Omron SMARTSLICE GRT1-ML2 Quick user guide

Trajexia motion control system
TJ1-MC04, TJ1-MC16, TJ1-ML04, TJ1-ML16, TJ1-PRT, TJ1-DRT, TJ1-CORT, TJ1-FL02
GRT1-ML2
HARDWARE REFERENCE MANUAL
Cat. No.
I51E-EN-05
Austria
Tel: + ()
www.omron.at
Belgium
Tel: + ()
www.omron.be
Czech Republic
Tel: +
www.omron-industrial.cz
Denmark
Tel: +
www.omron.dk
Finland
Tel: + ()
www.omron.fi
France
Tel: + ()
www.omron.fr
Germany
Tel: + ()
www.omron.de
Hungary
Tel: +
www.omron.hu
Italy
Tel: +
www.omron.it
Middle East & Africa
Tel: + ()
www.omron-industrial.com
Netherlands
Tel: + ()
www.omron.nl
Norway
Tel: + ()
www.omron.no
Poland
Tel: + ()
www.omron.pl
Portugal
Tel: +
www.omron.pt
Russia
Tel: +
www.omron-industrial.ru
Spain
Tel: +
www.omron.es
Sweden
Tel: + ()
www.omron.se
Switzerland
Tel: + ()
www.omron.ch
Turkey
Tel: +
www.omron.com.tr
United Kingdom
Tel: + ()
www.omron.co.uk
OMRON EUROPE B.V.
Wegalaan -, NL- JD, Hoofddorp, The Netherlands. Tel: + () Fax: + () www.omron-industrial.com
Authorised Distributor:
Note:
Although we do strive for perfection, Omron Europe BV and/or its subsidiary and affiliated companies do not warrant or make any representations regarding the correctness or completeness
of information described in this catalogue. Product information in this catalogue is provided ‚as is‘ without warranty of any kind, either express or implied, including, but not limited to, the
implied warranties of merchantability, fitness for a particular purpose, or non-infringement. In a jurisdiction where the exclusion of implied warranties is not valid, the exclusion shall be
deemed to be replaced by such valid exclusion, which most closely matches the intent and purpose of the original exclusion. Omron Europe BV and/or its subsidiary and affiliated companies
reserve the right to make any changes to the products, their specifications, data at its sole discretion at any time without prior notice. The material contained in this catalogue may be out of
date and Omron Europe BV and/or its subsidiary and affiliated companies make no commitment to update such material.
Cat. No. IE-EN-
Trajexia motion control system HARDWARE REFERENCE MANUAL
Cat. No.
I51E-EN-04

HARDWARE REFERENCE MANUAL I
Revision 5.0
Notice
OMRON products are manufactured for use according to proper procedures
by a qualified operator and only for the purposes described in this manual.
The following conventions are used to indicate and classify precautions in
this manual. Always heed the information provided with them. Failure to
heed precautions can result in injury to people or damage to property.
Definition of precautionary information
Trademarks and Copyrights
PROFIBUS is a registered trademark of PROFIBUS International.
MECHATROLINK is a registered trademark of Yaskawa Corporation.
DeviceNet is a registered trademark of Open DeviceNet Vendor Assoc INC.
CIP is a registered trademark of Open DeviceNet Vendor Assoc INC.
CANopen is a registered trademark of CAN in Automation (CiA).
ModbusTCP is a registered trademark of Modbus IDA.
Trajexia is a registered trademark of OMRON.
Motion Perfect is a registered trademark of Trio Motion Technology Ltd.
All other product names, company names, logos or other designations
mentioned herein are trademarks of their respective owners.
/i
WARNING
Indicates a potentially hazardous situation, which, if not avoided,
could result in death or serious injury.
Caution
Indicates a potentially hazardous situation, which, if not avoided,
may result in minor or moderate injury, or property damage.
© OMRON, 2010
All rights reserved. No part of this publication may be reproduced, stored in a retrieval sys-
tem, or transmitted, in any form, or by any means, mechanical, electronic, photocopying,
recording, or otherwise, without the prior written permission of OMRON.
No patent liability is assumed with respect to the use of the information contained herein.
Moreover, because OMRON is constantly striving to improve its high-quality products, the
information contained in this manual is subject to change without notice. Every precaution
has been taken in the preparation of this manual. Nevertheless, OMRON assumes no
responsibility for errors or omissions. Neither is any liability assumed for damages resulting
from the use of the information contained in this publication.

HARDWARE REFERENCE MANUAL II
Revision 5.0
About this manual
This manual describes the installation and operation of the Trajexia Motion
Control System.
Please read this manual and the related manuals listed in the following table
carefully and be sure you understand the information provided before
attempting to install or operate the Trajexia Motion Control units. Be sure to
read the precautions provided in the following section.
/i
Name Cat. No. Contents
Trajexia motion con-
trol system
QUICK START
GUIDE
I50E Describes how to get quickly familiar
with Trajexia, moving a single axis using
MECHATROLINK-II, in a test set-up.
Trajexia motion con-
trol system HARD-
WARE
REFERENCE MAN-
UAL
I51E Describes the installation and hardware
specification of the Trajexia units, and
explains the Trajexia system philosophy.
Trajexia motion con-
trol system
PROGRAMMING
MANUAL
I52E Describes the BASIC commands to be
used for programming Trajexia, commu-
nication protocols and Trajexia Studio
software, gives practical examples and
troubleshooting information.
Sigma-II Servo
Driver manual
SIEP S800000 15 Describes the installation and operation
of Sigma-II Servo Drivers
Sigma-III with
MECHATROLINK
interface manual
SIEP S800000 11 Describes the installation and operation
of Sigma-III Servo Drivers with MECHA-
TROLINK-II interface
Sigma-V Servo
Driver manual
SIEP S800000-44-O-OY
SIEP S800000-46-O-OY
SIEP S800000-48-O-OY
Describes the installation and operation
of Sigma-V Servo Drivers
JUNMA series servo
drive manual
TOEP-C71080603 01-OY Describes the installation and operation
of JUNMA Servo Drivers
V7 Inverter TOEP C71060605 02-OY Describes the installation and operation
of V7 Inverters
F7Z Inverter TOE S616-55 1-OY Describes the installation and operation
of F7Z Inverters
G7 Inverter TOE S616-60 Describes the installation and operation
of G7 Inverters
JUSP-NS115 man-
ual
SIEP C71080001 Describes the installation and operation
of the MECHATROLINK-II application
module
SI-T MECHATRO-
LINK interface for
the G7 & F7
SIBP-C730600-08 Describes the installation and operation
of MECHATROLINK-II interfaces for G7
and F7 Inverters
ST-T/V7 MECHA-
TROLINK interface
for the V7
SIBP-C730600-03 Describes the installation and operation
of MECHATROLINK-II interfaces for V7
Inverters
MECHATROLINK IO
Modules
SIE C887-5 Describes the installation and operation
of MECHATROLINK-II input and output
modules and the MECHATROLINK-II
repeater
SYSMAC CS/CJ
Series Communica-
tions Commands
W342 Describes FINS communications proto-
col and FINS commands
Omron Smartslice
GRT1-Series, slice I/
O units, Operation
manual
W455-E1 Describes the installation and operation
of Omron slice I/O units
Omron G-series
user’s manual
I566-E1 Describes the installation and operation
of G-series Servo Drivers
Omron Accurax G5
user’s manual
I572-E1 Describes the installation and operation
of Accurax G5 Servo Drivers
Trajexia Studio user
manual
I56E-EN Describes the use of Trajexia Studio
programming software
Name Cat. No. Contents

HARDWARE REFERENCE MANUAL III
Revision 5.0
Functions supported by unit versions
During the development of Trajexia new functionality was added to the
controller unit after market release.
This functionality is implemented in the firmware, and/or the FPGA of the
controller unit.
In the table below, the overview of the applicable functionality is shown
related to the firmware and FPGA version of the TJ1-MC__.
/i
Verify the firmware and FPGA versions of the TJ1-MC__
Connect the TJ1-MC__ to Trajexia Studio software. Refer to the
Programming Manual.
Open the terminal window and type the following commands:
Type PRINT VERSION in the terminal window. The version parameter returns
the current firmware version number of the motion controller.
Type PRINT FPGA_VERSION SLOT(-1) in the terminal window. The
parameter returns the current FPGA version number of the TJ1-MC__.
WARNING
Failure to read and understand the information provided in this
manual may result in personal injury or death, damage to the pro-
duct, or product failure. Please read each section in its entirety and
be sure you understand the information provided in the section and
related sections before attempting any of the procedures or opera-
tions given.
Functionality TJ1-MC__ Firmware
version
TJ1-MC__ FPGA
version
Full support TJ1-FL02 V1.6509 21 and higher
Support BASIC commands FINS_COMMS V1.6509 All versions
Support TJ1-DRT V1.6509 All versions
Support TJ1-MC04 andTJ1-ML04 V1.6607 21 and higher
Support TJ1-CORT, GRT1-ML2, Mod-
busTCP, Sigma-V series Servo Drivers
(except DATUM and REGIST BASIC com-
mands) and allow Inverters to be controlled
as servo axes
V1.6652 21 and higher
Support for G-series Drivers, full support for
Sigma-V series Servo Drivers
V1.6714 21 and higher
Support for Accurax G5 Drivers V1.6720 21 and higher

Contents
HARDWARE REFERENCE MANUAL IV
Revision 5.0
1 Safety warnings and precautions................................................................................................................................................................ 1
1.1 Intended audience ............................................................................................................................................................................................................................1
1.2 General precautions .........................................................................................................................................................................................................................1
1.3 Safety precautions ............................................................................................................................................................................................................................1
1.4 Operating environment precautions..................................................................................................................................................................................................2
1.5 Application precautions.....................................................................................................................................................................................................................3
1.6 Unit assembly precautions................................................................................................................................................................................................................5
1.7 Conformance to EC Directives Conformance...................................................................................................................................................................................6
2 System philosophy ....................................................................................................................................................................................... 7
2.1 Introduction .......................................................................................................................................................................................................................................7
2.2 Motion control concepts ....................................................................................................................................................................................................................8
2.3 Servo system principles ..................................................................................................................................................................................................................19
2.4 Trajexia system architecture .........................................................................................................................................................................................................22
2.5 Cycle time ......................................................................................................................................................................................................................................23
2.6 Program control and multi-tasking ..................................................................................................................................................................................................29
2.7 Motion sequence and axes.............................................................................................................................................................................................................30
2.8 Motion buffers ...............................................................................................................................................................................................................................40
2.9 Mechanical system .........................................................................................................................................................................................................................42
3 Hardware reference .................................................................................................................................................................................... 43
3.1 Introduction .....................................................................................................................................................................................................................................43
3.2 All units ..........................................................................................................................................................................................................................................46
3.3 Power Supply Unit (PSU) ...............................................................................................................................................................................................................57
3.4 TJ1-MC__ .....................................................................................................................................................................................................................................59
3.5 TJ1-ML__........................................................................................................................................................................................................................................70
3.6 GRT1-ML2 ....................................................................................................................................................................................................................................143
3.7 TJ1-PRT .......................................................................................................................................................................................................................................158
3.8 TJ1-DRT .......................................................................................................................................................................................................................................162
3.9 TJ1-CORT ....................................................................................................................................................................................................................................166
3.10 TJ1-FL02 ......................................................................................................................................................................................................................................170
A Differences between Sigma-II and Junma .............................................................................................................................................. 188
Revision history .............................................................................................................................................................................................. 189

Safety warnings and precautions
HARDWARE REFERENCE MANUAL 1
Revision 5.0
1 Safety warnings and precautions
1.1 Intended audience
This manual is intended for personnel with knowledge of electrical systems
(electrical engineers or the equivalent) who are responsible for the design,
installation and management of factory automation systems and facilities.
1.2 General precautions
The user must operate the product according to the performance
specifications described in this manual.
Before using the product under conditions which are not described in the
manual or applying the product to nuclear control systems, railroad systems,
aviation systems, vehicles, safety equipment, petrochemical plants, and
other systems, machines and equipment that can have a serious influence
on lives and property if used improperly, consult your OMRON
representative.
1.3 Safety precautions
WARNING
Do not attempt to take the Unit apart and do not touch any of the
internal parts while power is being supplied.
Doing so may result in electrical shock.
WARNING
Do not touch any of the terminals or terminal blocks while power is
being supplied.
Doing so may result in electric shock.
WARNING
Never short-circuit the positive and negative terminals of the bat-
teries, charge the batteries, disassemble them, deform them by
applying pressure, or throw them into a fire.
The batteries may explode, combust or leak liquid.
WARNING
Fail-safe measures must be taken by the customer to ensure
safety in the event of incorrect, missing, or abnormal signals
caused by broken signal lines, momentary power interruptions, or
other causes.
Not doing so may result in serious accidents.
WARNING
Emergency stop circuits, interlock circuits, limit circuits, and similar
safety measures must be provided by the customer as external cir-
cuits, i.e., not in the Trajexia motion controller.
Not doing so may result in serious accidents.
WARNING
When the 24 VDC output (I/O power supply to the TJ1) is over-
loaded or short-circuited, the voltage may drop and result in the
outputs being turned off.As a countermeasure for such problems,
external safety measures must be provided to ensure safety in the
system.
WARNING
The TJ1 outputs will go off due to overload of the output transistors
(protection).As a countermeasure for such problems, external
safety measures must be provided to ensure safety in the system.

Safety warnings and precautions
HARDWARE REFERENCE MANUAL 2
Revision 5.0
1.4 Operating environment precautions
WARNING
The TJ1 will turn off the WDOG when its self-diagnosis function
detects any error.As a countermeasure for such errors, external
safety measures must be provided to ensure safety in the system.
WARNING
Provide safety measures in external circuits, i.e., not in the Tra-
jexia Motion Controller (referred to as "TJ1"), in order to ensure
safety in the system if an abnormality occurs due to malfunction of
the TJ1 or another external factor affecting the TJ1 operation.
Not doing so may result in serious accidents.
WARNING
Do not attempt to disassemble, repair, or modify any Units.
Any attempt to do so may result in malfunction, fire, or electric
shock.
Caution
Confirm safety at the destination unit before transferring a program
to another unit or editing the memory.
Doing either of these without confirming safety may result in injury.
Caution
User programs written to the Motion Control Unit will not be auto-
matically backed up in the TJ1 flash memory (flash memory func-
tion).
Caution
Pay careful attention to the polarity (+/-) when wiring the DC power
supply.A wrong connection may cause malfunction of the system.
Caution
Tighten the screws on the terminal block of the Power Supply Unit
to the torque specified in this manual.
Loose screws may result in burning or malfunction.
Caution
Do not operate the Unit in any of the following locations.
Doing so may result in malfunction, electric shock, or burning.
- Locations subject to direct sunlight.
- Locations subject to temperatures or humidity outside the
range specified in the specifications.
- Locations subject to condensation as the result of severe
changes in temperature.
- Locations subject to corrosive or flammable gases.
- Locations subject to dust (especially iron dust) or salts.
- Locations subject to exposure to water, oil, or chemicals.
- Locations subject to shock or vibration.
Caution
Take appropriate and sufficient countermeasures when installing
systems in the following locations.
Inappropriate and insufficient measures may result in malfunction.
- Locations subject to static electricity or other forms of noise.
- Locations subject to strong electromagnetic fields.
- Locations subject to possible exposure to radioactivity.
- Locations close to power supplies.

Safety warnings and precautions
HARDWARE REFERENCE MANUAL 3
Revision 5.0
1.5 Application precautions
Caution
The operating environment of the TJ1 System can have a large
effect on the longevity and reliability of the system.
Improper operating environments can lead to malfunction, failure,
and other unforeseeable problems with the TJ1 System.
Make sure that the operating environment is within the specified
conditions at installation and remains within the specified condi-
tions during the life of the system.
WARNING
Do not start the system until you check that the axes are present
and of the correct type.
The numbers of the Flexible axes will change if MECHATROLINK-
II network errors occur during start-up or if the MECHATROLINK-II
network configuration changes.
Not doing so may result in unexpected operation.
WARNING
Check the user program for proper execution before actually run-
ning it in the Unit.
Not checking the program may result in an unexpected operation.
Caution
Always use the power supply voltage specified in this manual.
An incorrect voltage may result in malfunction or burning.
Caution
Take appropriate measures to ensure that the specified power with
the rated voltage and frequency is supplied. Be particularly careful
in places where the power supply is unstable.
An incorrect power supply may result in malfunction.
Caution
Install external breakers and take other safety measures against
short-circuiting in external wiring.
Insufficient safety measures against short-circuiting may result in
burning.
Caution
Do not apply voltage to the Input Units in excess of the rated input
voltage.
Excess voltage may result in burning.
Caution
Do not apply voltage or connect loads to the Output Units in
excess of the maximum switching capacity.
Excess voltage or loads may result in burning.
Caution
Disconnect the functional ground terminal when performing with-
stand voltage tests.
Not disconnecting the functional ground terminal may result in
burning.
Caution
Always connect to a class-3 ground (to 100Ωor less) when install-
ing the Units.
Not connecting to a class-3 ground may result in electric shock.

Safety warnings and precautions
HARDWARE REFERENCE MANUAL 4
Revision 5.0
Caution
Always turn off the power supply to the system before attempting
any of the following.
Not turning off the power supply may result in malfunction or elec-
tric shock.
- Mounting or dismounting expansion Units, CPU Units, or any
other Units.
- Assembling the Units.
- Setting dipswitches or rotary switches.
- Connecting or wiring the cables.
- Connecting or disconnecting the connectors.
Caution
Be sure that all mounting screws, terminal screws, and cable con-
nector screws are tightened to the torque specified in this manual.
Incorrect tightening torque may result in malfunction.
Caution
Leave the dust protective label attached to the Unit when wiring.
Removing the dust protective label may result in malfunction.
Caution
Remove the dust protective label after the completion of wiring to
ensure proper heat dissipation.
Leaving the dust protective label attached may result in malfunc-
tion.
Caution
Use crimp terminals for wiring. Do not connect bare stranded wires
directly to terminals.
Connection of bare stranded wires may result in burning.
Caution
Double-check all the wiring before turning on the power supply.
Incorrect wiring may result in burning.
Caution
Wire correctly.
Incorrect wiring may result in burning.
Caution
Mount the Unit only after checking the terminal block completely.
Caution
Be sure that the terminal blocks, expansion cables, and other
items with locking devices are properly locked into place.
Improper locking may result in malfunction.
Caution
Confirm that no adverse effect will occur in the system before
changing the operating mode of the system.
Not doing so may result in an unexpected operation.
Caution
Resume operation only after transferring to the new CPU Unit the
contents of the VR and table memory required for operation.
Not doing so may result in an unexpected operation.
Caution
When replacing parts, be sure to confirm that the rating of a new
part is correct.
Not doing so may result in malfunction or burning.

Safety warnings and precautions
HARDWARE REFERENCE MANUAL 5
Revision 5.0
1.6 Unit assembly precautions
Caution
Do not pull on the cables or bend the cables beyond their natural
limit. Doing so may break the cables.
Caution
Before touching the system, be sure to first touch a grounded
metallic object in order to discharge any static build-up.
Otherwise it might result in a malfunction or damage.
Caution
UTP cables are not shielded. In environments that are subject to
noise use a system with shielded twisted-pair (STP) cable and
hubs suitable for an FA environment.
Do not install twisted-pair cables with high-voltage lines.
Do not install twisted-pair cables near devices that generate noise.
Do not install twisted-pair cables in locations that are subject to
high humidity.
Do not install twisted-pair cables in locations subject to excessive
dirt and dust or to oil mist or other contaminants.
Caution
Use the dedicated connecting cables specified in operation manu-
als to connect the Units.
Using commercially available RS-232C computer cables may
cause failures in external devices or the Motion Control Unit.
Caution
Outputs may remain on due to a malfunction in the built-in transis-
tor outputs or other internal circuits.
As a countermeasure for such problems, external safety measures
must be provided to ensure the safety of the system.
Caution
The TJ1 will start operating in RUN mode when the power is
turned on and if a BASIC program is set to Auto Run mode.
Caution
Always check the “Status-Words” of each GRT1-ML2 coupler.
Not doing so can lead to missing or incorrect I/O data.
Caution
Always check the status of the connected MECHATROLINK-II
devices in a BASIC program.
Not doing so may result in an unexpected operation.
Caution
The TJ1-CORT unit is developed to exchange I/O data between
the Trajexia system and a CANopen network.
The TJ1-CORT is not able to exchange motion commands.
Using the TJ1-CORT to exchange motion commands may result in
unexpected operation.
Caution
Install the unit properly.
Improper installation of the unit may result in malfunction.
Caution
Be sure to mount the TJ1-TER supplied with the TJ1-MC__ to the
right most Unit.
Unless the TJ1-TER is properly mounted, the TJ1 will not function
properly.

Safety warnings and precautions
HARDWARE REFERENCE MANUAL 6
Revision 5.0
1.7 Conformance to EC Directives Conformance
1.7.1 Concepts
The concepts for the directives EMC and Low Voltage are as follows:
EMC Directives
OMRON devices that comply with EC Directives also conform to the related
EMC standards so that they can be more easily built into other devices or
machines. The actual products have been checked for conformity to EMC
standards. Whether the products conform to the standards in the system
used by the customer, however, must be checked by the customer.
EMC-related performance of the OMRON devices that comply with EC
Directives will vary depending on the configuration, wiring, and other
conditions of the equipment or control panel in which the OMRON devices
are installed. The customer must, therefore, perform final checks to confirm
that devices and the over-all machine conform to EMC standards.
Low Voltage Directive
Always ensure that devices operating at voltages of 50 to 1,000 VAC or 75 to
1,500 VDC meet the required safety standards.
1.7.2 Conformance to EC Directives
The Trajexia Motion Controllers comply with EC Directives.
To ensure that the machine or device in which a system is used complies
with EC directives, the system must be installed as follows:
1. The system must be installed within a control panel.
2. Reinforced insulation or double insulation must be used for the DC
power supplies used for the communications and I/O power supplies.

System philosophy
HARDWARE REFERENCE MANUAL 7
Revision 5.0
2 System philosophy
2.1 Introduction
fig. 1
The system philosophy is centred around the relationship between:
• System architecture
• Cycle time
• Program control and multi-tasking
• Motion sequence and axes
• Motion buffers
A clear understanding of the relationship between these concepts is
necessary to obtain the best results for the Trajexia system.
2.1.1 Glossary
Motion sequence
The Motion Sequence is responsible for controlling the position of the axes.
Servo period
Defines the frequency at which the Motion Sequence is executed. The servo
period must be set according to the configuration of the physical axes. The
available settings are 0.5ms, 1ms or 2ms.
Cycle time
Is the time needed to execute one complete cycle of operations in the TJ1-
MC__. The cycle time is divided in 4 time slices of equal time length, called
"CPU Tasks". The cycle time is 1ms if SERVO_PERIOD=0.5ms or
SERVO_PERIOD=1ms and 2ms if the SERVO_PERIOD=2ms.
CPU tasks
The operations executed in each CPU task are:
AXIS TYPE
AXIS TYPE
AXIS CONTROL LOOP
Position
Loop
Position
Loop
Buffer &
profile
gererator
Buffer &
profile
gererator
Servo Driver
MOTOR
Position
Loop
Position
Loop
Speed Loop
Speed Loop
Torque
Loop
Torque
Loop
Servo Driver
MOTOR
ENC
Speed Loop
Torque
Loop
Via
ENC
Program Buffer
BASIC PROGRAMS
Process 1
Process 2
Process 3
…
Process 14
Comms
TJ1-MC__
AXIS TYPE
TJ1 ML__
-
TJ1 FL02
-
Ethernet
FINS
Ethernet
TJ1 PRT
-
MC I/O
Profibus
BUILT-IN TJ1-ML16
All othe
r
Servo
Drivers
CPU task Operation
First CPU task Motion Sequence
Low priority process

System philosophy
HARDWARE REFERENCE MANUAL 8
Revision 5.0
Program
A program is a piece of BASIC code.
Process
Is a program in execution with a certain priority assigned. Process 0 to 12
are Low priority processes and Process 13 and 14 are High priority
processes. First the process priority, High or Low, and then the process
number, from high to low, will define to which CPU task the process will be
assigned.
2.2 Motion control concepts
The TJ1-MC__ offers these types of positioning control operations:
1. Point-to-Point (PTP) control
2. Continuous Path (CP) control
3. Electronic Gearing (EG) control.
This section introduces some of the commands and parameters used in the
BASIC programming of the motion control application.
Coordinate system
Positioning operations performed by the TJ1-MC__ are based on an axis
coordinate system. The TJ1-MC__ converts the position data from either the
connected Servo Driver or the connected encoder into an internal absolute
coordinate system.
The engineering unit that specifies the distances of travelling can be freely
defined for each axis separately. The conversion is performed through the
use of the unit conversion factor, which is defined by the UNITS axis
Second CPU task High priority process
Third CPU task Motion Sequence (only if SERVO_PERIOD=0.5ms)
LED Update
High priority process
Fourth CPU task External Communications
CPU task Operation

System philosophy
HARDWARE REFERENCE MANUAL 9
Revision 5.0
parameter. The origin point of the coordinate system can be determined
using the DEFPOS command. This command re-defines the current position
to zero or any other value.
fig. 2
A move is defined in either absolute or relative terms. An absolute move
takes the axis (A) to a specific predefined position with respect to the origin
point. A relative move takes the axis from the current position to a position
that is defined relative to this current position. The figure shows an example
of relative (command MOVE) and absolute (command MOVEABS) linear
moves.
2.2.1 PTP control
In point-to-point positioning, each axis is moved independently of the other
axis. The TJ1-MC__ supports the following operations:
• Relative move
• Absolute move
• Continuous move forward
• Continuous move reverse.
050 100 A
MOVE(30)
MOVE(50)
MOVEABS(50)
MOVE(60)
MOVEABS(30)

System philosophy
HARDWARE REFERENCE MANUAL 10
Revision 5.0
Relative and absolute moves
fig. 3
To move a single axis either the command MOVE for a relative move or the
command MOVEABS for an absolute move is used. Each axis has its own
move characteristics, which are defined by the axis parameters.
Suppose a control program is executed to move from the origin to an axis
no. 0 (A) coordinate of 100 and axis no. 1 (B) coordinate of 50. If the speed
parameter is set to be the same for both axes and the acceleration and
deceleration rate are set sufficiently high, the movements for axis 0 and axis
1 will be as shown in the figure.
At start, both the axis 0 and axis 1 moves to a coordinate of 50 over the
same duration of time. At this point, axis 1 stops and axis 0 continues to
move to a coordinate of 100.
The move of a certain axis is determined by the axis parameters. Some
relevant parameters are:
/i
Defining moves
fig. 4
The speed profile in this figure shows a simple MOVE operation. Axis A is
the time, axis B is the speed. The UNITS parameter for this axis has been
defined for example as meters. The required maximum speed has been set
to 10 m/s. In order to reach this speed in one second and also to decelerate
to zero speed again in one second, both the acceleration as the deceleration
rate have been set to 10 m/s2. The total distance travelled is the sum of
distances travelled during the acceleration, constant speed and deceleration
segments. Suppose the distance moved by the MOVE command is 40 m,
the speed profile is given by the figure.
050
50
100 A
BMOVEABS(100) AXIS(0)
MOVEABS(50) AXIS(1)
Parameter Description
UNITS Unit conversion factor
ACCEL Acceleration rate of an axis in units/s2
DECEL Deceleration rate of an axis in units/s2
SPEED Demand speed of an axis in units/s2
0
10
123 456
A
B
ACCEL=10
DECEL=10
SPEED=10
MOVE(40)

System philosophy
HARDWARE REFERENCE MANUAL 11
Revision 5.0
fig. 5
The two speed profiles in these figures show the same movement with an
acceleration time respectively a deceleration time of 2 seconds. Again, Axis
A is the time, axis B is the speed.
fig. 6
Move calculations
The following equations are used to calculate the total time for the motion of
the axes.
• The moved distance for the MOVE command is D.
• The demand speed is V.
• The acceleration rate is a.
• The deceleration rate is d.
/i
0
10
123 456
A
B
ACCEL=5
DECEL=10
SPEED=10
MOVE(40)
0
10
123 456
A
B
ACCEL=10
DECEL=5
SPEED=10
MOVE(40)
Acceleration time =

System philosophy
HARDWARE REFERENCE MANUAL 12
Revision 5.0
Continuous moves
The FORWARD and REVERSE commands can be used to start a
continuous movement with constant speed on a certain axis. The
FORWARD command moves the axis in positive direction and the
REVERSE command in negative direction. For these commands also the
axis parameters ACCEL and SPEED apply to specify the acceleration rate
and demand speed.
Both movements can be cancelled by using either the CANCEL or
RAPIDSTOP command. The CANCEL command cancels the move for one
axis and RAPIDSTOP cancels moves on all axes. The deceleration rate is
set by DECEL.
2.2.2 CP control
Continuous Path control enables to control a specified path between the
start and end position of a movement for one or multiple axes. The TJ1-
MC__ supports the following operations:
• Linear interpolation
• Circular interpolation
• CAM control.
Acceleration distance =
Deceleration time =
Deceleration distance =
Constant speed distance =
To t a l t i m e =

System philosophy
HARDWARE REFERENCE MANUAL 13
Revision 5.0
Linear interpolation
fig. 7
In applications it can be required for a set of motors to perform a move
operation from one position to another in a straight line. Linearly interpolated
moves can take place among several axes. The commands MOVE and
MOVEABS are also used for the linear interpolation. In this case the
commands will have multiple arguments to specify the relative or absolute
move for each axis.
Consider the three axis move in a 3-dimensional plane in the figure. It
corresponds to the MOVE(50,50,50) command. The speed profile of the
motion along the path is given in the diagram. The three parameters
SPEED, ACCEL and DECEL that determine the multi axis movement are
taken from the corresponding parameters of the base axis. The MOVE
command computes the various components of speed demand per axis.
A is the time axis, B is the speed axis.
A
B
3
1
2

System philosophy
HARDWARE REFERENCE MANUAL 14
Revision 5.0
Circular interpolation
fig. 8
It may be required that a tool travels from the starting point to the end point
in an arc of a circle. In this instance the motion of two axes is related via a
circular interpolated move using the MOVECIRC command.
Consider the diagram in the figure. It corresponds to the MOVECIRC(-
100,0,-50,0,0) command. The centre point and desired end point of the
trajectory relative to the start point and the direction of movement are
specified. The MOVECIRC command computes the radius and the angle of
rotation. Like the linearly interpolated MOVE command, the ACCEL, DECEL
and SPEED variables associated with the base axis determine the speed
profile along the circular move.
CAM control
fig. 9
Additional to the standard move profiles the TJ1-MC__ also provides a way
to define a position profile for the axis to move. The CAM command moves
an axis according to position values stored in the TJ1-MC__ Table array.
The speed of travelling through the profile is determined by the axis
parameters of the axis.
The figure corresponds to the command CAM(0,99,100,20). A is the time
axis, B is the position axis.
2.2.3 EG control
Electronic Gearing control allows you to create a direct gearbox link or a
linked move between two axes. The MC Unit supports the following
operations.
• Electronic gearbox
•LinkedCAM
• Linked move
• Adding axes
050
50
-50
A
B

System philosophy
HARDWARE REFERENCE MANUAL 15
Revision 5.0
Electronic gearbox
fig. 10
The TJ1-MC__ is able to have a gearbox link from one axis to another as if
there is a physical gearbox connecting them. This can be done using the
CONNECT command in the program. In the command the ratio and the axis
to link to are specified.
In the figure, A is the Master axis, and B is the CONNECT axis.
/i
A
B
2:1 1:1
1:2
Axes Ratio CONNECT command
0 1
1:1 CONNECT(1,0) AXIS(1)
2:1 CONNECT(2,0) AXIS(1)
1:2 CONNECT(0.5,0) AXIS(1)
Other manuals for SMARTSLICE GRT1-ML2
1
This manual suits for next models
11
Table of contents
Other Omron Control System manuals
Popular Control System manuals by other brands
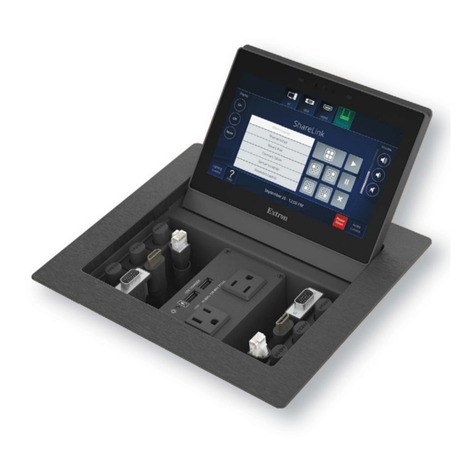
Extron electronics
Extron electronics TouchLink TLP Pro 525C Series user guide
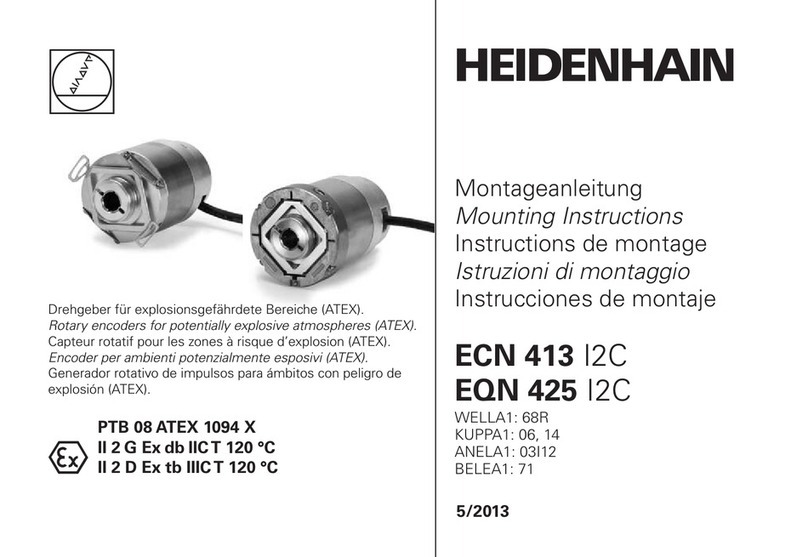
HEIDENHAIN
HEIDENHAIN ECN 413 2C Mounting instructions
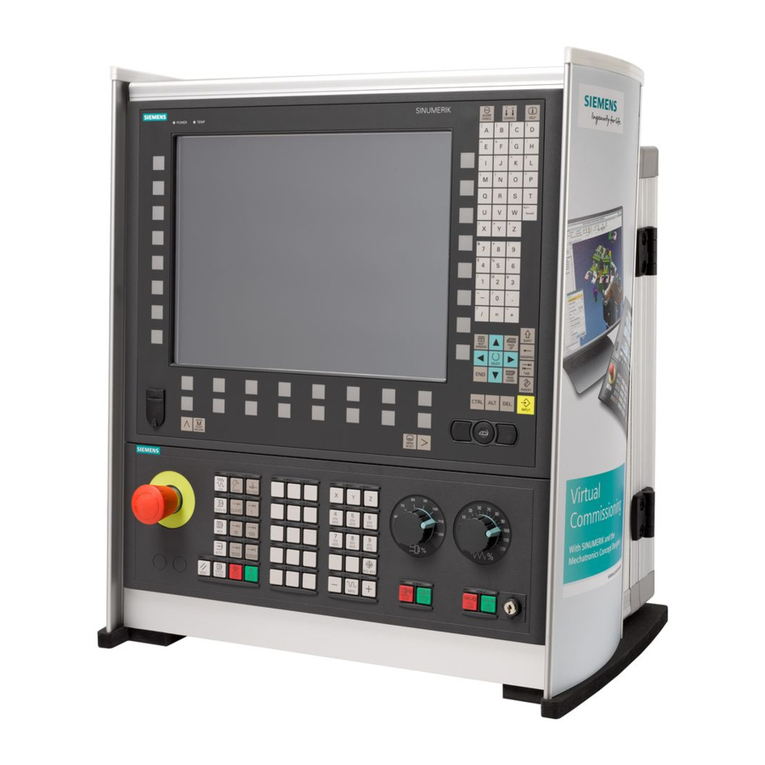
Siemens
Siemens SINUMERIK 840D sl Function manual
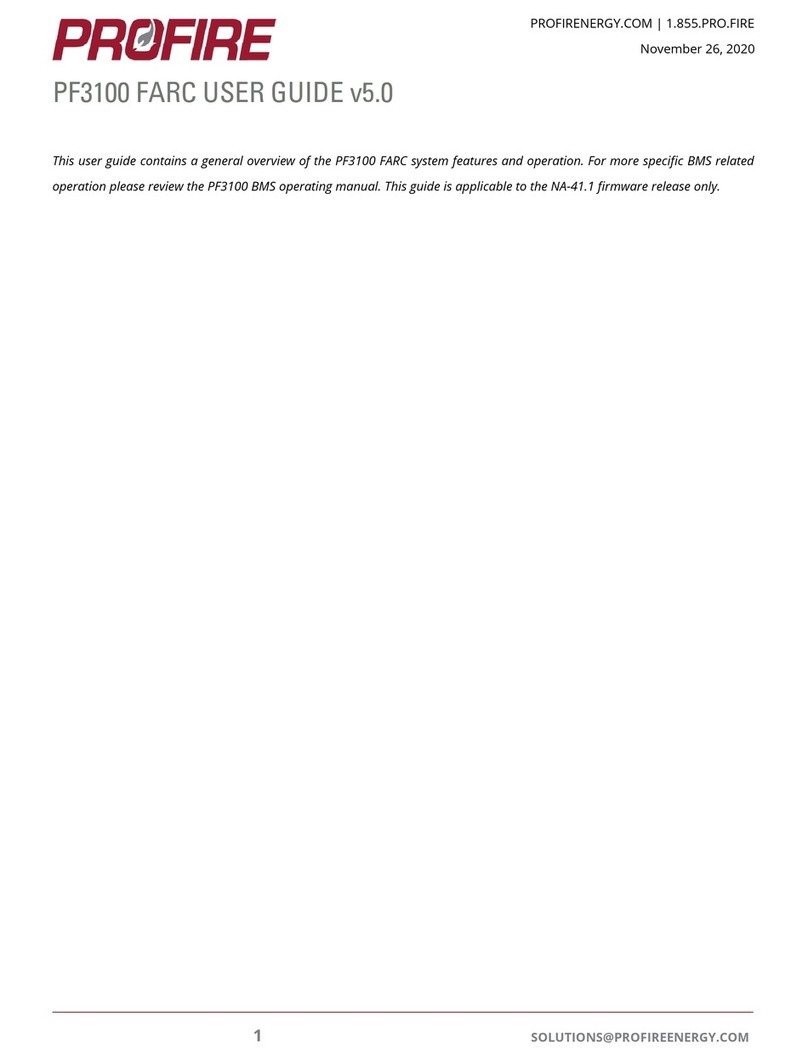
ProFire
ProFire PF3100 FARC user guide
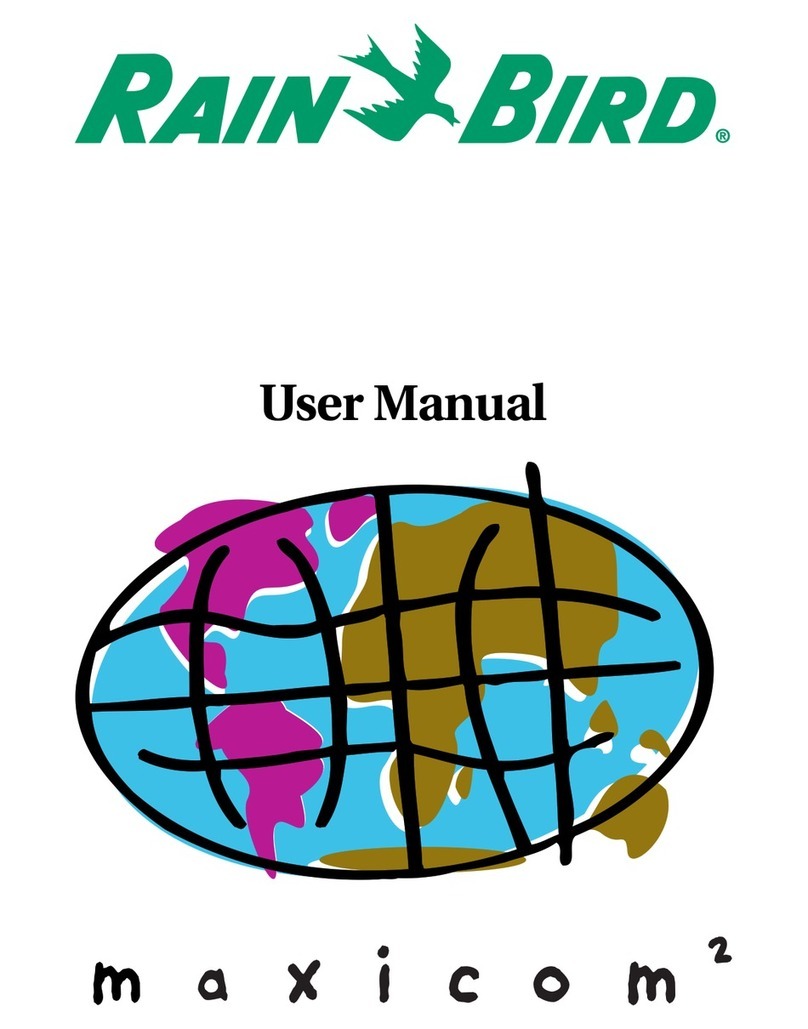
Rain Bird
Rain Bird Freedom System for Maxicom2 user manual
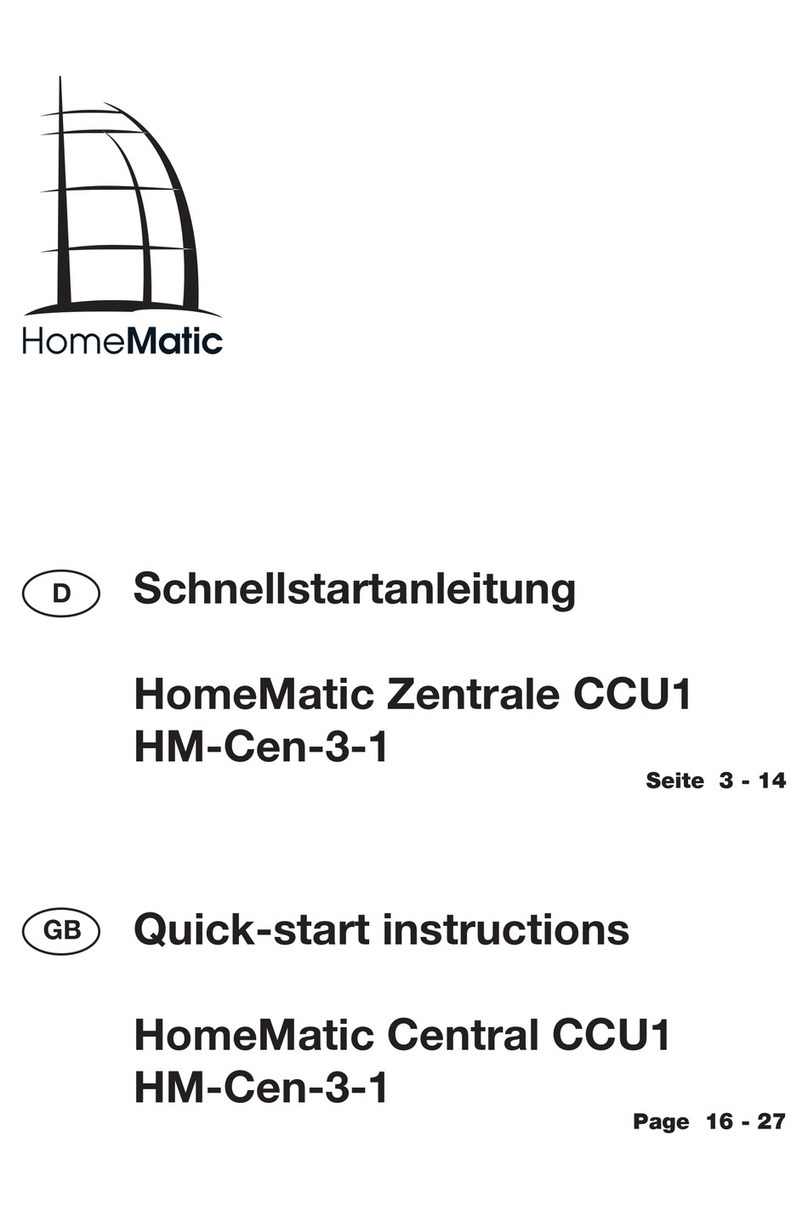
HomeMatic
HomeMatic HM-Cen-3-1 Quick start instructions