Penta KB Power SIMG User manual

INSTALLATION AND OPERATING INSTRUCTIONS
MODEL SIMG
KB Part No. 8832 — Signal Isolator or KBMG-212D Regenerative Drive
See Sa ety Warning on Page 1
The in ormation contained in this manual is intended to be accurate. However, the Manu acturer
retains the right to make changes in design which may not be included herein.
™
A COMPLETE LINE OF MOTOR DRIVES
© 2000 KB Electronics, Inc.
!
Pending

TABLE OF CONTENTS
Section Page
i. Sa ety Warning . . . . . . . . . . . . . . . . . . . . . . . . . . . . . . . . . . . . . . . . . . . . . . . . . . . . . . . . . . 1
I. Introduction . . . . . . . . . . . . . . . . . . . . . . . . . . . . . . . . . . . . . . . . . . . . . . . . . . . . . . . . . . . . 2
II. Installation Instructions . . . . . . . . . . . . . . . . . . . . . . . . . . . . . . . . . . . . . . . . . . . . . . . . . . . . 6
III. Connections to the SIMG . . . . . . . . . . . . . . . . . . . . . . . . . . . . . . . . . . . . . . . . . . . . . . . . . 12
IV. Calibration Procedure . . . . . . . . . . . . . . . . . . . . . . . . . . . . . . . . . . . . . . . . . . . . . . . . . . . .16
V. Installing the SIMG Finger-Sa e Cover . . . . . . . . . . . . . . . . . . . . . . . . . . . . . . . . . . . . . . . 17
VI. Limited Warranty . . . . . . . . . . . . . . . . . . . . . . . . . . . . . . . . . . . . . . . . . . . . . . . . . . . . . . . 18
Tables
1. General Per ormance Speci ications . . . . . . . . . . . . . . . . . . . . . . . . . . . . . . . . . . . . . . . . . . 6
2. Terminal Block Wiring In ormation . . . . . . . . . . . . . . . . . . . . . . . . . . . . . . . . . . . . . . . . . . . 12
3. Resistor or Signal Following rom Armature Voltage . . . . . . . . . . . . . . . . . . . . . . . . . . . . .14
Figures
1. Control Layout . . . . . . . . . . . . . . . . . . . . . . . . . . . . . . . . . . . . . . . . . . . . . . . . . . . . . . . . . . 3
2A. Mechanical Speci ications . . . . . . . . . . . . . . . . . . . . . . . . . . . . . . . . . . . . . . . . . . . . . . . . . .4
2B. Mechanical Speci ications (Continued) . . . . . . . . . . . . . . . . . . . . . . . . . . . . . . . . . . . . . . . . 5
3. KBMG/SIMG Assembly Diagram . . . . . . . . . . . . . . . . . . . . . . . . . . . . . . . . . . . . . . . . . . . . . 7
4. Removing the KBMG Finger-Sa e Cover . . . . . . . . . . . . . . . . . . . . . . . . . . . . . . . . . . . . . . . 8
5. Removing Terminal Block TB1 . . . . . . . . . . . . . . . . . . . . . . . . . . . . . . . . . . . . . . . . . . . . . . 9
6. Removing the KBMG Finger-Sa e Cover Panel . . . . . . . . . . . . . . . . . . . . . . . . . . . . . . . . . . 9
7. Removing the KBMG Finger-Sa e Cover Field Tab . . . . . . . . . . . . . . . . . . . . . . . . . . . . . . . 9
8. Connection Diagram . . . . . . . . . . . . . . . . . . . . . . . . . . . . . . . . . . . . . . . . . . . . . . . . . . . . . 10
9. Installing Field Connector . . . . . . . . . . . . . . . . . . . . . . . . . . . . . . . . . . . . . . . . . . . . . . . . . 11
10. Voltage Following Connection . . . . . . . . . . . . . . . . . . . . . . . . . . . . . . . . . . . . . . . . . . . . . . 12
11. Main Speed Potentiometer Connections . . . . . . . . . . . . . . . . . . . . . . . . . . . . . . . . . . . . . . 13
12. Signal Following rom Armature Voltage . . . . . . . . . . . . . . . . . . . . . . . . . . . . . . . . . . . . . . .14
13. Enable Switch Connection . . . . . . . . . . . . . . . . . . . . . . . . . . . . . . . . . . . . . . . . . . . . . . . . 16
14. Removing The SIMG Finger Sa e Cover Field Tab . . . . . . . . . . . . . . . . . . . . . . . . . . . . . . 17
ii

1
i. SAFETY ARNING! Please read carefully:
Be sure to ollow all instructions care ully. Fire and/or electrocution can result due to
improper use o this product.
This product should be installed and serviced by a quali ied technician, electrician, or
electrical maintenance person amiliar with its operation and the hazard involved. Proper
installation, which includes wiring, mounting in proper enclosure, using or other over cur-
rent protection and grounding, can reduce the chance o electric shocks, ires, or explo-
sion in this product or products used with this product, such as electric motors, switches,
coils, solenoids, and relays. Eye protection must be worn and insulated adjustment tools
must be used when working with control under power. This product is constructed o
materials (plastics, metals, carbon, silicon, etc.) Which may be a potential hazard.
Proper shielding, grounding, and iltering o this product can reduce the emission o radio
requency inter erence (RFI) which may adversely a ect sensitive electronic equipment.
I in ormation is required on this product, contact our actory. It is the responsibility o the
equipment manu acturer and individual installer to supply this sa ety warning to the ulti-
mate user o this product. (SW e ective 11/92)
This control contains electronic start/stop and enable circuits that can be used to start
and stop the control. However, these circuits are never to be used as sa ety disconnects
since they are not ail-sa e. Use only the AC line or this purpose.
!
This product complies with all CE directives pertinent at the time o manu acture.
Contact actory or detailed installation instructions and Declaration o Con ormity.

I. INTRODUCTION
Thank you or purchasing the SIMG Bipolar Signal Isolator (P/N 8832). KB
Electronics, Inc. is committed to providing total customer satis action by pro-
ducing quality products that are easy to install and operate. The SIMG is
manu actured with sur ace mount components incorporating advanced cir-
cuitry and technology.
The SIMG provides input isolation and is used to isolate, ampli y, and condi-
tion DC voltage signals rom any external source (power supplies, motors,
tachometer generators, transducers, and potentiometers). The isolated out-
put voltage o the SIMG provides input signals to the KBMG-212D (here-
ina ter re erred to as KBMG) Regenerative Drive (P/N 8831). In also pro-
vides isolation or motor direction switching and an isolated power supply or
transducer or potentiometer operation. The PWR LED provides indication
that power is applied.
All input connections (+15, -15, SIG, COM, and EN) are made via a barrier
terminal block and are isolated rom AC line and motor wiring.
The SIMG is actory calibrated to accept a signal input voltage o -10V to
+10V DC. OFFSET and MAX trimpots are provided in order to recalibrate the
SIMG or speci ic applications.
2

FIGURE 1 – CONTROL LAYOUT
(Illustrates Factory Setting o Jumpers and Approximate Trimpot Settings)
3
TACH
CON3
T1(-)
T2(+)
PWR TB1
L1
COM ENSIG
-15V+15V
L2
J1
ENABLE
A90
T7
A180
T50
F-
CON2
F+
1.7A
F-
OFFSET
2.5
5.0
7.5
10A
MAX
F+
F+
F-
M2
RACCMAXFCLIR RCL FACC
M1
DB RESP
SIMG BIPOLAR SIGNAL ISOLATOR

FIGURE 2A – MECHANICAL SPECIFICATIONS (INCHES / mm)
(Shown Mounted onto KBMG)
4
0.95
[24.21]

FIGURE 2B – MECHANICAL SPECIFICATIONS (INCHES / mm)
(Shown Mounted onto KBMG)
5
L1 L2
M2
RACCMAXFCLIR RCL FACC
M1
DB RESP
2.67
[67.92]
0.48
[12.32]
3.80
[96.52]
4.68
[118.99]
0.19
[4.83] TYP
3.80
[96.65]
2.50
[63.50]
0.75
[19.05]

TABLE 1 – GENERAL PERFORMANCE SPECIFICATIONS
II. INSTALLATION INSTRUCTIONS: Mounting the SIMG onto the KBMG
See igure 3 on page 7. Note: This igure is also supplied as a separate drawing.
arning! Make sure all power is disconnected from the KBMG before
proceeding.
A. Removing the KBMG Finger-Safe Cover
I a inger-sa e cover is not installed on the KBMG, proceed to section IIC (Modi ying
the KBMG Finger-Sa e cover). I a inger-sa e cover is installed on the KBMG,
remove the two (2) socket head 5-40 X 5/16” screws located at the rear o the KBMG
using the supplied 3/32” hex key. Also, remove the two (2) 6-32 X 1-3/4” screws
located on either side o terminal block TB1. See igure 4 on page 8.
6
—
±5 to ±25
MAX Trimpot Range (with 10V DC Input) (% Speed)
Parameter Specification Factory Setting
Voltage Following Input Range (V DC) -10 to +10
Potentiometer Operation (kΩ) 5 —
OFFSET Trimpot Range (with 0V DC Input) (% Speed) ± 50 0
+15V DC and -15V DC Power Supply Max. Current Rating (mA DC)
0 – 110 100
25 —
Forward, Reverse, and Enable Input Switch Types Dry Contact or
Open Collector
Input/Output Linearity (%) 0.1 —
Thermal Dri t (mV/ ºC) 0.4 —
Ambient Operating Temperature Range (ºC) 0 – 50
—
!

B. Removing Terminal Block
TB1 from the KBMG
Remove terminal block TB1 rom
the KBMG by rocking it back and
orth or using a screwdriver to gen-
tly pry it o . See igure 5 on page
9. The removed terminal block
TB1 will not be used and may be
discarded.
C. Modifying the KBMG Finger-
Safe Cover
Once the KBMG inger-sa e cover
is removed, it has to be modi ied to
accommodate the SIMG. Cut out
the inger-sa e cover panel
at seven (7) places as
shown in igure 6 on page
9. (Note: Some inger-
sa e covers may already
have the panel removed.)
To access the ield termi-
nals (F+ and F- on the
KBMG) cut out the ield
tab o the KBMG inger-
sa e cover at three (3)
places as shown in igure
7 on page 9.
7
FIGURE 3 – KBMG/SIMG ASSEMBLY DIAGRAM
Snap on cover
(4 places)
SIMG
Finger-Safe Cover
6-32 x 1-3/4" Screws
(2 places)
5-40 x 5/16"
Screws
(2 places)
Cable
Assembly
Note:
Yellow to F+
Brown to F-
SIMG
KBMG
Finger-Safe Cover
KBMG

D. Installing the KBMG Finger-
Safe Cover
Once the KBMG inger-sa e
cover has been modi ied, it
can be installed onto the
KBMG. Initially, use only the
two (2) 5-40 X 5/16” socket
head screws, using the sup-
plied 3/32” hex key. Do not
over tighten these screws or
damage may result to the
KBMG inger-sa e cover.
Note: All jumpers on the
KBMG must be set to their
appropriate positions
before installing the
KBMG finger-safe cover.
E. Installing the SIMG onto
the KBMG
The terminal block located
on the bottom o the SIMG
plugs onto the six (6) header
pins where TB1 was
removed rom the KBMG.
The two holes on the back o
the SIMG snap onto the in-
ger-sa e cover.
8
KBMG
Finger-Sa e
Cover
KBMG
5-40 x 5/16"
6-32 x 1-3/4"
Screws
FIGURE 4 – REMOVING THE KBMG
FINGER-SAFE COVER

Use the two (2) 6-32 X 1-3/4”
screws previously removed to
secure the SIMG to the KBMG. Do
not over tighten these screws or
damage may result to the SIMG and
KBMG. See igure 3 on page 7.
9
KBMG
Terminal Block
TB1
FIGURE 5 –
REMOVING
TERMINAL
BLOCK TB1
KBMG Finger-Safe Cover
Remove Panel (cut 7 places) to Install SIMG.
FIGURE 6 – REMOVING THE KBMG
FINGER-SAFE COVER PANEL
KBMG Finger-Safe Cover
Remove Tab (cut 3 places) to Access Field Terminals.
FIGURE 7 – REMOVING THE KBMG
FINGER-SAFE FIELD TAB

FIGURE 8 – CONNECTION DIAGRAM
10
-
+
+
-
DC TACHOMETER
GENERATOR
-+
G
TACH
CON3
T1(-)
T2(+)
A90
T7
A180
T50
PWR TB1
J1
ENABLE
+15V -15V SIG COM EN
CON2
OFFSET
MAX
F+ F-
F+
F-
AC
LINE
L2
L1
GROUND
DB RESP
M1
ARMATURE
7.5
5.0
1.7A
2.5
RCL FCL MAX FACC
M2 F- F+
RACC
A
FIELD
(SHUNT MOTORS ONLY)
10A
IR
SIMG BIPOLAR SIGNAL ISOLATOR

F. iring the SIMG to the KBMG
See igure 8 on page 10.
The SIMG is powered rom the KBMG with a connector that is installed rom the
SIMG CON2 to the KBMG F+ and F- terminals. The yellow wire connects to the
KBMG F+ terminal and the brown wire connects to the KBMG F- terminal. When the
ield connector is properly installed the wires should cross over each other. See ig-
ure 9. I the connector is wired incorrectly, the SIMG PWR LED will not illuminate
and the control will not operate. Note: It is recommended that these wires be twist-
ed at least three (3) times to help reduce noise.
11
FIGURE 9 – INSTALLING
FIELD CONNECTOR

III. Connections to the SIMG
Safety arning! Do not use F D-STOP-REV contacts as a safety discon-
nect since they are not fail-safe. Use only the AC line for this purpose.
Note: SIMG Enable jumper J1 must be installed, or a connection must be made
between EN and COM terminals of SIMG TB1 in order for the KBMG to operate.
A. Voltage Following – Uses a
voltage source to vary motor
speed. See igure 10. Connect
the voltage source to TB1 ter-
minals SIG and COM. When a
0V DC signal is applied, the
control will operate at the mini-
mum set speed (set by the
OFFSET trimpot on the SIMG).
When a 10V DC signal is
applied, the motor will operate
at the maximum set speed (set
by the MAX trimpot on the SIMG).
Applying a positive (+) signal to SIG terminal, with respect to COM terminal, will oper-
ate the motor in the orward direction.
12
!
3.5
Connection Designation
Supply ire Gauge (A G – Cu) Maximum Tightening Torque
(in-lbs)
MaximumMinimum
Logic Connections 24 14
TABLE 2 – TERMINAL BLOCK (TB1) IRING INFORMATION
(KBMG Jumper J4 in 10V Position)
(SIMG Enable Jumper J1 Installed)
±10VDC
EN COM SIG -15 +15
J1
TB1
VDC
FIGURE 10 – VOLTAGE FOLLO ING
CONNECTION

Applying a negative (-) signal to SIG terminal, with respect to COM terminal, will
operate the motor in the reverse direction.
13
Unidirectional With Reversing Contact Bidirectional Potentiometer
J1
TB1
5K
REV
REV FWD
FWD
STOP
EN COM SIG -15 +15 EN COM SIG -15 +15
EN COM SIG -15 +15 EN COM SIG -15 +15
J1
TB1
J1
TB1
Forward Reverse
5K
5K
J1
TB1
5K
A. B.
D. C.
FIGURE 11 – MAIN SPEED POTENTIOMETER CONNECTIONS
(KBMG Jumper J4 in 15V Position, SIMG Enable Jumper J1 Installed)

B. Signal Following from
Armature Voltage – Uses
motor armature voltage as a
signal input. I the signal input
voltage applied to the SIMG is
derived rom a motor armature
voltage output, it is necessary
to install a 1/4W resistor in
series with the signal lead into
the SIMG. For a 90V DC
motor, install a 150K resistor.
or a 180V DC motor, install a
330K resistor.
C. Unidirectional Potentiometer
Operation (Forward) – Uses a
potentiometer to vary motor speed.
See igure 11A on page 13.
Connect the 5K potentiometer to
TB1 terminals marked “SIG” (wiper
o potentiometer), “+15V” (high side
o potentiometer), and “COM” (low
side o potentiometer). Use the
potentiometer to vary motor speed.
I the motor is not running in the
desired direction, either reconnect
the high side o the potentiometer to TB1 terminal marked “-15V” or reverse the
motor leads.
14
330K
Armature Voltage
Range (VDC) 1/4W Resistor (Ω)
0 – ± 90 150K
0 – ± 180
EN COM SIG -15 +15
J1
TB1
1/4W Resistor
(See Table 3)
Armature
+
-A
FIGURE 12 – SIGNAL FOLLO ING FROM
ARMATURE VOLTAGE
TABLE 3 – RESISTOR FOR
SIGNAL FOLLO ING FROM
ARMATURE VOLTAGE

D. Unidirectional Potentiometer Operation (Reverse) – Uses a potentiometer to vary
motor speed. See igure 11B on page 13. Connect the 5K potentiometer to TB1 ter-
minals marked “SIG” (wiper o potentiometer), “-15V” (high side o potentiometer),
and “COM” (low side o potentiometer). Use the potentiometer to vary motor speed
and the switching device to select motor direction. I the motor is not running in the
desired direction, either reconnect the high side o the potentiometer to TB1 terminal
marked “+15V” or reverse the motor leads.
E. Bidirectional Potentiometer Operation – Uses a potentiometer to vary motor
speed and direction. See igure 11C on page 13. Connect the 5K potentiometer to
TB1 terminals marked “SIG” (wiper o potentiometer), “+15V” (high side o poten-
tiometer), and “-15V” (low side o potentiometer). Use the potentiometer to vary
motor speed and direction.
When the potentiometer is in the center position, the control output can be set to
zero, using the OFFSET trimpot. Rotating the trimpot clockwise will cause the motor
to rotate in the orward direction. Rotating the potentiometer counterclockwise will
cause the motor to rotate in the reverse direction.
F. Unidirectional Potentiometer with Reversing Contacts – Uses a potentiometer to
vary motor speed. See igure 11D on page 13. Connect the 5K potentiometer to TB1
terminals marked “SIG” (wiper o potentiometer), “+15V” (high side o potentiometer),
and “COM” (low side o potentiometer). Use the potentiometer to vary motor speed
and the switching device to select motor direction. When the potentiometer is set to
0% ( ully counterclockwise), the motor will operate at the minimum set speed (set by
the OFFSET trimpot on the SIMG). When the potentiometer is set to 100% ( ully
clockwise) the motor will operate at ull speed (set by the MAX trimpot on the SIMG).
15

G. Enable Switch Connection
Safety arning! Do
not use Enable or
Start/Stop contacts as a sa ety
disconnect since they are not
ail-sa e. Use only the AC line
or this purpose. See igure 13.
I a Start/Stop unction is
required, remove SIMG Enable
jumper J1 and wire a switch to
EN and COM terminals o
SIMG TB1. When the switch is
opened, the control will stop.
When the switch is closed, the
control will operate.
H. Tachometer Generator Connection
See igure 8 on page 10. To wire a 7V or 50V per 1000RPM tachometer generator
to the SIMG, connect the positive (+) side o the tachometer generator to terminal
“T2” and the negative (-) side o the tachometer generator to terminal “T1“ o the
SIMG. Note: I the positive (+) and negative (-) tachometer generator connections
are not connected as described above, the motor will run at ull speed only.
I. Motor Field Connection
I a shunt wound motor is used, the motor ield wires connect to F+ and F- terminals
on the SIMG. To access these terminals, cut out the ield tab o the SIMG inger-sa e
cover at three (3) places as shown in igure 14 on page 17.
16
EN COM SIG -15 +15
Enable
Open to Stop
J1
TB1
FIGURE 13 – ENABLE S ITCH CONNECTION
(SIMG Enable Jumper J1 Removed)
!

17
SIMG Finger-Sa e Cover
Cut Out Tab (3 Places) to Access Field Terminals.
(For Shunt Wound Motors Only.)
FIGURE 14 – REMOVING THE SIMG FINGER-SAFE COVER FIELD TAB

IV. CALIBRATION PROCEDURE
(See Safety arning, on page 1)
The SIMG is actory calibrated, but readjustments to the OFFSET and MAX trimpots can
be made to customize or a particular signal input requirement. It may be necessary to
repeat the calibration steps to achieve accurate settings.
A. Unidirectional Voltage Following Calibration
See igure 10 on page 12.
1. Apply 0V DC input signal (or connect SIG and COM terminals).
2. Monitor the KBMG output and adjust the OFFSET trimpot on the SIMG or the
desired minimum setting.
3. Apply the maximum voltage input signal.
4. Monitor the KBMG output voltage and adjust the MAX trimpot on the SIMG or the
desired maximum setting.
B. Unidirectional Potentiometer Operation Calibration:
See igure 11A, B or C on page 13.
1. Set potentiometer to 0% rotation ( ully counterclockwise).
2. Monitor the KBMG output and adjust the OFFSET trimpot on the SIMG or the
desired minimum setting.
3. Set potentiometer to 100% rotation ( ully clockwise).
4. Monitor the KBMG output voltage and adjust the MAX trimpot on the SIMG or the
desired maximum setting.
18
This manual suits for next models
1
Table of contents
Other Penta KB Power Controllers manuals
Popular Controllers manuals by other brands
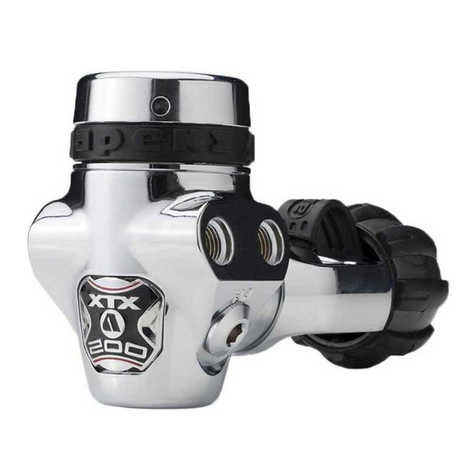
Apeks
Apeks FSR Series Technical maintenance manual

Roca
Roca SUPERMASTER 24 V DC Use manual: instructions and notices
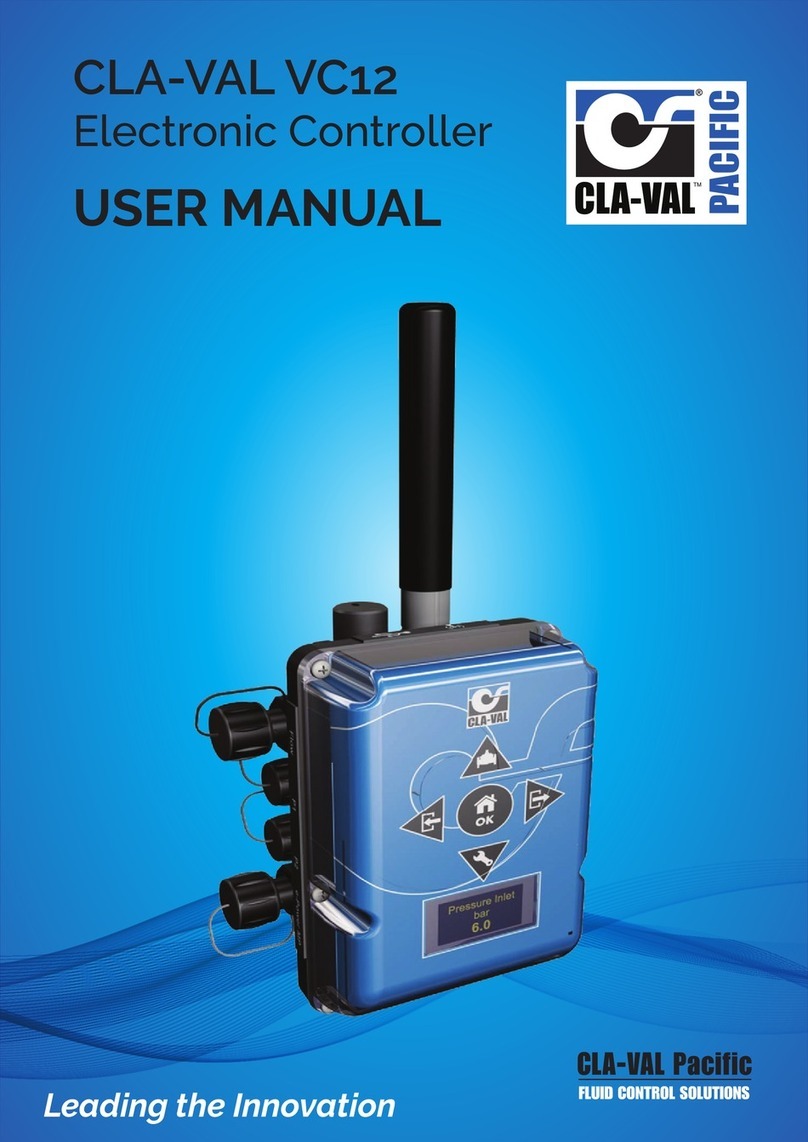
CLA-VAL
CLA-VAL VC12 user manual
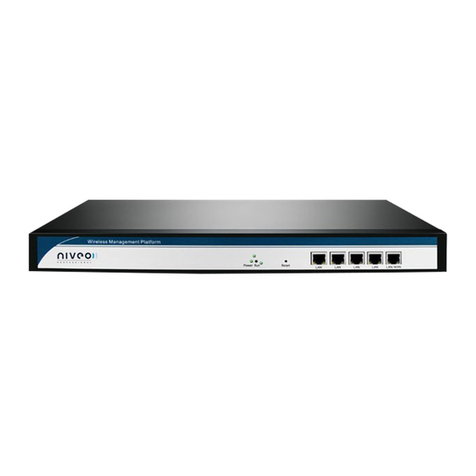
Niveo Professional
Niveo Professional NWAC7000 user manual
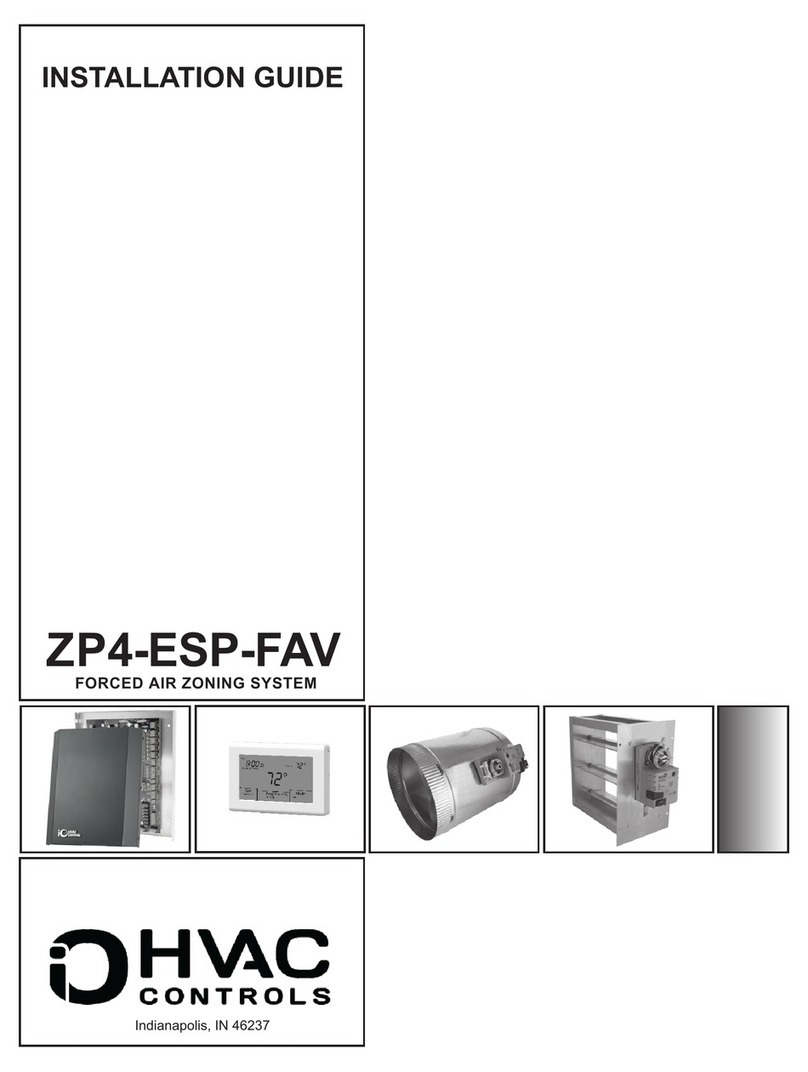
HVAC Controls
HVAC Controls ZP4-ESP-FAV installation guide
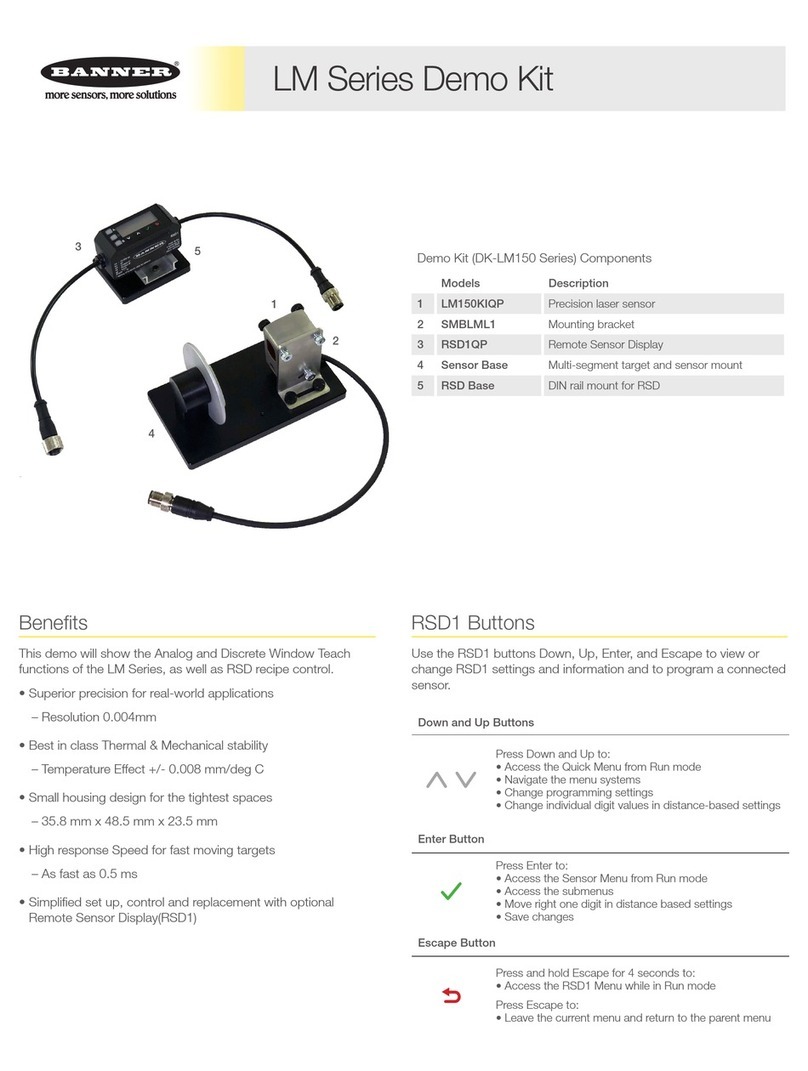
Banner
Banner LM Series quick start guide