PEMTECH PT605 User manual

PT605
CO2Gas Analyzer
Revision 7.2
January 2013
Operator’s
Manual
Pem-Tech, Inc.
Houston, Texas
U.S.A
www.pem-tech.com
Gas Detection Technology

2
Table of Contents
Sections Page No.
Specifications 5
Operation 6
Overview 6
Figure 1. System Layout 7
Front Panel 8
Messages and reading display during 10
Normal sampling cycle
Alarm LEDs and keypad switches 10
Installation and Unit Startup 11
System Wiring 13
Power Supply Input 13
AC Power Input 13
DC Power Input 13
4-20mA Analog output 13
User connection and wiring diagram 14
Alarm Relay contacts 15
RS232 / 485 Serial Communication 15
Connecting Gas stream to the Analyzer 15
Unit startup check list 16
STOP –Important Installation and 17
Maintenance note
Sensor Calibration 17
Sensor calibration procedure 18
Tips on good calibration 19
Sensor calibration errors 20
Fine tuning of 4-20mA analog output 21
Alarm Relays 22
Programming Alarm levels 22
MODBUS RTU Communication 23
Edit / Assign unit address 23
MODBUS Communication and 24
Data register list
Replacing Analyzer Sensor Assembly 27
Care 28
Maintenance 28
Spare Parts List 29

3
NOTICE
PEM-TECH INCORPORATED SHALL NOT BE LIABLE FOR TECHNICAL OR
EDITORIAL ERRORS OR OMISSIONS MADE HEREIN, NOR FOR INCIDENTAL OR
CONSEQUENTIAL DAMAGES RESULTING FROM THE FURNISHING,
PERFORMANCE, OR USE OF THIS MATERIAL.
LIMITED WARRANTY
Pem-Tech, Incorporated warrants all the equipment to be free from defects in
workmanship and material. The products will operate in conformance with the
published specifications when subjected to intended and proper usage for the period of
one (1) year from the date of shipment.
The warranty provides only the benefits specified and does not cover defects which
result from acts beyond the control of PEM-TECH including, but not limited to: damage
by accident, negligence, tampering, or failure to operate in accordance with the
procedures outlined in the Operations Manual. PEM-TECH’s liability under no
circumstances will exceed replacement of the unit claimed to be defective.
Tampering with the equipment and altering it for uses other than the intended use or
replacement of parts not supplied by the company, shall immediately void and cancel
all the warranties with respect to the affected products.
The warranties specified herein are in lieu of any and all other warranties, express or
implied. In no event, whether as a result of breach of warranty or alleged negligence,
shall PEM-TECH be liable for special or consequential damages, including, but not
limited to, loss of profits or revenue, loss of equipment or down time costs.

4
SERVICE POLICY
Pem-Tech has service facility at the factory. For all the repairs contact at our toll free
number 1-800-379-3894 or visit our website www.pem-tech.com
For all repairs call us for a Return Material Authorization number (RMA). Inform us
briefly the nature of the problem and obtain shipping address. Properly pack the
equipment before shipping. Also include your complete shipping address and contact
name and phone number.
For non-warranty repairs you must provide the limit to repair costs. State if a quote for
repair cost is required before you can authorize the repair cost. For this an additional
charge may be applicable.
NOTE:
1. For all the repairs under warranty, serial number must be legible on the items being
repaired.
2. Shipping point is FOB Houston.

5
SPECIFICATIONS
Typical Range: 0-5%, 0-10%, 0-20%
(Other Ranges also available)
Range is pre-programmed at the factory
Electrical Classification: Class I Div 1, Suitable for use in Hazardous
Location
Weight 70 Lbs (31.8 Kg)
110 Lbs (49 Kg ) with Fiberglass enclosure
Sample Gas Physical properties: Dry and particle free
Temperature: 10 F to 110 F (4 C to 50 C)
Sample inlet Tube Fittings: ¼” Stainless Steel tube fittings
Repeatability: When challenged with same calibration gas,
within 0.1 % (analyzer with 5, 10, & 20 range)
2 % (analyzer with 50% or higher range)
Accuracy: 3 %
Alarm Relays: 3 SPDT fully programmable dry relay contacts Form “C”
Type . Rated 5 amps @ 125 VAC or 24 VDC
Analog Output: 4-20 mA ( 350 maximum loop resistance )
Display: 4 lines by 16 character LCD display with backlight
Supply Voltage: 18-28 VDC
117 VAC (240 VAC option available)
Power Consumption: < 4.5 watts

6
OPERATION
Overview
The following figure illustrates an overview of the units operation. Refer to drawing
number Figure 1 for details on system layout.
When the power is applied to the unit it will display startup messages such as current
alarm set points, and sensor calibration data. These settings and calibration data are
retained in the non-volatile memory. The unit is calibrated and all the initial
adjustments are performed at the factory.
Note: User may wish to change the alarm settings. Refer to the section on Alarm
Calibrations.
After the startup messages the system will begin the warm up cycle for approximately 5
minutes (300 seconds). This allows the sensor to clear and run self diagnostics.
Sample Conditioning
Pressure Regulators
External Filters
Main CPU Board Assembly
Control Logic
Flow Meter +
Coalescing Filter
H2S
Sensor Asmbly
Sampling System Junction Box
Infra Red (IR)
CO2 Detector
Assembly Block
Gas Sample
routing & Vent
block with tube
Main Electronics and Control Assemblies
Termination / User
connection Box
Terminal Blocks
4-20mA
Alarm Relays
AC / DC power Input
Sensor Signal conditioning
AC-DC , DC-DC power convertors. Alarm
relays
Dry Sample in
¼ Tube Fitting
Vent
PT605 Analyzer –Block Diagram
Main CPU Board Assembly with LCD
Display. Control Logic Circuitry

7
Figure 1. PT605 CO2 Analyzer in fiberglass enclosure. Complete unit layout

8
Front Panel
PT605 front panel is equipped with a large liquid crystal display with back light, four alarm
LEDs for visual alarm indicators, and keypad switches. The CO2concentration and signal
output from the Infra-Red sensor are continuously displayed on the LCD. The keypad switches
are used to reset alarms, calibrate sensors and program unit configuration.
Following are the prompts and messages on the LCD during sample and clear cycle.
Front Panel Assembly
LCD Prompts & Messages
The first line on the LCD displays the concentration of the CO2in the process stream. The
second line displays the current sensor output. The signal from the sensor is a tool for sensor
diagnostic and trouble shooting.
CO2 = 1.0 %
Snsr Signl = 1.20

9
Alarm LEDs and Keypad switches
There are 4 LEDs on the front panel labeled AL1 thru AL3 and a Fault LED. These LEDs are the
visual indicators of any active alarms. The alarm relays and LEDs can be reset by pressing the
RESET key on the front panel. The resetting of the alarms via reset switch can only be
performed in the clear cycle.
When the “PRGM”(program) key switch is pressed the unit will initiate a sequence of prompts
giving user option to select one by pressing the ENTER key. The list of option includes:
Sensor Calibration
Adjust Alarm Level
4-20mA Adjustment
Set Unit Address
Display Calib data

10
Installation and Unit Startup
PT605 analyzer should be installed approximately 5 feet above the ground. A ¼”
stainless steel tubing should be used to connect the sample input of the analyzer to the
stream. A minimum of 50 PSIG sample stream pressure is required. The maximum
inlet pressure of the installed pressure regulator is 2000 PSIG with maximum output
pressure of 30 PSIG. The analyzer sampling system requires a flow rate of one (1.0)
SCFH.
For stream with high pressure an external pressure regulator close to sampling point
must installed to reduce the pressure before connecting to the analyzer.
For streams with heavy moisture contents and other contaminants an additional in-line
filter must be installed.
Important Note
PT605 requires a clean and dry gas sample from the process stream for
proper operation. The sample input must be at a minimum pressure of 50
PSIG and must have a regular flow through the sampling system. All vent
fittings must be left open to atmosphere and should not have any back
pressure.
Refer to figure 1 for the location of the junction box with customer connection and
terminals. Also refer to figure 3 for connections and wiring diagram. The connection
box has 2 each ¾” NPT female cable entry ports. Install proper cable glands (user
supplied) for the type of cable being installed. Also a ¾” conduit hub is provided on
the bottom of the fiberglass enclosure for cable entry inside the fiberglass enclosure.
PT605 Analyzer is suitable for use in hazardous location. The unit can be mounted to
the wall or panel. Refer to figure 2 for the mounting holes and dimensions on the
fiberglass enclosure. Six (6) mounting holes are provided on the enclosure for wall
mounting.
The analyzer should be installed approximately 5 feet above the ground. Extreme
temperature condition must be avoided. Avoid installing the unit with the front facing
the direct sunlight.

11
Figure 2. Fiberglass Enclosure for PT605 CO2 Analyzer

12
System Wiring
A square junction box on lower right is used for user connection. See figure 1. Two (2) each ¾”
Female NPT Cable entry hubs are provided. Inside the junction box are terminals for AC or DC
Power Input, Relay contacts for external alarm signals & 4-20mA output.
See figure 3 for the customer connection boards inside the junction box.
Power Supply Input
The analyzer operates on either AC or DC power supply. A standard 117 VAC or 24 VDC
power is supplied to the unit.
AC Power Input:
A screw in type terminal connector is provided in the top customer connection junction box for
AC power input. The terminal block is labeled “L N G”.Pull the 3-pin connector plug from
the socket, connect the 117 VAC power supply lines to the proper pins and insert the plug back
into the socket.
DC Power Input:
If the unit is powered by DC, connect 16 –24 VDC supply to the 2 pin DC power input terminal
in one of the junction boxes. The terminal is clearly labeled as DC IN on the customer
connection board. Simply connect the positive and negative supply lines to the connector pin
labeled as + and -, respectively.
4-20mA analog output:
PT605 Analyzer generates a linear 4-20mA DC analog output equivalent to CO2concentration in
the stream. This analog output can be connected to devices like PLC, DCS and chart recorders.
The analog output generated corresponds to the full scale of the analyzer.
Table below gives the corresponding mA reading for an analyzer with the full scale range of
10%. The (CO2) % vs. (analog output) mA will be different for the unit with different full
scale range.
CO2in Stream Analog Output
(%) mA
00
4.0
2.5
8.0
5.0
12.0
7.5
16.0
10
20.0

13
Figure 3. User connection and Terminations for Power, alarms,
and 4-20mA analog output

14
Alarm Relay Contacts:
The analyzer is equipped with 3 each dry alarm relay contacts (potential free). Each relay can
be programmed anywhere between 0 and the full range of the analyzer.
The relays are Form “C” type relays. On the customer connection board each alarm terminal is
labeled appropriately. An alarm terminal is a 3 pin terminal labeled as:
NO Normally Open
C Common
NC Normally closed
Use “C” and “NO” terminal for normally open contacts and “C” and “NC” terminals for
normally closed contacts.
RS232 / RS485
The serial port RS232 or RS485 (jumper selectable) is provided for communication with PLCs.
Industry standard MODBUS RTU ® protocol is used for data communication. Refer to
section on MODBUS Communication later in this document for additional details.
Connecting the gas stream to the analyzer
PT605 requires a clean and dry gas sample from the process stream for proper operation. A
minimum of 50 PSIG line pressure is needed. In normal operation the pressure should not
exceed 500 PSIG. The regulator installed on the analyzer has maxim inlet pressure rating of
2000 PSIG with 30 PSIG on the output port. However, a drastic pressure drop from over 2000
PSIG to 30 PSIG will increase the temperature of the gas which could be damaging to the
sampling system over the extended period of time. For high-pressure stream an additional
pressure-reducing regulator must be installed at the sampling point. A ¼” stainless tube shall
be used to connect sample stream to the pressure regulator on the analyzer.
An additional in-filter must be used for stream with high moisture content and contaminants.
The in-line filter installed on the unit is coalescing filter to remove the residual contaminants
from the gas sample.
Be sure to shut off the pressure regulator (turn counter-clockwise) before flowing the gas to the
analyzer.
Use the unit startup checklist on the next page for proper step by step startup.

15
Unit Startup Check list
Use the following steps as a guide for proper startup procedure.
Unit must be installed in shaded area to avoid extreme heat conditions.
Perform all the system wiring as discussed in the previous section.
Be sure the unit is connected with proper AC or DC supply. But DO NOT switch the
power ON at this time.
Secure and tighten all covers to the junction boxes.
Check for maximum stream pressure and temperature. For high pressure streams install a
regulator at the sampling point and then run ¼” tubing to the analyzer regulator. Do not
connect stream with high pressure straight to the regulator installed on the analyzer.
Be sure the stream is free of heavy particles, contaminants and heavy moisture to avoid
damage to the sampling system.
Shut off the regulator on the analyzer by rotating the knob counter clockwise.
Connect the stream to the analyzer via ¼” stainless steel tube.
Make sure the 3 - way valve next to the pressure regulator is switched to “SAMPLE”
position.
Switch ON the AC or DC power to the analyzer. The LCD should display start up
messages.
After start up messages and warm up cycle the unit will begin its normal operation. If
alarm relays are being used then set alarm levels when the system is in normal cycle. Refer
to section on programming alarm set points later in this document.
Switch ON the flow from the gas stream.
Slowly turn the pressure regulator knob in clockwise direction to start the sample flow to
the analyzer. Set the pressure between 25 and 30 PSIG indicated on the pressure gauge.
Set the flow rates in the Air and Sample flow meter to 1.0 SCFH. The flow meters are
located in the sampling system enclosure. Secure and tighten the cover on the sampling
system enclosure. See System layout diagram.
The analyzer is calibrated at the factory and is therefore, ready for normal operation.
However, if the user wishes to calibrate the unit then wait for at least 5 to 10 minutes
before attempting the calibration.

16
Important Installation & Maintenance Note
Do not block Vents on the system enclosures.
There is a vent located on the right side of the enclosure. This vent must be left open to
atmosphere and must not have any back pressure. Blocking vent or attaching long tubes
on these vents will create back pressure that may result in sensor contamination. If the
installation of the vent tubes is necessary then keep the tubes as short as possible and at
least ¼” diameter.
Turn off the sample valve if the purging pump is not running.
It is imperative that the sample gas must be particle and liquid free. Install an additional
external sample conditioning system if necessary. Also the flow rate indicated in the flow
meter must be set to 1.0 SCFH

17
Sensor Calibration
Typically the CO2 concentration of the calibration gas should be close to 50% of the full
scale range of the analyzer. The following table lists the calibration gas for analyzer
with different full scale range.
Range of Analyzer
Recommended
Calibration Gas
5 %
2.5 %
10 %
2.5 - 5 %
20 %
5 –15 %
Calibration Gas Required:
1. Pure Nitrogen (to purge the sampling chamber and infra-red gas cell)
2. CO2 Nitrogen Balanced. See table above for recommended calibration gas for the
analyzer.
The sensor calibration is performed simply by pressing the PRGM switch and following the
prompts on the LCD. The user is not required to make any kind of hardware adjustments.
The calibration procedure is fully automated. The analyzer will display messages on the LCD
and prompts for the user input when needed. The calibration is performed by first applying
the pure nitrogen to purge the sensor and the sampling system in order to set the baseline zero.
Then a known concentration of nitrogen balanced CO2calibration gas is applied to set the
correct reading. The microprocessor makes all the adjustments necessary and stores the
calibration data in a non-volatile memory. The analyzer will display the message for any
calibration errors, otherwise a “Calibration OK” message is displayed and the unit will return to
normal operation.
Note: To abort the sensor calibration at any time press RESET key. The unit will
display the sensor abort message for few seconds before returning to normal operation.

18
Step by Step Calibration Procedure
Remove the cap from the calibration port of the three way valve installed. Move the valve
handle to CALIB position. This will shut off the sample input from the stream and allow the
calibration gas to flow to the sensor. Connect the calibration gas to the CALIB port on the valve.
When applying the nitrogen or calibration gas be sure the gas flow indicated in the flow meter
is 1.0 SCFH.
Press the PRGM switch. This will initiate a sequence of prompts giving user to select the option
displayed on the LCD by pressing the ENTER key. One of the options displayed is Sensor
Calibration. To exit from the list of prompts press the RESET switch and the unit will return to
normal operation.
Remove the cap from the calibration port of the three way valve installed. Move the valve
handle to CALIB position. This will shut off the sample input from the stream and allow the
calibration gas to flow to the sensor. Connect the calibration gas to the CALIB port on the valve.
When applying calibration gas be sure the gas flow indicated in the flow meter is 1.0 SCFH.
STEP 1: When the analyzer is in normal operating mode press and hold the PRGM switch
until the programming options are displayed. Use the ▲and ▼arrow keys to scroll thru the
options until Calibrate Sensor is displayed on the LCD. Press ENTER to select.
STEP 2. The analyzer will display Calibrate Sensor Message for few seconds and then
prompts user to apply the nitrogen gas to purge and press ENTER key when ready. Attach
the nitrogen supply line to the 3-way valve set in CALIB position, and apply the gas slowly
reaching the flow rate to 1 SCFH indicated in the flow meter. Press ENTER key when set.
STEP 3. The unit will display the current concentration of CO2 and the signal output from
the Infra Red sensor. In this step the analyzer sets the zero or reference signal from the
infrared sensor. Now apply the nitrogen gas for approximately 2 minutes to purge all the
CO2 from the sensor sampling system. The voltage indicated on the last line of the LCD
should start decreasing. The sensor output should be between 0.35 and 0.5 volts.
Once the voltage has stabilized press the ENTER key to record the zero point.
Apply Nitrogen
Press ENTER when
ready
Press ENTER
When purged
CO2 = 0.0
SensrSignl = 0.4 v

19
STEP 4. After purge cycle the following message will be displayed.
The unit is now ready for gas standard. Apply the CO2 calibration gas and make sure the
flow meter is set at 1.0 SCFH. Calibration gas must be applied for at least 2 minutes. When the
Sensor Signal reading has stabilized then by using ▲ and ▼ arrow keys adjust and match the
CO2 concentration on the LCD with the CO2 concentration of the calibration gas being applied.
Press ENTER key to accept the change.
STEP 5. Press the RESET switch when finished to save the calibration data and return to
normal operation.
If calibration is not successful the error message is displayed and the analyzer defaults back to
the previous calibration data.
Apply Calib Gas
CO2 = 0.0
SensrSignl = 0.4 v

20
Tips on good calibration
In order to perform good calibration, follow the instructions below
1. Make sure the flow meter is stable and set at 1 SCFH. Not enough pressure on the
calibration gas may cause flow meter to fluctuate and will result in inconsistent flow of gas
through the sensor.
2. Note the steady change in the sensor signal ( displayed on the last line of the LCD). The
sensor signal should rise as the sensor is exposed to CO2 during the sampling and should
clear to zero state when in purge mode. The typical zero state of a sensor is between 0.35
and 0.5 volts.
Sensor Calibration Error
The unit will display messages if sensor calibration error occurs.
Error Message
Description
Remedy
Zero too High
Sensor is unable to clear
Check any blockage on sensor vent
lines. Also check if purging pump
is operating.
Zero too Low
Sensor drift below baseline
Sensor old or deteriorated. Replace
with new one.
No Span
Or Span too low
Sensor was unable to detect any
change
Check the CO2 concentration of the
calibration gas being applied.
Also check the flow meter for
proper flow rate.
Check for possible leaks in the
tubing inside the sampling system.
If problem persists then sensor may
need to be replaced.
If the calibration fails then the analyzer will restore the old calibration data.
Other manuals for PT605
1
Table of contents
Other PEMTECH Measuring Instrument manuals
Popular Measuring Instrument manuals by other brands

Tecsis
Tecsis TM1 Series operating instructions

Viavi
Viavi CAA06M user guide
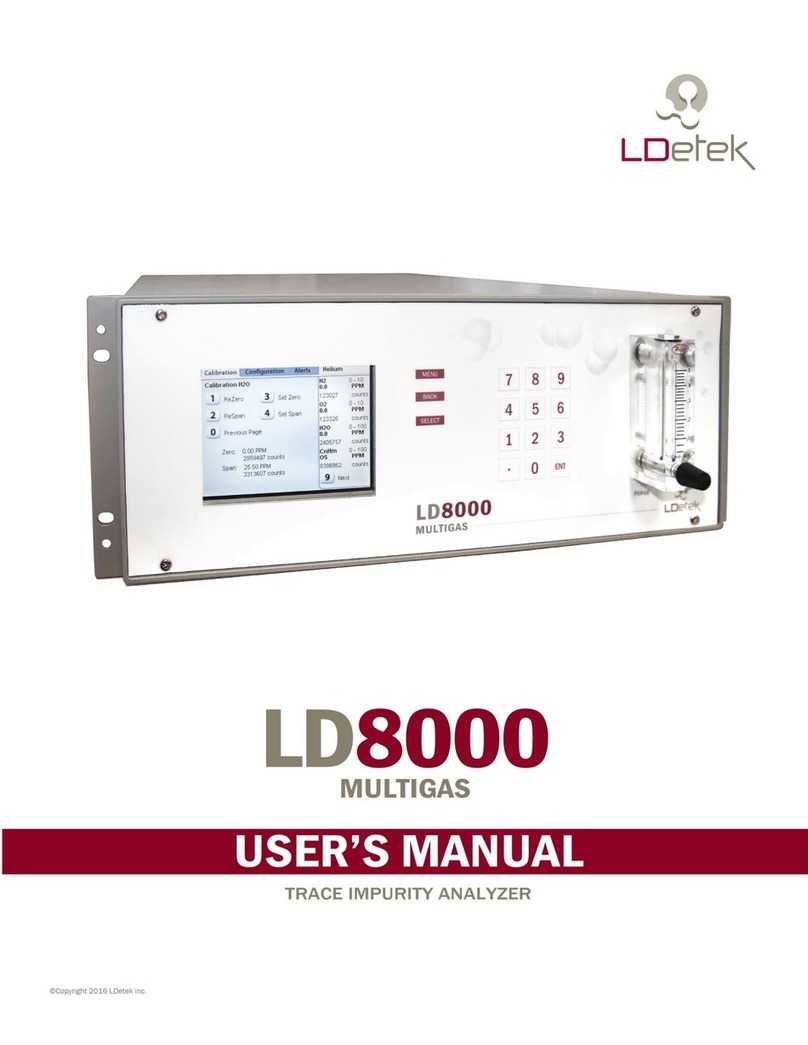
LDetek
LDetek MULTIGAS LD8000 user manual
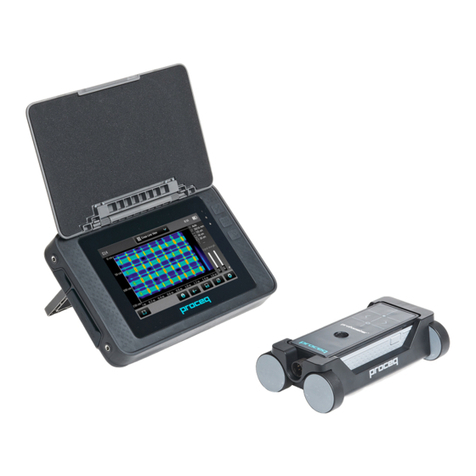
Proceq
Proceq PROFOMETER PM-6 operating instructions
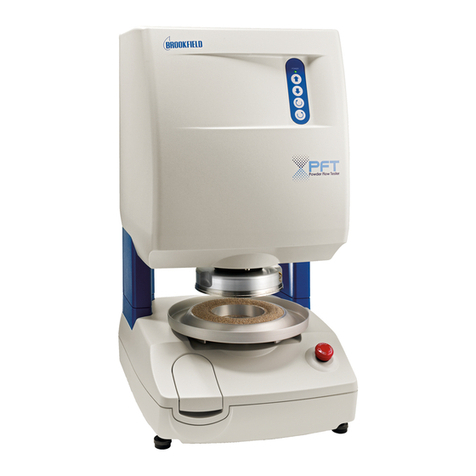
Brookfield
Brookfield PFT Powder Flow Tester operating instructions
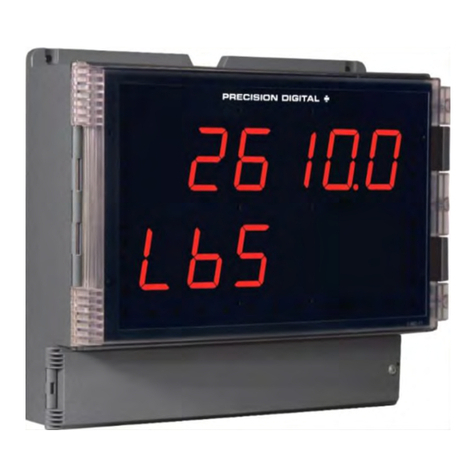
PRECISION DIGITAL
PRECISION DIGITAL Helios PD2-6100 instruction manual