Rockwell Automation Allen-Bradley B Series User manual

ProDySC Dynamic Voltage Sag Corrector
1608P – Series B, 200 Amp Devices
User Manual

Important User Information
Solid-state equipment has operational characteristics differing from those of electromechanical equipment. Safety Guidelines for the
Application, Installation and Maintenance of Solid State Controls (publication SGI-1.1 available from your local Rockwell Automation sales
office or online at http://www.rockwellautomation.com/literature/) describes some important differences between solid-state equipment and
hard-wired electromechanical devices. Because of this difference, and also because of the wide variety of uses for solid-state equipment, all
persons responsible for applying this equipment must satisfy themselves that each intended application of this equipment is acceptable.
In no event will Rockwell Automation, Inc. be responsible or liable for indirect or consequential damages resulting from the use or application
of this equipment.
The examples and diagrams in this manual are included solely for illustrative purposes. Because of the many variables and requirements
associated with any particular installation, Rockwell Automation, Inc. cannot assume responsibility or liability for actual use based on the
examples and diagrams.
No patent liability is assumed by Rockwell Automation, Inc. with respect to use of information, circuits, equipment, or software described in
this manual.
Reproduction of the contents of this manual, in whole or in part, without written permission of Rockwell Automation, Inc., is prohibited.
Throughout this manual, when necessary, we use notes to make you aware of safety considerations.
ProDySC, Allen-Bradley, Rockwell Software, Rockwell Automation, andTechConnect are trademarks of Rockwell Automation, Inc. Trademarks not belonging to Rockwell Automation are property of
their respective companies.
Additional Resources
These documents contain additional information concerning related products from Rockwell Automation.
You can view or download publications at http:/www.rockwellautomation.com/literature/. To order paper copies of
technical documentation, contact your local Allen-Bradley distributor or Rockwell Automation sales representative.
WARNING: Identifies information aboutpractices or circumstances that can cause an explosion in a hazardous environment,
which may lead to personal injury or death, property damage, or economic loss.
ATTENTION: Identifies information about practices or circumstances that can lead to personal injury or death, property
damage, or economic loss. Attentions help you identify ahazard, avoid a hazard, and recognize the consequence.
SHOCK HAZARD: Labels may be on or inside the equipment, for example, a drive or motor, to alert people that dangerous
voltage may be present.
BURN HAZARD: Labels may be on or inside the equipment, for example, a drive ormotor, to alert people that surfaces may
reach dangerous temperatures.
IMPORTANT
Identifies informationthat is critical for successfulapplication and understanding of the product.
This product contains a sealed lithium battery which is permanently connected and should only be removed or replaced bytrained
professionals.
At the end ofits life, the battery contained in thisproduct should be collected separately from any unsorted municipal waste.
The collection and recycling of batteries helps protect the environment and contributes to the conservation ofnatural resources as
valuable materials are recovered.
Resource Description
Industrial Automation Wiring and Grounding Guidelines, publication 1770-4.1 Provides general guidelines for installing a Rockwell Automation industrial system.
Product Certifications website, http://www.ab.com Provides declarations of conformity, certificates, and other certification details.

Rockwell Automation Publication 1608P-UM006A-EN-P - April 2015 3
Table of Contents
Important User Information. . . . . . . . . . . . . . . . . . . . . . . . . . . . . . . . . . . . . . . . . . . . . . 2
Additional Resources. . . . . . . . . . . . . . . . . . . . . . . . . . . . . . . . . . . . . . . . . . . . . . . . . . . . . 2
Ch 1 - Introduction
Safety Considerations . . . . . . . . . . . . . . . . . . . . . . . . . . . . . . . . . . . . . . . . . . . . . . . . . . . . 5
Ch 2 - Installation
Installation Check List . . . . . . . . . . . . . . . . . . . . . . . . . . . . . . . . . . . . . . . . . . . . . . . . . . . 7
Inspecting and Unpacking. . . . . . . . . . . . . . . . . . . . . . . . . . . . . . . . . . . . . . . . . . . . . . . . 7
Location (Environment) . . . . . . . . . . . . . . . . . . . . . . . . . . . . . . . . . . . . . . . . . . . . . . . . . 7
Floor Mounting . . . . . . . . . . . . . . . . . . . . . . . . . . . . . . . . . . . . . . . . . . . . . . . . . . . . . . . . . 8
Clearance . . . . . . . . . . . . . . . . . . . . . . . . . . . . . . . . . . . . . . . . . . . . . . . . . . . . . . . . . . . . . . . 8
Circuit Breaker Recommendations . . . . . . . . . . . . . . . . . . . . . . . . . . . . . . . . . . . . . . . . 8
Electrical Terminations . . . . . . . . . . . . . . . . . . . . . . . . . . . . . . . . . . . . . . . . . . . . . . . . . . 9
Accessing Terminations . . . . . . . . . . . . . . . . . . . . . . . . . . . . . . . . . . . . . . . . . . . . . . . . . . 9
3-Wire vs. 4-Wire Configurations. . . . . . . . . . . . . . . . . . . . . . . . . . . . . . . . . . . . . . . . 10
3- Wire Models. . . . . . . . . . . . . . . . . . . . . . . . . . . . . . . . . . . . . . . . . . . . . . . . . . . . . . . . . 10
4- Wire Models. . . . . . . . . . . . . . . . . . . . . . . . . . . . . . . . . . . . . . . . . . . . . . . . . . . . . . . . . 11
Electrical Terminations and Ratings . . . . . . . . . . . . . . . . . . . . . . . . . . . . . . . . . . . . . . 12
Ch 3 - Communications
Dry Contacts. . . . . . . . . . . . . . . . . . . . . . . . . . . . . . . . . . . . . . . . . . . . . . . . . . . . . . . . . . . 13
Serial Communications Port. . . . . . . . . . . . . . . . . . . . . . . . . . . . . . . . . . . . . . . . . . . . . 14
Ch 4 - Applying Power and Operation
Applying Power . . . . . . . . . . . . . . . . . . . . . . . . . . . . . . . . . . . . . . . . . . . . . . . . . . . . . . . . 15
Operation. . . . . . . . . . . . . . . . . . . . . . . . . . . . . . . . . . . . . . . . . . . . . . . . . . . . . . . . . . . . . . 16
Ch 5 - Display Screen
Overview. . . . . . . . . . . . . . . . . . . . . . . . . . . . . . . . . . . . . . . . . . . . . . . . . . . . . . . . . . . . . . . 19
Home Screen . . . . . . . . . . . . . . . . . . . . . . . . . . . . . . . . . . . . . . . . . . . . . . . . . . . . . . . . . . . 21
System Status. . . . . . . . . . . . . . . . . . . . . . . . . . . . . . . . . . . . . . . . . . . . . . . . . . . . . . . . . . . 21
Voltage Sag Events . . . . . . . . . . . . . . . . . . . . . . . . . . . . . . . . . . . . . . . . . . . . . . . . . . . . . . 22
Voltage Sag Log. . . . . . . . . . . . . . . . . . . . . . . . . . . . . . . . . . . . . . . . . . . . . . . . . . . . . 22
Voltage Sag Detail . . . . . . . . . . . . . . . . . . . . . . . . . . . . . . . . . . . . . . . . . . . . . . . . . . 23
Voltage Sag RMS Voltage Charts. . . . . . . . . . . . . . . . . . . . . . . . . . . . . . . . . . . . . 24
Voltage Sag Notification . . . . . . . . . . . . . . . . . . . . . . . . . . . . . . . . . . . . . . . . . . . . 24
System Events . . . . . . . . . . . . . . . . . . . . . . . . . . . . . . . . . . . . . . . . . . . . . . . . . . . . . . . . . . 25
System Event Log. . . . . . . . . . . . . . . . . . . . . . . . . . . . . . . . . . . . . . . . . . . . . . . . . . . 25
System Event Detail. . . . . . . . . . . . . . . . . . . . . . . . . . . . . . . . . . . . . . . . . . . . . . . . . 26
System Event Notification. . . . . . . . . . . . . . . . . . . . . . . . . . . . . . . . . . . . . . . . . . . 27
System Configuration . . . . . . . . . . . . . . . . . . . . . . . . . . . . . . . . . . . . . . . . . . . . . . . . . . . 28
Model Information . . . . . . . . . . . . . . . . . . . . . . . . . . . . . . . . . . . . . . . . . . . . . . . . . . . . . 28
Run System Tests . . . . . . . . . . . . . . . . . . . . . . . . . . . . . . . . . . . . . . . . . . . . . . . . . . . . . . . 29
Diagnostics Mode. . . . . . . . . . . . . . . . . . . . . . . . . . . . . . . . . . . . . . . . . . . . . . . . . . . . . . . 29
Ch 6 - Maintenance
Preventative Maintenance . . . . . . . . . . . . . . . . . . . . . . . . . . . . . . . . . . . . . . . . . . . . . . . 31
Servicing . . . . . . . . . . . . . . . . . . . . . . . . . . . . . . . . . . . . . . . . . . . . . . . . . . . . . . . . . . . . . . . 34
Transient Voltage Surge Suppressor (TVSS) . . . . . . . . . . . . . . . . . . . . . . . . . . . . . . 36
Ch 7 - Specifications and Dimensions
Approximate Dimensions . . . . . . . . . . . . . . . . . . . . . . . . . . . . . . . . . . . . . . . . . . . . . . . 38

4Rockwell Automation Publication 1608P-UM006A-EN-P - April 2015
Table of Contents
Notes:

Rockwell Automation Publication 1608P-UM006A-EN-P - April 2015 5
Chapter 1
Introduction
The Allen-Bradley Bulletin 1608P ProDySC Dynamic Sag Corrector is
engineered to provide years of trouble-free voltage sag (dip) protection. The
patented DySC technology does not use batteries, requires only routine
maintenance, includes three-stage transient voltage, surge suppression, and has
unparalleled energy efficiency. Most electronic devices that are found in industry
today are susceptible to power disturbances. Momentary sags in line voltage can
reset or damage sensitive production equipment. The ProDySC provides
instantaneous and dynamic sag correction to help your equipment ride through
these common events. The ProDySC connects normal utility power directly to
the load until a voltage sag occurs. During a sag event, the ProDySC inverter is
activated-adding missing voltage to keep the load voltage within the normal
range. When utility power returns to normal, the inverter is deactivated and the
ProDySC is quickly ready to correct the next sag.
The ProDySC reports these voltage sag events through its integrated touch
screen display. It provides system status, voltage sag notification and history,
runtime statistics and system history in a simple and intuitive touch-based user
interface.
SafetyConsiderations The ProDySC is designed to operate in industrial applications. Follow these
guidelines to help ensure that the safety and installation of the ProDySC are
handled with appropriate care.
SHOCK HAZARD: The ProDySC has high voltage present up to 5 minutes after
disconnection from the AC line. If the exposed or disconnected terminals,
cables,orparts ofthe ProDySCaretouchedit canlead toseriousinjuries or even
death. Wait for a minimum of 5 minutes beforeperforminganyserviceortest
on the ProDySC after power is removed. High voltage remains if red status
indicatorsabovecapacitorbanks arelighted.Keep the cabinet doors closed and
lockedtohelpensurepropercoolingairflowand tohelp protectpersonnel from
dangerous voltages inside the ProDySC.
ATTENTION: - To reduce the risk offire or electric shock, install this ProDySC in
atemperature andhumidity controlled,indoorenvironment,freeof conductive
contaminants.
•Avoid installing the ProDySC directly near heat-emitting equipment such as ovens, heaters, or
furnaces.
•Ambient temperature must not exceed 40°C (104°F).
•Do not operate near water or excessive humidity (95% max).
•When punching or drilling holes for conduit fittings, take care to avoid dropping metallic particles
inside the enclosure as this can result in electrical damage.
•The system is not intended for outdoor use.
•The operating environment should be maintained within the parameters stated in this manual.
•Only authorized service personnel should perform service on the ProDySC.
•Help ensure all power is disconnected before installation or service.

6Rockwell Automation Publication 1608P-UM006A-EN-P - April 2015
Chapter 1
ATTENTION: Electrostatic discharge (ESD) can damage internal components.
Do not touch circuit boards or electronic componentswith hands or metal
objects.
•Help ensure the area around the ProDySC is clean and uncluttered.
•Observe all DANGER, CAUTION, and WARNING notices that are affixed to the inside and outside of the
equipment.

Rockwell Automation Publication 1608P-UM006A-EN-P - April 2015 7
Chapter 2
Installation
Installation Check List Before proceeding, take a few minutes to review the necessary steps to install your
ProDySC.
•All packing materials and restraints have been removed.
•The ProDySC is placed in its installed location.
•All conduits and cables are properly routed to the ProDySC.
•All power cables are properly terminated.
•A ground conductor is properly installed and terminated.
•If neutral connection is required, that it is properly terminated on the
ProDySC.
•The area around the installed ProDySC is clean and dust-free.
•Adequate work space exists around the ProDySC.
•Adequate lighting is provided around the ProDySC.
•Operational checks have been reviewed and completed.
Inspecting and Unpacking •Lift only at the base with a fork truck or pallet jack.
•Carefully inspect the outer packaging for evidence of damage during
transit. Do not install a damaged cabinet. Report any damage to the carrier
and contact your local sales or service immediately.
•Check the ProDySC label for correct model number with the packaging
list to verify you have received the correct voltage, current, and wiring
configurations.
•After removing the packaging material, inspect the contents for any
evidence of physical damage, and compare each item with the Bill of
Lading. If damage has occurred or shortages are evident, contact your
carrier immediately.
Location (Environment) Install the ProDySC in a protected environment. The location must provide
adequate airflow around the ProDySC in an atmosphere free from excessive dust,
corrosive fumes, or conductive contaminants. Do not operate the ProDySC in an
environment where the ambient temperature or humidity is beyond the specified
limits that are given in this manual.

8Rockwell Automation Publication 1608P-UM006A-EN-P - April 2015
Chapter 2 Installation
Floor Mounting Secure the ProDySC to the floor using fasteners and fittings appropriate for the
type of floor. Holes are provided in the base channels; see Figure 1 for mounting
dimensions.
Note: Top or bottom cable entry is allowed. See Figure 1 and Figure2 on page 9.
Figure 1 - Bottom View Floor Mount Dimensions
Clearance ProDySC doors hinge on both right and left. See Figure 26 on page 38 for
dimensions including door swing. Leave required clearances:
•Door swing must allow doors to open at least 90°
•3”[75 mm] on right side for air filter clearance when the door is open
•Left side clearance is required for bottom entry cable installation
Circuit Breaker
Recommendations
Branch circuit protection upstream of the ProDySC is required. Maximum
allowed circuit breaker ratings are listed in Table 1. Branch circuit protection that
is rated less than the ProDySC current rating may result in nuisance tripping.
Table 1 - Branch Circuit Protection Ratings
1.38
35
1.00
25
1.20
31
6X
.625
16
2.01
51
9.00
229
11.00
279
3.58
91
37.25
946
28.00
711
37.25
946
18.75
476
Removable Plate for
Bottom Conduit Entry
ProDySC Rating Max. MCCB Rating
200 A 250 A
WARNING: To reduce the risk of fire, use only on circuits that are provided with
250 ampere maximum branch circuit protection in accordance with the
National Electric Code ANSI/NFPA 70.

Rockwell Automation Publication 1608P-UM006A-EN-P - April 2015 9
Installation Chapter 2
Electrical Terminations Use a qualified electrician to install the ProDySC in compliance with all local,
and national electric codes. The ProDySC input (line) and output (load)
terminals are located behind the left door. Terminal details are shown in Figure 5
on page 12.
Accessing Terminations For top entry, remove the top gland plate, which is shown in Figure 2, to access
input and output terminals. This plate may be removed for drilling or punching
holes for conduit. Alternate bottom entry should utilize the bottom gland plate
shown in Figure 1. Access to the communications port is above the front doors, as
shown in Figure 6 on page 13. A separate conduit knock-out is provided for top
entry of communications conductors, as shown in Figure 2.
Note: When punching or drilling holes for conduit fittings, take care to avoid
dropping metallic particles inside the enclosure. Metallic contamination voids
the product warranty.
Figure 2 - Top Conductor Entry
3.00
76
11.00
279
2.00
51
9.00
229
20.75
527
51.07
1297
Area
Recommended
For Top
Conduit Entry
(Shown Without
Cover)
I/O Knockouts
WARNING: Metallic Particles inside the Enclosure Void the Warranty

10 Rockwell Automation Publication 1608P-UM006A-EN-P - April 2015
Chapter 2 Installation
3-Wire vs. 4-Wire
Configurations
ProDySC models are available for use with either 3-wire (L1, L2, L3) or 4-wire
(L1, L2, L3, N) sources. The input N conductor must be connected to 4-wire
models for proper operation. Do not connect a N conductor to 3-wire models.
3- Wire Models Bulletin 1608P part numbers containing V3 are configured for 3-wire source (L1,
L2, L3) and 3-wire loads (X1, X2, X3). Do not connect a N conductor to 3-wire
models. Figure 3 shows the 3-wire ProDySC system wiring schematically.
Figure 3 - ProDySC 3-Wire Configuration
Note for Canadian Users: The 200 A ProDySC models rated greater than 440Vhave not been
evaluated for compliance with CSA 22.2 No. 107.1-01 when connected to corner-grounded or
ungroundeddeltapower sources.ContactRockwell AutomationTechnical Support for assistance.
L3 X3
X1
X2L2
CB
CB
CB
Customer supplied
circuit breaker
GND GND
CBI
G
X1
X2
X3
L1
L2
L3
L1
ProDySC
Electronics
3-WIRE SOURCE

Rockwell Automation Publication 1608P-UM006A-EN-P - April 2015 11
Installation Chapter 2
4- Wire Models Bulletin 1608P part numbers containing V4 are configured for 4-wire source (L1,
L2, L3, N) and either 3-wire or 4-wire loads. The source N conductor must be
connected for proper operation of these models. Connect both input and output
N conductors to the bus bar labeled NEUTRAL (See Figure 5). Figure 4 shows
the 4-wire ProDySC system wiring schematically.
Figure 4 - ProDySC 4-Wire Configuration.
L3 X3
X1
X2L2
CB
CB
CB
Customer supplied
circuit breaker
GND GND
CBI
G
X1
X2
X3
L1
L2
L3
L1
ProDySC
Electronics
N N
N
4-WIRE SOURCE

12 Rockwell Automation Publication 1608P-UM006A-EN-P - April 2015
Chapter 2 Installation
Electrical Terminations and
Ratings
Input connections are marked L1, L2, and L3 for the source connections. Output
connections are marked X1, X2, and X3 for the load connections (See Figure 5).
In 4-wire models only, connect both input and output N conductors to the
NEUTRAL bus bar. Do not connect to the NEUTRAL bus bar in 3-wire
models. Replace all shields and covers when wiring is completed. The doors must
be closed and latched securely.
Figure 5 - Electrical Terminations
•Input/Output mechanical lugs accept AWG 6 to 350 kcmil [16 to 150 mm2] conductors. Tighten lugs to
275 lb-in [31 N-m]. Lugs require 5/16” hex key tool for installation.
•Input/Output mechanical lugs may be removed and replaced with pressure (crimp) lugs. Two 1/2” holes (1.75”
spacing) are provided.
•NEUTRAL Bus and Ground Bus are provided with 3/8”-16 threaded studs (9.525mm diameter). Tighten nuts to 25 lb-ft
(300 lb-in) [33.9 N-m].
WARNING: The ProDySC must be safety-grounded according to the National
Electrical Code.Inaddition, all local,state,andfederal regulationsapplicable to
the installation of electrical systems and accident prevention regulations must
be strictly observed
*5281'%86
1(875$/%86
$&287387
&211(&7,216
$&,1387
&211(&7,216
6+2:1:,7+
'22523(1

Rockwell Automation Publication 1608P-UM006A-EN-P - April 2015 13
Chapter 3
Communications
Both dry contacts (relays) that indicate status and a Serial Communications Port
(RS-232) are available for monitoring the ProDySC.
Dry Contacts Three relay contacts indicate ProDySC status. The contacts are form A and close
upon occurrence of the named event: (a) any SAG EVENT, when rms input
voltage drops below 88.5% of rated value; (b) OUTPUT OK, when output
voltage remains between 87% and 110%; and (c) a system ALARM event. The
relay contact ratings are 24V at 1A.
For access, remove the small metal cover from the top of the ProDySC
(See Figure 6).
•All wiring is to be Class 2, limited to 24 Volts, AC or DC.
•Acceptable wire gauges range from 24AWG to 12AWG (0.205-2.5mm2).
•Torque connections to 5.0 lb-in (0.6 N-m).
•For permanent installation of communications conductors, a standard
conduit knockout is located on the cabinet top (See Figure 2).
Figure 6 - Access Cover Location
I/O
COMM
PORT
ACCESS

14 Rockwell Automation Publication 1608P-UM006A-EN-P - April 2015
Chapter 3 Communications
Serial Communications Port The ProDySC serial port is a DE-9 female connector. The pin-out follows
standard RS-232 protocol: pin 2 is RxD, pin 3 is TxD and pin 5 is common
(return). All other pins are unused. Contacts are galvanically isolated from the
system power and grounds.
•Protection: The RS-232 port is ESD-protected to 15kV.
•Protocol: 57.6k bps, 8 data bits, one stop bit, no parity, flow control off
•Data packets are SLIP encoded (with 2 byte length field).
•Data accessible through this port includes load voltages, load currents,
status, and event and diagnostic logs.
•Consult Rockwell Automation technical support for specifications to the
ProDySC SLIP protocol.
Figure 7 - Serial Communications Port

Rockwell Automation Publication 1608P-UM006A-EN-P - April 2015 15
Chapter 4
Applying Power and Operation
Applying Power •Before applying power to the ProDySC, make certain there are no metal
filings or any conductive debris in or on any components inside the
cabinet.
•Verify ProDySC voltage rating matches ac source voltage.
•Verify all input/output wiring including grounding has been completed
and properly tightened.
•Replace all covers. Close all cabinet doors.
•Put CBI circuit breaker in the OFF position.
•Apply power from the upstream branch protection device. The ProDySC
touch screen becomes active and displays "System Offline" in the upper left
corner.
•Wait for the ProDySC to display "READY TO CLOSE CBI" in the upper
left corner of the touch screen. Rotate CBI circuit breaker to the ON
position. The ProDySC electronics become energized in this mode and
power is supplied to the load.
•Verify that the touch screen displays "OK" in the upper left corner. Verify
that the voltage, current, and frequency readings in the status display are
correct.
•If a "Critical" or "Fatal" system event appears on the touch screen,(1) rotate
CBI circuit breaker to the off position (2) call for technical support.
•Verify output (load) voltage is present and within its nominal rating.
IMPORTANT
NOTICE: If the ProDySC input power is cycled in the sequence OFF--ON--OFF--
ON within one minute, a “Limit Cycle Timeout” alarm will occur. In such a case,
sag correction will be inhibited for one minute, after which the alarm will
automatically reset.

16 Rockwell Automation Publication 1608P-UM006A-EN-P - April 2015
Chapter 4 Applying Power and Operation
Operation
The ProDySC contains three power electronics modules (one module per phase)
and controls that continuously monitor the line voltage. The modules are series-
connected to the input line, and operate by adding the compensating voltage
needed to restore the line to its nominal output. When the utility line voltage is
within normal range the ac static switch components remain closed and no
compensating voltage is added. When an insufficient line voltage event occurs,
the static switches open and the sag-correcting electronics quickly add the
balance of voltage necessary to regulate the load voltage.
The ProDySC accepts line input power over 3 wires into terminals L1, L2, L3
and provides sag compensated three-phase output power at terminals X1, X2,
and X3. In 4-wire systems the input Neutral is connected directly to the output
Neutral terminal.
A touchscreen display provides indication of the status of the ProDySC
operation. After power is switched on, the green "OK" box will be displayed in
the upper left hand corner of the display, indicating that the output voltage is
within a normal range of -13% to +10% of nominal.
A red "FAULT" box isdisplayed in the upper left hand corner of the display when
a fault condition is present on the ProDySC. During this period sag correction is
disabled and the ProDySC will continue to bypass the utility voltage directly to
the load through the static bypass path. An orange "FAULT OVER" box is
displayed when the previous fault condition has cleared. Sag correction will
remain inhibited until the reset period has expired (approximately 1 minute).
A blue "SYSTEM OFFLINE" box is displayed when the input circuit breaker
(CBI) is open.
SHOCK HAZARD: Dangerous voltages are present within the ProDySC System.
The unit should never be operated with the enclosure door open except by
qualified and authorized personnel who are trained and familiar with the
operation of the unit and the location ofcomponents and voltages. Failure to
comply with this warning could result in injury or death.

Rockwell Automation Publication 1608P-UM006A-EN-P - April 2015 17
Applying Power and Operation Chapter 4
A list of conditions and indications is given in Table 2. Under some conditions
the ProDySC will automatically open CBI to prevent damage to the ProDySC or
to protect loads from severe voltage unbalance. Those conditions are the last four
listed in the table below. Refer to Chapter 5 for further information on system
alarms and status display.
Table 2 - Operational Conditions and Indications
*Thetouchscreenwill powerdownif bothinput and outputvoltagesfallbelow 75%of nominal.
An error message will be displayed while the red or orange text box is displayed. Refer to
Chapter 5 for further information on accessing fault codes and status history.
CONDITION DEFINITION DISPLAY STATUS* INVERTER MODE
Normal: 88.5% < V LINE < 110% Green “OK” Standby Static BP
Sag Event: V LINE < 88.5% for less
than specified runtime Green “OK” Running Inverter
Runtime Exceeded: Cumulative runtime
exceeded Blinks Red, thenOrange for 1
min. Repeats if condition
persists
Inhibited Static BP
Normal Mode,
Overload: Load current > 110% Red during OL condition,
Orange for 1 min. after OL ends Inhibited Static BP
Output Over-Current
while inverter running
(I2t)
Load current > 150%
for 3 cycles Blinks Red, then Orange for 1
min. Repeats if condition
persists
Inhibited Static BP
Inverter Module
Over-temperature:
Module temperature
limit exceeded Blue, ProDySC offline Disconnected CBI Open
ProDySC cabinet
Over-temperature:
Internal temperature
limit exceeded Blue, ProDySC offline Disconnected CBI Open
Static Switch Failure: Open SCR(s) Blue, ProDySC offline Disconnected CBI Open
Main Fuse Open Open Fuse(s) Blue, ProDySC offline Disconnected CBI Open

18 Rockwell Automation Publication 1608P-UM006A-EN-P - April 2015
Chapter 4 Applying Power and Operation
Notes:

Rockwell Automation Publication 1608P-UM006A-EN-P - April 2015 19
Chapter 5
Display Screen
Overview The ProDySC® touch screen display is a window to voltage sags and ProDySC
protection. The display provides system status, voltage sag notification and
history, runtime statistics and system history in a simple and intuitive touch-
based user interface.
When the system first starts, a welcome screen displaying the ProDySC product
logo appears. This screen disappears after 5 seconds, when the “Home” screen
appears.
Note: The touch screen is optimized for use with a plastic stylus or bare finger.
Atinstallation time performthe following
stepstoconfigure your system:
Step 1: Press the “CONFIG” button
at the bottom of the “HOME” screen
(See Figure 8).
Figure 8 - Home Screen
Step 2: Begin calibration by pressing
“CALIBRATE TOUCH SENSOR”
(See Figure 9).
Figure 9 - System Configuration

20 Rockwell Automation Publication 1608P-UM006A-EN-P - April 2015
Chapter 5 Display Screen
Note: To recalibrate from any screen, hold anywhere on the screen for 10 seconds. You will see a
small progress bar at the bottom of the screen. When the progress bar reaches 100 percent, the
calibration screen will open.
Step 3: The “Touch Screen
Calibration” screen will then appear
(See Figure 10). Press and hold on the
center of the touch target, release when
the touch target begins to flash. Repeat
with the next two touch targets.
Step 4: The screen uses the new
calibration configuration. You can test
the calibration before saving by
pressing anywhere on the screen to
ensure the touch target appears where
you press. After testing, press the
“SAVE” button. Press the “BACK”
button to return to the “System
Configuration” screen.
Figure 10 - Touch Screen Calibration
Step 5: Set date and time by pressing
“SET SYSTEM CLOCK” in “System
Configuration.” Press “SAVE” when
completed.
Figure 11 - Set System Date and Time
Other manuals for Allen-Bradley B Series
3
This manual suits for next models
1
Table of contents
Other Rockwell Automation Power Distribution Unit manuals
Popular Power Distribution Unit manuals by other brands
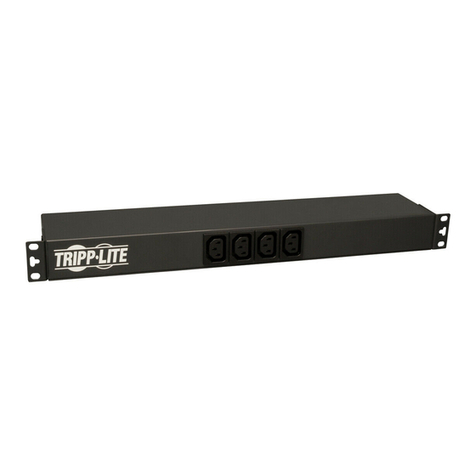
Tripp Lite
Tripp Lite PDUH20DV owner's manual
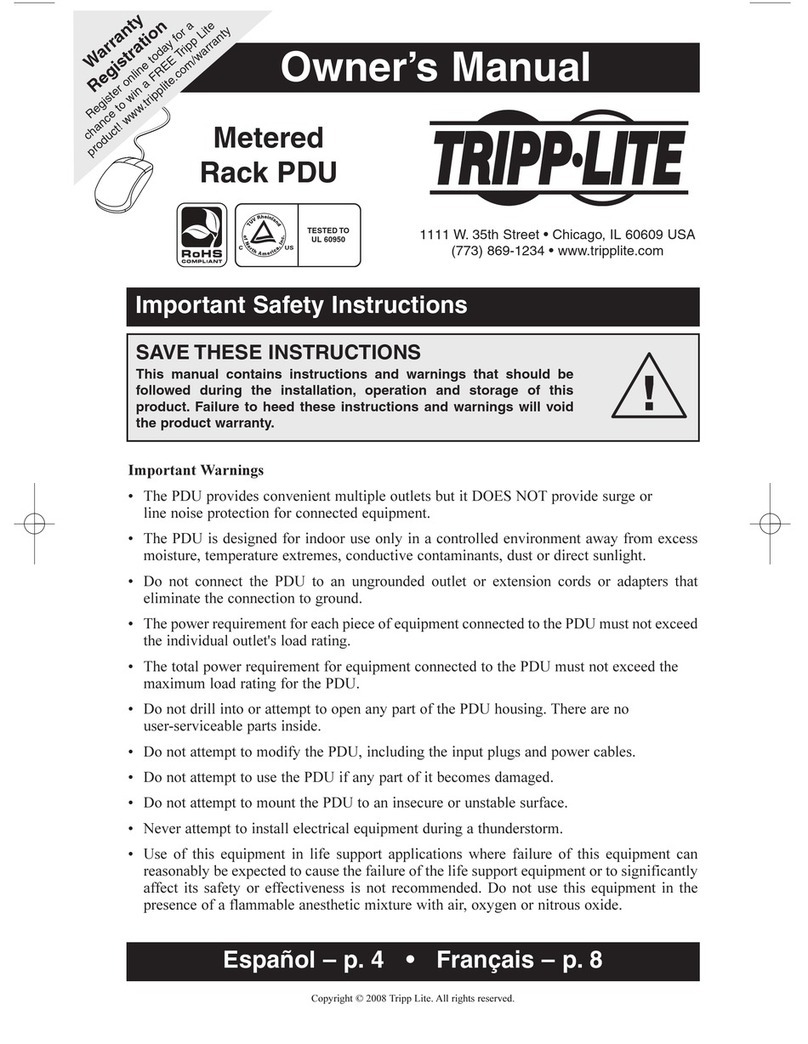
Tripp Lite
Tripp Lite Metered Rack PDU owner's manual
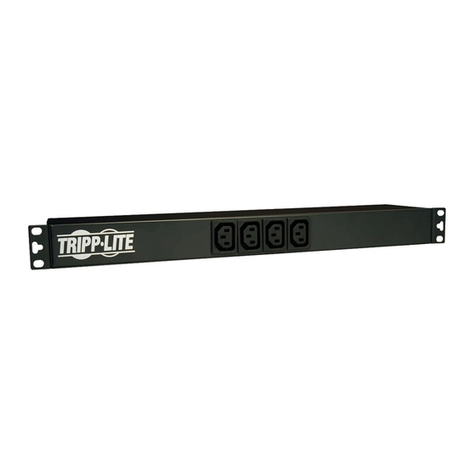
Tripp Lite
Tripp Lite PDUNV Specifications

Tripp Lite
Tripp Lite Power Distribution Unit (PDU) PDU6K owner's manual
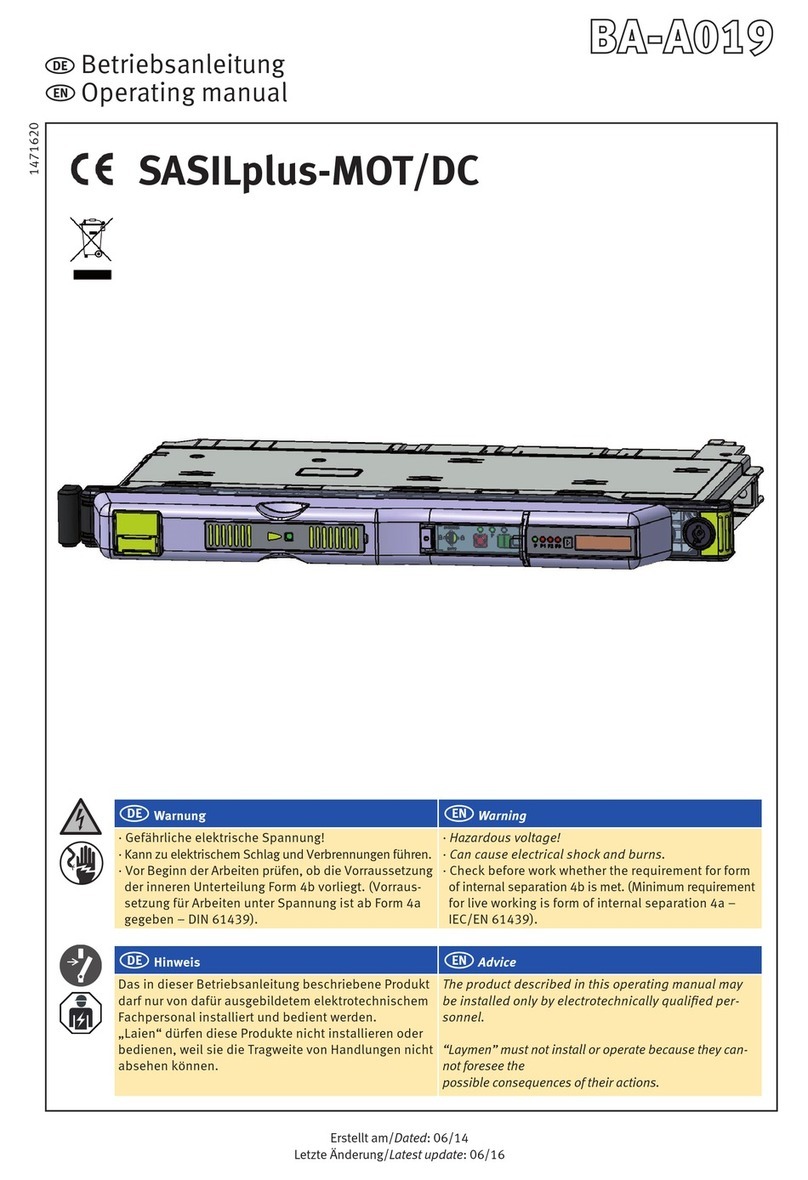
JEAN MÜLLER
JEAN MÜLLER SASILplus-MOT Series operating manual
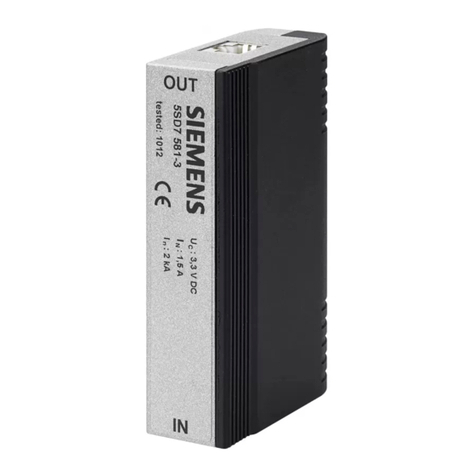
Siemens
Siemens 5SD7 581-3 operating instructions