Makita 9237CB Manual

Model No.
Description
PRODUCT
CONCEPT AND MAIN APPLICATIONS
P 1/ 14
Specification
Dimensions: mm (")
Width (W)
Height (H)
Length (L) 431 (17)
198 (7-3/4)
187 (7-3/8)
9237C/ 9237CB
Polisher 180mm (7")
Models 9237C/ 9237CB have been developed based on 9227C/ 9227CB.
In addition to the benefits of the current models, 9237C/ 9237CB feature
the following value-adding benefits:
• Loop handle with elastomer soft grip
• Elastomer bumper on gear housing
• Vent dust cover for protection from ingress of wool fibers
The only specification difference between 9237C and 9237CB is
the method of protection against electric shock:
9237C: Grounding
9237CB: Double insulation
W
L
110 50/6010 1,100 580 1,600
120 50/6010 --- 580 1,600
220 50/605.7 1,200 710 1,800
230 50/605.5 1,200 710 1,800
Continuous Rating (W)
Voltage (V) Cycle (Hz) Input Output Max. Output (W)Current (A)
Standard equipment
Optional accessories
Note: The standard equipment for the tool shown above may vary by country.
Loop handle or Side grip .........................................1
Hex wrench 6 . ........................................................1
M8x25 Hex socket head bolt ...................................1 (for some countries)
Sleeve 18 .................................................................1 (for some countries)
Wool pad 180 ..........................................................1 (for some countries)
Wool bonnet 180......................................................1 (for some countries)
Rubber pad 170........................................................1 (for some countries)
Sanding lock nut ......................................................1 (for some countries)
Lock nut wrench 28 .................................................1 (for some countries)
240 50/605.3 1,200 710 1,800
*1 The indication of rpm on Name plate is ‘3,200 min.ˉ¹’.
*2 with Loop handle
Specification Model No.
No load speed: min.ˉ¹=rpm
Diameter of pad: mm (")
Protection against electric shock
Power supply cord: m (ft)
Weight according to
EPTA-Procedure 01/2003*2: kg (lbs)
9237C 9237CB
180 (7)
Europe, Korea: 4.0 (13.1)
Brazil, Chile, Peru, Oceania: 2.0 (6.6)
Other countries: 2.5 (8.2)
0 - 600/3,200
*1
Double insulationGrounding
Yes
Yes
Constant speed control
Variable speed control by dial
Soft start
Electronic
control
Yes
(600 - 3,200 min.ˉ¹)
3.4 (7.5)
Grip 36 complete (for 9237C)
Grip 37 (for 9237CB)
Wool pad 180
Wool bonnet 180
Sanding lock nut
Rubber pad 170
Lock nut wrench 28
Wrench 17
TECHNICAL INFORMATION
H

P 2/ 14
[1] NECESSARY REPAIRING TOOLS
CAUTION: Repair the machine in accordance with “Instruction manual” or “Safety instructions”.
Code No. Description Use for
1R026 Bearing setting pipe 16-8.2 removing Spindle from Spiral bevel gear 52
1R005 Retaining ring R pliers RT-2N removing Retaining ring R-32
1R027
1R032
1R217
Bearing setting pipe 18-10.2 removing Ball bearing 6201LLB
removing Spiral bevel gear 52
1R258
1R268 Spring pin extractor M3
1R269
1R283 Round bar for arbor 9-50 removing Spindle from Spiral bevel gear 52
1R291
1R350 Ring 60 holding Gear housing when removing Shaft lock pin
V block holding Bearing box when removing Ball bearing 6201LLB
supporting Bearing box when removing Spiral bevel gear 52
[2] LUBRICATION
Apply Makita Grease SG No. 0 to the portions designated with the black triangle to protect parts and product
from unusual abrasion.
And apply Isoflex NB52 to the portion designated with the gray triangle.
Fig. 1
Item No.
18 Gear housing complete Gear room where Spiral bevel gear 52 engages with Armature’s gear.
38
Bearing box
Controller
Handle set L
Handle set R
Armature
Spiral bevel gear 52
Dial 28 apply Isoflex NB52 to Cam portion. a little
25g approx.
Description AmountPortion to lubricate
Bearing setting plate 8.2
Bearing extractor removing Ball baring 608 and Ball bearing 6201LLB
Retaining ring S & R pliers removing Retaining ring S-12
Ring 22
Repair
removing Shaft lock pin
38
18

Motor housing set
P 3/ 14
Fig. 2
[3] DISASSEMBLY/ASSEMBLY
[3] -1 Armature
DISASSEMBLING
Loop handle 4x12 Tapping screw (2 pcs.)
(1) Separate Gear housing and Armature entirety from Motor housing set as drawn in Fig. 2.
Note: Without removing Handle L, Stop ring E-6 on Armature rear side, and Magnet sleeve on Armature rear side,
it is impossible to pull out Armature from Motor housing.
1. Remove Carbon brushes, Pad 165 and
Loop handle or Grip 36 from the machine.
4. Unscrew four 5x35 Tapping screws from
the machine.
Note for 9237C only:
Unscrew M4x8 Pan head screw to remove
Lead unit in this step.
5. Pull out Gear housing and Armature from
Motor housing set.
And unscrew four 4x16 Tapping screws
from Gear housing complete.
3. Remove Stop ring E-6 and Magnet sleeve from
Armature shaft end while shifting Controller.
2. Remove Head cover by unscrewing two 4x12
Tapping screws. And remove Handle set L
by unscrewing four 4x18 Tapping screws.
6. Remove Bearing box from Gear housing complete.
Pad 165
Carbon brush
Carbon brush
Repair
Grip 36
Stop ring E-6 Magnet sleeve
Controller
5x35 Tapping
screw (4 pcs.)
4x16 Tapping
screw (4 pcs.)
M4x8 Pan head screw (1 pc.)
Controller
Gear housing
complete
Gear housing complete
Armature
Bearing box
Handle set L
4x18 Tapping
screw (4 pcs.)
Head cover Note: No need to unscrew this
4x18 Tapping screw.

4. Remove Ball bearing 608LLB from the commutator end
of Armature assembly using with 1R269.
And then, remove Insulation washer.
Leg of 1R269
P 4/ 14
Fig. 3
Fig. 4
[3] DISASSEMBLY/ASSEMBLY
[3] -1 Armature (cont.)
DISASSEMBLING
(2) Remove Armature from Gear housing complete as drawn in Fig. 3.
(3) Remove Bearing retainer 48 and Ball bearings from Armature as drawn in Fig. 4.
1. Remove M5x12 Pan head screw from Bearing
box side of Gear housing complete.
Remove M5x16 Pan head screw from the top
side of Gear housing complete.
2. Pull out Armature section from Gear housing
complete.
Repair
M5x16 Pan
head screw
Retaining
ring S-12
1. Remove Retaining ring S-12 from
Armature shaft end using with 1R291.
2. Remove Ball bearing 6201LLB from Armature assembly
while gripping the legs of 1R269 with Water pump pliers.
3. Remove
Bearing retainer 48 from
Armature
assembly.
M5x12 Pan
head screw
Bearing
box side Top side
Gear housing
complete Armature
Ball bearing 6201LLB
Ball bearing
6201LLB
Ball bearing 608LLB
Insulation washer
Bearing retainer 48
Bearing retainer 48
Ball bearing
6201LLB
Water pump pliers

Gear housing
complete
groove
groove
notches
Fig. 5
Fig. 6
ASSEMBLING
(1) Assemble Bearing retainer 48 to Armature assembly as drawn in Fig. 5.
Repair
Bearing retainer 48Assemble Bearing retainer 48 to Armature
while facing its collar side to Armature’s fan.
2. Tighten Bearing retainer 48 with M5x16 Pan head
screw on the back side and M5x12 Pan head screw
on Bearing box side.
3. Assemble Bearing box section to Gear housing
complete with four 4x16 Tapping screws.
4. Assemble Gear housing complete while aligning Spindle to Switch trigger.
Collar Retaining ring S-12
Ball bearing 6201LLB
Ends of
Bearing retainer 48
1. Aligning the ends of Bearing retainer 48
to the groove of Gear housing complete,
assemble the armature section into
the housing until the ends of the retainer
are fit in the notch of the housing.
(2) Assemble Armature section to Gear housing complete as drawn in Fig. 6.
M5x16 Pan head screw
M5x12 Pan head screw
Bearing
box side
Switch trigger
Top side Gear housing
complete
Bearing box
Armature
Spindle
Gear housing
complete
Motor housing set
P 5/ 14
[3] DISASSEMBLY/ASSEMBLY
[3] -1 Armature (cont.)

P 6/ 14
Fig. 7
Fig. 8
[3] DISASSEMBLY/ASSEMBLY
[3] -2 Spiral bevel gear 52, Ball bearing 6201LLB
DISASSEMBLING
(1) Disassemble Spiral bevel gear 32 and Spindle from Bearing box as drawn in Fig. 7.
(2) Disassemble Ball bearing 6201LLB as drawn in Fig. 8.
Repair
1. Separate Bearing box section by unscrewing
four 4x16 Tapping screws.
1R026 or 1R032
1R217
1R217
Bearing box
2. Receive Bearing box section on 1R217, and put 1R026
or 1R032 on Spindle end. Then, push down Spindle
with Arbor press.
3. Press down Spindle from Bearing box section with 1R283.
Then, remove Spiral bevel gear 32 and Labyrinth ring.
1R283
Bearing box
Spiral bevel gear 32
Spindle
Retaining ring R-32
Bearing box
1. Remove Retaining ring R-32 from
Bearing box using with 1R005.
1R005
1R258 1R258
1R027
2. Put Bearing box onto 1R258 as shown below.
Press down Ball bearing 6201LLB from Bearing box
with 1R027.
Note: Ball bearing 6201LLB is damaged by the removal process.
Do not re-use the removed one.
Ball bearing 6201LLB
Labyrinth ring

P 7/ 14
[3]-3 Shaft lock mechanism
ASSEMBLING
DISASSEMBLING
Repair
Fig. 9
(1) Assemble Labyrinth ring to Spindle as drawn in Fig. 9.
(2) Assemble the rest of parts by reversing the disassembly procedure. (Refer to Figs. 8 and 7.)
Labyrinth ring
Put Labyrinth ring into Spindle while facing the collar portion
to the reverse side of threaded portion.
Collar portion
Spindle
Threaded portion
While applying 1R268 to Shoulder pin 9 through the small hole
on Pin cap, tap 1R268 with a hammer.
Now, Shoulder pin 9 comes out from Gear housing complete.
Shoulder pin 9
Pin cap
Pin cap
Pin cap
Compression
spring 8
1R268
1R350
Fig. 10 Fig. 11
(1) Separate Gear housing and Armature assembly from Motor housing set as drawn in Fig. 2.
(2) Separate Armature assembly from Gear housing complete as drawn in Fig. 3.
(3) Disassemble Shaft lock mechanism as drawn in Figs. 10 and 11.
[3] DISASSEMBLY/ASSEMBLY
[3] -2 Spiral bevel gear 52, Ball bearing 6201LLB (cont.)
Note: Do not re-use removed Pin cap
because removal one damages
the inside surface of the cap,
producing plastic dust.
Release 1R268 from Pin cap carefully
so that Pin cap will not pop out by
Compression spring 8.

P 8/ 14
[3] DISASSEMBLY/ASSEMBLY
[3]-3 Shaft lock mechanism
ASSEMBLING
Repair
Fig. 12 Fig. 13
(1) Be sure to use a new Pin cap for replacement and to eliminate all the plastic dust on Shoulder pin 9. (Fig. 12)
(2) Assemble the Parts for Shaft lock mechanism as drawn in Fig. 13.
Plastic dust
Shoulder pin 9
Shoulder
pin 9
2. Assemble a new Pin cap by pressing
it to Shoulder pin 9.
Note: Do not forget to assemble
Compression spring 8.
1. Insert Shoulder pin 9 through
the hole of Gear housing
complete.
Pin cap
Compression
spring 8

Circuit diagram for 9237C
P 9/ 14
Fig. D-1
Yellow
Color index of lead wires' sheath
Black
Red White
Blue Green
Orange
Transparent
Field
Terminal block
Power supply cord
Connector 2-SD
Choke coil
(if it is used.)
Polyolefin tube
Noise suppressor
(if it is used.)
Blue lead wire is used for some
countries in stead of white.
Brown lead wire is used for some
countries in stead of black.
Green/ yellow lead wire
is used for some countries
in stead of green.
[View from Commutator side]
Controller
Switch

Wiring diagram for 9237C
Wiring from Motor housing set
P 10/ 14
Name plate
Field lead wire (black)
Field lead wire (black) and Brush holder’s lead wire (orange) are passed through
the right bottom opening of Name plate side.
Grounding lead wire (green) has to be routed from the center bottom opening.
Grounding lead wire (green)
Brush holder’s lead wire (orange)
5 4 3
Fasten the terminals with M4x8
Pan head screws while facing
the flat side to Terminal block.
Note: Do not bent the terminals.
Connect the receptacles of Controller’s lead wires to Switch terminals
so that Lead wires come to the reverse side of Lock button.
And tilt the connected receptacles as drawn to the left.
Lock button
Terminal block
[Handle set R side]
Wiring to Switch’s Terminals
Wiring to Terminal block
Fig. D-2
Fig. D-3
Fig. D-4
1
flat side
flat side
[Strain relief side]
Symbol of grounding
Assemble Terminal block to
Handle set (R) while facing
the symbol of grounding
to Strain relief side.
Receptacle covered with tube
has to be connected to the
terminal on Lock button side.
Connect Receptacles to Switch terminals 1
while facing the connecting area of Lead wires
to the reverse side of Switch trigger.
Switch trigger

Wiring under Switch
Wiring in Handle set (R)
P 11/ 14
Pin
Strain relief
Rib
Noise suppressor (with three lead wires)
Noise suppressor (with three lead wires)
and Choke coil are put to the place
as drawn above if they are used.
Connector 2-SD
Route Lead wires under Switch and decentralize
them with the ribs and pins of Housing R.
Noise suppressor’s lead wires ( 3 pcs.) must be beyond Switch trigger by routing between the ribs and the pin
of Handle set R near the upper side of Switch.
Come out at least 15 mm long
of Power supply cord from
Strain relief, and clamp the cord
with Strain relief.
Fig. D-5
Fig. D-6
15 mm
Choke coil
Strain relief
Wiring diagram for 9237C
Route Lead wires under Switch
as drawn in Fig. 6.
Be careful not to put Lead wires
on the rib for Terminal block setting.
Set Terminal block to Handle
set (R) as drawn in Fig. D-4.
Fix the following lead wires
in this Lead wire holder.
* Field lead wire (black)
* Brush holder’s lead wire (orange)
* Grounding lead wire (green)

P 12/ 14
Yellow
Color index of lead wires' sheath
Black
Red
Blue
Orange
White
Fig. D-7
Field
Connector
2-SD
Circuit diagram for 9237CB
Power supply cord
Choke coil
(if it is used.)
Polyolefin tube
Noise suppressor
(if it is used.)
Blue lead wire is used for some
countries in stead of white.
Brown lead wire is used for some
countries in stead of black.
[View from Commutator side]
Controller
Switch

P 13/ 14
Name plate
Field lead wire (black)
Field lead wire (black) and Brush holder’s lead wire (orange) are guided out through
the right bottom opening of Name plate side.
Brush holder’s lead wire (orange)
Fig. D-8
Fig. D-9
Wiring diagram for 9237CB
Wiring from Motor housing set
5 4 3
Connect the receptacles of Controller’s lead wires to Switch terminals
so that Lead wires come to the reverse side of Lock button.
And tilt the connected receptacles as drawn left.
Lock button
Wiring to Switch’s Terminals
1
Receptacle covered with tube
has to be connected to the
terminal on Lock button side.
Connect Receptacles to Switch terminals 1
while facing the connecting area of Lead wires
to the reverse side of Switch trigger.
Switch trigger

Strain relief
Rib
Connector 2-SD
Fig. D-10
Fig. D-11
15 mm
Choke coil
Noise suppressor (with two Lead wires)
Strain relief
Pin
P 14/ 14
Wiring diagram for 9237CB
Wiring under Switch
Wiring in Handle set (R)
Noise suppressor (with two lead wires)
and Choke coil are put to the place
as drawn above if they are used.
Route Lead wires under Switch and decentralize
them with the ribs and pins of Housing R.
Noise suppressor’s lead wires ( 2 pcs.) must be beyond Switch trigger by routing between the ribs and the pin
of Handle set R near the upper side of Switch.
Come out at least 15 mm long
of Power supply cord from
Strain relief, and clamp the cord
with Strain relief.
Be careful not to put Lead wires
on these ribs.
Route Lead wires under Switch
as drawn in Fig. 11.
Fix Field lead wire (black) and
Brush holder’s lead wire (orange)
in this Lead wire holder.
Other manuals for 9237CB
8
This manual suits for next models
1
Table of contents
Other Makita Sander manuals

Makita
Makita BO4565 User manual
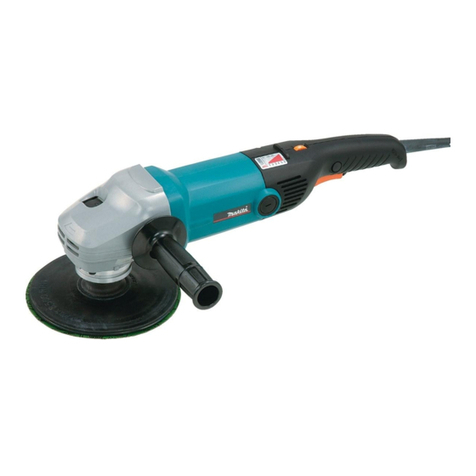
Makita
Makita SA7000C User manual

Makita
Makita 9741 User manual

Makita
Makita DBO480 User manual
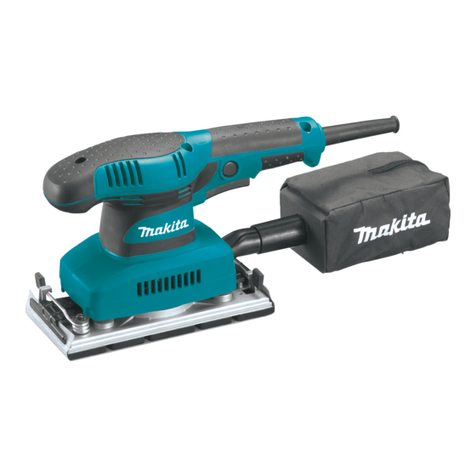
Makita
Makita BO3710 User manual
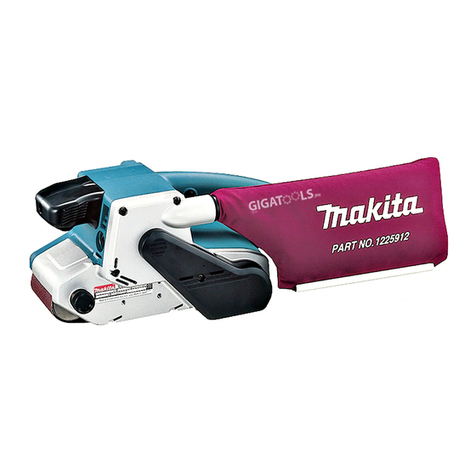
Makita
Makita 9902 User manual
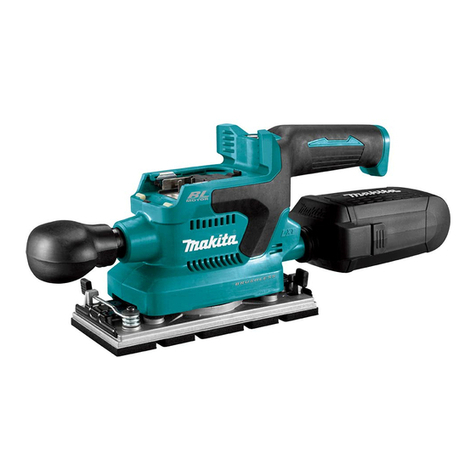
Makita
Makita DBO380 User manual

Makita
Makita M929 User manual

Makita
Makita PV001G User manual
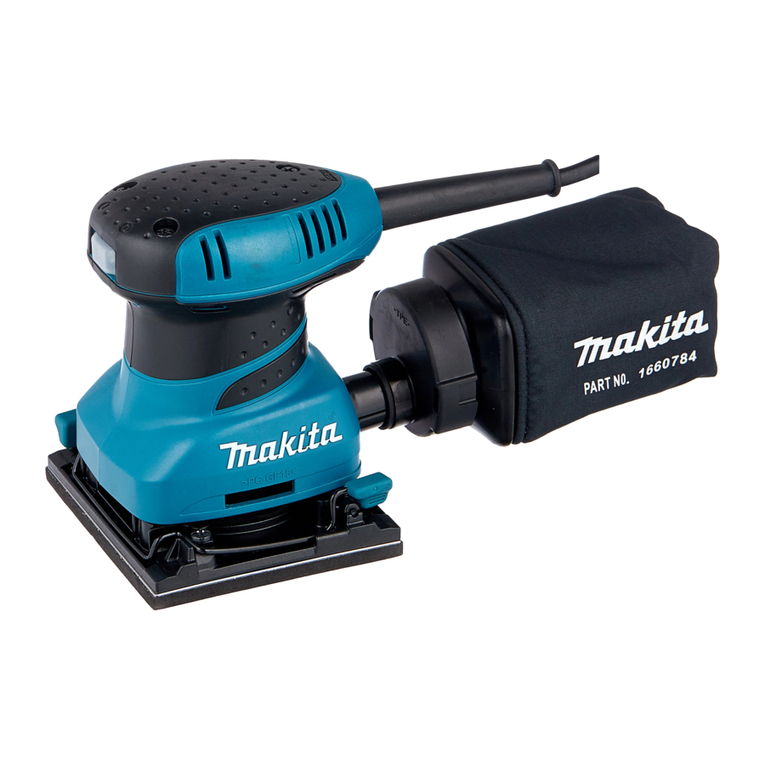
Makita
Makita BO4555 User manual
Popular Sander manuals by other brands
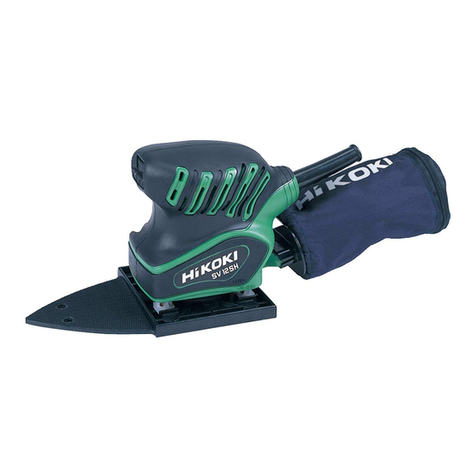
HIKOKI
HIKOKI SV 12SH Handling instructions

NORAUTO
NORAUTO BR7189 Installation Manual and Security Information
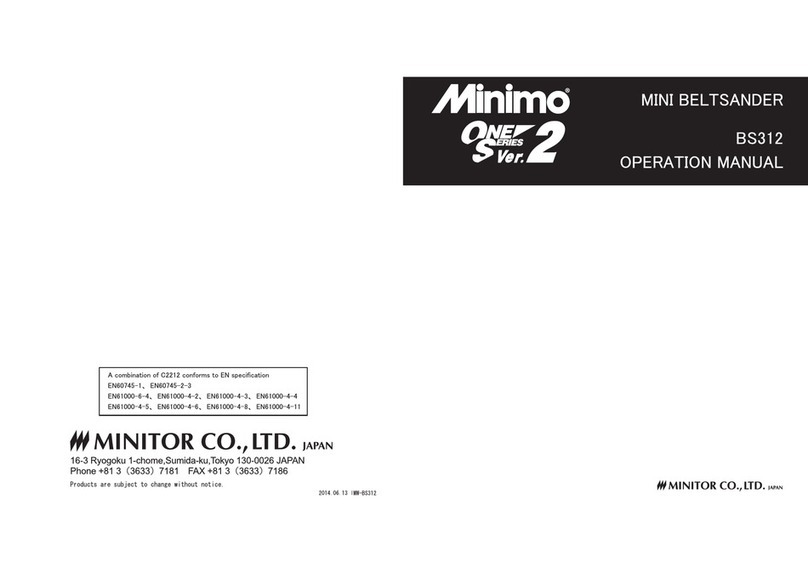
MINIMO
MINIMO BS312 Operation manual
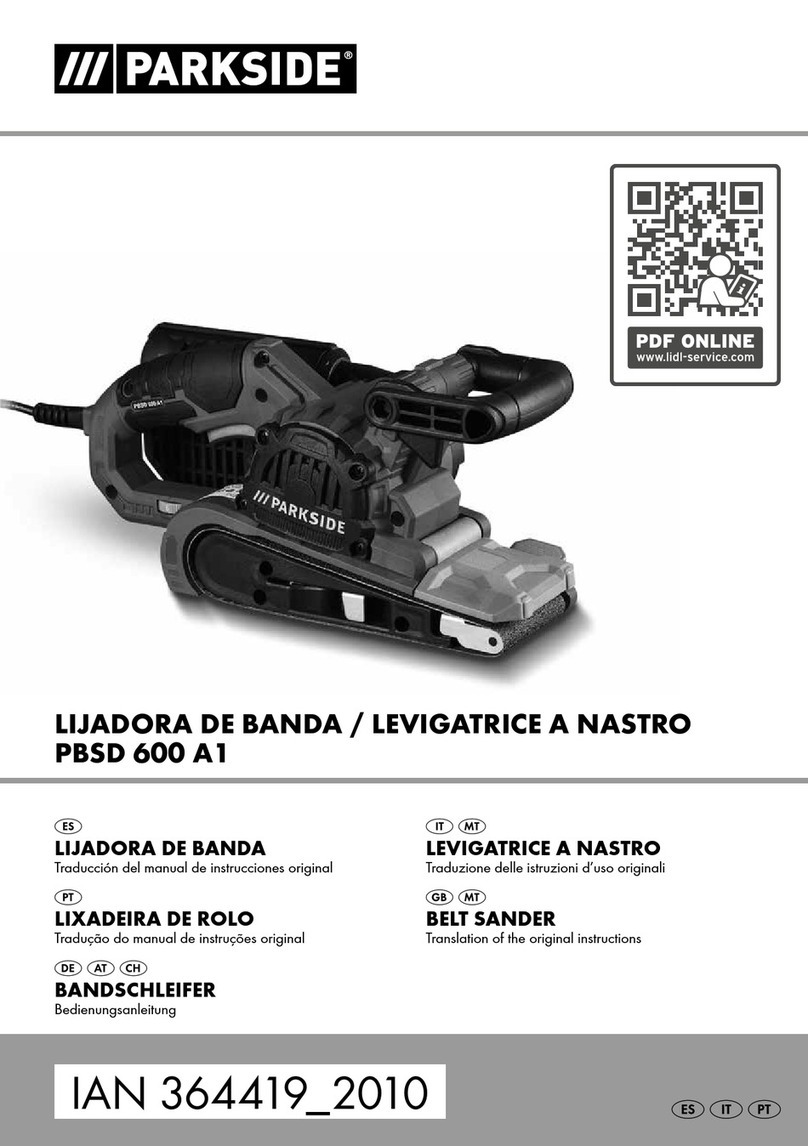
Parkside
Parkside 364419 2010 Translation of the original instructions

PEUGEOT
PEUGEOT EnergySand-127 user manual

Black & Decker
Black & Decker 90518305 instruction manual