Rickard PCD User manual

INTRODUCTION
The RICKARD PCD may be supplied complete with electronic pres-
sure controls which will enable the damper to maintain a constant
branch duct static pressure at all times. The pressure controller may
be mounted remote from the PCD in a separate control panel.
In the case of the damper-mounted controller, a 220/24Volt trans-
former and 2m PVC power lead with plugtop are included and the
controller is completely pre-wired in the factory. In the case of the
controller which is mounted remotely, the contractor must provide a
24V AC power supply and must also complete the wiring between
the controller and the damper actuator.
The static pressure sensor is supplied loose, to be fitted to the
branch duct in a suitable position by the contractor. The intercon-
necting cable between the controller and the sensor form part of the
supply and although the standard length supplied is 20m, additional
cable may be supplied if required.
INSTALLATION
The PCD may be manufactured to any size required, both in terms of
the width and the height of the unit. Although the standard depth is
150 mm, this too may be varied to suit any requirements but may
not be less than 150 mm.
When damper widths exceed 1000 mm, the aluminium blades are
split and a mullion is fitted down the centre of the casing. In this
case two actuators would be fitted, one for each section. As a rule
the area of blades on one actuator should never exceed 0.5 m². For
example, a damper of say 1400 × 1400 mm would consist of four
sections, each 700 × 700 mm and each having its own actuator.
The standard PCD would be manufactured with 35mm sheet metal
flanges complete with four fixing holes on each flange or pre-
manufactured flanges such as MEZ flanges are available as an op-
tional extra.
The PCD must always be installed with the actuator on the down-
stream side of the vanes. The PCD may be installed with the Lindrive
actuator on the top or bottom depending on the specific installation,
but not on the sides (the vanes must always be horizontal).
The Pressure Sensor is supplied loose and is easily fitted to the duct
on site. Drill a 10mm diameter hole in the duct to accept the sens-
ing probe and fix the sensor by means of two self tapping screws.
Ensure that the sensing probe protrudes into the air stream and is
not obstructed by internal duct lining or any other such obstruction.
In all cases the pressure sensor for a branch duct should be fitted on
the branch duct itself and not in the feeder duct to the individual
terminal nor in the terminal unit itself.
Generally it is recommended that the sensor be fitted at a point
which is half to two thirds of the distance from the damper to end of
the duct run so that the most representative pressure is sensed.
Avoid placing the sensor close to bends or other obstructions.
OPERATION
To adjust the duct static pressure, turn the pressure adjustment po-
tentiometer screw. Clockwise rotation of this screw causes the PCD
to open and increase the duct static pressure. The flashing green
LED indicating light on the controller indicates that the controller is
transmitting a signal to drive the damper open. This signal will
continue even after the damper has reached the mechanical limit
stops, unless the setpoint has been reached. Note that 20 turns of
the potentiometer cover the full range of adjustment.
The frequency with which the light flashes is an indication of how
close the damper is to the required setpoint. As the duct static pres-
sure approaches setpoint, the flashing slows down and will stop
flashing altogether when setpoint is reached. In the same way, the
red LED indicating light indicates that the controller is transmitting a
signal to close the damper. At setpoint both lights are off. An indi-
cating light which remains on continuously means that the duct pres-
sure is far from setpoint and that the actuator is driving continuously
to correct the pressure. The problem in this case may be that the
static pressure upstream of the damper is incorrectly set.
DAMPER MOUNTED CONTROLS
In this case the pressure controller is mounted in a panel which is
attached to the side of the damper.
A 20m length (standard) of sensor cable with DIN type connector
fitted to one end, is attached to the controller and must be plugged
into the pressure sensor once it has been fitted to the branch duct.
Pressure Adjustment
Potentiometer Screw

REMOTE MOUNTED CONTROLLER
In some cases the Pressure Control Dampers may be mounted in
positions where it is difficult to access the controller for the purpose
of adjusting the static pressure setpoint. In this case the controller
may be supplied separately, to be mounted in a remote control pan-
el which is more easily accessible.
On the front face of this controller are the two indicating lights
which indicate whether the controller is transmitting a signal to drive
the damper open (green) or closed (red). The static pressure set-
point adjustment screw is also located here, as well as a DIN socket
for the pressure indicating gauge connection, as detailed below.
The controller has a multi-pin plug-in connector and matching base
with screw terminals to facilitate field wiring. The pressure sensor
and actuator are wired directly to this base and a 24 Volt AC power
supply must be connected to the terminals as shown on the follow-
ing diagram. The control characteristics are exactly the same as for a
damper mounted controller.
PRESSURE SENSOR
The RICKARD Static Pressure Sensor operates by measuring the air-
flow through the sensing probe. This airflow is due only to the static
pressure in the duct as the probe must enter the duct at right angles
to the air stream, so that the velocity of the air does not influence
the reading.
It is therefore most important that the sensing probe is not altered
in any way that may influence the air flow through the probe. This
would include modifications such as extending the probe with an
additional length of tubing or even blocking the ventilation holes at
the back of the sensor enclosure.
Pressure sensors are available with the following duct static pressure
control ranges:
0 –100 Pa
0 –200 Pa
0 –500 Pa
Note that the same controller is used in all cases; the range is deter-
mined by the choice of sensor only.

PRESSURE INDICATION
The RICKARD pressure controller provides a facility for connecting a
meter which will give a direct indication of duct static pressure. This
eliminates the need for manometers and pitot tubes which are clum-
sy and require special holes to be drilled into the duct for taking
readings. Both locally and remote mounted controllers have a DIN
socket to which the Pressure Indicating Meter is connected. It is
normal practice to have at least one such portable meter permanent-
ly available at each installation.
Especially during commissioning, this meter makes it easy to monitor
the duct static pressure as it receives the same signal as that control-
ler receives from the sensor.
Note that the indication is given as a percentage of the full scale
reading of that particular sensor –e.g. an indicated 30% for a 0 –
200 Pa sensor is equal to 60 Pa.
FACE AND BYPASS DAMPER CONTROL
The Rickard static pressure controller may be used to control more
than one damper, as in the case of face and bypass dampers. In this
case the two actuators are simply wired in the opposite sense so that
the one damper drives open while the other drives shut.
The controller is able to drive up to four Lindrive actuators simulta-
neously.
OTHER ACTUATORS AND CONTROLS
Should there be a need to use controls not supplied by RICKARD, it
must be noted that the Lindrive actuator requires a controller with a
3-point floating control output. It cannot accept a 0 –10 Volt DC
control signal.
Should the latter be the case, it may be necessary to fit an actuator
which is compatible with the selected controller. This actuator may
be of the push-pull type or the type which has a rotary action.
These actuators would normally be free-issued to RICKARD for fitting
to the damper in our factory.
COMMISSIONING PROCEDURE
The function of the PCD is to maintain a constant pressure in the
system regardless of airflow. This constant pressure is necessary to
allow the VAV diffusers to work correctly as they are sized and set to
deliver design volumes at a specific pressure. Two methods of com-
missioning are suggested here. The first and easier method assumes
that there is a high degree of confidence in the system, while the
second offers a more exhaustive and expensive alternative which
proves the systems thoroughly.
For either commissioning technique to be useful, it should firstly be
established that the thermostat/controllers of the VAV terminals are
set to control at a realizable temperature. If the temperature set
point requires more of the air conditioning system than the design
conditions allow, the system may never perform satisfactorily.
METHOD 1
Select the pressure control damper in the branch duct furthermost
from the supply air fan and drive it to its fully open state. Next,
establish the system design volume diversification factor and fully
open enough of the VAV terminals, in the branch duct under consid-
eration, so that the maximum simultaneous air volume is passing
through the PCD. Now select the VAV terminal requiring the highest
pressure to satisfy its design volume, carefully measure the diffuser
neck total pressure (or duct static in the case of WBD units) and
adjust the main/riser duct static pressure controller to achieve the
desired pressure at the terminal being considered. Finally, without
changing any of the criteria in the branch duct, adjust the branch
duct static pressure controller so that pressure in that branch will be
controlled at the level which has been set through the adjustment of
the main riser controller.
To set the remaining branch duct static pressures, in each case select
the VAV terminal requiring the highest pressure to satisfy its maxi-
mum design supply air volume, drive to the fully open state, carefully
measure the spigot total pressure (or duct static pressure in the case
of WBD terminals) and adjust the static pressure controller accord-
ingly.
The system is now fully operational.

METHOD 2
For each pressure control damper and associated branch duct, select
the diffuser which needs the highest spigot total pressure to enable
it to supply maximum design air volume and drive this diffuser to
fully open. Also drive all pressure control dampers to fully open.
Next, drive the other diffusers until design maximum air is leaving
the Air Handling Unit and is being distributed uniformly throughout
the conditioned space. At this stage diffuser spigot total pressures at
fully open diffusers will be on or slightly above their respective maxi-
mum air requirements. Adjust the duct static pressure controllers
until the diffusers which need the highest spigot total pressures have
sufficient pressure available. At this stage the system is fully com-
missioned, but it may be tested by monitoring duct pressures while
changing the air flows around the system. For a system operating
satisfactorily one would expect duct pressures to vary by 7 - 10% as
air flows vary from 30% to 100%.
Please note that these commissioning recommendations do not
check a system for all faults. They are intended only to set up and
test the pressure controls and, to a lesser extent, the diffusers. Gross
system faults, such as disconnected or ruptured flexible ducting, will
not be traced using these methods.
MAINTENANCE
The Rickard PCD dampers require no routine preventative mainte-
nance. No adjustment should be required once the system is com-
missioned.
Although the Rickard Lindrive actuator has a 3 year warranty, the
replacement procedure for an installed damper actuator is discussed
should it become necessary.
It is very important to note that no attempt should be made to loos-
en the motor spindle or shaft from its internal mountings. The only
way to fasten it again will be by removing the damper completely.
Never attempt to turn the spindle as this will damage the motor
gears as well as dislocate the spindle from the internal mounting.
ACTUATOR REPLACEMENT PROCEDURE
1. Measure and record the exact position of the top lock nuts
on the spindle. These are the minimum airflow position nuts
and should not be adjusted.
2. Unlock the two brass lock nuts on the spindle/shaft using
two 13mm spanners. Do not turn the spindle.
3. Disconnect the three wires, but remember to make a note of
the wire positions. Refer to section 4 for the wiring diagram.
4. Loosen and remove the three fixing screws from the casing.
5. Remove the actuator by rotating it anti-clockwise on the
spindle.
6. Fit the new actuator by screwing it onto the spindle.
7. Line up the fixing holes with the self-clinching nuts on the
casing and fasten the screws.
8. Connect the wires in there respective positions as before.
9. Place the top lock nuts in position as measured and lock
them together without turning the spindle.
WARRANTY
RICKARD AIR DIFFUSION (Pty) Ltd (RICKARD) warrants that its
Dampers, inclusive of any Rickard options and accessories (whether
factory or field installed) shall be free from defects in material or
workmanship for a period of two year from the date of shipment and
agrees to repair or replace, at its option, any parts that fail during
said two year period due to any such defects which would not have
occurred had reasonable care been taken, provided that such parts
have been inspected by RICKARD and found defective and provided
the components have been given normal and proper usage and all
parts and controls remain unaltered.
RICKARD makes no warranty of merchantability of products or of
their fitness for purpose or any other express or implied warranty
which extends beyond the limited warranty above. RICKARD’S liabil-
ity for any or all losses and damages resulting from defects shall in
no event exceed the cost of repair or replacement of parts found
defective upon examination by RICKARD. In no event shall RICKARD
be liable for incidental indirect or consequential damages or damag-
es for injury to persons or property. RICKARD shall not be responsi-
ble for freight to or from its plant in connection with the inspection,
repair or replacement of parts under the terms of this limited warran-
ty, nor for the cost of removal or installation.
Popular Control Unit manuals by other brands
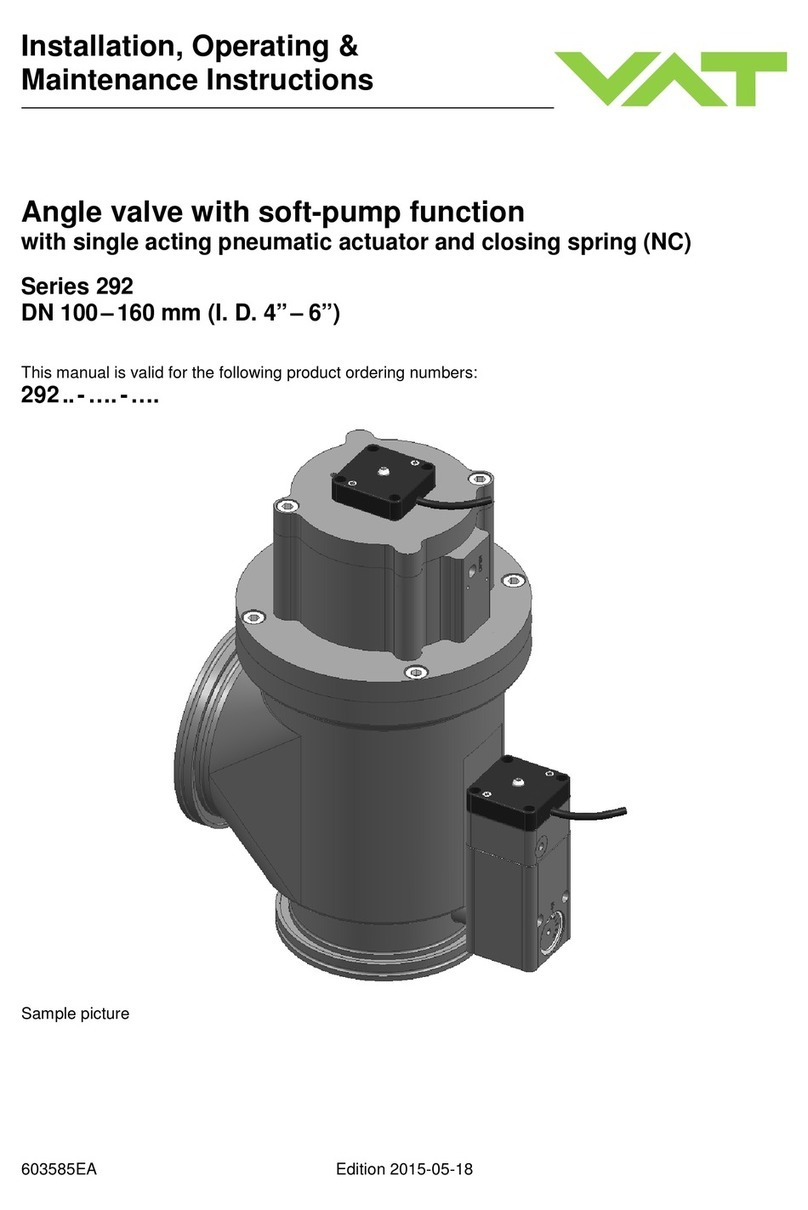
VAT
VAT 292 Series Installation, operating, & maintenance instructions
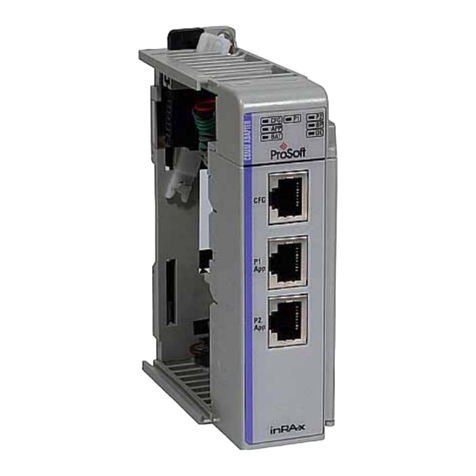
ProSoft Technology
ProSoft Technology inRAX MVI69-S3964R user manual
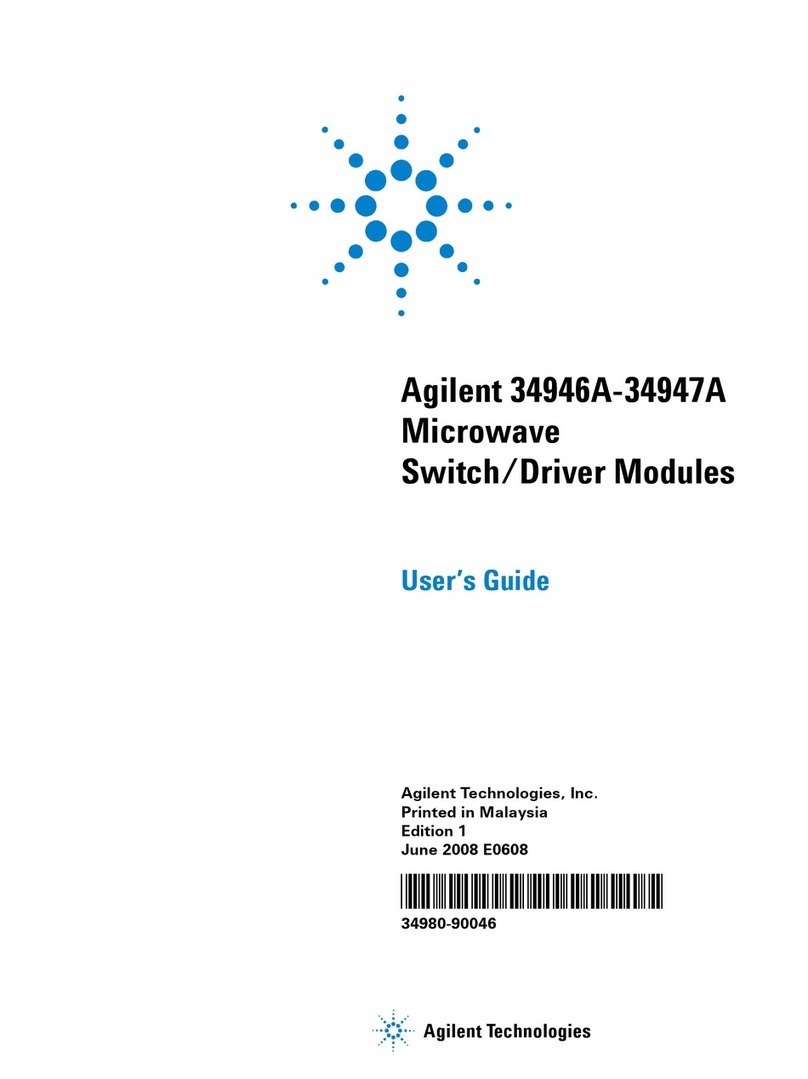
Agilent Technologies
Agilent Technologies 34946A user guide
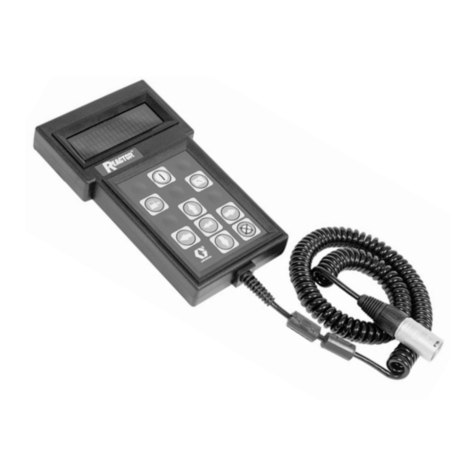
Graco
Graco 246085 Installation & operation
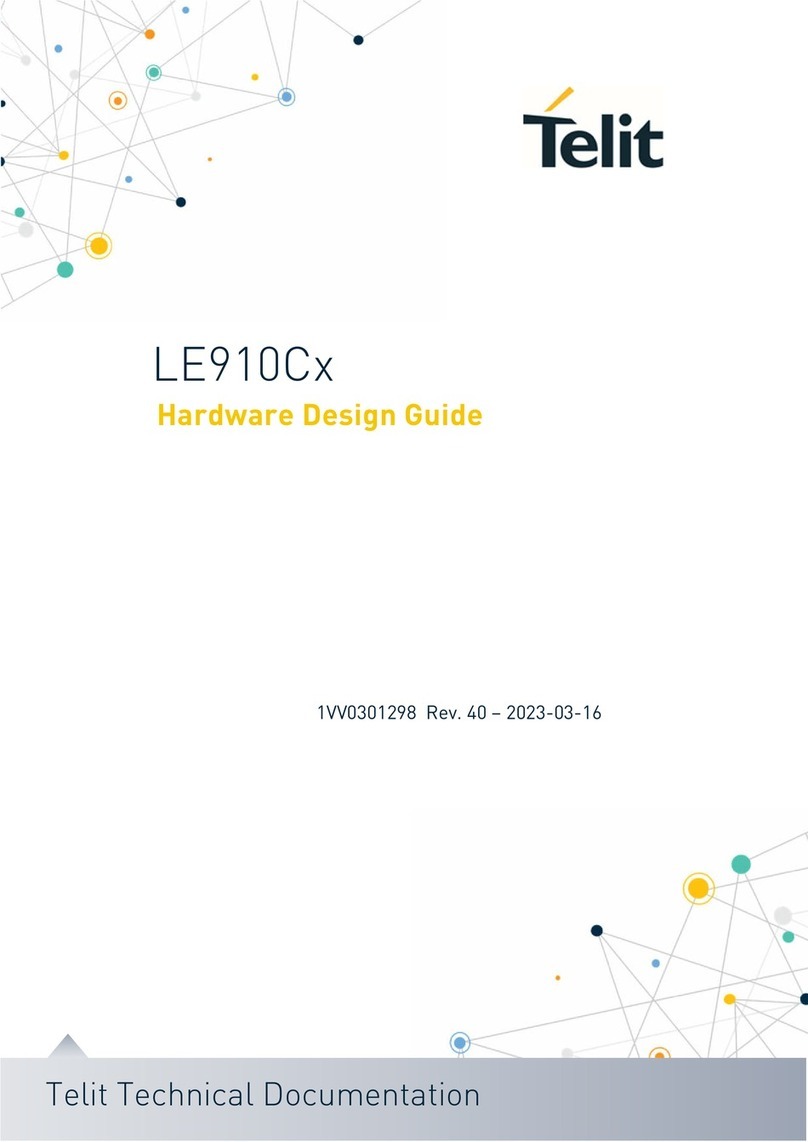
Telit Wireless Solutions
Telit Wireless Solutions LE910C1-NAD Hardware Design Guide
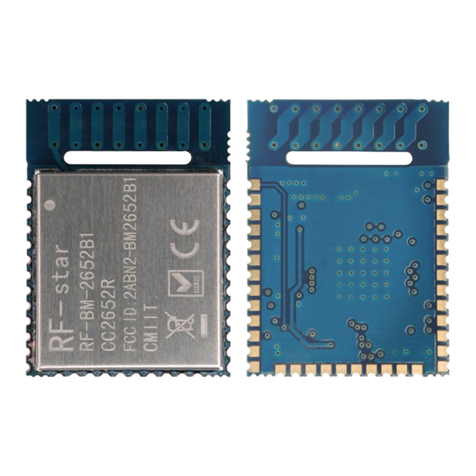
RF-Star
RF-Star RF-BM-2652B1 manual