Rational SCC Line Installation guide

-1-
Training Manual
Diagnostic and Troubleshooting
SCC Line
SelfCooking Center - Combi Master
Edition 11-2006

-2-
Training Manual
Diagnostic and Troubleshooting
SCC Line
Edition 11-2006
General hints:
Isolate the appliance from mains supply
before opening the appliance
When working with chemicals, i.e. aggressive cleaning materials
always wear protective clothing, goggles and gloves!
After maintenance / repair the appliance must be checked for electric safety
in accordance with your national, state and local requirements!
Whenever working on any gas component like:Gas valve, gas blower
and / or changing connected type of gas a detailed
flue gas analysis MUST be done using adequate
CO and CO2 measuring equipment!
This shall ONLY be done by trained technicians!
Always check appliance for possible gas leakages!
Part 1: Topic: CM technique Page:
1. CM Overlay
2. CM Principle
3. CM Water level control
4. CM Steam control
5. CM Key code
6. CM PCB
7. CM Main fan Motor
8. CM Sequence of events
9. CM Service level
10. CM Diagnostic
11. CM Running times
12. CM Basic settings
13. CM Function test
14. CM Error history
15. CM Failure code
16. CM Gas principle
17. CM Gas components
18. CM Burner sequence of events
19. CM Gas Conversion
20. CM Gas changing installation altitude
21. CM Gas Flue gas analysis
22. CM Gas adjustment table
23. CM Gas Changing gas blower speed
04
05
06
07
08 - 09
10
11
12 - 16
17
18
19
20 - 21
22 - 23
24
25
26
27
28
29
30
31 - 32
33
34

-3-
Part 2: Topic: SCC Technique Page:
1. SCC Overlay
2. SCC Self Cooking Control until software 01-07-12
3. SCC Combi Steamer mode until software 01-07-12
4. SCC Self Cooking Control since software 02-01-01
5. SCC Combi Steamer mode since software 02-01-01
6. SCC Programming, CleanJet
4. SCC Principle
5. SCC Operator PCB; LED code;
6. SCC I/O PCB; LED Code
7. SCC Main fan Motor; LED code
7. SCC Sequence of events (cooking modes)
8. SCC Service level
9. SCC Diagnostic mode overview
10. SCC Diagnostic mode
11. SCC Running times overview
12. SCC Running times
13. SCC Basic settings overview
14. SCC Basic settings
15. SCC Function test overview
16. SCC Function test
17. SCC Overview Service messages / intermittent buzzer code
17. SCC Service messages
18. SCC Calibration
19. SCC Drain valve
20. SCC Gas principle
21. SCC Gas technique
22. SCC Burner sequence of events
23. SCC Gas conversion
24. SCC Gas adjustment of installation altitude
25. SCC Flue gas analysis
26. SCC Gas adjustment table
27. SCC Gas changing gas blower speed
Part 3: Topic: Common topics SCC and CM Page:
1. Software flashing SCC
2.
SCC Fault tree „pcb/EEPROM changing; software update“
3. Software flashing CM
5. CM Fault tree „Changing pcb/EEPROM, Fault E1“
6.
CM flashing via PC
7. Electrical descaling pump
8. Installation Checklist
9. Preventative maintenance list
10. Water Info
Part 4: Fault list SCC and CM
1. Index
2. Fault list SCC
3. Fault list CM
Part 5: Circuit diagram (Training version 3NAC 400V)
SCC - CM Reference sheet
35
36
37
38
39
40
42
44
45
46
48 - 53
54
56
57 - 59
60
61 - 62
64
65 - 67
68
69 - 70
72
73 - 74
76 - 77
78
80
82
83
84
85
86 - 87
88
89
91
92
93 - 94
95
96
98 - 99
100 - 103
104 - 106
108
110
111 - 121
122 - 127

-4-
S
C
M
Steam
Hot Air
Combi Steam
Low Temperature Steam
Finishing
Cool Down
Cabinet temperature display
Cabinet temperature setting
Timer
Core temperature
Time - Core temperature display
Time - Core temperature setting
CM Technique from 04 - 2004

-5-
S
C
M
B1
B3
F4
M4
Y1 Y2
B2
M1
S2
B5
F3
CM Technique from 04 - 2004
B1 Thermocouple cabinet
B2 Thermocouple quenching / Steam control
B3 Thermocouple core temperature
B5 Thermocouple steam generator (preheating, 180°C (356°F) max)
F3 Safety temperature limiter steam generator 160°C
F4 Safety temperature limiter cabinet 360°C
Y1 Solenoid valve filling
Y2 Solenoid valve quenching
M1 Fan motor (without jumper)
M4 SC-pump
S2 Level electrode
CM 201/202 only:
M2 Fan motor top (with jumper)

-6-
S
C
M
Water level control Steam Generator
V
AC
S2
M4
Y1 Y2
B2
S2
B5
F3
Center S2 ==> Ground: 2 - 6V AC: water level too low
steam heating must switch OFF
solenoid valve filling Y1 ON
Center S2 ==> Ground: 0V AC: water level reached
steam heating can switch ON
solenoid valve filling Y1 switched OFF
Every 2 minutes steam elements will switch off for water level control
Notes:
X12

-7-
S
C
M
Y1 Y2
B2
B1
°C /°F
t(sec)
B2 -2
B2 -1
B1 -100°C(212°F)
70°C
(158°F)
1. Filling of interior cabinet based on time
and temperature control of B1 cabinet sen-
sor
2. After steam saturation inside cabinet
steam will also fill quenching chamber
3. Depending on the frequency of tempera-
ture raise of the quenching sensor B2 the
duration of the next steam supply is
calculated.
B2-1: B2 temperature with partial load
B2-2: B2 temperature with full load
4. The amount of steam inside the cabinet is
directly depending on the temperature
variation of quenching sensor B2.
Steam Control CM from 04 - 2004
Intelligent steam control via quenching sensor
Notes:

-8-
S
C
M
Key code CM from 04 - 2004
CLEn
CLEn
CLEn
SC
CALC
A) Cool down cabinet below 60°C
B) Spray inside cabinet with Rational cleaner
C) Close cabinet door
D) Select „Cool Down
E) Press core temperature key for 10 sec.
F) „CLEn“ will show in cabinet temperature display
G) Press timer key 1x; Cleaning program starts automatically
(open cabinet door and rinse interior cabinet after
40 min.)
Close door again. Since Software version C1-06-05
a 10 min step hot air will follow to dry the interior cabinet.)
H) After end of program, leave cabinet door open over night.
This should be done after each installation to verify free drain connec-
tion and before disconnection the unit for storage.
A) Open cabinet door
B) Select „Cool Down“
C) Press core temperature key for 10 sec.
D) „CLEn“ will be shown in cabinet temperature display
E) Select „SC“ with temperature dial
F) Close water tap
G) Press timer key 1x and remain on „Cool Down“ position for
about 45 sec.
A) Open cabinet door
B) Select „Cool Down“
C) Press core temperature key for 10 sec.
D) „CLEn“ will be shown in cabinet temperature display
E) Select „CALC“ with temperature dial
F) Press timer key 1x and follow procedure of the
decalcification instruction. (See user manual CM).
1. Cleaning program
2. Empty steam generator
3. Select descaling program

-9-
S
C
M
100°C
212°F
A) Select any mode
C) Press timer and core temperature key
simultaneously for 10 sec. until ==>
D) Display changes from °C to °F or vice versa
E) Release both keys
Key code CM from 04 - 2004
Notes:
4. Changing temperature display from °C to °F

-10-
S
C
M
X7
X19
X20
F1 F2
Transformer
0,1 AT2AT
1
1
X7
X19
X20
X18
X23
X31
RS 485
X8
X12
X26
X27
X32X24
X30
RS 232
X63
X3X4X6
X2
X50
2 AT
1234
on
off
11
1
1
1
1
1
F6.1
F6.1
2AT
2AT
X16
X16
F6
F6
42.00.004
42.00.047
X2 B3 Core temperature
X3 B1 Interior cabinet
X4 B2 Quenching / Steam control
X6 B5 Steam generator
X7 ON - OFF switch
X8 Buzzer
X12 Level electrode
X 16 power supply from transformer (42.00.047)
X18 SC - pump
X19 Solenoid valves
X20 Energy optimising / Sicotronic
X23 Vent hood (signal door open / closed)
X24 SSR
X26 SSR pulsing (USA version only)
X27 Door contact switch
X30 Serial interface (RS232)
X31 BUS interface
X32 Timer / Core Temp. Potentiometer
X50 external EEPROM
X63 Not used
Counting sequence
Notes: Since February 2006 PCB 42.00.004 is replaced by 42.00.047.
(Conversion kit: 87.00.139, pls. see Technical info 04-06)
The transformer on the new PCB 42.00.047 is no more existing and replaced by
external transformer 40.00.227
CM PCB (42.00.004) from 04-2004
1
CM PCB (42.00.047) from 02-2006 (without transformer)
Temperature
potentiometer

-11-
S
C
M
Motor for CM 40.00.274
Jumper 40.01.581 is used on floor model 201 and 202 for top position motor only!
Jumper is not used on models 61 - 102 with one motor only! (Service 34 will be shown!)
LED
Jumper
Reason
1x Motor doesn’t start, no changing
signal from hallsensor
2x Voltage too low on motor pcb
3x Voltage too high on motor pcb
4x rpm measurement defective
5x Motor pcb temperature >105°C
6x Supply voltage <80V
7x Motor pcb defective
8x Motor pcb defective
LED code fan motor SCC and CM from 04/2004
Remedy
Check for motor blockage or change mo-
tor.
Check supply voltage or
change motor.
Check supply voltage or
change motor.
Change motor.
Check cooling system (cooling fan, air
intake filter), otherwise change motor
Check power supply
(F1-F2)
Change motor.
Change motor.

-12-
S
C
M
Mode: Steam 100°C (212°F)
Temp. preset, not adjustable
Function Step
Select Steam mode
Select time or core temperature
Close cabinet door
Check water level inside
steam generator
Preheat steam generator,
if B5 is below 85°C (185°F);
Timer starts after successful preheating
Steam supply up to steam saturation
inside cabinet
Hot Air supply (only 50%) when set
temperature (100°C/212°F) can not be
reached in time by Steam alone
Quenching (set to 70°C/158°F)
Responsible sensor
Reed switch S3
Level electrode S2 in-
side Steam Generator
Thermocouple B5 inside
Steam Generator
Logic on PCB
Quenching sensor B2
(Steam control)
Cabinet sensor B1
Quenching sensor B2
Signal
Door open: 12VDCX27:(1-2)
Door closed: 0VDC X27:(1-2)
X12:(1-4) > 2VAC => no water
X12:(1-4) ~ 0VAC => water
SSR active: 12VDCX24:(1-2)+(5-6)
SSR not act: 0VDC X24:(1-2)+(5-6)
Gas units: Bus signal
SSR active: 12VDCX24:(1-2)+(5-6)
SSR not act.: 0VDC X24:(1-2)+(5-6)
Gas units: Bus signal
SSR active: 12VDCX24:(7-8)
SSR not act.: 0VDC X24:(7-8)
Gas units: Bus signal
B2 above set Temp.: Y2 active
B2 below set Temp.: Y2 not active
Remark
Solenoid Y1 energizes when
no water, 230VAC, X19:(1-3)
Heating off,
if B5 > 180°C (356°F)
Blinking dot in timer
Steam saturation is calculated
by quenching duration and rate
Decision of Hot Air supply by
PCB logic
Y2 active: 230VAC X19:(2-4)
Y2 not act.: 0VAC X19:(2-4)
1
2
3
4
5
6
7
8
9

-13-
S
C
M
Mode: Low temperature steam
Temp. range
30-99°C (86-210°F)
Function Step
Select vario steam mode
(Temp. setting 30-99°C (86-210°F))
Select time or core temperature
Close cabinet door
Check water level inside
steam generator
Preheat steam generator,
if B5 is below 85°C (185°F);
Timer starts after successful preheating
Steam supply until set temperature
inside cabinet is reached
Hot Air supply (only 50%) when set
temperature can not be reached
in time by Steam alone
Quenching (set to 70°C/158°F)
Responsible sensor
Reed switch S3
Level electrode S2 in-
side Steam Generator
Thermocouple B5 inside
Steam Generator
Logic on PCB
Cabinet sensor B1
Cabinet sensor B1
Thermocouple B2
Signal
Door open: 12VDCX27:(1-2)
Door closed: 0VDC X27:(1-2)
X12:(1-4) > 2VAC => no water
X12:(1-4) ~ 0VAC => water
SSR active: 12VDCX24:(1-2)+(5-6)
SSR not act: 0VDC X24:(1-2)+(5-6)
Gas units: Bus signal
SSR active: 12VDCX24:(1-2)+(5-6)
SSR not act.: 0VDC X24:(1-2)+(5-6)
Gas units: Bus signal
SSR active: 12VDCX24:(7-8)
SSR not act.: 0VDC X24:(7-8)
Gas units: Bus signal
B2 above set Temp.: Y2 active
B2 below set Temp.: Y2 not active
Remark
Solenoid Y1 energizes when no
water, 230VAC, X19:(1-3)
Heating off,
if B5 > 180°C (356°F)
Blinking dot in timer
Blinking dot in timer display
Decision of Hot Air supply by
PCB logic
Y2 active: 230VAC X19:(2-4)
Y2 not act.: 0VAC X19:(2-4)
1
2
3
4
5
6
7
8
9
Note:
Below 100°C (212°F) fan at lowest speed when no energy required for longer than 2 minutes.

-14-
S
C
M
Mode: Combination
Temp. range
30-300°C (86-572°F)
Function Step
Select Combination mode
(Temp. 30-300°C (86-572°F))
Select time or core temperature
Close cabinet door
Check water level inside
steam generator
Preheat steam generator,
if B5 is below 85°C (185°F);
Timer starts after successful preheating
Hot Air supply until set temperature
inside cabinet.
Hot air has priority
Steam supply up to steam saturation
inside cabinet
Quenching (set to 70°C/158°F)
Responsible sensor
Reed switch S3
Level electrode S2 in-
side Steam Generator
Thermocouple B5 inside
Steam Generator
Logic on PCB
Cabinet sensor B1
Quenching sensor B2
(Steam control)
Quenching sensor B2
Signal
Door open: 12VDCX27:(1-2)
Door closed: 0VDC X27:(1-2)
X12:(1-4) > 2VAC => no water
X12:(1-4) ~ 0VAC => water
SSR active: 12VDCX24:(1-2)+(5-6)
SSR not act: 0VDC X24:(1-2)+(5-6)
Gas units: Bus signal
SSR active: 12VDCX24:(7-8)
SSR not act.: 0VDC X24:(7-8)
Gas units: Bus signal
SSR active: 12VDCX24:(1-2)+(5-6)
SSR not act.: 0VDC X24:(1-2)+(5-6)
Gas units: Bus signal
B2 above set Temp.: Y2 active
B2 below set Temp.: Y2 not active
Remark
Solenoid Y1 energizes when
no water, 230VAC, X19:(1-3)
Heating off,
if B5 > 180°C (356°F)
Blinking dot in timer
Hot air supply active, until
set temperature is reached
Steam saturation is calculated
by quenching duration and rate
Y2 active: 230VAC X19:(2-4)
Y2 not act.: 0VAC X19:(2-4)
1
2
3
4
5
6
7
8
9
Note:
Below 100°C (212°F) fan at lowest speed when no energy required for longer than 2 minutes.

-15-
S
C
M
Mode: Finishing
Temp. range
30-300°C (86-572°F)
Function Step
Select Finishing
(Recom. Temp. 100-140°C (212-284°F))
Select time or core temperature
Close cabinet door
Check water level inside
steam generator
Preheat steam generator,
if B5 is below 85°C (185°F);
Timer starts after successful preheating
Hot Air supply
Electric units: 12 sec on - 6 sec off
Gas units: 30 sec on - 15 sec off
Steam supply
Electric units: 6 sec on - 12 sec off
Gas units: 15 sec on - 30 sec off
Quenching (set to 70°C/158°F)
Responsible sensor
Reed switch S3
Level electrode S2 in-
side Steam Generator
Thermocouple B5 inside
Steam Generator
Logic on PCB
Cabinet sensor B1
Quenching sensor B2
(Steam Control)
Quenching sensor B2
Signal
Door open: 12VDCX27:(1-2)
Door closed: 0VDC X27:(1-2)
X12:(1-4) > 2VAC => no water
X12:(1-4) ~ 0VAC => water
SSR active: 12VDCX24:(1-2)+(5-6)
SSR not act: 0VDC X24:(1-2)+(5-6)
Gas units: Bus signal
SSR active: 12VDCX24:(7-8)
SSR not act.: 0VDC X24:(7-8)
Gas units: Bus signal
SSR active: 12VDCX24:(1-2)+(5-6)
SSR not act.: 0VDC X24:(1-2)+(5-6)
Gas units: Bus signal
B2 above set Temp.: Y2 active
B2 below set Temp.: Y2 not active
Remark
Solenoid Y1 energizes when no
water, 230VAC, X19:(1-3)
Heating off,
if B5 > 180°C (356°F)
Blinking dot in timer
Hot air supply active, until
set temperature is reached
Steam saturation is calculated
by quenching duration and rate
Y2 active: 230VAC X19:(2-4)
Y2 not act.: 0VAC X19:(2-4)
1
2
3
4
5
6
7
8
9
NOTE: For initial heating of cabinet => alternately energy supply of Hot Air and Steam (Electric 12/6 sec, Gas 30/15 sec)
F
Note:
Below 100°C (212°F) fan at lowest speed when no energy required for longer than 2 minutes.

-16-
S
C
M
Mode: Hot Air
Temp. range
30-300°C (86-572°F)
Function Step
Select Hot Air
(Temp. 30-300°C (86-572°F))
Select time or core temperature
Close cabinet door
Timer starts at once
Hot Air supply until set temperature
inside cabinet is reached
Quenching (set to 90°C/194°F)
Responsible sensor
Reed switch S3
Logic on PCB
Cabinet sensor B1
Quenching sensor B2
Signal
Door open: 12VDC X27:(1-2)
Door closed: 0VDC X27:(1-2)
SSR active: 12VDC X24:(7-8)+(3-4)
SSR not act.: 0VDC X24:(7-8)+(3-4)
B2 above set Temp.: Y2 active
B2 below set Temp.: Y2 not active
Remark
Blinking dot in timer display
Y2 active: 230VAC, X19:(2-4)
Y2 not act.: 0VAC, X19:(2-4)
1
2
3
4
5
6
Note:
Below 100°C (212°F) fan at lowest speed when no energy required for longer than 2 minutes.

-17-
S
C
M
X7
X19
X20
F1 F2
Transformer
0,1 AT2AT
1
1
X7
X19
X20
X18
X23
X31
RS 485
X8
X12
X26
X27
X32X24
X30
RS 232
X63
X3X4X6
X2
X50
2 AT
1234
on
off
11
1
1
1
1
1
F6.1
F6.1
2AT
2AT
X16
X16
F6
F6
42.00.004
42.00.047
1234
on
Switch unit ON
On operator PCB set DIP switch 1 to „ON“ position
Select service package with timer dial:
Diagnostic Program
Error code history
Running times
Basic settings
Activate with core temperature key the desired service package
Select with timer dial the desired step
Activate selected step by pressing timer key
To de-activate service package set DIP switch 1 to „OFF“ position
.
Switch unit ON
On operator PCB set DIP switch 3 to „ON“ position
First step of function test is displayed
Select desired step of function test with timer dial
Activate selected step by pressing timer key
Activate selected step with core temperature key
To de-activate function test set DIP switch 3 to „OFF“ position.
A)
B)
C)
D)
E)
F)
G)
A)
B)
C)
D)
E)
F)
G)
dP
SE
rt
1234
on
Function Test
Service level CM from 04 - 2004
F1
1234
on
1234
on
Notes:
Er

-18-
S
C
M
Description
Software Version
B1 Cabinet sensor
B2 Quenching sensor
B3 Core sensor
B5 Steam generator sensor
PCB temperature
S3 Door contact
S2 Water level steam
generator
Steam elements
0 - off; 1 - 50%; 2 - 100%
Hot Air elements
0 - off; 1 - 50%; 2 - 100%
Speed fan motor top
Speed fan motor bottom
Energy optimising
(Sicotronic)
SSR pulsing (US version)
Unit size and type
Flame Current Steam
Flame Current Hot Air top
Flame Current Hot Air bottom
dP #
dP 1
dP 2
dP 3
dP 4
dP 5
dP 6
dP 7
dP 8
dP 9
dP 10
dP 11
dP 12
dP 13
dP 14
dP 15
dP 16
dP 17
dP 18
Connector
X 3
X 4
X 2
X 6
X27:(1-2)
X12:(1-4) S2
X19:(1-3) Y1
BUS
BUS
X 20
X 26
Cabinet display
Software
version: C - 1 -
actual value
actual value
actual valuet
actual value
actual value
S3: 1 - 0
Temp. B5
Temp. B1
Set rpm
Set rpm
61 - 202
Timer display
Software
Version:06.05
max value
max value
max value
max value
max value
1 - 0
Y1: 1 - 0
0 - 1 - 2
0 - 1 - 2
actual rpm
actual rpm
1 - 0
1 - 0
ELE - GAS
x.x µA*
x.x µA*
x.x µA*
Comment
Reset by pressing
for 5 sec.
Reset by pressing
for 5 sec.
Reset by pressing
for 5 sec.
Reset by pressing
for 5 sec.
Reset by pressing
for 5 sec.
USA version only
since SW Version:
C1-06-05 (flame current)
since SW Version:
C1-06-05 (flame current)
since SW Version:
C1-06-05 (flame current)
Service level: dP -- Diagnostic Program
+
* With SW Version C1-06-05 the flame current will show as 20-24µA
(This value must be divided by 4 to get the correct flame current e. g. 22:4 = 5,5µA.)
Starting with SW version C1-07-01 the actual flame current is shown .
+
+
+
+

-19-
S
C
M
Service Level: rt -- Running Time
rt #
rt 1
rt 2
rt 3
rt 4
rt 5
rt 6
rt 7
rt 8
rt 9
rt 10
rt 11
rt 12
rt 13
Description
Total S3 door openings
Total time Y1 valve filling
Total time Y2 valve quenching
Total time M4 SC-pump
Total time steam heating time
Total time hot air heating time
Total time steam mode
Total time hot air mode
Total time combination mode
Total time vario steam mode
Total time finishing mode
Total time cleaning program
Total running time unit
Timer display: 1-999
Temp. display: >1000
number
min
min
min
hrs
hrs
hrs
hrs
hrs
hrs
hrs
hrs
hrs
Comment
Reset by pressing
for 5 sec.
Reset by pressing
for 5 sec.
Reset by pressing
for 5 sec.
Reset by pressing
for 5 sec.
Reset by pressing
for 5 sec.
Reset by pressing
for 5 sec.
Can not be reset
Can not be reset
Can not be reset
Can not be reset
Can not be reset
Can not be reset
Can not be reset
+
+
+
+
+
+
Notes:

-20-
S
C
M
Service level: SE -- Basic settings
Select desired step with timer dial
(fan motor and heating elements are automatically OFF)
Activate selected step with timer key
Steam heating time since last SC-Automatic
Press time and core key simultaneously for 5 seconds to set steam heating time to
preset steam heating time plus 1 minute ==> test function for SC-Automatic
Preset Steam heating time until SC-Automatic
(default 45min)
Press time key and adjust preset steam heating time from 20 - 120 minutes with
timer dial
Flushing time SC-Automatik
(default 45 seconds)
Press time key and adjust flushing time of SC-automatik from 30 - 90 seconds with
timer dial
Operation steam generator pump
(oFF - continous or on - pulsing)
Press time key and select „on“ or „oFF“ with timer dial
Show mode (on - oFF) SHO
Press time key and select „on“ or „oFF“ in with timer dial
Setting new gas type (G20, G25, G30, G31, 13A)
Press time key, keep it pressed and select new gas type with timer dial
Confirm new gas type by pressing core temperature key once
NOTE: After changing gas type a waste gas analysis must be carried out in the func-
tion test. Corresponding gas blower speed is automatically adjusted
Presetting of CO2screw on gas valve after gas type modification / changing gas valve
Press time key, keep it pressed and select with timer dial “ST“ for steam, “HA1“ for
hot air top or “HA2“ for hot air bottom (only 201/202) with timer dial;
Average lenght in mm of CO2screw on gas valve is shown on timer display
Adjustment of installation altitude above sea level (since SW C1-06-05)
-500- -1m, 0-999m, 1000-1499m, 1500-1999m, 2000-2499m, 2500-2499m, 3000-
3499m, 3500-3499m, 4000-4499m, 4500-4499m
Press time key, keep it pressed and select installaton altitude in 500m steps by timer
dial. Confirm altitude setting by pressing simultaneously core temperature key once.
SE 1
SE 2
+
SE 3
SE 4
SE 5
SE 6
SE 7
SE 8
+
+
+
+
+
+
Table of contents
Other Rational Grill manuals
Popular Grill manuals by other brands

Miele
Miele KM 411 operating instructions

BOSKA
BOSKA Party Pro instructions
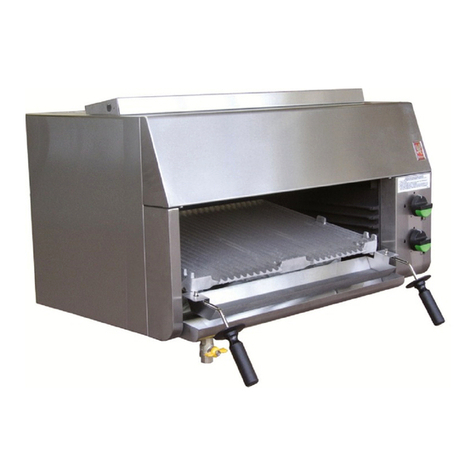
Falcon
Falcon STEAKHOUSE PLUS G1518 Installation and servicing instructions

KitchenAid
KitchenAid 730-0954G (NG) Installation Instructions and Use & Care Guide

KitchenAid
KitchenAid 720-0732 Installation Instructions and Use & Care Guide

Napoleon
Napoleon PRO22K-LEG-2 Assembly, use and care manual