Royal Enfield M2d User manual

M2d
Proportional Pneumatic Control Valve with integrated Driver
Product Manual
Page 1 of 15
M2d
Proportional Pneumatic Control Valve with Integrated Driver
Product Manual

M2d
Proportional Pneumatic Control Valve with integrated Driver
Product Manual
Page 2 of 15
Contents
Warnings & Notices _____________________________________________________________ 3
Overview _____________________________________________________________________ 4
Typical Applications _____________________________________________________________ 5
Product Layout_________________________________________________________________ 6
Product Specifications ___________________________________________________________ 7
System Requirements____________________________________________________________ 7
Components _______________________________________________________________________ 8
Tools_____________________________________________________________________________ 8
Configuration _______________________________________________________________________ 8
Implementation Instructions _______________________________________________________ 9
Receipt Inspection & Handling _________________________________________________________ 10
Installation and Removal _____________________________________________________________ 10
Start-Up & Shutdown ________________________________________________________________ 10
Wiring External Connections (using CBL-001 and CBL-003) ____________________________________ 11
LED Indicators _____________________________________________________________________ 12
Configuration of Command Signal via DIP Switch Settings_________________________________ 13
Calibration & Periodic Maintenance_________________________________________________ 13
Configuring and Tuning for Closed-Loop Control _____________________________________________ 14
Product Warranty ______________________________________________________________ 15

M2d
Proportional Pneumatic Control Valve with integrated Driver
Product Manual
Page 3 of 15
Warnings & Notices
WARNING:
Installation and operation of electric and high pressure systems (fluids and compressed gas) involves risk including
property damage and personal injury or death.
Installers and users should be properly trained or certified and take safety precautions. This product may cause
death, personal injury, or property damage if improperly used or installed.
The information in this document and other information from Enfield Technologies and its authorized representatives
are intended for use by persons having technical expertise in selecting and using these products. Product owners
(“you”) should analyze all technical and safety requirements of your specific application, including the
consequences of any possible failure, before selecting a product. This product may not be suitable for all
applications, such as those acting upon people. Suitability is solely your responsibility. Because the requirements
for each application may vary considerably, you are solely responsible for conducting any testing or analysis that
may be required to determine the suitability of the product for your application, and to ensure that all performance,
safety and warning requirements for your application are met.
Caution:
While the product is low voltage, it is an open-frame electronic component and care should be taken to prevent un-
intentional contact with the product to avoid damage to person or property.
The M2d is an electro-static sensitive device. Use appropriate electro-static discharge (ESD) procedures during
handling and installation.
Notice:
Use and purchase of this product is subject to Enfield Technologies’ Terms and Conditions of Sale and Use.
Improper installation or use voids warranty. Consult factory regarding special applications. Specifications are
subject to change. Reasonable efforts have been made to provide useful and correct information in this document,
but this document may contain errors and omissions, and it is subject to change.
Contact: Enfield Technologies
35 Nutmeg Drive
Trumbull, CT 06611 USA
+1 203 375 3100
+1 800 504 3334 toll free North America
www.enfieldtech.com

M2d
Proportional Pneumatic Control Valve with integrated Driver
Product Manual
Page 4 of 15
Overview
The M2d is an instrument-grade, proportional, pneumatic
directional control valve with an integrated driver. The M2d
utilizes a specialized linear force motor rather than a
traditional proportional solenoid.
The valve includes integrated on-board driver electronics, as
well as a feedback output to monitor valve activity and a
drive sleep interrupt input. The highly efficient bi-directional
motor driver includes factory calibrated dither and deadband
elimination settings. Onboard signal conditioning accepts
either voltage or current command signals.
The aperture of the M2d is controlled at very high speed, allowing the valve to respond quickly to set-point
command changes. When at a given set-point, the aperture is held steady rather than pulsing to create an average
flow from a duty cycle. The result is high fidelity - commands are faithfully reproduced increasing overall system
performance.
Internal construction allows the valve to operate from vacuum through high pressure simultaneously. Common
applications include the control of position, pressure, force or flow. The M2d is suitable for both open-loop and
closed-loop systems.
M2d
drive
controller
master
control
valve
plant
sensor
signal
treatment
signal
treatment
loop
controller
actuator
set
point
Ws
Wm
Xm
Xs
Wp
Wc
driver
process
variable
M2d Valve Diagram (ISO 1219)

M2d
Proportional Pneumatic Control Valve with integrated Driver
Product Manual
Page 5 of 15
Typical Applications
There are numerous applications and configurations for the M2d. Below are a chart of generic application
descriptions and three common applications in pneumatics.
Control Objective
Technology
Control Scheme
Position
Mass Flow
Pneumatic
Open-Loop
Motion
Volumetric Flow
Closed-Loop
Pressure
Velocity (speed)
Force
Others
Basic Closed-Loop Proportional Pneumatic Position Control System
Basic Closed-Loop Proportional
Gas Pressure Control System
Basic Open-Loop Proportional
Gas Flow Control System
master
control
compressed
air
set
point
pressure
sensor
M2d valve
1
24
5 3
pressure
controlled
volume
vacuum
master
control
compressed
air
set
point
pressure
sensor
M2d valve
1
24
5 3
M2d valve
1
24
5 3
pressure
controlled
volume
vacuum
master
control
compressed
air
set
point M2d valve
1
24
5 3
process
master
control
compressed
air
set
point M2d valve
1
24
5 3
M2d valve
1
24
5 3
process
master
control
compressed
air
set
point
actuator with internal position feedback sensor
M2d
valve
1
2
4
5
3
atm
atm
extend
retract
load
valve
command

M2d
Proportional Pneumatic Control Valve with integrated Driver
Product Manual
Page 6 of 15
Product Layout
Top View Photo
Bottom View Photo

M2d
Proportional Pneumatic Control Valve with integrated Driver
Product Manual
Page 7 of 15
Product Specifications
System Requirements
Specification
Value
Physical Characteristics
SI Units
Imperial Units
Mass (Weight)
0,852 kg
(30.0 oz)
Approximate Physical Dimensions (L x W x H)
171.9 mm x 55.0 mm x 45.0 mm
6.77” x 2.17” x 1.77”
Materials
Aluminum, Nitrile, 440C SS, 316 SS, Nickel Plated Steel, Glass-Filled Nylon
Valve Function
5-Port Bi-Directional Flow Control Valve, Normally Closed Center
Valve Type
Lapped Spool and Sleeve
Control Mechanism
Direct-Acting, Patented Linear Force Motor
Ports
3/8” NPTF
Mounting Direction
Stationary: Perpendicular to gravity
Moving: Perpendicular to direction of motion
Performance Characteristics
Shifting Time (ISO 12238)
2.8 ms
Bandwidth
110 Hz
Pressure (at any port)
Vacuum 1.5 MPa (15 bar)
Vacuum 225 psig
Maximum Effective Aperture
30 mm2
0.047 in2
Flow Capacity and Critical Pressure Ratio (ISO 6358)
C = 4.5 x10-8 s·m4/kg; b 0.4
Cv= 0.9
Flow Rate of Air at 20 C (68F) and 65% RH
(refer to Mass Flow Graphs)
900 SLPM
(6.0 bar 5.0 bar)
60 SCFM
(80 psig atm)
Leakage Rate (80psig atm)
0.6 SCFM
Turndown Ratio
200:1
Electrical Characteristics
Power
20W Max
Supply Voltage
24Vdc Nom. (12-36Vdc)
Current
1.1A Max
Electrical Connections
Alden PL500 6-Pin (Command), Alden P500 4-pin (Power)
1
Input Impedance
120 kΩ
Input Signal Ranges
-10 Vdc to 10 Vdc
-5 Vdc to 5 Vdc
-0 Vdc to 5 Vdc
---0 Vdc to 10 Vdc
--0 mA to 20 mA
---4 mA to 20 mA
Output Signal
0 to 5 Vdc Valve Current Monitor
Status LED’s
Power On, Reverse Polarity Warning, Operating Condition
Environmental Characteristics
Environmental Protection Class
IP65
Temperature
0C – 50C
32F – 122F
Humidity
5% - 95% RH
Filtration Requirements
Clean, dry, non-lubricated air; 5 µm particulate and 0.3 µm coalescing
filters recommended.
Lubrication Requirements
Lubrication is not recommended and may void warranty.
Operating Fluids
Inert, non-flammable pneumatic fluids only. No liquids.

M2d
Proportional Pneumatic Control Valve with integrated Driver
Product Manual
Page 8 of 15
The following components are minimally required to implement a system. Refer to the Product Specifications and
Configuration Instructions for details.
Components
Component
Notes
Recommendations & Sources
24V DC, 30W power
supply
Power supply to convert AC line voltage to
low voltage DC system power.
Enfield Technologies A-PWR-BS-24V-36W
Command cable
--
Enfield Technologies part number:
A-CBL-A1-06P-M-XX00
Power cable
--
Enfield Technologies part number:
A-CBL-A1-04P-M-XX00
Command signal
source
Voltage/Current command (see Product
Specifications) from a “master controller”
such as a computer or PLC; a simple
potentiometer is sufficient.
Enfield Technologies ASG-1 Signal Source
if a simple potentiometer is needed
(requires regulated excitation voltage; LS-
Cable optional)
Pneumatic device*
If not using for flow control into the
atmosphere, the system will have a “device”
being controlled such as an actuator or
pressure chamber (fixed or flexible)
Enfield Technologies ACT family actuators
with internal position feedback sensors if a
double acting air cylinder is needed
(requires regulated excitation voltage and
LS-Cable)
Tools
Small flat head screw driver (preferably with a non-conductive shaft)
For connecting wires to terminal blocks
For making tuning and setting adjustments to rotary potentiometers
Wire cutter & stripper
Voltmeter (recommended)
Optional, but recommended for tuning and diagnostics
Multimeter recommended to also permit measurement of current and resistance
2 or 3 channel oscilloscope recommended for advanced system tuning and diagnostics
Configuration
Analog signal grounds (“DC common”) for all system electronics that interrelate with each must be tied together
(made common)

M2d
Proportional Pneumatic Control Valve with integrated Driver
Product Manual
Page 9 of 15
Implementation Instructions
The M2d can be used in many applications. Accordingly, it can be configured in many ways. These configuration
instructions cover standard open-loop and closed-loop implementations as well as some advanced variations. The
concepts of open-loop versus closed-loop systems, are important to implementing this or any pneumatic control
system.
WARNING:
Installation and operation of electric and high pressure systems (fluids and compressed gas) involves
risk including property damage and personal injury or death.
Installers and users should be properly trained or certified and take safety precautions. This product may
cause death, personal injury, or property damage if improperly used or installed.
The information in this document and other information from Enfield Technologies and its authorized
representatives are intended for use by persons having technical expertise in selecting and using these
products. Product owners (“you”) should analyze all technical and safety requirements of your specific
application, including the consequences of any possible failure, before selecting a product. This product
may not be suitable for all applications, such as those acting upon people. Suitability is solely your
responsibility. Because the requirements for each application may vary considerably, you are solely
responsible for conducting any testing or analysis that may be required to determine the suitability of
the product for your application, and to ensure that all performance, safety and warning requirements
for your application are met.
Caution:
While the product is low voltage, it is a sensitive electronic component and care should be taken to prevent un-
intentional contact with the product to avoid damage to person or property.
The M2d is an electro-static sensitive device. Use appropriate electro-static discharge (ESD) procedures during
handling and configuration.
Notice:
Use and purchase of this product is subject to Enfield Technologies’ Terms and Conditions of Sale and Use.
Improper installation or use voids warranty. Consult factory regarding special applications. Specifications are
subject to change. Reasonable efforts have been made to provide useful and correct information in this document,
but this document may contain errors and omissions, and it is subject to change.

M2d
Proportional Pneumatic Control Valve with integrated Driver
Product Manual
Page 10 of 15
Receipt Inspection & Handling
Upon receipt, ensure the packaging is intact and the product is not damaged.
Use care when handling the product. Avoid inadvertent contamination of the ports
Observe common electro-static discharge (ESD) procedures when configuring the command signal DIP
switches.
Non-conductive tools are recommended, such as those with polymer or carbon-fiber type shafts.
Installation and Removal
(Do not leave the command signal floating. A command signal must be present whenever power is applied to the
valve. The factory default command signal range is 0…10 Vdc. Make sure to apply a 5 Vdc command signal when
power is applied to hold the valve in the closed position)
Install the M2d as follows:
Verify the desired command signal input
o(see following section: Configuration of Command Signal via DIP Switch Settings)
Install the M2d using the two (2) mounting holes provided.
Connect all signal and power connections to the appropriate connectors on the M2d.
Connect the M2d to the target apparatus pneumatically and ensure that the apparatus and the surrounding
area are safe for operation.
Connect the M2d to the pneumatic supply (see filtration requirements in Product Specifications)
Configure and tune the master controller as required for specific application.
Remove the M2d as follows:
Ensure the target apparatus is in a safe state.
Disconnect the pneumatic supply from the M2d
Remove the pneumatic connections between the M2d and the target apparatus
Disconnect all signal connections from the M2d
Remove the two (2) mounting screws.
Package the Device Controller in appropriate packaging (the original packaging is preferred).
Start-Up & Shutdown
Ensure that the electromechanical system is in a state such that the system is safe, even in the event of unexpected
system operation.
Ensure that your application will remain safe before making any change (powering down, removing valve,
powering on, etc) even in the event of unexpected valve operation
Ensure that the M2d is properly connected to the master controller on startup to ensure proper valve operation
Ensure that the target apparatus is properly connected to the M2d on startup to ensure proper operation
Apply or remove the command signal to the M2d (verify actual command signal)
Apply or remove electrical power to the M2d
Apply pneumatic supply last on start-up.
Remove pneumatic supply first on shutdown

M2d
Proportional Pneumatic Control Valve with integrated Driver
Product Manual
Page 11 of 15
Wiring External Connections (using CBL-001 and CBL-003)
(Do not leave the command signal floating. A command signal must be present whenever power is applied to the
valve. The factory default command signal range is 0…10 Vdc. Make sure to apply a 5 Vdc command signal when
power is applied to hold the valve in the closed position)
Power Cable – CBL-001
(+PWR) connect the power input to a 24 Volt DC power supply (+) output (minimum 1.0A, 25W).
(PGND) connect the ground to the power supply ground (-) output.
(/DRVSLP) connect the drive sleep input to ground (PGND) to disable the valve driver.
(N/C) no connection
Command Cable – CBL-003
(CMD+) command signal input (+), connect to the master controller command signal output
(CMD-) command signal input (-), connect to the master controller command signal output
o(or connect directly to AGND for 0...5…10 Vdc command signals)
(AUX1+) functionality not supported by the M2d
(AUX1-) functionality not supported by the M2d
(IFBK) current feedback output (0…5 Vdc)
(AGND) connect the ground to the power supply ground (-) output

M2d
Proportional Pneumatic Control Valve with integrated Driver
Product Manual
Page 12 of 15
Common Ground: All DC powered components in the system should share a common ground to reduce the
chance that power anomalies will create erroneous command or feedback signals.
Shared Power Supply: Enfield Technologies recommends that if a common power supply is used for both the
M2d and the feedback sensor, that it should have a separately regulated power supply connections for the
valve and the sensor.
LED Indicators
The M2d is equipped with three LED indicators:
Power Indicator: Upon successful powering of the device, the power indicator will light green. If the power
connections are reversed, the power indicator will light red.
Power LED
Condition
Off
Power Off
Green
Normal Operation
Red
Reversed Power Connection
Status Indicators 1 and 2: Both status indicators will light green for one second, after which they will light
amber for one second. After this sequence, the states of these two LEDs describe the operation of the Device,
as outlined in below.
Status LED 1
Status LED 2
Condition
Off
Off
Normal Operation
Blinking Amber (Quickly)
Any
Short Circuit Fault
Blinking Green (Slowly)
Any
Open Circuit Fault
Any
Green (Solid)
Reference Voltage Error
Any
Amber (Solid)
Symmetry Fault

M2d
Proportional Pneumatic Control Valve with integrated Driver
Product Manual
Page 13 of 15
Configuration of Command Signal via DIP Switch Settings
Configure the Command Signal Input as follows
Remove the spanner ring from each connector
Remove the four (4) Phillips-head screws from the cap
Remove the cap and adjust the DIP switch settings
Note: The Factory Default Command Signal Setting is (0V →+10V)
Command Signal
SW1
SW3
1 2 3 4
5 6 7 8
1
-10V →+10 V
О
О
-5 V →+5V
О
О
0V →+5V
О
О
0V →+10V
О
О
0mA →+20mA
О
О
О
4mA →+20mA
О
О
О
Notes: (O) Indicates Dip Switch in the ON Position
SW2 functionality not supported by the M2d
Calibration & Periodic Maintenance
The M2d does not require periodic factory calibration, but periodic tuning of the control system may be required due
to physical changes (friction, machine and/or parts wear, etc) in the system under control and to account for any
sustained changes in the operating environment’s conditions such as temperature and humidity. Keep the M2d free
from dirt, debris, and excessive moisture.
SW1 DIP switches:
#2 and #8 in the ON position
In this view #8 is on the left, and
#1 is on the right
ON is towards the edge of the valve
SW2 not used by the M2d
SW3 DIP switches
#1 and #2 in the OFF position
In this view #2 is on the left,
and #1 is on the right
ON is towards the edge of the valve

M2d
Proportional Pneumatic Control Valve with integrated Driver
Product Manual
Page 14 of 15
Decommissioning & Corrective Maintenance
The device is not serviceable in the field. If corrective maintenance is required, contact the manufacturer for return
authorization at +1 203 375 3100 (+1 800 504 3334 toll free in North America) or via email at
Configuring and Tuning for Closed-Loop Control
These instructions use a proportional pneumatic positioning system adjusted for high response as an example.
Tuning for a pressure, force, or closed-loop mass flow control system is similar even thought the sensors and valve
plumbing may be different.
Tuning Theory
The objective of tuning is to make the system stable under its maximum expected load while seeking to achieve
accuracy, minimal overshoot, minimum or maximum speed, or other performance objectives. Many system
parameters influence stability including friction, command and feedback signal accuracy and quality (noise), and
exogenous disturbances.
In full PID systems, there are many established tuning theories and methods, most notably the Ziegler-Nichols
method. Advanced control methods are complex because changes in tuning one term often affects the other terms,
and thus the process can be recursive with several possible solutions. Academic and practical information on these
theories and methods are widely available.
Tuning a pneumatic system is more of an art than a science. The system probably has components from several
different vendors and the components all have different dynamics characteristics such as friction, variations in
signal levels, and so forth. Every application has a different set of parameters including the amount and physical
orientation of the load, the speed at which the system must operate and the desired smoothness of operation, and
the operating environment. Even identically configured systems have differences due to slight variations in the many
parts used to make each component. Assuming that the system is required to respond rapidly, it must be tuned to
operate “on the edge” of oscillation. That is, the system should be tuned to respond quickly to a command without
breaking into uncontrolled oscillation or “hunting” because of signal over-saturation or target overshoot.

M2d
Proportional Pneumatic Control Valve with integrated Driver
Product Manual
Page 15 of 15
Product Warranty
This product is covered by Enfield Technologies’ standard 1-year Limited Warranty. The terms of the Limited
Warranty are subject to change. The Limited Warranty is available online at www.enfieldtech.com or by request (see
contact information below).
Product Revision and Change Record
Contact information:
Enfield Technologies
35 Nutmeg Drive
Trumbull, CT 06611
USA
+1 203 375 3100
+1 800 504 3334
Toll free North America
www.enfieldtech.com
Table of contents
Popular Control Unit manuals by other brands
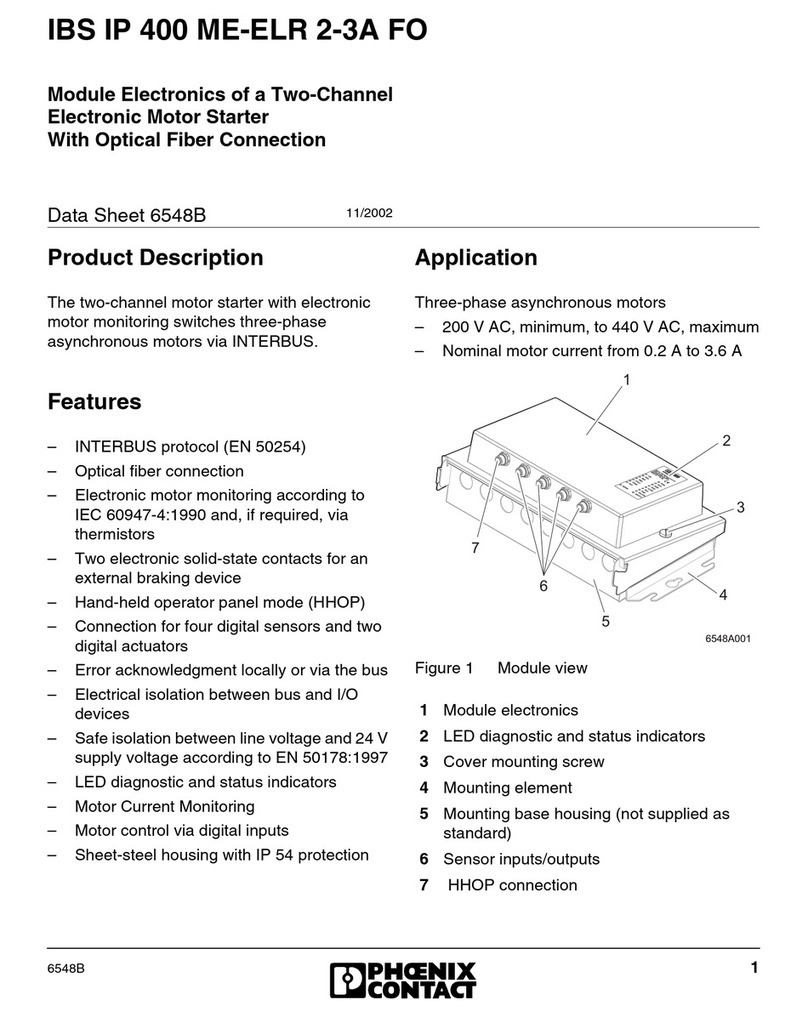
Phoenix Contact
Phoenix Contact IBS IP 400 ME-ELR 2-3A FO datasheet

KLINGER
KLINGER 3530 Installation operation & maintenance
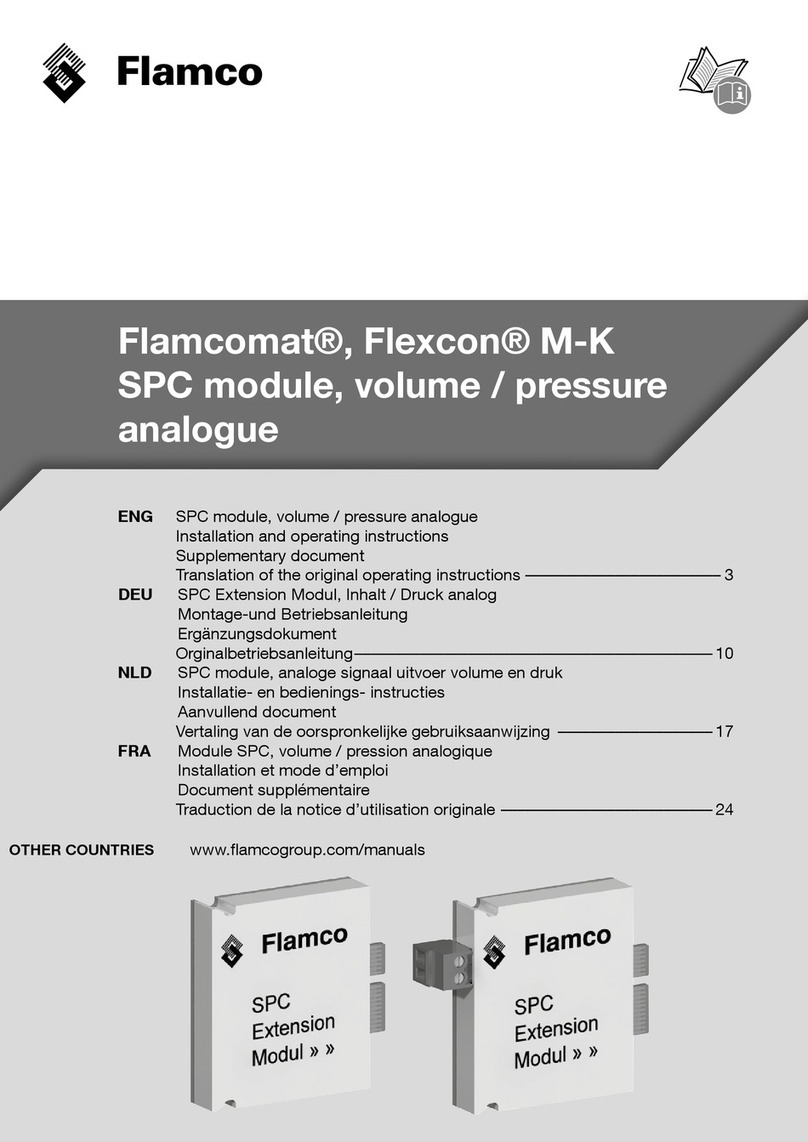
flamco
flamco SPC Extension Module Supplementary Document

KIESELMANN
KIESELMANN 5093 xxx 000 series operating instructions
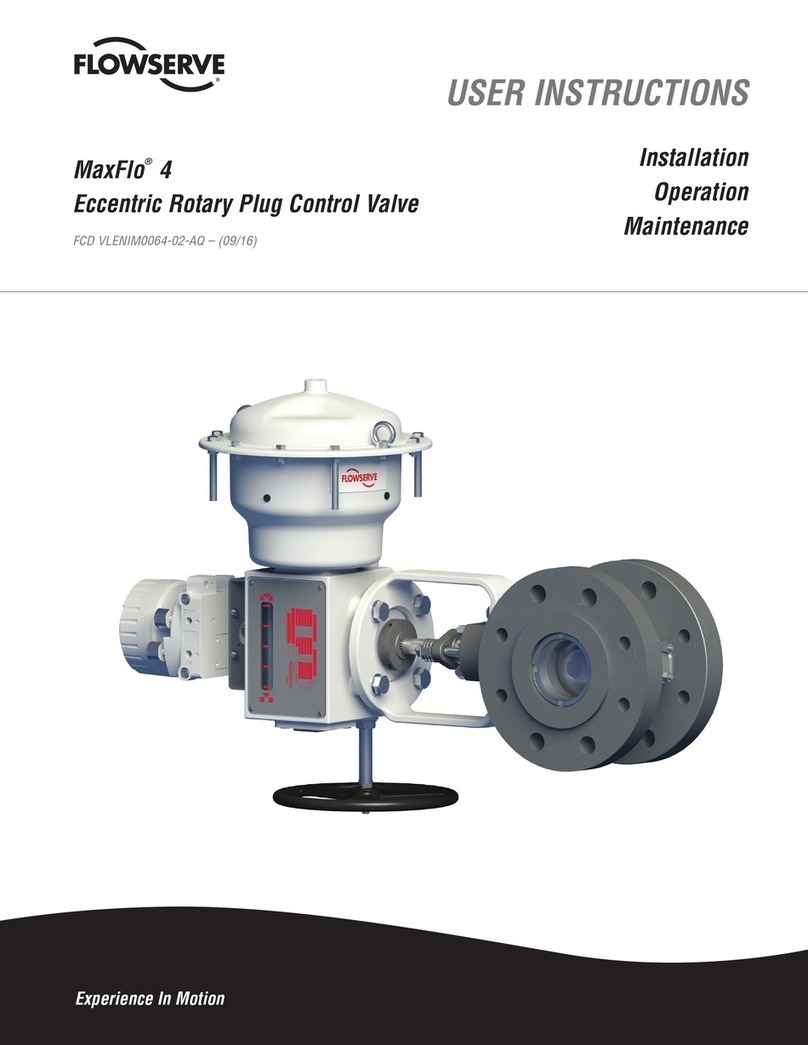
Flowserve
Flowserve MaxFlo4 User instructions
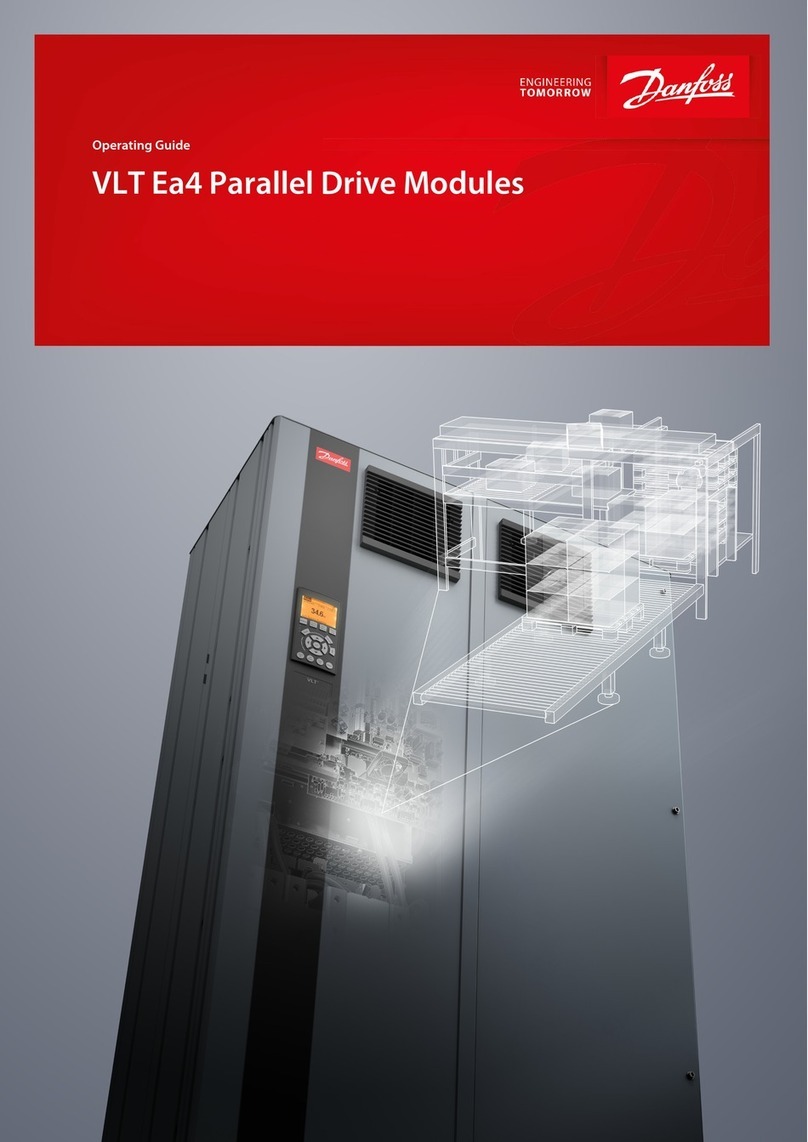
Danfoss
Danfoss VLT Ea4 operating guide