Onlab ONDRIVE ED07 User manual

V1.1-ENG
www.onlab.com.tr
ONDRIVE ED07
Automatic Door Control
ler
User Manual

V1.1-ENG
www.onlab.com.tr
All rights reserved. It is prohibited to copy, modify or reproduce the whole or any part of the
printed or digital version of this document without the permission of Onlab. Onlab reserves to
change or improve any part of this document without prior notice. The latest version of this
document can be reached from www.onlab.com.tr web site. Onlab is not responsible for the
mistakes in this document that may cause any fault or damage.
Onlab Elektrik Elektronik Bilişim Sanayi ve Ticaret A
Sanayi Mahallesi Teknopark Bul arı No:1/3A Z06 34906 Pendik/İSTANBUL
Tel: 0216 504 54 21
Fax: 0216 504 54 22
Web: www.onlab.com.tr
E-Mail: [email protected]r
Model :
ED07
Document Number :
1.1
Document Date :
11.10.2019
SW version :
1.01

V1.1-ENG
www.onlab.com.tr
CONTENTS
GENERAL VIEW ...................................................................................................................... 1
TECHNICAL SPECIFICATIONS ............................................................................................ 2
CABLE CONNECTIONS AND PROPERTIES ....................................................................... 3
BUTTON DEFINITIONS IN INSPECTION MODE AND USAGE INFORMATION .......... 4
PROGRAMMING (Ver:1.01) .................................................................................................... 4
USER PASSWORD SETTINGS ............................................................................................... 6
MOTION PROFILES ................................................................................................................ 6
Motor Types : ............................................................................................................................. 6
CONNECTION TO ELEVATOR CONTROL PANEL ............................................................ 7
OUTPUT RELAYS AND INPUT SIGNALS MONITORING MENU .................................... 8
LEARNING THE DOOR .......................................................................................................... 9
ENCODER MATCHING ........................................................................................................ 10
MANUFACTURER SETTINGS ............................................................................................. 11
ERROR MESSAGES ............................................................................................................... 12

V1.1-ENG
1 www.onlab.com.tr
GENERAL VIEW
GRID
L: 220Vac Line 15V: 15V supply (+) terminal for input signals
N: 220V AC Neutral GND 15V supply (-) terminal for input signals
PE: Earth
INPUT
EIN2: Programmable input 2
EIN1: Programmable input 1
MOTOR
PE: Earth
U: U Phase COM: Common terminal for open/close signals
V: V Phase OPEN: Open signal input
W: W Phase CLOSE: Close signal input
ENCODER
PE: Earth
OUTPUT
FL1: Common terminal of fault relay
5V: (+) supply for encoder
FL2: NO terminal of fault relay
GND: (-) supply for encoder
OP1: Common terminal of “door opened” relay
A+: A+ channel of encoder
OP2: NO terminal of “door opened” relay
A-: A- channel of encoder
CL1: Common terminal of “door closed” relay
B+: B+ channel of encoder
CL2: NO terminal of “door closed” relay
B-: B- channel of encoder
Z+: Z+ channel of encoder
Z-: Z- channel of encoder
*Mechanical dimensions of the product are given in another document on Onlab website.
Connector Descriptions

V1.1-ENG
2 www.onlab.com.tr
TECHNICAL SPECIFICATIONS
GRID
Nominal Voltage 220 V
ac
Voltage Tolerance 170 -264 V
ac
Frequency Tolerance 50/60 Hz ±%5
Internal Fuse 2 A
MOTOR
Type PMSM
Maximum Output Power 150 W
Nominal Current 0,7 A
rms
Output Frequency 0 – 120.0 Hz
Control Method Vector control
Short Circuit Protection Yes
ENCODER
Encoder Type 3 channels incremental
Encoder Resolution 100-2048 ppr
Encoder Voltage 5 V
dc
USER
INTERFACE
Language Options Turkish / English
Screen 2x16 Character LCD
Button 4 buttons
Warning Sound Buzzer
INPUTS
Open the door
Close the door
Programmable input 1 (Nudging / Photocell)
Programmable input 2 (Photocell / Nudging)
OUTPUTS
Fault relay (5A @ 250V
ac
or 30V
dc
)
Door opened relay (5A @ 250V
ac
or 30V
dc
)
Door closed relay (5A @ 250V
ac
or 30V
dc
)
ERROR TYPES
Press detected
Module error
Encoder V
CC
error
High V
dc
error
Low V
dc
error
Maximum door speed 80 cm/s
Operating Temperature -20 ~ +60 °C
EMC Approval EN 12015 / EN 12016

V1.1-ENG
3 www.onlab.com.tr
CABLE CONNECTIONS AND PROPERTIES
It is recommended to use 3x0,3mm
2
stranded wire to connect GRID connector.
Cable that will be used to connect MOTOR connector should be 3x0,5 mm
2
stranded wire and
cable length should be smaller than or equal to 1,75m.
Motor cable connection must be done with the correct order according to the colors gi en
below. Otherwise, the de ice will gi e an error and cannot mo e the door.
Colors of Motor Cable
U
V
W
:
:
:
Blue
Red
B
rown
Cable that will be used to connect ENCODER should be 8x0,22mm
2
stranded wire and cable
length should be smaller than or equal to 1,75m. It is strongly ad ised to use shielded cable
for encoder connection and shield of this cable can be connected to PE terminal if it is needed.
Encoder cable connection must be done with the correct order according to the colors gi en
below. Otherwise, the de ice will gi e an error and cannot mo e the door.
Colors of Encoder Cable
+5V
GND
A+
:
:
:
Red
Brown
Yellow
A-
:
Green
B+
:
White
B-
:
Blue
Z+
:
Grey
Z-
:
P
ink
Cable that will be connected to the INPUT and OUTPUT terminals can be in arious lengths
that can be adjusted according to the application and place it is mounted.

V1.1-ENG
4 www.onlab.com.tr
BUTTON DEFINITIONS IN INSPECTION MODE AND USAGE
INFORMATION
Upper line of LCD screen shows the status of the door. Door speed (V=XX cm/s) is shown in the
left of lower line and position of the door (P=XXX cm) is shown in the right side of the lower line.
After initial power-up of the de ice, door mo es with learning speed to the opening direction if there
is no CLOSE signal and it mo es to the closing direction if there is a CLOSE signal. In the
meantime, position info is not known, so it is written as “---” to the LCD screen.
De ice will get into “Inspection” mode by pressing the ENTER button. At that mode motor is
deenergized and door waits at its current position. This will enable the operator to adjust mechanical
settings of the door without cutting out the electricity of the de ice. At that mode there are some
functionalities of ENTER, UP and DOWN buttons. Those functionalities of the buttons are
described below. Please press the ESC button to get out of “Inspection” mode.
De ice gets into “Manual Motion” mode if ESC button is pressed. At that mode door mo es to
closing direction if the UP button is hold as pressed and door mo es to opening direction if the
DOWN button is hold as pressed. It is needed to press ENTER button to get out from “Manual
Motion” mode.
ENTER = By holding this button pressed for 2 seconds, “Programming Mode” will be
acti e.
UP = If this button is pressed, Total Run number of the door is shown on the LCD
screen for 5 seconds.
DOWN = If this button is pressed, learning process starts. Firstly, the door mo es to
opening direction. After it reaches to completely opened position, door mo es
in closing direction. During learning process, encoder alue is displayed on
upper right part of the LCD screen.
ESC = When this button is pressed, de ice gets out of “Inspection” position.
PROGRAMMING (Ver:1.01)
For getting into “Programming” mode of ONDRIVE board, firstly it needs to be pressed to ENTER
button and take the de ice into “Inspection” mode. Then, holding the ENTER button pressed
programming can be started.
Desired parameter can be selected using DOWN and UP buttons.
For getting out “Programming Mode”, ESC button should be pressed in main menu. Then LCD
screen shows “Exit ->ENTER” “Return ->ESC”. When ENTER button is pressed, de ice
00:Language
English
Parameter Number
Stored Parameter Value
Parameter Name
00:Language
> English
When this symbol is on screen
parameter alue can be changed.

V1.1-ENG
5 www.onlab.com.tr
gets out from “Programming Mode”. Otherwise, if ESC button is pressed, de ice returns into
pre ious menu.
Pressing ENTER button in main menu, displayed program can be started.
If the program has a parameter alue, an arrow is displayed at the beginning of lower LCD line.
Parameter alue can be changed ia DOWN and UP buttons. When ENTER button is pressed,
displayed alue is stored. Otherwise, if ESC button is pressed pre iously stored alue is stored
again.
Program Factory
Settings
Parameters / Explanations
00:
Language
Turkce
Turkce
–
English
01:
Open HighSpeed
35 cm/s
20
-
80 (
High speed le el while
opening
)
02:
Open LowSpeed
5 cm/s
2
-
19 (
Low speed le el while
opening
)
03:
Op. Acc. Dist.
20 cm
5
-
90 (
Total
distance
of a
cceleration
region while
opening
)
04:
Op. Acc. Jerk
5 cm
1
-
40 (
Distance
of a
cceleration jerk region
while
opening
)
05:
Op. Dec. Dist.
15 cm
5
-
90 (
Total
distance
of deceleration
region
while
opening
)
06:
Op. Dec. Jerk
5 cm
1
-
40 (
Distance
of deceleration jerk region
while
opening
)
07:
Op.LowSpdDist
2 cm
1
-
90 (
Distance
of low speed
region while opening
)
08:
Op.Pres.Le el
% 60
20
-
100 (
Pressure le el
while
opening.
% of motor nominal current
)
09:
Cl.High Speed
25 cm/s
20
-
80 (
High
speed le el while closing
)
10:
Cl.Low Speed
5 cm/s
2
-
19 (
Low speed le el while closing
)
11:
Cl.Acc.Dist.
20 cm
5
-
90 (
Total distance of acceleration region while closing
)
12:
Cl.Acc.Jerk
5 cm
1
-
40 (
Distance of acceleration jerk region while
closing
)
13:
Cl.Dec.Dist.
15 cm
5
-
90 (
Total distance of deceleration region while closing
)
14:
Cl.Dec.Jerk
5 cm
1
-
40 (
Distance of deceleration jerk region while closing
)
15:
Cl.LowSpdDist
5 cm
1
-
90 (
Distance of low speed region whil
e
closing
)
16:
Cl.Pres.Le el
% 45
20
-
100
(
Pressure le el during closing. % of motor nominal current
)
17: Run InputType Open -
Close
Open - Close, Close
(
Selection of door operation with inputs.
)
18: Limit Relays Open
Contact
Open Contact, Close Contact
(
Selection of limit relay operation when reached to limit)
19: Fault Relay Open
Contact
Open Contact, Close Contact
(
Fault
relay operation
if
an error or photocell signal is detected)
20: Demo Mode 0 s
0 – 30
(Time for demo operation. 0 means demo is cancelled. Any alue other
than 0 runs the door in demo mode in which door opens and closes
consecuti ely whate er the input signals are. At opened limit and closed
limit door waits for selected time.)
21:
SetUserPassw.
(
User password can be set.
)
22:
CancelU.Pass
?
(
User password is changed with 0000 and cancelled)
23: Cl.LowSpdPres % 45 20-100
(
Pressure le el at closing low speed region. % of motor nominal current
)
24: EIN1
Input
Nudging
Nudging / Photocell
25: EIN2
Input
Photocell
Nudging / Photocell
26:
Door Type
Telescopic
Teles
copic
-
Central
-
Internal
27: Motor Type
Motor 1-Motor 2- Motor 3 (This parameter cannot be modified,
preprogrammed by Onlab according to the motor type the dri er is
matched at the production)
28: Working Mode NORMAL
NORMAL / SOFT CLOSE
(If this parameter is selected as SOFT CLOSE, door press le el does not
exceed 150 N during closing operation
)
29: Encoder Match Passi e Acti e-Passi e (After the serial production in Onlab, encoder matching
process is done. Dri ers are sent to the customer after this operation.)
Manufact. Set.
CAUTION! Only the door manufacturer can reach those parameters.
99: Factory Set ? (If this parameter is set, all of the parameter alues will be reset to
factory settings.
)
* actory Setting values can be different in customer specific software.

V1.1-ENG
6 www.onlab.com.tr
USER PASSWORD SETTINGS
The user can set a password for accessing to the “Programming” mode of ONDRIVE board.
The user password is not acti e initially. The password can be set in menu 21 and can be
cancelled in menu 22. After 5 consecuti e failed attempts, “Programming” mode of ONDRIVE
board will be blocked. To unlock the “Programming” mode of ONDRIVE board, the user needs
to enter 6 digits PUK code. This PUK code is generated from the serial number of the
ONDRIVE board. The manufacturer and user PUK codes are different. The user should contact
the Onlab technical ser ice team to get the PUK code.
MOTION PROFILES
Motor Types :
Ondri e de ice has 3 different PM synchronous motor options from different motor
manufacturers. When ordered, Ondri e de ice will be preprogrammed with the appropriate
motor type according to the desired motor option and will be sent to the user with that setting.
Motor 1, Motor 2, Motor 3
Detailed mechanical and electrical parameters of the motors can be reached from Onlab
website.
Time (sec)
P07 P05 P03 P46
P46 Skate distance
P03 Open acceleration distance
P05 Open deceleration distance
P07 Open low speed distance
Time (sec)
P11 P13 P15 P46
P11 Close acceleration distance
P13 Close deceleration distance
P15 Close low speed distance
P46 Skate distance
SPEED (cm/s)
CLOSING
OPENNED LIMIT CLOSED
LIMIT
OpenHigh
Speed
SPEED (cm/s)
Opening
Low Speed Skate open speed
Close High
Speed
OPENNED LIMIT
Close Low
Speed
CLOSED
LIMIT
Skate close speed
OPENING

V1.1-ENG
7 www.onlab.com.tr
CONNECTION TO ELEVATOR CONTROL PANEL
1) Connection with 24Vdc Supply Output of Control Panel (Recommended)
2) Connection with Internal 15V Supply
ONDRIVE
COM
RA: Open the door NO contact
RA
RK
OPEN
CLOSE
CONTROL PANEL
1000
(
-
24 VDC)
100
(+ 24 VDC)
K15
K5
K3
RK:
Close the door NO contact
EIN2
EIN1
15V
GND
B+
B
-
Z+
Z
-
EIN1 : Nudgi g co tact
EIN2 : Photocell co tact
ONDRIVE
COM
RA:
Open the door NO contact
RA
RK
OPEN
CLOSE
CONTROL PANEL
1000
(-
24 VDC)
100
(+ 24 VDC)
K15
K5
K3
RK: Close the door NO contact
EIN2
EIN1
15V
GND
B+
B
-
Z+
Z
-
EIN1 : Nudgi g co tact
EIN2 : Photocell co tact

V1.1-ENG
8 www.onlab.com.tr
OUTPUT RELAYS AND INPUT SIGNALS MONITORING MENU
Status of the input signals and output relays can be monitored ia using up and down buttons
in normal operation menu.
“-” symbol means no signal for input signals and “X” symbol means acti e for input signals.
Below an example of LCD screen iew for input signals is gi en:
Similarly, “-” symbol means released for output relays and “X” symbol means operated for
output relays. Below an example of LCD screen iew for output relays is gi en:
OPEN :- EIN1:-
CLOSE:X EIN2:-
OP RL:- FLT RL:-
CL RL:X

V1.1-ENG
9 www.onlab.com.tr
LEARNING THE DOOR
After initial power-up of the Ondri e de ice at the first time, “Learn the door” warning will
be seen on LCD screen in Inspection mode and it will not be possible to operate the de ice to
open or close the door without the completion of “door learning” process.
To learn the door, it is enough to press “DOWN” button in Inspection mode after setting the
parameters gi en in pre ious chapters. At that case, firstly the door will mo e to opening
direction and then it will mo e to closing direction. After the completion of skate closing,
door learning process will end. After this, by pressing ESC button, the de ice will enter to
Normal Operation Mode.
In door learning process, firstly the door should move to opening direction and then it
should move to closing direction. If in door learning process, the door starts to move
closing direction firstly, please navigate the menu to “Manufacturer Settings” and change
the value of “Motion Direction” parameter in menu 41 to “Inverted”. Then press SC and
NT R buttons consecutively and return to Inspection mode. At that mode start learning
process again by pressing DOWN button.

V1.1-ENG
10 www.onlab.com.tr
ENCODER MATCHING
In PM synchronous motor applications, encoder offset alue is the angle difference between
absolute encoder zero point and motor’s magnetic axis. It is crucial to obtain the true offset
alue to dri e the motor with the right angle and to reach higher efficiency.
Parameter 29 in settings menu is called as “Encoder Match” item and has two alues: Passi e
and Acti e. To set this parameter, na igate the menu to parameter 29 and press the ENTER
button for 3 seconds, it is possible to adjust the desired alue when
symbol is seen on the
screen.
After setting the alue of this parameter as “Acti e”, press ESC and ENTER buttons
consecuti ely. Then, in Inspection mode “Match Encoder” warning will appear on LCD
screen.
Encoder matching process will begin if UP button is pressed in Inspection mode. Firstly
“Encoder Matching Started” will be written on screen. After the completion of the process,
“Encoder Matching Completed” will be written on screen.
Note:
During encoder matching process, the belt dri en by the motor should be remo ed if it
is possible. If it is not possible, the door should not be in the limit regions of door opening and
closing, it should be in a point somewhere in the middle.
If encoder matching parameter is set as “Acti e”, e en if door learning process is completed
before, all of the measurements of the door will be reset. Thus, after the completion of
encoder matching process, “Needs to learn” warning will appear on screen again in Inspection
Mode. AT that stage, please follow the instructions that are described in LEARNING THE
DOOR section.
During the production, motor and driver are made as a set and “ ncoder Matching”
process is done by Onlab. Therefore, users do not need to perform “ ncoder Matching”
process until they change motor and/or driver electronics.

V1.1-ENG
11 www.onlab.com.tr
MANUFACTURER SETTINGS
Constructional settings of the door mechanism used with Ondri e are encrypted under
“Manufacturer Settings” section for disabling users to reach those parameters. After the
parameter 29 in menu, when “Manufacturer Settings” is displayed on screen, press the ENTER
button and a 4-digit password will be asked by Ondri e. By entering the password, following
parameters will be displayed. Those parameters can be isualized until the power of the de ice
is OFF and ON again. Default password for manufacturing settings is “1 2 3 4”. E ery
manufacturer can assign a new password using parameter 51, but this password cannot be
cancelled. If this password is entered as false for 5 times, a 6-digit PUK code will be needed.
This PUK code is generated from the serial number of Ondri e board. Manufacturer and user
PUK codes are different from each other.
Program Factory
Settings
*
Parameters / Explanations
40:
LearningSpeed
6 cm/s
2
-
19 (
Learning speed le el
)
41: Motion Direc. NOT
INVERTED
NOT INVERTED / INVERTED (In door learning process, if the
door goes to closing direction firstly, change this parameter to
INVERTED.
4
2
:
OpenHoldForce
%
1
0
0
1
-
100(
Open hold force setting
. % of motor nominal current
)
4
3
:
Cls.HoldForce
%
1
0
0
1
-
100 (
Close hold force setting. % of motor nominal current
)
4
4
:
SkateOpenSpe.
7 cm/s
1
-
20 (
Speed le el while opening the skate
)
4
5
:
SkateCloseSpe.
7 cm/s
1
-
20 (
Speed le el while closing the skate
)
4
6
:
Skate Distan.
6 cm
1
-
199 (
Skate length
)
47:
Wheel Circum.
80 mm
30
-
999 (
Circuimference
of the wheel on the motor shaft
)
48: Spd.Cnt.Le el 16
1-20
Speed control sensiti ity of the motor
(Increasing this parameter decreases the error and oscillations in
speed, but increasing this parameter more than required will result to
noise and ibrati
ons on the motor)
49: Cur.Cnt.Le el 4
1-20
Current control sensiti ity of the motor
(Decreasing this parameter will decrease the response time to torque
change requirements but noise and ibration of the motor will
increase)
5
0
:
Reset Counter
(Toplam Çalışma Sayacını Sıfırlama)
5
1
:
SetMan.Passw.
(
Used for changing manufacturer password.
)
5
2
:
LearnPressLe
% 1
0
0
20
-
10
0(
Pressure le el at learning operation
)
5
3
:
Op.Limit Dist
15
mm
5
-
50
5
4
:
Cl.Limit Dist
10
mm
1
-
10
5
5:
PressDet.Time
1000
ms
20
-
2000
56: Standard Type EN 81-20
EN_81_1_2_A3_1, EN_81_1_2_A3_2, EN_81_20
(There are 3 modes that are gi en abo e. At door closed position,
those modes will lead to different results in operation if there is no
OPEN and CLOSE signal.
EN_81_1_2_A3_1: Motor is deenergized.
EN_81_1_2_A3_2: Close hold force is applied to the motor.
EN_81_20: Door is opened until the skate is opened completely and
it will be stopped. Then, motor is deenergized.
99. Factory Set ? (If this parameter is set, all of the parameter alues will be reset to
factory settings.
)
* actory Setting values can be different in customer specific software.

V1.1-ENG
12 www.onlab.com.tr
ERROR MESSAGES
There are 5 error types that can be detected by ONDRIVE motor dri er. Possible reasons and
recommended solutions for those errors are listed below:
Error Message Description Possible Reasons and Solutions
Pressure Fault An o erload situation has been
detected in the door due to a
mechanical blockage, an
obstacle pre ention or any
problem due to connection
faults.
1)
Check if the door has a
mechanical problem or not.
2)
Check the encoder
connections. Are the color
codes correct and connected to
the right pin?
3)
Check motor phase cables.
Are the color codes for each
phase correct? One or more of
them can be disconnected from
connector. Or there can be any
broken or damaged cable.
4)
Check the encoder, it can be
damaged.
Module Error Circuit that includes IGBT
in erter detected a fault due to
o ercurrent or o er oltage.
1)
Motor can draw a huge current
due to a fault in connectors,
windings or cables.
2)
Grid oltage can be high.
3)
Deceleration ramps of the door
can be ery short and steep.
4)
One or more of the IGBTs can
be damaged.
5)
Current or oltage detection
circuit can be damaged.
Encoder VCC
Error
Encoder board draws more
than allowed current limit.
1)
Check the encoder connections
and cables.
2)
Encoder can be damaged.
High Vdc Error DC bus oltage increased
abo e allowed oltage limit.
1)
Grid oltage can be high.
2)
Deceleration ramps of the door
can be ery short and steep.
Low Vdc Error DC bus oltage decreased
below allowed oltage limit.
1)
Measure the DC bus oltage.
Table of contents
Popular Controllers manuals by other brands
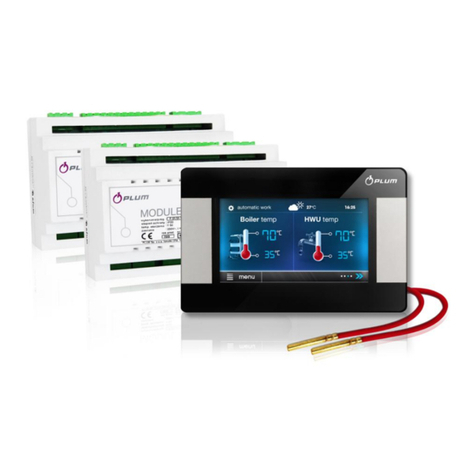
Plum
Plum ecoMAX810P3-L TOUCH Service and assembly manual
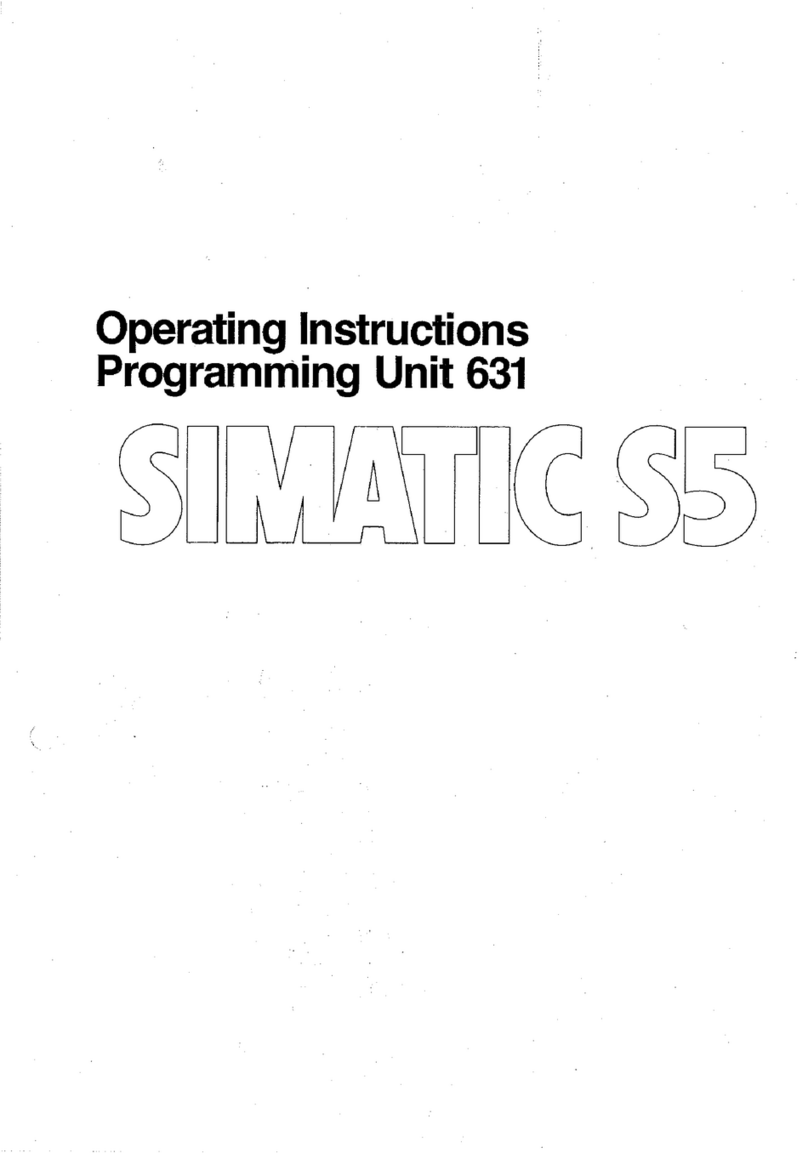
Siemens
Siemens SIMATIC S5 operating instructions
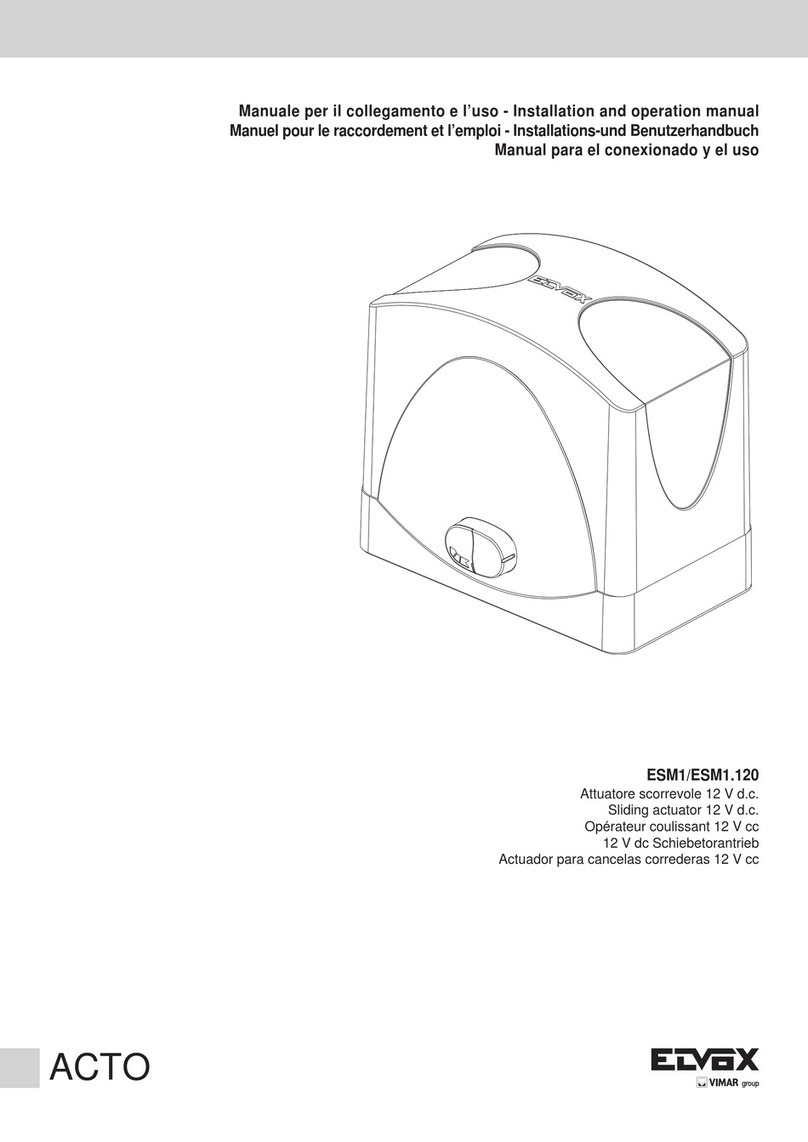
Vimar
Vimar ELVOX ACTO ESM1 Installation and operation manual
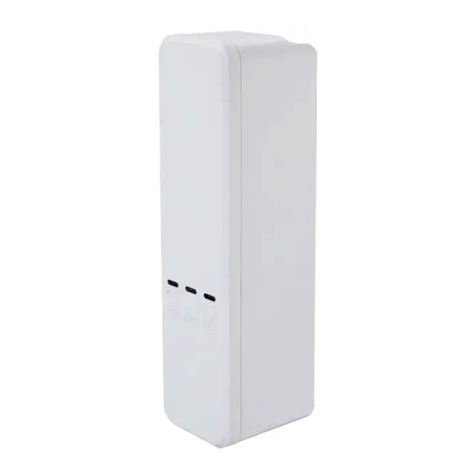
NEAR
NEAR NSM12 quick start guide
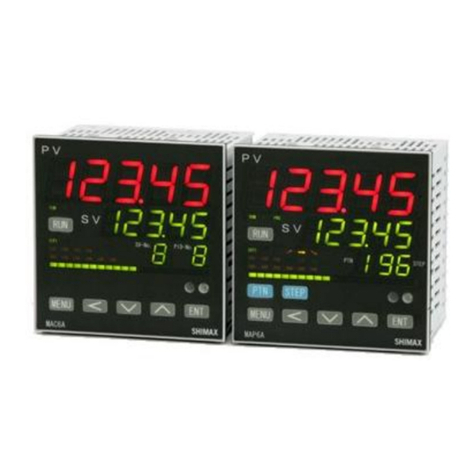
Shimax
Shimax MAC6A instruction manual
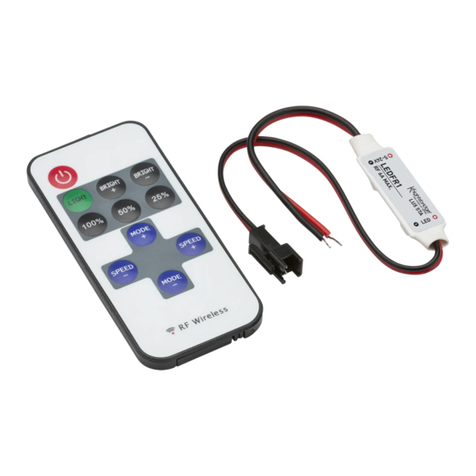
Knightsbridge
Knightsbridge Knightsbridge LEDFR1 Installation & maintenance manual