PFS FP16 LE User manual

11785 SE Highway 212 – Suite 305
Clackamas, OR 97015-9050
(503) 650-0088
WWW.PFSTECO.COM
Pacific Energy
Fireplace Products Ltd.
Project # 20-583
Model: FP16 LE
AKA: FP16 AR LE
Type: Residential Non-catalytic Wood
Fired Heater
April 28, 2020
Revised April 14, 2021
ASTM E3053 Standard Test Method for
Determining Particulate Matter
Emissions from Wood Heaters Using
Cordwood Test Fuel (EPA ALT-125)
Contact: Mr. Jeff Bain
2975 Allenby Road
Duncan, BC V9L 6V8, Canada
Jeff.Bain@pefp.net
250-748-1184
Prepared by: Sebastian Button,
Laboratory Supervisor

Project # 20-583 Model: FP16 LE
Page | 1
Revision Summary
Date: April 28, 2020 –Original Issue
Date: October 14, 2020 –The following revisions were made per request from EPA:
-A drawing of the firebox and volume calculations were added to the main test report, page 11.
Date: December 18, 2020 –The following revisions were made per request from EPA:
-The “Notes” section was edited to provide clarity with respect to fuel preparation and
characteristics, as well as address negative filter weights.
Date: February 22, 2021 - The following revisions were made per request from EPA:
-The “Notes” section was further edited to clarify that conditioning was done at a medium burn
setting.
-The user manual was updated to provide more detailed instruction on proper use of the air
control, see appendix B.
-The “Test Run Narrative” section was updated to state that the medium fire test was performed
on a coal bed established by performing a non-sampling high fire test.
Date: March 4, 2021 - The following revisions were made per request from EPA:
-Revision summary for the October 14, 2020 revision was added, it had previously been omitted
and the change listed was erroneously shown in the December 18, 2020 entry, this has now been
corrected.
Date: April 14, 2021 - The following revisions were made per request from EPA:
-A copy of the laboratory sample analysis procedures was added to appendix A.

Project # 20-583 Model: FP16 LE
Page | 2
Contents
Affidavit ......................................................................................................................................................... 3
Introduction ................................................................................................................................................... 4
Notes ......................................................................................................................................................... 4
Wood Heater Identification and Testing ........................................................................................................ 5
Test Procedures and Equipment .................................................................................................................. 6
Results .......................................................................................................................................................... 7
Summary Table ......................................................................................................................................... 7
Test Run Narrative .................................................................................................................................... 8
Run 1 ..................................................................................................................................................... 8
Run 2 ..................................................................................................................................................... 8
Run 3 ..................................................................................................................................................... 8
Test Conditions Summary ............................................................................................................................. 9
Appliance Operation and Test Settings .................................................................................................... 9
Settings & Run Notes ................................................................................................................................ 9
Appliance Description ................................................................................................................................. 10
Appliance Dimensions ............................................................................................................................. 10
Firebox Volume ....................................................................................................................................... 11
Test Fuel Properties .................................................................................................................................... 14
Sampling Locations and Descriptions ......................................................................................................... 15
Sample Points ......................................................................................................................................... 15
Sampling Methods ...................................................................................................................................... 16
Analytical Methods Description ................................................................................................................... 16
Calibration, Quality Control and Assurances .............................................................................................. 16
Appliance Sealing and Storage ................................................................................................................... 16
Sealing Label .......................................................................................................................................... 16
Sealed Unit .............................................................................................................................................. 17
List of Appendices ....................................................................................................................................... 18

Project # 20-583 Model: FP16 LE
Page | 3
Affidavit
PFS-TECO was contracted by Pacific Energy Fireplace Products Ltd. (Pacific Energy) to
provide testing services for the FP16 LE Wood-Fired Room Heater per ASTM E3053,
Standard Test Method for Determining Particulate Matter Emissions from Wood Heaters
Using Cordwood Test Fuel, which was approved for use under EPA ALT-125. All testing
and associated procedures were conducted at PFS-TECO’s Portland Laboratory
beginning on 4/3/2020 and ending on 4/3/2020. PFS-TECO’s Portland Laboratory is
located at 11785 SE Highway 212 –Suite 305, Clackamas, Oregon 97015. Testing
procedures followed ASTM E3053, with variances as described in EPA ALT-125.
Particulate sampling was performed per ASTM E2515, Standard Test Method for
Determination of Particulate Matter Emissions Collected by a Dilution Tunnel, with the
exception of caveats described in EPA ALT-125.A copy of EPA ALT-125 is included in
Appendix A for reference, as required by the approval letter.
PFS-TECO is accredited by the U.S. Environmental Protection Agency for the certification
and auditing of wood heaters pursuant to subpart AAA of 40 CFR Part 60, New Source
Performance Standards for Residential Wood Heaters and subpart QQQQ of 40 CFR Part
60, Standards of Performance for New Hydronic Heaters and Forced Air Furnaces,
Methods 28R, 28WHH, 28 WHH-PTS, and all methods listed in Sections 60.534 and
60.5476. PFS-TECO holds EPA Accreditation Certificate Numbers 4 and 4M (mobile).
PFS-TECO is accredited by IAS to ISO 17020:2012 “Criteria for Bodies Performing
Inspections”, and ISO 17025:2005 “Requirements for Testing Laboratories.” PFS-TECO
is also accredited by Standards Council of Canada to ISO 17065:2012 “Requirements for
Bodies Operating Product Certification Systems.”
The following people were associated with the testing, analysis and report writing
associated with this project.
Sebastian Button, Laboratory Supervisor

Project # 20-583 Model: FP16 LE
Page | 4
Introduction
Pacific Energy of Duncan, BC, contracted with PFS-TECO to perform EPA certification
testing on FP16 LE Wood-Fired Room Heater. All testing was performed at PFS-TECO’s
Portland Laboratory. All testing was performed by Sebastian Button.
Notes
• Prior to start of testing, 50 hours of conditioning was performed by Pacific Energy
staff at a medium burn setting, in accordance with ASTM E3053.
• Prior to start of testing, the dilution tunnel was cleaned with a steel brush.
• Front filters were changed on sample train A at one hour for all 3 test runs.
• A total of 3 test runs were completed. Test runs were performed in accordance
with ASTM E3053. All runs have been found to be appropriate, no anomalies
happened, and all runs reported below have been validated and found compliant.
See the Run Narrative section for further detail on each run.
• All fuels loads were positioned in an east-west orientation in the firebox, in
accordance with the manufacturer’s instructions.
• No fuel pieces used for testing were intentionally debarked.
• All fuel pieces were split to meet the individual and total load weight criteria based
on the firebox volume.
• No fuel pieces were squared.
• Negative weights found on filters are due to filter material sticking to O-rings and
have been appropriately handled. Negative weights on O-rings and probes are
treated as zero in accordance with ASTM E2515.

Project # 20-583 Model: FP16 LE
Page | 5
Wood Heater Identification and Testing
• Appliance Tested:
FP16 LE
• Serial Number: 4040060459;
PFS Tracking Number 0065
• Manufacturer: Pacific Energy Fireplace Products Ltd.
• Catalyst:
No
• Heat exchange blower:
Optional
• Type:
Wood Stove
• Style:
Built-In Fireplace
• Date Received:
Thursday, March 05, 2020
• Testing Period –Start:
Friday, April 03, 2020
Finish:
Friday, April 03, 2020
• Test Location:
PFS-TECO Portland Laboratory
11785 SE HWY 212 - Suite 305, Clackamas, OR 97015
• Elevation: ~
131 Feet above sea level
• Test Technician(s):
Sebastian Button
• Observers: None

Project # 20-583 Model: FP16 LE
Page | 6
Test Procedures and Equipment
All Sampling and analytical procedures were performed by Sebastian Button. All
procedures used are directly from ASTM E3053 and ASTM E2515. See the list below for
equipment used. See Appendix C submitted with this report for calibration data.
Equipment List:
Equipment ID#
Equipment Description
041
Rice Lake 3'x3' floor scale w/digital weight indicator
132
Digiweigh DWP-440 Platform Scale
53
APEX XC-60-ED Digital Emissions Sampling Box A
54
APEX XC-60-ED Digital Emissions Sampling Box B
57
California Analytical ZRE CO2/CO/O2 IR ANALYZER
064
Digital Barometer
109A/B
Troemner 100mg/200mg Audit Weights
107
Sartorius Analytical Balance
051
10 lb audit weight
101
Dewalt Tape Measure
117
Digital Calipers
095
Anemometer
111
Microtector
115
Delmhorst Wood Moisture Meter
SA17187
Gas Analyzer Calibration Span Gas
CC170624
Gas Analyzer Calibration Mid Gas

Project # 20-583 Model: FP16 LE
Page | 7
Results
The weighted average emissions rate for the 3 run test series was measured to be 1.4
g/hr with a Higher Heating Value efficiency of 63%. The average CO emission rate for the
3 tests was 0.9 g/min. The Pacific Energy FP16LE Wood-Fired Room Heater meets the
2020 cordwood PM emission standard of ≤2.5 g/hr per CFR 40 part 60, §60.532 (c).
Detailed individual run data can be found in Appendix A submitted with this report.
Summary Table
High Fire
Test
Low Fire
Test
Medium Fire
Test
Date
4/3/2020
4/3/2020
4/3/2020
Run Number
1
2
3
PM Emission Rate (g/hr)
4.15
0.36
1.02
Burn Rate (kg/hr)
4.25
0.98
1.47
Heat Output (BTU/hr)
46,972
12,229
17,793
HHV Efficiency (%)
57.0%
65.7%
63.7%
LHV Efficiency (%)
61.0%
70.3%
68.2%
CO Emissions (g/MJ output)
0.71
4.60
3.23
CO Emissions (g/kg dry fuel)
8.08
60.32
41.03
CO Emissions (g/min)
0.59
0.99
1.01
1st Hour Emission Rate (g/hr)
3.60
0.84
2.03
Weighting Factor (%)
20%
40%
40%
Weighted particulate emission average of 3 test runs: 1.4 grams per hour.
Weighted average HHV efficiency of 3 test runs: 63%.
Average CO emission rate for 3 test runs: 0.9 grams per minute

Project # 20-583 Model: FP16 LE
Page | 8
Test Run Narrative
Run 1
Run 1 was performed on 04/03/2020 as a high fire test run per ASTM E3053. Emissions
sampling began from a cold start ignition of kindling and start-up fuel. The test fuel load
was loaded 19 minutes into the test. Testing was completed when 90% of the test fuel
load was consumed. Total test time was 81 minutes, main test fuel load burn time was 62
min. The particulate emissions rate from kindling ignition to test completion was 4.15 g/hr.
The burn rate of the test fuel load was 4.25 kg/hr. The main test load portion of the run
had an overall HHV efficiency of 57%. The train A front filter was changed at 1 hr. All test
results were appropriate and valid. There were no anomalies and all test criteria were
met.
Run 2
Run 2 was performed on 04/03/2020 as a low fire test run per ASTM E3053. The overall
test duration was 354 minutes. The burn rate for the test run was 0.98 kg/hr. The
particulate emissions rate for the test run was 0.36 g/hr. The run had an overall HHV
efficiency of 65.7%. The train A front filter was changed at 1 hr. All test results were
appropriate and valid. There were no anomalies and all test criteria were met.
Run 3
Run 3 was performed on 04/03/2020 as a medium fire test run per ASTM E3053. A non-
sampling high fire test was performed to establish a coal bed prior to starting the run. The
overall test duration was 230 minutes. The burn rate for the test run was 1.47 kg/hr,
therefore the medium fire category requirements were met, less than the mid-point of the
high and low burn rates (2.62 kg/hr). The particulate emissions rate for the test run was
1.02 g/hr. The run had an overall HHV efficiency of 63.7%. The train A front filter was
changed at 1 hr. There were no anomalies and all criteria were met.

Project # 20-583 Model: FP16 LE
Page | 9
Test Conditions Summary
Testing conditions for all runs fell within allowable specifications of ASTM E3053 and
ASTM E2515. A summary of facility conditions, fuel burned, and run times is listed below.
1This is the weight of the kindling and startup fuel
2Total test time was 81 min, high fire test load burn duration was 62 min.
Appliance Operation and Test Settings
The appliance was operated according to procedures as described in the Operations
Manual, found in Appendix B submitted with this report. Detailed run information can be
found in Appendix A submitted with this report.
Settings & Run Notes
Pre-Burn Air Setting
Test Run Air and Fan Settings
Run 1
N/A –Cold Start Ignition
Air control set to high fire test setting (fully open), fan on (single
speed).
Run 2
Air control set to High Fire Setting in
accordance with ASTM E3053
Air control set to low fire test setting (fully closed), fan on (single
speed).
Run 3
Air control set to High Fire Setting in
accordance with ASTM E3053
Air control set to medium fire test setting (1/4” PAC Opening), fan on
(single speed).
Runs
Ambient (°F)
Relative
Humidity (%)
Average
Barometric
Pressure
(In. Hg.)
Preburn
Fuel
Weight
(lbs)
Test Fuel
Weight
(lbs)
Test Fuel
Moisture
(%DB)
Test Run
Time
(Min)
Pre
Post
Pre
Post
1
59
63
41.2
40.5
30.05
4.941
13.19
21.1%
812
2
63
65
39.9
31.8
29.99
13.19
15.56
22.1%
354
3
68
65
30.2
30.3
29.88
13.64
15.31
22.8%
230

Project # 20-583 Model: FP16 LE
Page | 10
Appliance Description
Model(s): FP16 LE
Additional Models Discussion: In addition to the tested model, this design is offered as
the FP16 AR LE. The difference between the models is that the FP16 LE has a rectangular
door design, while the FP16AR LE has an arched door design. Both models use an
identical design in aspects that may affect emissions or air control and are presumed to
have the same emissions performance as the test specimen provided for certification.
Appliance Type: Built-in Fireplace
Firebox Volume: 1.33 ft3
Air Introduction System: Primary Air enters the firebox from the front bottom of the
appliance and is channeled up the sides on the appliance and down through the air wash,
as well as through a pilot air opening in the front of the firebox. Primary air is controlled
via a damper arm located below the ashlip which moves left (open) to right (closed).
Secondary air is pulled through a fixed opening in the rear bottom of the appliance and
channeled up through secondary air baffle. Dimensions on all these features can be found
in Appendix D.
Baffles: A stainless steel secondary air baffle directs all flames towards the front of the
firebox.
Refractory Insulation: The firebox is lined with 1” thick firebrick.
Flue Outlet: 6-inch exhaust outlet located on the top of the appliance.
Fan: The FP16 LE is equipped from the factory with a convection fans that attach to either
side of the appliance.
Appliance Dimensions
FP16 LE Unit Dimensions
Height
Width
Depth
Firebox Volume
39”
38”
18.5
1.33 ft3
Appliance design drawings can be found in Appendix D submitted with the CBI copy of
this report.

Project # 20-583 Model: FP16 LE
Page | 11
Firebox Volume

Project # 20-583 Model: FP16 LE
Page | 12
Appliance Front
Appliance Left

Project # 20-583 Model: FP16 LE
Page | 13
Appliance Right
Appliance Rear

Project # 20-583 Model: FP16 LE
Page | 14
Test Fuel Properties
Test fuel used was Maple cordwood, split and air-dried to the specified moisture content
range. Typical fuel loads are pictured below:
Typical Kindling Load Typical Startup Load
Typical High Fire Load Typical Low Fire Load

Project # 20-583 Model: FP16 LE
Page | 15
Sampling Locations and Descriptions
Sample ports are located 16.5 feet downstream from any disturbances and 1 foot
upstream from any disturbances. Flow rate traverse data was collected 12 feet
downstream from any disturbances and 5.5 feet upstream from any disturbances. (See
below).
Sample Points

Project # 20-583 Model: FP16 LE
Page | 16
Sampling Methods
ASTM E2515 was used in collecting particulate samples. The dilution tunnel is 6 inches
in diameter. All sampling conditions per ASTM E2515 were followed. No alternate
procedures were used with the exception of caveats described in ALT-125: Pall TX40
Emfab filters were used, filter temperatures were maintained between 80 and 90°F for all
tests, filters were weighed in pairs where applicable, and no sampling intervals fell outside
of proportional rates of +/- 10%.
Analytical Methods Description
All sample recovery and analysis procedures followed ASTM E2515 procedures. At the
end of each test run, filters, O-Rings and probes were removed from their housings,
dessicated for a minimum of 24 hours, and then weighed at 6 hour intervals to a
constant weight per ASTM E2515-11 Section 10.
Calibration, Quality Control and Assurances
Calibration procedures and results were conducted per EPA Method 28R, ASTM E2515-
11 and ASTM E3053. Test method quality control procedures (leak checks, volume meter
checks, stratification checks, proportionality results) followed the procedures outlined.
Appliance Sealing and Storage
Upon completion of testing, the appliance was secured with metal strapping and the seal
below was applied, the appliance was then returned to the manufacturer’s location at:
2975 Allenby Road Duncan, BC V9L 6V8, Canada, for archival.
Sealing Label

Project # 20-583 Model: FP16 LE
Page | 17
Sealed Unit

Project # 20-583 Model: FP16 LE
Page | 18
List of Appendices
The following appendices have been submitted electronically in conjunction with this
report:
Appendix A –Test Run Data, Technician Notes, Sample Analysis, and Alternate Test
Method Approval
Appendix B –Labels and Manuals
Appendix C –Equipment Calibration Records
Appendix D –Design Drawings (CBI Report Only)
Appendix E –Manufacturer QAP (CBI Report Only)

SECTION 1 – Model Identification
Model Name(s)/Number(s) FP16LE
Manufacturer Pacific Energy Fireplace Products
Address 1 2975 Allenby Road
Address 2 Duncan, BC V9L 6V8, Canada
Appliance Category(s) (Free-standing, Insert, etc.) Built-in Fireplace
Usable Firebox Volume - ft31.33
Catalytic/Non-Cat Non-Cat
Convection Air Fan (No, Standard, Optional) Optional
SECTION 1B – Laboratory Information
Testing Laboratory PFS-TECO
Address 1 11785 SE Hwy 212 Ste 305
Address 2 Clackamas, OR 97015
ISO/Accreditation Info ISO 17025
Dates Tested 4/3/2020
Test Methods/Standards ASTM E3053 (ALT-125), ASTM E2515
Dilution Tunnel Inside Diameter - in. 6.00
Filter Diameter - mm 47
Filter Material Pall Type TX40
WOOD HEATER TESTING SUMMARY
Table of contents
Other PFS Heater manuals
Popular Heater manuals by other brands

Scarlett
Scarlett Comfort SC-FH53007 instruction manual
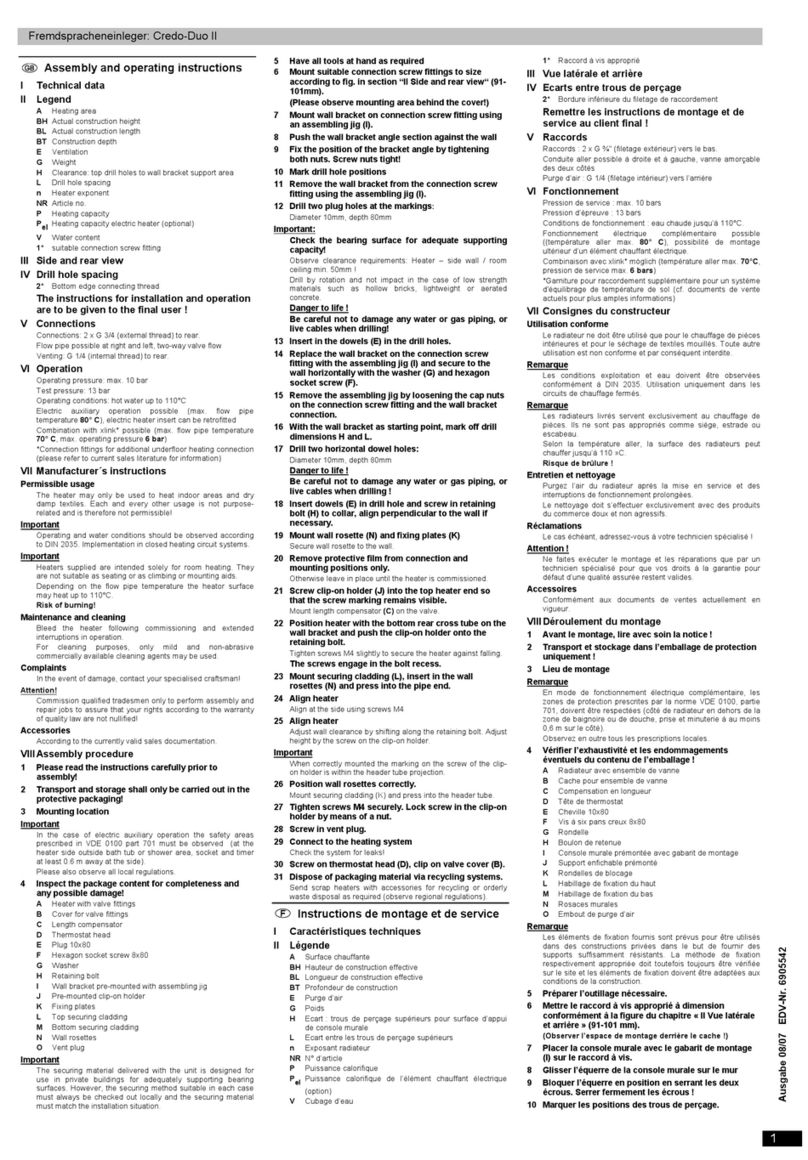
Kermi
Kermi Credo-Duo II Assembly and operating instructions

GoodHome
GoodHome Kelso DQ1920 Assembly manual
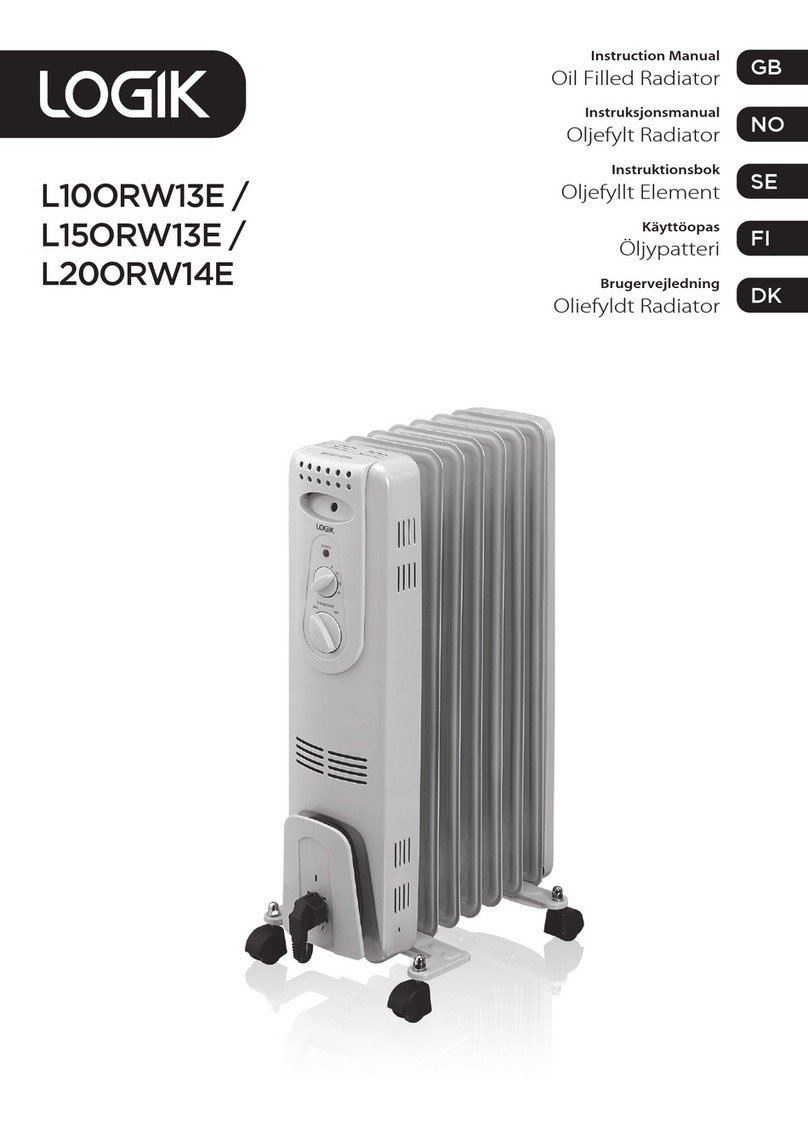
Logik
Logik L20ORW14E instruction manual
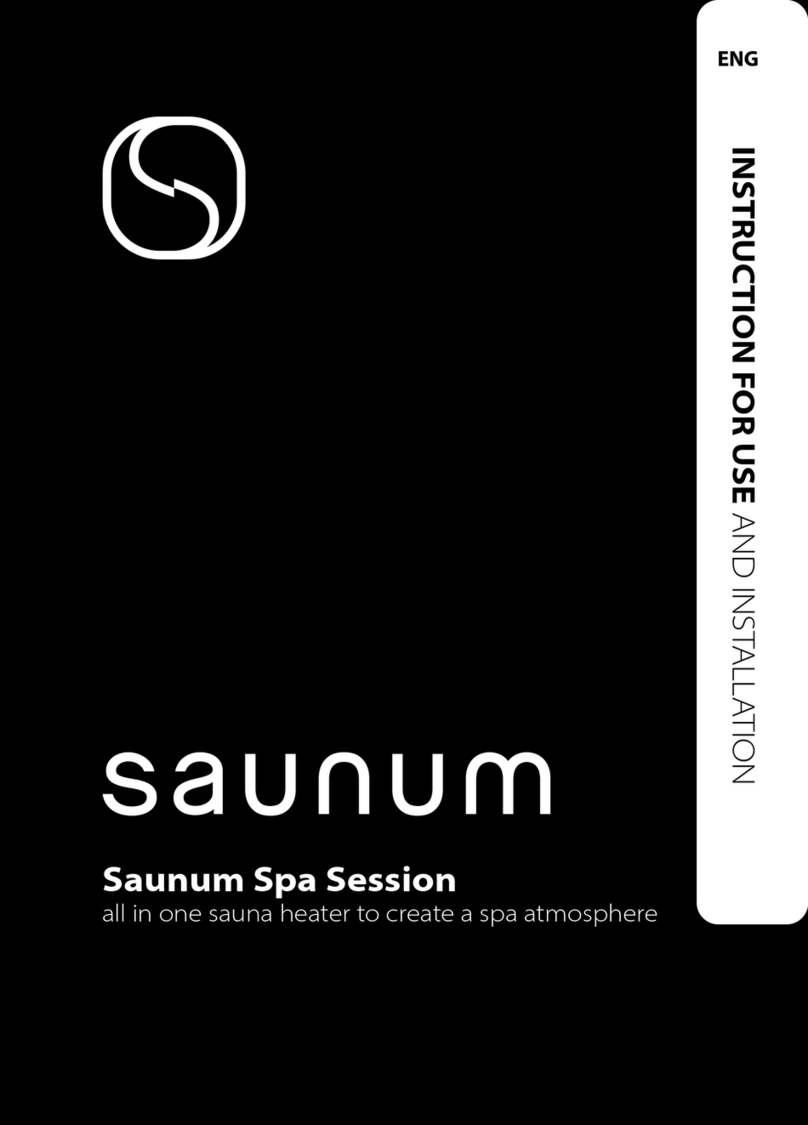
Saunum
Saunum Spa Session Instructions for use and installation
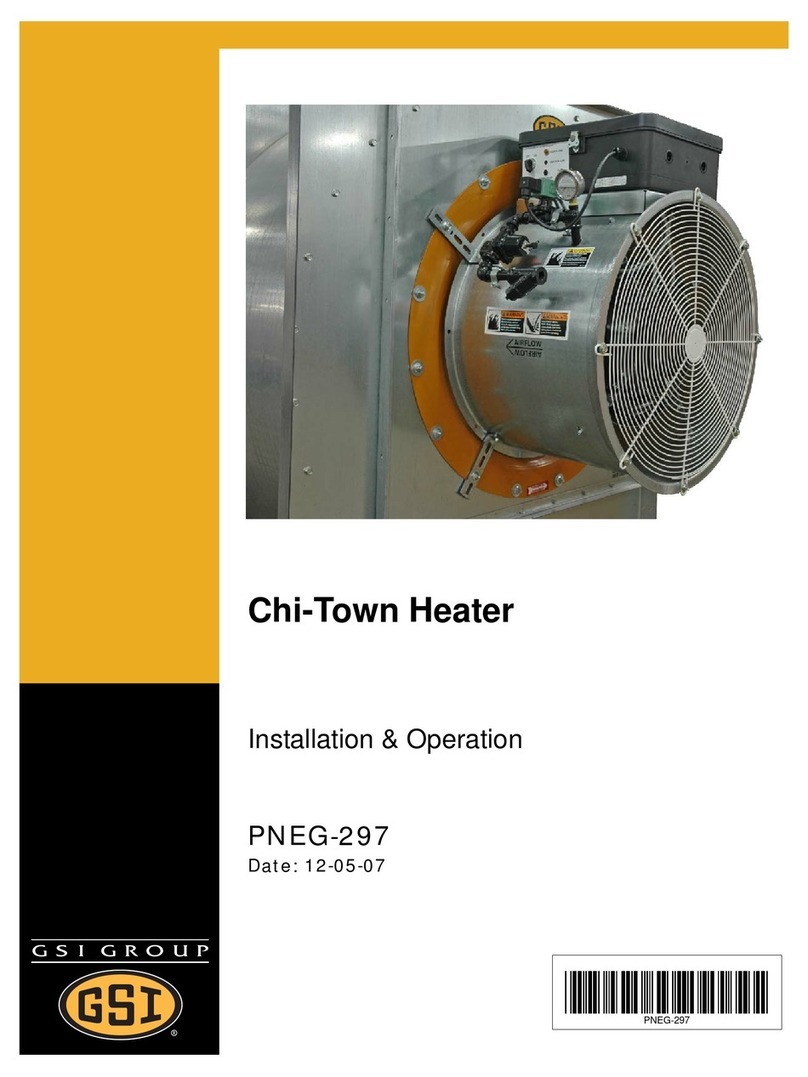
GSI Group
GSI Group Chi-Town Installation & operation