Rtelligent R Series User manual

R60X3 user manual - 1 -
szruitech.com
Contents
1.Product Description..................................................................................................................... - 2 -
2.Application Environment and Installation.................................................................................- 2 -
2.1Environmental requirement......................................................................................................- 3 -
2.2 Drive installation dimensions..................................................................................................- 3 -
3.Drive Port and Connection......................................................................................................... - 3 -
3.1 Port function description..........................................................................................................- 4 -
3.2 Power supply input................................................................................................................... - 4 -
3.3 Motor connection...................................................................................................................... - 4 -
3.4 Control signal connection........................................................................................................- 4 -
3.4.1 PUL、DIR Port:connection for pulse command........................................................ - 6 -
3.4.2 ENA port: enable/disable................................................................................................ - 6 -
3.4.3 Examples for control signal connection........................................................................- 7 -
4. The setting of operating parameters....................................................................................... - 8 -
5. Common Faults and Troubleshooting.....................................................................................- 4 -
6. Drive working status LED indication......................................................................................- 10 -
7. Guarantee Clause.................................................................................................................... - 10 -

R60X3 user manual - 2 -
szruitech.com
1. Product Description
Thank you for choosing Rtelligent R series digital stepper driver.
R60X3 Three-axis stepper motor driver, based on a 32-bit three-core DSP processing chip
platform, adopts internal PID current control algorithm design, and has excellent performance.
R60X3 Three-axis independent control driver, split-drive three-axis stepper motor. The R60X3
can drive three 2 phase/3 phase stepper motors with base below 60, which is especially
suitable for multi-axis equipment or platform robots.
The current and subdivision parameters are set by the R60X3 special debugging software.
The driver has over-voltage, under-voltage, and over-current protection. The input and output
control signals are optically isolated.
Power supply
24 - 48 VDC
Output current
Debug software settings, up to 4.2 amps (peak)
Current control
PID current control algorithm
Segment settings
Debugging software setting, 200 ~ 65535
Speed range
Optional suitable stepper motor, up to 3000rpm
Resonance
suppression
Automatically calculate the resonance point to suppress intermediate
frequency vibration
Parameter
adaptation
Drive initialization automatically detects motor parameters and
optimizes control performance
Pulse mode
Direction & Pulse
Pulse filtering
2MHz Digital Signal Filter
Idle current
The current is automatically halved after the motor stops running
We hope that our products with excellent performance can help you to complete the sports

R60X3 user manual 2-- 3 -
szruitech.com
control program successfully.
Please read this technical manual before using the products.
2. Application Environment and Installation
2.1 Environmental requirement
Item
Rtelligent R60X3
Installation environment
Avoid dust, oil and corrosive environment
Vibration
0.5G(4.9m/s2)Max
Operating temperature/humidity
0℃~ 45℃/ 90% RH or less (no condensation)
Storage and transportation temperature:
-10℃~ 70℃
Cooling
Natural cooling / away from the heat source
Waterproof grade
IP54
2.2 Drive installation dimensions
21 50
97
175
11,5
31
5
5
2.3 Drive installation requirements

R60X3 user manual 2-- 4 -
szruitech.com
When installing, please attach the drive to the metal surface of the cabinet to facilitate
heat dissipation. Please note that sufficient space should be reserved in the placement to
obtain sufficient heat dissipation; if necessary, a cooling fan can be configured to ensure good
heat dissipation conditions in the control cabinet.
During assembly, avoid drillings and other foreign matters falling inside the drive.
During assembly, please use M3 screw to fix.
When there is a vibration source near the installation (such as a drilling machine), please
use a vibration absorber or install anti-vibration rubber gaskets.
3. Drive Port and Connection
3.1 Port function description
Function
Grade
Definition
Remarks
Power supply
input port
V+
Input DC power positive
DC 24~48V
V-
Input DC power negative
Motor 1
A1+
Connect both ends of Phase A
winding of Motor 1
A1-
B1+
Connect both ends of Phase B
winding of Motor 1
B1-
Motor 2
A2+
Connect both ends of Phase A
winding of Motor 2
A2-
B2+
Connect both ends of Phase B
winding of Motor 2
B2-
Motor 3
A3+
Connect both ends of Phase A
winding of Motor 3
A3-
B3+
Connect both ends of Phase B
winding of Motor 3
B3-
15
Pin
Control
signal
interface
1
PUL1+
Motor 1 pulse port
3.3-24V
compatible
2
PUL1-
3
DIR1+
Motor 1 direction port
4
DIR1-
5
PUL 2+
Motor 2 pulse port
3.3-24V
compatible
6
PUL 2-
7
DIR 2+
Motor 2 direction port
8
DIR 2-
9
PUL 3+
Motor 3 pulse port
3.3-24V
compatible
10
PUL 3-
11
DIR 3+
Motor 3 direction port
12
DIR 3-
13
ENA+
Enable signal port
3.3-24V
compatible
14
ENA-
15

R60X3 user manual 2-- 5 -
szruitech.com
3.2 Power supply input
The power supply of the driver is DC power, the input voltage range is between 24V ~ 50V,
and the power is greater than 200W.
Power selection reference:
Voltage:
The stepping motor has the characteristic that the torque decreases with the increase of
the motor speed, and the input power voltage level will affect the magnitude of the high-speed
torque drop of the motor. Properly increasing the voltage of the input power can increase the
output torque of the motor at high speed.
Stepping servo has higher speed and torque output than ordinary stepping. Therefore, if
you want to obtain better high-speed performance, you need to increase the power supply
voltage of the driver.
Current:
The work of the drive is to convert the input power supply with high voltage and low
current to the low voltage and high current at both terminals of the motor winding. In actual use,
select a suitable power source according to the motor model, load torque and other factors.
The effects of regeneration voltage:
The stepper motor also retains the characteristics of the generator when it is working.
During deceleration, the kinetic energy accumulated by the load will be converted into
electrical energy and superimposed on the driver circuit and input power. When using, pay
attention to the setting of acceleration and deceleration time to prevent the protection of the
driver or power supply.
When the driver is powered off, when you pull the load to make the motor move, you will
see that the driver LED indicator is on, which is also affected by this.
3.3 Motor connection
4线电机
A+
A -
B+
B-
8线串联
A+
A -
B+
B-
8线并联
A+
A -
B+
B-

R60X3 user manual 2-- 6 -
szruitech.com
6线串接
A+
A -
B+
B-
NC
NC
6线中心抽头
B+
B-
A+
A -
NC
NC
The matching motor of the R60X3 drive is the low resistance and low inductance hybrid
stepper motor.
The common 2-phase stepper motor’s lead number are 4, 8 and 6.
There is only one connection mode for 4 leads motor.
Series and parallel connection mode are used by 8 leads motor:
When series used, the winding inductance increased. The set of drive current should be about
0.7times than before. This is suitable for low speed required.
When parallel used, the winding inductance decreased. The set of drive current should be
about 1.4times than before. This is suitable for high speed required.
Parallel and central tapping connection mode are used by 6 leads motor:
When parallel used, all the winding connected, and the inductance was higher. This is suitable
for low speed required.
When central tapping used, half of the winding connected, and the inductance was lower. This
is suitable for high speed required.
3.4 Control signal connection
3.4.1 PUL、DIR Port: connection for pulse command
The R60X3 control signal is a pulse input and supports three-axis differential / pulse &
direction mode.
Pulse level is 3.3V ~ 24V compatible (no string resistor required)
Pulse & Direction(PUL + DIR)
正
转
反
转
P
U
L
D
I
R
3. 4. 2 ENA port: enable/disable
When the default optocoupler is off, the drive outputs the current to the motor. When the
internal optocoupler is on, the drive will cut off the current of each phase of the motor so that
the motor is in a free state, and the stepper pulse can not be responded.
When the motor is in an error state, enable disconnection. The level logic of the enable
signal can be set to the opposite by the debug software.

R60X3 user manual 2-- 7 -
szruitech.com
3. 4. 3 Examples for control signal connection
Common Anode
Pul+
Pul-
Dir+
Dir-
Ena +
Ena -
控制器
驱动器
Vcc
Common Cathode
Vcc
Pul+
Pul-
Dir+
Dir-
Ena+
Ena-
驱动器
Vcc
Vcc
控制器
Difference
Pul+
Pul-
Dir+
Dir-
Ena+
Ena-
驱动器
Pul+
Pul-
Dir+
Dir-
Ena+
Ena-
控制器

R60X3 user manual 2-- 8 -
szruitech.com
4. The setting of operating parameters
R60X3 operating parameters are set by the debugging software, and the debugging interface is as
follows:
The three axis related parameters are independent and can be set separately as needed.
Parameter analysis:
①Current: peak value of output current of each axis. 5600 mA
②Subdivision: the subdivision value of each axis. 200-65535
③Standby time: the delay time when the motor enters half flow when it is stationary
④Standby current: Set the current percentage during standby
⑤Shaft time after power-on: the time when the current is fully established after power-on
⑥S curve time: S-filter time inside the input command; unit is 50 us
⑦Pulse bandwidth limitation: input pulse limit frequency
⑧ENA level: enable signal logic level
⑨ENA state: driver action setting when enabled

R60X3 user manual 2-- 9 -
szruitech.com
5. Common Faults and Troubleshooting
Phenomenon
Possible situations
Solutions
Motor does
not work
Power indicator is off
Check the power supply circuit for normal
power supply
The motor rotor is
locked but the motor
does not work
Pulse signal is weak; increase the signal
current to 7-16mA
The speed is too slow
Select the right micro-stepping
Drive is protected
Solve the alarm and re-power
Enable signal problem
Pull up or disconnect the enable signal
Command pulse is
incorrect
Check whether the upper computer has pulse
output
The steering
of motor is
wrong
The rotary direction of
motor is reverse
Change the motor wiring sequence or adjust the
command direction
The motor cable is
disconnected
Check the connection
The motor has only
one direction
Damaged input port
Alarm
indicator is on
The motor connection
is wrong
Check the connection
The voltage is too high
or too low
Check the power supply
Damaged motor or
driver
Replace the motor or driver
The position
or speed is
wrong
The signal is disturbed
Eliminate interference for reliable grounding
The command input is
incorrect
Check the upper computer instructions to
ensure the output is correct
Incorrect speed setting
Check the DIP switch status and correctly
connect the switches
Motor lost step
Check if the command speed is too large and the
motor selection is small
The drive
terminal
Short circuit between
terminals
Check power polarity or external short circuit

R60X3 user manual 2-- 10 -
szruitech.com
burned up
Internal resistance
between terminals is
too large
Check whether there is any solder ball due to
excessive addition of solder on the wire
connections
The motor is
out of
tolerance
Acceleration and
deceleration time is
too short
Reduce command acceleration or increase
drive filtering parameters
Motor torque is too low
Select the motor with high torque
The load is too heavy
Check the load weight and quality and adjust
the mechanical structure
The current of power
supply is too low
Replace the appropriate power supply
6. Drive working status LED indication
LED status
Drive status
Green indicator is on for long time
Drive not enabled
Green indicator is flickering
Drive working normally
One green indicator and one red indicator
Motor 1 overcurrent
Two green indicator and one red indicator
Motor 2 overcurrent
Three green indicator and one red indicator
Motor 3 overcurrent
One green indicator and two red indicators
Drive input power
overvoltage
One green indicator and three red
indicators
The internal voltage of
the drive is wrong
7.Guarantee Clause
7.1 Warranty period: 18 months
We provide quality assurance for one year from the date of delivery and free maintenance
service for our products during the warranty period.
7.2 Exclude the following:
■ Improper connection, such as the polarity of the power supply is reversed and insert/pull

R60X3 user manual 2-- 11 -
szruitech.com
the motor connection when the power supply is connected.
■ Beyond electrical and environmental requirements.
■ Change the internal device without permission.
7.3 Maintenance process
For maintenance of products, please follow the procedures shown below:
(1) Contact our customer service staff to get the rework permission.
(2) The written document of the drive failure phenomenon is attached to the goods, as well as
the contact information and mailing methods of the sender.
Mailing address:
Post code:
Tel.:
Other manuals for R Series
1
This manual suits for next models
1
Table of contents
Other Rtelligent Control Unit manuals
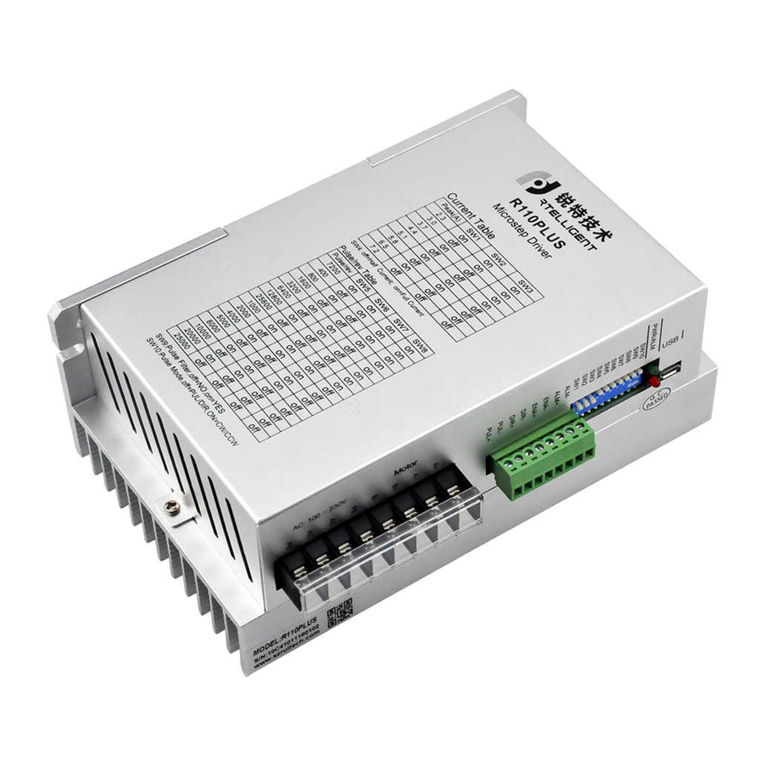
Rtelligent
Rtelligent R110PLUS User manual

Rtelligent
Rtelligent Ruitech R Series User manual
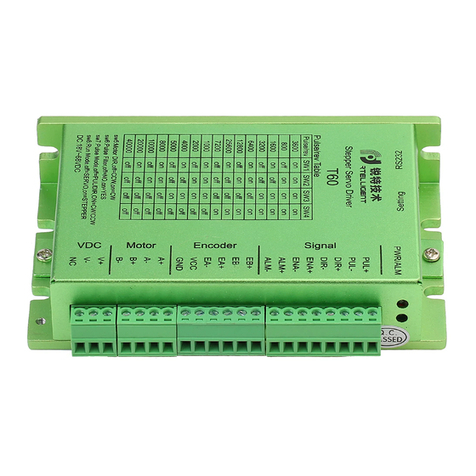
Rtelligent
Rtelligent T60-IO User manual
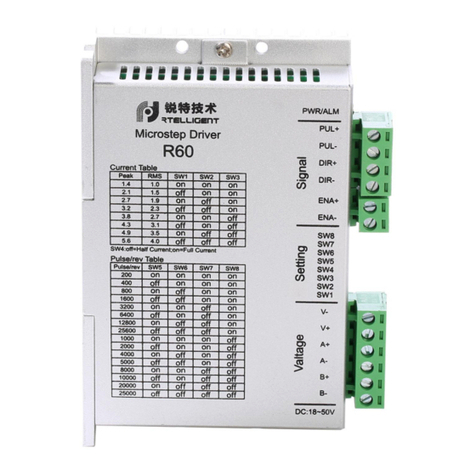
Rtelligent
Rtelligent R60 User manual
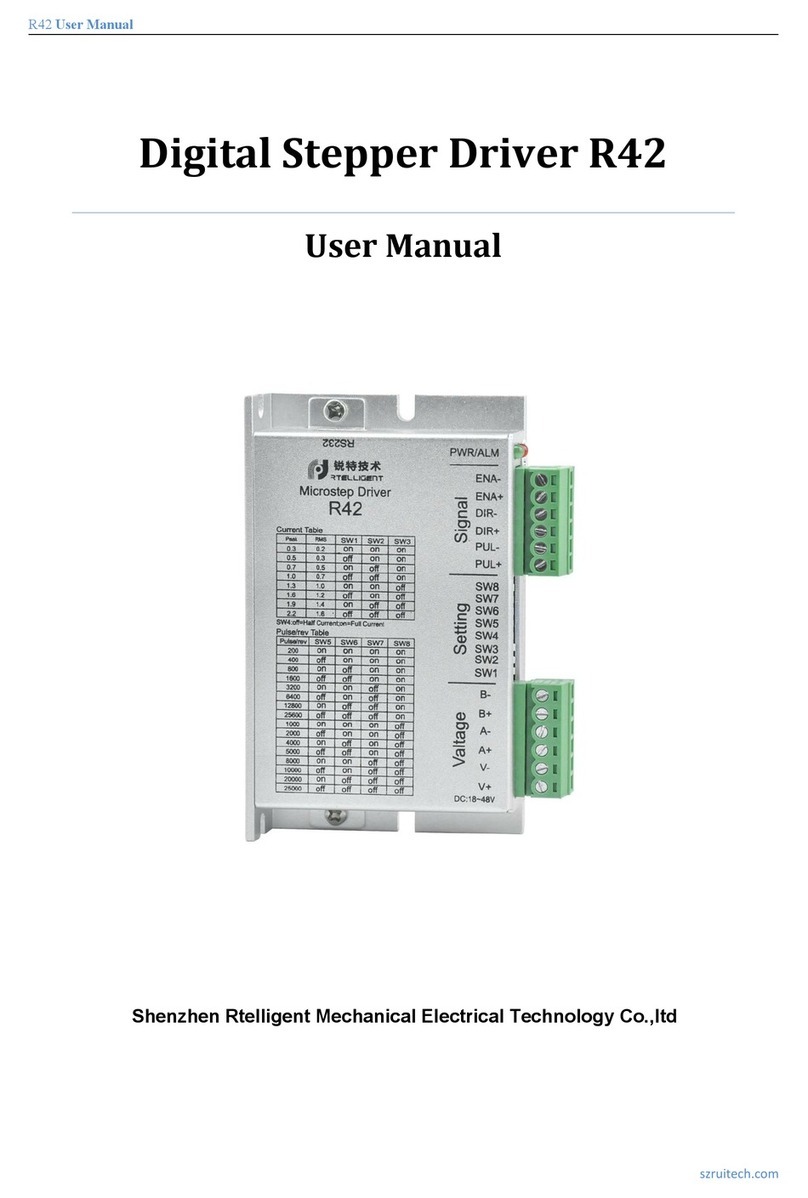
Rtelligent
Rtelligent R42 User manual
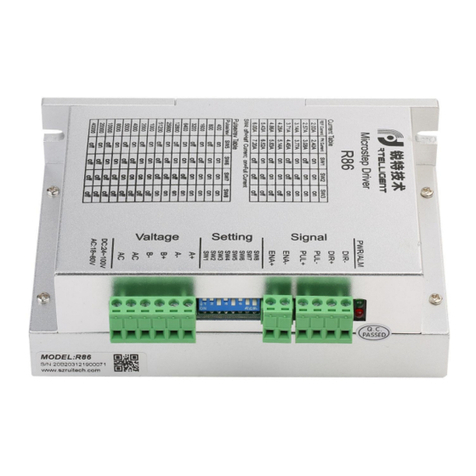
Rtelligent
Rtelligent R86 User manual
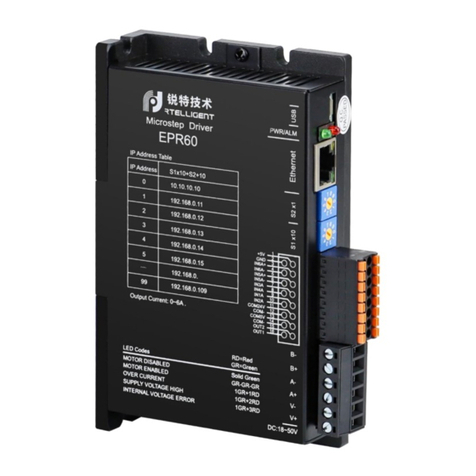
Rtelligent
Rtelligent EP Series User manual
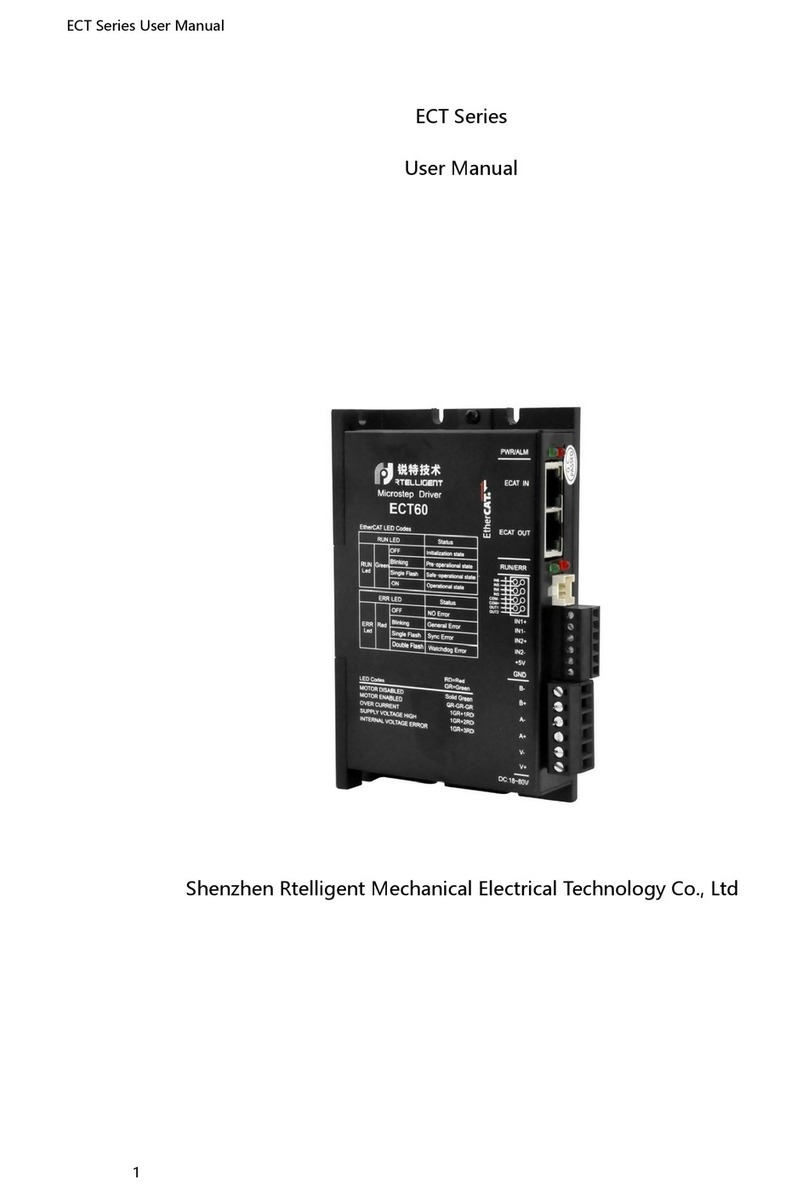
Rtelligent
Rtelligent ECT Series User manual
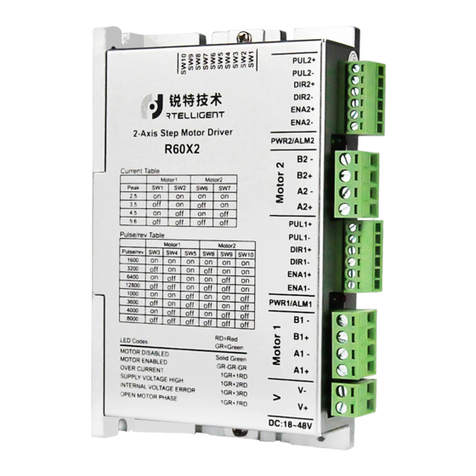
Rtelligent
Rtelligent R60X2 User manual
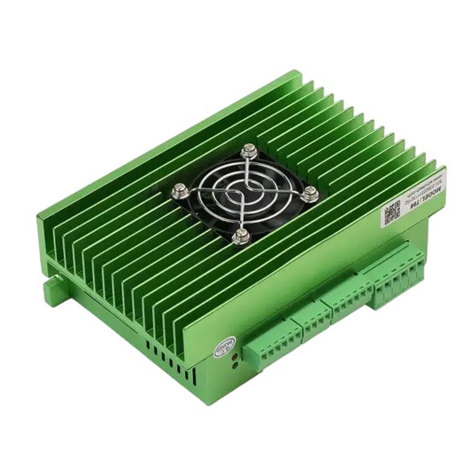
Rtelligent
Rtelligent T86-IO User manual