Paccar Winch Gearmatic GH30B Installation and user guide

1
WINCH DIVISION
P.O. BOX 547 BROKEN ARROW, OK U.S.A. 74013
PHONE (918) 251-8511 FAX (918) 259-1575
www.paccarwinch.com
LIT2363_R6_2-2012
Printed in U.S.A. © PACCAR Inc
All Rights Reserved
GH30B
with FreeFall Attachment
(Liebherr Units Only)
SERVICE AND MAINTENANCE MANUAL
REFER TO MATERIAL LIST LIT-2360
FOR SPECIFIC PARTS IDENTIFICATION

2
TABLE OF CONTENTS
INTRODUCTION
The following service instructions have been prepared to provide assembly, disassembly, and maintenance
information for the Gearmatic Model GH30B with FreeFall option. It is suggested that before doing any work on these
units, all assembly and disassembly instructions should be read an understood.
Some illustrations in this manual may show details or attachments that are different from your hoist. Also,
some components have been removed for illustrative purposes.
Continuing product improvement may cause changes in your hoist, which are not included in this manual.
Whenever a question arises regarding your Gearmatic hoist or this manual, please contact Gearmatic Product Sup-
port Department for the latest available information.
Telephone- 1-918-251-8511
08:00-16:30 Central Time Zone, Monday thru Friday
FAX- 1-918-259-1575
www.paccarwinch.com
GENERAL DESCRIPTION ........................................................3
SAFETY RECOMMENDATIONS .............................................4
GENERAL INSTALLATION .....................................................5
WIRE ROPE INSTALLATION ..................................................6
HOIST OPERATION ................................................................7
PREVENTATIVE MAINTENANCE .......................................8-9
OIL REQUIREMENTS ......................................................10-11
HOIST DISASSEMBLY ....................................................12-14
FREEFALL ATTACHMENT SERVICE .............................15-17
BRAKE CYLINDER SERVICE .........................................18-19
CABLE DRUM SERVICE ....................................................20
PRIMARY PLANET CARRIER SERVICE .......................21-22
OUTPUT PLANET CARRIER SERVICE .............................23
HOIST ASSEMBLY ................................................................24
CROSS-SECTION ..............................................................25-26
COMPRESSIONTOOLINGDIAGRAM .....................................28
METRIC CONVERSION CHART ...........................................30

3
EXPLANATION OF MODEL NUMBER
GH30 B - FF - SPL - 40 000 - 41
GH30 - DESIGNATES GEARMATIC 30 SERIES HOIST FAMILY
B - EVOLUTIONARY DESIGNATION
FF - FULL RELEASE FREE FALL EQUIPPED
SPL - SPECIAL ORDER DESIGNATION
40 - TOTAL GEAR REDUCTION (40:1)
000 - MOTOR CODE, 000 WITHOUT MOTOR, ISO = MOTOR MOUNT & SHAFT TO ISO
SPECIFICATIONS
41 - DRUM OPTION DESCRIPTION
The primary sun gear is directly coupled to the hydraulic
motor by solid coupler in the static brake assembly. As the
motor turns in the hoisting direction the planetary assem-
blies reduce the input speed of the motor and rotate the
final planet carrier and winch drum.
The Free-Fall assembly contains the final drive planetary
reduction for the winch. The final planet carrier is attached
to the cable drum by splines and the internal ring gear is
mounted on ball bearings. The internal ring gear is kept
from rotating by a multi-disc brake. The brake is applied
by springs that force the piston against the pressure plate
which prevents the ring gear from rotating.
When hydraulic oil is introduced into the annular area
formed between the piston and the freefall housing, the
effective spring load is reduced as the hydraulic pressure
increases. When a load is suspended on the winch cable
and hydraulic pressure is applied to move the piston to the
end of its travel, or the full release position, the internal
ring gear will rotate and allow the load to drop freely to the
ground.
The free fall circuit must be activated by a detent switch.
Release of the freefall brake with use of a metered and
controlled hydraulic signal must be done by means of a
detent type control. Using the freefall brake to stop a load
during lowering once the freefall brake has been pressur-
ized may result in damage to hoist and wire rope.
Free Fall Brake
Release Port

4
GENERAL SAFETY RECOMMENDATIONS
Safety for operators and ground personnel is of prime concern. Always take the necessary precautions to
ensure safety to others as well as yourself. To ensure safety, the prime mover and hoist must be operated with care
and concern for the equipment and a thorough knowledge of the machine’s performance capabilities. The following
recommendations are offered as a general safety guide. Local rules and regulations will also apply.
1. Be certain equipment (boom, sheave blocks, etc.) is
either lowered to the ground or blocked securely be-
fore servicing, adjusting, or repairing hoist.
2. Be sure personnel are clear of work area BEFORE
operating hoist.
3. Read all warning and caution tags provided for safe
operation and service of the hoist and become fa-
miliar with the operation and function of all controls
before operating the hoist.
4. Inspect rigging and hoist at the beginning of each
work shift. Defects should be corrected immediately.
Do not operate a hoist with defects.
5. Keep equipment in good operating condition. Per-
form scheduled servicing and adjustments listed in
the “Preventive Maintenance” section of this manu-
al.
6. An equipment warm-up procedure is recommended
for all start-ups and essential at ambient tempera-
tures below +40°F (+4°C).
7. Do not exceed the maximum pressure (PSI, kPa)
or flow (GPM, lpm) stated in the hoist specifications
found in the specific sales brochure.
8. Operate hoist line speeds to match job conditions.
9. Protective gloves should be used when handling wire
rope.
10. Never attempt to handle wire rope when the hook
end is not free. Keep all parts of body and clothing
clear of cable rollers, cable entry area of fairleads,
sheaves and hoist drum.
11. When winding wire rope on the hoist drum, never at-
tempt to maintain tension by allowing wire rope to slip
through hands. Always use “Hand-Over-Hand” tech-
nique.
12. Never use wire rope with broken strands. Replace
wire rope that is damaged. Refer to wire rope sup-
plier manual.
13. Do not weld on any part of the hoist without approval
from PACCAR Winch Engineering.
14. Use recommended hydraulic oil and gear lubricant.
15. Keep hydraulic system clean and free from contami-
nation at all times.
16. Use correct anchor for wire rope and pocket in
drum.
17. Do not use knots to secure or attach wire rope.
18. The Gearmatic designed wire rope anchors are not
intended to support the rated load. ALWAYS main-
tain a minimum of five (5) wraps of wire rope on the
drum. It is recommended that the last five (5) wraps
of wire rope be painted bright red to serve as a visual
reminder.
19. Never attempt to clean, oil or perform any mainte-
nance on a machine with the engine running, unless
instructed to do so in this manual.
20. Never operate hoist controls unless you are properly
positioned at the operators station and you are sure
personnel are clear of the work area.
21. Assure that personnel who are responsible for hand
signals are clearly visible and that the signals to be
used are thoroughly understood by everyone.
22. Ground personnel should stay in view of the opera-
tor and clear of the hoist drum. Do not allow ground
personnel near wire rope under tension. A safe dis-
tance of 1½ times the working length of the wire rope
should be maintained.
23. Install guarding to prevent personnel from getting
any part of body or clothing caught at a point where
the cable is wrapped onto the drum or drawn through
guide rollers or potential “pinch points”.
24. Install switches or valves that will shut off power to
the hoist, in locations where they can be reached
by anyone entangled in the wire rope before being
drawn into the hoist or any “pinch point”.
25. “Deadman” controls, which automatically shut off
power to the hoist whenever the operator leaves his
station or releases the hoist control lever, should be
installed whenever practical.
26. Never allow anyone to position any part of body un-
der a suspended load.
27. Avoid sudden “shock” loads or attempting to “jerk” a
load free. This type of operation may cause heavy
loads, in excess of rated capacity, which may result
in failure of wire rope, hoist or boom structure.
28. Whenever possible, install the hoist in a location that
is not immediately adjacent to a “normal” operator’s
station.
29. All hoist controls shall be located within easy reach of
the operator. The controls shall be installed in such
a location that the operator is removed from the elec-
trical path to ground if the load, rigging, or wire rope
come in contact with or within proximity to an electri-
cally energized conductor.

5
GENERAL INSTALLATION
1. The hoist must be mounted with the centerline of the
drum in a horizontal position.
2. When mounting the hoist, use SAE grade 8 (ISO class
10.9) capscrews or bolts and nuts using both mount-
ing holes in each end plate. Use narrow, hardened
washers under the bolt heads and nuts.
3. It is important that the hoist be mounted on a surface
that will not flex when the hoist is in use, since this
could bind the working parts of the hoist. Also, be sure
the hoist is mounted on a flat surface. If necessary,
use shim stock to insure proper mounting. The mount-
ing surface must be flat within 0.020 inches (.5 mm).
4. Hydraulic lines and components that operate the hoist
should be of sufficient size to assure minimum back
pressure at the hoist motor ports. To insure adequate
static brake load holding ability, back pressure on the
hoist brake release port should not exceed 100 psi
(690 kPa).
5. Make certain that the hoist drum is centered behind
the first sheave and the fleet angle does not exceed
1½ degrees.
The hoist should also be mounted perpendicular to an
imaginary line from the center of the drum to the first
sheave to ensure even spooling.
6. The hoist directional control valve must have a valve
without detents and with a spring centered spool such
that the valve returns to the centered position when-
ever the handle is released.
DO NOT use a control valve with any detents or latch-
ing mechanism that would hold the control valve in an
actuated or running position when the operator releas-
es the control handle. Use of the wrong type of control
valve could lead to unintentional operation of the hoist,
which could result in property damage, personal injury
or death.
DO NOT weld hoist to mounting surface. Welding may
not provide adequate structural support for winch loads.
This may cause loss of load control, which could result
in property damage, injury or death. Welding may also
damage bearings and seals, resulting in premature fail-
ure.
CAUTION
WARNING
! !
CAUTION
WARNING
! !

6
THE CABLE ANCHORS ALONE ON HOISTS ARE NOT INTENDED TO HOLD RATED LOADS.
Hoist loads applied directly to the wire rope anchor may cause the wire rope to pull free and result in the sudden
loss of load control and cause property damage, personal injury or death. A minimum of 5 wraps of wire rope must
be left on the drum barrel to achieve rated load.
CAUTION
WARNING
! !
The wedge and anchor pocket must be clean and dry. The
end of the wire rope being anchored to the drum must be
clean and dry and not frayed. Anything on the end of the
wire rope to keep it from fraying (i.e. tape or wire) must not
be in contact with the wedge when the installation is com-
plete. Consult the wire rope manufacturer on the proper
treatment of the dead end of the wire rope.
Some wire rope manufacturers recommend when using
rotation resistant wire rope, that the rope end be seized,
welded or brazed before inserting the wire rope into the
wedge socket to prevent core slippage or loss of rope lay.
WIRE ROPE INSTALLATION
Winches built in August 2010 and later will be supplied
with a cable drum that has two wire rope anchor pockets to
enable the winch to be configured for underwound (Model
code U) applications. Make certain to install the wire rope
in the anchor pocket that is correct for your application.
Take the free end of the wire rope and insert it through
the small opening on the cable drum flange. Loop the
wire rope and push the free end about 3/4 of the way back
through the pocket. Install the wedge as shown below,
then pull the slack out of the wire rope. The “dead” end
of the rope needs to extend slightly beyond the end of the
wedge as shown.
Using a hammer and brass drift, drive the wedge as deep
into the pocket as possible to ensure it is fully seated and
no further movement is detected. Applying a load on the
wire rope will also help seat the wedge in the pocket.
It is important that the wire rope have the proper tension-
ing when it is installed on the drum. When the wire rope
is first installed, you should operate the hoist, with light
to moderate loads, with reeving that let’s you place these
loads on the hook block and the drum with all the rope off
the drum except for the last five wraps.
WIRE ROPE INSTALLATION
A
B
CABLE POCKET COVER
CABLE WEDGE
CABLE DRUM
CABLE
Attempting to use the incorrect wire rope anchor pocket
may cause permanent damage to wire rope, cable drum
and wire rope slipping free of wedge. These conditions
may result in loss of load control, property damage, in-
jury or death.
CABLE WEDGE PLACEMENT
A) Wire rope anchor pocket for standard rotation. Drum
rotates counter clockwise (CCW) to hoist a load when
viewed from the motor end.
B) Wire rope anchor pocket for underwound rotation. U
is the last character in the model code. Drum rotates
clockwise (CW) to hoist a load when viewed from the
motor end.

7
HOIST OPERATION
The following warnings and instructions are basic to safe hoist operation. Please read them carefully and follow them
each time your hoist is operated. These instructions are provided in addition to any information furnished by the Original
Equipment Manufacturer. Equipment operators should be completely familiar with the overall operation of the tractor
on which the hoist is mounted. If you have any questions concerning the safe operation of this hoist or the equipment
it is mounted on, contact the equipment manufacturer that installed the hoist, or the PACCAR Winch Division Product
Support Department at 1-918-251-8511, Monday through Friday, 0800 to 1630 hours CTZ, by fax at 1-918- 259-1575,
or via the internet at www.paccarwinch.com.
Warm-up Procedures
A warm-up procedure is recommended at each start-up
and is essential at ambient temperatures below +40°F
(4°C).
The engine should be run at its lowest recommended RPM
with the hydraulic hoist control valve in neutral allowing
sufficient time to warm up the system. The hoist should
then be operated at low speeds, raise and lower with no
load on the hook, several times to prime all lines with warm
hydraulic oil, and to circulate gear lubricant through the
planetary gear sets.
After the boom is properly positioned, we recommend
the operator slowly pay-out, then haul-in a short length of
wire rope. The hoist should perform these operations in a
smooth and controlled manner. If the hoist does not oper-
ate smoothly or makes any unusual sounds, the source of
the problem should be identified and corrected before any
attempt is made to lift a load.
Slowly pay-out wire rope from the hoist drum until it reach-
es the load. Securely fasten the hoist wire rope to the load
and be sure all ground personnel are a safe distance from
the load. Slowly lift the load a short distance and stop. A
small amount of “bounce” may be observed, depending on
the weight of the load, size and type of wire rope, reaving
and the amount of boom extension. Allow the load to sta-
bilize and then watch for any sign of downward movement
or cable drum rotation. The hoist static brake should hold
the load in place without allowing any downward move-
ment at all. If the load creeps down, it should be lowered
to the ground immediately and the source of the problem
identified and corrected.
If the hoist is holding the load securely, proceed with nor-
mal operations in accordance with the equipment manu-
facturer’s operating procedures and load charts.
Care must be taken to pay-out wire rope as the boom
is lowered. Failure to pay-out sufficient wire rope could
result in a “two-blocking” condition that could result in
damagetoand/orfailureofthehoist,wirerope,sheaves
and/or boom.
CAUTION
Ground personnel must stay in view of the operator and
clear of the load and hoist drum at all times. Do not
allow personnel near the hoist line under tension. Do
not allow personnel near the hoist drum while the hoist
is in operation. Do not allow personnel to be in line
with the load. Do not allow personnel to stand under a
suspended load. A safe distance of at least 1½ times
the working length of the cable should be maintained by
ground personnel. Abroken cable and/or lost load may
cause property damage, personal injury, or death
Failure to properly warm up the hoist, particularly un-
der low ambient temperature conditions, may result in
temporary brake slippage due to high back pressures
attempting to release the brake, which could result in
property damage, severe personal injury, or death.

8
Aregular programofpreventivemaintenance foryourplan-
etary hoist is required to minimize the need for emergency
servicing and promote safe, reliable hoist operation.
The user of Gearmatic hoist products is responsible for
hoist inspection, testing, operator training and mainte-
nance noted below with frequency dependent upon the
severity of the hoist duty cycle and the thoroughness of
the preventive maintenance program. Field experience,
supported by engineering tests, indicate the three service
procedures listed below are the most critical to safe, reli-
able hoist operation and MUST be observed.
• Regular Gear Oil Changes
• Use of Proper Gear Oil – recommended type for pre-
vailing ambient temperatures and additives.
• Periodic Disassembly and Inspection of All Wear Com-
ponents.
Equipment inspection records as well as records of pre-
ventive maintenance, repairs and modifications must be
available for a minimum of five (5) years. These records
should include but not limited to, hoist model and serial
number, name and employer of repair technician, date and
description of work performed.
Pre-use Inspection (each shift the hoist is used): This in-
spection must be performed prior to placing the hoist into
service and then as necessary during the day for extended
operation.
1. Check for external oil leaks and repair as necessary.
This is extremely important due to the accelerated
wear that can be caused by insufficient lubricating
oil in the hoist. If a leak is noticed, the gear oil level
must be checked as described in 500-hour inspection.
Lubricant level must be visible in the lower half of the
sight glass in the freefall housing and primary input
oil level plug. Use only recommended lubricants. See
Recommended Lubricants chart in this manual.
2. Check hydraulic plumbing for damage, such as chafed
or deteriorating hoses and repair as necessary.
3. Visually inspect for loose or missing bolts, pins, retain-
ers or cotter pins and replace or tighten as necessary.
4. The gear oil should be changed after the first 250
hours of operation. The regular gear oil change inter-
vals may be adopted after the first oil change.
5. Inspect the wire rope, rigging and all sheaves accord-
ing to the wire rope and rigging manufacturer’s recom-
mendations.
6. A warm-up procedure is recommended at each start-
up and is mandatory at ambient temperatures below
+40°F (4°C). The engine should be run at its lowest
RPM with the hydraulic hoist control in neutral allow-
ing sufficient time to warm up the system. The hoist
should then be operated at low speeds, hoisting and
lowering with no load, several times to prime all hy-
draulic lines with warm oil and to circulate lubricant
through the planetary gear sets.
500-Hour Inspection (every 3 months) or monthly in Se-
vere Duty Applications or prior to placing the machine in
service if it has not been used for three months or more.
1. Perform the Pre-use Inspection. Check oil level in pri-
mary housing and freefall housing.
2. Inspect all hoist fasteners for tightness and corrosion.
Replace all corroded fasteners and tighten per the
torque specifications on page 11.
3. The hydraulic system filters should be changed after
the first 250 hours of operation then every 2000 hours,
at least once a year, and in accordance with the tractor
manufacturer’s recommendations.
4. Every 1000 hours, take a sample of the gear oil from
the hoist following the oil sampling procedure on page
11. The oil sample must be taken prior to changing
the gear oil. Analyze the sample for wear metals, vis-
cosity, signs of overheating, oxidation, water and other
contaminants. If the oil sample contains an unusual
amount of metallic particles, the hoist should be re-
moved from service and undergo a tear-down inspec-
tion.
Every 2000-Hours or at least Once Per Year
or semi-annually in Severe Duty Applications.
1. Perform the Pre-Use and 500-hour Inspections.
2. Change the lubricating oil in the hoist after an oil sam-
ple is taken.
Failure to properly warm up the hoist, particularly un-
der low ambient temperature conditions, may result in
temporary brake slippage due to high back pressures
attempting to release the brake, which could result in
property damage, severe personal injury or death.
CAUTION
WARNING
! !
PREVENTATIVE MAINTENANCE

9
The gear oil should be changed whenever the ambient
temperature changes significantly and an oil from a dif-
ferent viscosity range would be more appropriate. Our
tests indicate that excessively heavy or thick gear oil may
contribute to intermittent brake slippage. Make certain the
gear oil viscosity used in your hoist is correct for your pre-
vailing ambient temperature.
NOTE: If the oil sampling/analysis has not been performed
as required, tear-down inspections will be required. Refer
to Hoist Disassembly section of this manual.
The GH30B-FF hoist has an oil seal which separates the
primary housing gear oil from the free-fall housing gear oil.
The free-fall end is filled to the center of the sight gauge
shown on the drawing. The motor end is filled until oil
drains out of the level plug shown on the drawing. Wire
rope must be spooled off the drum to allow access to the
drum drain plug. Rotate the drum until the drain plug is at
the lowest point.
To change the gear oil, remove the drain plugs shown on
the drawings below from each end of the hoist and the
drum and collect a sample from each housing for oil analy-
sis. Removing the vent plugs will speed the oil drain. When
the oil has drained, install the drain plugs.
Refill the hoist with the recommended gear oil and install
the fill plug.
3. The vent plugs are located in the free fall housing cov-
er and motor adapter. It is important to keep the vent
plugscleanand unobstructed.Wheneverthe gearoilis
changed, the vent plugs should be removed, cleaned
in solvent and reinstalled. Do not paint over the vent
plugs or replace with a solid plug or grease fitting.
Failure to use the proper type and viscosity gear oil may
result in loss of load control, property damage, injury or
death.
OIL FILL
VENT
FREE FALL
OIL LEVEL
SIGHT GAUGE
OIL DRAIN
FREE FALL END
E PORT OIL DRAIN
PRIMARY HOUSING
OIL LEVEL
VENT
OIL FILL
BRAKE RELEASE
PORT
MOTOR END
FREE FALL
BRAKE RELEASE PORT
DRUM OIL
DRAIN PLUG
OIL DRAIN
PRIMARY HOUSING
OIL LEVEL
VENT
OIL FILL
BRAKE RELEASE
PORT
MOTOR END
February 2012
Serial Number 1200211 and Up
2008 till February 2012

10
Recommended Planetary Gear Oil
Failure to use the proper type and viscosity of planetary gear oil may contribute to intermittent brake slippage which
could result in property damage, severe personal injury or death. Some gear lubricants contain large amounts of EP
(extreme pressure) and anti-friction additives which may contribute to brake slippage and damage to brake friction
discs or seals. Oil viscosity with regard to ambient temperature is also critical to reliable brake operation. Our tests
indicate that excessively heavy or thick gear oil may contribute to intermittent brake slippage. Make certain that the
gear oil viscosity used in your hoist is correct for your prevailing ambient temperature.
RECOMMENDED PLANETARY GEAR OIL
PREVAILING AMBIENT TEMPERATURE
oF -40 -30 -20 -10 0 10 20 30 40 50 60 70 80 90 100 110 120 130 oF
AGMA 5 EP, ISO VG 220
AGMA 4 EP, ISO VG 150
MOBILGEAR SHC 150
SYNTHETIC OR EQUIVALENT
oC -40 -30 -20 -10 0 10 20 30 40 50 oC
NOTE: SHADED TEMPERATURE RANGE IN THE CHART ABOVE NOT RECOMMENDED FOR SEVERE APPLICATIONS SUCH AS: OFFSHORE
CRANES, SUSTAINED FAST DUTY CYCLES OR FREQUENT LIFTING.
i
TexacoShell
Meropa 150
Meropa 220
Omala 150
Omala 220
Chevron
Gear Compounds EP 150
Gear Compounds EP 220
RECOMMENDED PLANETARY GEAR OIL
PREVAILING AMBIENT TEMPERATURE
oF -40 -30 -20 -10 0 10 20 30 40 50 60 70 80 90 100 110 120 130 oF
AGMA 5 EP, ISO VG 220
AGMA 4 EP, ISO VG 150
SYNTHETIC OR EQUIVALENT
oC -40 -30 -20 -10 0 10 20 30 40 50 oC
NOTE: SHADED TEMPERATURE RANGE IN THE CHART ABOVE NOT RECOMMENDED FOR SEVERE APPLICATIONS SUCH AS: OFFSHORE
CRANES, SUSTAINED FAST DUTY CYCLES OR FREQUENT LIFTING.
i
TexacoShell
Meropa 150
Meropa 220
Omala 150
Omala 220
Chevron
Gear Compounds EP 150
Gear Compounds EP 220
TexacoMobil Shell
Meropa 150
Meropa 220
Omala 150
Omala 220
Chevron
Gear Compounds EP 150
Gear Compounds EP 220
MOBILGEAR 600 XP 220 OR EQUIVALENT
MOBILGEAR 600 XP 150 OR EQUIVALENT
Mobilgear 600 XP 150
Mobilgear 600 XP 220
Planetary hoists are factory filled with Mobilgear 600 XP 150, or equivalent. Consult your oil supplier for other equivalent
oils if required.
Tear-down Inspection
Once every 10,000 hours or 6 years, the hoist should be
completely disassembled and undergo a complete inspec-
tion. Also, if a hoist has an unknown history of repair and/
or maintenance, the hoist should undergo a tear-down in-
spection prior to being placed into service.
A tear-down inspection of the hoist should include the
complete disassembly, cleaning, inspection and replace-
ment of all worn, cracked, corroded or distorted parts such
as pins, bearings, shafts and brake components. All seals
and o-rings should be replaced during a tear-down inspec-
tion. Always use new Spirol pins in the planet gear shafts.
Any deficiency must be corrected
Immediately.
Before placing the hoist back in service, the rebuilt hoist
must be pull tested to the rated load of the hoist with a
dynamometer or equivalent measuring device. The hoist
should be dynamically tested by rotating the drum several
times, in both raising and lowering directions, while un-
der load of at least 30% of the hoist rated lifting capacity.
Check for smooth, quiet operation during this procedure.
OIL CAPACITY FOR THE GH30B FREE FALL
EQUIPPED WITH A -04 AND 41 DRUM IS APPROXIMATELY
19 PINTS (9 LITER) FREE FALL END
3 PINTS (1.4 LITER ) MOTOR END

11
OIL SAMPLING AND ANALYSIS
Proper oil sampling and analysis of the sample, is a vital
part of a comprehensive preventive maintenance program.
Information obtained from the oil analysis is best utilized in
conjunction with a regular program of preventive mainte-
nance. The early warning of abnormal wear provided by
an analysis program allows the user to substitute preven-
tive maintenance for a far more costly and dangerous fail-
ure that may lead to loss of load control that could result in
property damage, personal injury or death. Early detection
of accelerated component wear allows the scheduling of
corrective maintenance and can reduce in-operation fail-
ures and costly down time.
Taking a Valid Oil Sample
Since the GH30B-FF hoist has an oil seal which separates
the free-fall end oil from the motor end oil, a sample from
each end must be analyzed at each maintenance interval.
Prepare the hoist by cleaning the drain area and drain ex-
tension tube in order to obtain an uncontaminated sample.
Operate the hoist in both directions for one to two minutes
and then take the oil sample from the drain port as soon as
possible. Do not take the sample from the first oil out of the
drain port. Take a sample from the mid-stream flow of the
oil to obtain an accurate representation of the oil condition.
After taking an oil sample, refill hoist with recommended
lubricant.
Analysis
General Guide Lines
(After approximately 250 hours of operation)
Note: The first oil change usually contains more “wear
metals”. Following the initial break-in period, the wear
metal levels should stabilize at a lower number.
Iron Contaminates
100 to 400 ppm Normal
400 to 700 ppm Caution – Abnormal Sample (monitor
more frequently), tear-down inspection
may be required.
701 ppm & up Unacceptable –Abnormal Sample (tear
down inspection required)
In all contaminate monitoring, equally important as the
level of contamination, is the change in the amount of con-
tamination compared to previous samples.
Moisture contamination will lead to the formation of acids
that damage all internal components. Silica found in the oil
typically indicates “dirt” and contaminated lubricant supply
or poor maintenance practices.
Hot oil may cause personal injury and/or burns to un-
protected skin. Make certain the oil has cooled to a safe
temperature (less than 110°F or 43°C) before taking an
oil sample, changing oil or servicing the hoist.
RECOMMENDED BOLT TORQUE
The general purpose torque shown in the chart applies to SAE Grade 5 & Grade 8 bolts, studs and standard steel full, thick and
high nuts.
Higher or lower torques for special applications will be specified such as the use of spanner nuts, nuts on shaft ends, jam nuts and
where distortion of parts or gaskets is critical.
Lubricated torque values based on use of SAE 30 engine oil applied to threads and face of bolt or nut.
Dr
y
Lubed Dr
y
Lubed Dr
y
Lubed Dr
y
Lubed
Torque
(
LB-FT
)
Grade 5 Grade 8
1/4 20
28
5/16
3/8
18
24
16
24
7/16
1/2
9/16
5/8
86129
17 13 24 18
45 35
70 50
2331
50 35
80
110 80 150 110
1105575
150 115 210 160
14
20
13
20
12
18
11
18
265 200
Torque
(
LB-FT
)
Grade 5 Grade 8
380 280
7/8 9
14 420 325 600 450
3/4 10
16
680
1 1/8 7
12 790 590 1290 970
18
14 640
7
12 1120 835
910485
1460
1820 1360
1 3/8 6
12 1460 1095 2385 1790
1 1/4
3160 2370
RECOMMENDED FASTENER TORQUE
Bolt Dia.
Inches Thds Per
Inch Bolt Dia.
Inches Thds Per
Inch
1 1/2 6
12 1940
LB-FT X 1.3558 = N-M X 0.7376 = LB-FT
LB-FT X 0.1383 = Kg-m X 7.233 = LB-FT

12
The GH30B-FF weighs approximately 1650 lbs (750 kg).
Make certain lifting equipment has adequate capacity. Using
undersized or poorly maintained lifting equipment may result
in a dropped load, property damage injury or death.
CAUTION
1. Remove the wire rope from the hoist. Drain the gear
oil by removing the oil fill plugs and the drain plugs
on both ends of the hoist and cable drum. Remove
the hydraulic hoses and mounting bolts, and clean the
outside surface of the hoist in preparation for disas-
sembly. To ease aligning parts on reassembly, mark
the winch bolted connections with a paint pen or scribe
line.
2. Stand the hoist on the free-fall end. Tag and remove
the hoses that connect the motor assembly to the
brake release port on the hoist.
3. Remove the four capscrews and lockwashers secur-
ing the motor and lift the motor off the hoist. Remove
and discard the o-ring installed on the motor pilot.
4. Remove the motor adapter (31) by removing the four
capscrews (35) and lockwashers (16) securing it to the
winch. Remove brake hub (39) and bearing (20).
5. Note: The brake parts group will come out of the
winch with the primary housing cover because
the parts are captured by the retaining ring (209).
Remove the spring tension from the primary housing
cover (201) by loosening the capscrews (17) one turn
each alternating across the housing. Remove the pri-
mary housing cover (201) turning in a slight rotary mo-
tion when lifting out of the housing.
HOIST DISASSEMBLY
DRAIN PLUGS
35
16
31
39
20
17
201
NOT
E

13
6. Remove the three divider plates (211), and one brake
plate (212).
7. Remove the primary sun gear (7), thrust washer (48),
primary planet carrier assembly (300), primary ring
gear (6), and pilot bearing (12).
212
211
300 6
12
7
48
*
8. Mark the tie plates to the side of the hoist to ease re-
assembly. Remove the tie-plate capscrews and lock-
washers and remove the tie-plates (21). Remove the
sun gear shaft (5). Remove the primary housing (1)
using eye-bolts and lifting straight up off of the drum.
9. Use lifting clamps to lift the drum assembly straight up
and remove it from the freefall assembly.
5
1
21
*NOTE: GH30B-FF winches built prior to serial
number 0801914 do not have thrust washer (48.)
If early style planet carrier (300) is replaced,
thrust washer (48) must be ordered and installed
with new planet carrier

14
10. Stand the freefall end of the hoist with the drum side
down and place blocks under the end plate to balance
the assembly.
11. Remove capscrews (35) and lockwashers (16) which
secure the freefall assembly to the end plate (3). Re-
move two capscrews (806) in the bearing support, and
install ½” -13 thread eyebolts in their place to lift the
freefall assembly from the support end plate (3).
See Warning on page 15
806
806
3
16
35
802
12. Remove the thrust button (27) and the output planet
carrier assembly (400) from the end plate.
Refer to subassembly sections for disassembly and as-
sembly of subassemblies.
400
10
3
9
8
26
27
The complete freefall assembly must be removed to service the internal parts, because the bearing support (802)
cannot be removed without first removing the freefall assembly at the support end-plate (3). This is done by removing
the bolts and lockwashers (35 & 16).
CAUTION

15
2. Turn the freefall assembly on the opposite side, so the
bearing support capscrews (806) are facing up. Re-
move bolts securing bearing support (802) to freefall
housing (801).
3. Remove the springs (804) and freefall piston (803).
FREE FALL ATTACHMENT
The GH30B freefall assembly weighs approximately
250 lb (114 kg). Make certain lifting equipment has ad-
equate capacity. Using undersized or poorly maintained
lifting equipment may result in a dropped load, property
damage, injury or death.
Refer to Winch disassembly to remove the freefall assem-
bly from the winch.
Follow this procedure after the freefall assembly has been
removed from the support end housing (3).
1. Set the freefall assembly with the freefall ring gear (4)
up and remove retaining ring (38). Remove the free-
fall ring gear (4). Remove o-ring (29) and discard.
38
4
29
802
806
801
804
805
803
801
DISASSEMBLY
Remove retaining ring (38) from the center ring gear
bearing support BEFORE removing capscrews (806.) If
capscrews are removed before retaining ring, the retain-
ing ring will be forced out of the groove by spring force.
Dislodging of the retaining ring may result in serious per-
sonal injury and certain damage to hoist components.
CAUTION
The bearing support is under spring tension from the
freefall assembly brake springs. Loosen each bearing
support capscrews one turn at a time until spring ten-
sion is released.
CAUTION
It may be necessary to apply a very short burst of shop
air at the freefall release port to break free the piston
from the freefall housing. If this is done, ensure all per-
sonnel are clear of the piston path. Loosely bolt the
bearing support back onto the freefall housing and use
shortest possible burst of low pressure shop air.
CAUTION

16
FREE FALL ATTACHMENT
4. Remove the two spacers (815), ten divider plates
(814), and seven friction plates (813).
Clean and Inspect
1. Thoroughly clean and inspect all parts. Check sealing
surfaces on the free fall housing, bearing support, and
piston. Ensure the free fall release port is clean and
free of debris.
2. Place free fall friction disc on a flat surface and check
for distortion with a straight edge. Friction material
should appear even across the entire surface with the
groove pattern visible. Replace friction discs or divider
plates if distorted, burned, wear is uneven, or splines
are worn to a point. Minimum thickness of friction ma-
terial is .160 in. (4 mm.) measured at the center of the
friction surface
3. Check free fall spring free length. Minimum free length
is2.910in.(73.9mm.) Ifitisrequiredbymeasurement
to replace one spring, you must replace all springs.
815
814
813

17
ASSEMBLY
FREE FALL ATTACHMENT
1. Place the freefall housing (801) on a clean work sur-
face with the bearing support (802) side facing up.
Coat the friction plates with gear oil prior to installa-
tion.
2. Place a spacer (815) in the freefall housing. The sev-
en (7) friction discs and ten (10) divider plates must
be installed in the proper order. Install a divider plate
(814) on top of the spacer (815). Install a friction disc
(813) on the divider plate and alternate until all seven
friction discs are installed. Install the remaining three
divider plates on top of the last fiction plate. Install the
remaining spacer (815) on top of the friction disc and
divider plate stack.
3. Install o-rings (810 and 811) and back-up rings (809
and 812) in freefall piston (803) grooves. The back-up
ring is always installed toward the low pressure side of
the o-ring. In this case, the back-up rings are toward
the outer surfaces with the concave surface toward
the o-ring.
4. Apply a light coat of grease to the back-up rings, o-
rings, and freefall housing piston surfaces. Ensure the
freefall release port is vented to atmosphere, and set
the piston (803) into the housing (801). Tap with a soft
mallet to drive the piston into the housing. Install the
springs (804) onto the pins in the brake piston.
5. Install o-ring (808) in the bearing support and coat
lightly with grease. Set the bearing support in the
housing and align in proper position in reference to
the housing. Install capscrews (806) and lockwashers
(807) hand tight. Evenly tighten the capscrews one
turn at a time until the bearing support is seated with
the housing. Torque the capscrews to 110 ± 10 lb-ft
(149 N-m).
6. Turn over the freefall housing so the bearing support
bolts are down. Install one of the bearings (37) onto
the bearing support.
7. Install a hand pump with a shut-off valve to the freefall
release port and pressurize to 500 to 700 psi (3450
to 4820 kPa) and let stand for 5 five minutes. If there
is any loss of pressure, the freefall piston should be
removed and the sealing rings and surfaces inspect-
ed. WHILE THE PRESSURE IS APPLIED AND THE
FREEFALL DISCS RELEASED, install the ring gear
into the discs and align the friction disc teeth with the
ring gear splines. Install the remaining bearing (815)
and then install retaining ring (38) on the bearing sup-
port.
8. Install o-ring (29) in the freefall housing and grease
lightly prior to bolting to the support end plate. Refer to
WinchAssembly for instructions to complete assembly
of the hoist.

18
209
201
208
210
207
202
204
205
203
206
BRAKE CYLINDER
DISASSEMBLY
1. A hydraulic press or spring compressor tool is re-
quired to disassemble the brake subassembly. Place
the brake subassembly on the press with the primary
housing cover (201) down. Place a heavy steel bar
across the large diameter of the pressure plate (210)
and compress the springs until spring force is removed
from the retaining ring (209). Remove the retaining
ring with retaining ring pliers. Slowly release the press
force on the pressure plate.
2. Remove the pressure plate (210), spring separator
(208), and springs (207).
3. Remove the brake piston (202) from the primary hous-
ing cover (201). Remove the o-rings and back-up
rings from the brake piston and discard (items 203,
204, 205, and 206).
Clean and Inspect
1. Thoroughly clean and inspect all parts. Check seal-
ing surfaces on the primary housing cover and brake
piston. Ensure the brake release port is clean and free
of debris.
2. Place brake friction disc on a flat surface and check
for distortion with a straight edge. Friction material
should appear even across the entire surface with the
groove pattern visible. Replace friction discs or divider
plates if distorted, burned, wear is uneven, or splines
are worn to a point. Minimum thickness of friction ma-
terial is .160 in. (4 mm.) measured at the center of the
friction surface
3. Check brake spring free length. Minimum free length
is2.910in.(73.9mm.) Ifitisrequiredbymeasurement
to replace one spring, you must replace all springs to
maintain consistent spring force distribution.

19
5. Install the spring separator (208). The spring spacer
seats on the piston. Install the springs (207) in the
spring separator and space evenly. There are 24
holes in the spring spacer, so with 12 springs put a
spring in every other hole. Align the empty holes with
the fill and drain holes as shown in the photograph
below.
6. Install the pressure plate (210) onto the springs with
the flat surface toward the springs.
7. Place a heavy steel bar across the outside diameter
of the pressure plate. Use the press to compress the
springs until there is clearance to install the retaining
ring (209) into the groove in the piston. Install the re-
taining ring and make certain it is seated securely BE-
FORE releasing press or spring compressor. Use a
hammer and punch to seat the retaining ring as shown
below.
1. Ahydraulic press or spring compressor tool is required
to assemble the brake subassembly. Place the brake
housing cover (201) on a clean work surface with the
motor side up and space it at least 2-inches (50 mm.)
off the table with wood or metal blocks. This gives
clearance for the brake piston (202) installation.
2. Install the o-rings (204, 205) and back-up rings (203,
206) in the piston grooves. The back-up ring is always
to the low pressure side of the o-ring, which is the out-
side surface of the piston for this part as shown in the
illustration below. The concave side of the back-up
ring provides a seat for the o-ring. Lightly grease the
o-rings and back-up rings after installation on the pis-
ton.
3. Apply grease to the housing cover at the piston seat-
ing surface and install the brake piston in the primary
housing cover (201) – if necessary, tap lightly to seat
in the housing cover.
4. Place the primary housing cover on the press table
with the motor side down. Place a spacer under the
piston to keep it raised in the housing cover.
BRAKE CYLINDER
ASSEMBLY
PRESSURE SIGNAL
BACKUP RING
#203
BACKUP RING
#206
O-RING
#205
O-RING
#204
Fill or Drain Hole

20
505
508
502 504
506 503
506
501 507
549
CABLE DRUM
SERVICE
DISASSEMBLY
1. Stand the drum with the freefall end flange down. Re-
move the twelve capscrews (508) and lift the motor
end flange (503) off of the drum barrel. Remove the oil
seal (505) and o-ring (504) from the motor end flange
and discard.
2. Use bearing pullers to remove the bearing (504) from
the drum barrel.
3. Rotate the drum barrel so the freefall end flange is
facing up. Remove the twelve capscrews (507) and
lift the flange off of the drum barrel. Discard o-ring
(506).
ASSEMBLY
1. Install the bearing (504) into the motor end of the drum
barrel (502) and ensure it is seated.
2. Apply Loctite Aviation Gasket sealant or equivalent to
the outside diameter of the seal (505) and install the
seal in the motor end drum flange (503) with the spring
side of the seal toward the drum barrel.
3. Install o-ring (506) on the motor end drum flange and
grease lightly. Slowly lower the motor end flange (503)
onto the bearing end of the drum barrel (502). Apply
Loctite 242 to the capscrews (508) and torque to 110
lb-ft (149 N-m).
4. Set drum barrel on motor flange end. Install o-ring
(506) on freefall end drum flange (501) and grease
lightly.
5. Slowly lower freefall end drum flange onto drum bar-
rel. Apply Loctite 242 to the capscrews (507) and
torque to 110 lb-ft (149 N-m).
Note: The capscrews used to fasten the drum flange
to the drum barrel are different lengths for each drum
flange. The motor end flange capscrews are 2 inch
long hex heads, and the freefall end capscrews are
1-¼ inch-long socket heads.
Other manuals for Gearmatic GH30B
1
Table of contents
Other Paccar Winch Winch manuals
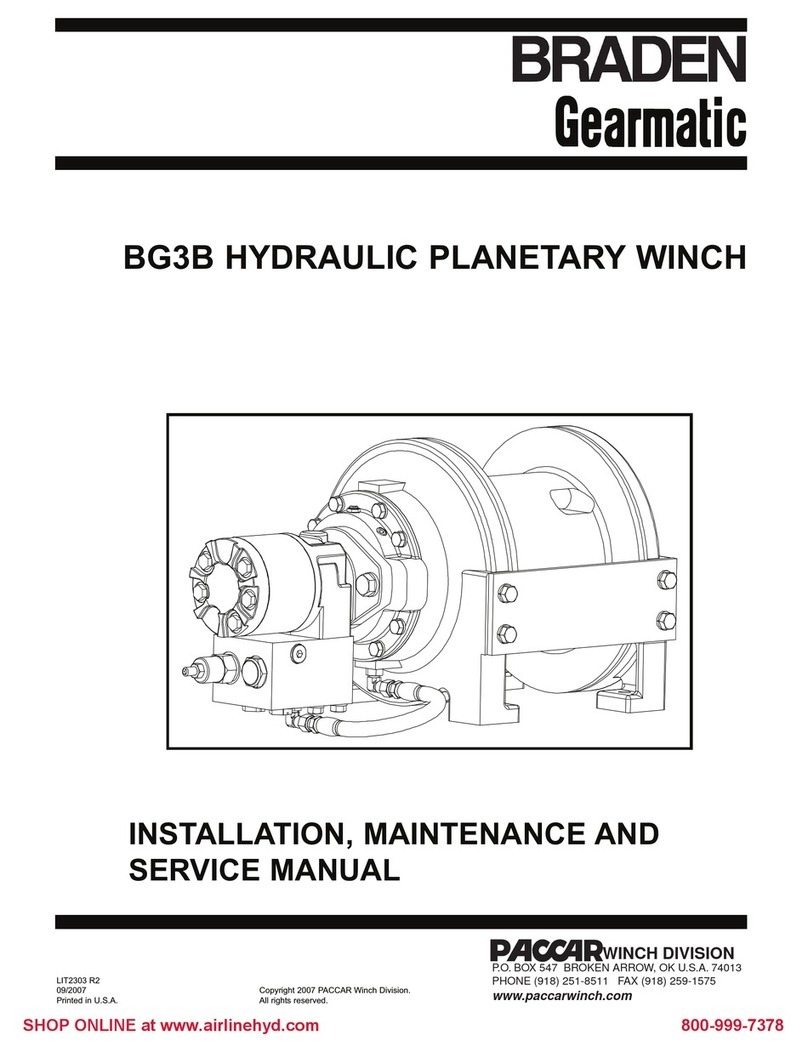
Paccar Winch
Paccar Winch Braden Gearmatic BG3B Manual
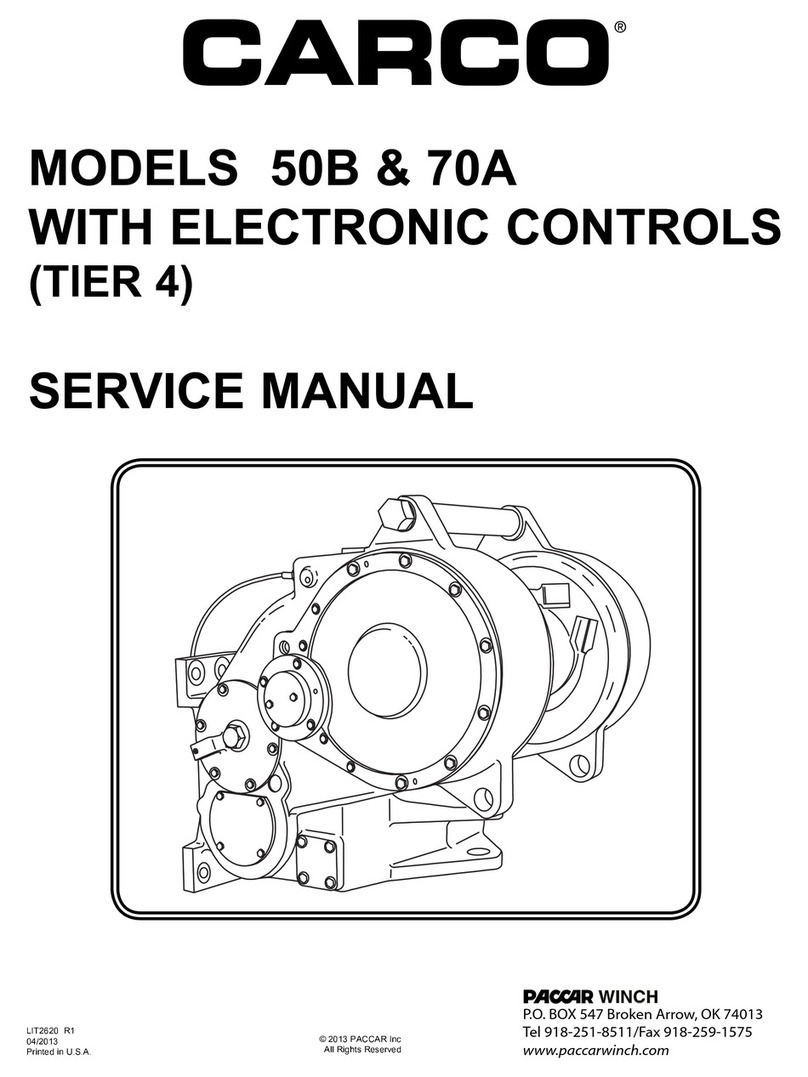
Paccar Winch
Paccar Winch Carco 50B User manual
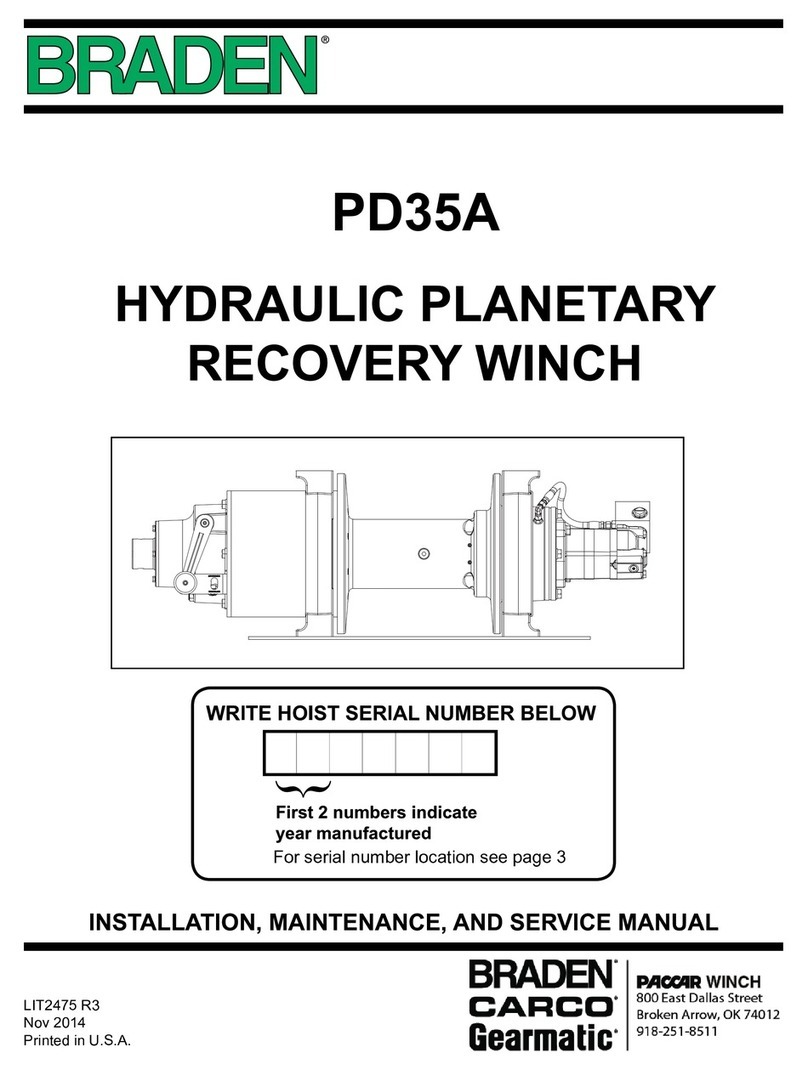
Paccar Winch
Paccar Winch Braden PD35A Manual
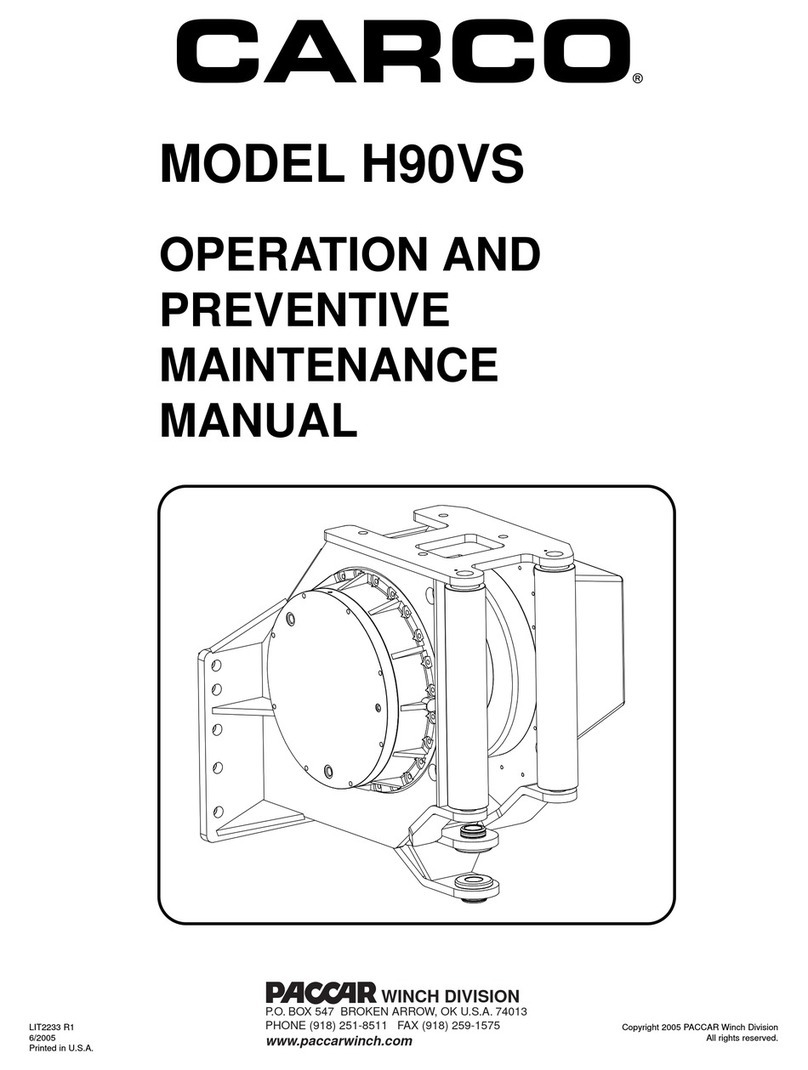
Paccar Winch
Paccar Winch CARCO H90VS Owner's manual

Paccar Winch
Paccar Winch Carco 50A User manual
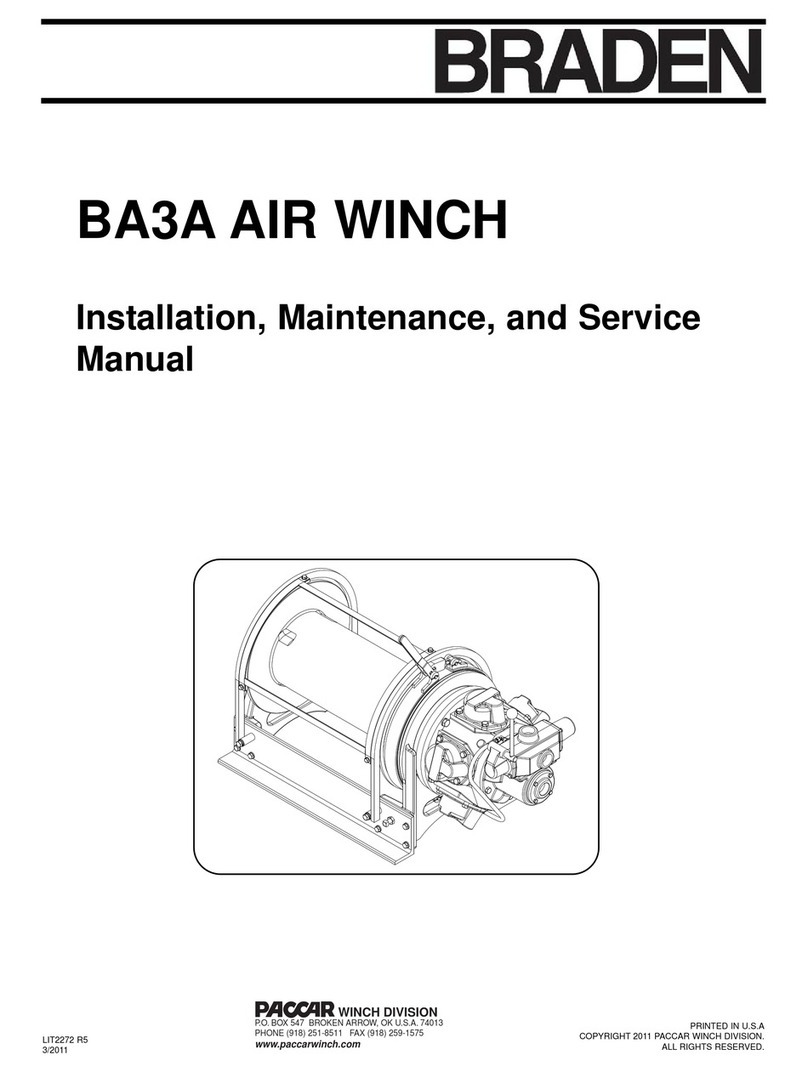
Paccar Winch
Paccar Winch BRADEN BA3A Manual

Paccar Winch
Paccar Winch CARCO H50VS User manual
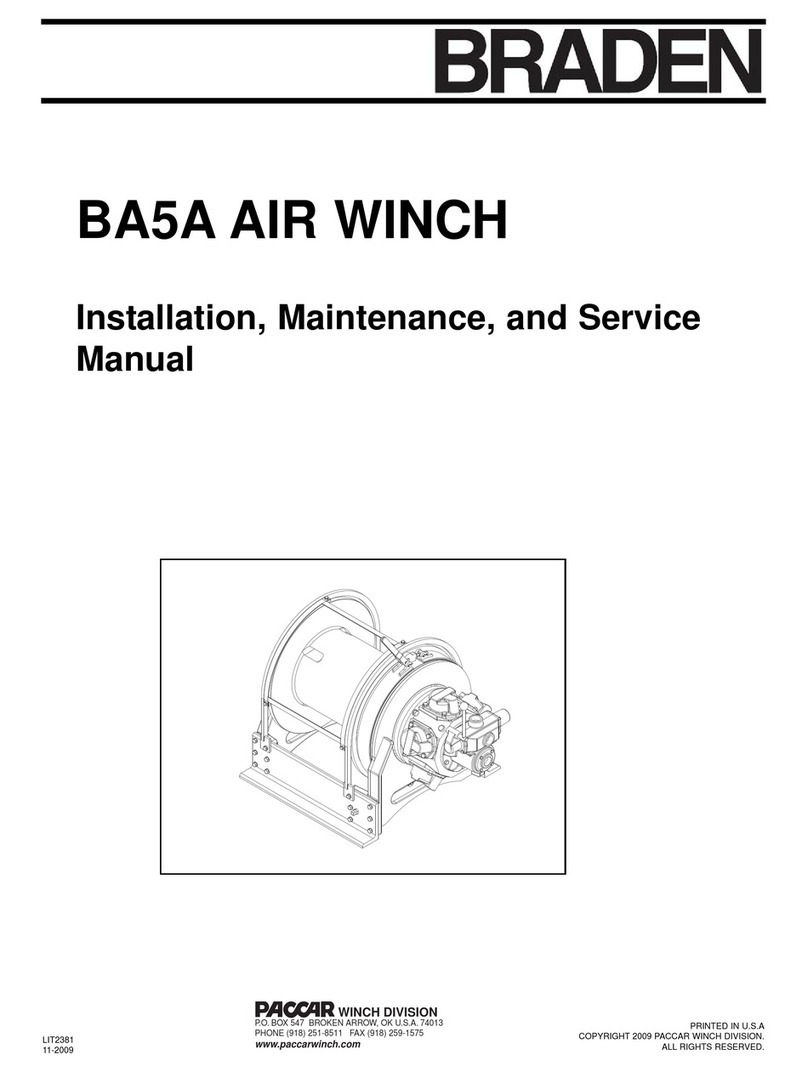
Paccar Winch
Paccar Winch BRADEN BA5A Manual

Paccar Winch
Paccar Winch BRADEN H20R Manual

Paccar Winch
Paccar Winch PA58VS User manual