RoboVent CLARION CFX Series User manual

Owner’s Manual
Installation, Operation & Maintenance
Revised 11-25-20
Clarion Series (CFX-)
Oil Mist Collectors


Owner’s Manual
Installation, Operation & Maintenance
Clarion Models:
Manufactured by:
RoboVent
37900 Mound Road Sterling Heights, MI 48310 USA
(888) 762-6836 www.robovent.com
©2016 RoboVent All rights reserved.
CFX-1000
CFX-2000
CFX-3000
CFX-6000
CFX-9000
CFX-3000
CFX-2000
CFX-1000

4 ROBOVENT • CLARION SERIES OWNER’S MANUAL
Dear Customer,
Thank you for purchasing a RoboVent Clarion Oil Mist Collector. This manual will
help you use the many features available to customize the unit to your specific needs.
When your RoboVent Clarion Series unit needs scheduled maintenance, keep in mind
that RoboVent has specially trained staff in servicing our mist and particle collectors. We
would be pleased to set up a preventative maintenance program or answer your questions
and concerns.
At RoboVent we are committed to making your facility a safe and healthy
environment for your workers. Please take time to read this manual thoroughly before
installing and operating the unit.
Congratulations!

ROBOVENT • CLARION SERIES OWNER’S MANUAL 5
Important Safety Instructions ...................Section 100 .........................Page 6
Features of the Clarion Series Collectors .........Section 200 .......................Page 7-8
Receiving & Inspection ..........................Section 300 .........................Page 9
Installation ......................................Section 400 ...................Pages 10-11
Operation.......................................Section 500 ........................Page 12
Motor Greasing Guide...........................Section 600 ........................Page 13
Maintenance....................................Section 700 ........................Page 23
Appendix A:.......................General Wiring Diagrams
Appendix B: ..........HEPA Filter Installation & Maintenance
Appendix C:........................................Parts List
Table of Contents

6 ROBOVENT • CLARION SERIES OWNER’S MANUAL
Failure to follow all instructions may result in electric shock,
bodily injury and/or destruction of the unit.
Use of controls, adjustments, or performance of procedures
other than those specified herein, may
result in electrical shock.
IMPORTANT SAFETY INSTRUCTIONS
1. Read all instructions thoroughly.
2. Heed all warnings.
3. Do not block intake or exhaust vents. Keep the exhaust vent free from
debris and materials that could restrict airflow. Prolonged restriction could
damage the motor and electrical components. Any blockage of the air
flow will decrease efficiency of this unit.
4. Refer all service matters to qualified service personnel. Servicing is
required when the unit is damaged in any way including the control
panel, supply wiring or in the case of excessive filter loading.
5. Risk of serious personal injury or death!
Use extreme care to make sure you are never in a position where your
body (or any item you are in contact with, such as a screwdriver or test
instrument) can accidentally touch the blower wheel.
6. Disconnect power before working on the motor or blower
wheel. The motor or blower wheel should be disassembled
only by a factory authorized technician.
SECTION 100
Important Safety Instructions

ROBOVENT • CLARION SERIES OWNER’S MANUAL 7
SECTION 200
Features of the Clarion Series Collectors
1. Filtration System
The RoboVent Clarion Series oil mist collectors utilize a
proprietary design with a superior ability to process oil-laden
air in way that causes miniscule droplets to coalesce and
precipitate for far more effective capture. Traditional oil mist
collectors rely on dated principles with limited success, such
as centrifugal pocket filters, individual cartridge or panel
filters, electrostatic precipitators and others.
Unlike other manufacturers, the RoboVent Clarion uses
packed-bed filter technology (see Figure 1)that only require
a single filter in our collectors, reducing your replacement
and maintenance costs. Furthermore, our application-specific
filter media means that we can apply the right media to your
application, ensuring long life and clean air. All of this, backed
by our 9 month filter life guarantee.
2. High Performance Blower Design
Each RoboVent Clarion Series Collector comes with a high
output blower and direct drive motor. This highly efficient
blower design and direct drive system maximizes the airflow
(CFM) delivered by the motor power requirements. (see Figure
2).
3. Control Panel
The built-in Control Panel of the RoboVent Clarion Series contains
all the electrical control devices, including the motor starter with
thermal overload relay, on/off selector switch and service discon-
nect switch. (see Figure 3).
4. Sturdy 12 GA Reinforced
Collector Housing Construction
This heavy-duty construction secures a lifetime of industrial
use. Seams are robotic welded and sealed to assure there
are no leaks or cracks that could contaminate the facility
air system. Each unit is pre-tested for air leaks during
construction and again before installation.
FIGURE 1
FIGURE 2
Pic of Clarion
Control Panel
FIGURE 3

8 ROBOVENT • CLARION SERIES OWNER’S MANUAL
SECTION 200
Features of the Clarion Series Collectors
5. Acoustic Silencing Plenum (option)
High-density sound materials and Bass Trap Acoustics
have been implemented as part of the outlet plenum. The
acoustically designed plenum greatly reduces motor and
blower noise levels and decreases ambient noise into the
facility.
6. Front Door Filter Access
Screen filters are easily accessible through an oversized front
access door. Filter replacement is made easy and requires less
time and effort than traditional loading systems.
8. Integral Mounting Rails
Mounting rails on base for machine top mounting or suspending
from building structure.

ROBOVENT • CLARION SERIES OWNER’S MANUAL 9
Receiving
RoboVent Equipment is typically shipped on skids or in crates. The number of skids/crates will vary,
depending on the type, size and accessories ordered. These skids/crates are too heavy to lift by hand, and
will need to be unloaded by an industrial fork-truck or similar equipment.
Inspection
A visual inspection of your equipment should be performed before it is removed from the truck. Dents,
scratches, and other damages should be noted on the shipping documents, and also photographed.
The structural integrity of the housing can be adversely affected by large dents. RoboVent should be
immediately notified of any structural damage to your equipment. It is the purchaser’s responsibility to
file shortage reports and damage claims with the carrier and with your RoboVent Representative. The
carrier is responsible for any damage to the equipment while it is in transit unless specific arrangements
are made otherwise.
Compare the number of items received against the carrier’s bill of lading. Inspect all
items for apparent damage. Immediately report any shortages or obvious damage to the carrier and to your local
RoboVent Representative, call the factory at 1-(888)-762-6836,
or email: customer.service@robovent.com.
When all skids are completely unpacked and uncrated, check all items received against the packing lists. Further
inspect the unit and components for hidden damage. Again, report any shortage or damage to the carrier and to
your local RoboVent Representative.
The filter cartridges are typically shipped installed in your collector. Be sure to check them for alignment, as they
may have shifted during transit. If they have shifted, it is possible that damage may have been done. Remove all
filter cartridges and inspect thoroughly.
Note: Do not return any damaged components without first contacting your RoboVent Representative
to obtain a Returned Goods Authorization (RGA).
Small Parts
Carefully inspect all packing material before it is discarded, to be sure that no small parts have been missed.
SECTION 300
Receiving & Inspection

10 ROBOVENT • CLARION SERIES OWNER’S MANUAL
SECTION 400
Installation
The Clarion Oil Mist Series
The RoboVent Clarion Oil Mist Series Collectors are universally
designed to cover a large spectrum of oil and coolant mist
applications.The application will determine the type of mounting
system needed.The most common is the machine mounted Collector.
In most cases this will work because of the small footprint of the
Collector. The CFX Series units also have the ability to be ducted to
one or several machines saving money and floor space.
Machine Mounting Installation:
This is the typical installation type and the simplest set-up when
space permits;
First locate a suitable mounting location on the top of the machine
where the Clarion unit can be mounted.
Many CNC machines have a cover plate along the top or side that
is designated for attaching a filtration flex hose. Locate this if
applicable. The cut-out under the cover plate should be about 6”-8”
diameter but will depend on the size of the machine.
The Clarion unit has a side inlet opening where the mist laden
air enters into the Collector. Locate a level place along the top of
the CNC or machine that will allow a short flexible duct or rigid
metal duct connection from the Collector to machine. This distance
should be as short as possible. Do not locate the suction intake
on machining applications in direct line of the cutting
spray.
Remove the cover plate from the machine (if present, alternatively
cut a circular opening through the machine skin to suit the flange
size), and install an angle flange (see Figure 4).
Secure the Clarion Unit to the top of the machine that will allow a
minimum of 12”clearance under the Collector (see Figure 5).This will
be for the drain hoses (Detailed in the following section).
FMC-1100 on CNC OpMan
A
DETAIL A
SCALE 1 / 9
A
FIGURE 4
FIGURE 5
DETAIL A
SCALE 1 / 9
A
FIGURE 6

ROBOVENT • CLARION SERIES OWNER’S MANUAL 11
SECTION 400
Installation(continued)
After securing the Collector, fit an angle flange to the Clarion unit’s
intake, then connect a short length of flexible duct or a section of
rigid metal duct from the Collector inlet to the angle flange that was
installed on the top of the CNC (see Figure 6).
Connecting Drain Hoses:
The Clarion Series Collectors has 2 or 3 drain outlets located on the
underside of the Collector. Connect the provided clear plastic tubing
to each drain.The tubing can be installed in two ways. It can be loop
connected (see Figure 7) or submerged into the reservoir tank. Either
installation will work to create a fluid air trap so your Collector will
drain properly. This is essential otherwise air or coolant can be drawn
backwards through these tubes into the Collector, because of the
negative vacuum pressure inside the Collector. Failure to properly
install the drain hoses will greatly reduce efficiency of the Collector as
it will prevent coolant from draining down the tubes, and the unit will
not function properly.
Each tube must have a loop (as shown) that will create the fluid air
trap to isolate the internal reservoir. Secure the loop with a zip-tie and
FMC-1100 on CNC OpMan
DETAIL A
SCALE 1 / 5
A
FIGURE 7
place the open end over an area that will allow the coolant to drain back into the machine or the coolant sump. Do
not submerge the open end into the coolant as this will form a double trap.
The other option is to set up a submerged system that does not require a loop set-up. If this installation is preferred
make sure the open end of each tube is totally submerged into the machine’s coolant sump or reservoir. If the
reservoir runs low or below the tubing you will lose the fluid air trap.The tubing must be submerged at least 12”into
the reservoir.
Electrical Hook-up:
The Oil Mist Series requires a 3 phase, 460 volt electrical feed (230 Volt and 110 Volt available as options on certain
models. Verify your particular model by looking at the rating tag on the Collector or on the relevant Specification
Sheet). Amperage requirements for the motor can be found on the Specification Sheet for the particular Clarion
collector. Electrical connections should only be done by a licensed electrician and accordance with NEC and all
applicable local codes. (See Appendix for electrical schematic.)
The exact electrical connection will be determined by what model unit is ordered.

12 ROBOVENT • CLARION SERIES OWNER’S MANUAL
SECTION 500
Operation
Clarion Oil Mist Collector Start-Up
Once the Collector is properly mounted, the proper flex duct
installed, the drain hoses and sump primed and electrical power is
connected you are ready for Start Up.
1. Check Blower Rotation: Check blower rotation of the unit
by jogging the motor. Proper blower rotation can be observed
by either removing the blower access panel or by looking down
through the vents in the top of the motor. Blower rotation
should be CLOCKWISE when viewed from above the motor. The
blower will still draw air if run backward but it will only be a
fraction of what it should be (see Figure 15).
2. Check filters. Make sure all the filters are sealed around the
edges and that there is no air-flow between the track and the
filter.
3. Check the drainage system. Make sure each looped drain
line is full with fluid. If coolant is sucked back up into the
Collector you may need to increase the size of the loop in the
line. Periodically check that there is coolant in the drain loops
at all times (when using the loop installation method).This is
extremely important in the functioning of the Clarion unit.
4. Record differential pressure. Over the first several weeks it will be important to monitor the differential
pressure from the dirty air to clean air side. If static pressure increases rapidly there may be an issue with the
application which may require a different filter combination. In this case call RoboVent Technical Support at
1-(888)-762-6836, or email: customer.service@robovent.com
Motor
Blower
Wheel
Venturi
FIGURE 15

ROBOVENT • CLARION SERIES OWNER’S MANUAL 13
SECTION 600
Motor Greasing Guide

Your RoboVent unit will have one of four motor manufacturers installed:TECO,
Marathon,Weg, orBaldor.
These motors are created with anti-friction, grease-lubricated bearings. Grease is essential
to your motor bearings because it creates an oil lm that counteracts the abrasive metal-to-
metal contact that can occur between rotating elements. Follow RoboVent’s Motor Greasing
Guidelines to properly lubricate your electric motor.
NOTE: 1 Pump = 1 gram of grease
OUNCES OZ GRAMS G GREASE GUN PUMPS
0.1 oz 2.835 g 2.8 pumps
1 oz 28.35 g 28 pumps
2 oz 56.70 g 56 pumps
3 oz 85.05 g 84 pumps
4 oz 113.40 g 112 pumps
5 oz 141.75 g 140 pumps
Grease Conversion Chart for use with this grease gun
Manual Grease Gun
Heavy Duty Lever Grease Gun w/ 18"
Hose Ext & Coupler
Fastenal Part No. (SKU) 0425881
DELIVERY RATE = 1 OZ PER 28 PUMPS
SECTION 600
Motor Greasing Guide
14 ROBOVENT • CLARION SERIES OWNER’S MANUAL

Teco Motor Greasing Guidelines
Lubrication Procedure
It is advisable to re-grease when the motor is running to allow the new grease to be evenly
distributed inside the bearing. Before re-greasing, the inlet tting should be thoroughly
cleaned to prevent any accumulated dirt from being carried into the bearing with the new
grease. The outlet of grease drainage should be opened to allow the proper venting of old
grease. Use a grease gun to pump grease through grease nipple into the bearings. After re-
greasing, operate the motor for 10-30 minutes to allow any excess grease to vent out.
Approved Greases
• All motors with ZZ bearings will have SHELL Alvania R3 (lithium base grease).
• All motors with open bearings will have Polyrex EM (polyurea base grease).
• Certain T-frame models will utilize special grease and will be noted on the lubrication
nameplate.
Relubrication Time Interval & Amounts
*Fill new grease until it overows and the old grease is entirely replaced.
BEARING SIZE MOTOR HP GREASE 1800 RPM 3600 RPM
AMOUNT HOUR CHANGE HOUR CHANGE
IN GRAMS INTERVAL INTERVAL
All motors listed are ODP
DE & NDE: 6306ZZ 5 30 grams 3000 hours 2000 hours
DE & NDE: 6306ZZ 7.5 30 grams 3000 hours 2000 hours
DE: 6308ZZ 10 30 grams 3000 hours 2000 hours
DE: 6310ZZ 20 40 grams 3000 hours 2000 hours
DE: 6311ZZ & DE: 6212C3 30 40 grams 3000 hours 2000 hours
DE & NDE: 6213 & DE: 6212C3 40 50 grams 3000 hours 2000 hours
DE & NDE: 6213 & DE & NDE: 6213C3 50 50 grams 3000 hours 1000 hours
DE: 6314, NDE: 6213, DE: 6313C3 & NDE: 6213C3 75 80 grams 3000 hours 1000 hours
DE & NDE: 6317, DE: 6313C3 & NDE: 6213C3 100 120 grams 2000 hours 1000 hours
DE & NDE: 6317 & DE & NDE: 6313C3 125 120 grams 2000 hours 1000 hours
Relubrication Time Interval
SECTION 600
Motor Greasing Guide
ROBOVENT • CLARION SERIES OWNER’S MANUAL 15

Marathon Motor Greasing Guidelines
Lubrication Procedure
1. Stop motor. Disconnect and lock out of service.
2. Remove contaminates from grease inlet area.
3. Remove ller and drain plugs.
4. Check ller and drain holes for blockage and clean as necessary.
5. Add proper type of amount of grease. See the relubrication amounts table for volume
of grease required.
6. Wipe o excess grease and replace ller and drain plugs.
7. Motor is ready for operation.
Approved Greases
• Chevron SRI #2
• Rykon Premium #2
• Exxon Polyrex EM
• Texaco Polystar RB
Service Types
• Seasonal Service: The motor remains idle for a period of 6 months or more.
• Standard Service: Up to 16 hours of operation per day, indoors, 100° F max ambient temp.
• Severe Service: Greater than 16 hours of operation per day. Continuous operation under
high ambient temp (100 to 150° F), dirty moist locations, high vibration, heavy shock
loading or where shaft extension end is hot.
SECTION 600
Motor Greasing Guide
16 ROBOVENT • CLARION SERIES OWNER’S MANUAL

NEMA FRAME SIZE MOTOR HP VOLUME OF GREASE
140 5 HP 4 grams
180 7.5 HP 8 grams
210 10 HP 12 grams
250 20 HP 16 grams
280 30 HP 19.5 grams
320 40 HP-50 HP 23.5 grams
360 60 HP-75 HP 27.5 grams
400 100 HP 34 grams
440 125 HP 42.5 grams
Relubrication Amounts
1800 RPM OVER 1800 RPM 1800 RPM OVER 1800 RPM 1800 RPM OVER 1800 RPM
OR LESS OR LESS OR LESS
SERVICE
CONDITIONS
Standard 3 yrs 6 months 2 yrs 6 months 1 year 3 months
Severe 1 yr 3 months 1 yr 3 months 6 months 1 month
Seasonal The motor remains idle for a period of 6 months or more
Relubrication Time Interval
NEMA FRAME SIZE IN RPMs)
140180 210360 400510
SECTION 600
Motor Greasing Guide
ROBOVENT • CLARION SERIES OWNER’S MANUAL 17

Weg Motor Greasing Guidelines
Lubrication Procedure
Machines without Grease Nipples
Motors up to frame size 215T are normally tted without grease ttings. In these cases the
regreasing shall be done during preventive maintenance service paying attention to the
following aspects:
1. Take motor apart carefully.
2. Take all the grease out.
3. Wash the bearing with kerosene or diesel.
4. Dry the bearings
5. Regrease the bearing immediately.
Motors Fitted with Grease Fitting
It is strongly recommended to grease the machine while running. This allows the grease
renewal in the bearing housing. When this is not possible due to rotating parts by the
grease device (pulleys, bushing, etc.) that oer some risk to physical integrity of the operator,
proceed as follows:
1. Clean the area near the grease nipple.
2. Put approximately half of the total grease and run the motor for 1 minute at full speed.
3. Then turn o the motor and pump in the rest of the grease.
Note: The injection of all the grease with the motor in standstill can make the grease penetrate into the motor,
through the bearing housing inner seal.
Approved Grease
• Mobile Polyrex EM Grease
Special Note
The table below is specically intended for relubrication with MOBIL Polyrex EM grease and
bearing absolute operating temperature of:
• 70°C (158°F) for 254/6T to 324/6T frame size motors
• 85°C (185°F) for 364/5T to 586/7T frame size motors
• For every 15°C (59°F) above these limits, relubrication intervals must be reduced by half.
• Shielded bearing (ZZ) are lubricated for bearing life as long are they operate under
conditions and temperature of 70°C (158°F).
***When motors are used on the vertical position, their relubrication interval is reduced
by half if compared to horizontal position motors.***
On applications with high or low temperatures, speed variation etc., the type of grease and
relubrication intervals is given on an additional nameplate attached to the motor.
SECTION 600
Motor Greasing Guide
18 ROBOVENT • CLARION SERIES OWNER’S MANUAL

FRAM SIZE MOTOR HP GREASE AMOUNT IN GRAMS 3600 RPM 1800 RPM
254 / 6T 20 HP 13 grams 15700 hours 20000 hours
284 / 6T 30 HP 18 grams 11500 hours 20000 hours
324 / 6T 40 HP 21 grams 9800 hours 20000 hours
364 / 5T 60 HP 27 grams 3600 hours 9700 hours
404 / 5T 100 HP 27 grams 3600 hours 9700 hours
444 / 5TS 125 HP 27 grams 3600 hours 9700 hours
RELUBRICATION
INTERVALS IN HOURS
324 / 5T 40 HP 21 grams 9800 hours 20000 hours
364 / 5T 60 HP 27 grams 4800 hours 9700 hours
404 / 5T 100 HP 34 grams 3000 hours 6000 hours
444 / 5T 125 HP 45 grams 2300 hours 4700 hours
Relubrication Time Interval & Amount of Grease
SECTION 600
Motor Greasing Guide
ROBOVENT • CLARION SERIES OWNER’S MANUAL 19

Baldor Motor Greasing Guidelines
Lubrication Procedure
***Lock o and tag out power at the disconnect before servicing***
*** Motor should be warm prior to greasing***
1. Locate the grease inlet, clean the area, replace the pipe plug with a grease tting.
2. Remove grease drain plug.
3. Add recommended amount of grease. Stop when new grease appears at shaft hole
in the endplate or grease outlet plug.
4.Replace grease inlet plug and run the motor for 15 minutes.
5. Replace the grease drain plug.
Correct Grease Gun Procedures
1. Use hand-operated grease gun, not a pneumatic grease gun. Pump grease slowly,
taking 10 to 12 seconds to complete each stroke.
2. Apply quantity of grease called for. Over-lubrication can be as damaging as under-
lubrication.
3.Do not over-lubricate motors. Over-lubrication of a motor can seriously damage it by
forcing grease into motor windings. Over-lubrication of the extract motor can force
grease into the centrifugal switch causing it to malfunction.
Approved Grease
• Shell Dolium R (factory installed)
• Chevron SRI (standard service conditions)
• Darmex 707 (high temp conditions)
• Arrowshell 7 (low temp conditions)
SECTION 600
Motor Greasing Guide
20 ROBOVENT • CLARION SERIES OWNER’S MANUAL
This manual suits for next models
5
Table of contents
Popular Fan manuals by other brands

Westinghouse
Westinghouse WST6508 user manual

Chicago Electric
Chicago Electric 66878 Set up and operating instructions

Vents
Vents TwinFresh Comfo RA1-25 user manual
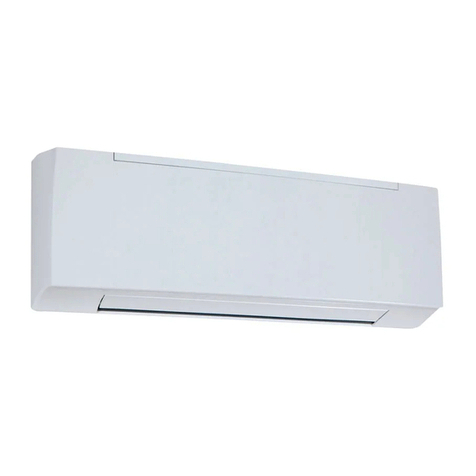
Sabiana
Sabiana Carisma Fly CVP-ECM Installation, use and maintenance manual
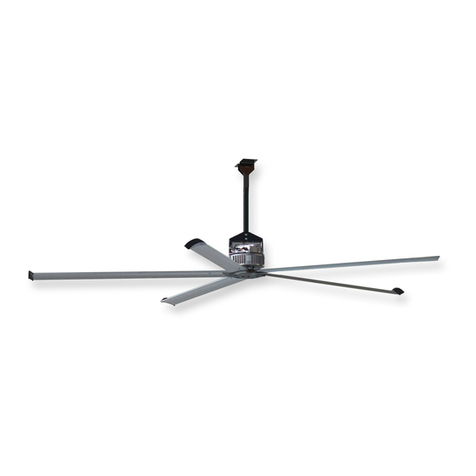
aerauliqa
aerauliqa THS Series Specific Manual
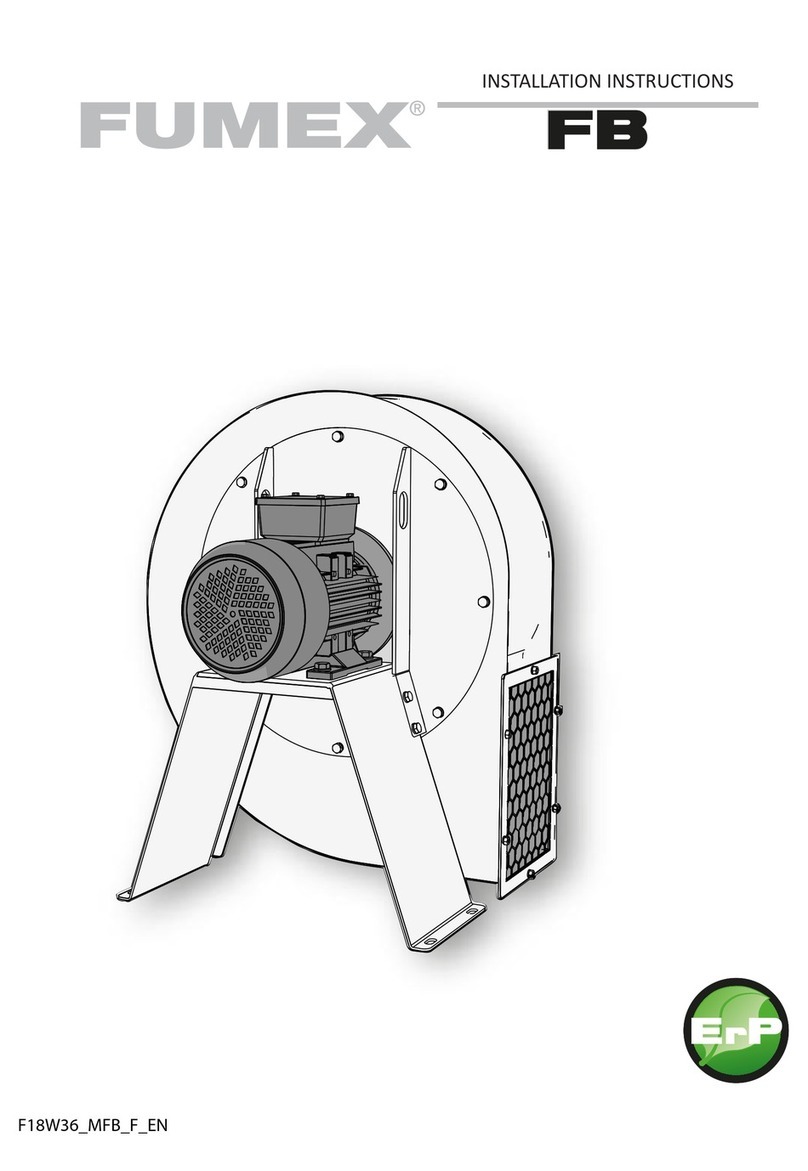
Fumex
Fumex FB Series installation instructions
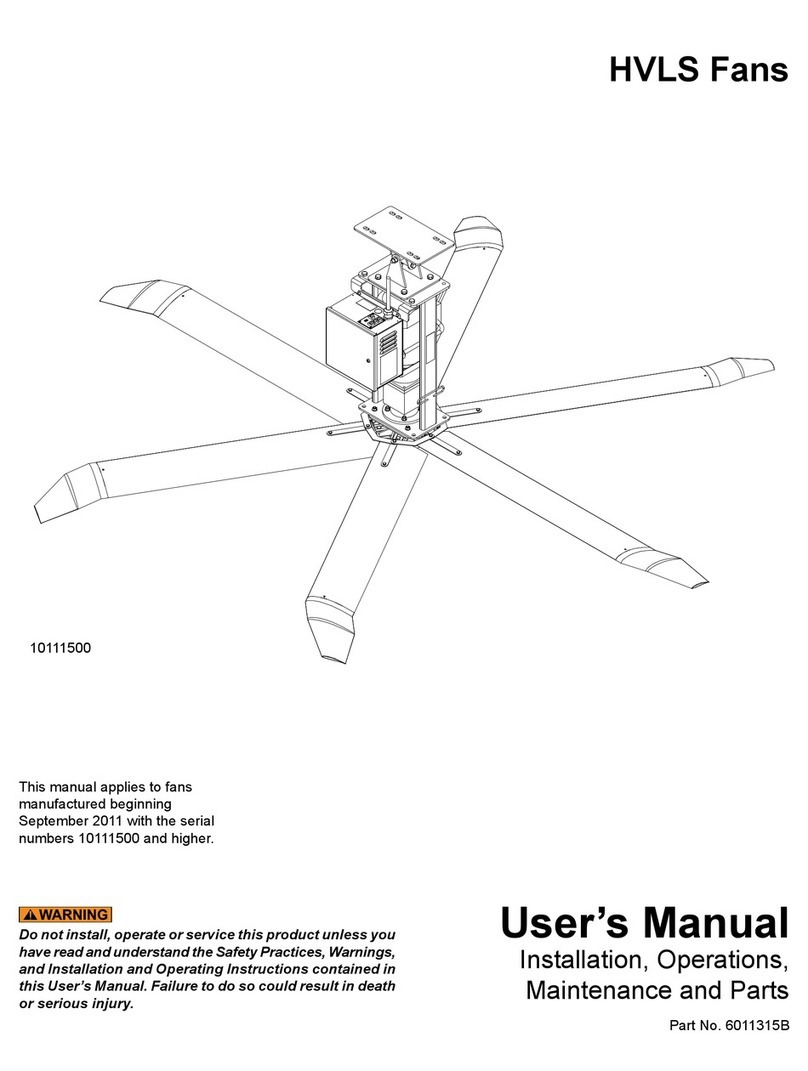
4Front Engineered Solutions
4Front Engineered Solutions HVLS user manual
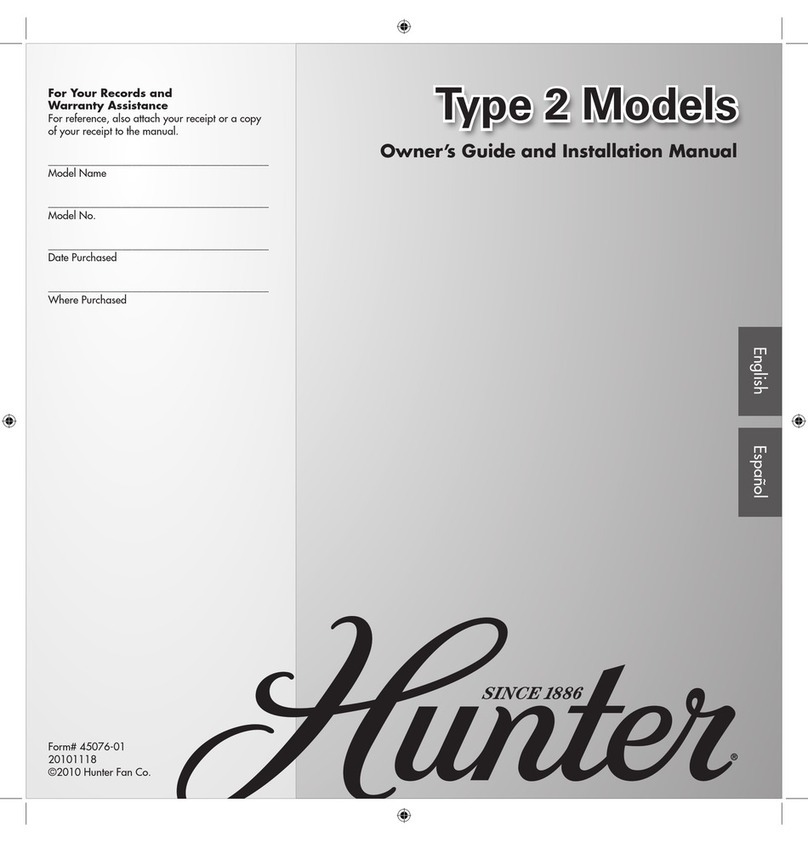
Hunter
Hunter Type 2 Models Owner's guide and installation manual
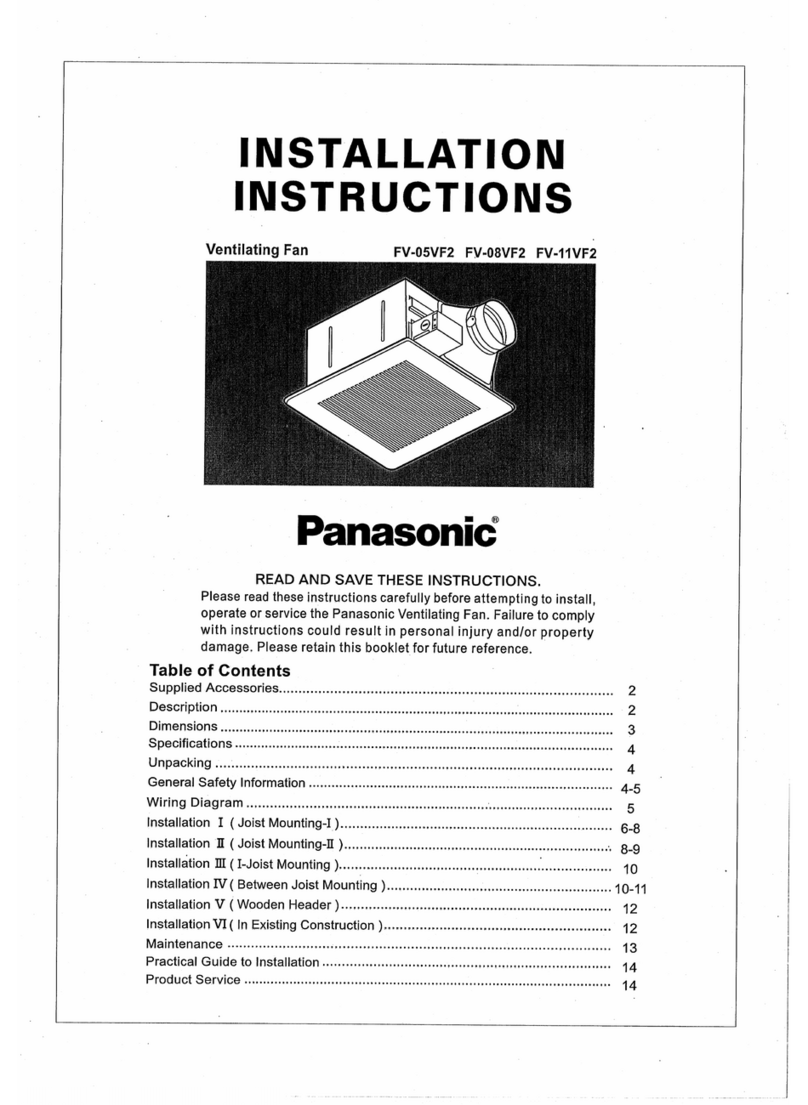
Sonnet
Sonnet FV-05VF2 installation instructions
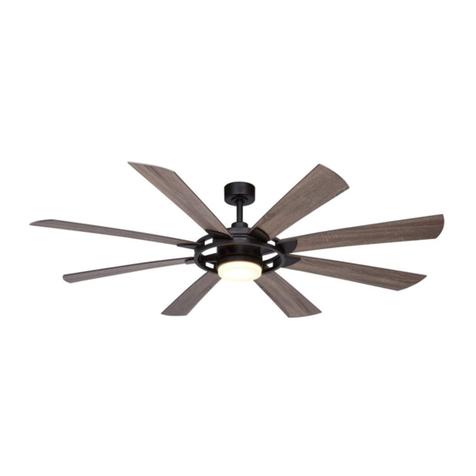
Vaxcel
Vaxcel F0092 quick start guide
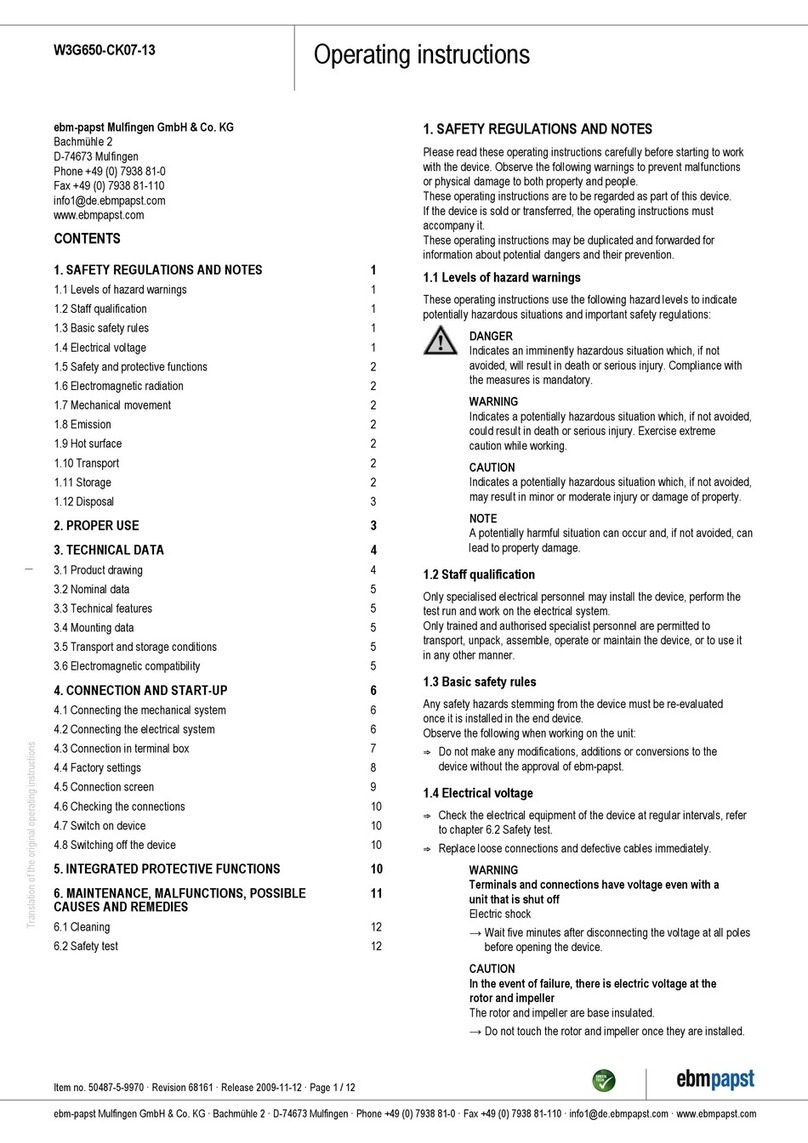
Ebmpapst
Ebmpapst W3G650-CK07-13 operating instructions

Gree
Gree FHBQ-D8-K Service manual