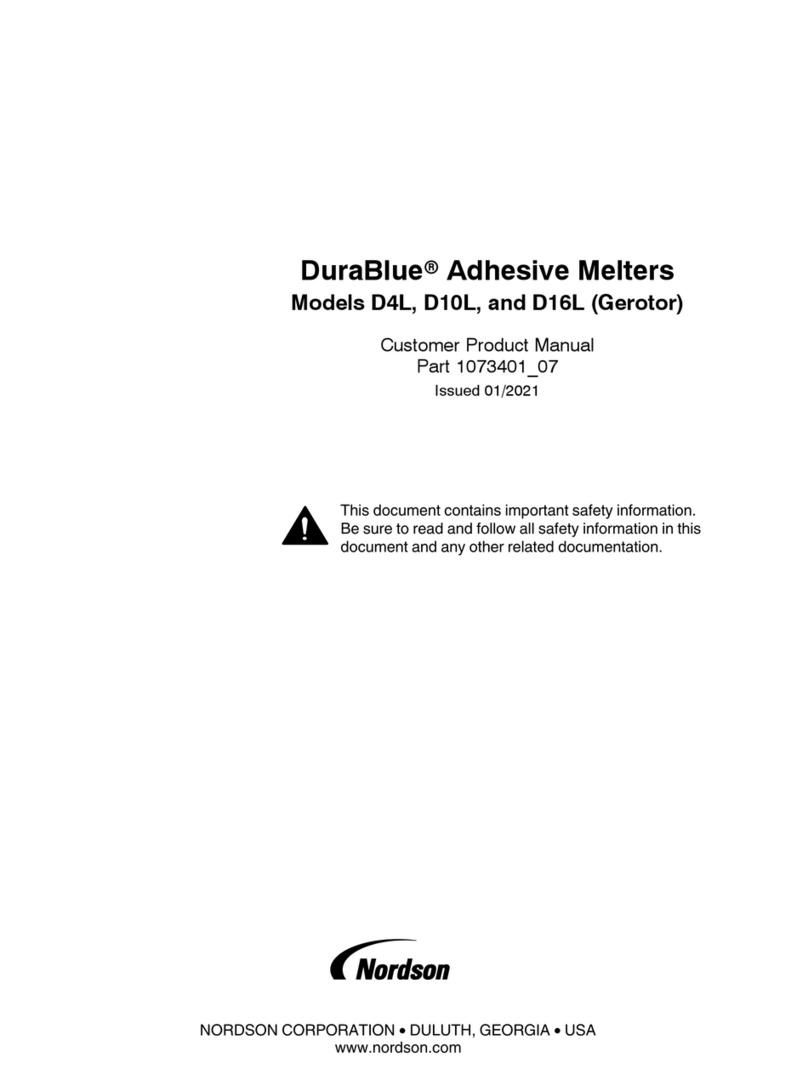
Nordson
Nordson DuraBlue D4L User manual

Nordson
Nordson Rhino SD2 User manual
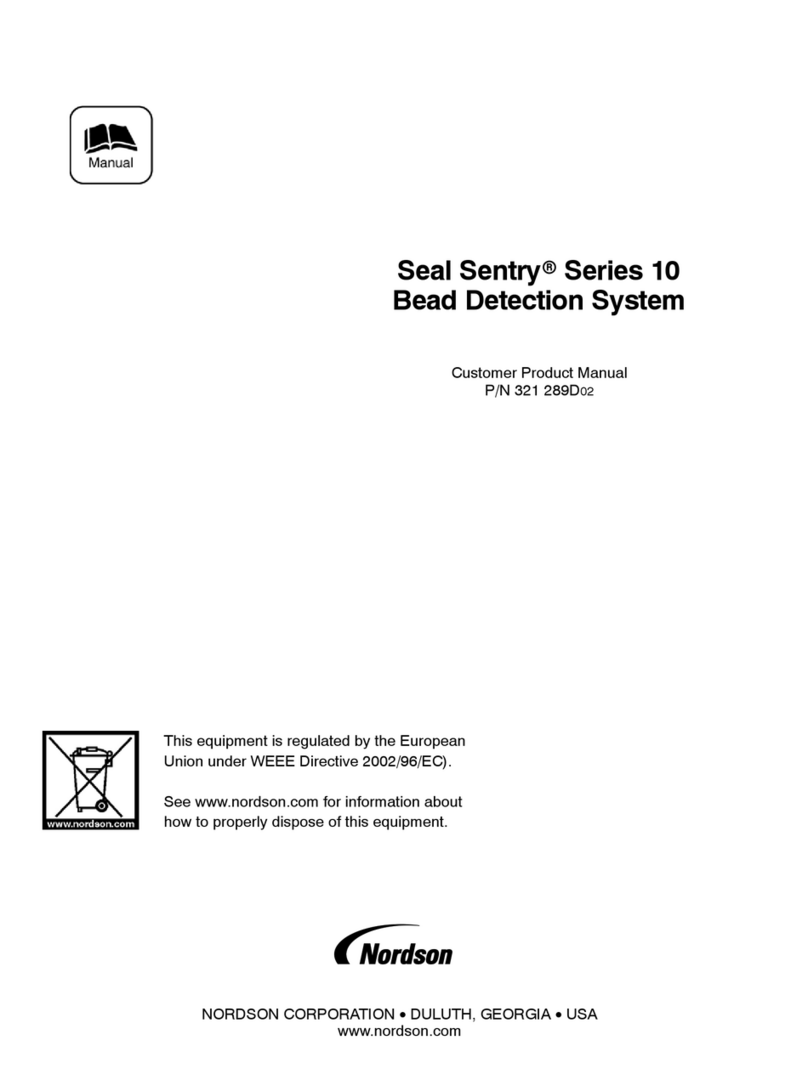
Nordson
Nordson Seal Sentry 10 Series Reference guide
Popular Measuring Instrument manuals by other brands

Bosch
Bosch UniversalLevel 3 Original instructions
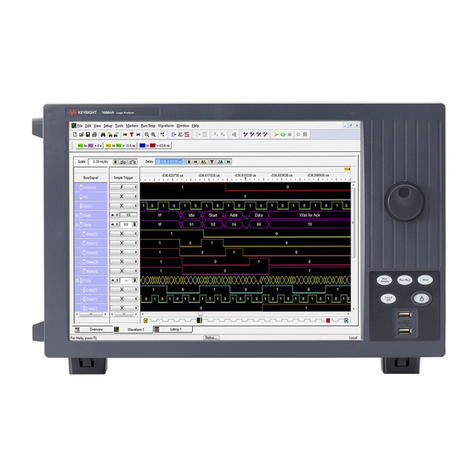
Keysight Technologies
Keysight Technologies 16861A Service guide
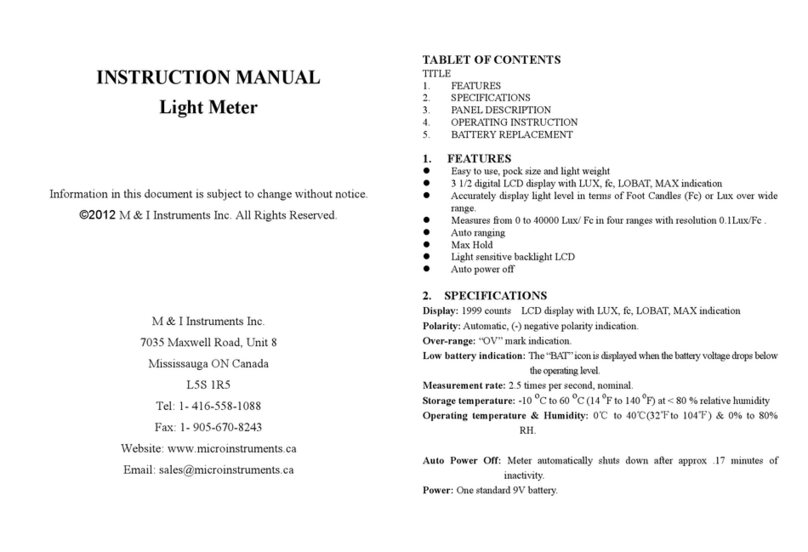
M & I Instruments
M & I Instruments DT-86 instruction manual
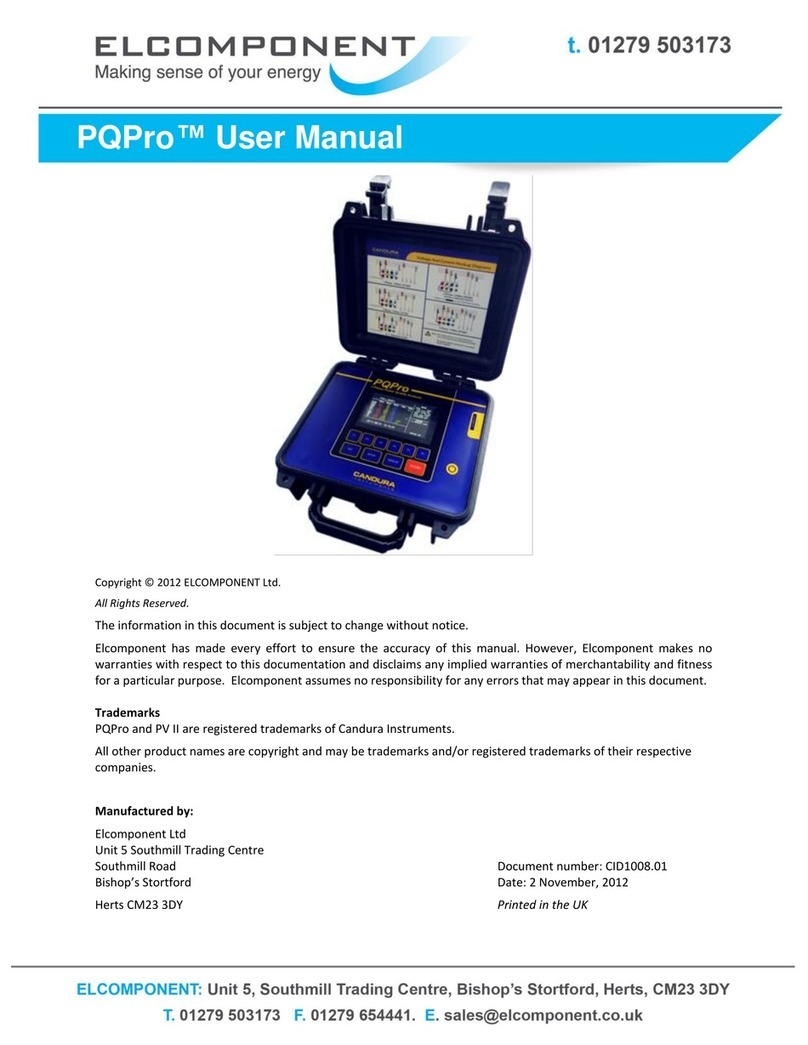
Elcomponent
Elcomponent PQPro user manual
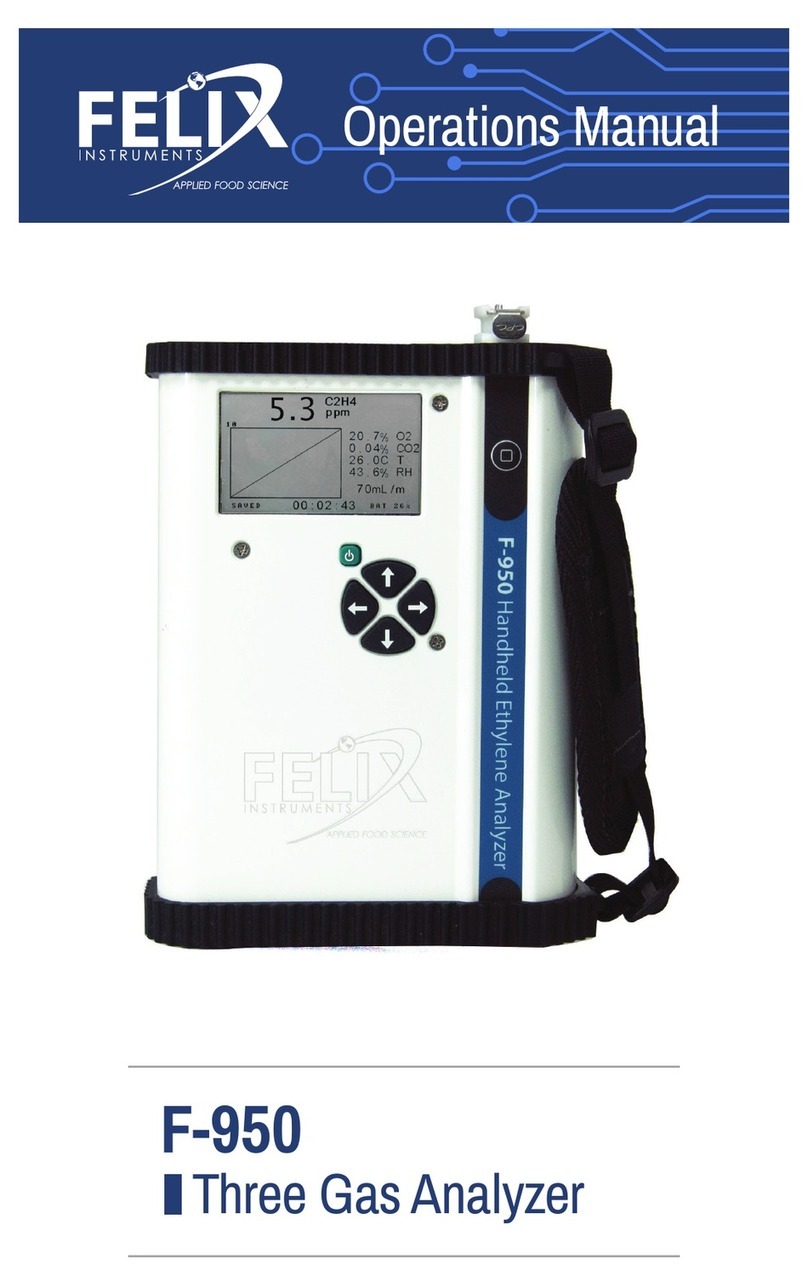
Felix Storch
Felix Storch F-950 Operation manual

Sper scientific
Sper scientific AquaShock 850046K user manual