Ampcontrol iMAC2 User manual

IntegratedMonitoringandControlSystem
iMAC2UserManual
Version: 4 –October 2018
Designed and Manufactured in Australia by Ampcontrol Pty Ltd

IMAC2B009 V2 Uncontrolled Copy - Refer to Ampcontrol Website for Latest Version Page 1 of 53
Ampcontrol Pty Ltd –ABN 28 000 915 542
iMAC System User Manual
iMAC2B009 V4 –10/18
APPROVED FOR EXTERNAL DISTRIBUTION –PROPERTY OF AMPCONTROL PTY LTD –NOT TO BE REPRODUCED IN PART
WARNING!
The warning symbol highlights a potential risk of injury or death.
Please share these warnings with other operators.
CAUTION!
The caution symbol highlights a potential risk of damage to
equipment.
Please share these cautions with other operators.
NOTE
The note symbol highlights key information.
Please share these notes with other operators.
ENVIRO
The enviro (environmental) symbol highlights areas which may have an
impact on the surrounding fauna and/or flora.

IMAC2B009 V2 Uncontrolled Copy - Refer to Ampcontrol Website for Latest Version Page 2 of 53
Ampcontrol Pty Ltd –ABN 28 000 915 542
iMAC System User Manual
iMAC2B009 V4 –10/18
APPROVED FOR EXTERNAL DISTRIBUTION –PROPERTY OF AMPCONTROL PTY LTD –NOT TO BE REPRODUCED IN PART
Copyright Notice
The Ampcontrol iMAC Integrated Monitoring and Control system described in this document is the property
of AMPCONTROL PTY LTD. It is furnished under a license agreement and is to be used only in
accordance with the terms of the agreement.
No part of the hardware or documentation may be reproduced, transmitted, transcribed, stored in a retrieval
system, or translated into any language or computer language, in any form or by any means, without prior
written permission of AMPCONTROL PTY LTD.
The iMAC signalling technique is protected by patent.
Disclaimer
While every effort has been made to assure the accuracy and clarity of this document, AMPCONTROL PTY
LTD assumes no liability resulting from any omissions in this document, or from misuse of the information
obtained herein. The information in this document has been carefully checked and is believed to be entirely
reliable with all of the necessary information included. AMPCONTROL PTY LTD reserves the right to make
changes to any products described herein to improve reliability, function, or design, and reserves the right to
revise this document and make changes from time to time in content hereof with no obligation to notify any
persons of revisions or changes. AMPCONTROL PTY LTD does not assume any liability arising out of the
application or any use of any product or circuit described herein; neither does it convey license under its
patent rights or the rights of others.
Before You Begin
Thank you for purchasing the Ampcontrol iMAC System.
WARNING!
In the interests of safety and correct equipment operation, please
take the time to read and understand the content in this manual.
Ampcontrol Contact Details
7 Billbrooke Close, Cameron Park, NSW, 2285
P +61 1300 267 373 | F +61 2 4903 4888
EMAIL: customerservice@ampcontrolgroup.com
WEB: ampcontrolgroup.com

IMAC2B009 V2 Uncontrolled Copy - Refer to Ampcontrol Website for Latest Version Page 3 of 53
Ampcontrol Pty Ltd –ABN 28 000 915 542
iMAC System User Manual
iMAC2B009 V4 –10/18
APPROVED FOR EXTERNAL DISTRIBUTION –PROPERTY OF AMPCONTROL PTY LTD –NOT TO BE REPRODUCED IN PART
TABLE OF CONTENTS
INTRODUCTION........................................................................................................7
Document Scope..............................................................................................7
Supplementary Documents ..............................................................................7
Definitions.........................................................................................................8
Fieldbus System Configurations.....................................................................10
SAFETY AND OTHER WARNINGS.........................................................................12
Safe Use of Equipment...................................................................................12
RECEIVING AND STORAGE...................................................................................13
Receiving........................................................................................................13
Inspection.......................................................................................................13
Storage after Delivery.....................................................................................13
Unpacking of Equipment.................................................................................13
iMAC SYSTEM OVERVIEW.....................................................................................14
Typical Installation..........................................................................................15
Application Software.......................................................................................16
iMAC Modules................................................................................................16
iMAC Address Range.....................................................................................17
Fault Finding Statistics....................................................................................17
Networking .....................................................................................................18
Local and Global Data....................................................................................19
Sequence Control...........................................................................................19
Emergency Stop SIL Qualification ..................................................................21
IECEx Certifications......................................................................................21
FIELDBUS SIGNALLING PROTOCOL.....................................................................23
iMAC2 SUPERVISORY CONTROLLER...................................................................24
Power Supply.................................................................................................25
Digital Inputs...................................................................................................25
Relay Outputs.................................................................................................26
Serial Communications Port ...........................................................................26
Ethernet Communications Port.......................................................................27
Fieldbus Ports ................................................................................................27
Memory..........................................................................................................27

IMAC2B009 V2 Uncontrolled Copy - Refer to Ampcontrol Website for Latest Version Page 4 of 53
Ampcontrol Pty Ltd –ABN 28 000 915 542
iMAC System User Manual
iMAC2B009 V4 –10/18
APPROVED FOR EXTERNAL DISTRIBUTION –PROPERTY OF AMPCONTROL PTY LTD –NOT TO BE REPRODUCED IN PART
Intrinsically Safe Battery.................................................................................27
Data Point Table.............................................................................................28
iMAC FIELDBUS MODULES....................................................................................29
Intrinsically Safe Barriers................................................................................29
Intrinsically Safe Remote Keypad...................................................................31
Digital Input Modules......................................................................................31
Analogue Input Modules.................................................................................31
Output Modules..............................................................................................32
Serial Interface Modules.................................................................................33
Specialty Modules ..........................................................................................34
Protection Modules.........................................................................................34
End-of-Line Modules ......................................................................................34
INSTALLATION........................................................................................................35
General Warnings...........................................................................................35
Mandatory Installation Practices.....................................................................36
Mechanical Arrangement................................................................................37
Electrical Connections....................................................................................37
COMMISSIONING AND CALIBRATION ..................................................................38
iMAC2 CONTROLLER OPERATION SUMMARY ..................................................39
iMAC2 Controller User Interface...................................................................40
System Menu ...............................................................................................41
iMAC2 Controller LEDs.................................................................................44
Selectors & DIP Switches.............................................................................44
SERVICE, MAINTENANCE & DISPOSAL..............................................................45
Equipment Service .......................................................................................45
Equipment Maintenance...............................................................................46
Disposal........................................................................................................46
iMAC2 CONTROLLER SPECIFICATIONS.............................................................47
EQUIPMENT LIST .................................................................................................49
iMAC2 Controllers & Accessories.................................................................49
Intrinsically Safe Barriers..............................................................................49
Intrinsically Safe Remote Keypads ...............................................................49
Digital Input Modules....................................................................................50
Analogue Input Modules...............................................................................50

IMAC2B009 V2 Uncontrolled Copy - Refer to Ampcontrol Website for Latest Version Page 5 of 53
Ampcontrol Pty Ltd –ABN 28 000 915 542
iMAC System User Manual
iMAC2B009 V4 –10/18
APPROVED FOR EXTERNAL DISTRIBUTION –PROPERTY OF AMPCONTROL PTY LTD –NOT TO BE REPRODUCED IN PART
Output Modules............................................................................................51
Serial Interface Modules...............................................................................52
Specialty Modules ........................................................................................52
Protection Modules.......................................................................................52
EOL and MEOL Modules............................................................................53

IMAC2B009 V2 Uncontrolled Copy - Refer to Ampcontrol Website for Latest Version Page 6 of 53
Ampcontrol Pty Ltd –ABN 28 000 915 542
iMAC System User Manual
iMAC2B009 V4 –10/18
APPROVED FOR EXTERNAL DISTRIBUTION –PROPERTY OF AMPCONTROL PTY LTD –NOT TO BE REPRODUCED IN PART
TABLE OF FIGURES
Figure 1.1: 2-Wire iMAC Fieldbus System Configuration 10
Figure 1.2: 3-Wire iMAC Fieldbus System Configuration 11
Figure 1.3: MLB Intrinsic Safety Barrier (Provides both 2-Wire and 3-Wire Terminal Connections) 11
Figure 4.1: Block Diagram of a Simple iMAC 2-Wire System 15
Figure 4.2: Tree Network of iMAC2 Controllers 18
Figure 4.3: Example of the use of Upstream Sequence Bits for Conveyor Sequence Control 20
Figure 4.4: Example of the use of Downstream Sequence Bits for Conveyor Sequence Control 20
Figure 4.5: An Implementation of Emergency Stops on a 2-Wire iMAC Fieldbus 21
Figure 5.1: Bipolar Pulse Width Modulated iMAC Fieldbus Signal 23
Figure 6.1: iMAC2 Controller (Front) 24
Figure 6.2: iMAC2 Controller (Right Side) 24
Figure 6.3: iMAC2 Controller (Rear) 24
Figure 6.4: iMAC2 Controller Terminal Layout 25
Figure 6.5: General Purpose Input Internal Circuitry 25
Figure 6.6: iMAC2 Controller’s Data Point Table 28
Figure 7.1: Utilisation of MLB and SLB Barriers in an Intrinsically Safe System 30
Figure 8.1: iMAC2 Controller Enclosure Dimensions 37
Figure 10.1: iMAC2 Controller Operational Interface (Front) 39
Figure 10.2: iMAC2 Controller Operational Interface (Right Side) 39
Figure 10.3: iMAC2 Controller Operational Interface (Left Side) 40
Figure 10.4: iMAC System Menu –Home Page 41
Figure 10.5: iMAC System Menu (Maintenance Page) 42
Figure 10.6: iMAC System Menu (Serial Communications Page) 43
Figure 10.7: iMAC System Menu (Version Page) 43

IMAC2B009 V2 Uncontrolled Copy - Refer to Ampcontrol Website for Latest Version Page 7 of 53
Ampcontrol Pty Ltd –ABN 28 000 915 542
iMAC System User Manual
iMAC2B009 V4 –10/18
APPROVED FOR EXTERNAL DISTRIBUTION –PROPERTY OF AMPCONTROL PTY LTD –NOT TO BE REPRODUCED IN PART
INTRODUCTION
Document Scope
This document is intended to provide an overview of the functionality of the iMAC System. It also serves as
a user manual for the general operation of the iMAC2 Controller.
This document is not intended to provide information on the operation of individual modules, instruction on
programming the iMAC2 Controller or modules, or how to access the Modbus communication registers.
Please refer to the relevant supplementary documents for this information.
Supplementary Documents
The iMAC2 System User Manual is intended to be read in conjunction with the following documents:
1.2.1 System Documentation
IMAC2B010 iMAC2 Controller Ethernet Communications Manual
IMAC2B011 iMAC2 Controller Web Interface Manual
IMAC2B015 iMAC2 Controller Ethernet-IP (CIP) Communications Manual
IMACB094 iMAC System Installation Requirements
IMACB153 iMAC Controller Serial Communications Manual
IMACB182 iMAC SIL Emergency Stop Qualification
IMACB005 iMAC Module Programming Manual
1.2.2 Module Documentation
IMACB003 iMAC RO4 Module Technical Datasheet
IMACB018 iMAC LPU Module Technical Datasheet
IMACB020 iMAC DI8 Module Technical Datasheet
IMACB045 iMAC IIM Module Technical Datasheet
IMACB046 iMAC DI4 Module Technical Datasheet
IMACB047 iMAC EOL/MEOL Module Technical Datasheet
IMACB060 iMAC LED4 Module Technical Datasheet
IMACB061 iMAC SSW Module Technical Datasheet
IMACB062 iMAC SQM Module Technical Datasheet
IMACB066 iMAC AIM Module Technical Datasheet
IMACB067 iMAC RTD1 Module Technical Datasheet
IMACB141 iMAC ARM Module Technical Datasheet
IMACB142 iMAC CRM Module Technical Datasheet
IMACB143 iMAC EMM Module Technical Datasheet
IMACB144 iMAC GRM Module Technical Datasheet
IMACB146 iMAC IRK Keypad Technical Datasheet
IMACB147 iMAC PIM Module Technical Datasheet
IMACB148 iMAC SIM-G Module Technical Datasheet
IMACB149 iMAC SIM-G2 Module Technical Datasheet
IMACB150 iMAC SIM-T Module Technical Datasheet
IMACB151 iMAC MLB Barrier Technical Datasheet
IMACB152 iMAC SLB Barrier Technical Datasheet
IMACB154 iMAC SIM-P Module Technical Datasheet
IMACB172 IMAC LIM Module Technical Datasheet

IMAC2B009 V2 Uncontrolled Copy - Refer to Ampcontrol Website for Latest Version Page 8 of 53
Ampcontrol Pty Ltd –ABN 28 000 915 542
iMAC System User Manual
iMAC2B009 V4 –10/18
APPROVED FOR EXTERNAL DISTRIBUTION –PROPERTY OF AMPCONTROL PTY LTD –NOT TO BE REPRODUCED IN PART
Definitions
1.3.1 System Definitions
Term
Definition
2-Wire System
A 2-Wire iMAC system has a fieldbus that contains a Signal Line and a Common
Line. The Signal Line is fed through all of the emergency stop contacts and
terminated into the EOL module. In a 2-Wire System, all iMAC fieldbus modules
communicate over the Signal Line. This means that if an emergency stop is
activated, the Signal Line is broken and all modules downstream of the activated
emergency stop will lose communication with the iMAC2 Controller.
3-Wire System
A 3-Wire iMAC system has a fieldbus that contains a Signal Line, Monitoring Line
and a Common Line. The Signal Line is fed through all of the emergency stop
contacts and terminated into the EOL module. The Monitoring Line is terminated
into an MEOL module. In a 3-Wire System, all iMAC fieldbus modules communicate
over the Monitoring Line. The advantage of the 3-Wire System, over the 2-Wire
System, is that when the Signal Line is broken by an emergency stop,
communication with all modules is still possible via the Monitoring Line.
A-Line
The Signal Line in a 3-wire system.
AR
The Auxiliary Relay (AR) of the iMAC2 Controller. The operation of the AR can be
customised using the application (SLP) software.
B-Line
The Monitoring Line in a 3-wire system or the Signal Line in a 2-wire system.
C-Line
The Common Line for 3-wire and 2-wire systems
Common Line
The Common Line as the name suggests is the common return communications
line of the L1 fieldbus. The Common Line is used in both 2-Wire and 3-Wire
Systems.
CR
The Control Relay (CR) of the iMAC2 Controller. Provides emergency stop function
via End-Of-Line module monitoring.
Fieldbus
The iMAC Fieldbus is the communications backbone for the iMAC system. Can be
run as either a 2-Wire or 3-Wire System.
iMAC
Integrated Monitoring and Control
Monitoring
Line
The Monitoring Line forms part of the L1 fieldbus in a 3-Wire system and is
terminated into a MEOL module
In 3-Wire Systems, all the modules communicate over the Monitoring Line.
This allows communication to continue with all modules if an emergency stop is
activated, which opens the Signal Line. The Signal Line is fed through the
emergency stop contacts.
Multi-drop
The term multi-drop refers to a communications line that allows multiple
communicating devices to be connected to the same line.
Signal Line
The Signal Line forms part of the L1 fieldbus in both 2-Wire and 3-Wire systems.
The Signal Line is feed through the emergency stop contacts and is terminated into
the EOL module. In a 3-Wire System, the Signal Line is used only for tripping and
the modules communicate on the Monitoring Line. In a 2-Wire System, the Signal
Line is used for both tripping and communication.
SLP
Supervisory Logic Program. The Ampcontrol proprietary programming language for
the iMAC2 Controller's application software.
Application (SLP) software must be written, compiled and installed in order for the
iMAC2 Controller to perform intended operation.

IMAC2B009 V2 Uncontrolled Copy - Refer to Ampcontrol Website for Latest Version Page 9 of 53
Ampcontrol Pty Ltd –ABN 28 000 915 542
iMAC System User Manual
iMAC2B009 V4 –10/18
APPROVED FOR EXTERNAL DISTRIBUTION –PROPERTY OF AMPCONTROL PTY LTD –NOT TO BE REPRODUCED IN PART
1.3.2 Module Definitions
Term
Definition
AIM
Analogue Input Module that connects to the iMAC L1 fieldbus. There are two types
available, a 0-10V model and a 4-20mA model.
ARM
Auxiliary Relay Module that connects to the iMAC L1 fieldbus. Provides a relay
output that mimics the operation of the iMAC2 Controller's AR. Note: requires
specific application (SLP) software for operation.
CRM
Control Relay Module that connects to the iMAC L1 fieldbus. Provides a relay
output that mimics the operation of the iMAC2 Controller's CR. Note: requires
specific application (SLP) software for operation.
DI4
Digital Input Module (4x digital inputs) that connects to the iMAC L1 fieldbus.
Provides remote monitoring of four voltage free contacts.
DI8
Digital Input Module (8x digital inputs) that connects to the iMAC L1 fieldbus.
Provides remote monitoring of eight voltage free contacts.
EMM
End of line Monitoring Module that connects to the iMAC L1 fieldbus. Provides a
changeover relay output that de-energises if the Signal Line is unhealthy.
EOL
End Of Line Module that terminates the Signal Line of the iMAC L1 fieldbus.
GRM
General Relay Module that connects to the iMAC L1 fieldbus. Provides an output
relay that can be remotely controlled by the iMAC2 Controller.
IIM
Input and Indication Module that connects to the iMAC L1 fieldbus. Provides five
voltage free contact inputs and four LED outputs for indication.
IRK
iMAC Remote Keypad that connects to the iMAC L1 fieldbus. Allows the user to
operate the iMAC2 Controller's interface remotely.
LED4
LED Output Module that connects to the iMAC L1 fieldbus. Provides four LED
outputs for indication.
LIM
LED Indication Module which interfaces directly to the iMAC Fieldbus, providing a
highly configurable remote indication module.
LPU
Lightning Protection Unit Module that connects to the iMAC L1 fieldbus. Provides
surge protection for a multi-dropped iMAC module.
MEOL
Monitoring End Of Line Module that terminates the Monitoring Line of the iMAC L1
fieldbus in a 3-Wire System.
MLB
Master Line Barrier is an intrinsically safe barrier required for I.S. applications. It
connects between the iMAC2 Controller and hazardous area L1 fieldbus.
RO4
Relay Output Module (4x relays) that connects to the iMAC L1 fieldbus. Provides
four relay outputs that can be remotely controlled by the iMAC2 Controller, or linked
to follow the states of an iMAC input module.
RTD1
Resistance Temperature Device Module that connects to the iMAC L1 fieldbus.
Provides a remote temperature input using a PT100 RTD sensor.
SIM-G
Serial Interface Module (GasGuard) that connects to the iMAC L1 fieldbus. This
module provides an interface between an Ampcontrol GasGaurd Controller and the
iMAC L1 fieldbus.
SIM-G2
Serial Interface Module (GasGuard x2) that connects to the iMAC L1 fieldbus. This
module provides an interface between two Ampcontrol GasGaurd Controllers and
the iMAC L1 fieldbus.
SIM-P
Serial Interface Module (Programmable) that connects to the iMAC L1 fieldbus.
This module provides an interface between a Modbus RTU RS485 slave device
and the iMAC L1 fieldbus.

IMAC2B009 V2 Uncontrolled Copy - Refer to Ampcontrol Website for Latest Version Page 10 of 53
Ampcontrol Pty Ltd –ABN 28 000 915 542
iMAC System User Manual
iMAC2B009 V4 –10/18
APPROVED FOR EXTERNAL DISTRIBUTION –PROPERTY OF AMPCONTROL PTY LTD –NOT TO BE REPRODUCED IN PART
Term
Definition
SIM-T
Serial Interface Module (Trolex™) that connects to the iMAC L1 fieldbus. This
module provides an interface between a Trolex™TX94 Series Controller and the
iMAC L1 fieldbus.
SLB
Slave Line Barrier that connects to the iMAC L1 fieldbus. This barrier allows the
connection of non-intrinsically safe modules to an intrinsically safe iMAC L1
fieldbus.
SQM
Sequence Module that connects to the iMAC L1 fieldbus. This module allows
sequenced control of equipment using the iMAC2 Controller's sequencing bits.
SSW
Speed Switch Module that connects to the iMAC L1 fieldbus. This module provides
conveyer belt slip protection and speed indication.
Fieldbus System Configurations
The iMAC fieldbus can be configured as either a 2-wire or 3-wire system depending on the required
application. Each of these configurations can be used within hazardous areas, provided that the fieldbus is
correctly installed utilising an iMAC MLB intrinsically safe barrier.
1.4.1 2-Wire System
2-Wire systems are typically used for low cost emergency stop systems or for monitoring systems that don’t
require an emergency stop function such as a mine wide gas monitoring system. If the iMAC2 Controller
emergency stop function is not required, the EOL module is not required, however an EOL module is still
recommended for providing fieldbus diagnostic functions.
Figure 1.1: 2-Wire iMAC Fieldbus System Configuration
CR
IMAC
CONTROLLER
Stop Switches
EOL
iMAC
Input Module
B
C
Stop Switches
iMAC
Input Module
1oo1 Safety Output

IMAC2B009 V2 Uncontrolled Copy - Refer to Ampcontrol Website for Latest Version Page 11 of 53
Ampcontrol Pty Ltd –ABN 28 000 915 542
iMAC System User Manual
iMAC2B009 V4 –10/18
APPROVED FOR EXTERNAL DISTRIBUTION –PROPERTY OF AMPCONTROL PTY LTD –NOT TO BE REPRODUCED IN PART
1.4.2 3-Wire System
3-Wire systems are typically used for emergency stop systems where constant monitoring of all modules is
required, regardless of whether an emergency stop has been activated.
In a 2-Wire system, when an emergency stop is activated, all modules downstream of the activated switch
go offline and cannot be monitored. The 3-Wire system addresses this shortcoming of the 2-wire system by
using separate signal and monitoring lines.
The Signal Line (or A-line) is fed through all of the emergency stop contacts and terminated into the EOL
module. The Monitoring Line (or B-line) is terminated into an MEOL module. All iMAC fieldbus modules are
connected to and communicate across the Monitoring Line.
The A-line and B-line are separated using a resistor, the resistor value is typically 47 ohms and allows faults
to be detected. Monitoring and comparing the EOL and MEOL module resistance readings allows the
system to detect short circuit cabling faults between the A and B lines.
Figure 1.2: 3-Wire iMAC Fieldbus System Configuration
1.4.3 Intrinsically Safe Systems
If the iMAC fieldbus is required to be intrinsically safe, a Master Line Barrier (MLB) is required. The MLB
barrier provides I.S. protection and incorporates the A-line resistor for three wire systems (i.e. there is no
need for an additional external A-line resistor; the MLB provides this via its A-line connection).
Figure 1.3: MLB Intrinsic Safety Barrier (Provides both 2-Wire and 3-Wire Terminal Connections)
WARNING!
The MLB barrier must be installed in the safe area.
For full intrinsic safety requirements, please refer to the I.S.
documentation.
1oo1 Safety Output
CR
IMAC
CONTROLLER
Stop Switches
MEOLEOL
iMAC
Input Module
Resistor
Stop Switches
A
B
C
iMAC
Input Module
IMAC
CONTROLLER Resistor A
B
C
I.S.
Protection
MLB
(Master Line Barrier)

IMAC2B009 V2 Uncontrolled Copy - Refer to Ampcontrol Website for Latest Version Page 12 of 53
Ampcontrol Pty Ltd –ABN 28 000 915 542
iMAC System User Manual
iMAC2B009 V4 –10/18
APPROVED FOR EXTERNAL DISTRIBUTION –PROPERTY OF AMPCONTROL PTY LTD –NOT TO BE REPRODUCED IN PART
SAFETY AND OTHER WARNINGS
For safety reasons, the iMAC System must be installed, operated and serviced only by competent electrical
personnel. Please read and understand this instruction manual completely before installing, operating or
servicing this equipment. Failure to install or operate this system in accordance with the instructions
contained in this manual may create hazardous operating conditions.
Safe Use of Equipment
The equipment supplied has been designed and manufactured to ensure safe operation. The equipment
must only be used within the design parameters.
The instructions within this manual must be observed as an aid towards achieving the safest possible
installation.
Persons responsible for installation, maintenance, or operation, must observe the following
instructions:
2.1.1 Changes to Equipment
Changes in the design and modifications to the equipment are not permitted. Unauthorised changes made
to the hardware or operating firmware will void the manufacturer's warranty, and may compromise the
integrity of the system into which it is installed and other connected equipment.
2.1.2 Equipment Knowledge
Experience with, or understanding of, this equipment is essential for the safe installation and removal of
the equipment. Therefore, please read and understand this manual prior to use. Competency based
training courses are recommended and are available on request.
2.1.3 Manual Handling
Precautions have been taken to ensure all equipment is safe to handle and free from sharp edges.
However, care should always be taken when handling enclosures.
2.1.4 Installation
Correct operation and safety depend on the iMAC System and associated equipment being installed
correctly. Mechanical and or electrical installation and maintenance of plant and equipment must only be
carried out by appropriately qualified personnel and must be tested thoroughly prior to operation.
WARNING!
When installing intrinsically safe equipment, the Conditions of
Certification must be adhered to. Failure to comply with the Conditions
of Certification may seriously compromise the integrity of the system
and/or its components. The user must ensure that the “Conditions of
Safe Use” outlined in the certificate are met or the certificate (and the
I.S. rating) will not be valid.
2.1.5 Operation
As safety depends on the iMAC System functioning correctly it is highly recommended that all safety
functions of the system be periodically tested to ensure correct operation.

IMAC2B009 V2 Uncontrolled Copy - Refer to Ampcontrol Website for Latest Version Page 13 of 53
Ampcontrol Pty Ltd –ABN 28 000 915 542
iMAC System User Manual
iMAC2B009 V4 –10/18
APPROVED FOR EXTERNAL DISTRIBUTION –PROPERTY OF AMPCONTROL PTY LTD –NOT TO BE REPRODUCED IN PART
RECEIVING AND STORAGE
Receiving
All possible precautions are taken to protect the equipment against damage or losses during shipment,
however before accepting delivery, check all items against the packing list or bill of loading. If there are
shortages or evidence of physical damage, notify Ampcontrol immediately.
Notify Ampcontrol within 7 days (maximum) in case of shortages or discrepancies, according to the packing
list. This action will help ensure a speedy resolution to any perceived problems. Keep a record of all claims
and correspondence. Photographs are recommended.
Where practicable do not remove protective covers prior to installation unless there are indications of
damage. Boxes opened for inspection and inventory should be carefully repacked to ensure protection of
the contents or else the parts should be packaged and stored in a safe place. Examine all packing boxes,
wrappings and covers for items attached to them, especially if the wrappings are to be discarded.
Inspection
Equipment that is found to be damaged or has been modified away from its published specification must not
be used. Please contact Ampcontrol if the equipment is suspected to be different than that ordered or if it
does not match the published specifications.
Storage after Delivery
When the equipment is not to be installed immediately, proper storage is important to ensure protection of
equipment and validity of warranty.
All equipment should be stored indoors, preferably on shelves and protected from the elements.
Unpacking of Equipment
The method of packing used will depend on the size and quantity of the equipment. The following cautions
should be interpreted as appropriate.
CAUTION!
Take care when unpacking crates as the
contents may have shifted during transport.
ENVIRO
The disposal of packaging materials, replaced parts, or components
must comply with environmental restrictions without polluting the soil,
air or water.
Ensure that any timber and cardboard used as packaging is disposed
of in a safe and environmentally responsible manner.
Where possible, dispose of all waste products i.e. oils, metals, plastic
and rubber products by using an approved recycling service centre.

IMAC2B009 V2 Uncontrolled Copy - Refer to Ampcontrol Website for Latest Version Page 14 of 53
Ampcontrol Pty Ltd –ABN 28 000 915 542
iMAC System User Manual
iMAC2B009 V4 –10/18
APPROVED FOR EXTERNAL DISTRIBUTION –PROPERTY OF AMPCONTROL PTY LTD –NOT TO BE REPRODUCED IN PART
iMAC SYSTEM OVERVIEW
The iMAC system is an Integrated Monitoring and Control system designed specifically for long line
distributed monitoring and control in harsh hazardous areas such as mining and heavy industry. The system
is IECEx Ex ia Group I certified allowing use in intrinsically safe underground mining applications.
The iMAC system is basically a configurable logic controller, with fieldbus connected I/O modules. Modules
are simply multi-drop connected to the iMAC fieldbus which reach up 10km and beyond. Note: the maximum
length possible depends on a number of factors such as the number and type of modules connected, the
distribution of modules, and the fieldbus cable type. Ampcontrol has a number of optimised iMAC fieldbus
cables available to cater for your specific system requirements. Please consult with a qualified Ampcontrol
applications engineer whom will be able to discuss and advise the most cost effective cable to meet your
requirements.
Key Features:
Remote monitoring and control using a flexible range of I/O modules
Digital input modules (most input modules are powered directly from the fieldbus)
Relay output modules
Analogue input modules
Serial interface modules
Fault tolerant fieldbus with high electrical noise immunity
Advanced fieldbus diagnostics (including individual module loop resistance readings and individual
module communications error counters)
Fieldbus E/stop function qualifies for SIL2 or SIL3 applications
Intrinsically Safe Certification (IECEx Ex ia Group I)
Typical Applications:
Emergency Stop Systems
Overland bulk material conveyors (E/stop, Pullkey monitoring, belt drift/wander, belt tear, blocked
chute, sequencing, and remote isolation controls)
Underground mining conveyors (E/stop, Pullkey monitoring, belt drift/wander, belt tear, blocked
chute, sequencing, and remote isolation controls)
Underground mine wide gas monitoring systems (NERZ/ERZ systems, CH4, CO, CO2, O2, H2S
monitoring)
Longwall monitoring and control (AFC, BSL, E/stop, sequencing and remote isolation controls)
Coal prep-plant/washery monitoring
Rail network traffic monitoring
Any application that requires reliable monitoring and control of fieldbus I/O distributed over large
distances. Up to 10km and beyond can be achieved, subject to system configuration and cable type.

IMAC2B009 V2 Uncontrolled Copy - Refer to Ampcontrol Website for Latest Version Page 15 of 53
Ampcontrol Pty Ltd –ABN 28 000 915 542
iMAC System User Manual
iMAC2B009 V4 –10/18
APPROVED FOR EXTERNAL DISTRIBUTION –PROPERTY OF AMPCONTROL PTY LTD –NOT TO BE REPRODUCED IN PART
Typical Installation
The iMAC system consists of a Controller which drives either a 2-wire or 3-wire fieldbus to which I/O
modules are multi-drop connected; the fieldbus is terminated with specialised End-Of-Line (EOL) module(s)
to ensure the integrity of the fieldbus.
Figure 4.1: Block Diagram of a Simple iMAC 2-Wire System
The iMAC2 Controller is analogous to a mini-PLC. It communicates with I/O modules and can be
programmed to process input data and affect output controls. The application program is known as SLP –
Supervisory Logic Program. The SLP programming language is a proprietary Ampcontrol language with
specialised control and monitoring functions.
The majority of iMAC input modules derive their power directly from the fieldbus line, whilst the majority of
iMAC output modules require a local power supply to operate.
A host system (e.g. PLC) can communicate with the iMAC2 Controller via a configurable RS232/RS485
serial port using Modbus protocol. Data can be exchanged between iMAC2 Controller and host system via a
read/wire Modbus register map. The iMAC2 Controller provides an Ethernet TCP/IP port that allows read-
only access to the iMAC2 Controller’s Data Point Table. The Ethernet port also provides a Web Interface,
allowing system data to be viewed in real time, as well as a viewing platform for the Controller’s historical
logs.
The Controller displays monitoring and control data on a four (4) line LCD screen. The user navigates the
application software defined display screens via the unit’s keypad, which also allows for user supervisory
control messages.
Remote monitoring and control is implemented through modules connected to the fieldbus. Local control is
implemented through the Controller’s inputs and outputs. The Controller’s critical safety relay is called the
Control Relay (CR). The Controller also has an Auxiliary Relay (AR) output, which can be used for general
control applications.
CR
Control Relay L1+
L1-
iMAC2 Controller End of Line (EOL)
Module
Input
Module
Output
Module
Input
Module

IMAC2B009 V2 Uncontrolled Copy - Refer to Ampcontrol Website for Latest Version Page 16 of 53
Ampcontrol Pty Ltd –ABN 28 000 915 542
iMAC System User Manual
iMAC2B009 V4 –10/18
APPROVED FOR EXTERNAL DISTRIBUTION –PROPERTY OF AMPCONTROL PTY LTD –NOT TO BE REPRODUCED IN PART
Application Software
Ampcontrol’s qualified applications engineers can develop specific application (SLP) software that tailors the
functionality of the iMAC2 Controller to the customer’s individual requirements.
iMAC Modules
A wide range of iMAC fieldbus modules are available for designing flexible and expandable systems to meet
your specific application requirements.
4.3.1 Input Modules
Digital input modules are available for monitoring switch contact devices such as e/stops, pullkeys, float
switches, level switches, belt drift switches, belt wander switches, belt tear switches, blocked chute switches
etc.
Analogue input modules are available for monitoring 4-20mA or 0-10V process devices such as pressure
sensors, gas sensors, load sensors, level sensors etc.
Temperature input modules are available for monitoring temperature via PT100 RTD sensor elements.
4.3.2 Output Modules
Output modules can be controlled directly from input modules or indirectly via iMAC2 Controller application
(SLP) software. In addition to general relay output modules, specialised output modules are available for
duplicating the iMAC2 Controller Control and Auxiliary relays for redundancy and for passing belt sequence.
LED output modules are available for providing system status indication.
4.3.3 Serial Interface Modules
A number of serial interface modules are available, allowing Slave Modbus RTU devices such as
Ampcontrol’s GasGuard Controllers, Trolex™Controllers and Ampcontrol’s range of IS UPS
(Uninterruptable Power Supplies) to communicate with the iMAC2 Controller over the fieldbus.
4.3.4 Specialty Modules
Specialty modules are available for monitoring conveyor speed/slip.
4.3.5 Protection Modules
Protection modules are available for providing intrinsic safety. For non-intrinsically safe applications lightning
protection modules are available for providing a level of protection against nearby lightning strike transients.
4.3.6 End of Line Modules
End Of Line (EOL) modules are used to terminate the iMAC fieldbus and form part of the key safety function
of the iMAC system.

IMAC2B009 V2 Uncontrolled Copy - Refer to Ampcontrol Website for Latest Version Page 17 of 53
Ampcontrol Pty Ltd –ABN 28 000 915 542
iMAC System User Manual
iMAC2B009 V4 –10/18
APPROVED FOR EXTERNAL DISTRIBUTION –PROPERTY OF AMPCONTROL PTY LTD –NOT TO BE REPRODUCED IN PART
iMAC Address Range
Each Controller can communicate and control 255 module data addresses.
All input modules must be given a unique address from 1 to 255. Output modules are also given an address
from 1 to 255 but do not have to be unique. Output modules can share the same address as each other.
Output modules with the same address will operate at the same time. Output modules can also be given the
same address as an input module, in these cases the output module will respond directly to the input
module’s data.
Address 0 is reserved for specialised applications, for example CRM, ARM and GRM modules utilise
Address 0. If a standard iMAC module is set to Address 0, the module will go offline and will not respond to
fieldbus datascans. This can be a handy feature for fault finding. A module set to Address 0 will appear
offline, but will still respond to rollcall scans allowing to its address to be set to a valid Address from 1 to
255.
Note: Non-addressable iMAC modules such as SQM, RKM and EOL rollcall as Address 0 even though they
don’t actually utilise Address 0, this is true for all non-addressable modules.
Fault Finding Statistics
The Controller records a number of statistics for every fieldbus address in the range 1-255. In addition to a
DATA register, every fieldbus address has an associated STATUS register, RESISTANCE register and
ERROR register. The module’s status bits, fieldbus loop resistance and number of communication errors
are recorded in these registers which are available to host systems via the Modbus interface.

IMAC2B009 V2 Uncontrolled Copy - Refer to Ampcontrol Website for Latest Version Page 18 of 53
Ampcontrol Pty Ltd –ABN 28 000 915 542
iMAC System User Manual
iMAC2B009 V4 –10/18
APPROVED FOR EXTERNAL DISTRIBUTION –PROPERTY OF AMPCONTROL PTY LTD –NOT TO BE REPRODUCED IN PART
Networking
The iMAC2 Controller is equipped with two fieldbus ports, the L1 driving port and the L2 listening port.
Controllers can be networked together by connecting the listening L2 fieldbus port of one Controller to the
parent driving L1 fieldbus of another Controller.
Controllers can be networked in a tree structure, with the Master Controller being at the top of the tree. The
Master Controller drives a line, to which many Slave Controllers can be connected. Each Slave Controller
can drive its own L1 fieldbus which may have many Slave Controllers connected to it. A maximum of 16
iMAC2 Controllers can be networked together on the iMAC system.
Figure 4.2: Tree Network of iMAC2 Controllers
WARNING!
The L1 fieldbus lines from two Controllers must never be connected
together. This would violate the Intrinsic Safety Approval and may
damage the drive circuits.
In a networked iMAC system, each individual Controller will drive its own fieldbus, via the L1 port.
The L2 fieldbus port shall only be used for connection to a ‘Parent L1 Line’ owned by a Controller further up
the tree. The Controller’s L2 connection terminals are electrically isolated and the Controller responds to
parent L1 signals like any other module connected to the parent L1 fieldbus.
The iMAC2 Controller’s application (SLP) software can be programmed to utilise the iMAC2 Controller’s 16-
position rotary switch to select the Controller’s network address.
Networking can also be achieved by connecting each iMAC2 Controller to a PLC, which then allows
communication over the site’s PLC network.
L2
L1
iMAC2 Controller
#1
iMAC2
Controller #1
Local Network
L1
L2 iMAC2
Controller #3
Local Network
L1
L2 iMAC2
Controller #4
Local Network
L1
iMAC2 Controller
#2
iMAC2 Controller
#3
iMAC2 Controller
#4
iMAC2
Controller #2
Local Network

IMAC2B009 V2 Uncontrolled Copy - Refer to Ampcontrol Website for Latest Version Page 19 of 53
Ampcontrol Pty Ltd –ABN 28 000 915 542
iMAC System User Manual
iMAC2B009 V4 –10/18
APPROVED FOR EXTERNAL DISTRIBUTION –PROPERTY OF AMPCONTROL PTY LTD –NOT TO BE REPRODUCED IN PART
Local and Global Data
An iMAC fieldbus address can be configured as LOCAL or GLOBAL. If the address is local, it is not passed
around the network. A local address is only available at the Controller to which the module is connected.
To output local data, the output module must be connected to the same communication line as the local
address. Local data can only be displayed on the Controller driving the L1 fieldbus to which the local
modules are connected.
If the address is global it is passed throughout the network. A global address can have only one owner
(input module or Controller) within the whole network. But a global address can be output in many places
across the network.
Usually each Controller within a network has a range of local addresses, which are used for local monitoring
and control. The results, or summary, of the monitoring information is published into a range of global
addresses for display and control at other Controllers.
Sequence Control
The iMAC System provides four specialised control bits for sequence control. These are generally used for
conveyor sequence control, but can be re-purposed for other applications. The sequence control bits are
called:
L1 Sequence Down Bit
L1 Sequence Up Bit
L2 Sequence Up Bit
L2 Sequence Down Bit
The “L1 Sequence Down Bit” and the “L2 Sequence Up Bit” are used by the iMAC2 Controller to initiate
downstream and upstream sequenced starts (respectively). These bits can be set and cleared by the
Controller’s application (SLP) software. This is in contrast to the “L1 Sequence Up Bit” and the “L2
Sequence Down Bit” which are read only. These bits are set by other Controllers in the iMAC Network.
The “L1 Sequence Down Bit” is transmitted from the iMAC2 Controller’s L1 fieldbus port. Any iMAC2
Controller’s that are networked with this Controller, via their L2 fieldbus ports, will receive this bit and store it
as the “L2 Sequence Down Bit”.
The “L2 Sequence Up Bit” is transmitted from the iMAC2 Controller’s L2 fieldbus port. The upstream iMAC2
Controller in the network will receive this bit and store it as the “L1 Sequence Up Bit”.
The Controller’s application (SLP) software can be customised to affect conveyor control via these
sequence bits, Figure 4.3 and Figure 4.4 show typical upstream and downstream examples.
Other manuals for iMAC2
1
Table of contents
Other Ampcontrol Control System manuals
Popular Control System manuals by other brands
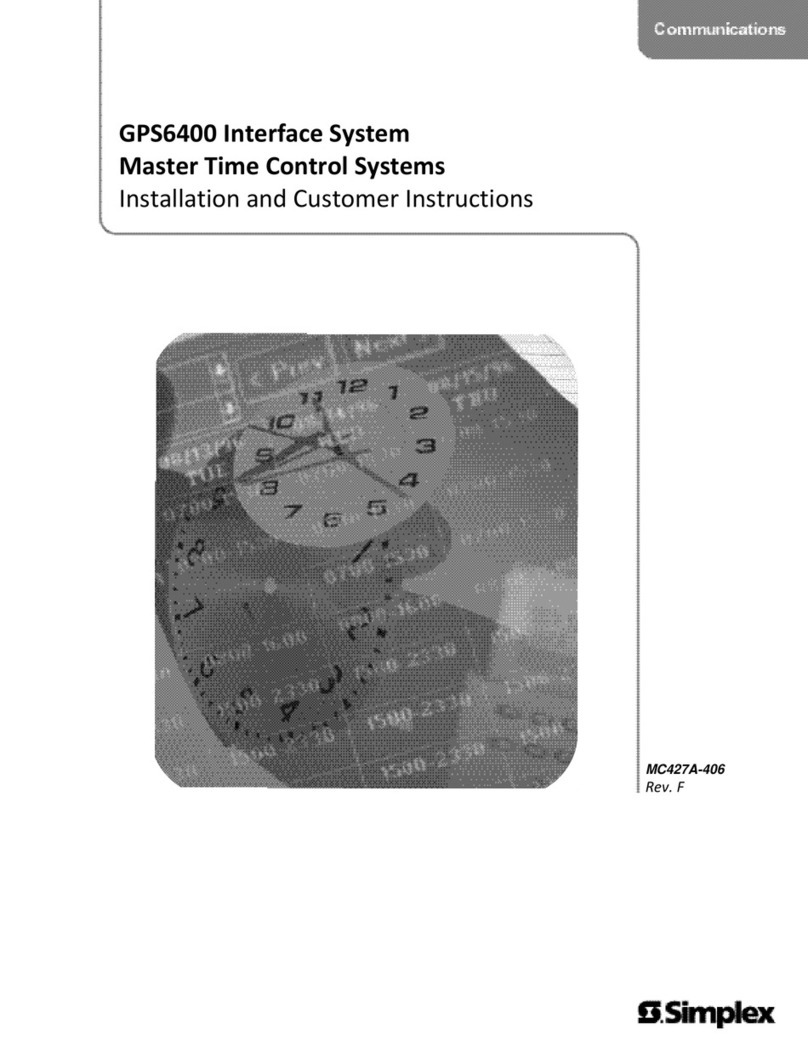
Simplex
Simplex GPS6400 installation instructions
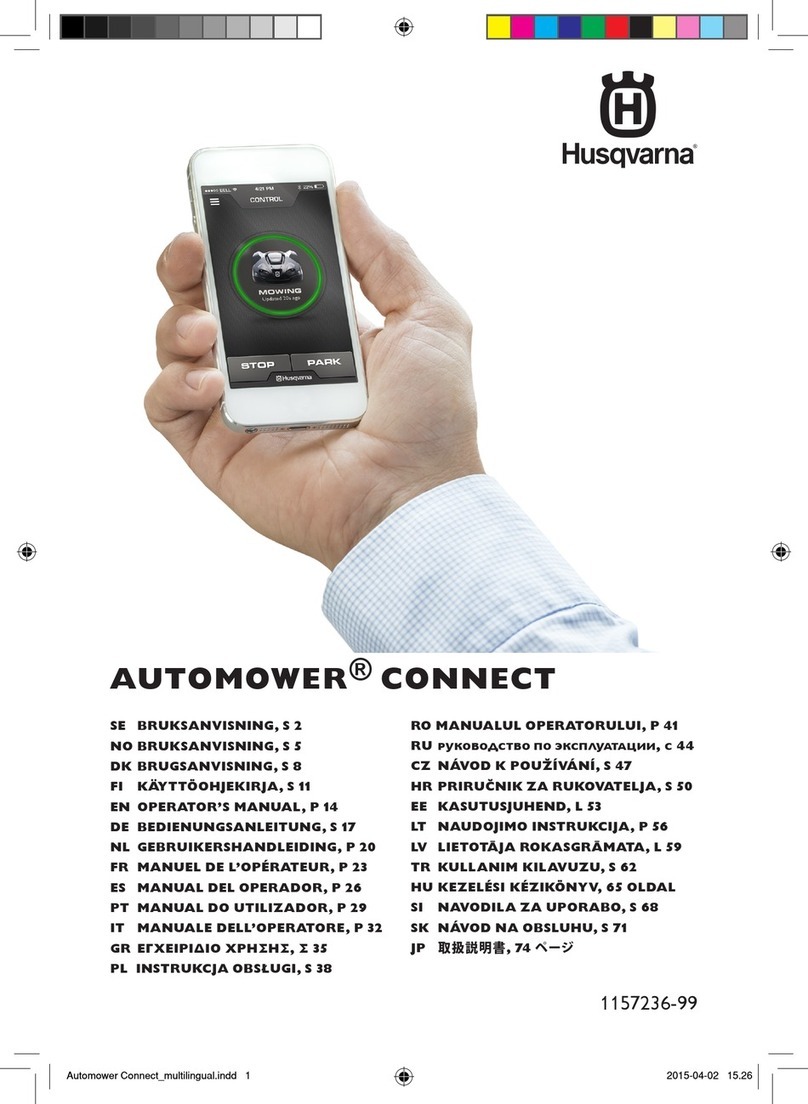
Husqvarna
Husqvarna Automower Connec Operator's manual
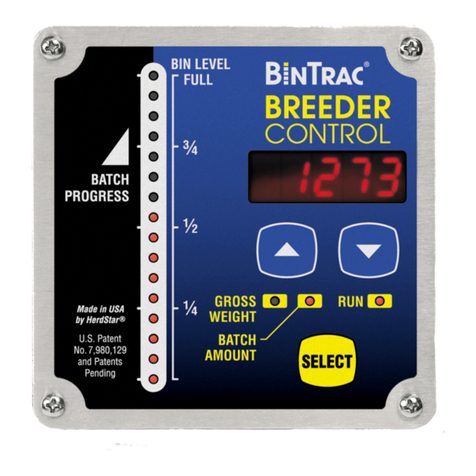
herdstar
herdstar BinTrac Breeder Control installation manual
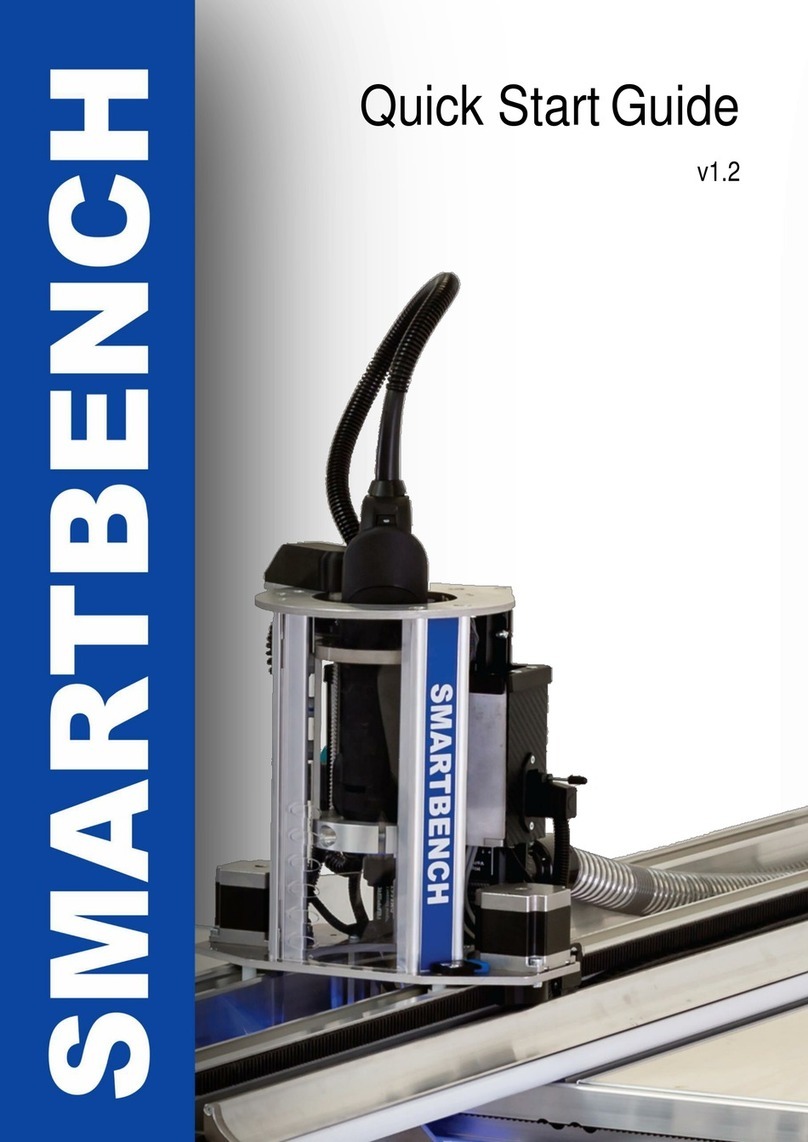
Yeti
Yeti SMARTBENCH quick start guide

Exhausto
Exhausto EFC 25 Installation & operating instructions
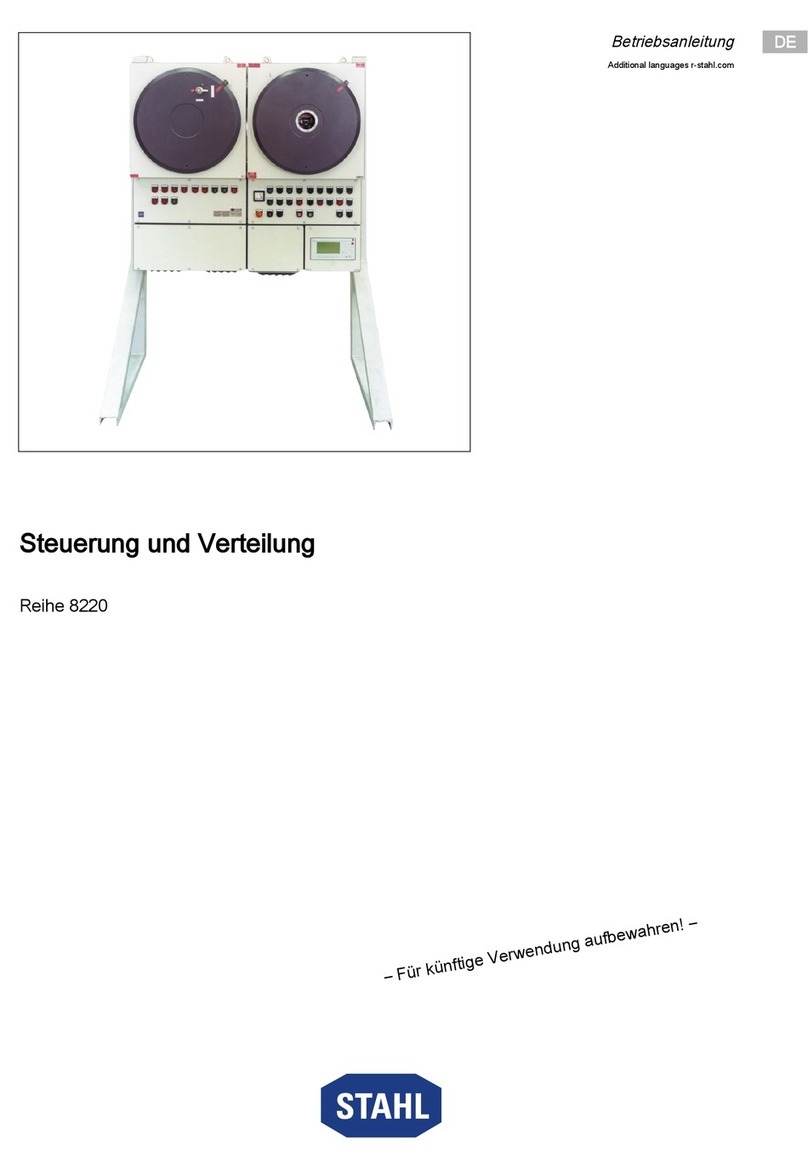
Stahl
Stahl 8220 Series operating instructions