RCRCM Hornet Motor Glider Manual

Hornet Motor Glider

RCRCM Hornet Build
March 2016
Introduction
The RCRCM Hornet is a fully moulded motor glider with the following characteristic:
◦ Wingspan: 2.027mm
◦ Length: 1.23m
◦ Kit weight: 850g
◦ Flying weight: 1650g (Carbon Option)
◦ Airfoil: RC Series
◦ Wing area: 34.6dm²
◦ Control surface: aileron, flap, rudder, elevator
It is similar to, but in many ways quite different to, the well known RCRCM Typhoon. The Hornet has
an enlarged cockpit area that makes for a lot of choice in selecting motor and battery combinations.
The major advantage of the Hornet is that it can be built in many flavours to perform a large variety of
roles from a hand or bungee launch pure glider right through to a entry level hot liner capable of high
speeds.
A ballasted nose cone and bungee hook can be fitted if a pure glider is required.
A motor glider with modest power can be built if gliding and thermalling is the primary function.
A powerful in-runner motor can be fitted if high speed powered flight is the objective.
In this build I have chosen to add a modest amount power in the 280-350 watts range to be used only
to gain height, hence forth being a glider for thermalling and moderate slope soaring. At around 1.6Kg
flying weight this glider will not float like a DLG but should thermal well in moderate lift. I'll not add a
ballast system for the slope to keep the total flying weight to a bare minimum.
I did also consider adding FPV (First Person View) equipment to thermal in a virtual reality environment.
If a total energy vario (as used in full size gliders) was available I would have gone this way. I'm sure
such a thing is not that far away so the Hornet may well end up an FPV ship in the future.
Unpacking
Inspection
When your kit arrives carefully inspect the box for damage before the courier leaves your property.

Inventory
1 x Fuselage with cockpit canopy bell crank cover plate
2 x Wings
2 x Fully flying elevators
1 x Carbon main spar
2 x 4mm control rods
1 x Small components bag
◦ 2 x Aileron servo covers
◦ 2 x Flap servo covers
◦ 2 Flap control rod fairings

◦ 12 x threaded rods
◦ 23 x threaded metal clevises (1 is pre fitted on the bell crank)
◦ 4 x wing servo mounts
◦ 1 x cockpit servo tray
Kit Item Weights
Fuselage 298g
Canopy 17g
Left wing 326g
Right wing 325g
Left elevator 25g
Right elevator 30g
Accessory bag and spar 101g
Total kit weight 1122g
Electronic Component Selection
Power
I chose an emax GT2812 1180Kv motor weighing 105g that would produce 1.4Kg of thrust at 28A
(10200 rpm) on a standard 10 x 5 prop. This equated to 336watts. I selected an emax 40A
continuous rated ESC. It had a linear 3A 5v BEC but with 6 digital servos and an RX on board
this would be pushed to the limit. I elected to run a separate 3A (5A burst) Ubec powered off the
LiPo balance plug. The ESC weighed 34g.
Prop
I selected a folding prop 10 x 6 (40mm base, 5mm shaft) with carbon fibre blades weighing 34g.

Servos
I went with emax ES09D plastic geared sevos for the wing and rudder. They are dual bearing,
2.2Kg/cm at 4.8v, weighing 11.6g each. This range of servos was designed specifically for 450
helis swash plates where holding power and centering are key characteristics. They would fit in
the wing hard on the top skin without the supplied plywood servo mounts.
Foot Note :-After having seen and flown the plane I would recommend metal geared servos, especially for the flaps that
are prone to damage in a careless landing.
Fully flying horizontal stabilisers need the biggest, badest, servo that can be fitted in regardless of
the design speed. Centering and holding must be brutal and repeatable if the glider is going to be
capable of always flying at the speed selected by the mode switch. When flying at the extremity
of line-of-sight, especially in a breeze, the pilot must have total confidence in the glider trim
producing the desired air speed. I chose an Hyperion Atlas DS-13tmb for this job. It weighs
19.2g, is capable of 3.6Kg/cm at 4.8v and is programmable so control throws etc can be very finely
tuned without loss of power.
Initial CG Balance Test
The first build activity is to verify the target CG position is attainable with components selected.
Tape all the components that will be going into the glider in their respective positions and try a CG
test. At this early stage it is not necessary to be totally accurate, the objective being to verify that
motor and LiPo choices made are practical. The target supplied by RCRCM was 73.5mm back
from the leading edge, my model balanced at 77mm back indicating I need more weight forward.
This was not unexpected given I was working on a minimum power implementation. It showed
me that tail weight will be critical and I must make it as light as possible. This theme would prevail
throughout the build. I really dislike adding ballast to make the CG target.
Radio Preparation
Open a new model on the radio to be used, select a normal tail and a 4 servo wing configuration.
Zero all the trims and subtrims. Install the ESC and servos in the respective ports on the receiver
and power it up on the bench. This will center all the servos in preparation for setting up control
rod lengths etc. Be careful not to move the servo arm position once this is done.
Firewall and Motor
There is a nice fibreglass fire wall supplied that has to be firmly fixed in the glider nose. The
firewall angle determines the motor angle that has a bearing on performance and trim under power.
I like about 2-3 deg of down thrust and 1-2 deg of right thrust to counteract the propeller effects.
Getting the firewall into the glider in the correct position is important so I made up a wooden prod
that tightly fitted the center hole. This would be a guide for installation of the firewall.

The glider is then held level in the flying attitude with the firewall and prod in place. The angle can
then be adjusted as shown. When the correct position has been established the firewall can be
fixed with a small amount of CA glue to keep it in position while the permanent fixing is laid up.
I used a mixture of carbon tow and light glass roving. This is epoxied in place on both sides of the
firewall. Peal ply is then applied to remove excess resin and ensure the layup is compacted.
The peal ply is removed when the resin has set.
Fuselage tray and servos
I like to get really positive containment for the elevator servo and do this by cutting the elevator
servo slot tight and then opening up the rudder servo hole to allow the elevator servo to be slid in

sideways. A three sided rudder servo mount was then made from ply and screwed to the supplied
servo tray. This allows both servos to be very positively mounted without having a hole larger
than necessary to enable the servo to be slipped in without damaging the control wire.
I made up a 1.5mm ply battery tray and glassed it place to provide a firm base for the LiPo and to
strengthen the cockpit area that is a traditional problem area in molded gliders. The Hornet is
stiffer than most around the cockpit but the additional strength will help with the inevitable not so
perfect landing.
The servo tray is glassed in place and finished with peel ply material. The servos can then be
fitted in place.
Tail Feathers and Linkages
Rudder
The cut out for the rudder horn was marked up and the slot cut. The horn was fixed in place with
epoxy mixed with a little micro balloons to thicken it up a bit while curing.

Due to CG concerns I replaced the supplied 4mm control rods with square 3mm ones to save
weight in the rear. These rods have all the carbon aligned longitudinally and have little crush
strength. I fitted shrink wrap material to the rod ends to stop them from splitting. The rudder
clevis edges had to be ground off to clear the rudder horn fairing.
Horizontal Stabiliser
These fully flying elevators are very effective but pose a problem in setting up the initial position.
My eye-o-meter thought the wing section looked like it would need around 0.75 deg angle of attack,
certainly no more than 1 deg. Having lent my incidence meter I set the glider up on a flat bench

top and used V blocks to adjust the wing seam to be 3mm higher at the leading edge than the
trailing edge. I then adjusted the elevator so that the leading and trailing seams were equal and
marked the position on the vertical stabiliser. I then cut a length of fishing braid and marked the
positions of the center seam of the fuselage and elevator leading edge. I'll keep this in my flight
box to check elevator trim after assembly at the flying area. The marks were 72mm apart, this will
be my base starting trim point for the maiden flights.

Wings
The servo fairings have to be filed and fitted to their respective recesses.
I used silicon sealer to fix the covers in place after the servos and control rods were fitted.
Ailerons
I found the fibre glass aileron horns would not readily fit under the fairings and therefore discarded
them. I made some brass ones that had the advantage of only requiring a simple hole drilled
through the top skin and epoxying in place.

Flaps
The top skin of the wing must be cut out where the flap horn fairing are to be fitted. Leave
sufficient material for a base to glue in the supplied fairings. The fibreglass flap horns has to be
fitted under the top skin of the wing. The balsa trailing edge spar has to be dremelled out to allow
passage of the control rod.
The horns were then epoxied in place with the top edge of the horn contacting the upper wing skin.
A nice neat way of doing flap controls. I used silicon sealer to semi permanently attach the fairing
to the cut out in the top wing skin.
The flap clevis needs to be recessed to allow the flaps to be fully deployed.

Wing Servos
Build designs must allow for inevitable repairs and equipment replacement so I did not epoxy the
servos in. Instead I used silicon sealant that can be prised off if repairs are necessary. At least
3-4 days must be allowed for the material set sufficiently for flight.
NB : This glider will operate sub 100km/hr, this fixing method is most certainly not suitable for
anything anything faster. If a warmliner is being built use the supplied ply mounts or epoxy the
case to the top skin.
I chose not to use the supplied specific wing servo mounts but made my own plywood retainers
that were epoxied to the wing skin providing positive servo location.

Control Rod Set Up
Insert the servos into the ply locators, tape the flaps and ailerons in the neutral position. Install
the control rods into the clevises and attach the servo horn.
Ailerons
Adjust the aileron control rod length so as to have the servo horn at 90 deg to the control rod. In
most situations the servo spline will not allow the horn to be fitted at 90 deg so plug the servo into
the RX and use the radio subtrim to achieve the correct position.
Flaps
The flap travel needs to be about 5mm up and as much as possible down. To achieve this the
control arm must be fitted to the servo at an angle of at least 45 deg towards the wing leading edge.
Depending on the radio type use of subtrim and end points will allow sufficient travel to get 75 to 80
deg of down flap. This may take some experimenting to get the correct horn position and control
rod length. In some cases the control rod may have to be bent to avoid fouling balsa spar or skin.
It is important that the flap operates smoothly over it's whole range.
Take all the time necessary to ensure both the aileron and flap operation works perfectly, once you
are satisfied with the operation the servos can be fixed in position with silicon sealer.
NB. Once the servos are installed it is not possible to easily adjust the horn position as the horn
fixing screw is not accessible. Should this adjustment be necessary the servo has to be removed.
Radio Programming
Operational Planning
To fly this glider I'll not install any flight stabilisation devices. I'll use 4 of the 5 available flight
modes on the Sanwa SD-10G radio:
Launch mode (Allocated to the right spring switch).
I'm right handed and launch the glider with my left hand, holding the radio in the right. The
objective is to gain air speed at a shallow angle, as speed builds the elevator become more
effective and the ascent angle increases. By this stage I'm settled and flying the plane as
it climbs, just before releasing the launch switch I push forward dropping the nose to
increase air speed in preparation of the camber and power coming off.
◦ Motor on full. (There is no throttle stick as such just on or off with the mode)
◦ Both flaps and aileron down 3mm. ( I want maximum lift for a steep climb)

◦ High rates selected (I want full control at low speed)
◦ Aileron/rudder mixing off
◦ 60% exponential on ailerons and elevator
◦ No aileron differential
◦ 1.5 mm up elevator to initiate the climb out
◦ 2mm right rudder to counter prop wash rotation
◦ Flight timer started
Normal mode (Allocated to the middle position, left hand switch)
◦ High/medium/low rates for ailerons, elevator, rudder on right hand switch
◦ Camber control (flaps plus ailerons) active on the left slider
◦ Flaps only active on the right slider
◦ Aileron/rudder mixing on
◦ Flaps to elevator mixing on
◦ Aileron differential on
◦ Exponential on
◦ Aileron and flaps in the aligned position
◦ Elevator trimmed for best glide angle
Loiter (in thermal) mode (Allocated to the forward position, left hand switch)
◦ Medium rates for ailerons, elevator, rudder selected
◦ Camber control (flaps plus ailerons) active on the left slider
◦ Flaps only active on the right slider
◦ Aileron/rudder mixing on
◦ Aileron and flaps set 3mm down
◦ Elevator trimmed for slow speed
Landing mode (Allocated to the back position, left hand switch)
◦ High rates selected for ailerons, elevator, and rudder
◦ Camber control (ailerons only) active on the left slider
◦ Flaps control active on the right slider
◦ 60% exponential on ailerons and elevator
◦ Aileron/rudder mixing off
◦ Aileron differential off
◦ Crow active (aileron up and flaps down)
◦ Elevator trimmed for moderate descent
These modes may appear complicated at first but it really does reduce the pilot workload during
both the launch and landing. It is common to spend about a month fine tuning these parameters.
A glider such as the Hornet deserves to be flown with precision and accuracy, as the designer
obviously intended.
The Sanwa SD10-G radio has a full set of menus dedicated to gliders allowing the functions above
to be easily programmed. Many other radios do not have specific glider set ups. In the case of
the Frsky Taranis radio there are many templates on the net that people have built for a wide range

of aircraft types. If an appropriate template can be found programming work can be greatly
reduced.

Flight Testing
I always use a test plan for new planes, each flight has a single specific purpose and that is the
only characteristic that is explored during the flight. I have found this to be the fastest way to get
a new glider dialled in performing to the optimum.
Glide Test
A with an new project there are lots of unanswered questions about the flight characteristic. I was
not prepared to exert even my modest amount of power and simply launch the plane and see if it
would fly. I chose an area over a gully where the plane could be firmly hand launched downward
to gain airspeed and then have rising ground to land onto or contain the plane and minimise
damage should things go wrong.
The glide tests were very successful, it flew nicely with the CG at 73mm and the elevator string
length at 72mm. I did two glide throws before moving on to powered testing. It became very
clear that a lot of space would be required for the initial clean wing landings that were in my test
plan.
Maiden Powered Flight

The first powered flight was made at our local college sports grounds. It offered lots of space, and
very few people about. This flight was also was very successful. With 3mm camber down (both
flaps and ailerons) and 1mm of up elevator it easily climbed away under full power from my spring
switch on the radio. I did a couple of circuits to verify trim deciding not to change anything, no
clicks. I then went into a high altitude clean wing stall, no problem at all, just dropped the nose and
carried on. The objectives being achieved, next up was a clean wing landing. There was a
gentle wind right to left in the above photo so I was able to do a base leg outwards the sea and a
long flat final. The Hornet just goes on and on in ground effect with a clean wing.
Next flight was a CG test. I climbed to 300 – 400 feet and put the nose down in a 40 deg dive, it
pulled up indicating a forward CG. I repeated the trimming flight with the CG 3 mm further back
with similar but better results. I suspect I'll eventually end up flying at around 84mm to maintain a
consistent 40 deg dive but I don't like making large CG changes so it will take a while to reach that
level of tune.
Next flight verified Loiter mode, certainly flew slower and with adequate control. Nice.
Next flight tested crow at altitude, the initial setting I would use in the turn to final was stable with
just hint of ballooning so I carried on and landed in this configuration. My initial setting does not
have a lot of down flap so it could be carried to the ground. The space used for the landing was
about 50% of the previous clean wing landings. Aileron control with reflex was adequate.
Next flight was full flap testing. It certainly slowed the speed in a steeper descent, control was a
bit mushy but this was expected. Just before the landing flair I dumped the flaps back the initial
crow settings to avoid damaging the flaps on the ground. Going to have to remember about this
in the future, it would be very easy to to excited about a perfect landing and forget about protecting
the flaps.
Final Impression
Overall I pleased with the plane and it's performance. It will be several months before I stop
making changes to the programming and the way I fly it but at this point it is a winner, achieving all

the objectives I set out for the build. The Hornet will never be up there with the best 3.5M thermal
gliders but if I see a nice looking thunder storm approaching I can put in the car assembled and be
flying in 10 minutes. Such windows of opportunity are short lived and do not allow for a major
expedition of getting a big tow line glider in the air. A nice 2M glider that will reward precise flying.
Good luck, enjoy the ride.

Gallery

Table of contents
Other RCRCM Toy manuals
Popular Toy manuals by other brands
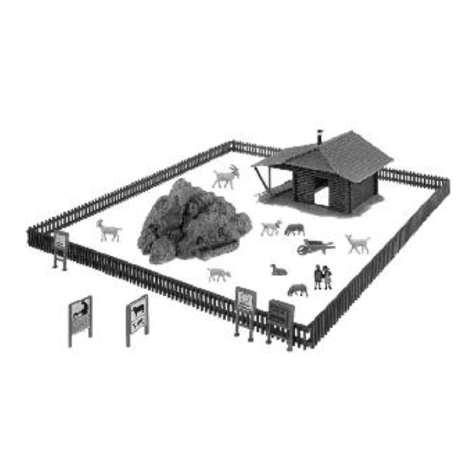
Faller
Faller GOATS AND SHEEP PATTING ZOO instructions
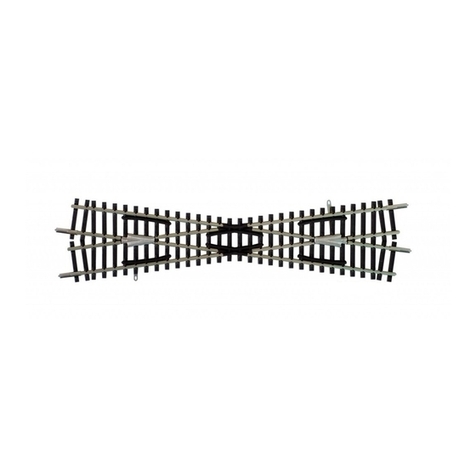
TILLIG BAHN
TILLIG BAHN 83161 manual
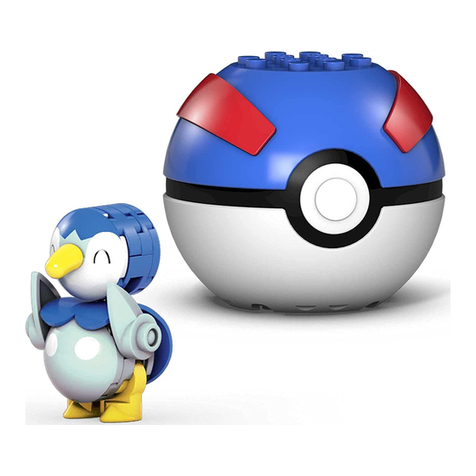
Mega Construx
Mega Construx POKEMON WONDER BUILDERS PIPLUP GMD26 manual
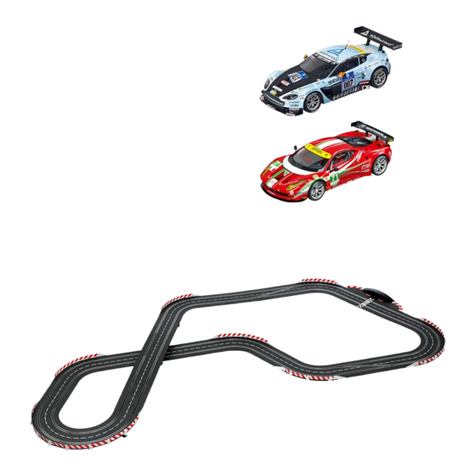
Carrera
Carrera 30158 GT ACTION Assembly and operating instructions

Mega Bloks
Mega Bloks PIRATES OF THE CARRIBEAN DEAD MAN'S CHEST Water Wheel... manual
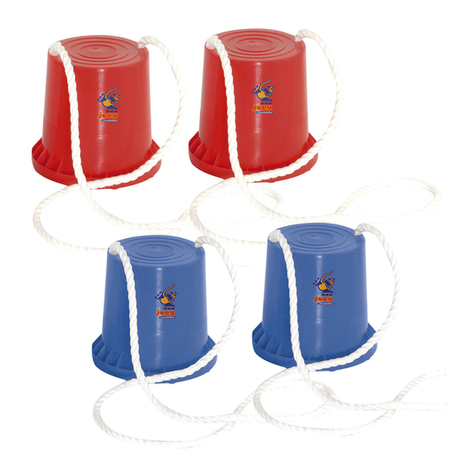
Hudora
Hudora joey Instructions for use