rotork SS User guide

Limit Switch Boxes
Safety Manual
Models: SS, SF, SB, HW, SX, SW, SY, SH,
SI, SK, SQ, ES, TB, SP, SM
Microswitch Bolt Switch: BM
A4US
US
A4
US A4
US
A4
A4 US
US
A4
US
A4
A4 US

Safety Manual
2
Section Page
Contents
Introduction 2
1. Specification of the safety functions 3
2. Warnings 3
3. Configuration of the product 4
4. Limitation of use 7
5. Failure modes and estimated failure rates 8
6. Test and maintenance requirements 9
7. Troubleshooting 11
8. Hardware fault tolerance 11
9. Classification 11
10. Mean repair time 11
11. Systematic capability 11
Introduction
Soldo®limit switch boxes are used as position
indicators by means of an electrical signal, if
they mount microswitches or sensors, or by
means of analogue signal if they mount position
transmitters. They can also have both signals
when they mount both electrical devices.
Transmitters can be of the following type:
• Siemens SITRANS TH300
• Siemens SITRANS TH320/420
• PR electronics 5437D
These, combined with a potentiometer, become
position transmitters.
Purpose of this Safety Manual, written in
compliance with IEC 61508-2, Annex D, is to
give all the necessary information to the system
integrator for a correct use of the product in
Safety Instrumented Systems for SIL classified
applications.
A4US
US
A4
US A4
US
A4
A4 US
US
A4
US
A4
A4 US

3
1. Specification of the safety functions
The safety function is of 2 types:
Type A – Switches
The device is classified Type A according to IEC 61508-2.
The safety function is defined as follows:
1. De-energize-to-trip operation: when the actuator,
on which the device is mounted, starts to drive the
emergency valve to its safe position.
2. De-energize-to-trip operation: when the actuator, on
which the device is mounted, reaches the “safe position”.
NOTES:
the above-mentioned safety functions can be
considered equivalent. In both cases, the safety function
shall correspond to the situation in which the switches pass
from “operating position” to “released position”, i.e. the limit
switch box, when used with safety function, shall work in
“deenergize-to-trip” mode, and shall be configured in that
way to perform the safety function.
The response time for the activation of the safety function is
less than 10 ms.
The choice of the safety function to be implemented is
responsibility of the system integrator.
Type B – Position Transmitters
(available for models SS, SF, SB, HW, SX, SW, SY, SH, SI)
The device is classified Type B according to IEC 61508-2.
The safety function is defined as follows:
1. Correct measuring of the position of the actuator on
which the device is mounted (normally angular position),
and generation of 4-20 mA output signal proportional to
the position, within ±2 % of tolerance.
The product has normally a single channel configuration
(only one input is measured, only one current output is
generated), with HFT=0.
A redundant (1oo2) configuration can be obtained in
these ways:
•
with one single micro switch box, internally completely
redundant (2 potentiometers, 2 position transmitters,
2 separate outputs)
•
with two micro switch boxes, each one internally in single
channel configuration
In both cases, the two analog outputs shall be voted 1oo2 by
the downstream controller.
The minimum response time is the following (in case no
digital filter is applied).
•
with position transmitters Siemens TH320/420 and PR
electronics 5437D: ≤ 75 ms
•
with position transmitters Siemens TH300: ≤ 250 ms
NOTE:
In the following paragraphs, a distinction between
Type A and Type B is used, where necessary.
The IEC 61508 standard describes a package of general
requirements for every phase of the lifecycle of safety
systems. The reliability analysis performed has shown that
these products are suitable for use in such systems for
safety class SIL 2 or SIL 3 according to switch options and
barriers used.
For installation, maintenance, test and commissioning of
these rotary switch boxes, the documents prescribed by
the IEC 61508 standard should be used. Depending on the
determined SIL class, they also prescribe the required measure
of authority, skills and independence of the concerning
personal. All indications and prescriptions within the
subjoined general installation and maintenance instructions
are the basis for these above mentioned documents. In order
to warrant the reliability, the supplemental prescriptions
mentioned below, should be observed as well.
•
Suitably trained personnel shall carry out installation in
accordance with applicable code of practice
•
The user should not repair this equipment
•
If the equipment is likely to come into contact with
aggressive substances, it is the responsibility of the
user to take suitable precautions that prevent it from
being adversely affected, thus ensuring that the type of
protection is not compromised
Aggressive substances – ex. Acidic liquids or gases that
may attack the switch box housing
•
The electrical ratings on nameplates or on adhesive
labels on the enclosure must be respected, otherwise the
product’s SIL grade will not be guaranteed
•
PEPPERL & FUCHS SIL certified barriers must be used
in conjunction of the correct P+F proximity switches as
described in PEPPERL & FUCHS documentations for SIL
applications
•
Operational testing shall be performed according to the
following indications
•
Maximum applicable voltage: 24 Volt DC. Line
monitoring system works only if terminals 1-2 and
4-5 (normally closed) or 2-3 and 5-6 (normally open)
are connected; don’t connect contemporary normally
open and normally closed
•
This safety manual has to be used in conjunction with
the safety manual the position transmitter included in
the device: Siemens TH320/420 (par. 4, 14 and 15),
or Siemens TH300 (par. 7), or PR Electronics 5437D
(par. 7, 17 and 18)
2. Warnings
A4US
US
A4
US A4
US
A4
A4 US
US
A4
US
A4
A4 US

4
Safety Manual
3. Configuration of the product
Type A: Microswitch box configurations
Rotork Instruments Italy S.r.l.
Via Portico, 17
24050 Orio al Serio (Bergamo) Italy
Tel +39 035 451161 FAX +39 035 531763
http: //www.soldo.net
e-mail: info.instruments-
italy@rotork.com
Additional Warning for SIL boxes
IOM00069_ENG Rev 0-4
4
3. CONFIGURATION OF THE PRODUCT
Type A: Microswich Box configurations
View.
1
Actuator mounted in
open position
View 2 Actuator mounted and
moved
in close position
View 3 Box & microswiches in
open position
View 4 Box & microswiches in
close position
View 5 two slotted proximity
sensors
View 6 two cylindrical
proximity sensors
View 7 two mechanical
sensors
View 8
Shown three
magnetic sensors
View 1. Actuator mounted in open position
View 3. Box & microswitches in open position
View 5. Two slotted
proximity sensors
View 6. Two cylindrical
proximity sensors
View 7. Two mechanical
sensors
View 8. Shown three
magnetic sensors
View 2. Actuator mounted and moved in close position
View 4. Box & microswitches in close position
A4US
US
A4
US A4
US
A4

5
3. Configuration of the product
Rotork Instruments Italy S.r.l.
Via Portico, 17
24050 Orio al Serio (Bergamo) Italy
Tel +39 035 451161 FAX +39 035 531763
http: //www.soldo.net
e-mail: info.instruments-
italy@rotork.com
Additional Warning for SIL boxes
IOM00069_ENG Rev 0-4
5
Type A:Microswich Bolt configurations
Type A: Easy switch configuration
Type B: Position transmitter configurations
View 12 Bolt switches in close
position
View 13 Shown Bolt switches
open position
View 1
6 easy switch configuration
View 9 two microswitches
configuration
View 10 three microswitches
configuration
View 11 four microswitches
configuration
View 1
7 4…20 mA position transmitter
and microswitches configuration
View 1
8 4…20 mA redundant position
transmitter configuration
View 9. Two microswitches
configuration
View 12. Bolt switches in
close position
View 17. 4…20 mA position transmitter and
microswitches configuration
View 13. Shown bolt switches
open position
View 18. 4…20 mA redundant position
transmitter configuration
View 10. Three microswitches
configuration
View 16. Easy switch configuration
View 11. Four microswitches
configuration
Type A: Easy switch configuration
Type B: Position transmitter configurations
Type A: Microswitch box configurations (continued)
A4 US
US
A4
US
A4
A4 US

6
Safety Manual
3. Configuration of the product
View 19. Single transmitter 1oo1 operation
Sensor Input 1 Position transmitter:
PR 5437 or Siemens
TH300/320/420
Safety PLC
View 20. Two transmitters 1oo2 operation
Sensor
Sensor
Input 1
Input 1
Position transmitter:
PR 5437 or Siemens
TH300/320/420
Position transmitter:
PR 5437 or Siemens
TH300/320/420
Safety PLC
Default parameters
Siemens TH320/420 and PR 5437D
•
Safety error: 3.5 mA or 23 mA (defined as a failure signal). The devices enter this mode if the system detects a safety related
error in Safety Operation mode. The possible errors are listed in the error list of the device.
Function/Parameter Setting
Output range 0% 4,0 mA (20 mA overturned potentiometer)
Output range 100% 20,0 mA (4 mA overturned potentiometer)
Limit Check Configuration Enabled
Output Limit – Error value Must be ≤ 3,6 mA or ≥ 21,0 mA (if enabled on output)
Output Lower Limit 3,8 mA
Output Upper Limit 20,5 mA
Sensor Error Action “Broken and Shorted”
Broken Sensor - Error Value 23,0 mA
Shorted Sensor - Error Value 3,5 mA
Sensor Drift - Error Value Must be ≤ 3,6 mA or ≥ 21,0 mA (if enabled)
Input Limits - Error Value 23,0 mA
Analog Output Calibration Gain Must be 1,0 (calibration of output current is not allowed)
Analog Output Calibration Offset Must be 0,0 (calibration of output current is not allowed)
Loop Current Mode “Enabled” (HART®7 only)
HART®Polling Address 0 (HART 5 only)
Damping (Response time) 0 sec
Siemens TH300
Function/Parameter Setting
Broken wire monitoring ON
Short-circuit monitoring* ON
Current Output Scaling Lower Limit: 3,8 mA
Upper Limit: 20,5 mA
Fault Current 22,8 mA or 3,6 mA
*Short circuit threshold shall be ≤ 5 Ω
A4US
US
A4
US A4
US
A4

7
3. Configuration of the product 4. Limitation of use
Rotork Instruments Italy S.r.l.
Via Portico, 17
24050 Orio al Serio (Bergamo) Italy
Tel +39 035 451161 FAX +39 035 531763
http: //www.soldo.net
e-mail: info.instruments-
italy@rotork.com
Additional Warning for SIL boxes
IOM00069_ENG Rev 0-4
7
4. LIMITATION OF USE
Type A
Environment:
Standard versions suitable for ambient temperature from -20°C up to +80°C. Microswitch Boxes and
Bolt Switches for low and high temperature available on request.
Environmental limits are indicated on product nameplate as indicated on samples below.
Note:
For the specific case of Pepperl+Fuchs proximity switch model SJ-3.5-S1N, switch’s lower
temperature working limit has been improved by Rotork Instruments Italy and assessed by the
Certification Body from -40°C (P+F declared value) down to -50°C performing the following tests:
1000000 cycling test at -50°C checking the functionality during the test
Two weeks stall test at -50°C checking the functionality at the end of the test.
While Pepperl+Fuchs proximity switch models SJ3,5-SN and NJ4-12GK-SN are qualified for safety
functions in a temperature range from -40°C to +100°C.
Lifetime:
The lifetime is estimated to be of 20 years.
Type B
Environment:
The ambient operating temperature range of Siemens TH320/420 and PR 5437D is -40 °C up to +80
°C; while for Siemens TH300 is -40 °C up to +85 °C.
Environmental limits are indicated on product nameplate.
Lifetime:
The useful lifetime of the Siemens TH320/420 and PR Electronics 5437D is 15 years.
Linear control range
Lower limit of the control range (default value = 3.80 mA)
Upper limit of the control range (default value = 20.5 mA)
Lower fault current value (default value = 3.6 mA)
Upper fault current value (default value = 22.8 mA)
Recommended setting range for lower fault current range and lower
control range limit
Recommended setting range for upper fault current range and upper
control range limit
Type A
Environment
Standard versions suitable for ambient temperature from
-20 to +80°C. Microswitch boxes and bolt switches for low
and high temperature available on request.
Environmental limits are indicated on product nameplate as
indicated on sample below.
Rotork Instruments Italy S.r.l.
Via Portico, 17
24050 Orio al Serio (Bergamo) Italy
Tel +39 035 451161 FAX +39 035 531763
http: //www.soldo.net
e-mail: info.instruments-
italy@rotork.com
Additional Warning for SIL boxes
IOM00069_ENG Rev 0-4
7
4. LIMITATION OF USE
Type A
Environment:
Standard versions suitable for ambient temperature from -20°C up to +80°C. Microswitch Boxes and
Bolt Switches for low and high temperature available on request.
Environmental limits are indicated on product nameplate as indicated on samples below.
Note:
For the specific case of Pepperl+Fuchs proximity switch model SJ-3.5-S1N, switch’s lower
temperature working limit has been improved by Rotork Instruments Italy and assessed by the
Certification Body from -40°C (P+F declared value) down to -50°C performing the following tests:
1000000 cycling test at -50°C checking the functionality during the test
Two weeks stall test at -50°C checking the functionality at the end of the test.
While Pepperl+Fuchs proximity switch models SJ3,5-SN and NJ4-12GK-SN are qualified for safety
functions in a temperature range from -40°C to +100°C.
Lifetime:
The lifetime is estimated to be of 20 years.
Type B
Environment:
The ambient operating temperature range of Siemens TH320/420 and PR 5437D is -40 °C up to +80
°C; while for Siemens TH300 is -40 °C up to +85 °C.
Environmental limits are indicated on product nameplate.
Lifetime:
The useful lifetime of the Siemens TH320/420 and PR Electronics 5437D is 15 years.
NOTE:
For the specific case of Pepperl+Fuchs proximity switch model
SJ-3.5-S1N, switch’s lower temperature working limit has
been improved by Rotork Instruments Italy and assessed by
the Certification Body from -40°C (P+F declared value) down
to -50°C performing the following tests:
•
1000000 cycling test at -50°C checking the functionality
during the test
•
Two weeks stall test at -50°C checking the functionality
at the end of the test
While Pepperl+Fuchs proximity switch models SJ3,5-SN
and NJ4-12GK-SN are qualified for safety functions in a
temperature range from -40 to +100°C.
Lifetime
The lifetime is estimated to be of 20 years.
Type B
Environment
The ambient operating temperature range of Siemens
TH320/420 and PR 5437D is -40 to +80 °C; while
Siemens TH300 is -40 to +85 °C.
Environmental limits are indicated on product nameplate.
Lifetime
The useful lifetime of the Siemens TH320/420 and PR
Electronics 5437D is 15 years.
While the maximum lifetime of Siemens TH300 in a safety
application is 20 years. After this the user must replace the
products.
A4 US
US
A4
US
A4
A4 US

8
Safety Manual
5. Failure modes and estimated failure rates
Type A
Microswitch Boxes configuration λD [1/h] λS [1/h] SFF [%]
With Pepperl+Fuchs NAMUR sensors,
standard NAMUR amplifier 9,6E-09 1,6E-08 > 60 > 99
including PST
With Pepperl+Fuchs NAMUR sensors,
standard NAMUR amplifier, redundant configuration <1,0E-09 <1,0E-08 > 90 > 99
including PST
With Pepperl+Fuchs NAMUR sensors,
fail-safe interface 7,0E-11 2,5E-08 > 99
With Pepperl+Fuchs sensor model NBB2-V3-E2 9,6E-09 1,6E-08 > 60 > 99
including PST
With Soldo®REED and Nova V3 sensors,
or micromechanical switches <1,0E-09 <1,0E-08 > 60 > 99
including PST
With Soldo®REED and Nova V3 sensors, or
micromechanical switches, redundant configuration 9,6E-09 1,6E-08 > 90 > 99
including PST
Soldo®Microswitch Boxes – Safety Function Type A
λd [1/h] λs [1/h] SFF [%]
4,8E-10 <1,0E-09 > 60 > 99% including Partial Stroke Test or Full Stroke Test
Soldo®BOLT – Safety Function Type A
NOTES:
•
No internal diagnostics is included in the device. Diagnostic
is only possible via external means as described in par. 6.
•
The random failure rates are estimated in the following way:
•
FMEDA of the product
•
Performing of cycling test at low and high temperature
•
Evaluation of field feedback
Rotork Instruments Italy has an effective system to manage
field feedbacks, including failure and root cause analysis.
Type B
Configuration λDU [1/h] λDD [1/h] λS [1/h] SFF [%]
Soldo®micro switch boxes with position transmitters
Siemens TH320/420 / PR electronics 5437D 2,95E-08 4,66E-07 0,00E+00 94,04%
Soldo®micro switch boxes with position transmitters
Siemens TH300 5,69E-08 1,18E- 06 0,00E+00 95,40%
λand SFF values of Soldo®microswitch boxes according to IEC 61508
NOTES:
•
The random failure rates are estimated with a FMEDA
of the product
A4US
US
A4
US A4
US
A4

9
6. Test and maintenance requirements
6.1 Proof test
Type A
The proof test should be performed at least once a year,
during the testing of the actuator-valve assembly on which
the device is mounted.
The “Proof Test” of the device corresponds to the “Full
Stroke Test” of the actuator-valve assembly. Considering the
functioning of the microswitch, the “Proof Test Coverage”
can be considered 100%.
Type B
The proof test should be performed at least once a year,
during the testing of the actuator-valve assembly on which
the device is mounted.
The procedure is the following:
Step Action
1Bypass the safety PLC or take other appropriate action
to avoid a false trip/measurement.
2
Disconnect the input signal(s) from the input terminals
and connect instead a simulator suited for simulating
the actual input setup for each active input channel.
3Apply input value(s) to each active channel,
corresponding to 0% and 100% output range.
4Observe whether the output acts as expected.
5Restore the input terminals to normal operation,
i.e. re-connect the input signal(s).
6
Measure the process value at the connected input(s)
and observe that the output current corresponds to the
applied input value(s).
7Remove the bypass from the safety PLC or otherwise
restore normal operation.
6.2 Line monitoring
In order to properly detect the fault in the field wiring,
additional resistance is required at the switch in the field.
The addition of a 1 kΩ resistor in series and 10 kΩ resistor in
parallel to the switch allows a small amount of current (i1<i)
to flow when switch change status from NC to NO, allowing
the IS barrier to detect an open or short of the field.
Line monitoring introduction
Soldo®line monitoring system provides four 10 kΩ resistors
to allow the customer to choose if connecting Normally open
logic or Normally closed logic.
Line monitoring system works only if the customer connects
terminals 1-2 and 4-5 (normally closed) or 2- 3 and 5-6
(normally open).
Line monitoring is available with:
•
Electro-mechanical SPDT, max 4 provided
•
Electro-mechanical DPDT, max 2 provided
•
Electro-magnetic N1 and N3, max 4 provided
•
Reed type SPDT, max 4 provided
•
Reed type DPDT, max 2 provided
Line monitoring performances
•
Maximum applicable voltage: 24 VDC
•
Switch 1 and 2 in NC position: circuit resistance 11 kΩ
•
Switch 1 and 2 in NO position: circuit resistance 11 kΩ
A4 US
US
A4
US
A4
A4 US

10
Safety Manual
6. Test and maintenance requirements
Rotork Instruments Italy S.r.l.
Via Portico, 17
24050 Orio al Serio (Bergamo) Italy
Tel +39 035 451161 FAX +39 035 531763
http: //www.soldo.net
e-mail: info.instruments-
italy@rotork.com
Additional Warning for SIL boxes
IOM00069_ENG Rev 0-4
10
R1=10 kΩ
R2=10 kΩ
R3=1 kΩ
1° wiring diagram: 2 switches SPDT 2° wiring diagram: one switch DPDT
Detected Faults
Fault Effect in NC Effect in NO
Open circuit R1 Not relevant* Open circuit
Open circuit R2Open circuit Not relevant*
Open circuit R3Open circuit Open circuit
Change of R1 value Not relevant* R ≠ 11 kΩ
Change of R2 value R ≠ 11 kΩNot relevant*
Change of R3 value R ≠ 1 kΩR ≠ 1 kΩ
* fault is not relevant to the safety function of paragraph 1
Excluded Faults:
According to EN/ISO 13849-2 standard, short circuit can be excluded because the resistor is of the
film type.
6.3. PARTIAL STROKE
In the case of Partial Stroke Test, the 0° position microswitch is tested at 100%, while the 90° position
microswitch is not tested.
6.4. PERIODICAL MAINTENANCE
No particular periodic maintenance is requested.
7. TROUBLESHOOTING
Type A
Problem
Possible causes
Solutions
Switches do not work Incorrect wiring Correct the wiring
Switches do not work Switches damaged Substitute
Visual position indicator does
not properly indicate valve
position
Fixing screw not properly fixed
Fix it
Open circuit Electrical failure Pcb substitution
Random change of resistance
value
Electrical failure Pcb substitution
Please note that, with the use of Pepper+Fuchs fail-safe interface (when the proximity switch allows
it), the values of d, PFDAVG and SFF are improved, and globally adequate for SIL 3 application.
1° wiring diagram: 2 switches SPDT 2° wiring diagram: one switch DPDT
Rotork Instruments Italy S.r.l.
Via Portico, 17
24050 Orio al Serio (Bergamo) Italy
Tel +39 035 451161 FAX +39 035 531763
http: //www.soldo.net
e-mail: info.instruments-
italy@rotork.com
Additional Warning for SIL boxes
IOM00069_ENG Rev 0-4
10
R1=10 kΩ
R2=10 kΩ
R3=1 kΩ
1° wiring diagram: 2 switches SPDT 2° wiring diagram: one switch DPDT
Detected Faults
Fault Effect in NC Effect in NO
Open circuit R1 Not relevant* Open circuit
Open circuit R2Open circuit Not relevant*
Open circuit R3Open circuit Open circuit
Change of R1 value Not relevant* R ≠ 11 kΩ
Change of R2 value R ≠ 11 kΩNot relevant*
Change of R3 value R ≠ 1 kΩR ≠ 1 kΩ
* fault is not relevant to the safety function of paragraph 1
Excluded Faults:
According to EN/ISO 13849-2 standard, short circuit can be excluded because the resistor is of the
film type.
6.3. PARTIAL STROKE
In the case of Partial Stroke Test, the 0° position microswitch is tested at 100%, while the 90° position
microswitch is not tested.
6.4. PERIODICAL MAINTENANCE
No particular periodic maintenance is requested.
7. TROUBLESHOOTING
Type A
Problem
Possible causes
Solutions
Switches do not work Incorrect wiring Correct the wiring
Switches do not work Switches damaged Substitute
Visual position indicator does
not properly indicate valve
position
Fixing screw not properly fixed
Fix it
Open circuit Electrical failure Pcb substitution
Random change of resistance
value
Electrical failure Pcb substitution
Please note that, with the use of Pepper+Fuchs fail-safe interface (when the proximity switch allows
it), the values of d, PFDAVG and SFF are improved, and globally adequate for SIL 3 application.
Detected faults
Fault Effect in NC Effect in NO
Open circuit R1Not relevant* Open circuit
Open circuit R2Open circuit Not relevant*
Open circuit R3Open circuit Open circuit
Change of R1value Not relevant* R ≠ 11 kΩ
Change of R2value R ≠ 11 kΩ Not relevant*
Change of R3value R ≠ 1 kΩ R ≠ 1 kΩ
* fault is not relevant to the safety function of paragraph 1
Excluded faults
According to EN/ISO 13849-2 standard, short circuit can be
excluded because the resistor is of the film type.
6.3 Partial stroke
In the case of Partial Stroke Test, the 0° position microswitch
is tested at 100%, while the 90° position microswitch is not
tested.
6.4 Periodical maintenance
No particular periodic maintenance is requested.
A4US
US
A4
US A4
US
A4

11
7. Troubleshooting
Type A
Problem Possible causes Solutions
Switches do not work Incorrect wiring Correct the
wiring
Switches do not work Switches
damaged
Substitute
Visual position indicator
does not properly
indicate valve position
Fixing screw not
properly fixed
Fix it
Open circuit Electrical failure PCB substitution
Random change of
resistance value
Electrical failure PCB substitution
Please note that, with the use of Pepper+Fuchs fail-safe interface (when the
proximity switch allows it), the values of λd, PFDAVG and SFF are improved, and
globally adequate for SIL 3 application.
Type B
On detection of a fault, the output goes out-of-range
(Safe State), according to the following table.
Micro switch box series
Output behaviour on
detection of a fault
Soldo®micro switch boxes with
position transmitters Siemens
TH320/420 / PR electronics 5437D
Output ≤ 3,6 mA or
Output ≥ 22,8 mA
Soldo®micro switch boxes with
position transmitters Siemens TH300
Output ≤ 3,5 mA or
Output ≥ 23 mA
A suitable configuration tool is able to show the diagnostic
message describing the detected error:
•
If the fault is caused by a sensor error or sensor wiring,
the LED on transmitter will flash red and the correct
output current will automatically be re-established when
the fault has been corrected
•
If the fault is in the device itself (detected by internal
diagnostic measures), the LED on the transmitter will light
constantly RED
There are 2 ways of bringing the device out of Safe State:
1. Power-cycle the device
2. Reset the device by using a configuration tool that
supports a reset of the device. If the error is persistent,
the device will enter the Safe State again
8. Hardware fault tolerance
Type A
The normal HFT of the device is 0, unless the case of
microswitch boxes (e.g. using Nova V3 DPDT switch) or bolt
switches in which two microswitches are used “in parallel” to
obtain redundancy. The connection to obtain this redundancy
is up to the final user.
Route 2H for architectural constraints is applied.
Rotork Instruments Italy S.r.l.
Via Portico, 17
24050 Orio al Serio (Bergamo) Italy
Tel +39 035 451161 FAX +39 035 531763
http: //www.soldo.net
e-mail: info.instruments-
italy@rotork.com
Additional Warning for SIL boxes
IOM00069_ENG Rev 0-4
11
Type B
On detection of a fault, the output goes out-of-range (Safe State), according to the following table.
Micro switch box series
Output behaviour on detection of a fault
Soldo™ micro switch boxes with position
transmitters Siemens TH320/420 / PR electronics
5437D
Output ≤ 3,6 mA or Output ≥ 22,8 mA
Soldo™ micro switch boxes with position
transmitters Siemens TH300 Output ≤ 3,5 mA or Output ≥ 23 mA
A suitable configuration tool is able to show the diagnostic message describing the detected error:
If the fault is caused by a sensor error or sensor wiring, the LED on transmitter will flash red
and the correct output current will automatically be re-established when the fault has been
corrected.
If the fault is in the device itself (detected by internal diagnostic measures), the LED on the
transmitter will light constantly RED.
There are 2 ways of bringing the device out of Safe State:
1. Power-cycle the device.
2. Reset the device by using a configuration tool that supports a reset of the device. If the
error is persistent, the device will enter the Safe State again.
8. HARDWARE FAULT TOLERANCE
Type A
The normal HFT of the device is 0, unless the case of microswitch boxes ( e.g. using Nova V3 DPDT
switch ) or Bolt Switches in which two microswitches are used “in parallel” to obtain redundancy. The
connection to obtain those redundancy is up to the final user.
Route 2Hfor architectural constraints is applied.
Type B
The product has normally a single channel configuration, HFT=0.
A 1oo2 configuration can be obtained in this ways:
with one single micro switch box, internally completely redundant (2 potentiometers, 2
position transmitters, 2 separate outputs)
with two micro switch boxes, each one internally in single channel configuration
In both cases, the two analog outputs shall be voted 1oo2 by the downstream controller.
9. CLASSIFICATION
Type A
The product is classified Type A according to IEC 61508.
Type B
The product is classified Type B according to IEC 61508.
View 14
shows an
example of realization
of a redundant
configuration
View 14 shows an example of realization of a redundant
configuration
Type B
The product has normally a single channel configuration,
HFT=0. A 1oo2 configuration can be obtained as follows:
•
with one single micro switch box, internally completely
redundant (2 potentiometers, 2 position transmitters,
2 separate outputs)
•
with two micro switch boxes, each one internally in single
channel configuration In both cases, the two analog
outputs shall be voted 1oo2 by the downstream controller
9. Classification
Type A
The product is classified Type A according to IEC 61508.
Type B
The product is classified Type B according to IEC 61508.
10. Mean repair time
In case of failure, the complete limit switch box must be
substituted. So the mean repair time (MRT) is four hours
(conservative value).
The MRT is estimated considering availability of skilled
personnel for maintenance, spare parts and adequate tools
and materials on site (i.e. it encompasses the actual time to
repair and the time before the component is put back into
operation).
11. Systematic capability
The systematic capability of the device is 3.
This systematic capability is guaranteed only if the user:
1. Uses the device according to the instructions for use
2. Uses the device in the appropriate environment
A4 US
US
A4
US
A4
A4 US

Rotork plc
Brassmill Lane, Bath, UK
tel +44 (0)1225 733200
fax +44 (0)1225 333467
email [email protected]
As part of a process of on-going product development, Rotork reserves the right to amend and change
specifications without prior notice. Published data may be subject to change. For the very latest version
release, visit our website at www.rotork.com
The name Rotork is a registered trademark. Rotork recognises all registered trademarks. Published and
produced in the UK by Rotork. POWTG0120
Rotork is a corporate
member of the Institute
of Asset Management
PUB109-157- 00
Issue 01/20
www.rotork.com
A full listing of our worldwide sales and
service network is available on our website.
A4US
US
A4
US A4
US
A4
A4 US
US
A4
US
A4
A4 US
This manual suits for next models
15
Table of contents
Other rotork Switch manuals
Popular Switch manuals by other brands
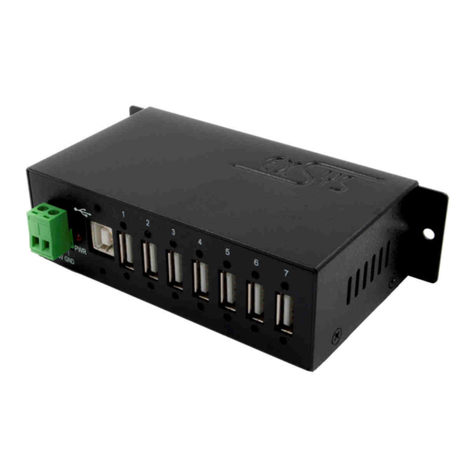
Exsys
Exsys EX-1177HMVS manual

Lutron Electronics
Lutron Electronics Maestro MS-B202 installation guide
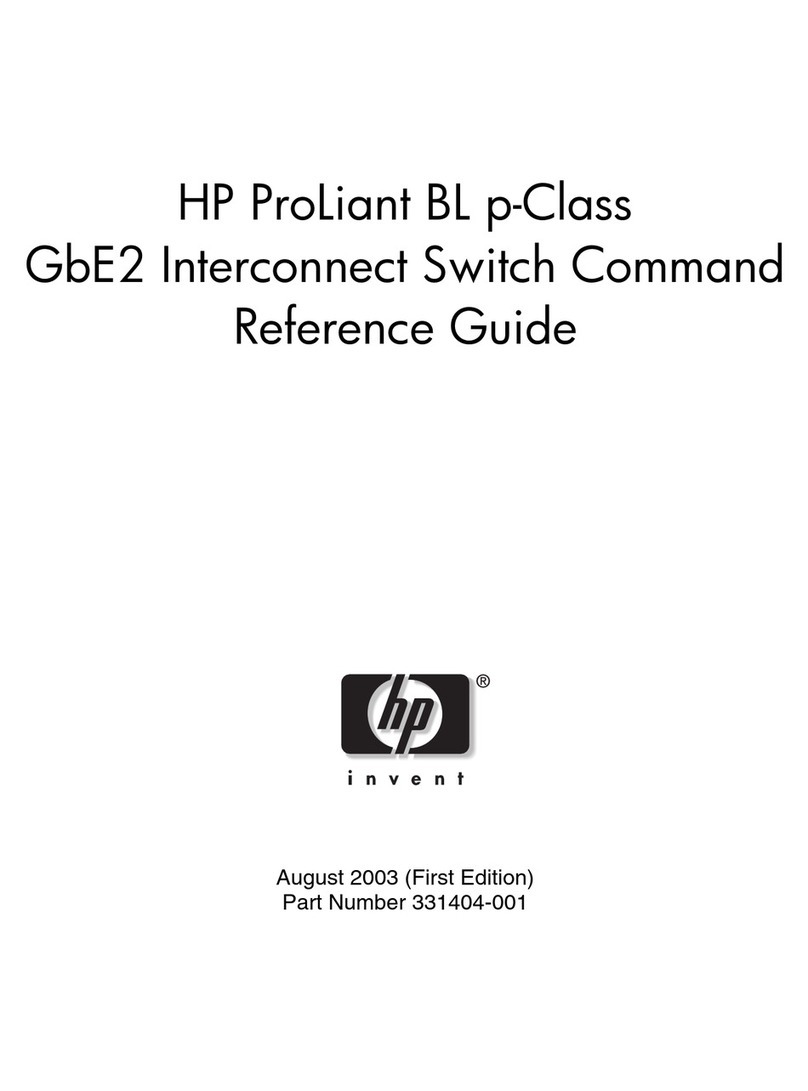
HP
HP ProLiant BL p-Class GbE2 Command reference guide
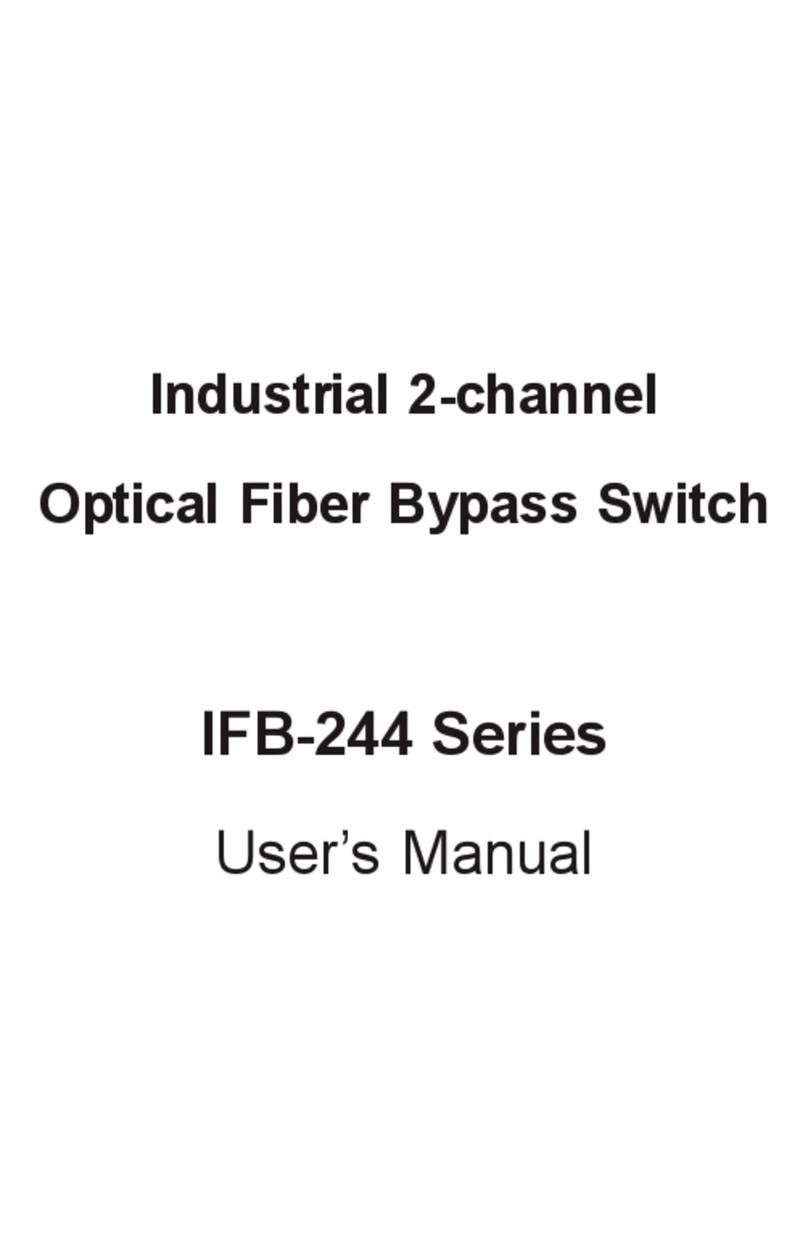
Planet
Planet IFB-244-SLC user manual
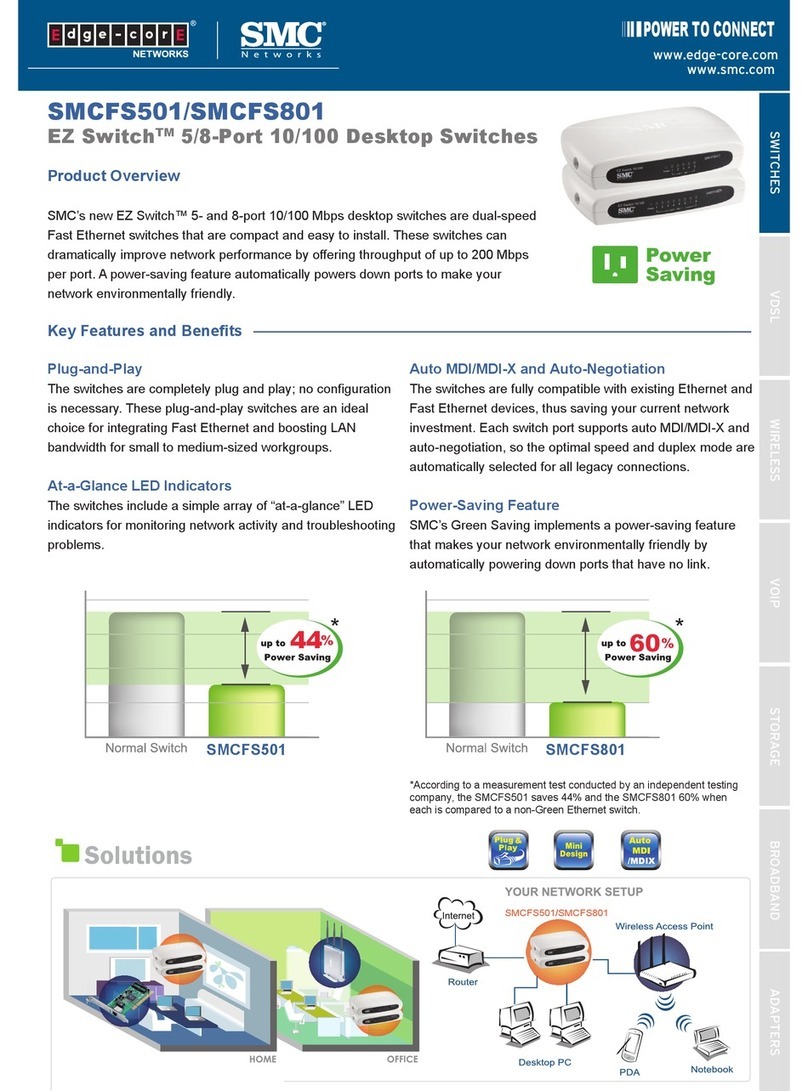
SMC Networks
SMC Networks SMCFS501 - FICHE TECHNIQUE Product overview
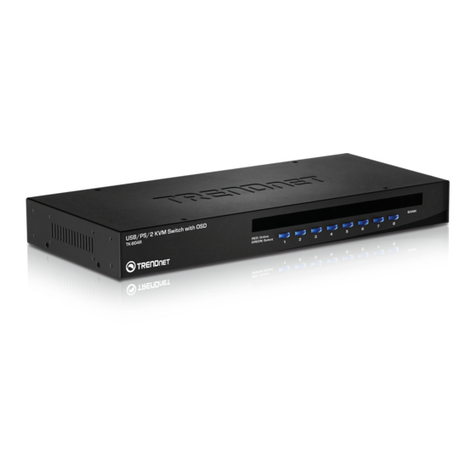
TRENDnet
TRENDnet TK-804R Quick installation guide