rollease acmeda AUTOMATE MT02-0401-331011 User manual

4 Channel Motor Controller
INSTALLATION & OPERATION MANUAL
GROUP
CONTROL
DRY CONTACT
INPUT
AUTOMATE_4-M-CTRL_PRGM_GL_v2.1_DEC_2022
Automate | 4 Channel Motor Controller provides individual and group control of one to four ML motors.
This motor controller can be activated manually or automatically via Dry Contact Switches, TCP/IP protocol and
RS485 communication and can be customised to suit a variety of configurations, allowing singel window control,
floor control and entrie building control.
Part #: MT02-0401-331011 Automate | 4 Motor Controller 85-240VAC Input
Features:
• Individual and Group Control of up to 4 ML motors.
• 4 individual Inputs for dry contact switches via termina; block and RJ45.
• 2 Master Inputs for dry contact control of all 4 motors and making larger groups.
• Customisable motor groups and dry contact function using DIP switch selections.
• Advanced control using ARC Serial Commands via TCP/IP and RS485.

2 | Automate™Programming Instructions | 4 Channel Motor Controller ROLLEASE ACMEDA
SAFETY INSTRUCTIONS
COMPLIANCE STATEMENT
WARNING: Important safety instructions to be read before installation and use.
Incorrect installation or use can lead to serious injury and will void manufacturer’s liability and
warranty. It is important for the safety of persons to follow the enclosed instructions. Save these
instructions for future reference.
• Do not expose to water, moisture, humid and damp environments or extreme
temperatures.
• Persons (including children) with reduced physical, sensory or mental capabilities, or lack
of experience and knowledge should not be allowed to use this product.
• Use or modification outside the scope of this instruction manual will void warranty.
• Installation and programming to be performed by a suitably qualified installer.
• Follow installation instructions.
• For use with motorized shading devices.
• Keep away from children.
• Frequently inspect for improper operation. Do not use if repair or adjustment is necessary.
• Keep clear when in operation.
• Replace battery with correctly specified type.
This device complies with Part 15 of the FCC Rules / Industry Canada
licence-exempt RSS standard(s). Operation is subject to the following
two conditions:
(1) this device may not cause harmful interference, and
(2) this device must accept any interference received, including
interference that may cause undesired operation.
Le présent appareil est conforme aux CNR d’Industrie Canada
applicables aux appareils radio exempts de licence. L’exploitation est
autorisée aux deux conditions suivantes:
(1) l’appareil ne doit pas produire de brouillage, et
(2) l’utilisateur de l’appareil doit accepter tout brouillage
radioélectrique subi, même si le brouillage est susceptible d’en
compromettre le fonctionnement.
Changes or modifications not expressly approved by the party
responsible for compliance could void the user’s authority to operate
the equipment.
This equipment has been tested and found to comply with the limits for
a Class B digital device, pursuant to part 15 of the FCC Rules. These
limits are designed to provide reasonable protection against harmful
interference in a residential installation.
This equipment generates uses and can radiate radio frequency energy
and, if not installed and used in accordance with the instructions,
may cause harmful interference to radio communications. However,
there is no guarantee that interference will not occur in a particular
installation.
If this equipment does cause harmful interference to radio or television
reception, which can be determined by turning the equipment off and
on, the user is encouraged to try to correct the interference by one or
more of the following measures:
- Reorient or relocate the receiving antenna.
- Increase the separation between the equipment and receiver.
- Connect the equipment into an outlet on a circuit different from that
to which the receiver is connected.
- Consult the dealer or an experienced radio/TV technician for help.
To satisfy FCC / IC RF exposure requirements, a separation distance of
20 cm or more should be maintained
between the antenna of this device and persons during device
operation.
To ensure compliance, operations at closer than this distance is not
recommended.
Les antennes installées doivent être situées de facon à ce que la
population ne puisse y être exposée à une distance de moin de 20
cm. Installer les antennes de facon à ce que le personnel ne puisse
approcher à 20 cm ou moins de la position centrale de l’ antenne.
La FCC des éltats-unis stipule que cet appareil doit être en tout temps
éloigné d’au moins 20 cm des personnes pendant son functionnement.
Important safety instructions to be read prior to operation.
• It is important for the safety of persons to follow the enclosed instructions.
• Persons (including children) with reduced physical, sensory or mental capabilities, or lack
of experience and knowledge should not be allowed to use this product.
• Frequently inspect for improper operation. Do not use if repair or adjustment is necessary.
DANGER - RISK OF ELECTRIC SHOCK
WARNING: INSTALLATION BY LICENSED
ELECTRICAL WORKERS ONLY. COVER
SHALL NOT BE REMOVED IN NORMAL USE.
DANGER - RISQUE DE CHOC ELECTRIQUE
ATTENTION: INSTALLATION PAR DES
ÉLECTRICIENS AGRÉÉS UNIQUEMENT. LE
COUVERCLE NE DOIT PAS ÉTRE RETIRÉ EN
UTILISATION NORMALE.
Consignes de sécurité importantes à lire avant utilisation.
• Pour la sécurité des personnes, il est important de suivre les instructions fournies.
• Les personnes (y compris les enfants) dont les capacités physiques, sensorielles ou
mentales sont réduites ou qui manquent d’expérience et de connaissances ne devraient
pas être autorisées à utiliser ce produit.
• Gardez les télécommandes hors de la portée des enfants.
• Inspectez fréquemment l’utilisation non conforme. Ne pas utiliser si une réparation ou un
réglage est nécessaire.
Do not dispose of in general waste.
Please recycle batteries and damaged electrical products appropriately.
Ne pas jeter avec les déchets ordinaires.
Veuillez recycler les piles et les produits électriques endommagés de
manière appropriée.
For AU Market
For US Market
For EU Market
For EU Market
For UK Market
5005833
For US Market
OUT1OUT 2OUT3OUT 4 OUT5OUT 6OUT7OUT 8 OUT 9 OUT10 OUT 11 OUT12 OUT13 OUT14 OUT 15 OUT16 OUT17 OUT18
OUT1OUT 2OUT3OUT 4 OUT5OUT 6OUT7OUT 8 OUT 9 OUT10 OUT 11 OUT12 OUT13 OUT14 OUT 15 OUT16 OUT17 OUT18

ROLLEASE ACMEDA Automate™Programming Instructions | 4 Channel Motor Controller | 3
CONTENTS
1 OVERVIEW 4
2 SPECIFICATIONS 5
2.1 Motor controller 5
2.2 Wire gauge & Strip Lengths 5
2.3 Dry Contact Terminals 5
2.4 Dry Contact RJ45 6
2.5 Motor GROUP DIP Switches (SW1, SW2, SW3, SW4) 6
2.6 Motor MODE DIP Switches (MASTER, SWITCHES) 6
2.6.1 Table of Motor Operation MODES 7
3 INSTALLATION 8
3.1 Standard Dry Contact Switches 8
3.2 RJ45 Dry Contact Switches 8
4 ADVANCED SETUP & FUNCTIONS 9
4.1 Daisy Chain 9
4.2 Setting New Pre-Set Positions 9
4.3 Resetting Pre-Set Positions 9
4.4 RS485 10
4.4.1 RS485 Terminal Design 10
4.4.2 RS485 Parameters 10
4.4.3 RS485 Message Format to 4CH Motor Controller 10
4.4.4 RS485 Message Format to Mechanical Limit Motor Address 10
4.4.5 RS485 Setup (Via RA Serial Port Application) 11
4.5 TCP/IP 12
4.5.1 TCP/IP Terminal Design 12
4.5.2 TCP/IP Parameters 12
4.5.3 TCP/IP Message Format 12
4.5.4 TCP/IP Setup (Via LinQ Tool) 13
5 SERIAL COMMANDS TABLE 14
5.1 Controller/Global Commands 14
5.2 Motor Commands (RS485) 16
5.3 Motor Commands (TCP/IP) 17
6 TROUBLE SHOOTING 18
7 NOTES 19

4 | Automate™Programming Instructions | 4 Channel Motor Controller ROLLEASE ACMEDA
1 OVERVIEW
# ITEM FUNCTION
1 AC Input Connect to mains power supply
2 Earth Rail Connect earth/ground wires of inputs and outputs.
3 AC Output Connect to up to 4x mechanical limit motors
4 Master Push Terminals Connect to standard dry contact wall switches
5 Master RJ45 Ports Connect to RJ45 dry contact wall switches
6 Individual Switch Push Terminals Connect to 4x standard dry contact wall switches
7 Individual Switch RJ45 Ports Connect to 4x RJ45 dry contact wall switches
8 RS485 Port Communicate using ARC Serial Commands by RS485
9 TCP/IP Port Communicate using ARC Serial Commands by TCP/IP
10 Motor Select DIP Switch Select motor/s for each individual switch control
11 Motor Select Button Update PCB with new motor & mode selections
12 Programming Button Reset intermediate position programming
13 Switch Mode DIP Switch Select how th eindividual switch/s will function
14 Master Mode DIP Switch Select how the master switch/s will function
15 Power LED Indicate PCB power and programming status
16 Motor LEDs Indicate motor movement for 4x motors
17 Fuses Protection for over-current and over-voltage
1
3
2
4
6
5
8
9
10
11
12
13
14
15
16
17
7

ROLLEASE ACMEDA Automate™Programming Instructions | 4 Channel Motor Controller | 5
2 SPECIFICATIONS
Input 85 - 240VAC, 1.25(1.25)A EACH CHANNEL
Power Factor 0.47
No load power loss 1.65W
Efciency with 100% load @ 110V 68%
Efciency with 100% load @ 240V 68%
Operating temperature range 32°F - 122°F | [0°C - 50°C]
Operating humidity conditions 20% - 60%
Storage temperature range -4°F - 158°F | [-20°C - 70°C]
Storage humidity conditions < 80%
Fuses 2x 250V, 5A
AC Input & Output Terminals
Wire Gauge 1.0 - 2.5mm2(14 - 18AWG)
Wire Type Solid core & stranded
Wire Strip Length 11mm - 12mm
Master & Individual Push Terminals
Wire Gauge 1.0 - 1.5mm2(16 - 18AWG)
Wire Type Solid core & stranded
Wire Strip Length 8.5mm - 9.5mm
O Open
C Close
G Ground
SStop
2.1 Motor controller
2.2 Wire gauge & Strip Lengths
2.3 Dry Contact Terminals

6 | Automate™Programming Instructions | 4 Channel Motor Controller ROLLEASE ACMEDA
Pin no. Pinout Denition T568A Color T568B Color Pins of plug face
1Pre-set 1
Default: 20% open white/green stripe white/orange stripe
2Pre-set 2
Default: 40% open green solid orange solid
3Pre-set 3
Default: 60% open white/orange stripe white/green stripe
4 12V+ blue solid blue solid
5Pre-set 4
Default: 80% open white/blue stripe white/blue stripe
6 Down orange solid green solid
7 Up white/brown stripe white/brown stripe
8 Ground brown solid brown solid
Use these DIP switches to group motors to the corrosponding switch.
NOTE: Master switches are grouped to controll all 4x motors.
Use these DIP switches to select which operation modes the shades will follow when a dry contact
input of UP, DOWN or STOP is received.
2.4 Dry Contact RJ45
2.5 Motor GROUP DIP Switches (SW1, SW2, SW3, SW4)
2.6 Motor MODE DIP Switches (MASTER, SWITCHES)
SW4 ON
OFF
ON
OFF
ON
OFF
ON
OFF
ON
OFF
ON
OFF
SW3
SW2
SW1
SWITCHES
MASTER
1 2 3 4
1 2 3 4
1 2 3 4
1 2 3 4
1 2 3 4
1 2 3 4
Selection of Individual
Switch Inputs 1-4
Example shows switch 2
grouped to motor 1 only.
Example shows both switches
and master in mode 1
Selection of Motor 1-4
8
Pin Position
76
54
32
1

ROLLEASE ACMEDA Automate™Programming Instructions | 4 Channel Motor Controller | 7
Mode Description DIP Switch Setting
1
Maintained
Motor Action
(Default - as
shipped)
Required Switch Type = SPDT Momentary (with Center OFF)
Motor moves to limit when an Open or Closed button is pressed and released.
Single Press (while moving)
If a button is pressed and released one time while the motor is moving, the
motor will stop.
2
SOBR
(Stop On
Button
Release)
Required Switch Type = SPDT Momentary (with Center OFF)
Motor moves toward limit as long as an Open or Close button is pressed and
held.
Motor stops when button is released.
3
Momentary
Action
(Latch and
Run)
Required Switch Type = SPDT Momentary (with Center OFF)
Motor moves toward limit as long as an Open or Close button is pressed and
held.
If the button is released within 1.5 seconds, then the motor stops.
If the button is held for more than 1.5 seconds, then the motor wil latch and
run to limit.
4
Sequencing
Action
(Single Pole
Single Throw)
Required Switch Type = SPST Momentary “Doorbell” Single Press
When connected to the “Close” pin;
A momentary contact and release of a switch will move the Motor towards the
limit. The motor will stop at the limit unless the switch is pressed again while
moving. In this instance the motor will stop.
Subsequent button presses will move the motor in the opposite direction. This
results in a “sequencing” action, allowing the user to control the motor to go
Up, Stop, Down, Stop using successive button presses.
When connected to the “Open” pin;
A maintained contact will run the motor in the Open direction. A broken
connection will run the motor in the Close direction. This allows the user tp
itilize a common maintained light switch to operate the motor to the Open
and Close limits, but the motor cannot be stopped in between. (It should be
possible for a user to perform a “quick toggle” of the switch - Off, then On
again in less than 0.5 seconds, to achieve Stop).
If a magnetic window sensor switch is connected to this Open pin and the
contact is maintained (requires a normally closed magnetic switch) the motor
will Open and remain there until the magnetic switch is retuned to “broken
contact position”.
5
Tilt Mode 1
Typically used
for shades with
small vanes.
Required Switch Type = SPDT Momentary (with Center OFF)
Single Press
Motor tilts toward limit (using 0.10 second pulses) when Open or Close button
is pressed and held.
Motor stops when button is released, or motor reaches a limit.
If a button is pressed and held for >1.5 seconds then released, the motor will
run to limit. Pressing the button again while the motor is moving will stop the
motor.
6
Tilt Mode 1
Typically used
for shades with
medium vanes.
Required Switch Type = SPDT Momentary (with Center OFF)
Motor moves to limit when an Open or Closed button is pressed and released.
Single Press
As pere Mode 5, but 0.25 second pulses.
7
Tilt Mode 1
Typically used
for shades with
large vanes.
Required Switch Type = SPDT Momentary (with Center OFF)
Motor moves to limit when an Open or Closed button is pressed and released.
Single Press
As per Mode 5, but 0.50 second pulses.
2.6.1 Table of Motor Operation MODES
ON
OFF
ON
OFF
ON
OFF
ON
OFF
ON
OFF
ON
OFF
ON
OFF
1 2 3 4
1 2 3 4
1 2 3 4
1 2 3 4
1 2 3 4
1 2 3 4
1 2 3 4

8 | Automate™Programming Instructions | 4 Channel Motor Controller ROLLEASE ACMEDA
3 INSTALLATION
Ensure all motors have their limits set and are operating correctly.
NOTE: Refer to the motor datasheet for maximum motor run time.
Ensure all motors have their limits set and are operating correctly.
NOTE: Refer to the motor datasheet for maximum motor run time.
IMPORTANT
IMPORTANT
3.1 Standard Dry Contact Switches
3.2 RJ45 Dry Contact Switches
Provides basic control of UP, DOWN and STOP.
Refer to DIP Switch Mode table for additional functions to enable:
• Bell Press (SPST) Switch
• Magnetic Reed Switch
• Shades with vanes (Small, Medium, Large)
• UP, DOWN and STOP function (eg. Latch and Run)
Adds additional option for intermediate pre-set positions.
1. Connect all motors and switches to the outputs of the controller, ensuring that cables are
restrained within the nominated cable knockout.
2. Select the Switch MODE
NOTES: There are 2x Switch MODE DIP switch gangs on the PCB:
• SWITCHES: Mode for all individual input switches.
• MASTER: Mode for all master inputs.
3. Select the Motor Group
NOTES:
• Each DIP switch gang corresponds to an individual switch input.
• Each switch present on the gang corresponds to a motor.
• By moving a switch to the ON position, the corresponding motor is added to the motor
group for the given switch.
• Inputs on a master terminal control all 4x motors.
4. Complete the mains power connection to the controller, ensuring that cables are restrained
within the nominated cable knockout.
5. Press and hold the Motor Select Button for 3 seconds.
NOTE: If the motor is moving in the wrong direction, disconnect the mains power supply and
reverse the L1 and L2 wires for each impacted motor.
Set up is now complete.
1. Complete all steps for the standard dry contact switches (section 3.1).
2. Press and hold the PROGRAM button for 3 seconds.
NOTE: This initiates a motor calibration mode. All connected motors will move to their upper
limit, lower limit, then return to the upper limit. Once completed, the RJ45 dry contact switch
can connveniently move the shade to intermediate pre-set positions.
Set up is now complete.

ROLLEASE ACMEDA Automate™Programming Instructions | 4 Channel Motor Controller | 9
4 ADVANCED SETUP & FUNCTIONS
4.1 Daisy Chain
4.2 Setting New Pre-Set Positions
4.3 Resetting Pre-Set Positions
Each 4CH motor controller contains 2x master dry contact cage
clamp terminal blocks and 2x master RJ45 ports. Each respective
terminal is wired parallel to each other, meaning that a dry con-
tact connection received on one terminal (eg. UP shorted to GND
on Master 1) will be passed through to the other terminal (eg. UP
signal also presnt on Master 2).
To setup the 4CH motor controller for daisy chaining, simply con-
nect the master port of one controller to the spare maste rport of
another.
1. Move the shade, or group of shades to the desired position.
2. On a switch that is paired to the shade group, press the desired pre-set position button (eg.
pre-set 1) on the dry contact switch for 3 seconds. The current position will now be saved for
the motors.
To reset the pre-set positions, press the ‘PROGRAMMING’ button for 3 seconds. The motor con-
troller will now re-calibrate to the limits of each shade and restore all pre-set positions to their
default values.
NOTES:
• Master daisy chain connection is for dry contact only.
• ARC Serial Commands are not transmitted via daisy chain.
• A Signal received on the master port/s will control all 4x motors.
• It is recommended to daisy chain using the same type of switch being used to control the
motors (ie. Don’t daisy chain using the RJ45 port if standard dry contact switches are being
used).
Max Distance for Daisy Chain: 1000m using 18-gauge (1mm2) wire.
Max Quantity of Controllers on Bus: 32 controllers.

10 | Automate™Programming Instructions | 4 Channel Motor Controller ROLLEASE ACMEDA
Pin no. Pinout Denition T568A Color T568B Color Pins of plug face
1 5V+ white/green stripe white/orange stripe
8
Pin Position
76
54
32
1
2Not used green solid orange solid
3Not used white/orange stripe white/green stripe
4 + RS485 blue solid blue solid
5 - RS485 white/blue stripe white/blue stripe
6Not used orange solid green solid
7Not used white/brown stripe white/brown stripe
8 Signal Ground brown solid brown solid
4.4 RS485
4.4.1 RS485 Terminal Design
4.4.2 RS485 Parameters
4.4.3 RS485 Message Format to 4CH Motor Controller
4.4.4 RS485 Message Format to Mechanical Limit Motor Address
Protocol USART
Baud rate 9600 (default), or 115200
Date bit 8
Parity bit None
Stop bit 1
Start
Character
Controller
Address Command Data End
Character
! 3 byte ASCII 1 byte ASCII Optional ;
0-9 & A-Z, broadcast address
000 for querry, range 001-zzz
non-numerical
ASCII
“?” for inquiry of
motor status
Start
Character
Controller
Address
Delimiter
Character Motor Address Command Data End
Character
! 3 byte ASCII D 3 byte ASCII 1 byte ASCII Optional ;
0-9 & A-Z,
broadcast
address 000 for
querry, range
001-zzz
0-9 & A-Z,
broadcast
address 000 for
querry, range
001-zzz
non-
numerical
ASCII
“?” for
inquiry
of motor
status

ROLLEASE ACMEDA Automate™Programming Instructions | 4 Channel Motor Controller | 11
4.4.5 RS485 Setup (Via RA Serial Port Application)
Ensure all motors have their limits set and are operating correctly.
NOTE: Refer to the motor datasheet for maximum motor run time.
IMPORTANT
Allows for control over an RS485 network.
1. Complete all steps for the standard dry contact switches (section 3.1).
2. Press and hold the PROGRAM button for 3 seconds.
NOTE: This initiates a motor calibration mode. All connected motors will move to their upper
limit, lower limit, then return to the upper limit.
3. Download the RA Serial Port Application (Serial String Compiler & Testing Tool) available on
the Rollease Acmeda website.
4. Run the application.
5. Referring to the serial commands table of this manual, send commands to the 4CH motor
controller to operate the shades.
Set up is now complete.

12 | Automate™Programming Instructions | 4 Channel Motor Controller ROLLEASE ACMEDA
Pin no. Pinout Denition T568A Color T568B Color Pins of plug face
1 TX+ white/green stripe white/orange stripe
8
Pin Position
76
54
32
1
2TX- green solid orange solid
3 RX+ white/orange stripe white/green stripe
4 TRD2+ blue solid blue solid
5 TRD2- white/blue stripe white/blue stripe
6RX- orange solid green solid
7 TRS3+ white/brown stripe white/brown stripe
8 TRD3- brown solid brown solid
4.5 TCP/IP
4.5.1 TCP/IP Terminal Design
4.5.2 TCP/IP Parameters
4.5.3 TCP/IP Message Format
Operating Software LinQ Tool
WiFi bridge Wireless router
WiFi frequency 2.4GHz
IP protocol IPv4
Start
Character
Controller
Address Command Data End
Character
! 3 byte ASCII 1 byte ASCII Optional ;
0-9 & A-Z, broadcast address
000 for querry, range 001-zzz
non-numerical
ASCII
“?” for inquiry of
motor status
NOTES:
As commands over TCP/IP are sent to the IP address of the 4CH Motor Controller, no delimiter is
required in the message format.

ROLLEASE ACMEDA Automate™Programming Instructions | 4 Channel Motor Controller | 13
4.5.4 TCP/IP Setup (Via LinQ Tool)
Ensure all motors have their limits set and are operating correctly.
NOTE: Refer to the motor datasheet for maximum motor run time.
IMPORTANT
Adds additional option for intermediate pre-set positions.
1. Complete all steps for the standard dry contact switches (section 3.1).
2. Press and hold the PROGRAM button for 3 seconds.
NOTE: This initiates a motor calibration mode. All connected motors will move to their upper
limit, lower limit, then return to the upper limit.
3. Connect a network cable between the 4CH motor controller and router.
4. Download the LinQ Tool available on the Rollease Acmeda website.
5. Run the application.
6. Press the green drop-down arrow on the ‘connect’ box, and then press ‘scan for hubs on the
network’. The LinQ tool will now scan for all 4CH motor controllers on the same network as
the PC or laptop.
7. Check that the connection has been established by selecting a motor on the LinQ tool, and
then pressing the up or down arrow on the LinQ tool command controls box.
8. Refferring to the serial commands table of this manual, send commands to the 4CH motor
controller to operate the shades.
Set up is now complete.

14 | Automate™Programming Instructions | 4 Channel Motor Controller ROLLEASE ACMEDA
5 SERIAL COMMANDS TABLE
5.1 Controller/Global Commands
Cmd Description Eg. Downlink Eg. Uplink
NAME? Get controller
name !000NAME?; !000NAME4CH_MT_CTRL; TCP/IP
MAC? Get controller
MAC address !000MAC?; !000MACaa:bb:cc:11:22:33; TCP/IP
SN? Get the serial
number !000SN?; !00SNMT02-0401-331011; TCP/IP
FWV? Get controller
rmware version !000FWV?; !000FWVA03; TCP/IP
N? Get controller
name !000N?; !000N4CH_MT_CTRL; RS485
NChange controller
name !000NBLDG3; !000NBLDG3; ALL
V? Get controller
address !000V?; !245VA03; RS485
v? Get motor
addresses !000v?; !MT1vM01;!MT2vM01;
!MT3vM01;!MT4vM01; ALL
GChange controller
address !245G111; !111A; RS485
000B Change baud rate !000B960; or
!000B115; !000B960; or !000B115; RS485
P‘MOTOR SELECT’
via serial input !000P; !000A; ALL
K‘PROGRAMMING’
via serial input !000K; !000A; ALL
TTest controller
connection !000T; !000A; ALL
P? Get all controller
parameters !111P?;
!111P;SW1,1111;SW2,1010;
SW3,1100;SW4,1000;
SWM,0010;MST,0100;
MT1,LC1,RC1,UT1,DT1,RT1,TA1,TS1,TN1;
MT2,LC2,RC2,UT2,DT2,RT2,TA2,TS2,TN2;
MT3,LC3,RC3,UT3,DT3,RT3,TA3,TS3,TN3;
MT4,LC4,RC4,UT4,DT4,RT4,TA4,TS4,TN4;
ALL
000* Controller factory
reset !111D000*; !111D000A; ALL

ROLLEASE ACMEDA Automate™Programming Instructions | 4 Channel Motor Controller | 15
NOTES:
• For uplink, controller always replies with own address (eg. 111).
• For P? command, the following variables are presented:
• All DIP switch congigurations (eg. SW1:1111)
• Each motor conguration:
• XXX motor address, followed by
• LCx = Last Command
• RCx = Run Counter
• UTx = Up Time
• DTx = Down Time
• RTx = Running Time
• TAx = Tilt Angle Ratio
• TSx = Tilt Steps
• TNx = Tilt Number
NOTE: Milliseconds presented in HEX format.

16 | Automate™Programming Instructions | 4 Channel Motor Controller ROLLEASE ACMEDA
5.2 Motor Commands (RS485)
Cmd Description Eg. Downlink Eg. Uplink Notes
N? Get motor name !000DMT1N?; !000DNT1NMotor 1; -
N Change motor name !000DMT1NBed9; !000DMT1NBed9; -
Ro? Get motor room !000DMT1Ro?; !000DMT1RoKitchen; -
Ro Change motor room !000DMT1RoKitchen; !000DMT1RoKitchen; -
r? Request current
motor position !000DMT1r?;
!000DMT1U; ‘PROGRAMMING’ not complete.
!000DMT1r00b00;
!XXXrYYbZZ; where,
XXX = Motor Address
YY = Position %
ZZ = Tilt
After Up travel: ‘Tilt Number’ variable =
‘Tilt Steps’ available, meaning ZZ ‘Tilt %’ = 100%
After DOWN travel: ‘Tilt Number’ = 0,
meaning ZZ ‘Tilt %’ = 0%.
o Open / Up !000DMT1o; !000DMT1o;
!000DMT1r50b99;
1st uplink: Conrmation ‘o,’
2nd uplink: New position at stop or limit.
c Close / Down !000DMT1c; !000DMT1c;
!000DMT1r50b00;
1st uplink: Conrmation ‘c,’
2nd uplink: New position at stop or limit.
sStop !000DMT1s; !000DMT1s;
!000DMT1r50b00;
1st uplink: Conrmation ‘s,’
2nd uplink: New position at stop or limit.
mMove motor to
percentage !000DMT1m80;
!000DMT1U; ‘PROGRAMMING’ not complete.
!000DMT1r80b00; Eg. Move MT1 to 80%
oA Tilt
Jog Open / Up !000DMT1oA; !000DMT1oA;
!000DMT1r50b00;
1st uplink: Conrmation ‘oA,’
2nd uplink: New position at stop or limit.
cA Tilt
Jog Close / Down !000DMT1cA; !000DMT1cA;
!000DMT1r50b00;
1st uplink: Conrmation ‘cA,’
2nd uplink: New position at stop or limit.
b
Tilt
Rotate angle to
percentage
!000DMT1b75;
!000DMT1U; ‘PROGRAMMING’ not complete.
!000DMT1r00b75;
Calculate the milliseconds required to achieve
desired % and then apply the pulse and
corrosponding step.
pGa Set Tilt angle ratio
(pulse time) !000DMTpGa050; !000DMT1pGa050; Set’tilt angle ratio’ (pulse) to X.XX sec.
Eg. 050 = 0.5 seconds.
pGr Set Tilt steps
(moving dist.) !000DMT1pGr008; !000DMT1pGr008; Set ‘tilt steps’ value to XXX
Eg. 004 = 4 steps total.
pPr? Get motor preset
positions !000DMT1pPrX?; !000DMT1pPr80; X = 1, 2, 3, 4 (pre-set positions)
pPrXr Change motor
preset positions !000DMT1pPrXrYY; !000DMT1pPr1r80;
X = 1, 2, 3, 4
YY = 0 - 99%
Only travel % can be set, not tilt %.
Eg. Changed MT1 Pre-set 1 to 80%.
pPm Move motor to
preset position !000DMT1pPmX; !000DMT1r80b00; X = 1, 2, 3, 4

ROLLEASE ACMEDA Automate™Programming Instructions | 4 Channel Motor Controller | 17
5.3 Motor Commands (TCP/IP)
Cmd Description Eg. Downlink Eg. Uplink Notes
N? Get motor name !MT1NAME?; !MT1NAMEMotor1; -
N Change motor name !MT1NBed9; !MT1NBed9; -
Ro? Get motor room !MT1ROOM?; !MT1ROOMdefault; -
Ro Change motor room !MT1RoKitchen; !MT1RoKitchen; -
r? Request current
motor position !MT1r?;
!MT1U; ‘PROGRAMMING’ not complete.
!MT1r00b00;
!XXXrYYbZZ; where,
XXX = Motor Address
YY = Position %
ZZ = Tilt
After Up travel: ‘Tilt Number’ variable =
‘Tilt Steps’ available, meaning ZZ ‘Tilt %’ = 100%
After DOWN travel: ‘Tilt Number’ = 0,
meaning ZZ ‘Tilt %’ = 0%.
o Open / Up !MT1o; !MT1o;
!MT1r50b99;
1st uplink: Conrmation ‘o,’
2nd uplink: New position at stop or limit.
c Close / Down !MT1c; !MT1c;
!MT1r50b00;
1st uplink: Conrmation ‘c,’
2nd uplink: New position at stop or limit.
sStop !MT1s; !MT1s;
!MT1r50b00;
1st uplink: Conrmation ‘s,’
2nd uplink: New position at stop or limit.
mMove motor to
percentage !MT1m80;
!MT1U; ‘PROGRAMMING’ not complete.
!MT1r80b00; Eg. Move MT1 to 80%
oA Tilt
Jog Open / Up !MT1oA; !MT1oA;
!MT1r50b00;
1st uplink: Conrmation ‘oA,’
2nd uplink: New position at stop or limit.
cA Tilt
Jog Close / Down !MT1cA; !MT1cA;
!MT1r50b00;
1st uplink: Conrmation ‘cA,’
2nd uplink: New position at stop or limit.
b
Tilt
Rotate angle to
percentage
!MT1b75;
!NT1U; ‘PROGRAMMING’ not complete.
!MT1r00b75;
Calculate the milliseconds required to achieve
desired % and then apply the pulse and
corrosponding step.
pGa Set Tilt angle ratio
(pulse time) !MT1pGa050; !MT1pGa050; Set’tilt angle ratio’ (pulse) to X.XX sec.
Eg. 050 = 0.5 seconds.
pGr Set Tilt steps
(moving dist.) !MT1pGr008; !MT1pGr008; Set ‘tilt steps’ value to XXX
Eg. 004 = 4 steps total.
pPr? Get motor preset
positions !MT1pPrX?; !MT1pPr80; X = 1, 2, 3, 4 (pre-set positions)
pPrXr Change motor
preset positions !MT1pPrXrYY; !MT1pPr1r80;
X = 1, 2, 3, 4
YY = 0 - 99%
Only travel % can be set, not tilt %.
Eg. Changed MT1 Pre-set 1 to 80%.
pPm Move motor to
preset position !MT1pPmX; !MT1r80b00; X = 1, 2, 3, 4

18 | Automate™Programming Instructions | 4 Channel Motor Controller ROLLEASE ACMEDA
6 TROUBLE SHOOTING
Problem Cause Remedy
Motors not moving
No power to controller Check all electrical connections to the
controller. Check all electrical connections
to each of the motors.
Fuse blown Check both fuses. Replace as required.
DIP switch in wrong
mode
Check that the DIP switches are in the
correct mode, making sure to check that
the switch group is set correctly and that a
valid operation mode is selected. Try
controlling the shades by the master port.
DIP settings not updated
to microcontroller
Press and hold the ‘MOTOR SELECT’ button
for 3 seconds to update the microcontroller
with the DIP settings.
Motor run time reached Allow the motor/s time to cool down
before trying to operate the shade.
Motors moving in
the wrong direction
Wiring of L1 and L2 of
motor is incorrect
Disconnect the controller from the power,
and then swap the L1 and L2 wires of the
motor.
Motors not moving
as expected
DIP switch in wrong
mode
Check that the DIP switches are in the
correct mode, making sure to check that
the switch group is set correctly and that a
valid operation mode is selected. Try
controlling the shades by the master port.
DIP settings not updated
to microcontroller
Press and hold the ‘MOTOR SELECT’ button
for 3 seconds to update the microcontroller
with the DIP settings.
For additional troubleshooting and setup tutorials, visit:

ROLLEASE ACMEDA Automate™Programming Instructions | 4 Channel Motor Controller | 19
7 NOTES

20 | Automate™Programming Instructions | 4 Channel Motor Controller ROLLEASE ACMEDA
9 SLEEP MODE
ROLLEASE ACMEDA | AUS-
TRALIA
110 Northcorp Boulevard,
Broadmeadows VIC 3047, AUS
ROLLEASE ACMEDA | USA
Level 7 / 750 East Main Street
Stamford, CT 06902, USA
T +1 800 552 5100 | F +1 203
ROLLEASE ACMEDA | EUROPE
Via Conca Del Naviglio 18,
Milan (Lombardia) Italy
Table of contents
Popular Controllers manuals by other brands
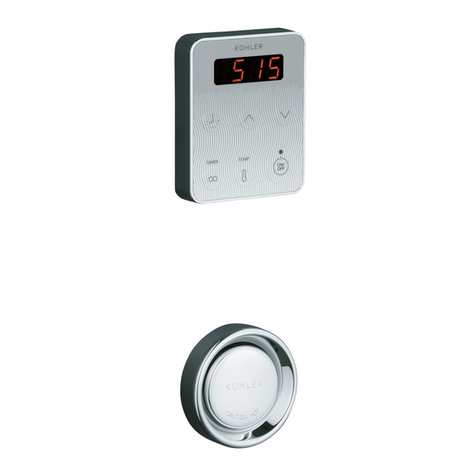
Kohler
Kohler K-1663 installation guide

Pinnacle
Pinnacle microguard installation manual
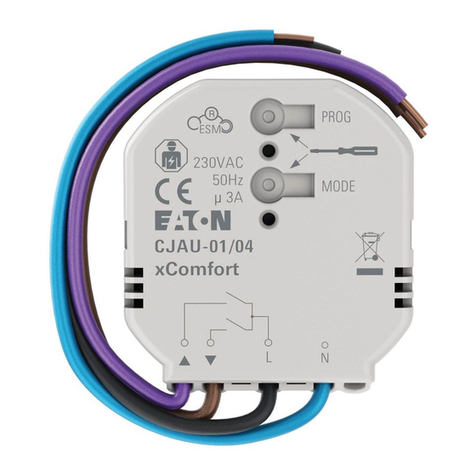
Eaton
Eaton CJAU-01/04 Series Instruction leaflet
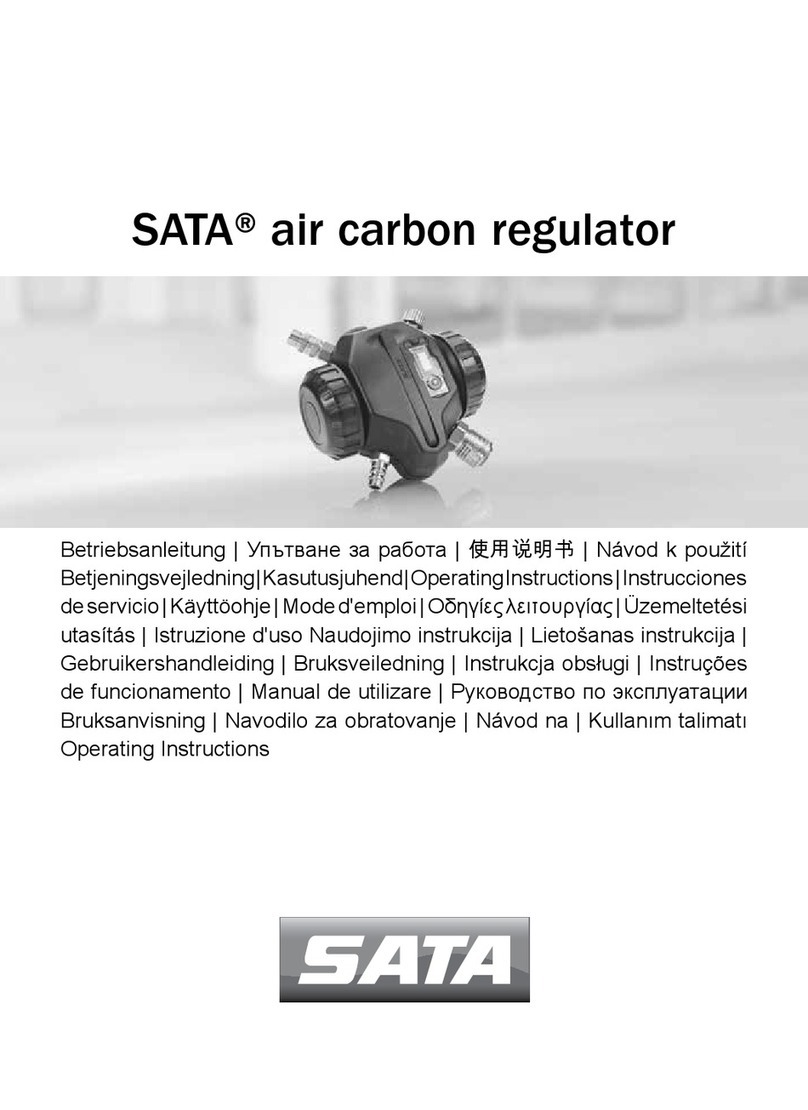
SATA
SATA air carbon regulator operating instructions
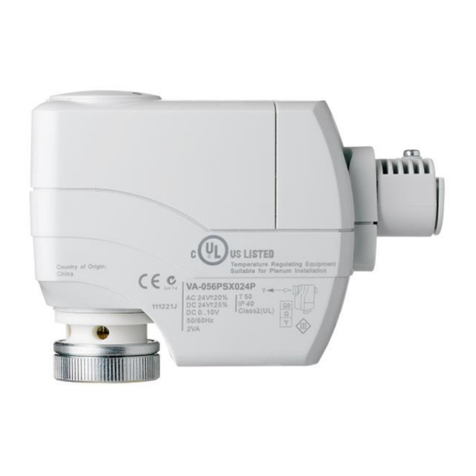
Distech Controls
Distech Controls VA-056P Series Hardware installation guide
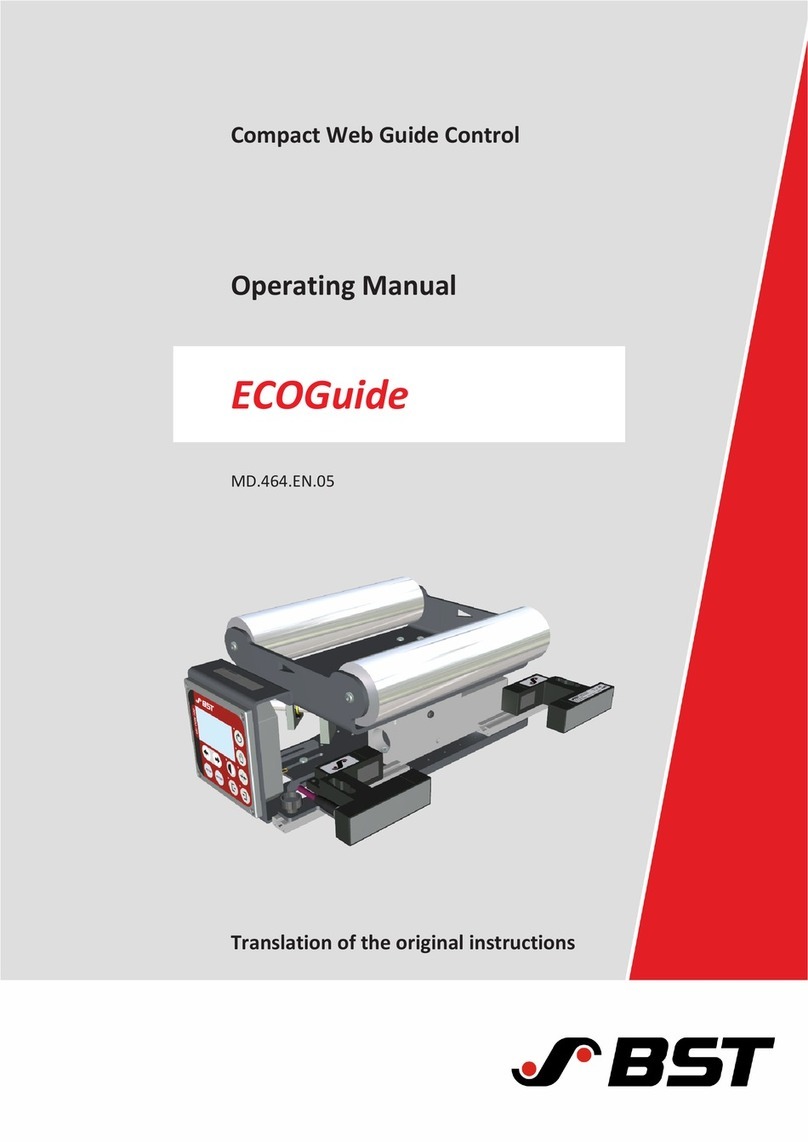
BST
BST ECOGuide MD.464.EN.05 operating manual
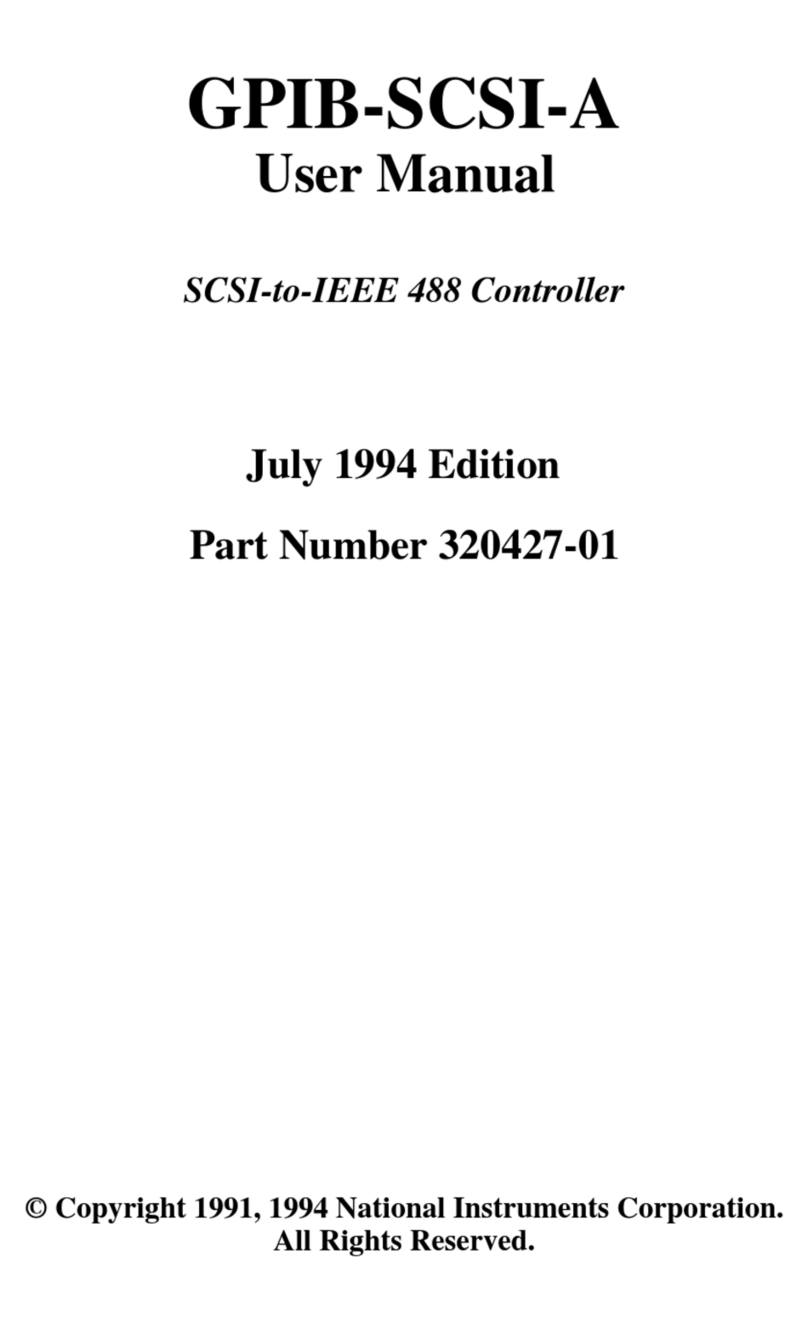
National Instruments
National Instruments GPIB-SCSI-A user manual
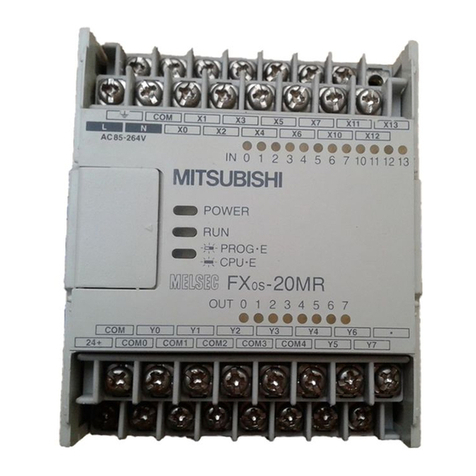
Mitsubishi
Mitsubishi FX0S Series quick start guide
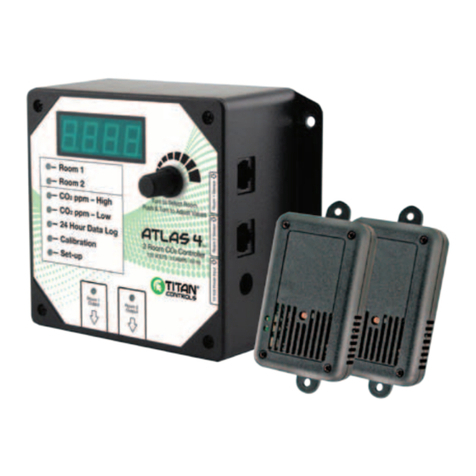
Sunlight Supply
Sunlight Supply Titan Controls Atlas 4 instruction manual
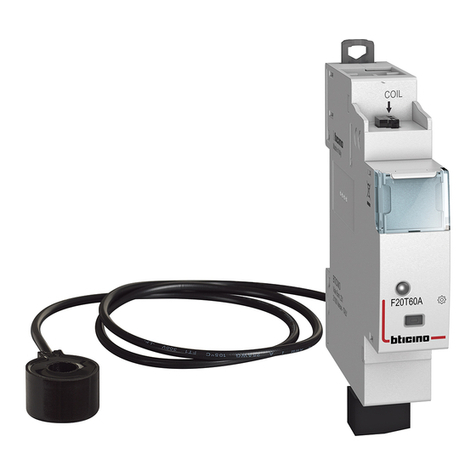
Bticino
Bticino F20T60A manual
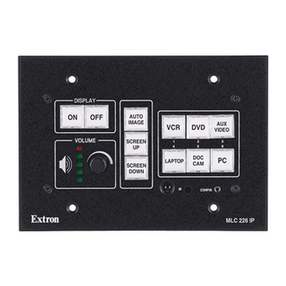
Extron electronics
Extron electronics MLC 226 IP Series Setup guide
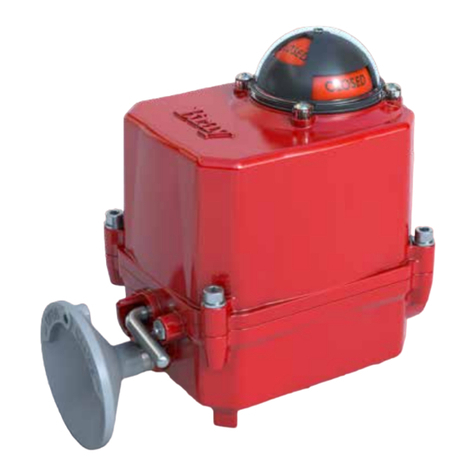
Bray
Bray 71 Series Installation, operation and maintenance manual