Plum ecoMAX920P2-I Specification sheet

1
ecoMAX920P2-I
Weather controller
FOR CENTRAL HEATING SYSTEMS
OPERATION AND INSTALLATION MANUAL
Manual version: 1.0_EN
05-2019
ecoSTER TOUCH*
ecoNET300*
ecoNET.apk
www.econet24.com
* ecoSTER TOUCH and internet module ecoNET300 are not part of
standard equipment controller.


TABLE OF CONTENTS
1SAFETY INFORMATION........................................ 4
2CONTROLLER INTENDED USE.............................. 5
3INFORMATION CONCERNING DOCUMENTATION5
4DOCUMENTATION STORAGE .............................. 5
5USED SYMBOLS ................................................... 5
6WEEE DIRECTIVE 2012/196/UE........................... 5
FOR THE USER .............................................. 7
7CONTROLLER DESCRIPTION ................................ 8
7.1 CONTROLLER STRUCTURE....................................... 8
7.2 CONTROLLER OPERATION....................................... 8
7.3 DISPLAY MAIN SCREEN .......................................... 9
7.4 MENU LEVELS ................................................... 10
7.5 MAIN MENU ..................................................... 10
7.6 INSTALLER’S SERVICE MENU.................................. 10
7.7 USER’S MAIN MENU ........................................... 11
8CONTROLLER OPERATION................................. 12
8.1 ACTIVATING AND DEACTIVATING ........................... 12
8.2 PRESETTING TEMPERATURES ................................ 12
8.3 TIME PROGRAMS ............................................... 12
8.4 SUMMER -WINTER ............................................ 13
8.5 WORK MODE SETTING ........................................ 13
8.6 HOLIDAY PLANNING............................................ 14
8.7 CHANGING NAMES ............................................. 14
8.8 CORRECTION OF TEMPERATURE READINGS .............. 15
8.9 PARENTAL LOCK................................................. 15
8.10 SCREEN BRIGHTNESS ADJUSTMENT ........................ 15
8.11 SOFTWARE UPDATE ............................................ 15
9CONTROLLER FUNCTIONS................................. 15
9.1 INFORMATIVE FUNCTION ..................................... 15
9.2 ANTI -FREEZE.................................................... 15
9.3 ROOM TEMPERATURE STABILIZATION..................... 16
9.4 SOLAR ............................................................. 17
9.5 INTERNET ......................................................... 17
FOR THE INSTALLER.................................... 19
10 CONTROLLER ASSEMBLY................................... 20
10.1 GENERAL REQUIREMENTS .................................... 20
10.2 OUTPUT MODULE ASSEMBLY................................ 20
10.3 TEMPERATURE SENSORS ASSEMBLY........................ 20
10.4 CONNECTING A HEAT SOURCE............................... 21
10.5 CONNECTING PUMPS.......................................... 21
10.6 CONNECTING SERVOS ..........................................21
10.7 OUTPUT TEST.....................................................22
10.8 CONTROL PANEL ASSEMBLY ..................................22
10.9 CONNECTING THE CONTROL PANEL.........................22
10.10 CONNECTING THE ROOM PANELS ...........................22
10.11 HEAT SOURCE OUTPUT MODULATION .....................23
10.12 WEATHER CONTROL SETTINGS...............................24
10.13 ROOM THERMOSTAT SETTINGS..............................24
11 HYDRAULIC DIAGRAMS .................................... 26
12 ELECTRICAL SYSTEM ......................................... 34
12.1 ELECTRICAL DIAGRAM..........................................36
13 SERVICE MENU ................................................. 37
13.1 H1 CIRCUIT SERVICE SETTINGS...............................39
13.2 H2 CIRCUIT SERVICE SETTINGS...............................40
13.3 H3 CIRCUIT SERVICE SETTINGS...............................42
13.4 HUW CIRCUIT SERVICE SETTINGS...........................42
13.5 SYSTEM ............................................................43
13.6 SOLAR ..............................................................44
13.7 BUFFER SETTINGS ...............................................45
13.8 PANEL ADDRESS .................................................45
14 TECHNICAL DATA.............................................. 46
15 TRANSPORTATION AND STORAGE CONDITIONS46
16 TEMPERATURE SENSORS CHECK ...................... 46
17 REPLACEMENT OF MAINS FUSE........................ 46

4
1SAFETY INFORMATION
Requirements concerning safety are listed in
particular sections of this instruction. Apart
from them it in necessary to fulfill the following
requirements.
Controller can be assembled only by
qualified installer and in accordance with
currently valid standards and
regulations.
Prior to starting the assembly, repairs or
maintenance and during the execution
of any connection works, it is necessary
to switch off the mains supply and make
sure that no terminals no electrical
wires are energized.
After deactivating the controller with the
use of a keyboard, terminals of the
controller can be under a dangerous
level of voltage.
The controller can be utilized only in
accordance with its intended use.
Additional automatics should be used in
order to protect central heating and
HUW system against the results of
regulator failure or software errors.
Particularly control automatics which
reduce HUW temperature in order to
protect users against burns.
The controller cannot be used as the
only protection against frozen central
heating system.
Values of programmed parameters must
be set in accordance with a particular
building and hydraulic system.
The controller is not an intrinsically safe
device. It means that in case of failure it
can be a source of sparks or high
temperature which surrounded by ashes
or flammable gases can cause fire or
explosion.
Modification of the programmed
parameters should be made only by a
person who read this manual.
Use only in heat circulation system
made in accordance with currently valid
regulations.
Electrical system including the controller
should be 3-wired and protected with
fuse selected in accordance with used
loads.
The controller cannot be used with
damaged housing.
Never make any modifications in
controller structure.
The controller consists of two
components: control panel and output
module. Replaced component must be
compatible.
The controller is equipped with a
protection against Legionella bacteria.
The controller periodically heats the
HUW tank up to a temperature which
can cause scalding to operator. Installer
should provide information whether the
function is active and additional
automatics protecting against scalding is
installed.
Keep children away from the controller.

5
2Controller intended use
The controller is intended for controlling:
-central heating system,
-HUW tank,
-HUW circulation system,
-solar circulation system.
The controller can be connected to the
automatic boiler equipped with activating or
deactivating contact (ON/OFF switch).
The controller can control the pump and valve
switching additional heat sources, e.g. boiler
with water jacket.
Using the controller for other purposes than its
intended use is forbidden. Manufacturer does
not bear any responsibility for any loss caused
by such use.
3Information concerning
documentation
This instruction applies only to controllers with
software and hardware versions listed on the
first page. Program version can be verified in:
menu →information.
Manufacturer nor supplier of the controller
does not bear any responsibility for damages
due to non-compliance with this manual.
4Documentation storage
Please keep this operation and assembly
manual and other valid documentation in a
safe place for future reference. In case of
moving or selling the device, hand this
documentation over to a new user or owner.
5Used symbols
The following graphical symbols are used in the
manual:
- useful information and tips,
- useful information concerning property
damage, health or life threat for people
or pets.
Caution: important information were labeled
with the aforementioned symbols in order
make the manual easier to understand.
However it does not release the user nor
installer from responsibility of complying with
requirements which are not labeled with any
symbols!
6WEEE Directive 2012/196/UE
Purchased product is designed and made of
materials of highest quality.
The product meets the requirements of the
Directive 2012/19/EU of 4 July 2012 on
waste electrical and electronic equipment
(WEEE), according to which it is marked by
the symbol of crossed-out wheeled bin (like
below), meaning that product is subjected to
separate collection.
Responsibilities after finishing a period of using
product:
dispose of the packaging and product at the
end of their period of use in an appropriate
recycling facility,
do not dispose of the product with other
unsorted waste,
do not burn the product.
By adhering obligations of waste electrical and
electronic equipment controlled disposal
mentioned above, you avoid harmful effects on
the environment and human health.

6

CONTROLLER OPERATION MANUAL
ecoMAX920P2-I
FOR THE USER

8
7Controller description
7.1 Controller structure
The controller consists of a touch control
panel (1) and control module (3). Both
components are connected with a 4-signal
cable (2). An external temperature sensor
(4) connected with the module (3) with 2-
wire cable (5) is necessary for proper
operation of the system. Touch control panel
(1) can be placed in a house apartment, e.g.
in the living room or hall. Module (3) should
be placed in the boiler room close to
electrical devices included in the central
heating system. Cable (2) should meet the
requirements listed in installer’s manual.
Control panel is equipped with a room
temperature sensor and therefore it also acts
as a room thermostat. There is a possibility
of connecting many control panels measuring
room temperature for various heat
circulations.
7.2 Controller operation
Heat source
The controller controls the operation of heat
source, e.g. an automatic gas, oil or pellet
boiler, by activating or deactivating it
according to a heat demand of the central
heating system.
Hot utility water
The controller controls the operation of HUW
pump loading a hot water tank up to a user-
defined temperature. Preparation of HUW
can be programmed in time intervals. The
controller also controls a HUW circulating
pump. It enables quick transportation of
HUW to a bathroom or kitchen located far
away.
Heating circuits
The controller control the operation of one
direct heating circuit (radiator) and two
adjustable heating circuits (radiator or floor).
Water temperature in heating circuits is set
by weather, i.e. water temperature in the
heating circuit is calculated in accordance
with a temperature from the external sensor.
Due to this, despite of varying external
temperature, a room temperature in heated
compartments are kept on a set level.
Dependent and independent heating
circuits
- Dependent heating circuits –controller
touch panel can be a common room
thermostat for many heating circuits. For
example, room temperature readings on a
panel installed in the living room affect
operation of both radiator and floor circuit.
Both these circuits heat up a common
temperature sensor located on the screen by
supplying heat.
- Independent heating circuit –there is a
possibility of connecting many control panels
measuring room temperature independently
and affecting assigned heating circuits. It is
the way to obtain independency of heating
circuits, e.g. in case when one part of the
building is used for the whole year and the
second part is used periodically, e.g. for rent.
More details are include in pt.10.10.
Solar system
The controller controls a basic solar system
heating the HUW tank. Apart from
temperature sensors, no additional module is
necessary to operate the solar system.

9
7.3 Display main screen
Legend:
1. „Salon” - control panel name. It is also a
name of the compartment in which the
panel is located. Default name in “Panel
1”. This name should be changed in
menu →basic settings →change panel
name
2. Holiday mode –symbol concerning
running holiday mode. Mode can be
programmed in menu →basic settings.
This symbol is displayed automatically.
3. Arrow for changing screen –press this
arrow in order to switch to HUW
preparation screen or separate heating
circuit screen if any additional functions
are active.
4. Important information –graphical
symbol appears in case of important
information for user occurs, e.g.
information concerning temperature
sensor damage.
5. Enter MENU button
6. Symbol of active heat source –this
symbol indicates that the boiler is active.
7. Heating mode symbol –possible
options: day and night.
8. Preset room temperature –it is set
separately for day and night mode. Press
this symbol in order to edit the preset
room temperature.
9. Navigation bar –indicates location of
displayed screen and number of screens
possible to be displayed. Screens can be
changed with the use of (3) and (11)
arrows.
10. Temperature measured by external
temperature sensor
11. Arrow for changing screens –press
this symbol in order to switch to HUW
preparation screen or separate heating
circuit screen if any additional functions
are active.
12. Date and hour
13. Parental lock symbol –lock can be
deactivated in menu →basic settings.
14. Current work mode symbol –press
this symbol in order to go to work mode
selection.
15. Measured room temperature –by
room temperature sensor located in the
control panel.

10
7.4 Menu levels
Two main menu levels are used in the controller:
- user’s main menu,
- installer’s service menu.
7.5 Main menu
Press “menu” to display rotational main menu.
Legend:
1. Back to previous menu button
2. Back to display main window button –menu press it to get back to main window from every
menu sublevel
3. Info button –press to obtain detailed information concerning the parameter selected on a
display
4. Press to enter service level for installer
7.6 Installer’s service menu
Click MENU button and select in order to enter the installer’s menu level. This level is
protected with a password (default password: 0000). More details concerning service menu is
included in further parts of the installer’s instruction.

11
7.7 User’s main menu
Caution: particular menu positions can be invisible in case there is no
appropriate sensor, module or setting.

12
8Controller operation
8.1 Activating and deactivating
Press the switch on the screen in order to
activate the controller. “Activate controller?”
message will be displayed.
Accept your choice in order to activate the
controller. To deactivate the controller, press
MENU button, search for in rotational
menu and press it.
Caution: when the controller is
deactivated, an anti-freeze function
will not work! Therefore it is
recommended to change worm
mode of heating and HUW circuits
to off instead of deactivating the
controller.
8.2 Presetting temperatures
Heating circuits
Preset room temperature can be
set separately for “day” and
“night” mode. This temperature
can be changed by clicking
directly on a preset temperature
value in controller main window, element no.
8. Preset room temperature can be also
changed by entering:
menu →preset temperatures
At low external temperatures it is
recommended that the difference
between preset temperatures for
day and night is not higher than
2°C
HUW tank
Preset temperature in HUW tank can be
changed by clicking on a preset HUW tank
temperature in HUW window. In order to
enter HUW window, click an arrow in
controller main window, element no. 11.
HUW preset temperature can be also entered
in: menu →preset temperatures.
HUW tank loading function becomes
active after connecting a tank
temperature sensor.
8.3 Time programs
The controller includes a function
of programming time periods. In
situation when the user is outside
his home or at night, the
controller can decrease the amount of
supplied heat energy what affects fuel
consumption.
Time programs are defined separately for
heating circuits, UW tank and HUW
circulation system. Time programs can be set
separately for each day of the week. In case
when many heat circulation systems are
assigned to a common control panel, time
programs entered for this panel are global
and can be used for all circulation systems
simultaneously. Time programs are entered
in:
menu →time programs
In the example below, a “night” period will
last from 00:00 till 06:00. “Day” period will
last between 06:00 –09:00. From 15:00 to
22:00 the “day” period was entered. “Night”
period will last from 22:00 to 00:00.
After accepting the entered time period for a
particular day, the controller will propose a
possibility of saving this setting for other
days of the week. Due to this, entering time
periods is quick and intuitive.
Operation within time periods for “day” and
“night”:

13
“Day” period
Heating
circuits
Preset room temperature is
set to day temperature value.
HUW tank
HUW tank is loaded up to
HUW preset temperature
HUW
circulation
system
HUW circulating pump
transports heat from the HUW
tank to a distant HUW
receivers. Pump is on for a
pump operation time every
pump interval time. Time
settings are included in
service menu.
Heat source
Active
“Night” period
Heating
circuits
Preset room temperature is
set to night temperature
value.
HUW tank
HUW tank is off
HUW
circulation
system
HUW circulating pump is off
Heat source
Active
8.4 Summer - winter
Outside the heating season the
controller can be switched to
SUMMER mode. It enables to
deactivate heating circuits such as
radiation or floor heating and maintain
operation of HUW tank loading function.
SUMMER mode can be activated manually:
menu
Summer-winter
Summer mode
= YES
SUMMER mode can be also activated
automatically. In order to do this, select:
Summer mode = AUTO. The controller will
enter SUMMER mode when the external
temperature exceeds the SUMMER mode act.
temperature parameter. The controller will
deactivate SUMMER mode when the external
temperature drops below SUMMER mode
deact. temperature parameter.
Automatic switching into SUMMER
mode is possible only when the
external temperature sensor is
connected.
8.5 Work mode setting
It is possible to select work mode
which is suitable for user’s
requirements.
User can select work mode in two
ways: directly in a display main window by
pressing a symbol in an upper middle area of
the display or by entering: menu →work
modes.
Main modes
Auto
Preset room temperature is
switched between “day” and
“night” temperatures depending
on clock indications and defined
time programs for particular
days of the week.
HUW tank is loaded during a
period corresponding to “day”
temperature. For time programs
corresponding to “night”
temperature, the HUW tank is
off.
Off
The controller deactivates a
particular heating circuit or HUW
tank. Anti –freeze function
remains active provided that is
in active in service menu.
Day
Comfort mode. Preset room
temperature is constant and
corresponds the entered “day”
value. HUW tank maintains
constant preset temperature.
Night
Economy mode. Preset room
temperature is constant and
corresponds the entered “night”
value. It is not possible to select
this mode for HUW tank. Instead
of this it is recommended to
select “Off” mode + 1x HUW
loading for HUW.
Auto-Eco
Preset room temperature is
maintained within defined time

14
periods as “day” temperature.
Circuit is off outside the defined
time periods. Anti –freeze
function remains active provided
that is in active in service menu.
It is not possible to select this
mode for HUW tank. Instead of
this it is recommended to select
“Off” mode + 1x HUW loading
for HUW.
Additional modes
Outside
Time mode. Enables to save heat
energy when a person is out.
Away time is set, e.g. 3 hours.
During this period room
temperature for heat circuits is
set as “night”. HUW tank is
turned off. After the set time is
over, system switches to a
previous work mode. Set outside
time to 0 in order to switch off
this mode.
Party
Time mode. Enables to achieve
full heat comfort by temporary
activation of modes responsible
for saving heat energy. A time is
set, e.g. 5 hours. During this
period room temperature for
heat circuits is set as “day”.
HUW tank is loaded to a set
temperature. After the set time
is over, system switches to a
previous work mode. Set party
time to 0 in order to switch off
this mode.
Airing
Time mode. Enables to save heat
energy when rooms are aired.
Airing time is set, e.g. 6
minutes. After the set time is
over, system switches to a
previous work mode. Set party
time to 0 in order to switch off
this mode. This mode has no
influence on operation of HUW
tank.
Enables a single HUW load in
situation when HUW tank heat
energy saving mode is active.
1 x HUW
loading
User can select main mode for
HUW tank as “Inactive” and, if
necessary, activate an additional
“1 x HUW loading” mode in order
to save heat energy resulting
from stoppage losses of HUW
tank.
This mode can also be useful in
situation when “Auto” mode is
selected for HUW tank and night
decrease is in progress. “1 x
HUW loading” mode can be used
for a single loading of HUW tank
regardless of a night decrease.
Work mode can be selected separately for
each heating circuit and separately for HUW
tank. In case when many heating circuits are
assigned to a common control panel, work
mode change is global and applies to all
circuits simultaneously. “Auto-eco” and
“Night” modes are not available for HUW
tank.
8.6 Holiday planning
The controller is equipped with a
function enabling to plan holiday,
i.e. days during which the user is
outside his home.
menu
Basic settings
Holiday
Enter holiday start and end date and set the
Activation = off.
During a set period, independently of the
selected work mode, the controller will
maintain a room preset temperature
corresponding to a set “night” value.
menu
Basic settings
Holiday
HUW tank will be off.
8.7 Changing names
It is possible to change a default
name of the control panel and
names of heating circuits
displayed in the controller.
Control panel name can be
changed in:

15
menu
Basic settings
Change panel
name
Usually, name of the control panel should
correspond to a room in which it is installed,
e.g. “living room” or “hall”.
In case there are many control panels
installed in the system, their names can
correspond to particular parts of a building or
buildings in which they are installed, e.g.
“ground floor”, “1st floor”, 2nd floor”.
Default name of the panel is
restored if the “PANEL 1” field is left
blank.
8.8 Correction of temperature
readings
menu
Basic settings
Room
sensor temperature correction
Temperature sensor readings
can be corrected. Temperature
sensor is located in the control panel.
Correction value can be entered with
accuracy of 0,1°C.
8.9 Parental lock
It is possible to lock the touch
screen against children. Lock is
activated in: menu
Basic
settings
Parental lock.
Lock is activated automatically after a set
inactivity time. In order to unlock the
controller, press the screen in any place and
hold it for 4s.
8.10 Screen brightness adjustment
Three screen brightness levels are available:
-“Edition” –screen brightness
for editing parameters, i.e.
when the controller is
operated
-“Day” –screen brightness
between 06:00 –22:00,
-“Night” –screen brightness between
22:00 –06:00.
8.11 Software update
Software can be modified with
the use of microSD memory
card. In order to change the
program, insert the memory
card into a slot in the control panel.
New software should be saved in *.pfc
format on a memory card in a form of two
files: file with a program for the control panel
and file with a program for the controller A
module. Save new software directly on a
memory card. Do not nest data in a sub-
folder. Enter:
Menu →General settings →Software update
and replace programs in the controller A
module and panel.
Inserting the memory microSDHC card into the control
panel.
9Controller functions
9.1 Informative function
The controller is equipped with a detailed
information function. This function provides
the user with additional information
concerning any parameter in the controller
menu. In order to obtain additional
information, select the parameter and press
“i” button in a lower bar of the controller.
Information window will be displayed.
9.2 Anti - freeze
Anti –freeze function is applicable only to
active controller work modes: “off” or “auto-
eco”. In “auto-eco” mode, this function is
executed only during a night reduction.

16
View of main menu screen with turned OFF work mode
with active anti-freeze function.
When measured temperature drops below
7°C, all heating circuits become active.
Independently of this, heating circuits can be
activated by the external temperature sensor
readings.
Description of anti-freeze protection against
the external temperature sensor readings:
Direct circuit (H1)
When the external temperature drops below
3°C, an anti-freeze delay time, e.g. 4h
(parameter located in service settings) must
expire. If after this time the external
temperature is still under 3°C, a direct
heating circuit pump will be activated for 30
minutes. After 30 minutes the pump will be
off. Heat source (boiler) is activated along
with the pump and it heats the water in
direct circuit up to a minimum value (service
parameter). Next activation of the pump will
take place after an anti-freeze delay time,
e.g. 4h, unless the external temperature
exceeds 3°C. In such case the pump will not
be activated.
Adjustable circuits (H2, H3)
After the external temperature drops below
3°C, an anti-freeze delay time, e.g. 4h
(parameter located in service settings) must
expire. After this time the external
temperature is still under 3°C, an adjustable
heating circuit pump will be activated for 15
minutes. After 15 minutes, water
temperature in the circuit will be checked. If
it is higher than 13°C, the pump will be
stopped. If it is lower than 13°C, the pump
will continue its operation and heating circuit
will be heated by a heat source (boiler) up to
a minimum value (service parameter). The
pump will be stopped unless the external
temperature exceeds 3°C.
Do not disconnect or leave the
controller in STAND-BY mode
without antifreeze functions active
within a freezing hazard period.
View of main menu screen with turned OFF work mode
with active anti-freeze function.
If heating circuits have to be off during this
period, activate “off” or “auto-eco” mode for
heating circuits and HUW tank instead of
turning the controller off.
Description of the anti-freeze function for
HUW tank:
After the HUW tank sensor temperature
drops below 5°C, HUW tank will be loaded up
to a minimum temperature value (service
parameter).
menu
Service settings
HUW circuit
settings
Minimum temperature
Do not disconnect the controller
within a freezing hazard period.
9.3 Room temperature stabilization
Stability of maintaining room temperature
depends on:
- selection of weather control settings,
- selection of room thermostat settings.
Selection of weather control settings
Room temperature maintained in heated
compartments depends on a temperature of
water in heating circuit. Water temperature
in heating circuit is set depending on a
temperature outside the building. The colder
is outside, the higher heating circuit
temperature. This dependence is expressed
in the controller in a form of a heating curve.
Heating curve can be changed and it reflects
Anti-freeze function deactivated!

17
thermal characteristics of the building. The
less heated building the higher heating curve
should be. Heating curve should be selected
experimentally by changing it in several day
intervals. Detailed description concerning
how to select a heating curve and weather
control settings are given in installer’s
manual. Heating curve should be selected by
the installer.
Selection of room thermostat settings
The controller enables correction of preset
temperature of water in heating circuit in
accordance with room temperature readings.
The higher discrepancy between preset and
measured room temperature, the higher
correction of temperature of water in heating
circuit. Detailed description concerning room
thermostat settings are given in installer’s
manual.
9.4 Solar
he controller operates a basic solar system
which loads the HUW tank. Solar system
operation requires additional temperature
sensors. No additional module is required.
Information concerning condition of the solar
system can be found in:
menu
Information
Solar
or on the last screen of the display which can
be accessed by clicking an arrow on the right
side of the main screen, element no. 11.
Optimize preparation of HUW in
order to take a full advantage of
heat gains from the solar panel.
Preparation of HUW can be optimized by
appropriate programming of time program
for HUW tank. Set HUW tank work mode to
“Auto”. Define time program for HUW tank in
such way to set insolation periods as “night”.
Due to this the boiler will not heat up the
HUW tank. Similar effect can be obtained by
setting the work mode for HUW tank to “Off”
manually.
Loading HUW tank can be also optimized by
setting a lowest possible preset temperature
of HUW tank. The lower preset temperature
of HUW tank, the less often boiler will
become active in order to load the tank and
solar energy gain will be higher.
Installer from a service level should set the
highest possible HUW tank maximum
temperature. This will generate the
maximum heat gain. On the other hand there
is a risk of scalding with hot water and
exceeding temperature limit for a particular
HUW tank!
Risk of scalding with HUW! In order
to protect against scalding, install
an additional protective automatics,
e.g. thermostatic mixing valve.
During periods of very high insolation, there
can be a situation in which the HUW tank is
not able to absorb big amount of heat. In
such case, a solar pump transporting heat
from a solar panel to HUW tank becomes off.
Due to a risk of damaging the pump, it is
turned off only when the solar panel
temperature drops. In practice, the solar
system is turned on again the next day after
the sunrise. It indicates a normal operation
resulting from the fact that there is no
possibility of absorbing the heat surplus.
9.5 Internet
The regulator can be connected with the
Internet with the use of an additional
ecoNET300 module. Detailed information is
available on the manufacturer’s website.


CONTROLLER ASSEMBLY AND SERVICE SETTINGS MANUAL
ecoMAX920P2-I
FOR THE INSTALLER

20
10 Controller assembly
10.1 General requirements
The controller should be installed by a
qualified installer in accordance with
currently valid standards and regulations.
Prior to installing the controller make sure
that it will properly cooperate with hydraulic
and electrical system. It is recommended to
install an output module inside boiler room
first. During the assembly, control panel
should be electrically connected to the output
module and left in the boiler room. In will be
used to verify if electrical connections are
proper. After verification, the control panel
can be moved to a residential room.
10.2 Output module assembly
The regulator casing does not provide dust
and water immunity. In order to provide the
protection from these factors the regulator
should be enclosed with a proper casing.
The regulator is to be enclosed –which
means the regulator should be screwed on to
the flat horizontal or vertical surface (e.g.
room wall). To screw on the regulator use
mounting holes and proper screws. Location
and spacing of mounting holes are shown in
the picture below. The regulator must not be
used as a free-standing device.
Arrangement and spacing of the mounting holes in the
housing.
After installation make sure that the device is
properly mounted and it is impossible to
detach it from the mounting surface.
The regulator casing provides the IP20
protection rating. The casing on the
connectors cover side provides IP00 rating,
and because of that connectors must be
unconditionally covered with the cover.
If there is a need to gain an access to the
terminals side, it is a must to disconnect the
mains voltage and make sure there is no
dangerous voltage on regulator terminals.
10.3 Temperature sensors assembly
The regulator is compatible only with CT4,
CT-10, CT6-P, CT6-W sensors. The use of
other sensors is prohibited.
At least one heating circuit temperature
sensor and one external temperature sensor
(weather sensor) are necessary to activate
the controller.
The controller is equipped with
various types of temperature
sensors. Connecting an
inappropriate sensor will cause
incorrect operation of the
controller.
Sensors for heating circuits
Direct heating circuit sensor (H1-S) should
be installed in a hydraulic coupling. If there
is no hydraulic coupling in the system, it can
be fixed to a supplying pipe coming out of
the heat source (boiler).
Assemble the adjustable heating circuit
sensor (H2-S or H3-S) on a pipe after the
heating circuit pump. The temperature
sensors should be installed in a sleeve
located in stream of running water in pipe,
but also it can be installed on the pipe, on
condition that it is thermally isolated from
the pipe.
Mounting temperature sensor: 1 - pipe, 2 –clamps, 3 -
thermal insulation, 4 - temperature sensor.
Insulate sensors affixed to the external
surface of the pipe with the use of thermal
insulation covering the sensor together with
the pipe.
Table of contents
Popular Temperature Controllers manuals by other brands
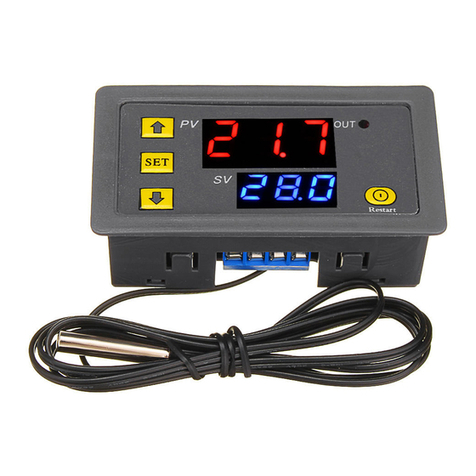
BANGGOOD
BANGGOOD W3230 instruction manual
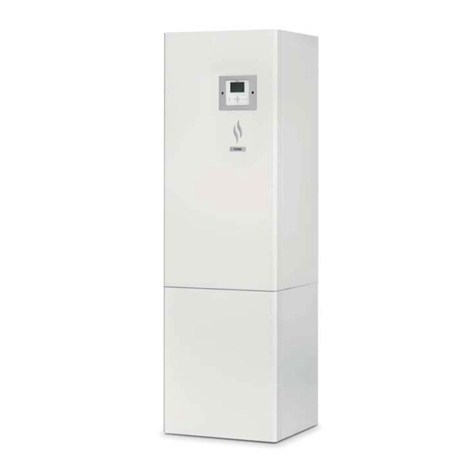
Hitachi
Hitachi YUTAKI S80 R410A Series Installation and operation manual

Consort
Consort SLPBWP Installation & Control Guide
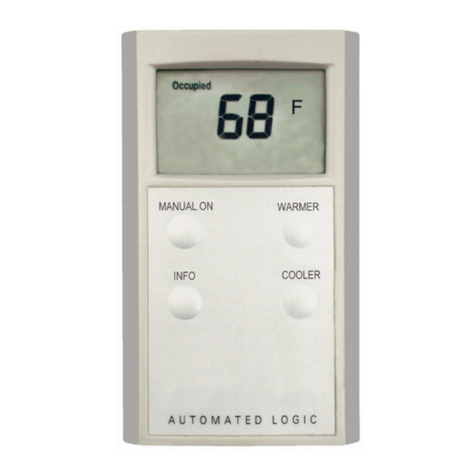
Automated Logic
Automated Logic RS Standard Technical instructions
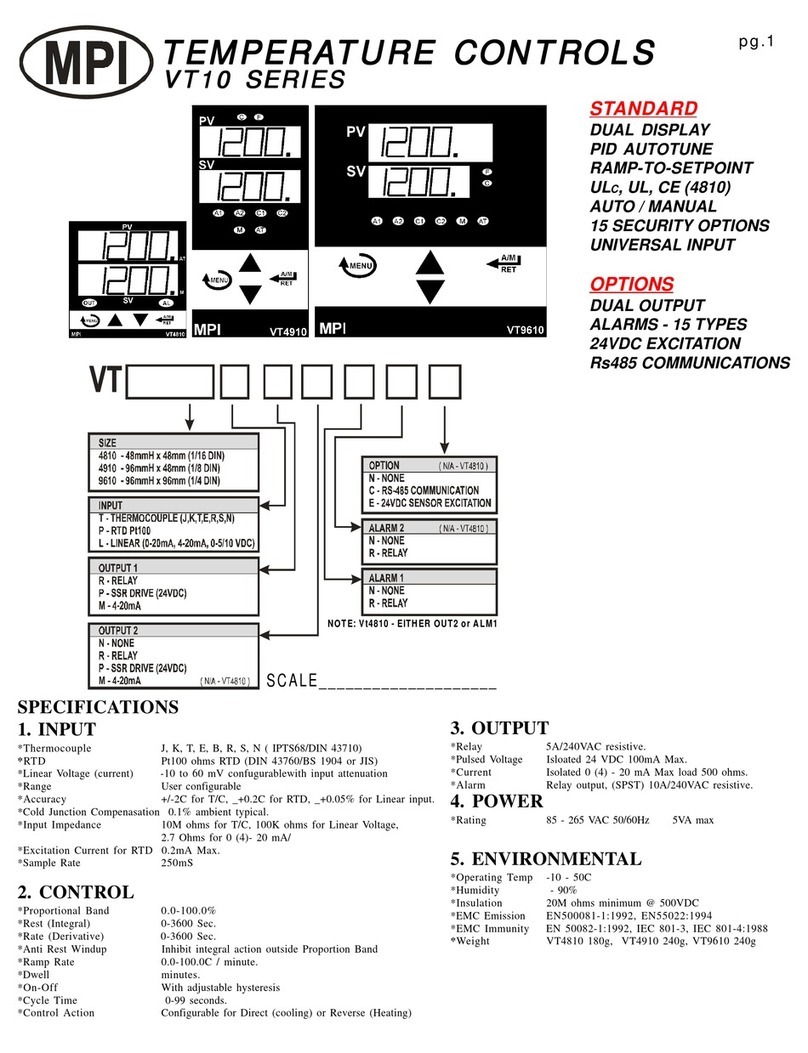
MPI
MPI VT10 Series manual
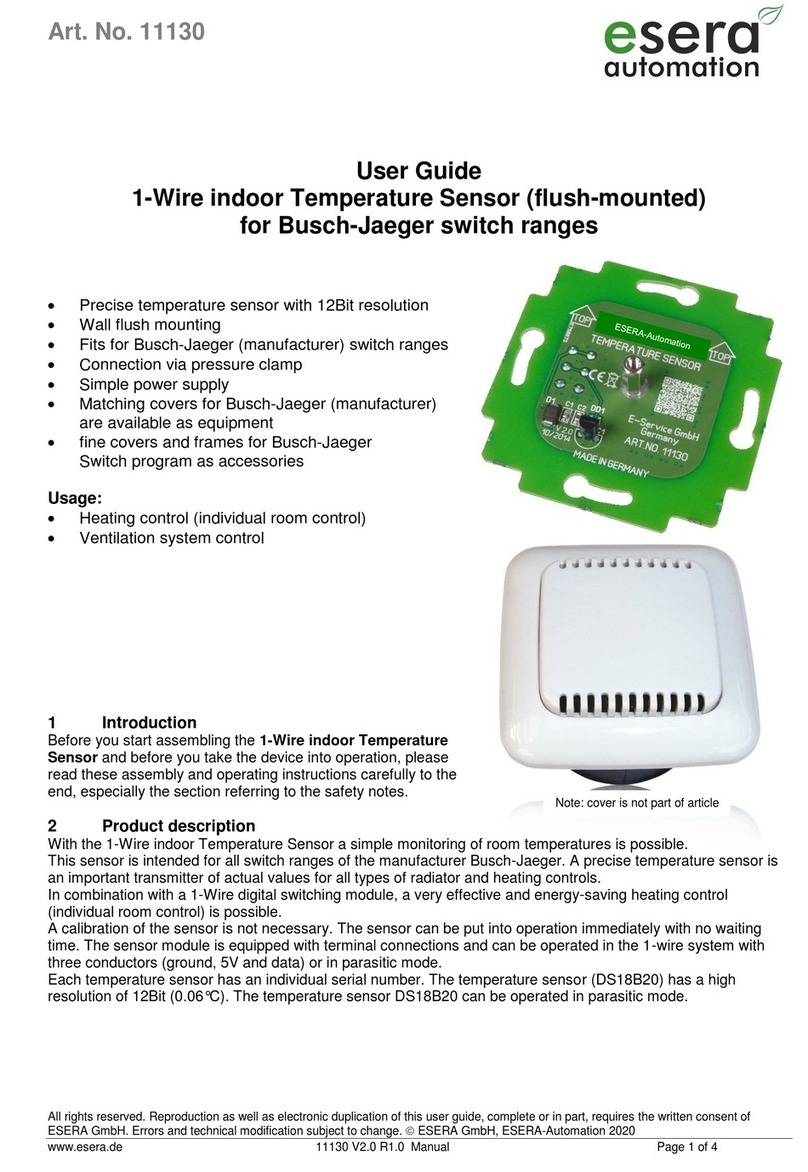
esera automation
esera automation 11130 user guide