Pellas X R16 User manual

1 | S t r o n a


1 | S t r o n a
TABLE OF CONTENTS
1. GENERAL INFORMATION..........................................................................................................................................3
1.1. Transportation..............................................................................................................................................3
1.2. Storage..........................................................................................................................................................3
1.3. Control of burner’s delivery..........................................................................................................................4
1.4. Free space around burner ............................................................................................................................4
2. PRODUCT DESCRIPTION............................................................................................................................................5
2.1. Construction of burner .................................................................................................................................6
2.1.1. Group 1 (R16, R26, R35) .......................................................................................................................6
2.1.2. Group 2 (od R44 do R150) ....................................................................................................................7
2.2. Quality requirements for pellets fuel...........................................................................................................8
2.3. Burner nameplate template.........................................................................................................................9
2.4. Technical data...............................................................................................................................................9
2.5. Safety systems ............................................................................................................................................13
2.6. Technical data of controller, description of functions and burner settings...............................................13
3. INSTALLATION.........................................................................................................................................................14
3.1. Chimney......................................................................................................................................................14
3.2. Boiler / oven ...............................................................................................................................................14
3.3. Fuel hopper.................................................................................................................................................17
3.4. External feeder ...........................................................................................................................................17
3.4.1. External feeder - type 1 ......................................................................................................................17
3.4.2. External feeder - type 2 ......................................................................................................................18
3.4.3. External feeder - type 3 ......................................................................................................................19
3.4.4. Feeder position...................................................................................................................................20
3.5. STB protection ............................................................................................................................................20
3.6. Boiler temperature sensor .........................................................................................................................20
4. BURNER AND FEEDER ASSEMBLY ...........................................................................................................................21
4.1. Installation in boiler....................................................................................................................................22
4.1.1. Mounting scheme for burners from group 1 (R16, R26, R35)............................................................22
4.1.2. Mounting scheme for burners from group 2......................................................................................22
4.2. Mounting of pellet inlet stub......................................................................................................................23
4.3. Connecting the feeder................................................................................................................................24
4.4. Connecting the controller...........................................................................................................................24
5. ADDITIONAL CONNECTIONS AND FIRST STARTUP .................................................................................................24
6. EXPLOITATION AND SAFETY REGULATIONS ...........................................................................................................25
6.1. Exploitation.................................................................................................................................................25
6.2. Maintenance of furnace .............................................................................................................................25

2 | S t r o n a
6.3. Specification of the inspection intervals ....................................................................................................26
6.4. Scope of operational activities ...................................................................................................................26
6.5. Safety regulations referring to installation and exploitation of burner.....................................................27
6.6. Guarantee...................................................................................................................................................27
7. SERVICE OF DEVICES...............................................................................................................................................28
7.1. Photosensor................................................................................................................................................28
7.2. Electrical igniter replacement.....................................................................................................................29
7.3. Feeder pipe cleaning...................................................................................................................................29
7.4. Burner cleaning...........................................................................................................................................29
8. TROUBLESHOOTING ...............................................................................................................................................30
9. ELECTRICAL SCHEMES.............................................................................................................................................31
9.1. Electrical scheme of PellasX controller.......................................................................................................31
9.2. Electrical scheme - R16, R26......................................................................................................................31
9.3. Electrical scheme - R35...............................................................................................................................32
9.4. Electrical scheme - group 2 (R44 - R150)....................................................................................................32
10. REPORTS ...............................................................................................................................................................33
10.1. First start-up report................................................................................................................................33
10.2. Inspection report....................................................................................................................................34
11. LIST OF PICTURES AND TABLES.............................................................................................................................35
12. NOTES ...................................................................................................................................................................36
The author of this Manual is the company PELLASX Sp. z o.o. Sp.k.
The use of part or all of this manual in other publications is possible only with the written
permission of the author.

3 | S t r o n a
1. GENERAL INFORMATION
Read the user’s manual carefully before activating burner.
PellasX burner requires installation according to this user’s manual. Following advice
included in this USER’S MANUAL will guarantee safe functioning and installation of the device.
All doubts and ambiguities as to condition of equipment or given functions of parts of burner
should be reported to the seller in order to get explanations.
Installation of burner should be carried out by a service person who is
authorized and trained by the producer.
Improper installation may lead to loss of guarantee.
Every user of heating boiler devices should know and comply to all local rules of law.
Particularly before activating a heating installation in accordance with construction law.
The seller does not bear any responsibility for burner installation which is not in accord-
ance to valid local regulations and for lack of required protocols and permissions.
1.1. Transportation
PellasX burner is packed in a carton with a divider (burner with a controller,
mounting flange and a feeder). The device must be carried in packaging, according to
markings on the parcels. During transportation it should be protected against unfavorable
environmental conditions (snow, rain, dust) and it should not be exposed to shocks, hits and the
packaging should be protected against damages.
Loading and unloading must be carried out in a way which does not expose the devices to
shocks. Improper loading, unloading and transportation (throwing, rapture sliding, crushing
with other heavy goods) can be a cause of damage to the product.
In case of damage of the packaging or product, the device should be subjected to
control in operation. In case when improper work of a fan or feeder motor is observed
(loud work, rubbing), possibly other faults, e.g. electronics (vanishing of characters on display of
LCD display) the burner should be sent to the service team in order to carry a reparation.
Consignments delivered by forwarding companies should be checked in presence
of the courier when the goods are delivered. In case of any incompatibilities a
protocol should be prepared.
1.2. Storage
PellasX burner should be stored in environmental conditions in accordance to following
guidelines:
•Dry and draughty rooms, free from substances like gases, corrosive liquids and fumes, which
are harmful to burner. Burner and feeder can not be stored in rooms where artificial
fertilizers, chlorinated lime, acids, chemicals etc. are kept.
•Best storage temperature +5°C to +40°C. Relative humidity should not exceed 70%.
•During storage, the device can not have direct contact with the floor. PellasX
burner until final assembly should be kept in carton and on a pallet. Burners can be stored
and transported in three layers maximum.

4 | S t r o n a
•In case when a burner is stored for over 2 years from its production date or in
environmental conditions not similar to above description, before installing it should be
subject to activating - test by an authorized service person. To prove proper quality and
safety of a burner, the above inspection will be documented by service person in the
guarantee card.
1.3. Control of burner’s delivery
Before commencing assembly activities check the following: condition of packaging, make sure
that there are no visible damages and if delivery is complete and not damaged. Possible
reservations and problems should be reported to the supplier immediately. He is responsible for
insuring the merchandise.
1.4. Free space around burner
According to local safety regulations referring to heating devices, provide free space around
burner, at least 1 m around boiler and space for service of burner.
The boiler room should be clean, dry and well aired. Airflow to the boiler should be at least
equal to exhaust of fumes through the chimney.
ATTENTION!
Controller and all devices cooperating with it should be installed on the boiler or its
area, in places where the temperature is the lowest (below 50⁰C). Electronic devices
operating at high temperature may be damaged or not work properly.
ATTENTION!
In order to minimize the risk of fire is not
allowed to store flammable materials near
the burner (minimal length 1m).

5 | S t r o n a
2. PRODUCT DESCRIPTION
PellasX is a brand under which since 2001 burners for biomass have been produced. These
products are characterized with stepless regulation of settings allowing for usage in all types of ovens
or heating boilers. In case when exchange of burner is done in an old boiler, then it is not necessary
to make changes in existing installation. Firing up, sustaining fire after reaching preset temperature
and feeding fuel is automatic.
The uniqueness of the R-line solution is the number of the design improvements used as
compared to the burners available previously with the rotary combustion chamber. This makes the
operation of R-line burners reliable and free of technical problems. Significant changes in the
technological parameters and the components used have been introduced which makes the economic
attractiveness and the environmental usability of the technology considerably better with the burner
being one of the most modern solutions in the world.
Rotary combustion chamber allows the automatic and constant removal of ash being the residue of
the combustion process to ensure high stability of the combustion itself. With such a solution not just
the pellets, but also oat* or fruit stones are high-efficiency fuels. The chamber structure ensures
higher durability of the bearings and facilitates the quick bearings replacement.
The unique solutions employed in the R-line burners include:
•Hybrid Drive System–Fuel and air are supplied in a synchronized manner i.e. the fuel is
supplied according to the air supply rate and vice versa;
•Overpressure Combustion System –Air is supplied into the combustion chamber at the central
point to increase the flame spin and reduce the risk of backfire.
•Pellet inlet with firewall –The firewall in the pellet inlet supports the overpressure combustion
system, and also provides physical barrier between internal and external feeders, significantly
reducing the risk of backfire to the fuel tank.
•Air Vane System –provides precise, directional air supply to the combustion chamber,
improving combustion efficiency and extending grate lifetime;
•Expansion pipe system –elimination of jams, seizures and blockages of rotary combustion
chamber caused by thermal stresses;
•Lambda probe –available for all units to improve the combustion process and reduce the fuel
consumption.
PellasX burners are used in households, bakeries, hotels, public utilities, schools and
production halls or warehouses. They are made of heat-resistant acid-proof steel and are equipped
in best quality parts available on the market. The product which you have at your disposal is the
highest quality, most technologically advanced burner available on the market.
*Using oat fuel reduce burner power and result in increased fuel consumption (up to 50%)
and increased ash production.

6 | S t r o n a
2.1. Construction of burner
R-line burners are split into two groups:
1. Group 1 (R16, R26, R35)
2. Group 2 (from R44 to R150)
2.1.1. Group 1 (R16, R26, R35)
Pic. 1. Construction of R16, R26, R35 burners.
The burner is composed of the following subassemblies:
•Combustion chamber including: furnace (1) made of the highest quality heat-resistant, high-
chromium cast iron and a covering pipe (2),
•Blowing assembly including a cover made of ABS plastic (3), X.PLUG socket (4) located to the
right of the burner where the controller plug is to be connected,
•Blowing system (5) located between the blowing assembly and the combustion chamber. In
the upper part there is located a pellet inlet with internal firewall (6), where polyurethane pipe
from external feeder is to be connected.
The cover of burner does not have any protruding nor sharp parts. It does not threat one’s health.
The temperature of burner’s cover during operation should not exceed 60ºC with exception of places
of raised temperature, i.e. bakery.
ATENTION!
The manufacturer reserves the exclusive right to
implement any modifications in construction of
burner and feeder, its software and wiring,
otherwise it is released from any liability to the
buyer.

7 | S t r o n a
2.1.2. Group 2 (od R44 do R150)
Pic. 2. Construction of R44 –R150 burners.
The burner is composed of the following subassemblies:
•Combustion chamber including: furnace (1) made of the highest quality steel heat-resistant
steel and a covering pipe (2),
•Blowing assembly including a cover made of stainless steel (3) and a socket (4) located to the
right of the burner where the controller plug is to be connected,
•Blowing system (5) located between the blowing assembly and the combustion chamber. In
the upper part there is located a pellet inlet with firewall (6), where polyurethane pipe from
external feeder is to be connected.
The cover of burner does not have any protruding nor sharp parts. It does not threat one’s health.
The temperature of burner’s cover during operation should not exceed 60ºC with exception of places
of raised temperature, i.e. bakery.
ATENTION!
The manufacturer reserves the exclusive right to
implement any modifications in construction of
burner and feeder, its software and wiring,
otherwise it is released from any liability to the
buyer.

8 | S t r o n a
2.2. Quality requirements for pellets fuel
In table below given requirements as to quality of pellet fuel are shown. Using fuel which
complies to DIN 51731 or DIN PLUS certification or meet the rules of EN-14961-2 norm, extends
longevity of burner. The pellet storage location should be dry and well-ventilated. It is important that
prior to the hopper filling the pellet temperature is equal to the boiler room temperature.
Table 1. Quality requirements for pellet fuel.
Wooden pellet
Units
CERTIFICATE
Quality criteria
DIN plus
DIN 51731
Diameter
mm
4≤d<10(6)
4≤d<10(6)
Length
mm
5 x D(3)
<50
Density
kg/dm³
1,12
1,0< Density <1,4>
Ash
%
<0,5(1);(7)
<1,50
Humidity
%
<10
<12
Humidity when delivered
%
Not specified
Not specified
Caloric value
MJ/kg
>18(1)
17,5<HW<19,5(2)
Sulphur
%
<0,04(1)
<0,08
Nitrogen
%
<0,3(1)
<0,3
Chlorine
%
<0,02(1)
<0,03
Dust collected
%
<2,3
-
Additives facilitating
pressing
%
<2(8)
(4)
Ash melting temperature
-
Not specified
Not specified
Arsenic
mg/kg
<0,08
<0,08
Lead
mg/kg
<10
<10
Cadmium
mg/kg
<0,5
<0,5
Chrome
mg/kg
<8
<8
Copper
mg/kg
<5
<5
Quicksilver
mg/kg
<0,05
<0,05
Zink
mg/kg
<100
<100
Halogens
mg/kg
<3
<3
(1)
Dry weight
(2)
Free from water and ash
(3)
No more than 20% of pellets can be as long as 7,5 x diameter
(4)
DIN forbids to use additives. This ban is not valid to small heating systems.
(5)
In warehouse of the producer
(6)
Tolerance in differences in diameter ± 10 %
(7)
Allowed content of dust up to 0,8%, if it is naturally higher, specific for given sort of wood
(8)
Only natural additives from biomass are allowed
ATTENTION!
Change of pellets diameter during using of
burner (e.g. from 6mm to 8mm) requires
regulating the controller by a qualified
installer.

9 | S t r o n a
2.3. Burner nameplate template
Pic. 3. Burner nameplate template.
2.4. Technical data
Main properties of PellasX burners from R-line:
Safety
•Overpressure Combustion System and firewall in pellet inlet provide protection from flashback,
•Burner temperature sensor,
•Polyurethane pellet feeding pipe –melts in case of flashback, cutting of the fuel supply.
Reliability
•Hybrid Drive System –lower electricity consumption costs and full synchronization of fuel
feeding into the air,
•Air Vane System –provides precise, directional air supply to the combustion chamber,
improving combustion efficiency and extending grate lifetime;;
•Automatic start after power failure with memory of the last settings;
•Grate made of high-chromium heat-resistant cast iron.
Modern control system
•Automatic operation: firing up, cleaning, flame control
•Stepless (electronical) power regulation
•Possibility of control over burning process by broadband lambda probe (optional)
•Low emission of CO and CO₂
•Low consumption of electricity
•Low heat inertia
•High burning efficiency –up to 99%
•Very precise flame sensor
•Fully compatible with automatics of oil and gas boilers and with bakery ovens
•Possibility of handling the chimney exhaust fan (the fan works periodically and does not
ventilate the boiler)

10 | S t r o n a
Table 2. Technical data.
Type
R16
R26
R35
R44
R70
R100
R120
R150
Heating
power
4 - 16 kW
5 - 26 kW
8 - 35 kW
10 - 44 kW
15 - 70 kW
30 - 100 kW
40 - 120 kW
50 - 150 kW
Power supply
230 V AC /
50Hz
230 V AC /
50Hz
230 V AC /
50Hz
230 V AC /
50Hz
230 V AC /
50Hz
230 V AC /
50Hz
230 V AC /
50Hz
230 V AC /
50Hz
Average
power
consumption
50 W
50 W
50 W
70 W
85 W
85 W
85 W
85 W
Weight
15 kg
15 kg
17 kg
24 kg
27 kg
29,5 kg
33,5 kg
41 kg
Noise
emission
63 dB
63 dB
63 dB
63 dB
72 dB
72 dB
72 dB
72 dB
Feeder’s
length
2 m
2 m
2 m
2 m
2 m
2 m
2 m
2 m
Fuel
pellet
6-8mm
pellet
6-8mm
pellet
6-8mm
pellet
6-8mm
pellet
6-8mm
pellet
6-8mm
pellet
6-8mm
pellet
6-8mm
oat*
(see p. 5)
oat*
(see p. 5)
oat*
(see p. 5)
oat*
(see p. 5)
oat*
(see p. 5)
oat*
(see p. 5)
oat*
(see p. 5)
oat*
(see p. 5)
dry pit
dry pit
dry pit
dry pit
dry pit
dry pit
dry pit
dry pit
Burning
efficiency
up to 99 %
up to 99 %
up to 99 %
up to 99 %
up to 99 %
up to 99 %
up to 99 %
up to 99 %
Efficiency in
boiler
up to 96 %
up to 96 %
up to 96 %
up to 96 %
up to 96 %
up to 96 %
up to 96 %
up to 96 %
Power
modulation
YES
YES
YES
YES
YES
YES
YES
YES
Lambda probe
YES
(optional)
YES
(optional)
YES
(optional)
YES
(optional)
YES
(optional)
YES
(optional)
YES
(optional)
YES
(optional)
CH pump
service
YES
YES
YES
YES
YES
YES
YES
YES
DHW pump
service
YES
YES
YES
YES
YES
YES
YES
YES
Mixer service
YES
YES
YES
YES
YES
YES
YES
YES
Buffer service
YES
(optional)
YES
(optional)
YES
(optional)
YES
(optional)
YES
(optional)
YES
(optional)
YES
(optional)
YES
(optional)
Additional
feeder service
(silo)
YES
(optional)
YES
(optional)
YES
(optional)
YES
(optional)
YES
(optional)
YES
(optional)
YES
(optional)
YES
(optional)
Room
temperature
sensor
YES
(optional)
YES
(optional)
YES
(optional)
YES
(optional)
YES
(optional)
YES
(optional)
YES
(optional)
YES
(optional)
Return
temperature
sensor
YES
(optional)
YES
(optional)
YES
(optional)
YES
(optional)
YES
(optional)
YES
(optional)
YES
(optional)
YES
(optional)
Fumes
temperature
sensor
YES
(optional)
YES
(optional)
YES
(optional)
YES
(optional)
YES
(optional)
YES
(optional)
YES
(optional)
YES
(optional)
Weather
automatics
YES
(optional)
YES
(optional)
YES
(optional)
YES
(optional)
YES
(optional)
YES
(optional)
YES
(optional)
YES
(optional)

11 | S t r o n a
PellasX burner has simple and compact construction, which allows for easy assembly in boiler’s door.
Pictures below show the dimensions of burner and mounting holes.
Group 1
•R16
•R26
•R35
Group 2
•R44
•R70
•R100
•R120
•R150
Table 3. Dimensions of group 1 burners.
Type
Mounting holes
Burner dimensions

12 | S t r o n a
Table 4. Dimensions of group 2 burners
Type
Mounting holes
Burner dimensions

13 | S t r o n a
2.5. Safety systems
PellasX burners are equipped with following safety systems, which effectively protect the user
against flashback of fire:
1. Burner temperature sensor
Once the burner themperature rise over 90°C (setting: alarm temperatures may be modified
depending on the conditions in which the device operates i.e. bakery ovens or dryers; please
note that such changes can only be done by an authorized service person), the sensor changes
work mode into burning off mode, at the same time it switches off the external feeder and sets
the fan for 100% power.
2. Overpressure Combustion System
Air is supplied into the combustion chamber at the central point to increase the flame spin
and reduce the backfire risk.
3. Pellet inlet with firewall
The firewall in the pellet inlet supports the overpressure combustion system, and also provides
physical barrier between internal and external feeders, significantly reducing the risk of backfire
to the fuel tank.
ATTENTION! The counterweight of firewall in group 2 burners may not be blocked by
any means.
4. Flexible pouring pipe
Flexible pouring pipe is an elastic connection between external feeder and burner. Its main
function is delivering fuel to burner, additionally it also protects against backfiring. Under
influence of high temperature pipe starts to deform and extend which makes fuel deliver-ing
impossible.
Inspection of safety systems - see chapter 6.2: Specification of the inspection interval.
2.6. Technical data of controller, description of functions and burner settings
See User’s manual of controller.

14 | S t r o n a
3. INSTALLATION
3.1. Chimney
The parameters of chimney should be adjusted to requirements of heating device, of which
fumes are led away to chimney. The chimney can be made of ceramics or steel. Chimney should be
clean, and its draft sufficient for PellasX burner operating with heating device in scope of preset power
output. In case when chimney draft is not sufficient, it is possible to install a mechanical fumes
exhaust. Before operation chimney should be checked and approved by a qualified chimney-sweeper.
It should be remembered that a high chimney with big capacity of fumes needs more heat and
temperature of inner part of it should not be lower than 80ºC, 1m below the top to avoid condensation
on top of the chimney. To reduce the inner profile of the chimney, a steel pipe with proper diameter
can be installed. All advice referring to chimney duct should be taken from a professional company.
Strong wind, too high or too low chimney have influence on efficiency of burner and its settings. In
such cases it is advised to install a stabilizer of chimney draft which will ventilate chimney and help in
maintaining stable draft. If chimney is too small, then burner may not work correctly, in such case it
is necessary to install a mechanical fumes exhaust.
Table 5. Minimum chimney draft.
BURNER TYPE
MINIMAL CHIMNEY DRAFT [Pa]
R16
15
R26
15
R35
15
R44
20
R70
25
R100
30
R120
30
R150
35
3.2. Boiler / oven
PellasX burners can be installed in majority of boilers. The power of burner in relation to boiler
or oven power must be adjusted by installer. The burner is fixed (preferably in boiler’s door) with M8
screws (for quantity and dimensions of holes see table 3 and 4). The boiler chamber needs to fulfill
minimum size requirements given in tables 6-8. If boiler chamber is too small, the burner may operate
incorrectly.

15 | S t r o n a
Pic. 4. Positioning of burner and direction of flame.
Table 6. Minimum dimensions of furnace chamber.
BURNER TYPE
MINIMUM DIMENSIONS OF FURNACE CHAMBER
MINIMUM VOLUME OF
FURNACE CHAMBER
[m3]
MINIMUM LENGHT OF
FURNACE CHAMBER
[mm]
R16
0,020
350
R26
0,023
400
R35
0,030
520
R44
0,038
520
R70
0,070
790
R100
0,099
790
R120
0,109
930
R150
0,119
995
H
A
L

16 | S t r o n a
Table 7. Minimum dimensions of rectangular furnace chamber.
BURNER TYPE
MINIMUM DIMENSIONS OF RECTANGULAR
FURNACE CHAMBER
WIDTH A [mm]
HEIGHT
H [mm]
MINIMUM LENGHT OF
FURNACE CHAMBER L
[mm]
R16
218
262
350
R26
218
262
400
R35
218
262
520
R44
273
327
520
R70
273
327
790
R100
324
388
790
R120
324
388
930
R150
324
388
995
Table 8. Minimum dimensions of cylindrical furnace chamber.
BURNER TYPE
MINIMUM DIMENSIONS OF CYLINDRICAL
FURNACE CHAMBER
MINIMUM DIAMETER OF
CHAMBER D [mm]
MINIMUM LENGTH OF FURNA-
CE CHAMBER L [mm]
R16
270
350
R26
270
400
R35
270
520
R44
337
520
R70
337
790
R100
400
790
R120
400
930
R150
400
995
Table 9. Pressure in burning chamber.
BURNER TYPE
PRESSURE IN BURNING CHAMBER [Pa]
R16
10
R26
10
R35
15
R44
20
R70
25
R100
25
R120
30
R150
30

17 | S t r o n a
3.3. Fuel hopper
Fuel hopper can be made of any non-flammable material, i.e. steel. It can have any
capacity and should be located in proper distance from burner (Pic.9). In lower part of fuel hopper a
spiral feeder in covering pipe is mounted. The slope of feeder should not be bigger than 45° in relation
to the floor. Fuel hopper must be covered with a lid which would protect rotating screw of the feeder
against damage by leftovers.
It is forbidden to manipulate on the bottom of the hopper during operation of feeder. It is a
threat to body injury –particularly to fingers. It must be remembered to refill the fuel hopper with
pellets type fuel before activating the burner. Never pour the fuel hopper with damp ordisintegrating
fuel. It can cause difficulties in operation of burner –burner blockade.
3.4. External feeder
Table 10. Types of external feeders.
R16
R26
R35
R44
R70
R100
R120
R150
L<2m
TYPE 1
TYPE 1
TYPE 1
TYPE 2
TYPE 2
TYPE 2
TYPE 3
TYPE 3
L≥2m
TYPE 2
TYPE 2
TYPE 2
TYPE 2
TYPE 2
TYPE 2
TYPE 3
TYPE 3
3.4.1. External feeder - type 1
Pic. 5. Assembling of external feeder type 1.

18 | S t r o n a
Fuel feeder connects fuel hopper with burner. It is made of 60,3mm galvanized steel pipe (1).
Inside of the pipe, there is a steel spiral (2), driven by 230VAC motorgear (3). The motorgear is to be
connected with the burner controller by its cable with plug (see electrical scheme). Lower part of the
feeder should be mounted in lower part of fuel hop. The upper part of feeder is to be connected with
pellet inlet of the burner, using the flexible polypropylene pipe (4).
Type 1 feeder assembling (Pic. 5):
1. Insert the pin (5) into the shaft hole (6), then screw the spiral (2) on the pin (5). Secure
the spiral by tightening M8 nut (5) with washer on the pin;
2. Put the shaft (6) with mounted spiral (2) on the motorgear shaft (10). Secure the
connection using M6x10 screw (8);
3. Slide the spiral inside the pipe (1). Fix the motorgear on the pipe flange using M5x8 screws
with washers (9);
ATTENTION: The spiral should end in the middle of opening in the feeder (pic. 9).
In case of the spiral being too long, cut it to proper length.
3.4.2. External feeder - type 2
Pic. 6. Assembling of external feeder type 2.
Fuel feeder connects fuel hopper with burner. It is made of 60,3mm galvanized steel pipes (1)
(2). Inside of the pipes, there is a steel spiral (5), driven by 230VAC motorgear (9). The motorgear is
to be connected with the burner controller by its cable with plug (see electrical scheme). Lower part
of the feeder should be mounted in lower part of fuel hop. The upper part of feeder is to be connected
with pellet inlet of the burner, using the flexible polypropylene pipe .
This manual suits for next models
7
Table of contents
Popular Stove manuals by other brands
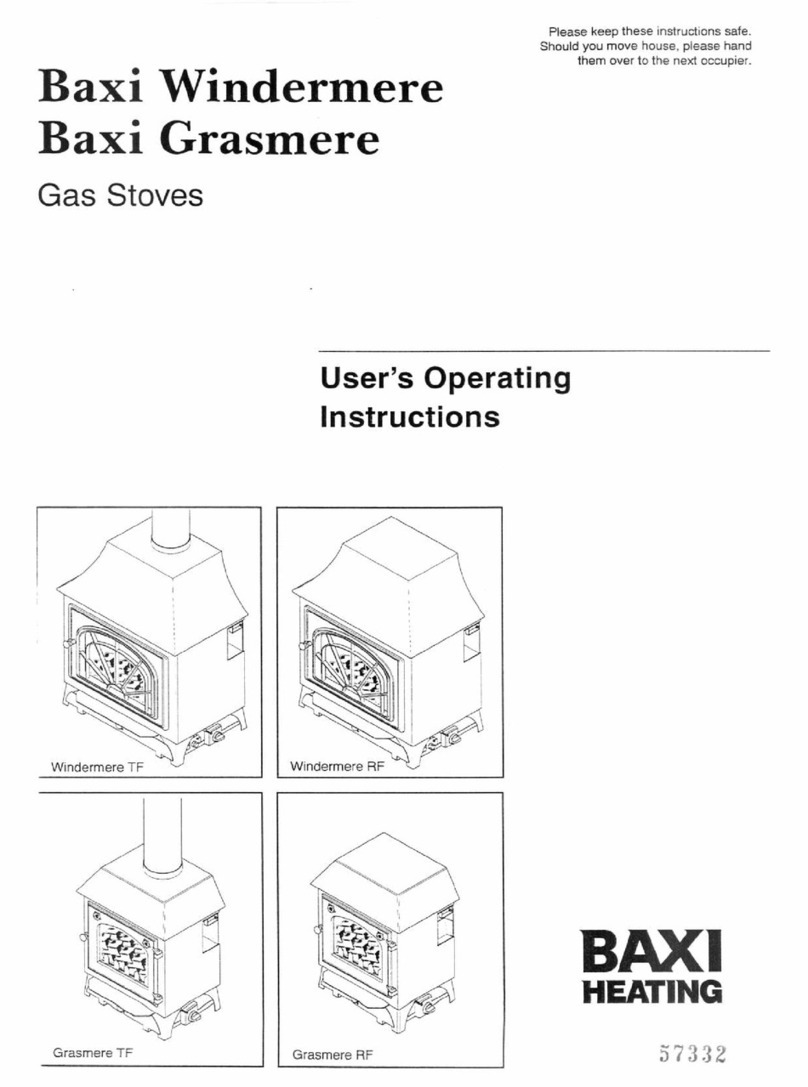
Baxi
Baxi windermere RF User operating instructions
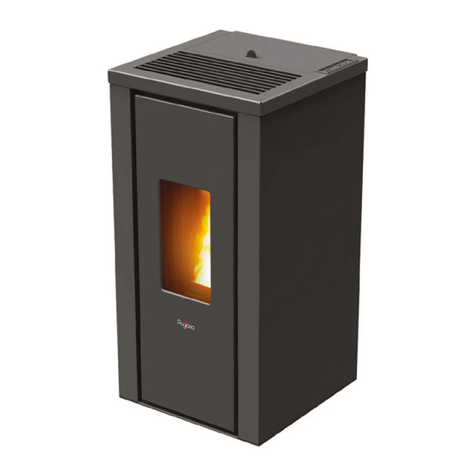
Cadel
Cadel VERA 7 user manual

Jøtul
Jøtul GF 300 CF Installation and operation instructions
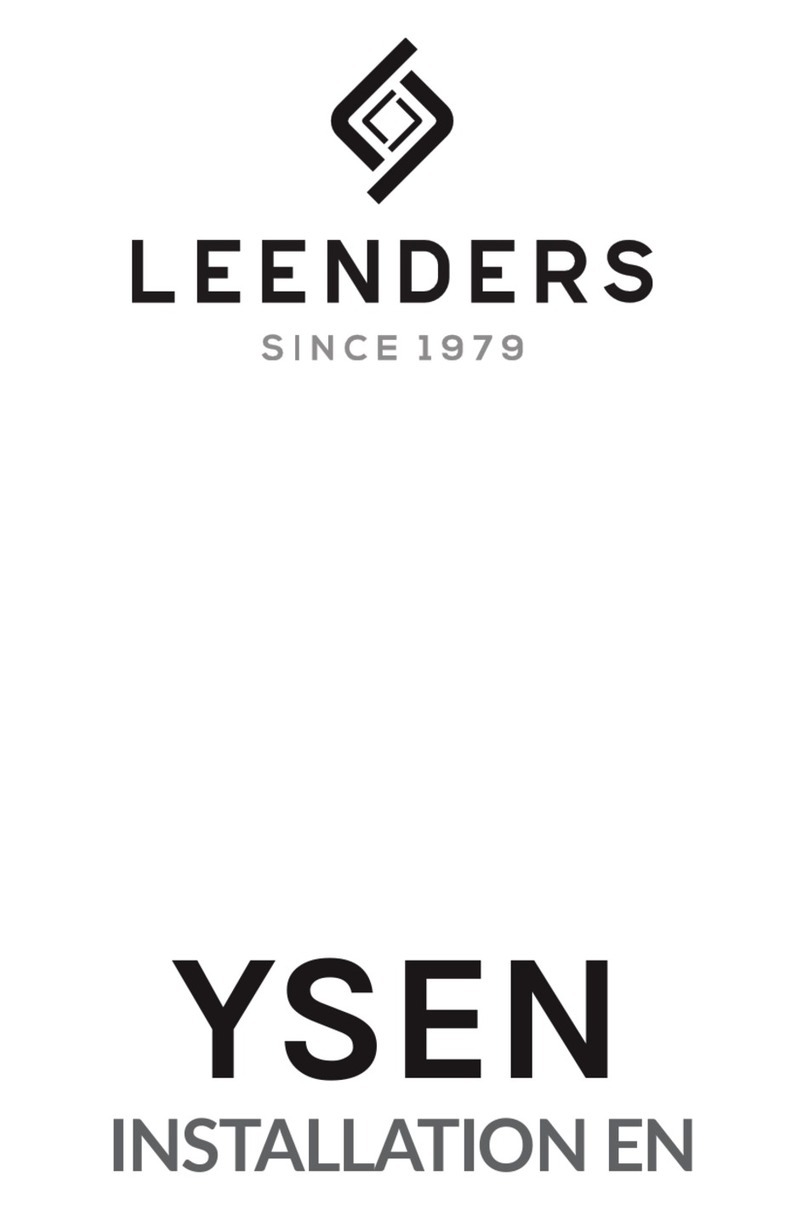
Leenders
Leenders Ysen Installation

Vogelzang International
Vogelzang International VG60 Owner’s Instruction and Operation Manual

Piazzetta
Piazzetta E904 Instructions for installation
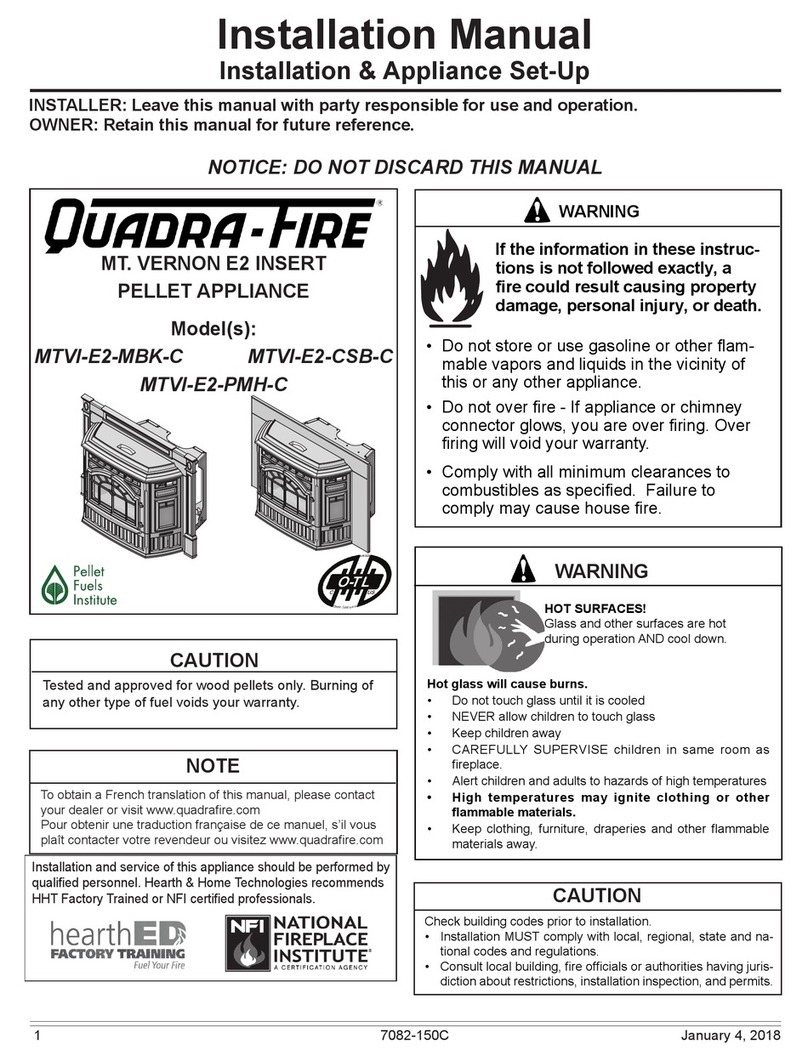
Quadra-Fire
Quadra-Fire MTVI-E2-MBK-C installation manual
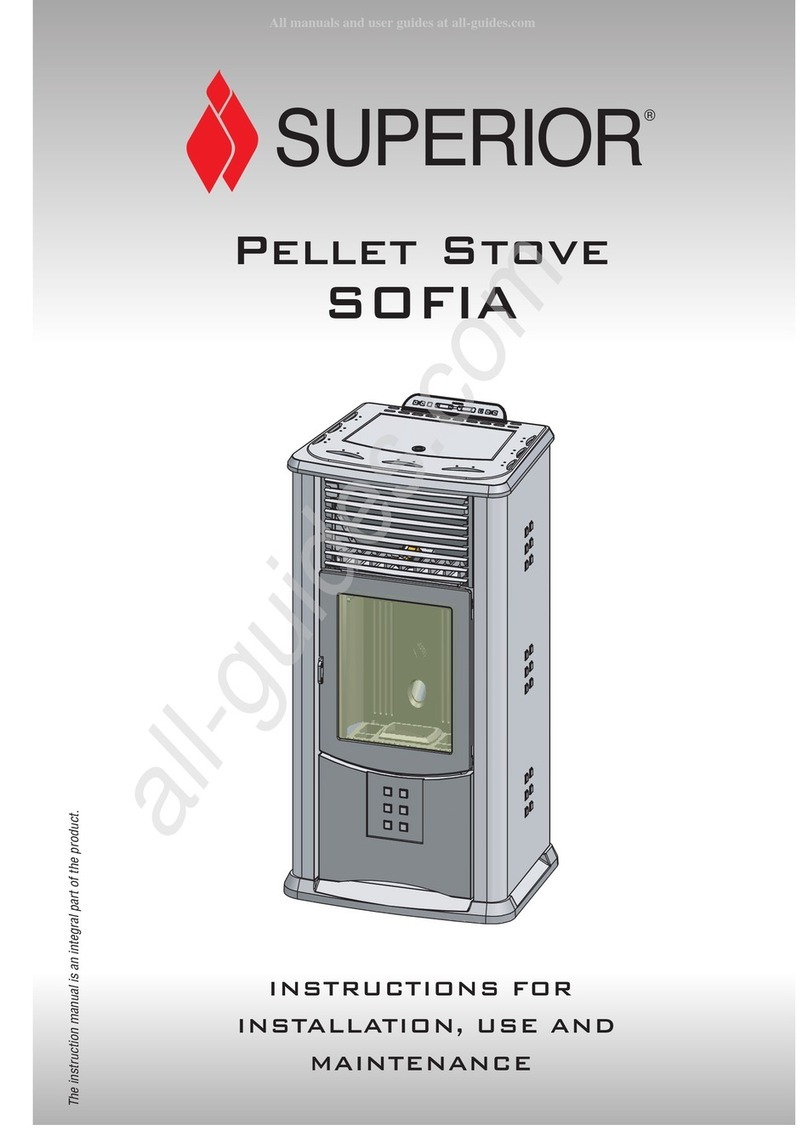
Superior
Superior Sofia Instructions for installation, use, maintenance

Vilpra Sauna
Vilpra Sauna Fornax VPR-14 Installation and operation manual

Cichewicz
Cichewicz MOC 20 manual

CARRON
CARRON Dante 5KW Installation and operating instructions
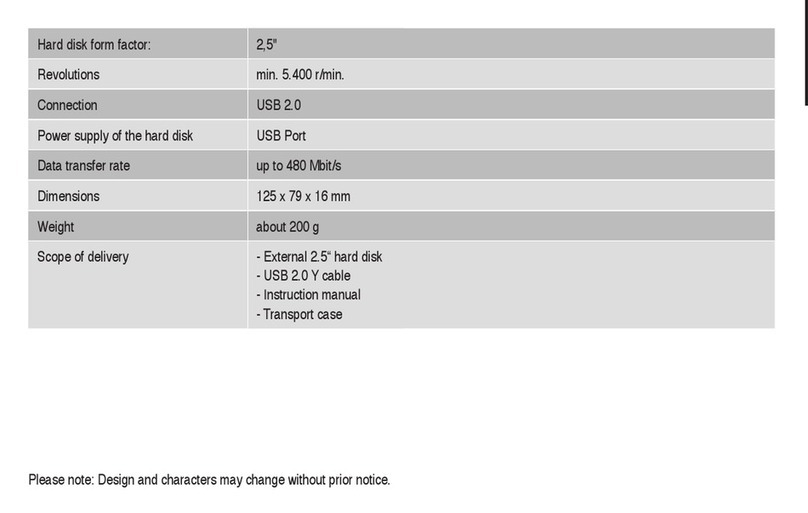
TakeMS
TakeMS mem.line user manual