Process Technology SH Series User manual

S
SH
H
S
Se
er
ri
ie
es
s
Inline Heater System for Solvent or Gas
Installation and Operation Manual
This instruction manual explains the basic operation of the Process Technology inline solvent or gas heater.
We recommend reading this manual carefully prior to operating the heater to help ensure proper use of the equipment .
Please supply the model and serial numbers when ordering spare parts or when receiving technical assistance.
www.processtechnology.com
7010 Lindsay Dr., Mentor, OH 44060 Phone: 440-974-1300 Fax: 440-974-9561 USA/CN: 800-621-1998

M-55-02 SH Inline Heater System Manual
Revision – Date: 00 – 06/07/07
2
Table of Contents
Related Documents........................................................................................................................................3
Section 1: Introduction...............................................................................................................................4
SH inline heater model number designation..............................................................................................5
Safety network..........................................................................................................................................7
Section 2: Pre-Installation.........................................................................................................................8
Section 3: Installation................................................................................................................................8
Uncrating and inspection...........................................................................................................................8
Mounting heater and control......................................................................................................................8
Plumbing connections...............................................................................................................................9
Electrical connections................................................................................................................................9
Incoming power connections.............................................................................................................9
RS232/RS485 serial communications interface (optional)................................................................9
Customer interface plug (optional)....................................................................................................9
Section 4: Temperature controller...........................................................................................................10
Temperature controller E5CN .................................................................................................................11
Display features ......................................................................................................................................11
Operations for E5CN...............................................................................................................................12
Operation indicators........................................................................................................................12
Using the keys ................................................................................................................................13
Mode parameter settings ................................................................................................................14
Changing primary set point.............................................................................................................16
High alarm.......................................................................................................................................16
PID tuning.......................................................................................................................................17
Operations for SLC .................................................................................................................................18
Safety limit controller.......................................................................................................................18
Programming ..................................................................................................................................18
Section 5: Operation................................................................................................................................19
System start-up.......................................................................................................................................19
Normal operation.....................................................................................................................................19
Shut down procedure..............................................................................................................................19
Section 6: Service and maintenance.......................................................................................................19
Maintenance............................................................................................................................................19
Service policy..........................................................................................................................................20
Warranty policy .......................................................................................................................................21

M-55-02 SH Inline Heater System Manual
Revision – Date: 00 – 06/07/07
3
RELATED DOCUMENTS
The following documents are to be used in conjunction with this manual:
ANSI/NFPA70 – National Electric Code, latest edition. To be used in conjunction with electrical service, wire sizing,
routing and protection.
SEMI S2 – Semiconductor Equipment Safety Guidelines, latest edition. To be used in conjunction with safe operation,
access and decommissioning procedures.
OMRON E5CN INSTRUCTION MANUAL – To be used to access features of the E5CN temperature controller. (Secure
appropriate manual for any optional temperature controller used in place of the E5CN).
ANY – State or local building codes that would cover the electrical, mechanical, or physical installation of electrical heating
equipment.
National Electric Code
NFPA 1999 Copyright
National Fire Protection Association
Quincy, Mass. 02269

M-55-02 SH Inline Heater System Manual
Revision – Date: 00 – 06/07/07
4
Section 1: Introduction
Process Technology’s SH In-Line Heater is designed to provide energy-efficient, safe heating of solvents and non-
flammable gasses (such as nitrogen). Wetted surfaces of the heater are constructed of chemically milled (etched) 316
stainless steel. The heater is a compact, completely welded, insulated, pressure resistant vessel. It is designed for use in
either Single Pass or Multi-Pass Flow applications. The junction box includes two threaded couplings for optional gas
fittings, which could be used to keep the junction box under positive gas pressure.
The SH In-Line Heater can withstand operation at a variety of temperature and pressure conditions. The maximum
operating condition for the SH In-Line Heater is 160oC at 50 PSI.
Warning: Safe operation of the equipment requires that each of the temperature sensors be wired
properly into a customer supplied control system, in accordance with local regulations, where applicable.
Refer to Section 3.5 for additional information. Failure to use the supplied temperature sensors for their
intended purposes may void all or part of the equipment warranty. Consult factory for technical assistance.
This SH In-Line Heater consists of:
316 stainless steel fluid path
304 stainless steel, insulated housing
Two J- type thermocouple Heater over-temperature sensors
One J-type thermocouple Process control sensor
TCO, over-temperature fuse
½-inch OD stainless steel tube inlet and outlet connections
Optional Heater Equipment may include:
E or K-type thermocouples or RTD temperature sensors
Custom inlet and outlet connections
This SH In-Line heater control system consists of the following:
Solid state control relays
PID temperature controller (series E5CK)
Over-temperature controller
Ground-fault protection (Earth leakage protection)
Optional System Equipment may include the following:
Circuit breaker and electrical disconnect
Built to SEMI and CE standards
Remote control electrical interface
RS-232, RS485 serial communication interface
Warning: The heater design and over-temperature protection devices vary depending on the specific
application. This heater (reference model and serial numbers in Appendix) was designed and built for a
specific inert gas heating application. This manualprovides information for inert gas heating applications
ONLY. This heater should not be used to heat process solvents or combustible fluids.

M-55-02 SH Inline Heater System Manual
Revision – Date: 00 – 06/07/07
5
SH inline heater system model number designation:
Model / Part numbers are descriptive and usually follow this format.
Example:
SHV = SH In-Line Heater
Size (Output wattage represented as 100 watts)
Supply voltage
V120 - 120 VAC
V208 - 208 VAC
Phase: 1 = Single, 3 = Three
Plumbing Connection (represented as 1/100 inch)
SN50 = 1/2" Non Threaded Tube Connection
SN75 = 3/4" Non Threaded Tube Connection (Standard
)
V50 = 1/2" Swagelok VCR connections
V75 = 3/4" Swagelok VCR connections
Custom Options
CE = SEMI S3 and CE compliant
SHV - 20
-
208 - 1 SN50 -X CB = Include disconnect and circuit breaker
RI = Remote control interface
RC = Controller communications (RS232, RS 485)
-## = Revision number, indicating specific design features for a p
a
This example represents a2kW, 208VACinput voltage, single phase
and 1/2 inch process connections.

M-55-02 SH Inline Heater System Manual
Revision – Date: 00 – 06/07/07
6
Figure 1: Dimensional Drawing.

M-55-02 SH Inline Heater System Manual
Revision – Date: 00 – 06/07/07
7
SAFETY NETWORK:
The SH inline heater is protected from accidental damage or unsafe operating conditions with a network of safety interlocks. The safety
interlocks will disengage power to the heaters until power is manually restored at the control. The safety interlocks offered on the SH
inline heater are listed below.
TCO Heater Over-Temperature Fuse:
Any over-temperature situation will cause the main load contactor to disengage, and sound the audible alarm. This will require a manual
reset of the heater once the overheat event has been corrected. The over temperature sensor has a fixed setting of 169°C (336°F).
(Maximum Heater Temperature)
Safety Limit Controller (SLC):
This over-temperature controller is a separate controller mounted inside the control enclosure. It uses a separate temperature sensor to
monitor the hot-zone temperature in the heater.
This over-temperature controller has two different settings:
1. Over-temperature cutoff (SP2). This setting needs to be adjusted manually by the customer, to be set at 135°F (57°C).
This setting will cut off power to the heaters if the internal temperature rises above this value, but will automatically re-
engage the heaters when the temperature drops below this value. This is not an alarm set point.
2. High Limit (HSP1). This high-temperature alarm setting is set at 145°F (63°C). If this temperature is detected at this
sensor. the controller will disengage the main load contactor and sound the audible alarm. This will require a manual
reset of the heater once the overheat event has been corrected.
Heat Sink Thermal Cutoff:
The heat sink for the solid state relays (SSRs) is equipped with a bimetallic temperature switch. If the cooling fan on the heat sink wer to
fail, the temperature of the het sink would gradually rise, resulting in eventual SSR failure. This switch willl cause the main load
contactor to disengage, and sound the audible alarm. This will require a manual reset of the heater once the overheat event has been
corrected. The over temperature sensor has a fixed setting of 176°F (80°C). (Maximum Heat Sink Temperature)

M-55-02 SH Inline Heater System Manual
Revision – Date: 00 – 06/07/07
8
Section 2: Pre-Installation:
Note: Before beginning installation of the SH inline heater system, carefully read this entire section.
1) Space Requirements: The standard dimensions of the various models are shown in Table 2 (see appendix for custom made units).
Allow additional space on all sides of the unit for the control ventilation and service access.
Dimensions
kW Width Depth Height
1-3 29 ½” (750mm) 13 ½” (343mm) 36” (915mm)
Table 2
2) Inlet and Outlet Plumbing: The SH inline heater is supplied with ½-inch tubes for inlet and outlet plumbing connections. Reference
the specific model number ordered and section 1.1 “SH Inline heater system model number designation” of this manual to confirm
the required plumbing connections.
3) Electrical Connections: The SH inline heater is supplied with customer specified power requirements. Reference the specific
model number ordered and section 1.1 SHP inline heater system model number designation” of this manual for the required power
requirements. Confirm these requirements by checking the product identification tag located on the lower face of the cabinet. Fuse
the incoming power line for the rated amperage using an approved electrical disconnect box.
Section 3: Installation:
Uncrating and Inspection:
1) The SH inline heater systems are crated and shipped in a horizontal position. If the unit is not horizontal, return the crate to a
horizontal position and inspect carefully.
2) Remove front side of the crate.
3) Remove the protective packaging material.
4) Remove the unit from crate by grasping the sides of the cabinet and lifting out of the crate.
5) Inspect the unit for any apparent damage.
Mounting Heater and Control:
1) Location: SH inline heater systems are designed for remote installation, keeping point of use areas uncluttered and free of
potential obstructions. The unit is designed to use a minimum amount of wall space making chase areas a suitable location for
installation.
2) Mounting: The SH inline heater system is designed to be wall mounted and should be placed in a vertical and level position.

M-55-02 SH Inline Heater System Manual
Revision – Date: 00 – 06/07/07
9
Plumbing Connections:
Process Line Connections:
1) Remove the protective plastic caps from inlet and outlet plumbing on the heater.
2) Locate the inlet and make the required connection to the customer supplied fitting. (Do not reverse).
3) Tighten the connection as required. Take care not to over-tighten.
4) Repeating the above procedure for the outlet plumbing.
Electrical Connections:
Incoming Power Connections:
SH inline heater systems are designed to operate on 3 wire, single phase, electrical supplies (2 power wires, 1 ground wire). All
electrical connections should conform to local electrical codes and/or NFPA 70/79.
1) Check the system tag located on the equipment for Power Requirements.Do not operate this heater on Voltages other than the
Voltage rating on the system tag.
2) Open the front cover on the left hand side of the cabinet by loosening cover screws.
3) Fuse the incoming line for the rated amperage using an approved electrical disconnect box.
4) Supply power to the unit from the electrical panel into the cabinet through the opening at the “service entrance”. This opening will
need to be made by the customer. Ensure that the wire has sufficient amp capacity to safely carry the power load.
5) Connect the leads from the incoming power line to the appropriate terminals (reference the Electrical Schematic) making sure not
to disturb existing wiring. Use care that no loose strands of wire are exposed out of the Terminal Block. Torque all wires to the
specified ratings located on the wiring diagrams and component labels.
6) Grounding is done internally from the Incoming Power Strip. Reference the wiring diagram in the appendix.
RS-232 / RS-485 Serial Communication Interface (Optional):
In units supplied with the RS-232 / RS-485 serial communication interface, the Temperature Controller is equipped with RS-232 / RS-
485 Serial Communication capability for use with a customer-supplied host computer. If this option is used, all temperature and related
parameters can be monitored or altered from the host computer. On standard units, the DB-9 receptacle(s), labeled REMOTE
COMMUNICATIONS, is(are) located at the rear (or bottom) of the cabinet. An independent serial cable should be installed between the
host computer and the DB-9 receptacle.
Customer Interface Plug (Optional):
The Auxiliary Equipment Interface Plug is used for communication between the Process Controller and customer-supplied devices. The
interface plug is located on the rear (or bottom) of the Cabinet enclosure. Refer to dimensional drawings in the appendix.
Reference the electrical drawings supplied in the appendix for options provided and proper interface connector pin orientation.

M-55-02 SH Inline Heater System Manual
Revision – Date: 00 – 06/07/07
10
Section 4: Temperature Controller:
Figure 2: Temperature Controller and Control Panel.
The SH inline heater system incorporates a self-tuning, PID microprocessor based, digital temperature controller with a set high
temperature alarm. The PID feature enhances the controller's ability to reach and maintain a constant process temperature. The self-
tuning feature enables the controller to measure the process characteristics and indicate desired values, which can be displayed on LED
displays.
This section provides a description of, and instructions for the Omron E5CN Controller. For a complete user guide, see the Omron
website, www.omron.com.

M-55-02 SH Inline Heater System Manual
Revision – Date: 00 – 06/07/07
11
Figure 3: E5CN Temperature Controller.
DISPLAY FEATURES:
No. 1 display (PV): Shows the process value (outlet temperature), modes and parameter symbols.
No. 2 display (SV): Shows set points, parameter operation read value, or the variable input value.
Level key: Switches the controller between auto and manual operation.
Mode key: Press this key to change parameters within a setting level.
Up and Down arrow keys: Advances, increases or decreases the setting or values in the No. 2 display. Holding these
keys down will speed up the rate of change.

M-55-02 SH Inline Heater System Manual
Revision – Date: 00 – 06/07/07
12
OPERATIONS for E5CN:
Operation Indicators:
ALM1: Illuminates when the alarm 1 setting is ON (tripped) (120°C).
ALM2: Illuminates when the alarm 2 setting is ON (tripped) (110°C).
ALM3: Not available on this controller.
HA: Not available on this controller.
OUT1: Illuminates when the control output 1 is ON.
OUT2: Illuminates when control output 2 is ON (Not used).
STOP: Illuminates when the control operation has stopped.
CMW: Illuminates when communications wiring is enabled.
: Illuminates when setting change protection is ON.
MANU: Illuminates when the controller is in Manual operation mode.
The following tables show the correspondence between symbols shown on the No.1 and
No.2 displays and alphabetic characters.
Figure 4: Omron Temperature Controller Display Symbols

M-55-02 SH Inline Heater System Manual
Revision – Date: 00 – 06/07/07
13
OPERATIONS for E5CN (Continued):
Using the keys:
This section describes the basic functions of the front panel keys.
Level Key: Press this key to move between setting levels. The setting level is selected in the following order:
operation level: adjustment level, initial setting level, communications setting level.
Mode Key: Press this key to change parameters within a setting level. The parameters can be reversed by holding
down the key (moving one per second in reverse order).
Up Key: Each press of this key increments the value displayed on the No. 2 display or
advances thesetting. Holding the key down speeds up the incrementation.
Down Key: Each press of this key decrements values displayed on the No. 2 display or reverses the setting.
Holding the key down speeds up the incrementation.
Selecting Menu Levels:
The following section describes how to access the various menu levels in the Omron controller.
Operations Level: Press the mode key.
Adjustment Level: Press and hold the level key for at least 1 second.
Initial Setting Level: Press and hold the level key for at least 3 seconds.
Protect Level: Press and hold the level key and the mode key simultaneously for at least 3 seconds.
Advanced Function Setting Level: (Note: in order to access this level, the ICPt setting in the protect level must be set at
0) Index through the initial setting level and adjust the AmoV setting to “-169”.

M-55-02 SH Inline Heater System Manual
Revision – Date: 00 – 06/07/07
14
OPERATIONS for E5CN (Continued):
Mode Parameter Settings:
The Omron E5CN temperature controller has been programmed prior to shipment, so no additional programming is
normally necessary. The table below shows the various controller settings for this unit when properly configured to operate
the TYTAN inline heater.
The selections in bold indicate settings that have been changed from the original factory default for operation with the
TYTAN inline heater.
Level Parameter
Description Setting
Operations
Level R-S Run – Stop selection RUN
AL-1 Alarm value 1 100°C
AL-2 Alarm value 2 90°C
Adjustment
Level LAdJ Adjustment level
At Autotune execute OFF
INS Temperature input shift 0.0
P Proportion band 80**
I Integral time 233**
D Derived time 40**
SPRt SP ramp set value OFF
OL-H MV upper limit 100.0
OL-L MV lower limit 0.0
Initial Setting
Level IN-t Input type 7
d-U Temperature units selection C
SL-H Set point upper limit 95
SL-L Set point lower limit 0
CNtL Control type (PID on/off) Pid
S-HC Control type (standard or heating/cooling) StNd
St Self-tune OFF
PtRN Program pattern OFF
CP Control period 1
OREV Operation direction (direct/reverse) OR-R
Alt1 Alarm 1 type 8
Alt2 Alarm 2 type 8
AMOV Advanced function level Set to -169
** The P, I and D values may change following the execution of Auto-tune.
Table 3: Omron E5CN Parameters

M-55-02 SH Inline Heater System Manual
Revision – Date: 00 – 06/07/07
15
OPERATIONS for E5CN (Continued):
Level Parameter
Description Setting
Advanced
Function Setting
Level
INIt Parameter initialize OFF
MSPU Multiple set point uses OFF
SPRU Set point ramp time unit M
AL IN Alarm 1 output contacts N-C
ALH1 Alarm 1 hysteresis 0.1
AL2N Alarm 2 output contacts N-C
ALH2 Alarm 2 hysteresis 0.1
ALFA 2-PID constant 0.65
INF Input digital filter 0.0
PVAd Additional PV display OFF
O-dP MV display OFF
Ret Automatic return of display mode OFF
A1Lt Alarm 1 latch OFF
A2Lt Alarm 2 latch OFF
PRLt Protect level move time 3
SERO Output input error OFF
CJC Cold junction compensation method ON
COLR PV display color Red
PV-b PV stable range 5.0
A1ON Alarm 1 on delay 0
A2ON Alarm 2 on delay 0
A1OF Alarm 1 off delay 0
A2OF Alarm 2 off delay 0
IstP Input shift type INS1
MVSE Additional MV for stop/error OFF
AMAd Auto/manual switching function OFF
Rt Robust tuning OFF
Out1 Control output 1 assignment O
ALM1 Alarm 1 output assignment ALM1
ALM2 Alarm 2 output assignment ALM2
CSEL Display text switch ON
CMOV Move to calibration level 0
Protect Level OAPt Operation/adjustment protection 0
ICPt Initial/communication protection 0=unlocked
WtPt Setting change protection OFF
PRLP Move to protect level 0

M-55-02 SH Inline Heater System Manual
Revision – Date: 00 – 06/07/07
16
OPERATIONS for E5CN (Continued):
Changing Primary Set Point:
1. The process Set Point can be changed in thenormal display mode.
2. Press the up and down arrow keys to select the desired setting.
After changing the process set point (SP-0) on the Omron controller, you must manually adjust the SP2 setting on the
Future Design over-temperature control. See OPERATIONS Over-Temperature Controller FDC-L91 section.
High Alarm:
The Omron E5CN temperature controller incorporates an independent high-temperature alarm. Alarm 1 (AL-1) prevents
heater operation above a preset maximum temperature that may harm the process and potentially the tank material. If the
process temperature exceeds the preset high alarm value, the heater will be disengaged and the audibly alarm will sound.
The temperature controller will activate once the process temperature exceeds the set point by the preset value. The
factory setting of this alarm temperature is 248°F (120°C).
The high alarm value can be adjusted to a lower setting through the operations level.
1. Press the mode key to enter the operations level.
2. Press the mode key to index through the operations level to the AL-1 setting.
3. Press the up or down key to adjust AL-1 to the desired setting.
4. Press the mode key to index through the operations level to the AL-2 setting.
5. The AL-2 setting is normally set at 10°C below AL-1. Press the up and down keys to adjust AL-2 to the desired setting.
6. Press and hold the level key for a minimum of three seconds to return to the normal display.

M-55-02 SH Inline Heater System Manual
Revision – Date: 00 – 06/07/07
17
OPERATIONS for E5CN (Continued):
PID Tuning:
The Omron E5CN temperature controller incorporates the capability of automatically tuning the PID parameters (Auto-
Tuning) to fit the characteristics of the process. The optimum PID parameters are automatically set by forcibly changing the
Manipulated Variable (MV) to calculate the characteristics (limit cycle method) of the control target. Depending on the auto-
tune level selected, AT-1 or AT-2, the controller will run this test at either 40% or 100% of the actual Process Set Point.
When the auto tuning is complete, the appropriate PID tuning parameters will be automatically installed into the non-volatile
memory of the temperature controller.
1. Turn on water supply and set the desired water flow.
2. Set the Process Temperature Set point to the desired value.
(See OPERATIONS; Changing Primary Set point,).
3. Press and hold the level key for a minimum of one second to enter the adjustment level.
4. Press the mode key to index through the adjustment level to get to the At settting.
5. Press the up or down arrow key to adjust the At value to oN.
6. Press and hold the level key for at least 3 seconds to return to the normal display.
7. Turn the ENABLE HEATER switch past the ON position to the RESET position, then release the switch, which will
move to the ON position. If all criteria for the various safety devices have been met, the heater will begin to heat.
8. When the process is complete, the appropriate PID tuning parameters will be installed and retained in the non-
volatile memory.

M-55-02 SH Inline Heater System Manual
Revision – Date: 00 – 06/07/07
18
OPERATIONS for SLC:
Safety Limit Controller (SLC) Model FDC-L91:
1. This over-temperature controller is located inside the electrical portion of the SH
heater. It uses a separate temperature sensor to monitor the temperature on the
surface of the heating elements.
2. This controller has two discreet set points:
SP2: This is the over-temperature cutoff setting, which is set for 135°F
(57°C).
HSP1: This is an element high-temperature alarm setting, which is
factory set at 145°F (63°C). Do not adjust this setting.
Programming:
To Change the SP2 set point on the FDC-L91 over-temperature controller, follow the following procedure:
Do not change any of the other settings in this controller.
1 ) Turn the “Enable Heater” switch to the Off position. Leave the “Control Power” switch in the On position.
2 ) Open the door to the control-portion of the unit.
3 ) Identify the over-temperature controller, tagged 1SLC.
4 ) Press the Index key ( ) twice until “SP2” is highlighted.
5 ) Using the “” or “” buttons, adjust the SP2 value until it is 18°F (10°C) higher than the set point on the temperature controller.
Note: Do not change any other settings on this controller.
6 ) Close the door to the control portion of the enclosure.
7 ) Follow the procedure for “System Startup” (page 17) to start the heater.
Caution: When the enclosure door is open, be careful not to touch the electrified components inside. To avoid shock
hazard, this procedure should only be performed by qualified personnell.
Figure 5: Over-temperature
controller

M-55-02 SH Inline Heater System Manual
Revision – Date: 00 – 06/07/07
19
Section 5: Operation
System Start-Up:
After completing installation, the following calibrations must be performed before operating the heater.
1) Check the switch positions on the control interface (if supplied).
Caution: All switches should be in the off position.
2) Turn on process gas/liquid at its supply source.
3) Engage electrical supply at customer's source. Ensure that OPTIONAL circuit breaker(s) are in the "ON" position.
4) Engage the "CONTROL POWER" switch on the control panel. At this time the temperature controller and all optional displays will
come on.
Note: Temperature controller set point should be set to "0" at this time to prevent accidental heater engagement
during calibration procedures. Reference temperature controller section if required.
Normal Operation:
Normal operation of the SH inline heater system will consist of the following steps:
1) Initiate process flow.
2) Make sure that the “Off-On-Reset” switch is in the “Off” position.
3) Energize the unit by turning on the Electrical Disconnect.
4) Turn the “Control Power” switch to the “On” position.
5) Adjust the desired set point on the temperature controller.
6) Turn the “Off-On-Reset” switch all the way to the “Reset” position and release to the “On” position. If all safety circuit requirements
are satisfied, the heaters will operate at this point.
Note: If the temperature set point is changed, it is necessary to recalibrate the temperature controller.
Shut Down Procedure:
1) Turn “Off-On-Reset” switch to “Off”.
2) Allow heater to cool below 95°F (35°C).
3) Turn Main Power OFF.
Section 6: Service and Maintenance:
Maintenance:
Normal maintenance of SH inline heaters consists of the following:
1) Replace the heater control relays and fan after approximately 24-30 months of use. Actual life expectancy varies with application
conditions such as hours of operation, control tuning parameters, applied voltage and amperage.
2) The Solid State Relay fan should be replaced and the heat sink is to be cleaned every 24 months.

M-55-02 SH Inline Heater System Manual
Revision – Date: 00 – 06/07/07
20
Service Policy:
Process Technology supports its product line with a strong technical support and field service program. If SH inline heater fails to
perform properly, follow the outlined steps for resolution.
Note: If the unit was damaged in transit, contact the freight carrier directly. Process Technology is not responsible
for shipping damage.
1) Verify connections and program parameters.
2) Contact the Process Technology Technical Service Group. When placing this call, please have available the model number
and serial number of the unit (located on the system tag), information about the application of the equipment, and information
regarding the chemical constituents of the process fluid. The Service Technician will evaluate the situation and determine a
course of action for troubleshooting and repair.
3) If the Technician determines that the unit should be returned to the factory for evaluation, a Return Material Authorization
(RMA) Number will be issued. A return will not be accepted without prior authorization.
Note: Equipment must be returned to Process Technology within 30 days of return authorization.
Typically, the SH inline heater will not have been exposed to chemicals. However, Process Technology personnel are instructed to
handle any returned equipment as if it contains residual chemicals. A package containing returned equipment will not be opened
until chemical information is received. Therefore, Process Technology requires that the following procedures be followed for all
returns, whether or not they are likely to contain chemical residues.
To protect the safety of Process Technology’s workers and any others that may come in contact with this equipment in the course
of transport, evaluation, and repair, Process Technology requires that these practices be followed in returning the equipment to the
factory:
1) Rinse the equipment until it is free of any chemical residues and drain any fluid from elements and piping. This is required for
safe transport and handling of the equipment.
2) Wrap the unit in plastic and secure. Make sure that it does not leak. (Process Technology is not responsible for damage
caused by leakage during shipping.)
3) Carefully package the unit for shipment.
4) Indicate the type of chemical (this includes DI Water) that was in use at the time of failure. Include this information on the
packing slip or place the information on the outside of the box. Process Technology will not risk exposure of its personnel to
unknown chemicals. A return will not be evaluated until chemical information is received.
5) Clearly mark the outside of the box with the RMA number.
6) Ship the component to Process Technology via prepaid freight.
Upon receipt of a returned unit, Process Technology will follow these steps:
1) The equipment will be carefully unpacked, inspected and cleaned, and an evaluation will be done.
2) A Process Technology technician will contact the customer with information regarding the scope of work to be performed, the
cost, and the amount of time needed.
3) After a purchase order and authorization to perform the repair are received, the repairs will be completed and the unit
returned.
4) If the returned unit has been used in a chemical application and Process Technology determines that it is not repairable, the
equipment will be returned at Process Technology’s expense to the customer site for proper disposal.
Table of contents
Popular Heater manuals by other brands

Bimar
Bimar SE1600 Instruction booklet

Daikin
Daikin RDXYQ8T7V1B installation manual
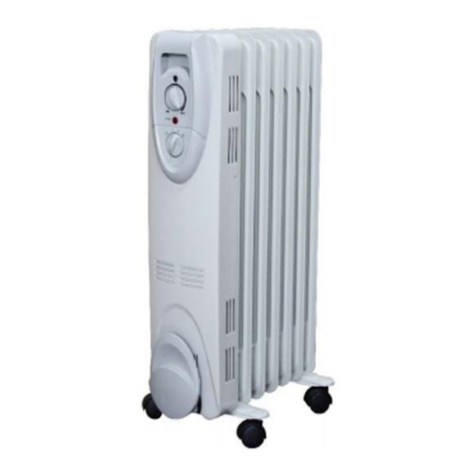
anko
anko HD904-11 user manual

Grill'D
Grill'D Soul Steel Retro Short Installation and operation manual
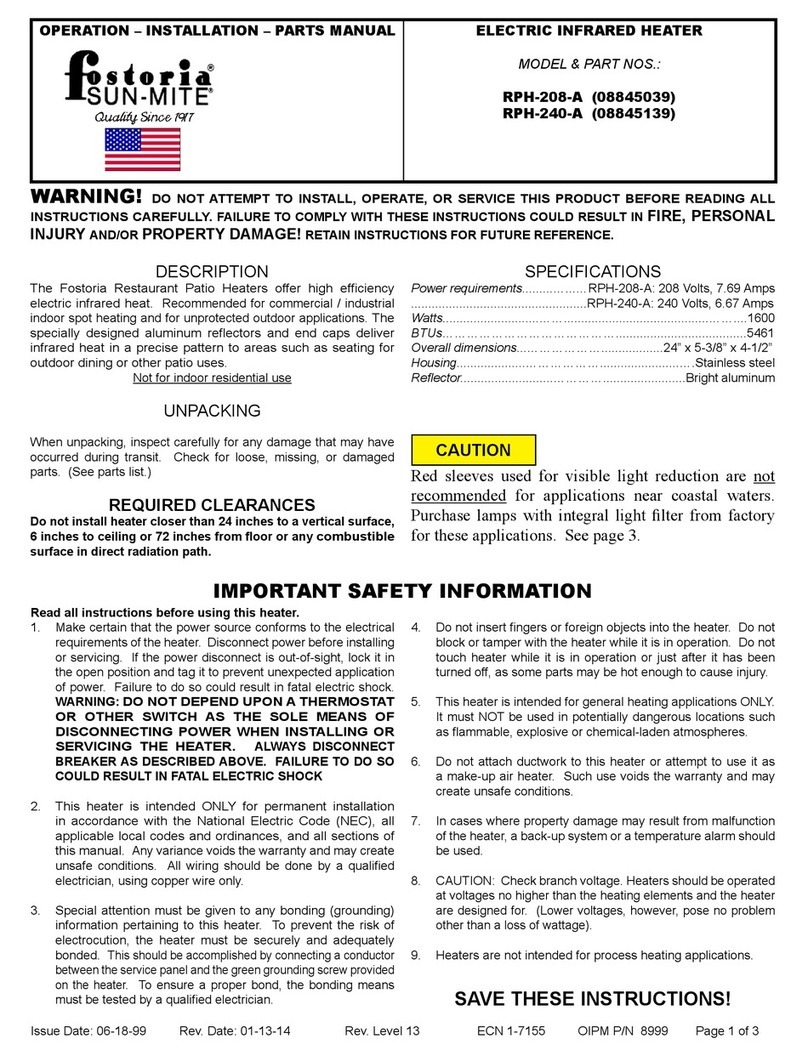
Fostoria
Fostoria SUN-MITE RPH-240-A Operation-Installation-Parts Manual
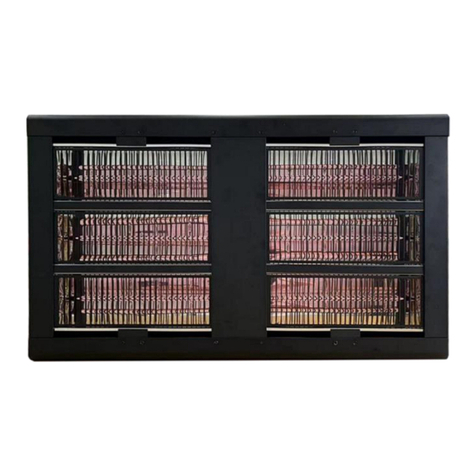
Herschel
Herschel Vulcan 6S Installation & operating instructions
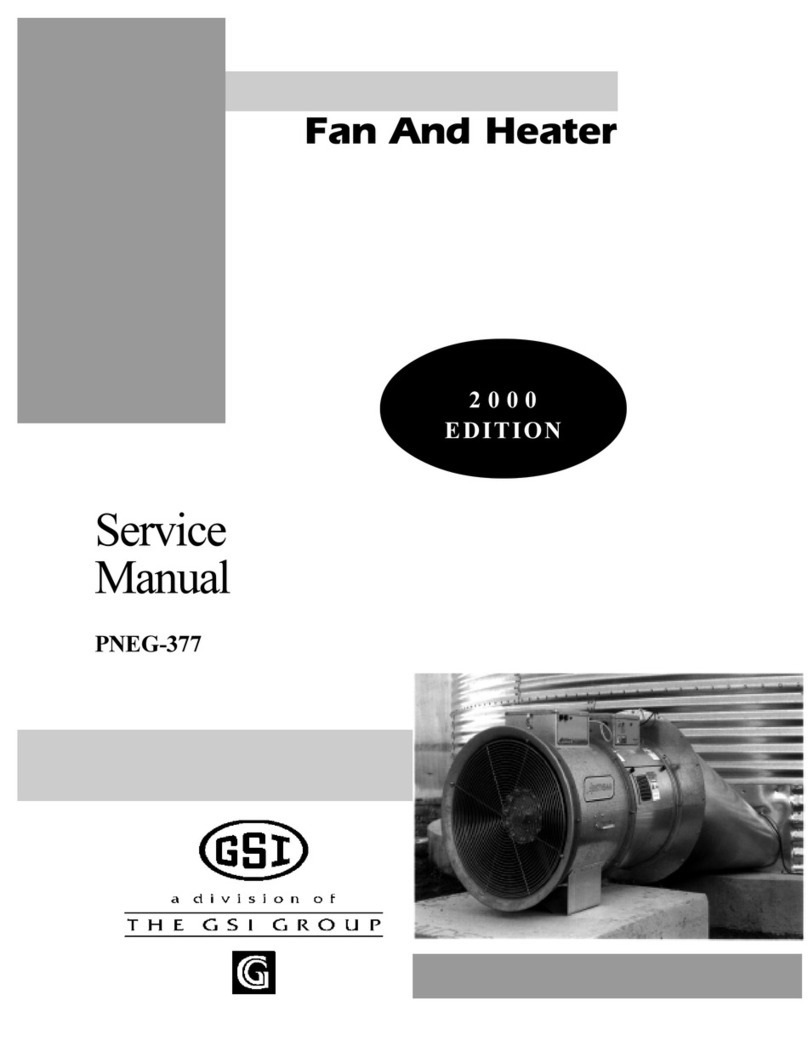
GSI Group
GSI Group PNEG-377 Service manual
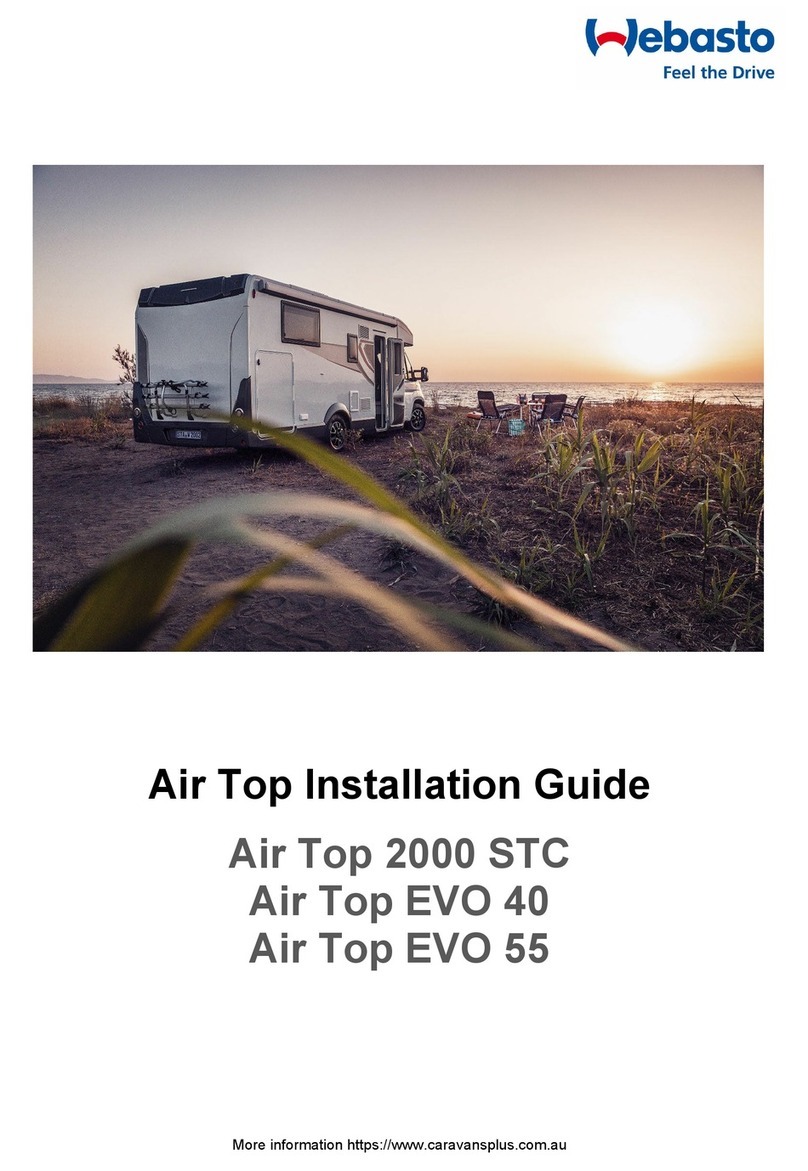
Webasto
Webasto Air Top 2000 STC installation guide

Eterna
Eterna OH211T installation instructions

SINOTECH
SINOTECH GD440 manual
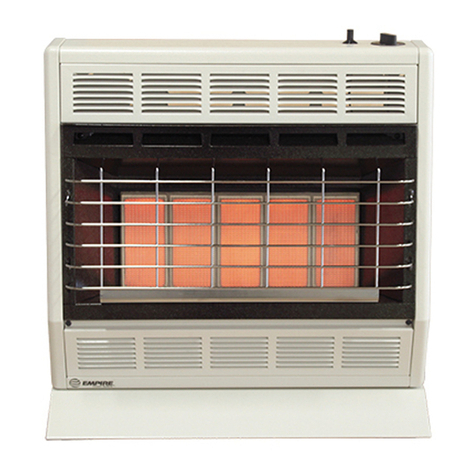
Empire Heating Systems
Empire Heating Systems SR-6-4 Installation instructions and owner's manual
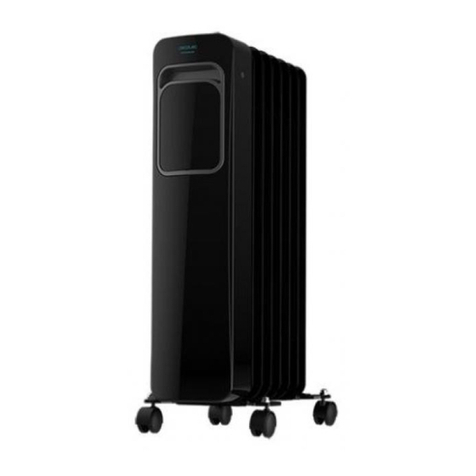
cecotec
cecotec READYWARM 7000 instruction manual