Ryobi RC-3100B Operation manual

OWNER’S OPERATING MANUAL
BELT DRIVEN COMPRESSOR
MODEL RC-3100B
KEEP THIS MANUAL FOR FUTURE REFERENCE
Your new compressor has been engineered and manufactured to Ryobi’s high
standard of dependability, ease of operation and operator safety. Properly cared
for, it will give you years of rugged, trouble free performance. If you use your
compressor properly and only for what it is intended, you will enjoy years of
safe, reliable service.
SPECIFICATIONS
Voltage...................................................................................................230V~50Hz
R
Intermittent duty............................................................................................S3 75%
ated power........................................................................................ 2.2kW/3.0HP
Receiver capacity...............................................................................................100l
Type.....................................................................................................Oil lubricated
Free air delivery (FAD)................................................................................365l/min
Oil type.........................................................................................................SAE-30
Oil capacity......................................................................................................500ml
CFM...................................................................................................................12.9
Working pressure.................................................................................10bar/145psi
No load speed...........................................................................................1375min-1
Sound pressure level.......................................................... LpA71.5dB(A),k=3dB(A)
Sound power level............................................................. LWA91.5dB(A),k=3dB(A)
Net weight......................................................................................................59.2kg
THANK YOU FOR BUYING A RYOBI
BELT DRIVEN COMPRESSOR
CAUTION: Carefully read through this entire owner’s
manual, paying close attention to the general
safety rules and rules for safe operation,
before using.
1

2
IMPORTANT SAFETY INSTRUCTIONS
The purpose of safety rules is to attract your
attention to possible dangers. The safety symbols
and the explanations with them, require your
careful attention and understanding. The safety
warnings do not by themselves eliminate any
danger. The instruction or warnings they give are
not substitutes for proper accident prevention
measures.
SAFETY ALERT SYMBOL. Indicates
caution or warning. May be used in
conjunction with other symbols or
pictures.
Failure to obey a safety warning can result in
serious injury to yourself or to others. Always follow
the safety precautions to reduce the risk of fire,
electric shock and personal injury.
Do not attempt to operate this tool until you have
read thoroughly and completely understood the
safety rules, etc. contained in this manual. Failure
to comply can result in accidents involving fire,
electric shock or serious personal injury. Save this
Owners Operating Manual and review it frequently
for continual safe operation and for instructing
others who may use this tool.
APPLICATIONS
Air compressors are utilized in a variety of air
system applications. Match hoses, connectors, air
tools, and accessories to the capabilities of the air
compressor.
SPECIFIC SAFETY INSTRUCTIONS
WARNING. If not used and maintained
correctly this compressor when used with
some pneumatic tools can cause serious
injury and death. Before attempting to operate this
machine, it is important that you read, understand
and follow these instructions very carefully. They
are designed for the safety of yourself and others
ensuring a long and trouble free service life from
your machine. If not used correctly and as detailed
in these instructions pneumatic tools can be
dangerous. This product can cause injury to the
operator and others.
The warnings and safety instructions must be
followed to ensure reasonable safety and efficiency
in using this product.
NOTE: The operator is responsible for following the
warnings and safety instructions in this manual and
on the product.
Ensure that this compressor is disconnected from
the mains supply when not in use and the air
receiver fully discharged before servicing,
lubricating or making adjustments and when
changing accessories. Always switch ON and OFF
using the ON/OFF switch on the compressor
before switching OFF at the mains supply.
WARNING. When spraying paint or
cleaning agents the fine mist produced
could ignite. When performing this type
of operation the compressor must be a minimum of
4 Metres away from the work area. Do not smoke
and keep naked flames and other sources of
ignition well away from the work area. Make sure
that the area in which you are working has good
ventilation and protect your nose and mouth with a
suitable face mask. Always check the safety data
sheets for substances being sprayed & ensure
manufacturers instructions are followed.
Protect yourself. Goggles will protect your eyes
from flying particles.
These compressors produce noise levels in excess
of 70dB(A). Persons working near the compressor
must be supplied with ear protection.
Drain tanks of moisture after each day’s use. If unit
will not be used for a while, it is best to leave drain
valve open until such time as it is to be used. This
will allow moisture to completely drain out and help
prevent corrosion on the inside of tanks.
This air compressor must be used in a suitable
environment. There must be adequate ventilation,
the ambient temperature must be +5/+40°C. The
workingareamustbefreefromdust,acidvapour,
explosive gasses and flammable materials.
Compressed air can be potentially dangerous when
not used correctly. Do not exceed the maximum
rated air pressure for the accessory. Do not direct
compressed air at yourself, any other person or
animals. Do not direct any liquid or any other
material that is being sprayed by yourself towards
any other person or animals.
Only use hoses and connectors designed for use
with compressed air. The maximum working
pressure of hoses and connectors must be higher
than the maximum working pressure of the com-
pressor. Do not attempt to move the compressor by
pulling on the air hose.

3
IMPORTANT SAFETY INSTRUCTIONS
This compressor is designed for tyre inflation, the
operation of pneumatic tools, spray painting and
spraying non-corrosive cleaning agents. Do not use
this compressor for filling cylinders for breathing or
diving apparatus. Compressed air from this
compressor must not be used for pharmaceutical,
food or health applications.
When spraying flammable liquids such as paint and
non-corrosive cleaning agents the distance
between the compressor and the work area must
be a minimum of 4 metres. When spraying liquids
always wear a suitable face mask designed for
protection against the liquid being sprayed. Always
wear approved safety glasses.
Do not attempt to modify the compressor or any
pneumatic tools in any way. Use only accessories
and pneumatic tools that are rated for the capacity
of the compressor. Never leave the compressor
pressurised.
Always transport the compressor by lifting or
pulling it with the appropriate grips or handles.
Do not insert your fingers or other objects inside
the motor housing to avoid physical damage or
damage to the compressor.
If any part of the compressor is damaged, it should
be carefully checked to determine that it will
operate correctly and perform its intended function.
Check for the alignment of parts, damage to parts,
air leaks and any other conditions that may affect
its operation. A guard or any other part that is
damaged or defective should be properly repaired
or replaced by an authorised service centre.
Defective pressure switches must be replaced prior
to further use of the compressor.
WARNING. This compressor must be
connected to a power socket that is
safeguarded by a suitable circuit breaker
or fuse.
To reduce the risk of electric shock, do not expose
to rain. Store indoors.
Inspect tanks yearly for rust, pin holes, or other
imperfections that could cause it to become unsafe.
Never weld or drill holes in the air tanks.
Only use recommended parts. To avoid the risk of
bursting, only hoses with a rated pressure of 10
bar, or more should be used. Never attempt to re-
pair faulty hoses.
Avoid kinking or trapping the air hose. Always
replace faulty hoses - never attempt a repair if a
leak is detected.
Make sure the hose is free of obstructions or
snags. Entangled or snarled hoses can cause loss
of balance or footing and may become damaged.
Do not operate this air compressor if it does not
contain a legible warning label.
Always disconnect the air supply and power supply
before making adjustments, servicing a product, or
when a product is not in use.
Make sure your extension cord is in good condition.
When using an extension cord, be sure to use one
heavy enough to carry the current your product will
draw. A wire gauge size (A.W.G.) of at least 14 is
recommended for an extension cord 25 feet (7.6m)
or less in length. A cord exceeding 50 feet (15.2m)
is not recommended. If in doubt, use the next
heavier gauge. The smaller the gauge number, the
heavier the cord. An undersized cord will cause a
drop in line voltage resulting in loss of power and
overheating.
Never store a tool with air connected. Storing the
tool with air connected can result in unexpected
firing and possible serious personal injury.
Protect your lungs. Wear a face or dust mask if the
operation is dusty. Following this rule will reduce
the risk of serious personal injury.
Keep the motor vent clear and free from dust, wipe
regularly to maintain an adequate supply of clean
air to the air compressor.
If the power supply cord is damaged, it must be
replaced only by the manufacturer or by an
authorized service center to avoid risk.
SAVE THESE INSTRUCTIONS
1) WORK AREA
a) Keep your work area clean and well lit.
Cluttered benches and dark areas invite
accidents. Floor must not be slippery from wax
or dust.
b) Do not operate air compressors in explosive
atmospheres, such as in the presence of
flammable liquids, gases, or dust. Power
tools create sparks which may ignite the dust or
fumes.

4
IMPORTANT SAFETY INSTRUCTIONS
c) Keep bystanders, children, and visitors
away while operating an air compressor.
Distractions can cause you to lose control.
d) Operate air compressor in an open area at
least50cmawayfromanywallorobjectthat
could restrict the flow of fresh air to
ventilation openings.
2) ELECTRICAL SAFETY
a) Avoid body contact with grounded surfaces
such as pipes, radiators, ranges, and
refrigerators. There is an increased risk of
electric shock if your body is grounded.
b) Don’t expose air compressors to rain or wet
conditions. Water entering an air compressor
will increase the risk of electric shock.
c) Do not abuse the cord. Never use the cord
to carry the air compressor or pull the plug
from an outlet. Keep cord away from heat,
oil, sharp edges, or moving parts. Replace
damaged cords immediately. Damaged cords
increase the risk of electric shock.
d) When operating an air compressor outside,
use an outdoor extension cord marked
“W-A” or “W”. These cords are rated for
outdoor use and reduce the risk of electric
shock.
3) PERSONAL SAFETY
a) Eye protection which conforms to ANSI
specifications and provides protection
against flying particles both from the
FRONT and SIDE should ALWAYS be worn
by the operator and others in the work area
when loading, operating, or servicing this
product. Eye protection is required to guard
against flying fasteners and debris, which could
cause severe eye injury.
b) The employer and/or user must ensure that
proper eye protection is worn. We
recommend a Wide Vision Safety Mask for use
over eyeglasses or standard safety glasses
that provide protection against flying particles
both from the front and side. Always use eye
protection which is marked to comply with
ANSI Z87.1.
c) Additional safety protection will be required
in some environments. For example, the
working area may include exposure to a noise
level which can lead to hearing damage. The
employer and user must ensure that any
necessary hearing protection is provided and
used by the operator and others in the work
area. Some environments will require the use
of head protection equipment. When required,
the employer and user must ensure that head
protection marked to comply with ANSI Z89.1 is
used.
d) Stay alert, watch what you are doing, and
use common sense when operating the air
compressor. Do not use product while tired
or under the influence of drugs, alcohol, or
medication. A moment of inattention while
operating an air compressor may result in
serious personal injury.
e) Dress properly. Do not wear loose clothing
or jewellery. Contain long hair. Keep your
hair, clothing, and gloves away from moving
parts. Loose clothes, jewellery, or long hair can
be caught in moving parts.
f) Do not overreach. Keep proper footing and
balance at all times. Proper footing and
balance enables better control of the product in
unexpected situations.
g) Use safety equipment. Always wear eye
protection. Dust mask, nonskid safety shoes,
hard hat, or hearing protection must be used
for appropriate conditions.
h) Do not use on a ladder or unstable support.
Stable footing on a solid surface enables better
control of the air compressor in unexpected
situations.
4) AIR COMPRESSOR USE AND CARE
a) Do not exceed the pressure rating of any
component in the system.
b) Protect material lines and air lines from
damage or puncture. Keep hose and power
cord away from sharp objects, chemical spills,
oil, solvents, and wet floors.
c) Check hoses for weak or worn condition
before each use, making certain all
connections are secure. Do not use if defect
is found. Purchase a new hose or notify an
authorized service center for examination or
repair.

5
SPECIFIC SAFETY RULES
d) Release all pressures within the system
slowly. Dust and debris may be harmful.
e) Store idle air compressors out of the reach
of children and other untrained persons. Air
compressors are dangerous in the hands of
untrained users.
f) Maintain air compressors with care. Follow
maintenance instructions. Properly maintained
products are easier to control.
g) Check for misalignment or binding of
moving parts, breakage of parts, and any
other condition that may affect the
product’s operation. If damaged, have the
air compressor serviced before using. Many
accidents are caused by poorly maintained
products.
h) Keep the exterior of the air compressor dry,
clean, and free from oil and grease. Always
use a clean cloth when cleaning. Never use
brake fluids, gasoline, petroleum-based
products, or any strong solvents to clean the
unit. Following this rule will reduce the risk of
deterioration of the enclosure plastic.
5) SERVICE
a) When servicing a product, use only
identical replacement parts. Follow
instructions in the Maintenance section of
this manual. Use of unauthorized parts or
failure to follow Maintenance instructions may
create a risk of injury.
b) Service must be performed only by qualified
repair personnel. Service or maintenance
performed by unqualified personnel may result
in a risk of injury.
c) Disconnect power supply, open drain valve
to decompress tanks and allow water to
drain, and allow air compressor to become
cool to the touch before servicing. Turn
pressure regulator knob fully counterclockwise
after shutting off air compressor.
ELECTRICAL
ELECTRICAL CONNECTION
This product is powered by a precision-built electric
motor. It should be connected to a power supply
that is 230 V, AC only (normal household current),
50 Hz. Do not operate this product on direct current
(DC). A substantial voltage drop will cause a loss of
power and the motor will overheat. If the product
does not operate when plugged into an outlet,
double check the power supply.
GROUNDING INSTRUCTIONS
This product must be grounded. In the event of a
malfunction or breakdown, grounding provides a
path of least resistance for electric current to
reduce the risk of electric shock. This product is
equipped with an electric cord having an
equipment-grounding conductor and a grounding
plug. The plug must be plugged into a matching
outlet that is properly installed and grounded in
accordance with all local codes and ordinances.
Do not modify the plug provided. If it will not fit the
outlet, have the proper outlet installed by a
qualified electrician.
WARNING. Improper installation of the
grounding plug is liable to result in a risk
of electric shock. When repair or
replacement of the cord is required, do not connect
the grounding wire to either flat blade terminal. The
wire with insulation having an outer surface that is
green with or without yellow stripes is the
grounding wire.
Check with a qualified electrician or service
personnel if the grounding instructions are not
completely understood, or if in doubt as to whether
the product is properly grounded.
Repair or replace a damaged or worn cord
immediately.
This product is for use on a nominal 230 V circuit
and has a grounding plug. Only connect the
product to an outlet having the same configuration
as the plug. Do not use an adaptor with this
product.
WARNING! FILL WITH COMPRESSOR OIL
BEFORE USING. RUNNING THE
COMPRESSOR WITH NO OIL OR LOW OIL
VOIDS WARRANTY

6
1. Reset button
2. On/Off pressure switch
3. Air outlet pressure regulator
4. Air outlet quick release connector (regulated)
5. Transportation handle
6. Air outlet pressure gauge
7. Air receiver pressure gauge
8. Rubber foot x 2
9. Wheel x 2
10. Drain valve
11. Air receiver tank
12. Oil drain plug
13. Dipstick
14. Air filter
15. Safety valve
16. Air outlet pressure regulator lock ring
DESCRIPTION
11
23
8
9
4
6
7
5
14
13
10
1
12
15
16

7
UNPACKING
CAUTION. This packaging contains
sharp objects. Take care when
unpacking. Remove the machine,
together with the accessories supplied, from the
packaging. Check carefully to ensure that the
machine is in good condition and account for all the
accessories listed in this manual. Also make sure
that all the accessories are complete.
If any parts are found to be missing, the machine
and its accessories should be returned together in
their original packaging to the retailer. Do not throw
the packaging away, keep it safe throughout the
guarantee period, then recycle if possible,
otherwise dispose of it by the proper means. Do
not let children play with empty plastic bags due to
the risk of suffocation. Take care when lifting the
compressor from the packaging.
CAUTION. Do not lift the compressor by
the pressure regulator. To prevent injury,
get assitance when lifting or moving the
compressor. This unit weighs 59.2kg.
ASSEMBLY
PACKING CONTENTS
• Belt driven compressor
• Wheels x 2
• Wheel fixings (bolt, nut) x 2
• Rubber foot x 2
• Rubber foot fixings (bolt, nut) x 2
• Dipstick
• Operator’s Manual
WARNING. If any parts are damaged or
missing, do not operate this product until
the parts are replaced. Use of this
product with damaged or missing parts
could result in serious personal injury.
WARNING. Do not connect to power
supply until assembly is complete.
Failure to comply could result in
accidental starting and possible serious
personal injury.
WARNING. Do not attempt to modify this
product or create accessories not
recommended for use with this product.
Any such alteration or modification is
misuse and could result in a hazardous
condition leading to possible serious
personal injury.
FITTING THE WHEELS
Fit the two transportation wheels to either side of
the compressor as shown in Fig.1 using a spanner
(not supplied).
FITTING THE RUBBER FOOT
To fit a rubber foot locate the bolt provided through
the hole in the rubber foot and hole on the
compressor support bracket (Fig.2). Tighten the nut
with a spanner or socket (not provided) to secure
the rubber foot into position.
Fig. 1
Bolt Wheel Nut
Fig. 2

8
ASSEMBLY
INSTALLING THE DIPSTICK
Remove the plastic shipping plug from the oil fill
hole. Remove the dipstick from the poly bag and
push it into the oil fill hole (Fig 3).
WARNING. You must replace the plastic
shipping plug with the dipstick. Failure
to do so may result in injury.
FILLING THE COMPRESSOR WITH OIL
WARNING. Do not attempt to start the
air compressor without first adding oil to
the crankcase. Serious damage can
result unless filled with oil. The pump is
shipped without oil from the factory. Only
use non-detergent oils since
multi-viscosity motor oils leave carbon
deposits on pump components, thus
reducing performance and compressor
life.
WARNING. Drain the tank to release all
tank air pressure before removing the
dipstick. Be sure the air vent in dipstick
(Fig.3) is free from debris. If air vent
is blocked, pressure can build in
crankcase causing damage to the
compressor and possible personal injury.
Remove the dipstick by twisting it upwards by
hand. Fill the compressor pump with an air
compressor oil such as SAE-30 non-detergent (API
CG/CD Heavy Duty) oil at slow intervals, Fig.4,
until the oil reaches between the minimum and
maximum marks on the dipstick (Fig.3). Take care
not to exceed the maximum mark. Use SAE-10
during extreme winter conditions.
LOCATING THE AIR COMPRESSOR
This compressor should be positioned on a stable,
flat surface (or one with a maximum inclination of
15º), Fig.5. Ensure that it is completely stable.
Do not cover or box in the compressor. Always
position it with good all round ventilation.
MAX
MIN
AIR
VENT
Fig. 3
Fig. 4
15°
Fig. 5

9
ASSEMBLY
MOVING THE AIR COMPRESSOR
Before moving the compressor, switch off and
disconnect it from the mains power supply.
• Always use the handle
• Do not lift by (or put strain on) air taps, valves
or hoses.
• Take care when moving the compressor to
avoid damaging the valves or fittings.
WARNING. When the compressor is
used for spraying paint or spraying
cleaning agents the fine mist produced
could ignite. When performing this type
of operation the compressor must be a
minimum of 4 Metres away from the
work area. Do not smoke and keep
naked flames and other sources of
ignition well away from the work area.
OPERATION
DANGER. Do not disassemble any part
of the compressor with air in tank -
bleed the tank. Failure to depressurize
tank could result in explosion and/or
serious personal injury.
WARNING. Do not allow familiarity with
products to make you careless.
Remember that a careless fraction of a
second is sufficient to inflict severe injury.
WARNING. Always wear eye protection
with side shields marked to comply with
ANSI Z87.1. Failure to do so could result
in objects being thrown into your eyes
resulting in possible serious injury.
WARNING. Do not use any attachments
or accessories not recommended by the
manufacturer of this product. The use of
attachments or accessories not
recommended can result in serious
personal injury.
WARNING. Do not attach any tools to
the open end of the hose until start-up
has been completed.
NOTE. Do not use in an environment that is dusty
or otherwise contaminated. Using the air
compressor in this type of environment may cause
damage to the unit.
NOTE. The wiring to a receptacle and the length of
any extension cords being used play an important
role in the operation of this product. Wiring
intended for lights cannot properly carry an air
compressor motor, and wire that is heavy enough
for a short distance may be insufficient for a greater
distance.
Before using this product, verify your
receptacle is wired appropriately for air compressor
use and the length and gauge of any extension
cord used is sufficient to carry the current of the air
compressor.
BASIC COMPRESSOR OPERATION
Important Note: This manual is provided to allow
the correct assembly and basic safe operation of
the compressor. It must be read in conjunction with
the manual that is supplied with any other
accessory intended for use with this compressor.
For more detailed information on the use of
compressors and accessories, we strongly
recommend that you purchase a good quality
publication, in order to allow you to use this product
to its full potential.
The electric motor drives an air pump which draws
in air from the atmosphere and delivers it into the
air receiver tank through the air receiver tank
supply tube. When the air pressure in the air
receiver tank reaches the operating pressure of 10
Bar the pressure switch operates and switches
OFF the mains supply to the motor. At the same
time the air that is in the pump cylinder, air receiver
tank, supply tube and the pressure switch is
discharged. This depressurises the pump and the
pressure regulating system allowing the pump to
re-start when the air pressure in the air receiver
tank falls below the minimum operating pressure of
8 Bar. The pressure switch is fitted with a delayed
discharge valve which will start the air pump motor.
The pressure relief safety valve is set to operate at
10.5 Bar and is connected directly onto the air
receiver tank and will operate if the set pressure of
10.5 Bar is exceeded should the pressure switch
fail.

10
OPERATION
OVERLOAD PROTECTION
This compressor has a thermal overload device. If
the motor gets too hot, the thermal overload device
cuts the power which prevents damage to the
motor.
If the thermal overload device operates, let the
motor cool down for 5 minutes and push the reset
button.
If you start the compressor and the overload cutout
operates again, stop the compressor and
disconnect from the power supply and have your
compressor examined by a qualified service agent.
SWITCHING ON AND OFF
WARNING. Switching On & Off must be
done using the On/Off switch mounted
on the compressor. Switching the
compressor Off at the mains supply can
damage the motor and will invalidate the
guarantee.
Before switching on the power supply to the
compressor check that the On/Off switch is in the
Off position (pressed in) (Fig.6).
Check that the air outlet pressure regulator is
closed (Fig 7).
Check that the drain valve is closed (Fig.8).
Connect the compressor to a suitable 16A mains
supply. Switch on the compressor by pulling up the
On/Off switch (Fig.9). The compressor will now
start.
When the air receiver tank is pressurised to its
working capacity the compressor will automatically
switch off. When the compressor switches off there
will be the sound of leaking air while the pressure
regulating system is depressurised, this will last for
only a few seconds and is quite normal. Check all
valves and regulators for leaks. Note during
extended periods of use the air receiver tank
supply tube will become hot.
WARNING. Always ensure the switch is
in the OFF position (pressed in) and
the pressure gauge reads zero before
changing air tools or disconnecting the
hose from the air outlet. Failure to do so
could result in possible serious personal
injury.
Fig. 6
Fig. 7
Fig. 8
Fig. 9
Press down
for OFF
Pull up for
ON

11
OPERATION
CONNECTING/DISCONNECTING AIR HOSE
WARNING. Never exceed the air tool’s
pressure rating as recommended by the
manufacturer. When using this air
compressor as an inflation device,
always follow the maximum inflation
guidelines stated by the manufacturer of
the item being inflated.
Make sure the air compressor is off and
unplugged.
Rotate pressure regulator knob fully in the
counter-clockwise direction so that the outlet
pressure is at zero (0) psi.
Connect a hose to the compressor using the hose
to compressor quick release connector (Fig.10).
Make sure to push the air fitting fully into the
coupler until the sleeve springs forward to lock in
place.
When using the regulated air output first determine
the working pressure of the accessory by referring
to the accessory manual. Slowly open the air outlet
pressure regulator (Fig.11) at the same time
observing the air outlet pressure gauge until the
pressure gauge reads the minimum pressure for
the accessory.
Fine adjustments to the air pressure can be made
until the accessory is working at its optimum
performance.
When the correct operating air pressure has been
set, the air outlet pressure regulator can be locked
by tightening the locking ring (Fig.12).
Do not exceed the maximum rated air pressure for
the accessory.
NOTE: Always use the minimum amount of
pressure necessary for your application. Using a
higher pressure than needed will drain air from the
tank more rapidly and cause the unit to cycle on
more frequently.
To disconnect an air hose or an air tool:
Confirm that the outlet pressure is at zero (0) psi.
When disconnecting a hose from the quick release
connector, always firmly hold the fitting end of the
hose.
Push back on the release sleeve on the quick
release connector. With a firm grip, pull out the
quick-connect air fitting that is attached to the quick
release connector, Fig.13.
Fig. 10
Fig. 11
Fig. 12
Fig. 13

12
OPERATION
SAFETY VALVE
Check the operation of the safety valve, under
pressure, daily by pulling the ring as shown in
Fig.14. Air should be released when you pull the
ring and stop when the ring is released.
• If the valve does not operate as described, or
if the valve is stuck, it must be replaced by
qualified service personnel before using the
compressor.
WARNING. Do not remove or attempt to
adjust the safety valve.
DANGER. Do not attempt to tamper with
the safety valve. Anything loosened from
this device could fly up and hit you.
Failure to heed this warning could result
in death or serious personal injury.
DRAINING THE RESERVOIR
CAUTION. It is important to drain the
reservoir before storage to help prevent
tank corrosion.
Switch the air compressor off, by pressing the
On/Off button to the off position (pressed down),
and remove the plug from the mains supply.
Pull the ring on the safety valve to release pressure
until pressure gauge reads less than 20 psi.
Release the ring.
Place a suitable container beneath the compressor
to catch any condensation.
Carefully undo the drain valve nut anti-clockwise
until you hear a hissing noise, this is the reservoir
depressurising (Fig.15).
When the gauge indicates zero and the hissing has
stopped, tighten the drain valve nut again.
OIL CHANGING
Replace the oil after the first 100 hours of
operation and every 300 hours subsequently.
Remember to check the oil level at regular
intervals.
For changing the pump oil, be sure to do the
following:
1. Turn the unit off and unplug the power cord
from the receptacle.
2. Allow the compressor time to cool if it has been
in operation.
3. Open the drain valve to bleed all air from the
tank.
4. Close the drain valve.
5. Remove the dipstick on the pump.
6. Remove the oil drain plug with a box end
wrench or socket. Drain the oil into a suitable
container and dispose of properly. The
compressor may need to be tipped slightly
towards the drain hole to allow all of the oil to
drain.
7. Reattach the oil drain plug.
8. Refill the compressor pump with an air
compressor oil such as SAE-30 non-detergent
(API CG/CD Heavy Duty) oil at slow intervals
until the oil reaches between the minimum and
maximum marks on the dipstick. Take care not
to exceed the maximum mark. Use SAE-10
during extreme winter conditions.
Fig. 14
Fig. 15

13
MAINTENANCE
WARNING. When servicing use only
identical replacement parts. Use of any
other parts may create a hazard or
cause product damage.
WARNING. Always wear eye protection
with side shields marked to comply with
ANSI Z87.1. Failure to do so could result
in objects being thrown into your eyes
resulting in possible serious injury.
WARNING. Before carrying out any
maintenance, always disconnect the
compressor from the mains supply, drain
the air receiver and, if necessary, allow
the machine to cool down before starting
work.
CLEAN THE AIR FILTER (MONTHLY)
The air filter must be examined monthly, more often
in dusty conditions.
Remove the securing bolt and pull the filter from
the compressor, Fig.16.
Unclip the front and rear of the filter and pull out the
filter element, Fig.17.
Clean the filter using a soft brush.
If necessary, the filter can be carefully cleaned in
warm soapy water.
Rinse and let the filter dry completely before
refitting.
If the filter or filter element is damaged, you must
replace it.
Reassemble the filter and refit it to the compressor
using the securing bolt.
CHECK THE NON-RETURN VALVE
(EVERY 6 MONTHS)
If the reservoir pressure decreases for no apparent
reason, it is possible that the non-return valve is
leaking. To check this:
Make sure that the reservoir is not under pressure
and the compressor is switched OFF.
Examine the non-return valve, and replace the
gasket and valve if necessary, Fig.18.
Fig. 16
Fig. 17
Fig. 18
Gasket
Spring
Valve

14
MAINTENANCE
CHECKING THE BELT TENSION
WARNING. Make sure that the
compressor is disconnected from the
electrical supply before checking the
drive belt.
The belt must flex by approximately 10 mm when a
3 Kg load is applied (Fig.19). Reset the tension if
necessary, ensuring that the pulley and flywheel
remain correctly aligned.
GENERAL MAINTENANCE
The compressor must be drained completely by
opening the drain valve. Drain the air receiver tank
after approx. 2 hours of use.
The air filter can be removed for either cleaning or
replacing. Clean the air filter element after every
100 hours of use or if low pressure is experienced.
Replace the air filter after 200 hours of use. Note:
Under no circumstances should the compressor be
operated with the air filter removed.
Cleaning and maintaining the compressor regularly
will give a long and trouble free life.
Before long term storage it is advisable to give the
compressor a thorough clean. This should include
the removal of all fitted accessories. Do not use
any solvents as these can damage plastic parts.
Only use a clean cloth dampened with warm soapy
water. Any metal parts should be given a wipe with
a light machine oil to prevent rusting.
WARNING. Do not at any time let brake
fluids, gasoline, petroleum-based
products, penetrating oils, etc., come in
contact with plastic parts. Chemicals can
damage, weaken or destroy plastIc
which may result in serious personal
injury.
10 mm
3
Kg
Fig. 19
STORAGE
When you have finished using the air
compressor:
• Set the switch to “OFF’ and unplug the cord.
• Be sure to drain the moisture from the air tank.
• Protect the electrical cord and air hose from
damage.
• Store the air compressor in a clean and dry
location away from children.
SERVICE
Now that you have purchased your tool, should a need ever exist of repair or service, simply contact your
nearest Ryobi Authorised Service Centre or other qualified service organistion. Be sure to provide all
pertinent facts when you call or visit.

15
TROUBLESHOOTING
PROBLEM POSSIBLE CAUSE REMEDY
The compressor has
stopped and does not
start.
The compressor does not
reach the set pressure and
overheats easily.
Compressor does not
start.
Air leaking from the non-
return valve when the
compressor is not running.
Air pressure from the
regulator will not adjust.
The compressor is very
noisy and makes a
metallic knocking sound.
Bad electrical connections.
Overload cutout switch has
tripped.
Motor windings burnt out.
Compressor head gasket blown or
valve broken.
The reservoir has already fully
pressurised.
Faulty non-return valve.
The diaphragm within the
regulator body is broken.
Compressor damaged and needs
overhaul.
Check electrical connections. Clean
and tighten if necessary.
Switch off and wait approx 5 minutes.
Press the reset button and switch on
again.
Contact your nearest service agent.
Return the machine to your nearest
service agent.
Open drain valve to expel air.
Compressor should start again when
pressure reduces.
Drain receiver completely of air.
Remove the valve end plug,
Carefully clean the valve seat and the
gasket.
Reassemble.
Replace regulator.
Return the machine to your nearest
service agent.
SYMBOLS
SYMBOL SIGNAL MEANING
DANGER: Indicates an imminently hazardous situation, which, if not avoided, will
result in death or serious injury.
WARNING Indicates a potentially hazardous situation, which, if not avoided, could
result in death or serious injury.
CAUTION Indicates a potentially hazardous situation, which, if not avoided, may result
in minor or moderate injury.
CAUTION (Without Safety Alert Symbol) Indicates a situation that may result in
property damage.

SYMBOLS
16
Safety Alert Symbol Indicates danger, warning or caution. It means attention!!!
Your safety is involved.
Read Your Operator's
Manual
Your manual contains special messages to bring attention
to potential safety concerns as well as operating and
servicing information. Please read all the information
carefully to ensure satisfaction and safe use.
Wear Hearing Protection Hearing protection must be worn when operating this
equipment.
Air and condensation water can burst from the
compressor when the drain plug is removed.
Risk of Bursting
Risk of Electric Shock Hazardous Voltage. Disconnect from power source before
servicing. Do not use in damp conditions.
Hot Surface To reduce the risk of injury or damage, avoid contact with
any hot surface.
Enclosure Alert Do not operate the portable compressor with the doors
or enclosure open.
Unexpected Starting The compressor may start without warning.
Recycle Symbol Waste electrical products should not be disposed of with
household waste. Please recycle where facilities exist.
Check with your Local Authority or retailer for recycling
advice.
CE Marking Conforms to relevant safety standards.
Oil Use SAE-30 non-detergent (API CG/CD Heavy Duty) oil.
To stop the compressor, use the switch located on the
pressure switch body. Never use the main switch or
unplug the compressor.
Do Not Pull Out The
Plug.

17
NOTES

18
NOTES

19
NOTES

Table of contents
Other Ryobi Compressor manuals
Popular Compressor manuals by other brands

EKOM
EKOM DK50 2V/50 Installation, operation and maintenance manual
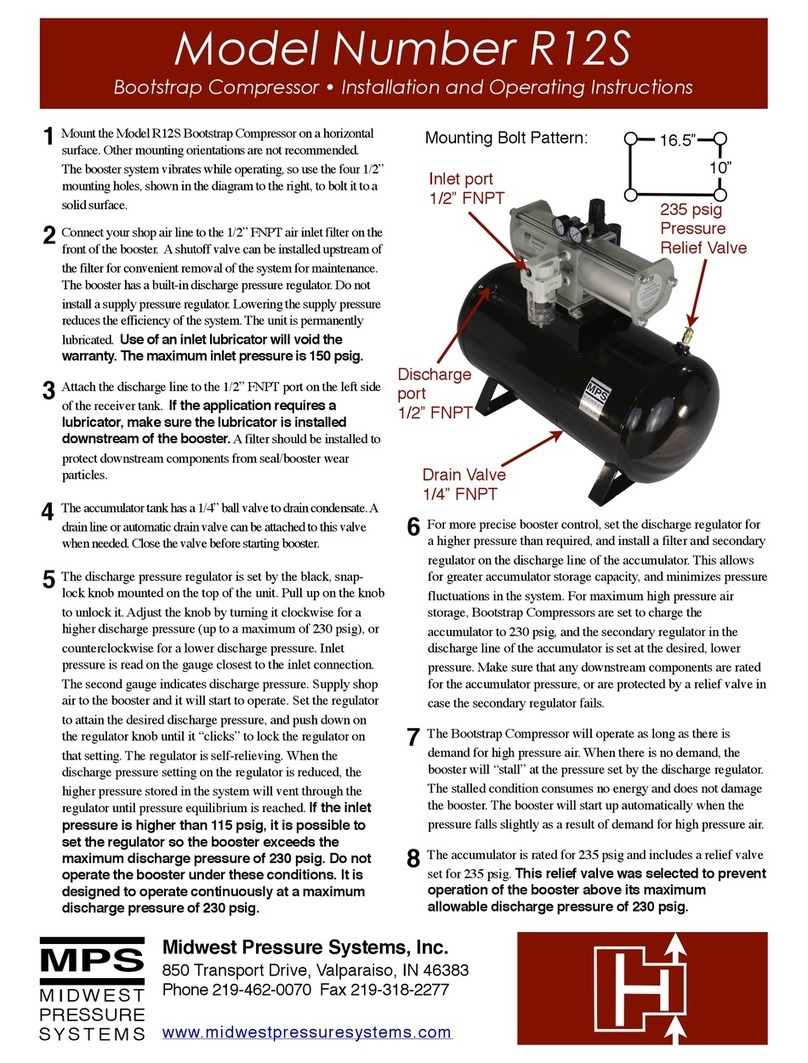
MPS
MPS R12S Installation and operating instructions
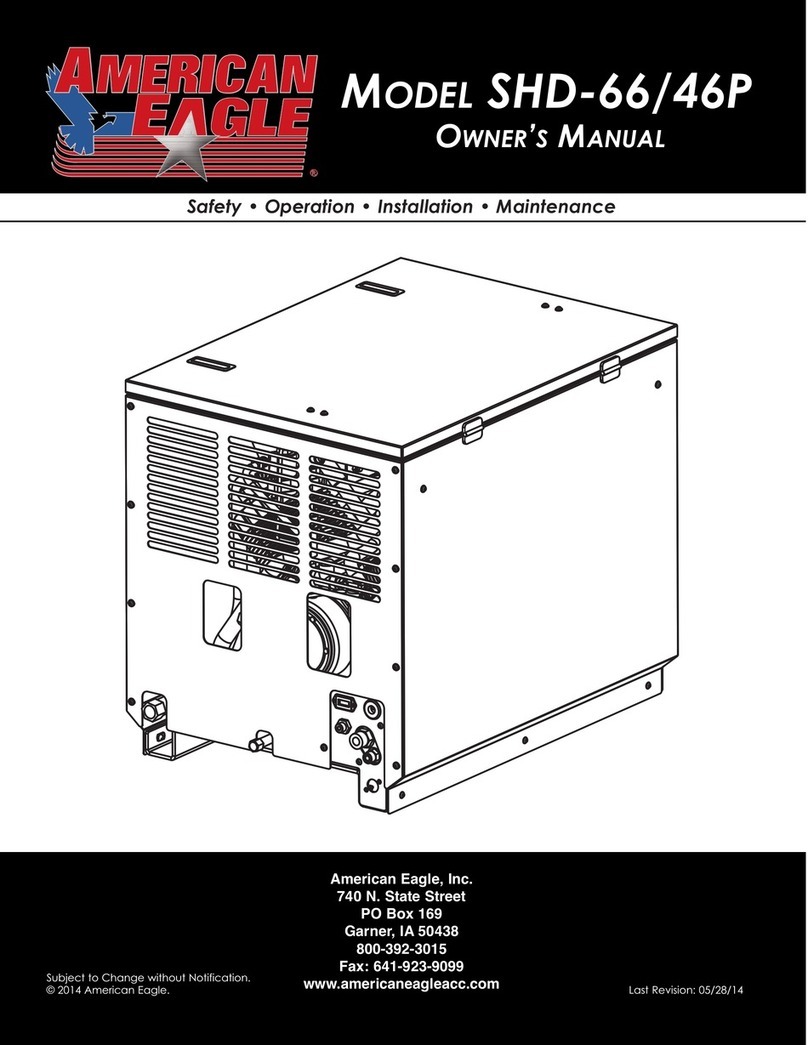
American Eagle
American Eagle SHD-66 owner's manual
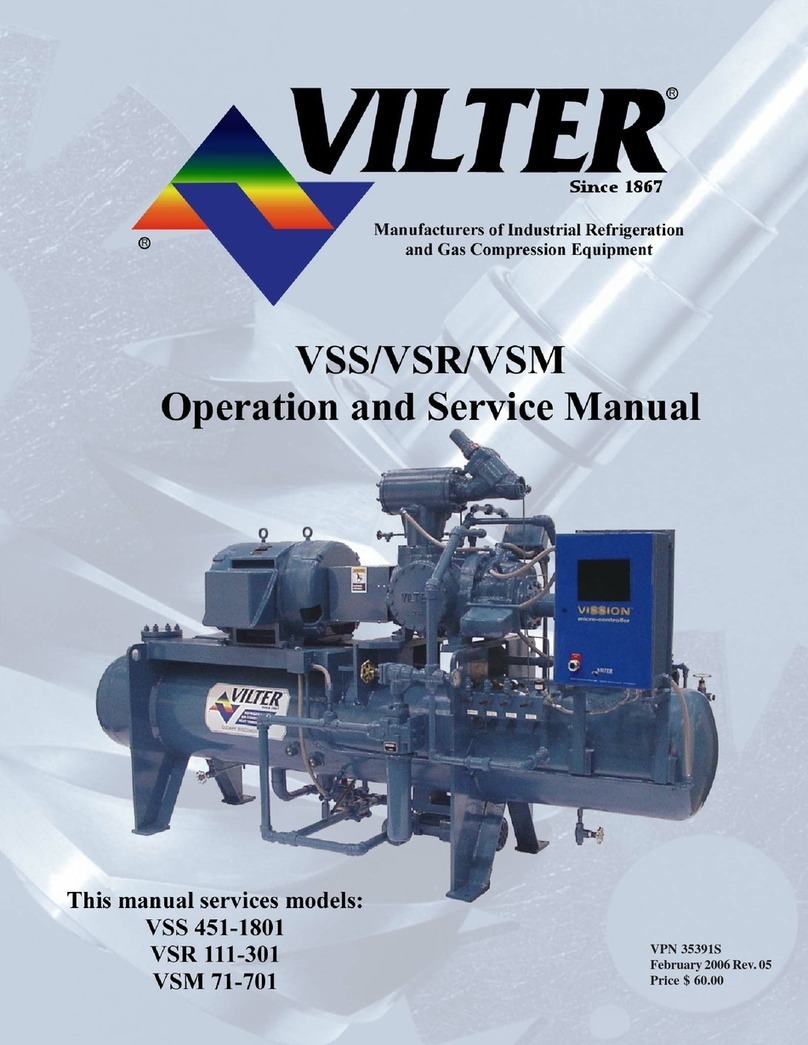
Vilter
Vilter VSS 451-1801 Operation and service manual
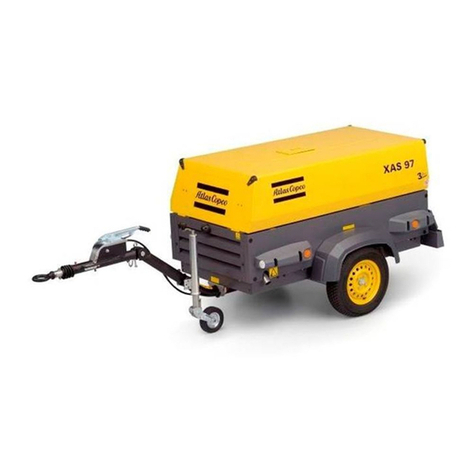
Atlas Copco
Atlas Copco XAS 97 DD instruction manual

PRESONUS
PRESONUS ACP88 Using instructions

Sealey
Sealey SA4050 quick start guide
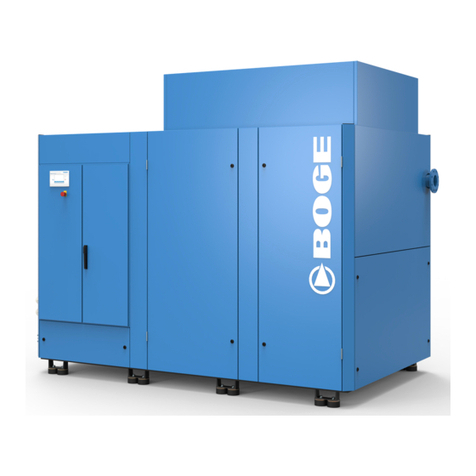
Boge
Boge S Series operating instructions

Invacare
Invacare Venture HomeFill II Owner's operator and maintenance manual
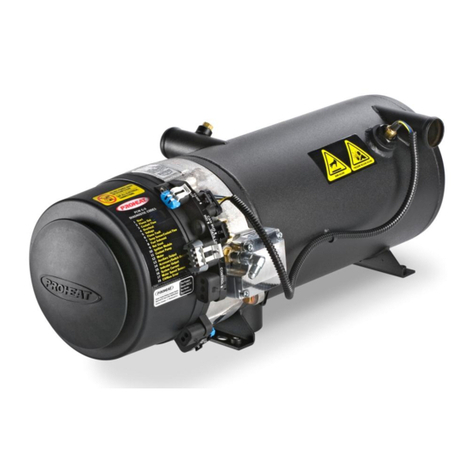
Proheat
Proheat M Series Service bulletin
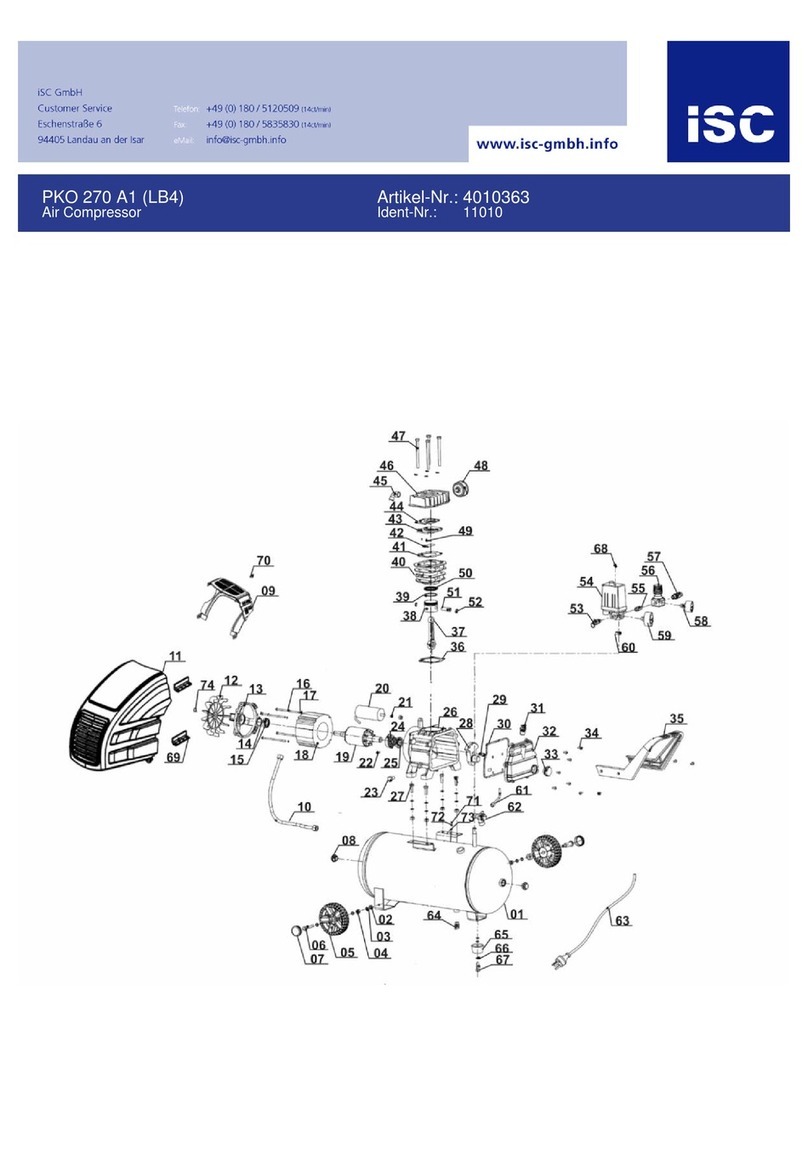
Parkside
Parkside PKO 270 A1 operation and safety notes original operating instructions
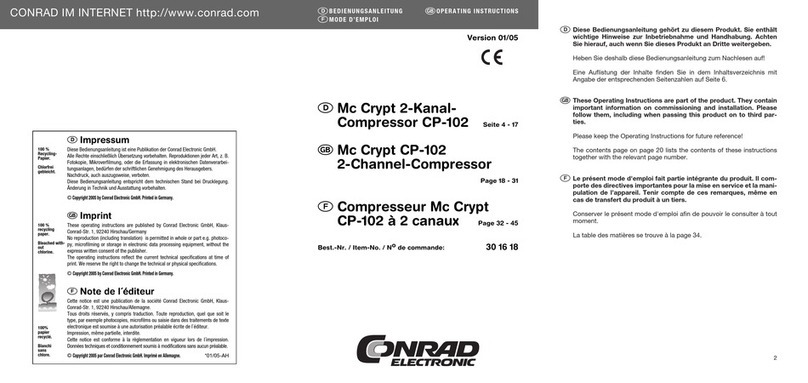
Conrad
Conrad Mc Crypt CP-102 operating instructions