RCBS Dillon Conversion Kit Instruction sheet

Rifle Bullet Feeder — Dillon® Conversion Kit
PRODUCT INSTRUCTIONS

LIFETIME LIMITED WARRANTY
Your Rie Bullet Feeder – Dillon Conversion Kit is
warranted to be free from defects in material or work-
manship for lifetime of the original consumer purchaser.
All RCBS products are intended for non-commercial use
by hobbyists. Any other use of these products will void
the warranty. Should you believe that your Rie Bullet
Feeder – Dillon Conversion Kit is defective in material
or workmanship, you must return it to Ammunition
Accessories Inc. through its Oroville operation (herein-
after “Oroville Operations”) postage paid for evaluation.
If defective, the product will be repaired or replaced at
Oroville Operations’ option, at no charge.
Send a dated proof of purchase to Oroville Operations
for return shipping and handling, along with the Rie
Bullet Feeder - Dillon Conversion Kit to:
Ammunition Accessories Inc.,
Oroville Operations
605 Oro Dam Blvd East
Oroville, California 95965
Warranty services cannot be provided without
meeting the above requirements.
THIS LIFETIME LIMITED WARRANTY DOES NOT
COVER DEFECTS OR DAMAGE RESULTING FROM:
CARELESSNESS, MISUSE, COMMERCIAL USE,
ABUSE, IMPROPER INSTALLATION, MODIFICATION,
OR NORMAL WEAR AND TEAR. THE IMPLIED
WARRANTIES OF MERCHANTABILITY AND FITNESS
FOR A PARTICULAR PURPOSE ARE LIMITED TO THE
DURATION OF THIS LIFETIME LIMITED WARRANTY.
OROVILLE OPERATIONS IS NOT LIABLE FOR
DAMAGES IN EXCESS OF THE PURCHASE PRICE OF
THE PRODUCT AND UNDER NO CIRCUMSTANCES
SHALL OROVILLE OPERATIONS BE LIABLE FOR
CONSEQUENTIAL OR INCIDENTAL DAMAGES.
HOWEVER, SOME STATES DO NOT ALLOW
LIMITATIONS ON INCIDENTAL, OR CONSEQUENTIAL
DAMAGES, SO THE ABOVE LIMITATION OR
EXCLUSION MAY NOT APPLY TO YOU.
The above warranty provides the sole and exclusive
warranty available to the customer in the event of a
defect in material or workmanship in the reloading
product. This warranty gives you specic legal rights,
and you may also have other rights which vary from
State to State.
SAFETY
Reloading is an enjoyable and rewarding hobby that
can be conducted safely. But, as with any hobby,
carelessness or negligence can make reloading
hazardous. This product has been designed from
the beginning with the user’s safety in mind. When
reloading, safety rules must be followed. By observing
these rules, the chance of a hazardous occurrence
causing personal injury or property damage is
minimized.
GENERAL
• Use all equipment as the manufacturer recommends.
Study the instructions carefully and become
thoroughly
familiar with the operation of the product. If you do
not have written instructions, request a copy from the
equipment manufacturer.
• Do not take short cuts. Attempting to bypass
established procedures is an invitation to
an accident.
• Observe “good housekeeping” in the reloading area.
Keep tools and components neat, clean and orderly.
Promptly and completely clean up primer and
powder spills.
• Reload only when you can give your undivided
attention. Do not reload when fatigued or ill, or
under the inuence of medications or alcohol.
• Develop a reloading routine to avoid mistakes
which may prove hazardous. Do not rush - load
at a leisurely pace.
• Always wear adequate eye protection to protect your
eyes from ying particles. You assume unnecessary
risk when reloading without wearing safety glasses.
WARNING!
Before using the Rie Bullet Feeder – Dillon Conversion Kit, read these instructions carefully to fully learn how to
safely operate the related reloading equipment. Failure to properly operate the related reloading equipment can result
in severe personal injury and/or equipment damage.
If you have any questions while assembling or operating this tool,
Call us at 1-800-533-5000 or 1-530-533-5191
Monday – Thursday 6:30 am – 4:00 pm Pacific Time
(hours may vary)
Or email us at [email protected]
This instruction manual contains specic safety and operating information. It should be considered a permanent part
of your reloading equipment and remain with the equipment at all times for easy reference.
2

LOADING DATA
• Use only laboratory tested reloading data. We highly
recommend the current SPEER
®
Reloading Manual.
OBSERVE ALL WARNINGS ABOUT THE USE
OF MAXIMUM LISTED LOADS.
WARNING/ CAUTION
PRIMERS AND POWDER
• Store primers and powder beyond the reach of
children and away from heat, dampness, open ames
and electrical equipment. Avoid areas where static
electricity is evident.
• DO NOT use primers of unknown identity.
• Dispose of unknown primers in accordance with
applicable regulations.
• Keep primers in the original factory container until
ready to use. Return unused primers to the same
factory packaging for safety and to preserve their
identity. Primer packaging is designed to provide
safe storage.
• DO NOT store primers in bulk. The blast of just a few
hundred primers is sufcient to cause serious injury to
anyone nearby.
• DO NOT force primers. Use care in handling
primers.
• DO NOT have more than one can of powder on the
bench at one time. Powder cans should be stored
away from the bench to avoid picking up the
wrong one.
• DO NOT use any powder unless its identity is
positively known. The only positive identication is
the manufacturer’s label on the original canister.
Discard all mixed powders and those of uncertain
identity.
• If you use a powder measure, replace the lids on both
the powder hopper and powder can after the powder
hopper has been lled.
• When using a powder measure, settle the powder in
the powder hopper before charging any cases. Throw
and check the weight of at least ten charges. This will
assure you that the correct powder charge is being
thrown.
• When you nish a reloading session, pour any
remaining powder back into its original factory
container. This will preserve the identity and shelf
life of the powder.
• DO NOT smoke while reloading.
RECORD KEEPING
• Keep complete records of reloads. Apply a descriptive
label to each box showing the date produced, and
the primer, powder and bullet used. Labels for this
purpose are packed with SPEER
®
bullets.
• Never attempt to guess at the identity of your
ammunition.
USE
The RCBS Rie Bullet Feeder – Dillon Conversion Kit
has been designed to use the RCBS Rie Bullet Feeder
on Dillon
®
RL550B and XL650 Progressive Presses
using a Dillon Powder Measure. The RCBS Bullet Feeder
will increase your progressive rie load rate by ~50% by
reducing the manual operation of placing a bullet onto
the case mouth. All parts and adapters are included for
you to be able to feed jacketed bullets. Dillon Powder
Measures require this Kit’s additional adapters. Dillon
presses mounted on Strong Mounts, require this Kit’s
additional mounting system.
The Bullet Feeder is designed to work with FMJ,
JACKETED, or SEMI JACKETED Hollow Point, Soft
Point, and Round Nose designed bullets ONLY. Cast or
swaged LEAD bullets are NOT to be used and will void
the Warranty. The lube from lead bullets deposits on the
moving parts and collects dust and dirt, slowing down
the function of the Bullet Feeder and eventually causing
the motor to burn out. The deposited lube also does not
allow the bullets to be positioned properly for feeding
from the sorting Wheel to the Feed Tube.
The RCBS Rie Bullet Feeder feeds and seats
most bullets in one station. This allows you to crimp
bullets in a separate operation, if you deem necessary.
Shorter cartridges may not completely seat and may
require an additional Seat Die in a subsequent station.
The Collator will hold approximately 150+ bullets
depending on caliber and bullet weight.
Terminology Reference
The following abbreviations are used throughout this
instruction manual:
• BHCS – Button Head Cap Screw
• SHCS – Socket Head Cap Screw
• PM – Powder Measure
This Product Instruction Manual is meant to supplement
the manual you received with your RCBS Rie Bullet
Feeder, not replace it. You will need to reference that
document to complete your Bullet Feeder installation.
Contact RCBS if you need another copy or see our
website to download one.
Because RCBS has no control over the choice of components, the manner in which they are assembled, the use of
this product, or the firearms in which the resulting ammunition may be used, we assume no responsibility, expressed
or implied, for the use of ammunition reloaded with this product.
3

UNPACKING
Refer to the list below to identify parts as you unpack your new Rie Bullet Feeder – Dillon Conversion Kit.
Parts Bag #1
1/4-20 x 1/2” Long BHCS (4)
1/4-20 x 3” Long BHCS (2)
8-32 x 1/2” Long BHCS (2)
8-32 Hex Nut, Zinc Plated (1)
10-32 x 1-1/4” SHCS (1)
Note: Keep the packaging foam inside the Bullet Feeder
Bowl Assembly throughout the installation process.
Parts Bag #2
Dillon PM Bracket
Dillon Adjustment Bracket
Dillon Clamp
Dillon Clamp Anchor
Cam
Upper Tube
Lower Tube
Bag #1 Bag #2
Tube
Coupling
4

ASSEMBLY
Reference the part schematic on page 11 for more
information.
You will need the following tools in order to assemble
and install this Kit:
• 3/32” hex key/ Allen wrench
• 5/32” hex key/ Allen wrench
• 3/8” open end wrench or small adjustable wrench
This Product Instruction Manual is meant to supplement
the manual you received with your RCBS Rie Bullet
Feeder, not replace it. You will need to reference that
document to complete your Bullet Feeder installation.
Contact RCBS if you need another copy or see our
website (www.rcbs.com) to download one.
Bowl Support Tubes
Assemble the Bowl Support Upper Tube (#781312) and
Lower Tube (#781313) to each end of the Tube Coupling
(#781314) using the four 1/4-20 x 1/2” BHCS (Photo
1). Tighten screws securely with a 5/32” hex key/ Allen
wrench.
The Bullet Feeder Support Tube Assembly can now be
clamped to the Case Feeder Support Tubes on your
Dillon Press.
Powder Measure Adapter
Remove the locknut from the Bellcrank Bolt of the
Powder Measure (Photo 2) using a 3/8” wrench. Save
the locknut for future use if desired. Do not remove the
Bellcrank Bolt from the pivot hole and try to minimize
the movement of Bellcrank Assembly Brackets.
Photo 2. PM Bellcrank Locknut
Install the triangular PM Bracket (#781310) using the
existing Bellcrank Bolt, if possible. If it is damaged,
replace it with the 10-32 x 1-1/4” SHCS provided
with this Kit. Ensure the PM Bracket is in the correct
orientation (Photo 3). Do not fully tighten the Bellcrank
Bolt at this time. Check to verify the Bellcrank Cube is
correctly engaged in the Powder Bar’s slot (consult your
Powder Measure Manual for more information). Now
tighten the Bellcrank Bolt until snug using a 5/32”
hex key.
Photo 3
Next mount the Cam (#181253) onto the “L”-shaped
Adjustment Bracket (#781311) with a 8-32 x 1/2” Long
BHCS and 8-32 Hex Nut (Photo 4), using a 3/32” hex
key. Note the ats of the Hex Nut t within the slot
on the back of the Bracket (Photo 5). Slightly tighten
the BHCS so it is easy to adjust later during setup of
the Press.
Photo 1. Support Tube Assembly
5

Photo 4
Photo 5
Next install this Cam Adjustment Bracket onto the
triangular PM Bracket as shown (Photo 6), using the
other 8-32 x 1/2” Long BHCS. Again, only slightly
tighten the BHCS for now.
Photo 6
INSTALLATION
Note: Reference the part schematic on page 11 for more
information.
Bullet Feed/ Seat Die Installation
First, tighten the setscrew on your PM Die Lock Ring
to keep it from moving. Next carefully detach the PM
Failsafe Rod from the Bellcrank Link Brackets (consult
your Powder Measure Manual for more information).
Next, remove your Powder Measure Assembly from the
Powder Measure Die by loosening the two SHCS 6-7
turns each using a 5/32” hex key (Photo 7). Slide the
notched-clamp collar outward and pull the PM off the
Die body. Finally, remove the PM Die from the
Die Plate.
Photo 7
Install the Bullet Feed/Seat Die Assembly into the
Die Plate at the station immediately after the Powder
Measure station. Screw it down until the Bullet Drop
Tube (A) on the back side of the Seat Die Assembly,
nearly contacts the Lock Ring (B) (Photo 8). Orient the
Seat Die Assembly so the Die’s window is facing front of
Press (Photo 10).
Photo 8
Notched-Clamp
Collar
PM Die
Body
6

NOTE: You will be able to load cartridge lengths of
approximately 2.0 – 2.5 inches at this setting. For
longer cartridges, raise the Seat Die Assembly as
needed up so that the lower part of the window (A)
is higher than the Lock Ring (B) (Photo 9).
Photo 9
Bullet Seat Depth Adjustment
Slide the Die Plate, with Bullet Feed/Seat Assembly
installed, into the press. Now install a properly sized
and trimmed Cartridge Case into the Bullet Seat
station of the press (no primer or powder is needed).
Manually drop a bullet with nose pointed up into the
top of the Bullet Feed Die (Photo 10).
Photo 10
Manually squeeze the Bullet Feeder’s Push Bar
Mechanism, allowing the bullet to drop into the Seat
Die Body (Photo 11). Visually check to ensure the
bullet has dropped down inside the Guide bushing
under the Seat Plug. If it did not, the Seat Plug needs
to be positioned higher to allow the bullet to drop. See
Adjustment section for more information.
Photo 11
CAUTION: A bullet will be fed with each cycling of
the Push Bar. If a powder drop problem is incurred and
that case is removed from the shell plate station, the
bullet that was fed into the Bullet Feed/ Seat Assembly
MUST be removed from the Bullet Guide. If the bullet is
not removed and the next case is introduced, there will
be two bullets in the Bullet Guide and the bullets will jam
and possibly bend or damage the free floating Seat Plug.
A single bullet can be easily removed from the Seat
Die Body by abruptly slapping the Bullet Guide, located
at the bottom of the Seat Die, upward into the Die
repeatedly. This will cause the Seat Plug to push the
bullet out through the Bullet Guide’s Retention Ring.
Loosen the Seat Plug Stop near the top of its length.
Pull the press Handle to seat the bullet in the case.
Adjust the Seat Plug Stop and Seat Die Body position
as needed to obtain approximately the proper overall
Cartridge length. This is a trial-and-error process. Fine
tuning will still be needed after the Powder Measure is
installed so make sure the Seat Plug Stop has some
adjustment available up or down.
Powder Measure Installation
Install your PM Die into the appropriate station of the
Die Plate until the lock-ring contacts the Die Plate.
Reinstall the PM Assembly over the PM Die and slightly
tighten the two SHCS on the clamp so PM can still
rotate (consult your Powder Measure Manual for more
information). Note the PM Triangular Bracket is above
the Die’s Lower Platform (Photo 12).
Push Bar
Mechanism
Seat Plug
Stop
7

Photo 12
Rotate the PM Assembly so the Cam Adjustment
Bracket is aligned with the Bullet Feeder’s Push Bar
mechanism. Adjust the position of the Cam and “L”
shape Bracket so it will activate the Push Bar, allowing
bullets to drop one at a time. There should be only a
slight gap between the Push Bar’s bottom edge and
Cam’s radius, as well as a slight gap between the Push
Bar and “L” Bracket. Adjust the Cam’s position vertically
and horizontally to obtain this relationship (Photo 13).
(see Adjustment section for more information)
Photo 13
Next, reinstall the PM Failsafe Rod to the Bellcrank
Brackets (consult your Powder Measure Manual for
more information). Place a properly sized/ trimmed
case at the powder drop station and fully lower the
Press Handle. The Cam on the PM Assembly should
engage the Push Bar and drop a bullet into the Seat Die
Assembly. Ensure that the Cam does not contact any
other components throughout its range of motion.
Bowl Assembly Installation
Install the Upper Tube (#781240 or 781241) into the
Bullet Feeder Bowl (Photo 14). Slide one end of the
Continuous Spring into the Upper Tube. The other
end will slide into the Switch Block Assembly later.
Photo 14
Attach the Collator Bowl Assembly to the top of the
Support Tube Assembly with the 1/4-28 x 2” BHCS and
a 1/4-28 Hex Nut (A) (see Photo 15) supplied with your
Bullet Feeder Bag #3. Tighten this just enough so that
the Bowl Assembly will still pivot. Install the Bracket Pin
into the middle adjustment position (B). See Trouble-
shooting section of your Rie Bullet Feeder Manual for
more information.
Photo 15
Triangular
Bracket
Lower
Platform
Small Gap
Between Cam
Small Gap Between
“L” Bracket
8

Bowl Support Tubes Installation
When you are complete with this section, ensure that
the placement of the Bullet Feeder does not interfere
with the operation of your press.
Various options exist depending on the conguration of
your reloading press. Choose the correct option below
based on the accessories you have (Strong Mounts,
Case Feeder, etc.).
The goal is to install your Bullet Feeder Bowl in a
location above the Seat Die Assembly so no kinks are
in the Continuous Spring and bullets can drop through
it freely (Photo 16). Hold the Bowl Assembly up above
the Feed/ Seat Die and check Continuous Spring’s
alignment. This is approximately where you want the
Bowl to be positioned when complete.
Photo 16
For Presses with Strong Mounts
If your press is installed on Strong Mounts (Photo 17),
the green square tubing provided with your Rie Bullet
Feeder will not be tall enough. Therefore, you will need
to mount your RCBS Bullet Feeder Bowl Assembly
using the Support Tube Assembly provided in this kit
(Photo 1).
Photo 17
For Presses with No Strong Mounts
The green square tubing provided with your Rie
Bullet Feeder may be long enough.
The Clamp and Clamp Anchor (781315 and 781316,
respectively) supplied with this Kit give you the ability
to mount your Bullet Feeder Bowl to the green square
tubing from RCBS (Photo 18) or the black round
tubing on the Dillon Case Feeder (Photo 19). Choose the
option that is best suited for your situation. Assemble
the Clamp as shown using the two 1/4-20 x 3” Long
BHCS provided. Tighten both rmly to keep Bowl
Assembly stable.
Photo 18. RCBS Tube require square side of Clamp
Photo 19. Dillon Tube require round side of Clamp
Ensure that the placement of the Bullet Feeder does not
interfere with the operation of your press.
Insert the smaller end diameter of the clear Bullet Drop
Tube into the Switch Block (Photo 16). Insert free end of
clear tube into Bullet Feed/ Seat Die Assembly.
The installation of your RCBS Bullet Feeder Dillon
Conversion Kit is now complete. Before you begin
loading, verify the Bullet Seat Die is adjusted for proper
cartridge length and that bullets feed reliably through
the mechanism.
Refer to the Product Instructions received with your
RCBS Rifle Bullet Feeder for the remainder of the steps.
CAUTION: A bullet will be fed with each cycling of
the Push Bar. If a powder drop problem is incurred and
that case is removed from the shell plate station, the
bullet that was fed into the Bullet Feed/ Seat Assembly
MUST be removed from the Bullet Guide. If the bullet is
not removed and the next case is introduced, there will
be two bullets in the Bullet Guide and the bullets will jam
and possibly bend or damage the free floating Seat Plug.
Switch Block
Clear Bullet
Drop Tube
Continuous
Spring
Strong
Mounts
9

ADJUSTMENT
Note: Reference the part schematics on page 11 of this
booklet and the Bullet Feeder Instruction Manual for
more information during assembly and installation.
Bullet Seating Depth
Bullet seating depth is controlled by adjusting the Seat
Plug Stop (A) up or down. Shorter length cases may
be accommodated by moving the Retaining Ring to a
higher groove on the free oating bullet Seat Plug (B)
(Photo 20). However, larger diameter bullets may not
drop into position if the Seat Plug (B) is hanging too low.
This is a trial and error adjustment. Seat Plug Stop has
approximately 0.5” total adjustment.
Photo 20
CAM Plate
The CAM Plate on the upper portion of the Case
Activated Linkage System is used to stroke the Push
Bar on the Bullet Seating Die. With a case activating
the Linkage System and the stroke is all the way up, the
dogleg shaped black plastic CAM should trip the Push
Bar to allow a bullet to fall. Adjust the CAM (A) vertically
or CAM Plate (B) horizontally until the Push Bar (C) is
activated properly (Photo 21).
Photo 21
Bullet Feeder Mechanism
The Spring Holder (A) prevents two bullets from feeding
at the same time. The height of this must be adjusted
based on the length of the bullet being used. Loosen
the Spring Holder Cap (B) so that the assembly moves
up and down. Place a bullet into the Bullet Drop Body
cutout. Slide the Spring Holder up or down so the white
Bullet Drop Pin (C) is level with the tip of the bullet. The
Bullet Drop Pin is designed to contact the side of the
bullet and hold it in place until the next cycle. Boat Tail
bullets may require the Drop Pin to be set a little higher.
Adjust as needed (Photo 22).
Photo 22
10

ITEM # PART # DESCRIPTION QTY.
1 781310 Dillon PM Bracket 1
2 781311 Dillon Adjustment Bracket 1
3 781312 Dillon Upper Tube 1
4 781313 Dillon Lower Tube 1
5 781314 Tube Coupling 1
6 781315 Dillon Clamp 1
7 781316 Dillon Clamp Anchor 1
8 181253 Cam 1
11

PRECISIONEERED RELOADING EQUIPMENT
We think that we make the very best reloading equipment in the world. If you agree, please tell your friends.
If you disagree, tell us we want to do something about it!
Customer Service
1-800-533-5000 (US or Canada) or 530-533-5191
Hours: Monday - Thursday, 6:30 a.m. - 4:00 p.m. Pacic Time
(hours may vary)
e-mail: [email protected] or visit our website at www.rcbs.com
RCBS 605 Oro Dam Blvd. East Oroville, CA 95965
Federal Premium Ammunition - RCBS - Alliant Powder - CCI - Speer Ammo - Speer Bullets
Fusion Ammunition - Estate Cartridge - Blazer Ammunition - Force on Force
Weaver - BLACKHAWK! - Champion - Gunslick Pro - Outers
Buck Commander - Ramline - Redeld - Shooters Ridge
7200586/1011
Table of contents
Popular Wire Feeder manuals by other brands
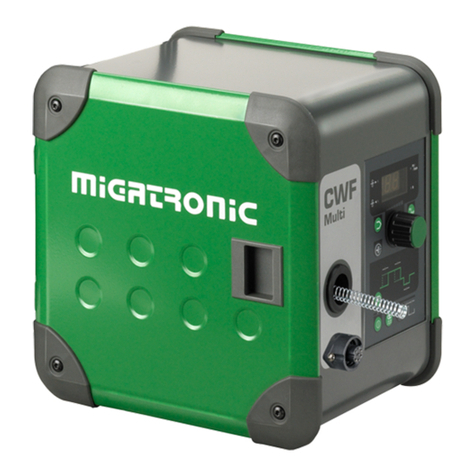
Migatronic
Migatronic CWF Multi user guide
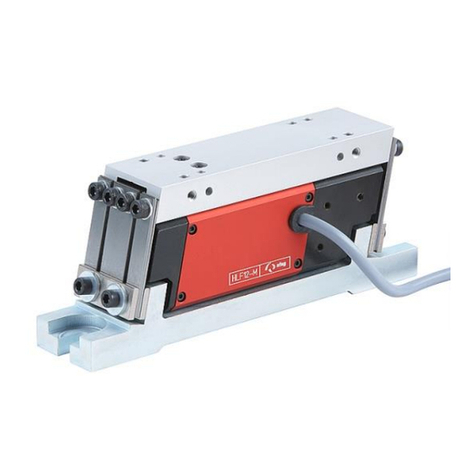
Afag
Afag HLF07-M Translation of operating and installation instructions

ESAB
ESAB Origo Feed 304 Truck instruction manual
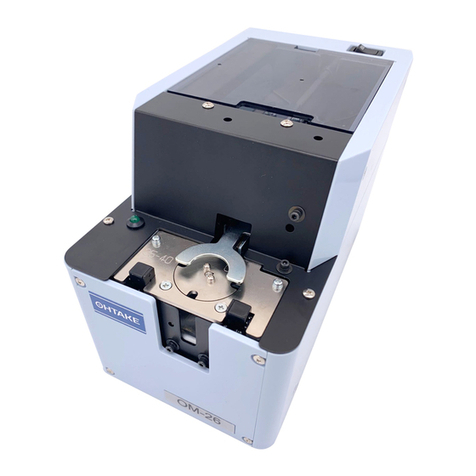
OHTAKE
OHTAKE OM-26R Series Operation manual
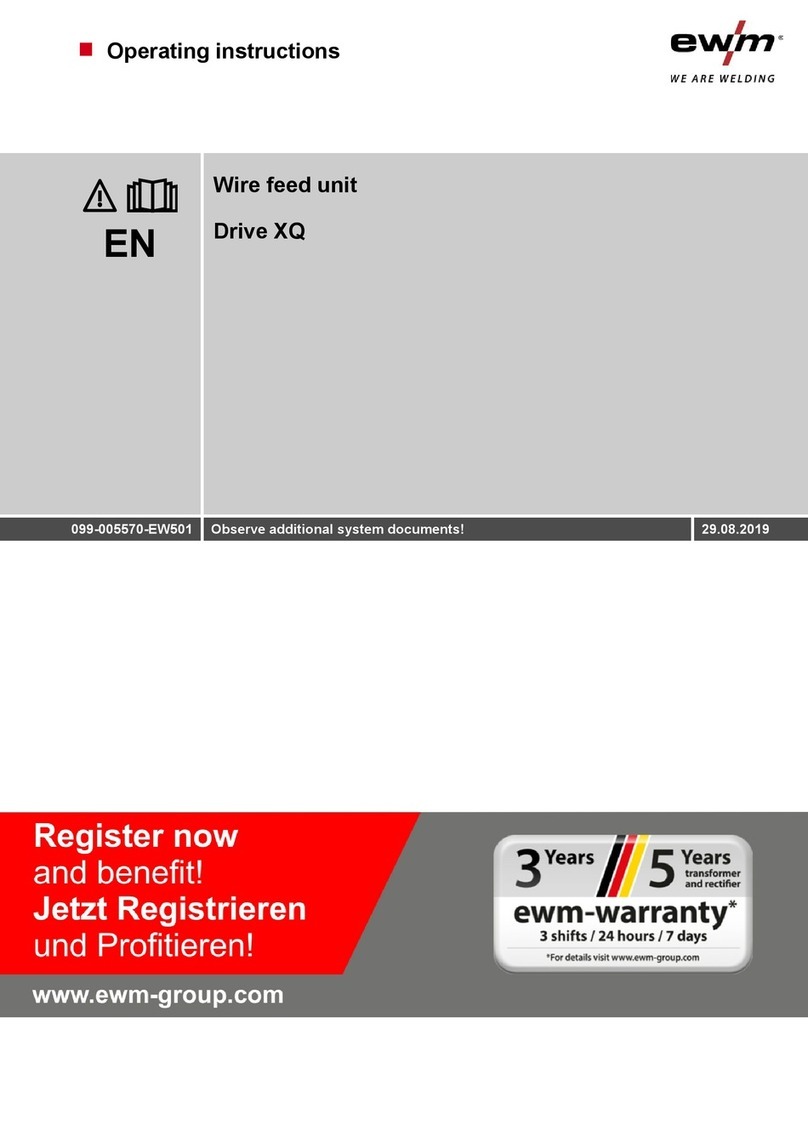
EWM
EWM Drive XQ operating instructions

Cumberland
Cumberland Hi-Lo Installation and operation manual