Pearl Abrasive WP3000 User manual

Pearl Abrasive Co. 2. 1WET AIR POLISHER
REV. 2
MODEL WP3000
WET AIR POLISHER
OWNER’S/OPERATOR’S MANUAL
Thank you for purchasing the Pearl WP3000 wet
polisher. The WP3000 is the premier wet polisher
for the stone and countertop fabrication trades.
Designed to wet polish natural stone, quartz, and
engineered stone materials, the WP3000 is a high
quality tool engineered for professional users.

– 2–

– 3–
FOR REPAIR INFORMATION, CALL:
Pearl Abrasive Co.: 800-969-5561
Please visit www.pearlabrasive.com for
Authorized Repair Centers
INTENDED USE
This pneumatic tool is designed to be used with a backing pad (flexible
dia) and appropriate abrasive for polishing stones. It should be used
for such applications and within its marked capacity and ratings. Only
accessories specifically recommended by PEARL should be used with
this tool. Use in any other manner or with other accessories could lead
to unsafe operating conditions.
SPECIFICATIONS
MODEL WP3000
Pad Size 4"(100mm) in round
R.P.M. without load 0-5000 RPM
Air Consumption 16CFM at 80-90 PSI
Output 0.24 W
Compressor Output 3.76 W (5 HP)
Max Working Pressure 0.6 MPa (6 bar/90 PSI)
Noise Level 83 dB*
Net weight 1.2 G
*This value is an emission level and is not sufficient risk evaluation.
Manufacture reserves the right to change specifications without notice.

– 4–
CAUTION

– 5–
BOX CONTENTS:
Contents Qty
WP3000 1
Handle 1
Air Hose 1
Exhaust
House 1
Hose Band 1
Air Hose
Joint Assy. 1
Coupler 1
Instruction
Manual 1

– 6–
SAFETY WARNINGS
• Read and understand all safety warnings and instructions. Failure to follow the
warnings and instructions may result in electric shock, fire and/or serious injury.
GENERAL AIR TOOL WARNING
1. Read this instruction manual before use.
2. Do not use the tool for a purpose other than designated by the manual.
3. Do not depress the shaft lock while the tool is rotating. It may cause a serious
injury or damage the tool.
4. eep work area clean and well lit. Cluttered or dark areas invited accidents.
5. Always wear personal protective equipment such as safety goggles, hearing
protectors and dust mask or respiratory protective equipment (PPE).
6. Follow ANSI Z87.1 or local/national standards for eye-wear and other
personal protective equipment requirements. Everyday eyeglasses are not
safety glasses.
7. Exposure to certain chemicals in dust generated from workpiece and/or
abrasive materials can result in lung damage and other physical injury. Your
risk of exposure varies, depending on how often you do this type of work. To
reduce your exposure to dust, work in a well-ventilated area and work with
approved safety equipment designed to filter out microscopic particles.
8. Dress properly. Do not wear loos clothing or jewelry as they can be caught
in moving parts. Contain long hair with a cap or a hair cover.
9. When operating an air tool outside, always wear gloves, safety shoes
(preferably non- skid) and hard hat.
10. Use sound insulation walls if required by your local provisions and
regulations.
11. Stay alert, be careful with what you are doing when operating an air tool. Do
not use tool while tired or under the influence of drugs, alcohol or medication.
12. Do not overwork and have a rest before you get too tired.
13. Always check ration direction before use.
14. Never place you hand or face near the rotating accessory
15. Do not operate the tool continually at full throttle without a work load on the
tool.
16. Do not dismantle or modify the tool.
17. Do not direct the tool towards bystanders and/or animals. Fragments of
workpiece or of a broken accessory may fly away and cause injury. eep
bystanders out of work area.

– 7––
18. Do not abuse the hose. Never use the air hose for carrying. The tool can
start suddenly and may cause injury. eep the air hose away from sharp
edges.
19. Do not use damaged air hose. Damaged air hose increase the risk of
accident.
20. Never work near inflammable liquid or in a highly explosive area.
21. Make sure that the tool is off before connecting to the air compressor.
22. Always disconnect the tool from air supply before removing any accessory
or maintenance work.
23. Do not force tool. Use the correct tool for your application. The correct tool
will do the job better and safer.
24. If any physical hand/wrist discomfort is experienced, stop work promptly and
seek medical attention. Hand, wrist and arm injury may result from repetitive
work, motion and overexposure to vibration. Thake frequent rest and limit
daily time of use.
25. Handle the tool with care. Dropping the tool on a ground, crashing it into
objects any cause the tool to deform and crack.
26. Use only an air compressor. Use of high pressure gas other than an air such
as an oxygen and acetylene will increase the risk of explosion.
27. Pneumatic tool’s exhaust air contains oil and contaminated moisture. Make
sure it is not directed towards you or anyone within the work area.
28. Do not overreach. eep proper footing and balance at all times.
29. When working at height, make sure that nobody in underneath, and ensure
also that the tool is kept on a stable platform.
30. Always inspect wires and pipes inside the workpiece. Carefully use the tool
so that the rotating part will not contact them. The rotating part contacting
electric wires and gas pipes while operating the tool will increase the risk of
electric shock and gas leak.
31. When polishing, pay attention to dust and sand on the surface of polishing
pad or polishing buff, so that they do not leave scratches on the workpiece.
32. Do not press the tool too hard against the workpiece. It is not only inefficient
but also may cause damages to the tool.
33. Never lay the tool until the accessory has come to a complete stop.

– 8–
SPECIFIC WARNINGS FOR WP3000
1. Only qualified/trained operators should use this tool.
2. Use clamps etc. to secure and support the workpiece.
3. Use accessories made for pneumatic tools.
4. Hold the tool firmly, especially when starting.
5. When using polishing pads with Velcro, always ensure that the pad is fixed
centrally to the backing pad.
CAUTION
1. Do not abuse the tool. Do not throw, drop or shock the tool.
2. Do not carry the tool by the air hose, and at the same time, do not pull it to
disconnect.
3. Do not cover or block an exhaust. Blocked exhaust prevents the tool from
working properly. Also, never direct exhaust air towards bystanders and/or
animals.
4. Dress properly
5. Do not wear loose fitting clothing or jewelry that could be caught in moving
parts.
6. Do not cover or block exhaust. Blocked exhaust prevents the tool from
working properly.
7. Immediately stop operating the tool if you feel the tool is not working
correctly. If damaged have the tool serviced.
8. Stay alert, be careful while operating this tool. Do not use tool while tired or
under the influence of drugs, alcohol, or medications.
SPECIFIC CAUTION FOR MAINTENANCE
1. Immediately stop operating the tool whenever you fell that the tool is not
working properly. If damaged, have the tool serviced.
2. Use appropriate pressure. Excessively high pressure will increase the
number of revolutions or strokes causing potential failure and accidental
injury.
3. Use only identical replacement parts when servicing.
4. Do not store unused accessories and tools in an area where temperature
changes a lot and/or under the direct sunlight. Store them in a dry area and
out of reach of children.

– 9––
5. Inspect tool before use; check if parts and accessories are free from
damage.
6. Do not use damaged accessory.
7. Never use solvents or other harsh chemicals to clean the non-metallic parts
of the tool.
8. Before use each day place 2-3 drop of pneumatic tool oil in the air inlet of
the tool. Run tool for 2-3 seconds to allow moving parts to become
lubricated. Lubricating the tool before and during work is not needed.
Excessive oil will turn into a tar-like substance inside the tool, causing the
vanes to stick in the rotor and slow the tool down.
9. At the end of the shift disconnect air and water line and hang the tool upside
down to allow any water to drain from the tool.
10. Clean coupler fittings on air hoses so that a motor will not ingest powder
dust and sand. Also, use clean water from a tap.
11. If you notice deformation of a backing pad in any way, discontinue its use
and replace the backing pad.
12. Do not submerge the tool in water. This will expose the inner moving parts
to moisture that will shorten the life expectancy.
13. Do not leave accessories attached to the threads of the spindle. This can
result in damage to the spindle or accessory. Excessive force to the spindle
trying to remove corroded accessories could damage the gears and
bearings.
14. If you notice any abnormal noise or vibration when operating the product,
immediately discontinue its use. Inspect and replace any damaged parts. If
abnormal noise or smell persist, return the machine for service or repair.
15. For further operational and handling information or for replacement of parts
and components, please contact the agent from whom you purchased the
tool.

– 10 –
SPECIFIC CAUTION FOR AIR SUPPLY
1. Use a clean lubricated air supply that will give a measured pressure at the
tool of 87 PSI/6 bar (0.6 MPa)
2. Air pressure for this tool MUST NOT exceed 87 PSI/6 bar (0.6 MPa);
excessively high air pressure will increase the number of revolutions causing
not only potential failure or breakage but could also lead to an unexpected
accident or injury.
3. Equip the air compressor with a replaceable filter that can be easily cleaned.
4. Use safety shuttle valves so air flow can be stopped in case of a line break.
5. Use anti-whip devices across hose couplings to prevent hose from whipping
in the event of hose failure or coupling disconnect.
6. Regularly clean the tool’s air vents.
7. Connect the tool to the air supply as shown in Figure 1.
ABOUT AIR PRESSURE AND VOLUME
1. The manufacturer specification on the tool is 5000 PM at 80-90 PSI.
Pressure over 90 PSI exceeds the max speed rating for the rotor bearings
that could potentially cause them to overheat and lock.
2. The air consumption of this polisher is very important. This tool requires 16
CFM (cubic feet per minute) for the tool to run at a constant speed. Each
additional tool that is attached to an air compressor will require 16 CFM.
ABOUT SILENCER
1. To comply with OSHA code 1926.52 Noise exposure Standard, this polisher
comes fitted with and internal silencer. When operated within factory
specifications (80-90 PSI @ 16 CFM) the silencer bring the noise to less
than 84 db. The silencer also provides back pressure to help assure that you
are getting a constant RPM level.

– 11 –
ABOUT SHAFT LOCK SYSTEM
1. WP3000 is equipped with a Shaft Lock System,
which promotes replacement of polishing pads
by replacing backing pads.
2. With traditional method with Velcro, often
polishing pads were attached off –center, i.e.
away from the spindle, and this affected the
drive shaft and damaged a bearing and a gear.
3. Since Shaft Lock System makes it easier to
replace backing pad, you can simply replace
backing pad to change polishing pad.
4. A shaft lock button, indicated in Figure 2, is provided to prevent the spindle
from rotating when installing or removing a backing pad. To engage the lock,
depress the button and rotate the spindle until you are unable to rotate any
further.
HOW TO REPLACE THE BACKING PAD
1. Hold the tool with the backing pad facing
upwards.
2. Rotate the backing pad anti-clockwise,
until you cannot rotate any further.
3. Detach the backing pad from the spindle.
4. Place a new backing pad onto the
spindle
5. Rotate the backing pad clockwise, until
you cannot rotate any further.
Then rotate a backing pad counter-
clockwise.
Do not depress the shaft lock while the tool
is rotating. It may cause a serious injury
or Saguchi Global damage the tool.
CAUTION
Fig. 2

– 12 –
WET AIR POLISHER TOOL PREVENTATIVE
MAINTENANCE AND SOLUTIONS
Learn how to prevent the 5 most common issues
that cause pneumatic tool failures
1. RUNNING THE TOOL IN E CESS OF THE
RECOMMENDED 85 PSI OPERATING PRESSURE.
The Pearl WP3000 are designed to run at or below 87 PSI. This
operating pressure is derived from the optimum speed and torque
needed for most polishing applications, while staying below the
maximum speed rating of the rotor bearings. By raising and lowering
the air pressure, you change the speed at which the tool will run.
The power or torque comes from the CFM or volume of air. If your
compressor’s CFMs are under-sized, your pressure will drop once
the reserve in your tank is depleted. Raising the pressure to 100
PSI and higher will raise the RPM of the tool. At this point, you are
reaching or exceeding the maximum
speed rating of the 516-18 bearing of
28,000 RPM, causing it to heat up
and wear out prematurely.
Sudden changes in speed will
also cause premature wear on
the bearing, so you should turn
the air on and off slower to allow
the bearing time to accelerate
and decelerate. Fig. 1: Worn Bearings

– 13 –
2. CONTAMINATION AND WATER GETTING
INSIDE THE TOOL
One of the big differences between the Pearl WP3000 and others,
is that our polishers are all steel inside. Air oil should be used to
treat the steel inside the tool and prevent it from rusting when not in
use. If water and contamination is allow to enter the tool, it will
shorten the life of the vanes and bearings inside the rotor assembly.
Contamination in the air will get into the vane slots on the rotor and
cause the vanes to stick and stop floating.
3. E CESSIVE OILING OR USING THE
WRONG TYPE OF OIL
The Pearl WP3000 oil is designed to coat the inside of the tool and
prevent it from rusting when the tool is not in use. For this tool to
work effectively, we recommend adding the oil at the end of the day.
The oil is not needed to run the tool, it is only added to prevent the
tool from rusting. Adding the wrong oil or excessive oiling of the tool
can cause a tar-like build-up inside the tool, causing the vanes to
also stick in the rotor assembly.
* Air line lubricators are not recommended due to the excessive
amount of oil.

– 14 –
4. E CESSIVE DOWNWARD PRESSURE APPLIED
DURING POLISHING
The WP3000 has four vanes in the rotor assembly which are used
to trap the air and convert air flow into the torque needed to run the
tool. In a no-load condition, the rotor will turn between 20,000 to
22,000 RPM, which allows the spindle shaft to turn at 4,000 RPM
to 4,400 RPM. Under light downward pressure the rotor will slow
down to 18,000 to 19,000 RPM, and the spindle will turn at 3,600
RPM to 3,800 RPM. As the rotor and vanes turn inside the tool, it
goes through a power and vent cycle. During the power cycle, the
vanes extend out from the rotor and the air pushing on the front
side, cause the rotor to turn. About a quarter of the way through
the rotation, that same vane transitions into the vent cycle and the
air is exhausted from the tool. Therefore, one to two vanes are
always loaded under pressure and creating the torque needed to
turn the rotor. When excessive downward pressure is applied to the
tool, the vanes will rub against the rotor on the backside causing a
groove to form as the vane is pushed back into the rotor under
pressure.
Over time, half of the vane
will become worn away in
the grooved area causing
the vane to become brittle
and crack, or splinter along
the groove line. When the
vane splinters, as shown in
vane 4 in Figure 2, it is the
pieces of the vane that
break off that get trapped
between the rotor and the
cylinder causing the tool to
lock up. Excessive down-
ward pressure will also
cause premature wear on
the gears.
Fig. 2:
1. New vane
2. Used vane with no grooves
3. Used vane with grooves
4. Used vane cracked along the groove

– 15 –
5. HAMMERING OF THE TOOL INTO THE STONE
During the process of polishing and/or core drilling, you should
slowly apply the polisher to the stone. Hammering or quickly
impacting the polisher into the stone will cause the spindle to go
from 4,000 RPM to 2,000 RPM or lower. This sudden impact will
cause the gears to wear out and/or chip. This impacting is also
evident by the play and indentation found on the woodruff key for
the spindle gear.
Please note: while core drilling, the gears can start to wear out
or chip and the tool can continue to run for a week or two before
locking up.
To avoid some of the previously described potential issues, Pearl has
created Filter/Regulator (F/R) manifold systems. These F/R manifold
systems consist of a Filter/ Regulator with a shut off/dump valve, and a
aluminum manifold with two or more aluminum quick disconnects. The
filter/regulator will allow you to set the pressure at 85 PSI, remove and
dump any water from your air, and remove contamination down to five
microns. These new manifold systems and parts are available through our
distributor network, and via our website.

– 16 –
PEARL WP3000
(WATERFEED SYSTEM WITH CLEAR HOSE)
REPLACEMENT PARTS LIST

– 17 –
PEARL WP3000
(WATERFEED SYSTEM WITH CLEAR HOSE)
REPLACEMENT PARTS LIST

– 18 –
PEARL WP3000
REPLACEMENT PARTS LIST

– 19 –
PEARL WP3000
REPLACEMENT PARTS LIST
60 876752 Muffl r 2
61 876753 Wat r Hos Joint Assy 1
62 876754 Air Hos Joint Assy 1
63 876755 Wat r Hos Joint Assy 1
64 876756 Packing 1
90 876750 Exhaust Hos 1
A1 876757 Coupl r 1
*Parts may b chang d with/without notic .

WP3000MANUAL • ©P arl Abrasiv Co., Comm rc CA • 01/18
East Coast:
Romedy Tool Repair - 770-932-8175
121 Price Hills Trail, Sugar Hill, GA 30518
West Coast:
Pearl Abrasive Co. - 800-969-5561
4900 Zambrano Street, Commerce, CA 90040
LIMITED TIME WARRANTY OF PEARL WP3000
Pearl Abrasive Co. warrants this product against material defect and
defective workmanship for a period of 90 days from original purchase.
Proof of purchase will be required. If Pearl receives notice of defective tool,
under this warranty our obligation is limited to the repair or replacement of
parts, without charge. This does not apply to accessories.
For warranty claims, send the complete tool to:
Table of contents
Popular Sander manuals by other brands

Chicago Pneumatic
Chicago Pneumatic CP7859 Operator's manual

Craftsman
Craftsman 315.116900 Operator's manual
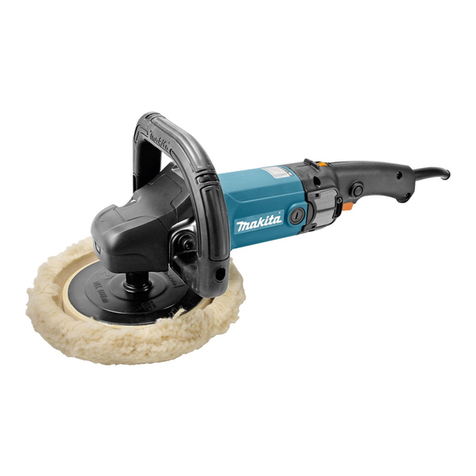
Makita
Makita 9237CB technical information

Jula
Jula Meec tools 210-255 operating instructions
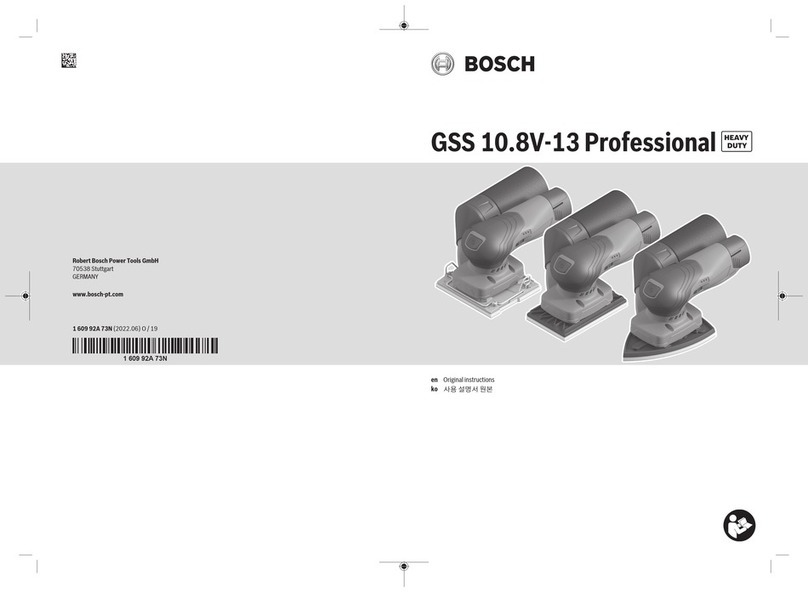
Bosch
Bosch Professional GSS 10.8V-13 Original instructions

Stanley
Stanley FATMAX SFMCW221D1 Original instructions