piezosystemjena NV200/D NET User manual

1 CEO: Dr. Bernt Götz • Phone +493641/66880 • Fax +493641/668866 • www.piezosystem.com
Instruction Manual
Digital Piezo Amplifier
NV200/D NET
Please read carefully before switching on the power! Please see safety instructions for
using piezoelectric actuators and power supplies!
21.12.2021
Rev 0

2 CEO: Dr. Bernt Götz • Phone +493641/66880 • Fax +493641/668866 • www.piezosystem.com

3 CEO: Dr. Bernt Götz • Phone +493641/66880 • Fax +493641/668866 • www.piezosystem.com
Table of contents
1Introduction............................................................................................................................................. 4
2Certification of piezosystem jena ..........................................................................................................4
3Declaration of conformity....................................................................................................................... 4
4Purchased part package........................................................................................................................5
5Instructions for using piezo electrical elements and power supplies ................................................. 5
6Safety instructions.................................................................................................................................. 6
6.1 Icons ................................................................................................................................................ 6
6.2 Installation & power supply ............................................................................................................7
6.3 Operation.........................................................................................................................................7
6.4 Maintenance and inspection.......................................................................................................... 8
6.5 Environmental conditions............................................................................................................... 8
7Instructions for checking the function of the system / quick start....................................................... 8
8How to operate the digital amplifier NV200/D NET ............................................................................. 9
8.1 Introduction......................................................................................................................................9
8.2 Technical data............................................................................................................................... 10
8.3 Connectors and Pin Assignment .................................................................................................11
8.4 Establishing communication ........................................................................................................ 14
8.5 Command list ................................................................................................................................ 18
8.6 Error messages.............................................................................................................................22
8.7 Status register ............................................................................................................................... 23
8.8 Feedback control modes.............................................................................................................. 24
8.9 Arbitrary waveform generator ...................................................................................................... 27
8.10 Data recorder ................................................................................................................................ 28
8.11 Trigger............................................................................................................................................28
8.12 Temperature measurement ......................................................................................................... 29
9Troubleshooting....................................................................................................................................30

4 CEO: Dr. Bernt Götz • Phone +493641/66880 • Fax +493641/668866 • www.piezosystem.com
This instruction manual includes important information for using piezo actuators and
electronics. Please take the time to read this information. Piezo positioning systems
are mechanical systems that offer the highest precision. Correct handling
guarantees that this precision will be maintained over a long period of time.
1 Introduction
This manual describes the digital piezo amplifier series NV200/D NET from piezosystem jena. You
will also find additional information regarding piezoelectric products.
Definition: All systems from piezosystem jena such as electronics, actuators, and optical systems are
called “units”.
If you have any problems, please contact the manufacturer of the system: piezosystem jena,
Stockholmer Str. 12, 07747 Jena. Phone: +49 36 41 66 88-0
2 Certificationof piezosystem jena
The company piezosystem jena GmbH has worked according to a DIN EN ISO 9001 certified quality
management system since 1999. Its effectiveness is verified and proven by periodic audits by the
TÜV.
3 Declaration of conformity
The CE Declaration of Conformity is available on our website www.piezosystem.com.

5 CEO: Dr. Bernt Götz • Phone +493641/66880 • Fax +493641/668866 • www.piezosystem.com
4 Purchased part package
Please check the completeness of the delivery after receiving the shipment:
•piezo amplifier NV200/D NET
•wide range power supply 24 VDC
For optional needed drivers or available software see our homepage.
5 Instructions for using piezo electrical elements and power supplies
•Piezoelectric actuators from piezosystem jena are controlled by voltages up to 180 V. These
values can be quite hazardous. Therefore, read the installation instructions carefully and
ensure that only authorized personnel handle the power supply.
•After transportation, piezoelectric actuators should be allowed to adapt to room temperature
for approximately 2 hours before being switched on.
•Piezoelectric actuators are made from ceramic materials with and without metallic casings.
The piezo-ceramic is a relatively brittle material. This should be noted when handling
piezoelectric actuators. All piezo elements are sensitive to bending or shock forces.
•Due to the piezoelectric effect, piezo actuators can generate electrical charges by changing
the mechanical load or the temperature, or by actions such as the ones described above.
•Piezoelectric actuators are able to work under high compressive forces. Only actuators with a
pre-load can be used under tensile loads (these tensile forces must be less than the pre-load
given in the data sheet). Please note that acceleration of the ceramic material (e.g., caused by
fall down, discharging, or high dynamic application) will occur.
•After excitation of the actuators by a voltage in the upper control range, the ceramic will move
and generate an opposite high voltage after disconnection.
•Heating of the ceramic material will occur during dynamic operation and is caused by structure
conditional loss processes. This may cause failure if the temperature exceeds specified values
cited below. With increasing temperature up to the Curie temperature TC, (usual values
approx. 140 °C –250 °C) the piezoelectric effect disappears. We recommend working in
temperatures up to TC/2 (normally up to 80 °C).
•Piezoelectric actuators, such as stacks or other devices, work electrically as a capacitor.
These elements are able to store electrical energy over a long period of time (up to some
days) and the stored energy may be dangerous.
•If the actuator remains connected to the drive electronics, it will be unloaded within a second
after shutdown and quickly reaches harmless voltage values.
•Piezo actuators can only generate voltages by warming or cooling (caused by the longitudinal
change). The discharge potential should not be ignored due to the inner capacitance. This
effect is insignificant at usual room temperature.
•Piezo actuators from piezosystem jena are adjusted and glued. Any opening of the unit will
cause misalignment or possible malfunction and will result in the loss of the guarantee.
•Please only use original parts from piezosystem jena.
Please contact piezosystem jena or your local representative if there are any problems with your
actuator or power supply.
Caution! Shock forces may damage the built-in ceramic elements. Please avoid such forces, and
handle the units with care, otherwise the guarantee will be lost.

6 CEO: Dr. Bernt Götz • Phone +493641/66880 • Fax +493641/668866 • www.piezosystem.com
6 Safety instructions
6.1 Icons
RISK OF ELECTRIC SHOCK! Indicates that a risk of electric shock is present and the associated
warning should be observed.
CAUTION! REFER TO OPERATOR´S MANUAL –Refer to your operator’s manual for additional
information, such as important operating and maintenance instructions.
RISK OF ELECTRIC SHOCK!
•Do not open the units! There are no user serviceable parts inside and opening or removing
covers may expose you to dangerous shock hazards or other risks. Refer all servicing to
qualified service personnel.
•Do not spill any liquids into the cabinet or use the units near water.
CAUTION!
•Allow adequate ventilation around the units so that heat can properly dissipate. Do not block
ventilated openings or place the units near a radiator, oven, or other heat sources. Do not put
anything on top of the units except those that are designed for that purpose (e.g. actuators).
•Only work with the units in a clean and dry environment! Only specially prepared units (e.g.
actuators) can work under other conditions!
•Please only use original parts from piezosystem jena. piezosystem jena does not give any
warranty for damages or malfunction caused by additional parts not supplied by piezosystem
jena. Additional cables or connectors will change the calibration and other specified data. This
can change the specified properties of the units and cause them to malfunction.
•Piezo elements are sensitive systems capable of the highest positioning accuracy. They will
demonstrate their excellent properties only if they are handled correctly! Please mount them
properly at the special mounting points.
Immediately unplug your unit from the wall outlet and refer servicing to qualified service personnel
under the following conditions:
•when the cords or plugs are damaged
•if liquid has been spilled or objects have fallen into the unit
•if the unit has been exposed to rain or water
•if the unit has been dropped or the housing is damaged

7 CEO: Dr. Bernt Götz • Phone +493641/66880 • Fax +493641/668866 • www.piezosystem.com
6.2 Installation & power supply
RISK OF ELECTRIC SHOCK!
•Do not insert or unplug the power plug with wet hands, as this may result in electrical shock.
•Do not install in rooms where inflammable substances are stored. If flammable substances
come into contact with electrical parts inside, it could result in fire or electrical shock.
•Do not damage or modify the power cord. Also, do not place heavy objects on the power cord,
or pull on or excessively bend it, as this could cause electrical damage and result in a fire or
electrical shock.
•Always grasp the plug portion when unplugging the power cord. Pulling on the power cord
may expose or snap the core wire, or otherwise damage the power cord. If the cord is
damaged, this could cause an electricity leak and result in a fire or electrical shock.
CAUTION!
•Do not use accessories other than the ones provided (e.g. power cord). Only plug the power
cord into grounded power equipment and sockets.
•Do not place heavy objects on any cables (e.g. power cords, sensor cables, actuator cables,
optical cables).
•Do not block ventilated openings or place the units near a radiator, oven, or other heat
sources.
•Plug in the power cord completely so that it cannot loosen inadvertently.
•Leave sufficient space around the power plug so that it can be unplugged easily. If objects are
placed around the power plug, you will be unable to unplug it in an emergency.
•Install the system so that the on/off-switch is easily accessible at all times.
•The power plug is the cut-off point to the main power supply.
6.3 Operation
RISK OF ELECTRIC SHOCK!
•Do not open the units! There are no user serviceable parts inside and opening or removing
covers may expose you to dangerous shock hazards or other risks. Refer all servicing to
qualified service personnel.
•Do not spill inflammable substances inside the voltage amplifier. If these items come into
contact with an electrical component inside the voltage amplifier, this may result in a fire or
electrical shock.
CAUTION!
•If the voltage amplifier emits smoke, high heat, or unusual smells, immediately turn off the
power switch and unplug the power plug from the outlet. Then contact our technical service.

8 CEO: Dr. Bernt Götz • Phone +493641/66880 • Fax +493641/668866 • www.piezosystem.com
6.4 Maintenance and inspection
CAUTION!
•Before cleaning the exterior box of the voltage amplifier, turn off the power switch and unplug
the power plug. Failure to do so may result in a fire or electrical shock.
•Clean the exterior box using a damp cloth that has been firmly wrung-out. Do not use alcohols,
benzene, paint thinner or other inflammable substances. If flammable substances come into
contact with an electrical component inside the voltage amplifier, this may result in a fire or
electrical shock.
6.5 Environmental conditions
The amplifier can be used:
•indoors only
•at an altitude of up to 2000 m
•at a temperature between: 5 ... 35 °C
•at a relative humidity between: 5 ... 95 % (non-condensing)
The recommended environmental conditions:
•indoors only
•at an altitude of up to 2000 m
•at a temperature between: 20 ... 22 °C
•at a relative humidity between: 5 ... 80 % (non-condensing)
7 Instructions for checking the function of the system / quick start
When you open the package, please check to make sure all the necessary parts are included (see
packing list) and nothing is damaged. Check the electronics and the actuator for any visible damage:
•The top and bottom plates of the actuator (if it does not have another shape) should be
parallel to each other and not have any scratches.
•If there is any damage to the system, please contact our local representative immediately!
•If the packaging material is damaged, please confirm this with the shipping company.
•Connect the piezo actuator by using the D-SUB 15pin connector. Be sure the cables are
connected properly to the electronics.
•Connect the device to PC with a USB cable.
•Connect the power supply (24 VDC).
•Normally, the PC installs necessary drivers automatically.
•After initialization, the LED lights green (open loop mode) or orange (closed loop mode).
•In case of irregularities, please read the chapter on troubleshooting.
•The function check is complete.

9 CEO: Dr. Bernt Götz • Phone +493641/66880 • Fax +493641/668866 • www.piezosystem.com
8 How to operate the digitalamplifierNV200/D NET
8.1 Introduction
The digital amplifier NV200/D NET is designed to control the D-actuators from piezosystem jena. It
can be used with actuators with or without integrated position sensor. Actuators with integrated
position sensor allows positioning without creeping or hysteresis by digital PID loop control. The
amplifier can be controlled by USB, Ethernet, SPI or analog voltage input and reaches a resolution of
16 bits. piezosystem jena supports driver for Windows® operating systems.
The integrated digital loop controller comes as PID controller, additionally a slew rate limiter, a low
pass filter of 4th order for set point filtering and a notch filter are available.
The digital amplifier NV200/D NET allows the interchangeability from D-actuators and amplifier. All
needed information is stored on the ID-chip, located in actuator’s connector, and will be read
automatically by the piezo controller after system start.
The actuator is connected to the NV200/D NET using the “PIEZO” plug. After switch on, the device
runs a self-test procedure, while the indicator LED is lightning red. This takes about 3 s. During this
step the controller reads the system specific parameters from the actuators ID-chip and sets up the
controller. If no actuator is connected, the LED stays red.
After the self-test, the actuator moves to its initial position. In case of open loop mode to the desired
voltage, in case of closed loop mode it moves to the set position.
In OL mode, the actuator is directly controlled by a voltage between -20 V and +180 V, however it will
be automatically limited to the admissible voltage range of the connected actuator. The reachable
stroke (pos. 1 to pos. 4) in unloaded condition can be seen on the actuator’s calibration protocol. The
stroke vs. voltage relationship is non-linear, shows hysteresis and creep and is affected by the
actuators load condition. The stroke decreases by higher stiffness loads. To reach a defined position,
actuators with integrated position sensors are used. They will have a smaller stroke in CL mode, the
remaining stroke, compared to OL mode is used as a reserve to reach the end positions (pos. 2 and
pos. 3) also under load.

10 CEO: Dr. Bernt Götz • Phone +493641/66880 • Fax +493641/668866 • www.piezosystem.com
8.2 Technical data
Input voltage
24VDC
Power supply connector
low voltage socket with 2.1 mm pin
Input current
max. 2A (rms) / 7A (peak) @ 24V, idle current 110 mA
Power consumption
max. 48W
Output voltages
-10 V... +180V or -20V … +130 V
(automaticallyadapted to the actuator)
Output current
200mA (continuous)
400mA (peak for 1.2ms)
NanoX®-mode:
2 x 100 mA (continuous)
2 x 200 mA (peak for 1.2ms)
Output voltage noise
0.7mVRMS @ 500 Hz bandwidth
Actuator/measurement
connector “PIEZO”:
15 pin D-Sub plug
Safety functions:
short circuit proof, over temperature protection
Display (LED):
green / orange / red
Interfaces
USB, Ethernet
Interface connectors
USB-C, RJ45
Cooling
passive
Dimensions (L * W * H):
165 x 120 x 65 mm³
Weight:
0.5kg

11 CEO: Dr. Bernt Götz • Phone +493641/66880 • Fax +493641/668866 • www.piezosystem.com
8.3 Connectors and Pin Assignment
8.3.1 Overview
I/O
connector
Ethernet
connector
USB
connector
Piezo actuator
connector
connector
Status
LED
Power supply
connector

12 CEO: Dr. Bernt Götz • Phone +493641/66880 • Fax +493641/668866 • www.piezosystem.com
8.3.2 Piezo actuator connector
Type: 15 pin D-SUB plug
Pin
Label
Description
1, 2, 11
AGND
Analog ground
3
+15V*
Operating voltage measurement +15V
4, 14
GND
Digital ground
5
SDA
I²C-Bus SDA
6
3.3Veeprom*
Supply voltage ID-Chip
7
Vout2
Second voltage for NanoX® actuator +180 V … -20V
8
Vout
Actuator voltage -20 V... +180V
9
+MEAS
Position signal -8 V... +8V
10
-15V*
Supply voltage measurement -15V
12
SCL
I²C-Bus SCL
13
DETECT
Actuator detection
15
Piezo ground
Actuator ground
[*] Not for external use
The actuator is connected to this plug. The actuator voltage goes to the piezo, the position signal from
the measurement system goes to the DSP, and the integrated actuator information is stored on an ID-
chip which goes to the main controller. It is important that the locking screws are screwed into the
front panel. The dangerous voltages will be switched on only after connecting the actuator. When
disconnecting the actuator, the dangerous voltages will be switched off by a safety relay.

13 CEO: Dr. Bernt Götz • Phone +493641/66880 • Fax +493641/668866 • www.piezosystem.com
8.3.3 I/O connector
Type: 15 pin D-Sub HD jack
Pin
Label
Description
1
MOD
Analog modulation input (0...10V), (Impedance 1 MΩ)
2
MON2
Not used
3
TRG in
Trigger input (TTL, 0 / 3,3V…5V)
4
SPI: CLK
SPI clock (3,3V logic, slave input)
5
DGND
Digital ground (for SPI & Trigger)
6
AGND
Analog ground (for MOD & MON)
7
DGND
Digital ground (for SPI & Trigger)
8
DGND
Digital ground (for SPI & Trigger)
9
SPI: MOSI
MOSI (3,3V logic, slave input)
10
TxD
Not used
11
MON
Analog monitor output (0 ...10V)
12
TRG out
Trigger output (TTL 3,3V)
13
SPI: /CS
Chip select (3,3V logic, low active, slave input)
14
SPI: MISO
MISO (3,3V logic, slave output)
15
RxD
Not used
shield wire
AGND
Analog ground
8.3.4 USB connector
The USB-C type connector supports USB 2.0 and allows the device to be controlled via a serial COM-
Port.
8.3.5 Ethernet connector
The RJ45 Ethernet connector allows the device to be controlled via a Telnet connection.
8.3.6 Power supply connector
The power supply connector is a low voltage socket with a 2.1 mm pin. The supply voltage is 24 V.

14 CEO: Dr. Bernt Götz • Phone +493641/66880 • Fax +493641/668866 • www.piezosystem.com
8.4 Establishing communication
8.4.1 Serial communication via USB
The NV200/D NET can easily communicate with your PC with the use of a terminal program such as
HTerm. A USB connection cable (included) is required to connect to your computer. The properties of
the COM port are: 115200 baud, 8bit, no parity, 1 stop bit, software handshake (XON / XOFF).
When the device is powered and connected, it answers after receiving “CR - carriage return” (Enter
Key) with its prompt “NV200/D NET>”
8.4.2 Telnet communication via Ethernet
The communication with the NV200/D NET over Ethernet can be done with the Windows Telnet
client. If not already enabled, this can be done via the “Turn Windows features on or off” functionality.

15 CEO: Dr. Bernt Götz • Phone +493641/66880 • Fax +493641/668866 • www.piezosystem.com
Alternatively, you can use other programs like Putty. After successful connection the full command set
is available.
The Telnet connection can be established via the IP address of the controller and the correct port
number. The default port number is 23.
By default, the IP address is set dynamically over DHCP. If necessary, it can be set static over the
configuration. To get the IP address of the device ask you network administrator or use our tool “IP-
Search”from the website.
It is possible to use the host name of the device, if the “DHCP FQDN option” is enabled. By default,
the host name is “C” + the last 6 digits of the MAC address. (Example: MAC=00:80:A3:E5:74:74 →
host name: “CE57474”). The MAC address can be found on the type plate of the device.

16 CEO: Dr. Bernt Götz • Phone +493641/66880 • Fax +493641/668866 • www.piezosystem.com
8.4.3 Ethernet configuration
The network settings can be changed via Telnet connection (port: 9999) or via a web browser.
It is possible to change the IP address and the default port (23) for Telnet communication with the
device. Under the item “Server” the IP address can be set to a static one or to DHCP. Under item
“Channel 1” the port can be changed.
By accessing the IP in a web browser, the settings can be accessed graphically.
CAUTION: By default, the IP address is retrieved over DHCP. In networks without a DHCP server
there is no access via Telnet possible without setting a static IP address.

17 CEO: Dr. Bernt Götz • Phone +493641/66880 • Fax +493641/668866 • www.piezosystem.com
8.4.4 SPI communication
Real-time communication can take place via the SPI interface. The device works as an SPI slave, i.e.
the device receives setpoints from an external SPI master. The return value retrieved over the MISO
channel can be set to different quantities (e.g. position values) via the USB or Ethernet interfaces.
The SPI connection is exclusively to send setpoints to the device. The device has to be configured via
the USB or Ethernet interfaces.
The interface requires the following configuration:
•3.3 V logic voltage
•SPI clock: max. 6 MHz
•SPI mode: 3 (CPOL = 1, CPHA = 1)
•SPI CS: low active
•Word length: 16 bit, MSB First
Value range of the SPI-setpoint:
•in closed loop mode [0x0000 … 0xFFFE] corresponds to 0 … 100% of the closed loop travel
of the connected actuator
•in open loop mode [0x0000 … 0xFFFE] corresponds to 0 … 100% of the admissible piezo
voltage of the connected actuator
•The value [0xFFFF] is used for error detection and is not interpreted as a setpoint
Value range of the return value:
•The value selected by spisrc command is converted into a 16 bit integer value with the
following scaling:
Configuration
Value
Scaling
spisrc,0
none
0x0000
spisrc,1
Measured position in closed loop
posmin 0x0000
posmax 0xFFFF
spisrc,2
Setpoint in open loop
avmin 0x0000
avmax 0xFFFF
spisrc,3
Piezo voltage (controller output)
avmin 0x2000
avmax 0xDFFF
spisrc,4
Position error
-posmax 0x2000
0 0x8000
+posmax 0xE000
spisrc,5
abs(Position error)
0 0x0000
2*posmax 0xFFFF
spisrc,6
Measured position in open loop
posmin 0x2000
posmax 0xDFFF
spisrc,7
Piezo current 1
-0.5A 0x0000
0 A 0x8000
+0.5A 0xFFFF
spisrc,8
Piezo current 2
-0.5A 0x0000
0 A 0x8000
+0.5A 0xFFFF
spisrc,9
Test value
0x5A5A

18 CEO: Dr. Bernt Götz • Phone +493641/66880 • Fax +493641/668866 • www.piezosystem.com
To synchronize the NV200/D NET PID controller loop execution to the SPI master the spitrg option
can be used. In mode spitrg,0 the internal 20 kHz clock is used to trigger the digital control loop
interrupt. In mode spitrg,1 the digital control loop interrupt is executed only when a new SPI
setpoint is received. This allows precise synchronization of several NV200/D NET controllers.
However, it is very important to make sure that SPI commands are sent with a 20 kHz update rate in
order to get the right timing for the digital filters, since they are parameterized with respect to a
constant sampling rate of 20 kHz.
8.5 Command list
All commands with one parameter to send are used in the following scheme:
<command>,<value>\r
Commands with indexing are used like this:
<command>,<index>,<value>\r
In case of read-only commands, commands without a value or to read back a value, the command is
issued without a value:
<command>\r
Command
Description
Value range
General Commands
s
Print full command list
-
reset
Hardware-reset of the controller
-
fenable
During controller power-up,cycle through the
entire piezo voltage range once
0= disabled
1= enabled
sinit
Initial actuator position after power-up
0 …100 %
set
Setpoint as position or voltage
In open loop: voltage in V
In closed loop: position in µm or µrad
Range is limited by the actuators
stroke and voltage range
meas
For actuators with sensor: Position in actuator
units (µm or mrad)
For actuators without sensor: Piezo voltage in V
-
imeas
Measured piezo current
0 = piezo current 1
1 = piezo current 2
ctrlmode
Controller operation mode
0 = PID control
1 = ILC (identification mode)
2 = ILC (feedforward controlmode)
3 = ILC (feedback control mode)
temp
Heat sink temperature
-
stat
Status register, see section 8.6 for details
-
posmin
Lower motion range limit
-
posmax
Upper motion range limit
-
avmin
Lower voltage range limit
-
avmax
Upper voltage range limit
-

19 CEO: Dr. Bernt Götz • Phone +493641/66880 • Fax +493641/668866 • www.piezosystem.com
modsrc
Signal source for setpoint
0 = set-Command via USB or
Ethernet
1 = Analog In
2 = SPI
3 = Arbitrary waveformgenerator
monsrc
Source of data for analog output
0 = position (closed loop)
1 = setpoint
2 = piezo voltage (controller output)
3 = position error
4 = abs(position error)
5 = position (open loop)
6 = piezo current 1
7 = piezo current 2
PID and filters
cl
PID open loop or closed loop mode
0 = open loop
1 = closed loop
sr
Slew rate limit
0.0000008 ... 2000.0
(2000 =
disabled)
kp
PID controller proportionaltermamplification
0 ... 10000 (0 = disabled)
ki
PID controller integraltermamplification
0 ... 10000 (0 = disabled)
kd
PID controller differential termamplification
0 ... 10000 (0 = disabled)
tf
PID controller differential term
pcf
PID controllers feed forward control amplification
0.0 … 1.0 (0 = disabled)
setlpon
Enable or disable setpoint lowpass filter
0 = off
1 = on
setlpf
Setpoint low pass filter cut-off frequency
1 ... 10000 Hz
notchon
Enable or disable notch filter
0 = off
1 = on
notchf
Notch filter frequency
1 … 10000 Hz
notchb
Notch filter -3dBbandwidth
1 … 10000 Hz (max. 2 * notchf)
poslpon
Enable or disable measured position lowpass
filter
0 = off
1 = on
poslpf
Measured position low pass filter cut-off
frequency
1 …10000 Hz
Arbitrary waveformgenerator
grun
Start or stop the arbitrary waveformgenerator
0 = stop
1 = start
gsarb
Start index for arbitrary waveformgenerator
output
0…1023
gearb
End index for arbitrary waveformgenerator
output
0…1023
gcarb
Number of cycles to run
0 = infinitely
1…65535
goarb
Offset index when arbitrary waveformgenerator
gets started
0…1023
giarb
Read current waveformgenerator index (e.g.
after a stop command)
-
gtarb
Output sampling factor (<value> * 50µs)
1…65535
gbarb
Output values in the buffer in relative units
index: 0…1023
value: 0.0…100.0 (%)
gparb
Output values in the buffer in length units (µmor
mrad)
index: 0…1023
value: posmin … posmax
gsave
Save the bufferin the EEPROM (End of process
is acknowledged by CR LF)
-
gload
Loading the buffer fromthe EEPROM (End of
process is acknowledged by CR LF)
-
Data recorder

20 CEO: Dr. Bernt Götz • Phone +493641/66880 • Fax +493641/668866 • www.piezosystem.com
recsrc
Source of data to be stored in data recorder
channel
recsrc,<ch>,<src>
ch:
0 = buffer A
1 = buffer B
src:
0 = piezo position in µm or mrad
1 = setpoint in µm or mrad
2 = piezo voltage in V (controller
output, not amplifier output)
3 = position error
4 = abs(position error)
5 = piezo position in µm or mrad
6 = piezo current 1 in A
7 = piezo current 2 in A
recast
Autostart mode of the data recorder
0 = off
1 = start on set-command
2 = start on grun-command
recstr
Data recorder stride (store only every nth value)
1….65535
reclen
Memory length for each of the two data recorder
channels
0 …. 6144
0 = infinite loop over maximum length
until recorder is stopped manually
recrun
Start or stop the data recorder
0 = stop
1 = start
recidx
Read current data recorder write index (e.g. after
a stop command)
-
recout
Read the data recorder line by line:
• ch: channel
• Index: Distance to index 0
• Length: number of values (max. to reclen or
rec_max)
Response:
recout, <ch>, <index>,<value>
ch:
0 = channelA
1 = channelB
Index:
0… 6143
Length:
1… 6144
recoutf
Read the complete data recorder comma-
seperated:
Response:
recoutf, <ch>, <value 1>,<value 2>,….,<value
reclen>
ch:
0 = channelA
1 = channelB
Trigger In
trgfkt
Function to run on trigger input
0 = none
1 = waveformgenerator start
2 = waveformgenerator step
3 = waveformgenerator sync
4 = ILC sync
5 = start data recorder
Trigger Out
trgedg
Trigger on falling and/or rising edge
0 = off
1 = falling, not inverted
2 = rising, not inverted
3 = both, not inverted
trgsrc
Signal source for trigger out
0 = position
1 = setpoint
trgss
Trigger output start (lower position)
(posmin+0.001)...(posmax-0.001)
trgse
Trigger output stop (upper position)
(posmin+0.001)...(posmax-0.001)
trgsi
Trigger output step size
0.001…(posmax-0.001)
trglen
Trigger length in samples t=50µs*trglen
(trglen=0→t=1µs)
0…255
SPI
spisrc
SPI monitor/ Return value via MISO
0 = 0x0000
Table of contents
Other piezosystemjena Amplifier manuals
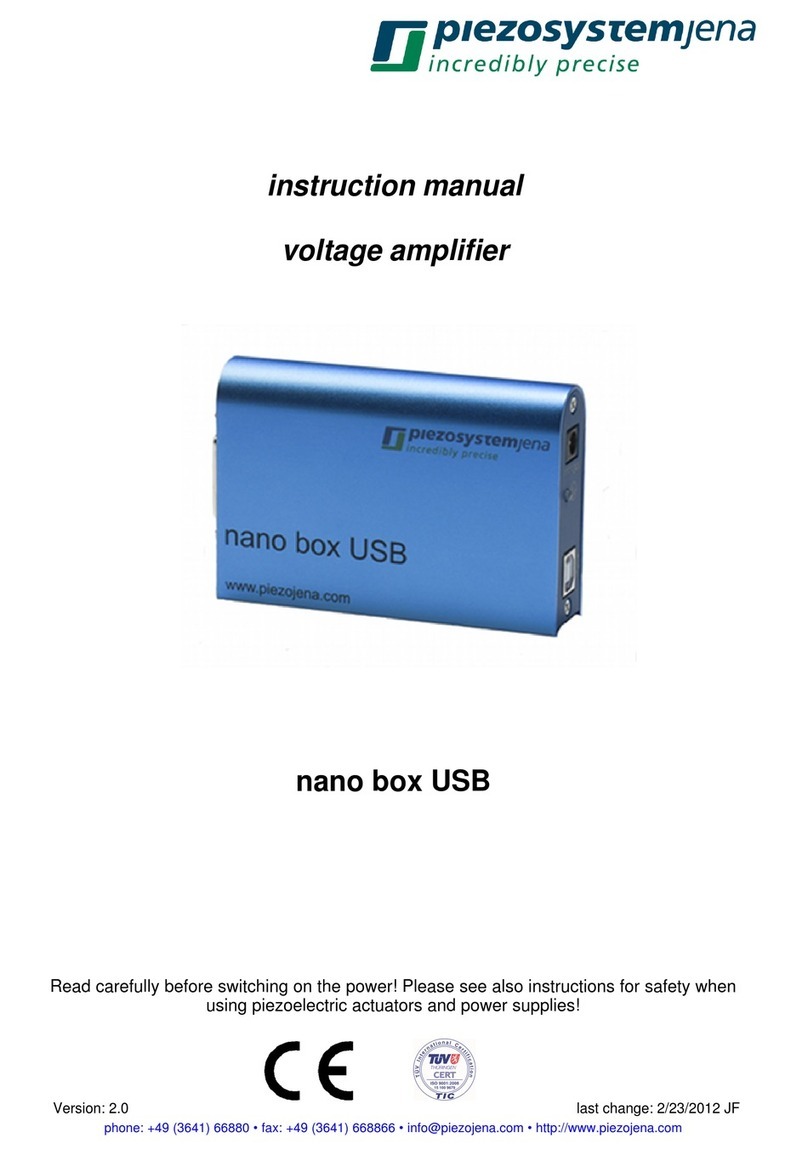
piezosystemjena
piezosystemjena nano box USB User manual
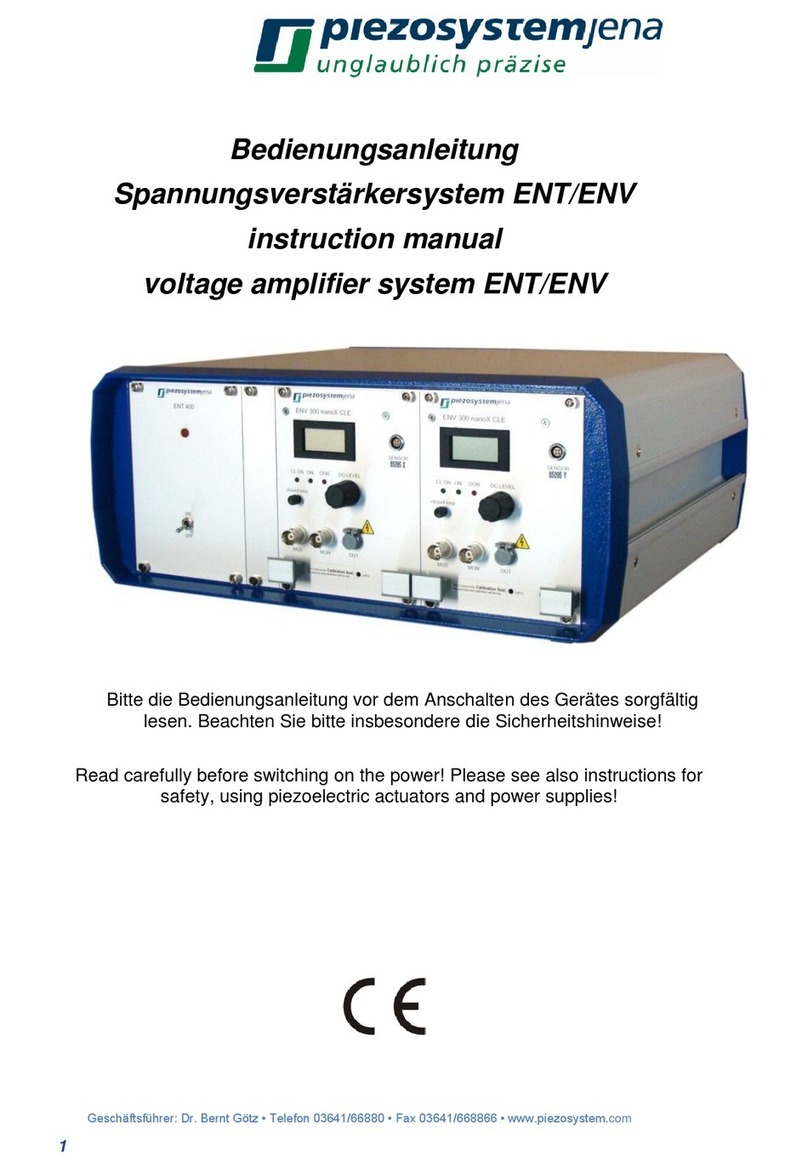
piezosystemjena
piezosystemjena ENT User manual

piezosystemjena
piezosystemjena NV40/3 User manual
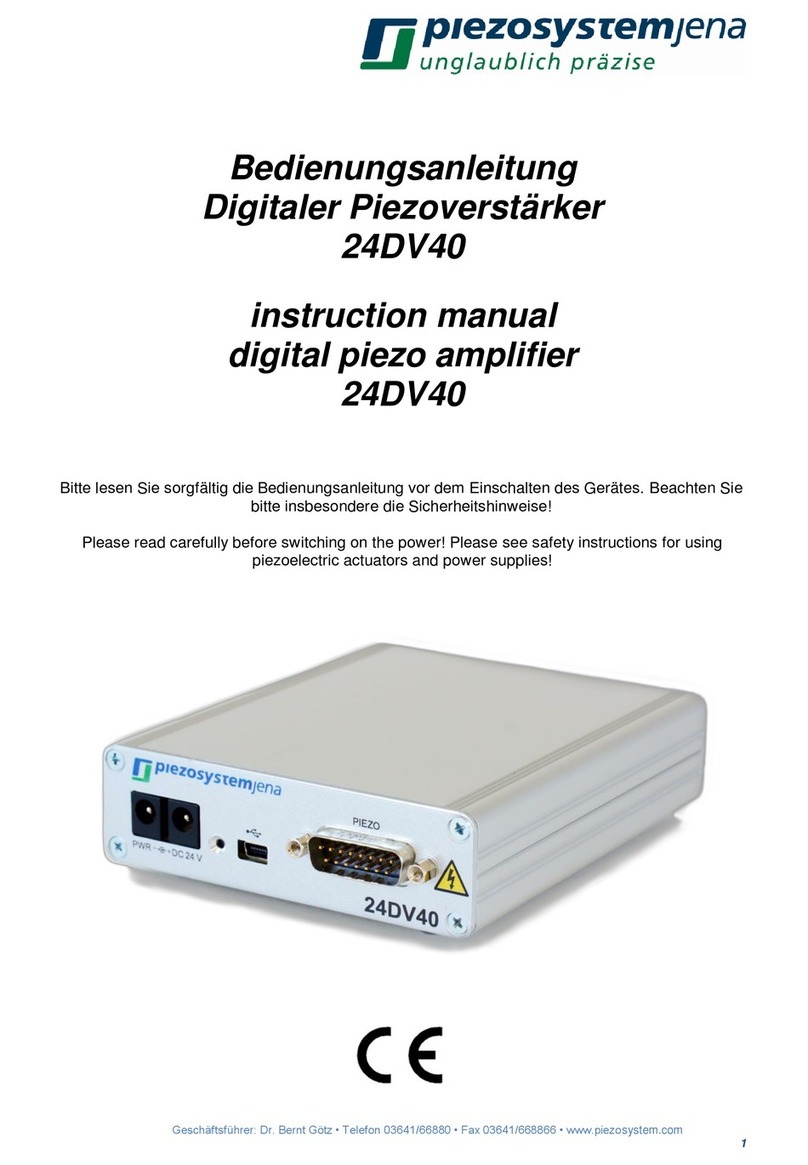
piezosystemjena
piezosystemjena 24DV40 User manual
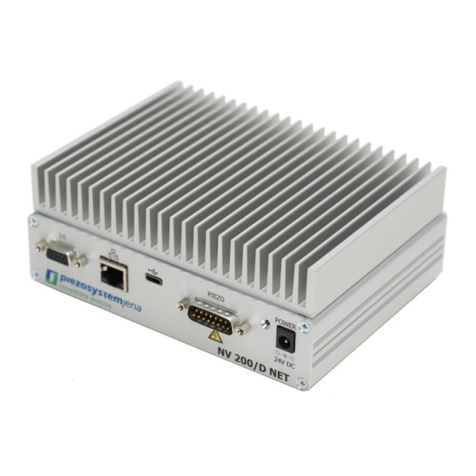
piezosystemjena
piezosystemjena NV200/D NET User manual
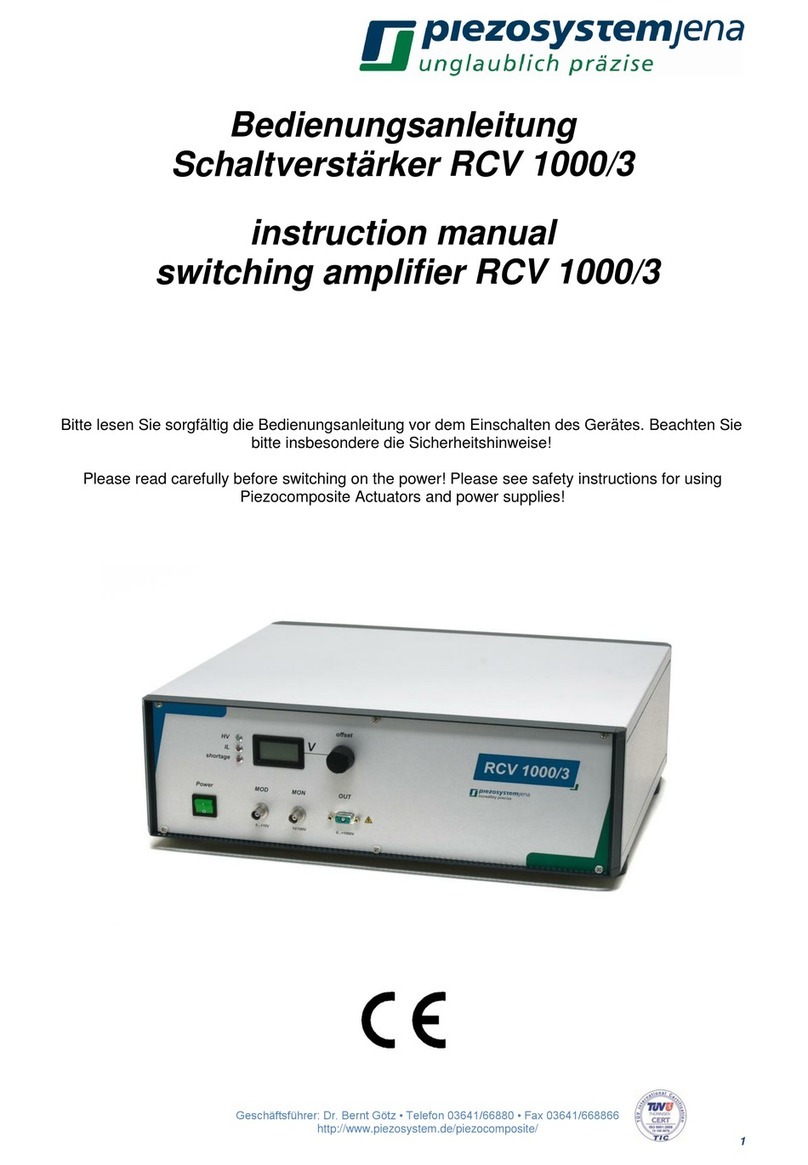
piezosystemjena
piezosystemjena RCV 1000/3 User manual
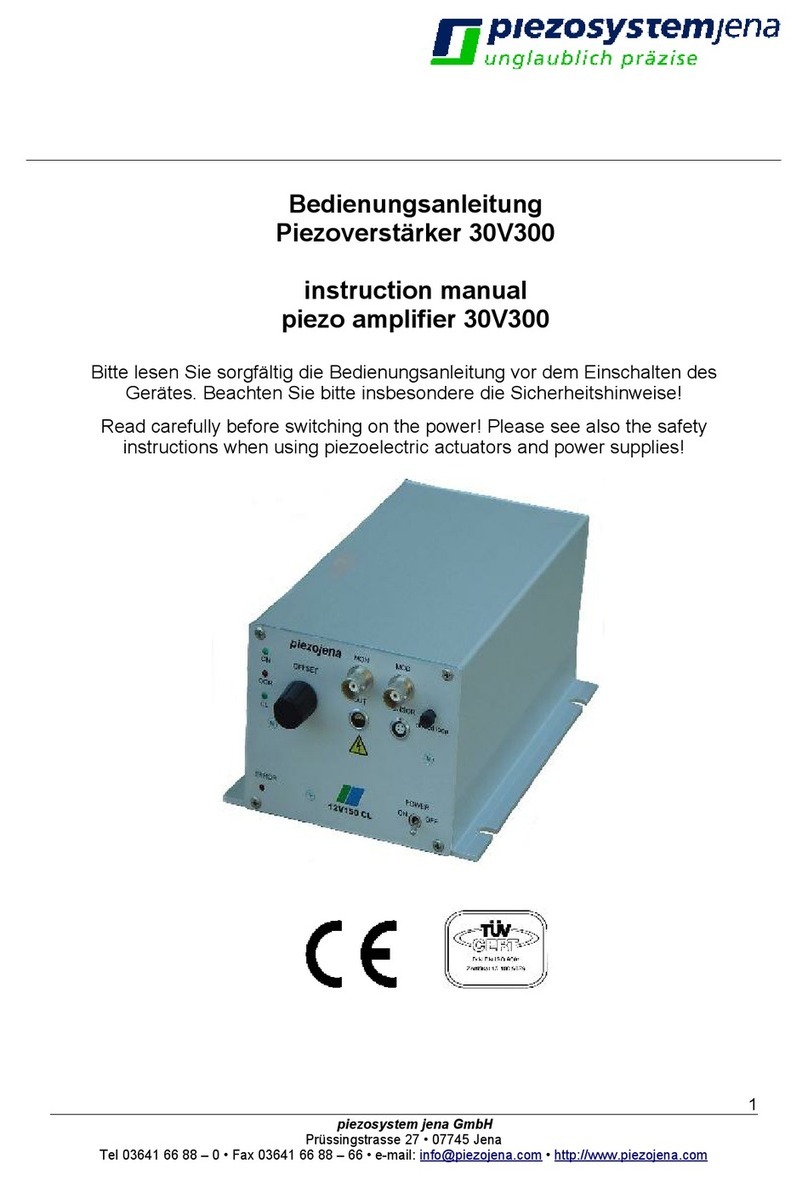
piezosystemjena
piezosystemjena 30V300 User manual
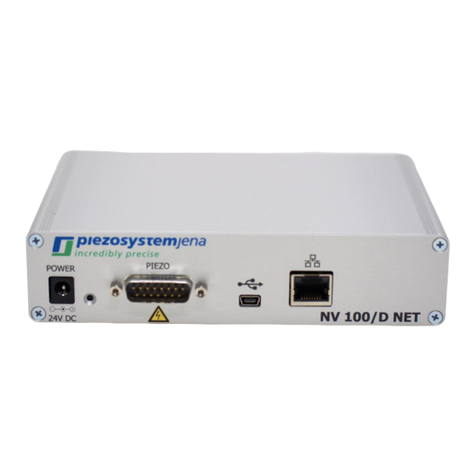
piezosystemjena
piezosystemjena NV100/D NET User manual
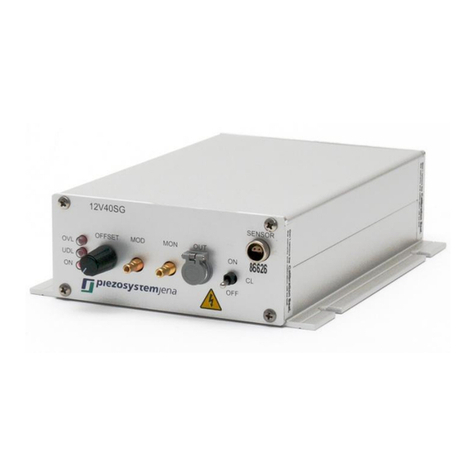
piezosystemjena
piezosystemjena 12V40 Series User manual
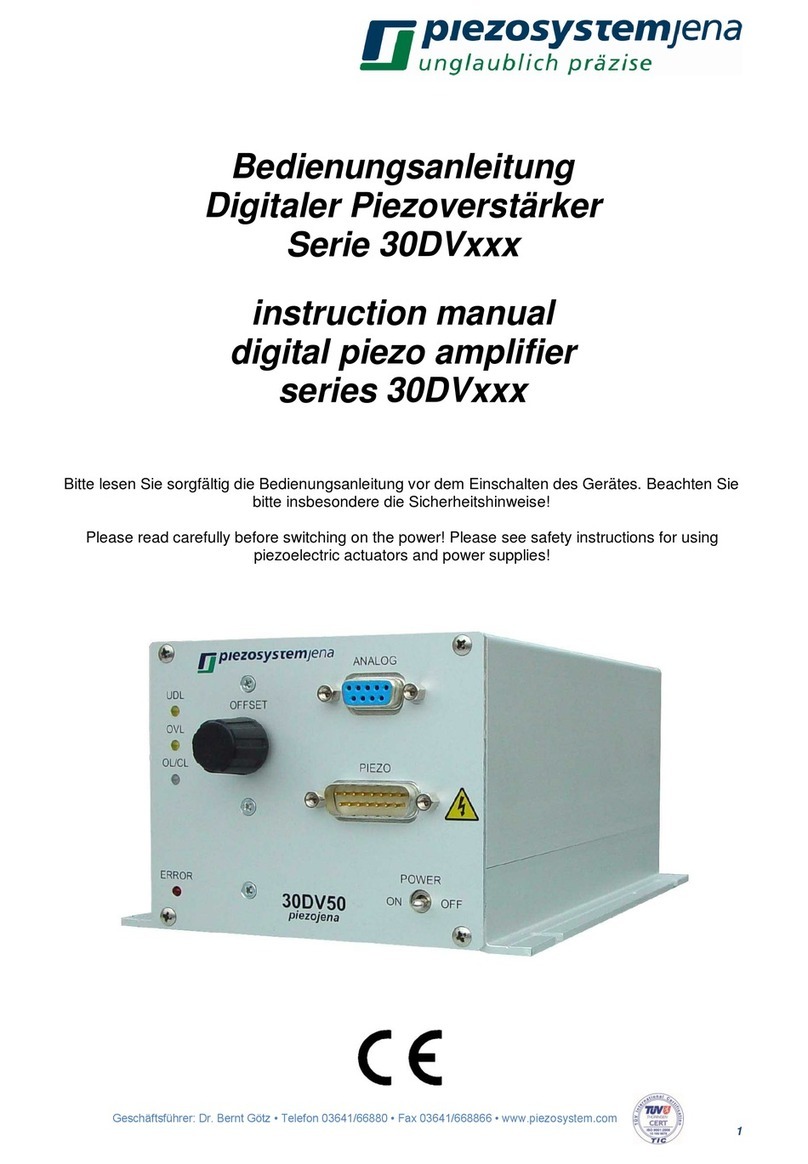
piezosystemjena
piezosystemjena series 30DV User manual