PowerBox Systems Core V 2.50 User manual

1
www.powerbox-systems.com
Manual
04/2021
V 2.5o

2PowerBox-Systems − World Leaders in RC Power Supply Systems
Dear PowerBox-Pilot,
Many thanks for placing your trust in us, and purchasing our
PowerBox CORE. You have chosen an extremely unusual
radio control system: the CORE has great presence and
allure, which you cannot fail to appreciate when you pick up
the transmitter for the first time. The CORE fits perfectly in
your hands, and is the perfect tool for controlling your valuable
models with precision.
30 months have passed between the initial idea and the start
of series production: in this time, we have developed everyt-
hing from the ground up: electronics, mechanical systems,
choice of components and suppliers, external appearance,
technical design, mold construction, software architecture,
basic operating philosophy and endless details.
Development started late, and the system had to be comple-
tely re-designed, but over time we realized that this offered
one great advantage: compatibility with old systems develo-
ped in the past did not have to be considered in any way. This
is a very important benefit, since there have been significant
technical advances in the field of 2.4 GHz systems since the
start of the current era.
A single example will suffice to underline this advantage: the
highly developed radio link, offering a range of more than 9
km. This is unique, and provides unrivalled system reserves.
Further advances are evident in our new bi-directional P²BUS
which operates as the telemetry interface, and is capable of
transferring data at unprecedented speed. The most im-
portant advance as far as the pilot is concerned is the user
interface, which is controlled using the transmitter’s integral
touch-screen: the entire menu system is accessed from here,
and the self-explanatory menus are completely logical in their
structure. The internal high-performance Linux computer provi-
des unlimited future expansion potential.
We are confident that we can guarantee our customers dura-
bility and quality at the very highest level, because we exclusi-
vely use components of the highest possible industrial quality,
produced by top manufacturers.
The entire production process – starting with circuit board
assembly and extending right through to final assembly in
our own premises – takes place in Germany. Each CORE is
hand-made, and represents an example of German crafts-
manship at its best! All our staff are united in their shared aim:
perfection!
We wish you many hours of pleasure and countless success-
ful flights with your new PowerBox CORE!

3
www.powerbox-systems.com
Content
1. Connections, controls...........................4
2. First Steps ....................................5
2.1 Switching on ................................5
2.2 Entering the menu............................5
2.3 Main Screen.................................6
2.3.1. Battery indicator ...............................6
2.3.2. Processor Status ..............................6
2.3.3. Flight Mode ...................................6
2.3.4. GPS .........................................6
2.3.5. Wifi ..........................................6
2.3.6. Aerial symbols.................................6
3. Menu.........................................7
3.1 Menu Settings ...............................7
3.1.1. System .......................................7
3.1.2. Screen .......................................8
3.1.3. Audio ........................................9
3.2 Model Menü.................................9
3.3 Function Menu...............................11
3.3.1. Function......................................11
3.3.2. Transmitter Control.............................11
3.3.3. Trim .........................................11
3.3.4. Setup ........................................12
3.3.5. Hold / Failsafe .................................13
3.3.6. Servo ........................................14
3.4 Binding a receiver ............................16
3.4.1. Binding.......................................16
3.4.2. Remove ......................................16
3.4.3. Range check ..................................17
3.4.4. Selecting CORE/M-Link .........................17
3.5 Mixer.......................................17
3.5.1. Flight Mode ...................................18
3.5.2. From/To ......................................18
3.5.3. Transmitter control .............................18
3.5.4. Gain .........................................18
3.5.5. Curve editor...................................18
3.6 Virtual switches..............................19
3.7 Servo Cut-OFF...............................20
3.8 Flightmodes.................................22
3.9 Speech output ...............................24
3.9.1. Source .......................................24
3.9.2. Value.........................................25
3.9.3. Control .......................................26
3.9.4. Replay .......................................26
3.9.5. Test..........................................27
3.10 Vario ......................................27
3.10.1. Sensor ......................................27
3.10.2. Vario ON/OFF ................................28
3.10.3. Start tone....................................28
3.10.4. Climb sensitivity ..............................28
3.10.5. Sink sensitivity ...............................28
3.10.6. Climb offset ..................................28
3.10.7. Sink offset ...................................28
3.11 Doorsequencer .............................28
3.11.1. Single mode..................................29
3.11.2. Loop mode ..................................29
3.12 File Manager ...............................32
3.13 Teacher/Student system......................33
4.Telemetry, Timers, Servo display,
Notes and Quick-Select-Buttons .................35
4.1 Telemetry ...................................36
4.1.1. Size..........................................36
4.1.2. Delete Widget .................................36
4.1.3. Rescan Sensors ..............................36
4.1.4. + Button ......................................36
4.1.5. Sensor .......................................37
4.1.6. Menu ........................................38
4.1.7. Address ......................................38
4.1.8. Value.........................................39
4.1.9. Alarm ........................................40
4.1.10. Erase .......................................41
4.2 Timer ......................................41
4.3 Servo display ................................43
4.4 Quick select menu ...........................43
4.5 Notes ......................................44
4.6 Minimum- and Maximum display ...............44
4.7 Anordnen der Widgets ........................44
5. Update .......................................45
5.1 CORE ......................................45
5.1.1. USB Update...................................45
5.1.2. Wifi Update ...................................46
5.2 Receiver ....................................46
6. Wifi ..........................................47
7. Charging the transmitter ........................48
8. Connections...................................49
9. Mechanical transmitter adjustments ..............49
10. Calibrating the transmitter controls ..............52
11.Specification ..................................53
12. Set contents..................................53
13. Core accessories..............................54
14. Service note ..................................56
15. Guarantee conditions . . . . . . . . . . . . . . . . . . . . . . . . . .56
16. Liability exclusion .............................56
17. FCC.........................................56
18. IC...........................................57
19. RF exposure statement (Portable Device) .........57

4PowerBox-Systems − World Leaders in RC Power Supply Systems
8 Toggle switches
Quick-select buttons
Optional stick switch
Loudspeaker
4 digital trims
4 proportional
controls
On / Off switch
4 push-buttons
Light sensor
1. Connections, controls
Quick-select buttons
Userdefined
menu
Screen
unock
Servo
monitor
Home
screen
History
back
History
forward

5
www.powerbox-systems.com
2. First Steps
2.1 Switching on
The CORE is switched on by holding the -Tbutton pressed in until it lights up red. Release the button briefly, then confirm the
power-on process by briefly pressing the button a second time. The transmitter is switched off in exactly the same way. The
button changes to green when the Linux system has booted; this process takes about 25 seconds. Once the CORE is running,
you will see the Home display on the screen: this shows fields containing telemetry values, timers, servo positions or quick-select
buttons for menus. These fields are known as widgets.
2.2 Entering the menu
The main menu is accessed by swiping a finger downwards from the top edge. You can now touch the left-hand menu symbol :
There is no need to press firmly, as the capacitive touch-screen simply responds to touch, like all modern smartphones. The sym-
bols in the Main menu are arranged in order of importance.
The CORE is fitted with a fully redundant power supply system, which is deliberately kept separate from the Linux computer
and the other processors. This means than any malfunctions in the complex Linux system cannot possibly result in the trans-
mitter switching itself off. The two real-time processors also function completely independently of the Linux computer. The
model remains fully controllable even if the Linux computer is pulled out when the system is running!
NOTE

6PowerBox-Systems − World Leaders in RC Power Supply Systems
2.3 Main Screen
2.3.1. Battery indicator
The two green battery symbols indicate the state of charge
of the two internal batteries. The charge status is divided up
into five blocks, each of which stands for 20% of charge. The
charge symbols change to orange and then red if the state of
charge falls below 20% and 10% respectively. You can also
set up a telemetry widget to display the exact battery voltage.
Setting up a telemetry widget provides the opportunity to add
an audible or spoken alarm.
2.3.2. Processor Status
This symbol is displayed when the workload on the Linux computer reaches a particular level. The symbol flashes briefly when
data is being processed.
2.3.3. Flight Mode
This field shows the current flight phase (flight mode). The name of the flight phase can be set individually in the Flight Mode
menu.
2.3.4. GPS
This symbol appears when the integral GPS has what is known as a “FIX”. This means that sufficient satellites have been picked
up to receive GPS data.
2.3.5. Wifi
This symbol is cancelled with a red line if WiFi is not active. WiFi is only active when it has been switched on manually, or automa-
tically during the Update process.
2.3.6. Aerial symbols
The aerial symbols illustrate in graphic form the LQI value of the Core’s aerials, i.e., it corresponds to the reception quality of the
return channel.
Hinweis: you can transfer any menu point to your own personal menu. This is accomplished simply by holding your finger on
the appropriate menu for a few seconds. When the “Person symbol” appears, the menu point is transferred into your personal
menu, which you can access conveniently using the quick-select button at the bottom of the screen. If you wish to remove
a menu point again, use the same procedure: keep your finger on the menu symbol in question, and that entry is duly erased.
NOTE

7
www.powerbox-systems.com
3. Menu
3.1 Menu Settings
This menu is used to enter your name, set the time display
format and select your preferred language. At this point you
will also find the Display settings such as background and icon
color, and the Audio menu for setting the various volume levels.
These settings are global for all models.
3.1.1. System
• Pilot name, Date and Time
Enter your name at Pilot ‘s name. You can change the name at any time. It is very important to set the correct Time of day and
Date, as the telemetry data log files cannot be assigned unambiguously without that information. Please be sure to set the date
and time of day. A later update will activate the internal GPS of the CORE, and at that time the clock will set itself automatically.
Functions
- Function overview
- Create or erase
functions
Mixers Flightmodes Virtual switches
www.powerbox-systems.com 7
3. MENÜ
Funktionen
- Funktionenübersicht
- Funktionen anlegen oder löschen
Mischer
Servos
- Servoübersicht
- Servos anlegen oder löschen
Servo Cut-off
Servo Monitor Modell
- Modellübersicht
- Laden, kopieren oder löschen
von Modellen
Flight Modes Empfänger Verwaltung
- Empfängerübersicht
- Empfänger binden oder entfernen
- Reichweitentest
Virtuelle Schalter
Datei Manager
Vario EinstellungenLehrer/Schüler Einstellungen
Sequenzer
Sprachausgabe
Einstellungen
- Systemeinstellungen
- Bildschirm
- Audio
Servos
- Servo overview
- Create or erase
functions
Servo Cut-off
Receiver management
- Receiver overview
- Bind or remove receiver
- Range check
Speech output
Servo Monitor
www.powerbox-systems.com 7
3. MENÜ
Funktionen
- Funktionenübersicht
- Funktionen anlegen oder löschen
Mischer
Servos
- Servoübersicht
- Servos anlegen oder löschen
Servo Cut-off
Servo Monitor Modell
- Modellübersicht
- Laden, kopieren oder löschen
von Modellen
Flight Modes Empfänger Verwaltung
- Empfängerübersicht
- Empfänger binden oder entfernen
- Reichweitentest
Virtuelle Schalter
Datei Manager
Vario EinstellungenLehrer/Schüler Einstellungen
Sequenzer
Sprachausgabe
Einstellungen
- Systemeinstellungen
- Bildschirm
- Audio
Model
- Model overview
- Create, load, copy and
erase models
File manager
www.powerbox-systems.com 7
3. MENÜ
Funktionen
- Funktionenübersicht
- Funktionen anlegen oder löschen
Mischer
Servos
- Servoübersicht
- Servos anlegen oder löschen
Servo Cut-off
Servo Monitor Modell
- Modellübersicht
- Laden, kopieren oder löschen
von Modellen
Flight Modes Empfänger Verwaltung
- Empfängerübersicht
- Empfänger binden oder entfernen
- Reichweitentest
Virtuelle Schalter
Datei Manager
Vario EinstellungenLehrer/Schüler Einstellungen
Sequenzer
Sprachausgabe
Einstellungen
- Systemeinstellungen
- Bildschirm
- Audio
Settings
- System settings
- Screen
- Audio
Teacher / Student Vario Sequencer

8PowerBox-Systems − World Leaders in RC Power Supply Systems
• Language
The Language setting affects the output of speech and telemetry data. When the sensors are scanned, the selected language
is sent to the sensor, which then sends back the telemetry values using the terminology in that language - if implemented.
• Units
It is also important to set your preferred units of measurement: the system sends your choice of Metric or Imperial to the tele-
metry sensors, and the sensors then deliver all telemetry values using your preferred units, such as kilometers / miles or liters /
gallons.
• Software
The Software menu will be discussed later; the transmitter and receivers can be updated at this point.
• Servo/Data
The Servo / Data setting determines whether the 3-pin output under the cover generates a PWM servo signal to act as a servo
tester, or a real-time telemetry output in the P²BUS format. The latter makes the telemetry data from the model accessible at the
transmitter itself for further processing. Typical uses of this would be for recording devices or variometers with expanded functi-
ons used for Triangle competitions.
Since Version 2.35 this socket has acted as S.BUS or SRXL input for the Teacher / Student system. These two protocols can
be generated by the receivers used by virtually all radio control systems. This allows the Core’s Teacher / Student system to be
very flexible in operation, even in conjunction with low-cost Student transmitters made by a variety of manufacturers.
• FastStart
This feature stores the currently loaded model settings in the real-time computer when the transmitter is switched off. Next time
you switch on, you immediately have control of the model. The Linux computer boots in the usual way. Settings and trims are
only available once the Linux computer is running. This feature is extremely practical for competition work, or if you simply want
to extend or retract the undercarriage when rigging or dismantling the model.
• Calibration
Another important point is the Calibration menu; this is described in full at a later stage.
3.1.2. Screen
• Background, Color, Icons, Brightness
You can select your preferred color scheme here. The
brightness control should be set to a value which enables you
to see the screen content clearly and distinctly. Please note
that the screen brightness does have a perceptible effect on
battery duration!
• Dimmer
The Dimmer time setting determines the point at which the
screen is automatically darkened.
• Automatic lock
The automatic screen lock can be released again using the - button.
• Idle Alarm
Enter a time here after which you wish the transmitter to generate an alarm if the sticks have not been moved. The purpose of
this feature is to help you to avoid leaving the transmitter switched on accidentally.

9
www.powerbox-systems.com
• Intro
The Intro Video setting enables you to switch the brief CORE logo sequence on or off when the system is switched on. Disa-
bling it shortens the initial boot time by a few seconds.
3.1.3. Audio
The Audio menu enables you to set different volume levels. In
the right-hand field you can set the volume to a fixed value.
However, you also have the option of assigning a rotary control
or switch for this purpose. The first step is to click on the central
field, which causes a further context window to open where
you can assign a transmitter control. All you have to do here
is move the rotary control or switch which you wish to use for
volume adjustment. When you leave the Context menu in which
you assigned the control, you will see directly in the Audio
menu how the rotary control or switch alters the volume level.
3.2 Model Menü
Select the Model button in the Main menu, and you will see
an overview of all models stored in the transmitter. You can also
set up, rename or erase models and model folders.
A At this point you can also store pictures (215 x 100 pixels,
*.jpg or *.png) for your model, and reset the model operating
time. The Export function makes it swift and simple to export a
model file onto a USB memory stick.
To create a new model, briefly touch the +button at the bottom
of the screen. Assign a name to your model, and confirm your
choice with OK. You will now see the Select screen for the
model type. At this point you can select the appropriate model
type, with the additional options of delta wing and V-tail.

10 PowerBox-Systems − World Leaders in RC Power Supply Systems
On the next screen you select one of the ranges on the right-hand side, e.g. Wing. The screen now shows a diagram of a wing
corresponding to your chosen type. If your configuration is more specialized, that presents no problems: at a later stage you can
very easily program individual functions manually.
Briefly press Control, and move the aileron stick to select the Aileron control in the Context menu. Now you select a transmitter
control which is to control the left aileron; this will be the left or right primary stick, depending on the transmitter mode you prefer.
The software of the CORE has no modes – it is only the mechanical settings of the transmitter sticks
which determines the stick mode.
NOTE
If you now leave the Select screen again, you will see that the same transmitter control has also been assigned automatically to
the right aileron. The next step is to select the servo outputs to which you intend to connect the aileron servos; this is accomplis-
hed by pressing +. Note that you can assign up to eight servos to a single function.
If your model is an aerobatic aircraft, you would naturally select two or three servos at this point, if you have multiple servos me-
chanically connected to a single control surface. At a later stage you will be able to set the travel, direction of rotation and center
position for each servo separately. If these parameters are too coarse for your application, you can set an individual curve with up
to 17 points for each servo.
Back in the Assignment screen it is also possible to rename the functions to suit your own preference.
If you decide to assign the wing flaps at this point, you will learn to appreciate one of the truly unique features of the CORE. As
with the ailerons, you again assign a transmitter control to the flaps. If each flap is operated by a separate servo, you won’t notice
anything unusual: you simply assign the flaps to your preferred servo outputs. However, if you also want the ailerons to double as
flaps, or want the ailerons to be mixed in to the flaps, you also assign the aileron outputs to the flap function. These functions are
now superimposed, i.e. the mixing is accomplished simply by assigning the servos. At a later stage you can adjust the servos
individually, both for the Aileron function and the Flap function. Servo travel, center and direction can be set separately for both
functions!
An even clearer example of this exceptional feature relates to models with a delta wing. If you select a delta using the Assistant,
the correct functions are assigned automatically. To clarify this, the manual method would be as follows:
As an example, servos 1 and 5 are assigned to Aileron. Servos 1 and 5 are also assigned to Elevator. Since the servos are
installed in a mirror-image arrangement, it is logical that the servos always operate as ailerons, regardless of whether the pilot
moves the elevator stick or the aileron stick. Now we switch to the Elevator function and reverse the direction of rotation of one
servo. The elevator function now works correctly, but the “reversed” elevator function has no effect on the servo direction when an
aileron command is applied, i.e. the ailerons still work correctly. That’s all there is to setting up a “delta mixer”.

11
www.powerbox-systems.com
Back to our Wing screen: when all the assignments are complete, press the - button, amongst the quick-select buttons at
the bottom in order to return to the overview. You can now continue assigning transmitter controls and servos to all the remaining
functions. When everything is finished, touch Continue at bottom right. The functions and servo assignments are complete.
3.3 Function Menu
You now arrive at the most important screen display: The
Function Overview. In principle, the set-up of the whole model
is carried out from this starting point. The display is arranged
logically from left to right:
Function > Control > Trim > Setup > Failsafe > Servo(s)
The individual points in detail:
3.3.1. Function
Each function always contains a transmitter control, the associated trim, the settings for the transmitter control – such as Expo
and Travel, Failsafe or Hold – and the assigned servos. Each function can also be renamed just as you wish at this screen: simply
touch the Function name.
3.3.2. Transmitter Control
At this point you can assign a transmitter control or a fixed value
to the function. A transmitter control may be a primary stick,
a proportional control, a switch or a push-button. Select the
control by moving it.
3.3.3. Trim
• Flightmode
Here you can select whether the effect of any trim adjustment
is to be Global – i.e. the trim value should be the same in all
flight modes – or Single – i.e. the trim value should be variable
separately in each flight mode. The method of using flight
modes is discussed later.
• Trim control
It is necessary to assign a trim control as the first step here.
This can be one of the four trims located adjacent to the pri-
mary sticks, or two of the four rubberized push-buttons. If you
select the push-buttons, the buttons always work together left
and right as the trim.

12 PowerBox-Systems − World Leaders in RC Power Supply Systems
• Trim Mode
You can choose any of four different trim modes. The stan-
dard one is Offset mode: In this mode a trim adjustment
affects the entire range of stick travel, i.e. including the
end-points. Alternative trim modes are Left and Right;
typically, these are intended for idle adjustment in the case of
engines and turbines. In the Center trim mode any adjustment
only affects the center range, i.e. the end-points remain
unchanged.
• Trim range
At this point you can limit the permissible trim range. The
percentage value
• Steps
Here you can set the number of trim steps or increments; not the size of the step.
• Direction
Here you can set the direction of the trim control; for example, you may need this function in connection with the trim buttons.
• Signal
At this point you can set whether the trims are to generate an audio signal when they are adjusted, or when they pass through
the center point. A vibration signal is also available.
3.3.4. Setup
At this point you can adjust the transmitter control input, Expo, transit time and curves.
• Flightmode
If you want the adjustments you make to affect all flight modes, set this menu point to Global. If you set this point to Single,
you can carry out individual adjustments for each flight mode separately. This tool is extremely powerful, but if you wish to make
use of it, you must first create flight modes – more on this later. Once you have set up the flight modes, all you need to do is ac-
tivate them, then enter your preferred adjustments for the transmitter control concerned. The transmitter control settings (travel,
curve, etc.) which you enter for, say, the “Landing” flight mode, will then have no effect in the “Thermal” flight mode.
If you change the Min. / Max. values but leave the number of steps the same, the step size changes accordingly.
NOTE

13
www.powerbox-systems.com
• Transmitter control rate
Here you can select a transmitter control which switches the rate on and off, or sets it to linear. The transmitter control can be
any of the primary sticks, proportional controls or switches.
• Rate
The purpose of the Rate button is to adjust the travel of the transmitter control. If you select nothing for Transmitter control
rate, the value is fixed. If you assign a transmitter control to Transmitter control rate, you can set different values on three
levels. The level initially selected with the transmitter control you have selected is shown in green. If you select a proportional
control as transmitter control, the values are applied in a linear fashion within the three levels.
• Transmitter control expo
At this point you can select a transmitter control which is used to switch an Expo characteristic, or set it to linear. You can choo-
se any transmitter control from the primary sticks, proportional controls or switches.
• Expo
The purpose of the Expo button is to adjust the exponential factor. If you select nothing for Transmitter control expo, the
value is fixed. If you assign a transmitter control to Transmitter control expo, you can use it to set different values on three
levels. The level initially selected using the transmitter control you have selected is shown in green. If you select a proportional
control as transmitter control, the values are applied in a linear fashion within the three levels.
• Curve editor
The curve editor is used to set up special curves, for exam-
ple, to program throttle curves.
- The first step is to select the number of points: up to 17 can
be specified.
- Use the arrow buttons to select the point which you wish to
move; the selected point changes color to green.
- Adjust the percentage value to shift the point up or down.
- The Smooth option can be used to even out the curve, and
thereby avoid jerks in the servo’s response.
- Raw removes the effect of the curve smoothing.
- Reset curve resets the curve to linear travel.
• Transit time
At this point you can set two transit times: one determines the servo transit time to the left, the other to the right. The time in
seconds determines how long the servo takes to move from one end-point to the other.
3.3.5. Hold / Failsafe
If you want a servo to take up a pre-determined position in case
of radio signal loss, you should select Failsafe here. The Learn
button now appears, enabling you to store the current position
in the receiver.
The receiver or receivers do not need to be bound at this
point. The Failsafe positions are repeatedly transmitted to
the receivers at regular intervals.
NOTE

14 PowerBox-Systems − World Leaders in RC Power Supply Systems
3.3.6. Servo
Here you will find the assigned servos again. Up to eight servos
can be assigned to each function. As already mentioned in
the Assistant, the travel and end-points of each servo can be
adjusted separately here. Any adjustments you make to a servo
at this point have no influence on the settings of the same servo
if it is also assigned to another function. This provides a simple
means of mixing in aircraft with multi-flap wings, delta wings and
V-tails.
If you wish to adjust a servo’s travel or center position, the first
step is to touch the appropriate button; you can now adjust
the value. As soon as you move the associated stick, the Select button shifts to the corresponding position. This means that you
do not need to select Left, Right and Center when adjusting the control surface; instead you select each point very conveniently
using the transmitter stick, altering the position of the control surface using the arrow buttons at the bottom of the screen. At the
same time, you can observe the effect of any change directly on the servo.
• Servo number
Indicates the receiver output at which this servo signal is present.
• Servo name
The servo name can be changed individually. Hold your finger on it to open up the keypad.
• Limit
Works like a mechanical stop – the servo does not move beyond the set point.
• Way
Adjusts the servo travel.
• Center
Offsets the servo center position. Acts like a “mechanical” center offset – it also affects the end-points.
• Direction
Reverses the direction of rotation of the servo.
• Curve editor
The travel of each servo can be adjusted using a 9-point curve to match the mechanical installation even more accurately. The
most common use for this function is to match servos to each other where they are mechanically linked (servo matching). At
top right you will see the name of the servo whose curve you wish to adjust, and the function which the servo controls. If you
alter the servo curve in the selected function, the change will have no effect on the travel which you have set for the same servo
in other functions.
- Center
The Center button is used to set a center offset which affects the whole of the servo’s travel. You will see the effect of
the change immediately in the graph on the left-hand side.
- Curve Editor
Press Edit. when you wish to adjust servo travel using a maximum of 17 points.

15
www.powerbox-systems.com
This is the procedure: use the arrow buttons to select the point
you wish to adjust. Briefly press the displayed setting at Value,
then adjust the servo for this position. The Smooth button
can be used to even out the course of the curve. Right at the
bottom you will find a Reset button which sets the curve back
to a straight line. Once you have set the desired curve, return
to the Servo Curve menu, where you will find three Preview
buttons:
- Servo curve
This displays the shape of the pure servo curve.
- Function curve
This displays the shape of the pure function curve. If
you have already set up Expo or Dual Rates, this will
be shown in this view.
- Result
This displays the net result of the function curve and
the servo curve.
3.3.6. Servo
Here you will find the assigned servos again. Up to eight servos
can be assigned to each function. As already mentioned in
the Assistant, the travel and end-points of each servo can be
adjusted separately here. Any adjustments you make to a servo
at this point have no influence on the settings of the same servo
if it is also assigned to another function. This provides a simple
means of mixing in aircraft with multi-flap wings, delta wings and
V-tails.
If you wish to adjust a servo’s travel or center position, the first
step is to touch the appropriate button; you can now adjust
the value. As soon as you move the associated stick, the Select button shifts to the corresponding position. This means that you
do not need to select Left, Right and Center when adjusting the control surface; instead you select each point very conveniently
using the transmitter stick, altering the position of the control surface using the arrow buttons at the bottom of the screen. At the
same time, you can observe the effect of any change directly on the servo.
• Servo number
Indicates the receiver output at which this servo signal is present.
• Servo name
The servo name can be changed individually. Hold your finger on it to open up the keypad.
• Limit
Works like a mechanical stop – the servo does not move beyond the set point.
• Way
Adjusts the servo travel.
• Center
Offsets the servo center position. Acts like a “mechanical” center offset – it also affects the end-points.
• Direction
Reverses the direction of rotation of the servo.
• Curve editor
The travel of each servo can be adjusted using a 9-point curve to match the mechanical installation even more accurately. The
most common use for this function is to match servos to each other where they are mechanically linked (servo matching). At
top right you will see the name of the servo whose curve you wish to adjust, and the function which the servo controls. If you
alter the servo curve in the selected function, the change will have no effect on the travel which you have set for the same servo
in other functions.
- Center
The Center button is used to set a center offset which affects the whole of the servo’s travel. You will see the effect of
the change immediately in the graph on the left-hand side.
- Curve Editor
Press Edit. when you wish to adjust servo travel using a maximum of 17 points.

16 PowerBox-Systems − World Leaders in RC Power Supply Systems
If you wish, you can reset the servo curve once you return to the Servo Overview. If you accidentally find yourself at the Reset
button, that is not a problem: simply select the Curve Editor again, and the curve will still be present there with the settings
you last selected.
NOTE
3.4 Binding a receiver
Select the Receiver button from the Main menu. As you will
now see, up to four receivers can be bound to the CORE
simultaneously.
It is even possible to use different types of receiver; for exam-
ple, one PBR-9D and one PBR-5S can be bound. All four
receivers are of “equal value”, i.e. there is no Master / Slave
assignment, and no restrictions in terms of telemetry. Teleme-
try sensors can be connected to all four receivers, all of which
send data to the CORE on an equal footing.
The receivers are identified by the four capital letters A to D.
The same letters appear in the telemetry data sent from the receivers, helping to differentiate between them.
3.4.1. Binding
There are two methods of binding receivers:
• Option 1
Connect a power supply to the receiver, and it will respond by flashing green at high frequency for ten seconds. Press the Bind
button on your CORE transmitter, and the receiver now binds to it; the LED lights a continuous green.
If you do not press the Bind button within the ten-second period, the LED switches to flashing slowly red – at this point the
receiver can no longer be bound to the transmitter. You can only re-start the process if you first disconnect the power supply.
• Option 2
Press the Bind button on your CORE, then connect the receiver to a power supply. The LED switches to continuous green
once the receiver is bound.
Technical information: during the binding procedure the PowerBox CORE generates a random sequence from a total of more
than 32 million numbers; this is then used as the basis for calculating the hopping sequence and encoding the signals. The
likelihood that two identical codes could be generated is therefore very close to zero.
NOTE
3.4.2. Remove
The Remove button has an important function: if you wish to uninstall a receiver from a model, it is essential to remove that recei-
ver from the model memory beforehand using this button. If you simply uninstall the receiver without first removing it at the trans-
mitter, then the other bound receivers will not work when you next switch the system on. This is an important safety feature, as it
ensures that all the bound receivers are working when you switch the system on, i.e. before you take off!

17
www.powerbox-systems.com
3.4.3. Range check
The Range check function reduces the transmitter’s output power, thereby simulating a large distance between transmitter and
model. This enables you to determine any possible weaknesses in reception in the receivers. In range check mode all the con-
trols should work perfectly at a range of at least 50 m. During the Range Test you can see the values for Link Quality (LQI). This
enables you not only to see whether the radio link is working, but also the quality of the link. This can be helpful in determining the
optimum aerial positions in the model before you fly it.
It is possible to adjust settings such as channel shift, frame
rate, iGyroSAT and others at the receiver itself. These
settings are usually accessed using a Telemetry widget, but
are also available if you press the receiver image in the Bind
menu.
NOTE
3.4.4. Selecting CORE/M-Link
If your transmitter is equipped with a supplementary Multi-
plex M-Link aerial, you will find the button for switching from
the CORE system to the M-Link system right at the top.
The M-Link system offers two binding modes:
• Bind 12K
14ms frame rate, 12 channels
• Bind 16K
21ms frame rate, 16 channels
Choose your setting. If you do not need more than twelve channels, you should always give preference to Option 12K, as the
servos are addressed at a higher rate in this mode. This can be advantageous in respect of smooth running, transit speed and
precision. In contrast, Option 16K offers sixteen channels and a slower frame rate; this is the best choice for use with older
servos.
Your choice applies to the current model, and is stored in the model file together with the relevant Bind information. If you change
the setting for a model which has already been bound, you will need to re-bind the receiver!
3.5 Mixer
Die The free servo mixers represent an additional method of
mixing functions with each other. Servo mixing by servo as-
signment has already been described in the Function menu,
but this option also enables you to mix functions with each
other with a response curve.

18 PowerBox-Systems − World Leaders in RC Power Supply Systems
You can create a new mixer by selecting the Mixer menu and pressing +. You can also immediately rename the Mixer to your own
choice by touching the Mixer button. Press the Setup button on the right in order to program the mixer. The following display
appears:
3.5.1. Flight Mode
As is the case with the transmitter controls and trims, the mixers also include the option of programming mixed functions from one
transmitter control to another separately for each flight mode. If you select the Global setting, the mixer will be identical in all flight
modes, and also if you are not using flight modes. Select Single if you wish the mixer to be effective only in particular flight modes.
3.5.2. From/To
The first step is to select the source function under From, and the target function under To.
3.5.3. Transmitter control
At this point you should select a switch, stick or proportional control. You can then use it to activate the mixer, switch the input to
the three available levels (1-2-3), or set it to linear response. The default entry here is On, which means that a fixed mixer input is
set.
3.5.4. Gain
The Gain button is used to set the magnitude of the mixer. Selecting On at Transmitter control sets a fixed value. If you
assign a switch or proportional control at transmitter control, you can set different values on three levels; the level selected by the
transmitter control is shown in green. If you select a proportional control as transmitter control, the values are applied in a linear
fashion between the three levels.
3.5.5. Curve editor
The curve editor enables you to set up special mixing curves.
• Points
Select the number of points – up to a maximum of 33 points.
• Select Point
Use the arrow buttons to select the point you wish to adjust. The selected point turns green.

19
www.powerbox-systems.com
• Value
Move the point up or down by altering the percentage value.
• Smooth
The Smooth option can be used to even out the curve, thereby causing the servo to move smoothly over its travel.
• Raw
Raw eliminates curve smoothing.
• Reset Curve
Reset curve sets the curve back to linear travel.
3.6 Virtual switches
The virtual switches can be used to digitize linear transmitter controls by setting up a switching threshold to generate a switched
state. It is also possible to set up a logical link between two or more switches or linear controls. This facility can be used as a very
easy method of implementing functions such as safety switches for electric power systems.
Select the Virtual Switch button in the menu, then press +to set up a new virtual switch. You can rename the virtual switch
by pressing the switch button. As you can see, this field includes a small triangle at top right. This means that a function can be
selected here by holding your finger on it. In this case the virtual switch can be erased again by holding your finger on the switch
button.
First select a transmitter control by briefly pressing the blank field (three dashes) under Control; press Control again at the next
screen. You can now select a switch or linear control as transmitter control by operating it..
A further alternative is to define a fixed value - On or Off. This is necessary, for example, if you only wish to assign a switching
threshold to one linear control. In this case select one transmitter control as fixed value, and define a linear control for the other
transmitter control.

20 PowerBox-Systems − World Leaders in RC Power Supply Systems
Yet another option is to use the output of a previously defined logical switch in turn as a transmitter control input.
In this way you can set up a logical link between three or more switches!
In this example a linear rotary control has been selected. In the following section you will see your transmitter control on the left,
and a bar display on the right showing two switching points.
The two switching points can now be placed in any position you like by moving them with your finger. The red area indicates the
“Off state”; the green area the “On state”. The orange area indicates “hysteresis”, i.e. the area in which no switching takes place.
You can very easily reverse the “Off state” and the “On state” by moving one of the two switching point sliders in front of or behind
the other. This adaptability provides maximum flexibility and simplicity, and you can immediately check the effect of your settings
by moving the switch or linear control. The transmitter control symbol on the left changes color to indicate the switched state.
If you wish to use a switch, you can very easily set the desired switch position to ON. If you select a 3-position switch it is also
possible to set two ON positions. Press OK once you have completed your settings.
You are now returned to the virtual switch overview, and you can define the second input using exactly the same procedure as
the first.
Selecting AND or OR logic defines the switching characte-
ristics you wish to use. At far right under Output you will see
the result of the two inputs. The virtual switch is immediately
available in order to control Functions, or switch a Mixer or a
Servo Cut-Off.
3.7 Servo Cut-OFF
This feature provides a very easy means of switching a servo output to a fixed, previously defined value. An example of this might
be a motor arming switch, or a fixed, pre-defined nosewheel position when the undercarriage is retracted. Select the Servo Cut-
Off menu, then press +in order to create a new cut-off function. At this point select the servo which you wish to move to a fixed,
pre-defined position, then press OK.
This manual suits for next models
1
Table of contents
Other PowerBox Systems Receiver manuals
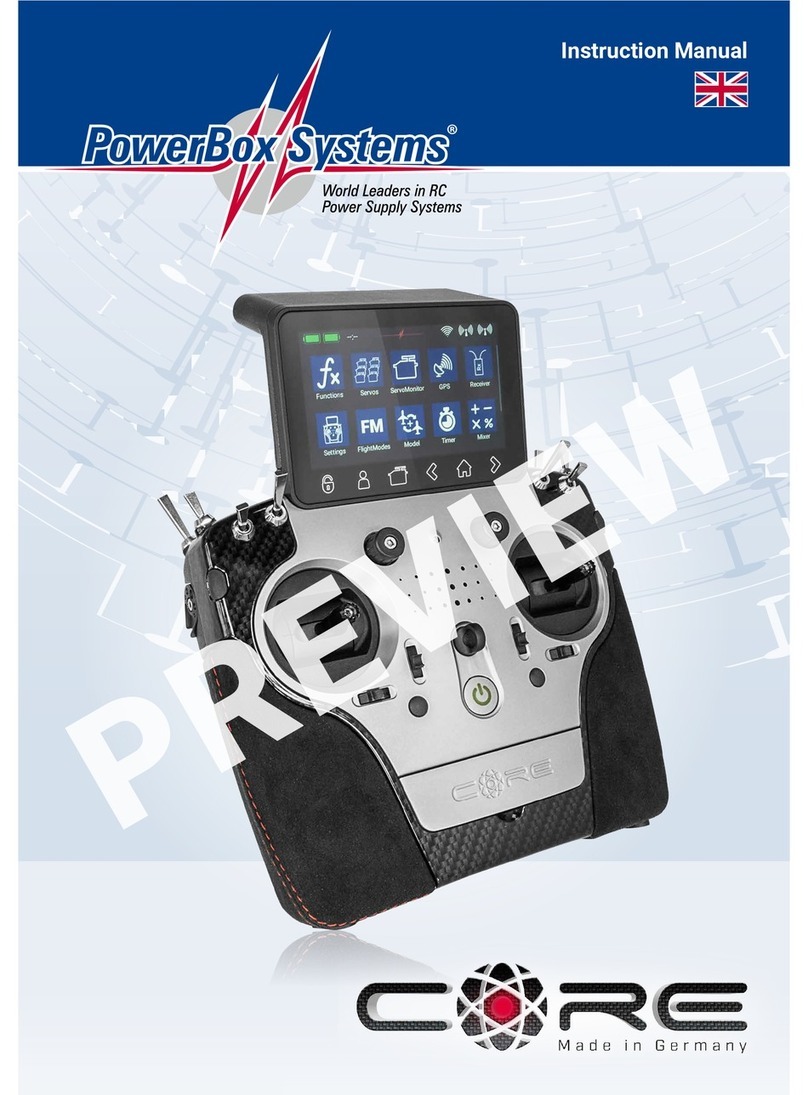
PowerBox Systems
PowerBox Systems CORE User manual
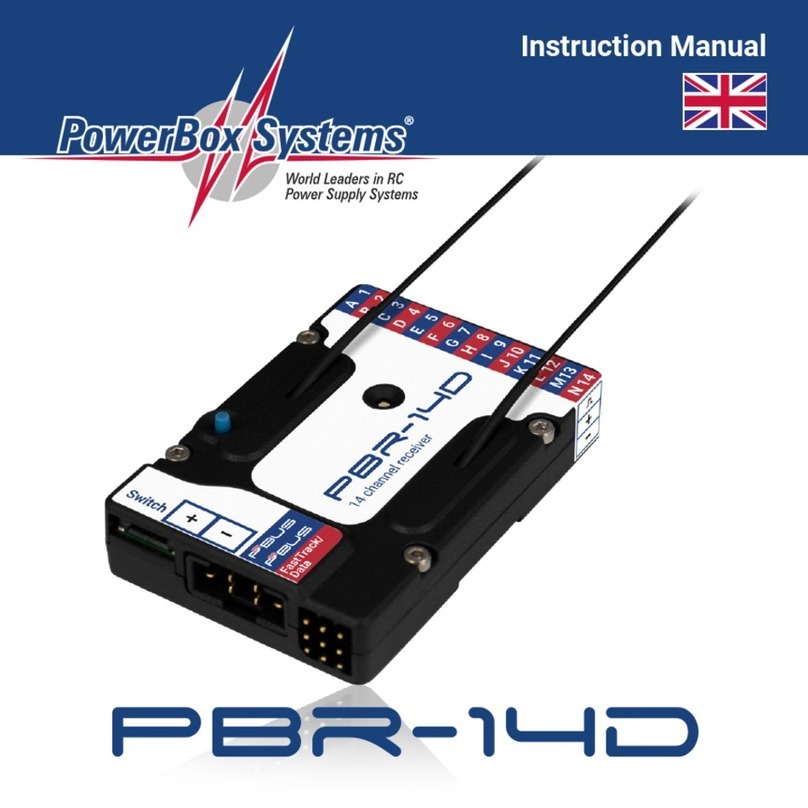
PowerBox Systems
PowerBox Systems PBR-14D User manual
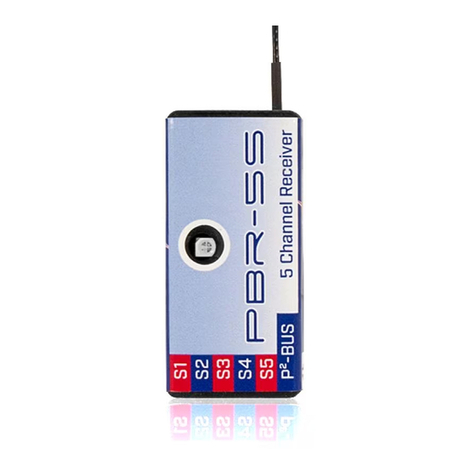
PowerBox Systems
PowerBox Systems PBR-5S User manual
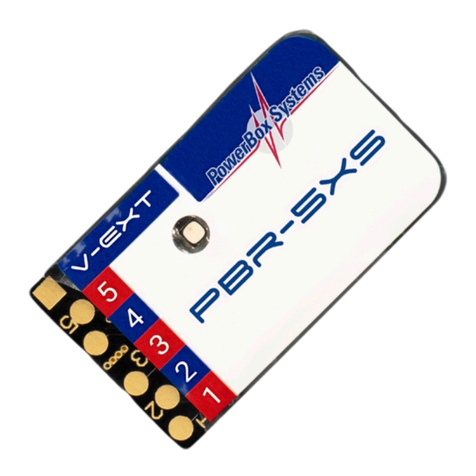
PowerBox Systems
PowerBox Systems PBR-5XS User manual
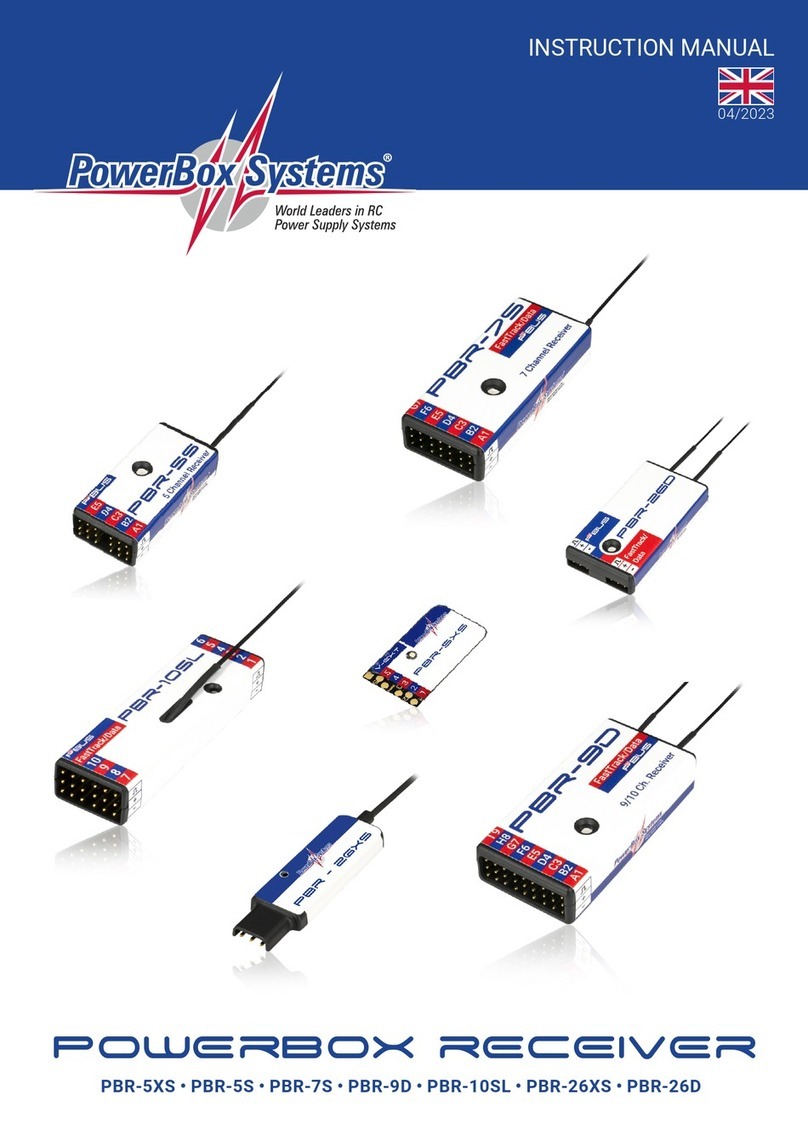
PowerBox Systems
PowerBox Systems PBR-5XS User manual
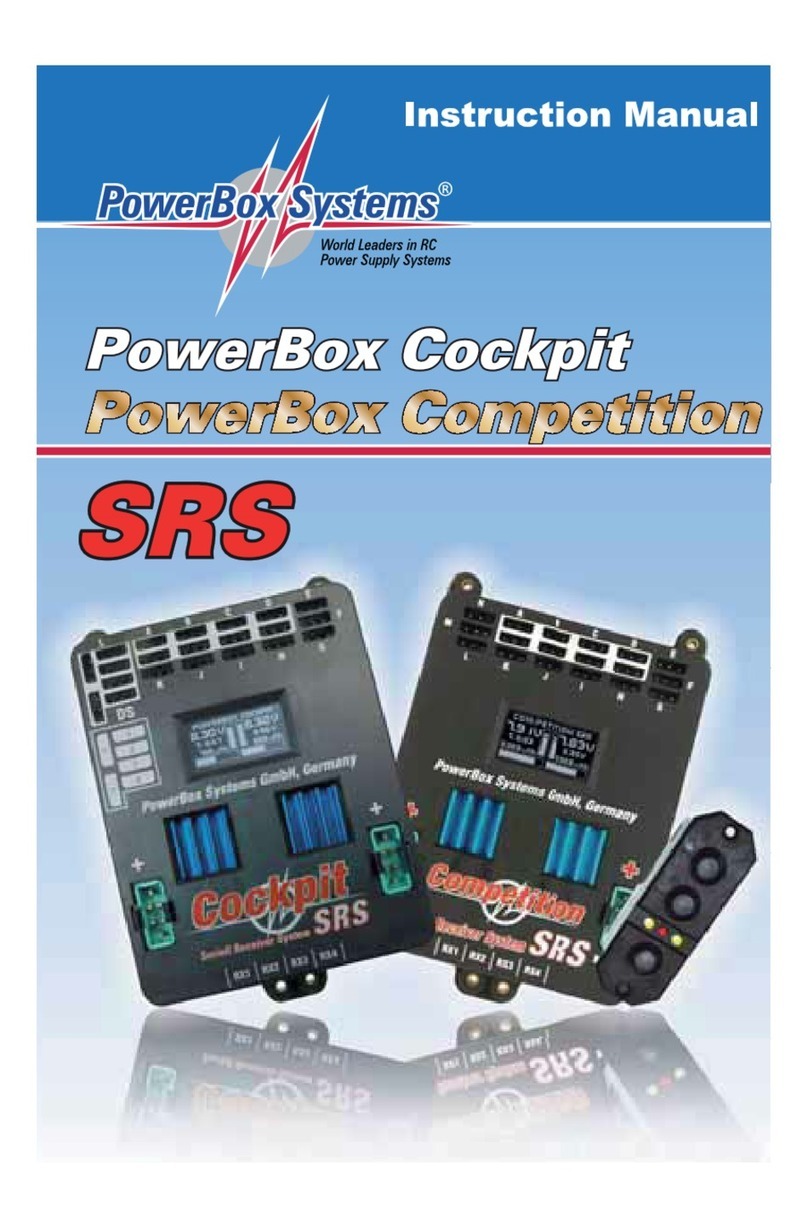
PowerBox Systems
PowerBox Systems PowerBox Cockpit User manual