Rapid Controls SAB-Q2 User manual

SAB-Q2 Quick Start January 12, 2011
SAB-Q2 Quick Start
This document aims to provide a systematic setup procedure to enable you to setup and use your SAB-Q2
as easily as possible This guide will concentrate on connections and basic setup More information is
available for advanced setup, refer to the SAB-Q2 manual If you do not have a SAB-Q2 manual, call
Rapid Controls or visit the Rapid Controls website, www rapidcontrols com
Figure 1: SAB-Q2 Connector and Jumper Placement
1. Power Connection (Connector J4)
Power input to J4 provides power to the board and the sensors Refer to the sensor requirements before
choosing a power source for the SAB-Q2 The following pins must be connected:
Pin 1 is connected to either +24VDC or +15VDC depending on the requirements of the sensor
Pin 2 is connected to ground
Pin 3 is connected to –15VDC if required by the sensor Otherwise, no connection is made
Rapid Controls nc.
Box 8390 Rapid City, SD 57709
Phone: 605-348-7688 Fax: 605-341-5496
http://www rapidcontrols com/ email: info@rapidcontrols com

SAB-Q2 Quick Start 2 of 5 January 12, 2011
2. Sensor Connections (Connector J3)
J3 provides the connections to the sensors Power from J4 is passed through to the sensor on J4 pins 5,
7, 12, and 14 The following pins must be connected for operation of sensor channel 0: (NOTE: MTS
and Balluff Color Codes are specified below, other sensor manufacturers may be different):
Pin 1 is connected to the sensor CLK+/INT+ wire (MTS: yellow; Balluff: yellow)
Pin 2 is connected to the sensor CLK-/INT- wire (MTS: green; Balluff: pink)
Pin 3 is connected to the sensor DATA+/GATE+ wire (MTS: pink; Balluff: gray)
Pin 4 is connected to the sensor DATA-/GATE- wire (MTS: gray; Balluff: green)
Pin 5 is connected to the sensor +power wire (MTS: red or brown: Balluff: brown)
Pin 6 is connected to the sensor ground wire (MTS: white; Balluff: blue) The shield may need to
be connected, depending on the type of sensor
Pin 7 is connected to the sensor –power wire (MTS: blue) if needed
The following pins must be connected for operation of sensor channel 1:
Pin 8 is connected to the sensor CLK+/INT+ wire (MTS: yellow; Balluff: yellow)
Pin 9 is connected to the sensor CLK-/INT- wire (MTS: green; Balluff: pink)
Pin 10 is connected to the sensor DATA+/GATE+ wire (MTS: pink; Balluff: gray)
Pin 11 is connected to the sensor DATA-/GATE- wire (MTS: gray; Balluff: green)
Pin 12 is connected to the sensor +power wire (MTS: red or brown; Balluff: brown)
Pin 13 is connected to the sensor ground wire (MTS: white; Balluff: blue) The shield may need to
be connected, depending on the type of sensor
Pin 14 is connected to the sensor –power wire (MTS: blue) if needed
3. Quadrature Connections (Connector J2)
The quadrature output from the SAB-Q2 is provided on connector J2 This connector also provides
marker outputs (quadrature Z line); see the manual for details The following connections should be
made for operation of quadrature channel 0:
Pin 1 is connected to the quadrature line A input of the controller
Pin 2 is connected to the quadrature line /A (A not) input of the controller
Pin 3 is connected to the quadrature line B input of the controller
Pin 4 is connected to the quadrature line /B (B not) input of the controller
Pin 5 is connected to the marker line Z input of the controller Optional
Pin 6 is connected to the marker line /Z (Z not) input of the controller Optional
Rapid Controls nc.
Box 8390 Rapid City, SD 57709
Phone: 888-510-7688 Fax: 605-341-5496
http://www rapidcontrols com/ email: info@rapidcontrols com

SAB-Q2 Quick Start 3 of 5 January 12, 2011
Pin 7 is connected to logic ground
The following connections should be made for operation of quadrature channel 1:
Pin 8 is connected to the quadrature line A input of the controller
Pin 9 is connected to the quadrature line /A (A not) input of the controller
Pin 10 is connected to the quadrature line B input of the controller
Pin 11 is connected to the quadrature line /B (B not) input of the controller
Pin 12 is connected to the marker line Z input of the controller Optional
Pin 13 is connected to the marker line /Z (Z not) input of the controller Optional
Pin 14 is connected to logic ground
4. Serial Communications (Connector J1)
Connector J1 provides serial communications The following pins must be connected for RS-232
communications:
Pin 1 is connected to logic ground on the host computer (pin 5 on a DB-9 connector, pin 7 on a
DB-25 connector)
Pin 2 is the SAB-Q2’s receive line and is connected to the host computer’s transmit line (pin 3 on
a DB-9 connector, pin 2 on a DB-25 connector)
Pin 3 is the SAB-Q2’s transmit line connected to the host computer’s receive line (pin 2 on a DB-
9 connector, pin 3 on a DB-25 connector)
If the host computer requires the use of hardware handshaking, the host’s DTR line must be tied to
the host’s DSR line (pin 4 to pin 6 on a DB-9), and the host’s RTS line must be tied to the host’s
CTS line (pin 7 to pin 8 on a DB-9)
Host DB-9
5
9
4
8
3
7
2
6
1
JP1
SAB-Q2 RS-232
1
2
3
4
5
6
7
8
9
10
Figure 2: Diagram of SAB-Q2 RS-232 Serial Cable
Note: Wires between pins 4 and 6 and pins 7 and 8 can be omitted if host computer does not require hardware handshaking
After connecting the host computer to the SAB-Q2 and setting the correct communications parameters,
apply power to the SAB-Q2 Press the spacebar several times quickly The SAB-Q2 will respond with
a menu If the SAB-Q2 does not present a menu, check the serial cabling and terminal software setup
Rapid Controls nc.
Box 8390 Rapid City, SD 57709
Phone: 888-510-7688 Fax: 605-341-5496
http://www rapidcontrols com/ email: info@rapidcontrols com

SAB-Q2 Quick Start 4 of 5 January 12, 2011
5. Send All nputs and Sensor Status Outputs (Connector J1)
Connector J1 is also used for send all input and sensor status outputs The two send all inputs
command the SAB-Q2 to send the absolute position of the sensor over the quadrature channel The
sensor status outputs show the status of the sensors The output will be active when the sensor is
operating properly The inputs are bi-directional and can source or sink current depending on the
voltage applied to J1-8 If the controller has a sinking output apply + 12 to 24 VDC to J1-8 and allow
the controller to ground the appropriate send all input to cause the send all function If the controller
has a sourcing output apply ground to J1-8 and allow the controller to source +12 to 24V to the
appropriate send all input to cause the send all function The X2 jumper connects the status outputs to
match the choice of common applied to J1-8 If the input common is grounded then the outputs must
be jumpered to be sinking If the input common is connected to +12 to 24V then the outputs must be
jumpered to be sourcing
Desired nput
and Output
Type
X2 Setup J1-8: /O
Common
Action to Activate nputs Effect of Active Outputs
Sinking inputs
Sinking outputs
1-3, 2-4
5-7, 6-8
Ground Apply +12 to 24V to J1-6 or J1-
7
Output will sink current through
load
Sourcing inputs,
Sourcing outputs
1-2, 3-4
5-6, 7-8
+12 to +24 VDC Ground J1-6 or J1-7 Output will source grounded load
Table 1: Input and Output Configurations
The followings pins are used for the send all inputs and sensor status outputs:
Pin 6 is the send all input for channel 0 Activating this input will cause the SAB-Q2 to send the
absolute position for channel 0
Pin 7 is the send all input for channel 1 Activating this input will cause the SAB-Q2 to send the
absolute position for channel 1
Pin 8 is the I/O common It should be connected as described in Table 1
Pin 9 is the channel 0 sensor status output An active output indicates a good sensor
Pin 10 is the channel 1 sensor status output An active output indicates a good sensor
6. nitial Power Up
After all connections are complete and have been checked for errors, apply power to the SAB-Q2 The
red board status LED should blink A green sensor status LED should light for each connected sensor
with a magnet
If the board status LED does not blink when power is applied, check that your power connections are
correct (see Section 1)
If your sensor is a PWM sensor, you must perform some setup before determining correct sensor
operation Please perform the setup described in sections 7 and 8a before continuing with this section
If the sensor status LED(s) do not light, appear dim or flicker, check that the sensor magnet is installed
as prescribed in your sensor documentation If the LED(s) still do not light, remove power from the
SAB-Q2 and verify all sensor connections
If, after insuring the sensor connections are correct, the SAB-Q2 still does not light the sensor status
LED(s), verify that your SAB-Q2 model is capable of supporting your sensor The SAB-Q2-?-RPM
Rapid Controls nc.
Box 8390 Rapid City, SD 57709
Phone: 888-510-7688 Fax: 605-341-5496
http://www rapidcontrols com/ email: info@rapidcontrols com

SAB-Q2 Quick Start 5 of 5 January 12, 2011
models are capable of operating with Start/Stop and PWM sensors The SAB-Q2-?-SSI models are
capable of operating with SSI sensors
7. Sensor Setup
A. Transducer Type
The SAB-Q2 default setting is RPM If a SSI or PWM sensor is being used then sensor type must
be changed to SSI or PWM in the setup menu Recommended SSI sensor is 24-bit binary SSI
SSI sensors can have their output divided by 2, 4, 8, or 16 by changing the sensor type This can
be used to adjust the effective resolution of the sensor if a sensor with too high a resolution is
ordered
B. Sensor Length
Enter the length of the sensor in inches This length must be greater than the farthest distance the
magnet can travel to on the wand If this length is too small, positions from the sensor could
become unpredictable
C. Gradient
The gradient (in microseconds per inch) of a RPM or PWM sensor must be entered This value is
printed on the head of the sensor at the factory If you are using a SSI sensor, enter a value of
1 00000
D. Recirculations
The number of recirculations determines the worth of each count A higher number of
recirculations increases the resolution of the counts but increases the update time The
approximate value of a count can be determined through the following formula: (0 002 ÷
recirculations) inches per count
8. Position Setup
A. Offset
The offset is subtracted from the position before calculating any analog output, before doing a
send all, and when activating the marker output Enter this value in counts
B. Marker
The marker position is the number of counts at which the marker output is activated See the SAB-
Q2 manual for more information
9. Further Setup
Some material related to setup of the SAB-Q2 is not covered in this guide For more information on
advanced setup, see the SAB-Q2 manual
Rapid Controls nc.
Box 8390 Rapid City, SD 57709
Phone: 888-510-7688 Fax: 605-341-5496
http://www rapidcontrols com/ email: info@rapidcontrols com
Table of contents
Other Rapid Controls Control Unit manuals
Popular Control Unit manuals by other brands
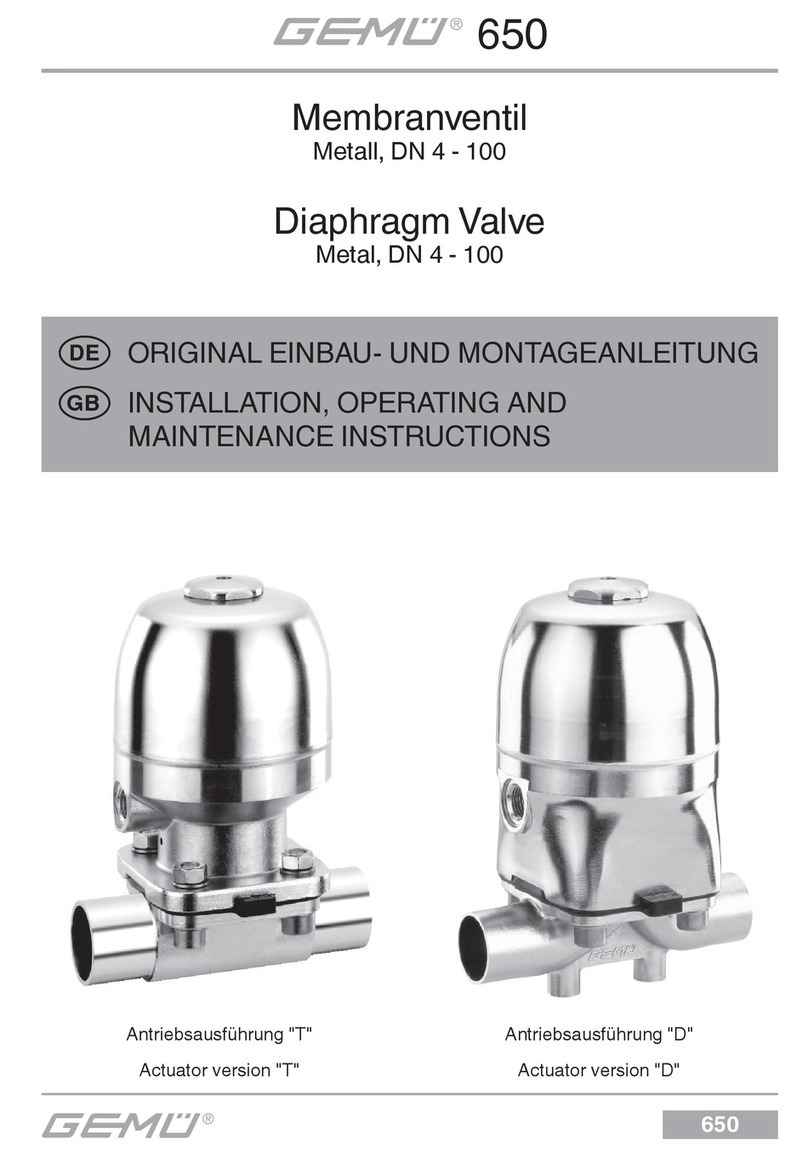
GEM
GEM 650 Installation, Operating and Maintenance Instruction
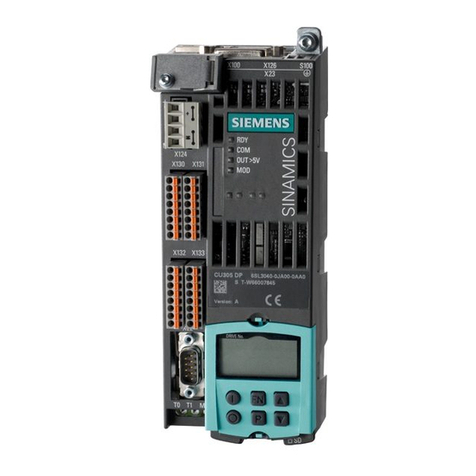
Siemens
Siemens SINAMICS S110 Getting started

Gira
Gira Dual 2347 00 user manual
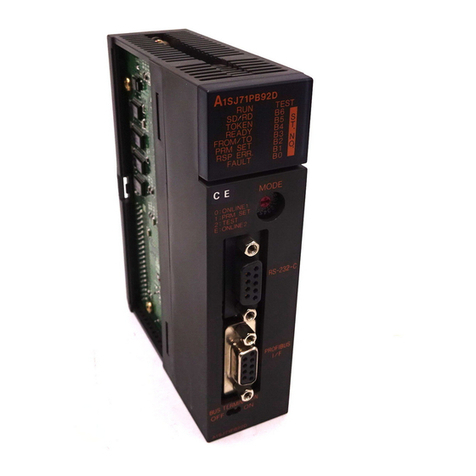
Mitsubishi
Mitsubishi AJ71PB92D user manual
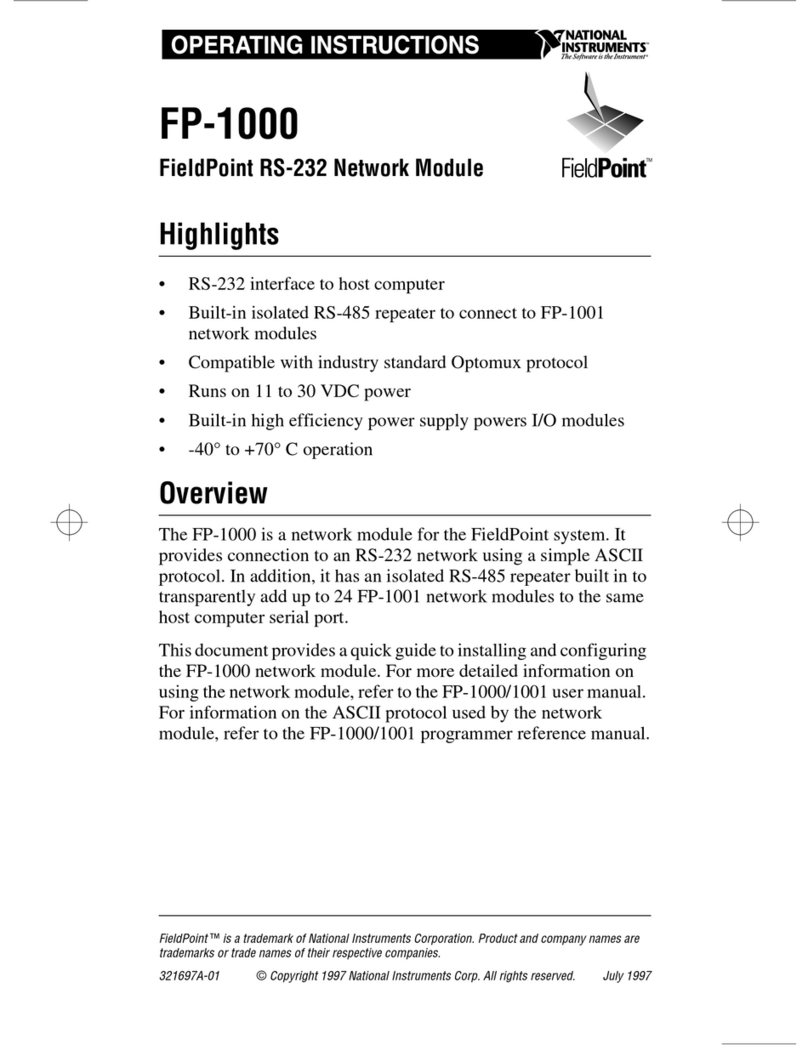
National Instruments
National Instruments FieldPoint FP-1000 operating instructions
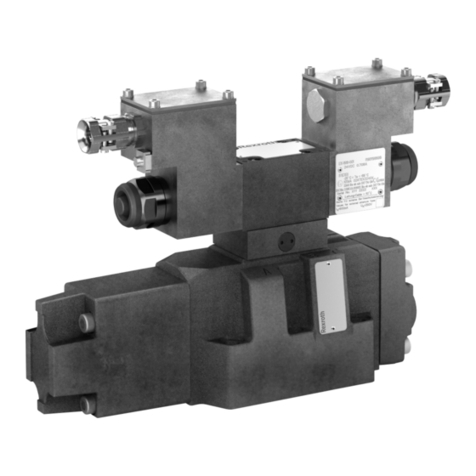
Bosch
Bosch REXROTH 4WRZ 7X/XE Series operating instructions