Phase Technologies SD Series User manual

Operation & Installation Manual
2XD
SERIES
SD
SERIES
PHASE
TECHNOLOGIES
Phase Converting | Voltage Doubling
VARIABLE FREQUENCY DRIVES

#3187280
2020 © Copyright.V2.3 All rights reserved. All contents are property of Phase Technologies, LLC.
No portion of this publication or its contents may be duplicated by any means, electronic or otherwise, without the express written consent of Phase
Technologies, LLC.
CONTACT INFORMATION
Address: 231 E. Main Street North, Rapid City, SD 57701
Phone: 605-343-7934
Fax: 605-343-7943
Toll Free: 866-250-7934
www.phasetechnologies.com
SD0xx Series & SD4xx Series
Phase Converting
Variable Frequency Drives
2XD2xx Series
Phase Converting & Voltage Doubling
Variable Frequency Drives

ii | P a g e
SAFETY MESSAGES AND WARNINGS
To ensure safe and reliable operation of the Essential Series drives, it is important to carefully read this
manual and to observe all warning labels attached to the unit before installing. Please follow all
instructions exactly and keep this manual with the unit for quick and easy reference.
Definitions of Warning Signs and Symbols
CAUTION: Indicates a potentially hazardous situation that could result in injury or damage to the
product.
WARNING: Indicates a potentially hazardous situation that could result in serious injury or death.
HIGH VOLTAGE: The voltage associated with the procedures referenced could result in serious
injury or death. Use caution and follow instructions carefully.
READ THESE WARNINGS BEFORE INSTALLING
OR OPERATING EQUIPMENT!
WARNING: Risk of electric shock. More than one disconnect switch may be required to de-
energize the equipment before servicing.
WARNING: Risk of electric shock. De-energize the unit by disconnecting all incoming sources of
power, then wait 10 minutes for internal charges to dissipate before servicing the equipment.
HIGH VOLTAGE: This equipment is connected to line voltages that can create a potentially
hazardous situation. Electric shock could result in serious injury or death. This device should be
installed only by trained, licensed, and qualified personnel. Follow instructions carefully and observe all
warnings.
WARNING: This equipment should be installed and serviced by qualified personnel familiar with
the type of equipment and experienced in working with dangerous voltages.
WARNING: Installation of this equipment must comply with the National Electrical Code (NEC) and
all applicable local codes. Failure to observe and comply with these codes could result in risk of electric
shock, fire, or damage to the equipment.
CAUTION: Circuit breakers, fuses, proper ground circuits, and other safety equipment and their
proper installation are not provided by Phase Technologies, LLC, and are the responsibility of the end
user.

iii | P a g e
CAUTION: Failure to maintain adequate clearance may lead to overheating of the unit and cause
damage or fire.
WARNING: Input power connections should be made by a qualified electrician into circuit with
adequate voltage and current carrying capacity for the model. Branch circuit protection to the unit
should be provided by appropriately sized fuses or a circuit breaker.
CAUTION: Use 600 V vinyl-sheathed wire or equivalent. The voltage drop of the leads needs to be
considered in determining wire size. Voltage drop is dependent on wire length and gauge. Use only
copper conductors.
CAUTION: Wires fastened to the terminal blocks shall be secured by tightening the terminal screws
to a torque value listed in Table 6 and Table 7.
CAUTION: The input wire gauge must be sized to accommodate the single-phase input current,
which will be significantly larger than the three-phase output current to the load.
CAUTION: The maximum wire gauge for the input terminals is listed in Table 6 and Table 7.
CAUTION: Never allow bare wire to contact metal surfaces.
CAUTION: Never connect AC main power to the output terminals U, V, W or Red, Blk/Yel, and Blk.
WARNING: Under certain conditions, the motor load may automatically restart after a trip has
stopped it. Make sure power to the drive has been disconnected before approaching or servicing the
equipment. Otherwise, serious injury may occur.

iv | P a g e
TABLE OF CONTENTS
INTRODUCTION.....................................................................................................................................................1
MODELS AND RATINGS........................................................................................................................................2
2.1 Model Nomenclature ....................................................................................................................2
2.2 Model Ratings................................................................................................................................3
2.3 Dimensional Drawings................................................................................................................... 4
2.4 Drive Configuration and Options.................................................................................................11
2.5 System Configuration Settings ....................................................................................................11
INSTALLATION....................................................................................................................................................12
3.1 Mounting.....................................................................................................................................12
3.2 Source Branch Circuit Protection........................................................................................... 13
3.3 Installing Power Cables........................................................................................................... 13
3.4 Control Terminals ........................................................................................................................17
3.5 Installing Power Cables................................................................................................................21
USING THE KEYPAD & DISPLAY .......................................................................................................................23
4.1 Display Modes .............................................................................................................................23
4.2 Password Protecting the Keypad................................................................................................. 23
4.3 Keypad Display Messages............................................................................................................24
4.4 Keypad Main Menu Items ...........................................................................................................25
4.5 Change Parameter Values ...........................................................................................................26
4.6 Read Measured Values................................................................................................................27
4.7 Read Timers.................................................................................................................................29
4.8 Restart Log...................................................................................................................................31
4.9 Fault Log ......................................................................................................................................32
ADJUSTABLE PARAMETERS.............................................................................................................................34
5.1 Changing Parameter Values ........................................................................................................ 34

v | P a g e
5.2 Restore Default Parameter Settings............................................................................................36
5.3 Auto Restarts ...............................................................................................................................36
5.4 All Parameters List.......................................................................................................................37
5.5 Changed Parameter List ..............................................................................................................37
OPERATION.........................................................................................................................................................47
6.1 Commissioning the Unit ..............................................................................................................47
6.2 Ground Fault Detection ...............................................................................................................47
6.3 Drive Set-up Procedure ...............................................................................................................48
6.4 Motor Overload Protection .........................................................................................................49
6.5 System Configuration ..................................................................................................................49
6.6 Start-Up and Shut-Down Ramp Times.........................................................................................51
CONSTANT PRESSURE SYSTEMS ....................................................................................................................53
7.1 Control Principles of Constant Pressure Systems........................................................................53
7.2 Perfect Pressure™ Setup –Analog Constant Pressure ................................................................57
7.3 Analog Constant Pressure Systems .............................................................................................58
7.4 Pre-Charge Mode.........................................................................................................................62
7.5 Lead/Lag Pump Control ...............................................................................................................63
7.6 Duplex / Multiplex Control ..........................................................................................................66
7.7 Tank Sizing ...................................................................................................................................69
7.8 Troubleshooting Constant Pressure Systems ..............................................................................69
TROUBLESHOOTING..........................................................................................................................................70
8.1 Fault Codes ..................................................................................................................................70
8.2 Clearing a Fault............................................................................................................................71
ROUTINE INSPECTION AND MAINTENANCE....................................................................................................75

INTRODUCTION
SD & 2XD Series variable frequency drives (VFDs) are inverter-based devices that convert single-
phase AC power to three-phase variable frequency output to provide speed control for three-phase AC
motors. The drives offer advanced motor control features through an intuitive, easy to use interface.
The simplified block diagrams below demonstrate how the drive converts the incoming single-phase AC
power to DC, then utilizes an inverter module to generate three-phase variable voltage and frequency
output to control the speed of the primary motor.
Figure 1 –SD Series Block Diagram
Figure 2 –2XD Series Block Diagram

2 | P a g e
MODELS AND RATINGS
2.1 Model Nomenclature
Figure 3 –SD Series Nomenclature
Figure 4 –2XD Series Nomenclature

3 | P a g e
2.2 Model Ratings Table 1 –SD Series Model Ratings
Model
Rated
HP
Rated Input
Voltage
Rated
Input
Current
Rated Output
Voltage
Rated
Output
Current
Switching
Frequency*
Weight
SD002
2
240V
Single
Phase
20 A
240V
Three
Phase
8 A
2-8 kHz
15 lb
SD003
3
30 A
10 A
15 lb
SD005
5
42 A
18 A
20 lb
SD007
7.5
58 A
27 A
20 lb
SD010
10
69 A
33 A
20 lb
SD015
15
92 A
46 A
145 lb
SD405
5
480V
Single
Phase
30 A
480V
Three
Phase
10 A
30 lbs
SD407
7.5
37 A
13 A
30 lbs
SD410
10
42 A
18 A
35 lbs
SD415
15
56 A
24 A
40 lbs
*Factory default for Switching Frequency is 2 kHz. Switching Frequency is an adjustable parameter set
through the keypad. Weights do not include optional output filter.
Table 2 –2XD Series Model Ratings
Model
Rated
HP
Rated Input
Voltage
Rated
Input
Current
Rated Output
Voltage
Rated
Output
Current
Switching
Frequency*
Weight
2XD205
5
240V
Single Phase
31 A
480V
Three
Phase
10 A
2-8 kHz
64 lb
2XD207
7.5
52 A
13 A
64 lb
2XD210
10
64 A
18 A
65 lb
2XD215
15
Upgraded to 1LH Series product line. See 1LHE215R
*Factory default for Switching Frequency is 2 kHz. Switching Frequency is an adjustable parameter set
through the keypad.
Weights do not include optional output filter.

4 | P a g e
2.3 Dimensional Drawings
Figure 5 –SD Series Line Drawing

8 | P a g e
Figure 9 –SD Series Line Drawing

9 | P a g e
Figure 10 –SD Series Line Drawing

10 | P a g e
Figure 11 –2XD Series Line Drawing

11 | P a g e
2.4 Drive Configuration and Options
SD & 2XD Series drives can be configured with a variety of optional equipment. Please remember to
follow all applicable NEC and local codes to ensure safety and compliance.
CAUTION: When not ordered and installed by Phase Technologies, circuit breakers or fuses,
proper ground circuits, disconnects and other safety equipment and their proper installation are the
responsibility of the end user.
CAUTION: The AC motor load must be connected directly to the main output terminals of the
panel. Do not install relays or disconnect switches between the output terminals and the motor
load.
Fuses or motor overload devices as required by NEC and local safety codes may be installed between
the drive and the motor, however the SD & 2XD Series are equipped with adjustable solid state motor
overload protection.
Output Filters
Some installations may require a load reactor or sine wave filter between the drive and the motor. A
filter reduces harmonics in the PWM output voltage, smoothing the waveforms to reduce vibration in the
motor. Filters also reduce common mode currents in the motor windings that can discharge through
motor bearings, causing pitting and premature motor failure.
Mitigating Electromagnetic Interference (EMI)
Devices that utilize power switching electronics, such as SD & 2XD Series drives, produce high
frequency emissions commonly known as electromagnetic interference (EMI). These emissions can be
conducted on power cables or emitted (radiated) through the air. Conducted and emitted noise can
sometimes interfere with radio signals or sensitive electronic equipment near the installation. The use
of shielded cables and rigid metal conduit on both input and output lines between the converter and the
motor is recommended to help reduce EMI.
2.5 System Configuration Settings
A SD & 2XD Series drives are capable of operating several types of systems, including:
•Simple ON/OFF motor control from the keypad or remote switches
•Digital constant pressure water systems
•Analog constant pressure water systems
•Multiple pump control
Firmware in the drive interprets input signals and other data differently, depending upon the type of
system being operated. It is therefore important to select the appropriate System Configuration setting
either through the Programmable Parameters on the keypad. Detailed information on setting System
Configuration can be found in Section 6.5.

12 | P a g e
INSTALLATION
3.1 Mounting
The drive must be mounted in an upright position with adequate clearance for cooling and maintenance
access. See Section 2.3 for details. The mounting surface must be sturdy and capable of bearing the
weight of the unit. Fasten the unit to the mounting surface using screws or bolts of an appropriate size
through the holes on the mounting brackets. The enclosure can be wall mounted. Brackets for wall
mounting are standard. Lifting hooks are provided on the top of the enclosure.
In order to allow for proper cooling and air circulation around the enclosure, maintain minimum
clearance of 6 inches on the sides and top and 18 inches below. The drives are cooled by fans with
ventilation openings on the side and bottom of the enclosure. The surface around the enclosure should
be of a non-flammable material and clear of obstacles.
Figure 12 –Minimum Clearances
Ambient Temperature Rating
SD & 2XD Series drives are intended for use in ambient temperatures no higher
than 50˚C (122°F).
6” Minimum
6” Minimum
18” Minimum
6” Minimum
CAUTION: Failure to maintain
adequate clearance may lead to
overheating of the unit and cause
damage or fire.
NOTE: Outdoor type 3R conduit hubs should be
used with outdoor Type 3R enclosures to maintain
environmental integrity.

13 | P a g e
3.2 Source Branch Circuit Protection
Branch circuit protection must be installed in the circuit sourcing the drive. See Table 3 for
recommended circuit breaker/fuse sizing, which is based on 125% of the rated input current. Fuses may
be used for circuit protection; consult local electrical code for proper sizing. Installation of a disconnect
means within sight of the drive is recommended.
Table 3 –Fuse/Breaker Recommendations
Model
Input Current
Fuse/Breaker
SD002
20 A
25 A
SD003
30 A
40 A
SD005
42 A
55 A
SD007
58 A
75 A
SD010
69 A
90 A
SD015
92 A
115 A
SD405
30 A
40 A
SD407
37 A
50 A
SD410
42 A
55 A
SD415
56 A
70 A
2XD205
31 A
40 A
2XD207
52 A
65 A
2XD210
64 A
80 A
3.3 Installing Power Cables
CAUTION: Installations must comply with all NEC and local electrical code requirements.
Connection to input and output power is made on the power terminal block. See Table 4for connection
descriptions and Figure 14 for terminal block locations.
Important Note About Output Filters:
Models that include a sinewave filter have a different power terminal connection configuration. Refer to
Figure 15 for connecting models with output filters.
Table 4 –Power Terminal Descriptions
Terminal Name
Description
L1, L2
Input power terminals for single-phase input
U, V, W
Output power terminals for three-phase output
BUS -
*Important* DO NOT connect power
GND
Earth safety ground
Table 5 –Power Terminal Descriptions –SD002, SD003 only

14 | P a g e
Terminal Name
Description
L1, L2
Input power terminals
BLK, BLK/YEL
2-wire output power terminals
RED, BLK/YEL, BLK
3-wire output power terminals
RED
Auxiliary/Start/Run Winding
BLK/YEL
Motor Winding Common
BLK
Main Winding
GND
Earth ground
Table 6 –Input Power Terminal Wiring Specifications
Input Power Terminals
Model
SD007, SD010, SD015,
2XD205, 2XD207,
2XD210
SD002, SD003,
SD005, SD405,
SD407, SD410
Wire Size
Torque
Wire Size
Torque
2 - 6 AWG
120 lb-in
20–6 AWG
15 lb-in
8 AWG
40 lb-in
10 - 14 AWG
35 lb-in
Table 7 –Output Power Terminal Wiring Specifications
Output Power Terminals
Model
SD007-B, SD010-B, SD015, SD405, SD407,
SD410, SD415
2XD205-O, 2XD207-O, 2XD210-O,
SD002, SD003, SD005, SD007, SD010,
2XD205, 2XD207, 2XD210
Wire Size
Torque
Wire Size
Torque
4 –18 AWG
16 in. lbs
20–6 AWG
10.5 lb-in
This manual suits for next models
18
Table of contents
Other Phase Technologies DC Drive manuals
Popular DC Drive manuals by other brands
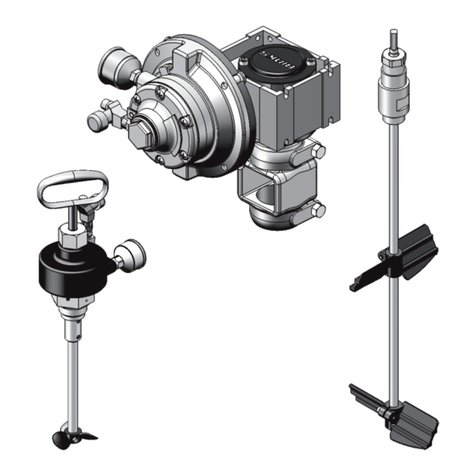
Binks
Binks QS-5012-1-CE Service manual
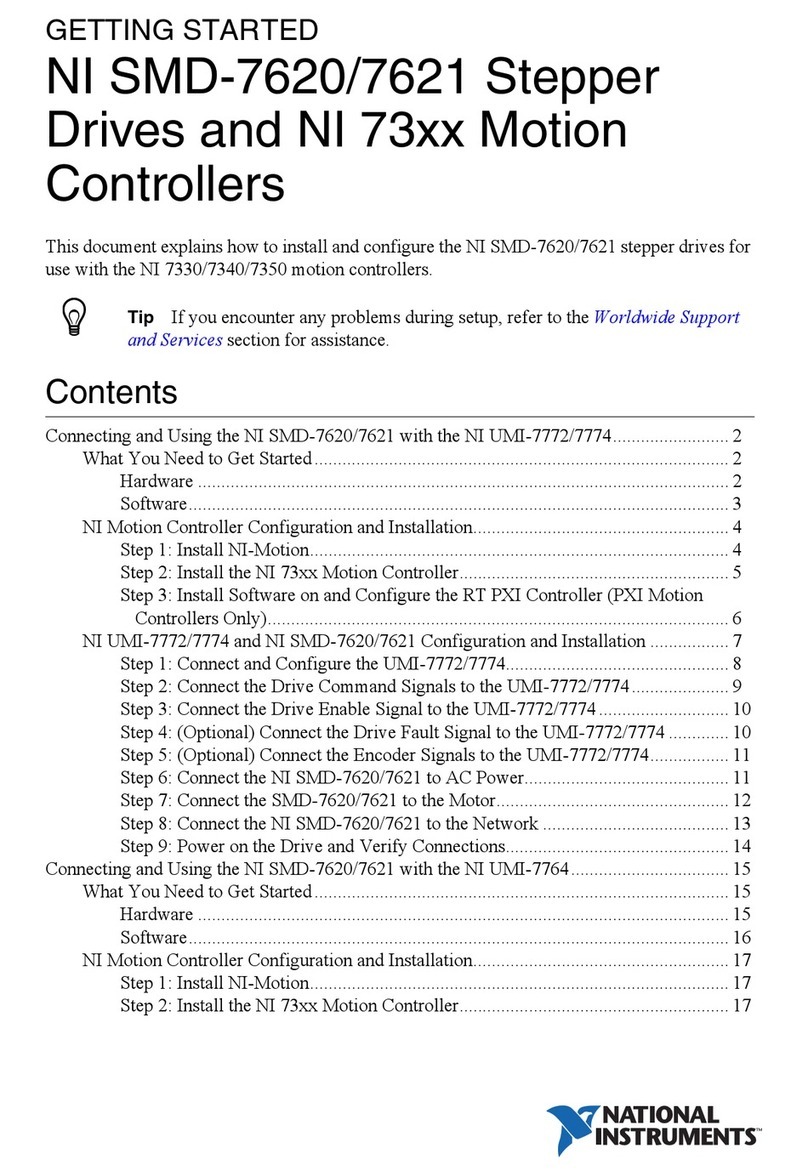
National Instruments
National Instruments NI 73 Series Getting started
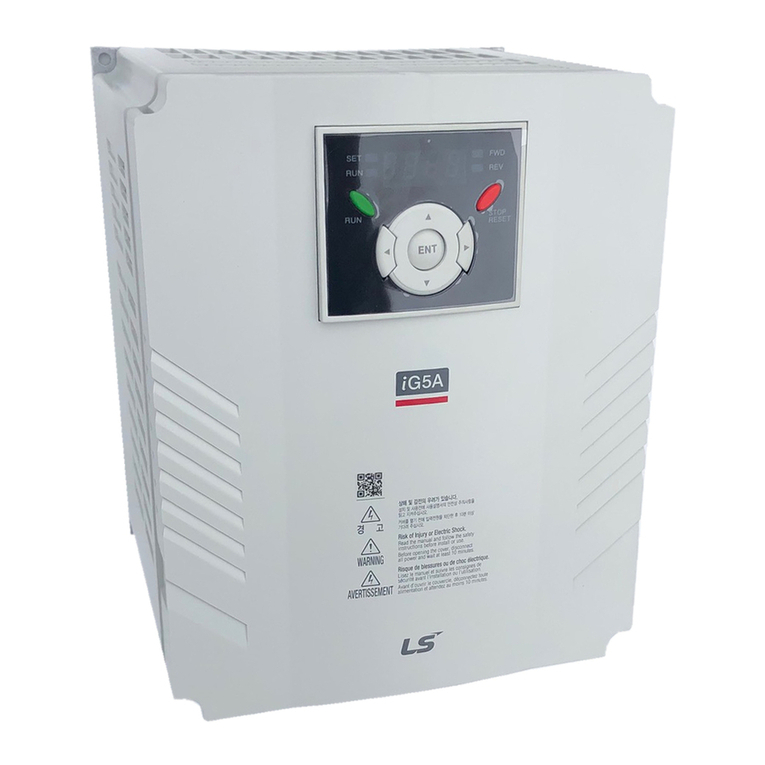
LSIS
LSIS Starvert iG5A Series manual

GFA
GFA ELEKTROMAT SI 45.15 FU-40,00 installation instructions
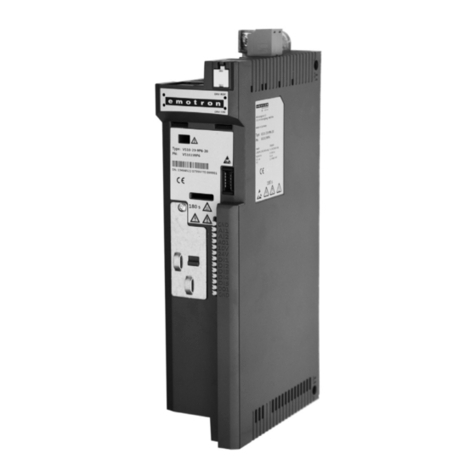
CG
CG Emotron VS30401P3 Mounting and switch on instruction
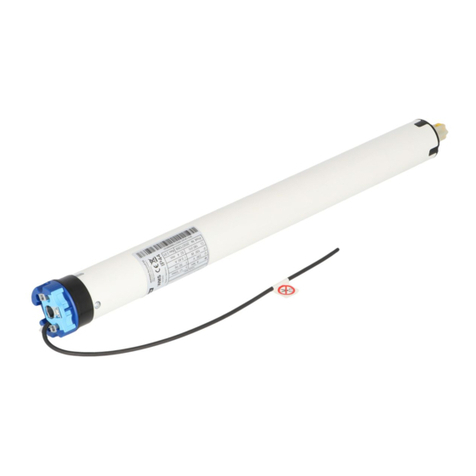
WAREMA
WAREMA WMS-ZM Setting instructions