PumpSmart PS220 User manual

Configuration &
Operation Manual
PumpSmart®Control Solutions PS220 v6

PS220 Configuration & Operation Guide
1 PS220
Getting
Started
Congratulations on the purchase of your PumpSmart® PS220 .
Leveraging our 160+ years in pump design, manufacture, and operation,
ITT Gould’s Pumps has one goal; improving the profitability of your plant
operations. Our products and services target your biggest issues to increase
process uptime, reduce maintenance costs , and lower operating energy
costs.
The PumpSmart®PS220 integrates a world leading ABB variable frequency
drive with decades of pump control logic, that has been field tested on tens
of thousands of applications worldwide. The PumpSmart®PS220 variable
speed pump control system provides real-time control and protection of
your pumps while also providing valuable process insight. By protecting
against unplanned pump failure due to process upsets, ITT Gould’s Pumps
can keep your process running longer and reduce an may eliminate un-
planned repair activities. In addition, through the “Right-Sizing” of your
pump to your system, we can reduce not only your energy consumption,
but the wear and tear on your pumps and process system.
Since 1999 the PumpSmart®patented logic has been the world leader in changing process control with pump protection for
pumping systems. From single pump applications to multi-pump applications, the PumpSmart®PS220 can accurately control
to Pressure, Flow, SmartFlow®, TDH, Level, and temperature with up to 6 pumps working together.
For additional information on the PumpSmart PS220 please take the time to review, and understand the safe installation,
operation and maintenance guidelines provided in the ABB ACS880 Hardware Manual., or visit www.ittproservices.com.
The PS220 has been designed for safe and reliable operation when properly installed, applied and maintained in accordance
with the instructions in the ACS880 Hardware Manual and PS220 Configuration and Operation Guide. ITT Monitoring and
Control shall not be liable for physical injury, damage or delays caused by failure to follow these instructions.

PS220 Configuration & Operation Guide
PS220 2
Getting
Started
Important Safety Reminder Page 03
PS220 Wizards Page 05
Basic Startup Page 07
SmartFlow Page 18
Process Control Page 34
Pump and VFD Page 43
protection
Multipump Page 64
Multivariable Page 68
Options and Features Page 72
Parameter Restore Page 159
Appendices Page 161
Keypad Use A-1 Page 161
Fault Tracing A-2 Page 167
Parameter Listing A-3 Page 178
Miscellaneous Page 199
Multipump connections Page 206
Basic Wiring & Installation A-4 Page 207
Quick Reference
• Wall mount units Page 211
• Floor mount units Page 213

PS220 Configuration & Operation Guide
3 PS220
Getting
Started
Products manufactured and furnished by ITT Monitoring and Control will provide safe, trouble-free service when properly
installed, maintained and operated. We have an extensive network of experienced sales and service professionals to assist
in maximizing your satisfaction with our products.
Safe installation, operation and maintenance of ITT’s equipment are essential end user responsibilities. The ACS880 Hard-
ware Manual and PS220 Configuration and Operation Guide identify specific safety risks that must be considered at all
times during the life of the product. Understanding and adhering to these safety warnings is mandatory to ensure person-
nel, property and/or the environment will not be harmed. Adherence to these warnings alone, however, is not sufficient;
it is expected that the end user will also comply with industry and corporate safety standards. Identifying and eliminating
unsafe installation, operation and maintenance practices is the responsibility of all individuals involved in the installation,
operation and maintenance of industrial equipment.
Safety Symbol and Signal Word Explanation:
IMPORTANT SAFETY REMINDER
This is the dangerous voltage alert symbol. It warns of high voltage which can cause death or physical
injury. Obey all safety messages that follow this symbol to avoid possible injury or death.
This is the safety alert symbol. It is used to alert you to potential personal injury hazards. Obey all safety
messages that follow this symbol to avoid possible injury or death.
DANGER indicates a hazardous situation which, if not avoided, will result in death or
serious injury.
DANGER
WARNING indicates a hazardous situation which, if not avoided, could result in death or
serious injury.
WARNING
CAUTION indicates a hazardous situation which, if not avoided, may result in minor or
moderate injury.
CAUTION
NOTICE used without the safety alert symbol addresses practices which, if not avoided, may
result in property damage.
NOTICE

PS220 Configuration & Operation Guide
PS220 4
Getting
Started
With respect to PumpSmart drives and the operation of pumping equipment the following risks bear reinforcement above
and beyond normal safety precautions:
Never work on the PS220 drive, the motor cable or the motor when main power is applied. After switching off
the input power, always wait 5 minutes to allow drive internal capacitors to discharge before working on the
drive, the motor or the motor cable. Failure to do so will result in serious injury or death.
DANGER
Do not work on control cables when power is applied to the drive or to external control circuits. Externally
supplied control circuits may cause dangerous voltages inside the drive even if the main power on the drive is
switched off. Failure to do so will result in serious injury or death.
DANGER
All electrical installation and maintenance work must be undertaken by a qualified electrician only. Failure to do
so could result in serious injury or death.
WARNING
Operation of any pumping system with a blocked suction and discharge must be avoided in all cases. Opera-
tion, even for a brief period under these conditions, can cause superheating of internal pumpage and result in a
violent explosion. All necessary measures must be taken by the end user to ensure this condition does not occur.
Failure to do so could result in serious injury or death.
WARNING
Never operate rotating equipment unless all protective coupling and shaft guards are in place. Personal injury
may occur if the driven equipment is operated without coupling and shaft guards. Failure to do so could result
in serious injury or death.
WARNING
Handle the unit carefully. The PS220 is heavy. Do not lift it alone.
Wall Mounted Units: Do not lift the PS220 by the front cover. Place the unit only on its back.
Floor Mounted Units: Lift the PS220 by the lifting lugs only. Do not tilt the unit. The unit will overturn from a tilt
of about 6 degrees. Use extreme caution when maneuvering a unit that has been placed on wheels.
Failure to do follow these instructions could result in serious injury or death or damage to the equipment
WARNING

PS220 Configuration & Operation Guide
5 PS220
Getting
Started
PumpSmart PS220 Wizard Menu
The PumpSmart PS220 utilizes a time saving versatile range of configurations to make initial setup incredibly easy. The
PS220 wizards have been designed to cover a wide range of common applications for pumping systems used around the
world.
The table below lists all of the Wizards that are in this section. Each section will describe the steps that you will need to
follow to properly configure the function(s) and will show step by step screen shots as you progress from beginning to
end. Additional information may also be shown, to assist you along the way, such as the table of all parameters used with
the function.
A thorough detailed explanation of each functions capability and use are in the individual Features & Function section in
this manual.
When reconfiguring the Pumpsmart PS220 it is highly recommended to restore the parameters to the original factory
default settings. Please use the PARAMATER RESTORE assistant shown in the Menu Tree below.
PS220 Wizard Menu Tree
Basic Startup
SmartFlow
Process Control
Pump & VFD Protection
Multi-pump
Multivariable
Parameter Restore
Keypad Use
Fault Tracing
Parameter List
Miscellaneous
Options & Features
Appendix

PS220 Configuration & Operation Guide
PS220 6
Basic
Startup
THIS PAGE IS INTENTIONALLY LEFT BLANK

PS220 Configuration & Operation Guide
7 PS220
Basic
Startup
Basic Startup Wizard
The PumpSmart PS220’s default mode of operation utilizes the Electric
Motor connected and will run the Pump using the Basic Speed Control
Functionality. The Basic Startup will configure the Pumpsmart PS220 with
the language you select, allow you to define the motor characteristic,
execute a Motor ID, and verify correct motor rotation. You will then select
the start/stop method, the operating speed range, and the method used
to send the speed set point reference for the system to work.
This procedure provides a baseline for all of the Pumpsmart function-
ality to properly perform. It MUST be performed prior to any other
functions/ features can be configured.
This functionality can only be configured with the Pumpsmart PS220
Configuration Wizard.
To access this Wizard, from the Home Screen follow the path:
MENU>PS220 Configuration>Basic Startup>
The steps that you will perform are as follows:
1. Configure the Motor Parameters.
2. Configure Basic Startup information.
The Screen Shots that follow will show you step by step, from start to
finish as you progress, how to configure this functionality.

PS220 Configuration & Operation Guide
PS220 8
Basic
Startup
Motor Parameter Configuration Wizard
The Pumpsmart PS220 will not operate unless the Electric Motor connected is
configured with all necessary information required.
The steps that you will perform are as follows:
1. Configure the Motor Setup
2. Perform the Motor ID Run
3. Perform a Motor Jog for Direction
DIIL Permissive
The PS220 will not run the motor unless
the Permissive input [DIIL] is closed
(24Vdc). This includes performing the
Motor ID Run. If not closed a warning
message will appear on the keypad
display:
The PS220 drive will come from the
factory with a jumper between the DIIL
input and 24Vdc. See Appendix A-4,
Instrument Wiring, for details on wiring
this switch.
NOTE – The DIIL Permissive input cannot be
defeated through a parameter setting. If your
application does not use a Permissive switch
input, leave the factory jumper in place. Refer to
Appendix A-4, Instrument Wiring, for details.
Safe Torque Off
The PS220 will not run the motor unless
the Safe Torque Off (STO) is closed. The
Safe Torque Off inputs are typically used
for the external E-Stop circuit. If the
E-Stop is active (STO open) the keypad
will display:
The PS220 drive will come from the
factory with jumpers installed between
the STO Output and Inputs 1 and 2. If
an E-Stop push button is installed in
the STO circuit be sure the E-Stop is not
activated.
Fault Safe Torque Off - A5A0
Detail for the following Motor
Setup will come from the motor
nameplate. Be sure that if the
motor is a dual wound motor you
select the voltage and full load
amps for the motor as wired.

PS220 Configuration & Operation Guide
9 PS220
Basic
Startup
1. Configure the Motor Setup
1. Enter the mains Supply voltage 2. Configure the Motor Full Load Amps/
Current (FLA)
3. Configure the Motor Nominal Voltage 4. Enter the Motor Nominal Frequency
5. Configure the Motor full load RPM
(Slip Speed)
6. Configure the Motor nominal power
(HP or kW)

PS220 Configuration & Operation Guide
PS220 10
Basic
Startup
2. Perform a Motor ID RUN
The PumpSmart PS220 drive uses specific motor details to create a mathematical model of the motor.
This model enables more accurate motor control and is created by using the motor data you have just
entered. It will be magnetizing the motor from 20 to 60 seconds at zero speed. This is called a Standstill
ID run as the motor will not turn. It is also referred to as a MAG ID, or ID Run. Once all the motor data
has been entered, you will see the following warning flash on the top of the screen:
This warning indicates that a Motor Identification run is required before the pump may be operated.
Note – Although the motor may not appear to respond to the start command. There may be an audible
high-pitched sound coming from the motor which is normal.
A warning message, “ID run Active” will be displayed during the ID. Once the ID run has completed,
the message “ID DONE” will be displayed.
Note – If the motor is repaired or replaced in the future, a Motor Identification run must be performed
again to maintain the accuracy of the PumpSmart drive.
The following procedure,
while not spinning the mo-
tor, will energize the motor.
All safety precautions must
be followed before initiating
the Motor ID run. Failure to
do so could result in serious
injury or death.
WARNING
1.
2. 3.

PS220 Configuration & Operation Guide
11 PS220
Basic
Startup
3. Perform a Motor Jog for Direction
Jogging the pump motor for correct rotation can be accomplished through the Motor Jog function.
The Pumpsmart PS220 will rotate at 60 RPM and continue to do so until the rotation is confirmed to
be correct (or incorrect). If incorrect the drive will prompt you to correct the rotation and then ask you
to start it again to then confirm that rotation is correct. It will always run at only 60RPM.
Note. If it is determined that the rotation direction is incorrect there is no need to change any wiring
on the (motor) load side of the PS220 to correct the rotation. When answered as incorrect it is all auto-
matically corrected by an internal Pumpsmart PS220 setting.
Never work on the Pumpsmart PS220,
the motor cable or the motor when main
power is applied. After switching off the
input power, always wait 5 minutes to al-
low drive internal capacitors to discharge
before working on the drive, the motor,
or the motor cable. Failure to do so will
result in serious injury or death.
DANGER
The Screen Shots below follow the sequence when the initial rotation
is incorrect. If rotation correct only screens 1, 2.and 3, and 8 will apply.
If the motor rotation is incorrect select No and run the rotation check
again, where screens 4-8 will apply.
1. 2. 3.
4. 5. 6.
7. 8.

PS220 Configuration & Operation Guide
PS220 12
Basic
Startup
Jogging the Motor
Checking the pump motor for correct rotation can be accomplished through the Motor Jog function. The
Pumpsmart PS220 will rotate at 60 RPM and continue to do so until the rotation is confirmed to be correct
(or incorrect). If incorrect the PS220 will prompt you to correct the rotation and then request to re-start it and
confirm that rotation is correct. It will always only operate at 60RPM. Once you conform the rotation to be
correct it will automatically stop.
Note. There is no need to change any wiring on the (motor) load side of the Pumpsmart PS220 to correct the
rotation. It is all done by and internal parameter.
Never work on the PS220 drive, the motor cable or the motor when main power
is applied. After switching off the input power, always wait 5 minutes to allow
drive internal capacitors to discharge before working on the drive, the motor, or
the motor cable. Failure to do so will result in serious injury or death.
Motor Jog
Rotation Re-checking
Checking the motor for correct rotation can be done initially by using the Basic Startup Wizard. The motor will run at
60RPM until the operator confirms the correct rotation. If it is incorrect the drive will automatically reverse it.
If it is desired to run the jog function an additional time, the drive start/stop source must be in Keypad. If originally set to
something other than keypad you must run the Basic wizard again, changing the start/stop source to Keypad. Be sure to
complete the Basic wizard when doing this. Then run the Basic wizard again to cause the Jog function to be available.
The jog function can be simulated using parameters as well. See this procedure outline below.
This procedure is for a Pump that CANNOT be run in REVERSE.
To recheck the rotation, you will need to follow the steps outlined below:
NOTE: ALL IDENTICAL SAFEY PRECAUTIONS SHOULD BE TAKEN AND FOLLOWED AS NOTED IN THE BASIC STARTUP
SECTION PRIOR TO PERFORMING THIS FUNCTION AGAIN
1. Place the drive in Local Control, if it is in remote.
2. Set parameters 30.11 and 30.12 to 60 RPM. Please remember or document what they were set to originally.
3. Press the Green Start button and watch for rotation.
4. Press the Red Stop button.
If the rotation is NOT correct go to step5, otherwise go to step 6.
5 . Go to parameter 99.16 and change the setting to reverse phase V and W
The 2 choices are (0) UVW and (1) UWV. Repeat steps 3 and 4.
6. Set parameters 30.11 and 30.12 back to original settings.
7. Place the drive back to the original control mode of Remote if necessary.
This procedure is for a Pump that CAN be run in REVERSE
1. Place the drive in Local Control, if it is in remote. (Manual speed control)
2. Press the Green Start button and watch for rotation. (The reference may be adjusted if desired)
3. Press the Red Stop button.
If the rotation is NOT correct go to step 4, otherwise go to step 5.
4. Go to parameter 99.16 and change the setting to reverse phase V and W
The 2 choices are (0) UVW and (1) UWV. Repeat steps 2 and 3.
5. Place the drive back to the original control mode of Remote if necessary

PS220 Configuration & Operation Guide
13 PS220
Basic
Startup
4. Configure the Start and Stop source.
PumpSmart is designed to operate in Remote mode (REM/LOC pushbutton). At this point
you will determine how PumpSmart starts and stops in Remote mode. By default it is set to
Keypad, where the green pushbutton starts PumpSmart and the red pushbutton stops it.
Other choices are available. Refer to the “Start/Stop” section in this manual for the details on
these choices.
Note - when in LOC PumpSmart will start/stop only by the keypad Start/Stop pushbuttons.
1. “ARROW RIGHT” then
“ARROW DOWN” to
change start/
stop source.
2. “SAVE” 3. “Next”
5. Configure Minimum Speed
By default, the minimum speed is set to 25% of the motor nameplate speed entered earlier. Since pumps only devel-
op pressure at the square of the operating speed caution is to be taken to make sure that the minimum speed is high
enough to prevent the pump from “dead heading”. A “Dead Head Test” can be performed or you can contact your
authorized Pump Sales Engineer to determine this speed if you are unsure. Refer the section “Dead Head” in this
manual for more details on this topic.
1. “ARROW RIGHT”
To change
2. “SAVE” to
continue
The Maximum Speed by default is configured to the motor
nameplate speed. Since pumps develop pressure at the square
of the operating speed, and the Power consumed at the cube
of the speed, caution is to be taken to make sure that the
maximum speed is within all limits of the pumping system
to prevent damage that may occur. Contact your authorized
Pump Sales Engineer to determine this speed if you are unsure.
Assure that the system operating conditions are within the capabil-
ities (e.g. speed, pressure, temperature, power, etc.) of the driven
equipment as rated by the manufacturer. Exceeding any of these limits
could result in failure of pumping system components resulting in
serious physical injury and damage to equipment

PS220 Configuration & Operation Guide
PS220 14
Basic
Startup
6. Configure the Operating Mode
At this point you determine if you will be running PumpSmart in Speed
Control or in Process Control (PID). If you select Speed Control your next
prompt will be to ask where the speed reference is to come from. If you
select Process Control here you will be prompted to go on to the Process
Control wizard where you will determine the process set-point (reference,
ex.: PSI, GPM, etc.) source in the Process Control wizard.
7. Configure a Speed Set-point Source (Control Reference)
The Pumpsmart PS220 can be configured for the setpoint to be sourced in one of three ways:
1. Keypad
2. Analog Input (AI1, AI2)
3. Fieldbus Control
Keypad is the default setting when
configuring the Pumpsmart PS220 for the first time.
If using an analog input (4-20mA or 0-10Vdc) go to
the next page to see an analog input setup.
If using Fieldbus as a speed reference please refer to the
Fieldbus Quick Start Guide for instructions on setting this up.
Once determined press Select to continue.

PS220 Configuration & Operation Guide
15 PS220
Basic
Startup
When Using an Analog Input Reference:
An analog input signal can be sent into the Pumpsmart PS220 from a PLC, DCS or other form
of higher level control system.
A 4-20mA or 0-10Vdc analog signal will need to be wired into either
analog input 1 or analog input 2. Note: the following detail speaks
about analog input 1 but setup for analog input 2 is identical.
“AI scaled at AI min” refers to the speed value (RPM) that corresponds
to the minimum input value of the reference signal (4mA). This is
defaulted to 0 RPM.
“AI scaled at AI max” refers to the speed value (RPM) that corresponds
to the maximum input value of the reference signal (20mA). This is
defaulted to 0 RPM. While it can be set to any value by the user it is
typically set to the motor nameplate speed or slip speed.
NOTE: The PS220 analog inputs are default to current type inputs.
If your input reference signal provided is a DC Voltage type of signal
you will need to change the analog input jumper (J1, or J2) to voltage
in addition to setting its corresponding parameters in group 12 to
voltage. Please refer to the options and features section for proper
parameter settings of the drive.
1. “ARROW RIGHT” to change
2. “ARROWS” to change
3. “Save”
1. “ARROW RIGHT” to change
2. “ARROWS” to change
3. “Save”
4. “Next”

PS220 Configuration & Operation Guide
PS220 16
Basic
Startup
Basic Wizard Complete
Once the speed reference is configured the Basic Wizard is complete. At this point you
can exit to the home screen, set a speed reference and run the pump, or you may run any
of the other PumpSmart wizards (ex.: SmartFlow, Pump Protection, Multipump, etc.).

PS220 Configuration & Operation Guide
17 PS220
SmartFlow
THIS PAGE IS INTENTIONALLY LEFT BLANK

PS220 Configuration & Operation Guide
PS220 18
SmartFlow
Basic SmartFlow
Basic SmartFlow utilizes a complex algorithm that will calculate the actual flow
of the pump it is connected to. External sensors are not required in a Basic
SmartFlow application. Any manufacturer’s centrifugal pump may work with
Smartflow.
Basic SmartFlow is designed for low to medium specific speed pumps, under
3000NS. A pump with a specific speed under 3000 will have the following
characteristics.
1. Power rises as flow increases with no “dips or bumps” in the power curve.
2. The power value at shut off is at least 25% less than the power at BEP
(Best Efficiency Point).
See the figure to the right for these characteristics.
Advanced SmartFlow
The PumpSmart PS220 may be utilized on pumps that do meet the criteria
mentioned previously for Basic Smart Flow. In these cases it will require
configuring Advanced SmartFlow.
To configure the Advanced SmartFlow functionality, additional pumping
system information will be required. Suction and discharge pressures readings
are required for the advanced algorithms to function successfully. This infor-
mation is also used to configure the information needed for the Smart TDH
functionality.
SmartFlow Configuration Wizard

PS220 Configuration & Operation Guide
19 PS220
SmartFlow
Configuring Basic or Advance SmartFlow
To access the SmartFlow Wizard, from the Home Screen follow the path:
MENU>PS220 Configuration>SmartFlow.
The screen shots that follow will show you step by step as you progress, from
start to finish as you progress, how to configure this functionality
The steps to be performed are:
1. Configure the Flow Unit
2. Configure the Pump Specific Properties
3. Configure Fluid Specific Gravity
4. Execute a Smartflow Tune
5. Exit the Wizard
A. Select Basic SmartFlow from the SmartFlow menu list
B. Select the unit of measurement to be used
A B
The SmartFlow unit selection
identifies what units SmartFlow will
display in. It also will be used for
providing the necessary Pump Pro-
tection and input to other internal
functions when required.
Note – The SmartFlow unit can be
set independently from units that
may have already been used for the
language selected at first startup.
The information required for this configuration can be found on the Pump
Performance Curve. See the figure on page 17 for an example of a typical
Pump Performance Curve.
C. Configure the Pump Type
Note – For magnetic drive pumps with metallic containment shell select Mag
Drive. For non-metallic shells select SS Centrifugal as the Pump Type. PD pumps
must be centrifugal. They cannot be a piston pump.
SS Centrifugal – Single Suction
Centrifugal
DS Centrifugal – Double Suction
Centrifugal
Mag Drive – Magnetic Drive Pump
PD Pump – Positive Displacement
(Gear Pump)
C
Table of contents
Popular Controllers manuals by other brands

Wilo
Wilo CONTROL BOX CE+ WeH Installation and operating instructions

Muller Elektronik
Muller Elektronik SPRAYER-Controller Orchard/Vineyard MIDI 3.0 Installation and operating instructions
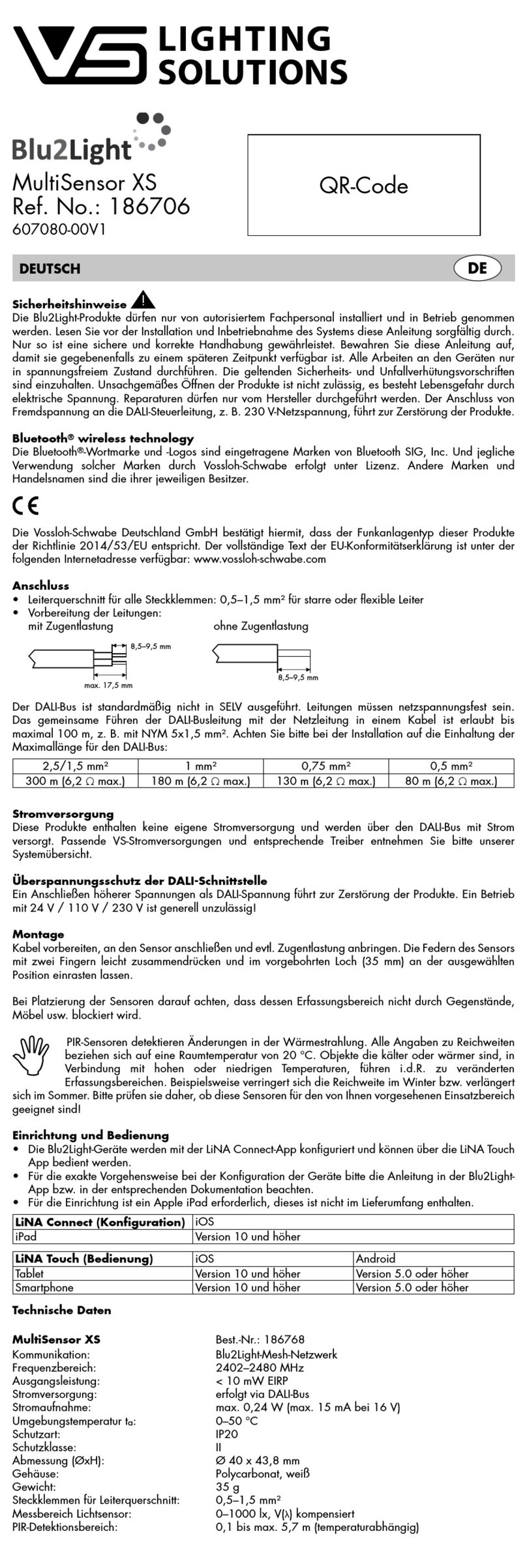
VS LIGHTING SOLUTIONS
VS LIGHTING SOLUTIONS Blu2Light MultiSensor XS manual
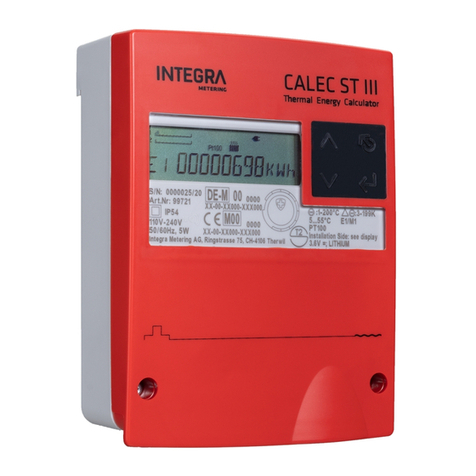
Integra
Integra CALEC ST III Standard installation manual
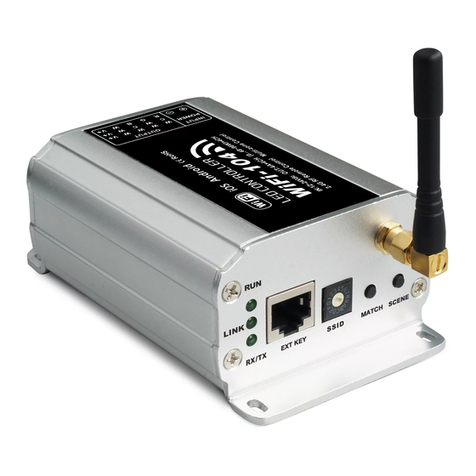
Ltech
Ltech WiFi-104 manual

Siemens
Siemens RWD68 quick start guide