Prior NanoScan OP400 Programming manual

PLEASE READ THE INSTRUCTIONS BEFORE
ATTEMPTING TOUSE THE NANOSCAN OP400 SYSTEM
IDENTIFYINGYOURSYSTEM COMPONENTS
INSTALLINGYOURSYSTEM
• Save this manual as it contains important safety information and operating instructions.
• Before using the system, please follow and adhere to all warnings, safety and operating instructions located
on the product and in this user manual.
• Do not expose the product to open flames, extreme hot or cold temperatures, water or moisture.
• Do not allow objects to fall on or liquids to spill on the product.
• Connect the AC power cord only to designated power sources as marked on the product.
• Make sure the electrical cord is located so that it will not be subject to damage.
• To reduce the risk of damage, unplug the product from the power source before connecting the components together.
• DANGER - never alter the AC cord or plug. If the plug will not fit into the outlet, have a proper outlet installed
by a qualified electrician.
• Use only the proper type of power supply cord set (provided with the system) for this unit.
• Do not attempt to disassemble the product. Doing so will void the warranty. This product does not contain
consumer serviceable components. Service should be performed by authorized service centers.
NANOSCAN OP400 QUICK START INSTRUCTIONS
The standard NanoScan OP400
system consists of:
(1) - NanoScan OP400
Piezo Objective Scanner
(1) - NPC-D-6110 Controller
(1) - Microscope Thread Adapter
(1) - 1.3mm (0.05 inch) Hex Key
(1) - Objective ens Thread Adapter (optional)
(1) - Objective ens Spacers (optional)
NanoScan OP400 Piezo
Objective Scanner NPC-D-6110 Controller
www.prior.com
Microscope Thread Adapter
STEP 1: Select the position for the
OP400 on the nosepiece.
STEP 2: Insert the microscope thread
adapter.
STEP 3: Connect the OP400 to the
nosepiece. Tighten with the hex key.
STEP 4: Insert the objective lens using the appropriate objective lens adapter. Note no
adapter is necessary for M32. Other objectives can be inserted into the nose piece using
option parfocal spacers.
STEP 5: The OP400 unit is
now properly installed.
Objective Lens Thread Adapter Parfocal Objective Spacer
Please take care with the cabling. Under no circumstances use the cabling to hold the stage.

CONNECTING YOUR SYSTEM - FRONTOFUNIT
www.prior.com
POS MON connector Analogue position
monitor (POS MON) output BNC
connector(s) – single ended output(s).
ANA I/P” connector Analogue
command input BNC connector(s) – single
ended input(s). Signal used to control the
stage position
On/Off switch
Earth Stud - M4 threaded stud
Provides additional product ground to help reduce interference of
background electrical noise. Do not raise above 0V ground potential
Power Connector 4 pin miniDIN with screen Input
+24V dc ±0.75V @ 5A Provides power to the
controller electronics. ON Y connect an approved
power supply.
Provides digital inputs and outputs for interfacing controller to
external equipment. 25 pin D-type socket; 5V TT input/output
MUST use shielded cable.
TRIG Input
TRIG Output
IN_POS Output
Stepped Input
Stepped Output Interface Connector
Ethernet Connector
Dual connector master/slave
configuration. Used to communicate
with an external computer.
USB Connector Type B
Used to communicate with an
external computer.
Controller Synchronizing signals.
Only used to synchronize multiple
6000 controllers.
Power Indicator ED
Indicates the power status and functionality of the
product. RED steady = Controller configuring/not
ready (can take up to 30 seconds). GREEN steady =
Controller powered and ready for operation
C OSED INDICATOR ED
Indicates the status of the stage control oop
OFF = Stage NOT connected
ORANGE = Stage settings being loaded on connection
RED = Controller operating in OPEN loop mode
GREEN = Controller operating in C OSED loop mode
YE OW = Controller servo output frozen
COMS Indicator ED
Indicates the state of the controller communications with
the connected computer. Not lit = No communications
taking place. GREEN lit or flashing =
Communications are taking place
IN POS Indicator ED
Indicates the status of the stage position in
C OSED loop mode. ORANGE = Stage settings
being loaded on connection. OFF = Stage has not
reached the desired position. GREEN = Stage has
reached the desired position (within specified limits)
Nano Mechanism Connector – connect the OP400 to
this position. This provides the stage piezo HV supply,
power for calibration EEPROM and measuring
signals for capacitive sensor operation. NOTE High
Voltage present on connector – up to 160VDC
CONNECTING YOUR SYSTEM - BACKOFUNIT
TURNINGON YOUR SYSTEM
1. Once the stage is mounted, connect stage to the controller ensuring that the connector screws are tightened to the controller
lock posts.
2. Connect Power to controller and USB interface to the PC.
3. Switch ON controller using switch on rear panel. After approx. 30 seconds, the relevant stage channel should show two green
lights (Closed and IN-POS). This indicates the stage is operating in the C OSED loop mode and IN-POS ED indicates stage has
reached position within a pre-defined band.
4. The analogue input and POS MON output is 0V to +10V giving a scale factor of 40µ/volt. The analogue input is enabled by
default. The Scale Factor is in microns per volt. 50 microns per volt for the OP400.
5. The system has 8 memory positions for PID settling (accessible via the USB interface). The system has been shipped with
optimized settings for different objective loads, resolution and step settle requirements. The default setting has been optimized for
loads from 150g to 500g. To change to the other settings it is necessary to connect to a computer, the next section demonstrates
how to change to other settings. Do not change settings too fast for load used or damage to the unit may occur.

SOFT ARE
The standard customer-facing application for the system is called ‘Nanobench 6000’, and is included on the
USB drive included in the shipment. This also includes software or links to software which must be installed
before the software can be used.
Visual C++ untime
Labview untime Engine
‘Nanobench 6000’ runs on Windows XP, 7, 8, 10.
Once Nanobench and associated software has been installed and controller functional, go to
Windows Device Manager, and find the COM port that the controller is connected to (e.g. ‘COM12’).
Select the correct COM port within Nanobench 6000, then click ‘Connect’: At this point the
software should connect to the controller and begin reading the live measured position.
www.prior.com

SOFT ARE
www.prior.com
Presets
The QGOP-400-UP/QGOP-400-INV/QGOP-400UP-HL and QGOP-400-INV-HL come with stored
settings which have been optimized for fast step settle times and objective loads. The datasheet
provided with your OP400 provides information on the presets for your device.
Table of contents
Popular Valve Positioner manuals by other brands
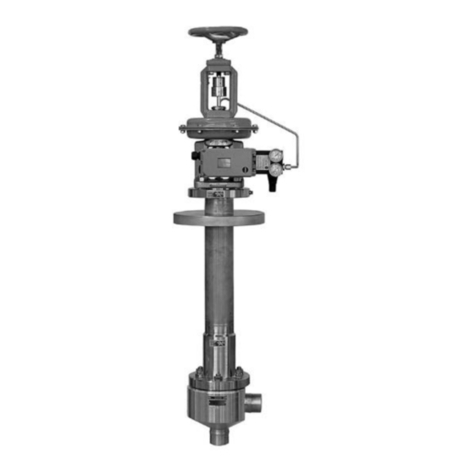
Samson
Samson 3248-1 Mounting and operating instructions
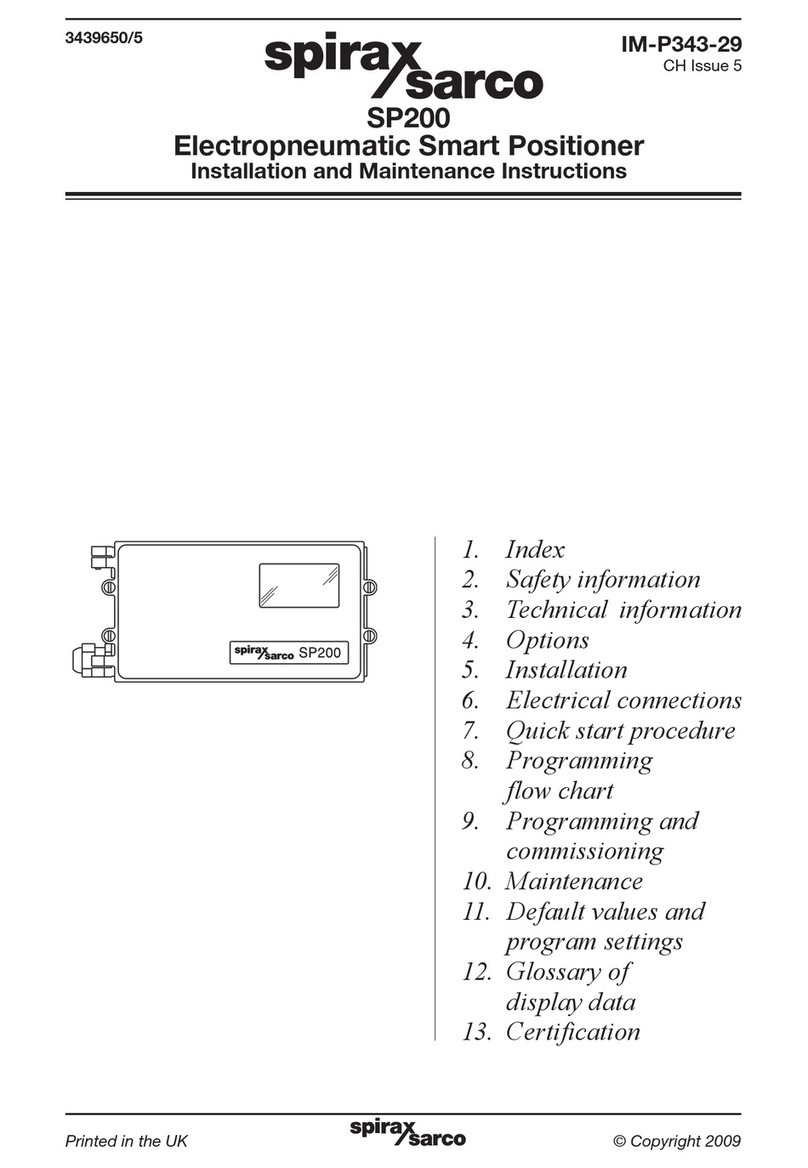
Spirax Sarco
Spirax Sarco SP200 Installation and maintenance instructions
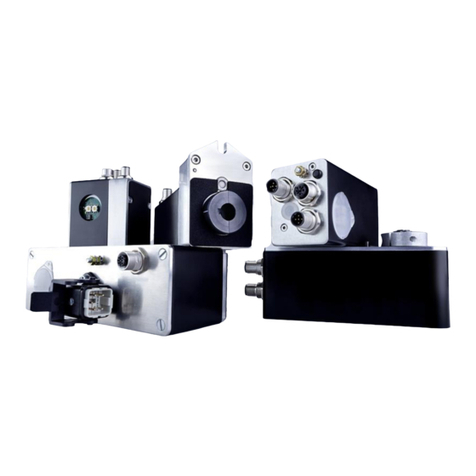
halstrup-walcher
halstrup-walcher PS 3 EIP Series instruction manual
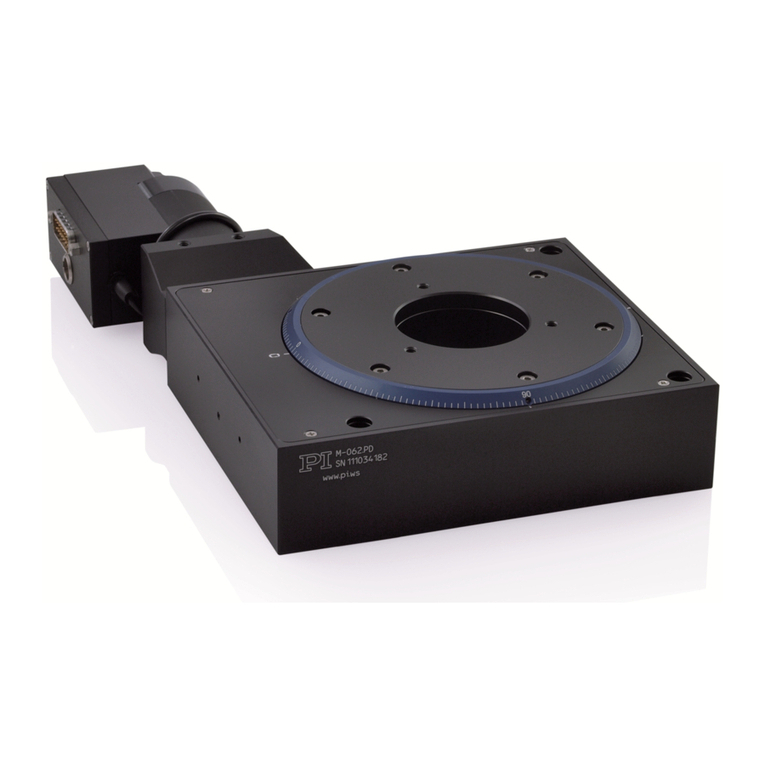
Physik Instrumente
Physik Instrumente M-06 Series Short instructions
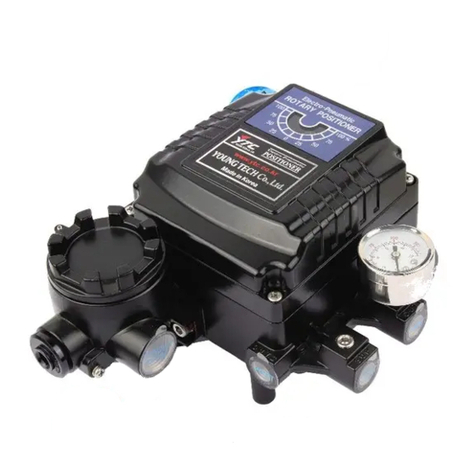
Ytc
Ytc YT-1000L product manual
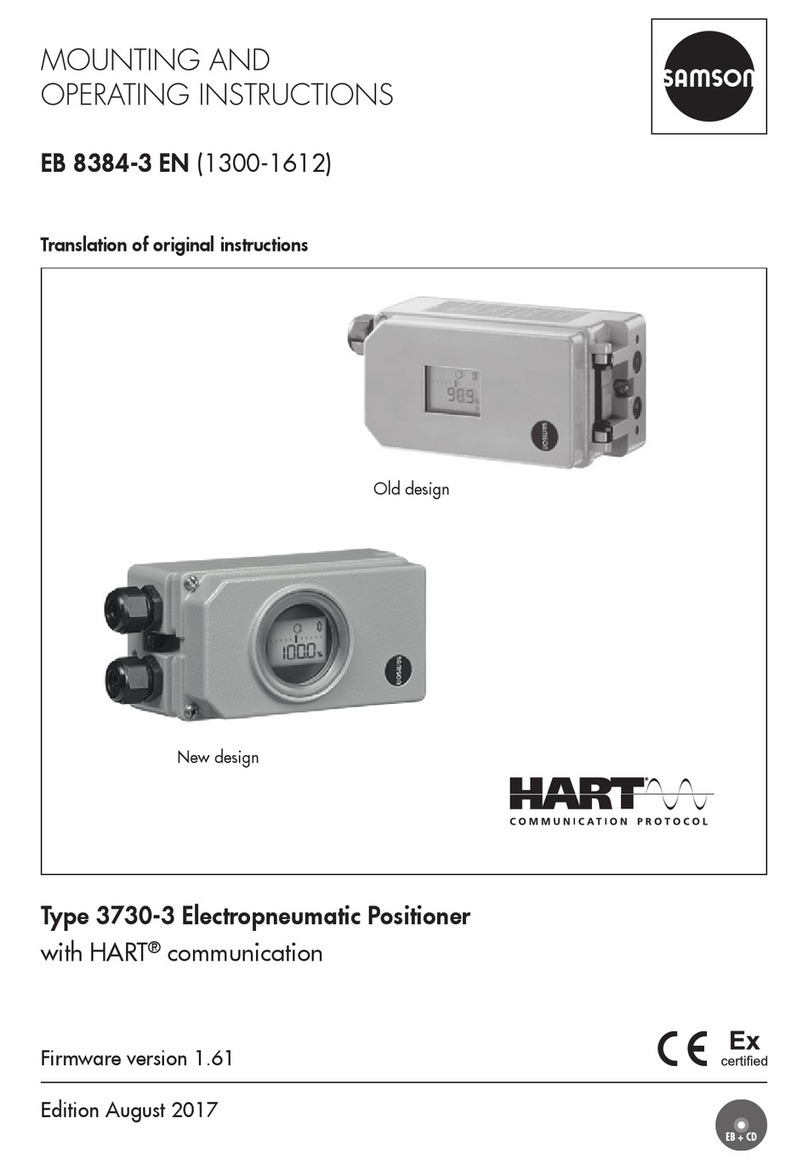
Samson
Samson TROVIS 3730-3 Mounting and operating instructions
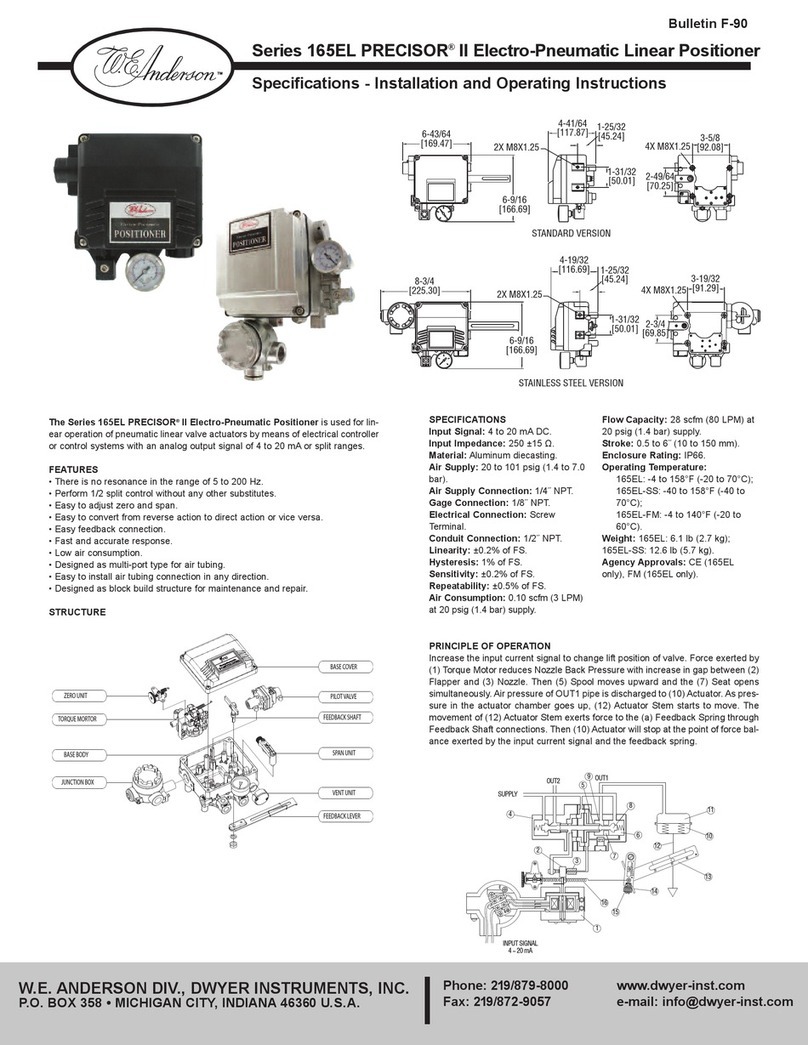
W.E. Anderson
W.E. Anderson PRECISOR II 165EL Series Installation and operating instructions

Baker Hughes
Baker Hughes Masoneilan SVI3 Special instructions
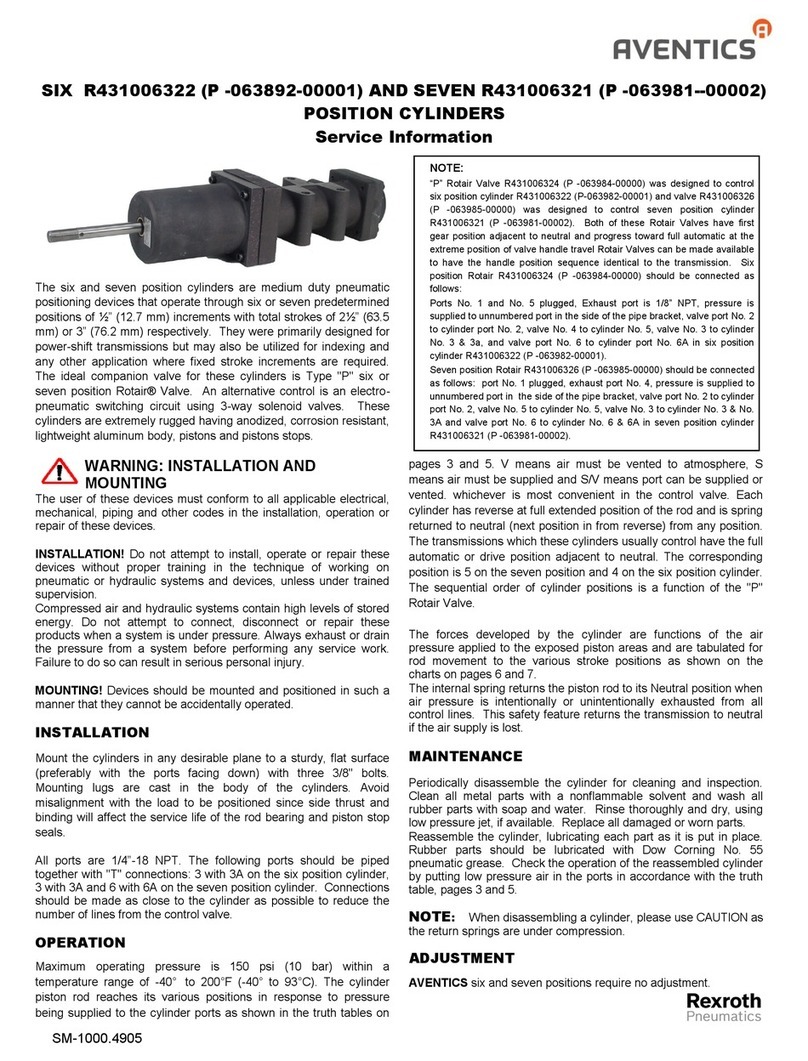
Aventics
Aventics R431006322 Service information

Parker
Parker 404 product manual
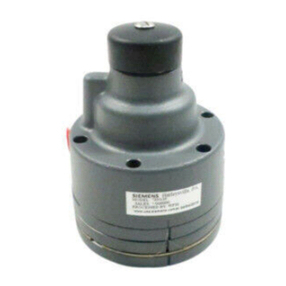
Siemens
Siemens 73N12F Installation and service instructions
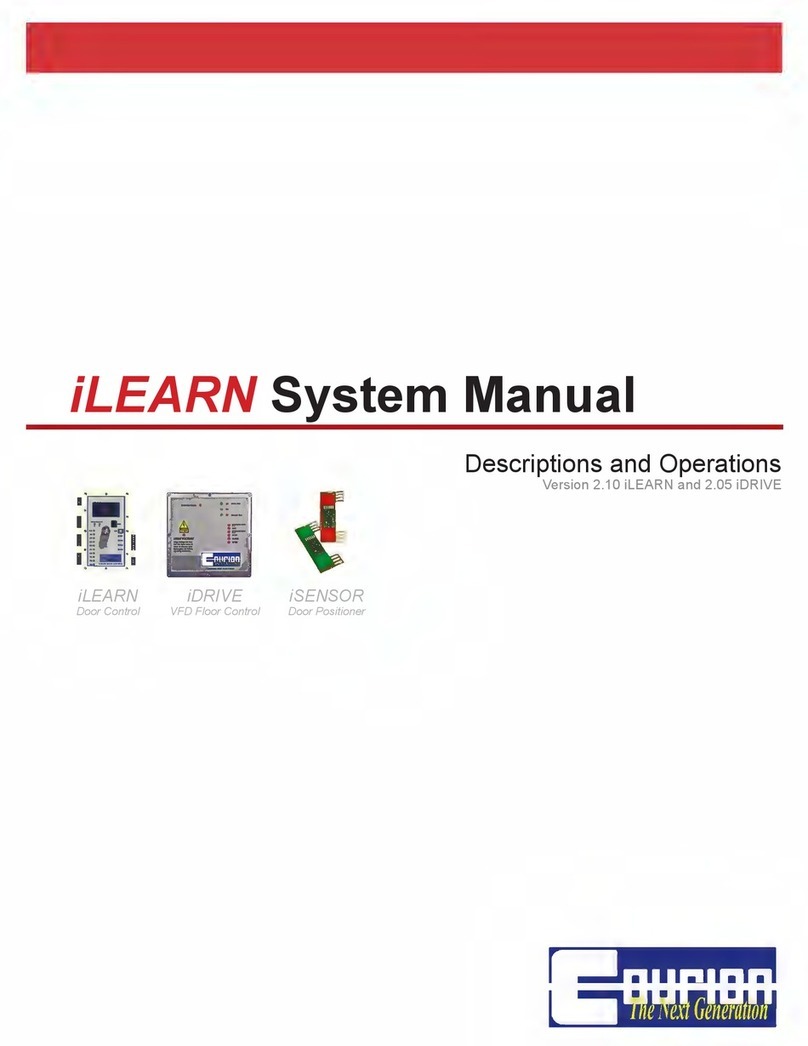
Courion
Courion iLEARN System manual