RSSI RSS-4000 Series User manual

02/05/2018 INSTALLATIONGUIDELINES
PAGE 2
Table of Contents
1GENERAL.....................................................................................................................................................4
1.1 LIMITED WARRANTY ............................................................................................................................................................ 4
2INSTALLATION..........................................................................................................................................5
2.1 INTRODUCTION...................................................................................................................................................................... 5
2.2 SAFETY ................................................................................................................................................................................. 5
2.2.1 Safety Precautions............................................................................................................................................................ 5
2.3 MOBILIZATION...................................................................................................................................................................... 5
Figure 2-1, RSS-4000.................................................................................................................................................................... 5
Table 2-1 –RSS-4000 SeriesDimension Chart............................................................................................................................. 6
Figure 2-2, RSS-4000.................................................................................................................................................................... 6
2.4 INSTALLATION INSTRUCTIONS.INSTALLING THE RSS-4000IS A SIMPLE 5-STEP PROCESS..................................................... 6
2.4.1 STEP ONE -EXCAVATE.......................................................................................................................................................... 6
Figure 2-3, Excavation.................................................................................................................................................................. 7
Table 2-2, Excavation Details....................................................................................................................................................... 7
2.4.2 STEP TWO –PLACE BARRIER................................................................................................................................................. 7
Figure 2-4, Barrier Placement...................................................................................................................................................... 7
2.4.3 STEP THREE –CONDUITCONNECTIONS................................................................................................................................. 7
Figure 2-5, Conduit Connections.................................................................................................................................................. 8
2.4.4 STEP FOUR –CONCRETE ........................................................................................................................................................ 8
Figure 2-6, Concrete..................................................................................................................................................................... 9
2.4.5 STEP FIVE –CONDUITAND TERMINATION OF CONTROLS.................................................................................................... 10
Figure 2-7, EPU Control Panel &Battery Back-up.................................................................................................................... 10
2.4.5.1INSTALLATION OF SHIELDED ETHERNETCABLE FROM BARRIER TO BARRIER CONTROL PANEL (BCP)................................ 12
Figure 2-8, Controls Conduit, Ethernet Run Into J-box. ............................................................................................................. 12
Figure 2-9, Ethernet Connection at EPU, Ethernet Wiring Diagram.......................................................................................... 12
Figure 2-10, EPU Ethernet Switch.............................................................................................................................................. 13
Figure 2-11, Ethernet Connection and Ground........................................................................................................................... 13
Figure 2-12, Servo Drive Box Inside Barrier.............................................................................................................................. 14
2.4.5.2INSTALLATION,TERMINATION,ANDTESTINGOF FIBER CABLE............................................................................................ 14
2.4.6 JOB DOCUMENTATION......................................................................................................................................................... 16
3COMMISSIONING....................................................................................................................................16
3.1 START-UP......................................................................................................................................................................... 16
3.2 TEST.................................................................................................................................................................................. 16
ATTACHMENT 1, START-UP/TURN-OVER PROCEDURES.................................................................18
ATTACHMENT 2, SAFETY LOOP SET-UP................................................................................................22
Figure 1, Safety Loop Detector ................................................................................................................................................... 22
Figure 2, Factory settings for loop detector................................................................................................................................ 22
ATTACHMENT 3, SERVO DRIVE SET-UP ................................................................................................23
Figure 9, Home Menu................................................................................................................................................................. 23
Figure 10, Main Menu................................................................................................................................................................ 23
Figure 11, Barrier Control Menu................................................................................................................................................ 24
ATTACHMENT 4, VEHICLE DETECTORLOOP INSTALLATION GUIDE......................................25
Figure 1 Figure 2 Figure 3.................................................................................................................................................. 25
Figure 4 Figure 5.................................................................................................................................................................. 25
Figure 6 Figure 7.................................................................................................................................................................. 26
Illustration 1................................................................................................................................................................................ 26
.................................................................................................................................................................................................... 27

02/05/2018 INSTALLATIONGUIDELINES
PAGE 3
ATTACHMENT 5, TRAFFIC LIGHT INSTALLATION...........................................................................28
Figure 1, Traffic Light PoleBase................................................................................................................................................ 28
FIGURE 2,TRAFFIC LIGHT CONFIGURATIONS –2 & 3 LIGHTS.........................................................28
ATTACHMENT 6, WATER-PROOF CONNECTORS...............................................................................29

02/05/2018 INSTALLATIONGUIDELINES
PAGE 4
1GENERAL
This document describes the basic installation of the RSSI 4000 Series Electric Bollard Vehicle Barrier. It is
NOT all encompassing and is based on “typical”installations. Integrators/Contractors are highly encouraged
to review these guidelines and contact RSSI to clarify any issues or to answer questions prior to Mobilization.
RSSI is a barrier manufacturer; on questions related to civil issues specific to a particular jobsite,
Integrators/Contractors should refer to the Architectural Firm that designed the project or a licensed Civil
Engineer familiar with the local site conditions and requirements.
1.1 Limited Warranty
RSSI Barriers, LLC Warrants the RSS-4000 Series of Barriers (RSS-4002, RSS-4003) to be free of defects in
workmanship and materials for a period of 1 year for electrical and mechanical components –PARTS
ONLY. Warrantywill begin from the date of shipment from the factoryor if installed by RSSI Barriers LLC,
from the date ofinstallation unless otherwise agreed on.
RSSI Barriers, LLC reserves the right of final determination as to the existence and causes of any defect or
failure. Any part or parts found to be defective and that are returned to RSSI Barriers, LLC within the
warranty period, shall at our option be repaired or replaced free of charge F.O.B. the factory. Shipping costs
are the responsibilityof the Integrator, Contractor or the End User.
The warranty will not apply to the following circumstances that are beyond our control. Misuse, vandalism,
accident, neglect, unauthorized repairs or modifications, acts of God (lightning, floods, insect damage, etc...),
power surges, incorrect installation, or application.
The warranty set forth above is entirely exclusive and no other warranty whether written or oral, is expressed
or implied. RSSI Barriers, LLC specifically disclaims any and all implied warranties, merchantability or
fitness for a particular purpose. It is the purchaser’s sole and exclusive responsibility to determine whether or
not the equipment will be suitable for a particular purpose. In no event shall RSSI Barriers, LLC be held liable
for direct, indirect, incidental, special, consequential damages or loss of profits whether based on contract, tort,
or any other legal theory during the course of the warranty or at any time thereafter. The end user agrees to
assume all responsibility for all liability involving the use of this product, releasing RSSI Barriers, LLC of all
liability.
All RSSI barriers require minimal maintenance; however, there are some tasks that need to be performed after
the barrier is installed to insure compliance with the warranty provided. When the RSSI barrier is installed
and not accepted by the end user until a later date, the maintenance tasks located in the Quarterly Preventative
Maintenance Checklist (provided with the Operator Manual for each job) must be accomplished until
acceptance by the end user. Likewise, after acceptance the end user is required to conduct these quarterly
preventive maintenance tasks to ensure the warrantyis valid.
IN ORDER TO USE THE VEHICLE BARRIER, YOU MUST UNDERSTAND AND BE IN FULL
UNCONDITIONAL AGREEMENT WITH ALL STIPULATIONS OUTLINED ABOVE. IF YOU ARE
NOT IN FULL AGREEMENT, DO NOT PUT UNIT INTO OPERATION. PLACING THE VEHICLE
BARRIER INTO OPERATION WILL BE CONFIRMATION THAT YOU ARE IN FULL
UNCONDITIONAL AGREEMENT WITH ALL OF THE ABOVE.

02/05/2018 INSTALLATIONGUIDELINES
PAGE 5
2INSTALLATION
2.1 Introduction
This section provides basic information on the installation of the RSS-4000 Electric Bollard System and is
designed to assist system integrators and subcontractors.
2.2 Safety
Highlights an essential installation or maintenance procedure, practice, condition, statement, etc. which if not
strictly observed, could result in injury to, or death of, personnel or long term health hazards.
Highlights an essential installation or maintenance procedure or statement, which, if not strictly observed,
could result in damage to the system, equipment or injury.
Highlightsan essential installation or maintenance procedure, condition, orstatement.
2.2.1 SafetyPrecautions
The following minimum safety precautions should be observed while performing procedures in this
document. Refer to locallyprescribed safety requirements of the end user and/or the State you are in.
•Dangerous voltages are present at system connections. Ensure power is OFF prior to connecting or
disconnecting cables.
•Do not wear metal frame glasses, rings, watches, or other metal jewelry while working on electronic
equipment during the installation process.
2.3 Mobilization
•The RSS-4000 Series Electric Bollard Vehicle Barrier consists of a steel vault and Insert Assembly
that is hot dip galvanized with an anti-skid top surface with 1 foot x 1 foot removable bollard inserts.
Figure2-1,RSS-4000

02/05/2018 INSTALLATIONGUIDELINES
PAGE 6
•The Bollard Assembly Height is 36 inches at deployment. All barriers are shipped fully
operational, self-contained for easy installation. The weight of the barrier depends upon the unit
purchased. (See Table 2-1)
Description
Dimensions(W x L x H)
Weight
RSS-4002 - 2 Post
36.5” x 84”x 61.5”
6,720 lbs
RSS-4003 - 3 Post
36.5”x 126” x 61.5”
8,260 lbs
Table2-1–RSS-4000SeriesDimensionChart
•Before you begin, you will need the following available on site prior to installation:
•Equipment for excavation, soil compaction, removal and disposal of spoils
•Street Saw or other like equipment for demolition.
•Concrete placing and finishing tools
•3000 PSI (minimum) Mix Concrete (see Figure 2-6)
•Equipment capable of lifting and setting the RSS-4000 in place
•Email us at Service@rssi.com for the most up-to-date drawings and specifications.
Figure2-2,RSS-4000
2.4 InstallationInstructions. InstallingtheRSS-4000isasimple5-stepprocess.
2.4.1 StepOne-Excavate
•The first step is to excavate the existing roadway to a dimension of the appropriate barrier size. (See
Table 2-2)

02/05/2018 INSTALLATIONGUIDELINES
PAGE 7
Figure2-3,Excavation
Barrier Size
Excavate Area
(W x L x H)
Rebar Type #5
Concrete
(3000 PSI min.)
RSS-4002-2 Post
84” x 108” x 62”
Not Required,
fabricated into
barrier
Approx 8.5 yards
RSS-4003-3 Post
84” x 150”x 62”
Not Required,
fabricated into
barrier
Approx. 9 yards
Table2-2,ExcavationDetails
Ensure barrier placement according to the approved site plan to ensure road crown, underground utilities,
associated passive knee walls or static bollards are taken into account.
2.4.2 StepTwo–PlaceBarrier
Once the soil is compacted (to local standard), place the RSS-4000 Vault with Insert Assembly into the pit
leaving a 1 foot area for concrete on each end and 2 foot area to the front and rear. The barrier is typically
installed ½ inch above grade to allow water to flow around the barrier. Local conditions may dictate
installing the barrier flush to the existing roadway.
Figure2-4,BarrierPlacement
2.4.3 StepThree–ConduitConnections
•RSS-4000 barriers are self-contained shipped from the factory ready to install. Connect the
appropriate PVC conduit to the power (1”), control (1”) and sump pump (1½”) PVC sleeves in the
metal stub outs located on the front and side of the barrier. If the job site requires rigid conduits, the
PVC sleeve in the stub outs will have to be replaced.

02/05/2018 INSTALLATIONGUIDELINES
PAGE 8
Figure2-5, ConduitConnections
RSSI requires at least one of the 5” gravity drains be installed (4” PVC) to each barrier. Additionally, the
Sump Pump discharge (1” PVC) should be “SEPARATE”fromthe Gravity Drain.
2.4.4 StepFour–Concrete
ENSURE ALL OPENINGS (SMALL HOLES ARE CUT IN BARRIER VAULT TO
ACCOMMODATE THE HOT DIP GALVANIZE PROCESS)ARE COVERED BEFORE
CONCRETE IS POURED. FAILURE TO DO SO WILL RESULT IN EQUIPMENT
MALFUNCTION.
•Pour the concrete (3,000psi minimum) around the RSS-4000 unit. Be careful not to damage the
electrical or drainage conduit. Vibrating to remove air pockets and a light broom finish is
recommended. (See Figure 2-6 below) Allow sufficient time for concrete to harden before driving
over barrier.
Conduit Stub Outs:
- Controls (1“ Conduit)
- Power (1“ Conduit)
Gravity Drain –one on each side
- 5” hole for 4”Conduit
- Mandatory to hook-up at least
one
Pump Stub Out:
- Sump Pump (1-1/2“ PVC)

02/05/2018 INSTALLATIONGUIDELINES
PAGE 9
Figure2-6,Concrete

02/05/2018 INSTALLATIONGUIDELINES
PAGE 10
When barriers are aligned beside each other and a monolithic pour is used for two or more barriers, vibrate
the concrete into the excavation to ensure adequate displacement of concrete. Place barriers in accordance
with Installation Drawings.
2.4.5 StepFive–ConduitandTerminationofControls
•Some locations will have existing conduit, others you will have to trench and install/run new conduit.
Based on the layout and distance from the barriers to the BarrierControl Panel (BCP), a handhold or J-
Box may be installed. After conduit has been installed, move onto the controls. Barrier Control Panels
arrive complete from the factory. All control and power wiring(providedbyIntegrator/Contractor) from
the barrier, BCP and operator controls are labeled to coordinate with a termination strip in the control
box. Operator Controls are custom made to adapt to each location. Typically, Panels are placed on an
equipment pad within 50-100 feet from the barriers. (See Figure 2-7).
Figure2-7,EPUControlPanel &BatteryBack-up
Electrical Power Wiring should be sized by a Master Electrician or EE per N.E.C. Code based on distance
from EPU/BBS to barriers. Ground Rod should be installed adjacent to the Control Panel per N.E.C. code.
RSSI requires the use of Shielded Ethernet Cable to terminate between the barriers and the EPU.
Additionally, RSSI requires the use of specific waterproof connectors for terminating connections in the
barrier junction boxes (See Attachment 3 for cut sheets). Contact RSSI before terminating with any other
connectors.

02/05/2018 INSTALLATIONGUIDELINES
PAGE 11
Electrical Terminations
1. Local commercial power (120/240VAC) 1P 3 wire 30A is wired to Battery Backup Panel (BBP) at
MAIN CB-1 (L1 –L2, Neutral - Ground).
2. BBP transferspower to Barrier Control Panel (BCP) MAIN Disconnect Switch.
3. The Servo Box is inside the barrier powered through the BCP fuses FU1 and terminals 4L1 –4L2 –
Ground and wired through the Barrier Power J-box (splices).
4. The Barrier Heat Grid is powered through the BCP terminals 1H1 and 1H2 and wired through the
Barrier Power J-box (splices).
5. The 120V Sump Pump is powered from the BCP terminals SP1&2 and Neutral wired through the
Barrier Power J-box (splices).
6. The 24Vdc Traffic Lights are powered from the BCP PLC outputs and fused at 2amps.
7. The 24Vdc Barrier Warning LED Lights are powered from the BCP PLC fused outputs and wired
through the Control J-Box splices.
8. The IR Beams(if applicable) are powered through the BCP +24Vdc (Red wire)/-24Vdc (Black wire)
power terminal blocks to each IR Beam (splices in stands) Connect the Red wire to Brown and Gray wires
of IR pigtail and Black wire to Blue wire of IR pigtail.
9. The Barrier Heat Thermostat (mounted outside) is connected at BCP terminals +24Vdc and PLC input
(splices at thermostat); if applicable.
10. The PrimaryOperator Control panel is powered through the BCP +24Vdc and -24Vdc output terminal
blocks to.
Control Terminations
1. The Servo Box inside the barrier communicates with the BCP via shielded twisted pair Ethernet cable
(Cat5e) from a Ethernet switch to servo box (Tech will be required to terminate and label RJ45 connector
on cable end at Ethernet switch in the BCP) Servo Box is pre-terminated at factory.
2. BCP receives vehicle presence indications from the LOOPS in the roadway to the front of the LOOP
DETECTORS in the BCP. (Bottom DIP switch must be set to right position at this point).
3. BCP receives INPUTS from IR Sensor(if applicable) (black wire on sensor pigtails) the black wire is
connected to blue wire connected on PLC input.
4. BCP controller receives a contact closure from the thermostat (mounted outside) to the BCP PLC
inputs. This activates the barrier heat grid Contactors H1 & H2.
5. BCP receives INPUT from Battery Backup Panel (BBP) when commercial poweris lost and/or when a
Low Voltage condition is present. BBP terminations are marked (+24VDC) I:1/0 and I:1/1. The BCP
terminations are mark (+24VDC), (I:1/0) for Loss of Power and(I:1/1) for Low Voltage condition.

02/05/2018 INSTALLATIONGUIDELINES
PAGE 12
ENSURE A QUALIFIED; LICENSED ELECTRICIAN TERMINATES THE
ELECTRICAL CONNECTIONS ACCORDING TO NATIONAL ELECTRIC CODE AND
ANY APPLICABLE STATE AND LOCAL CODES.
2.4.5.1InstallationofShieldedEthernetCablefromBarrierto BarrierControlPanel(BCP)
•Shielded Ethernet cable is provided byRSSI and rolled up inside unit. The cable is terminated
inside at Servo Drive using the TIA/EIA568A wiring on the RJ45. This wire will need to be
ran through Control J-Box and Controls conduit back to the BCP.
Figure2-8,ControlsConduit,EthernetRunIntoJ-box.
•Inside the EPUpanel, terminate Ethernet Cable with RJ-45 connector. Use the TIA/EIA
568A Wiring diagram.
Figure2-9,EthernetConnectionatEPU,EthernetWiringDiagram

02/05/2018 INSTALLATIONGUIDELINES
PAGE 13
•Once termination has been made, plug the cable into the Ethernet Switch.
Figure2-10,EPUEthernetSwitch
•Connect Ethernet shield wire to (Earth Ground) on top of switch at pin #4. If metal RJ45is
used, no grounding is required.
Figure2-11, EthernetConnectionandGround

02/05/2018 INSTALLATIONGUIDELINES
PAGE 14
This box should ONLY be opened at the RSSI factory. It is considered a “LRU” Line
Replacement Unit. Opening this box VOIDS THE WARRANTY.
Figure2-12,ServoDriveBoxInsideBarrier
The Ethernet cable is designed to be a straight run with no splices, severe bendsor stretching. Splicing this
cable will lead to premature failure of the network communication to the Servo Drive.
It is highly recommended to use experienced technicianstrained to install shielded twisted pair terminations.
After installing, test with a regular network cable tester.
2.4.5.2Installation,Termination,andTestingofFiberCable
●If applicable, Fiber converters are located in the BCP and in location of Control Console.
●Fiber must be run in locations where the distance from the BCP to the Fiber Convertor Panel is
more than 300 feet.
●A technician terminates the fiber and conducts a BASIC go/no go indication test. At this point the
fiber terminations could be connected up and possibly even work, however without further testing
with an OTDR, Ethernet errors could occur. Power meters are also used by fiber technicians to

02/05/2018 INSTALLATIONGUIDELINES
PAGE 15
measure Power/Loss through the run and certify the fiber installation. It is highly recommended
that this certification be done after termination.
●Connecting the fiber terminations (ST) to the fiber convertors
1. Line up pegs with slots, push in and turn clockwise to lock
2. There is a (TX) transmit and (RX) receive (marked on convertor)
3. Take each pair of fiber cables (already terminated and tested) and connect to TX and RX
4. Connect other end of fiber optic cable and termination to RX and TX (opposite)
5. You should get LINK light indication on fiber convertor, if not, reverse connectors
●Cleaning the fiber terminations before, during and after the termination procedures is a key to
success.
NOTE
It is highly recommended to use experienced technicians trained to install,
terminate, test, and certify fiber. After installing, at a minimum test
connection with an OTDR tester.
CAUTION
The Fiber cable is designed to be a straight run with no splices
or severe bends or stretching.

02/05/2018 INSTALLATIONGUIDELINES
PAGE 16
2.4.6 JobDocumentation.
•Drawings. RSSI provides submittal drawings upon request. Typical drawing packages are available
by emailing us at Sales@rssi.com. Typical drawings show civil/installation layouts for barriers,
tentative conduit layouts, Wire and Conduit Legend, and a Foundation drawing for the Control Panel
Enclosures. As-Built drawings showing PLC I/O and interconnect wiring diagrams are printed and
ship inside the BCP.
A CDcontaining Equipment Manuals, Bill of Materials, Operator’s Manual and AS-Built Drawings (effective
ship date) is also mailed to the Project Manager.
•Operator Manual. Each project includesoperator manualsthat ship insidethe BCP.
•Bill of Materials (BOM). Each job includes a BOM that ship inside the BCP. It contains a detailed list of
systemcomponents,part numbers,and manufacturer.
3COMMISSIONING
Ensure a “CERTIFIED” installer or a RSSI Technician performs the Commissioning
procedures. NOT DOING SO WILL VOID THE WARRANTY.
3.1 START-UP.
Upon completion of all terminations between the barriers, barrier related equipment, control panel, and
operator controls, PRIOR to applying any power, the wiring should be checked out to ensure proper
connection of terminated wires. It is imperative installers refer to and follow the as built drawings provided
inside each control panel and Section A of the Start-Up/Turn-Over Procedures in Attachment 1.
3.2 TEST.
After the start-up procedures in Section A have been completed, it’s time to run the remainder of the Sections
of the Start-Up/Turn-Over Procedures Checklist in Attachment 1.
In closing, we want to reiterate that these guidelines are not intended to be all inclusive and are “Typical”.
Local requirements and site conditions mayrequire modifications. Integrators/Contractors should refer to the
Architectural Firm that designed the project or a licensed Civil Engineer familiar with the local site conditions
and requirements for clarifications. If you have any issues or questions, Integrators/Contractors are highly
encouraged to contact RSSI (850) 871-9300 or Toll Free at (866) 249-1029 for clarifications.

02/05/2018 INSTALLATIONGUIDELINES
PAGE 17
6 Attachments
1. Commissioning Checklist
2. Safety Loop Set-Up
3. Servo Drive Set-up
4. Vehicle Detector Loop Installation
5. Traffic Light Installation
6. Waterproof Connectors
* * END OF SECTION * *
RSSI Barriers LLC
6530 E Highway 22
Panama City, FL 32404
(850) 871-9300
www.rssi.com

02/05/2018 INSTALLATIONGUIDELINES
PAGE 18
Attachment 1, Start-Up/Turn-Over Procedures
Start-Up/Turn-Over Test Procedures - RSS-4000 Barrier System At
_____________________________________________________________:
A. Visual Check Battery Backup System(BBS):
1. Verify that all field wiringand cables are connected asper “As Built”
Drawings (From Battery back-up to BCP).
2. Insure that all terminal screws and cablesare tight.
3. Insure there are no loose or naked wires.
4. Insure that all circuit breakers are turned OFF, Inverter switch and CB on top is OFF.
B. Voltage Test: Normal Power
1. Verify battery charger DIP switches are set correctly (S1=off, S2=on)
2. Connect 2 each 12v batteries in series to the inverter, also connect charger wires (series)
. Then check for 24vdc at the inverter, all battery cable connections must be tight and clean.
3. Connect main power source to CB1.Then turn on mainpower source to verify correct
incoming voltage (240vac or 208VAC) at CB1.
4. Turn ON CB1 and observe contactor C1 energized, check for correct voltage at terminal
blocks 3L1 and neutral (240vac). This is where the power leaves the BBS and powers
barrier control panel.
5. Turn on CB2
6. Turn on CB3, battery charger power light should come on and should show some current
draw on meter. Check batteries for 26-28vdc to verify charger is working.
7. Turn on inverter CB’s and power switch, power light should turn green when stabilized.
Check for correct voltage at the bottomof CB2 (240vac). The system is now operational.
D. Control Panel Check: (Normal Power)
1. In the Control Panel, turn all circuit breakers off.
2. Open Servo-Drive Fuse Holders F1 & F2.
3. Turn on Main Disconnect and check for correct voltages.
4. Turn on CB3 and CB1 (turns on 24v power supply).
5. Turn-on CB 5- supplies 24vdc operating power to PLC, Touch Screen, Ethernet Switch,
and Loop Detectors. All these devices will boot up and stabilize in a few minutes.
6. Push in FU1- energizes the servo drive inside the barrier.
7. Turn on CB4-Supplies operating power to the sump pump in the barrier. Check
for correct voltage.
E. Battery Backup System Operational Check:
1. Turn off CB1 in BBS panel and observe contactor C1 de-energize and C2 energize.
2. Check voltage at terminal blocks 3L1 and 3L2 (240vac)

02/05/2018 INSTALLATIONGUIDELINES
PAGE 19
3. Turn CB1 back on and after approx. 4 seconds, the contactor C2 should de-energize
and C1 should energize.
4. Check voltage at terminal blocks 3L1 and 3L2 (240vac or 208vac).
5. Check inverter power light, it should be green.
6. If batteries go below 20vdc, the inverter will go into stand-by mode and power light
will be red. In this case, cycle the inverter power switch when main power comes back
on, check for condition of batteries, battery cables and signs of corrosion. Check battery
charger for charging voltage and amps and allow batteries to re-charge.
F. Testing Ethernet Connectivity(if necessary)
1. Using a laptop, connect your Ethernet cable to an empty port on the Ethernet switch
(located in EPU panel).
2. Set your static TCP/IP address to 192.168.1.200 with subnet mask 255.255.255.0
(no gateway is needed for this test).
3. a. Go to DOS PROMPT and type PING 192.168.1.10 you should get replies from the PLC.
b. Go to DOS PROMPT and type PING 192.168.1.11 you should get replies from the Drive.
c. Go to DOS PROMPT and type PING 192.168.1.12 you should get replies from the HMI.
4. IF you do not get replies from the devices, ensure your laptop is on the correct subnet
again and troubleshoot connectivity problems to any device. Test Ethernet cabling end
to end with an Ethernet Cable Tester.
G. Tuning the Barrier
1. On the touch screen, go to the main screen and check for any alarms and reset or clear.
2. On the touch screen, go to the LOGIN box and login: maint password: 12345.
3. On the touch screen, select the JOG/TEACH box and push the JOG UP button
until the barrier rises up one foot.
4. On the touch screen, return to the main screen and select the HOME box and
then select the HOME button (will flash while homing, the barrier will slowly
creep down until homed) the barrier is now homed. Return to main screen.
5. On the touch screen, select the BARRIER CONTROL box and run the barrier to
the UP position using the JOG UP button. Measure the bollard assembly in the up
position to ensure it reaches 35-36 inches. Go into TEACH menu and press TEACH UP
position. Using JOG DOWN button run barrier to DOWN position and ensure down position
is all the way down into roadway. Enter the TEACH Menu and press
TEACH DOWN POSITION.
6. If equipped with manual push button operators station, test all the up and down
commands and check for proper position lights.
7. Check all traffic signal lights making sure the sequences are correct, check barrier
warning lights.
8. If equipped with heat package, set the barrier’s heat thermostat to engage
H1 heat contactor (it will pull in), then check for correct voltage at 1H1 and 1H2 (208 or 240VAC).
H. Safety Loop Check:

02/05/2018 INSTALLATIONGUIDELINES
PAGE 20
1. Position a person at the RSSIControl Panel/Box and drive a vehicle
slowly over the safety loops and the barriers. The RED LED (detects presence)
will light as the vehicle travels over the safety loops and will turn off as the
vehicle clears them.
2. With the Barrier in the DOWN position, pull a vehicle forward on the front
edge of the front safety loop and stop. The LED indicator on the safetyloop
detector in the RSSI Control Panel/box shouldindicate RED (detects presence).
3. Touch the Barrier UP Icon on the “Touch screen”. Barrier should not operate.
4. Back the vehicle off the safetyloop. Touch the Barrier UP Icon and as the
barrier starts to raise pull the vehicle onto the front edge of the safetyloop.
The barrier should stop and lowerto the down position.
WARNING-Ensuretouse extreme caution when pulling the vehicle forward asthe barrier isrising. Recommend placing
wheel chocks to prevent vehicle fromtraveling onto the barrier.
5. With the Barrier in the DOWN position, pull a vehicle forward to the rear
edge of the back safety loop and stop. The LED indicator on the safety loop
detector in the RSSI Control Panel/Box should indicate RED (detects presence).
6. Press the Barrier UP Icon, Barrier should not operate.
7. Pull the vehicle off the safety loop. Touch the Barrier UP Icon and as the barrier
starts to raise Back up the vehicle onto the back edge of the safety loop. The barrier
should stop and lower to the down position.
WARNING-Ensure to use caution when backing the vehicle as the barrier is rising. Recommend placing wheel chocks
toprevent vehicle fromtraveling onto the barrier.
Repeat for additional barriers.
G. Verify Approved Sequence of Operation
1. Step by Step run through the approved sequence of operation for the appropriate gate
2. For additional technical support, please contact RSSI at (850) 871-9300 or
Toll Free at (866) 249-1209.
This manual suits for next models
2
Table of contents
Popular Control System manuals by other brands

Intelligent Motion Systems
Intelligent Motion Systems MicroLYNX-4 Quick manual
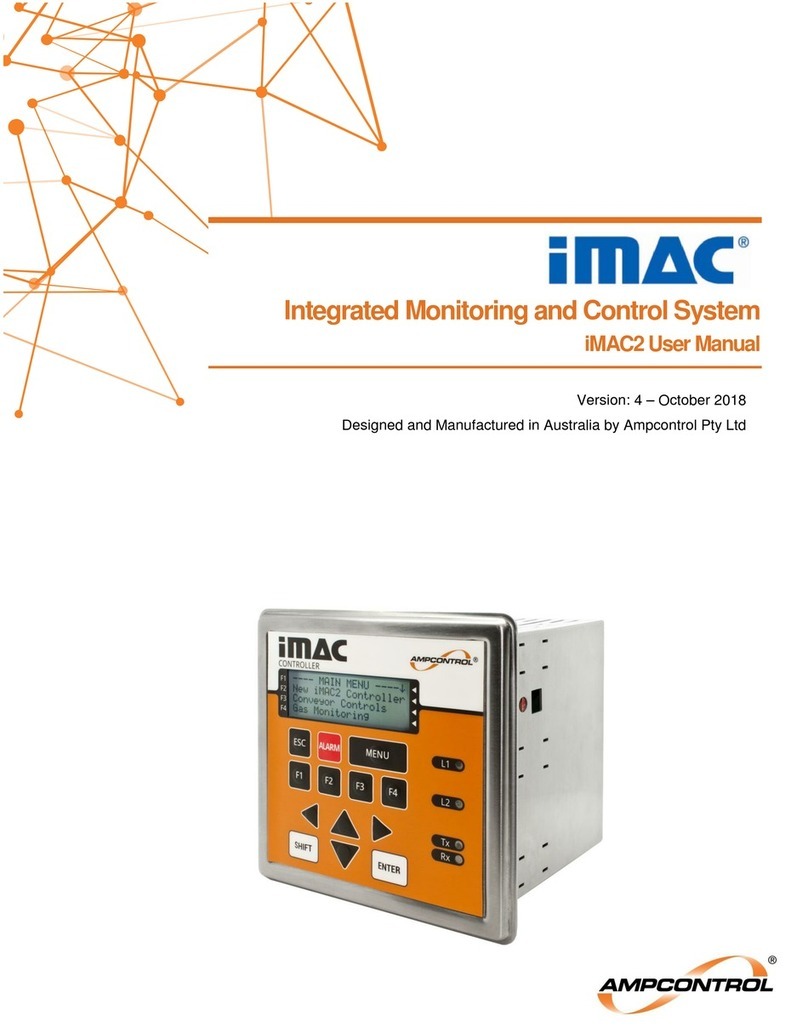
Ampcontrol
Ampcontrol iMAC2 user manual
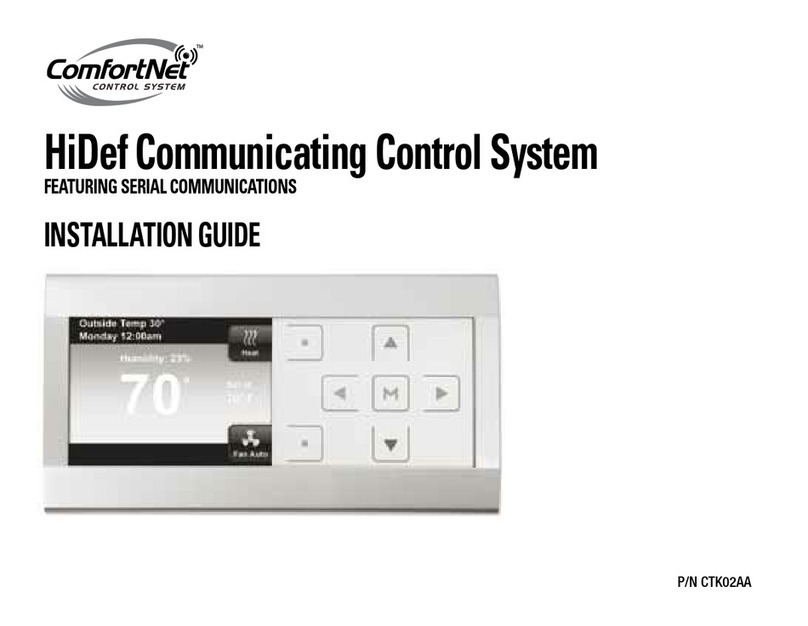
ComfortNET
ComfortNET CTK02AA installation guide
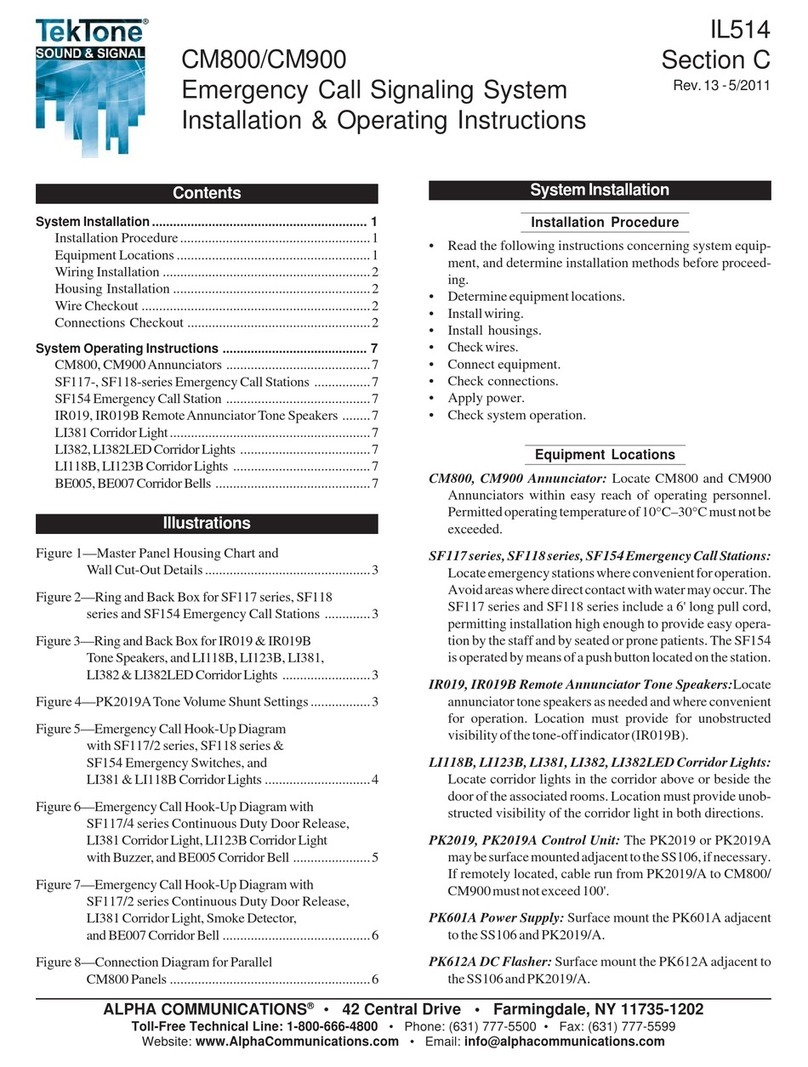
Alpha Communications
Alpha Communications TekTone CM800 Installation & operating instructions
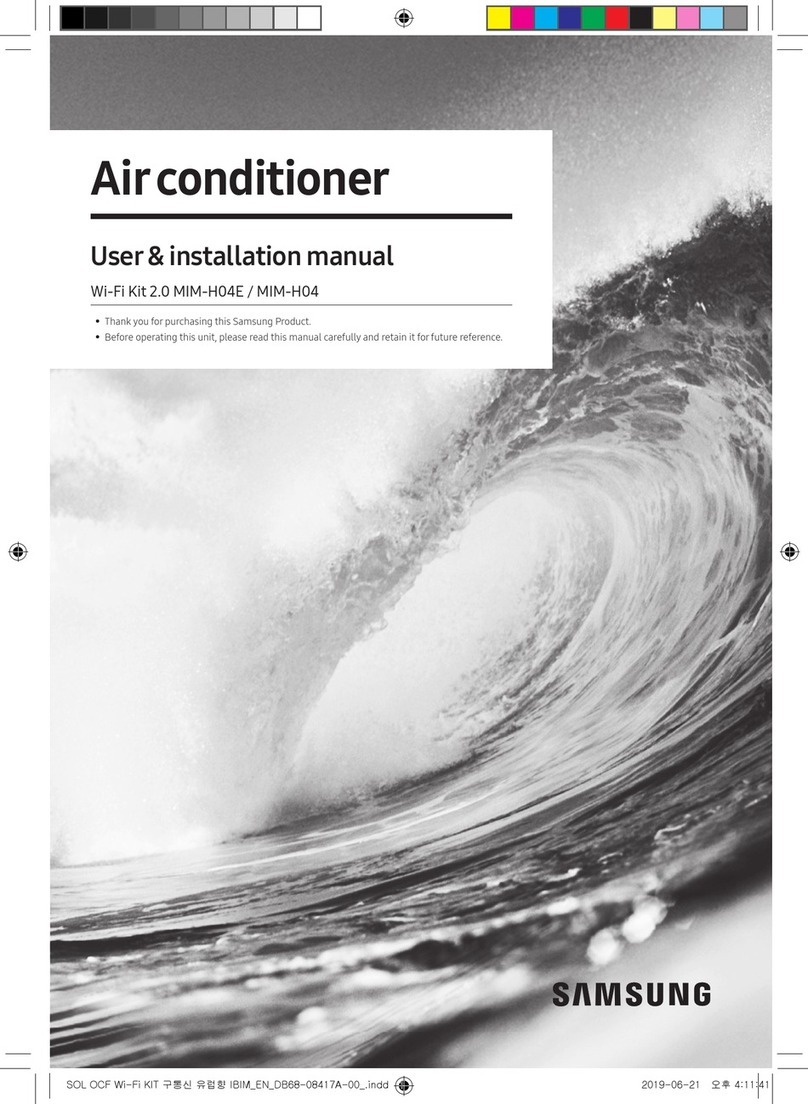
Samsung
Samsung Wi-Fi Kit 2.0 User & installation manual
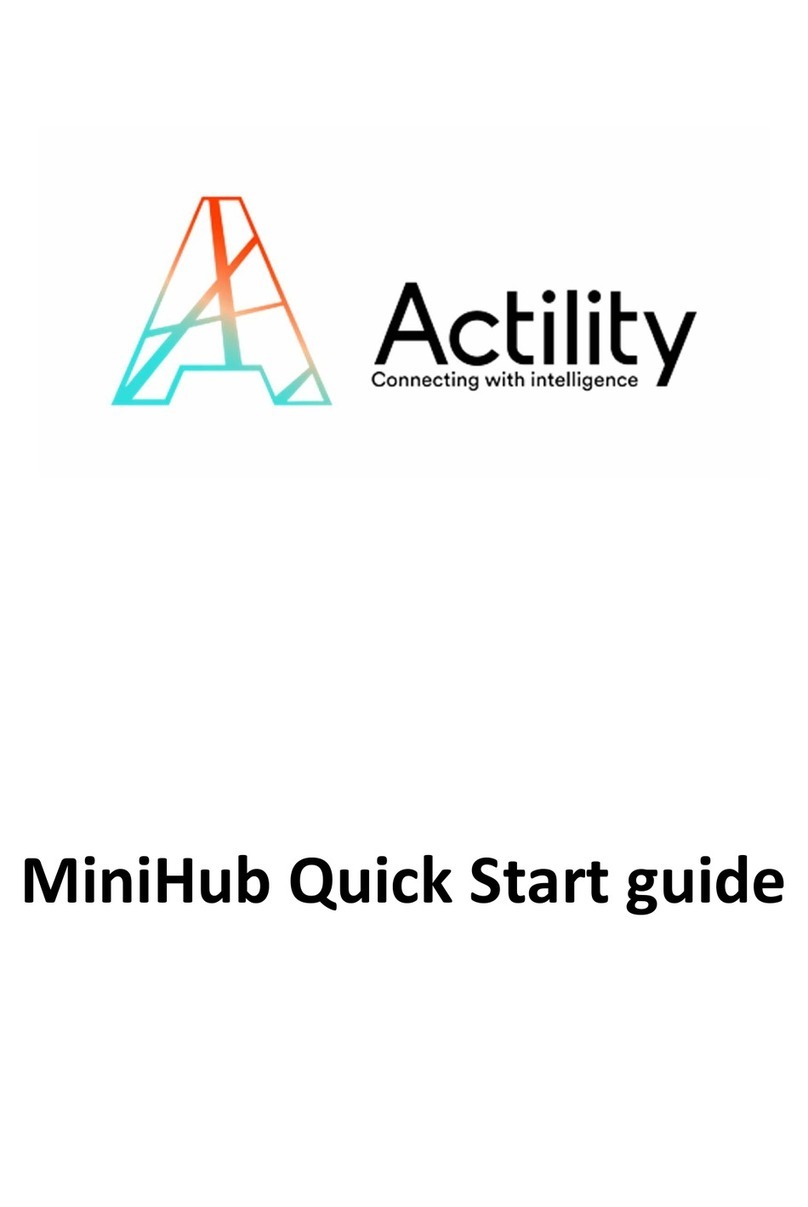
Actility
Actility MiniHub quick start guide
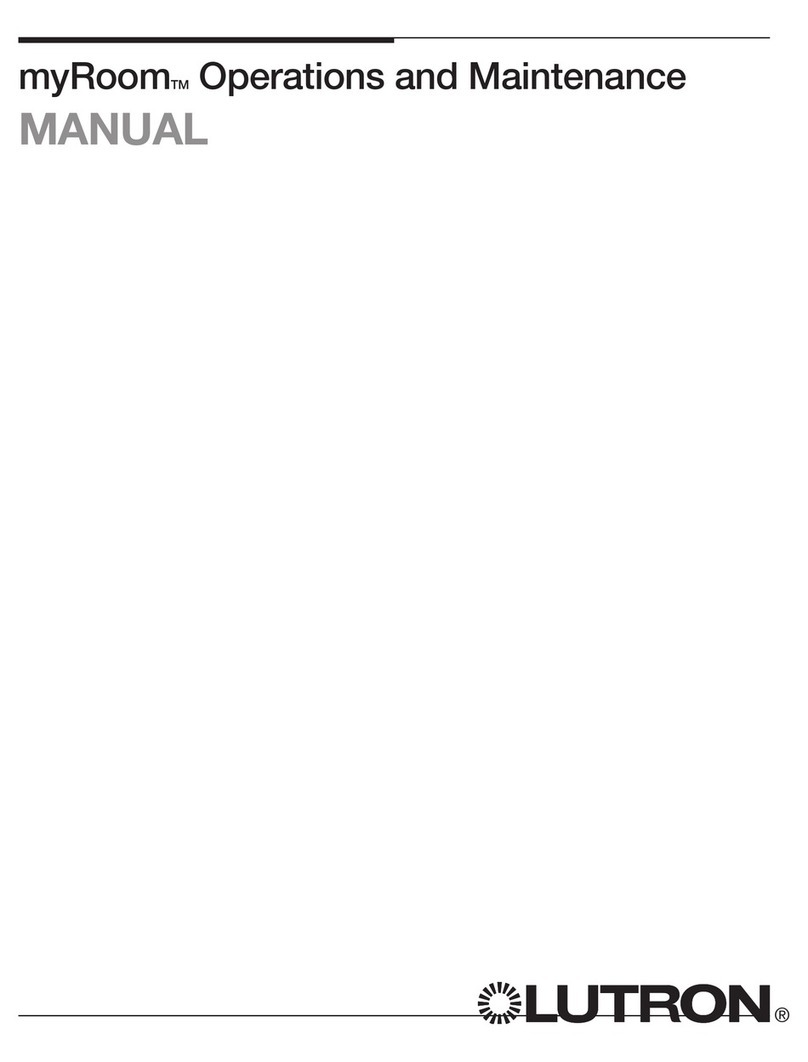
Lutron Electronics
Lutron Electronics myRoom Operation and maintenance manual
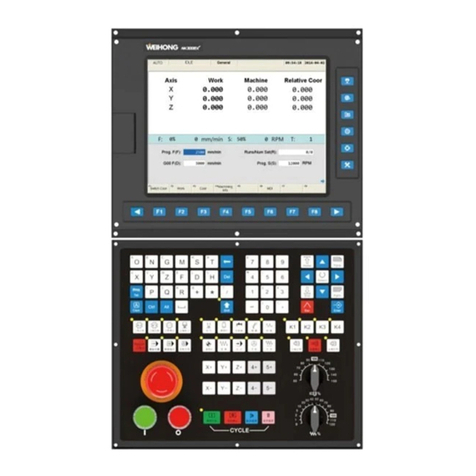
WEIHONG
WEIHONG NK300CX quick start guide
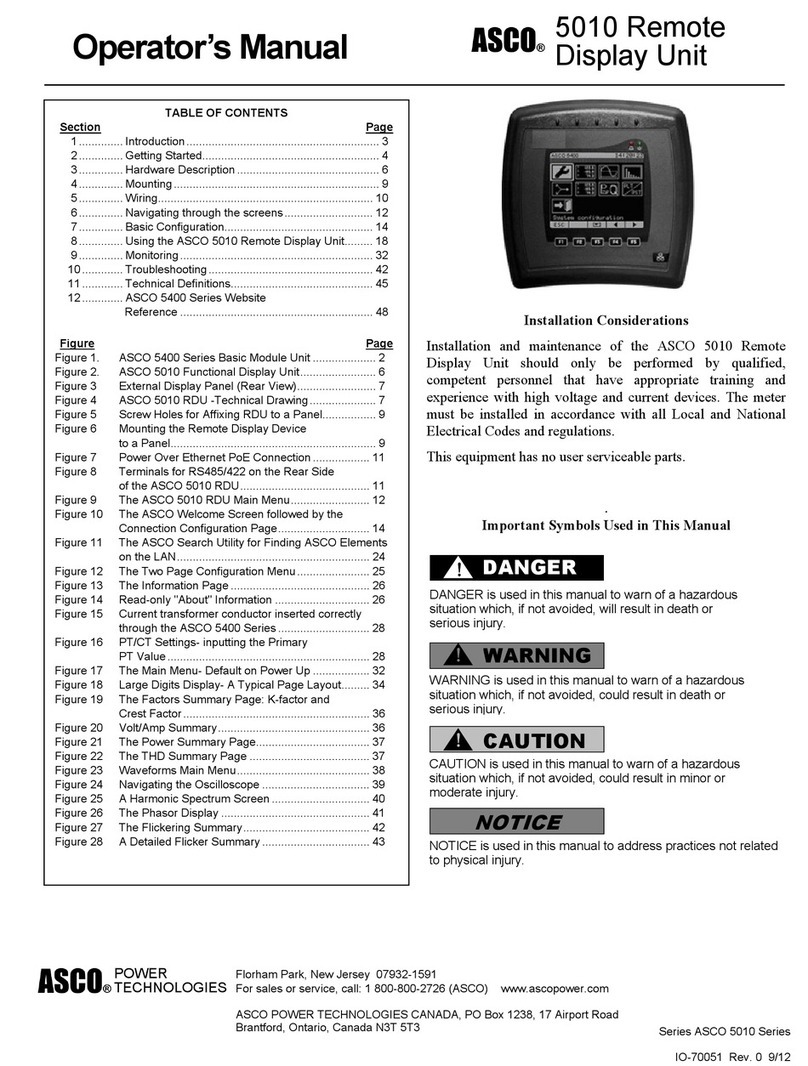
ASCO POWER TECHNOLOGIES
ASCO POWER TECHNOLOGIES 5010 Operator's manual

Minka Group
Minka Group minkaAire AireControl WC1000 instructions
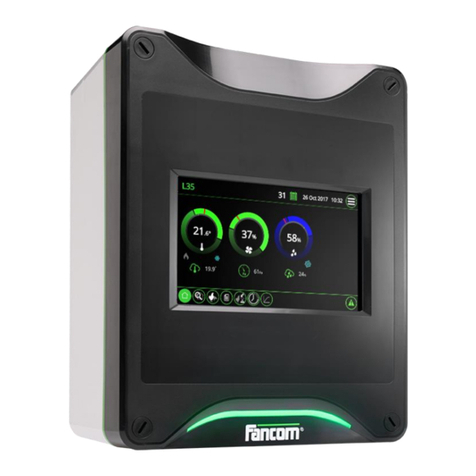
Fancom
Fancom Lumina 35 installation manual
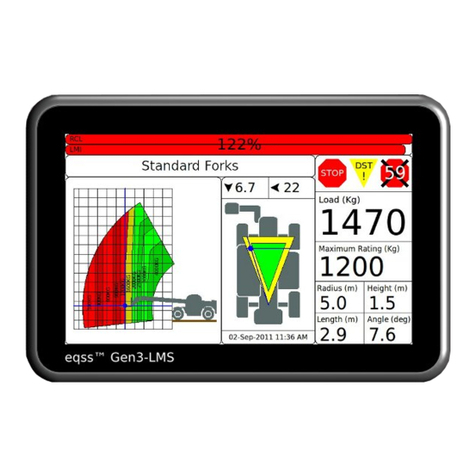
eqss
eqss Gen-3 LMS installation manual