RDS Technology Artemis 100 User manual

1
Artemis 100
Variable Rate Drill Controller
Calibration and Operation
Software
Reference A500.000 rev. 7
Electro-Magnetic Compatibility (EMC)
This product complies with Council Directive
89/336/EEC when installed and used in accordance
with the relevant instructions.
Service and Technical Support
PLEASE CONTACT YOUR NEAREST DISTRIBUTOR
If unknown then fax: 44 (0) 1453 733322
© Copyright RDS Technology Ltd 2001
Document number
S/DC/500-10-310 : Issue 1 : 4/7/01
\UK310-1.DOC
User Guide

ARTEMIS 100 – VARIABLE RATE DRILL CONTROLLER
2
Contents
Overview_______________________________________________4
Operating Summary ____________________________________5
Power On/Off................................................................................................................. 5
Switch Functions........................................................................................................... 5
Normal Display Mode ___________________________________6
Programming Modes.................................................................................................... 6
Work Status Indicator ................................................................................................... 6
AForward Speed Display____________________________7
A.1 View Forward Speed ......................................................................................... 7
A.2 Speed Alarms ......................................................................................................... 7
A.3 Speed Sensor Calibration...................................................................................... 7
Manual Calibration........................................................................................................ 8
Auto Calibration ............................................................................................................ 9
BArea Display ____________________________________10
B.1 View Area Totals ..............................................................................................10
B.2 Zero Area Total................................................................................................. 10
B.3 Set Implement Width .......................................................................................11
C. Drilling Rate Functions___________________________12
C.1 View Drilling Rate ............................................................................................. 12
C.2 Adjusting the Drilling Rate............................................................................... 12
C.3 Drilling Rate Indicator ......................................................................................12
C.4 Changing the Target Rate ...............................................................................13
C.5 Set Current Rate to become new Target Rate ..............................................13
C.6 Product Calibration.......................................................................................... 14
C.7 Set "Thousand Grain Weight".......................................................................... 15
C.8 Select Unit ........................................................................................................16
C.9 Set % Step for Rate Offset...............................................................................16
C.10 Frequently asked Questions ...........................................................................17

ARTEMIS 100 – VARIABLE RATE DRILL CONTROLLER
3
D. Fan Speed Display ______________________________ 18
D.1 View Fan Speed............................................................................................... 18
D.2 Fan Under-Speed Alarm ................................................................................. 18
D.3 Fan Over-speed Alarm .................................................................................... 18
D.4 Set Low Fan Speed Alarm.................................................................................. 19
E. Tramlining______________________________________ 20
E.1 Manually advance bout number..................................................................... 20
E.2 Hold Bout number........................................................................................... 20
E.3 Symmetrical Tramlining .................................................................................. 21
E 4.1 Asymmetrical Left Tramlining........................................................................... 22
E 4.2 Asymmetrical Right Tramlining....................................................................... 23
E 4.3 10-bout Tramlining............................................................................................ 24
E 4.4 18-bout Tramlining........................................................................................... 25
E.5 Programme Tramline Bout .................................................................................. 26
F. Hopper level Alarm _____________________________ 28
G. Programme Functions and Fault Diagnosis _______ 29
G.1 Programme Modes 1 –4.................................................................................. 29
G.2 Error Codes...................................................................................................... 30
G2.1 Alarms irrespective of "Work" Status ................................................ 30
G.2.2 Alarms when the drill is in work........................................................ 31

ARTEMIS 100 – VARIABLE RATE DRILL CONTROLLER
4
Overview
The Artemis 100 Drill Control is a CAN Bus control system suited for both
conventional and pneumatic drills. The system has two CAN Modules - one
for controlling the electric motor driving the metering unit, and another
controlling the various sensor inputs and tramlining outputs. All the
components are connected via a custom wiring loom. The cab instrument
has a 6-way Amphenol sealed connector allowing it to be easily
disconnected and transferred to another drill as required. A separate heavy
duty power cable powers the CAN Modules and motor. An in-line heavy duty,
quick-release connector simplifies mounting and dismounting the drill.
The metering unit is controlled via an electric motor, allowing the drilling rate
to be varied at the touch of a button. The drilling rate can be varied in 5% or
greater steps from the pre-programmed target rate.
The instrument measures and indicates;
•Forward Speed
•Part Area and Total Area worked
•Tramline bouts
•Seed Application Rate (kg/ha or Seed/m2)
•Fan Speed
•Low Hopper Level
The instrument has a number of alarm functions for fan over-speed, forward
over-speed and under-speed, and hopper level. In addition, a number of
extra alarms are displayed as fault codes.
The instrument must be initially calibrated to suit the implement being
controlled. Seed calibration is very simple to undertake via a priming switch
provided on the drill. Other default settings are also programmable in the
calibration mode.
Area totals and all calibration data are automatically stored in memory when
the instrument is powered off.

ARTEMIS 100 – VARIABLE RATE DRILL CONTROLLER
5
Operating Summary
Power On/Off
Switch the system on/off via the toggle switch on the rear of the head unit.
Switch Functions
Current Bout
Press to select
the Display
Function
Decrease
Rate
Channel
Indicator
At Target rate
Indicator
Increase
Rate
Preset Tramlining
bout Indicator
EITHER:
1. View Area Total
Select the channel then
press to switch
between Area Total 1 and
Area Total
2. Advance Bout Number
Select the channel then
press to manually
advance the Bout Number.
3. Set Target Rate
Select the channel then
press and hold to
display rate. Use +RATE and
-RATE to adjust.
4. HOLD continuously to
enter Programme mode 1 /
Programme Mode 2
(Normal Mode is resumed
when the button is released).
CH Function Units
1Forward Speed km/h
2Area Total 1 or 2 ha
3Tramline/Current bout -
4Seed Rate kg/ha or seeds/m2
5Fan Speed rpm
6Hopper level alarm 'lo.1, lo.2'
These channels perform different functions
when the instrument is set in to Programme
Modes 1, 2, 3, or 4
Increase Rate
Or,
HOLD whilst
powering on to
enter CAL Mode 2
(for automatic
product
calibration)

ARTEMIS 100 – VARIABLE RATE DRILL CONTROLLER
6
Normal Display Mode
The instrument has a normal display mode displaying six work functions
Select a channel by pressing the button once or more.
When the drill is in work, the selected channel is displayed for 10
seconds before defaulting back to the tramline bout display
( channel).
When the drill is out of work, the instrument will continue to display the
selected channel.
Programming Modes
There are 4 programming modes with various calibration factors and default
settings.
Access to the programming modes is required for some settings which are
changed as part of the normal operating procedure (such as product
calibration). Changing these settings is described within the normal operating
instructions (sections A, B, C, C, D, E and F).
Other settings are made on installation and do not normally need to be
changed unless the instrument is switched onto a different drill. These settings
are appended to in the back of this manual (section G). The operator does not
normally need to refer to them.
Work Status Indicator
The indicator is used to indicate the channel to which the information on
the display relates.
It also shows the working status of the drill. If the cursor is flashing then the
drill is out of work, if the cursor is solid then the drill is in work.

ARTEMIS 100 – VARIABLE RATE DRILL CONTROLLER
7
AForward Speed Display
A.1 View Forward Speed
The forward speed is derived either from an
encoder on the landwheel, or from a radar
sensor
depending on your particular installation.
The speed is displayed in km/hr only.
A.2 Speed Alarms
(i) If you stop with the drill still in work, the
instrument will beep twice, and the display
alternates between the selected channel and
the forward speed channel, until you start
moving again.
(ii) If you drive too fast, the motor control will be
unable to maintain the required seed rate.
Again, the instrument will default to the
speed channel, the display will flash "HIGH"
and the instrument will beep until you slow
down. The maximum forward speed is
calculated by the software for the seed rate
being achieved.
A.3 Speed Sensor Calibration
The forward speed is derived from the
distance travelled in millimetres for each
pulse received from the speed sensor. The
speed sensor is either a rotary encoder on
the landwheel, or a radar sensor.
You can either calculate and manually enter
the Speed Sensor Factor (S.S.F.) or do an
"Autocal".
Figure 1 : Select Fwd. Speed

ARTEMIS 100 – VARIABLE RATE DRILL CONTROLLER
8
Manual Calibration
If a rotary encoder is fitted, the theoretical
calibration figure equals the rolling
circumference of the land wheel in
millimetres divided by the pulses per rev. of
the encoder,
e.g. diameter (mm) x 3.142
360
The cal factor should normally be a figure
around 10 (mm/pulse).
If a radar sensor is fitted, then accept the
default factor of 7.78 mm/pulse for the RDS
radar sensor.
To manually enter the calibration factor:
1. Select the forward speed channel (fig. 2).
2. Press and hold the button until the cal
factor appears on the display (fig 2).
3. Continue holding the button and
PRESS to select the digit/decimal point
to change (fig. 3).
4. HOLD to change the digit (or move the
decimal point). Releasing the button selects
the next digit.
5. Release the button to return to the
normal display mode.
Failure to correctly programme the speed
sensor factor will result in the drilling rate
being displayed incorrectly. Auto calibration
is likely to be more accurate than manual
calibration.
Figure 2 : Enter CAL Mode 1 (S.S.F.)
Figure 3 : Change S.S.F.
2 1
2 43

ARTEMIS 100 – VARIABLE RATE DRILL CONTROLLER
9
Auto Calibration
Auto-calibrate in field conditions for
maximum accuracy.
1. Place two markers 100 metres apart and
position some reference point on the tractor
(e.g. the cab step), opposite the first
marker.
2. Select the forward speed channel.
3. Press and hold the button until the cal
factor appears on the display.
4. Continue holding the button and press
the button. The display will show "AUto"
ready to start the test run (fig. 4).
5.Drive up to the second marker and stop
exactly opposite the marker. The instrument
counts and displays the pulses received
from the speed sensor over the measured
distance.
NOTE: The instrument only displays up to 9999
pulses then cycles back to 0000, however
the pulses are still being counted internally.
6. Press the button (fig. 5). The calibration
factor is automatically calculated and stored
in memory. The instrument then returns to
the normal display mode.
Figure 5 : Stop Autocal
Figure 4 : Start AutoCal
100 metres
6
5
3 4

ARTEMIS 100 – VARIABLE RATE DRILL CONTROLLER
10
BArea Display
B.1 View Area Totals
The area display is derived from the forward
speed sensor and the programmed
implement width.
There are two area registers. Each can be
independently reset to zero.
Press to cycle between the two area
registers 'tot.1' and 'tot.2'.
The display then shows the area
accumulated since that total was last reset.
B.2 Zero Area Total
1. Select the total 1 or total 2 and release.
2. HOLD for 5 seconds.
The instrument gives 10 beeps, then the total
resets to zero.
Figure 8 : Zero Area Total
Figure 7 : Select Area Register 1 / 2
Figure 6 : Select Area Channel
1 2

ARTEMIS 100 – VARIABLE RATE DRILL CONTROLLER
11
B.3 Set Implement Width
1. Select the Area Total channel ( ).
2. Press and hold the button for 5
seconds. The display will flash "tot.1", then
"tot.2" then show the programmed
implement width (fig. 9).
Default width = 4 metres.
3. Continue holding the button and
PRESS to select the digit/decimal point
to change.
4. HOLD to change the digit (or move the
decimal point). Releasing the button selects
the next digit (fig. 10).
5. Release the button to return to the
normal display mode.
Figure 10 : Change Implement Width
Figure 9 : View Implement Width

ARTEMIS 100 – VARIABLE RATE DRILL CONTROLLER
12
C. Drilling Rate Functions
C.1 View Drilling Rate
This channel displays the current drilling rate
in either Kg/Ha or Seeds/m2, depending
upon the selection made at the beginning of
the calibration routine.
The resolution for Kg/Ha units is:
0 to 24.9 0.1 Kg
25 to 250 1 Kg
250 to 9995 5 Kg
The resolution for Seeds/m2 is 1 Seeds/m2
C.2 Adjusting the Drilling Rate
Press the button to decrease the drilling
rate.
Press the button to increase the drilling
rate.
The rate adjusts by the % step programmed
in programme mode 3, i.e. 5%, 10%, 15%,
20% or 25% of the programmed target or
base drilling rate.
C.3 Drilling Rate Indicator
The left indicator is used to remind the
operator of his drilling rate. When the
indicator is in position 2, then the drill is
operating at the target rate.
If the indicator is in position 1 then the drill is
operating at plus the target rate.
If the indicator is in position 3 then the drill is
operating at minus the target rate.
Figure 11 View Drilling Rate (kg/ha)
Pos. 1
Pos. 2
Pos. 3

ARTEMIS 100 – VARIABLE RATE DRILL CONTROLLER
13
C.4 Changing the Target Rate
If the drilling rate is currently at the target
rate (the rate indicator is in position 2), then:-
1. With the rate display selected, press and
hold the button for 5 seconds (fig. 12).
The display will initially show either the top
row of segments or the bottom row of
segments to indicate the currently selected
units, then the current target rate.
2. When the number is flashing, release the
button.
3. Press and hold either the button to
increase the target rate, or the button
to decrease the target rate (fig. 13). The
longer the switch is held, the faster the
number changes.
4. When the desired target rate is displayed,
press and hold the button for 3 seconds
(fig 14) to revert back to normal operating
mode.
C.5 Set Current Rate to become
new Target Rate
If the drilling rate is not currently at the target
rate (rate indicator is in either position 1 or
3), then after pressing and holding the
button for 5 seconds, the current drilling
rate becomes the new target drilling rate
(the rate indicator moves to position 2).
On releasing the button, the instrument
will revert to normal operating mode.
Figure 12 View current Target Rate
Figure 13 Adjust Target Rate
Figure 14 Return to Normal Mode
1 2
4
3

ARTEMIS 100 – VARIABLE RATE DRILL CONTROLLER
14
C.6 Product Calibration
1. Place a container under the seed outlet of
the metering unit and press the priming
button adjacent to the metering unit, to
dispense the product.
The instrument automatically switches to the
programme mode, and the display will count
up the theoretical weight (in grams) of
product based on the calibration factor
currently stored in memory.
NOTE:If the drill has an "Accord" type metering unit,
you must consult the operators manual and
ensure that the metering slide is set to the
optimum position to achieve the required
drilling rate, before the motor is calibrated.
2. Once you have dispensed sufficient product,
release the priming switch and weigh the
product metered out. The theoretical weight
will remain flashing on the display.
NOTE:If the priming switch is held for long enough
to exceed 9999 grams then the instrument
will simply show ‘High’, informing the
operator that he must re-test to ensure the
weight does not exceed 9999 grams.
Press the button to re-select channel 4,
and the display will reset to "0000" ready for
another calibration.

ARTEMIS 100 – VARIABLE RATE DRILL CONTROLLER
15
5. Using the or button, adjust the
displayed weight to match the measured
weight. The longer the switch is held, the
faster the number changes.
6. When the correct weight is displayed, press
the button to confirm the entry. The
instrument will automatically re-calculate the
calibration factor (grams/pulse of the motor
encoder) and store it in memory.
The display will show "donE" for 5 seconds,
then the instrument will revert back to the
normal display mode.
7. If you display the drilling rate in Seeds/m2,
check the T.G.W. (Thousand Grain Weight)
setting is correct.
C.7 Set "Thousand Grain Weight"
The T.G.W. must be set in order enable the
instrument to display a drilling rate in
Seeds/m2correctly.
1. Press and hold the button as you switch
the instrument on. The instrument is then in
programme mode 3 on channel 1 (fig. 15).
2. Press to select channel 2 ( ). The
display will show the Thousand Grain
Weight in grams (fig. 16).
3. PRESS to select the digit/decimal point
to change (fig. 16).
4. HOLD to change the digit (or move the
decimal point). Releasing the button selects
the next digit.
5. Switch off to exit the programme mode (fig
17).
Figure 15 Enter Cal Mode 3
Figure 16 Adjust T.G.W. (Channel 2)
Figure 17 Return to Normal Mode
Off-On
+ Switch On
1
243
5

ARTEMIS 100 – VARIABLE RATE DRILL CONTROLLER
16
C.8 Select Unit
1. Press and hold the button as you switch
the instrument on. The instrument is then in
programme mode 3 on channel 1 (fig. 15).
The display shows either the top row of
segments to indicate the kg/ha unit is
selected, or the bottom row of segments to
indicate that the Seeds/m2unit is selected.
2. Press the button to change units (fig.
18).
If the Seeds/m2unit is set, check the T.G.W.
setting is correct for the product being
drilled (C.7).
3. Switch off to exit the programme mode.
C.9 Set % Step for Rate Offset
This sets the amount by which the rate is
adjusted away from the target rate when you
press the or buttons.
1. Press and hold the button as you switch
the instrument on. The instrument is then in
programme mode 3 on channel 1 (fig. 15).
2. Press to select channel 3 ( ). The
display will show a number indicating the %
step (5 - 25% in 5% increments) (fig. 19).
3. PRESS to select the required % step.
4. Switch off to exit the programme mode (fig.
17).
Figure 18: Change Units
Figure 19: Set % Rate Step
2
2
3

ARTEMIS 100 – VARIABLE RATE DRILL CONTROLLER
17
C.10Frequently asked Questions
•I have been drilling and there is some product left in the hopper. I think the
system has under-applied.
Perform a product calibration (C.6). If the measured amount tallies with the
amount displayed on the instrument, the product calibration factor is correct.
Check the forward speed sensor calibration and the implement width setting. If
all these settings are correct and over/under application still occurs, there may
be a problem with the motor control, in which case contact your service agent.
•I pressed the priming switch to prime the metering unit prior to metering
out the test quantity. Does this affect the calibration routine?
Before metering out the test quantity, press the button to re-select channel
4 and zero the instrument count. The priming quantity is then ignored. The
proceed as normal (C.6).
•I'm working in Seed/m2and then change product. Do I need to change any
settings?
You need to re-calibrate for the new product. Enter the appropriate T.G.W.
value either before or after the product calibration. Failure to set the T.G.W
correctly for the product being drilled, will result in the drilling rate being
incorrectly displayed.
•I want to check for blocked coulters.
Whilst the drill is lifted and the fan running, press the priming switch until seed
is dispensed from the coulters. When you return to the cab the instrument will
be flashing the theoretical weight dispensed. Simply press the button to
return to the normal display mode (the calibration factor is only recalculated if
you adjust the displayed weight figure using the + / - rate buttons).
Alternatively, when you move off, the instrument reverts to the normal display
mode.
•I operated the priming switch and want to continue normal drilling, without
changing the calibration.
The instrument will be flashing the theoretical weight dispensed. Don't press
any buttons. Just move off and the instrument will beep three times and revert
back to the normal display mode. The previously stored calibration factor will
be retained and used.

ARTEMIS 100 – VARIABLE RATE DRILL CONTROLLER
18
D. Fan Speed Display
D.1 View Fan Speed
This channel displays the fan speed in RPM,
typically about 3000 RPM (fig. 20).
D.2 Fan Under-Speed Alarm
If the fan speed drops below a programmed
under-speed alarm level, the display defaults
to this channel and shows the actual speed
(flashing display). The audible alarm sounds
5 beeps. The alarm is cancelled either by
pressing the button, or when the fan
speed is restored and within the normal
alarm range. If the fan speed drops below
the programmed under-speed level by 500
RPM or more, then motor operation will be
inhibited and the instrument will beep
continually. Motor operation is re-enabled
when the fan speed is restored and within
the normal alarm range.
The under-speed alarm is programmable
(D.4), typically = 2700 RPM.
D.3 Fan Over-speed Alarm
If the fan speed goes above 4500 RPM, then
the over-speed alarm sounds. The alarm is
cancelled either when the button is
pressed, or when the fan speed is restored
and within the normal alarm range.
The over-speed alarm threshold is non-
programmable.
The alarms are inhibited if the forward speed
is less than 2 km/hr.
Figure 20: View Fan Speed

ARTEMIS 100 – VARIABLE RATE DRILL CONTROLLER
19
D.4 Set Low Fan Speed Alarm
1. With the fan speed display selected, press
and hold the button for 5 seconds. The
instrument will then display the alarm
speed with the first digit flashing (fig 21).
2. Continue holding the button as you
PRESS the button to select the
digit/decimal point to change (fig 22).
3. Still holding the button, HOLD to
change the digit (or move the decimal
point) (fig. 22). Releasing the button
selects the next digit.
4. Switch off to exit the programme mode.
Figure 21: View Fan Alarm Speed
Figure 22: Change Fan Alarm Speed
32
1

ARTEMIS 100 – VARIABLE RATE DRILL CONTROLLER
20
E. Tramlining
There are five systems of tramlining - symmetrical, asymmetrical left,
asymmetrical right 10 bout and 18 bout. The tramline bout is programmable
from "oFF" (no tramlining) to 15 in symmetrical, asymmetrical left and
asymmetrical right sequences.
The display defaults to the channel after 10 seconds (unless the Area Total
was selected).
Selection of asymmetrical tramlining is denoted by a decimal point on the
display between the current bout number on the left and the tramline bout
number on the right.
Left or right asymmetric tramlining is selected in the programming mode.
NOTE: The tramline functions on the RDS Artemis 100 are identical to the RDS Multi-
function Drill Control hence the illustrations depict the MFDC 100 instrument.
E.1 Manually advance bout number
Press to advance the current bout
number by one.
E.2 Hold Bout number
Press to 'hold' the current bout when
the drill is lifted.
The display will flash 'StoP'.
Press again to resume the normal bout
sequence.
Figure 23: Advance Bout Number
A decimal point
indicates an
asymmetric tramlining
regime is selected
Figure 24: Hold Bout Number
Table of contents
Other RDS Technology Controllers manuals
Popular Controllers manuals by other brands
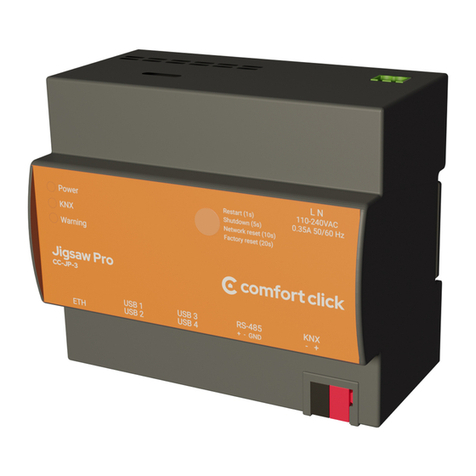
ComfortClick
ComfortClick Jigsaw Pro CC-JP-3 manual
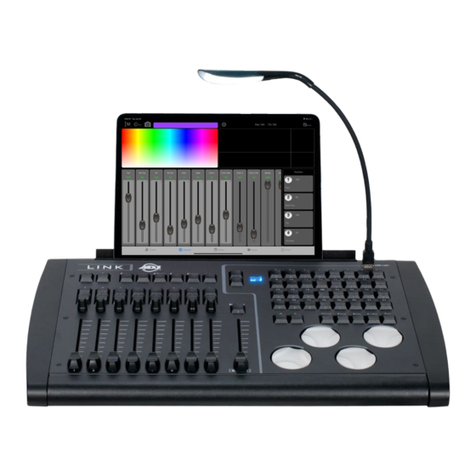
ADJ
ADJ Airstream Link manual
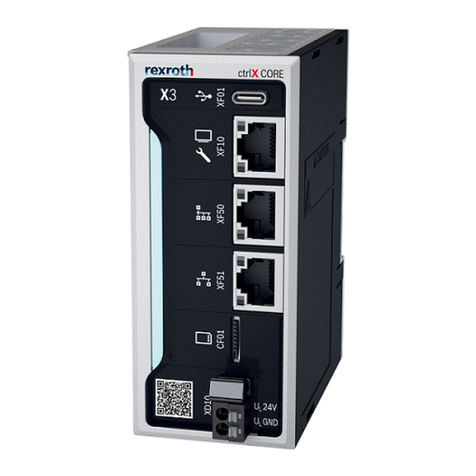
Bosch
Bosch rexroth ctrlX CORE operating manual
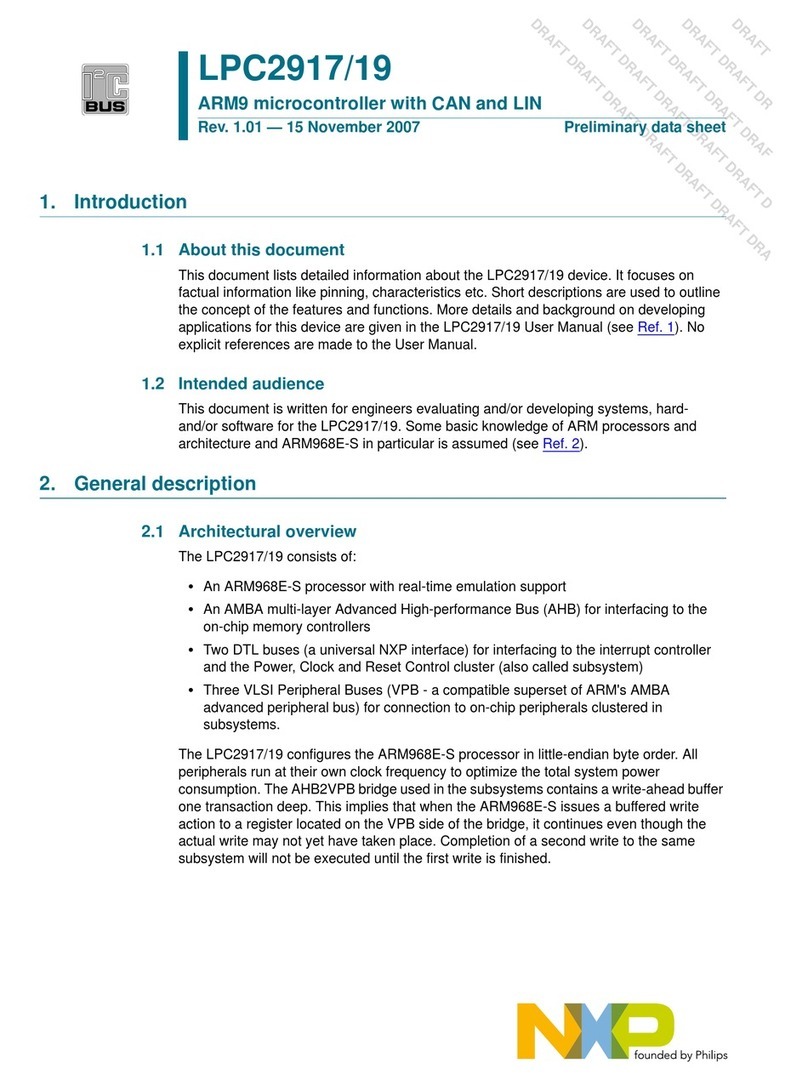
NXP Semiconductors
NXP Semiconductors LPC2917 Preliminary data sheet
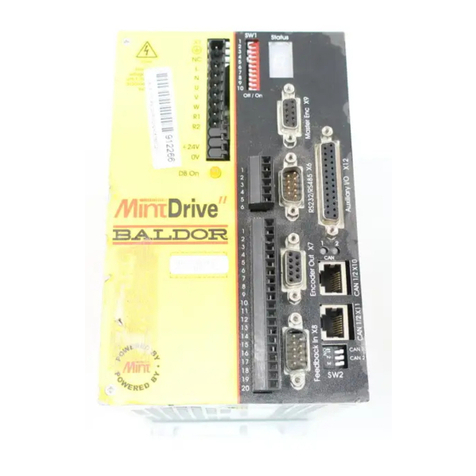
Baldor
Baldor MintDrive installation manual
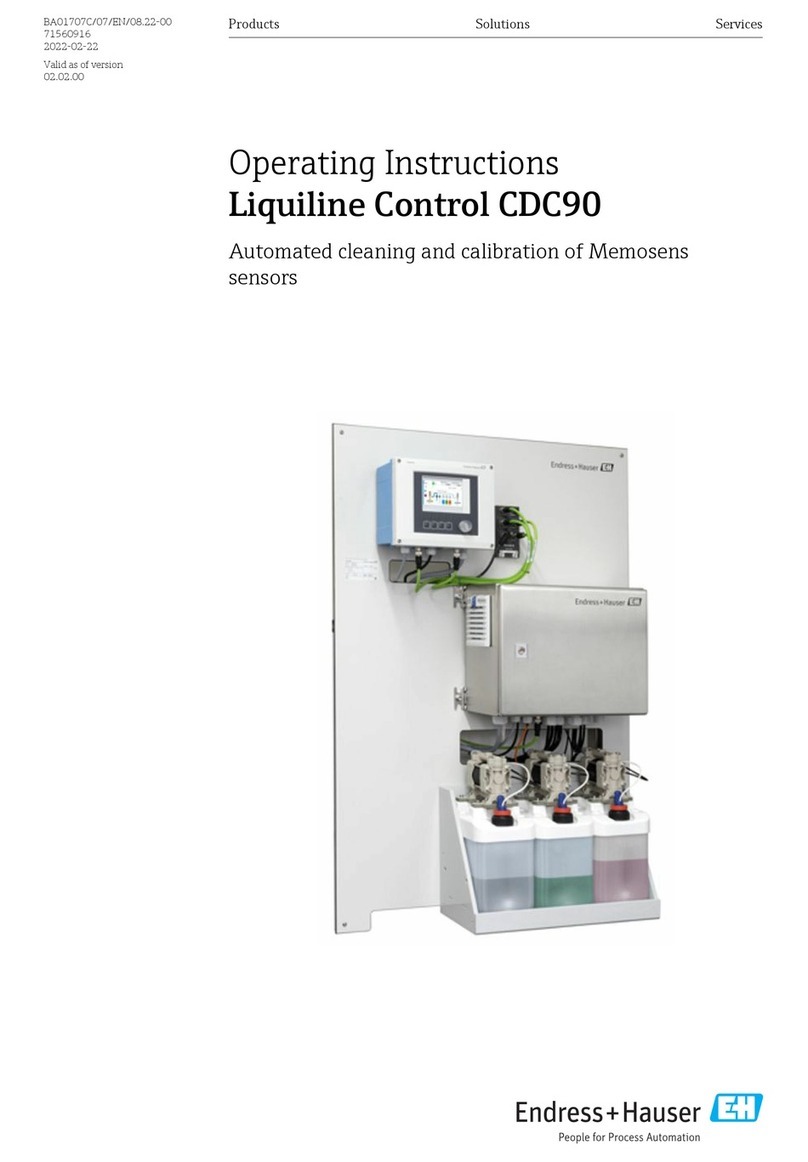
Endress+Hauser
Endress+Hauser Liquiline Control CDC90 operating instructions