Rietschle PICO DLT Series User manual

DLT
DLT 6
DLT 10
DLT 15
DLT 25
DLT 40
Betriebsanleitung
Verdichter
B 380
1.7.98
Werner Rietschle
GmbH + Co. KG
Postfach 1260
D-79642 Schopfheim
07622/ 392-0
Fax 07622/392300
e-mail:[email protected]
http://www.rietschle.com

E
OG1
A
D
B
FG
F
N
E
Ausführungen
Diese Betriebsanleitung gilt für folgende trockenlaufende Drehschieber-Verdichter: Typenreihe DLT 6 bis DLT 40.
Sie haben einen Nenn-Volumenstrom von 6, 10, 15, 25 und 40 m3/h bei 50 Hz. Die druckseitigen Belastungsgrenzen (bar) sind auf dem
Datenschild (N) angegeben. Die Abhängigkeit des Volumenstroms von den Überdrücken zeigt das Datenblatt D 380.
Beschreibung
Die genannte Typenreihe hat druckseitig ein Anschlußgewinde und saugseitig einen Geräuschdämpfer. Die angesaugte Luft wird durch ein
eingebautes Mikro-Feinfilter gereinigt. Der durch den Abrieb der Lamellen entstehende Kohlestaub wird ebenfalls durch einen integrierten Filter
abgeschieden.DerVerdichterbefindetsichineinerSchallhaubeausKunststoff.InnerhalbderSchallhaubebefindetsichaucheinVentilator,durch
den die Kühlung der DLT erfolgt. Die Druckluft wird bei den Baugrößen 15, 25 und 40 mit größerer Motorleistung durch ein Kühlsegment gekühlt.
Motor und Verdichter haben eine gemeinsame Welle. Das Druck-Regulierventil erlaubt die Einstellung des Druckes auf gewünschte, jedoch nach
oben begrenzte Werte.
Zubehör: Bei Bedarf Rückschlagventil (ZRK), Motorschutzschalter (ZMS) und Schlauchanschluß (ZSA).
Verwendung
Die Verdichter DLT sind für den Einsatz im gewerblichen Bereich geeignet, d.h. die Schutzeinrichtungen entsprechen EN DIN 294
Tabelle 4 für Personen ab 14 Jahren.
Die DLT eignet sich zur Erzeugung von Überdruck zwischen 0 und der auf dem Datenschild (N) angegebenen Höchstgrenze (bar). Dauerbetrieb
ist zulässig.
Die Umgebungstemperatur und die Ansaugtemperatur muß zwischen 5 und 40°C liegen. Bei Temperaturen außerhalb dieses
Bereiches bitten wir um Rücksprache.
Diese trockenlaufenden Verdichter eignen sich zum Fördern von Luft mit einer relativen Feuchte von 30 bis 90%.
Es dürfen keine gefährlichen Beimengungen (z.B. brennbare oder explosive Gase oder Dämpfe), extrem feuchte Luft, Wasser-
dampf, aggressive Gase oder Spuren von Öl, Öldunst und Fett angesaugt werden.
Die Standard-Ausführungen dürfen nicht in explosionsgefährdeten Räumen betrieben werden.
Bei Anwendungsfällen, wo ein unbeabsichtigtes Abstellen oder ein Ausfall des Verdichters zu einer Gefährdung von Personen
oder Einrichtungen führt, sind entsprechende Sicherheitsmaßnahmen anlagenseits vorzusehen.
Handhabung und Aufstellung (Bild und )
Zum Demontieren des Ausblasgitters (G), Ansauggitters (G1) und Gehäusedeckels (b) müssen für Wartungsarbeiten mindestens 30 cm Platz
vorhanden sein. Zusätzlich ist zu beachten, daß die Kühllufteintritte (E) und Kühlluftaustritte (F) mindestens 10 cm Abstand zur nächsten Wand
haben (austretende Kühlluft darf nicht wieder angesaugt werden).
Die DLT können nur in horizontaler Einbaulage fehlerfrei betrieben werden.
Bei Aufstellung höher als 1000 m über dem Meeresspiegel macht sich eine Leistungsminderung bemerkbar. In diesem Fall bitten
wir um Rücksprache.
Die Aufstellung der Verdichter auf festem Untergrund ist ohne Verankerung möglich. Bei Aufstellung auf einer Unterkonstruktion empfehlen wir
eine Befestigung über elastische Pufferelemente. Die Vibrationen dieser Drehschieber-Verdichter sind sehr gering.
Installation (Bild )
Der Verdichter darf nicht ohne das serienmäßige Regulier- und Begrenzungsventil betrieben werden, damit der zulässige
Verdichtungsenddruck (siehe Datenschild) nicht überschritten wird.
Bei Aufstellung und Betrieb ist die Unfallverhütungsvorschrift »Verdichter« VBG 16 zu beachten.
1.Druckanschluß bei (B).
Bei zu enger und/oder langer Druckleitung vermindert sich der Volumenstrom des Verdichters.
2.Die elektrischen Motordaten sind auf dem Datenschild (N) bzw. dem Motordatenschild angegeben. Die Motoren entsprechen DIN/VDE 0530
und sind in Schutzart IP 55 und Isolationsklasse F ausgeführt. Das entsprechende Anschlußschema befindet sich im Klemmenkasten des
Motors (entfällt bei Ausführung mit Stecker-Anschluß). Die Motordaten sind mit den Daten des vorhandenen Stromnetzes zu vergleichen
(Stromart, Spannung, Netzfrequenz, zulässige Stromstärke).
3.Motor über Motorschutzschalter anschließen (zur Absicherung ist ein Motorschutzschalter und zur Zugentlastung des Anschluß-Kabels ist eine
Pg-Verschraubung vorzusehen).
Wir empfehlen die Verwendung von Motorschutzschaltern, deren Abschaltung zeitverzögert erfolgt, abhängig von einem evtl. Überstrom.
Kurzzeitiger Überstrom kann beim Kaltstart des Verdichters auftreten.
Die elektrische Installation darf nur von einer Elektrofachkraft unter Einhaltung der EN 60204 vorgenommen werden. Der
Hauptschalter muß durch den Betreiber vorgesehen werden.

G
b
e
m
s
fmD
s
s
Inbetriebnahme (Bild )
1.Motor zur Drehrichtungsprüfung (Drehrichtungspfeil (O)) kurz starten.
Achtung! BeidiesemAnlaufdarfdieDruckleitungnichtangeschlossensein(beiRückwärtslauf desVerdichtersund angeschlossener
Druckleitung kann sich ein Vakuum aufbauen, das Beschädigungen an den Lamellen verursacht, die zum Bruch der Lamellen führen).
2.Druckleitung an (B) anschließen.
Ist der Verdichter durch eine Leitung von mehr als 3 m Länge mit dem Verbraucher verbunden, empfehlen wir den Einbau eines
Rückschlagventils(ZRK) zwischen Verdichter und Leitung, um nach dem Abstellen einen Rückwärtslauf zu vermeiden.
3.Die erforderlichen Druckbereiche können mit dem Druck-Regulierventil (D) entsprechend dem auf dem Drehknopf angebrachten Symbolschild
eingestellt werden.
Risiken für das Bedienungspersonal
Geräuschemission: DiehöchstenSchalldruckpegel(ungünstigsteRichtungundBelastung), gemessennachdenNennbedingungenDIN45635
Teil 13 (entsprechend 3.GSGV), sind in der Tabelle im Anhang angegeben. Wir empfehlen bei andauerndem Aufenthalt in der Umgebung des
laufenden Verdichters das Benutzen persönlicher Gehörschutzmittel, um eine Dauerschädigung des Gehörs zu vermeiden.
Wartung und Instandhaltung
Bei Wartungsmaßnahmen, bei denen Personen durch bewegte oder spannungsführende Teile gefährdet werden können, ist der
VerdichterdurchZiehen desNetzsteckersoderBetätigen desHauptschaltersvomE-Netzzu trennenundgegenWiedereinschalten
zu sichern. Wartung nicht bei betriebswarmem Verdichter durchführen. (Verletzungsgefahr durch heiße Maschinenteile).
1. Schmierung
Die DLT hat eine Dauerfettschmierung für die Lager und braucht nicht nachgeschmiert zu werden.
2. Luftfilterung (Bild und )
Bei ungenügender Wartung der Luftfilter vermindert sich die Leistung des Verdichters.
Die Filterpatronen (e) für Saugluft und (f➝Zubehör) für Blasluft sind je nach Verunreinigung durch Ausblasen von innen nach außen zu reinigen.
Trotz Reinigen der Filter wird sich deren Abscheidungsgrad zunehmend verschlechtern. Wir empfehlen daher eine halbjährliche Erneuerung der
Filter.
Filterwechsel:
Ausblasgitter (G) abschrauben. Schraubdeckel (s) und Rändelknopf (m) lösen. Filterpatrone (e) und (f) herausnehmen und reinigen bzw.
austauschen. Der Zusammenbau erfogt in umgekehrter Reihenfolge.
3. Lamellen (Bild und )
Lamellenkontrolle: DLT 6 - 25 haben 6 Kohlelamellen bzw. DLT 40 hat 7 Kohlelamellen, die sich während des Betriebs allmählich abnützen.
DLT 6, DLT 10 und DLT 15: Erste Kontrolle nach 7.000 Betriebsstunden, danach alle 1.000 Betriebsstunden.
DLT 25 und DLT 40: Erste Kontrolle nach 5.000 Betriebsstunden, danach alle 1.000 Betriebsstunden.
Ausblasgitter (G) abschrauben. Gehäusedeckel (b) vom Gehäuse abschrauben. Lamellen (d) zur Überprüfung herausnehmen. Alle Lamellen
müssen eine Mindesthöhe (X) haben:
Type X (Mindesthöhe)
DLT 6 20mm
DLT10 20mm
DLT15 24mm
DLT25 24mm
DLT40 35mm
Die Lamellen dürfen nur satzweise gewechselt werden.
Lamellenwechsel: Stellt man bei der Lamellenkontrolle fest, daß die Mindesthöhe bereits erreicht oder unterschritten ist, so ist der Lamellensatz
zu wechseln.
Gehäuse und Rotorschlitze ausblasen. Lamellen in die Rotorschlitze einlegen. Beim Einlegen ist darauf zu achten, daß die Lamellen mit der
schrägen Seite (Y) nach außen zeigen und diese Schräge in Drehrichtung (O1) mit dem Verlauf der Gehäusebohrung(Z) übereinstimmt.
Gehäusedeckel (b) und Ausblasgitter (G) anschrauben. Vor Inbetriebnahme den freien Lauf der Lamellen durch Drehbewegung des Ventilators
überprüfen, dazu Ansauggitter (G1) abschrauben.

ZY
X
O
1
b
d
/ PM6
DLT 610 15 25 40
dB(A) 50 Hz 62 63 66 67 71
60 Hz 63 65 67 70 74
kg 3 ~ 16,1 19,0 27,2 32,0 49,0
1 ~ 17,2 19,0 29,0 35,0 52,0
mm 402 422 476 507 593
mm 209 209 241 241 269
mm 208 208 246 246 272
Störungen und Abhilfe
1. Verdichter wird durch Motorschutzschalter abgeschaltet:
1.1 Netzspannung/Frequenz stimmt nicht mit den Motordaten überein.
1.2 Anschluß am Motorklemmbrett ist nicht korrekt.
1.3 Motorschutzschalter ist nicht korrekt eingestellt.
1.4 Motorschutzschalter löst zu rasch aus.
Abhilfe: Verwendung eines Motorschutzschalters mit überlastabhängiger Abschaltverzögerung, die den kurzzeitigen Überstrom beim Start
berücksichtigt (Ausführung mit Kurzschluß- und Überlastauslöser nach VDE 0660 Teil 2 bzw. IEC 947-4).
1.5 Die Filterpatrone des Ausblasfilters ist verschmutzt.
1.6 Das Regulierventil ist verschmutzt, so daß der zulässige Druck überschritten wird.
2. Blasleistung ist ungenügend:
2.1 Ansaugfilter und/oder Ausblasfilter sind verschmutzt.
2.2 Druckleitung ist ist lang oder zu eng.
2.3 Undichtigkeit am Verdichter oder im System.
2.4 Lamellen sind beschädigt.
3. Enddruck (max. Überdruck) wird nicht erreicht:
3.1 Undichtigkeit am Verdichter oder im System.
3.2 Lamellen sind beschädigt.
3.3 Antriebsleistung wurde zu klein gewählt.
4. Verdichter wird zu heiß:
4.1 Umgebungs- oder Ansaugtemperatur ist zu hoch.
4.2 Kühlluftstrom wird behindert.
4.3 Fehler wie unter 1.5 und 1.6.
5. Verdichter erzeugt abnormales Geräusch:
5.1 Das Verdichtergehäuse ist verschlissen (Rattermarken).
Abhilfe: Reparatur durch Hersteller oder Vertragswerkstatt.
5.2 Das Regulierventil “flattert”.
Abhilfe: Ventil ersetzen.
5.3 Lamellen sind beschädigt.
Anhang:
Reparaturarbeiten: Bei Reparaturarbeiten vor Ort muß der Motor von einer Elektrofachkraft vom Netz getrennt werden, so daß kein unbeabsich-
tigter Start erfolgen kann.
FürReparaturenempfehlenwir den Hersteller, dessenNiederlassungenoder Vertragsfirmen in Anspruchzunehmen,insbesondere, wenn essich
evtl. um Garantiereparaturen handelt. Die Anschrift der für Sie zuständigen Service-Stelle kann beim Hersteller erfragt werden (siehe Hersteller-
Adresse).
Nach einer Reparatur bzw. vor der Wiederinbetriebnahme sind die unter “Installation” und “Inbetriebnahme” aufgeführten Maßnahmen wie bei der
Erstinbetriebnahme durchzuführen.
Innerbetrieblicher Transport: Zum Anheben und Transportie-
ren ist die DLT 15 - DLT 40 an der Transportöse aufzuhängen.
Gewichte siehe Tabelle.
Lagerhaltung: Der DLT-Verdichter ist in trockener Umgebung
mit normaler Luftfeuchtigkeit zu lagern. Bei einer relativen
Feuchtevonüber80%empfehlenwirdieLagerungingeschlos-
sener Umhüllung mit beigelegtem Trockenmittel.
Entsorgung: Die Verschleißteile (als solche in der Ersatzteil-
liste gekennzeichnet) sind Sonderabfall und nach den landes-
üblichen Abfallgesetzen zu entsorgen.
Ersatzteilliste: E 380 ➝DLT 6 - DLT 40
Schalldruckpegel (max.)
Gewicht (max.)
Länge
Breite
Höhe
9.98

DLT
DLT 6
DLT 10
DLT 15
DLT 25
DLT 40
Operating Instructions
Compressors
BE 380
1.7.98
Werner Rietschle
GmbH + Co. KG
Postfach 1260
D-79642 Schopfheim
07622/ 392-0
Fax 07622/392300
e-mail:[email protected]
http://www.rietschle.com
Rietschle (UK) Ltd.
P.W.D.C.
Paddock Wood
Kent TN12 6UU.
01892/835237
Fax 01892/834643

E
OG1
A
D
B
FG
F
N
E
Pump Ranges
These operating instructions concern the following dry running rotary vane compressors: Models DLT 6 to DLT 40.
They have nominal capacities of 6, 10, 15, 25 and 40 m3/hr operating on 50 cycles. The pressure limits (bar) are indicated on the data plate (N).
The pumping curves showing capacity against pressure can be found in data sheet D 380.
Description
All models are complete with a pressure connection and a silencer on the inlet. All the air handled is filtered by a built-in micro-fine filter. Excess
carbon dust from the carbon blades is also filtered on the exhaust side by built-in filters. The compressor unit is encased in a rugged black plastic
sound enclosure. The cooling fan for the DLT is located inside the sound enclosure. On sizes 15, 25 and 40 with the larger motor the compressed
air is cooled by an aftercooler. Both the motor and compressor have a common shaft. Pressure can be adjusted to the required levels, however,
they are limited to a maximum point.
Optional extras (as required): Non return valve (ZRK), motor starter (ZMS) and pipe connection (ZSA).
Suitability
The units DLT are suitable for the use in the industrial field i.e. the protection equipments corresponds to EN DIN 294 table 4, for
people aged 14 and above.
The units DLT produce pressure up to the maximum limits, which are shown at the data plate (N). They may be operated continuously.
The ambient and suction temperatures must be between 5 and 40°C. For temperatures outside this range please contact your
supplier.
These dry running compressors are suitable for use with air of a relative humidy of 30 to 90%.
Dangerous mixtures (i.e. inflammable or explosive gases or vapours), extremely humid air, water vapour, aggressive gases or
traces of oil and grease must not be handled.
The standard versions may not be used in hazardous areas.
For all applications where an unplanned shut down of the compressor could possibly cause harm to persons or installations, a
corresponding safety backup system must be installed.
Handling and Setting up (pictures and )
There must be a minimum space of 30 cm in front of exhaust grid (G), suction grid (G1) and housing cover (b) for servicing. The cooling air
entries (E) and the cooling air exits (F) must have a minimum distance of 10 cm from any obstruction. The discharged cooling air must not be
re-circulated.
The DLT compressors can only be operated reliably if they are installed horizontally.
For installations that are higher than 1000 m above sea level there will be a loss in capacity. For further advice please contact your
supplier.
When the compressors are installed on a solid base, they do not need to be fixed down. If the compressors are installed on a base plate we would
recommend fitting anti-vibration mounts. This range of compressors are almost vibration free in operation.
Installation (picture )
The compressors may not be operated without the standard pressure regulating and limiting valves fitted so that the maximum
pressure is not exceeded (see data plate).
For operating and installation follow any relevant national standards that are in operation.
1.Pressure connection at (B).
Long and/or small bore pipework should be avoided as this tends to reduce the capacity of the compressor.
2.The electrical data can be found on the data plate (N) or the motor data plate. The motors correspond to DIN/VDE 0530 and have IP 55
protection and insulation class F. The connection diagram can be found in the terminal box on the motor (unless a special plug connection is
fitted). Check the electrical data of the motor for compatibility with your available supply (voltage, frequency, permissible current etc.).
3.Connect the motor via motor starter. It is advisable to use thermal overload motor starters to protect the motor and wiring. All cabling used
on starters should be secured with good quality cable clamps.
We recommend that motor starters should be used that are fitted with a time delayed trip resulting from running beyond the amperage setting.
When the unit is started cold overamperage may occur for a short time.
The electrical installation may only be made by a qualified electrician under the observance of EN 60204. The main switch must
be provided by the operator.

G
b
e
m
s
fmD
s
s
Initial Operation (picture )
1.Initially switch the compressor on and off for a few seconds to check the direction of rotation against the direction arrow (O).
Note: On this initial start the pressure pipework should not be connected. If the compressor runs backwards with the pipework
connected a pressure could build up within the housing which could result in damaged rotor blades.
2.Connect the pressure pipe at (B).
For pipework longer than 3 m we recommend using non-return valves (ZRK), to avoid reverse rotation when the units are switched
off.
3.Therequestedpressurerangescanbeadjustedbyturningthepressureregulatingvalve(D)accordingtothesymbols on the top of the regulating
valve.
Potential risks for operating personnel
Noise Emission: The worst noise levels taking into consideration direction and intensity measured according to DIN 45635 part 3 (as per
3. GSGV), are shown in the table at the back. When working permanently in the vicinity of an operating compressor, we recommend wearing
ear protection to avoid any damage to hearing.
Maintenance and Servicing
Whenmaintainingtheseunitsand having such situationswherepersonnelcouldbehurtby moving parts or byliveelectricalparts,
the compressor must be isolated by totally disconnecting the electrical supply. It is imperative that the unit cannot be re-started
during the maintenance operation. Do not maintain a compressor that is at its normal operating temperature as there is a danger from
hot parts.
1. Lubrication
The DLT compresors have bearings that are greased for life. They need not be serviced.
2. Air filtration (pictures and )
The capacity of the compressor can become reduced if the air inlet filters are not maintained correctly.
The filter cartridges (e) on the inlet and (f➝optional extras) for compressed air have to be cleaned depending on the amount of contamination.
This is achieved by blowing compressed air from the inside of the cartridge outwards. Even if the cartridges are cleaned their separating efficiency
deteriorates. We would therefore recommend exchanging the cartridges every six months.
Changing the filters:
Screw off exhaust grid (G). Remove screwed cover (s) and milled knob (m). Pull filter cartridges (e) and (f) off and clean or exchange. Re-assemble
in reverse order.
3. Blades (pictures and )
Checking blades: DLT 6 - 25 have 6 blades whilst the DLT 40 has 7 blades. The blades have a low but permanent wear factor.
DLT 6, DLT 10 and DLT 15: first check after 7,000 operating hours, thereafter every 1,000 operating hours.
DLT 25 and DLT 40: first check after 5,000 operating hours, thereafter every 1,000 operating hours.
Screw off exhaust grid (G). Screw off housing cover (b) from housing. Remove blades (d) for inspection. All blades must have a minimum
height (X):
Model X (minimum height)
DLT 6 20mm
DLT10 20mm
DLT15 24mm
DLT25 24mm
DLT40 35mm
Blades must be changed completely.
Changing blades: If the minimum height is reached, then the whole set of blades should be changed.
Before fitting new blades clean out the housing and the rotor slots with compressed air. Place the blades with the radius outwards (Y) so that the
bevel is in the direction of rotation (O1) and corresponds with the radius of the housing (Z).
Fix end cover (b) and exhaust grid (G). Before restarting the pump check free movement of the blades by turning the motor cooling fan before
refitting the cooling grid (G1).

ZY
X
O
1
b
d
/ PM6
DLT 610 15 25 40
dB(A) 50 Hz 62 63 66 67 71
60 Hz 63 65 67 70 74
kg 3 ~ 16,1 19,0 27,2 32,0 49,0
1 ~ 17,2 19,0 29,0 35,0 52,0
mm 402 422 476 507 593
mm 209 209 241 241 269
mm 208 208 246 246 272
Noise level (max.)
Weight (max.)
Length
Width
Height
Trouble Shooting:
1. Motor starter cuts out compressor:
1.1 Check that incoming voltage and frequency corresponds with the motor data plate.
1.2 Check the connections on the motor terminal block.
1.3 Incorrect setting on the motor starter.
1.4 Motor starter trips too fast.
Solution: Use a motor starter with a time delay trip (version as per IEC 947-4).
1.5 Filter cartridges on the exhaust side are contaminated.
1.6 The regulating valve is dirty causing excess pressure.
2. Insufficient pressure capacity:
2.1 Inlet and/or exhaust filters are obscured.
2.2 Pressure pipework is too long or too small.
2.3 Leak on the compressor or on the system.
2.4 Blades are damaged.
3. Compressor does not reach the required pressure:
3.1 Leaks on the compressor or on the system.
3.2 Blades are damaged.
3.3 Motor rating selected too small.
4. Compressor operates at an abnormally high temperature:
4.1 Ambient or suction temperature too high.
4.2 Cooling air flow is restricted.
4.3 Problem as per 1.5 and 1.6.
5. Unit emits abnormal noise:
5.1 The compressor cylinder is worn.
Solution: send your complete unit off for repair to the supplier or approved service agent.
5.2 The regulating valve is noisy.
Solution: replace valve.
5.3 Blades are damaged.
Appendix:
Repair on Site: For all repairs on site an electrician must disconnect the motor so that an accidental start of the unit cannot happen.
Allengineersarerecommendedtoconsulttheoriginalmanufactureroroneofthesubsidiaries,agentsorserviceagents.Theaddressofthenearest
repair workshop can be obtained from the manufacturer on application.
After a repair or before re-installation follow the instructions as shown under the headings ”Installation and Initial Operation”.
Lifting and Transport: To lift and transport the DLT 15 - DLT 40 the eye bolt on the compressor must be used.
The weight of the compressors are shown in the accompanying
table.
Storage: DLT units must be stored in dry ambient conditions
with normal humidity. We recommend for a relative humidity of
over80%thatthecompressorunitsshouldbestoredinaclosed
container with the appropriate drying agents.
Disposal: The wearing parts (as listed in the spare parts lists)
should be disposed of with due regard to health and safety
regulations.
Spare parts list: E 380 ➝DLT 6 - DLT 40
9.98

DLT
DLT 6
DLT 10
DLT 15
DLT 25
DLT 40
Compresseurs
Instruction de service
BF 380
1.7.98
Werner Rietschle
GmbH + Co. KG
Postfach 1260
D-79642 Schopfheim
07622/ 392-0
Fax 07622/392300
e-mail:[email protected]
http://www.rietschle.com
Rietschle Sarl
8 rue des Champs
F-68220 Hésingue
0389702670
Fax 0389709120

E
OG1
A
D
B
FG
F
N
E
Séries
Cette instruction de service concerne les compresseurs à palettes fonctionnant à sec suivants: DLT 6 jusqu’à DLT 40.
Leur débit nominal est respectivement de 6, 10, 15, 25, 40 m3/h, en 50 Hz. Les valeurs maximales de surpression admissibles (en bar) sont
mentionnées sur la plaque signalétique (N). Les courbes de débit en fonction du taux de surpression sont données par la fiche technique D 380.
Description
Lesappareils citésci-dessus, sont équipés d’un raccord au refoulement, ainsi que d’un silencieuxcôté aspiration. L’air aspiré est purifié au travers
d’unfiltremicroniqueintégré.Lapoussièredegraphiterésultantdel’usuredespalettesestégalementretenueparunfiltreintégré.Lecompresseur
se trouve sous un capot insonorisant en plastique. A l’intérieur de celui-ci, un ventilateur assure également le refroidissement du DLT. L’air
surpressé pour les grandeurs 15, 25 et 40 ayant un moteur plus puissant, est de plus refroidi par un serpentin.
Lemoteuretlecompresseursontmontéssurlemêmeaxe.Lavalvederéglagepermetderégulerlapressionnécessaire,jusqu’auxlimitesadmises
de l’appareil.
Accessoires: S’il y a lieu, clapet anti-retour (ZRK), disjoncteur moteur (ZMS), embout (ZSA).
Application
Ces appareils DLT ne peuvent être utilisés que dans une aire industrielle, c'est-à-dire répondant aux protections prévues
par EN DIN 294 tableau 4 pour les personnes au-delà de 14 ans.
Lasérie DLT permetdes surpressions entre 0 etla valeur maximale (en bar)indiquée sur la plaque signalétique(N). Un fonctionnement en continu
à ces valeurs est possible.
Latempératureambiante etd’aspirationdoitse situerentre5et40°C. Pourdestempératuresen dehorsdecettefourchette, veuillez
nous consulter.
Ces compresseurs fonctionnant à sec sont conçus pour véhiculer un air d’une humidité relative de 30 jusqu’à 90%.
On ne peut aspirer des additifs dangereux (par ex. vapeurs ou gaz inflammables, explosifs), de l’air extrêmement humide, de la
vapeur d’eau, des gaz agressifs, des traces d’huile ou de graisse.
Les exécutions standard ne peuvent être utilisées dans des zones à risque d'explosion.
Si lors de l’utilisation du compresseur, un arrêt non intentionnel ou une panne de celle-ci peut conduire à un danger pour les
personnes ou l’installation, il faut prendre les mesures de sécurité adéquates.
Maniement et implantation (photos et )
Pour permettre, lors de travaux d’entretien, le démontage du capot de refoulement (G), du capot d’aspiration (G1), et du couvercle de corps (b),
un espace de 30 cm au moins doit être disponible. De plus, les entrées (E) et sorties (F) d’air de refroidissement, doivent être séparées de parois
environnantes d’au moins 10 cm (l’air refoulé ne doit pas être réaspiré).
Les DLT ne peuvent fonctionner correctement qu’en position horizontale.
En cas d’installation au delà de 1000 m au dessus du niveau de la mer, une diminution sensible des performances est à signaler.
Dans ce cas, veuillez nous consulter.
L’implantation du compresseur au sol peut se faire sans ancrage particulier. La mise sur plots antivibratoires est préconisée si le compresseur
est monté sur un châssis. Les vibrations de ces compresseurs restent minimes.
Installation (photo )
Le compresseur ne doit pas être utilisé sans la valve de réglage pression montée en série, destinée à éviter un dépassement de
la valeur maximale de surpression admissible (voir plaque signalétique).
Pour l’implantation et le fonctionnement, il faut veiller à la conformité de la directive concernant la protection du travail.
1.Raccord de surpression en (B).
Une tuyauterie trop longue ou sous-dimensionnée réduit les performances du compresseur.
2.Les données électriques du moteur sont indiquées sur la plaque signalétique de la pompe, et du moteur. Elles répondent aux normes DIN/VDE
0530 et sont en IP 55, classe F. Le schéma de raccordement se trouve dans la boîte à bornes (ceci ne concerne pas les exécutions avec prise).
Les données électriques du moteur doivent être compatibles avec le réseau (type de courant, tension, fréquence, intensité).
3.Relier le moteur à un disjoncteur (nous préconisons un disjoncteur pour la protection du moteur, ainsi que le blocage du câble d’alimentation
par un presse-étoupe).
Nous recommandons un disjoncteur à coupure temporisée, pouvant supporter une éventuelle surintensité. Lors d’un démarrage à froid, une
éventuelle surintensité peut se produire momentanément.
L'installation électrique ne peut être réalisée que par un professionnel qualifié en respectant la norme EN 60204. L'interrupteur
principal doit être prévu par l'utilisateur.

G
b
e
m
s
fmD
s
s
Mise en service (photo)
1.Mettre le compresseur momentanément en service et contrôler le sens de rotation selon la flèche (0).
Attention! Lors de ce test, la tuyauterie de surpression ne doit pas être raccordée (en cas de rotation en sens inverse du compresseur
etderaccordementdelatuyauterie de refoulement, un vide peutsecréer,susceptibled’endommagerlespalettes,voirede les casser).
2.Raccord de surpression en (B).
Dans le cas où le compresseur est disposé à plus de 3 m de son point d’utilisation, nous préconisons l’emploi d’un clapet anti-
retour (ZRK), qui évitera un fonctionnement en sens inverse lors de l’arrêt.
3.Le taux de surpression est obtenu en tournant la valve de réglage (D) dans le sens des flèches.
Risques pour le personnel utilisateur
Emission sonore: le niveau sonore le plus élevé (mesuré sur une application sévère et du côté le plus bruyant) correspond à la directive
allemande 3 GSGV, mesuré selon les indications DIN 45635.
Nous recommandons, en cas de séjour prolongé à proximité du compresseur, de protéger l’oreille, pour éviter une détérioration de l’ouïe.
Entretien et maintenance
En cas d’intervention pouvant constituer un risque humain dû à des éléments en mouvement ou sous tension, il faut débrancher
la prise de courant, ou couper le commutateur principal, et garantir contre un réembranchement ou un réarmement. Ne pas
effectuer de maintenance sur un compresseur à température de fonctionnement (risque de blessure par des éléments chauds du
compresseur).
1. Graissage
Les roulements de la série DLT sont graissés à vie. Un regraissage n’est pas nécessaire.
2. Filtres à air (photos et )
Un entretien insuffisant des filtres à air diminue les performances du compresseur.
Les cartouches du filtre d’aspiration (e) et de refoulement (f ➝accessoires) sont à nettoyer plus ou moins souvent en fonction de leur
encrassement, par soufflage de l’intérieur vers l’extérieur. Mais en dépit d’un nettoyage régulier, leur degré de filtation se détériore. C’est pourquoi
nous recommandons de les changer tous les 6 mois.
Changement de filtre:
Dévisser le capot de refoulement (G), ainsi que la molette (s) et la bague (m). Sortir les cartouches filtrantes (e) et (f) pour les nettoyer ou les
changer. Le remontage se fait en sens inverse.
3. Palettes (photos et )
Contrôle des palettes: les DLT 6 à 25 ont 6 palettes en graphite, et 7 palettes pour la grandeur 40. Ces palettes subissent une usure lors du
fonctionnement.
DLT 6, DLT 10 et DLT 15: premier contrôle après 7000 h de service, puis toutes les 1000 h.
DLT 25 et DLT 40: premier contrôle après 5000 h de service, puis toutes les 1000 h.
Dévisser le capot de refoulement (G). Enlever le couvercle de corps (b) du corps. Sortir les palettes (d), afin des les vérifier. Elles doivent toutes
avoir une hauteur (X) minimum de:
Type X (hauteur mini)
DLT 6 20mm
DLT10 20mm
DLT15 24mm
DLT25 24mm
DLT40 35mm
Les palettes ne doivent être changées que par jeu complet.
Changement des palettes : si l’on constate lors du contrôle que la hauteur minimum est atteinte ou dépassée, il faut remplacer le jeu de palettes.
Nettoyer par soufflage le corps et les fentes du rotor. Disposer les palettes dans les fentes du rotor. Ceci, en veillant que le chanfrein (Y), soit situé
à l’arrière en se mettant dans le sens de rotation (O1) et épouse le contour intérieur du corps (Z).
Revisser le couvercle (b) et le capot de refoulement (G). Avant la mise en service, vérifier le libre mouvement des palettes en actionnant le
ventilateur, après avoir dévissé le capot d’aspiration (G1).

ZY
X
O
1
b
d
/ PM6
DLT 610 15 25 40
dB(A) 50 Hz 62 63 66 67 71
60 Hz 63 65 67 70 74
kg 3 ~ 16,1 19,0 27,2 32,0 49,0
1 ~ 17,2 19,0 29,0 35,0 52,0
mm 402 422 476 507 593
mm 209 209 241 241 269
mm 208 208 246 246 272
Niveau sonore (max.)
Poids (max.)
Longueur
Largeur
Hauteur
Incidents et solutions
1. Arrêt du compresseur par le disjoncteur moteur:
1.1 Tension ou fréquence du réseau non conforme aux données du moteur.
1.2 Raccordement mal effectué sur le bornier.
1.3 Disjoncteur moteur mal réglé.
1.4 Le disjoncteur déclenche trop rapidement.
Solution: utilisation d’un disjoncteur à coupure temporisée, qui tiendra compte d’une éventuelle surintensité au démarrage (exécution
VDE 0660 Partie 2 ou IEC 947-4).
1.5 Les cartouches-filtres au refoulement sont saturées
1.6 La valve de réglage est encrassée, de sorte que la valeur limite de surpression est dépassée.
2. Surpression insuffisante:
2.1 Filtre d’aspiration et/ou de refoulement saturés.
2.2 Tuyauterie trop longue et/ou sous-dimensionnée.
2.3 Problème d’étanchéité du système ou du compresseur.
2.4 Les palettes sont endommagées.
3. Pression limite (surpression maximale) non atteinte:
3.1 Problème d’étanchéité du système ou du compresseur.
3.2 Les palettes sont endommagées.
3.3 Moteur sous-dimensionné.
4. Le compresseur chauffe trop:
4.1 Température ambiante ou d’aspiration trop élevée.
4.2 Mauvaise circulation de l’air de refroidissement.
4.3 Problème identique à 1.5 et 1.6.
5. Bruit anormal sur le compresseur:
5.1 Le corps du compresseur est usé (facettes).
Solution: reprise du corps du compresseur par le constructeur ou un réparateur.
5.2 La valve de réglage vibre.
Solution: remplacer la valve.
5.3 Les palettes sont endommagées.
Appendice:
Réparations: Pour des travaux effectués sur place, le moteur doit être débranché du réseau par un électricien agréé, de sorte qu’aucun
redémarrage non intentionnel ne puisse survenir. Pour les réparations et en particulier s’il s’agit de garanties, nous recommandons de vous
adresser au constructeur, ou à des réparateurs agréés par lui. Les adresses de ces sociétés peuvent être obtenues sur demande. Après une
réparation, lors de la remise en fonctionnement, les points cités sous ‘„installation“ et „mise en service“ doivent être observés.
Transport interne: Pour la manutention des DLT 15 - DLT40,
il faut se servir des anneaux de levage.
Pour les poids, voir tableau.
Conditions d’entreposage: Le DLT doit être stocké dans une
atmosphère avec une humidité normale. Si celle-ci dépasse
80 %, nous préconisons un stockage sous emballage fermé
et avec un siccatif.
Recyclage: les pièces d’usure (mentionnées sur l’éclaté)
constituent des éléments à éliminer suivant les règles en
vigueur dans chaque pays.
Eclaté: E 380 ➝DLT 6 - DLT 40
9.98

DLT
DLT 6
DLT 10
DLT 15
DLT 25
DLT 40
Istruzioni di servizio
Compressori
BI 380
1.7.98
Werner Rietschle
GmbH + Co. KG
Postfach 1260
D-79642 Schopfheim
07622/ 392-0
Fax 07622/392300
e-mail:[email protected]
http://www.rietschle.com
Rietschle ItaliaS.p.A.
Via Brodolini, 17
I-20032 Cormano(Milano)
02/ 614512.1
Fax 02/ 66503399
e-mail:[email protected]
http://www.rietschle.it

E
OG1
A
D
B
FG
F
N
E
Esecuzioni
Queste istruzioni di servizio sono relative a compressori a palette funzionanti a secco modelli: DLT 6 - DLT 40.
Portatanominale:6,10,15,25e 40 m3/h.Ivalorilimite(inbar)sullatopressionesonoriportatinella targhetta. IlfogliodatiD380mostralarelazione
tra portata e sovrapressioni.
Descrizione
Questa serie dispone di un attacco sul lato pressione e di un silenziatore sull’aspirazione. L’aria aspirata viene pulita da un filtro microfine
incorporato. La polvere carboniosa prodotta dallo strisciamento delle palette viene fermata da un apposito filtro integrato. Il compressore è
alloggiato all’interno di una scatola insonorizzante in plastica dentro la quale si trova anche un potente ventilatore che provvede al raffreddamento
del DLT. L’aria compressa viene raffreddata nelle grandezze 15, 25 e 40 mediante un apposito radiatore. Motore e compressore sono montati
sullo stesso albero. La valvola di regolazione della pressione consente una regolazione della compressione fino ai valori limite consentiti.
Accessori: Sono fornibili a richiesta:, valvola di non ritorno (ZRK) salvamotore (ZMS) e attacco portagomma (ZSA).
Impiego
Le macchine DLT sono adatte per utilizzo in campo industriale, per cui i dispositivi di protezione sono conformi alle normative EN
DIN 294 tabella 4, per persone dai 14 anni in su.
Il DLT è adatto per produrre sovrappressioni fra 0 ed il valore limite (bar) riportato sulla targhetta (N). E’ ammesso il servizio continuo.
La temperatura ambiente e la temperatura d’aspirazione devono essere comprese fra 5 e 40°C. In caso di temperature al di fuori
di questo campo, vi preghiamo di interpellarci.
Questi compressori a secco sono adatti per trasportare aria con umidità relativa dal 30 al 90%.
Non possono essere aspirate sostanze pericolose (ad es. gas combustibili o esplosivi oppure vapori) aria estremamente umida,
vapore acqueo, gas aggressivi, tracce d’olio o vapori di olio e grasso.
Le esecuzioni standard non possono funzionare in ambienti con pericolo di esplosione.
Nei casi di impiego in cui un arresto imprevisto o un guasto del compressore possano causare danni a persone o cose, devono
essere previste delle misure di sicurezza nell’impianto.
Sistemazione e ubicazione (Fig. e )
Per smontare la griglia (G) di protezione al lato scarico, la griglia di protezione lato aspirazione (G1) ed il coperchio (b) devono esserci almeno
30 cm di spazio per consentire la manutenzione. Fare inoltre attenzione che l’ingresso dell’aria di raffreddamento (E) e l’uscita (F) distino almeno
10 cm dalle pareti più vicine (l’aria di raffreddamento già riscaldata non deve essere riaspirata).
I DLT possono funzionare perfettamente soltanto in posizione orizzontale.
Per installazione ad altitudine oltre i 1000 m sopra il livello del mare si nota una diminuzione della prestazione. In questo caso Vi
preghiamo di interpellarci.
La sistemazione a pavimento dei compressori è possibile anche senza ancoraggio. Per fissaggio ad una sovrastruttura raccomandiamo l’impiego
di gommini antivibranti. Le vibrazioni di questi compressori a palette sono comunque molto basse.
Installazione (Fig. )
Ilcompressorenonpuòfunzionaresenzalavalvola di regolazione e limitazione fornita di serie,pernonsuperarelasovrapressione
massima ammissibile (Vedere targhetta dati).
Durante l’installazione ed il funzionamento raccomandiamo di osservare le norme antinfortunistiche.
1.Attacco della pressione al punto (B).
Le prestazioni dei compressori diminuiscono se le tubazioni sono troppo strette o troppo lunghe.
2.I dati elettrici del motore sono riportati sia sulla targhetta (N).che sulla targhetta propria del motore. I motori sono a norme DIN/VDE 0530,
protezione IP 55, classe di isolamento F. Lo schema di collegamento relativo è situato nella scatola della morsettiera del motore (ciò non è
previsto nell’esecuzione con attacco a spina). Confrontare i dati motore con la rete (corrente, tensione, frequenza di rete e massima corrente
ammissibile).
3.Collegare il motore tramite salvamotore (prevedere per sicurezza un salvamotore ed un bocchettone Pg per l’attacco del cavo).
Raccomandiamo l’impiego di salvamotori con sganciamento ritardato a seconda dell’eventuale sovracorrente. Una breve sovracorrente può
infatti verificarsi all’avviamento a freddo del compressore.
L’allacciamento elettrico deve essere eseguito soltanto da un elettricista specializzato secondo le normeEN 60204. L’interruttore
principale deve essere previsto dall’installatore.

G
b
e
m
s
fmD
s
s
Messa in servizio (Fig. )
1.Avviare per un attimo il motore per verificare il senso di rotazione (vedere freccia senso rotazione).
Attenzione! Durante l’avviamento non deve essere collegata la tubazione della pressione (in caso di inversione di marcia con
tubazione collegata si può formare una depressione che può danneggiare le palette fino alla rottura).
2.Collegare la tubazione della pressione al punto (B).
Se il compressore è collegato all’utenza con tubazioni più lunghe di 3 m raccomandiamo di montare fra compressore e tubazione
una valvola di non ritorno (ZRK) per evitare un’inversione di rotazione durante la fase di arresto.
3.I campi di sovrapressione sono regolabili tramite la valvola di regolazione della pressione (D) secondo i simboli riportati sulla manopola stessa.
Rischi per il personale
Emissione di rumori: I valori massimi di pressione acustica (direzione, carico sbagliato) corrispondenti a 3.GSGV misurati in base a DIN 45635
parte 13, sono riportati nella tabella in appendice. Raccomandiamo in caso di permanenza prolungata in sala macchine, di utilizzare delle
protezioni individuali per le orecchie onde evitare danni irreversibili all’udito.
Cura e manutenzione
Prestare attenzione affinché qualunque operazione di manutenzione sul compressore venga effettuata esclusivamente in assenza
di tensione elettrica, disinserendo la spina o azionando l’interruttore principale (pericolo di ustioni per contatto con parti calde
della macchina).
1. Lubrificazione
Nei DLT i cuscinetti sono ingrassati permanentemente e non necessitano quindi di manutenzione periodica.
2. Filtraggio aria (Fig. e )
Una manutenzione insufficiente del filtro aria diminuisce la prestazione del compressore.
La cartucce filtranti (e) per l’aria aspirata e per l’aria soffiata (f➝accessori) vanno pulite con un getto d’aria soffiando dall’interno verso l’esterno.
Nonostante la pulizia del filtro, il grado di efficienza diminuisce progressivamente. Raccomandiamo quindi di sostituire i filtri ogni 6 mesi.
Sostituzione filtro: togliere la griglia (G), svitando i pomelli (m), il tappo (s) quindi rimuovere le cartucce filtranti (e) e (f) procedere a pulizia o
sostituzione. Rimontare seguendo il procedimento inverso.
3. Palette (Fig. e )
Controllo palette: I DLT 6-25 hanno 6 palette in grafite, mentre il DLT 40 ha 7 palette in grafite che durante il funzionamento si consumano
gradualmente.
DLT 6, DLT 10 e DLT 15: Il primo controllo va effettuato dopo 7000 ore di esercizio, successivamente ogni 1000 ore.
DLT 25 e DLT 40: Il primo controllo va effettuato dopo 5000 ore di esercizio, successivamente ogni 1000 ore.
Togliere la griglia (G) e il coperchio (b) del compressore. Estrarre le palette (d) per effettuare il controllo. Tutte le palette devono avere un’altezza
minima (X):
Tipo X (Altezza minima)
DLT 6 20mm
DLT10 20mm
DLT15 24mm
DLT25 24mm
DLT40 35mm
La serie di palette va sostituita interamente.
Sostituzionedellepalette:Se alcontrollodellepalettesirilevailraggiungimentoolariduzione dell’altezzaminimaandràsostituitalaseriecompleta
di palette.
Soffiare con un getto d’aria sulla carcassa e sulle cave del rotore. Sistemare le palette nelle cave del rotore facendo attenzione che la
smussatura (y) sia rivolta verso l’esterno e che coincida con la direzione di marcia (O1) e l’alesaggio della carcassa (Z). Rimontare il coperchio (b)
e la griglia (G). Prima della messa in servizio controllare la corsa delle palette facendo ruotare il ventilatore, previa rimozione della griglia di
aspirazione (G1).

ZY
X
O
1
b
d
/ PM6
DLT 610 15 25 40
dB(A) 50 Hz 62 63 66 67 71
60 Hz 63 65 67 70 74
kg 3 ~ 16,1 19,0 27,2 32,0 49,0
1 ~ 17,2 19,0 29,0 35,0 52,0
mm 402 422 476 507 593
mm 209 209 241 241 269
mm 208 208 246 246 272
Rumorosità (max.)
Peso (max.)
Lunghezza
Larghezza
Altezza
Guasti e rimedi
1. Compressore disinserito dal salvamotore:
1.1 Tensione di rete e frequenza non concordano con i dati motore.
1.2 Collegamento alla morsettiera del motore non corretto.
1.3 Salvamotore non regolato correttamente .
1.4 Sganciamento anticipato del salvamotore.
Rimedio: Utilizzo di un salvamotore con sganciamento ritardato in dipendenza dal sovraccarico e che tenga conto della sovracorrente allo
spunto (esecuzione con interruttore di sovraccarico e di cortocircuito secondo VDE 0660, PARTE 2 e IEC 947-4).
1.5 Cartuccia del filtro dell’aria compressa ostruita dallo sporco.
1.6 La valvola di regolazione sporca causa il superamento della sovrapressione massima ammissibile.
2. Soffieria insufficiente:
2.1 Filtro sull’aspirazione e/o allo scarico ostruiti da sporcizia.
2.2 Tubazione in compressione troppo lunga o troppo stretta.
2.3 Trafilamento o perdita al compressore o nel sistema.
2.4 Palette rovinate.
3. Pressione finale (sovrapressione max) non raggiunta:
3.1 Trafilamento al compressore o nel sistema.
3.2 Palette rovinate.
3.3 Potenza di azionamento insufficiente.
4. Il compressore si surriscalda:
4.1 Temperatura ambiente o d’aspirazione troppo elevata.
4.2 Il passaggio dell’aria di raffreddamento è ostruito.
4.3 Errore come al punto 1.5 e 1.6.
5. Il compressore produce un rumore anomalo:
5.1 La carcassa del compressore è usurata (rigatura).
Rimedio: Riparazione a cura della casa costruttrice o di una officina autorizzata.
5.2 La valvola di regolazione ”vibra”.
Rimedio: Sostituire la valvola.
5.3 Palette rovinate.
Appendice:
Riparazioni: Per riparazioni da effettuarsi presso la clientela deve essere disinserito il motore dalla rete da parte di un elettricista specializzato
evitando così un avviamento imprevisto. Raccomandiamo di rivolgervi alla casa costruttrice, alle sue filiali o rappresentanti in particolare per
riparazioni in garanzia. Potete richiedere gli indirizzi dei centri di assistenza alla casa costruttrice (vedere indirizzo casa costruttrice). Dopo una
riparazione e prima della nuova messa in servizio si devono seguire le indicazioni riportate alle voci ”Installazione” e ”Messa in servizio” come
avviene per la prima messa in servizio.
Trasporto interno. Per sollevamento e trasporto agganciare il
DLT 15 - DLT 40 all’apposito golfare.
Vedere tabella pesi.
Immagazzinaggio: Il compressore DLT deve essere immagaz-
zinato in ambiente asciutto e con tasso di umidità normale. In
casodiumiditàrelativaoltre l’80% raccomandiamolostoccaggio
in imballo chiuso e con sostanze essiccanti.
Smaltimento: Le parti usurabili (così definite nella lista parti di
ricambio) sono rifiuti speciali e devono essere smaltite in base
alle leggi vigenti sui rifiuti.
Lista parti di ricambio: E 380 ➝DLT 6 - DLT 40
10.98

DLT
DLT 6
DLT 10
DLT 15
DLT 25
DLT 40
Kompressor
Driftsvejledning
BD 380
1.7.98
Werner Rietschle
GmbH + Co. KG
Postfach 1260
D-79642 Schopfheim
07622/ 392-0
Fax 07622/392300
e-mail:[email protected]
http://www.rietschle.com
Rietschle A/S
Tåstruphøj 11
Postboks 185
DK-4300 Holbæk
59 / 44 4050
Fax 59/ 444006
e-mail:[email protected]
http://www.rietschle.dk

E
OG1
A
D
B
FG
F
N
E
Typer
Denne driftsvejledning omfatter tørtløbende lamelkompressorer type DLT 6 til DLT 40.
Kapaciten ved fri indsugning er 6, 10, 15, 25 og 40 m3/h ved 50Hz. Det maksimale overtryk (bar) er angivet på typeskilt. Ydelse i afhængighed
af kompressionstryk er vist i datablad D 380.
Beskrivelse
De nævnte typer har gevindtilslutning på tryksiden og en lyddæmper på sugesiden. Den indsugede luft filtreres gennem et mikrofinfilter.
Kompressorenhedener indbygget i en lyddæmpende kappe i kunststof. Under kappen er også indbygget køleluftsventilator. Motor ogkompressor
er monteret på samme aksel. Størrelserne 15, 25 og 40 med største motor har indbygget trykluftefterkøler.
Tryk kan indstilles på trykreguleringsventil, der dog kun kan justeres til kompressors maksimale tilladelige tryk.
Muligt tilbehør: Tilbageslagsventil ZRK, motorværn ZMS og slangestuds ZSA.
Anvendelse
Maskinerne er beregnet for anvendelse i erhvervsmæssigt øjemed, hvilket betyder at sikkerhedsbestemmelser efter EN DIN 294
tabel 4 for personer over 14 år er gældende.
DLT anvendes til overtryk mellem 0 og det på typeskilt (N) tilladelige tryk (bar). Kompressor kan arbejde kontinuerligt.
Omgivelsestemperaturen må være mellem 5 og 40°C, ved højere temperaturer bedes De kontakte os.
De tørtløbende kompressorer kan befordre luft med en relativ fugtighed mellem 30 og 90%.
Dermåikke befordres luftmedsporaf farligestoffer(brændbareeller eksplosivegasserogdampe), ekstrem fugtigluft,vanddamp,
aggresive dampe eller spor af olie, oliedampe og fedt.
Standardudførelsen bør ikke anvendes i eksplosionsfarlige rum.
Hvisuheldiganvendelsekanmedføredenmindstefareforpersonskade,mådertagesdenødvendigesikkerhedsmæssigehensyn.
Håndtering og opstilling (billede og )
Ved placering af kompressoren skal der være plads nok til, at dækslerne (G) og (G1) er tilgængelige af hensyn til kontrol og udskiftning af lameller
(30 cm). Der skal være 10 cm afstand til vægge, således at den kolde køleluft (E) ikke blandes med den varme afgangsluft (F).
DLT kompressorer skal monteres vandret.
Ved opstilling over 1000 m over havoverflade, reduceres kompressors ydelse. De er velkommen til at kontakte os.
Ved opstilling på fast underlag er det ikke nødvendigt at fastgøre kompressoren. Indgår pumpe som konstruktionselement, anbefaler vi at
kompressor monteres på svingningsdæmpere, selv om den kun foråsager små vibrationer.
Installation (billede )
Kompressor må ikke bruges uden den påbyggede sikkerheds- eller overtryksventil, da tryk angivet på typeskilt (N) ikke må
overskrides.
Ved installation skal de lokale myndigheders foreskrifter overholdes.
1.Trykledning tilsluttes ved (B).
Lange eller tynde trykledninger nedsætter kompressorens ydelse.
2.Motordata er angivet på typeskilt (N) eller typeskilt på motor. Motor er bygget efter DIN/VDE 0530, IP 55 isolation F. For motorer uden
fabriksmonteret kabel er der koblingsdiagram indlagt i klemmekasse.
3.Forsyn motoren med motorværn, og installer vakuumpumpen i henhold til stærkstrømsreglementet. Vi anbefaler motorværn med tids-
forsinkelse, da pumpe i startfase kort kan være overbelastet.Anvend PG forskruning ved kabeltilslutning.
Elinstallation må kun udføres af autoriseret elinstallatør efter stærkstrømsbekendtgørelsen afsnit 204-1 (DS-EN 60204). Det er
slutbrugers ansvar at sørge for installation af hovedafbryder.

G
b
e
m
s
fmD
s
s
Idrifttagelse (billede )
1.Kontroller, om omdrejningsretningen er korrekt (se pil (O) på ventilatordæksel).
Advarsel: kompressor må ikke afprøves med afspærret trykside, da der kan ske lamelbrud ved forkert omdrejningsretning, når der
er modtryk.
2.Trykledning tilsluttes ved (B).
Ved Trykledning over 3 m, skal der monteres tilbageslagsventil ZRK, for at forhindre at kompressor ved stop løber baglæns, da
dette kan give lamelbrud.
3.De ønskede trykområder kan indstilles ved hjælp af trykreguleringsventilen (D).
Risiko for betjeningspersonale
Støjgener: Det største støjniveau (værste retning og belastning) målt efter DIN 45635 del 13 (svarende til 3.GSGV) er angivet i appendiks.
Vi anbefaler brug af høreværn, såfremt man konstant skal arbejde i nærheden af pumpen for at undgå høreskade.
Vedligehold og reparation
Der må ikke foretages servicearbejde mens kompressor er under spænding!
Vent med at udføre service til kompressor er kold.
1. Smøring
Alle DLT typer har livstidssmurte lejer.
2. Luftfiltrering (billede og )
Snavsede filtre nedsætter pumpes ydelse!
Filterpatron(e) for indsugningsluft og(f➝tilbehør)fortrykluft kan renses med trykluft ved udblæsning indefra. Selv om filtrene renses formindskes
filterkapaciteten, og vi anbefaler derfor at filtrene udskiftes hvert halve år.
Skift af filtre:
Gitter (G) fjernes og prop (s) med evt. vakuumreguleringsventilsventil skrues af. Filterpatron (e) og (f) kan nu renses eller udskiftes. Montage sker
i omvendt rækkefølge.
3. Lameller (billedeog )
Lamellerne (d) slides og skal derfor kontrolleres. DLT 6-25 har 6 lameller og DLT 40 har 7 lameller. Første kontrol skal for størrelserne.
DLT 6-15 ske efter 7000 driftstimer og ved størrelse DLT 25-40 efter 5000 driftstimer. Lameller kontrolleres derefter for hver 1000 driftstimer.
Demonter gitter (G). Demonter dæksel (b) og tag lameller (d) ud for kontrol. Lameller skal have en minimumshøjde (X) på:
Type X (minimumshøjde)
DLT 6 20mm
DLT10 20mm
DLT15 24mm
DLT25 24mm
DLT40 35mm
Lameller må kun udskiftes som sæt!
Skift af lameller: Er lamelmål under minimumsgrænsen skal disse udskiftes.
Rens cylinder og rotorslidse med trykluft. Sæt lameller i rotorslidse således at den skrå flade (Y) vender udad og træder med hele fladen mod
cylindervæggen (Z).
Monter husdæksel (b) og gitter (G).
Førstartkontrolleres,omallelamellerkanbevægesigfritirotorslidserne,hvilketskerved,atgitter (G1)fjernesogmotordrejesviaventilatorvingen.

ZY
X
O
1
b
d
/ PM6
DLT 610 15 25 40
dB(A) 50 Hz 62 63 66 67 71
60 Hz 63 65 67 70 74
kg 3 ~ 16,1 19,0 27,2 32,0 49,0
1 ~ 17,2 19,0 29,0 35,0 52,0
mm 402 422 476 507 593
mm 209 209 241 241 269
mm 208 208 246 246 272
Støjniveau (max.)
Vægt (max.)
Længde
Bredde
Højde
Fejl og deres afhjælpning
1. Kompressor stopper fordi motorværn slår fra:
1.1 Forsyningsnettets data og motordata passer ikke.
1.2 Motor er ikke korrekt forbundet.
1.3 Motorværn er ikke korrekt indstillet.
1.4 Motorværn kobler for hurtigt ud.
Afhjælpning: anvend motorværn med tidsforsinket udkobling efter VDE 0660 del 2 hhv IEC 947-4.
1.5 Filterpatron (f) er snavset.
1.6 Reguleringsventil er stoppet og det tilladelige tryk overskrides.
2. Kapacitet er for lille:
2.1 Indsugningsfilter og/eller udstødningsfilter er snavset.
2.2 Trykledning er for lang eller for tynd.
2.3 System eller kompressor er utæt.
2.4 Lameller er beskadiget.
3. Sluttryk (max overtryk) opnås ikke:
3.1 Utæthed i system eller ved kompressor.
3.2 Lameller er beskadiget.
3.3 Motor er valgt for lille.
4. Kompressor bliver for varm:
4.1 Omgivelsestemperatur eller den indsugede luft er for varm.
4.2 Køleluftsstrøm bliver blokeret.
4.3 Fejl som under 1.5 og 1.6.
5. Kompressor støjer unormalt:
5.1 Pumpehus er slidt (bølger i cylinderhus).
Afhjælpning:lad pumpe hovedreparere hos os eller hos autoriseret reparatør.
5.2 Reguleringsventil „hopper“
Afhjælpning: udskift ventil
5.3 Lameller er beskadiget.
Appendiks:
Servicearbejde: Ved reparationer på opstillingsstedet skal motor frakobles forsyningsnet i henhold til stærkstrømsreglementet for at undgå
utilsigtet start.
Ved reparationer anbefales det at arbejde udføres af datterselskaber, agenter eller kontraktværksteder, især ved
garantireparationer.Adresser på disse opgives af fabrikant.
Efter udført reparation iagttages forholdsregler som nævnt under „installation“ og „drift“.
Flytning af maskine: Ved løft DLT 15 - DLT 40 anvendes det
monterede løfteøje.
Vægt fremgår af nedenstående tabel.
Lagring: DLT kompressoren oplagres i tør omgivelse med
normal luftfugtighed. Ved en relativ fugtighed på over 80%
anbefales forseglet indpakning med et fugtabsorberende
middel.
Skrotning: Sliddele er specialaffald (se reservedelsliste) og
skal bortskaffes efter gældende nationale regler.
Reservedelsliste: E 380 ➝DLT 6 - DLT 40
9.98
This manual suits for next models
5
Table of contents
Languages:
Other Rietschle Air Compressor manuals
Popular Air Compressor manuals by other brands
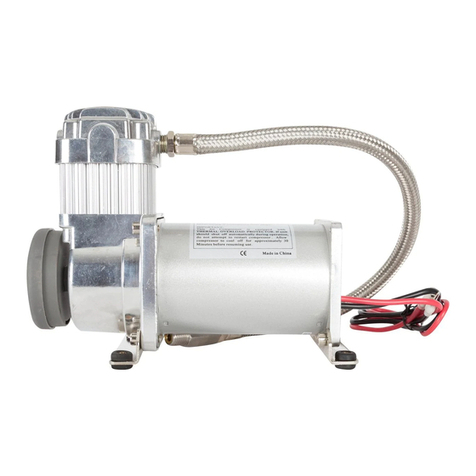
VIAIR
VIAIR 325C user manual

Klutch
Klutch 1230080 owner's manual
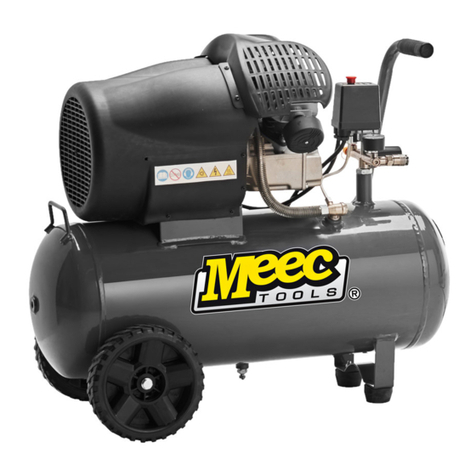
Meec tools
Meec tools 007341 operating instructions
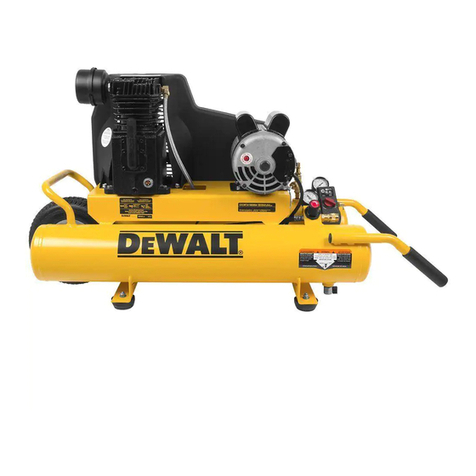
DeWalt
DeWalt Contractor's Electric Wheeled Portable Air Compressor... instruction manual
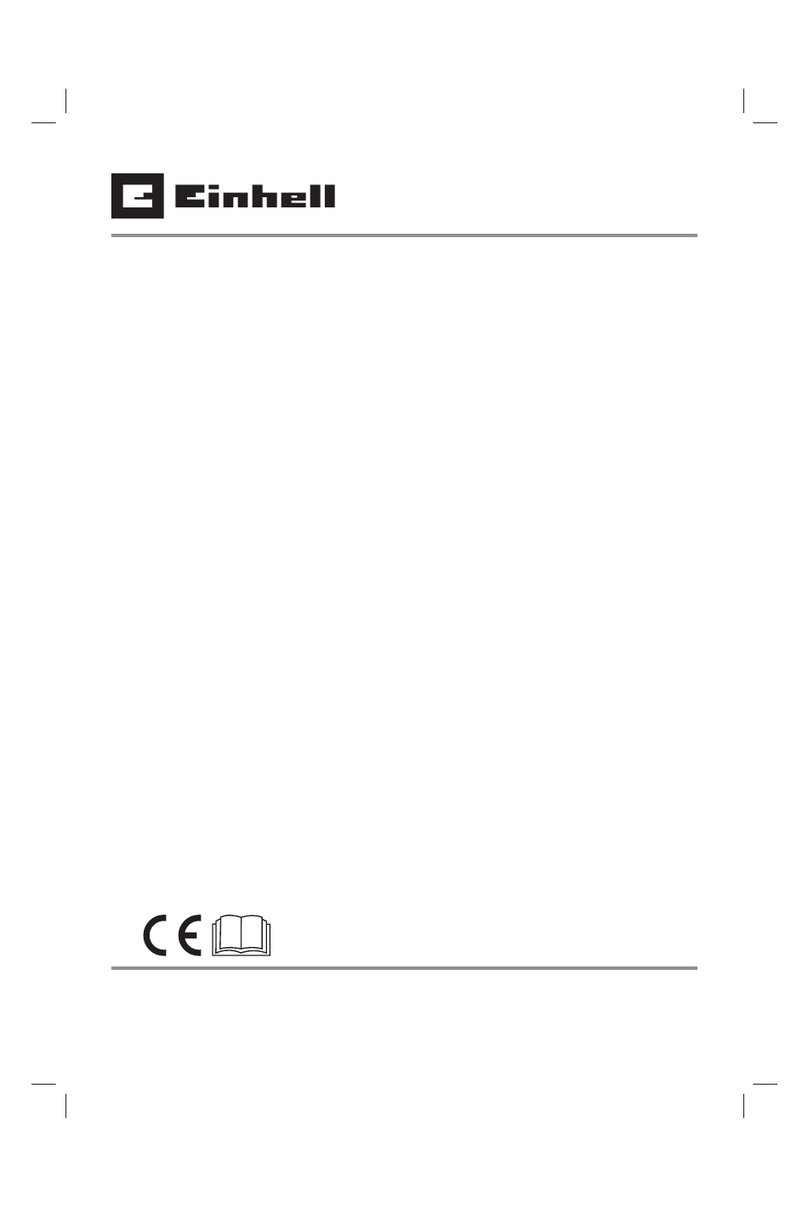
EINHELL
EINHELL TE-AC 430/50/10 Original operating instructions
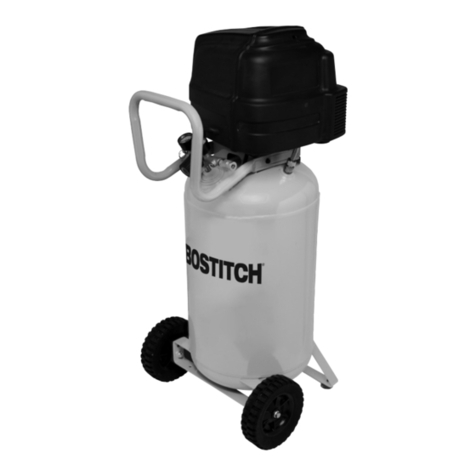
Bostitch
Bostitch CAP1615-OF instruction manual