Purelogic PLCM-E1b User manual

01. General information
02. Delivery set
03. Technical features
04. Main connectors and indicators
05. Software installation
06. Terms of Warranty
INSTRUCTION MANUAL
2
2
3
3
4
16
PLCM-E1b
CNC Ethernet controller

Edition from 05.06.2015 3
PLCM-E1b. CNC Ethernet controller
www.purelogic.ru8 (800) 555 63 74
01
02
General information
Delivery set
Technical features
The device is a controller of PLCM series ( see user’s manual), has
input/output port and Ethernet interface for PC connection. This port
corresponds with LPT-port of PC in form and location.
• Controller PLCM-E1b — 1 pcs.
• Instruction manual PLCM — 1 pcs
• Installation and setup guide PLCM-E1b — 1 pcs
• Ethernet cable — 1 pcs
03
01. General information
Voltage supply
Max current consumption
Max number of axes of CNC-machine
Operating temperature
Overall dimensions (W x H x L)
Control interface
STEP Max signal frequency
Number of outputs
Isolation resistance
Module’s height (without packing)
Number of inputs
12V, direct current
6
0...50 °С
83 х 27 х 66 mm
250mА
100 kHz
12 items, buffered 5V, 10mA MAX
500 mOhm
0.3 kg
5 items, buffered logic levels
“0”<1.8V, “1”>2.5V.
Max input voltage is 15V
Ethernet, connector “RJ-45”.
signal transmission STEP/DIR/
ENABLE and input signals.
MACH3-compatible
!Check www.purelogic.ru for more information.
POWER OFF DEVICE BEFORE MAKING ANY CONNECTIONS.
DO NOT CONNECT POWER SUPPLY’S TO GROUND, MASS,
HOUSING, ETC.
IT IS RECOMMENDED TO USE HIGH QUALITY NOISEPROOF CABLES
ETHERNET 5TH CATEGORY AND HIGHER
THE CONTROLLER WORKS WITH MACH3 R3.043.XXX VERSIONS AND
HIGHER, ALWAYS REMEMBER TO UPDATE MACH3. • For controller power supply, direct current source is used, supply
voltage is 12V.
• Ethernet connector is designed for PLCM-E1b connection to local
area network. The connection must be performed with cable 5 or of
higher category, You can apply patch-cords with straight through or
crossover crimping type. Direct connection to PC without commutator
usage is possible.
Main connectors and indicators 04

Edition from 05.06.2015 5
PLCM-E1b. CNC Ethernet controller
www.purelogic.ru8 (800) 555 63 74
04. Main connectors and indicators
Fig. 1. Connectors and indicators connection scheme
Fig. 2/3. Cable type setup / Speed and duplex mode setup
05 Software installation
1. Turn on the controller and connect it to Ethernet. Link LED must
flash on.
If it does not or blinks and network connection icon appears/disappears
in Windows, automatic type definition went incorrect (this was caused
by special features of some network cards).
In this case it is necessary to set up manually. Click on the [Start] icon-
[Control Panel], [Network and Sharing Center], Local Area Connection
– properties. Then press ‘configure’ (fig. 2). In ‘Advanced tab’ choose
‘Speed and duplex mode’ and set ‘10Mbit per second full duplex’ (fig. 3).
(Parameters and names can slightly differ in different network cards).
2. For device work with MACH3, you need to install plug-in.
Please download zip-file for PLCM controllers from here:
www.purelogic.ru/files/downloads/SOFT/PLCM.zip and run «setup.
exe». Software installation wizard for controller will be started. (fig. 4).
Press ‘Next’. If this is your first installation and you want to have all
necessary drivers installed, choose devices which are planned to apply
on the PC. (fig. 5). If none of the devices is chosen, only plug-in update
for MACH3 will be executed.
• P1 Port represents LTP PC port analog and has identical assignment
and location of contacts:
Outputs 1, 2, 3, 4, 5, 6, 7, 8, 9, 14, 16, 17.
Inputs 10, 11, 12, 13, 15.
• RESET button is for IP-address of controller current value reset to
default value
• Coil short-circuit module protection, wrong stepper motor connection
protection (192.168.10.10).
To do this it is necessary to:
1) Disconnect controller power supply.
2) Press and hold down RESET.
3) Supply power voltage, pressing RESET.
4) Release RESET in 1-2 sec.

Edition from 05.06.2015 7
PLCM-E1b. CNC Ethernet controller
www.purelogic.ru8 (800) 555 63 74
05. Software installation
Fig. 4. Software installation wizard Fig. 6. Automatic network installation
Fig. 5. Driver installation Fig. 7. Plug-in option
When choosing PLCM-E1b after ‘Next’ pressing, software installation
wizard will offer to execute automatic setting of network adapter PC for
correct connection to PLCM-E1b (fig. 6).
Controller automatic search can disrupt local network, use this
function only if you do not use local network resources on the PC and
do not use the Internet. Press ‘Next’, then ‘Install’. The master will copy
the necessary files and finish its work.

Edition from 05.06.2015 9
PLCM-E1b. CNC Ethernet controller
www.purelogic.ru8 (800) 555 63 74
05. Software installation
3. Having installed the plug-ins, when starting MACH3 choose the
appropriate plug-in in the window which is shown in fig. 7.
As a rule there are two versions of plug-ins for PLCM controllers: test
and stable.
Choose the one you are going to work with. Tick ‘Don`t ask me
again ‘ in order not to choose it every time. If there is necessity to
change output device choose: MACH3 – Function Cfg’s – Reset device
sel.
* If you decided to go to another version (test or stable version, you will
need to go to plug-in setting up after start-up (see further) and update
internal controller software.
4. After successful plug-in start, PLCM control option will appear in
menu MACH3 PlugIn. Choose this option.
* If you see the window as it is in fig. 8 and you cannot choose
controlling device, this means that Windows firewall blocks access to
PLCM-E1b. You must either add MACH3 to firewall exception or disable
firewall.
5. Execute plug-in setting.
Out of a falling out list it is necessary to choose one of the controllers
connected to the system.
After choosing the option additional controller settings will be available
(fig. 8). Пif the plug-in finds that weaving is out of date, you will be
prompted to update weaving in the controller. This procedure needs to
be performed once when first device installation.
Settings description:
Advance path planning time of Mach3 – specifies data size about motion
path, which the program needs to prepare beforehand. The more the
value, the more stable the machine works (e.g. when ToolPath picture
rotates , Mach stops calculating new trajectory data, therefore the
more of them were calculated beforehand, there is the less possibility
of ‘failure’ in motion while rotating the picture or some other load on
Mach3).
Time of advance calculation of path of PLMach – similar buffer,
not from Mach3 side, but in PLCM card. The buffer stabilizes the
work under short lineouts PLCM<>Mach3 and under slowing down
calculation of Mach.
Note: From one side the more value of these features, the better (the
buffer is bigger, the work is more stable) but with increase of buffer
FeedHold will be delayed by the sum of these parameters, i.e. If
Mach3 buffer=1 sec and PLMach buffer=0,5 sec, CNC-system reaction
time when pressing FeedHold =1,5 sec + stepper motor braking time
according to the defined acceleration profile.
Logging – with active logging, log exchange file PLCM<>Mach3 is
saved to ‘C:\Mach3\PLСM.log’. When exploring incorrect device work,
this file must be sent to Purelogic R&D technical Support with the
detailed problem description. To receive IP-address automatically we
recommend to leave this item active, if there is a device which can
dynamically assign IP-addresses (e.g. it can be a usual home network
gateway for internet connection )in you local network.
Usage of the following IP-address – this option must be used when
there is no DHCP-server which appoints IP-addresses.
Fig. 8. Plug-in setting in MACH3

Edition from 05.06.2015 11
PLCM-E1b. CNC Ethernet controller
www.purelogic.ru8 (800) 555 63 74
05. Software installation
Fig. 9. General scheme of CNC control
Brushless spindle
Power unit
Stepper motor/
Servo motor
Frequency
converter
CNC controller
PC with installed CNC
program MACH3
Power unit
Limit sensor
Up to 5 sensors
connection
12V
Ethernet / USB
LPT-cable
Connection via
Relay up to
3 devices
Control
LPT-cable
~220 ,
Vacuum
hold down
Cleaner
Cooling fan
Spindle
KRESS
Coolant
pump
~220 ,
~220 ,
Stepper/servo motor driver
Up to 4 drivers connection
Switching
regulator
48V, 70V
STEP
DIR
ENABLE

Edition from 05.06.2015 13
PLCM-E1b. CNC Ethernet controller
www.purelogic.ru8 (800) 555 63 74
05. Software installation
Restore IP button allows to reset IP-address of controller to those
installed by default.
If the controller is not found by the plug-in, follow the instructions in
item 6, if it is ok, skip item 6.
There is a complete solution for quick and easy configuration network
setting
In (C:\Mach3\Purelogic), supplied with the devise you will find set_
ip.exe file.
After starting, this application will set up of your PC network
connections.
In case when there are several network cards are installed (several
network connections) the program will offer to specify for what
connection to change the settings.
FOR CORRECT WORK WITH PLCM CONTROLLER IT IS NOT
RECOMMENDED TO PUT THE SWITCH IN AUTOMATIC POSITION.
You can assign your PC any address (e.g. 192.168.10.XX,
192.168.10.1.) The last value can be different different from 10, 11
and 12 (192.168.10.10 and 192.168.10.12 addresses for PLCM devices
established by the manufacturer.
Automatic address assignment installation will work with the controller
only when there is local DHCP server in the net. In all other cases the
controller will not contact the plug-in.
After necessary connection option and pressing the button install the
application apply required connection parameters.
After the installation the application will come with a message:
Fig. 10. Restore IP – reset IP to pre-defined Fig. 11. Application window view Set_IP
Fig. 12. Message about successful application of settings

Edition from 05.06.2015 15
PLCM-E1b. CNC Ethernet controller
www.purelogic.ru8 (800) 555 63 74
05. Software installation
(After pressing the button ‘install’ the application will require 2-3
minutes for introduction of changes. On ‘slow’ PC this procedure
will take a little more time). If for some reason you failed to make
connection to PLCM controller in automatic mode, produce setting
manually. Click on the [Start] icon-[Control Panel], [Network
connection].
Choose the connection which you intend to use with PLCM. (In this
case it means that if the computer has several network cards, you
can install one of them for work with PLCM and the other one use at
your discretion. We do not recommend to apply this approach in work
mode, as system loading of third party applies can cause delay of
tasks execution in Mach3 which can lead to loosing connection with
the controller. You can use several network cards when testing and
setting the system). With help of Double click of left mouse button open
‘network properties’ window.
Choose Internet protocols TCP/IP and press Properties.
In the opened window displace the switch to ‘Use this IP-address’
mode.
Enter any address like 192.168.10.XX in IP-address line, e.g.
192.168.10.1. The last number can be any but differ from 10, 11 and
12 (192.168.10.10 and 192.168.10.12 addresses for PLCM devices
established by the manufacturer). Net mask is 255.255.255.0. After
pressing OK you will need some time to apply the parameters. Switch
off firewall and anti virus software (or add MACH3 to exceptions).
Fig. 13. Network connection option Fig. 14/15. Network connection components/ TCP/IP configuration

Edition from 05.06.2015 17
PLCM-E1b. CNC Ethernet controller
www.purelogic.ru8 (800) 555 63 74
06. Terms of Warranty
Produced and accepted in accordance with obligatory requirements of
valid technical documentation and is qualified for exploitation.
Lot number:
Technical
Control
Department
4.2. The product with traces of foreign objects or substances impact,
including dust, liquids, insects, also objects having extraneous
inscription.
4.3. The product with traces of unauthorized tampering and (or) repair
process (traces of opening, home-made soldering, elements changing
etc).
4.4. The product with self-diagnostic function that shows improper
exploitation.
4.5. Technically complex product in respect of which assembly and
integration and start-up works were not performed by Seller specialists
or by recommended organizations, except in cases directly regulated
under goods documentation.
4.6. In cases when the product exploitation was performed in
conditions when power supply did not correspond with manufacturer’s
requirements, also when there is no electrical protection device .
4.7. The product which was resold by the initial buyer to the third party.
4.8. The product with defects which were caused by low-quality spare
parts or fulfilled their service life spare parts,consumable materials,
also using spare parts, consumable materials not corresponding with
manufacturer’s requirements.
06 Terms of Warranty
The warranty period is 12 months after purchasing and is valid only
if all operational conditions and scheduled maintenance are strictly
followed.
1. General terms
1.1. In case of product acquisition as separate components, Seller
guarantees working ability of every component, but does not
assume responsibility for the quality of their joint work (mismatch
of components). If you have questions please consult our technical
support team.
1.2. Seller does not guarantee compatibility of the purchased product
with the one that Buyer already has or bought from third parties.
1.3. Product’s component parts and configuration can be changed by
manufacturer without notice due to the product consistent technical
improvement.
2. Conditions for warranty acceptance
2.1. The product is accepted only in the same completeness of set as it
was purchased.
3. Warranty service procedure
3.1. Warranty service is performed by testing the claimed product
defect.
3.2. If the defect is proved, warranty repair is carried out.
4. We do not assume any responsibility for glass, electric lamps,
starters and expendable materials as well as:
4.1. Damaged product caused by inappropriate transport and store
conditions, wrong connection, operation in abnormal (off-design)
mode, or in conditions which are not manufacturer-supplied (including
temperature and humidity out of limits of recommended range), having
damages due to third-party circumstances (voltage jumps, natural
disasters, etc.), also having mechanical or thermal damages.

We draw your attention to the fact that there can be
some changes in this instruction due to the product
consistent technical improvement. You can always
download our latest versions at www.purelogic.ru
www.purelogic.ru
Contacts
Moscow +7 (495) 505-63-74
Voronezh +7 (473) 204-51-56
149 Office
160, Leninsky avenue, Voronezh,
Russia, 394033
Monday - Thursday: 8.00–17:00
Friday: 8.00–16.00
Break: 12.30–13.30
sales@purelogic.ru
Table of contents
Other Purelogic Controllers manuals
Popular Controllers manuals by other brands
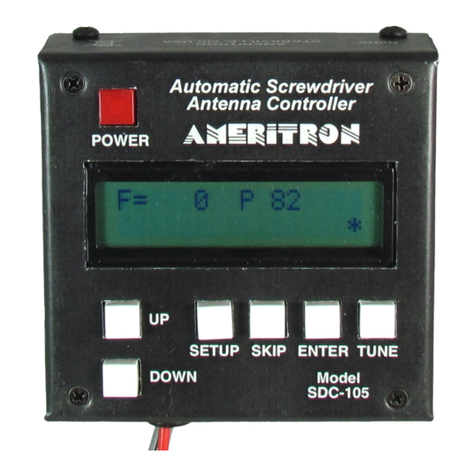
AMERITRON
AMERITRON SDC-105 instruction manual
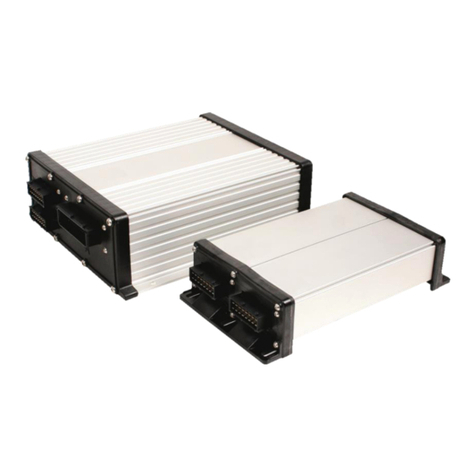
Mueller
Mueller ISOBUS SPRAYER-Controller MAXI 3.0 operating instructions
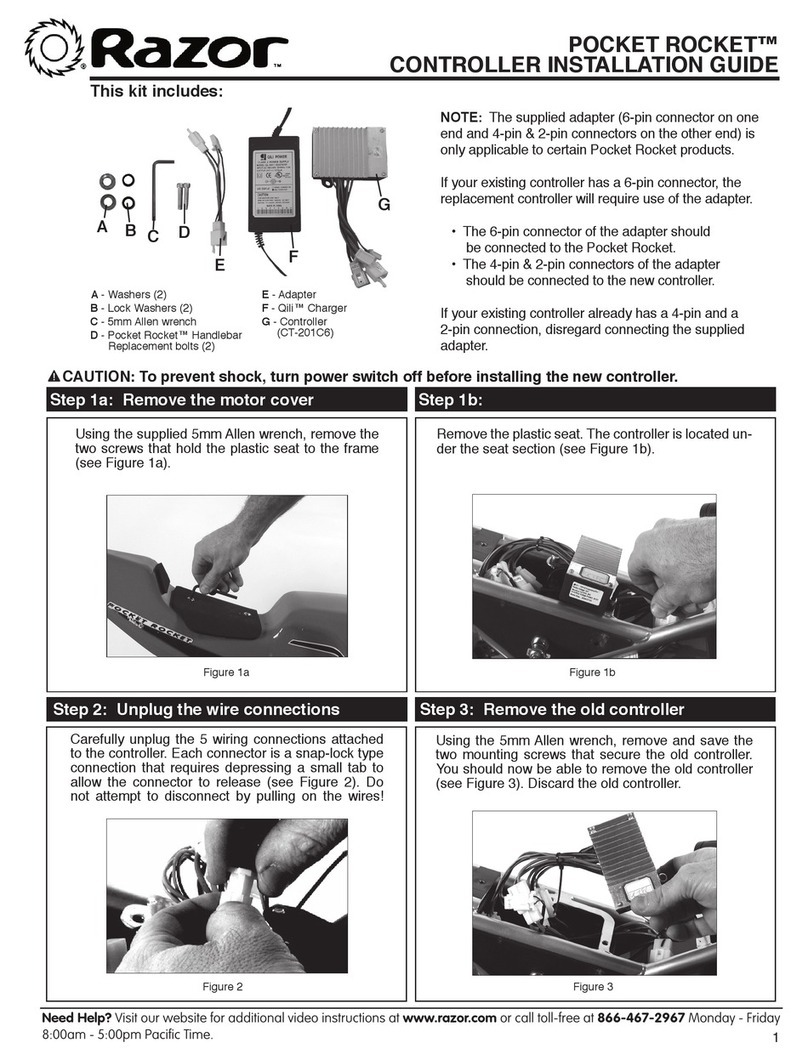
Razor
Razor POCKET ROCKET installation guide
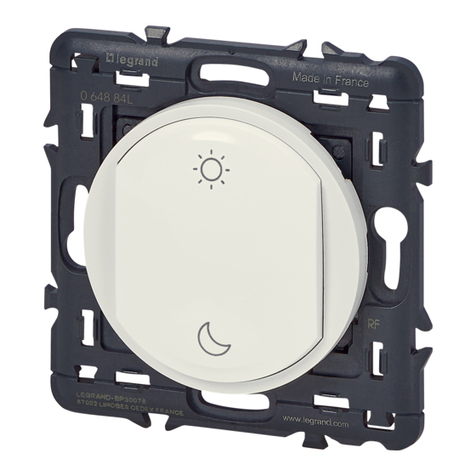
LEGRAND
LEGRAND 0 648 84L quick start guide

Curtiss-Wright
Curtiss-Wright EL30 Installation and service manual
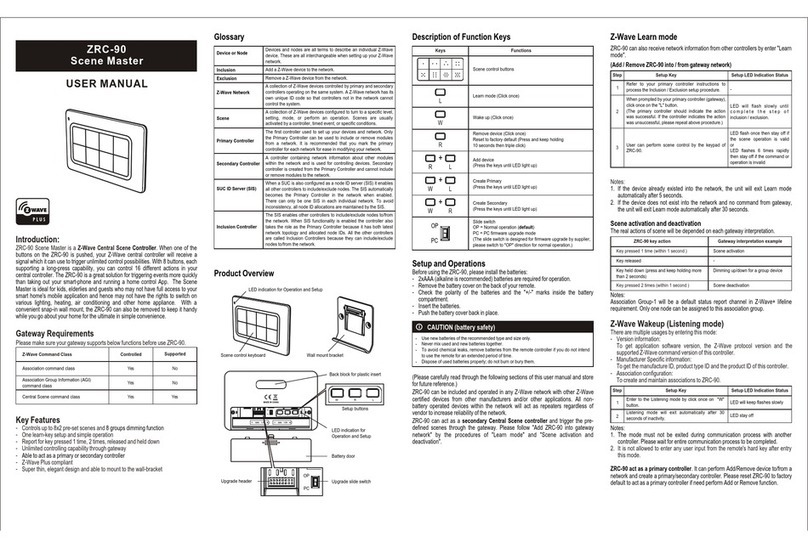
Remotec
Remotec ZRC-90 Scene Master user manual