Pololu G2 User manual

Pololu Simple Motor Controller
2 User’s uide
Pololu Simple Motor ontroller G2 User’s Guide © 2001–2019 Pololu orporation
https://www.pololu.com/docs/0J77/all Page 1 of 143

1. Overview . . . . . . . . . . . . . . . . . . . . . . . . . . . . . . . . . . . . . . . . . . . . . . 4
1.1. 18v15 and 24v12 included hardware . . . . . . . . . . . . . . . . . . . . . . . . . . . . 8
1.2. 18v25 and 24v19 included hardware . . . . . . . . . . . . . . . . . . . . . . . . . . . 10
1.3. Supported operating systems . . . . . . . . . . . . . . . . . . . . . . . . . . . . . . . 12
1.4. omparison to the original Simple Motor ontrollers . . . . . . . . . . . . . . . . . . . 12
2. ontacting Pololu . . . . . . . . . . . . . . . . . . . . . . . . . . . . . . . . . . . . . . . . . 14
3. Getting started . . . . . . . . . . . . . . . . . . . . . . . . . . . . . . . . . . . . . . . . . . 15
3.1. Installing Windows drivers and software . . . . . . . . . . . . . . . . . . . . . . . . . 15
3.2. Understanding the control center Status tab . . . . . . . . . . . . . . . . . . . . . . . 18
3.3. Errors . . . . . . . . . . . . . . . . . . . . . . . . . . . . . . . . . . . . . . . . . . . 22
3.5. LED feedback . . . . . . . . . . . . . . . . . . . . . . . . . . . . . . . . . . . . . . . 26
4. onnecting your motor controller . . . . . . . . . . . . . . . . . . . . . . . . . . . . . . . . . 29
4.1. onnecting power and a motor . . . . . . . . . . . . . . . . . . . . . . . . . . . . . . 30
4.2. Serial/I² interface pins . . . . . . . . . . . . . . . . . . . . . . . . . . . . . . . . . . 36
4.3. onnecting a serial device . . . . . . . . . . . . . . . . . . . . . . . . . . . . . . . . 39
4.4. onnecting an I² device . . . . . . . . . . . . . . . . . . . . . . . . . . . . . . . . . 41
4.5. onnecting an R receiver . . . . . . . . . . . . . . . . . . . . . . . . . . . . . . . . 42
4.6. onnecting a potentiometer or analog joystick . . . . . . . . . . . . . . . . . . . . . . 46
5. onfiguring your motor controller . . . . . . . . . . . . . . . . . . . . . . . . . . . . . . . . 51
5.1. Input settings . . . . . . . . . . . . . . . . . . . . . . . . . . . . . . . . . . . . . . . 51
5.1.1. onfiguring a limit or kill switch . . . . . . . . . . . . . . . . . . . . . . . . . . 57
5.2. Motor settings . . . . . . . . . . . . . . . . . . . . . . . . . . . . . . . . . . . . . . . 57
5.3. Advanced settings . . . . . . . . . . . . . . . . . . . . . . . . . . . . . . . . . . . . . 62
5.4. Upgrading firmware . . . . . . . . . . . . . . . . . . . . . . . . . . . . . . . . . . . . 65
6. Using the serial and I² interfaces . . . . . . . . . . . . . . . . . . . . . . . . . . . . . . . . 66
6.1. Serial and I² settings . . . . . . . . . . . . . . . . . . . . . . . . . . . . . . . . . . . 69
6.2. Binary commands . . . . . . . . . . . . . . . . . . . . . . . . . . . . . . . . . . . . . 71
6.2.1. Binary command reference . . . . . . . . . . . . . . . . . . . . . . . . . . . . 75
6.3. AS II commands . . . . . . . . . . . . . . . . . . . . . . . . . . . . . . . . . . . . . 87
6.3.1. AS II command reference . . . . . . . . . . . . . . . . . . . . . . . . . . . . 90
6.4. ontroller variables . . . . . . . . . . . . . . . . . . . . . . . . . . . . . . . . . . . . 96
6.5. yclic redundancy check ( R ) error detection . . . . . . . . . . . . . . . . . . . . 103
6.6. Serial daisy chaining . . . . . . . . . . . . . . . . . . . . . . . . . . . . . . . . . . . 105
7. Writing P software to control the Simple Motor ontroller G2 . . . . . . . . . . . . . . . . 108
8. Example code . . . . . . . . . . . . . . . . . . . . . . . . . . . . . . . . . . . . . . . . . 109
Pololu Simple Motor ontroller G2 User’s Guide © 2001–2019 Pololu orporation
Page 2 of 143

8.1. Example code to run smcg2cmd in . . . . . . . . . . . . . . . . . . . . . . . . . . 109
8.2. Example code to run smcg2cmd in Python . . . . . . . . . . . . . . . . . . . . . . . . 110
8.3. Example native USB code in #, Visual ++, and VB .NET . . . . . . . . . . . . . . . 111
8.4. Example serial code for Arduino . . . . . . . . . . . . . . . . . . . . . . . . . . . . . . 111
8.5. Example serial code for Orangutan . . . . . . . . . . . . . . . . . . . . . . . . . . . . 117
8.6. Example serial code for Linux and macOS in . . . . . . . . . . . . . . . . . . . . . 123
8.7. Example serial code for Windows in . . . . . . . . . . . . . . . . . . . . . . . . . 128
8.8. Example serial code in Python . . . . . . . . . . . . . . . . . . . . . . . . . . . . . 132
8.9. Example serial code for Linux or macOS in Bash . . . . . . . . . . . . . . . . . . . . 134
8.10. Example I² code for Arduino . . . . . . . . . . . . . . . . . . . . . . . . . . . . . 135
8.11. Example I² code for Linux in . . . . . . . . . . . . . . . . . . . . . . . . . . . . 137
8.12. Example I² code for Linux in Python . . . . . . . . . . . . . . . . . . . . . . . . . 140
8.13. Example R computation in . . . . . . . . . . . . . . . . . . . . . . . . . . . . 142
Pololu Simple Motor ontroller G2 User’s Guide © 2001–2019 Pololu orporation
Page 3 of 143

ide-by-side comparison of the different
G2 imple Motor Controllers.
1. Overview
The second-generation G2 Simple Motor ontrollers are
versatile, general-purpose motor controllers for brushed,
D motors. Wide operating voltage ranges and the ability
to deliver up to several hundred Watts in a small form
factor make these controllers suitable for many motor
control applications. With a variety of supported
interfaces—USB for direct connection to a computer, TTL
serial and I² for use with embedded systems, R hobby
servo pulses for use as an R -controlled electronic
speed control (ES ), and analog voltages for use with a potentiometer or analog joystick—and a wide
array of configurable settings, these motor controllers make it easy to add basic control of brushed D
motors to a variety of projects. A free configuration utility for Windows simplifies initial setup of the
device and allows for in-system testing and monitoring of the controller via USB.
The table below lists the members of the Simple Motor ontroller G2 family and shows the key
differences among them:
18v15 24v12 18v25 24v19
Minimum
operating voltage: 6.5 V 6.5 V 6.5 V 6.5 V
Recommended max
operating voltage: 24 V(1) 34 V(2) 24 V(1) 34 V(2)
Max nominal
battery voltage: 18 V 28 V 18 V 28 V
Max continuous current
(no additional cooling): 15 A 12 A 25 A 19 A
Dimensions: 2.1″ × 1.1″ 1.7″ × 1.2″
Available with
connectors installed? Yes Yes No No
130 V absolute max.
240 V absolute max.
Pololu Simple Motor ontroller G2 User’s Guide © 2001–2019 Pololu orporation
1. Overview Page 4 of 143

High-Power imple Motor Controller G2 18v25 or 24v19 simplified
connection diagram.
Key features
• Simple bidirectional control of one D brush motor.
• Five communication or control options:
1. USB interface for direct connection to a P .
2. Logic-level (TTL) serial interface for use with a microcontroller.
3. I² interface for use with a microcontroller.
4. Hobby radio control (R ) pulse width interface for direct connection to an R
receiver or RC servo controller [https://www.pololu.com/category/12/rc-servo-controllers].
5. 0 V to 3.3 V analog voltage interface for direct connection to potentiometers and
analog joysticks.
• Simple configuration and calibration over USB with a free configuration program for Windows
• Reverse-voltage protection
• Hardware current limiting with a configurable threshold
• urrent sensing
Note: AUSB A to Micro-B cable [https://www.pololu.com/product/2073] (not included) is
required to connect this controller to a computer.
Additional features
• Adjustable maximum acceleration and deceleration to limit electrical and mechanical stress
Pololu Simple Motor ontroller G2 User’s Guide © 2001–2019 Pololu orporation
1. Overview Page 5 of 143

on the system.
• Adjustable starting speed and maximum speed.
• Option to brake or coast when speed is zero.
• Optional safety controls to avoid unexpectedly powering the motor.
• Input calibration (learning) and adjustable scaling degree for analog and R signals.
• Under-voltage shutoff with hysteresis for use with batteries vulnerable to over-discharging
(e.g. LiPo cells).
• Adjustable over-temperature threshold and response.
• Adjustable PWM frequency from 1.13 kHz to 22.5 kHz (maximum frequency is ultrasonic,
eliminating switching-induced audible motor shaft vibration).
• Error LED linked to a digital ERR output, and connecting the error outputs of multiple
controllers together optionally causes all connected controllers to shut down when any one
of them experiences an error.
• Field-upgradeable firmware.
•Features of the serial, I²C, and USB interfaces:
◦ Optional R error detection to eliminate communication errors caused by noise or
software faults.
◦ Optional command timeout (shut off motors if communication ceases).
•Serial features:
◦ ontrollable from a computer via serial commands sent to the device’s USB virtual
serial ( OM) port, or via TTL serial through the device’s RX/TX pins.
◦ TTL serial uses 0 V and 3.3 V on TX, accepts 0 V to 5 V on RX.
◦ Supports automatic baud rate detection from 1200 bps to 500 kbps, or can be
configured to run at a fixed baud rate.
Pololu Simple Motor ontroller G2 User’s Guide © 2001–2019 Pololu orporation
1. Overview Page 6 of 143

◦ Supports standard compact and Pololu protocols as well as the Scott Edwards
Mini SS protocol and an AS II protocol for simple serial control from a terminal
program.
◦ Optional serial response delay for communicating with half-duplex controllers such
as the Basic Stamp.
◦ ontrollers can be easily chained together and to other Pololu serial motor and
servo controllers to control hundreds of motors using a single serial line.
•I²C features:
◦ ompatible with I² bus voltage levels from 1.8 V to 5 V.
•USB features:
◦ Full-speed USB interface (12 Mbps)
◦ Example code in #, Visual Basic .NET, and Visual ++ is available in the Pololu
USB Software Development Kit [https://www.pololu.com/docs/0J41]
•RC features:
◦ 1/4 µs pulse measurement resolution.
◦ Works with R pulse frequencies from 10 to 333 Hz.
◦ onfigurable parameters for determining what constitutes an acceptable R signal.
◦ Two R channels allow for single-stick (mixed) motor control, making it easy to use
two simple motor controllers in tandem on an R -controlled differential-drive robot.
◦ R channels can be used in any mode as limit or kill switches (e.g. use an R
receiver to trigger a kill switch on your autonomous robot).
◦ Battery elimination circuit (BE ) jumper can power the R receiver with 5 V or 3.3 V.
•Analog features:
◦ 0.8 mV (12-bit) measurement resolution.
◦ Works with 0 to 3.3 V inputs.
◦ Optional potentiometer/joystick disconnect detection.
◦ Two analog channels allow for single-stick (mixed) motor control, making it easy to
use two simple motor controllers in tandem on a joystick-controlled differential-drive
robot.
◦ Analog channels can be used in any mode as limit or kill switches.
Pololu Simple Motor ontroller G2 User’s Guide © 2001–2019 Pololu orporation
1. Overview Page 7 of 143

Note: This guide only applies to the G2 Simple Motor ontrollers, which have blue circuit
boards. If you have one of the first-generation Simple Motor ontrollers, which have
green circuit boards, you can find their user’s guide here [https://www.pololu.com/docs/0J44].
Warning: Take proper safety precautions when using high-power electronics. Make sure
you know what you are doing when using high voltages or currents! During normal
operation, this product can get hot enough to burn you. Take care when handling this
product or other components connected to it.
1.1. 18v15 and 24v12 included hardware
High-Power imple Motor Controller G2
18v15 with included hardware.
High-Power imple Motor Controller G2
24v12 with included hardware.
High-Power imple Motor Controller G2
18v15 with connectors soldered.
High-Power imple Motor Controller G2
24v12 with connectors soldered.
Pololu Simple Motor ontroller G2 User’s Guide © 2001–2019 Pololu orporation
1. Overview Page 8 of 143

High-Power imple Motor Controller G2 18v15 or 24v12,
bottom view with dimensions.
Pinout diagram of the High-Power imple Motor Controller G2 18v15 or 24v12.
The 18v15 and 24v12 versions are available with connectors included but not soldered in or with the
connectors pre-installed.
The terminal blocks are only rated for 16 A, so for higher-power applications, we recommend soldering
thick wires directly to the board.
These files provide further documentation of the hardware design of the Simple Motor ontroller G2
18v15 and 24v12:
•Dimension diagram [https://www.pololu.com/file/0J1600/pololu-smc-
g2-18v15-or-24v12-dimensions.pdf] (424k pdf)
•3D model [https://www.pololu.com/file/0J1602/pololu-smc-g2-18v15-or-24v12.step] (12MB step)
Pololu Simple Motor ontroller G2 User’s Guide © 2001–2019 Pololu orporation
1. Overview Page 9 of 143

•Drill guide [https://www.pololu.com/file/0J1601/umc08a-drill.dxf] (100k dxf)
1.2. 18v25 and 24v19 included hardware
High-Power imple Motor Controller G2
18v25 with included hardware.
High-Power imple Motor Controller G2
24v19 with included hardware.
High-Power imple Motor Controller G2
18v25 with connectors soldered.
High-Power imple Motor Controller G2
24v19 with connectors soldered.
High-Power imple Motor Controller G2
18v25, bottom view with dimensions.
High-Power imple Motor Controller G2
24v19, bottom view with dimensions.
Pololu Simple Motor ontroller G2 User’s Guide © 2001–2019 Pololu orporation
1. Overview Page 10 of 143

Pinout diagram of the High-Power imple Motor Controller G2 18v25 or 24v19.
The 18v25 and 24v19 versions come with connectors included but not soldered.
The terminal blocks are only rated for 16 A, so for higher-power applications, we recommend soldering
thick wires directly to the board.
High-Power imple Motor Controller G2 18v25 or 24v19
with thick wires soldered.
Pololu Simple Motor ontroller G2 User’s Guide © 2001–2019 Pololu orporation
1. Overview Page 11 of 143

These files provide further documentation of the hardware design of the Simple Motor ontroller G2
18v25 and 24v19:
•Dimension diagram [https://www.pololu.com/file/0J1603/pololu-smc-
g2-18v25-or-24v19-dimensions.pdf] (379k pdf)
•3D model [https://www.pololu.com/file/0J1605/pololu-smc-g2-18v25-or-24v19.step] (12MB step)
•Drill guide [https://www.pololu.com/file/0J1604/umc07a-drill.dxf] (102k dxf)
1.3. Supported operating systems
The Simple Motor ontroller G2 configuration software works on Windows 7, Windows 8, and
Windows 10.
We do not currently provide configuration software for Linux or macOS, but Section 8.6 has some
example code for controlling the Simple Motor ontroller via its USB serial port from Linux or macOS.
1.4. Comparison to the original Simple Motor Controllers
This section lists most of the things you should consider if you have an existing application using the
original Simple Motor ontroller controller (green board) and are considering upgrading to a Simple
Motor ontroller G2 (blue board).
Motor driver changes
The G2 Simple Motor ontrollers have configurable hardware current limiting: when the motor current
exceeds a configurable threshold, the motor driver uses current chopping to actively limit it. The
current limit threshold can be configured ahead of time, and can also be changed dynamically via
serial, I² , or USB. The SM G2 can also measure the current being drawn by the motor.
The G2 Simple Motor ontrollers do not support variable braking. Instead, they can either do full
braking or full coasting when the speed is zero.
Physical connection changes
You need to keep some things in mind when updating the physical connections of an existing
application:
• The Simple Motor ontroller G2 uses a USB Micro-B connector (the original controllers used
Mini-B).
• The through-hole capacitors have been replaced with SMT capacitors.
• The SM G2 18v15 and 24v12 boards have the same size and nearly the same layout as
the original SM 18v15 and 24v12. An S L pin was added.
Pololu Simple Motor ontroller G2 User’s Guide © 2001–2019 Pololu orporation
1. Overview Page 12 of 143

• The SM G2 18v25 and 24v19 are significantly smaller than the original SM 18v25 and
24v23, and the motor/power connections are different. Two S L pins were added, but
otherwise the control I/O pins are the same.
Configuration and software changes
There are several changes to keep in mind when configuring the Simple Motor ontroller G2 or
updating any software that communicates with it:
• The Simple Motor ontroller G2 uses different configuration software from the original Simple
Motor ontrollers.
• We do not currently provide a Linux version of the SM G2 configuration software.
• The Simple Motor ontroller G2 serial protocol is generally a superset of the original serial
protocol, so in many cases, serial interface software running on a microcontroller or computer
(using the controller’s RX and TX lines or its virtual USB serial ports) will not need to be
modified to work with the Simple Motor ontroller G2.
• The Simple Motor ontroller G2 native USB interface uses different product IDs and a
different arrangement of settings in memory. One command was added (Set current limit).
Most of the commands remain unchanged.
• Since the Simple Motor ontroller G2 does not have variable braking, any “Motor brake”
command received via serial or I² that specifies a non-zero brake amount will be interpreted
as a request for full braking. This also applies to the USB “Set speed” command.
New features
• The SM G2 boards have reverse voltage protection.
• The SM G2’s new I² interface provides another option for connecting to a microcontroller.
• The SM G2 can be configured to send R bytes for serial responses without requiring
them on serial commands.
• The SM G2’s native USB interface implements Microsoft OS 2.0 Descriptors, so it will work
on Windows 8.1 or later without needing any drivers. (The USB serial ports will work on
Windows 10 or later without drivers.)
Pololu Simple Motor ontroller G2 User’s Guide © 2001–2019 Pololu orporation
1. Overview Page 13 of 143

2. Contacting Pololu
We would be delighted to hear from you about any of your projects and about your experience with
the G2 Simple Motor ontrollers. You can contact us [https://www.pololu.com/contact] directly or post on
our forum [https://forum.pololu.com/]. Tell us what we did well, what we could improve, what you would
like to see in the future, or anything else you would like to say!
Pololu Simple Motor ontroller G2 User’s Guide © 2001–2019 Pololu orporation
2. ontacting Pololu Page 14 of 143

3. etting started
3.1. Installing Windows drivers and software
To install the drivers for the Simple Motor ontroller G2 on a computer running Microsoft Windows,
follow these steps:
1. Download the Simple Motor Controller 2 Software and Drivers for Windows
[https://www.pololu.com/file/0J1599/smc-g2-1.0.0-windows.zip] (550k zip)
2. Open the ZIP archive and run setup.exe. The installer will guide you through the steps
required to install the Simple Motor ontrol enter G2, the Simple Motor ontroller G2
command-line utility (smcg2cmd), and the Simple Motor ontroller drivers on your computer.
If the installer fails, you might have to extract all the files to a temporary directory, right click
setup.exe, and select “Run as administrator”.
3. During the installation, Windows will ask you if you want to install the drivers. lick “Install” to
proceed.
4. After the installation has completed, plug the Simple Motor ontroller G2 into your computer
via USB. Windows should recognize the controller and load the drivers that you just installed.
5. Open your Start Menu and search for “G2”. Select the “Simple Motor ontrol enter G2”
shortcut (in the Pololu folder) to launch the software.
6. In the upper left corner of the window, where it says “ onnected to:”, make sure that it shows
something like “18v25 #33FF-7006-4D4B-3731-4818-1543”. This indicates the version and
serial number of the controller that the software has connected to. If it says “Not connected”,
see the troubleshooting section below.
The SM G2’s native USB interface implements Microsoft OS 2.0 Descriptors, so it will
work on Windows 8.1 or later without needing any drivers. The USB serial ports will work
on Windows 10 or later without drivers.
The Simple Motor ontroller G2 software consists of two programs:
• The Simple Motor ontrol enter G2 is a graphical user interface (GUI) for configuring the
controller, viewing its status, and controlling it manually. You can find the configuration utility
in your Start Menu by searching for it or looking in the Pololu folder.
• The Simple Motor ontroller G2 ommand-line Utility (smcg2cmd) is a command-line utility
that can do most of what the GUI can do, and more. You can open a ommand Prompt and
type smcg2cmd with no arguments to see a summary of its options.
Pololu Simple Motor ontroller G2 User’s Guide © 2001–2019 Pololu orporation
3. Getting started Page 15 of 143

USB troubleshooting for Windows
If the Simple Motor ontroller G2 software cannot connect to your controller after you plug it into the
computer via USB, the tips here can help you troubleshoot the SM ’s USB connection.
If you are using the Simple Motor ontrol enter G2, try opening the “ onnected to:” drop-down box
to see if there are any entries in the list. If there is an entry, try selecting it to connect to it.
Make sure you have a Simple Motor ontroller G2 (blue board). The G2 software does not work with
the original Simple Motor ontrollers (green boards). If you have one of those products, you should
refer to its user’s guide instead of this user’s guide.
Make sure you are using software that supports the Simple Motor ontroller G2. The original Simple
Motor ontrol enter does not work with the SM G2. The SM G2 controllers have new USB product
IDs. Third-party software for the older controllers might need to be updated, depending on how the
software works. If you are a developer of such software, see Section 1.4.
If you have connected any electronic devices to your Simple Motor ontroller besides the USB cable,
you should disconnect them.
You should look at the LEDs of the Simple Motor ontroller. If the LEDs are off, then the controller
is probably not receiving power from the USB port. If the green LED is flashing very briefly once per
second, then the controller is receiving power from USB, but it is not receiving any data. These issues
can be caused by using a broken USB port, using a broken USB cable, or by using a USB charging
cable that does not have data wires. Using a different USB port and a different USB cable, both of
which are known to work with other devices, is a good thing to try. Also, if you are connecting the
controller to your computer via a USB hub, try connecting it directly.
If the controller’s green LED is on all the time or flashing slowly, but you can’t connect to it in the
software, then there might be something wrong with your computer. A good thing to try is to unplug
the controller from USB, reboot your computer, and then plug it in again.
If that does not help, you should go to your computer’s Device Manager and locate all the entries
for the Simple Motor ontroller. Be sure to look in these categories: “Other devices”, “Ports ( OM &
LPT)”, and “Universal Serial Bus devices”.
If the driver for the Simple Motor ontroller’s native USB interface is working, you should see an entry
in the “Universal Serial Bus devices” category named something like “Pololu High-Power Simple Motor
ontroller G2 18v15” (or the corresponding name if you have a different version).
If the drivers for the Simple Motor ontroller’s USB serial ports are working, you should see an entry in
the “Ports ( OM & LPT)” category named something like “Pololu High-Power Simple Motor ontroller
Pololu Simple Motor ontroller G2 User’s Guide © 2001–2019 Pololu orporation
3. Getting started Page 16 of 143

G2 18v15 ommand Port”. The serial port might be named “USB Serial Device” instead if you are
using Windows 10 or later and you plugged the controller into your computer before installing our
drivers for it. The generic name in the Device Manager will not prevent you from using the port, but
we recommend fixing the name by right-clicking on each “USB Serial Device” entry, selecting “Update
Driver Software…”, and then selecting “Search automatically for updated driver software”. Windows
should find the drivers you already installed, which contain the correct name for the port.
If any of the entries for the Simple Motor ontroller in the Device Manager has a yellow triangle
displayed over its icon, you should double-click on the entry to get information about the error that is
happening.
If you do not see entries for the Simple Motor ontroller in the Device Manager, then you should
open the “View” menu and select “Devices by connection”. Then expand the entries until you find
your computer’s USB controllers, hubs, and devices. See if there are any entries in the USB area that
disappear when you unplug the controller. This might give you important information about what is
going wrong.
Do not attempt to fix driver issues in your Device Manager using the “Add legacy hardware” option.
This is only for older devices that do not support Plug-and-Play, so it will not help. If you already tried
this option, we recommend unplugging the Simple Motor ontroller from USB and then removing any
entries you see for Simple Motor ontroller by right-clicking on them and selecting “Uninstall”. Do not
check the checkbox that says “Delete the driver software for this device”.
Pololu Simple Motor ontroller G2 User’s Guide © 2001–2019 Pololu orporation
3. Getting started Page 17 of 143

Windows 10 Device Manager showing the imple Motor Controller G2.
3.2. Understanding the control center Status tab
After installing the software for the Simple Motor ontroller G2, it is a good idea to run the Simple
Motor ontrol enter G2 software and look at the Status tab. The Status tab lets you monitor the
status of your motor controller in real time and control the speed of the motor. The Status tab also
shows what errors and limits are affecting your motor controller so it can help you quickly troubleshoot
any issues you are having.
To use the Status tab, you should connect your Simple Motor ontroller to your P using a USB cable
(not included) and run the Pololu Simple Motor ontrol enter. This is what the Status tab should
look like initially, before you have modified any settings or connected anything to the Simple Motor
ontroller (besides USB):
Pololu Simple Motor ontroller G2 User’s Guide © 2001–2019 Pololu orporation
3. Getting started Page 18 of 143

The tatus tab in the imple Motor Control Center G2 should look like this when you first
connect the controller to the PC.
Target speed and current speed
The Target speed is the speed that the motor controller is trying to achieve. The target speed source
is determined by the settings in the “Input settings” tab, and can come from serial/I² /USB commands,
analog voltages, or R signals.
The Current speed is the speed at which the controller is currently your driving your motor. There are
several reasons why the current speed might be different from the target speed: errors, acceleration
limits, deceleration limits, brake duration, maximum speed limits, starting speed limits, and gradual
temperature-based speed limiting. If any of these things are affecting the current speed, the
appropriate part of the Status tab will be highlighted to let you know. Anything that is stopping the
motor completely will be highlighted in red. Anything that is limiting the speed of the motor will be
highlighted in yellow. While hardware current limiting can affect the power delivered to the motor, it
does not affect this “current speed” reading.
Pololu Simple Motor ontroller G2 User’s Guide © 2001–2019 Pololu orporation
3. Getting started Page 19 of 143

The Simple Motor ontroller represents speeds internally as a number from -3200 (full reverse) to
3200 (full forward). However, by default the speeds in the Status Tab are displayed as percentages so
-3200 (full reverse) is shown as -100.00% and 3200 (full forward) is shown as 100.00%.
Below the Target Speed label is a two-dimensional diagram that represents the values of the inputs
that are used to set the Target Speed. This diagram is especially useful in R or Analog mode with
Mixing enabled because it graphically shows you the value of both input channels and makes it easier
to tell how well the Simple Motor ontroller is calibrated for your controller.
Motor limits
The “Motor limits” box in the Status tab shows the current values of the limits on the movement of the
motor. These limits will be equal to the hard motor limits specified in the “Motor settings” tab, unless
you have temporarily changed the motor limits using the command-line utility (smcg2cmd) or a serial/
I² /USB command. For more information on these limits, see Section 5.2.
Current limit
The “ urrent limit” is displayed below the “Motor limits” box. This is the current value of the hardware
current limit.
Input channels
The “Input channels” box in the Status tab shows the current status of the R and Analog input
channels of the device.
The Raw value is the raw, unscaled value of the input channel. For R channels, the raw value
is the width of pulses received on the input line (R 1 or R 2). It is typically between 1000 µs and
2000 µs, and it is stored internally as an integer in units of quarter-microseconds (6000 corresponds
to 1500 µs). For analog channels, the raw value is the average voltage measured on the input line
(A1 or A2). It is always between 0 mV and 3300 mV, and it is stored internally as a 12-bit integer (0
corresponds to 0 mV while 4095 corresponds to 3300 mV).
The Scaled value is a number between −3200 and 3200 that is determined entirely by the raw value
and the scaling parameters in the “Input settings” tab. If the scaling parameters are set up correctly,
then the scaled value should be 0 when the input is in its neutral position (if it has a neutral position),
and they should be ±100 % (±3200 internally) when the input is moved to either extreme.
The Status column summarizes the state of each channel. Here are the different things you might see
in this column:
•Valid: There is an R or analog input connected to this channel and it is working.
•Invalid (disconnected): This message is shown for analog channels when the controller
Pololu Simple Motor ontroller G2 User’s Guide © 2001–2019 Pololu orporation
3. Getting started Page 20 of 143
Table of contents
Other Pololu Controllers manuals
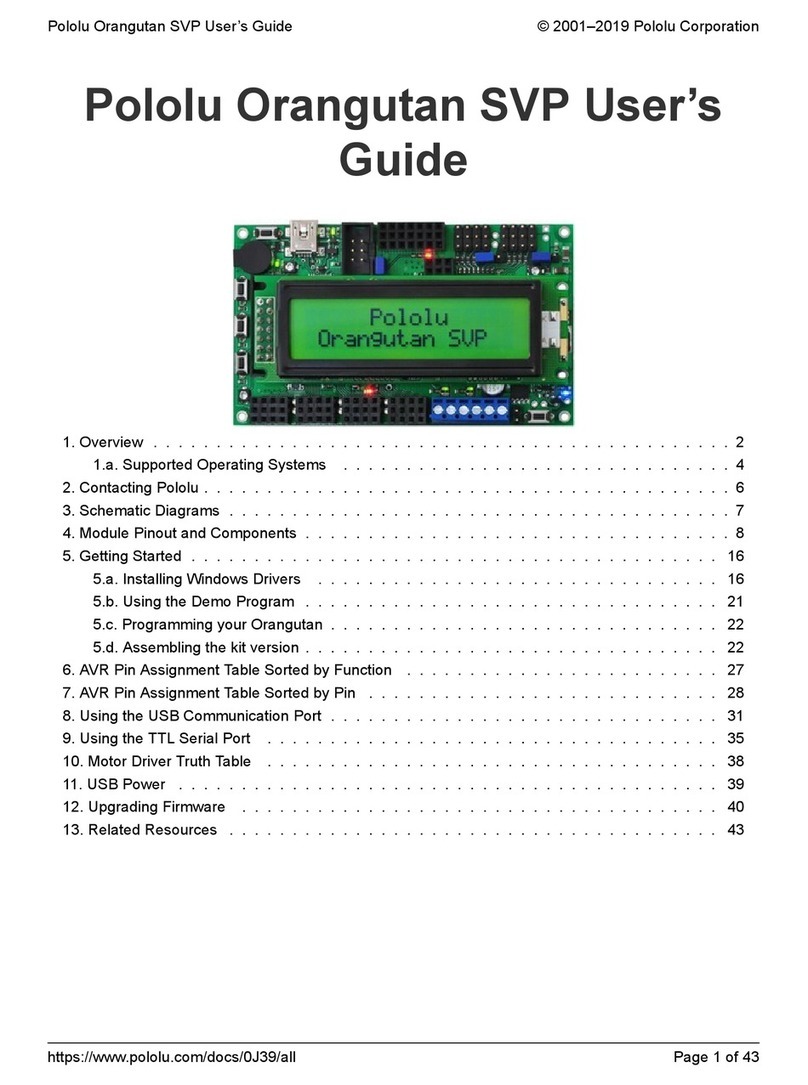
Pololu
Pololu Orangutan SVP-324 User manual
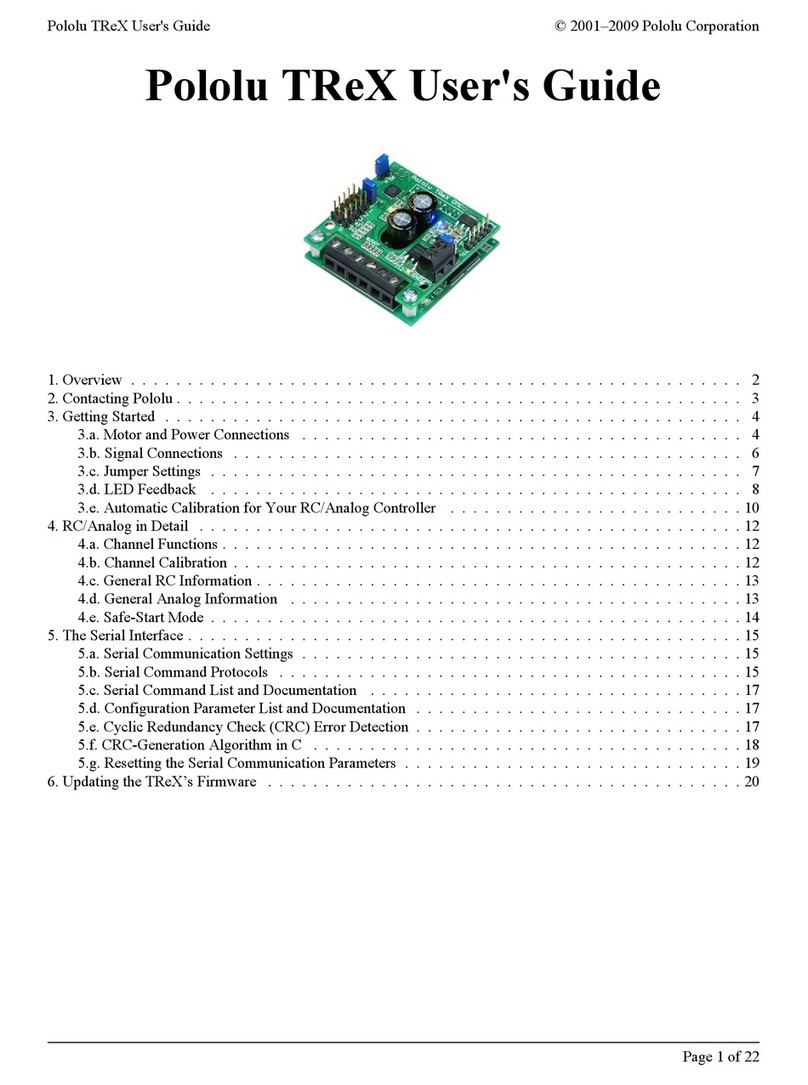
Pololu
Pololu DMC01 User manual
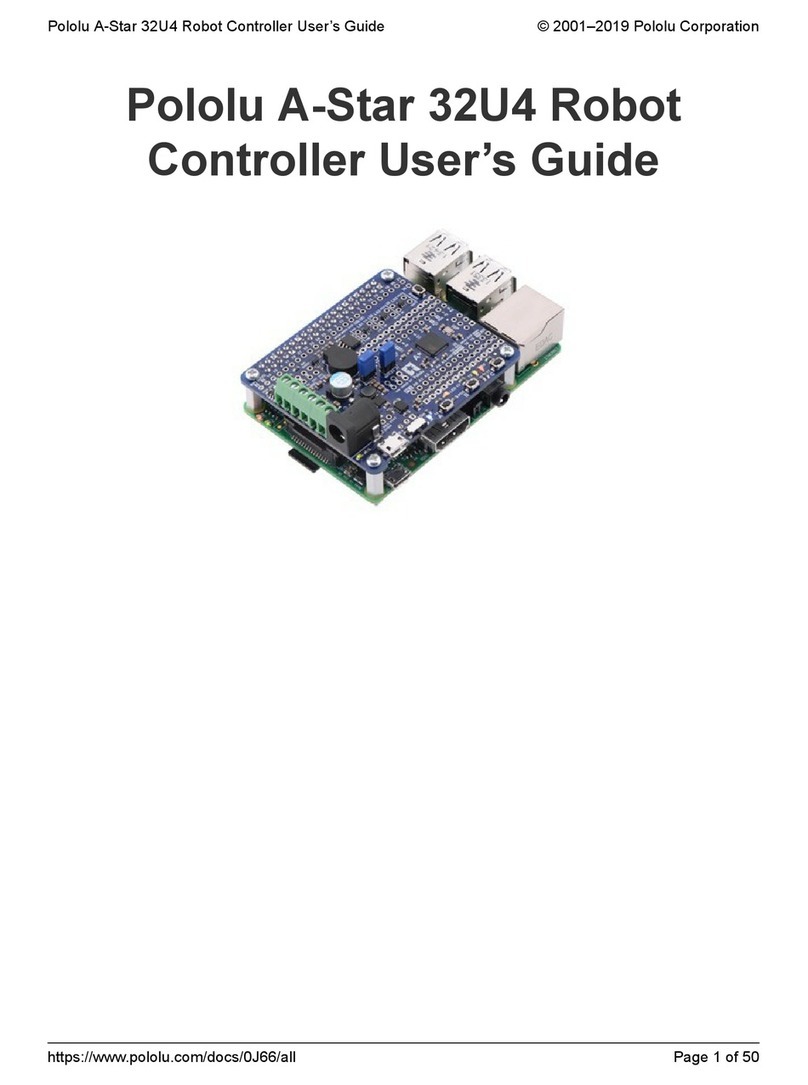
Pololu
Pololu A-Star 32U4 Series User manual
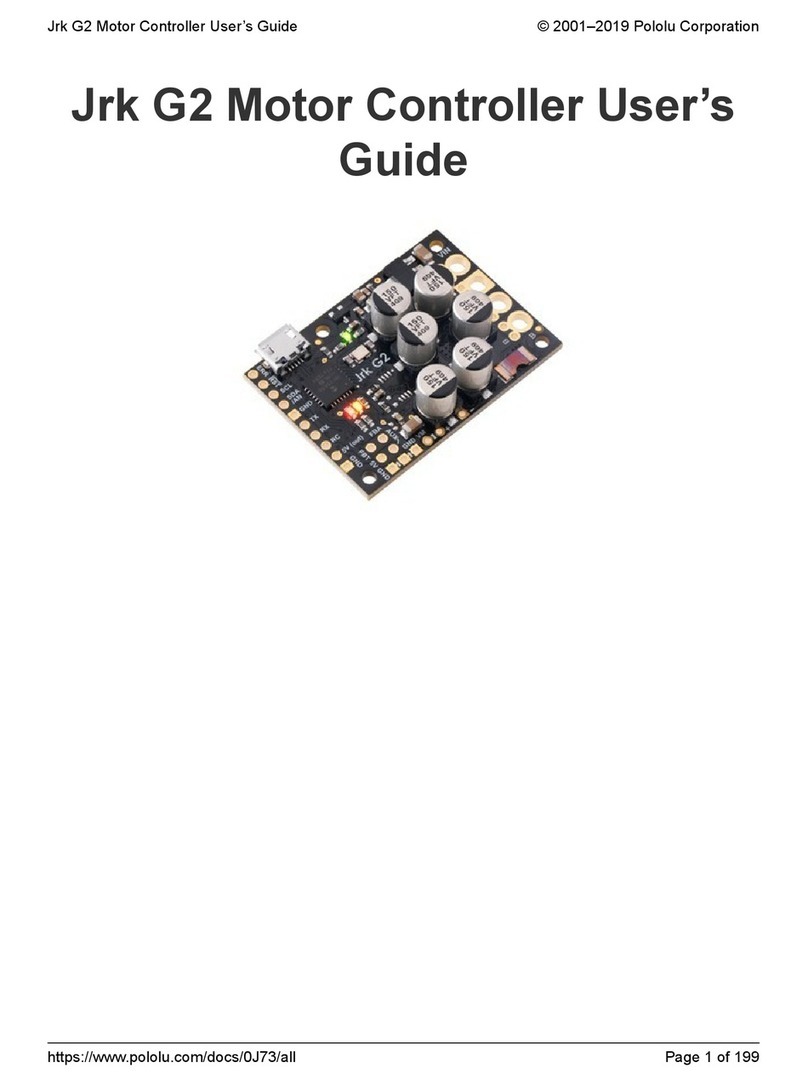
Pololu
Pololu Jrk G2 21v3 User manual
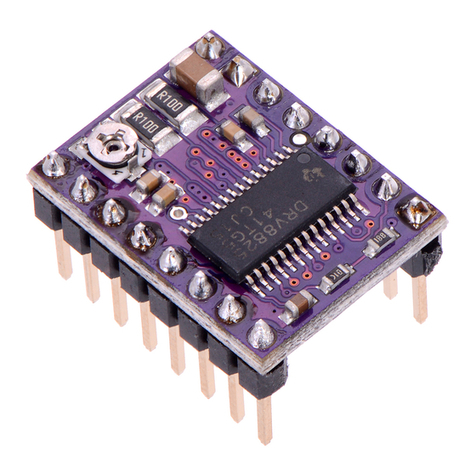
Pololu
Pololu DRV8825 User manual
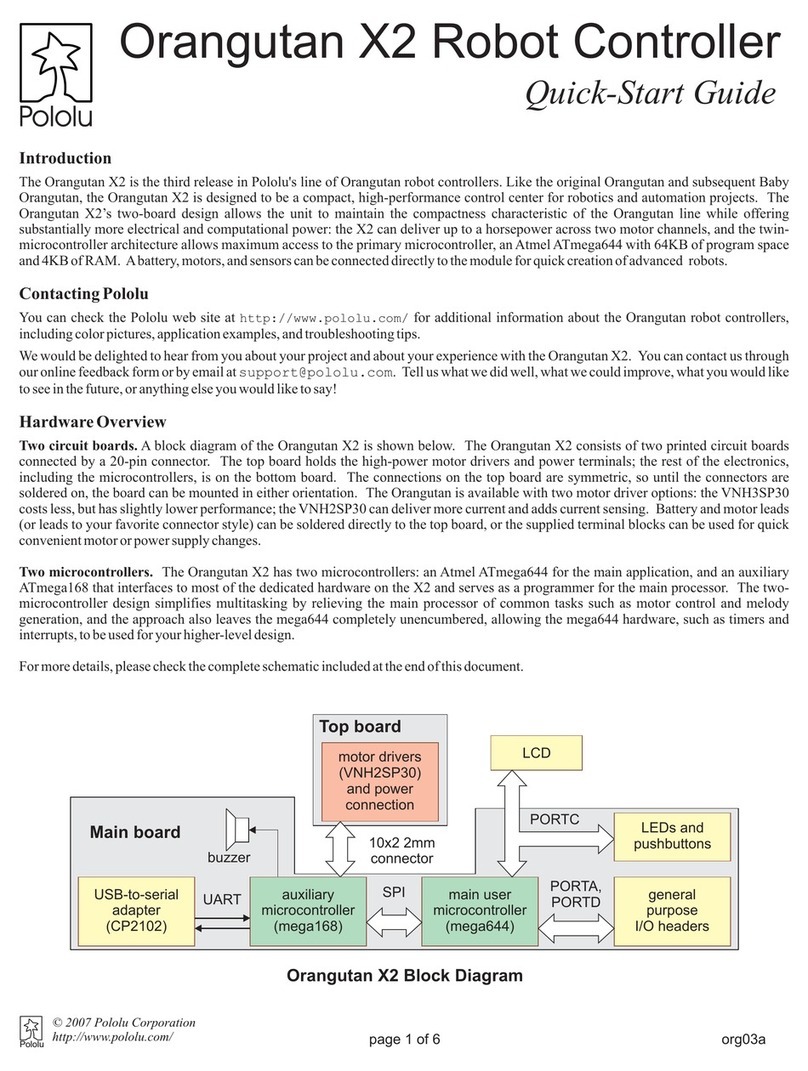
Pololu
Pololu Orangutan X2 User manual
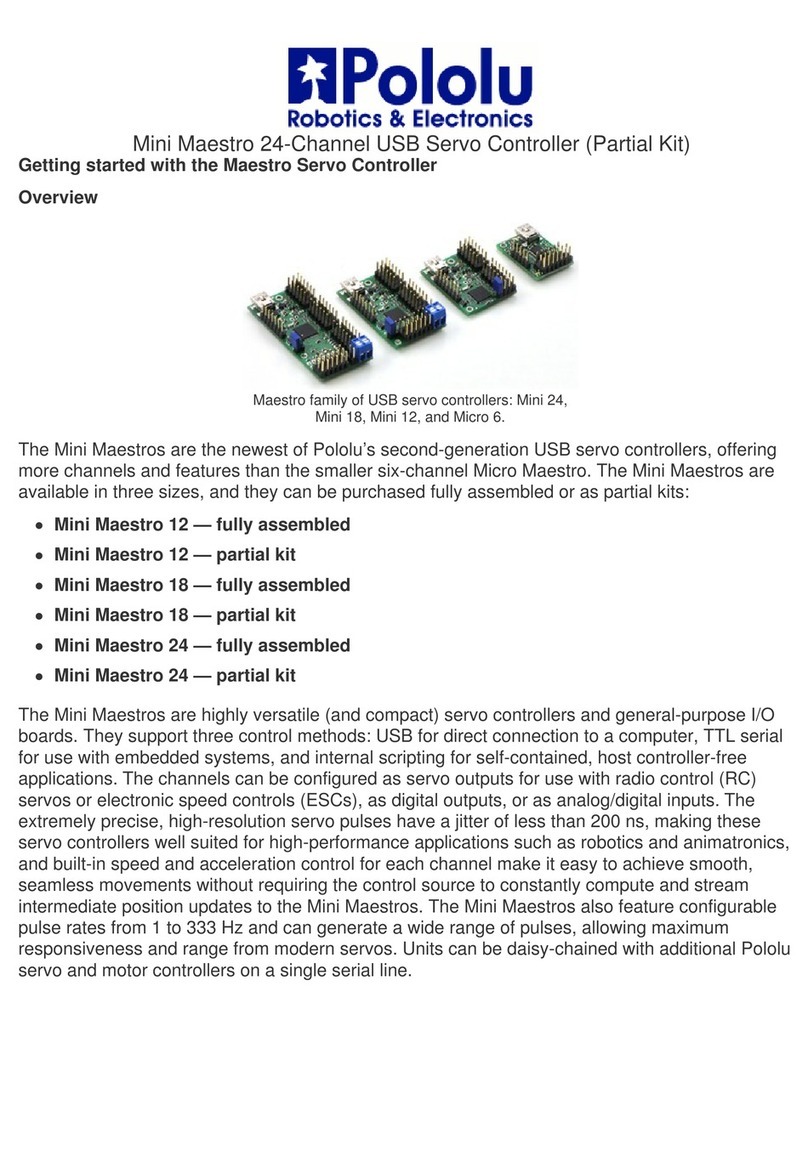
Pololu
Pololu Mini Maestro Series User manual
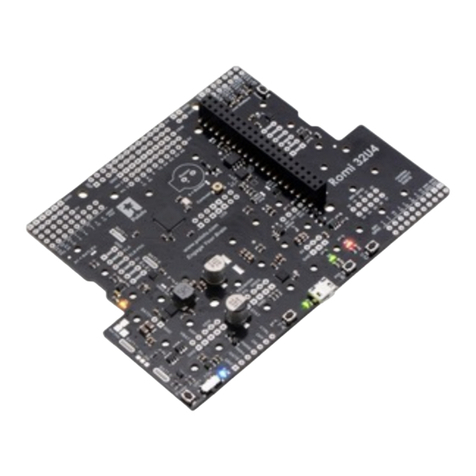
Pololu
Pololu Romi 32U4 User manual
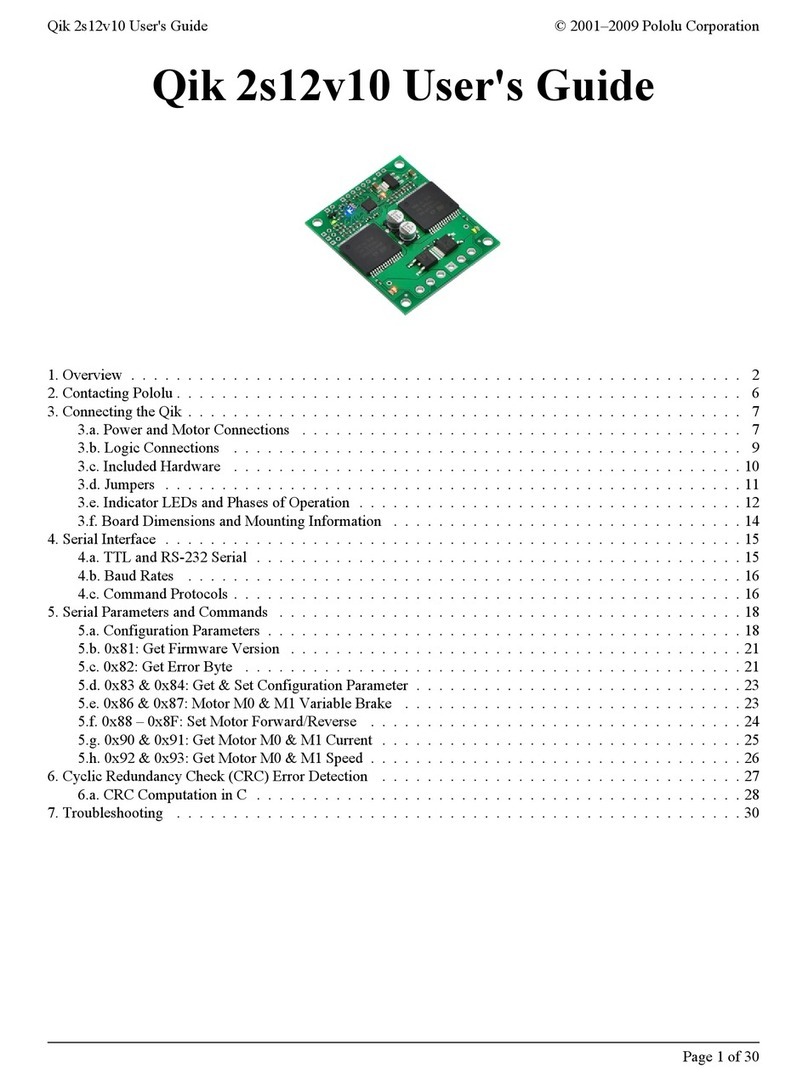
Pololu
Pololu Qik 2s12v10 User manual