OPTO 22 LCSX-PLUS User manual

SNAP-LCSX AND LCSX-PLUS
INSTALLATION GUIDE
Form 1061-191112—November 2019
43044 Business Park Drive • Temecula • CA 92590-3614
Phone: 800-321-OPTO (6786) or 951-695-3000
Fax: 800-832-OPTO (6786) or 951-695-2712
www.opto22.com
Product Support Services
800-TEK-OPTO (835-6786) or 951-695-3080
Fax: 951-695-3017
Email: [email protected]
Web: support.opto22.com

SNAP-LCSX and LCSX-PLUS Installation Guide
ii
SNAP-LCSX and LCSX-PLUS Installation Guide
Form 1061-191112—November 2019
Copyright © 1997–2019 Opto 22.
All rights reserved.
Printed in the United States of America.
The information in this manual has been checked carefully and is believed to be accurate; however, Opto 22 assumes no
responsibility for possible inaccuracies or omissions. Specifications are subject to change without notice.
Opto 22 warrants all of its products to be free from defects in material or workmanship for 30 months from the
manufacturing date code. This warranty is limited to the original cost of the unit only and does not cover installation, labor,
or any other contingent costs. Opto 22 I/O modules and solid-state relays with date codes of 1/96 or newer are guaranteed
for life. This lifetime warranty excludes reed relay, SNAP serial communication modules, SNAP PID modules, and modules
that contain mechanical contacts or switches. Opto 22 does not warrant any product, components, or parts not
manufactured by Opto 22; for these items, the warranty from the original manufacturer applies. Refer to Opto 22 form
1042 for complete warranty information.
Wired+Wireless controllers and brains are licensed under one or more of the following patents: U.S. Patent No(s). 5282222,
RE37802, 6963617; Canadian Patent No. 2064975; European Patent No. 1142245; French Patent No. 1142245; British Patent
No. 1142245; Japanese Patent No. 2002535925A; German Patent No. 60011224.
Opto 22 FactoryFloor, groov, groov EPIC, mobile made simple, Optomux, and Pamux are registered trademarks of Opto 22.
Generation 4, groov Server, ioControl, ioDisplay, ioManager, ioProject, ioUtilities, mistic, Nvio, Nvio.net Web Portal,
OptoConnect, OptoControl, OptoDataLink, OptoDisplay, OptoEMU, OptoEMU Sensor, OptoEMU Server, OptoOPCServer,
OptoScript, OptoServer, OptoTerminal, OptoUtilities, PAC Control, PAC Display, PAC Manager, PAC Project, PAC Project Basic,
PAC Project Professional, SNAP Ethernet I/O, SNAP I/O, SNAP OEM I/O, SNAP PAC System, SNAP Simple I/O, SNAP Ultimate
I/O, and Wired+Wireless are trademarks of Opto 22.
ActiveX, JScript, Microsoft, MS-DOS, VBScript, Visual Basic, Visual C++, Windows, and Windows Vista are either registered
trademarks or trademarks of Microsoft Corporation in the United States and other countries. Linux is a registered
trademark of Linus Torvalds. ARCNET is a registered trademark of Datapoint Corporation. Modbus is a registered trademark
of Schneider Electric, licensed to the Modbus Organization, Inc. Wiegand is a registered trademark of Sensor Engineering
Corporation. Allen-Bradley, CompactLogix, ControlLogix, MicroLogix, SLC, and RSLogix are either registered trademarks or
trademarks of Rockwell Automation. CIP and EtherNet/IP are trademarks of ODVA. Raspberry Pi is a trademark of the
Raspberry Pi Foundation. The registered trademark Ignition by Inductive Automation® is owned by Inductive Automation
and is registered in the United States and may be pending or registered in other countries. CODESYS® is a registered
trademark of 3S-Smart Software Solutions GmbH.
groov includes software developed by the OpenSSL Project for use in the OpenSSL Toolkit. (http://www.openssl.org)
All other brand or product names are trademarks or registered trademarks of their respective companies or organizations.
Opto 22
Automation Made Simple.

SNAP-LCSX and LCSX-PLUS Installation Guide iii
iii
Table of Contents
Chapter Introduction . . . . . . . . . . . . . . . . . . . . . . . . . . . . . . . . . . . . . . . . . . . . . . . . . . . . . . . . . . .1
Software. . . . . . . . . . . . . . . . . . . . . . . . . . . . . . . . . . . . . . . . . . . . . . . . . . . . . . . . . . . . . . . . . . . . . . . . . . . . . . . . . . . . . . . . . . . 2
What’s In This Guide. . . . . . . . . . . . . . . . . . . . . . . . . . . . . . . . . . . . . . . . . . . . . . . . . . . . . . . . . . . . . . . . . . . . . . . . . . . . . . . . 2
For Help . . . . . . . . . . . . . . . . . . . . . . . . . . . . . . . . . . . . . . . . . . . . . . . . . . . . . . . . . . . . . . . . . . . . . . . . . . . . . . . . . . . . . . . . . . . 3
Chapter Quick Start . . . . . . . . . . . . . . . . . . . . . . . . . . . . . . . . . . . . . . . . . . . . . . . . . . . . . . . . . . . 5
What You Will Need. . . . . . . . . . . . . . . . . . . . . . . . . . . . . . . . . . . . . . . . . . . . . . . . . . . . . . . . . . . . . . . . . . . . . . . . . . . . . . . . 5
Instructions . . . . . . . . . . . . . . . . . . . . . . . . . . . . . . . . . . . . . . . . . . . . . . . . . . . . . . . . . . . . . . . . . . . . . . . . . . . . . . . . . . . . . . . . 5
Chapter Setting the Faceplate Jumpers . . . . . . . . . . . . . . . . . . . . . . . . . . . . . . . . . . . . . . . . 7
Setting Faceplate Jumpers. . . . . . . . . . . . . . . . . . . . . . . . . . . . . . . . . . . . . . . . . . . . . . . . . . . . . . . . . . . . . . . . . . . . . . . . . . 8
Setting the Controller Address . . . . . . . . . . . . . . . . . . . . . . . . . . . . . . . . . . . . . . . . . . . . . . . . . . . . . . . . . . . . . . . . . 8
Setting the Host Port . . . . . . . . . . . . . . . . . . . . . . . . . . . . . . . . . . . . . . . . . . . . . . . . . . . . . . . . . . . . . . . . . . . . . . . . . . 9
Setting the Host Port Baud Rate . . . . . . . . . . . . . . . . . . . . . . . . . . . . . . . . . . . . . . . . . . . . . . . . . . . . . . . . . . . . . . . 9
Setting the Communication Mode . . . . . . . . . . . . . . . . . . . . . . . . . . . . . . . . . . . . . . . . . . . . . . . . . . . . . . . . . . . . 10
Setting the Boot Mode . . . . . . . . . . . . . . . . . . . . . . . . . . . . . . . . . . . . . . . . . . . . . . . . . . . . . . . . . . . . . . . . . . . . . . . 10
AUTO and E/R Jumpers . . . . . . . . . . . . . . . . . . . . . . . . . . . . . . . . . . . . . . . . . . . . . . . . . . . . . . . . . . . . . . . . . 10
X1 Jumper . . . . . . . . . . . . . . . . . . . . . . . . . . . . . . . . . . . . . . . . . . . . . . . . . . . . . . . . . . . . . . . . . . . . . . . . . . . . . . 10
Chapter Configuring the Serial Ports . . . . . . . . . . . . . . . . . . . . . . . . . . . . . . . . . . . . . . . . . . . 11
Opening the Controller. . . . . . . . . . . . . . . . . . . . . . . . . . . . . . . . . . . . . . . . . . . . . . . . . . . . . . . . . . . . . . . . . . . . . . . . . . . . 12
Identifying the Serial Card and Jumpers . . . . . . . . . . . . . . . . . . . . . . . . . . . . . . . . . . . . . . . . . . . . . . . . . . . . . . . . . . . . 13
Configuring COM Port 0 . . . . . . . . . . . . . . . . . . . . . . . . . . . . . . . . . . . . . . . . . . . . . . . . . . . . . . . . . . . . . . . . . . . . . . . . . . . 13
COM0 RS-485 Configuration and Wiring . . . . . . . . . . . . . . . . . . . . . . . . . . . . . . . . . . . . . . . . . . . . . . . . . . . . . . 14
COM0 Modem Configuration and Wiring . . . . . . . . . . . . . . . . . . . . . . . . . . . . . . . . . . . . . . . . . . . . . . . . . . . . . 15
Configuring COM Port 1 . . . . . . . . . . . . . . . . . . . . . . . . . . . . . . . . . . . . . . . . . . . . . . . . . . . . . . . . . . . . . . . . . . . . . . . . . . . 15
Configuring COM Port 2 (SNAP-LCSX-PLUS Only) . . . . . . . . . . . . . . . . . . . . . . . . . . . . . . . . . . . . . . . . . . . . . . . . . . . 16
COM2 RS-232 Configuration . . . . . . . . . . . . . . . . . . . . . . . . . . . . . . . . . . . . . . . . . . . . . . . . . . . . . . . . . . . . . . . . . 16
COM2 RS-485 Configuration . . . . . . . . . . . . . . . . . . . . . . . . . . . . . . . . . . . . . . . . . . . . . . . . . . . . . . . . . . . . . . . . . 16
Pin Connections for COM2 . . . . . . . . . . . . . . . . . . . . . . . . . . . . . . . . . . . . . . . . . . . . . . . . . . . . . . . . . . . . . . . . . . . 17
Configuring COM Port 3 (SNAP-LCSX-PLUS Only) . . . . . . . . . . . . . . . . . . . . . . . . . . . . . . . . . . . . . . . . . . . . . . . . . . . 17
COM3 RS-232 Configuration . . . . . . . . . . . . . . . . . . . . . . . . . . . . . . . . . . . . . . . . . . . . . . . . . . . . . . . . . . . . . . . . . 17
COM3 RS-485 Configuration . . . . . . . . . . . . . . . . . . . . . . . . . . . . . . . . . . . . . . . . . . . . . . . . . . . . . . . . . . . . . . . . . 17
Pin Connections for COM3 . . . . . . . . . . . . . . . . . . . . . . . . . . . . . . . . . . . . . . . . . . . . . . . . . . . . . . . . . . . . . . . . . . . 18

SNAP-LCSX and LCSX-PLUS Installation Guide
iv
Chapter Mounting and Connecting the Controller . . . . . . . . . . . . . . . . . . . . . . . . . . . . . . . 19
Panel Dimensions. . . . . . . . . . . . . . . . . . . . . . . . . . . . . . . . . . . . . . . . . . . . . . . . . . . . . . . . . . . . . . . . . . . . . . . . . . . . . . . . . 19
Panel Mounting . . . . . . . . . . . . . . . . . . . . . . . . . . . . . . . . . . . . . . . . . . . . . . . . . . . . . . . . . . . . . . . . . . . . . . . . . . . . . . . . . . 20
DIN-Rail Dimensions . . . . . . . . . . . . . . . . . . . . . . . . . . . . . . . . . . . . . . . . . . . . . . . . . . . . . . . . . . . . . . . . . . . . . . . . . . . . . . 20
DIN-Rail Mounting . . . . . . . . . . . . . . . . . . . . . . . . . . . . . . . . . . . . . . . . . . . . . . . . . . . . . . . . . . . . . . . . . . . . . . . . . . . . . . . . 21
Connecting the Controller to Remote I/O . . . . . . . . . . . . . . . . . . . . . . . . . . . . . . . . . . . . . . . . . . . . . . . . . . . . . . . . . . 21
Chapter Specifications and Troubleshooting . . . . . . . . . . . . . . . . . . . . . . . . . . . . . . . . . . . 23
Specifications. . . . . . . . . . . . . . . . . . . . . . . . . . . . . . . . . . . . . . . . . . . . . . . . . . . . . . . . . . . . . . . . . . . . . . . . . . . . . . . . . . . . . 23
Power Supply Recommendations . . . . . . . . . . . . . . . . . . . . . . . . . . . . . . . . . . . . . . . . . . . . . . . . . . . . . . . . . . . . 24
LED Descriptions . . . . . . . . . . . . . . . . . . . . . . . . . . . . . . . . . . . . . . . . . . . . . . . . . . . . . . . . . . . . . . . . . . . . . . . . . . . . 24
Troubleshooting . . . . . . . . . . . . . . . . . . . . . . . . . . . . . . . . . . . . . . . . . . . . . . . . . . . . . . . . . . . . . . . . . . . . . . . . . . . . . . . . . . 24

SNAP-LCSX AND LCSX-PLUS Installation Guide 1
1
1: IntroductionChapter 1
Introduction
The SNAP-LCSX and SNAP-LCSX-PLUS controllers are designed for use
with Opto 22’s SNAP or Mistic remote I/O systems and Opto 22’s
FactoryFloor software for industrial automation. The SNAP-LCSX and
LCSX-PLUS controllers provide powerful real-time industrial control in a
compact package.
The SNAP-LCSX and LCSX-PLUS controllers have identical dimensions and
share similar features, such as a single 5-volt power supply requirement
and DIN rail and panel mounting options. Both contain powerful 32-bit
processors capable of a wide range of computing functions. A
SNAP-LCSX controller (shown at right) is the same size as a SNAP power
supply.
The difference in the two controllers is shown below. The SNAP-LCSX has
two serial communication (COM) ports, and the SNAP-LCSX-PLUS has
four.
COM
+5V
RX3
RX2
RXI
RX0
RUN
HOST
COM 0
I/O
COM 1
SNAP-LCSX-PLUS
11AUX1
COM 2
1AUX2
COM 3
1
TX3
TX2
TXI
TX0
PWR
E/R
AUTO
X0
X1
H0
H1
B0
B1
B2
B3
A0
A1
A2
A3
A4
A5
A6
A7
SNAP-LCSX
SNAP-LCSX-PLUS

SOFTWARE
SNAP-LCSX AND LCSX-PLUS Installation Guide
2
SOFTWARE
The SNAP-LCSX and LCSX-PLUS controllers are designed to work in combination with Opto 22’s FactoryFloor®
software suite, which consists of four integrated components:
•OptoControl™, a graphical, flowchart-based development environment for machine control and process
applications
•OptoDisplay™, an intuitive human-machine interface (HMI) and trending package
•OptoServer™, a robust, OPC-compliant data server that connects the controller network with the PC
network
•OptoConnect™, a bi-directional link between the SNAP controller database and Microsoft’s SQL Server
and Access databases.
The SNAP-LCSX and LCSX-PLUS controllers are programmed using OptoControl on a PC workstation.
OptoControl is easy to use and self-documenting. It uses a plain English command set and a long tagname
database shared by all FactoryFloor components.
These controllers also work with Opto 22’s 16-bit software: Cyrano®, Mistic®MMI, and Mistic Data Server (MDS).
WHAT’S IN THIS GUIDE
This guide includes:
Chapter 1: Introduction provides Product Support information.
Chapter 2: Quick Start describes how to install a generic SNAP-LCSX controller using factory settings.
Chapter 3: Setting the Faceplate Jumpers provides detailed instructions for changing factory faceplate
settings.
Chapter 4: Configuring the Serial Ports provides detailed instructions for changing factory serial pot
settings.
Chapter 5: Mounting and Connecting the Controller shows how to mount the controller and then
connect it to I/O.
Chapter 6: Specifications and Troubleshooting provides specifications, power supply recommendations,
LED descriptions, and troubleshooting information.

INTRODUCTION
SNAP-LCSX AND LCSX-PLUS Installation Guide 3
FOR HELP
If you have problems installing or using the SNAP-LCSX or LCSX-PLUS controller and cannot find the help you
need in this guide, contact Opto 22 Product Support Monday through Friday, 8 a.m. to 5 p.m. Pacific Time.
Phone: 800-TEK-OPTO (800-835-6786 toll-free
in the U.S. and Canada)
951-695-3080
Monday through Friday,
7 a.m. to 5 p.m. Pacific Time
Fax: 951-695-3017
Email: suppor[email protected]
Opto 22 website: www.opto22.com
When calling for technical support, be prepared to provide the following information about your system to
the Product Support engineer:
•Software and version being used
•Firmware versions
•PC configuration (type of processor, speed, memory, and operating system)
•A complete description of your hardware and operating systems, including:
– type of power supply
– types of I/O units installed
– third-party devices installed (for example, barcode readers)
•Specific error messages seen.
NOTE: Email messages and phone calls
to Opto 22 Product Support are
grouped together and answered in the
order received.

FOR HELP
SNAP-LCSX AND LCSX-PLUS Installation Guide
4

SNAP-LCSX AND LCSX-PLUS Installation Guide 5
5
1: Quick StartChapter 1
Quick Start
This section gives quick instructions for installing a generic SNAP-LCSX controller using factory-default
settings, which are shown in the table on page 8. If you are not using the factory defaults, see “Setting the
Faceplate Jumpers”on page 7 and “Configuring the Serial Ports”on page 11 for additional information.
WHAT YOU WILL NEED
•SNAP-LCSX or LCSX-PLUS controller and box kit
•+5 VDC power supply
•PC with OptoControl and a free RS-232 serial port
•RS-232 cable
•multimeter
•small flathead screwdriver
•pair of wire strippers/cutters.
INSTRUCTIONS
1. With the power supply off or unplugged, connect it to the controller.
The SNAP-LCSX controller requires a power supply capable of delivering at least 500mA at 5V ±5 percent.
The controller does not have a power switch; to turn it off, switch off the power supply.
CAUTION: Reversing wire polarity may cause damage to your controller. This damage is not covered by Opto 22’s
warranty. If in doubt about which wire is which on your power supply, check with a meter.
a. With the power supply off or unplugged, connect the +5V lead from the power supply (normally
red) to the +5V terminal on the face of the SNAP-LCSX.
b. Connect the COM wire from the power supply (normally black) to the COM terminal on the face of
the SNAP-LCSX.

INSTRUCTIONS
SNAP-LCSX AND LCSX-PLUS Installation Guide
6
2. Connect the SNAP-LCSX controller to Opto 22 I/O units.
Use the built-in COM1 port to communicate with Opto 22 digital or analog (or both) I/O. Set up the I/O
unit as shown in its installation guide. The diagram on the next page illustrates connection with a B3000
brain board.
3. Connect the SNAP-LCSX controller to a personal computer (PC).
You can start with a pre-wired RS-232 cable that you don’t mind cutting, or you can make your own
cable. Cut off the end of the cable that DOES NOT plug into the computer and wire the cable as shown in
the diagram below:
4. Configure the controller using OptoControl.
In order to be useful with a SNAP-LCSX or LCSX-PLUS controller, a PC must have at least one element of
Opto 22’s FactoryFloor software suite installed: OptoControl, OptoDisplay, OptoServer, or OptoTerm. This
guide assumes that you will configure the controller using OptoControl. For instructions, see the
OptoControl User’s Guide.
Your SNAP-LCSX or LCSX-PLUS controller is now ready to run OptoControl strategies. The rest of this guide
gives detailed instructions in case you need to use non-factory settings.

SNAP-LCSX AND LCSX-PLUS Installation Guide 7
7
1: Setting the Faceplate JumpersChapter 1
Setting the Faceplate Jumpers
This chapter shows how to configure the controller’s faceplate jumpers.
For help with See page
Setting the Controller Address 8
Setting the Host Port 9
Setting the Host Port Baud Rate 9
Setting the Communication Mode 10
Setting the Boot Mode 10

SETTING FACEPLATE JUMPERS
SNAP-LCSX AND LCSX-PLUS Installation Guide
8
SETTING FACEPLATE JUMPERS
The following table summarizes faceplate jumper settings. Shaded entries show default settings.
Setting the Controller Address
Each Opto 22 controller connected to a host computer must have a unique address between
1 and 255 (1 and FF hexadecimal).
The table on the following page shows possible addresses and their corresponding jumper settings. The
factory default is 1. The most significant bit is 7 and the least significant bit is 0.
NOTE: Zero is not a valid address.
COM
+5V
RX3
RX2
RXI
RX0
RUN
HOST
COM 0
I/O
COM 1
SNAP-LCSX-PLUS
11
AUX1
COM 2
1
AUX2
COM 3
1
TX3
TX2
TXI
TX0
PWR
E/R
AUTO
X0
X1
H0
H1
B0
B1
B2
B3
A0
A1
A2
A3
A4
A5
A6
A7
Jumper(s) Description Position Setting
E/R EEPROM/RAM
In Run from RAM
Out Run from
EEPROM
Auto Autoboot
In Autoboot
enabled
Out Autoboot dis-
abled
X0 Communication In Binary
Out ASCII
X1 Boot Loader In Boot to kernel
Out Boot to loader
H0, H1 Host Port
H0 H1
In In COM0
Out In COM1
Baud 0–3 Baud Rate
B0 B1 B2 B3
Out In In In 115.2 KBd
In Out In In 76.8 KBd
Out Out In In 57.6 KBd
In In Out In 38.4 KBd
Out In Out In 19.2 KBd
In Out Out In 9600 Bd
Out Out Out In 4800 Bd
In In In Out 2400 Bd
Out In In Out 1200 Bd
In Out In Out 600 Bd
Out Out In Out 300 Bd
Address 0–
7Address Bits
Bit 0 In 1
Bit 1 In 2
Bit 2 In 4
Bit 3 In 8
Bit 4 In 16
Bit 5 In 32
Bit 6 In 64
Bit 7 In 128

SETTING THE FACEPLATE JUMPERS
SNAP-LCSX AND LCSX-PLUS Installation Guide 9
Setting the Host Port
The controller host port jumpers H0 and H1 determine which port the controller’s default host task will be
started on. Because the host task is required for communication to any of Opto 22’s programming or interface
software, the default host port must be set to the port attached to the host computer. The factory setting is
COM0.
You can change the host port to COM1, as shown in the table at right.
However, in general it should not be used this way with I/O, since COM1 was
designed to communicate with I/O.
Setting the Host Port Baud Rate
The factory setting for the host port baud rate is 38.4 KBd, but
baud rates from 300 Bd to 115 KBd are selectable using
jumpers B0 through B3. In general, it is best to choose the
fastest baud rate the host computer and the controller will
both support. Lower baud rates may be necessary for long
cable runs, in high-noise environments, or for compatibility
with modems or other data transmission equipment. The table
at right shows jumper settings for available baud rates. The
shaded entry is the default setting.
Address Jumpers.
COM Port H0 H1
COM0 In In
COM1 Out In
Baud Rate B0 B1 B2 B3
115.2 KBd Out In In In
76.8 KBd In Out In In
57.6 KBd Out Out In In
38.4 KBd In In Out In
19.2 KBd Out In Out In
9600 Bd In Out Out In
4800 Bd Out Out Out In
2400 Bd In In In Out
1200 Bd Out In In Out
600 Bd In Out In Out
300 Bd Out Out In Out

SETTING FACEPLATE JUMPERS
SNAP-LCSX AND LCSX-PLUS Installation Guide
10
Setting the Communication Mode
You can select ASCII or binary communications mode using jumper X0.
The factory default is binary, which is generally faster than ASCII. ASCII
is typically used only for compatibility with modems or other data
transmission equipment, or with host devices that for some reason
cannot support binary mode. The table at right shows jumper settings
for the communication mode.
Setting the Boot Mode
The boot mode jumpers determine how the controller acts when it is turned on. The AUTO, E/R, and X1
jumpers set the boot mode.
AUTO and E/R Jumpers
The AUTO jumper determines whether the controller automatically starts running your strategy (autoboot) or
waits until instructed to do so by the host computer. The E/R jumper determines whether the strategy is
executed from battery-backed RAM or from Flash ROM. The factory settings are non-autoboot and execute
from RAM.
There is no operational difference between execution from battery-backed RAM or ROM, except that the
SNAP-LCSX and LCSX-PLUS have significantly more space available in RAM for program storage. The drawback
to execution from RAM is that the program will be lost when the backup battery dies. (Battery life typically
exceeds three years.)
Before the controller will execute a program from ROM, you must have stored the program in Flash ROM by
selecting that download function in OptoControl. In general, it is best to wait until program development is
complete to use the autoboot feature or store the program in Flash ROM.
X1 Jumper
Typically, this jumper is needed only if the firmware in the controller has somehow been corrupted, and the
controller cannot execute its full kernel properly. The X1 jumper sets the controller to “boot to loader”mode,
which will prepare it for a kernel (firmware) download. Under normal conditions, however, you can update the
controller firmware using one of Opto 22’s firmware update utilities, without needing to set this jumper
The following table shows Auto, E/R, and X1 jumper settings. Default settings are shaded.
Boot Mode Auto E/R X1
Autoboot enabled In
Autoboot disabled Out
Run from RAM In
Run from EEPROM Out
Boot to kernel In
Boot to loader Out
Communication Mode X0
Binary In
ASCII Out

SNAP-LCSX AND LCSX-PLUS Installation Guide 11
11
“Configuring the Serial Ports” on page 111: Configuring the Serial PortsChapter 1
Configuring the Serial Ports
This chapter shows how to configure the controller’s serial ports.
The SNAP-LCSX comes with two serial ports:
• COM0 is selectable as RS-232, RS-485 half-duplex (2-wire), or RS-485 full duplex (4-wire). The default
mode is RS-232 for connection to a PC. In RS-232 mode, COM0 also supports RTS and DTR/DCD flow
control for use with modems.
• COM1 is an Opto 22 remote I/O port (half-duplex RS-485 only).
The SNAP-LCSX-PLUS has two additional serial ports, both configurable either as RS-232
or as half- or full-duplex RS-485. The default mode is RS-232. In RS-232 mode, COM2 and
COM3 support RTS flow control only. Interrupt (IRQ) functionality is available in RS-485 2-wire mode only.
Since most systems use the default modes, it’s not normally necessary to configure serial ports. However, if
you need to change the serial port configuration, you must open the controller and set configuration jumpers
on the serial card inside.
For help with See page
Opening the Controller 12
Identifying the Serial Card and Jumpers 13
Configuring COM Port 0 13
Configuring COM Port 1 15
Configuring COM Port 2 (SNAP-LCSX-PLUS Only) 16
Configuring COM Port 3 (SNAP-LCSX-PLUS Only) 17

OPENING THE CONTROLLER
SNAP-LCSX AND LCSX-PLUS Installation Guide
12
OPENING THE CONTROLLER
1. Following the illustration below, remove the SNAP-LCSX top cover and take the processor board and
serial board out of the case.
Top cover
Processor board
and serial board
Case

CONFIGURING THE SERIAL PORTS
SNAP-LCSX AND LCSX-PLUS Installation Guide 13
IDENTIFYING THE SERIAL CARD AND JUMPERS
The serial card is the card with the port connectors. Its jumpers (JP) are shown in the diagram below.
To change the serial port configuration, set jumpers on the serial card for each port as illustrated in the
following sections.
NOTE: JP7 must remain in its default position as shown above. Other positions are reserved for future use.
CONFIGURING COM PORT 0
The default mode for COM0 is RS-232, and the wiring diagram is
shown in step 3 on page 6. Pinouts are also shown below. Jumper
groups 2 and 4 control COM0. Default jumper settings are shown in
the diagram at right. (Jumpers F and G in JP2 are shown for
reference but grayed out, as they do not affect COM0.)
COM0 can also be configured for RS-485 two- or four-wire or for use
with a modem. See the following page for details.
JP2
OPTO 22
SNAP CANNED SX
SERIAL CARD
JP6JP3JP5
JP1
JP4
JP4
JP2
JP6
JP5
JP1
JP3
JP7
JP7
COM0 Default Jumpers.
Port connectors would be at
the top of this diagram.
Pinouts for COM0
Pin RS-232
1 DCD
2TX
3RX
4RTS
5 CTS
6 DTR
7 GND

CONFIGURING COM PORT 0
SNAP-LCSX AND LCSX-PLUS Installation Guide
14
COM0 RS-485 Configuration and Wiring
The following diagrams illustrate jumper settings and wiring for RS-485 two-wire and RS-485 four-wire.
(Jumpers F and G in JP2 are shown for reference but grayed out, as they do not affect COM0.)
RS-485 Two-Wire.
Port connectors would be at
the top of this diagram.
RS-485
Port connectors would be at
the top of this diagram.

CONFIGURING THE SERIAL PORTS
SNAP-LCSX AND LCSX-PLUS Installation Guide 15
COM0 Modem Configuration and Wiring
In RS-232 mode, COM0 also supports RTS and DTR/DCD flow control for use with modems, either with or
without a carrier detect. Check your modem documentation for additional wiring information, possible
jumper configuration, and initialization setup. You may also want to read Opto 22’s communication
application notes, available on the Opto 22 Web site or through our Bulletin Board Service. See page 3 for
details.
The following diagrams illustrate wiring for modems. Use the COM0 default jumper settings for modems
(shown in the diagram on page 13).
CONFIGURING COM PORT 1
COM1 comes from the factory set up for communicating
with Opto 22 remote I/O. COM1 is a two-wire RS-485 port
only. It will not typically require configuration unless you are
using it with devices that are not Opto 22 remote I/O.
Jumper group 6 controls COM1. Default jumper settings are
shown in the diagram at right. Pinouts are shown below.
Wiring to a Modem without Carrier
Wi
r
i
ng to a
M
o
d
em w
i
t
h
C
arr
i
er
COM1 Default Jumpers.
Pinouts for COM1
Pin RS-485
2-wire
1 TX/RX +
2 TX/RX -
3 COM
4 IRQ +
5 IRQ -

CONFIGURING COM PORT 2 (SNAP-LCSX-PLUS ONLY)
SNAP-LCSX AND LCSX-PLUS Installation Guide
16
CONFIGURING COM PORT 2 (SNAP-LCSX-PLUS ONLY)
The default for COM2 is RS-232, but this port can also be configured as RS-485 two-wire or four-wire. Jumpers
1A, 1B, 2F, and 2G control the mode for COM2. The grayed-out jumpers are shown for reference only.
NOTE: The mode may be shown incorrectly on the board itself. Use the diagrams below to set the mode.
COM2 RS-232 Configuration
COM2 RS-485 Configuration
Jumper functions and two-wire and four-wire jumper settings are shown below. Use jumper group 3 (JP3) for
COM2. Make certain that the JP7 jumper remains in its default position, as shown.
RS-232 Mode (default)
JP1
JP7
JP2
ABCDE F G ABCDE F G
11
RS-485 Mode
JP1
JP7
JP2
ABCDE F G ABCDE F G
11
RS-485 Jumper Functions Two-Wire and Four-Wire Jumper Settings
JP3
This manual suits for next models
1
Table of contents
Other OPTO 22 Controllers manuals
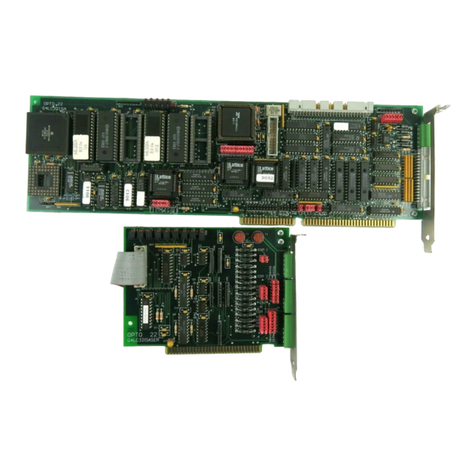
OPTO 22
OPTO 22 G4LC32ISA-LT User manual

OPTO 22
OPTO 22 groov EPIC User manual
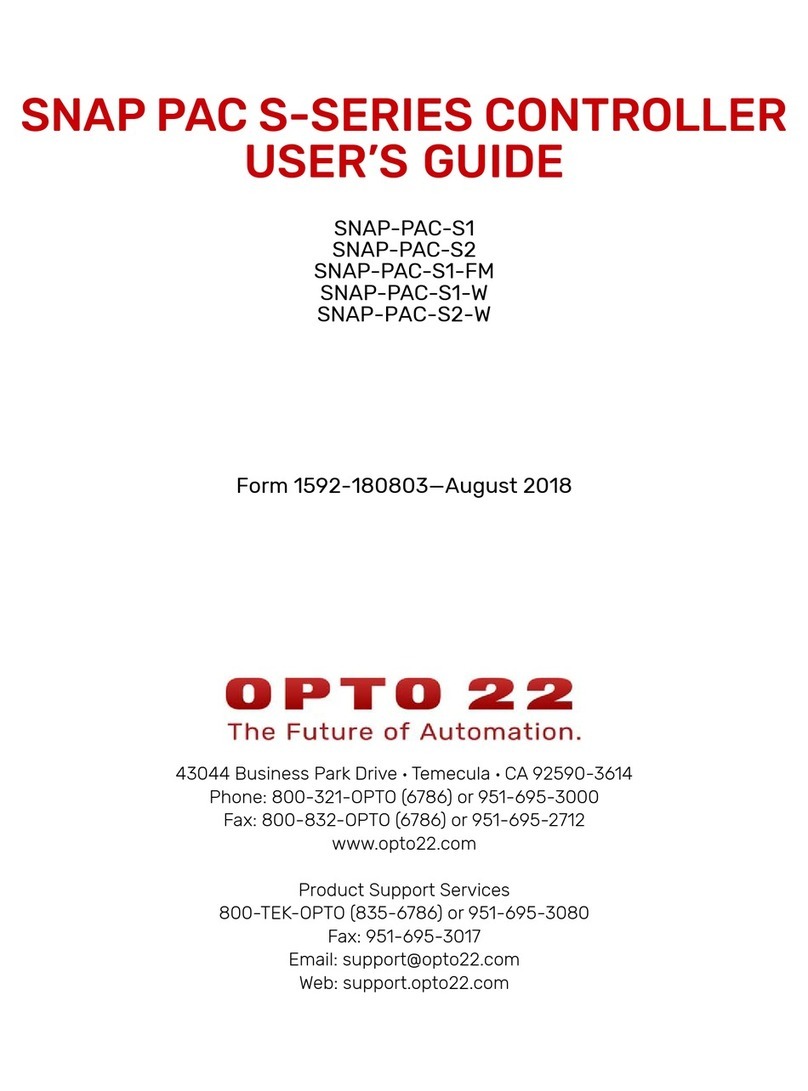
OPTO 22
OPTO 22 SNAP PAC S Series User manual
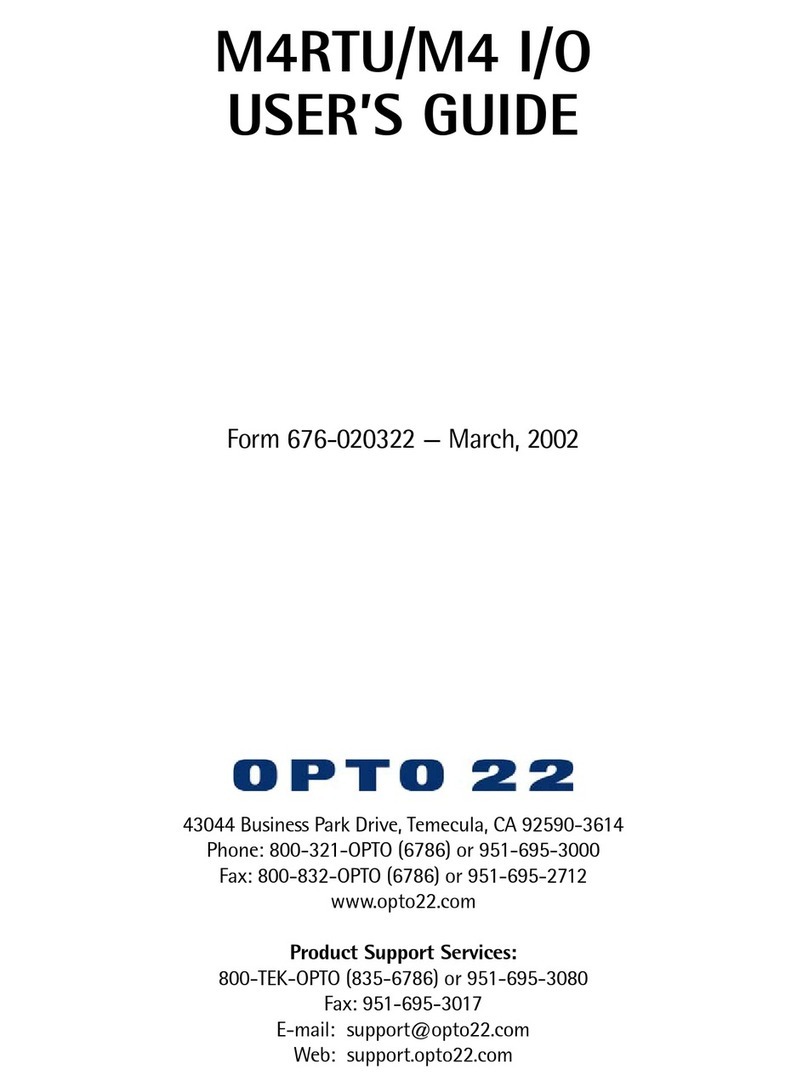
OPTO 22
OPTO 22 Modular M4RTU User manual
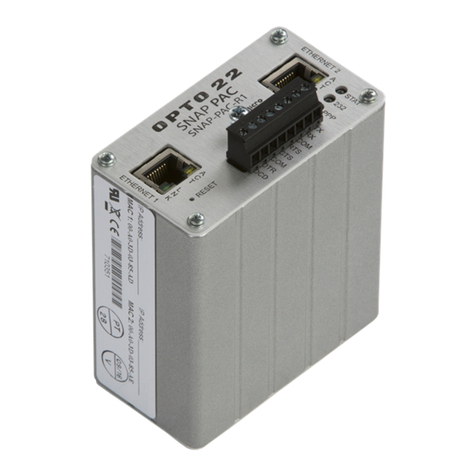
OPTO 22
OPTO 22 SNAP-PAC-R1 User manual
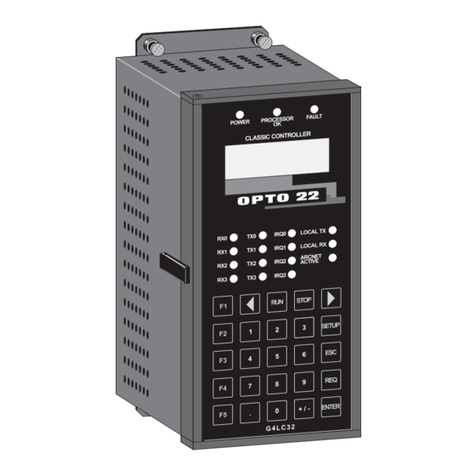
OPTO 22
OPTO 22 G4LC32 User manual
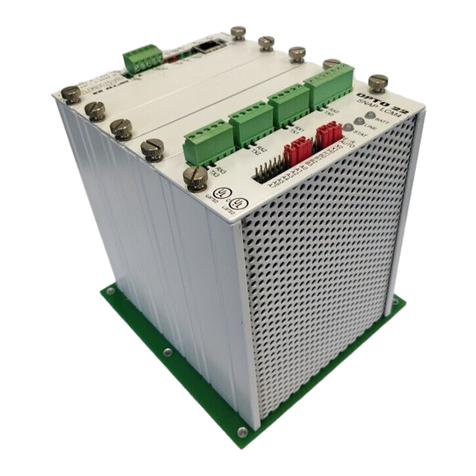
OPTO 22
OPTO 22 SNAP-LCM4 User manual
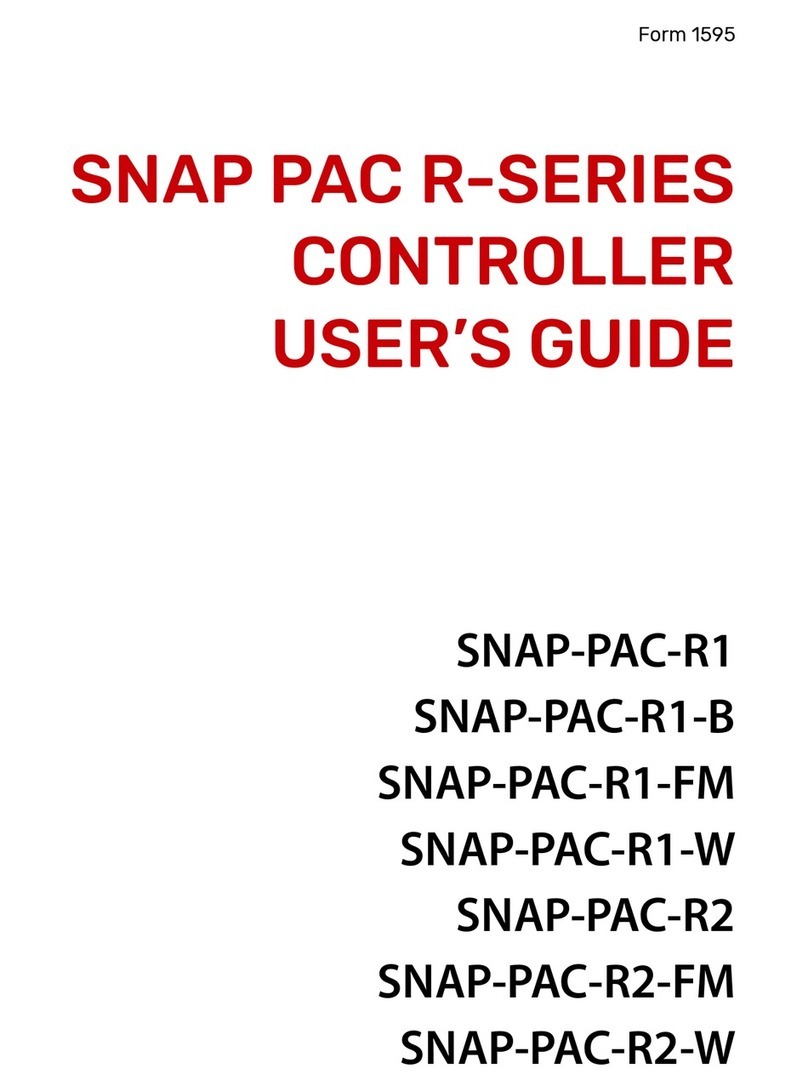
OPTO 22
OPTO 22 SNAP PAC R SERIES User manual
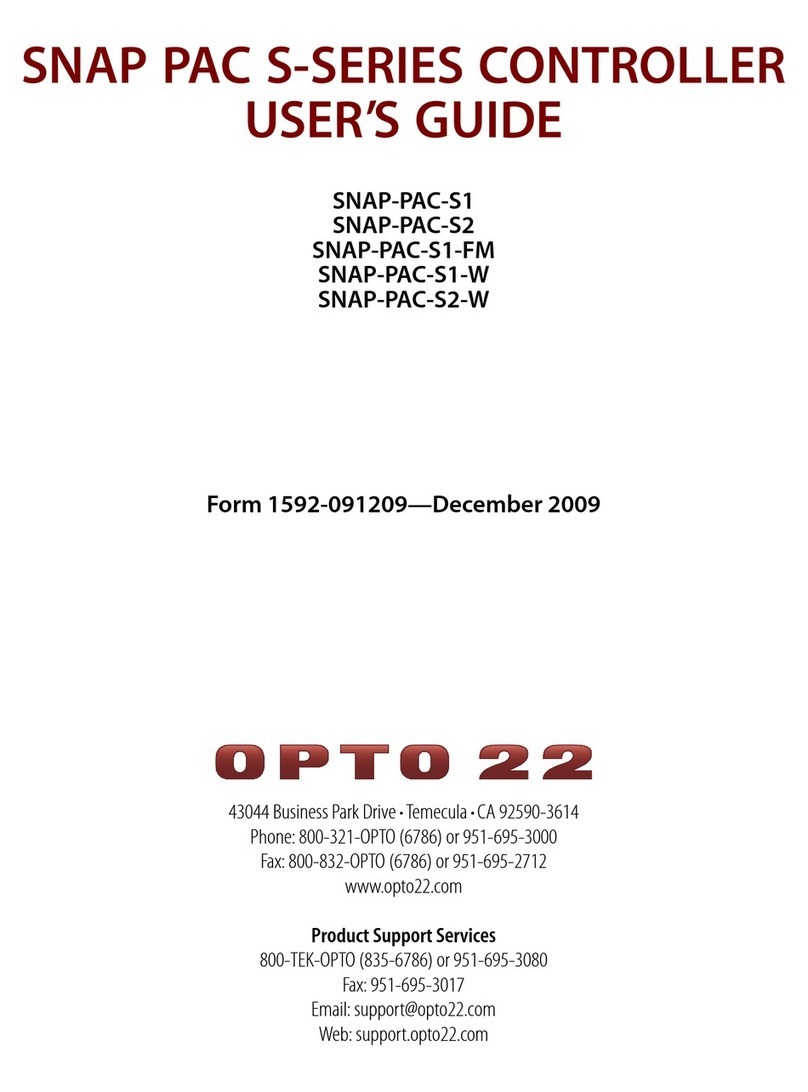
OPTO 22
OPTO 22 SNAP-PAC-S1 User manual

OPTO 22
OPTO 22 GROOV BOX User manual