Rohm LAPIS MK715x1 User manual

FEXK715x1EK1A_HardManual-01
MK715x1 Evaluation Kit(MK715x1EK1A)
MK715x1 Evaluation Kit Plus(MK715x1EK1AP)
Hardware Manual
Issue Date: Dec. 1, 2020

MK715x1EK1A Hardware Manual
FEXK715x1EK1A_HardManual-01 i
Precautions for the Specification
1) Contents of the Specification are the information at the time of their issuance. The information contained herein
is subject to change without notice.
2) LAPIS Technology has used reasonable care in preparing the information included in the Specification, but
LAPIS Technology does not warrant that such information is error free. LAPIS Technology assumes no liability
whatsoever for any damages incurred by you resulting from errors in or omissions from the information included
herein.
3) The technical information specified herein is intended only to show the typical functions of the Products and
examples of application circuits for the Products. No license, expressly or implied, is granted hereby under any
intellectual property rights or other rights of LAPIS Technology or any third party with respect to the information
contained in this document; therefore LAPIS Technology shall have no responsibility whatsoever for any dispute,
concerning such rights owned by third parties, arising out of the use of such technical information.
4) The Specification contains information related to the LAPIS Technology’s copyright and technical know-how.
Any use of them other than pertaining to the usage of appropriate products is not permitted. Further, the
Specification, in part or in whole, may not be reprinted or reproduced and disclosed to third parties without prior
consent of LAPIS Technology.
Precautions for the Products
●Precautions for Safety
1) The Products are designed and produced for application in ordinary electronic equipment (AV equipment, OA
equipment, telecommunication equipment, home appliances, amusement equipment, etc.).
2) For use of our Products in applications requiring a high degree of reliability (as exemplified below), please
contact and consult with a LAPIS Technology representative: transportation equipment (i.e. cars, ships, trains),
primary communication equipment, traffic lights, fire/crime prevention, safety equipment, medical systems,
servers, solar cells, and power transmission systems.
3) Do not use our Products in applications requiring extremely high reliability, such as aerospace equipment,
nuclear power control systems, and submarine repeaters.
4) The Products are designed for use in a standard environment and not in any special environments.
Application of the Products in a special environment can deteriorate product performance. Accordingly,
verification and confirmation of product performance, prior to use, is recommended if used under the following
conditions:
[a] Use in various types of liquid, including water, oils, chemicals, and organic solvents.
[b] Use outdoors where the Products are exposed to direct sunlight, or in dusty places.
[c] Use in places where the Products are exposed to sea winds or corrosive gases, including Cl2, H2S, NH3,
SO2, and NO2.
[d] Use in places where the products are exposed to static electricity or electromagnetic waves.
[e] Use in environment subject to strong vibration and impact.
[f] Use in proximity to heat-producing components, plastic cords, or other flammable items.
[g] Use involving sealing or coating the Products with resin or other coating materials.
[h] Use of the Products in places subject to dew condensation.
[i] Use in an environment where the temperature is always low, such as in a freezer.
[j] Use in an environment where the temperature change of this product increases due to the
influence of the surrounding heat source
(Example: IH cooking heaters, industrial robots, FAequipment, infrastructure equipment, etc.)
5) The Products might receive the radio wave interference from electronic devices such as Wireless LAN devices,
Bluetooth devices, digital cordless telephone, microwave oven and so on that radiate electromagnetic wave.
6) The Products are not radiation resistant.
7) Verification and confirmation of performance characteristics of Products, after on-board mounting, is advised.

MK715x1EK1A Hardware Manual
FEXK715x1EK1A_HardManual-01 ii
8) Confirm that operation temperature is within the specified range described in the Specification.
9) Although LAPIS Technology is continuously working to improve product reliability and quality, semiconductors
can break down and malfunction due to various factors. Therefore, if product malfunctions may result in serious
damage, including that to human life, sufficient fail-safe measures must be taken, including the following:
[a] Installation of protection circuits or other protective devices to improve system safety.
[b] Installation of redundant circuits in the case of single-circuit failure
10) Failure induced under deviant condition from what defined in the Specification can not be guaranteed.
11) This product is a specification to radiate the radio wave. It is necessary to acquire the attestation of decided
Radio Law of each region used to use the equipment that radiates the radio wave.
Please inquire about the attestation of Radio Law that this product acquires.
12) When product safety related problems arises, please immediately inform to LAPIS Technology, and consider
technical counter measure.
●Precautions for Reference Circuits
1) If change is made to the constant of an external circuit, allow a sufficient margin due to variations of the
characteristics of the Products and external components, including transient characteristics, as well as static
characteristics.
2) The reference circuit examples, their constants, and other types of information contained herein are applicable
only when the Products are used in accordance with standard methods. Therefore, if mass production is
intended, sufficient consideration to external conditions must be made.
●Precaution for Electrostatic
This product is Electrostatic sensitive product, which may be damaged due to Electrostatic discharge. Please
take proper caution during manufacturing and storing so that voltage exceeding Product maximum rating won't be
applied to the Products. Please take special care under dry condition (Grounding of human body / equipment /
solder iron, isolation from charged objects, setting of Ionizer, friction prevention and temperature / humidity control
etc.)
● Precautions for Storage / Transportation
1) Product performance and connector mating may deteriorate if the Products are stored in the following places:
[a] Where the Products are exposed to sea winds or corrosive gases, including Cl2, H2S, NH3, SO2and NO2.
[b] Where the temperature or humidity exceeds those recommended by LAPIS Technology Temperature: 5°C
to 40°C, Humidity 40% to 60%
[c] Storage in direct sunshine or condensation.
[d] Storage in high Electrostatic.
2) Even under LAPIS Technology recommended storage condition, connector mating, mountability, and heat
resistance of products over 1 year old may be degraded.
3) Store / transport cartons in the correct direction, which is indicated on a carton as a symbol, otherwise bent
leads may occur due to excessive stress applied when dropping of a carton.
● Precaution for Product Label
QR code printed on LAPIS Technology product label is only for internal use, and please do not use at customer
site.
It might contain internal products information that is inconsistent with product information.
● Precaution for Disposition
When disposing Products, please dispose them properly with an industry waste company.

MK715x1EK1A Hardware Manual
FEXK715x1EK1A_HardManual-01 iii
●Prohibition Regarding Intellectual Property
LAPIS Technology prohibits the purchaser of the Products to exercise or use the intellectual property rights,
industrial property rights, or any other rights that either belong to or are controlled by LAPIS Technology, other than
the right to use, sell, or dispose of the Products.
● The other precautions
1) Please use the Products in accordance with any applicable environmental laws and regulations, such as the
RoHS Directive. For more details, including RoHS compatibility, please contact a ROHM sales office. LAPIS
Technology shall have no responsibility for any damages or losses resulting non-compliance with any
applicable laws or regulations.
2) When providing our Products and technologies contained in the Specification to other countries, you must
abide by the procedures and provisions stipulated in all applicable export laws and regulations, including
without limitation the US Export Administration Regulations and the Foreign Exchange and Foreign Trade Act.
Copyright 2020 LAPIS Technology Co., Ltd.
2-4-8 Shinyokohama, Kouhoku-ku,
Yokohama 222-8575, Japan
http://www.lapis-tech.com/en/

MK715x1EK1A Hardware Manual
FEXK715x1EK1A_HardManual-01 iv
Preface
This document outlines the hardware of the MK715x1 evaluation kit [MK715x1EK1A] and MK715x1 evaluation
kit Plus [MK715XxEK1AP] equipped with Bluetooth®5 compatible Bluetooth low energy module MK715x1
[MK71521 or MK71511] made by Lapis Technology.
This evaluation kit is pre-installed with the AT command application that easily realizes Bluetooth®Low Energy
communication by using a simple AT command via UART.
The following related documents are available, so please refer to them if necessary.
⚫MK71511 Data Sheet
⚫MK71521 Data Sheet
⚫MK715x1 Software Development Startup Guide
⚫BLE Tool User’s Manual
⚫MK715x1 AT command application Quick Reference Guide
⚫MK715x1 AT command application User’s Manual
Note: In this document, MK715x1 refers to both MK71511 and MK71521.
•Bluetooth®is a registered trademark of Bluetooth SIG, Inc.
•All other company and product names are the trademarks or registered trademarks of the respective companies.

MK715x1EK1A Hardware Manual
FEXK715x1EK1A_HardManual-01 v
Table of Contents
Preface........................................................................................................................................................................... iv
Table of Contents............................................................................................................................................................v
1. Overview ..................................................................................................................................................................1
1.1 Handling precautions.........................................................................................................................................1
1.2 Main features of MK715x1EK1A/MK715x1EK1AP ...........................................................................................1
1.3 MK715x1EK1A/MK715x1EK1APconfiguration..................................................................................................2
1.4 Lineup................................................................................................................................................................2
2. Hardware specifications...........................................................................................................................................3
2.1 Power supply .....................................................................................................................................................4
2.2 Switch ................................................................................................................................................................5
2.2.1 Reset Button..................................................................................................................................................5
2.2.2 User buttons..................................................................................................................................................5
2.2.3 DIP-SW..........................................................................................................................................................6
2.3 LED....................................................................................................................................................................7
2.3.1 User LEDs.....................................................................................................................................................7
2.3.2 Power LED ....................................................................................................................................................8
2.3.3 UART status LED..........................................................................................................................................8
2.4 Virtual COM port................................................................................................................................................9
2.5 Current measurement pin................................................................................................................................10
2.6 Solder bridge ...................................................................................................................................................11
2.7 The pin assignment for External interface.......................................................................................................12
3. How to use sample software..................................................................................................................................14
3.1 PC set up.........................................................................................................................................................14
3.2 Smartphone Set up..........................................................................................................................................14
3.3 Terminal Software Operation...........................................................................................................................15
3.4 BLE Tool operation ..........................................................................................................................................15
3.4.1 Application start...........................................................................................................................................15
3.4.2 Data communication....................................................................................................................................16
3.4.3 Read device information..............................................................................................................................17
A. Appendix ................................................................................................................................................................18
A.1 Correspondence between each evaluation kit and Nordic SDK Example Project ..........................................18
A.2 Example Project modification steps required for MK71511EK1......................................................................18
Revision History............................................................................................................................................................23

MK715x1EK1A Hardware Manual
1. Overview
FEXK715x1EK1A_HardManual-01 1
1. Overview
1.1 Handling precautions
・MK715x1EK1A/MK715x1EK1AP can be used only for evaluating MK715x1. We do not take any responsibility
for any direct or indirect damage caused by installing this product in your product.
・We are not responsible for any modification or illegal use of this development kit.
1.2 Main features of MK715x1EK1A/MK715x1EK1AP
This evalution kit has access to all I/O and interface via connectors, and has user programmable 4 LEDs and 4
buttons. This evalution kit is compatible with Arduino Uno R3(Rev.3) and alllows the use of third paty Arduino Uno
R3 compatible shields. This evaluation kit is a great strating point for developing almost any Bluetooth®5.X Low
Energy application.
⚫Easy power supply by USB connection
⚫Coin battery(CR2032) holder
⚫Arduino Uno R3 compatible connector that can use a third party shield
⚫All I/O and interfaces can be accessed via connectors
⚫4 LEDs, 4 push buttons, 4 bit DIP-SW and reset button can be used
⚫Current measurement pin
⚫Connector for high frequency(RF) measurement
⚫External NFC antenna terminal(valid for MK71521EK1A/MK71521EK1AP only)
⚫Virtual COM port
Top View Bottom View
Fig. 1-1 : MK715x1EK1A appearance

MK715x1EK1A Hardware Manual
1. Overview
FEXK715x1EK1A_HardManual-01 2
1.3 MK715x1EK1A/MK715x1EK1APconfiguration
When you receive the MK715x1EK1A/MK715x1EK1AP, make sure that the following items are all included in
the kit. If you find any broken or missing items, please contact the distributor where you purchased the product or
the ROHM sales office.
MK715x1EK1A configuration
Component
Quantity
MK715x1 evaluation board
1
MK715x1EK1AP configuration
Component
Quantity
MK715x1 evaluation board
1
USB cable
1
J-Link LITE
1
1.4 Lineup
The MK715x1 evaluation kit has the following lineup depending on the installed modules and accessories.
Product name
Module
Accessories
MK71511 evaluation kit (MK71511EK1A)
MK71511
-
MK71521 evaluation kit (MK71521EK1A)
MK71521
-
MK71511 evaluation kit Plus (MK71511EK1AP)
MK71511
USB cable、J-Link LITE
MK71521 evaluation kit Plus (MK71521EK1AP)
MK71521
USB cable、J-Link LITE
※J-Link LITE is licensed for MK71511EK1/MK71521EK1.
※Use of MK71511EK1/ MK71521EK1 for purposes other than evaluation is prohibited.
Fig. 1-2 : MK715x1EK1A/MK715x1EK1AP Lineup
MK71511 evaluation kit (MK71511EK1A)
MK71521 evaluation kit (MK71521EK1A)
MK71511 evaluation kit Plus (MK71511EK1AP)
MK71521 evaluation kit Plus (MK71521EK1AP)

MK715x1EK1A Hardware Manual
2. Hardware specifications
FEXK715x1EK1A_HardManual-01 3
2. Hardware specifications
If you need the schematic/BOM list for this evaluation kit, please contact your distributor or ROHM sales
representative.
Fig. 2-1: Layout of MK715x1EK1A(Top View)
J-Link
Micro-USB
Power,Programming & Virtual COM
EXT. Power
Power Switch
User Btn2
Reset Button
NFC Antenna
Terminal
(Valid for MK71521)
User Btn4
User Btn1
User Btn3
Shield Current
Monitor
MK71511 or MK71521
Module Current
Monitor
UART Status LEDs
Power LED
User LED4
User LED2
User LED1
User LED3
RF Connector
DIP-SW

MK715x1EK1A Hardware Manual
2. Hardware specifications
FEXK715x1EK1A_HardManual-01 4
2.1 Power supply
This evalution kit can operate with three types of power supplies.
⚫USB
⚫Coin battery(CR2032)
⚫External power supply via 2.54mm pitch through hole connector (1.7V~3.6V)
These power supplies can coexist because the reverse current does not flow in the protection diode. If the voltage
drop due to the protection diode can not be ignored, short the protection diode with a solder bridge(SB_3V3,
SB_BAT, SB_EXT).
Normally, it is used by 5V power supply from USB and supplied to the 3.3V LDO regulator in FT232RQ and Arduino
Uno R3 compatible Shield. VDDIO, VSHLD, and VBMD are supplied from the 3.3V LDO regulator.
※When powering from USB, avoid turning off the Power SW for a long time.
※USB, Coin battery, External power can be safely connected simultaneously only if the protection diode is not
shorted.
※Take care not to damage the power supply if the protection diode is short-circuited.
Fig. 2-2 : Power supply

MK715x1EK1A Hardware Manual
2. Hardware specifications
FEXK715x1EK1A_HardManual-01 5
2.2 Switch
2.2.1 Reset Button
The P0.21 port of MK715x1 is assigned to the hardware reset function. In this evaluation kit, the reset button
is connected to P0.21. P0.21 (P0_21_RESET in Figure 2-3) is also connected to the Arduino Uno R3
compatible shield connector.
Fig. 2-3: Reset Button
Pushing the reset button puts MK715x1and Arduino Uno R3 compatible shield in reset.
P0.21 and reset button can be completely separated by cutting the solder bridge(SB_RESET).
2.2.2 User buttons
With this evaluation kit, 4 user buttons (Btn1, Btn2, Btn3, Btn4) are available. All buttons are active low (press the
button to connect to GND). In order for the user button to work properly, enable the internal pull-up resistor of the
GPIO port assigned to the user button. GPIO ports and push buttons can be completely separated by cutting the
solder bridge(SB_Btn1, SB_Btn2, SB_Btn3, SB_Btn4). The circuit configuration and port assignment are shown
below.
Fig. 2-4 : User buttons
Button
GPIO Port
Btn1
P0.13
Btn2
P0.14
Btn3
P0.15
Btn4
P0.16
Table. 2-1 : User button GPIO port assignment

MK715x1EK1A Hardware Manual
2. Hardware specifications
FEXK715x1EK1A_HardManual-01 6
2.2.3 DIP-SW
4-bit DIP-SW connected to GPIO is available. Each bit is pulled up to VDDIO. GPIO and DIP-SW can be
completely separated by cutting the solder bridge(SB_P22, SB_P23, SB_P26, SB_P27). The circuit configuration,
port assignment for each bit, and initial settings are shown below.
Fig. 2-5 : DIP-SW
Symbol
Pin No.
GPIO Port
Initial setting
SW1
1
P0.22
On
2
P0.23
Off
3
P0.26
Off
4
P0.27
Off
Table. 2-2 : port assignment for each bit, and initial settings

MK715x1EK1A Hardware Manual
2. Hardware specifications
FEXK715x1EK1A_HardManual-01 7
2.3 LED
4 User LEDs, 1 Power LED, 2 UART status LEDs are available in this evaluation kit.
2.3.1 User LEDs
4 User LEDs (green) are connected to GPIO port. The LEDs are active low driven. GPIO port should be in high
drive mode. GPIO and LED can be completely separated by cutting the solder bridge(SB_LED1, SB_LED2,
SB_LED3, SB_LED4). The circuit configuration and port assignment are shown below.
Fig. 2-6 : User LEDs
LED
GPIO Port
LED1
P0.17
LED2
P0.18
LED3
P0.19
LED4
P0.20
Table. 2-3 : LED GPIO port assignment

MK715x1EK1A Hardware Manual
2. Hardware specifications
FEXK715x1EK1A_HardManual-01 8
2.3.2 Power LED
The Power LED (red) lights on when the power (VDDIO) to the MK715x1 is turned on.
Fig. 2-7 : Power LED
2.3.3 UART status LED
The UART status LED (green) flashes during UART transmission and reception.
Fig. 2-8 : UART status LED

MK715x1EK1A Hardware Manual
2. Hardware specifications
FEXK715x1EK1A_HardManual-01 9
2.4 Virtual COM port
Serial communication is easily possible between the MK715x1 and PC. A virtual COM USB device connected
to four GPIO ports allows UART communication with or without hardware flow control. GPIO and UART line can be
completely separated by cutting the solder bridge(SB_P05, SB_P06, SB_P07, SB_P08).
Fig. 2-9 : Virtual COM Port
MK715x1 Port Name
MK715x1Function
Solder Bridge
FT232RQ Function
P0.05
RTS
SB_P05
CTS
P0.06
TXD
SB_P06
RXD
P0.07
CTS
SB_P07
RTS
P0.08
RXD
SB_P08
TXD
Table. 2-4 : Virtual COM Port assignment

MK715x1EK1A Hardware Manual
2. Hardware specifications
FEXK715x1EK1A_HardManual-01 10
2.5 Current measurement pin
The evaluation kit has two sets(JP_BMD, JP_SHLD) of current measurement pins. JP_BMD is for MK715x1
current measurement, JP_SHLD is for Arduino Uno R3 compatible shields current measurement(VSHLD only). For
current measurement, remove the solder bridge(SB_BMD or SB_SHDL) and insert an ammeter between JP_BMD
or JP_SHLD.
※Only the current flowing into MK715x1 via VBMD can be measured. The current sunk through the GPIO port
cannot be measured.
Fig. 2-10 : Current measurement pin
VBMD

MK715x1EK1A Hardware Manual
2. Hardware specifications
FEXK715x1EK1A_HardManual-01 11
2.6 Solder bridge
The evaluation kit has many solder bridges. Most solder bridges are used to disconnect components on the
board from GPIO ports. GPIO port with separated components can be used to interface with external circuits
connected to the connector. At shipment, all GPIO ports except for P0.00 and P0.01 are connected to the external
interface connector.
Fig. 2-11 : GPIO port separated from external interface connector
Solder Bridge
Default
Function
SB_P00
Open
Separate P0.00 from P00 in CNA5
SB_P01
Open
Separate P0.01 from P01 in CNA5
SB_XL1
Open
Separate P0.00 from 32.768kHz-SPXO
SB_XL2
Open
Separate P0.01 from 32.768kHz-SPXO
SB_P09
Closed
Separate P0.09 from P09 in CNA5(using NFC)
SB_P10
Closed
Separate P0.10 from P10 in CNA5(using NFC)
SB_LED1
Closed
Separate P0.17 from LED1
SB_LED2
Closed
Separate P0.18 from LED2
SB_LED3
Closed
Separate P0.19 from LED3
SB_LED4
Closed
Separate P0.20 from LED4
SB_BTN1
Closed
Separate P0.13 from Btn1
SB_BTN2
Closed
Separate P0.14 from Btn2
SB_BTN3
Closed
Separate P0.15 from Btn3
SB_BTN4
Closed
Separate P0.16 from Btn4
SB_RESET
Closed
Separate P0.21 from RESET Button
SB_BMD
Closed
To enable JP_BMD for current measurement
SB_SHLD
Closed
To enable JP_SHLD for current measurement
SB_3V3
Open
To short the diode for 3.3V output protection from UART Interface IC
SB_BAT
Open
To short the CR2032 coin battery protection diode
SB_EXT
Open
To short the diode for external power supply protection
SB_P05
Closed
Separate P0.05 from UART Interface
SB_P06
Closed
Separate P0.06 from UART Interface
SB_P07
Closed
Separate P0.07 from UART Interface
SB_P08
Closed
Separate P0.08 from UART Interface
SB1
Closed
Separate UART Interface IC from IO power supply
SB2
Closed
Separate 3.3V output from UART Interface IC
SB_P22
Closed
Separate P0.22 from DIP-SW
SB_P23
Closed
Separate P0.23 from DIP-SW
SB_P26
Closed
Separate P0.26 from DIP-SW
SB_P27
Closed
Separate P0.27 from DIP-SW
Table. 2-5 : Solder bridge shipping condition

MK715x1EK1A Hardware Manual
2. Hardware specifications
FEXK715x1EK1A_HardManual-01 12
2.7 The pin assignment for External interface
Equipped with 2.54mm pitch connector as external interface for IO signal from MK715x1.
Open
Btn3
Btn4
AREF
VSHLD
VSHLD
VSHLD
Open
A5
A4
A3Btn1
Btn2
LED1
LED2
LED3
LED4
DipSW(1)
DipSW(2)
DipSW(4)
DipSW(3)
D0
D1
D2
D3
D4
D5
D6
D7
D8
D9
D10
D11
D12
D13
Ground Ground
SDA
SCL
A2
A1
A0
nRESET
RTS
GPIO
GPIO
TXD
CTS
RXD
GPIO
GPIO
GPIO
GPIO
GPIO/AIN0
GPIO/AIN2
GPIO/AIN1
GPIO/AIN7
GPIO/AIN6
GPIO/AIN5
GPIO/AIN4
V5V
nRESET
VSHLD
V5V
nRESET
VSHLD
Ground
Ground
Ground
Ground
VSHLD VSHLD
VSHLD VSHLD
Open Open
CNA1
CNA5
CNA2
CNA3
CNA4
None
None
None
None
None
None
None
None
None
Fig. 2-12 : pin assignment table for External interface

MK715x1EK1A Hardware Manual
2. Hardware specifications
FEXK715x1EK1A_HardManual-01 13
Pin No.
Pin Name
MK715x1EK1AAssign
Arduino Function
nRF52 Port
nRF52 Function
1
P11
GPIO
D0
P0.11
GPIO
2
P12
GPIO
D1
P0.12
GPIO
3
P13
Btn1
D2
P0.13
GPIO
4
P14
Btn2
D3
P0.14
GPIO
5
P15
Btn3
D4
P0.15
GPIO
6
P16
Btn4
D5
P0.16
GPIO
7
P17
LED1
D6
P0.17
GPIO
8
P18
LED2
D7
P0.18
GPIO
Table. 2-6 : CNA1
Pin No.
Pin Name
MK715x1EK1AAssign
Arduino Function
nRF52 Port
nRF52 Function
1
P19
LED3
D8
P0.19
GPIO
2
P20
LED4
D9
P0.20
GPIO
3
P22
DIP-SW (1)
D10
P0.22
GPIO
4
P23
DIP-SW (2)
D11
P0.23
GPIO
5
P24
GPIO
D12
P0.24
GPIO
6
P25
GPIO
D13
P0.25
GPIO
7
GND
Ground
Ground
GND
Ground
8
P02
GPIO/AIN0
AREF
P0.02
GPIO/AIN0
9
P26
DIP-SW (3)
SDA
P0.26
GPIO
10
P27
DIP-SW (4)
SCL
P0.27
GPIO
Table. 2-7 : CNA2
Pin No.
Pin Name
MK715x1EK1AAssign
Arduino Function
nRF52 Port
nRF52 Function
6
P31
GPIO/AIN7
A5
P0.31
GPIO/AIN7
5
P30
GPIO/AIN6
A4
P0.30
GPIO/AIN6
4
P29
GPIO/AIN5
A3
P0.29
GPIO/AIN5
3
P28
GPIO/AIN4
A2
P0.28
GPIO/AIN4
2
P04
GPIO/AIN2
A1
P0.04
GPIO/AIN2
1
P03
GPIO/AIN1
A0
P0.03
GPIO/AIN1
Table. 2-8 : CNA3
Pin No.
Pin Name
MK715x1EK1AAssign
Arduino Function
nRF52 Port
nRF52 Function
8
N.C.
None
None
None
None
7
GND
Ground
Ground
GND
Ground
6
GND
Ground
Ground
GND
Ground
5
V5V
+5.0V Shield Power
+5.0V Shield Power
None
None
4
VSHLD
+3.3V Shield Power
+3.3V Shield Power
None
None
3
P21_RESET
nRESET
nRESET
P0.21
GPIO/nRESET
2
VSHLD
+3.3V Shield Power
+3.3V Shield Power
None
None
1
VSHLD
+3.3V Shield Power
+3.3V Shield Power
None
None
Table. 2-9 : CNA4
Pin No.
Pin Name
MK715x1EK1AAssign
Arduino Function
nRF52 Port
nRF52 Function
1
P00
Open
None
P0.00
GPIO/XL1
2
P01
Open
None
P0.01
GPIO/XL2
3
P21
nRESET
None
P0.21
GPIO/nRESET
4
P05
UART RTS
None
P0.05
GPIO/AIN3
5
P06
UART TXD
None
P0.06
GPIO
6
P07
UART CTS
None
P0.07
GPIO
7
P08
UART RXD
None
P0.08
GPIO
8
P09
GPIO
None
P0.09
GPIO/NFC1
9
P10
GPIO
None
P0.10
GPIO/NFC2
Table. 2-10 : CNA5
Pin No.
Pin Name
MK715x1EK1AAssign
Arduino Function
nRF52 Port
nRF52 Function
1
P24
GPIO
None
P0.24
GPIO
2
P25
GPIO
None
P0.25
GPIO
3
P21_RESET
nRESET
None
P0.21
GPIO/nRESET
4
GND
Ground
None
GND
Ground
5
P23
Dip Switch
None
P0.23
GPIO
6
V5V
+5.0V USB Power
None
None
None
Table. 2-11 : CNEX

MK715x1EK1A Hardware Manual
3. How to use sample software
FEXK715x1EK1A_HardManual-01 14
3. How to use sample software
The AT command application software is installed in this kit. Please prepare MK715x1 evaluation kit and
smartphone application "BLE Tool". This section briefly describes the operation of the AT command application,
using the MK715x1 side as a peripheral device and connecting to a central device such as a smartphone as an
example.
Fig. 3-1 : System configuration (when connecting to a smartphone, etc.)
Refer to "MK715x1 AT Command Application User's Manual" for detailed specifications of AT command application
for MK715x1.
3.1 PC set up
1) Connect MK715x1EK1 and the USB port of your PC with USB cable(A-microB type).
When using it for the first time, USB serial conversion IC driver should be installed.
Download driver software from the following site, if necessary.
https://www.ftdichip.com/Drivers/VCP.htm
2) Start up terminal software such as Tera Term, and set the serial port as follows:
Port:COM port number used
Baud Rate:57,600 bps
Data:8 bit
Parity:None
Stop:1 bit
Flow Control:Hardware
3.2 Smartphone Set up
The application on the smartphone uses BLE Tool. Please download and install from the following.
Google Play : https://play.google.com/store/apps/details?id=com.lapis_semi.bleapp
App Store : https://itunes.apple.com/jp/app/ble-tool/id915714158?mt=8&ign-mpt=uo%3D4
MK715x1
Evaluation-kit
Remote Device
(Central Device)
Local Device
(Peripheral Device)
Bluetooth
low energy
USB-Serial
HOST
(PC)
This manual suits for next models
2
Table of contents
Popular Remote Control manuals by other brands

Flying Industry Development
Flying Industry Development 002028 user manual
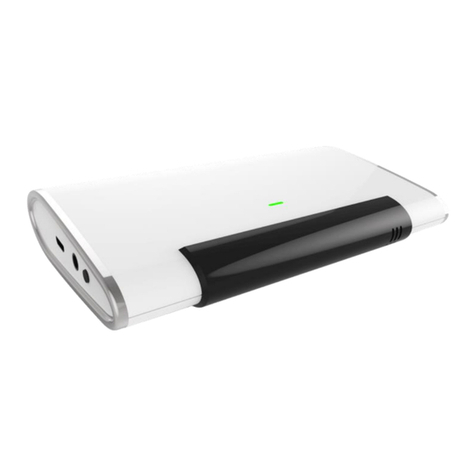
SmartDHOME
SmartDHOME IR Controller user manual
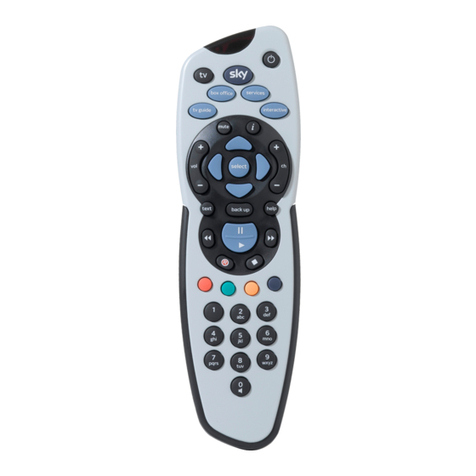
Sky
Sky Sky+ user manual

Pioneer
Pioneer CD-R33 owner's manual
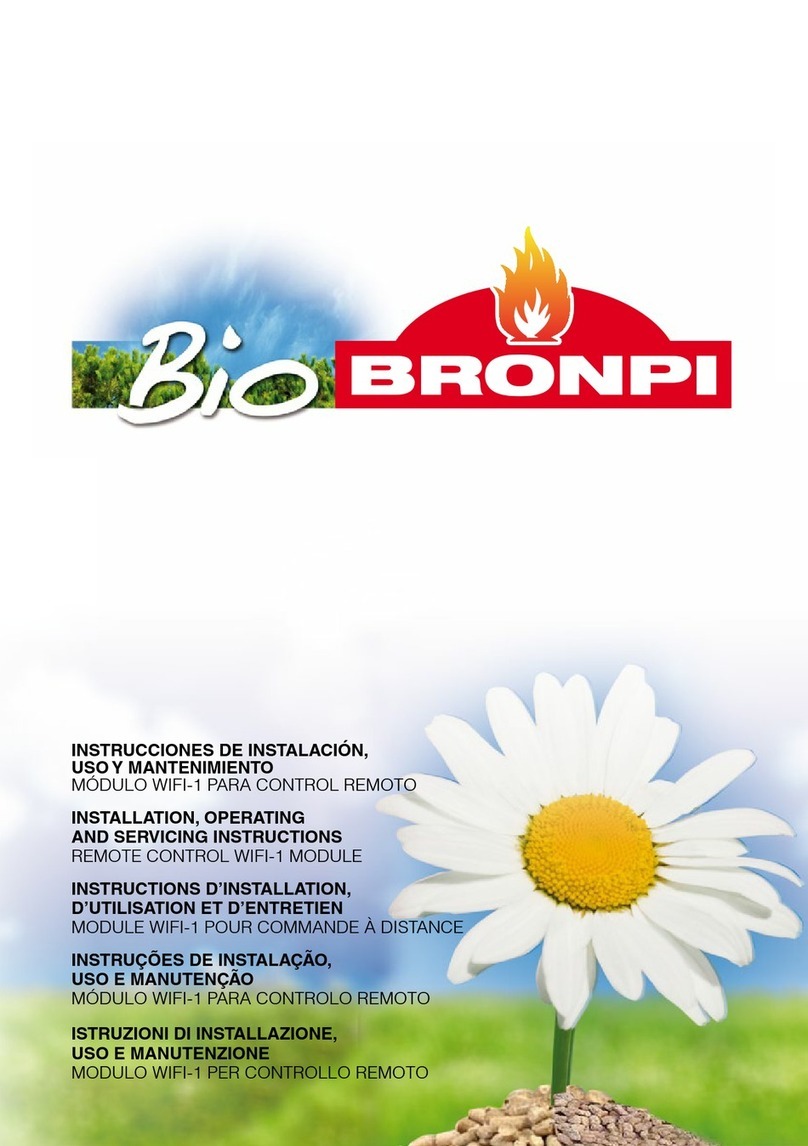
Bio Bronpi
Bio Bronpi KIT WIFI 1 Installation, operating and servicing instructions

HUGEWIN ELECTRONIC
HUGEWIN ELECTRONIC HXTC-3001 user manual