Protronic RZ3 User manual

Operating Manual
Hold-open system control
RZ3 / RZ4
manual, motorised
Protronic Innovative
Steuerungselektronik GmbH
Grimmaische Straße 92
04828 Bennewitz OT Pausitz
info@protronic-gmbh.de
Tel.: 034383 63 15-0
Fax: 034383 63 15-50
www.protronic-gmbh.de

Operating Manual RZ3/4
Page 2of 32 Protronic Innovative Steuerungselektronik GmbH
Grimmaische Str. 92, D-04828 Bennewitz, district Pausitz
Operating Manual RZ3, RZ4 Version 06-DE
Protronic Innovative Steuerungselektronik GmbH
Grimmaische Str. 92
04828 Bennewitz district Pausitz
Tel. +49 34383 6315-0
Fax +49 34383 6315-50
www.protronic-gmbh.de

Operating Manual RZ3/4
Page 3of 32 Protronic Innovative Steuerungselektronik GmbH
Grimmaische Str. 92, D-04828 Bennewitz, district Pausitz
1. Table of contents
1. Table of contents......................................................................................................................... 3
2. About this guide........................................................................................................................... 4
2.1. Explanation of symbols......................................................................................................................4
3. General........................................................................................................................................ 5
3.1. For which products are these instructions valid? ...............................................................................5
3.2. Warranty ............................................................................................................................................5
4. Security........................................................................................................................................ 5
4.1. Intended use......................................................................................................................................5
4.2. Use contrary to the intended purpose................................................................................................5
4.3. Authorized personnel.........................................................................................................................5
4.4. Unauthorized personnel (unauthorized persons)...............................................................................6
4.5. Monthly function check / maintenance intervals.................................................................................6
4.6. Responsibility of the operator.............................................................................................................7
4.7. Protection and safety devices............................................................................................................8
4.8. Dangers .............................................................................................................................................8
4.9. After the fire .......................................................................................................................................9
4.10. Spare parts ...................................................................................................................................9
5. Product labeling........................................................................................................................... 10
5.1. Product and type designation.............................................................................................................10
5.2. Marking on the product ......................................................................................................................10
5.3. Technical data....................................................................................................................................10
5.4. Name and address of the manufacturer.............................................................................................11
6. Declaration of Conformity............................................................................................................ 12
7. General functional description..................................................................................................... 13
7.1. Overview of display and operating elements......................................................................................13
7.2. Power supply display field..................................................................................................................13
7.3. Functions ...........................................................................................................................................14
7.4. Display and control panel smoke control panel..................................................................................15
7.5. Display panel smoke control panel for conveyor termination.............................................................16
7.6. Display and control panel Triggering device ......................................................................................17
7.7. Reset horn .........................................................................................................................................18
7.8. Display and control panel Motor.........................................................................................................18
7.9. Function variant personal protection..................................................................................................20
7.10. Omnicompact function variant.......................................................................................................20
8. Signals to be observed................................................................................................................ 21
8.1. Acoustic signals.................................................................................................................................21
8.2. Visual signals.....................................................................................................................................21
8.3. Manual opening of the FAA................................................................................................................21
8.4. Manual closing of the FAA.................................................................................................................22
8.5. Motorized opening of the FAA............................................................................................................22
8.6. Relay function....................................................................................................................................23
8.7. Function of the DIL switches..............................................................................................................25
8.8. Function of the sliding jumpers for the light barriers 1 and 2..............................................................27
9. Overview operating foil RZ3/4 - with motor ................................................................................. 29
10. Overview operating foil RZ3/4 - without motor ............................................................................ 30
11. Assembly and installation............................................................................................................ 31
12. Clarification of terms.................................................................................................................... 31

Operating Manual RZ3/4
Page 4of 32 Protronic Innovative Steuerungselektronik GmbH
Grimmaische Str. 92, D-04828 Bennewitz, district Pausitz
2. About this guide
The hold-open system RZ3 / RZ4 control unit is also referred to as a system or plant in the following.
These operating instructions are considered an integral part of the product and must be stored in such
a way that rapid access is possible at all times.
Security
The personnel must have read and understood the operating instructions before starting any work. It
contains important information that protects the operator against possible dangers or explains
interrelationships. Observe the warning and safety notes.
Illustrations
The illustrations are for basic understanding and may differ from the actual design depending on the
system.
2.1. Explanation of symbols
Safety instructions
Warning and safety instructions in this manual are identified by special symbols.
CAUTION
Indication of possibly dangerous situations, the consequence of
which may be slight (reversible) injuries.
WARNING
Indication of possibly dangerous situations, the consequence of
which may be serious (irreversible) injuries or even death.
DANGER
Indication of immediately dangerous situations, the consequence of
which can be serious injury or even death if the situation is not
avoided.
NOTE
Reference to possibly dangerous situations, the consequence of
which may be damage to property or the environment.
Information / Recommendations
References to useful information and recommendations that serve
efficient as well as trouble-free operation.
Clarification of terms
In the section "Clarification of terms", useful terms and definitions for the reader are explained.

Operating Manual RZ3/4
Page 5of 32 Protronic Innovative Steuerungselektronik GmbH
Grimmaische Str. 92, D-04828 Bennewitz, district Pausitz
3. General
3.1. For which products are these instructions valid?
Hold-open system control RZ3 / RZ4 manual, motorized
The hold-open system control RZ3 / RZ4 consists of an external control
module suitable for wall mounting with integrated power supply unit and
batteries (RZ3) or without power supply unit and batteries (RZ4). The control is
optionally equipped with a motor card.
3.2. Warranty
The warranty is described in the General Terms and Conditions of the manufacturer. Deviating
agreements require the contractual regulation in writing.
The limitation period for claims for defects can be extended by a
maintenance contract concluded with the manufacturer or with a
service partner authorized by the manufacturer. Wear parts are
excluded from this.
4. Security
4.1. Intended use
The hold-open system control RZ3 / RZ4 are exclusively intended for indoor operation of conveyor
system closures (in exceptional cases for automatic smoke barriers, fire doors and gates and flexible
fire curtains). See also general building authority approvals: abZ: Z-6.510-2627/-2626.
4.2. Use contrary to the intended purpose
Any use deviating from the intended use is considered misuse.
Other applications, inserts and modifications are not permitted for safety reasons for the protection of
the user and third parties and may impair safety and function.
4.3. Authorized personnel
Basically, a distinction is made between different qualifications of people involved with the system
during its product life cycles.
WARNING
Danger due to insufficient personnel qualification.
The system may only be operated or functionally tested by adequately qualified personnel.
Work reserved for specialist personnel may only be carried out by personnel authorized by the
manufacturer.

Operating Manual RZ3/4
Page 6of 32 Protronic Innovative Steuerungselektronik GmbH
Grimmaische Str. 92, D-04828 Bennewitz, district Pausitz
Operator
Operators are all persons who are at least 18 years of age and have been instructed in the operation
of the equipment by the manufacturer or an authorized representative. They must have read and
understood these instructions completely.
Operators are assigned the following tasks:
▪Operation of the system in other modes besides automatic mode
▪Operating the controls on the controller
▪Monthly function check
▪Partial elimination of malfunctions or initiation of measures to eliminate malfunctions.
Specialized personnel
Qualified personnel are all persons who have appropriate knowledge of hold-open systems due to
their professional training, professional experience and recent professional activity and who are
trained and authorized by the manufacturer to perform installation and maintenance work on the
control system. The qualified personnel must be qualified for this work due to their professional
training, experience and technical knowledge in the field of hold-open systems.
In addition to the operator's authority, the following tasks are assigned to the technical personnel:
▪Elimination of malfunctions that go beyond the operator's troubleshooting measures
▪Assembly work
▪Maintenance
4.4. Unauthorized personnel (unauthorized persons)
WARNING
Operation or other work on the system performed by unauthorized
persons can result in considerable danger to persons and even
death.
For example, an installation or conversion measure carried out by
unauthorized persons and thus improperly can result in malfunctions
of the system in the event of fire.
The manufacturer accepts no liability for damage caused by measures carried out by unauthorized
persons.
4.5. Monthly function check / maintenance intervals
A regular check of the function as well as maintenance of the system guarantee the reliable function of
the control module in case of fire and thus the safety of the building and persons.
Monthly function check (operator)
WARNING
If the system is damaged, the manufacturer or the authorized service
partner must be notified immediately in order to replace the damaged
parts. Otherwise, the safe functioning of the system in case of fire is
not guaranteed, which may result in serious injuries or even death.

Operating Manual RZ3/4
Page 7of 32 Protronic Innovative Steuerungselektronik GmbH
Grimmaische Str. 92, D-04828 Bennewitz, district Pausitz
The system must be subjected to a monthly function check. The operator must document the function
check in the log (see test logbook).
The following points must be examined:
▪Proper function (opening / closing)
▪Optional assemblies (e.g.: Safety contact strip, area light scanners, optical and acoustic signal
transmitters).
▪Visual inspection for damage (connections, housing, guide rails, end strip and fabric)
The function check is performed for the entire system (combination
of fire protection product and control components) and noted in the
corresponding log of the installed fire protection product.
Annual maintenance (qualified personnel)
The control module must be serviced at least once a year by qualified personnel authorized by the
manufacturer.
Maintenance must be documented in the maintenance log (see inspection log).
4.6. Responsibility of the operator
Operator
An operator is anyone who operates the plant for commercial or economic purposes or who allows
third parties to use it.
Operator duties
According to the Ordinance on Industrial Safety and Health, the operator of work equipment or
systems requiring monitoring (special attention is paid to the hazard moments of pressure, explosion
protection, fire protection and lifting of persons and goods) is responsible for their safe provision.
Among other things, the operator must ensure that (the list mentions the most important points and
does not claim to be exhaustive):
▪The equipment is only operated for its intended use
▪All persons who have to do with the system have been instructed in its safe handling and have
read and understood these instructions.
▪The system is only operated by instructed persons
▪The plant is always kept in technically perfect condition
▪Necessary inspection openings are available (e.g. for maintenance or repair) and all work on
the system can be carried out without restriction
▪Inspection and maintenance intervals specified by the manufacturer are adhered to and
documented
▪No conversion measures are carried out without first consulting the manufacturer
▪all performed modifications, any defects and repairs are documented
▪Damaged or defective parts are replaced immediately by personnel authorized by the
manufacturer
▪fire load free zones are maintained if necessary
▪all information and warning signs are visibly displayed on or near the equipment
Personnel involved in the installation, maintenance and repair of the system must:
▪have the appropriate training
▪always have access to the parts of the operating instructions that are relevant to them
▪Comply with applicable laws, standards and regulations
All national and international laws, standards and regulations, directives and codes of practice relevant
to the system and the place of installation must be complied with, even if they are not expressly
mentioned here.

Operating Manual RZ3/4
Page 8of 32 Protronic Innovative Steuerungselektronik GmbH
Grimmaische Str. 92, D-04828 Bennewitz, district Pausitz
Instruction / supervision of the operators
The operator must instruct the personnel regularly and always ensure quick access to these operating
instructions.
The safe work of the operators must be checked by the operator at sufficiently recurring intervals.
4.7. Protection and safety devices
WARNING
Risk of serious injury
- Never override protection and safety devices
Acoustic signal generator
The acoustic signal generator indicates the closing of the system.
Optical signal transmitter (optional)
The optical signal generator (flashing light) indicates the closing of the system.
Language module (optional)
In addition to the acoustic signal transmitter, the voice module indicates the closing process of the
system. An individual recorded voice output is emitted through a loudspeaker.
Monitoring clamping area (optional)
The monitoring of the closing area (e.g. light barriers, proximity switches) is used to detect the free
area.
4.8. Dangers
Even with proper installation and proper condition of the control unit, not all danger points on the
system can be covered. The following points out the residual dangers.
Electric current
DANGER
Danger to life due to electric current
- Work on the system may only be carried out by qualified personnel.
- Never bypass fuses or bypass protective devices.
- Opening of control unit housings only by qualified personnel
- Before opening the control unit housing, disconnect it from the
power supply and secure it against being switched on again.
- Keep moisture away from electrical parts.
Risk of danger from personnel
Increased risk of operator danger exists:
▪if children, elderly or disabled persons can operate the equipment,
▪when it is not possible to teach, train or supervise the operators,
▪if it is not possible to select persons authorized to operate the equipment,
▪when the number of people using the facility is very high,
▪for modifications to the product
No modifications, such as additions or conversions, may be made to the system without the prior
approval of the manufacturer. Any unauthorized structural or operational modification will invalidate the
operating permit.

Operating Manual RZ3/4
Page 9of 32 Protronic Innovative Steuerungselektronik GmbH
Grimmaische Str. 92, D-04828 Bennewitz, district Pausitz
4.9. After the fire
After a fire, the equipment must be inspected for damage by qualified personnel if the equipment in
the affected fire area was exposed to the influence of fire or smoke.
Contact the manufacturer or a maintenance partner authorized by
the manufacturer immediately.
4.10. Spare parts
WARNING
Risk of injury due to the use of incorrect spare parts!
The use of incorrect, faulty spare parts or spare parts not approved
for the equipment may result in danger to personnel, malfunction or
total failure of the equipment.
NOTE
The use of non-approved spare parts will void the manufacturer's
warranty.
Obtain the spare parts from the manufacturer (see 5.4.) or customer service.

Operating Manual RZ3/4
Page 10 of 32 Protronic Innovative Steuerungselektronik GmbH
Grimmaische Str. 92, D-04828 Bennewitz, district Pausitz
5. Product labeling
5.1. Product and type designation
Product designation (depending on the version):
▪Hold-open system control RZ3 (manual / motorized)
▪Hold-open system control RZ4 (manual / motorized)
5.2. Marking on the product
On the cover of the terminal box there are the following designations:
▪System and type designation: smoke control panel RZ3 (RZ4)
▪Manufacturer
▪Input voltage
▪Current consumption
▪Output voltage
▪Power output
▪Year of manufacture
▪CE marking
▪Ü marking
5.3. Technical data
The technical data of the equipment are given in the corresponding
test book.
Power supply characteristics MC-EV1 (RZ3):
Input voltage
▪Nominal value AC 230 V
▪Permissible range 198...253 V
Mains frequency
▪Nominal value 50/60 Hz
▪Permissible range 47...63 Hz
Environmental conditions
▪Ambient temperature 0°C ... 35°C
▪Rel. humidity 95 %
Input current at 230V
▪Nominal value at no load 35 mA
▪Nominal value at 1.0 A load 370 mA
▪Nominal value at 1.8 A load 510 mA
▪Inrush current max. 10
Output current
▪Control loop 2:
oBattery charging current max. 450 mA

Operating Manual RZ3/4
Page 11 of 32 Protronic Innovative Steuerungselektronik GmbH
Grimmaische Str. 92, D-04828 Bennewitz, district Pausitz
▪Control loop 1:
oConsumer current 1,765 A
This is composed of:
▪Self-consumption 60 mA
▪Terminal board + control board 180 mA
▪Motor board 25 mA
▪External consumers max. 1.5 A
connected battery
▪2xHP 2.2-12 (2.2 Ah 12 V)
▪or 2xHP 7.2-12 (7.2 Ah 12 V)
Only VdS-approved, maintenance-free batteries are used for hazard detection systems (in accordance
with printed matter VdS-2140).
Reporting thresholds
▪Mains fault Mains input voltage < 80 V AC
(a mains fault causes automatic switching from mains operation to battery operation).
▪Reset mains fault Mains input voltage > 85 V AC
▪(when this threshold value is reached -network return-, the system automatically switches from
battery operation to mains operation).
▪Battery fault UBat < 24 V
(If jumper J1 on the RZ3-MC-KL is set to ON, a trip occurs).
▪Deep discharge protection UBat < 21.8 V
Charging characteristics as a function of temperature
Housing RZ3: Bopla Combicard Plus 7000
RZ4: Bopla Combicard Plus 6000
Degree of protection IP64
Characteristics of smoke detection panel MC-Z (RZ3):
The MC-Z board, which can be plugged into the power supply, evaluates the line current of the fire
detectors and transmits the trigger signal to the control board in the event of a fault or alarm.
Triggering at:
▪Alarm I > 12 mA
▪Interruption I < 3.0 mA
▪Short circuit current max. 45 mA
▪Quiescent current (terminating resistor = 4k7) I = 4.5 mA
▪Line voltage ULin = 20.5...21.3 V
5.4. Name and address of the manufacturer
Protronic GmbH
Grimmaische Str. 92
D-04828 Bennewitz
Internet: www.protronic-gmbh.de
Tel: info@protronic-gmbh.de
Tel.: 034383 63 15-0
Fax: 034383 63 15-50

Operating Manual RZ3/4
Page 12 of 32 Protronic Innovative Steuerungselektronik GmbH
Grimmaische Str. 92, D-04828 Bennewitz, district Pausitz
6. Declaration of Conformity

Operating Manual RZ3/4
Page 13 of 32 Protronic Innovative Steuerungselektronik GmbH
Grimmaische Str. 92, D-04828 Bennewitz, district Pausitz
7. General functional description
The following chapter provides an overview of the display and operating elements, characteristic data
and controlled modules of the RZ3 hold-open system for conveyor system closures.
NOTE
For detailed information about connections of the RZ3 / RZ4,
please refer to the wiring diagrams.
7.1. Overview of display and operating elements
The RZ3 hold-open system contains the following display and control panels:
▪Power supply (1)
▪Smoke control panel (2)
▪Release device (3)
▪Horn Reset (4)
▪Motor (5)
Figure 1 - Display and operating elements of the hold-open system (control) type RZ3
7.2. Power supply display field
1
2
3
T
h
e
r
e
i
s
o
n
e
i
n
p
u
t
f
o
r
e
x
t
e
r
n
a
l
c
l
o
s
i
n
g
.
T
h
e
s
e
c
o
n
5
1
2
3
Figure 2 - Power supply
4

Operating Manual RZ3/4
Page 14 of 32 Protronic Innovative Steuerungselektronik GmbH
Grimmaische Str. 92, D-04828 Bennewitz, district Pausitz
The "Power supply" display field contains the following optical signals (LED):
▪Operation (mains) (1)
▪Fault (collective fault power supply) (2)
▪Network fault (3)
7.3. Functions
Disturbances:
In the event of a mains fault, both the LED fault (2) and the LED mains fault (3) light up. In the event of
a battery fault, only the LED fault (2) lights up.
A mains fault is indicated when the mains supply (230VAC) falls below a value that allows the
batteries to be charged. A battery fault is indicated when the battery voltage drops below a value of
approx. 24.0V during the active battery test (approx. every 70s), during which the battery is briefly
loaded.
New value alert:
When a fault occurs, the internal acoustic signal is activated. At the same time, the collective fault
output (X1:25/26/27) is switched.
The acoustic signal can be reset by pressing the horn button:
be switched off.
At the same time, the collective fault output is also reset. If a new fault occurs, the horn and the
collective fault output are activated again.
The mains fault output and the fault display remain switched on until the fault is eliminated or until the
next successful battery test is performed. If the battery is discharged, the fault indicator remains
switched on until the battery has reached a state of charge greater than 24.5V.
NOTE
If the battery charge level is too low, a controlled closing sequence
with possible freeing of the conveyor system cannot be
guaranteed.
Battery:
The batteries used are maintenance-free lead-acid batteries that have been tested and approved by
VdS for hazard alarm systems. The service life of 5 years specified by the battery manufacturer refers
to an ambient temperature of 20°C. The service life is reduced at higher temperatures. At higher
temperatures, the service life is reduced. At an ambient temperature of 20°C, depending on the load
on the system, the ambient temperature of the battery is 30°C-35°C and thus the service life is 3-4
years. At an ambient temperature of 45°C, the service life is already less than 2 years. The battery is
protected against deep discharge. If the battery voltage falls below approx. 21.8V, the control is
switched off. Charging takes place with a charging curve controlled via ambient temperature.

Operating Manual RZ3/4
Page 15 of 32 Protronic Innovative Steuerungselektronik GmbH
Grimmaische Str. 92, D-04828 Bennewitz, district Pausitz
7.4. Display and control panel smoke control panel
Figure 3 - Smoke control panel
The "Smoke control panel" display and control panel contains the following visual signals
(LED) and operating elements (buttons):
"Operation" - optical signal (1)
LED "Operation" (green) indicates that the fire alarm loop is correctly connected, i.e. there is no short
circuit, no open circuit and no fire alarm.
Trigger reset - pushbutton (3)
Pressing the button resets the fire alarm if the alarm conditions are no longer present.
The RZ3 has two different ways of triggering a fire.
Var.1: Triggering by fire alarm loop or button Test This triggering is stored by
the control system. The optical signal Operation (1) goes out, the red LED in
the control panel Triggering device Triggering lights up and the contact
Fire alarm (X1:6/7/8) switches.
Var. 2: Triggering via input X1:23/24. In this case, the optical signal Operation (1)
does not go out, the red LED in the control panel Triggering device
Triggering lights up and the contact Fire alarm (X1:6/7/8) does not switch. This
function is used to link several RZ3. In this case, the fire alarm is reset at the
control panel triggered by the fire alarm loop. The optical signal Operation (1)
does not light up on this control!
WARNING
Test - Push button (2)
Pressing the button simulates a fire alarm and triggers the
closing process. If conveyor technology is used (optional), all
required conveyor technology is also switched off.
1
2
3

Operating Manual RZ3/4
Page 16 of 32 Protronic Innovative Steuerungselektronik GmbH
Grimmaische Str. 92, D-04828 Bennewitz, district Pausitz
7.5. Display panel smoke control panel for conveyor termination
Figure 4 - Smoke control panel
The "Smoke control panel for conveyor closure" display panel contains the following visual
signals (LED):
Opened (1)
LED " " indicates that the movable sealing element is open and the associated control element is
activated accordingly.
Closed (2)
LED " " indicates that the movable sealing element is closed and the associated control element is
activated.
Scraper basic position (3)
LED indicates that the clearing arm (if a conveyor clearing system is installed) is in home position.
Closing range malfunction (4)
LED "!" indicates that the closing range of the isolation is occupied for longer than 120s, there is a
short circuit against +24V or the monitoring of the light barrier is disturbed.
NOTE
When the light barrier inputs are not in use, they must be bridged
with the relevant slide switch.
Closed area Free (5)
LED indicates that the closing area of the partition is free, e.g. in the case of monitoring by light barrier.
1
2
3
4
5

Operating Manual RZ3/4
Page 17 of 32 Protronic Innovative Steuerungselektronik GmbH
Grimmaische Str. 92, D-04828 Bennewitz, district Pausitz
7.6. Display and control panel Triggering device
Figure 5 - Release device
The "Triggering device" display and control panel contains the following optical signals (LED)
and buttons:
"" - Closing - optical signal and control element (1)
Button - manual closing initiates controlled closing process without activating emergency power.
LED closing lights up during the closing process.
Remote closing - optical signal (2)
LED "" - remote closing indicates active closing command by remote control (e.g. by conveyor
control or actuation of the remote pushbutton)
"" - Open - control element (3)
Button - Open resets manual closing and starts the opening procedure.
Triggering - optical signal (4)
LED Triggering lights up in case of: Fire alarm, short circuit or interruption of the fire alarm loop.
The "Test" button has been pressed.
Operation - optical signal (5)
LED -operation lights up when the voltage supply of the controller unit is switched on.
Fault - optical signal (6)
LED "!" -fault indicates general error of the CPU.
1
2
3
4
5
6

Operating Manual RZ3/4
Page 18 of 32 Protronic Innovative Steuerungselektronik GmbH
Grimmaische Str. 92, D-04828 Bennewitz, district Pausitz
7.7. Reset horn
WARNING
Fire alarm, electrical fault / danger to life
Do not continue working when the horn sounds an acoustic
warning signal.
Stop work / Use escape routes
Fire alarm / malfunction
If the internal horn sounds, there may be danger to life. The fire alarm has been triggered or there is a
technical malfunction. Follow the emergency plan in case of fire!
Acoustic signal
The internal horn sounds in the following cases:
▪Fire alarm
▪Power supply failure
▪Malfunction of the closing edge monitoring
▪Control malfunction
Figure 6 - Reset horn
Horn reset - control element (1)
The "Reset horn" control panel contains the following control element (button):
The button Reset horn switches off the internal horn, e.g. after a fire alarm. At the same time, the
collective fault message (K4 X1: 25, 26, 27) is reset. This is a new value alarm. A newly occurring fault
switches the horn on again. The visual indication of the fault remains until the fault is eliminated.
7.8. Display and control panel Motor
(RZ3, RZ4 motorized)
The "Motor" display and control panel contains the following optical signals (LED) and
buttons:
Figure 7 - Motor control panel
1
1
2
3
4

Operating Manual RZ3/4
Page 19 of 32 Protronic Innovative Steuerungselektronik GmbH
Grimmaische Str. 92, D-04828 Bennewitz, district Pausitz
- Motor off - optical signal and control element (1)
Pushbutton - Motor off interrupts the power supply to the drive. The associated LED remains lit
until this state is reset by pressing the button.
- Reset motor off - Control element (4)
When the button is pressed, the "Actuator off" state is reset.
"" Motor on - optical signal (2)
LED "Motor on" indicates that the motor is switched on for opening.
"!" - motor fault - optical signal (3)
LED "Motor fault" indicates that the motor is in overload. Simultaneously with this indication, the signal
"Motor off" is set.

Operating Manual RZ3/4
Page 20 of 32 Protronic Innovative Steuerungselektronik GmbH
Grimmaische Str. 92, D-04828 Bennewitz, district Pausitz
7.9. Function variant personal protection
The personal protection function variant is activated via the DIL switch DIL 3 in the OFF position.
The mode of operation to the "web-bound conveyor variant" differs as follows:
There is one input for external closing. The second input is used for an optional contact strip for
monitoring the closing area. The "Closed" output 35/36 is fed back to input 60/61, which means that
only one light barrier input is available for monitoring the closing area with a light barrier.
The stop function of the optional contact strip is switched off when the "Closed" limit switch is reached,
so that the closure can close completely.
The indicator (3) in the standard version used as "scraper in basic position" (Fig. 4 Smoke control
panel) lights up when the contact strip is not actuated.
The closing of the closing device can be interrupted at any time both by the occupied light barrier and
by the triggered contact strip. The closing process is not continued until the occupancy of the light
barrier and/or the triggering of the contact strip has ended.
If a fault is detected in the light barrier or the contact strip before a fire alarm is triggered, this is
indicated acoustically and visually. If a fire alarm is subsequently triggered, the faulty monitoring
device concerned is ignored and the closing device is closed.
See also subitem 8.7 Function of the DIL switches.
7.10. Omnicompact function variant
The Omnicompact functional variant is used for the conveyor system closures and fire protection
closures of the Omnicompact type.
The mode of operation differs only slightly from the mode of operation of the standard RZ3 / RZ4.
There is one input for external closing. The second input is used for an optional contact strip for
monitoring the closing area. The "Closed" output 35/36 is fed back to input 60/61, which means that
only one light barrier input is available for monitoring the closing area with a light barrier.
The stop function of the optional contact strip is switched off when the "Closed" limit switch is reached,
so that the closure can close completely.
The indicator (3) in the standard version used as "scraper in basic position" (Fig. 4 Smoke control
panel) lights up when the contact strip is not actuated.
Pushbuttons "Manual opening" (3) and "Manual closing" (1) (Figure 5. "Release device") are switched
in the so-called "dead man's mode". This means that the gate opens / closes only as long as the
button is pressed. In order to ensure this function, automatic opening must of course not be switched
on. The jumper that may have been installed for this purpose at the "Remote opening" input 68/69 on
the MC-MABM motor control board must be removed.
This manual suits for next models
1
Table of contents
Popular Control System manuals by other brands
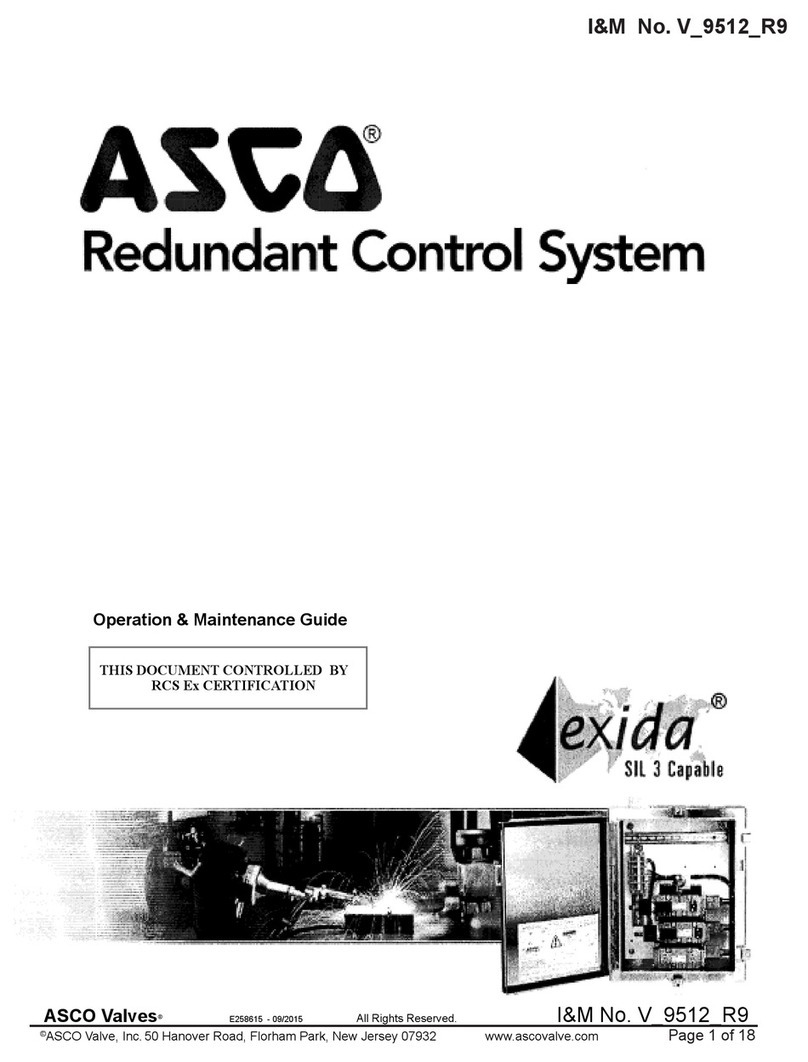
Asco
Asco RCS Operation & maintenance guide

Fasel Elektronik
Fasel Elektronik FCU-EXT-APP-CONTROL Installation
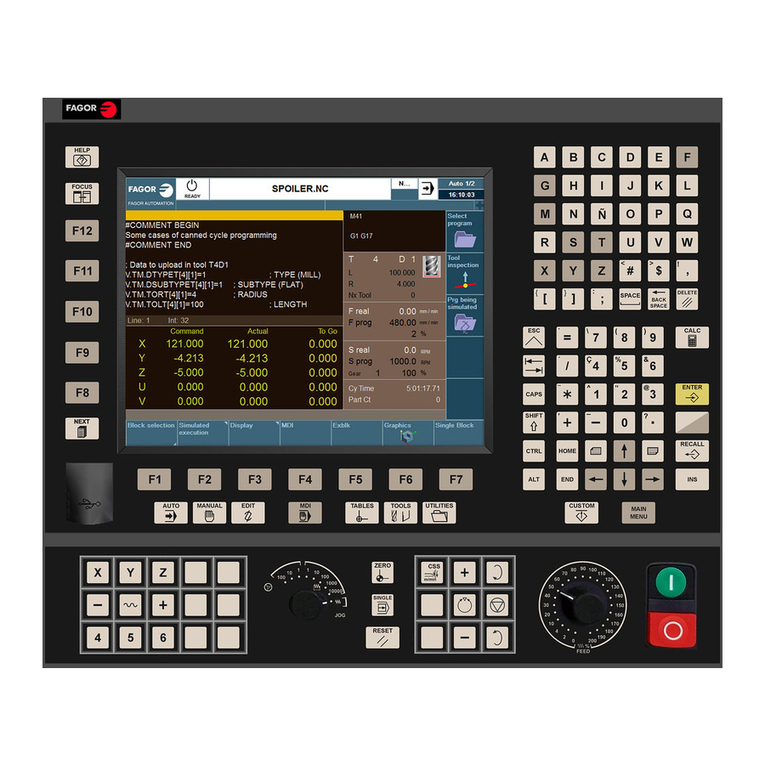
Fagor
Fagor CNC 8060 Users Quick Reference
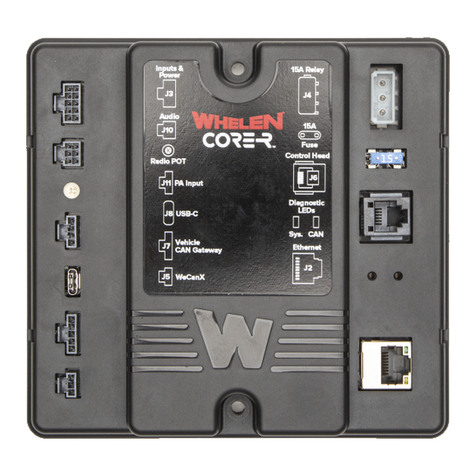
Whelen Engineering Company
Whelen Engineering Company Core R C399R manual
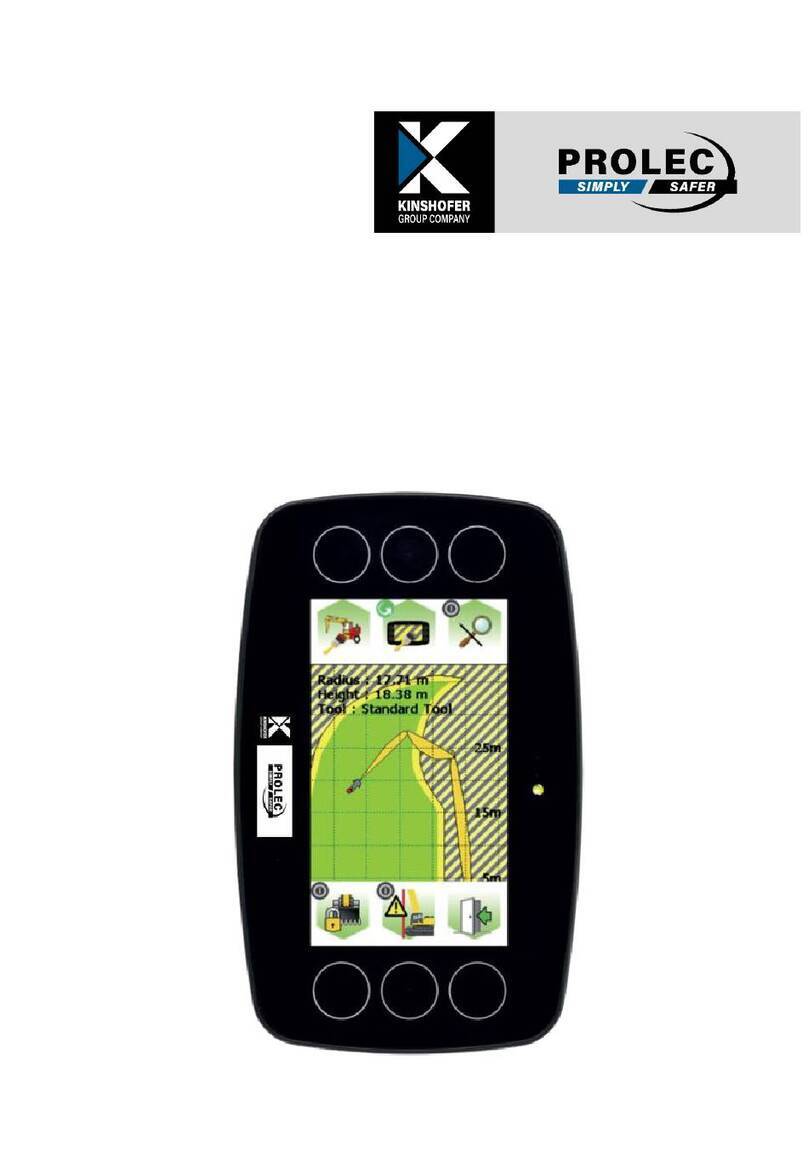
KINSHOFER
KINSHOFER PROLEC PME700 Operator's manual
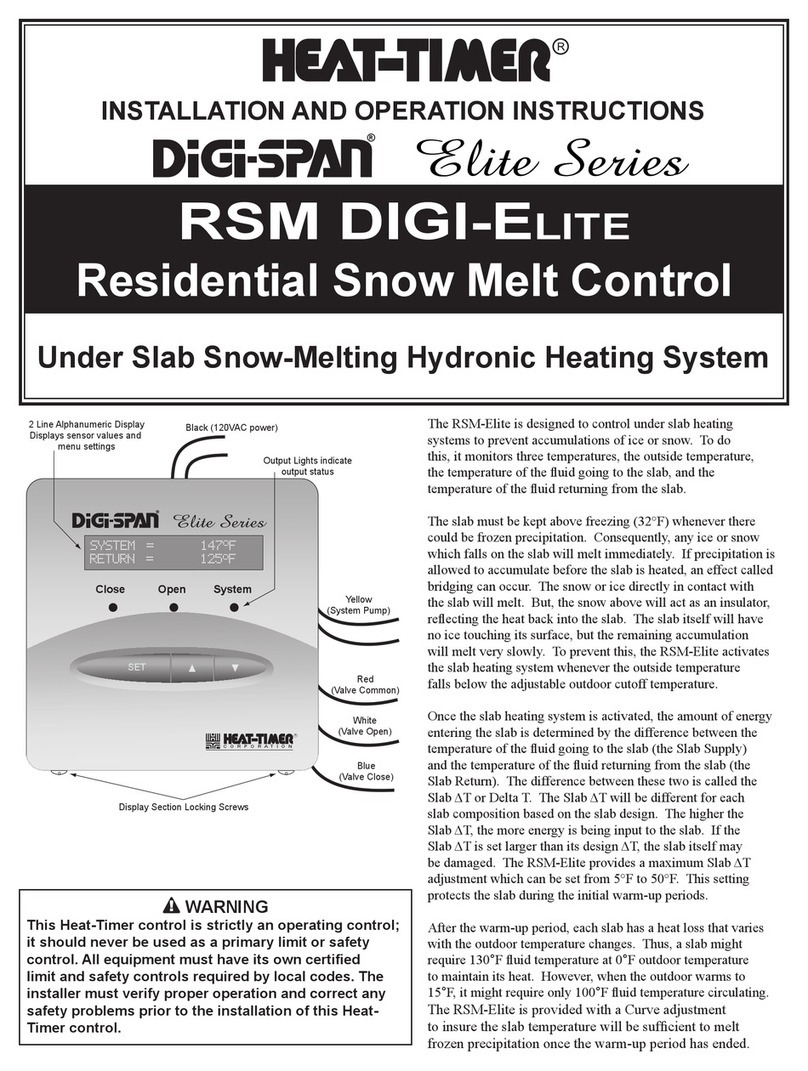
heat-timer
heat-timer DiGi-SPAN Elite Series Installation and operation instruction