Red Valve GS-700 User manual

GS-700 Diaphragm Actuator
Installation,Operation,andMaintenanceManual
IMPORTANT
Please take a moment to review this manual. Before performing any maintenance on the
valve be sure that the pipeline has been depressurized. Theimproperinstallationoruseofthis
product may result in personal injury, product failure, or reduced product life. Red Valve Co., Inc.
can accept NO liability resulting from the improper use or installation of this product. If you have
any questions or problems, please call the customer service hotline at (412) 279-0044. We
appreciate your comments. And thank you for choosing Red Valve.
Series 700 actuators are pneumatic
diaphragm operators that have spring return
in both direct and reverse acting styles,
offering fail open and fail closed modes
respectively. The pressed steel diaphragm
case construction along with the nylon
reinforced Buna-N rubber diaphragm permits
a maximum allowable air supply pressure of
80 psig (550 kPag).
This pre-formed diaphragm provides a
constant effective area throughout the full
extent of travel.
With effective diaphragm areas ranging from
60–160 in2(385–1030cm2), Series 700 actua-
tors can provide the necessary stem force to
meet virtually any operating requirement.


RED VALVE INSTRUCTION MANUAL
MODEL GS700 REVERSE-ACTING ACTUATOR
3.0 MAINTENANCE
3.1 GENERAL
Actuator parts are subject to normal wear and must be inspected and replaced when necessary. The frequency of inspection
and part replacement depends on the severity of the service conditions. Normally, only the rubber parts such as the
diaphragm, stem seal, gasket, and rings will require replacement.
3.2 PRECAUTIONS
Be aware that large pressure and spring forces are required to actuate a valve. Sudden release of these forces or of valve or
actuator pressure has the potential to cause personal injury or damage to property.
Before starting to disassemble the actuator, proceed as follows:
A. Isolate the valve from the line pressure.
B. Release fluid pressure from the valve.
C. Release air pressure from the diaphragm chamber of the actuator.
D. Remove all actuator spring preload. Note that if the actuator travel has been set up to be less than nominal, it may not be
possible to remove all preload with the spring adjuster nut alone. In this case, it will be necessary to disassemble the stem
connector to remove remaining spring preload.
3.3 REVERSE-ACTING ACTUATOR (Refer to Figure I and the Actuator Assembly Drawing)
3.3.1 Disassembly
A. Bypass or isolate the valve and reduce the diaphragm pressure to atmospheric.
B. Rotate the spring adjuster nut (Item 29) downward on the actuator stem until all spring preload is removed.
C. If necessary, remove the stem connector by removing the four cap screws (Item 23). Loosen the setscrew in the stem
clamp (Item 26) and remove the stem clamp from the actuator stem.
D. If necessary, remove the actuator from the valve by unthreading the hold-down nut or studs and nuts, as applicable.
E. Remove the spring adjuster nut (Item 29) from the actuator stem.
F. Remove the cap screws (Item 4) and hex nuts (Item 5) and remove the base (Item 3).
G. If the diaphragm is not being replaced, remove the stem and diaphragm plate assembly (items 11, 12, 13, 14, and 16). If the
diaphragm is being replaced, block the lower end of the actuator stem, then unscrew the flat head screw (item 11) and remove the
diaphragm plate (item 13), the diaphragm (item 14) and the diaphragm stop (item 12).
H.If necessary, remove the actuator stem (Item 16) from the bushing (Item 30).
1. If necessary, remove the cover (Item 2) and the yoke plate and bushing assembly (Items 31 and 30) by removing the hex nuts and
lockwashers (Items 9 and 10).
J. Remove the bushing from the yoke plate by removing one of the retaining rings (Item 34).

RED VALVE INSTRUCTION MANUAL
MODEL GS700 REVERSE-ACTING ACTUATOR
3.3.2 Assembly
A. If the diaphragm is being replaced, apply gasket compound (CV P/N 197077 or equivalent) to the surface of the diaphragm (item
14) where the diaphragm stop (item 12) seats. Assemble the diaphragm, diaphragm plate (Item 13) and diaphragm stop to the
actuator stem (Item 16) using the flat head screw (Item 11). Torque the flat head screw to the value shown on the assembly drawing.
B. Install the O-ring (item 36) with o-ring grease in the outside groove of the bushing (item 30). Install the bushing in the yoke plate
(Item 31). Note that the bushing should be oriented so that the larger internal groove is at the upper end of the yoke plate. Install the
upper and lower retaining rings (Rem 34) on the bushing. Install the U-cup seal (Item 33) with o-ring grease in the upper groove of
the bushing. Install the o-ring (Item 35) with o-ring grease in the lower groove of the bushing.
C. Place the spring plate (Rem 17) and spring (Item 15) into the yoke. Block the spring plate and the spring up as necessary to
permit assembly of the stem.
D. Install the yoke plate assembly in the yoke (Item 1). As an option, apply gasket compound (CV P/N 197077 or equivalent) to the
gasket (item 32). Place the gasket over the yoke plate. Orient and install the cover (Item 2) on the yoke. Install lockwashers (Item 10)
and hex nuts (item 9) on the cover studs. Torque the nuts to the value given on the assembly drawing.
E. Carefully lower the stem assembly through the bushing and the spring plate. Install the thrust washer (Item 18) and spring
adjuster nut (Item 29) on the stem. Rotate the spring adjuster nut until the spring is just starting to be compressed.
F. Place the base (item 3) on the cover and install the hex head cap screws (item 4), hex nuts (Item 5), and eyebolts (item 6 on the
actuator assembly drawing). Torque the fasteners to the value on the assembly drawing. Thread the vent (Item 40 on the assembly
drawing) intothe base.
G. Place the upper stem weldment (item 22) on the stem so that the bottom surface of the upper stem weldment is approximately
0.06" (1.5 mm) above the bottom of the stem.
H. After the actuator is mounted on a valve, place the stem lock plate (item 28) over the valve stem, then install the stem clamp (Item
27) on the valve stem.
1. Referring to Paragraph 2.3, position the stem clamp as required for valve seating and travel, then tighten the setscrew in the stem
clamp. Install the socket head cap screws (Item 23) with lockwashers (Item 24). Torque the fasteners to the value on the assembly
drawing.
J. Drill holes in the yoke as directed by the assembly drawing and install the indicator plate (Item 8 on the assembly drawing) and ID
plate (item 19on the assembly drawing) using drive screws (Item 20 on the assembly drawing).
K. If necessary for size 100, 160, and 160-5 actuators, install a bushing (Item 41 on the assemblydrawing) in the air inlet hole of the
cover.
L.Apply preload to the springby rotating the spring adjuster.
M. Cycle the actuator slowly several times to verify that no binding occurs during operation. Pressurize the actuator from 80 to 100
psig (5.5 to 7 bar) and check for leaks. Binding, noise or leakage is not acceptable.
Recommended Spare Parts:
Diaphragm p/n 185988 See #14 Fig.1
O-Ring p/n 357801 See #35 Fig.1
O-Ring p/n 357802 See #36 Fig.1
Gasket p/n 356998 See #32 Fig.1
Seal p/n 357800 See #34 Fig.1




RED VALVE INSTRUCTION MANUAL
MODEL GS700 DIRECT-ACTING ACTUATOR
3.0 MAINTENANCE
3.1 GENERAL
Actuator parts are subject to normal wear and must be inspected and replaced when necessary. The frequency of inspection
and part replacement depends on the severity of the service conditions. Normally, only the diaphragm will require
replacement.
3.2 PRECAUTIONS
Be aware that large pressure and spring forces are required to actuate a valve. Sudden release of these forces or of valve or
actuator pressure has the potential to cause personal injury or damage to property.
Before starting to disassemble the actuator, proceed as follows:
A. Isolate the valve from the line pressure.
B. Release fluid pressure from the valve.
C. Release air pressure from the diaphragm chamber of the actuator.
D. Remove all actuator spring preload. Note that, if the actuator travel has been set up to be less than nominal, it may not be
possible to remove all preload with the spring adjuster alone. In this case, it will be necessary to disassemble the stem
connector to remove the remaining spring preload.
3.3 DIRECT-ACTING ACTUATOR (Refer to Figure I and the Actuator Assembly Drawing)
3.3.1 Disassembly
A. Bypass or isolate the valve and reduce the diaphragm pressure to atmospheric.
B. Rotate the spring adjuster (item 21) downward on the actuator stem until all spring preload is removed.
C. If necessary, remove the stem connector by removing the four socket head cap screws (item 23). Loosen the setscrew in
the stem clamp (Item 27) and remove the stem clamp from the actuator stem.
D. If necessary, remove the actuator from the valve by unthreading the hold-down nut or studs and nuts, as applicable.
E. Remove the hex head cap screws (Item 4) and hex nuts (Item 5) and remove the cover (Item 3).
F. If the diaphragm is not being replaced, remove the stem and diaphragm plate assembly (Items 11, 12,13,14, and 16). If the
diaphragm is being replaced, unscrew the flat head screw (Item 11), then remove the diaphragm stop (Item 12), the diaphragm
(Item 14), and the diaphragm plate (Item 13).
G. If necessary, remove the actuator stem (Item 16), the spring (Item 15), the spring plate (Item 17), and the thrust washer (Item 18).
H.If necessary, remove the base (Item 2) by removing the hex head cap screws (Item 7) and lockwashers (Item 10).

RED VALVE INSTRUCTION MANUAL
MODEL GS700 DIRECT-ACTING ACTUATOR
3.3.2 Assembly
A. If the diaphragm is being replaced, apply gasket compound (CV P/N 197077 or equivalent) to the surface of the diaphragm (Item
14) where the diaphragm stop (Item 12) seats. Assemble the diaphragm, diaphragm plate (Rem 13), and diaphragm stop to the
actuator stem (Item 16) using the flat head screw (Item 11). Torque the flat head screw to the value shown on the assembly drawing.
B. Install the spring adjuster (Item 21) in the yoke (Item 1).
C. Assemble the base (Item 2) to the yoke using hex head cap screws (Item 7) and lockwashers (Item 10). Torque the screws to the
value given on the assembly drawing.
D.Place the thrust washer (Item 18), the spring plate (Item 17), and the spring (Item 15) in the yoke.
E. Place the stem assembly in the yoke and through the spring plate and thrust washer. Align the bolt holes in the diaphragm with
the bolt holes in the base.
F. Place the cover (hem 3), with bushing (Item 41) when required, on the base and install the hex head cap screws (Item 4), hex nuts
(Item 5), and eyebolts (Item 6). Torque the fasteners to the value on the assembly drawing.
G. Place the upper stem weldment (Item 22) on the stem so that the bottom surface of the upper stem weldment is approximately
0.06" (1.5 mm) above the bottom of the stem.
H. After the actuator, is mounted on a valve, place the stem lock plate (Item 28) over the valve stem, then install the stem clamp (Item
27) on the valve stem. Position the stem clamp as required for valve seating and travel, then tighten the setscrew in the stem clamp.
Install the socket head cap screws (Item 23) with lockwashers (Item 24). Torque the fasteners to the value on the assembly drawing.
I. Drill holes in the yoke as directed by the assembly drawing, then install the indicator plate (Item 8) and ID plate (Item 19)
using drive screws (Item 20).
J. Apply preload to the spring by rotating the spring adjuster.
K. Cycle the actuator slowly several times to verify that no binding occurs during operation. Pressurize the actuator from 80
to 100 psig (5.5 to 7 bar) and check for leaks. Binding, noise or leakage is not acceptable.
Recommended Spare Parts:
Diaphragm p/n 185988 See #14 Fig.1


Table of contents
Popular Controllers manuals by other brands
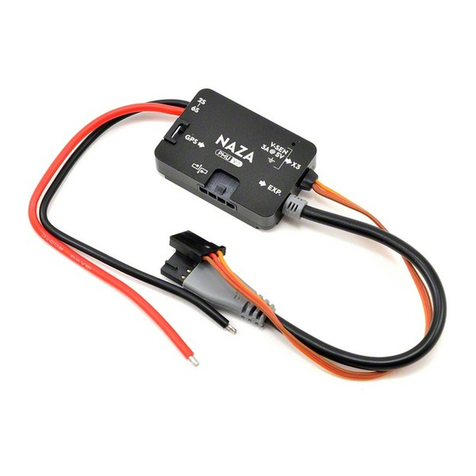
dji
dji Naza-M V2 quick start guide
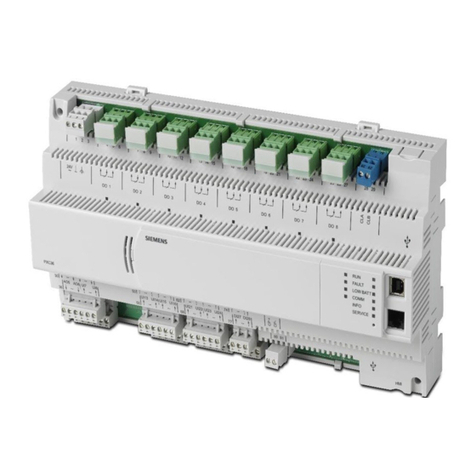
Siemens
Siemens PXC Compact Series installation instructions
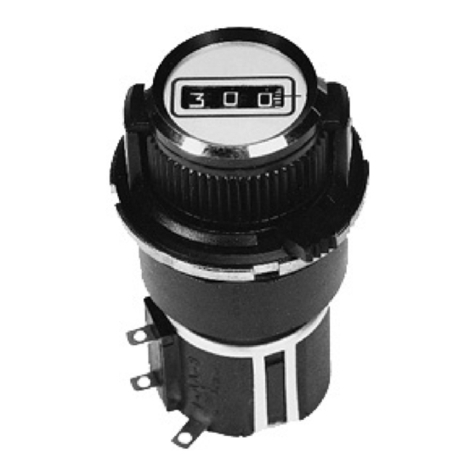
Ropex
Ropex RESISTRON PD-3 quick start guide
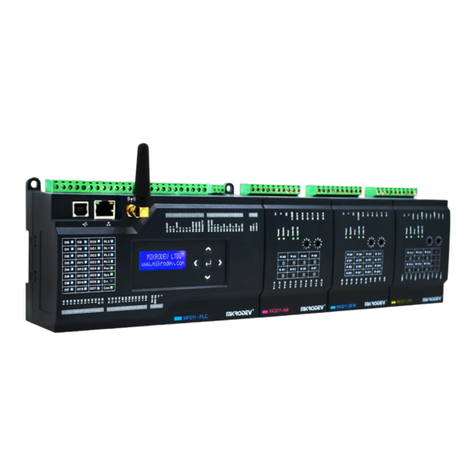
MIKRODEV
MIKRODEV PLC Series Hardware manual
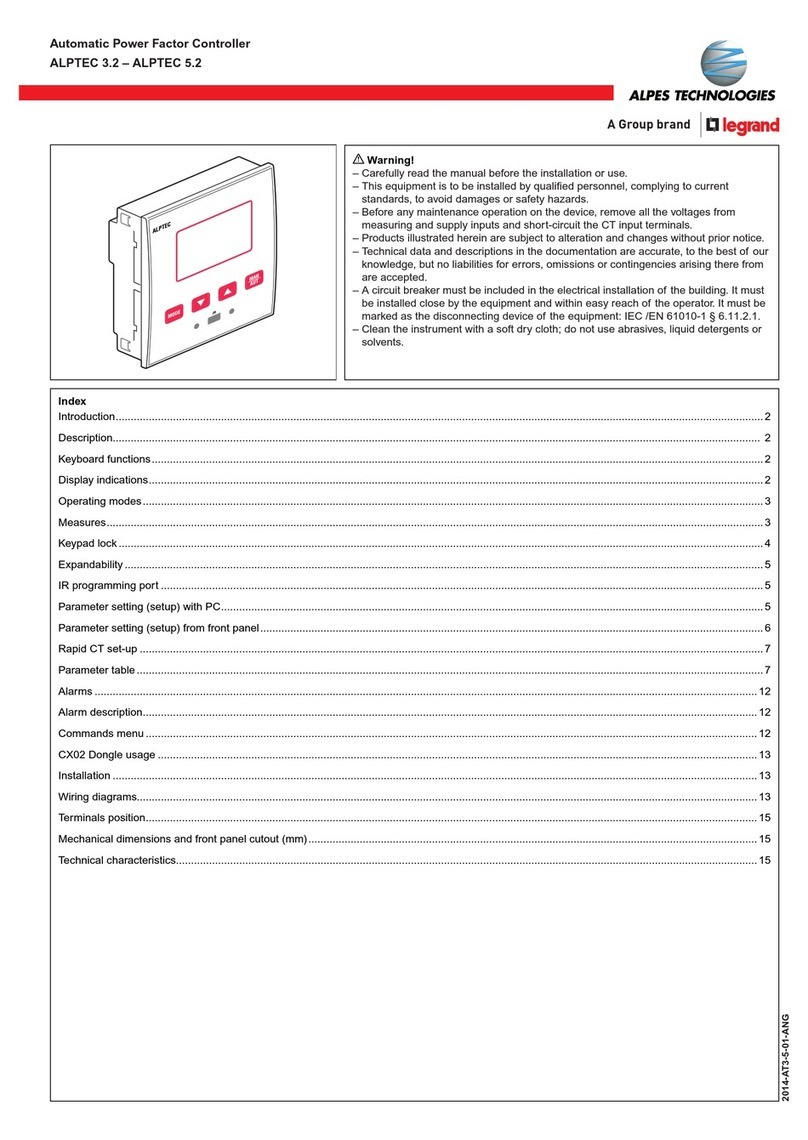
Alpes Technologies
Alpes Technologies ALPTEC 3.2 manual
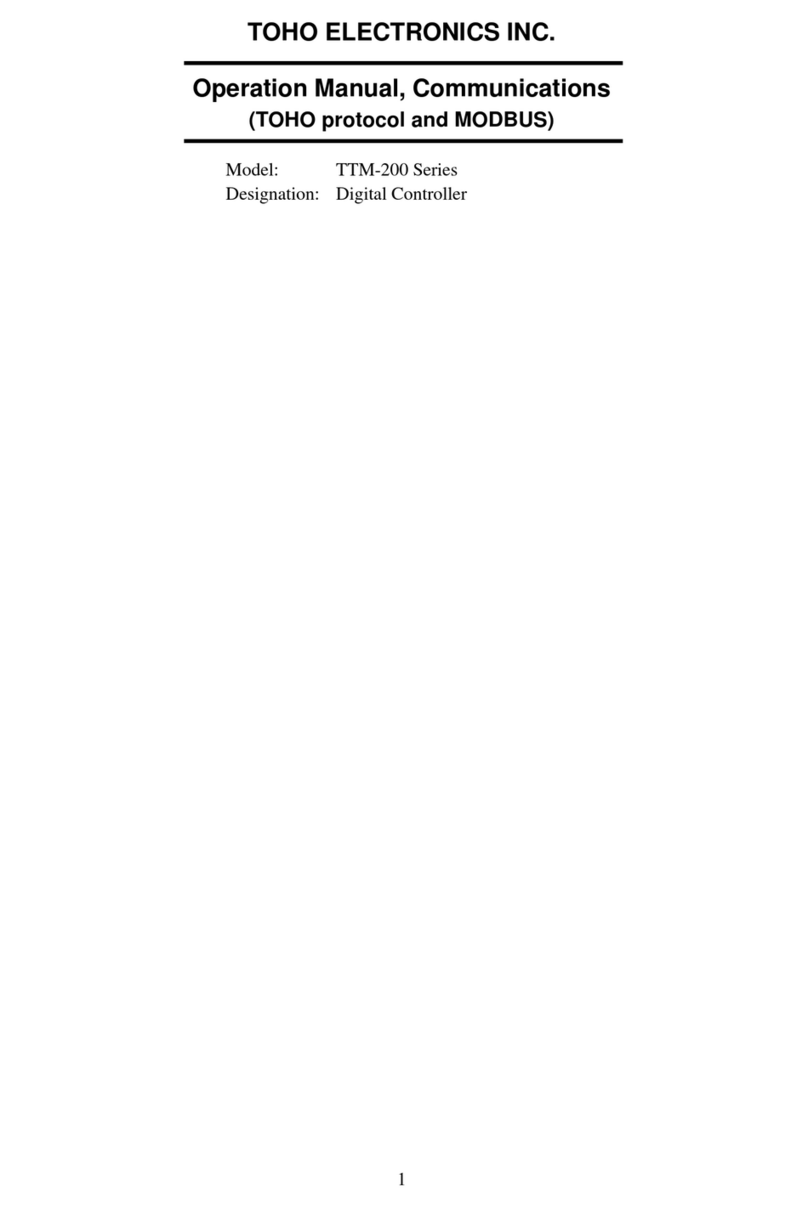
Toho Electronics
Toho Electronics TTM-200 Series Operation Manual, Communications