PARCOL 1-6940 Series User manual

MAN0038E / rev.6
INSTRUCTION MANUAL - USE - MAINTENANCE
1-6940 and
1-4640
SERIES
CAGE
CONTROL VALVES
for LIMITATIONS OF USE see PARCOL document "NTG 76/550E"
(Residual hazards with regard to essential safety requirements of Annex I of European Pressure Equipment Directive no 97/23/CE)

- 2 -
MAN0038E / rev.6
Summary
SAFEGUARDS........................................................................................................................................................................................3
INSTRUCTION MANUAL - USE - MAINTENANCE ................................................................................................................................4
FOREWORD.......................................................................................................................................................................................4
1. INSTALLATION.........................................................................................................................................................................4
2. VALVE DISASSEMBLY AND REASSEMBLY ..........................................................................................................................4
NUMBERING SYSTEM.......................................................................................................................................................................5
3. DISASSEMBLY.........................................................................................................................................................................6
3.1 VALVE TYPE 1-6941 / 1-4641 DISASSEMBLY ...................................................................................................................6
3.2 REPLACING OF PTFE RING ON THE PLUG......................................................................................................................6
3.3 VALVE TYPE 1-6942 / 1-4642 DISASSEMBLY ...................................................................................................................7
3.4 VALVE TYPE 1-6943 /1-4643 DISASSEMBLY ....................................................................................................................8
3.5 VALVE TYPE 1-6948 / 1-4648 DISASSEMBLY ...................................................................................................................9
3.6 STEM AND PLUG REPLACEMENT...................................................................................................................................10
4. PREPARING FOR REASSEMBLY .........................................................................................................................................10
4.4 VALVE TYPE 1-6941 / 1-4641 ASSEMBLY .......................................................................................................................12
4.5 VALVE TYPE 1-6942 / 1-4642 ASSEMBLY .......................................................................................................................12
4.6 VALVE TYPE 1-6943 / 1-4643 ASSEMBLY .......................................................................................................................12
4.7 VALVE TYPE 1-6948 / 1-4648 ASSEMBLY .......................................................................................................................13
5. SETTING VALVES WITH PNEUMATIC DIAPHRAGM ACTUATOR......................................................................................17
5.1 VALVES WITH "AIR-TO-CLOSE" ACTION 1-X-291 ..........................................................................................................17
5.2 VALVES WITH “AIR-TO-OPEN” ACTION 1-X-292 ............................................................................................................17
6. BALANCED PLUGS................................................................................................................................................................18
6.1 “Type S” INSERT (Fig. 28)..................................................................................................................................................18
6.2. “Type E” INSERT (Fig. 30)..................................................................................................................................................18
6.3. “Type C” and “Type D” INSERTS (Fig. 27-26)....................................................................................................................18
6.4 “Type R” INSERT (Fig. 29) .................................................................................................................................................18

- 3 -
MAN0038E / rev.6
SAFEGUARDS
GENERAL NOTICES
Beside the rules here below listed the plant man-
ager must meet the regulation in force concerning
safety and health of workers in jobsites.
Qualified staff only must be used to operate on the
valve.
The Company rejects any responsibility for personal
injury and damages to equipment imputable to improper
operation, use of non original spare parts or repairs
executed by unauthorised staff.
Transportation must be performed utilising original
packing up to job-site.
The Company rejects any responsibility for damages
occurred to things and people due to packing because
of having been tampered with.
USE AND MAINTENANCE
Pay attention to the stem connector and levers
connected to the stem, if any.
Never approach your hands to stem and levers
even when the valve is still, unless air supply is cut
off and spring is released: risk of personal injury.
DISASSEMBLY
WARNING DANGER
To avoid personal injury and damage to the process
system, isolate the valve from all pressure and
release pressure to the valve body before
attempting also partial disassembling.
WARNING DANGER
To avoid personal injury and damage, isolate the
actuator from all pressure and release pressure
before attempting disassembling connectors.
Stick to instruction manual when disassembling the
actuator, even partially.
LIFTING AND HANDLING
When lifting use eyebolts, if any, otherwise sling the
valve body.
WARNING DANGER
Valve-actuator assembly can be lifted by means of
eyebolts provided on the actuator only if
expressively stated in special plate.
NOISE
In particular conditions the valve may generate high
noise levels. In such cases it is therefore necessary
to take the necessary precautions, according to the
regulation in force.
TEMPERATURE
In case that hot fluids flow through the valve, the
operator must pay attention to not insulated parts.
PACKING
WARNING DANGER
Packing must not be released or replaced when
valve is under pressure.
DISPOSAL
Dispose of the valve and any other component
in security, according to local, national and
international law regulations about safety and
environmental standards.
Separate the components in the following
categories:
•electrical and electronic;
•ferrous scrap.
For disposal of electric and electronic components
please refer to relevant instruction manuals.
Please check local regulations regarding the
disposal of waste.

- 4 -
MAN0038E / rev.6
1-6940 and 1-4640 SERIES CONTROL VALVE
INSTRUCTION MANUAL - USE - MAINTENANCE
FOREWORD
Before installing 1-6940 and 1-4640 type valves
ascertain that the process operation pressures are not
higher than the ones allowable by the valve body rating
at the design temperature.
Furthermore the valve specific overall rating shall also
be considered (see general catalogue). The latter may
be more restrictive in some instances.
1. INSTALLATION
A straight pipe at least 6 DN long must be installed in
the piping upstream the valve and a further 3 DN length
must be installed downstream. Purpose of the above re-
quirements is to avoid stream deviations at body
connections, namely at the inlet one.
Reducers are allowed along above mentioned straight
lengths, provided that they are duly tapered and
concentric...
Before installing the valve in the line, namely the new
ones, clean piping and valves from all foreign materials,
such as welding chips, scale, oil grease or dirt.
Check piping connections arrangement for dimensions,
coaxiality and parallelism, to avoid tensile and bending
stresses, which could occur when fastening the valve to
the piping, namely in case of valves with flanged
connections.
If the valve body has butt welding connections the
installation in the pipeline should be done avoiding to
overheat the body wall.
If the valve plug is provided with a plastic seal insert it is
better to lift the plug over the seat when welding.
If excessive heating of the body is expected (small
valves, on line annealing, MIG welding, etc.) and the
trim is provided with plastic inserts, the body
temperature should be kept under control. The outside
surface temperature should not exceed 100°C at 70
80 mm distance from the welding bead.
In case of doubt it is better to remove the trim from
valve body before beginning to weld.
The face-to face dimensions of PARCOL valves are
according to IEC 534-3-1 standard, table 1.
Valves with threaded connections should be installed
with unions to allow their removal.
Control valves are normally installed with a by-pass to
allow their maintenance without shutting down the
process.The need of the by-pass must be stated for
each specific application.
The two shut-off valves located aside the control valve
must have the same port as the pipeline, not to cause
considerable head losses when completely open. The
by-pass valve should have the same port (full size or
reduced) as the control valve.
1-6940 and 1-4640 series valves are normally installed
in such a way that the flow action tends to open the
plug, unless otherwise specified.
The flow direction, according to what above specified, is
identified by the arrow printed on the indicating plate.
Valves are normally installed in vertical position with
upward oriented actuator.
Anyhow they may be installed and properly operate in
any other position. Valves should not be installed with
downward oriented actuator if the fluid holds solid
particles, which may then build-up into the packing.
2. VALVE DISASSEMBLY AND REASSEMBLY
When valves, typically over 6”, are installed
with plug in horizontal position it is necessary
to provide suitable tools, to correctly support
internal parts during disassembly and
reassembly operations (for further information
please contact Parcol).

- 5 -
MAN0038E / rev.6
NUMBERING SYSTEM
1
-
X X
4
X
TRIM TYPE
1
CONTOURED PLUG
2
CONTOURED PLUG INTEGRAL WITH STEM
3
MULTIHOLES CAGE
8
MULTIHOLES CAGE - PLUG WITH PILOT
BODY TYPE
69
STRAIGHT
46
ANGLE

- 6 -
MAN0038E / rev.6
3. DISASSEMBLY
3.1 VALVE TYPE 1-6941 / 1-4641 DISASSEMBLY
3.1.1. Disconnect and remove the valve actuator
(see actuator instruction manual)
3.1.2. Loose the packing (27), unscrew nuts (4)
and remove bonnet (2).
3.1.3. Remove gasket (8) from the body; some-
times problems can occur and the gasket
can be damaged. It is recommended to
replace it with PARCOL original spares.
3.1.4. The cage (9) must be drawn out from the
body with the plug, acting on the stem (7).
Should the cage removal get difficulties be-
cause of scales or build-ups. In this case
strike gently all around the upper end. When
the valve is supplied with the cage adapter
(11) this one has to be lifted out with the
cage.
3.1.5. To remove the bonnet seal set (27) see the
Parcol “Packing for Control Valves”
manual MAN0002E.
3.1.6. Lift out the seat (6) using the suitable
threaded holes.
3.1.7. Remove gasket (14).
3.2 REPLACING OF PTFE RING ON THE PLUG
3.2.1. DN ≤ 2”: remove the pin (52) by means of a
punch, than unscrew the plug (5) from the
plug post (53) by inserting a screwdriver into
the suitable slot at plug head.
3.2.2. DN > 2”: Unscrew screws (54) and remove
the plug post (53).
3.2.3. Replace the PTFE seal ring (51) with a new
one.
3.2.4. Tighten the plug flange till metal to metal
contact. (for DN ≤2” check that stem and
plug holes are aligned and drive the pin 52).
3.2.5. Insert the pin (52) into the hole and punch it
on both sides to lock it.
Figure 1
Item
Part Name
1
BODY
2
BONNET
3
STUD BOLT
4
NUT
5
PLUG
51
SEAL RING
52
PIN
53
PLUG POST
54
SCREW
55
NORD-LOCK WASHER
6
SEAT
7
STEM
8
GASKET
9
CAGE
12
PIN
14
GASKET
27
SET
Table 1

- 7 -
MAN0038E / rev.6
3.3 VALVE TYPE 1-6942 / 1-4642 DISASSEMBLY
3.3.1. Disconnect and remove the valve actuator
(see actuator instruction manual).
3.3.2. Loose the packing (27), unscrew nuts (4)
and remove bonnet (2).
3.3.3. Remove gasket (8) from the body;
sometimes problems can occur and the
gasket can be damaged. It is recommended
to replace it with PARCOL original spares.
3.3.4. Extract the plug (5) integral with stem.
3.3.5. Remove the seat retainer (10) from the body
using the suitable threaded holes.
Figure 2
3.3.6. Should the seat retainer removal get
difficulties because of scales or build-ups. In
this case strike gently all around the upper
end.
3.3.7. To remove the bonnet seal set (27) see the
“Packing for Control Valves” manual
MAN0002E.
3.3.8. Lift out the seat (6) using the suitable
threaded holes
3.3.9. Remove gasket (14).
Item
Part name
1
BODY
2
BONNET
3
STUD
4
NUT
5
PLUG
6
SEAT
8
GASKET
9
GUIDE BUSHING
10
SEAT RETAINER
14
GASKET
27
PACKING BOX
Table 2

- 8 -
MAN0038E / rev.6
3.4 VALVE TYPE 1-6943 /1-4643 DISASSEMBLY
3.4.1. Disconnect and remove the valve actuator
(see actuator instruction manual).
3.4.2. Loose the packing (27), unscrew nuts (4)
and remove bonnet (2).
3.4.3. Remove gasket (8) from the body;
sometimes problems can occur and the
gasket can be damaged. It is recommended
to replace it with PARCOL original spares.
3.4.4. Remove the plug (5) acting on the stem (7).
3.4.5. Remove the cage (9) from the body using
the suitable threaded holes.
3.4.6. Should the cage removal get difficulties be-
cause of scales or build-ups. In this case
strike gently all around the upper end. When
the valve is supplied with the cage adapter
(11) this one has to be lifted out with the
cage.
3.4.7. To remove the bonnet seal set (27) see the
“Packing for Control Valves” manual
MAN0002E.
3.4.8. Lift out the seat (6) using the suitable
threaded holes.
3.4.9. Remove gasket (14).
Figure 3
Figure 4 Figure 5 Figure 6
Item
Part Name
1
BODY
2
BONNET
3
STUD
4
NUT
5
PLUG
6
SEAT
7
STEM
8
GASKET
9
CAGE
10
BELLEVILLE WASHER
11
ADAPTER
12
PIN
14
GASKET
15
SPACER
16
GASKET
18
SPACER
27
PACKING BOX
Table 3

- 9 -
MAN0038E / rev.6
3.5 VALVE TYPE 1-6948 / 1-4648 DISASSEMBLY
3.5.1. Disconnect and remove the valve actuator
(see actuator instruction manual).
3.5.2. Loose the packing (27), unscrew nuts (4)
and remove bonnet (2).
3.5.3. Remove gasket (8) from the body; some-
times problems can occur and the gasket
can be damaged. It is recommended to
replace it with PARCOL original spares.
3.5.4. Extract the cage (9) together with the plug
(5) acting on the stem (7). Should the cage
removal get difficulties because of scales or
build-ups. In this case strike gently all
around the upper end.
3.5.5. For plug disassembly see “Balanced with
Pilot plugs” MAN0051E.
3.5.6. To remove the bonnet seal set (27) see the
“Packing for Control Valves” MAN0002E.
3.5.7. Lift out the seat (6) using the suitable
threaded holes.
3.5.8. Remove gasket (14).
Figure 7
Item
Part Name
1
BODY
2
BONNET
3
STUD
4
NUT
5
PLUG
6
SEAT
7
STEM
8
GASKET
9
CAGE
12
PIN
14
GASKET
27
PACKING BOX
28
SCREW
29
STOP WASHER
30
FLANGE
31
PILOT
32
SPRING
Table 4

- 10 -
MAN0038E / rev.6
3.6 STEM AND PLUG REPLACEMENT
Even if stem and plug are normally supplied as-
sembled, nevertheless the connecting procedure
of the two parts should be known, when screw
threaded and pinned.
It is recommended to use a new stem (not
drilled), while the plug may be reused.
It is not possible to cut the threaded end of the
stem and redrill it, because valve stem and
actuator stem are not long enough to recover
the reduction of the length.
3.5.9. Remove the pin by pushing it out with a
punch.
3.5.10. Thoroughly screw the new stem in the plug
using a rubber-protected pliers. Be aware not
to damage the grounded surfaces.
3.5.11. Lay down the guide section of the plug into a
"V" block.
3.5.12. Drill according to the Table 4 data driving the
tool in the existing hole in the plug.
3.5.13. Remove drill burrs.
3.5.14. Put some grease on the new pin and slip it
into the hole.
3.5.15. Check stem and plug on a lathe for alignment.
If necessary straighten them with a plastic or
rubber hammer.
Nominal pin diameter (mm)
3
4
5
Hole diameter (mm)
3
01.0
4
012.0
5
012.0
Table 4
4. PREPARING FOR REASSEMBLY
4.1. Clean thoroughly the seating surfaces of the
static gaskets (8) (14) e (16) fitting body with
bonnet, body with cage, body with seat and
cage with adapter.
4.2. Only for valves without metallic stop before
assembly the valve, insert the body-bonnet
gasket (8), install the bonnet (2) and measure
the "A" dimension as shown on figure7.
4.3. For valves with metallic stop proceed
according to the relevant paragraph.
Valve without metallic stop
Valve with metallic stop
Figure 8 - body-bonnet connection check dimensions

- 11 -
MAN0038E / rev.6
Figure 9 - body-bonnet nuts tightening sequence
VALVE
RATING
A-B
(mm)
150-300
0.4÷0.7
600
0.5÷0.8
900
0.6÷0.9
1500
07÷1.0
2500
0.8÷1.1
Table 7
DN
(in.)
Stud
Type
Stud.
No.
Wrench
Nut material
SA 194 Gr.4
SA 194 Gr. 2H
SA 194 Gr.8
TIGHTENING TORQUE
(Nm)
1/2
M12
6
19
32
50
M16
6
24
80
130
3/4-1
M14
6
22
50
85
M16
8
24
80
130
M20
8
30
150
250
1.1/2
M14
8
22
50
85
M20
8
30
150
250
M27
8
41
390
660
2
M18
8
27
110
180
M27
8
41
390
660
M33
8
50
720
1200
3
M20
8
30
150
250
M30
8
46
530
900
M33
10
50
720
1200
4
M20
10
30
150
250
M30
10
46
530
900
M36x3
10
55
980
1650
6
M24
12
36
260
440
M33
12
50
720
1200
8
M27
12
41
390
660
M33
12
50
720
1200
M36x3
12
55
980
1650
M42x3
12
65
1600
2700
10-14
M27
12
41
390
660
M33
12
50
720
1200
M36x3
12
55
980
1650
M39x3
16
60
1270
2150
12÷16
M30
12
46
530
900
M33
16
50
720
1200
12
M42x3
12
65
1600
2700
M45x3
16
70
2000
3400
14-16
M33
16
50
720
1200
M36x3
16
55
980
1650
16-20
M33
20
50
720
1200
M36x3
20
55
980
1650
20-24
M30
20
46
530
900
M36x3
24
55
980
1650
M42x3
24
65
1600
2700
24
M33
24
50
720
1200
M39x3
24
60
1270
2150
M45x3
24
70
2000
3400
Table 6

- 12 -
MAN0038E / rev.6
4.4 VALVE TYPE 1-6941 / 1-4641 ASSEMBLY
4.4.1. Put the seat gasket (14) into the body.
Always use original spare gaskets as they
have calibrated thickness for the correct
application. Incorrect gasket thickness may
cause wrong tightening of the cage into the
body.
4.4.2. Insert seat (6) into the body.
4.4.3. Assembly cage and plug, then insert it into the
body handling it by the stem. Be sure the plug
is coupled with the seat.
4.4.4. Check the two pieces for alignment by ro-
tating one on the other.
4.4.5. Measure the “X” quote as shown on figure 11
verifying that is within 0.4÷0.85mm.
4.4.6. Fit the bonnet (2)
4.4.7. Fit the packing box according to the “Packing
for Control Valves” manual MAN0002E.
4.4.8. Tighten the nuts (4) with the torque stated on
table 6 and according to the sequence shown
on figure 9.
4.4.9. Only for valves without metallic stop
measure the "B" quote as shown on figure 7
and, if necessary, continue tightening the nuts
(4) till dimension "A-B" is equal to that
indicated on table 6.
4.4.10. For valves with metallic stop check that the
“H” dimension (see figure 8) is the same on
three points at 120° equally spaced.
4.5 VALVE TYPE 1-6942 / 1-4642 ASSEMBLY
4.4.11. Put the seat gasket (14) into the body.
Always use original spare gaskets as they
have calibrated thickness for the correct
application. Incorrect gasket thickness may
cause wrong tightening of the seat retainer
into the body.
4.4.12. Insert seat (6) into the body.
4.4.13. Assembly the seat retainer and plug, then
insert it into the body handling it by the stem.
Be sure the plug is coupled with the seat.
4.4.14. Check the two pieces for alignment by
rotating one on the other.
4.4.15. Measure the “X” quote as shown on figure 12
verifying that is within 3.5÷3.8mm.
4.4.16. Fit the bonnet (2).
4.4.17. Fit the packing box according to the “Packing
for Control Valves” manual MAN0002E.
4.4.18. Tighten the nuts (4) with the torque stated on
table 6 and according to the sequence shown
on figure 9.
4.4.19. Only for valves without metallic stop
measure the "B" quote as shown on figure 8
and, if necessary, continue tightening the nuts
(4) till dimension "A-B" is equal to that
indicated on table 7.
4.4.20. For valves with metallic stop check that the
“H” dimension (see figure 8) is the same on
three points at 120° equally spaced.
4.6 VALVE TYPE 1-6943 / 1-4643 ASSEMBLY
4.6.1. Metallic seal (fig.10,11,12,13,14,19,20)
4.6.1.1. Put the seat gasket (14) into the body.
Always use original spare gaskets as
they have calibrated thickness for the
correct application. Incorrect gasket
thickness may cause wrong tightening of
the cage into the body.
4.6.1.2. Insert seat (6) into the body (for seat with
soft seal see section 9.2).
4.6.1.3. Insert the cage (9) into the body and be
sure it is coupled with the seat (6). Check
the pieces for alignment by rotating one on
the other.
4.6.1.4. Without adapter version (fig.10,11,12,19)
4.6.1.4.1. STD: Measure the “X” quote as shown
on figure 11 verifying that is within
0.5÷0.8mm.
4.6.1.4.2. AG: insert gasket (14) and the spacer
(15), then Measure the “X” quote as
shown on figure 12 verifying that is
within 0.8÷1.3mm.
4.6.1.4.3. HT: insert belleville washer (10) over
the cage with the larger side on the top
side. Insert the spacer and measure the
“X” quote as shown on figure 19
verifying that is within the gap in table
10.
4.6.1.5. Adapter version (fig.13,14,20)
4.6.1.5.1. Put the adapter (11) over the cage
without gasket.
4.6.1.5.2. STD: measure the “X” quote as shown
on figure 13 verifying that is within
0.5÷0.9mm.
4.6.1.5.3. AG: insert gasket (14) and the spacer
over the cage then Measure the “X”
quote as shown on figure 14 verifying
that is within 0.8÷1.4mm.
4.6.1.5.4. HT: insert belleville washer (10) over
the cage with the larger side on the top
side. Insert the spacer then measure
the “X” quote as shown on figure 16
verifying that is within the gap in table
10.
4.6.2. Soft seat version (fig.15,16,17,18)
4.6.2.1. Put the seat gasket (14) into the body.
Always use original spare gaskets as
they have calibrated thickness for the
correct application. Incorrect gasket
thickness may cause wrong tightening of
the cage into the body.
4.6.2.2. Insert the seat (6) without the seal ring
(19).
4.6.2.3. Insert the cage (9) into the body and be
sure it is coupled with the seat (6). Check
the pieces for alignment by rotating one on
the other.

- 13 -
MAN0038E / rev.6
4.6.2.4. Version without adapter (fig.15,16)
4.6.2.4.1. Measure the “X” quote as shown on
figure 15 (or figure 16 for balanced
version) verifying that is within the
following gap:
not balanced: 3.5÷3.8mm
balanced: 0.5÷0.8mm
4.6.2.4.2. Remove all components and insert the
seal ring (19) into the seat (6) verifying
that the level difference between the
soft insert and the seat is ~0.3mm.
4.6.2.4.3. Remount all components as for figure
15 (or figure 16 for balanced version).
4.6.2.5. Version with apadter (fig.17,18)
4.6.2.5.1. Put the adapter (11) over the cage
without gasket (16).
4.6.2.5.2. Measure the “X” quote as shown on
figure 17 (or figure 18 for balanced
version) verifying that is within the
following gap.
not balanced: 3.5÷3.9mm
balanced: 0.5÷0.9mm
4.6.2.5.3. Remove all components and insert the
seal ring (19) into the seat (6) verifying
that the level difference between the
soft insert and the seat is ~0.3mm.
4.6.2.5.4. Remount all components as for figure
17 (or figure 18 for balanced version).
4.6.3. Fit the packing box according to the “Packing
for Control Valves” manual MAN0002E.
4.6.4. Fit the bonnet (2)
4.6.5. Tighten the nuts (4) with the torque stated on
table 5 and according to the sequence shown
on figure 8.
4.6.6. Only for valves without metallic stop
measure the "B" quote as shown on figure 8
and, if necessary, continue tightening the nuts
(4) till dimension "A-B" is equal to that
indicated on table 7.
4.6.7. For valves with metallic stop check that the
“H” dimension (see figure 8) is the same on
three points at 120° equally spaced.
4.7 VALVE TYPE 1-6948 / 1-4648 ASSEMBLY
4.7.1. Insert seat (6) into the body without gasket
(14) and put the over the seat.
4.7.2. STD: measure the “X” quote as shown on
figure 11 verifying that is within 0.0÷0.3mm.
4.7.3. AG: insert gasket (14) and the spacer, then
measure the “X” quote as shown on figure 12
verifying that is within 0.4÷0.8mm.
4.7.4. HT: insert belleville washer (10) over the cage
with the larger side on the top side. Insert the
spacer then measure the “X” quote as shown
on figure 21 verifying that is within the gap in
table 11.
4.7.5. Remove all components and remount the seat
with gasket (14).
4.7.6. For the mounting of the piloted plug see
Parcol “Pilot Operated Balanced Plugs”
manual MAN0051E.
4.7.7. The plug must be inserted on de cage outside
the valve body. After that insert the assembly
inside the valve handling by the stem. Be sure
the cage is coupled with the seat.
4.7.8. If requested, mount adapter or spacer, Insert
gasket (8) and install the bonnet without
packing onto the stem.
4.7.9. Fit the packing box according to the “Packing
for Control Valves Manual” manual
MAN0002E.
4.7.10. Tighten the nuts (4) with the torque stated on
table 5 and according to the sequence shown
on figure 8.
4.7.11. Only for valves without metallic stop
measure the "B" quote as shown on figure 8
and, if necessary, continue tightening the nuts
(4) till dimension "A-B" is equal to that
indicated on table 7.
4.7.12. For valves with metallic stop check that the
“H” dimension (see figure 8) is the same on
three points at 120° equally spaced.
4.8. Install actuator over the valve.
4.9. Reset the valve.

- 14 -
MAN0038E / rev.6
Metallic seal version
Figure 11 Figure 12
Figure 10
Figure 14
Figure 13

- 15 -
MAN0038E / rev.6
1-6943 series with soft seal
Figure 15 - not balanced Figure 16 - balanced
Figure 17 - not balanced with spacer Figure 18 - balanced with spacer
Item
Part name
8, 14
GASKET
16
GASKET (if any)
19
SEAL RING
Table 8

- 16 -
MAN0038E / rev.6
HT version (only for metallic seal)
Figure 19 Figure 20 Figure 21
Table 10
Table 11
Item
Part name
8, 14
GASKET
10
BELLEVILLE WASHER
Table 9
Check dimension “X” for 1-6943 series
Port (in.)
8
10
12
14
16
20
24
X
(mm)
Without adapter
1.8÷2.2
2.0÷2.4
2.3÷2.7
2.9÷3.3
3.3÷3.7
3.8÷4.2
4.1÷4.5
With adapter
1.8÷2.3
2.0÷2.5
2.3÷2.8
Check dimension “X” for 1-6948 series
DN (in.)
10
12
14
16
20
24
X (mm)
1.3÷1.7
1.6÷2
2.2÷2.6
2.6÷3.0
3.1÷3.5
3.3÷3.7

- 17 -
MAN0038E / rev.6
5. SETTING VALVES WITH PNEUMATIC
DIAPHRAGM ACTUATOR
Valves are factory set and supplied complete with
test certificate. It is however suggested to further
check the setting before putting the valve in service.
This may be done by means of a pressure gauge
and an air pressure regulator with output adjustable
between 0 and 40 45 psi. Connect the pressure
regulator inlet with the air supply line and the outlet
with the valve actuator.
The pressure gauge measures the pressure in the
actuator.
Then proceed as below described for the two cases
"air-to-close" and "air-to-open".
5.1 VALVES WITH "AIR-TO-CLOSE" ACTION 1-X-291
5.1.1. Acting on the pressure regulator increase the
pressure on the diaphragm until the plug (5)
stops (against the seat) at the end of its travel).
5.1.2. Check that the pressure is equal to the (2)
stated in figure 22. Check if necessary the
connection between valve stem and actuator
stem, changing if necessary the mutual
adjustment until the requested value is met.
5.1.3. Check that the travel indicator is in the "0"
position marked on the indicator plate. Displace
the plate if necessary.
5.1.4. Slowly decrease the air pressure until the travel
indicator performs the rated travel. The air
pressure should be equal to the (1) stated in
figure 22 (plus/minus range tolerances).
5.1.5. Should the plug travel be shorter than the rated
one check the connection between valve stem
and actuator stem, changing if necessary the
mutual adjustment then calibrate again the
actuator.
Figure 22
5.2 VALVES WITH “AIR-TO-OPEN” ACTION 1-X-292
5.2.1. Acting on the pressure regulator increase the
pressure on the diaphragm until the plug
begins to move.
5.2.2. Check that the pressure is equal to the (1)
stated in figure 23. Check if necessary the
connection between valve stem and actuator
stem, changing if necessary the mutual
adjustment until the requested value is met.
5.2.3. Check that the travel indicator is in the "0"
position marked on the indicator plate. Dis-
place the plate if necessary.
5.2.4. Increase the air pressure until the plug has
completed the rated travel. Then the pressure
gauge should indicate a pressure equal to the
(2) stated in figure 23 (plus/minus range
tolerances).
5.2.5. Should the plug travel be shorter than the
rated one check the connection between
valve stem and actuator stem, changing if
necessary the mutual adjustment then
calibrate again the actuator.
Figure 23

- 18 -
MAN0038E / rev.6
6. BALANCED PLUGS
Clean thoroughly the seating surfaces of gaskets before
start mounting it.
6.1 “Type S” INSERT (Fig. 28)
6.1.1. Grease the chamfer on the top part of the
plug.
6.1.2. For flow direction from the top part of the plug
the seal ring must be mounted with the
opened side on the top side. Otherwise for
flow direction from the side of the plug, mount
the seal ring with the opened side on the
bottom side.
6.1.3. Tilt the seal ring and insert it only in one side
of the seal seat. Then push it gently on the
seat with both hands (Figure 24).
6.1.4. It is allowed to warm the seal ring till 100°C
for get the operation easier.
6.2. “Type E” INSERT (Fig. 30)
6.2.1. Grease the chamfer on the top part of the
plug.
6.2.2. Insert the OR on the proper seat.
6.2.3. Fit the seal ring on the seat over the OR as
for figure.
6.3. “Type C” and “Type D” INSERTS (Fig. 27-26)
6.3.1. Insert the first rod seal on the bottom seat
(49).
6.3.2. Insert in the central seat following the order:
- the energizer (46) or (48).
- the first seal ring (47). Be careful to put the
opening at 90° to the energizer opening.
- the second seal ring (47). Be careful to put
the opening at 180° to the first seal ring.
6.3.3. Insert the second rod seal (49) into the top
seat.
WARNING!!!: rings must be stretched just
the minimum for the assembly. A deeper
deformation can cause the seal breaking.
6.4 “Type R” INSERT (Fig. 29)
6.4.1. Port up to 2”
5.1.1.1 First couple the seat with the cage, insert
in the cage the plug assembled with the
flange (111), the washer and ring nut (113)
without the c-ring seal.
6.4.1.2. Measure from the top of the cage to the
ring nut (dimension A) as shown in figure
25.
6.4.1.3. Repeat the measure mounting the c-ring
seal with the opening top side (dimension
B) as shown in figure 25. If the difference
A-B is within the one in Table 12, tighten
the ring nut and bent the washer (114).
6.4.2. Port 3” and over
6.4.2.1. First couple the seat with the cage, insert
the plug assembled with the flange (111)
without the c-ring seal.
6.4.2.2. Measure from the top of the cage to the
ring nut (dimension A) as shown in figure
25.
6.4.2.3. Repeat the measure mounting the c-ring
seal with the opening top side (dimension
B) as shown in figure 25. If the difference
A-B is within the one in Table 12, tighten
the nut (112) and bent the washer (114).
Figure 25
Port (in.)
1½÷2
3÷8
10÷24
A-B (mm)
0.9÷1.8
1.7÷2.9
2.3÷3.7
Table 12
Figure 24

- 19 -
MAN0038E / rev.6
Figure 26 Figure 27
Figure 28 Figure 29
Figure 30
Item
Part name
32
SEAL RING
46
ENERGIZER
47
SEAL RING
48
SEAL RING
49
ROD SEAL
51
OR
52
SEAL RING
110
SEAL RING
111
PLUG FLANGE
112
BOLT
113
RING NUT
114
WASHER
Table 13

PARCOL S.p.A. Via Isonzo, 2 –20010 CANEGRATE (MI) –ITALY
Telephone: +39 0331 413 111 –Fax: +39 0331 404 215
This manual suits for next models
1
Table of contents
Popular Control Unit manuals by other brands
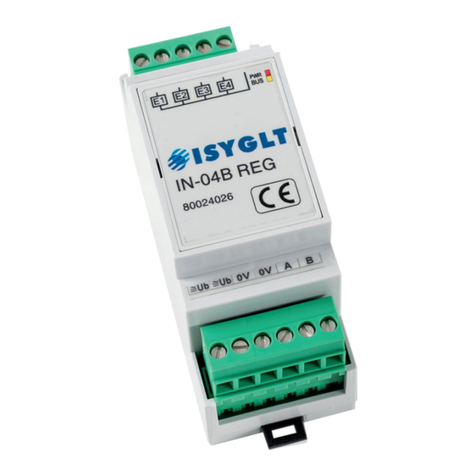
Seebacher
Seebacher ISYGLT IN-04B REG Technical Data/Instruction Manual
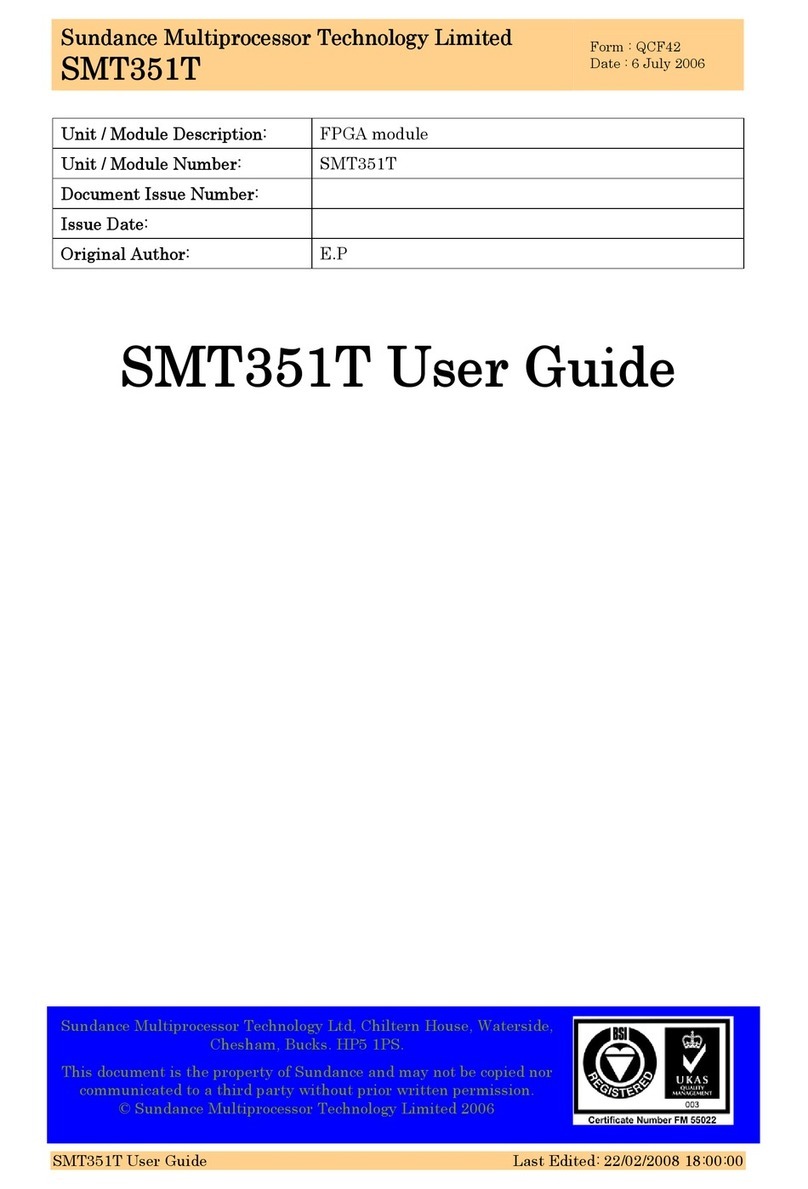
Sundance Technology
Sundance Technology SMT351T user guide
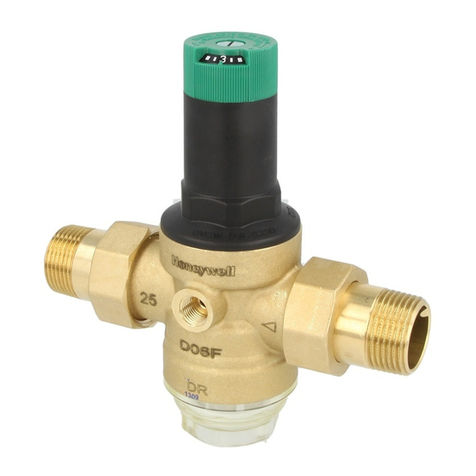
Honeywell
Honeywell D06F installation instructions
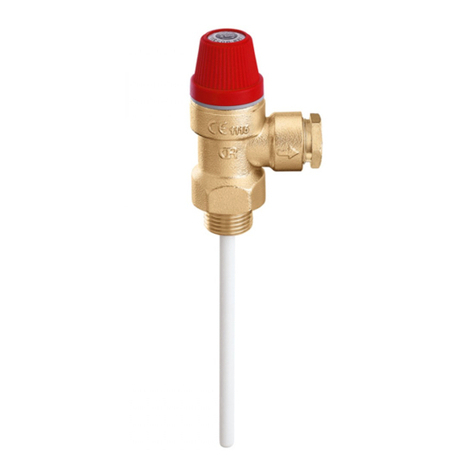
CALEFFI
CALEFFI 309 Series quick start guide

marklin
marklin 6021 quick start guide
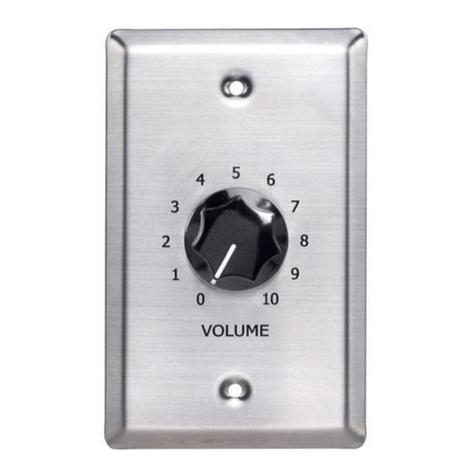
Power Dynamics
Power Dynamics PDVC100 instruction manual
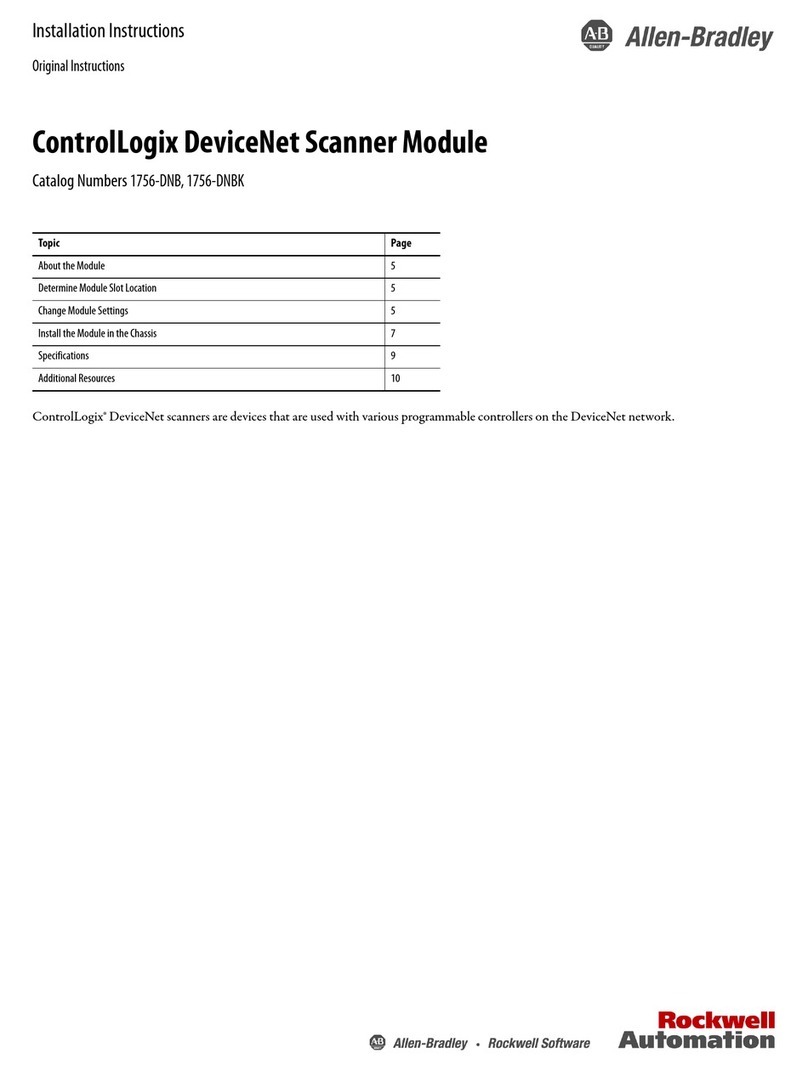
Allen-Bradley
Allen-Bradley ControlLogix DeviceNet installation instructions

Brähler Systems
Brähler Systems DIGIMIC DCen mini MkII quick guide
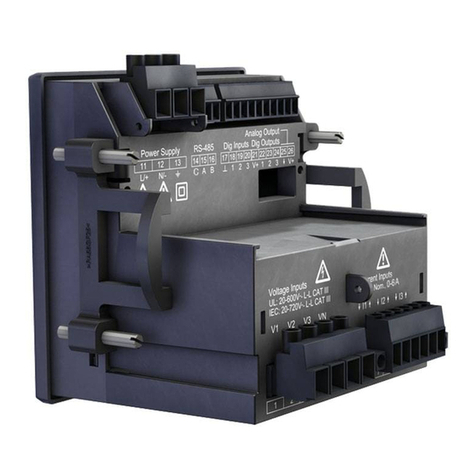
janitza
janitza 96-PTS-60 installation instructions
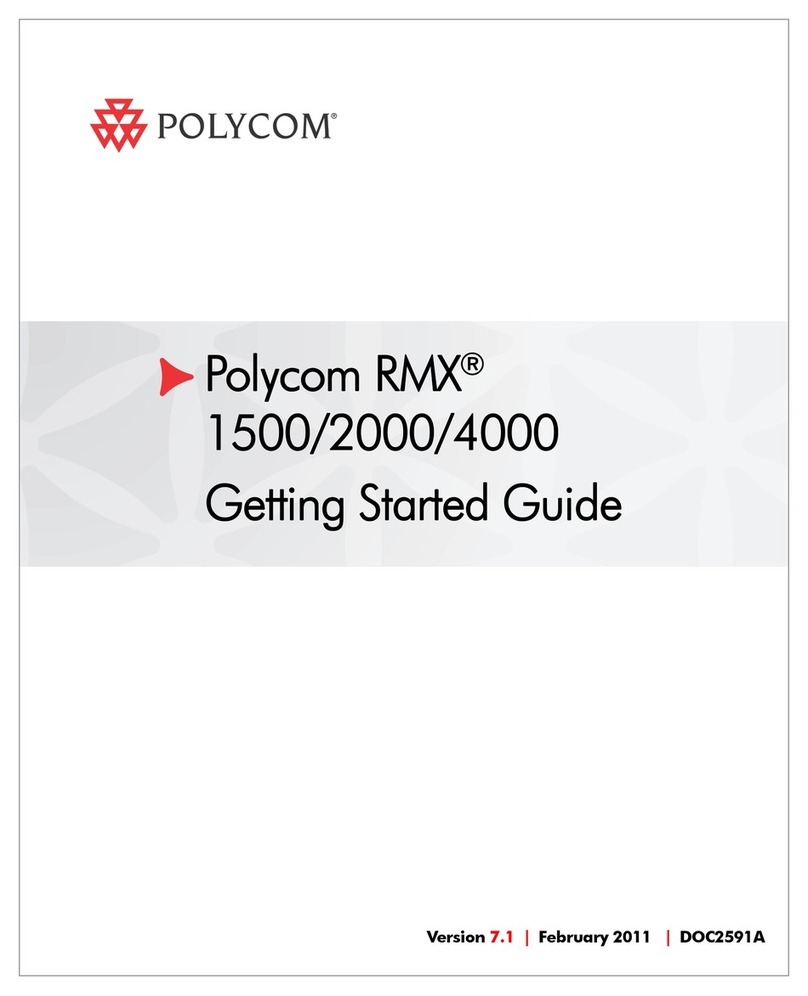
Polycom
Polycom RMX 1500 Getting started guide
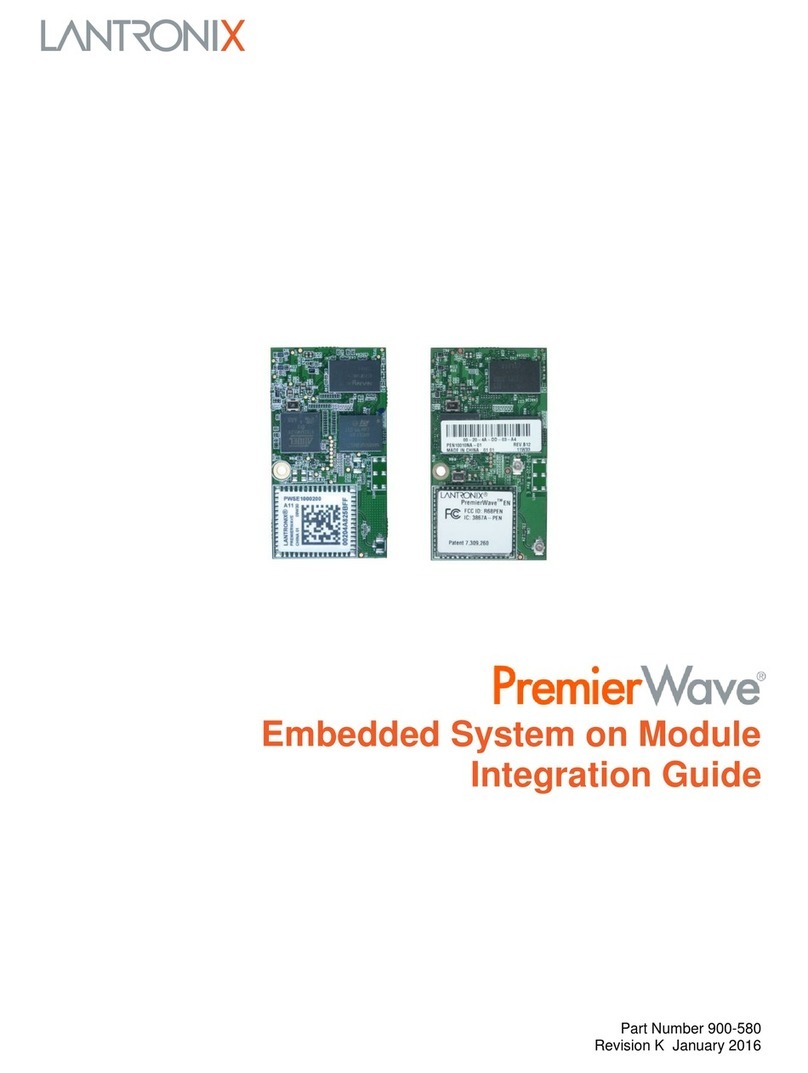
Lantronix
Lantronix PremierWave EN Integration guide
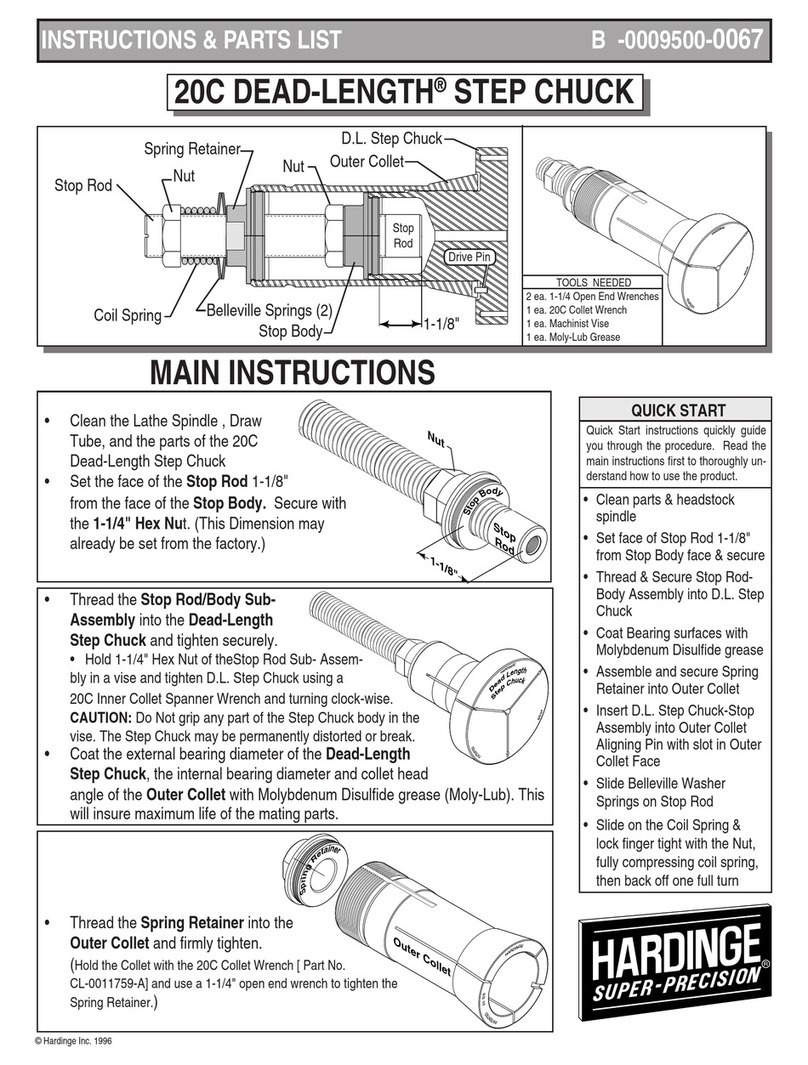
Hardinge
Hardinge 20C Instructions-parts list