Quest Engineering CHH-300 Manual

Installation, Operation and Maintenance Instructions
– Read and Save These Instructions –
Installation, Operation and Maintenance Instructions
4201 Lien Rd. Phone 608-237-8400
Madison, WI 53704 Toll-Free 1-866-413-5214
– Read and Save These Instructions –
Specications subject to change without notice.
TS-720
07/12
1
Quest Gas-Fired CHH-300
Warning: If the information in these instructions are not followed exactly, a re or
explosion may result causing property damage, personal injury or death.
- Do NOT store or use gasoline or other ammable vapors and liquids in the vicinity of
this or any other appliance.
- WHAT TO DO IF YOU SMELL GAS
• Do NOT try to light any appliance.
• Do NOT touch any electrical switch; do not use any phone in your building.
• Immediately call your gas supplier from a neighbor’s phone. Follow the gas supplier’s
instructions.
• If you cannot reach your gas supplier, call the re department.
- Installation and service must be performed by a qualied installer, service agency or the
gas supplier.
“Should overheating occur or the gas supply fail to shut off, do not turn off or disconnect
the electrical supply to the pump. Instead, shut off the gas supply at a location external to
the appliance.”
quest
quest

quest
quest 1-866-413-5214
Quest Gas Fired CHH-300 Installation, Operation and Maintenance Instructions
2
www.QuestOnTheJob.com

1-866-413-5214
Quest Gas Fired CHH-300 Installation, Operation and Maintenance Instructions
3
quest
quest www.QuestOnTheJob.com
This appliance is equipped with a Blocked-Flue shutoff device. If any part of the ue-gas
passageway in the combustion chamber, exhaust pipe or rain cap should become blocked or
adversely restricted, a pressure sensing switch (Fig.22 pg.12) will break the electrical control circuit
and not allow the burner to run or the gas valve to open. There is a “Manual Reset” button on this
switch that will have to be reset before re-ring can occur. If the burner fails to start after resetting
once, call a qualied service technician to clean the ue passageways and/or replace the switch.
Cleaning instructions can be found in Section (6.1 G) of the Maintenance section of this manual.

quest
quest 1-866-413-5214
Quest Gas Fired CHH-300 Installation, Operation and Maintenance Instructions
4
www.QuestOnTheJob.com
Table of Contents
1. System Description & Features ................................5
1.1 Description .....................................................5
1.2 Features ..........................................................6
2. Safety ......................................................................6
2.1 General Safety Guidelines...............................6
2.2 Safety Devices and Clearances .........................7
2.3 Heat Transfer Fluid ..........................................7
3. Specications..........................................................7
3.1 Construction Specications.............................7
3.2 Dimensions & Capacities Chart.......................8
3.3 Propane Burner & Fuel Specications .............8
3.4 Natural Gas Burner & Fuel Specications........9
3.5 Circulation Pump............................................9
3.6 Electrical Requirements for Complete System 1 0
3.7 Gauges & Indicator Lights ............................. 1 1
3.8 Controls & Electrical ..................................... 1 1
3.9 Controls, Switches, & Gauges Identication.. 1 3
4. Setup..................................................................... 14
4.1 Positioning Equipment on the job.................... 1 4
4.2 Hose & Accessory Connections..................... 1 4
4.3 Charging the Fluid System............................. 1 6
4.4 Propane Gas Burner Installation & Setup....... 1 7
4.5 Natural Gas Burner Installation & Setup........ 1 8
5. Operation.............................................................. 1 8
5.1 Startup .......................................................... 1 8
5.2 Shutdown...................................................... 1 9
6. Maintenance ......................................................... 1 9
6.1 Service Instructions and Checks .................... 1 9
6.2 Maintenance Frequency Chart....................... 2 3
7. Troubleshooting .................................................... 2 3
7.1 Fault Determination ...................................... 2 3
7.2 Burner Internal Faults .................................... 2 5
7.3 Electrical Schematics..................................... 2 6
Warranty....................................................... 2 9
Serial No. __________________________________
Purchase Date ______________________________
Dealer’s Name ______________________________
Page

1-866-413-5214
Quest Gas Fired CHH-300 Installation, Operation and Maintenance Instructions
5
quest
quest www.QuestOnTheJob.com
1. System Description & Features
1.1 Description
• The CHH is a fuel burning appliance, designed to heat uid “on demand” and provide pumped
circulation of the uid for use in various portable hydronic applications.
• The CHH provides a central source of hot “heat transfer uid” (HTF) for use with dependent heat
exchangers such as:
-Fan coils for heating and drying of structures.
-Multi-circuit line heat exchange hose or tubing for ground thawing, concrete
curing, snow melting and slab heating.
-Custom hydronic heat exchange accessories and applications.
• The CHH gas-red units can be equipped with either of 2 burners, each dedicated to burn one of the
following:
-Natural Gas.
-Propane Gas.
• Pumping and combustion control are achieved with electrical components. The CHH-300 requires a
120 volt, 20 amp, 3-wire grounding circuit.
• The CHH is designed for consistently-efcient outdoor operation.
2: CHH-300, Burner End1: CHH-300, Pump End

Quest Gas Fired CHH-300 Installation, Operation and Maintenance Instructions
6
www.QuestProtect.com
sales@Questprotect.com
quest
quest
1.2 Features
• All exposed components are made of non-corrosive materials such as stainless steel, brass or aluminum.
• The “HTF” circuit includes an open, atmospherically-vented expansion tank, which effectively eliminates
the system from pressure vessel classication.
• The control system includes a sequence of status indicator lights which provide a quick function check
and trouble-shooting aid for the operator.
• The combustion chamber/heat exchanger is completely fabricated from stainless steel and is not
susceptible to corrosion. Temperature turn-down for prolonged periods of operation (such as for concrete
curing) will not harm the chamber.
• For security and environmental protection, all valves, controls, burner, pump, lters and “HTF” tank ller
are either secured behind lockable access doors or are self-lockable.
• Temperature gauges, pressure gauge, system status indicator lights and “HTF” tank level gauge are visible
to the operator even when the system is securely locked down.
• Burners approved for use with the system, come with a permanently installed pressure gauge to simplify
adjustment of gas pressure when setting up the burner.
• Door handles and hose connection couplers for the external HTF circuit are recessed so as not to create
“snag-points” when moving, shipping or delivering the unit.
2. Safety
2.1 General Safety Guidelines:
CAUTION! This is a fuel burning appliance.
• Some surfaces will become extremely HOT!
• When using propane or natural gas, the chance of FIRE or EXPLOSION always exists!
Always follow safe-operating practices and comply with local re and gas codes.
• Before attempting to setup or operate this equipment, it is imperative that the Operator
reads and understands all the information in this manual.
• Untrained people should not attempt to operate this equipment until they receive proper
instruction.
• Maintain instructional and safety labels. Replace damaged labels.
• Observe all posted warnings and cautions.
• Always wear suitable protective clothing and accessories such as safety glasses,
leather gloves, certied work boots and hard hat when working with or operating this
equipment.
• Keep children, pets and all untrained by-standers clear from the heater and accessories.

Quest Gas Fired CHH-300 Installation, Operation and Maintenance Instructions
7
quest
quest www.QuestOnTheJob.com
2.2 Safety Devices and Clearances
• All safety devices must be in place and functioning properly when the equipment is in
operation.
• All hydronic heater panels and doors must be kept closed when the system is operating.
• The ue-gas exhaust pipe and rain-cap requires a minimum of 6” (152 mm) clearance,
from any type of combustible material.
• Clearance from any obstructive objects must be maintained to a minimum of 36” (914
mm) from both ends of the hydronic heater.
• Do not allow anything to obstruct the “Combustion Air Intake”.
2.3 Heat Transfer Fluid
Precautions and measures to follow when working with “heat transfer uid” (Inhibited aqueous propylene
glycol).
• Ventilation - Good general ventilation should be sufcient for most conditions.
• Respiratory protection - No respiratory protection should be needed.
• Skin protection - For brief contact, no precautions other than clean body-covering clothing should be
needed.
• Use impervious gloves when prolonged or frequently repeated contact should occur.
• Eye protection - Use safety glasses.
First aid measures.
• Eyes - Flush eyes with plenty of water.
• Skin - Wash off in owing water or shower.
• Ingestion - Induce vomiting if large amounts are ingested. Consult medical personnel.
• Inhalation - Remove to fresh air if effects occur. Consult a physician.
• Note to physician - No specic antidote. Supportive care. Treatment based on judgement of the physician
in response to reactions of the patient.
3 Specications
3.1 Construction Specications
• The “CHH” includes an aluminum “enviro-containment” base, with fork-lift pockets.
• The exterior enclosure panels are made of stainless steel.
• The framework for the enclosure and the base are built of structural aluminum. A top center hoisting hook
is included.

quest
quest 1-866-413-5214
Quest Gas Fired CHH-300 Installation, Operation and Maintenance Instructions
8
www.QuestOnTheJob.com
• Primary access for operation and service is provided for through hinged, lockable doors at the two ends
of the enclosure.
• Both side panels and both roof panels are fastener-attached for potential removal.
• Then combustion chamber/heat exchange section is fabricated from stainless steel.
• Access for cleaning the chamber is from the burner end with minimal disassembly required. The
procedure consists of removing the burner and inside chamber section.
• Temperature turn-down and condensing within the chamber can not harm the chamber.
• The exhaust ue for the burner exits through the roof of the enclosure. The exposed roof ashing is made
from aluminum. The rain cap and ue pipe are made of stainless steel.
3.2 Dimensions and Capacities
3.3 Propane Gas Burner and Fuel Specications (Fig. 3)
• The “Gas Burner” is a power, forced-draft, type with direct spark ignition, manufactured by Riello
Burners.
• A CSA/UL version gas train is factory installed in units equipped for either propane or natural gas. The gas
train works with either burner.
• Two gauges are mounted to pressure-tap ports on the gas train for use in setting the burner and
monitoring performance(Fig. 24) .
Length of Cabinet inches (millimeters) 72 (1829)
Width of Cabinet inches (millimeters) 22 (559)
Height of Cabinet inches (millimeters) 48 (1219)
Height to Top of Rain Cap inches (millimeters) 58 (1473)
Heat Transfer Fluid Capacity US gallons (liters) 20 (76)
Weight: with heat transfer uid pounds (kilograms) 600 (272)
Riello Burner Model Propane 40-G400-LP
Operational Mode single stage
Electrical Characteristics V / A / Hz / Ph 120 / 2.2 / 60 / 1
Orice: factory equipped # 1.5
Diaphragm: factory equipped # C14
Gas Supply Pressure: Minimum “WC (KPa) 8 (1.99)
Gas Supply Pressure: Maximum “WC (KPa) 13 (3.24)
Gas Manifold Pressure ( P): factory set “WC (KPa) 5.0 (1.25)
Heat Setting: factory set # 1
Air Gate Setting: factory set # 3.0
Heat Input B/tu/H (Watts) 250,000 (73,250)
Heat Output: @ 80% net efciency B/tu/H (Watts) 200,000 (58,600)

1-866-413-5214
Quest Gas Fired CHH-300 Installation, Operation and Maintenance Instructions
9
quest
quest www.QuestOnTheJob.com
3.4 Natural Gas Burner and Fuel Specications (Fig. 3)
• The “gas burner” is a power, forced-draft, type with direct spark ignition, manufactured by Riello Burners.
• A CSA/UL version gas train is factory installed in units equipped for either natural gas or propane. The gas train
works with either burner.
• Two gauges are mounted to pressure-tap ports on the gas train for use in setting the burner and monitoring
performance (Fig. 24).
3.5 Circulation Pump (Fig. 4)
• The HTF circulation pump is a stainless steel, direct drive centrifugal type.
• The pump is located inside the enclosure at the opposite end to the burner and can be accessed through a
hinged lockable door (Fig. 1).
• A panel-mounted pressure gauge is connected to the output side of the HTF pump by means of a 1/8” ID
hydraulic hose and ttings (Fig. 23).
3: Gas Burner, LP or Natural Gas Train
Riello Burner Model Natural Gas 40-G400-NG
Operational Mode single stage
Electrical Characteristics V / A / Hz / Ph 120 / 2.2 / 60 / 1
Orice: factory equipped # 2.2
Diaphragm: factory equipped # C4
Gas Supply Pressure: Minimum “WC (KPa) 7 (1.74)
Gas Supply Pressure: Maximum “WC (KPa) 10.5 (2.61)
Gas Manifold Pressure ( P): factory set “WC (pascals) 3.8 (946)
Heat Setting: factory set # 1
Air Gate Setting: factory set # 3.5
Heat Input B/tu/H (Watts) 300,000 (87.9)
Heat Output: @ 80% net efciency B/tu/H (Watts) 240,000 (70,320)

quest
quest 1-866-413-5214
Quest Gas Fired CHH-300 Installation, Operation and Maintenance Instructions
10
www.QuestOnTheJob.com
3.6 Electrical Requirements for Complete System
Supply Voltage Volts 120
Circuit Amperage Amps 20
Hertz HZ 60
Phase PH single
Control Circuit Voltage Volts 120
Power Inlet - NEMA Twistlock L5-20P
5: Power Inlet Plug
4: Fluid circulation Pump
Goulds Pump Model 1ST1E4C4
Impeller Diameter inches (millimeters) 5.1875 (132)
Motor Horsepower HP (Watts) 1.0 (746)
Voltages pump can run on Volts 120/240
Full Load Amp Rating - Franklin motor Amps 10.4/5.2
- Emerson motor Amps 12.3/6.2
System Design Flow Rate USGPM (liters/sec) 30 (1.89)
System Design Operating Pressure PSI (kilopascals) 35 (241)

1-866-413-5214
Quest Gas Fired CHH-300 Installation, Operation and Maintenance Instructions
11
quest
quest www.QuestOnTheJob.com
3.7 Gauges and Indicator Lights
• A cluster of gauges and status-indicator lights are located inside the UL approved control panel. This panel
is located behind the burner access door near the top (Fig. 2). These gauges and lights are visible from the
exterior through plexi-glass windows in the access door and the control panel door.
• A digital gauge (Fig. 12) monitors each of the following:
- HTF supply temperature.
-HTF return temperature.
• A digital hours meter (Fig. 12) logs system run-time.
• A series of 6, LED indicator lights (Fig. 13) illuminate in sequence as each of the following scenarios is
proven:
-#1 - 115 volt control power is present - clear lens.
-#2 - HTF level is adequate in reservoir - green lens.
-#3 - High temp auto switch has not interrupted the circuit - green lens.
-#4 - High temp limit control has not interrupted the circuit - green lens.
-#5 - High pressure switch has not interrupted the circuit - green lens.
#6 - Aquastat is calling for heat - green lens.
3.8 Controls and Electrical
• The UL approved electrical box, located inside the enclosure, above the burner, houses specic electrical
components, besides the lights and gauges, and serves as a junction box for cords going to and from remote
electrical components (Fig. 6 & Fig. 7).
• The following components are part of and are located in or on the UL approved box:
-Main power disconnect (Fig. 9).
-Pump ON/OFF switch (Fig. 10).
-Burner circuit ON/OFF switch (Fig. 11).
6: Control Panel, Outer 7: Control Panel, Inner

quest
quest 1-866-413-5214
Quest Gas Fired CHH-300 Installation, Operation and Maintenance Instructions
12
www.QuestOnTheJob.com
-Main system breaker (Fig. 14).
-Pump circuit breaker (Fig. 14).
-Burner circuit breaker (Fig. 14).
-Power disconnect switch (Fig. 15).
-Temperature gauge transformers 6VDC (Fig. 16).
-LED lights - 120 volt (Fig. 13).
-Hours meter - 120 volt (Fig. 12).
-Terminal blocks (Fig. 18).
-Contactors (Fig. 17).
-Electronic operating thermostat (Fig. 8).
• The following items are remotely connected to cords that exit from the control panel: (see chart below
for details of these components)
-Main power male inlet-plug (twist lock) (Fig. 5).
-Low water cut-off switch (mounted on HTF reservoir) (Fig. 19).
-High Temp Auto switch (mounted in HTF plumbing circuit) (Fig. 20).
-High Temp Limit switch (mounted in HTF plumbing circuit) (Fig. 21).
-High Pressure Limit switch (Fig. 22).
-HTF circulating pump (Fig. 4). (see pump chart above for details)
-Burner (Fig. 3). (see burner chart above for details)

1-866-413-5214
Quest Gas Fired CHH-300 Installation, Operation and Maintenance Instructions
13
quest
quest www.QuestOnTheJob.com
8: Operator, Digital 9: Main Power Switch Knob 10: Pump Switch 11: Burner Switch
12: Temperature Gauges & Hour Meter 13: LED Indicator Lights
3.9 Controls, Switches & Gauges Identication
• Mounted on Control Panel
• Mounted Behind Control Panel
• Mounted Remotely
14: Circuit Breakers 15: Main Power Switch Body 16: Transformers for Digital Temp. Gauges
17: Contactors 18: Terminal Blocks

quest
quest 1-866-413-5214
Quest Gas Fired CHH-300 Installation, Operation and Maintenance Instructions
14
www.QuestOnTheJob.com
• Pump and Gas Pressure Gauges
4. Setup
4.1 Positioning Equipment on the Job
Before choosing the location to place the central hydronic heater on a job site, several factors should be
considered.
• If possible, the CHH should be placed at a central position that will minimize and equalize the lengths
of hoses. This helps to ensure maximized and equalized HTF ow.
• Convenient access to a suitable electrical connection, if site power is to be used. 120V, 1PH, 60Hz,
20A, 3-wire grounding is required.
• Convenient access to bulk truck re-fueling in the case of propane systems.
• Do not locate in the path of job site trafc.
• Avoid locations that will expose the CHH to intense dust or other sources of air contamination. Clean
owing air is essential to maintain clean combustion.
• Observe all requirements listed in the “Instructions for Installation” document provided with this unit.
4.2 Hose and Accessory Connections
In order to make use of the heated uid, it is necessary to lay out a circuit of hoses to; distribute the hot uid,
transfer it’s heat to another medium and return the cooled uid to the CHH for re-heating (Fig. 25).
19: Low Water Cutoff 20: High Temp Auto Switch 21: High Temp Limit Switch 22: High Pressure Switch
23: Pump Pressure Gauge (PSI) 24: Gas Pressure Gauges (“WC)

1-866-413-5214
Quest Gas Fired CHH-300 Installation, Operation and Maintenance Instructions
15
quest
quest www.QuestOnTheJob.com
• Primary 1” hoses are used from the CHH quick-connect couplings (Fig. 26) to feed a manifold for either
multiple fancoils in air heating situations (Fig. 28) or multiple 5/8” hose circuits for ground thawing,
concrete curing, slab heating or snow melting (Fig. 29).
• Use only “approved hose” as supplied by ThermaStor. Otherwise, compatibility issues may arise.
• Hoses are pre-charged with the recommended mixture of water and propylene glycol and are equipped
with hydraulic-style quick couplers. Every hose has a male connector on one end and a female
connector on the other end; therefore any hose can be used for either the supply side or the return side
of the hose circuit.
• Route hoses to achieve minimum chance of damage from trafc of any kind and at the same time
minimize the overall circuit length.
• Provide protection from “Kinking” of hoses that would restrict ow.
• When connecting quick couplers, ensure that the connections are “Fully Engaged” and snapped into
place or ow will not take place through the coupler connection.
• For long term, building heating projects it is advised to insulate all hose sections located outdoors,
between the CHH-300 and the exterior building wall. Special “Insulating Wraps” are available for this
purpose.
25: Layout for Fluid Distribution
1. Central Hydronic Heating Unit
2. Burner& Heat Exchanger
3. Circulating Pump
4. Reservoir for Expansion & Filling
5. Primary Fluid Hoses, 1”
6. Secondary Fluid Hoses, 3/4” or 1”
7. Manifold for Multiple Connections
8. Fancoil Heat Exchanger
9. Heat Transfer Coil
10. Air Moving Fan
11. Heated Supply Air
12. Intake Air
13. Hose Grid Line Heat Exchanger 5/8”
14. Vapor Barrier
15. Insulated Tarps

quest
quest 1-866-413-5214
Quest Gas Fired CHH-300 Installation, Operation and Maintenance Instructions
16
www.QuestOnTheJob.com
4.3 Charging the Fluid System
• The CHH-300, all hose and all accessories are shipped pre-charged with the “approved blend” of heat
transfer uid (HTF). The required uid is a 50% blend of Inhibited propylene glycol and de-mineralized
neutral PH (#7)water. (Freeze protection to -29ºF). The HTF provided with a new system and accessories
is marketed as DowFrost. Use of any other product that cannot be proven to be equal in all respects will
void warranty of the system.
26: Hoses Connected to CHH Unit 27: Fancoil Connected to CHH Unit
28: Manifolds for Fancoils - Supply & Return 29: Manifold for Thaw & Cure
30: HTF Level Gauge & Vented Filler Cap 31: HTF Circuit Valves, Y-strainer & High Temp. Limit

1-866-413-5214
Quest Gas Fired CHH-300 Installation, Operation and Maintenance Instructions
17
quest
quest www.QuestOnTheJob.com
• Check the HTF level gauge (Fig. 30). The reservoir should be ¼ to ½ full when the system is cold. Add
approved uid, if necessary, at the vented ller cap (Fig. 30).
• Connect all primary hoses from the CHH-300 to the distribution manifold.
• Place all fancoils in the desired locations and route all the hoses to them OR lay out all hose grid circuits
for ground thaw or concrete curing.
• Connect hoses from the manifold to ONE fancoil or ONE thaw/cure loop ONLY.
• Open 2 HTF circuit valves (Fig. 31).Turn ON the circulating pump switch (Fig. 10) and let the uid
circulate until all the air is eliminated from the rst branch circuit. Air has been purged when steady
pressure of 30 to 35 PSI is observed at the glycol pressure gauge (Fig. 22).
• Connect each fancoil or thaw/cure loop, in turn, one at a time, in the same manner as above. When all
are connected and the pressure gauge maintains steady pressure, the system is charged and ready for
use.
• Check the HTF level again and top up if necessary (¼ to ½ full).
4.4 Propane Burner Installation and Setup (Fig. 3)
• Refer to the Riello Burner 40-G400 manual (which is included with this package) for detailed
information and instruction.
• Specic propane gas burner settings for the CHH-300 are as follows.
Riello Burner Model 40-G400
Orice: # 1.5
Diaphragm: # C14
Gas Supply Pressure: Minimum “WC (KPa) 8 (1.99)
Gas Supply Pressure: Maximum “WC (KPa) 13 (3.24)
Head Setting: factory set # 1
Gas Manifold Pressure ( P): factory set “WC (KPa) 5.0 (1.25)
Air Gate Setting: factory set # 3.0
Heat Input B/tu/H (Watts) 250,000 (73,250)
Heat Output: @ 80% net efciency B/tu/H (Watts) 200,000 (58,600)

quest
quest 1-866-413-5214
Quest Gas Fired CHH-300 Installation, Operation and Maintenance Instructions
18
www.QuestOnTheJob.com
4.5 Natural Gas Burner Installation and Setup (Fig. 3)
• Refer to the Riello Burner 40-G400 Manual (which is included with this package) for detailed
information and instruction.
• Specic natural gas burner settings for the CHH-300 are as follows.
5. Operation
5.1 Startup
• Make sure the CHH-300 is connected to a correct, stable power source (120V, 20A, 60Hz, 3-wire
Grounding) and proper gauge chords are used (12 gauge minimum).
• Verify adequate and correct fuel supply for the burner as it is equipped on the system (propane or
natural gas). Open all valves in the respective fuel-supply lines.
• Make sure at least one circuit of HTF hose is connected to the CHH-300 to provide adequate circulation
(see hose and accessory connections section 4.2).
• At the control panel (Fig. 6), remove 2 thumb screws to open and expose the inner panel (Fig. 7), turn
ON the three breakers located behind the light panel (Fig. 14). Close and refasten the panel.
• Turn ON the main power switch (Fig. 9). The white unit power light (Fig. 13) will come on, as well as the
two digital temperature gauges and hour meter (Fig. 12).
• Turn ON the pump switch (Fig. 10) and check the pump pressure gauge (Fig. 22). Steady pressure
around (30 to 35 PSI), indicates that no air remains in the uid circuit.
• Once a stable pump pressure is achieved, turn ON the burner switch (Fig. 11). The following sequence
should now occur: Observe the LED light cluster (Fig. 13).
-The glycol level light will turn on (indicating that there is a sufcient amount of HTF in the system).
-The high temp auto light will turn on (This indicates that the high temp auto safety switch has not
broken the circuit).
-The high temp limit light will turn on. (This indicates that the high temp limit safety switche has not
broken the circuit).
-The high pressure limit switch light will turn on. (This indicates that the blocked ue high pressure
safety switch has not broken the circuit).
-A few seconds later, the stat light will come on and the burner fan will purge the combustion
chamber for a few seconds.
Riello Burner Model 40-G400
Orice: # 2.2
Diaphragm: # C4
Gas Supply Pressure: Minimum “WC (KPa) 7 (1.74)
Gas Supply Pressure: Maximum “WC (KPa) 10.5 (2.61)
Head Setting: factory set # 1
Gas Manifold Pressure ( P): factory set “WC (KPa) 3.8 (0.95)
Air Gate Setting: factory set # 3.5
Heat Input B/tu/H (Watts) 300,000 (87,900)
Heat Output: @ 80% net efciency B/tu/H (Watts) 240,000 (70,320)

1-866-413-5214
Quest Gas Fired CHH-300 Installation, Operation and Maintenance Instructions
19
quest
quest www.QuestOnTheJob.com
-The burner should light following the pre-purge. If air is still present in the gas lines, the burner
may not light and will lock out. It might be necessary to push the red reset button on the burner
module 2 or 3 times until gas reaches the burner head and ignition takes place.
• Make sure the stat (Fig. 8) is set at the desired temperature. DO NOT Operate at temperatures above
200ºF, or damage to inline controls and certain accessory components can result. To adjust setpoint
on this control just use the up and down key. There is no need to go into the menu of the control to
perform this function. The control simultaneously displays setpoint temperature and actual supply uid
temperature.
• Once the setpoint temperature has been reached, the burner will cycle off and on as needed.
5.2 Shutdown
• Turn OFF the burner switch (Fig. 11). The burner will no longer recycle but the circulation pump will
continue to run.
• It is recommended that the uid be allowed to continue circulating until it has cooled down to 100ºF or
lower.
• Turn OFF the pump switch (Fig. 10). If any fancoils and hoses have been placed at a higher elevation
than the CHH-300, the primary hoses should be immediately disconnected from the CHH-300 (Fig. 26).
This will prevent uid from draining back and overowing at the HTF reservoir vent (Fig. 30).
• Turn OFF the main power switch (Fig. 9).
• Turn OFF manual gas supply valves.
• If the system is to be de-commissioned, it is now safe to disconnect the power supply, the natural gas or
propane supply (if applicable) and all HTF circulation hoses, manifolds and accessories.
6. Maintenance
6.1 Service Instructions and Checks
“CAUTION: Label all wires prior to disconnection when servicing controls. Wiring errors
can cause improper and dangerous operation. Verify proper operation after servicing.
A. To achieve and ensure clean combustion from the burner, a ““Flue-Gas Analyzer” must be used to verify
clean combustion. Perform the following checks while the burner is ring. Must be performed by a trained
service technician ONLY. Refer to the Riello burner Manual for burner adjustment instructions. This check
should be performed, every time, when putting the system into operation on a new project and a minimum
of once yearly.
a. Ensure that the gas manifold pressure is at 3.5”WC for propane red units or 3.8”WC for natural gas
red units. Adjust if necessary.
b. Regulation of combustion air ow is made by adjustment of the manual air adjustment plate. Initial
suggested setting is (3.5) for natural gas and (3.0) for propane gas.
c. Final position of the air adjustment plate must be set based on instrument readings of not greater
than 12.0% CO2 for propane-red systems and 10% CO2 for natural gas systems. Final readings must
be taken with all service-access doors closed.

quest
quest 1-866-413-5214
Quest Gas Fired CHH-300 Installation, Operation and Maintenance Instructions
20
www.QuestOnTheJob.com
B. After placing this unit in operation, the ignition system safety shutoff device must be tested. Must be
performed by a trained service technician ONLY. This check should be performed, every time, when putting
the system into operation on a new project or a minimum of once yearly.
a. Shut OFF the “Burner Circuit” power switch.
b. Disconnect the electrical wire which connects the “Ionization Probe” to the burner’s control box.
The wire has a clip-together connector for convenience.
c. Turn the power switch back ON and initiate burner lighting procedure. After the short pre-purge
cycle, the burner should light but go out in 5 seconds and lock out. If the burner does not lock out
with the ionization probe’s lead wire disconnected, consult the operator’s manual for troubleshooting
procedures.
d. To put the unit back in standard operating mode, turn OFF the burner circuit power switch, re-
connect the electrical wire which connects the “Ionization Probe” to the burner’s control box and turn
ON the “Burner Circuit” power switch.
C. Examine the ue gas exhaust pipe and rain cap to be sure they are solidly attached and free from any
type of obstruction. Clean if necessary.
a. This check should be performed, every time, when putting the system into operation on a new
project or a minimum of once yearly.
D. After placing this unit in operation, the low water safety shutoff device must be tested. Must be
performed by a trained service technician ONLY. The low water cutoff switch is located in plain view at the
same end of the CHH-300 as the circulating pump and is identied with a label.
a. Push the test switch on the outside of the control. This will simulate a “Low Water” condition and
open the burner circuit to prevent burner initiation.
b. By pushing the reset switch, the control will restore function to the burner circuit as long as there is
uid touching the probe. The electronic probe is a “self cleaning” type and should not require service.
c. This control should be tested every time, when putting the system into operation on a new project or
a minimum of once yearly.
E. After placing this unit in operation, the high temperature limit safety shutoff device must be tested. Must
be performed by a trained service technician ONLY. Two high temperature limit switches are located in plain
view at the same end of the CHH-300 as the circulating pump and are identied with labels. One of these
switches re-sets itself automatically and is set at a slightly lower temperature (about 5ºF) than the other which
must be manually re-set after its set point has been reached.
a. With the burner ring, set the main digital operating stat to a temperature value that is at least 5ºF
higher than the set point of the manual re-set high temperature limit switch.
b. When the uid temperature reaches the set point of the automatic re-set limit switch, it should shut
down the burner. As the uid cools down 2 or 3 degrees, the burner should re-re. This automatic re-set
limit switch should function like a second thermostat and will take over as operator of the burner.
c. If you now adjust the set point of the automatic re-set limit switch to a level a few degrees higher
than the set point of the manual re-set limit switch, the burner should continue to re until the set point
of the manual re-set high limit is reached. At this point the burner should be shut down and this time
should not come back on as the uid cools back down.
d. The manual re-set high limit will need to be manually re-set, by pushing the red re-set button. Adjust
the operator back down to a normal operating lower setting and re-adjust the automatic high limit back
down to its regular set point at about 5ºF lower than the manual re-set limit.
Table of contents
Other Quest Engineering Heater manuals
Popular Heater manuals by other brands
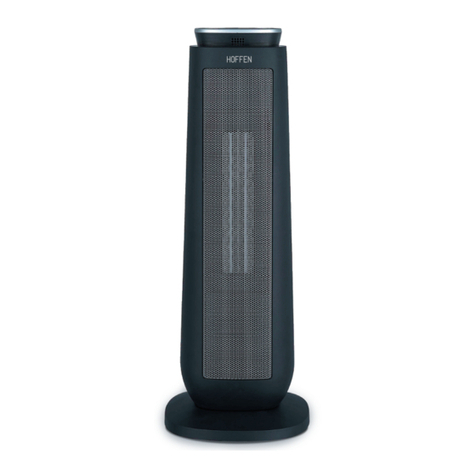
HOFFEN
HOFFEN ADTM-H102 instruction manual
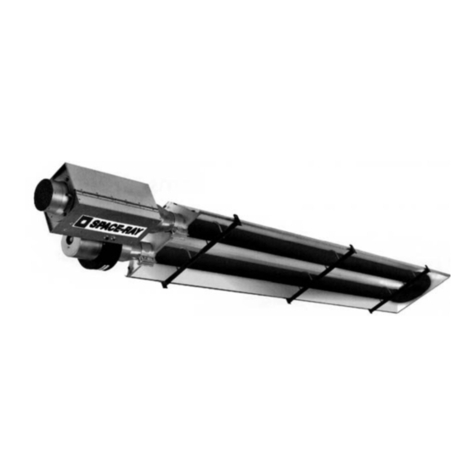
Space-Ray
Space-Ray CBU09 Installation, servicing and operating instructions
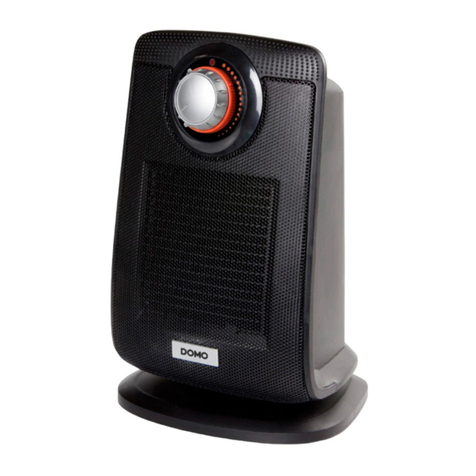
Linea 2000
Linea 2000 DOMO DO7338H Instruction booklet
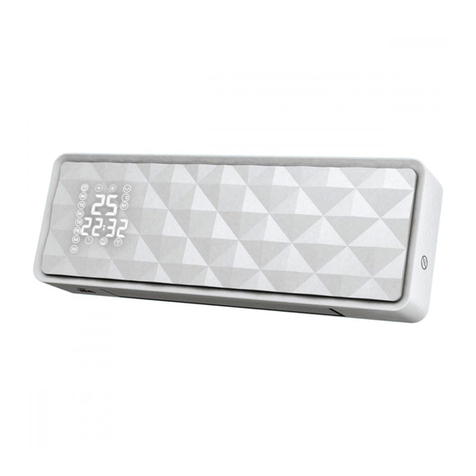
Somogyi Elektronic
Somogyi Elektronic home FKF 54202 instruction manual

LuxenHome
LuxenHome WHIF993 instruction manual
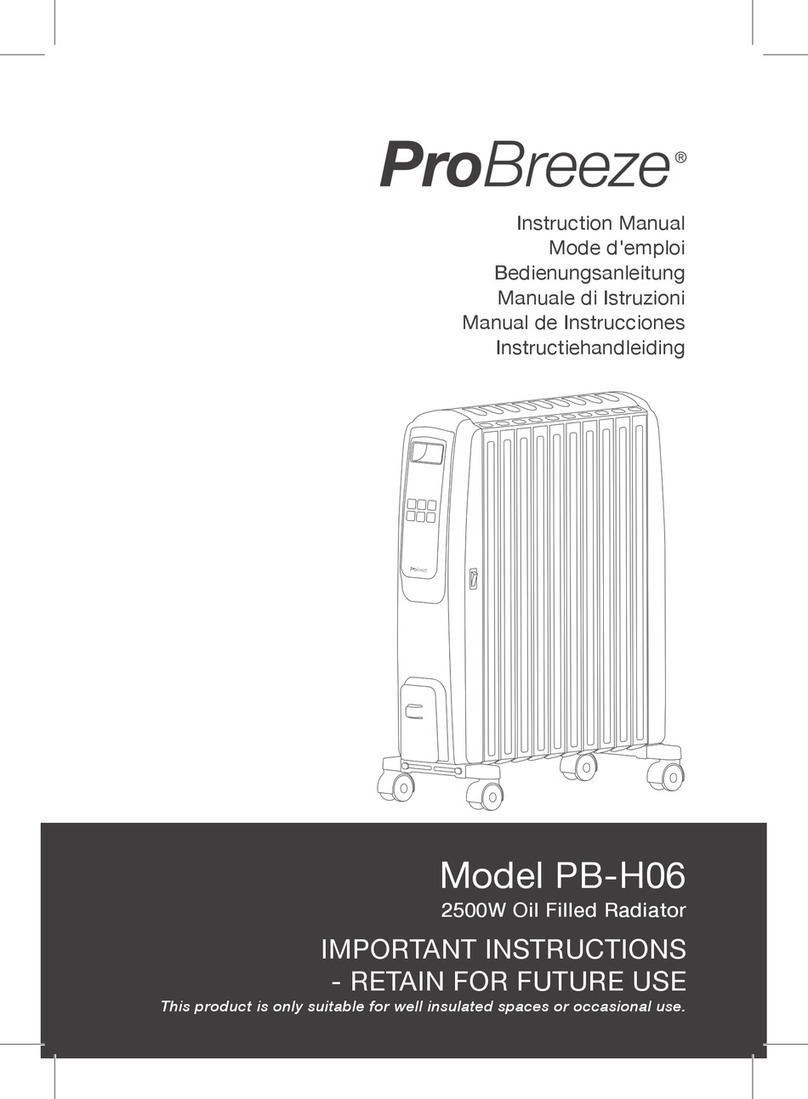
Pro Breeze
Pro Breeze PB-H06 instruction manual