Pilz PSSuniversal User manual

Planning Guide
Technical Catalogue
PSSuniversal
Issue 01/05
DRAFT

PSSuniversal
Status 01/05 1
Pilz GmbH & Co. KG, Sichere Automation, Felix-Wankel-Straße , 73760 Ostfildern, Germany
Telephone +49 711 3409-0, Telefax +49 711 3409-133, E-Mail: [email protected]
Contents Page
PSSuniversal system
Basics
System description
Modular structure 1.1-1
Module bus 1.1-2
Structure of module bus 1.1-2
Maximum system expansion 1.1-3
System limits 1.1-3
Local enable principle 1.1-4
Connection labelling on the base modules 1.1-5
Colour marking of connection levels 1.1-5
Separating supplies to form supply groups 1.1-6
Installation
Mounting position 1.2-1
Mounting rail 1.2-1
Module layout 1.2-1
Mounting distances 1.2-2
Installing the head module 1.2-3
Removing the head module 1.2-4
Installing base modules 1.2-5
Removing base modules 1.2-6
Installing an end bracket at the start of the system 1.2-7
Removing an end bracket at the start of the system 1.2-7
Installing a terminating plate and end bracket at the end of the system 1.2-8
Removing a terminating plate and end bracket at the end of the system 1.2-9
Inserting an electronic module 1.2-10
Mechanical coding 1.2-11
Removing an electronic module 1.2-12
Earthing 1.2-13

PSSuniversal
Status 01/05
2
Pilz GmbH & Co. KG, Sichere Automation, Felix-Wankel-Straße , 73760 Ostfildern, Germany
Telephone +49 711 3409-0, Telefax +49 711 3409-133, E-Mail: [email protected]
Modules
Head modules
PSSu H SB 2.1-1
PSSu H SB DP 2.1-9
Supply voltage modules
PSSu E F PS 2.2-1
PSSu E F PS1 2.2-11
PSSu E F PS-P 2.2-21
PSSu E F BSW 2.2-31
Digital input/output (standard)
PSSu E S 4DI 2.3-1
PSSu E S 4DO 0.5 2.3-9
PSSu E S 2DO 2 2.3-17
Digital input/output (failsafe)
PSSu E F 4DI 2.4-1
PSSu E F 4DO 0.5 2.4-11
PSSu E F 2DO 2 2.4-21
PSSu E F 2DOR 8 2.4-31
PSSu E F 4DI OZ 2 2.4-43
Voltage distribution
PSSu E PD 2.5-1
Order reference
Module overview
Electronic modules with base modules (screw terminals) 3.1-1
Electronic modules with base modules (cage clamp terminals) 3.1-2

2
PSSuniversal
Basics
System description
Status 01/05 1.1-1
Pilz GmbH & Co. KG, Sichere Automation, Felix-Wankel-Straße , 73760 Ostfildern, Germany
Telephone +49 711 3409-0, Telefax +49 711 3409-133, E-Mail: [email protected]
Modular structure
The PSS universal (PSSu) from Pilz is
a modular system for use in the
decentralised periphery of plant and
machinery. A modular PSSu type
system consists of:
`One head module
`At least one supply voltage
module
`Input/output modules for standard
and failsafe applications, which
may be installed in any sequence
`End bracket at the start of the
system to secure the system on
the mounting rail
`Terminating plate with integratable
end bracket at the end of the
system to secure the system on
the mounting rail
Head module
`Connects the sensor/actuator
level for standard applications to
master controllers via various
standard bus systems (e.g.
PROFIBUS)
`Connects the sensor/actuator
level for failsafe applications to
SafetyBUS p
`Co-ordinates the entire process
data traffic for standard and
failsafe applications
`Permits a failsafe output to be
switched via a standard signal,
depending on an enable from a
failsafe signal (local enable
principle)
Supply voltage modules
`Available for various functions
`Consist of an electronic module
and a base module
Input/output modules
`Available for a wide range of
input/output functions
`Consist of an electronic module
and a base module
Base modules
`Carrier units for the supply voltage
and input/output modules
`Used to connect the field wiring
`Available with the following
connection types:
- Cage clamp terminals or
- Screw terminals
Electronic modules
`Are plugged into base modules
`Can be inserted/removed
independently from the base
module
`Determine the function of the
supply voltage or input/output
module
`Communicate with the head
module via the module bus
Terminating plate
Head module
Mounting rail
(DIN EN50022)
End bracket
Electronic module
(grid width 2 x 12.6 mm)
Electronic module
(grid width 1 x 12.6 mm)
End bracket
(integrated into terminating plate)
Supply voltage module
(electronic module + base module)
Base module
(grid width 2 x 12.6 mm)
Base module
(grid width 1 x 12.6 mm)

PSSuniversal
Basics
System description
Status 01/05
1.1-2
Pilz GmbH & Co. KG, Sichere Automation, Felix-Wankel-Straße , 73760 Ostfildern, Germany
Telephone +49 711 3409-0, Telefax +49 711 3409-133, E-Mail: [email protected]
Module bus
The module bus is formed by
arranging the base modules together
and connecting them via a
mechanical latch.
`Data
2 independent bus systems are
available for FS data and ST data.
The data is processed in the head
module.
`Module supply
Supply for the head module and
the electronic modules. Various
supply voltage modules are
available for different functions
(e.g. voltage refresh, separating
the supply).
`Periphery supply
The supply for the actuators (load)
or input test pulses is provided at
the base module contacts,
depending on the function of the
electronic module. Various supply
voltage modules are available for
different functions.
The connection on the module
bus can be disconnected in order
to form supply groups. In this
case it is necessary to use an
appropriate supply module, which
disconnects the supply (module
supply, periphery supply and C-
rail supply) to the preceding (left-
hand) modules and provides a
new supply to subsequent (right-
hand) modules.
`C-rail
The C-rail is routed through all the
base modules via the module bus.
The C-rail is an additional power
rail, which is attached to the base
module connections. It is intended
as an option, providing additional
power if required.
Access to the C-rail is available
through the use of base modules
which contain the letter “C” in
their description (e.g. PSSu BP-CC
CC
C
1/8 S). The base module
connections on which the C-rail is
available are marked with a black
bar across the whole connection
level. I/O modules normally route
the C-rail connections on
connection level 3.
If the supply is separated on base
modules containing supply
modules, this is symbolised by the
fact that only the right-hand
connection on the connection
level is marked with a black bar.
This is normally connection 24.
Permitted infeed at C-rail:
- PE or
- 0 V or
- Screen or
- - 24 VDC ... + 24 VDC,
max. 10 A
Make sure that the C-rail supply
belongs to the same circuit as the
other base module connections.
Structure of module bus
Base module Base module
Module bus
Communication rail
(FS + ST data)
Rail for periphery supply
Rail for module supply
C-rail (cross connection)

2
PSSuniversal
Basics
System description
Status 01/05 1.1-3
Pilz GmbH & Co. KG, Sichere Automation, Felix-Wankel-Straße , 73760 Ostfildern, Germany
Telephone +49 711 3409-0, Telefax +49 711 3409-133, E-Mail: [email protected]
Maximum system expansion
System limits
Number of modules per system Explanation
Module type
Details are valid for designing a PSSu
system with any combination of ST
modules and FS modules, provided all
the following conditions are met.
Details are valid for designing a PSSu
system with ST modules only.
Restrictions may apply, depending on
the standard bus system that is used.
Details are valid for designing a PSSu
system with FS modules only.
Details are valid for designing a PSSu
system with dual-pole FS output
modules only
(e.g. PSSu E F DI OZ 2).
Max. 64
Max. 64
Max. 32
Max. 16
Input/output modules in total
(identifier: PSSu E F ... / PSSu E S ...)
Input/output modules for
ST applications
(identifier: PSSu E S ...)
Input/output modules for
FS applications
(identifier: PSSu E F ...)
Output modules with
dual-pole outputs for
FS applications
(identifier: PSSu E F ... OZ...)
Max. current load ExplanationSystem supply
The load is determined by the current
consumption of the head module and
electronic modules that are used. If a
heavier load arises, an additional supply
module must be used to refresh the
module supply. Further details can be
found in the description of the relevant
supply module.
The module bus rail for periphery supply
can take a max. 10 A load. If a heavier
load arises, an additional supply module
must be used to refresh the periphery
supply. The load is determined by the
current consumption of the sensors/
actuators on the electronic modules that
are used. Further details can be found in
the description of the relevant supply
module.
The C-rail can take a max. 10 A load. If a
heavier load arises, an additional supply
module must be used. Further details
can be found in the description of the
relevant supply module.
Max. 1.5 A
Max. 2 A
Max. 10 A
Max. 10 A
Module supply
when supplied via
- PSSu E F PS
Module supply
when supplied via
- PSSu E F PS1
Periphery supply
when supplied via
- PSSu E F PS
- PSSu E F PS1
- PSSu E F PS-P
C-rail

PSSuniversal
Basics
System description
Status 01/05
1.1-4
Pilz GmbH & Co. KG, Sichere Automation, Felix-Wankel-Straße , 73760 Ostfildern, Germany
Telephone +49 711 3409-0, Telefax +49 711 3409-133, E-Mail: [email protected]
Local enable principle
The new local enable principle
technique means that outputs on
failsafe output modules can now be
switched via a standard bus system
(e.g. PROFIBUS).
Configuration of the local enable
principle
`Via the PSS WIN-PRO system
software
`By configuring FS output modules
for the relevant standard bus
system (e.g. in the case of
Profibus, included in the GSD file)
`By assigning an FS output to a bit
in the ST process image of
outputs (ST-PIO). The FS output
will therefore operate as an enable
output.
`Ability to read the FS inputs via
the standard bus system.
Operation of the local enable
principle
`The configured FS outputs are
driven via a standard bus system.
`Provided the enable output carries
a “1” signal, the configured FS
outputs can be driven via a
standard bus system.
As soon as the enable output
carries a “0” signal, the configured
FS outputs are shut down safely.
Control via the standard bus
system is ignored.
Control via
standard bus system
Head Module
Input Module (ST)
Input Module (FS)
Power Supply
Output Module (ST)
Output Module (FS)
Control via
SafetyBUS p
Module Bus
&
ST Data
FS Data
Function model of the local enable
principle

2
PSSuniversal
Basics
System description
Status 01/05 1.1-5
Pilz GmbH & Co. KG, Sichere Automation, Felix-Wankel-Straße , 73760 Ostfildern, Germany
Telephone +49 711 3409-0, Telefax +49 711 3409-133, E-Mail: [email protected]
Connection labelling on the base
modules
The connections on the base
modules are indicated via two-digit
numbers. The first digit denotes the
column on the module. The second
digit denotes the connection level
within the PSSu system.
Colour marking of connection levels
The colour marking on the different
connection levels is helpful when it
comes to wiring. Various colour
markers are available to label the
connection levels. For the connection
diagram to remain consistent it
makes sense to arrange I/O modules
of the same type into groups (see
example).
The connection levels are typically
assigned as follows:
`Connection level 1 and 4
On I/O modules, connection levels
1 and 4 typically contain the
module’s inputs or outputs.
Marking in the example:
- Black [3]
`Connection levels 2 and 3
On I/O modules, connection levels
2 and 3 typically contain the
common supplies (+24 VDC, test
pulse outputs, 0 VDC).
Marking in the example:
- Red [1]: +24 VDC/test pulses
- Blue [2]: 0 VDC
Example:
Colour marking of connection levels
111
1
313
414
111
1
313
414
Head Module
111
1
313
414
111
1
313
414
111
1
313
414
111
1
313
414
111
1
313
414
111
1
313
414
111
1
313
414
PSSu E F 4DI
PSSu E F 4DI
Power Supply
PSSu E S 4DI
PSSu E F 4DI
PSSu E F DO
PSSu E F DO
PSSu E F 4DO 0.5
PSSu E S DO
111
1
313
414
PSSu E S 4DO 0.5
111
1
313
414
PSSu E S 4DI
Input Modules Output Modules
Connection Level 1
Connection Level
Connection Level 3
Connection Level 4
[1] : + 4 VDC
[ ] : 0 VDC
[3] : Inputs/outputs
[3]
[1] [ ]
[ ][1]
[3]

PSSuniversal
Basics
System description
Status 01/05
1.1-6
Pilz GmbH & Co. KG, Sichere Automation, Felix-Wankel-Straße , 73760 Ostfildern, Germany
Telephone +49 711 3409-0, Telefax +49 711 3409-133, E-Mail: [email protected]
Separating supplies to form supply
groups
Supply groups are formed by
separating the 24 V supply (periphery
supply) and, if necessary, also the
5 V supply (module supply). In this
case it is necessary to use a supply
module that disconnects the supply
(periphery supply, C-rail supply and,
if necessary, the module supply) to
the preceding (left-hand) modules
and provides a new supply to
subsequent (right-hand) modules.
Provided an appropriate base
module is used, in principle any
electronic supply voltage module is
suitable for separating supplies.
In each case you should take note of
the description of the relevant
electronic supply voltage module.
For example, supplies can be
separated on the following modules:
Principle:
Formation of supply groups for
periphery supply
Modules
Electronic module
PSSu E F PS
(no module
buffer)
PSSu E F PS1
(module buffer
for max.
20 modules)
PSSu E F PS-P
PSSu E F BSW
(block switching)
Base module
PSSu BS-R 1/8 S
PSSu BS-R 1/8 C
PSSu BS-R 2/8 S
PSSu BS-R 2/8 C
PSSu BS 1/8 S
PSSu BS 1/8 C
PSSu BS 2/8 S
PSSu BS 2/8 C
Separation of supply
C-rail Periphery
supply
Separation of supply from left-hand
modules and
supply infeed to right-hand modules
Separation of supply from
left-hand modules and
supply infeed to right-hand
modules
No separation
of supply
(5 V potential
looped
through)
Module
supply
Head Module
I/O Module
I/O Module
Power Supply
I/O Module
Power Supply
Power Supply
I/O Module
I/O Module
I/O Module
Power Supply
I/O Module
I/O Module
Periphery Supply 1
( 4 V DC)
C-rail
Supply
Periphery Supply
( 4 V DC)
C-rail
Supply
Periphery Supply 3
( 4 V DC)
C-rail
Supply
Supply Group 1 Supply Group Supply Group 3
4 V DC 4 V DC 4 V DC

2
PSSuniversal
Basics
Installation
Status 01/05 1.2-1
Pilz GmbH & Co. KG, Sichere Automation, Felix-Wankel-Straße , 73760 Ostfildern, Germany
Telephone +49 711 3409-0, Telefax +49 711 3409-133, E-Mail: [email protected]
Mounting position
`A PSSu system should preferably
be installed horizontally on a
vertical wall.
`If other mounting positions are
used (e.g. vertical installation),
there will be certain restrictions
with regard to
- Ambient temperature
Optimum upward heat
dissipation can no longer be
guaranteed.
- Vibration and shock stress
There will be increased
requirements on the system
fastenings: use additional
metallic end brackets!
Mounting rail
`A PSSu system is designed to be
installed on a zinc plated DIN rail
in accordance with DIN EN 50022.
Dimensions:
35 x 7.5 mm or 35 x 15 mm
`Where vibration and shock stress
place increased requirements on
the system fastenings, it is
recommended that the mounting
rail is screwed to the mounting
plate approximately every
200 mm.
Module layout
`The first module on a PSSu
system is always a head module.
`A supply voltage module is always
connected to the right of the head
module
- To supply the module electr-
onics to the head module and
subsequent I/O modules
- To provide 24 VDC for the
periphery supply
`Next right it is possible to install
I/O modules for FS and ST
applications.
- The I/O modules (input
modules, output modules) can
be installed in any order.
- I/O modules for FS applications
and ST applications can be
combined as required.
- In various applications it makes
sense to combine specific
modules into groups.
- It is not possible to mix base
modules with screw terminals
and cage clamp terminals.
- The max. number of I/O
modules is determined through
the defined system limits.
`Supply voltage modules may be
required to refresh the supply to
the module electronics. This can
be determined through the
defined system limits.
`To form supply groups, an
additional voltage supply module
is required at the start of each
group. The modules belonging to
the supply group will then follow
to the right.
`The final element in a PSSu
system is always a terminating
plate, containing the bus
terminating resistors.
`Various fastening elements are
used at the start and end of the
system to secure the system on
the mounting rail:
- End bracket at the start of the
system
- Plastic version (standard)
- Metal version
(increased requirements with
regard to vibration and
shock stress)
- End bracket at the end of the
system
- Plastic version (standard)
- Metal version
(increased requirements with
regard to vibration and
shock stress)
End bracket
(metal version
if necessary)
Head
module
Supply voltage module
Terminating plate
with integrated
End bracket
Additional metal end
bracket if required
I/O modules
with supply voltage modules to separate the supplies
if necessary)

PSSuniversal
Basics
Installation
Status 01/05
1.2-2
Pilz GmbH & Co. KG, Sichere Automation, Felix-Wankel-Straße , 73760 Ostfildern, Germany
Telephone +49 711 3409-0, Telefax +49 711 3409-133, E-Mail: [email protected]
Mounting distances
The values stated in the diagram
below are minimum specifications.
Appropriate air conditioning may also
be required. The values stated for
ambient temperature must be
maintained. These values can be
found in the technical details for the
individual modules.
35 mm
35 mm
20 mm 20 mm

2
PSSuniversal
Basics
Installation
Status 01/05 1.2-3
Pilz GmbH & Co. KG, Sichere Automation, Felix-Wankel-Straße , 73760 Ostfildern, Germany
Telephone +49 711 3409-0, Telefax +49 711 3409-133, E-Mail: [email protected]
Installing the head module
`Prerequisites:
- The mounting rail must already
be installed.
`Install an appropriate end bracket
to the left of the head module or
leave enough space to install it
later.
`Procedure:
- Slot the groove on the head
module on to the mounting rail
from below [1].
- Push the head module back [2]
until you hear it lock into
position.
[2]
[1]

PSSuniversal
Basics
Installation
Status 01/05
1.2-4
Pilz GmbH & Co. KG, Sichere Automation, Felix-Wankel-Straße , 73760 Ostfildern, Germany
Telephone +49 711 3409-0, Telefax +49 711 3409-133, E-Mail: [email protected]
Removing the head module
`Prerequisite:
- The supply voltage must be
switched off
- The bus connections must be
disconnected
- All the wiring must be removed
- All the base modules must have
been moved to the right (min.
30 mm) or have already been
removed.
`Procedure:
- Using a screwdriver, push the
rear locking element [1]
upwards until the locking hook
releases the anchor.
- Pivot the head module and
screw driver forwards [2] and
remove in a downward
direction [3].
[2]
[1]
[3]

2
PSSuniversal
Basics
Installation
Status 01/05 1.2-5
Pilz GmbH & Co. KG, Sichere Automation, Felix-Wankel-Straße , 73760 Ostfildern, Germany
Telephone +49 711 3409-0, Telefax +49 711 3409-133, E-Mail: [email protected]
Installing base modules
`Prerequisite: The head module
must already be installed.
`The head module must always be
followed on the right by a base
module that is suitable for an
appropriate supply voltage
module.
`The wiring should preferably be
carried out after the base modules
are installed, but before the
electronic modules are installed.
`Please note:
- For mechanical reasons it is not
possible to mix base modules
with screw terminals and base
modules with cage clamp
terminals.
- All contacts should be
protected from contamination.
`Procedure:
The same procedure applies for all
base modules (e.g. base modules
in grid widths 1 x 12.6 mm, 2 x
12.6 mm).
- Base modules should always
be installed to the right of the
head module.
- Slot the groove on the base
module on to the mounting rail
from below [1].
- Push the base module back [2]
until you hear it lock into
position.
- On the mounting rail, slide the
base module to the left until
you hear the two lateral
mounting hooks on the
adjacent module (head module
or base module) lock into
position [3].
[2]
[1]
[3]

PSSuniversal
Basics
Installation
Status 01/05
1.2-6
Pilz GmbH & Co. KG, Sichere Automation, Felix-Wankel-Straße , 73760 Ostfildern, Germany
Telephone +49 711 3409-0, Telefax +49 711 3409-133, E-Mail: [email protected]
Removing base modules
`Prerequisite:
- The supply voltage on the
corresponding supply module
must be switched off
- All the wiring must be removed
- The electronic module on the
relevant base module must
have been removed, plus the
electronic module on the base
module to the left.
- All the base modules to the
right of the relevant base
module must have been moved
to the right (min. 30 mm) or
have already been removed.
`Procedure:
The same procedure applies for all
base modules (e.g. base modules
in grid widths 1 x 12.6 mm,
2 x 12.6 mm).
- Insert the screwdriver into the
square opening on the base
module to the left of the
relevant module [1].
- Push the screwdriver
downwards and keep it
pressed down.
- Use the other hand to pull the
base module to the right [2]
until the locking element on the
base module you are removing
is completely free.
- On the mounting rail, slide the
base module to the right [3]
- Using a screwdriver, push the
rear locking element [4]
upwards [5] until the locking
hook releases the anchor.
- Pivot the base module and
screw driver forwards and
remove in a downward
direction.
NOTICE
Modules may be inserted and
removed a maximum of 20 times.
After this point a correct contact can
no longer be guaranteed.
[1]
[2]
[3]
[4]
[5]
[3]

2
PSSuniversal
Basics
Installation
Status 01/05 1.2-7
Pilz GmbH & Co. KG, Sichere Automation, Felix-Wankel-Straße , 73760 Ostfildern, Germany
Telephone +49 711 3409-0, Telefax +49 711 3409-133, E-Mail: [email protected]
Installing an end bracket at the start
of the system
`Select an end bracket, depending
on the vibration and shock stress
(plastic version/metal version)
`Procedure:
- Use a screwdriver for slotted-
head screws (M2).
- Loosen the fixing screw on the
end bracket until the terminals
are far enough apart for the end
bracket to be positioned on the
mounting rail.
Removing an end bracket at the start
of the system
`Procedure:
- Use a screwdriver for slotted-
head screws (M2).
- Loosen the fixing screw on the
end bracket until the terminals’
clamping force is lifted.
- Remove the end bracket from
the mounting rail.
- Place the end bracket on the
mounting rail, to the left of the
head module [1].
- Slide the end bracket up close
to the head module [2]
- Tighten up the end bracket [3].
[1]
[2]
[3]

PSSuniversal
Basics
Installation
Status 01/05
1.2-8
Pilz GmbH & Co. KG, Sichere Automation, Felix-Wankel-Straße , 73760 Ostfildern, Germany
Telephone +49 711 3409-0, Telefax +49 711 3409-133, E-Mail: [email protected]
Installing a terminating plate and end
bracket at the end of the system
`Select an end bracket, depending
on the vibration and shock stress
- Plastic version of end bracket
(integrated into terminating
plate)
- Additional end bracket if
required (metal version)
`Procedure:
- Use a screwdriver for slotted-
head screws (M2).
- Attach the terminating plate to
the mounting rail as the final
element on the system [1].
- Loosen the fixing screw on the
end bracket until the terminals
are far enough apart for the end
bracket to be positioned on the
mounting rail.
- Place the end bracket on the
mounting rail, to the right of the
terminating plate [2].
- Slide the end bracket and
terminating plate into each
other [3]
- Slide the terminating plate with
integrated end bracket up to
the final base module as far as
it will go [4]; ensure that contact
is made with the integrated bus
terminating resistors.
- Insert the screwdriver into the
terminating plate [5]
- Tighten up the integrated end
bracket [6].
`If an additional end bracket (metal
version) is required to secure the
system, this additional end
bracket is installed to the right of
the terminating plate.
Procedure:
- Loosen the fixing screw on the
metallic end bracket
- Place the metallic end bracket
on the mounting rail
- Slide the metallic end bracket
up close to the terminating
plate with the integrated end
bracket
- Tighten up the metallic end
bracket
[5]
[3]
[6]
[1]
[2]
[4]

2
PSSuniversal
Basics
Installation
Status 01/05 1.2-9
Pilz GmbH & Co. KG, Sichere Automation, Felix-Wankel-Straße , 73760 Ostfildern, Germany
Telephone +49 711 3409-0, Telefax +49 711 3409-133, E-Mail: [email protected]
Removing a terminating plate and
end bracket at the end of the system
`Procedure:
- Use a screwdriver for slotted-
head screws (M2).
- Insert the screwdriver into the
terminating plate [1]
- Loosen the fixing screw on the
end bracket [2].
- Move the terminating plate and
integrated end bracket to the
right [3].
Note: Do not damage the
elements used to connect to
the adjacent base module.
- Loosen the fixing screw on the
end bracket until the terminals’
clamping force is lifted.
- Remove the terminating plate
and integrated end bracket
from the mounting rail.
[3]
[2]
[1]
[3]

PSSuniversal
Basics
Installation
Status 01/05
1.2-10
Pilz GmbH & Co. KG, Sichere Automation, Felix-Wankel-Straße , 73760 Ostfildern, Germany
Telephone +49 711 3409-0, Telefax +49 711 3409-133, E-Mail: [email protected]
[2]
[1]
[1]
Inserting an electronic module
NOTICE
Modules may be inserted and
removed a maximum of 20 times.
After this point a correct contact can
no longer be guaranteed.
`Electronic modules should only be
plugged into base modules that
are installed and, preferably,
wired.
`Electronic modules with outputs
(output modules) may only be
inserted or removed when the
load is switched off.
If modules are inserted/removed
under load, the possibility of the
PSSu system switching to a safe
condition (STOP condition) cannot
be excluded. The corresponding
I/O-Group (SafetyBUS p) may also
switch to a STOP condition.
`Procedure:
- The electronic module must
audibly lock into position [1].
- Identify the electronic module
using the labelling strips [2]

2
PSSuniversal
Basics
Installation
Status 01/05 1.2-11
Pilz GmbH & Co. KG, Sichere Automation, Felix-Wankel-Straße , 73760 Ostfildern, Germany
Telephone +49 711 3409-0, Telefax +49 711 3409-133, E-Mail: [email protected]
Mechanical coding
Electronic modules have a two-part
coding element. The first time an
electronic module is plugged into a
base module, one part of the coding
element remains on the electronic
module, while its counterpart is fixed
on to the base module.
The coding element is designed to
help prevent plugging errors (e.g.
when exchanging modules).
`Once a base module has been
coded, only electronic modules
with the same coding can be
inserted.
`If a new electronic module is to be
plugged into a base module that
has already been coded, you will
initially need to remove the coding
counterpart on the electronic
module.
Electronic module
PSSu E F PS-P
Coding: yellow, A
PSSu E PD
Coding: light grey, A
PSSu E F PS
Coding: yellow, B
PSSu E F PS1
Coding: yellow, C
PSSu E F 4DI
Coding: yellow, D
PSSu E F 4DO 0.5
Coding: yellow, E
PSSu E F 2DO 2
Coding: yellow, F
PSSu E F DI OZ 2
Coding: yellow, G
PSSu E F 2DOR 8
Coding: yellow, H
PSSu E F BSW
Coding: yellow, I
PSSu E S 4DI
Coding: dark grey, A
PSSu E S 4DO 0.5
Coding: dark grey, B
PSSu E S 2DO 2
Coding: dark grey, C
Mechanical coding element
(rear view of electronic module)
Overview of the mechanical coding
elements on electronic modules
Other manuals for PSSuniversal
2
Table of contents
Other Pilz Measuring Instrument manuals
Popular Measuring Instrument manuals by other brands
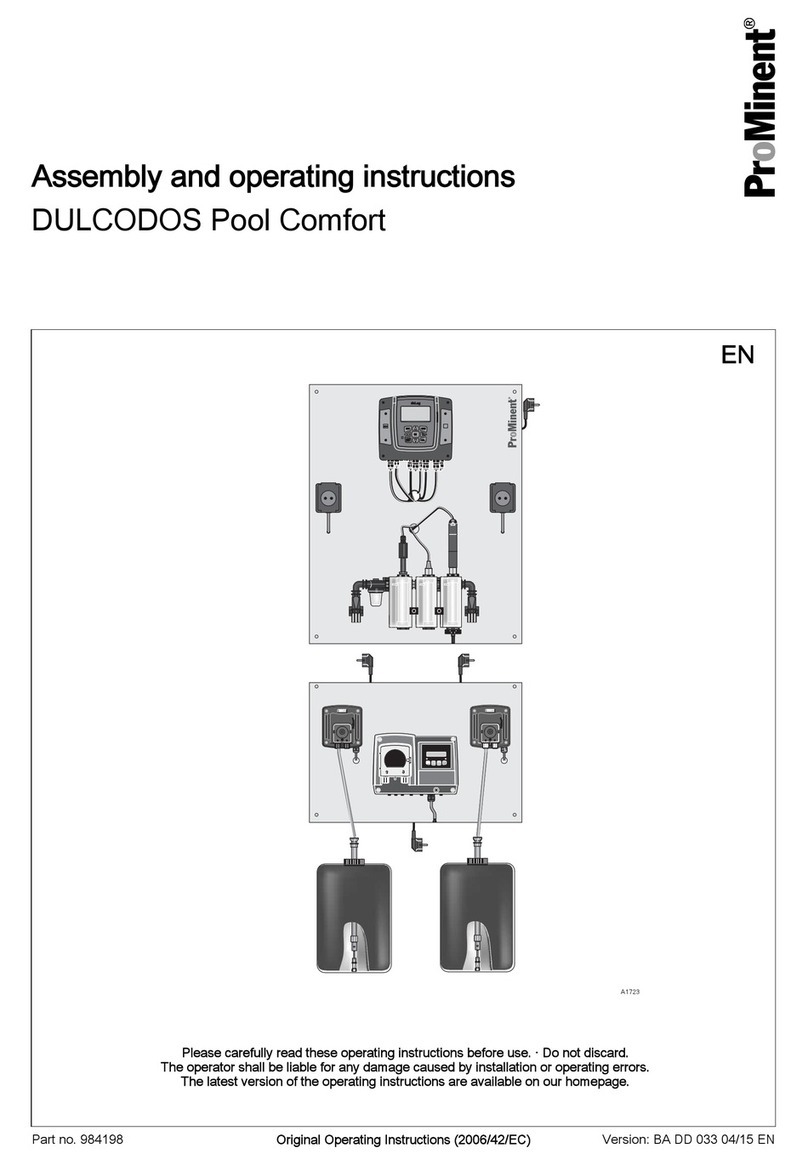
ProMinent
ProMinent DULCODOS Pool Comfort Assembly and operating instructions

Komshine
Komshine KFL-11M manual
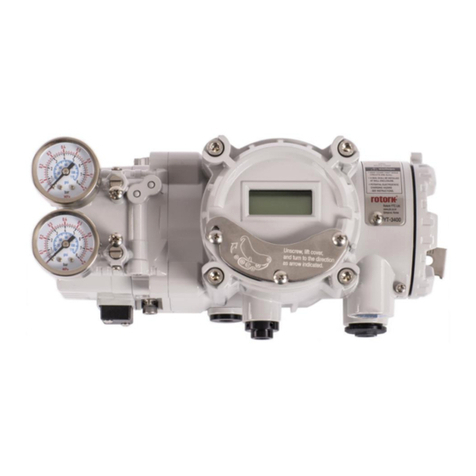
rotork
rotork 3450 Series product manual
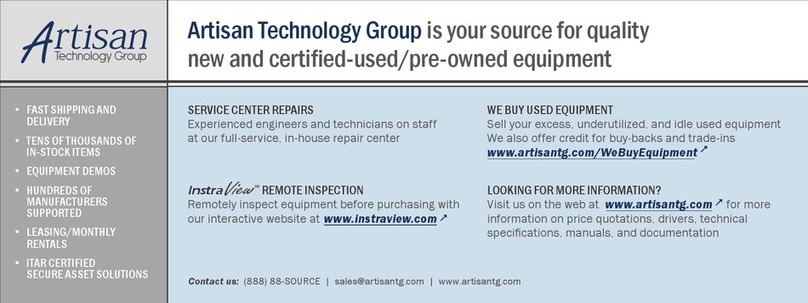
WAGNER
WAGNER FORCE DIAL FDL Series Operation manual
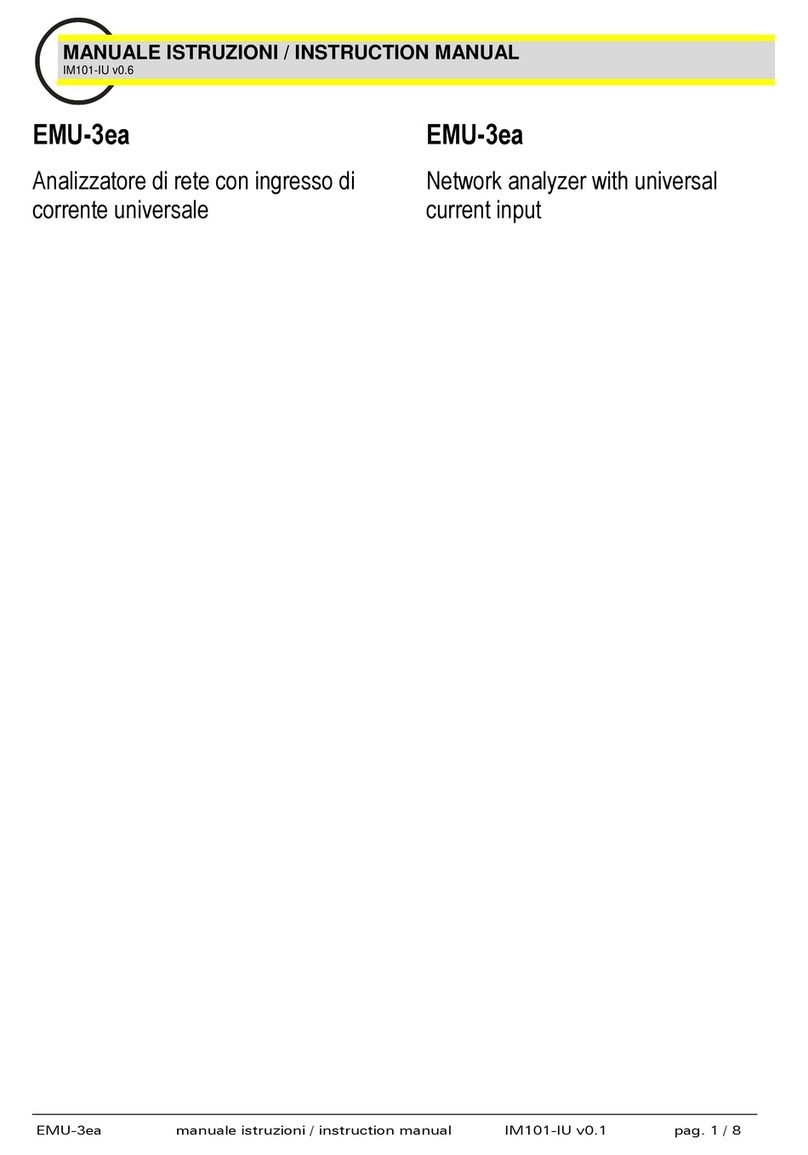
Contrel
Contrel EMU-3ea instruction manual

IFM Electronic
IFM Electronic efector 300 SI0508 operating instructions