OPW Petro Vend 200 M1010 Technical Document

Part Number: M1010, Rev. 10
Issue Date: 7/22/2021
Supersedes: 4/27/2021
M1010 - Petro Vend®200™
Fuel Control System
Installation Operation and Maintenance Guide

NOTE: Before you use this guide, make sure you have the latest revision. Check the revision
level of this document against the most current revision found at
http://www.opwglobal.com/opw-fms/tech-support/manuals-how-to-videos. Download the
latest revision if necessary.
OPW Fuel Management Systems is a part of Dover Fueling Solutions.
Copyright Information
© 2020 Dover Fueling Solutions. All rights reserved. DOVER, the DOVER D Design, DOVER FUELING
SOLUTIONS, and other trademarks referenced herein are trademarks of Delaware Capital Formation.
Inc./Dover Corporation, Dover Fueling Solutions UK Ltd. and their affi liated entities.
Contact OPW Fuel Management Systems
Visit us at http://www.opwglobal.com/opw-fms, or contact us at:
Call 1-877-OPW-TECH (877-679-8324)
For calls outside US and Canada, call +1-708-485-4200
Monday through Friday, 7 a.m. to 6 p.m., US CST
For technician registration, see
http://www.opwglobal.com/opw-fms/tech-support/technician-registration
For in-depth training via OPW University, see
http://www.opwglobal.com/opw-fms/tech-support/training-certification
Doc. No.: M1010 Rev.: 10
Page 2 of 98

Table of Contents
Section 1 PV200 Fuel Control System 6
1.1 Technical Specifications 7
1.2 Safety Warnings 8
1.3 Information Panels 8
1.4 Hazardous Areas 10
1.4.1 NFPA/NEC – Class I, Div. 1 & Div. 2 10
1.4.2 Installation Requirement 11
1.5 FCC Compliance 13
Section 2 System Overview 14
Section 3 PV200 Installation 18
3.1 Pedestal and Enclosure Installation 18
3.2 Aluminum Enclosure Conduit Knockouts 20
3.3 Flex Conduit Installation 20
3.4 Power and Communication Wiring 20
Section 4 Preparation of System Conduit & Wiring Requirements 22
4.1 Conduit/Wiring Requirements 22
4.1.1 Petro-Net Wiring 23
4.2 PV200 Power, Petro-Net 24
4.2.1 Grounding 27
4.2.2 Circuit Breakers 27
Section 5 Complete the Installation 28
Section 6 Maintenance 29
Section 7 Receipt Printer 30
7.1 Receipt Printer Installation 30
7.2 Load Receipt Printer Paper 31
Doc. No.: M1010 Rev.: 10
Page 3 of 98

7.3 Clear a Paper Jam 32
Section 8 Antenna Installation 34
Section 9 Main Board 36
9.1 Main Board Connections 36
9.2 Main Board LEDs 38
9.3 Main Board Jumpers 39
Section 10 PV200 Terminal Setup 40
10.1 Screen Controls 40
10.2 Readers Menu 41
Section 11 Exploded View Drawings 42
11.1 PV200 Enclosure Assembly 42
11.2 PV200 Display 43
11.3 PV200 Pocket 44
11.4 PV200 Door 45
11.5 Fastener Specifications 46
11.6 Cables 46
Appendix A - Software Upgrade Procedure 47
Appendix B - PV200™ Options Installations 49
Appendix B - 1 - Alpha Keypad Installation 50
Appendix B - 2 - ChipKey Reader Installation 53
Appendix B - 3 - Magnetic Card Reader Installation 57
Appendix B - 4 - Dual Magnetic Card Reader Installation 61
Appendix B - 5 - Proximity Reader Installation 67
Appendix B - 6 - AVI - PV200 Option Installation 71
Appendix B - 7 - DX Fleet Option 73
Appendix B - 8 - Modem and Gateway Installations 79
Doc. No.: M1010 Rev.: 10
Page 4 of 98

Section 1 PV200 Fuel Control System
Figure 1-1 PV200 Fuel Control System
About this manual:
This manual includes specified information about the PV200. Information related to the FSC3000 Fuel Site
Controller can be found in the M1700 FSC3000 Installation, Operation and Maintenance Manual.
Doc. No.: M1010 Rev.: 10
Page 6 of 98

1.1 Technical Specifications
Specification Table
Cabinet Dimensions: 18 inch H x 14 inch W x 10 inch D (46 cm x 36 cm x 26 cm)
Pedestal Dimensions: 40 inch H x 14 inch W x 9 inch D (122 cm x 36 cm x 23 cm) is
standard; 32-inch and 48-inch heights are optional
Power Requirements: 120 VAC/240 VAC (Switch Selectable), 50/60 Hz, 220 watts
maximum
Operating Temperature Range: -40°F to 122°F (-40°C to 50°C)
Range of Environmental Conditions:
Outdoor use, Altitude less than 5000m, temperature range, rel-
ative humidity (80 % for temperatures up to 31 °C decreasing
linearly to 50 % relative humidity at 40 °C), Wet location, Pol-
lution degree 2
Graphics display: 7 inch (18 cm) color display
Pedestal and Cabinet: Powder-coated aluminum
Reader Options:
Magnetic Card Reader
Chipkey
Proximity Reader
Alpha Keypad
Numeric Keypad (installed)
Pedestal Options:
48 inch (Standard)
40 inch: 40 inch ADA (Americans with Disabilities Act) com-
pliant for off island installations
32 inch: 32 inch ADA compliant for on island installations
Heaters: Turn ON (inside enclosure) 42° F ±2° F
Turn OFF (inside enclosure) 46° F ±2° F
Doc. No.: M1010 Rev.: 10
Page 7 of 98

1.2 Safety Warnings
This manual contains many important Safety Alerts. There can be a risk of injury or damage to property if you
do not obey these alerts. The panels below show the types of safety warnings that can be seen and how
each is specified.
DANGER: Indicates an immediately hazardous condition that, if not prevented, will
result in death or serious injury.
WARNING: Indicates a possibly hazardous condition that, if not prevented, could
result in death or serious injury.
CAUTION: Indicates a possibly hazardous situation that, if not prevented, could
result in minor or moderate injury.
NOTICE: Indicates important information not related to hazards. A condition that, if not
prevented, can result in property damage.
SAFETY INSTRUCTIONS: Indicates instructions and procedures related to safety or
gives the location of safety equipment
1.3 Information Panels
NOTE: This panel gives more information about an instruction or procedure.
IMPORTANT: This panel contains special information that is important and must be read and
obeyed.
Doc. No.: M1010 Rev.: 10
Page 8 of 98

REMINDER: This panel shows information that has been given before in the manual that is
important to show again.
TIP: A step or procedure that is recommended to make another step or procedure easier.
INFORMATION: This panel shows references to more information in other sources.
READ CAREFULLY: This panel points to information that must be fully read and understood
before doing the procedure(s) that comes after.
Doc. No.: M1010 Rev.: 10
Page 9 of 98

1.4 Hazardous Areas
Any fuel dispenser is a hazardous area as defined in the National Electrical Code. Installation must be in
accordance with the following:
lNational Electrical Code (NFPA No. 70)
lMotor Fuel Dispensing Facilities and Repair Garages Code (NFPA No. 30A)
1.4.1 NFPA/NEC – Class I, Div. 1 & Div. 2
The Class I, Division 1 and Class I, Division 2 hazardous areas are specified below:
Class I locations. Class I locations: Where flammable gases or vapors are or can be in the air in
quantities sufficient to cause explosive or ignitable mixtures. Class I locations include:
lClass I, Division 1. A Class I, Division 1 location is a location where:
nThere can be concentrations of flammable vapors during normal operation.
nThere can be concentrations of flammable vapors during repair or maintenance
operations or when the leakage of liquid fuel can occur.
nA release of concentrations of flammable vapors can occur as a result of
equipment failure, incorrect operation or unsatisfactory procedures that could also
cause a failure of electrical equipment.
lClass I, Division 2. A Class I, Division 2 location is a location where:
nAn accidental failure or incorrect operation of vapor containment system equipment
or containers that can release hazardous vapors from flammable liquids or gases.
nA failure or incorrect operation of positive mechanical ventilation precautions result
in the release of hazardous concentrations of flammable gases or vapors.
nConcentrations of flammable gases or vapors can occasionally flow from a
containment or ventilation system to an adjacent Class I, Division 1 location. This
flow of gases or vapors must be prevented by sufficient positive-pressure
ventilation from a source of clean air. Sufficient precautions to prevent ventilation
failure must be installed.
WARNING: To prevent possible fire or explosion, do not mount your
system site controller or any other electrical part of the system, including
printers and modems, within or above the defined "hazardous" areas.
IMPORTANT: It is the installer's responsibility to know and obey all local codes.
Doc. No.: M1010 Rev.: 10
Page 10 of 98

OPW Fuel Management System’s fuel control systems are listed for use in a non-classified area. All of the
equipment must be installed outside of the hazardous areas.
NOTE: Local codes can dictate specific installation requirements. Installation is subject to
approval by the local authority that has jurisdiction at the site.
1.4.2 Installation Requirement
OPW Terminals are designed to be installed above the hazardous area when using the terminal’s associated
pedestal.
The pedestal can be mounted in the hazardous area but a seal-off must be the first fitting for all conduits that
go into the area.
IMPORTANT: All unused knockout holes that have been removed must be sealed.
For more information on conduit and seal-off installation for PV200 see Conduit/Wiring Requirements.
Figure 1-1 Dispenser Installations
Doc. No.: M1010 Rev.: 10
Page 11 of 98

WARNING: Knockouts and installation hardware are provided for all
cabinetry. Do NOT drill holes in the enclosures. This would violate the
safety listing of the system.
CAUTION: Be sure to wear all required personal
protective equipment (PPE). This includes safety
glasses, hardhat, safety shoes and reflective vest.
Barricade the work area before installation.
Be sure to obey all applicable Lockout/Tagout (LOTO)
procedures before installation.
IMPORTANT: It is recommended to do a check of the electrical system with a multimeter to
make sure all connections are de-energized before you proceed with the installation.
Doc. No.: M1010 Rev.: 10
Page 12 of 98

1.5 FCC Compliance
This system complies with Part 15 of the Federal Communications Commission (FCC) Rules & Regulations.
Operation is applicable to these conditions:
lThis device must not cause harmful interference.
lThis device must accept interference received, including interference that can cause undesired
operation.
Doc. No.: M1010 Rev.: 10
Page 13 of 98

Section 2 System Overview
NOTE: It is necessary to use shielded pulser cable to prevent electrical noise when the pump
conduit is shared.
NOTE: Do not run Petro-Net wiring in the wiring trough.
For installations that will use wireless Ethernet communication refer to M00-20-6020 Wireless Ethernet
Radio User's Guide.
For installations that will use wireless Petro-Net modem communication refer to M00-20-7074 Wireless
Petro-Net Modem Installation Guide.
These guides can be downloaded at https://www.opwglobal.com/opw-fms/tech-support/manuals-how-to-
videos/technical-manuals.
Typical System Diagram with an Integrated FSC (Mechanical Pump Con-
trol)
Doc. No.: M1010 Rev.: 10
Page 14 of 98

Typical System Diagram with a Remote FSC (Mechanical Pump Control)
For installations with remote PCMs, see M1700 FSC3000 Installation, Operation and Maintenance Guide.
You can download this guide at http://www.opwglobal.com/opw-fms/tech-support/manuals-how-to-videos.
Doc. No.: M1010 Rev.: 10
Page 15 of 98

Typical System Diagram with an Integrated FSC (Electronic Pump Control)
Doc. No.: M1010 Rev.: 10
Page 16 of 98

Typical System Diagram with a Remote FSC (Electronic Pump Control)
For installations with remote DPC, see M1700 FSC3000 Installation, Operation and Maintenance Guide.
You can download this guide at http://www.opwglobal.com/opw-fms/tech-support/manuals-how-to-videos.
Doc. No.: M1010 Rev.: 10
Page 17 of 98

Section 3 PV200 Installation
DANGER: To prevent the possibility of explosion or fire, do not use electrical
or battery operated power tools in or near the Hazardous Area! Only use
pneumatic or hand tools.
The pedestal is available in 3 heights:
l48 inch
l40 inch (Standard) ADA (Americans with Disabilities Act) compliant for off island installations
l32 inch ADA compliant for on island installations
3.1 Pedestal and Enclosure Installation
INFORMATION: For your reference, the illustration below shows the dimensions and hole
placement of the pedestal's base plate, top plate, conduit knockout plate and the outer
dimensions of the pedestal.
1. Square the base-plate where it is to be installed.
Doc. No.: M1010 Rev.: 10
Page 18 of 98

2. Mark the four (4) most applicable locations for the anchor bolts. There are eight (8) bolt holes (see the
illustrations above).
3. Drill the holes.
4. Anchor the pedestal with 3/8” anchor bolts.
IMPORTANT: Use a type of anchor bolt that is appropriate for the material in which you will
anchor the pedestal (e.g. concrete).
5. Use the provided hardware to attach the enclosure to the pedestal. Align the provided gasket with the
mounting holes of the pedestal top plate. Carefully position the enclosure in place so that the open
installation holes are aligned with the installation holes of the pedestal (see the illustration above). Put
the four (4) bolts through the holes and tighten them using the provided washers and nuts.
Doc. No.: M1010 Rev.: 10
Page 19 of 98

3.2 Aluminum Enclosure Conduit Knockouts
To remove the Knockout plugs in the bottom of the enclosure, hold a center-punch in the green circled areas
shown in the illustrations above, and hit the punch with a hammer. The areas to hit are perpendicular to the
welds that hold the knockouts. Deburr the hole with a file and make sure there are no shavings inside the
enclosure.
IMPORTANT: All unused, open knockouts MUST be sealed!
3.3 Flex Conduit Installation
1. Remove the applicable knockouts from the base of the PV200 enclosure.
2. Install Flex Conduit from the rigid conduit to the knockouts in the pedestal conduit plate.
IMPORTANT: All unused knockout holes must be sealed to meet NEC compliance codes.
3.4 Power and Communication Wiring
1. Pull three (3) #14 AWG wires (green, black and white) from a dedicated circuit breaker to supply power
to the terminal.
NOTE: Petro-Net communication to other terminals should also be pulled in this conduit.
2. Connect power and neutral wires to the power connection terminal block marked “LINE” (or “L”) and
“NEUTRAL” (or “N”). Connect the ground to the wire to the terminal labeled “GROUND” (or “GND”).
CAUTION: Petro-Net communication wires can be in the same conduit with
the power wiring only when the communication wires have the same voltage-
insulation rating as the power wires.
3. Connect the Petro-Net wires to the communication terminal block.
Doc. No.: M1010 Rev.: 10
Page 20 of 98
Table of contents
Other OPW Control System manuals
Popular Control System manuals by other brands
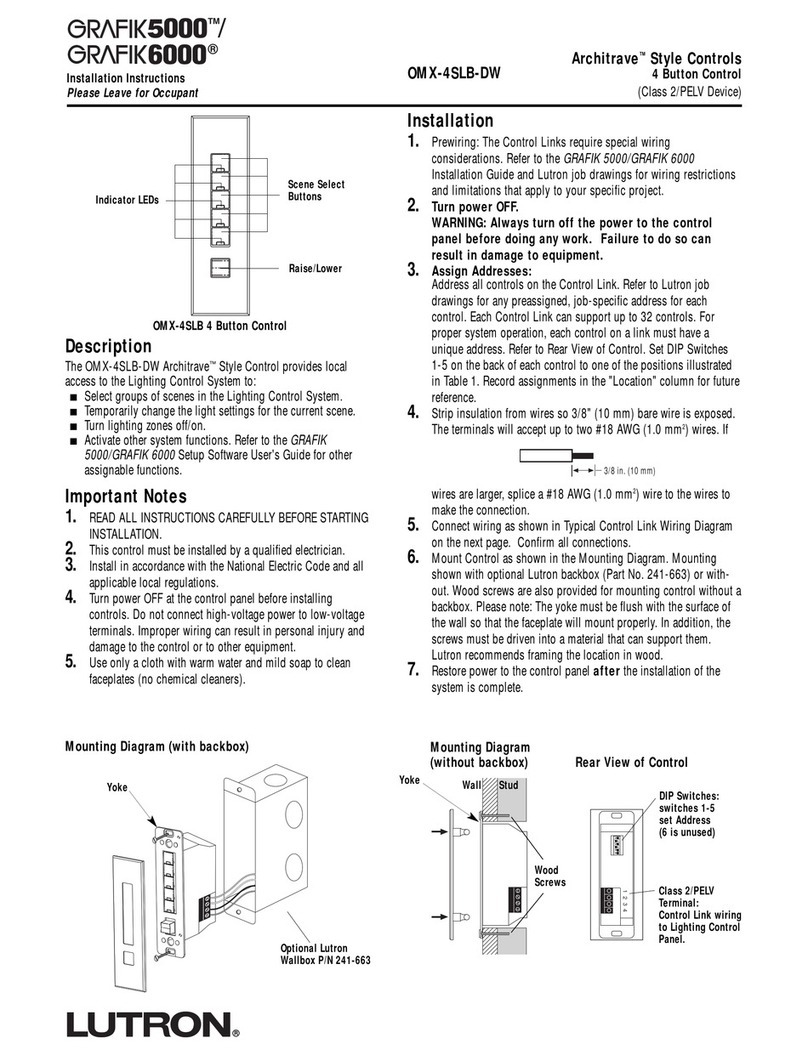
Lutron Electronics
Lutron Electronics Architrave GRAFIK5000 installation instructions
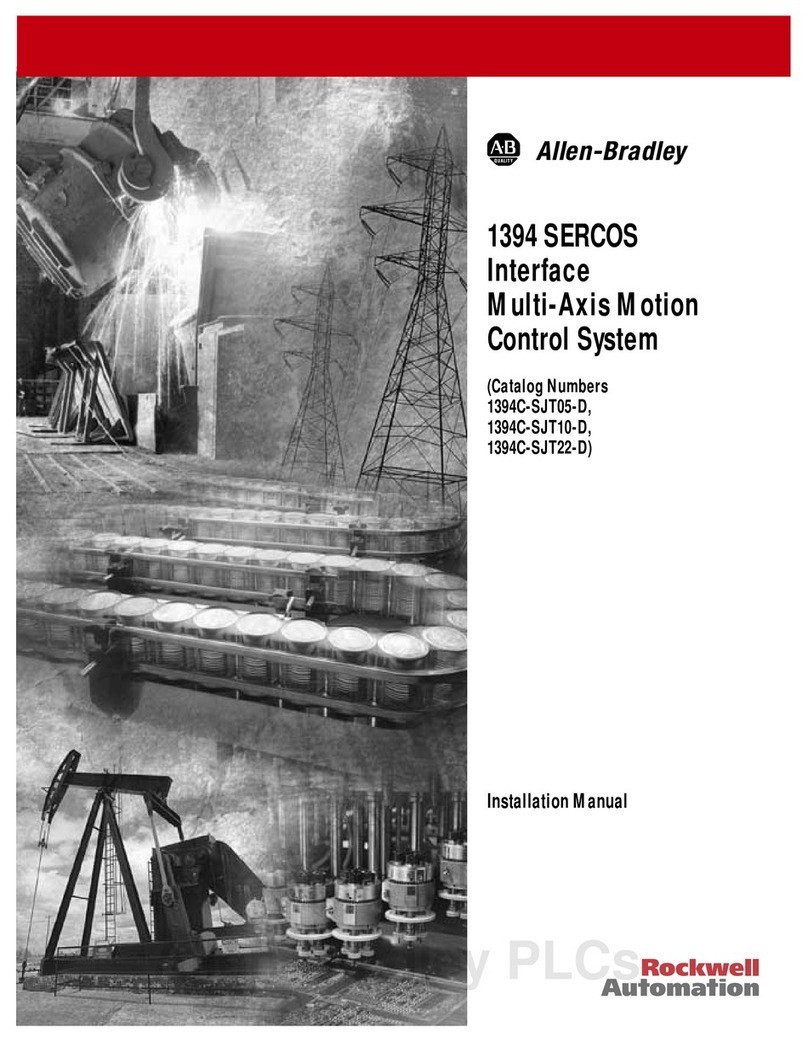
Allen-Bradley
Allen-Bradley 1394 SERCOS installation manual
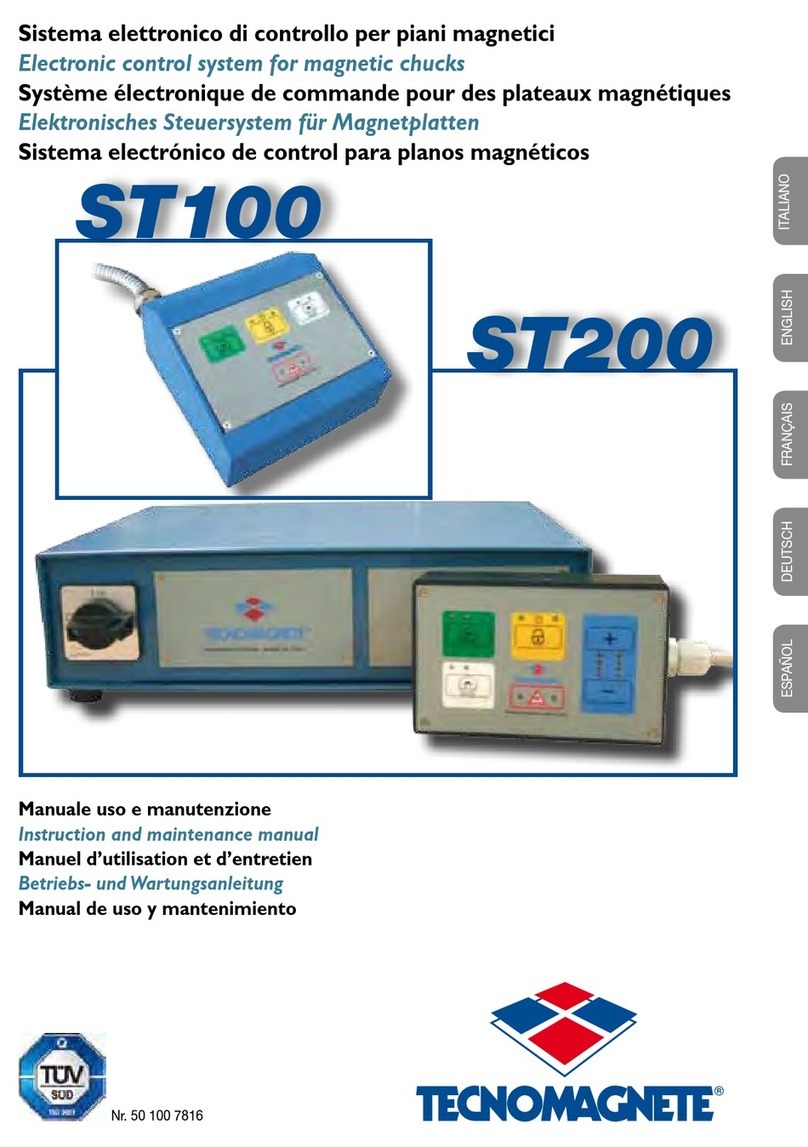
TECNOMAGNETE
TECNOMAGNETE ST100 Series Instruction and maintenance manual
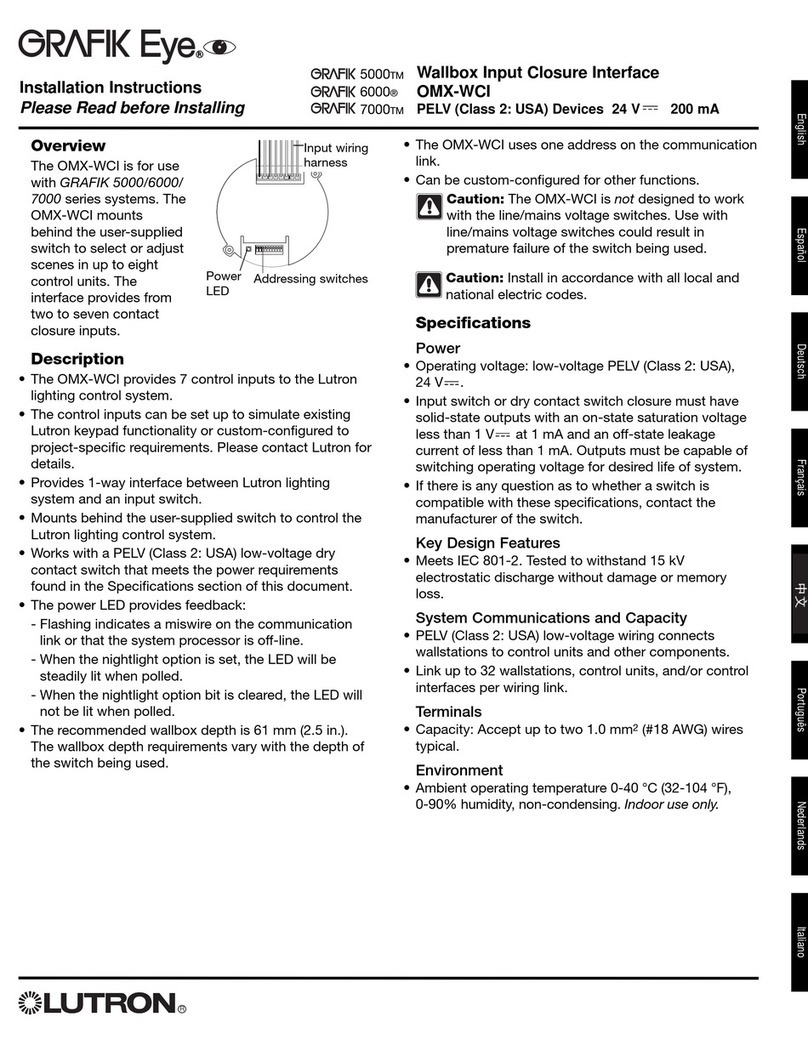
Lutron Electronics
Lutron Electronics Grafik Eye installation instructions
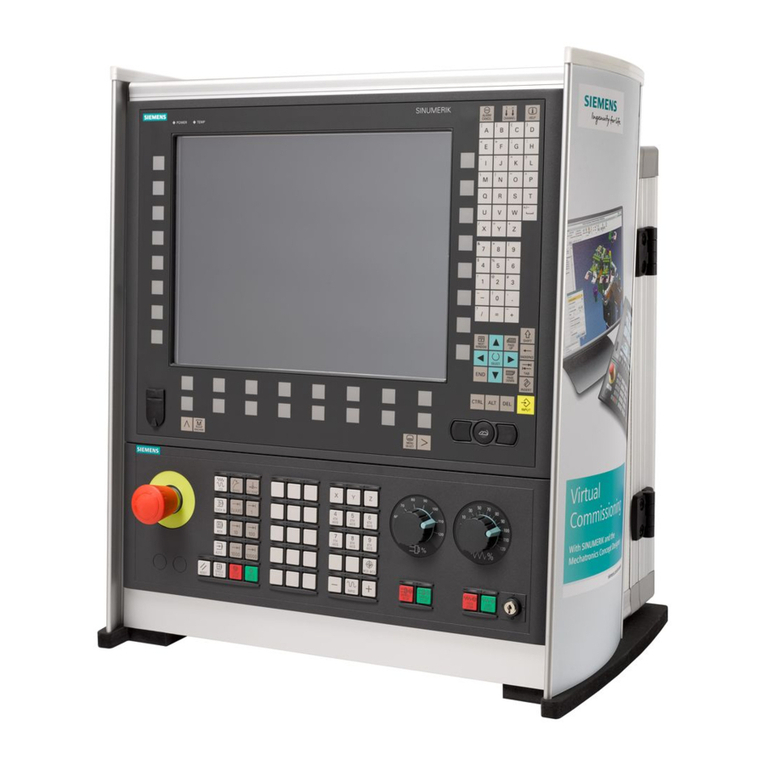
Siemens
Siemens SINUMERIK 840D sl Commissioning manual
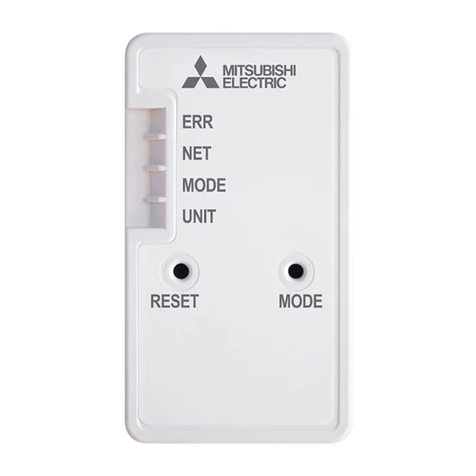
Mitsubishi Electric
Mitsubishi Electric MAC-588IF-E installation guide