Courion iLEARN User guide

iLEARN System Manual
Descriptions and Operations
Version 2.10 iLEARN and 2.05 iDRIVE
iLEARN
Door Control
iDRIVE
VFD Floor Control
iSENSOR
Door Positioner

2
ver.071217-2.10
iLEARN System Manual
THE INFORMATION CONTAINED IN THIS DOCUMENT
IS THE EXCLUSIVE PROPERTY OF COMPREHENSIVE MANUFACTURING
SERVICES, LLC. d/b/a COURION. ANY REPRODUCTION OR
DISSEMINATION OF THE CONTENTS, DESIGNS OR IDEAS
CONTAINED HEREIN IS HEREBY PROHIBITED.
© COURION 2013
Table of Contents
Introduction 3
Machine Room Power Requirements 3
iWIRE Package Provided By Courion 5
Interlock Wiring 6
Initial Start Up And Adjustment 8
iLEARN Door Control 13
iLEARN Door Control Menu 20
Diagnostics 20
Operating Parameters 29
Door Parameters 30
Gate Parameters 31
Event Counter 33
Event History 33
Upload History 33
Set Time and Date 34
Adjust Contrast 34
iDRIVE VFD Floor Control 35
iDRIVE.G VFD Gate Control 37
iSYSTEM Troubleshooting Guide 41
Frequently Asked Questions (FAQ) 45
iLEARN Door Control Error Messages 47
iLEARN Door Control Menu - Supplement 53
iLEARN-iLEM Addendum - Kone Elevator Controller 57
iLEARN-iLEM Addendum - Otis 211/411 Elevator Controller 58

3
ver.071217-2.10
iLEARN System Manual
Introduction
Wire the hoistway and car according to COURION’s Hoistway Wiring Diagrams. When possible,
COURION’s wiring diagrams, wire bundles, component wire terminals, and control designations are
pre-numbered and color coded to facilitate ease of installation and trouble-shooting. Please pay
close attention and follow COURION’s pre-numbered system to insure a proper and trouble-free
installation. Remember, wiring errors and loose connections lead to most control malfunctions during
initial start-up and adjustment.
COURION’s Next Generation System requires only one (1) iLEARN Door Control for Front and Rear
Hoistway Openings and Front and Rear Car Gates. All functions of COURION’s iLEARN Door Con-
trol are 100% factory tested to insure proper operation.
Hardware to mount the iLEARN Door Control enclosure to the machine room wall is included as
Hardware Kit #120. One (1) kit is required for each enclosure. If transformers are required, hardware
to mount the transformers is included as Hardware Kit #125. One (1) kit is required to mount each
pair of transformers.
Machine Room Power Requirements
COURION’s iLEARN Door Control requires a 110VAC power supply. COURION’s Hoistway Equip-
ment requires a 240 VAC 3-Phase power supply. A means to disconnect the supply power is gener-
ally required as part of the local electrical code. A disconnect switch with three (3) 15 AMP fuses
should be provided by the General Contractor in the Machine Room.
IMPORTANT!
When the power supply exceeds 260VAC, COURION supplies two (2) single-phase step down trans-
formers. These transformers should be mounted near the iLEARN Door Control. Two (2) single
phase transformers are wired in a polyphase bank to provide three-phase voltage transformation.
Drawing 112673 (on the following page) illustrates typical transformer wiring. DO NOT USE ANY
OTHER CONFIGURATION WHEN WIRING THE POLYPHASE TRANSFORMER BANK.

4
ver.071217-2.10
iLEARN System Manual
Wiring Diagram For Connecting Two Single Phase Dual Voltage Transformers
as One Three Phase Open Delta Transformer
460/230 VAC - 30 - 60 Hz with 115 V Tap (if required)

5
ver.071217-2.10
iLEARN System Manual
iWIRE Package Provided By Courion
COURION’s Next Generation System includes the following pre-numbered and color-coded wiring
bundles -
• iWIRE Motor Wiring Bundle (#90-947400) - Four (4) wire hoistway motor cable in an amount sufcient
to wire the COURION Door Motors, Gate Drives, and Retiring Cam Motors to the iDRIVE VFD Controls
located at each oor or car top.
• iWIRE CANbus Cable (#90-947405) - Two (2) twisted pair communication wires and a drain wire in an
amount sufcient to wire the iLEARN Door Control to all iDRIVE VFD Floor an Gate Controls.
• iWIRE Hoistway Cable (#90-947409) - Five (5) shielded 16 AWG insulated power wires, one (1) yellow 18
AWG insulated wires for the CANbus Address In/Address Out Input, and three (3) black 18 AWG insulated
wires as spares.
• iWIRE Floor/Gate Wiring Bundle (#90-947415) - Fifteen (15) 18 AWG insulated wires in an amount suf-
cient to wire the Door Push Buttons, EUDs, and Floor Zone Switches to the iDRIVE VFD Controls located
at each oor or car top.
• iWIRE Traveling Cable (#90-947416) - Four (4) twisted pair shielded serial CANbus communication wires,
ve (5) 16 AWG insulated power wires, and three (3) 18 AWG insulated wires as spares.
• iWIRE Interconnection Wiring Bundle (#90-947423) - Three (3) 16 AWG insulated power wires, and
twenty (20) 18 AWG insulated wires in an amount sufcient to run from COURION’s iLEARN Door Control
to the Elevator Control. When wiring the inter-control interface between COURION’s iLEARN Door Control
and the Elevator Control, please refer to the Elevator Control Wiring Schematics and COURION’s Inter-
control Interface Circuit Descriptions in this book for more details.
• iWIRE Hoistway Junction Box, Traveling Cable Junction Box, and Two (2) Flat Traveling Cable Grips
(#01-929200 & #01-929201)

6
ver.071217-2.10
iLEARN System Manual
Interlock Wiring
Courion offers two different styles of Interlocks for its Freight Door Systems, depending on customer
requirements and available hoistway space. The two types are: “Q” Style Interlocks and “P” Style
Interlocks.
When wiring COURION’s “Q” Style Interlocks, refer to COURION’s Floor Wiring Diagram and the
diagram on the inside of the interlock cover as an aid in identication of Door Closed, Floor Zone, and
Door Locked contacts.
“Q” Style Interlock

7
ver.071217-2.10
iLEARN System Manual
PA & PAE INTERLOCK
WIRING DIAGRAM
When wiring COURION’s “PA” Style Interlocks, refer to the terminal cross reference on the PA Inter-
lock connection diagram located below. Be sure to properly locate type “PAE” interlocks only at oors
with emergency unlocking devices (also known as EUDs). After wiring the “PA” interlocks, check
adjustment of the roller lever as indicated on the diagram located on the next page.

8
ver.071217-2.10
iLEARN System Manual
PA & PAE INTERLOCK
PO-70-3A

9
ver.071217-2.10
iLEARN System Manual
Initial Startup and Adjustment
A. Insure that all Hoistway Doors and Car Gates are in the FULL CLOSE Position.
B. Ensure that you have correctly completed all of your hoistway and car top wiring per COURION’s
Wiring Diagrams and the iSYSTEM User’s Manual. Most iSYSTEM malfunctions result from hoist-
way wiring errors or loose connections.
C. DO NOT complete the Elevator Control Interconnection until after completing the Initial Start-Up
and Adjustment Steps.
D. Please make sure you have placed the following temporary jumpers on COURION’s iLEARN
Door Control - L1 to INS (Inspection), L1 to HPB (Hall Push Buttons), and L1 to FSH (Fire Service
Phase-2 Hold). These jumpers will be removed after completing the interconnection interface with
the Elevator Control after the Start-Up and Adjustment procedures are completed.
E. If your Push Button Fixtures (Hall and COP) do not include a STOP button, then you need to pro-
vide a permanent jumper between DI-Common and DIO4 - Stop Button at EACH iDRIVE VFD Floor
Control and iDRIVE VFD Gate Control.
F. If you do not have an Emergency Unlocking Device at a particular oor, you need to provide a
permanent jumper between DI-Common and DI02 - EUD at EACH iDRIVE VFD Floor Control where
there is no EUD.
1. iLEARN Startup Wizard
a. Power up the 240 VAC Hoistway Power and 110 VAC to the iLEARN Door Control. The iLEARN
Door Control will automatically boot up to the STARTUP WIZARD screen. If it does not boot to the
STARTUP WIZARD, use the SELECT/MENU Knob on the iLEARN Door Control to scroll to the # of
iDRIVE Parameter under EDIT PARAMETER Menu Item and change the number of iDRIVEs to 0.
Restart the System.
STARTUP WIZARD Screen - Press SELECT/MENU Knob to continue.

10
ver.071217-2.10
iLEARN System Manual
b. Enter the # of Hoistway iDRIVEs (both front and rear openings) in your
hoistway.
c. Enter the # of Car Gates (1 or 2) in your hoistway. System Default = 0.
d. Enter the Car Top Control Type (iDRIVE.G or iDRIVE.PLC). See label on
Car Top Control Enclosure for Car Top Control Type.
e. Enter the # of Car Stations (1 or 2) in your hoistway. System Default = 2.
f. Enter Gate Travel (generally the height of your Opening). System Default =
96”.
g. Set the correct Time and Date for your System.
h. If you have entered 1 or 2 Car Gates during Step #9 above, then select
Yes to set up the FULL OPEN and FULL CLOSE position for your Front and
Rear Gate.
i. Close the Front (Rear) Gate and push the COP Close Button.

11
ver.071217-2.10
iLEARN System Manual
j. Open the Front (Rear) Gate and push the COP Open Button.
The iDRIVE.G Car Top Control Box now has set your FULL OPEN and FULL
Close position.
Using the MENU/SELECT Button, Exit back to the Main Screen.
IMPORTANT! iLEARN Door Control Parameters and iDRIVE VFD Door Control Parameters
are not SAVED until the system is restarted - please proceed to SYSTEM RESTART.
2. System Restart
a. Using the MENU/SELECT knob, turn and select DIAGNOSTICS.
b. Select RESTART SYSTEM
c. Turn MENU/SELECT knob to indicate YES and then push to restart your
COURION System.
Boot Screen - During the reboot process, COURION’s iLEARN Door Control
will establish communication with each of your iDRIVE VFD Floor Controls.
The number of iDRIVEs found should equal the number of iDRIVEs expect-
ed.
NOTE: If there is a discrepancy between the number of iDRIVEs found
and expected, DO NOT GO TO THE NEXT STEP. Proceed to the
TROUBLESHOOTING and ERROR MESSAGES Section of this Manual.

12
ver.071217-2.10
iLEARN System Manual
COURION Logo Screen - Press the MENU/SELECT Button.
System Status Screen - System OK
NOTE: If this screen indicates something other than SYSTEM OK,
please proceed to the TROUBLESHOOTING and ERROR MESSAGES
Section at the back of this Manual.
If you received an iSYSTEM Software Update Kit with your order, update the iLEARN Door
Control and iDRIVE software by following the instructions in Courion’s iSYSTEM Software
Update Manual.
After successfully updating the iSYSTEM Software, re-cycle the iLEARN Door Control power (110
VAC) and iDRIVE Hoistway power (240 VAC).
3. Initial Operation
a. Insure that all of the Hoistway Doors and Car Gates are in the FULL CLOSE Position.
b. Utilizing the Hall or Car Station Push Buttons, open and close the Hoistway Doors.
To ADJUST the Hoistway Door(s) Operation (if required), press the MENU/
SELECT Button and turn to DOOR PARAMETERS.

13
ver.071217-2.10
iLEARN System Manual
Scroll Down to Item 2.5 Slowdown Distance (Default = 8.0”) and adjust
to meet your site requirements. This is the distance away from FULL
OPEN and FULL CLOSE where the door speed will change from “Fast” to
“Slow”, as set by the iLEARN Control
Scroll Down to Item 2.6 Creep Distance (Default = 3.0”) and adjust to
meet your site requirements. This is the distance away from FULL OPEN
and FULL CLOSE where the door speed will change from “Slow” to
“Creep”, as set by the iLEARN Control.
To ADJUST the Car Gate Operation (if required), press the MENU/SE-
LECT Button and turn to GATE PARAMETERS.
Scroll Down to item 4.6 Car Gate Slowdown (Default = 15”). This is the
distance away from FULL OPEN and FULL CLOSE where the car gate
speed will change from “Fast” to “Slow”, as set by the Gate iDRIVE.G.
Scroll Down to Item 4.7 Creep Distance (Default = 3”). This is the dis-
tance away from FULL OPEN and FULL CLOSE where the car gate
speed will change from “Slow” to “Creep”
If your Hoistway Doors or Car Gate(s) do not operate properly during the initial operation, please
proceed to the TROUBLESHOOTING and ERROR MESSAGE Section at the back of this Manual.

14
ver.071217-2.10
iLEARN System Manual
iLEARN Door Control

15
ver.071217-2.10
iLEARN System Manual
iLEARN Door Control Description
SELECT/MENU Knob - The Select/Menu Knob is used to scroll through (turn) and select (push)
Menu Items on the iLEARN Display. After making a change in the Menu, the change is saved to
the iLEARN Control when you push the SELECT/MENU Knob.
IMPORTANT - Changes made on the iLEARN Door Control to the iDRIVE Parameters (Section 4
- Edit Parameters) will not be saved to the hoistway iDRIVEs until the System is restarted.
See the iLEARN Door Control Menu Screens Section of this Manual for further information.
USB Port - The USB Port is used to update the iLEARN and iDRIVE programs. It can also be
used to download the Event History captured by the iLEARN Door Control to a USB device.
SCADA CAN Port - This port allows the iLEARN Door Control to connect directly to an Elevator
Controller’s CAN port rather than using the AC inputs and relay outputs described below.
iDRIVE Network LEDs (RX & TX) - These LEDs indicate the receipt (RX/Red) and transmission
(TX/Green) of information over the CANbus network between the iLEARN Door Control and the
iDRIVE units on the network. During normal operation, these LEDs should be rapidly ashing. If
both lights are not rapidly ashing, there is a communication error on the CANbus network that
needs to be resolved - See the Troubleshooting and Error Message Section of this
Manual.
STATUS LED - This LED indicates the overall STATUS of your COURION System.
1 Flash Per Second - System is Ready with normal operation
2 Flashes Per Second - Active iDRIVE Fault on the CANbus Network
3 Flashes Per Second - Memory Failure
4 Flashes Per Second - CAN Controller Failure
If the STATUS LED is something other than 1 Flash Per Second - See the Troubleshooting and
Error Message Section of this Manual.
+5V & +24V LEDS - These LEDs indicate that the iLEARN Control has the necessary power for
the CANbus Network and Digital Inputs. These LEDs should be constantly ON.

16
ver.071217-2.10
iLEARN System Manual
Inter-Control Interface Circuit Descriptions
CAM - Retiring Cam - [J11:1 - J9:1] The CAM circuit is a NORMALLY OPEN circuit closed when
the car is ready to answer a call. Closing this circuit retires the CAM. This circuit must not be de-
pendent on the door interlock circuit, as the door interlock circuit is not complete until the CAM has
retired and the doors have been locked.
INS - Inspection - [J11:1 - J9:2] The INS (or Door/Gate Cut-Out) is a NORMALLY CLOSED circuit
opened when door or gate operation is undesirable. The circuit is typically opened when:
1. The Lift is operated in INSPECTION mode.
2. The PIT STOP SWITCH is actuated.
3. The car EMERGENCY STOP button is actuated.
AOF - Auto Open (Front) - [J11:1 - J9:3] The AOF circuit is a NORMALLY OPEN circuit mo-
mentarily closed to initiate door and gate opening after the car has leveled at a oor. This circuit
should be open when the doors have fully opened. This circuit should momentarily reclose in re-
sponse to a call registered at the oor where the car is already present. This circuit initiates door
and gate opening for FRONT entrances only. Auto Open is ignored when the elevator is on Fire
Service-Phase 2 operation.
AOR - Auto Open (Rear) - [J11:1 - J9:4] The AOR circuit is a NORMALLY OPEN circuit and func-
tions just like the AOF circuit, except this circuit initiates door and gate opening for REAR entranc-
es only. Auto Open is ignored when the elevator is on Fire Service-Phase 2 operation.
HPB - Hall Push Buttons - [J11:1 - J9:5] The HPB circuit is a NORMALLY CLOSED circuit opened
to disable corridor door OPEN and CLOSE buttons. This circuit must be opened on Fireghter’s
Service Phase 2 operation except during the transition from Phase 2 to Phase 1 operation. This
circuit may be opened during ATTENDANT operation.
ATC - Auto Time Close - [J11:1 - J8:1] The ATC circuit is a NORMALLY CLOSED circuit opened to
prevent Automatic Timed Closing of the freight elevator doors. This circuit must be opened when
the car has arrived at the designated recall landing during Fireghter’s Service Phase 1 Recall
Operation. This circuit is disabled when the Fireman’s in-car key switch is set to the ON position.
This circuit may also be opened during ATTENDANT operation of the lift to prevent Automatic
Timed Closing of the freight doors. This circuit may be left open indenitely if Automatic Timed
Closing is not desired.
FSR - Fire Service Recall - [J11:1 - J8:2] The FSR circuit is a NORMALLY OPEN circuit momen-
tarily closed to initiate door and gate closing when required during a Phase 1 Emergency Recall
Operation. This circuit must be opened when the car arrives at the designated recall landing.
This circuit is disabled when the Fireman’s in-car key switch is set to the ON position.

17
ver.071217-2.10
iLEARN System Manual
FSL - Fire Service Landing - [J11:1 - J8:3] The FSL circuit is a NORMALLY OPEN circuit closed
when the car is parked at the designated recall landing during Fireghter’s Emergency Operation
Phase 1 and 2.
FS2 - Fire Service Phase 2 - [l:11-1 - J8:4] The FS2 circuit is a NORMALLY OPEN circuit closed
only when the Fireman’s in-car key switch is set to the ON position. Please refer to ASME A17.1,
Rule 211.3c (2000) or Rule 2.27.3.3 (2002 or later) for a complete description of Fireghter’s Ser-
vice Phase 2 Emergency In-Car Operation.
FSH - Fire Service Phase 2 Hold - [J11:1 - J8:5] The FSH circuit is a NORMALLY CLOSED circuit
opened when the Fireman’s in-car key switch is set to the HOLD position.
During Fireghter’s Service Phase 2 Emergency Operation, the Fireman’s in-car key switch is
placed in the OFF position, the car is not at the designated level, and Phase 1 Operation is not in
effect, this circuit must open to disable the CLOSE push button and allow the door and car gate to
open.
DCF - Doors Closed Front - [J10:8 - J10:7] The Doors Closed Front circuit is a NORMALLY
OPEN relay that closes when all FRONT doors are in the closed position and the power close
function is complete.
DCR - Doors Closed Rear - [J10:6 - J10:5] The Doors Closed Rear circuit is a NORMALLY OPEN
relay that closes when all REAR doors are in the closed position and the power close function is
complete. This circuit will be open if there are no rear doors.
NOTE: Both the Doors Closed Front and Doors Closed Rear circuits will be OPEN if no power is
supplied to the iLEARN Door Control.
DNC - Door Not Closed - [J10:4 - J10:3] The Door Not Closed circuit is a NORMALLY OPEN re-
lay that closes when the active door and/or car gate is not in the closed position. Doors are con-
sidered closed when they are within 3” of FULL CLOSE. This circuit may be used to sound a door
open bell in response to a call.
DNO - Door Not Open - [J10:2 - J10:1] The Door Not Open circuit is a NORMALLY OPEN relay
that closes to indicate that the active door OR car gate is in the FULLY OPEN POSITION. This
circuit may be used to signal the Lift Control to re-activate Fireghters Emergency Operation
Phase 2 Hold when required.

18
ver.071217-2.10
iLEARN System Manual
SPECIAL NOTES:
Fireghter’s Emergency Operation Phase 2 to Phase 1 Transition - During the transition from Fire-
ghter’s Service Phase 2 to Phase 1 Operation, and when the lift is not at the designated recall land-
ing and the doors are not closing, the following special conditions apply:
• Reactivate Hall Push Buttons [J11:1 - J9:5] The Hall Push Buttons must be active during
the transition. This circuit must be reopened when either Phase 1 Operation is resumed or
Phase 2 Operation is reactivated.
• Reactivate Phase 2 Operation or Hold [J11:1 - J8:5] If the Fireghter’s in-car key switch is
turned from OFF to either HOLD or ON during the transition from Phase 2 to Phase 1 Op-
eration while the doors are closing, the closing cycle must be interrupted and the door and
car gate reopened. The re-open sequence is accomplished by opening the normally closed
HOLD circuit between J11:1 and J8:5 to break the closing cycle and establish the reopen
cycle. The normally closed HOLD circuit may be reestablished when the door and gate
have fully opened as indicated by the Doors Not Closed circuit J10:2 - J10:1. The Fireght-
er’s Emergency Operation Phase 2 circuit (J11:1 - J8:4) should remain closed until Phase 1
Operation is resumed following the transition.
PLEASE NOTE!
Instructions on the use of the COURION iLEARN Door Control circuits during Fireghter’s Emergency
Operation and transition are not intended to be inclusive. Please refer to ASME A17.1 Rule 211.3
(2000) or Rule 2.27.3 (2002 and later) for a complete description of the performance requirements.

19
ver.071217-2.10
iLEARN System Manual

20
ver.071217-2.10
iLEARN System Manual
This manual suits for next models
2
Table of contents
Popular Valve Positioner manuals by other brands

ABB
ABB TZIDC Commissioning Instruction
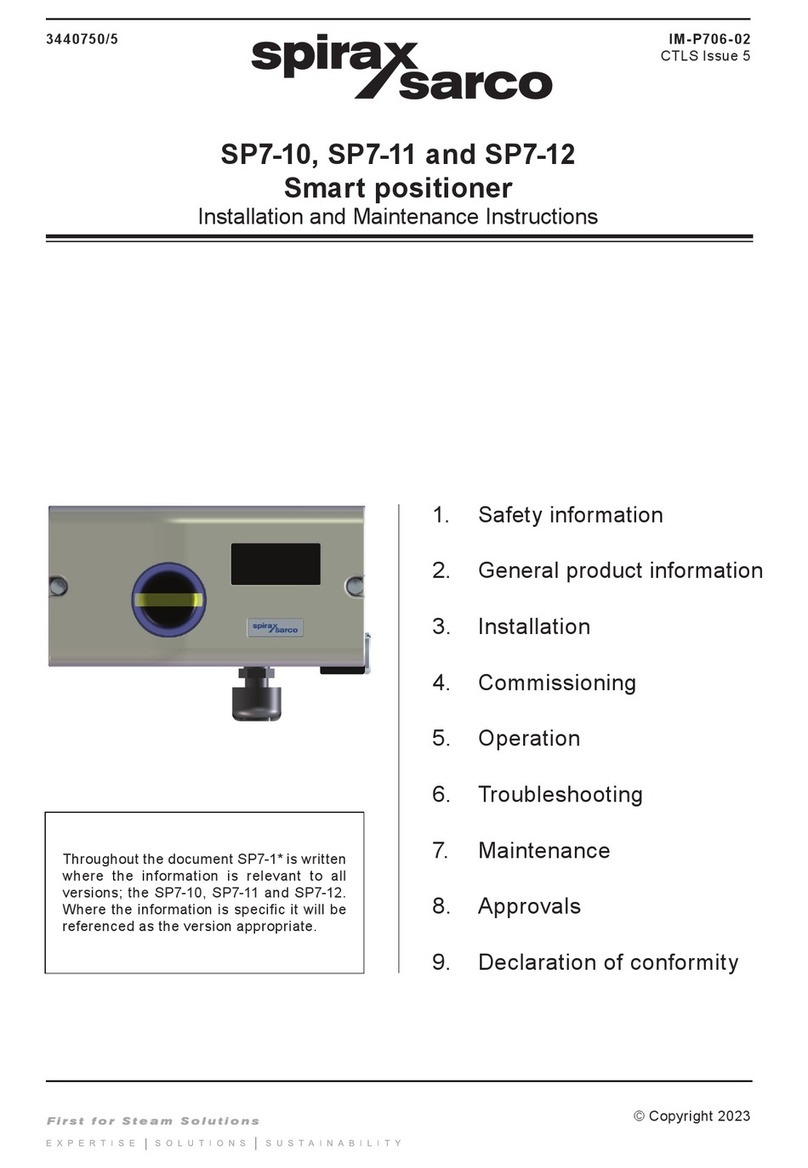
Spirax Sarco
Spirax Sarco SP7-11 Installation and maintenance instructions
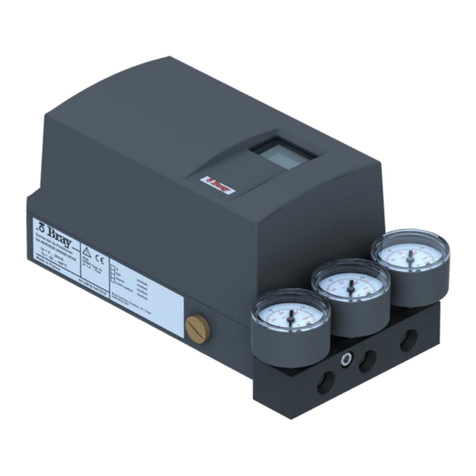
Bray
Bray 6A series quick start guide
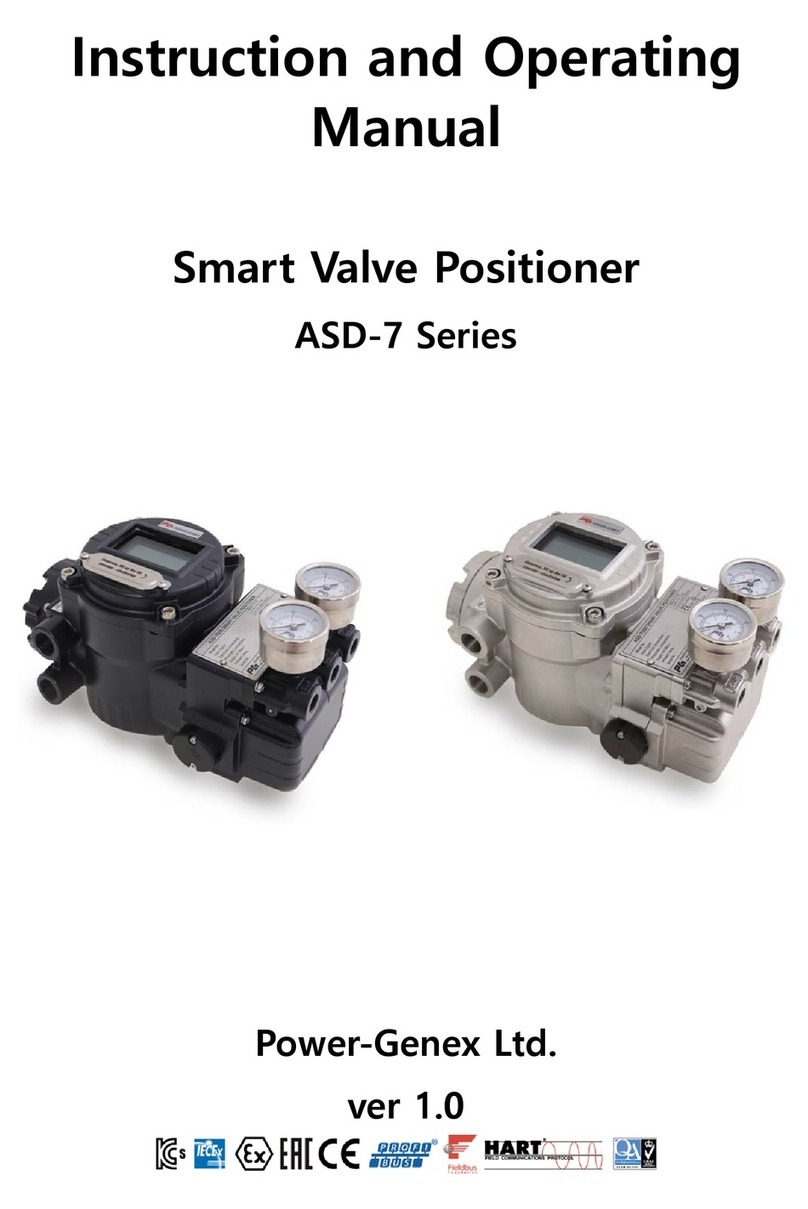
Power-Genex
Power-Genex ASD-7 Series Instructions and operating manual
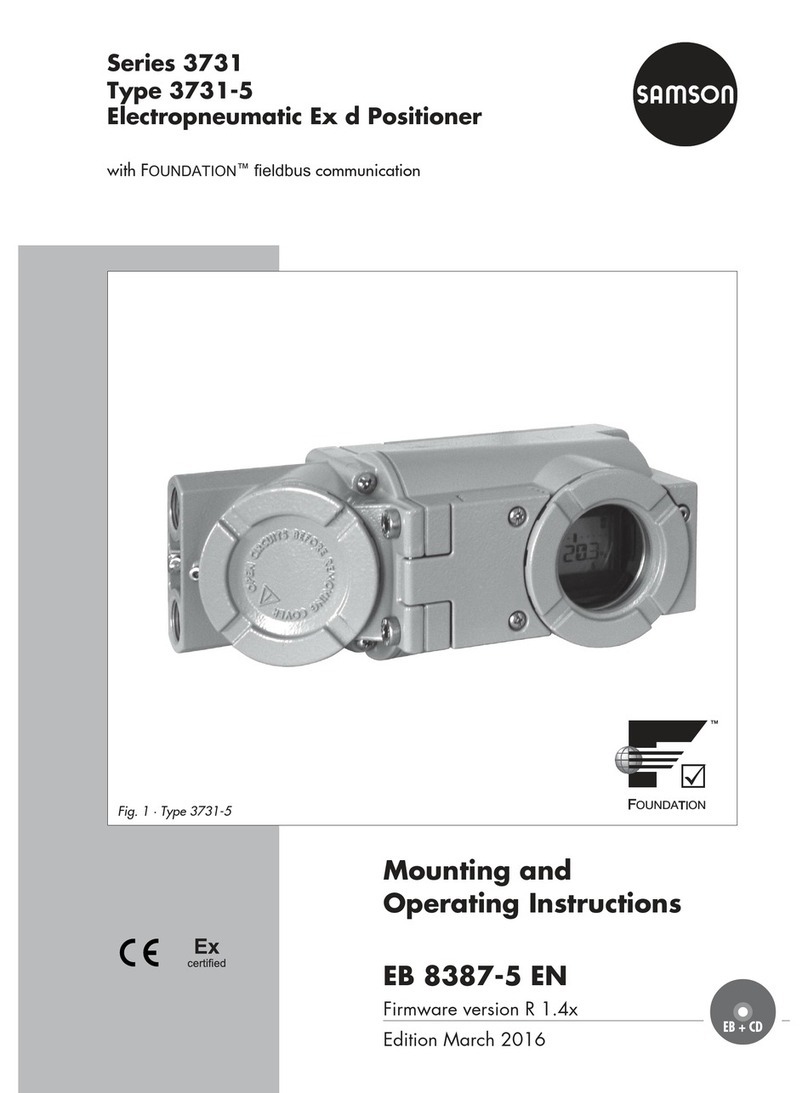
Samson
Samson 3731-5 Mounting and operating instructions
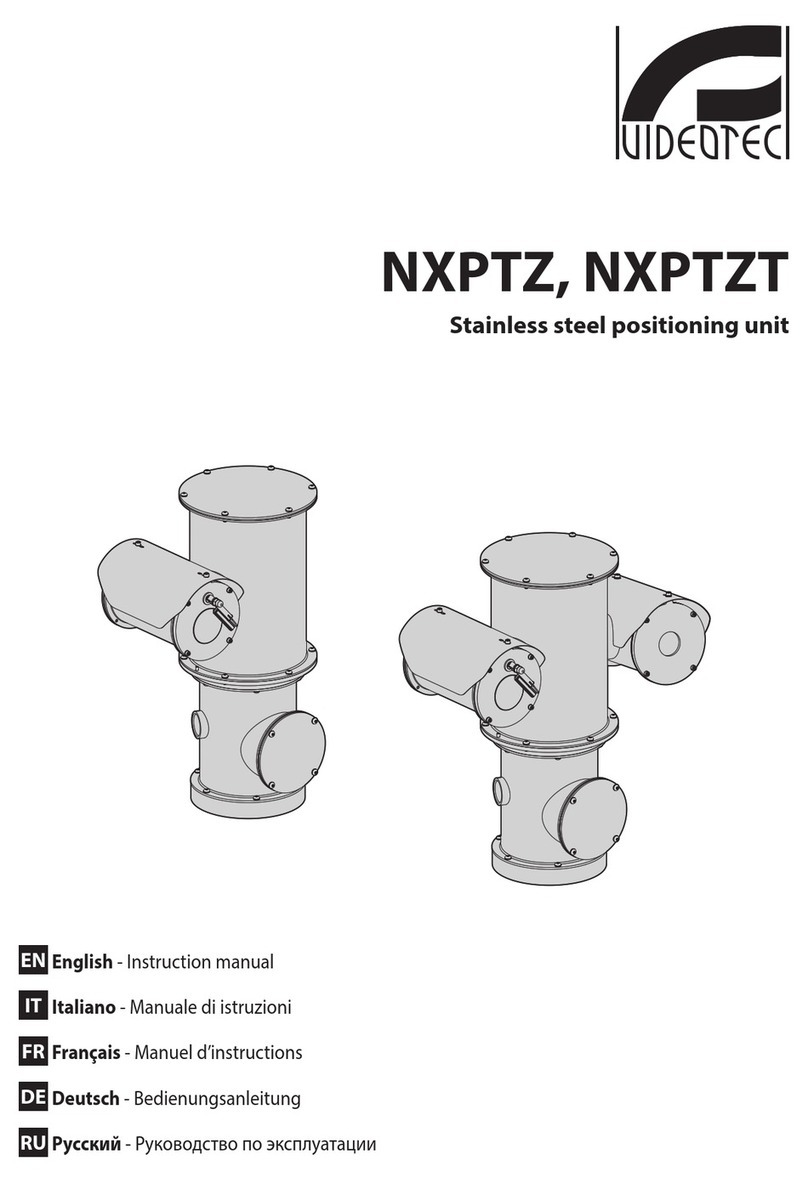
Videotec
Videotec NXPTZT instruction manual