Ntron SIL O2 Mounting instructions

1 | P a g e R e v . 1 .1
I s s u e 3 0 - 11-2018
The
SIL O2Oxygen Analyser
User Operation Manual
Rev. 1.1
30/11/2018

2 | P a g e R e v . 1 .1
I s s u e 3 0 - 11-2018

3 | P a g e R e v . 1 .1
I s s u e 3 0 - 11-2018
Contents
1. Introduction ....................................................................................................................................................6
1.1 The purpose of this User and Operation Manual...................................................................................6
2. Installation and Operation...............................................................................................................................7
2.1 Notes for a safe installation...................................................................................................................7
2.2 Installation...........................................................................................................................................10
2.2.1 Mounting the SIL O2 Analyser.......................................................................................................10
2.3 Electrical and Interface Connections...................................................................................................11
2.3.1 Sensor Input and Customer Interface Wiring..................................................................................11
2.3.2 Operational Settings and Wiring Configuration .............................................................................12
2.3.3 Typical Relay Configuration...........................................................................................................13
2.3.4 Sensor Process Connection options ................................................................................................15
2.4 Operation.............................................................................................................................................16
2.4.1 Calibration Procedures....................................................................................................................16
2.4.2 Setting the Zero point. ....................................................................................................................17
2.4.3 SPAN Calibration...........................................................................................................................18
..........................................................................................................................................................................18
3. Operational safety and maintenance instructions..........................................................................................19
3.1 Fault conditions...................................................................................................................................19
3.2 Wire break...........................................................................................................................................19
3.3 System faults.......................................................................................................................................19
3.4 Troubleshooting ..................................................................................................................................20
Possible Faults and their solutions........................................................................................................................20
3.4.1 Possible Sensor Faults ....................................................................................................................21
3.5 General Maintenance ..........................................................................................................................22
4. Specifications................................................................................................................................................23
5. Appendices ...................................................................................................................................................26
5.1 SIL O2 Analyser and Sensor Connection Diagrams ...........................................................................27
5.2 SIL O2 Analyser CE and ATEX Certificates......................................................................................28
5.3 Sensor CE and ATEX Certificates......................................................................................................29

4 | P a g e R e v . 1 .1
I s s u e 3 0 - 11-2018
Revision History
Revision No.
Change Description
Date
0
First Issue
19-10-2018
1
Note added for Non-ATEX Sensor usage
22-10-2018
1.1
Reference to 15% O2 in trouble shooting section removed.
30-11-2018
Calibration Span instruction amended and note added

5 | P a g e R e v . 1 .1
I s s u e 3 0 - 11-2018

6 | P a g e R e v . 1 .1
I s s u e 3 0 - 11-2018
1. Introduction
The Ntron SIL O2 Analyser is a ATEX approved SIL 2 rated Oxygen measuring instrument. It contains three
programmable alarm settings, industry standard Analogue Output(active source) and a non-programmable safety
trip relay. The range of operation is 0 to 25% Oxygen. The Reasolution is to 0.01%.
Together with one of the range of Ntron ATEX approved Oxygen Sensors, it forms a SIL2 rated measurement
unit which can operate on its own or as part of a larger installation.
Note. Non-Atex (Ex) Sensors variants of the models listed in the manual may also be used with the SIL O2
Analyser as long as they are installed in a Non-ATEX (Ex) or ‚Safe‘ area or zone.
The Alarm settings are typically factory set according to the end user’s requirements. Interface software and
hardware is available for the user to perform such functions themselves. Contact Ntron for further details.
1.1 The purpose of this User and Operation Manual
This Manual is limited to providing the user with necessary details on installation, interface wiring, operation
and maintenance of the SIL O2 Analyser and Oxygen Sensor, to ensure safe and reliable operation of this
Analyser and Sensor unit.
Note: This manual does not cover the design or application of a safety Instrumented System (SIS) into
which the SIL O2 Analyser unit may be incorporated. Further details of this can be obtained in the Ntron
SILO2 Technical and Safety Manual.
Increase (UP) and
Decrease (Down)
Pushbuttons. Pressing
simultaneously enables
entry into the
calibration mode.
Power, Error/Fault and
Alarm Level indicators
RS232
Communications
connection
The main user interface features
4-Digit LCD
Display/Readout

7 | P a g e R e v . 1 .1
I s s u e 3 0 - 11-2018
2. Installation and Operation
Note: For system application information, consult the SIL O2 Analyzer
Technical User Manual
2.1 Notes for a safe installation
Please do not short-circuit the + and -ve sensor cables while connecting to the SIL O2 Analyzer. This
could damage the sensor.
This system can also be used in a non-Ex area application. In all applications, the SIL O2 Analyzer Din
rail module is always located in the non-Ex area!
Assignment of the mounting rail housing terminals with intrinsically safe circuits and non-intrinsically
safe circuits is indicated on the nameplate and is clearly indicated. In addition, the 4-pin terminals of
intrinsically safe circuits follow the standard color protocol for intrinsically safe terminal connections and
are coloured Blue. Connections for intrinsically safe external circuits are arranged in such a way that, in
accordance with EN 60079-11, the exposed parts are at least 50 mm from the exposed connections and
parts of the non-intrinsically safe circuits.
For safe operation, a protective ground/earth connection to terminal 13 or 15 should be made.
Assembly / disassembly, installation, operation and maintenance may only be performed by qualified
personnel in accordance with regulatory requirements and the SIL O2 Oxygen Analysis Manual.
During installation, the technical data and the electrical values of the connected circuits must be
respected.
Electrical supply. The SILO2 Analyser operates with an Extra low Voltage (ELV) supply. (See
specification section in this manual)No special precautions are necessary but the ELV supply to the SIL
O2, if generated from a Mains power source, that mains power source and associated wiring must be in
accordance with IEC/EN standards and is the responsibilty of the user to provide and to ensure correct
and safe installation of such.
When the SIL O2 analyzer is integrated into another system, also refer to the system manual for
additional operational information.
The Ntron SILO2 Analyser is designed for use with a range of Ntron ATEX certified Oxygen Sensors to
form a measurement system.These Sensor options are detailed in the Specification section of this manual.
If the SIL O2 Analyser has been supplied with a Sensor, the two units will have been calibrated at the
Ntron factory prior to delivery. Otherwise, if a Sensor is supplied separately from the SIL O2 Analyser, a
calibration will be required prior to putting the system into operational service.

8 | P a g e R e v . 1 .1
I s s u e 3 0 - 11-2018
The Ntron Sensors suitable for use with the SIL O2 analyser are listed in the Installationn section which
follows.

9 | P a g e R e v . 1 .1
I s s u e 3 0 - 11-2018
The SIL O2 oxygen analyzer is an associated explosion-proof [Ex ia] IIC or [Ex ib] IIC electrical device
and should always be used outside potentially explosive areas (in a safe area). Only electrical circuits,
certified as intrinsically safe, can be connected to other intrinsically safe circuits in the Ex zone.
Before operation, the intrinsic safety must be verified for the SIL O2 oxygen analyzer circuit connected
to the circuit of other equipment, including the interconnecting cabling.
The data contained in the EC test certificate and the regulations of EN 60079-14: 2011-10 must be
observed.
The Sensors are ATEX rated devices and have certain conditions of use assigned.
Note. Non-Atex (Ex) Sensors variants of the models listed in the manual may also be used with the
SIL O2 Analyser as long as they are installed in a Non-ATEX (Ex) or ‚Safe‘ area or zone.
For Acetal-bodies Sensors, the following instructions apply;
The Sensor should be installed in such a way that it is not subject to impact by other objects and should
not be located close to additional heat sources. Note the ambient temperature range as it appears on the
Sensor labelling.
Care must be taken when installing equipment with plastic enclosures or plastic parts of enclosures to
ensure that the equipment is protected from any situations that could cause a build up of static charge. The
equipment must not be installed into locations in which it could come into contact with, through normal
or abnormal circumstances, fast moving dust laden air/gas or non-conductive fluids. The equipment must
be cleaned only with a damp cloth.

10 | P a g e R e v . 1 .1
I s s u e 3 0 - 11-2018
2.2 Installation
The installation must be in accordance with the local electrical codes and taking into account the details
in the Specification section of this manual.
The SIL O2 analyzer is designed for DIN rail mounting and can be supplied mounted in an additional
enclosure or provided without an additional enclosure for customer mounting in a system enclosure or
control panel.
The Sensor option chosen will determine the process connection/installation for that Sensor type. The
Sensor types and related process connections are given below.
Sensor Type: Process Connection:
Model OC-25 Ntron Sensor base, Flow Through or Tri-Clamp
Model OC-26 KF40 Flange
Model OC-200’Oxyprobe‘ series Bushing insert or Extract* Probe Holder
The Sensor is typically supplied with a correcponding connection cable of either standard length or to a
customer specified length.
*The Ntron OxyExtract Manual or Automatic probe insertion mechanism.
2.2.1 Mounting the SIL O2 Analyser
Mount the SIL O2 Analyser onto 35mm DIN rail as shown. Any Trunking/wireways above and below
the Analyer when in situ, must be positioned so that there is a minimum of 30mm clearance between
such trunking and the Analyser connection terminals.
115mm
100mm
67mm

11 | P a g e R e v . 1 .1
I s s u e 3 0 - 11-2018
2.3 Electrical and Interface Connections
2.3.1 Sensor Input and Customer Interface Wiring
The Ntron ATEX Sensor selected for use with the SIL O2 Analyser as listed in the Installation section
previously, has intrinisically safe parameter values which match the Isolation Barrier output which is built into
the SIL O2 Analyser. The Sensor connects to the Blue terminals as shown below.
The dark Grey terminals are for safe (Non-Ex area) customer interface connections. See the configuration
section on the following page.
13 14 15 16
+ve -ve
Customer Clean
Earth
O2 Sensor
1 2 3 4
+ -24 VDC
Relay 1
To customer Circuit
5 6 7 8
Relay 2 Transistor(DO)
To customer Circuit
9 10 11 12
Relay 3 4-20mA (AO)
To customer Circuits

12 | P a g e R e v . 1 .1
I s s u e 3 0 - 11-2018
2.3.2 Operational Settings and Wiring Configuration
The SIL O2 Analyser has two presettable alarm levels and associated Relays, referred to as RL1 and RL2. It
also has a third presettable alarm level with an associate Transistor Digital Output (DO) The programmed
setting of these outputs can vary depending on application. The Inspection and Calibration certificate supplied
with each SIL O2 Analyser and Sensor unit will detail these settings. See the Ntron SIL O2 Technical and
Safety manual for further details.
The SIL O2 Analyser has a main trip Relay referred to as RL3. This is not programmable and is normally
open(contacts)/de-energised when the Analyser is not under power. The Relay energises and its associate
contacts close when power is applied and the Analyser and Sensor are healthy and ready to operate.
The Analogue output is an industry standard 4-20mA active source output. The connected circuit should be of
maximum resistance 420 ohm.
To meet the SIL 2 operational requirements as an Analyser and Sensor unit, the main trip Relay is required to be
connected in series with other elements within the Analyser as shown in the diagrams below. For any other
configurations, See the Ntron SIL O2 Technical and Safety manual for further details.
*Special case for use of the 4-20 mA analogue output within a safety system
When using the 4-20 mA analogue output from the SILO2 Oxygen Analyser within the safety
system, this signal would typically be required to be processed by a safety PLC which would then
activate the Final Trip Element. See the Ntron SIL O2 Technical and Safety manual for further
details.
Relay 3 Main Trip
Relay 1 or 2
Relay 3 Main Trip
Analogue Output
1/5
2/6
9
10
9
10
11
12

13 | P a g e R e v . 1 .1
I s s u e 3 0 - 11-2018
2.3.3 Typical Relay Configuration
Power to the Analyser
Relay
Contact 1
Relay Contact
2
Relay Contact
3
Comments
Power Off
(All relay contacts in Fail
Open condition)
Relays
De-energised
Power on and system
good/healthy
**
**
All Relays
Energised
Power on and O2 alarm
level(s) reached
*
*
Relays 1 & 2
De-energised
Power on and System fault
**
**
All Relays
De-energised
These relays are programmed to respond to the measured Oxygen level setpoints (Alarms), rising or falling in
the range 0-25% Oxygen. These are pre-set to the customer’s requirements.
They operate in ‘Fail Safe’ mode which means that they are energized (under current), presenting a closed
contact to the customer/user when the SIL O2 module is under power and the status is healthy/good.
When at a level setpoint (Alarm) or when the SIL O2 module is not-powered, the relays are de-energised (not
under current), presenting an open contact to the customer/user. This is also known as ‘Fail Open’ (FO)
condition.
Transisitor (DO)
This is an NPN device that can switch 24VDC and can be configured to be normally open or normally closed.
Analogue 4-20mA
This is an active output and requires connection to a passive external circuit suitable for proper operation.
It is set to the range 0-25% Oxygen / 4-20mA (0% Oxygen = 4mA, 25% Oxygen = 20mA.)
This range can not be adjusted.
If the 4-20 mA output is not used, the SIL O2 terminals T11 and T12 must be wired by the user. This output is
internally connected in series with the SIL O2 Analyzer digital display, which will not work if the
aforementioned terminals are in open circuit!

14 | P a g e R e v . 1 .1
I s s u e 3 0 - 11-2018

15 | P a g e R e v . 1 .1
I s s u e 3 0 - 11-2018
2.3.4 Sensor Process Connection options
The Sensors are suitable for mounting directly onto process
Lines via a selection of process fittings. The electrical signal connectors
are rated to IP67.
Tri-Clamp Sensor Base
Flow Through Sensor Base
OC-25 Sensor
OC-26 Sensor KF40 Process fitting
KF40 Process fitting onto pipeline
OC-200 Sensor with Screwed Bush Process
fitting

16 | P a g e R e v . 1 .1
I s s u e 3 0 - 11-2018
2.4 Operation
Before turning on the SIL O2 analyzer for the first time or after disconnecting the sensor for maintenance /
replacement, make sure that a working sensor is connected. Otherwise, the SIL O2 analyzer will go into failure
mode, with the red error indicator on and the RL3 relay disabled. As the fault circuit performs a cyclic check
every 30 seconds or so. When the sensor is connected, resetting the red indicator and relay 3 occurs
automatically, but it is advisable to power off the system to allow the sensor to be disconnected / reconnected
under normal circumstances, if possible.
Turn on/apply power to the SIL O2 Analyser.
When operating under normal process/system conditions, the SIL O2 Analyser will give a digital readout of the
measured Oxygen level (from the Sensor in the process).
This measurement is converted into a 4-20mA output signal proportional to the Oxygen being measured.
If an Alarm level even occurs, the relevant programmed output device will operate (Relay or Transistor) and the
ineterface circuit to the user equipment will be interrupted. For further alarm or fault events and their conditions,
please see the troubleshooting section at the end of this Manual.
2.4.1 Calibration Procedures
The SIL O2 Analyser and Sensor unit requires periodic calibrations performing, the timing between such
calibrations being determined by the application and process requirements.
Typically, a periodic calibration check would reveal if any calibration adjustment is necessary. The SPAN
calibration point of 20.9% O2 (Air) is the important setting and typically, if calibration adjustment is required,
this is the value that would be adjusted. This adjustment can be made ussing ambient air as the calibration
standard or, for greater accuracy, certified cylinder gas at 20.9% O2.
It is possible to also adjust the Zero point of the SIL O2 Analyser. Typically this would only be required when
fitting a new/replacement Sensor. A Complete calibration procedure is given below.
Note: Calibration Adjustment procedure.
The displayed number change starts with the digit to the far right of the decimal point. Press and hold the
Up or Down buttons to change the reading. This gives an accelerated adjustment. More accurate
adjustment is achieved by pressing the Up or Down button at one press (press release, release of press,
etc.). When the display reads 20.9%, the calibration of the range is complete
19.05
19.05
1, 2, 3….
6
6
1-

17 | P a g e R e v . 1 .1
I s s u e 3 0 - 11-2018
2.4.2 Setting the Zero point.
This must be done each time a new sensor is installed before a span calibration is performed.
Subsequently, a zeroing can be performed periodically as needed.
A zeroing operation requires the application of a zero oxygen gas to the sensor, typically nitrogen (minimum
quality <100 ppm). Note: Accessing the Zero function when the sensor is in ambient air (20.9% O2) will result
in an error / fault condition.
Depending on the type of sensor installed, zero gas must be applied through a process fitting or calibration
adapter, and be sure to leave a free exhaust at a suitable location so that the sensor does not become pressurized.
The sensors to be used with the SIL O2 unit will generally give a small output at zero oxygen levels. The zero
adjustment function allows the user to adjust this small signal so that the SIL 2 analyzer displays 0.0 when no
oxygen is present in the measured gas.
•ZERO mode is activated after pressing the UP and DOWN button simultaneously for more than one
second. As an acknowledgment of receipt, the A3 LED flashes. An adjustment of the indicated value is
made by pressing the UP or DOWN buttons individually as required.
•The change starts with the digit to the right of the decimal point. (00.0) Press and hold the Up or Down
buttons to change the displayed reading. This allows an accelerated adjustment. Accurate adjustment is
achieved by pressing the Up or Down button at one press (press release, release of press, etc.). When
the display reads 0.0% O2, the setting is complete. By simultaneously pressing the two buttons or a
delay of 20 seconds, the ZERO operating mode ends.
0.00

18 | P a g e R e v . 1 .1
I s s u e 3 0 - 11-2018
2.4.3 SPAN Calibration
This can be done periodically or as needed in accordance with the requirements of the calibration protocol.
Calibration can be performed by applying either clean ambient air or a 20.9% certified oxygen rate to the sensor.
Note:
•The SIL 2 analyzer should only be calibrated at approximately 20.9% oxygen.
•If an ambient air calibration is performed, it is recommended to confirm the oxygen level with a
certified portable oxygen analyzer prior to calibration.
•If a zero setting is made first, then after the end of the zero operation mode, the Span mode is
automatically activated after a delay of 20 seconds.
•If A Span only calibration is required, then just press the UP or DOWN buttons individually to
increase or decrease the displayed value of oxygen to read 20.9. Note: Ensure the Sensor is in
20.9% oxygen when you do this!
•Calibration complete.
20.90
20.90

19 | P a g e R e v . 1 .1
I s s u e 3 0 - 11-2018
3. Operational safety and maintenance instructions.
If it is assumed that safe operation is no longer possible, the device must be taken out of service and protected
against accidental use. The reasons can be:
visible damage to the device
failure of the electrical function
long shelf life at temperatures above 85 ° C
Transport damage
Before the device can be put back into service, a professional routine check must be carried out in accordance
with DIN EN 61010, part. 1. This examination must be carried out by the manufacturer. Repair work on Ex devices
may only be carried out in accordance with § 9 of Ex. (Elex V).
3.1 Fault conditions
The SIL O2 Analyzer failure operation is not locked out by a fault. When a fault condition is repaired, the trip
relay RL3 and the red fault indicator will return to their "healthy" or "operational" state after a few seconds
following an automatic internal cyclic check.
3.2 Wire break
When manually disconnecting the sensor (for example for maintenance) or following a break in the sensor
connection cable, the SIL O2 Analyzer RL3 fault relay switches off and interrupts the safety circuit.
The red fault indicator will illuminate on the SIL O2 analyzer and the 4-20 mA analog output will reach a constant
high value of 22.0 mA. At the same time, the setpoint relays RL1 and RL2 will be deactivated.
When the sensor is reconnected or the cable fault is corrected, the RL3 relay automatically resets after about 30
seconds and the red LED goes out. At the same time, RL1 and RL2 are reset according to their setpoints and the
measured gas level. See also note on page 13 of this manual for reset requirements under specific conditions.
3.3 System faults
A number of internal faults in the SIL O2 analyzer generate a fault output and interrupt the safety circuit. In some
cases, cycling the power supply of the SIL O2 analyzer may be sufficient to remedy the problem. Otherwise,
please contact Ntron for assistance.

20 | P a g e R e v . 1 .1
I s s u e 3 0 - 11-2018
3.4 Troubleshooting
Possible Faults and their solutions
The following possible conditions are applicable to a system (Sil Analyser and Sensor) already installed
and commissioned. Some conditions below may also be applied to new systems not yet commissioned.
•Action: Performing a Zero calibration when the Oxygen Sensor is in ambient air.
Problem: An incorrect Zero level input to the Analyser will result in an overrange fault. This can
occur if a Zero calibration is performed when the Sensor is in ambient air. If this occurs, the Red fault
LED will illuminate and the Analyser display and Analogue output will read an over-range value. The
Alarm level LED’s may also illuminate. This may also occur if a genuine overrange event takes place,
with gas containing more than 25% O2 being applied. (25%O2 displayed)
Solution: re-calibrate with Nitrogen gas (Zero) and then re-calibrate at the Span point of 20.9%.
•Action: Powering on the Analyser with no sensor connected or a wire break to the sensor.
Problem: If the sensor is disconnected, this would ordinarily cause relays R1, R2 and R3 to de-
energise. Analyser display and Analogue output will read a fault value. (28% O2 displayed and 22mA
output)
Solution: Check Sensor wiring and connect the sensor to the Analyser. After approximately 30
seconds, the Analyser will reset and the Red LED should extinguish.
•Action: Unable to perform a Span calibration.
Problem: The Analyser cannot be adjusted to display 20.9% O2 during Span calibration.
Solution: The Sensor may be approaching end of life or has been damaged and cannot generate
sufficient output. Replace the sensor
Alarm level LED’s may or may not be illuminated depending on configuration.
•Action: Alarm Level LED’s (Yellow) illuminated.
Problem: Alarm level LED’s illuminated.
Solution: Genuine Oxygen level alarm event.
Incorrect sample gas levels being applied to the Sensor or incorrect alarm level settings are configured
within the Analyser. If this is not expected then check sample gas with independent instrument
gas/and/or re-configure Analyser Alarm setpoints. This will require interface with PC based software.
Table of contents
Other Ntron Measuring Instrument manuals
Popular Measuring Instrument manuals by other brands
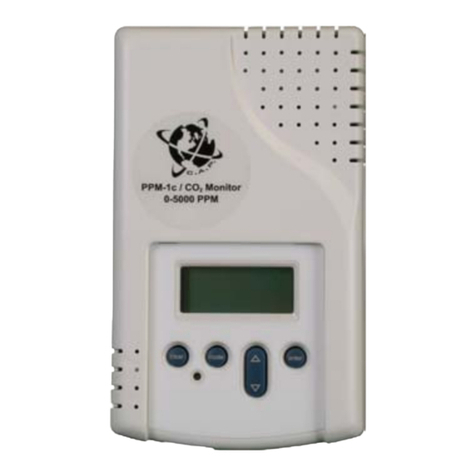
CAP
CAP Part Per Million PPM-1c manual
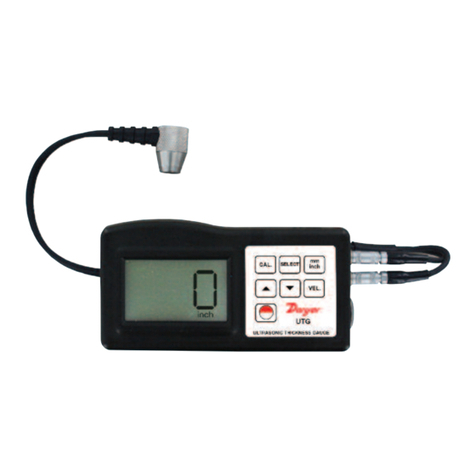
Dwyer Instruments
Dwyer Instruments UTG Installation and operating instructions

REED
REED PHT-316 instruction manual
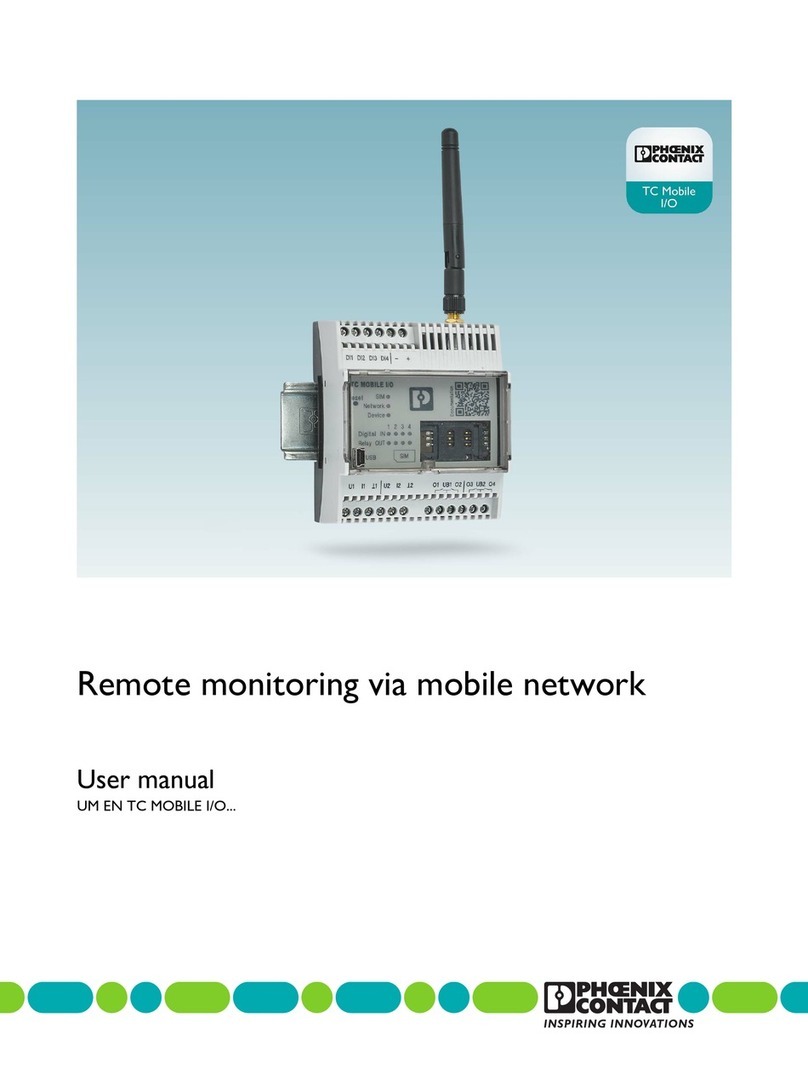
Phoenix Contact
Phoenix Contact TC MOBILE I/O Series user manual
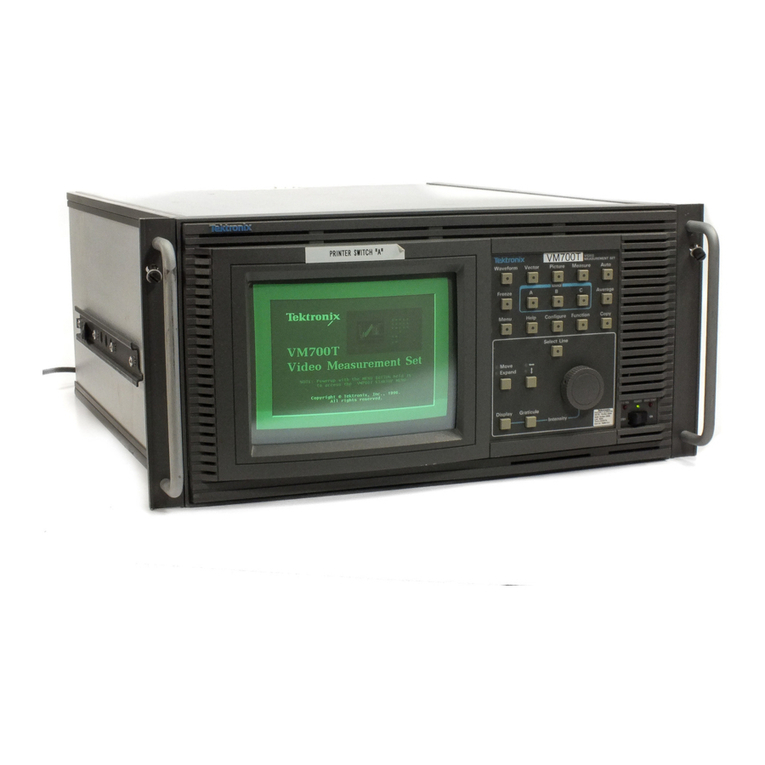
Tektronix
Tektronix VM700T user manual
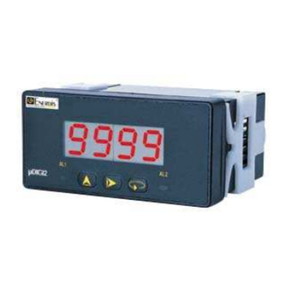
Chauvin Arnoux
Chauvin Arnoux Enerdis mDIGI2-P user manual