Purelogic PLC330 User manual

01. General information
02. Delivery set
03. Technical features
04. Driver functional capabilities
05. Connection
06. Stepper motor connection
07. Current and voltage option
08. Commutation timer of a coolant pump
09. PWN convertor > voltage
10. Step division option
11. Protection functions, setup
12. Common problems
13. Terms of Warranty
INSTRUCTION MANUAL
2
2
3
4
6
9
13
14
14
14
15
16
16
PLC330
Multichannel stepper motor driver

Edition from 03.06.2015 3
PLC330. Multichannel stepper motor driver
www.purelogic.ru8 (800) 555 63 74
01
02
General information
Delivery set
Technical features
PLC330 is a microstepping multichannel driver of stepper motor
control. The module allows to control 4 machine axes using LPT-port.
The driver has inbuilt coil short-circuit protection, back EMF effect
protection.
The multichannel driver supports control of frequency converter from
PWN signal of a controlling program and has inbuilt regulated timer for
control of a coolant pump. The module has 5 inputs for limit sensors or
E-STOP button connection.
The device is optimal for control of bipolar and unipolar Purelogic R&D
stepper motors (PL42/PL57 series). Work with other stepper motors is
also possible.
• Multichannel driver PLC330 — 1 pcs.
• LPT-cable — 1 pcs.
• Instruction manual — 1 pcs.
• Board for connecting sensors PLC330 Alarm Mod-A— 1 pcs.
• CD with software — 1 pcs.
03
01. General information
Control method
Supply voltage
Operating current of each stepper motor
Step division (microstep)
PWN converter parameters>voltage
Timer parameters of lubricoolant
control
Max shaft rotation frequency
Isolation resistance
Net weight
STEP Max signal frequency
Installed relays parameters
Operating temperature
Overall dimensions (W x H x D)
STEP/DIR/ENABLE from LPT port
18...30V (bogey value 27V)
1:1, 1:2, 1:8, 1:16
Uoutp. = 0...9.5V (when changing pulse
Frequency converters control ratio
Q=0...1)Power 10V from frequency
convertor
Operation frequency – 8...60 sec
Duration – 1...8 sec
30 cycles per second
500 MOhm
0,8 kg
100 kHz
220V/7А
0...50 °С
200 x 49 x 114 mm
0.5А...3.0 А (discrete regulation)
!Check www.purelogic.ru for more information.
TURN OFF POWER DEVICE BEFORE MAKING ANY CONNECTIONS AND
DRIVER OPERATION MODE CHANGINGS.
DO NOT MOUNT THE POWER SWITCH AFTER THE POWER SOURCE
ON THE DRIVER POWER LINE.
POWER SWITCH SHOULD BE INSTALLED BEFORE POWER SUPPLY, AT
~220V SIDE.
DO NOT CONNECT POWER SUPPLY’S TO GROUND, MASS,
HOUSING, ETC.
STRICTLY OBSERVE THE POLARITY OF POWER SUPPLY AND CONTROL
SIGNALS CONNECTIONS.

Edition from 03.06.2015 5
PLC330. Multichannel stepper motor driver
www.purelogic.ru8 (800) 555 63 74
04. Driver functional capabilities
Fig. 1. Multichannel stepper motor driver PLС330 dimensions
04 Driver functional capabilities
• Operation with any LPT CNC program (STEP/DIR – Mach, TurboCNC
etc.)
• Usage of one supplied voltage for supplying all the scheme, system of
module softstarter.
• Simultaneous control of 4 stepper motors – any bipolar and unipolar
stepper motors (4,6 or 8 outputs) FL57 and others type. We strongly
recommend to use the module with Purelogic R&D stepper motors.
• 4 identical stepper motor drivers (microstep 1:2, 1:8, 1:16, mode
AUTOSLEEP)
Current adjustment in coils of every stepper motor. Fixed PWN
frequency 20 kHz for current control in stepper motor coils.
• AUTO-SLEEP mode automatically reduces current in stepper motor
coils and reduces acoustic noise when in standstill.
• Coil short-circuit module protection, wrong stepper motor connection
protection , polarity reversal supply voltage protection
• Opto-isolation of module and LPT PC port. Current buffering of all
controlling pins of LPT port.
• Control of 2 high current relays 7А/220V and 2 opto-outputs for
commutation of additional machine equipment (spindle, coolant pump
or electric fan).
• Inbuilt regulated timer (time and relay operation duration is
regulated) for commutation of a coolant pump.
• Operation support of frequency converter (regulation of spindle
rotation, PWN converter>voltage), from MACH.
• Control of 5 external sensors state (limit switches) All the inputs are
optoisolated.
• Convenient dismountable clip connectors to step motor, power source
and relay loads.

Edition from 03.06.2015 7
PLC330. Multichannel stepper motor driver
www.purelogic.ru8 (800) 555 63 74
05. Connection
Fig. 2. Connection and setup of PLC330
05 Connection
Control signals connection
Multichannel driver PLC330 controls 4 stepper motors using standard
signals STEP/DIR/ENABLE.
The driver of every channel has its couple of signals STEP1/2/3/4 and
DIR1/2/3/4 and signal ENABLE is mutual for all the channels. н
Signals STEP/DIR/ENABLE are galvanically isolated from the controller
and are buffered. All the signals are allocated to the connector DB-25M
type (fig.2) for a more convenient connection to LPT PC port.
STEP signal characteristics are working voltage 3...5V, current
consumption 0.1 mА, min signal duration is 10ms. The step is carried
out on the signal back edge.
DIR signal characteristics are working voltage 3...5V, current
consumption 0.1 mА, operation time 1 ms.
ENABLE signal characteristics are working voltage 3...5V, current
consumption 0.1 mА, operation time 1 ms. When supplying logic ‘1’, the
module is turned on, ‘0’, the module is switched off.
Limit switches connection
Multichannel driver PLC330 has 5 optoisolated inputs for connecting
limit switches.
Limit switches are connected through an additional extension board. A
scheme of additional extension board is shown in fig.3. The extension
board is connected to the main board via a tail through adapter XP5
according to gig.2 (Alarm connector).
Usual contact limit switched and non-contact sensors PLL01 type with
signal output can be connected to the board. To do this every group of
limit switches connection has output voltage +5V, ground and signal
input.
LED HL1 indicates presence of board power voltage, LEDs HL2...HL6
indicate limit switches operation on inputs IN5...IN1.

Edition from 03.06.2015 9
PLC330. Multichannel stepper motor driver
www.purelogic.ru8 (800) 555 63 74
05. Connection
Relay loads connection К1, К2, К3
Multichannel driver PLC330 supports control of 2 high current relays
К1 and К2 for commutation of additional machine devices. LED HL1
indicates operation of K1 relay, HL2 indicates relay K2 operation.
Fig. 2 shows relay commutation when switched off. Control of every
relay happens from the corresponding contact in XP1 adapter.
Please note that relay K1 operates in controlling mode from LPT port
only when JMP1 switch is open in XP13.
Power source connection
Power source connection is performed according to fig. 6.
Multichannel driver PLС330 is optimal for operating stepper motor
Purelogic R&D series PL42/PL57.
Purelogic R&D stepper motor connection to the driver is performed as
it is shown in fig. 6.
Please note that in case of couple (phase) interchange PH1.x<>PH2.x,
the motor will start rotating in the opposite direction (inversion
analogue of DIR signal).
The driver has protection against wrong stepper motor coil connection
and coils linked together / ‘+’ power supply.
The length of wires leading to the stepper motor from the driver must
not exceed 10 meters. Longer wires can lead to driver’s work failures.
It is strongly recommended to interlace the stepper motor wires per
phase, then put this braid to the screened metal sheathes. Sheathes
and stepper motor frame must be grounded.
Fig. 3. Additional extension board, limit switches connection
Stepper motor connection 06
Fig. 4. Purelogic R&D stepper motor connection
PH1.1 [+А] Red (RED)
PH1.2 [-А] Orange (ORG)
PH2.1 [+B] Blue (BLU)
PH2.2 [-B] Green (GRN)

Edition from 03.06.2015 11
PLC330. Multichannel stepper motor driver
www.purelogic.ru8 (800) 555 63 74
Fig. 5. General scheme of CNC control
Brushless spindle
Power unit
Stepper motor/
Servo motor
Frequency
converter
Dumper
Some driver models
have input dumper
CNC controller
Stepper motor
driver
Up to 4 drivers connection
PC with installed CNC
program MACH3
Power unit
Limit sensor
Up to 5 sensors
connection
27V 27V 12V
Ethernet / USB
LPT-cable
Connection via
Relay up to
3 devices
Control
LPT-cable
~220 ,
Vacuum
hold down
Cleaner
Cooling fan
Spindle
KRESS
Coolant
pump
~220 ,
~220 ,
06. Stepper motor connection

Edition from 03.06.2015 13
PLC330. Multichannel stepper motor driver
www.purelogic.ru8 (800) 555 63 74
06. Stepper motor connection
Fig. 6. Stepper motor and voltage power scheme connection
Maximal driver voltage power option depends on the applied stepper
motor and desired maximum rotation speed.
Optimal supply voltage calculation for the stepper motor is carried out
according to the formula U=32*v (stepper motor phase inductance mH),
but not more than 30V.
Supply current must be chosen 50...70% from the claimed stepper
motor coil current.
Operating current installation is performed according to fig. 2 and fig.
7 by removable jumpers in XP6 (channel №1), XP7 ( channel №2), XP8
(channel №3), XP9 (channel №4). Operating current installation must be
performed only when driver power supply is off.
When there is no STEP signal for more than 2 sec, each driver goes to
sleep mode (AUTOSLEEP) and reduces coil current till 300 mA.
For back EMF compensation device it is recommended to use a
protection device – dumper (module PLZ005). Module connection to
power source is carried out according to fig. 6.
Current and voltage option 07
Fig. 7. A scheme of connection stepper motor driver and voltage supply

Edition from 03.06.2015 15
PLC330. Multichannel stepper motor driver
www.purelogic.ru8 (800) 555 63 74
08. Commutation timer of a coolant pump
08
09
10
Commutation timer of a coolant pump
PWN convertor > voltage
Stepper motor step division option
Multichannel driver PLC330 has inbuilt timer of a coolant pump
operation through relay K1.The timer starts only when there is logic ‘1’
on 16th contact of LPT adapter.
Please note that relay K1 operates in control mode from inbuilt timer
with closed switch JMP1 in adapter XP13.
Switching frequency of relay K1 is set by trimming resistor R1, duration
of relay hold being on is set by trimming resistor R2. Turn off power
device before making any settings.
Multichannel driver PLC330 has inbuilt PWN converter > voltage.
The convertor converts control signal ratio to voltage – pulse ratio
Q=0...1 > voltage U=0...9.5V. The converter is used for control of
frequency converter to which a spindle is connected.
The convertor is optoisolated from controller board PLC330 and draws
its power from FC.
Normally FC has 3 contacts of converter connection – power supply
10V, grounding and voltage input 0...10V. PWN signal of FC control
is generated by a controlling CNC program and is transmitted to the
corresponding contact in XP4 (14 contact).
Connection is performed according to fig. 2 in XP10.
The driver allows to divide electronically physical stepper motor step –
1, 2, 8 and 16. Thus positioning accuracy is higher. Step division mode
is called microstep mode. This mode allows to reduce stepper motor
resonances at low revs. But when using microstep a claimed moment is
reduced on stepper motor shaft.
It is recommended to use the driver in step division 1:8 or 1:16. In these
modes stepper motor rotates as smooth as possible, low-frequency
vibrations are minimal and influence of stepper motor midfrequency
resonance is reduced.
Switching step division mode of every channel is carried out according
fig.2 and fig. 8 by removable jumpers in adapters XP6 (channel №1),
XP7 ( channel №2), XP8 ( channel №3), XP9 (channel №4). Turn off
power device before making any settings.
Coil short-circuit module protection, wrong stepper motor connection
protection, protection against wrong stepper motor coil connection and
coils linked together / ‘+’ power supply.
In some cases by interturn short-circuit of stepper motor coil, short-
circuit protection may not work because there is no exceeding of
permissible alarm current.
This happens because under such coil short circuit resistance does not
equal 0 and the driver maintains the specified current.
Voltage jumps protection – the protection turns on when there is supply
voltage more than 30V, for driver protection against back EMF effect.
Protection functions, setup 11
Fig. 8. A scheme of stepper motor driver and voltage supply connection

Edition from 03.06.2015 17
PLC330. Multichannel stepper motor driver
www.purelogic.ru8 (800) 555 63 74
12. Common problems
12
13
Common problems
Terms of Warranty
Green LED is not on (HL4)
Green LED is not on (HL4)
Red LED is on (HL3)
Red LED blinks slowly (HL3)
Coil circuit protection operated.
The current through coils. exceeded
permissible current.
Check stepper motor connections
Exceeding voltage power protection
operated. It is necessary to reduce power
voltage or reduce stepper motor
braking speed
The warranty period is 12 months after purchasing and is valid only
if all operational conditions and scheduled maintenance are strictly
followed.
1. General terms
1.1. In case of product acquisition as separate components, Seller
guarantees working ability of every component, but does not
assume responsibility for the quality of their joint work (mismatch
of components). If you have questions please consult our technical
support team.
1.2. Seller does not guarantee compatibility of the purchased product
with the one that Buyer already has or bought from third parties.
1.3. Product’s component parts and configuration can be changed by
manufacturer without notice due to the product consistent technical
improvement.
2. Conditions for warranty acceptance
2.1. The product is accepted only in the same completeness of set as it
was purchased.
3. Warranty service procedure
3.1. Warranty service is performed by testing the claimed product
defect.
3.2. If the defect is proved, warranty repair is carried out.
4. We do not assume any responsibility for glass, electric lamps,
starters and expendable materials as well as:
4.1. Damaged product caused by inappropriate transport and store
conditions, wrong connection, operation in abnormal (off-design)
mode, or in conditions which are not manufacturer-supplied (including
temperature and humidity out of limits of recommended range), having
damages due to third-party circumstances (voltage jumps, natural
disasters, etc.), also having mechanical or thermal damages.
4.2. The product with traces of foreign objects or substances impact,
including dust, liquids, insects, also objects having extraneous
inscription.
4.3. The product with traces of unauthorized tampering and (or) repair
process (traces of opening, home-made soldering, elements changing
etc).
4.4. The product with self-diagnostic function that shows improper
exploitation.
4.5. Technically complex product in respect of which assembly and
integration and start-up works were not performed by Seller specialists
or by recommended organizations, except in cases directly regulated
under goods documentation.
4.6. In cases when the product exploitation was performed in
conditions when power supply did not correspond with manufacturer’s
requirements, also when there is no electrical protection device .
4.7. The product which was resold by the initial buyer to the third party.
4.8. The product with defects which were caused by low-quality spare
parts or fulfilled their service life spare parts,consumable materials,
also using spare parts, consumable materials not corresponding with
manufacturer’s requirements.
Produced and accepted in accordance with obligatory requirements of
valid technical documentation and is qualified for exploitation.
Lot number:
Technical
Control
Department

We draw your attention to the fact that there can be
some changes in this instruction due to the product
consistent technical improvement. You can always
download our latest versions at www.purelogic.ru
www.purelogic.ru
Contacts
Moscow +7 (495) 505-63-74
Voronezh +7 (473) 204-51-56
149 Office
160, Leninsky avenue, Voronezh,
Russia, 394033
Monday - Thursday: 8.00–17:00
Friday: 8.00–16.00
Break: 12.30–13.30
sales@purelogic.ru
Table of contents
Other Purelogic DC Drive manuals
Popular DC Drive manuals by other brands
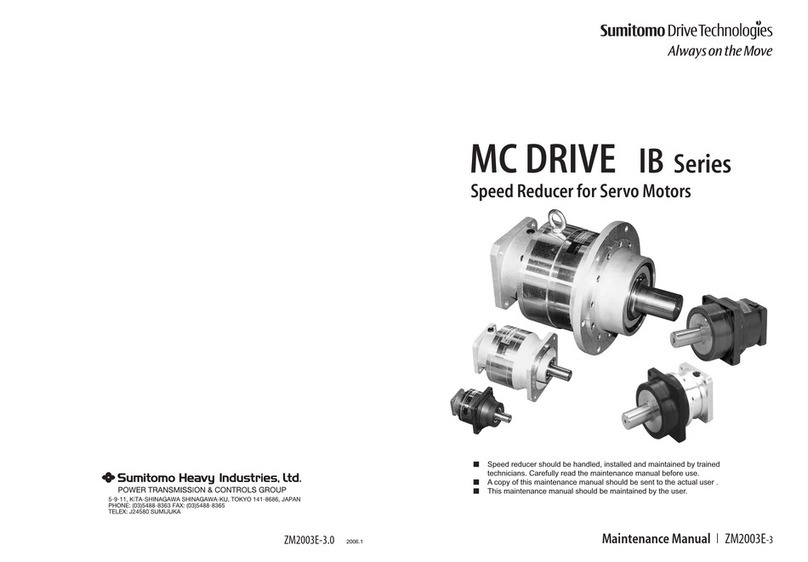
Sumitomo Drive Technologies
Sumitomo Drive Technologies IB Series Maintenance manual
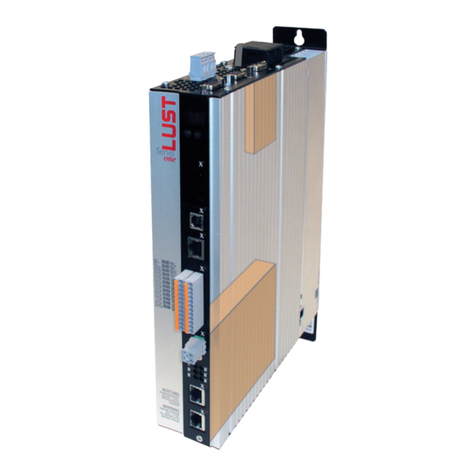
LTi Drives
LTi Drives ServoOne Single axis system Series specification
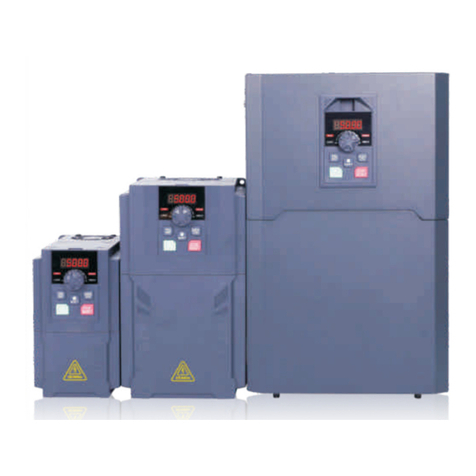
Vicruns
Vicruns 2S-0.4G-B user manual
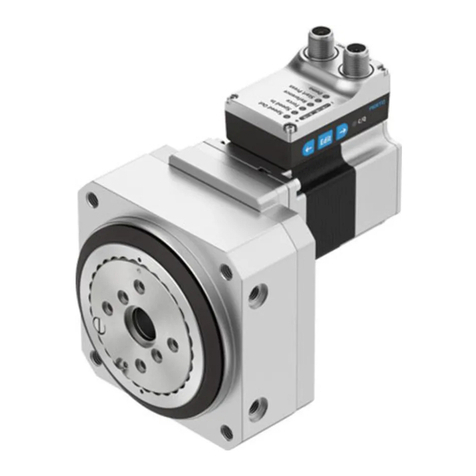
Festo
Festo ERMS Instructions & Operating
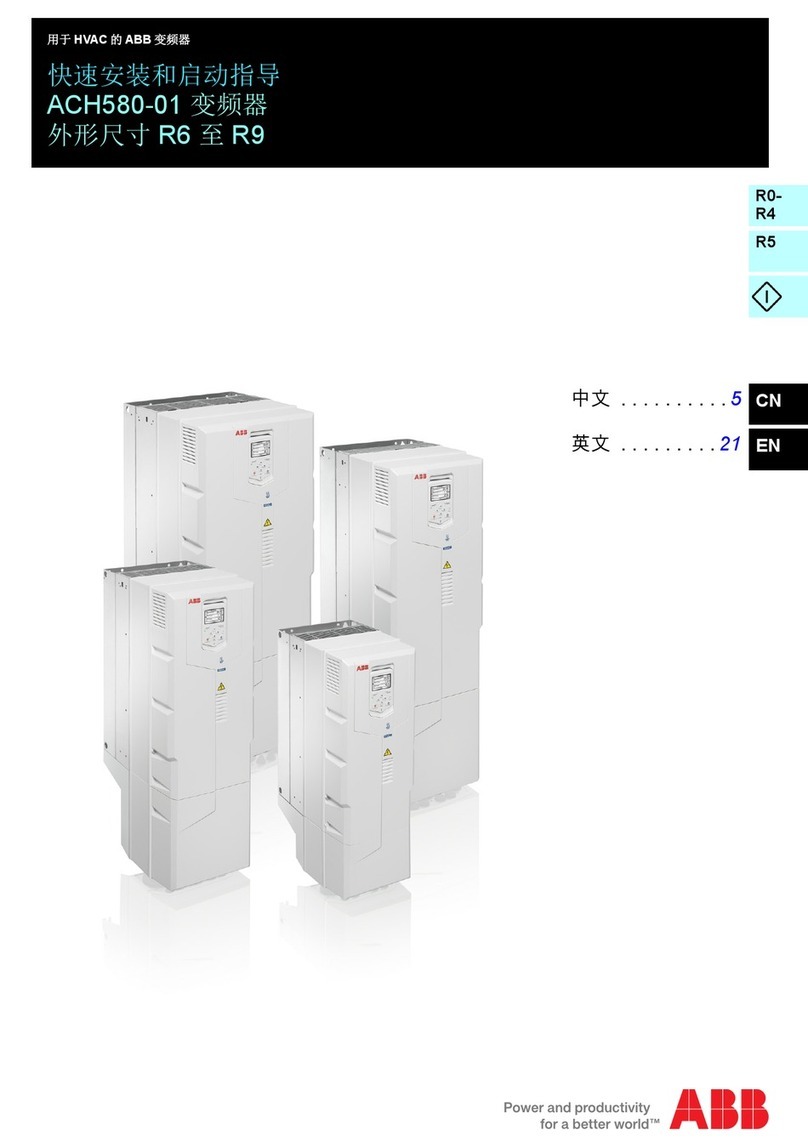
ABB
ABB R6 Quick installation guide
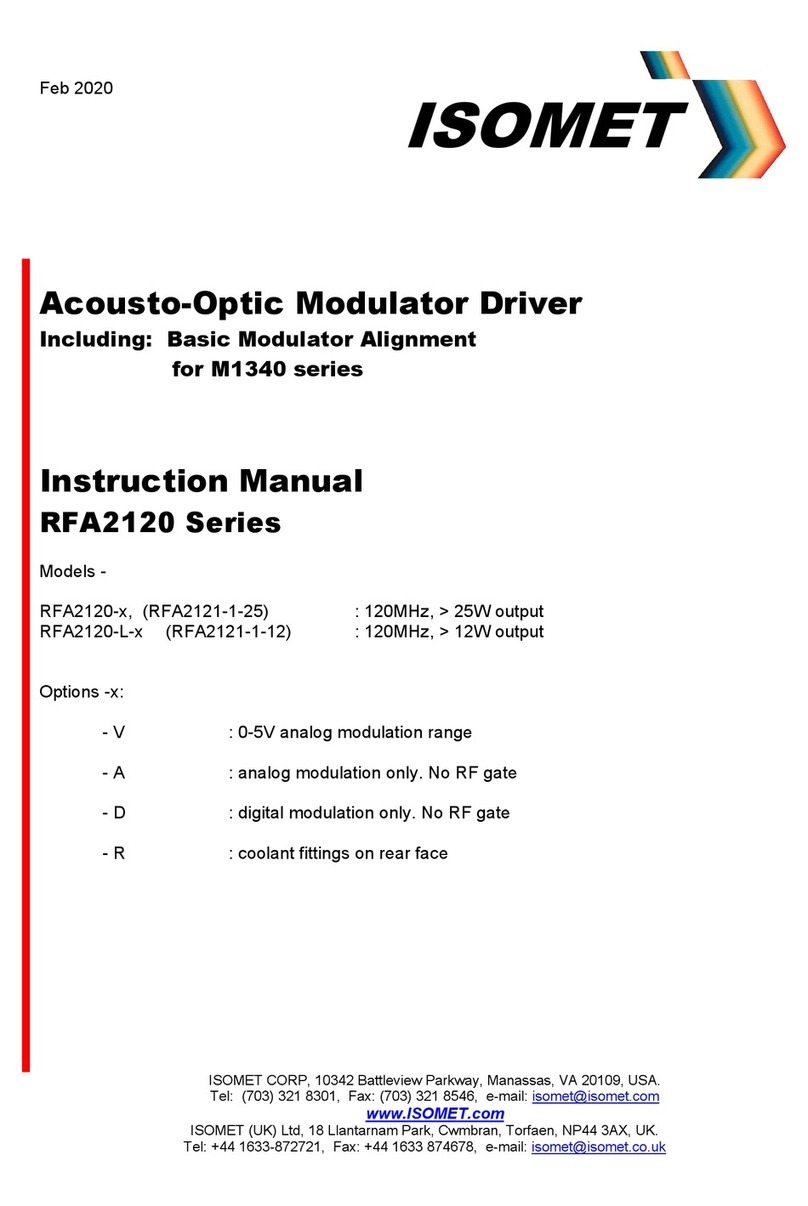
ISOMET
ISOMET RFA2120 Series instruction manual