Rifox 1113 User manual

Operating Manual
Breite: 170
Höhe:8,15
Oben Links
278,5 20
RIFOX - Hans Richter GmbH Spezialarmaturen Fon: +49 (0) 421 499 75 - 0 Internet: www.rifox.de
Page 1 of 6
11/2022 -Di. Subject to modifications
Model: 1113
Model: 1113-N
Model: 1118
Model: 1118-N
Float-Controlled Condensate Trap, PN 25
1 Safety instructions
1.1 Proper use
Any improper use, intervention in the design and deviation from the design data automatically lead to termination of the
warranty. The float-controlled condensate trap is designed for the discharge of condensate from steam, compressed air and
pressure gas systems. Any other usage is not permitted. The manufacturer is not liable for damage resulting from any other
usage. The user or operator bears the risk in this case. This also applies analogously to incorrect assembly, start-up, use and
maintenance.
1.2 Warnings and symbols
■Personal risk due to escaping operating medium because of pressure, temperature and weight. Failure to comply with
these warnings results in the risk of accidents.
■Follow the instructions in this operating manual.
■The operator must ensure that this operating manual and, if necessary, other relevant documents are available on site.
■Only trained or instructed personnel may be assigned to handling this equipment.
■Any mode of operation that may impair safety must be avoided.
2 General description and usage
2.1 Design of the condensate trap
Picture 1: Model WO-1113
Model WO-1113-N
Picture 2: Model EF-1118
Model EF-1118-N
1Housing cover 7Gasket
2Housing gasket 8Float control assembly
3Housing 9Supporting body assembly
4Control screw 10 Float
5Gasket 11 Holding screw for float control assembly
6Screw plug 12 Housing screws
13 Capsule venting for screw in

Operating Manual
Breite: 170
Höhe:8,15
Oben Links
278,5 20
RIFOX - Hans Richter GmbH Spezialarmaturen Fon: +49 (0) 421 499 75 - 0 Internet: www.rifox.de
Page 2 of 6
11/2022 -Di. Subject to modifications
2.2 Operation limits of housing material (Design)
For Model WO-1113 and WO-1118:
max. operating pressure (bar g) 25 23,2 20,8 17,2 14,8
max. operating temperature (°C) -10/20 100 200 300 400*
For Model WO-1113-N and WO-1118-N:
max. operating pressure (barg) 25 23,3 20,8 19,5
max. operating temperature (°C) -60/100 200 300 400
2.3 Function limit of control unit (for all four models) (* Special control units with oval-float)
Cross Section
max. line pressure in barg
Steam Compressed air
25/200 25 25
25/400 18 / 25* 25
30/550 12 / 20* 15 / 20*
50/1100 4 / 9* 5 / 9*
50/1650 3,5 / 5* 4 / 5*
2.4 Discharge capacity (for all four models, for hot condensate)
2.5 Function
■Due to the gravity the condensate flows downwards to the lowest point, which is the condensate trap housing. In the
lowest position of the float the outlet cross-section is close. Rising of the liquid level lifts the float and opens the outlet.
Condensate will be discharged through the upturned immersion tube. Decreasing condensate level closes the outlet again.
2.6 Compensation line
■In order to get proper function, the non-condensable gas must be able to leave the housing. Due to the vertical installation,
the non-condensable gas is able to leave the housing and flows into the steam/gas chamber above it, which has the same
pressure level. If the self-venting through the pipe must be extended, the control screw (4) can be replaced by a cutting ring
screw bolt and a compensation line can be installed leading upwards.
2.7 Automatic venting
■In the case of steam applications, automatic venting must be provided (vent jet).
2.8 Gastight under-level float control (only for gas applications)
■For gas applications, a gastight under-level float control is nearly exclusively used. Consult with Rifox, if necessary.
* only with screw material A4-70/ 1,4571/ 1.4104
For Model WO-1113 and WO-1118: For Model WO-1113-N and WO-1118-N:
Picture 3 Picture 4
For the cold condensate the discharge capacity is
higher because of medium temperature and density.
For the hot condensate the discharge capacity is lower
because of medium temperature and density.
1500
15000
0,1 1 10
Flow rate in kg/h
Pressure difference in bar (with reference to atmospheric pressure)
Performance:
110000
30 2000
20000
0,1 1 10
Flow rate in kg/h
Pressure difference in bar (with reference to atmospheric pressure)
Performance:
120000
30

Operating Manual
Breite: 170
Höhe:8,15
Oben Links
278,5 20
RIFOX - Hans Richter GmbH Spezialarmaturen Fon: +49 (0) 421 499 75 - 0 Internet: www.rifox.de
Page 3 of 6
11/2022 -Di. Subject to modifications
3 Assembly
The condensate trap has to be screwed into a pipeline between flanges.
■Remove transport caps from inlet and outlet.
■Fitting direction: according to Picture 1 and Picture 2.
■Supporting brackets: The weight of the condensate trap must be taken up by
the supporting brackets, which are welded onto the housing. A operation only on
the four feets is not allowed.
■To avoid downtimes, it is recommended to install stop valves with bypass to
pipeline, both in front of and behind the condensate trap.
■ For the model WO-1113-(N), remove the transport sefety device (see Picture 5)
before start-up and replace it with the control screw provided.
■ For the model EF-1118-(N), remove the fuse wire completely before start up.
4 Start-Up
Shut off the housing on both sides during strength tests with PT pressure.
The float-controlled unit is only suitable up to PS pressure value or alternative PT value shown in brackets according name
plate.
The lower value is max. allowable pressure. A pressure test with design pressure (PT) will destroy the float.
The pressure build-up and heating-up of the housing should not take place abruptly. If leakage is detected after the first
inspection, the screws (4 / 6 / 12) can be fixed under consideration of the given torque moments, as given in Section 6.5. The
screws can only be tightened on when the housing is unpressurized and at room temperature.
5 Observation and control
The function’s failure can be observed either as condensate blockage or as gas/ steam leakage.
■Condensate blockage can be determined by a): loosen the control screw (4) for a quarter rotation, while no condensate
leakage should occur; and by b): a surface thermometer on the housing for steam applications (if necessary, please consult
with Rifox).
■Gas / steam leakage: can be determined by an ultrasonic measuring device, and for steam applications by a surface
thermometer. In case of steam leakage, open the condensate trap according to Section 6.1. Make sure that float (10) can be
easily moved. If necessary, disassemble and clean the float control assembly (8). If damages/ wears are detected on parts or
on the sealing surface, the complete float control assembly (8) should be replaced.
6 Maintenance / Inspection
6.1 Opening the steam trap and dismantling the float control
6.1.1 Float control unit with spherical float
■ The steam trap has to be depressurized. Shut off the system securely in
front of and behind the steam trap.
■ Release any remaining pressure in the housing by loosening the control
screw (4) by only a quarter turn.
■Dismantle the steam trap from the pipeline system. Loosen the flange
connections and lift out of the pipeline carefully and place on the floor.
Attention: The condensate trap weights from 145 up to 160 kg depending
on the connection sizes. Lifting device is required.
■Loosen the housing screws (12) evenly crosswise. Put down the housing
cover (1). Attention: the housing cover weights about 16 kg.
■The float control unit is dismantled with a centering aid that is inserted in the bushing provided with 2 slots. By turning
counterclockwise (3-4 turns) the bushing is screwed out of the control support body (9). The control unit is detached from
the seat cone by means of gentle blows with a hammer on the front end of centering aid.
■Screw out the bushing completely.
■Remove float control unit (8) through the cover opening.
Picture 6
Special
Float
Screws
Bushing
Picture 5

Operating Manual
Breite: 170
Höhe:8,15
Oben Links
278,5 20
RIFOX - Hans Richter GmbH Spezialarmaturen Fon: +49 (0) 421 499 75 - 0 Internet: www.rifox.de
Page 4 of 6
11/2022 -Di. Subject to modifications
6.1.2 Float control unit with oval float
■The steam trap has to be depressurized. Shut off the system securely in front of and behind the steam trap.
■Release any remaining pressure in the housing by loosening the control screw (4) by only a quarter turn.
■Dismantle the steam trap from the pipeline system. Loosen the flange connections and lift out of the pipeline carefully and
place on the floor.
Attention: The condensate trap weights from 145 up to 160 kg depending on the connection sizes. Lifting device is required.
■Loosen the housing screws (12) evenly crosswise. Put down the housing cover (1). Attention: the housing cover weights
about 16 kg.
■Loosen the screws between float and fork by using a flat ring spanner.
■Remove the screws and the spring washer.
■Turn the oval float inside the housing and lift it out vertically.
■If only the float has to be replaced, continue with section 6.3.2 point 3.
■The supporting body with fork is dismantled with a centering aid that is inserted in the bushing provided with 2 slots. By
turning counterclockwise (3-4 turns), the bushing is screwed out of the control support body (9). The control is detached from
the seat cone by means of gentle blows with a hammer on the front end of centering aid.
■Screw out the bushing completely.
■Remove supporting body with fork through the cover opening.
6.2 Disassembling, cleaning and assembling the float control (Picture 7)
■After removing the cotter pin (p), the rotary valve (v) can be simply pulled out
to the side.
■Clean the parts using, for example, benzine.
■Check the rotary valve (v) for wear along the sealing edge. If wear is detected,
the support body (b) together with the rotary valve (v) must be replaced. The
thorough leakage test must be carried out by RIFOX.
■During assembly ensure that the notch in the rotary valve (v) points to the
punch mark on the support body (b) and the cotter pin (p) is inserted and secured
again carefully.
■It must be possible to move the float up and down easily by hand.
6.3 Installation of the float control unit and assemble the steam trap
6.3.1 Float control unit with spherical float
■The complete float control assembly (8) is inserted into the conical housing seat with the support body. Ensure the tube is
positioned vertically downwards.
■Screw in the bushing into the control support body (b) and tighten with the centering aid described in Section 6.1.
■Check the housing gasket (2), replace if it is damaged.
■Put on the housing cover (1).
■Tighten the housing screws (12) evenly crosswise. Tightening torque according to Section 6.5.
6.3.2 Float control unit with oval float
■The supporting body, float fork and rotary slide valve assembly is inserted into the conical housing seat with the support
body. Ensure the tube is positioned vertically downwards.
■Screw in the bushing into the control support body (b) and tighten with the centering aid described in Section 6.1.
■Insert the oval float vertically into the housing. Turn the oval float inside the housing to have the connection points of the
float fork and the float are aligned. The filling nipple of the oval float should point towards the housing opening.
■Attach the connecting elements (screws and spring washer) by hand and tighten with a flat ring spanner.
■Check the housing gasket (2), replace if it is damaged.
■Put on the housing cover (1).
■Tighten the housing screws (12) evenly crosswise. Tightening torque according to Section 6.5.
bpv
Picture 7

Operating Manual
Breite: 170
Höhe:8,15
Oben Links
278,5 20
RIFOX - Hans Richter GmbH Spezialarmaturen Fon: +49 (0) 421 499 75 - 0 Internet: www.rifox.de
Page 5 of 6
11/2022 -Di. Subject to modifications
6.4 Care and maintenance
■In the case of a great risk of dirt accumulation, the housing, when it is depressurized, should be rinsed thoroughly from
time to time. If necessary, the float control assembly (8) should also be checked according to Section 6.2.
■The dirt, which has been accumulated in the housing, can be removed away by screwing off the screw plug (6).
■For special applications, it is advisable to install a separate upstream strainer.
■The float control assembly (8) usually does not to be special maintained. The maintenance depends primarily on the wear
resistance of the valve gasket. See Section 6.1 and 6.2.
6.5 Tightening torque
Position Part Name
Tightening Torque (Nm)
1113 / 1118 1113-N / 1118-N
Weicheisen PTFE-Special 1.4571 PTFE-Special
4
Control screw for G½“ 80 55 175 80
Control screw for G¼“ 35 25 50 25
6 Screw plug G¾“ 100 80 250 80
12 Housing screw M12 50 40 50 40

Operating Manual
Breite: 170
Höhe:8,15
Oben Links
278,5 20
RIFOX - Hans Richter GmbH Spezialarmaturen Fon: +49 (0) 421 499 75 - 0 Internet: www.rifox.de
Page 6 of 6
11/2022 -Di. Subject to modifications
6.6 Spare parts
Only original spare parts can be used.
Pos. Part Name Model 1113 / 1118 Model 1113-N / 1118-N
1 Housing cover P265GH (P235GH-TC1; P250GH) 1.4571
2 Housing gasket soft iron / PTFE-Special 1.4571 / PTFE-Special
3 Housing P235GH-TC1 / P250GH / P265GH 1.4571
4 Control screw: ½“ and ¼“ G½“ (BSP) - 5.8
G¼“ (BSP) - 1.4104
G½“ (BSP) - A4
G¼“ (BSP) - A4
5 Gasket soft iron / PTFE-Special 1.4571 / PTFE-Special
6 Screw plug DIN 910 - 5.8 - G¾“ (BSP) DIN 910 - 1.4571 - G¾“ (BSP)
7 Gasket soft iron / PTFE-Special 1.4571 / PTFE-Special
8 Float control assembly 1.4112 / 1.4057 / 1.4301 / 1.4571
or complete 1.4571 1.4571
9 Supporting body assembly 1.4112 / 1.4057 / 1.4301 / 1.4571
or complete 1.4571 1.4571
10 Float 1.4301 / 1.4571 1.4571
11 Holding screw for float control
assembly 1.4571 1.4571
12 Housing screws DIN 2510 - 21 CrMo V 5-7 / 24 CrMo 5 - M12 DIN 939 / ISO 4032 - A4 - 70; DIN 934 - A4 - M12
13 Capsule venting for screw in 1.4104, 1.4571, 1.4301 -
Picture 8: Model WO-1113
Model WO-1113-N
Picture 9: Model EF-1118
Model EF-1118-N
7 Conformity assessment
The pressure equipment described is a pressure-keeping component in accordance with the Pressure Vessel Directive
2014/68/EU.
DN80 / DN 100: Conformity verified through the identifying mark: CE 0525.
A detailed declaration of conformity assessment according to PED is available as separate document. Please request if
necessary, if not attached.
This manual suits for next models
3
Table of contents
Other Rifox Fan manuals
Popular Fan manuals by other brands
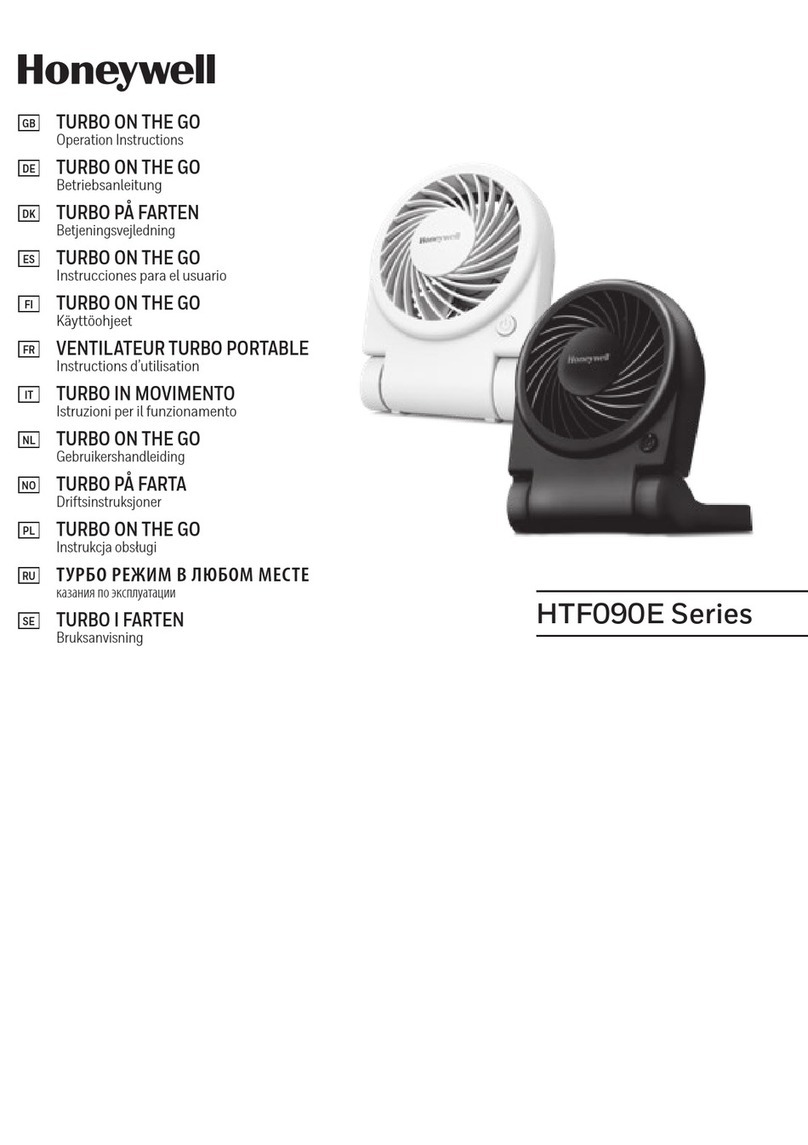
Honeywell
Honeywell HTF090E Series Operation instructions

Craftmade
Craftmade UT56 installation guide
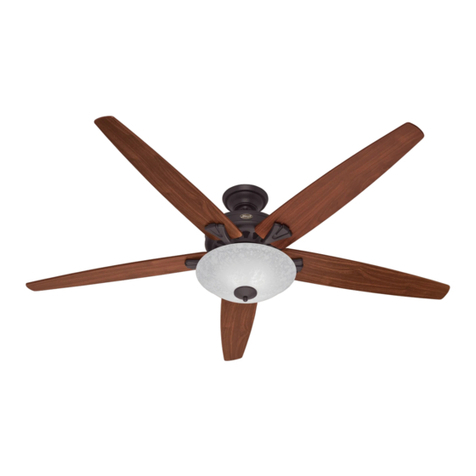
Hunter
Hunter Stockbridge Owner's guide and installation manual
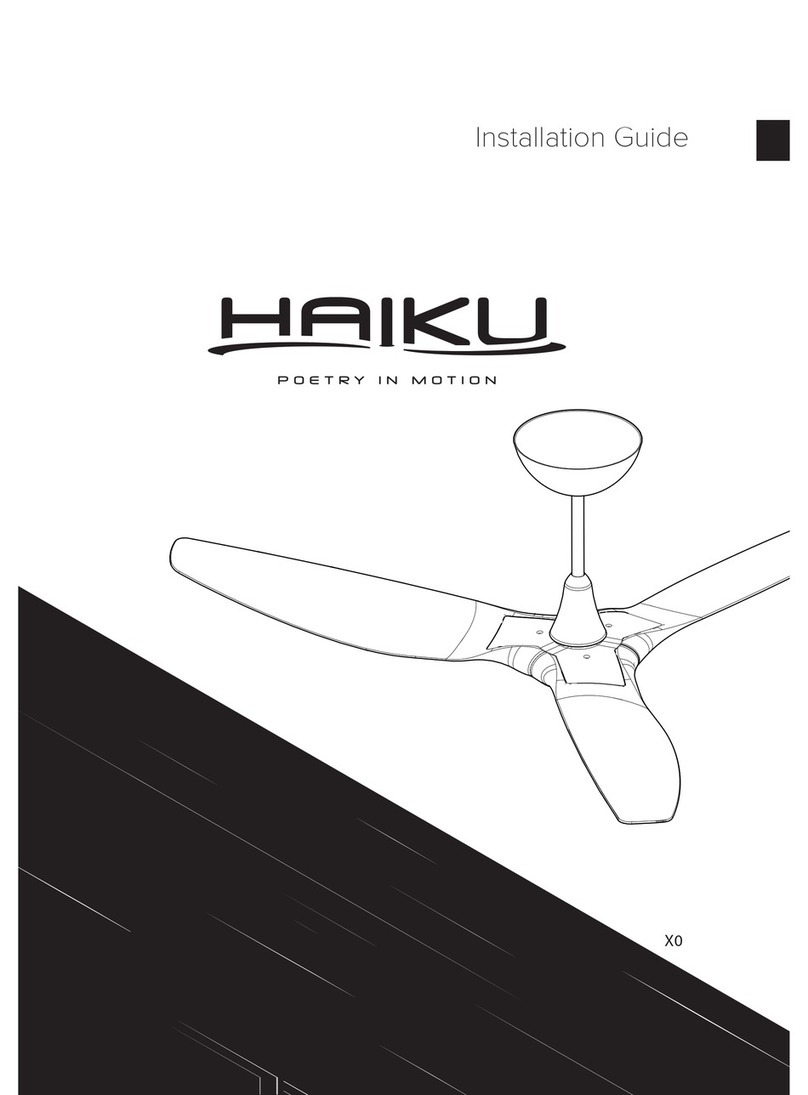
Haiku
Haiku K3150-X0 installation guide
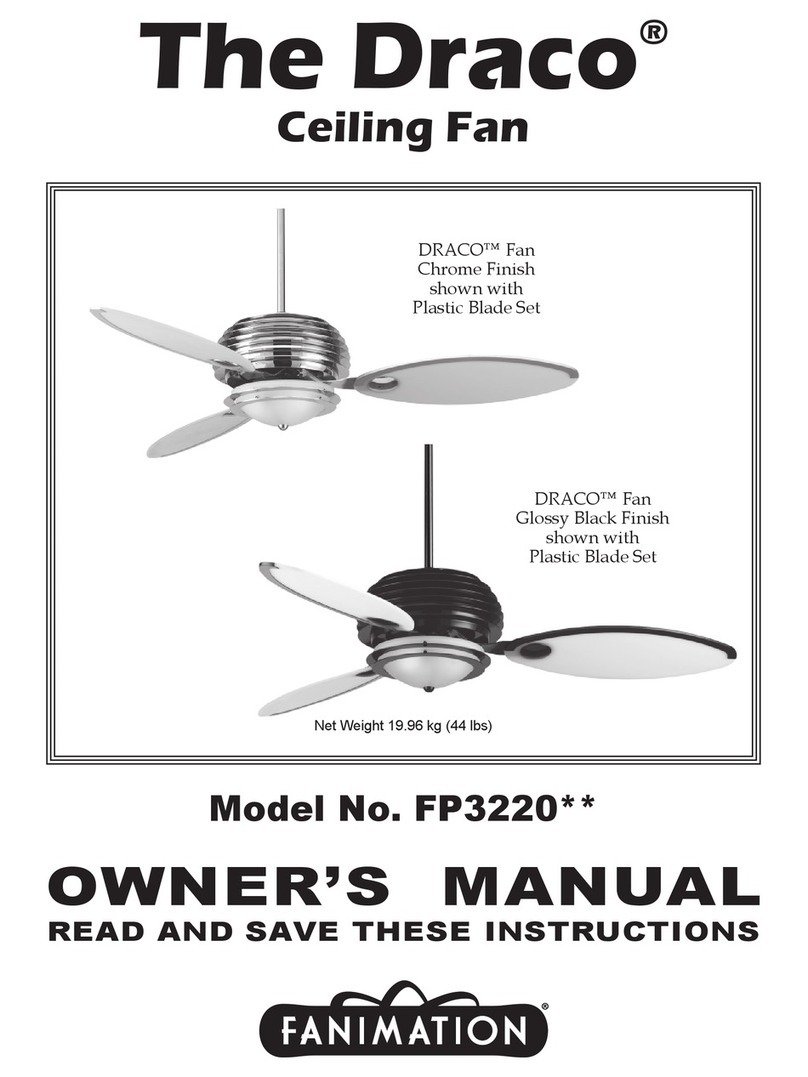
Fanimation
Fanimation Draco FP3220 Series owner's manual

Ventair
Ventair Brook 4 Important Installation Instruction and Warranty Instructions