SALUPO MULTIPLUS 1 SA684 Series Manual

INSTRUCTION AND INSTALLATION MANUAL
Direct starting electronic control panel 1 motor for clean water and sewage with display
and general disconnecting switch with door lock.
rev.6 11/01/2023
MULTIPLUS 1
SA684.xx / SA687.xx

INDEX
22
1. General instructions for installing
2. Warnings
3. Application examples
4. Wiring diagrams
4.1 Wiring diagrams SA684.xx
4.2 Wiring diagrams SA687.xx
5. Programming
5.1 Fast programming
5.2 Application cosφ
5.3 Application clean water
5.4 Application sewage
5.5 Application 4-20mAbar
5.6 Application 4-20mA meters
5.7 Advanced programming
6. General functioning of the control panel
6.1 General functioning
6.2 Application cosφ
6.3 Application clean water
6.4 Application sewage
6.5 Application 4-20mA bar
6.6 Application 4-20mA meters
9. Troubleshooting and proposed solutions
8. Data logger
.1 8 Alarm data logger
. 8 2 Event data logger
10. Alarm messages
11. Disposal of electrical & electronic equipment
12. Declaration of conformity CE and UK
13. Warranty certificate
23
23
24
26
27
29
30
30
31
32
28
33
35
35
36
36
37
37
39
40
41
42
42
43
39
7. Motor maintenance 38

ENGLISH
Make sure power supply is protected up to standard depending on application. The power of the
motor has to be within the control panel's limits of use.
Before acting upon anything inside, disconnect power supply. Regulation procedures must be
carried out by qualified personnel. In case protections intervene verify the cause of the problem
before resetting.
The manufacturer is released from all responsibilities for accidents to things or people, which
derive from misuse of the devices by unauthorized personnel or from lack of maintenance
and repair.
Install the control panel in an environment appropriate to its IP65 degree of protection. To fix the
enclosure, use the brackets for the boxes 03-04 and the special predispositions for the remaining
boxes. In order to fix the box, use the appropriate holes which are present or suggested on the
bottom. Pay particular attention to not touching or damaging any components while fixing the box.
When connecting electric cables, follow the wiring diagrams.
When fixing the cables in the terminal board use tools of correct size to avoid damaging the metal
feed clamps and their sockets.
It is the installer' s duty to verify the device after the installation although it has already
undergone regular testing by the manufacturer.
Eliminate whatever metal and/or plastic impurity which could happen to fall inside the box (screws,
washers, dust…).
If necessary substitute the various components only with those having the same characteristics and
components as the originals.
1. GENERAL INSTRUCTIONS FOR INSTALLING
2. WARNINGS
ELECTRIC SHOCKS
Risk of electric shocks if not complied with the requirements.
DANGER
Risk of personal injury and property if not complied with the requirements.
WARNING
Before installing and using the product read this book in all its parts. Installation and maintenance must be
performed by qualified personnel in accordance with current regulations.
The manufacturer will not be held responsible for any damage caused by improper or prohibited use of this
control panel and is not responsible for any damages caused by an incorrect installation or maintenance of the
plant. The use of non-original spare parts, tempering or improper use, make the product warranty null.
Be sure that the power of the motor is within the control panel range.Install the control panel in an environment
appropriate to its IP 65 degree of protection.
WARNING
To operate inside the control panel use tools of correct size to avoid damaging the sockets.
In order to fix the box use the appropriate holes present on the bottom, don't damage internal components and
eliminate any working debris inside the box.
Do not attempt operations when the control panel is open.The control panel must be connected to an efficient
earthing system.
DANGER
Before any intervention ensure that the control panel is disconnected from the electricity supply.
In the case of protections eliminate the cause of the malfunction before the restoration.
3
23

COMPONENTS KEY
3. APPLICATION EXAMPLES
Below are some practical examples of applications that can be implemented with the MULTIPLUS 1
control panel.
24
Float switch for clean water
Level probe
1 INPUT 2 INPUTS
KLIX1
COM
COM
MIN
MAX
KLIX1
G.MIN
COM
2
START/
STOP
COM
MIN
MAX
CLEAN WATER
DRY RUNNING COSφ
KLIX1
COM
MIN
MAX
G.MAX2
G.ALAR
COM
COM
COM
MIN
MIN
MAX
MAX
2 INPUTS1 INPUT 1 INPUT
G.MIN
KLIX1
G.MIN
G.MAX1
G.MAX2
G.ALAR
COM
START/
STOP
ALARM
KLIX1
COM
MIN
MAX
G.MAX2
COM
START/
STOP
COM
MIN
MAX
4

WHITE WATERS BLACK LIQUOR
ENGLISH
COMPONENTS KEY
3. APPLICATION EXAMPLES
Level probe
25
Float switch for clean water
Float switch for sewage
Pressure transducer 4-20mA
Piezoresistive probe 4-20mA
Below are some practical examples of applications that can be implemented with the MULTIPLUS 1
control panel.
4-20mA bar
5
STOP
START
KLIX1
KLIX1
G.MIN
G.MAX1
G.ALAR
G.ALAR
COM
COM
ALARM
START
ALARM
COM
STOP
COM
MIN
MAX
COM
MIN
MAX
TRANSD.
4-20m A
ANALOG
4-20 mA
+
-
6
KLIX1
COM
COM
MIN
MAX
ALARM
ANALOG
4-20 mA
+
-
7
PIEZOR.
4-20m A
G.ALAR
KLIX1
COM
4-20mA meters
SEWAGE

POWER SUPPLY
230 Vac 50/60 Hz
1 2
G.MIN
COM
MIN
COM
MAX
G.MAX1 G.MAX2 G.ALAR
PR.STA PR.EME
KLIX1
COM
N.C.
N.O.
COM
ALARM U V AVV.
MOTOR 1
3 4 5 6 7 8 9 10 14 15 16
SIREN 12V FLASHING
LAMP 12V
12 13
EXPANSION BOARD
+ -
ANALOG
4-20mA
Max 10 mm²
(M4)
0,8Nm
10 mm
Max 4 mm²
(M3)
0,5Nm
9,8 mm
Max 2.5 mm²
(M3)
0,5Nm
8,3 mm
PIEZORESISTIVE LEVEL TRANSMITTER 4-20mA WIRINGPRESSURE TRANSDUCER WIRING
+ BROWN
- WHITE
KEY
1-2 LEVEL PROBES OR MINIMUM FLOAT SWITCH
3-4 LEVEL PROBES OR MAX1 FLOAT SWITCH
5-6 MAX2 FLOAT SWITCH OR START PRESSURE SWITCH
7-8 ALARM FLOAT SWITCH OR EMERGENCY PRESSURE SWITCH
9-10 MOTOR KLIXON
12-13 INPUT 4-20mA
14-15-16 PURE CONTACT ALARM OUTPUT (MAX 5A)
MOTOR
M
1
COMMON
RUNNING
START-UP
4. WIRING DIAGRAMS
4.1 Wiring diagram SA684.xx
L1 N
26
+ RED
- BLUE
CAPACITOR

ENGLISH
1 2
G.MIN
COM
MIN
COM
MAX
G.MAX1 G.MAX2 G.ALAR
PR.STA PR.EME
KLIX1
COM
N.C.
N.O.
COM
ALARM
SIREN 12V FLASHING
LAMP 12V
3 4 5 6 7 8 9 10 14 15 16
R
MOT1
SR S T
SUPPLY
EXPANSION BOARD
+ -
ANALOG
4-20mA
12 13
Max 10 mm²
(M4)
0,8Nm
10 mm
Max 6 mm²
(M4)
2,5Nm
10 mm
Max 2.5 mm²
(M3)
0,5Nm
8,3 mm
L1 L2 L3
U
V
W
M
3
MOTOR
POWER SUPPLY
400 Vac 50/60 Hz
4.2 Wiring diagram SA687.xx
4. WIRING DIAGRAMS
KEY
3-4 LEVEL PROBES OR MAX1 FLOAT SWITCH
1-2 LEVEL PROBES OR MINIMUM FLOAT SWITCH
9-10 MOTOR KLIXON
12-13 INPUT 4-20mA
14-15-16 PURE CONTACT ALARM OUTPUT (MAX 5A)
5-6 MAX2 FLOAT SWITCH OR START PRESSURE SWITCH
7-8 ALARM FLOAT SWITCH OR EMERGENCY PRESSURE SWITCH
PIEZORESISTIVE LEVEL TRANSMITTER 4-20mA WIRINGPRESSURE TRANSDUCER WIRING
27
+ BROWN
- WHITE
+ RED
- BLUE

APPLICATION
COSFI
APPLICATION
COSFI
LANGUAGE
ENGLISH V3.0
LANGUAGE
ENGLISH V3.0
LANGUE
FRANCAISE V3.0
LINGUA
ITALIANO V3.0
APPLICATION
SEWAGE
APPLICATION
CLEAN WATER
APPLICATION
4-20mA bar
APPLICATION
4-20mA metri
PRESSING IT FOR MORE THAN 1s YOU GO OUT
OF THE SETUP AND THE PARAMETERS
ARE STORED IN THE MEMORY
PRESSING IT YOU WILL SEE THE REMAINING PART OF THE PARAMETERS
THAT CAN BE SET ACCORDING TO THE APPLICATION CHOSEN:
COSφ = SEE CHAPTER 5.2
CLEAN WATER = SEE CHAPTER 5.3
SEWAGE = SEE CHAPTER 5.4
4-20mA bar = SEE CHAPTER 5.5
4-20mA metres = SEE CHAPTER 5.6
COSFI < 0.45
ENTER MANUALLY
COSFI > 1.00
ENTER MANUALLY
THE COSφ MEASURED
IS LESS THAN 0.45
(POSSIBLE DRY
RUNNING)
It is used to scroll forward through the setup pages
It is used to increase the value of a parameter
It is used to scroll back through the setup pages
It is used to reduce the value of a parameter
Pressed it allows to enter the selected parameter
Pressed confirms the set value
POSSIBLE ANOMALIES DURING THE AUTO-LEARNING PHASE
}
SETUP PRESS
PAG + MAN 10s +
IGNITION
CONTROL PANEL
AUTO - LEARNING
ENTER TO START
AUTO - LEARN. 0 %
CF 0.80 13.2 A
AUTO - LEARNING
COMPLETED
5.1 Fast programming
5. PROGRAMMING
Pressed it exits the parameter
ON
IN THIS STAGE THE
MOTHERBOARD STARTS
FOR APPROXIMATELY 30s
THE MOTOR RECORDING
THE PARAMETERS
AUTOMATICALLY
NO LOAD MAXIMUM CURRENT
> -- A
THE MOTHERBOARD
DOES NOT DETECT
ANY CONNECTED
MOTOR
THE MOTHERBOARD HAS
CORRECTLY PERFORMED
THE AUTO-LEARNING
PROCEDURE
THE ABSORBED
CURRENT EXCEEDS
THE MAXIMUM
ALLOWED THRESHOLD
THE COSφ MEASURED
IS MORE THAN 1.00
(COSφ READING
ANOMALY)
28

ENGLISH
5.2 Application cosφ
MINIMUM COSFI
AUT. 0.68
MINIMUM COSFI
MAN. 0.68
MAN. IT INDICATES THAT
THE COSφ VALUE HAS
BEEN SET MANUALLY
AUT. INDICATES THAT THE COS VALUEφ
HAS BEEN SET WITH AUTO-LEARNING
IT IS USED TO SET MANUALLY THE
COSφ VALUE UNDER WHICH
THE PUMP RUNS DRY
DRY RUN DELAY
4 s
DRY RUN DELAY
4 s
IT IS USED TO SET THE
INTERVENTION DELAY FOR
DRY RUNNING PROTECTION
RANGE 0.04 ÷ 0.99
RANGE 1 ÷ 10s
EXTERNAL COMMAND
1 INPUT
EXTERNAL COMMAND
1 INPUT
IN 1 INPUT MODE THE EXTERNAL COMMAND IS:
OFF G.MIN OPEN (DISABLE MOTOR)
ON G.MIN CLOSED (ENABLE MOTOR)
EXTERNAL COMMAND
2 INPUTS
IN 2 INPUTS MODE THE EXTERNAL COMMAND IS:
OFF G.MIN AND G.MAX CLOSED (DISABLE MOTOR)
ON G.MIN AND G.MAX OPEN (ENABLE MOTOR)
EXTERNAL COMMAND
OFF
IN OFF MODE THE MOTHERBOARD
EXCLUDES THE CONTROL ON
THE EXTERNAL COMMAND
5.1
5. PROGRAMMING
29
THE MOTHERBOARD AUTOMATICALLY CALCULATES
THE WAITING FILLING TIME IN FUNCTION OF THE
WATER PRESENT IN THE WELL
IT IS USED TO SET A FILLING WAITING TIME WHICH INTERVENES EVERY TIME
THE MOTHERBOARD DETECTS A DRY RUNNING CONDITION
OFF EXCLUDES THE
WAITING FILLING
RANGE 1min ÷ 99h 59min
THIS SCREEN
IS DISPLAYED ONLY IF
THE WAITING FILLING
IS SET TO AUTOMATIC
IT SERVES
TO RESET THE FILLING
WAITING TIME
WAITING FILLING
ENTER TO RESET
WAITING FILLING
RESET
WAITING FILLING
AUTOMATIC
WAITING FILLING
AUTOMATIC
WAITING FILLING
0 h 30 min
WAITING FILLING
OFF
PRESSING IT FOR MORE
THAN 1s YOU GO OUT
OF THE SETUP AND THE
PARAMETERS ARE
STORED IN THE MEMORY
PRESSED IT DISPLAYS
THE REMAINING PART
OF THE PARAMETERS
SEE CHAPTER 5.5

30
5.3 Application clean water
5.4 Application sewage
5. PROGRAMMING
5.1
5.1
PROBES SENSITIV.
1Okohm
IT IS USED TO SET
MANUALLY THE PROBES
SENSITIVITY VALUE
RANGE 0 ÷ 100kohm
PROBES SENSITIV.
1Okohm
PROBES SENSITIV.
1Okohm
IT IS USED TO SET
MANUALLY THE PROBES
SENSITIVITY VALUE
RANGE 0 ÷ 100kohm
PROBES SENSITIV.
1Okohm
BY PRESSING IT YOU RETURN
TO THE FIRST SETUP SCREEN;
SEE CHAPTER 5.7
BY PRESSING IT YOU RETURN
TO THE FIRST SETUP SCREEN;
SEE CHAPTER 5.7
PRESSING IT FOR MORE THAN
1s YOU GO OUT OF THE SETUP
AND THE PARAMETERS ARE
STORED IN THE MEMORY
PRESSING IT FOR MORE THAN
1s YOU GO OUT OF THE SETUP
AND THE PARAMETERS ARE
STORED IN THE MEMORY
EXTERNAL COMMAND
1 INPUT
EXTERNAL COMMAND
1 INPUT
EXTERNAL COMMAND
2 INPUTS
IN 2 INPUTS MODE THE
EXTERNAL COMMAND IS:
OFF G.MIN AND G.MAX CLOSED
(DISABLE MOTOR)
ON G.MIN AND G.MAX OPEN
(ENABLE MOTOR)
IN 1 INPUT MODE THE
EXTERNAL COMMAND IS:
OFF G.MIN OPEN
(DISABLE MOTOR)
ON G.MIN CLOSED
(ENABLE MOTOR)

ENGLISH
5.5 Application 4-20mA bar
TRANSDUCER
10 bar
TRANSDUCER
10 bar
TRANSDUCER
16 bar
IT IS USED TO SET THE FULL
SCALE OF THE TRANSDUCER
USED
START PRESSURE
2.5 bar
START PRESSURE
2.5 bar
IT IS USED TO SET THE
PRESSURE REQUIRED TO
START THE MOTOR
START DELAY
OFF
START DELAY
OFF
IT IS USED TO SET THE DELAY
FOR STARTING THE MOTOR WHEN
THE SYSTEM PRESSURE
DROPS BELOW THE
START PRESSURE
RANGE 1min ÷ 99h 59min
STOP PRESSURE
3.0 bar
STOP PRESSURE
3.0 bar
IT IS USED TO SET THE
NECESSARY PRESSURE
ABOVE WHICH
THE MOTOR STOPS
TRANSDUCER
25 bar
OFF EXCLUDES THE START DELAY
START DELAY
0h 2 min
MINIMUM PRESSURE
OFF
MINIMUM PRESSURE
OFF
IT IS USED TO SET THE REQUIRED
PRESSURE BELOW WHICH THE
MOTOR STOPPED. AT THE MOTOR
STARTING THIS PARAMETER IS
BYPASSED FOR 1 MINUTE
MINIMUM PRESSURE
0.5 bar
OFF EXCLUDES THE
MINIMUM PRESSURE
TRANSDUCER 10bar: 0.1 ÷ 7.9bar
TRANSDUCER 16bar: 0.1 ÷ 13.9bar
TRANSDUCER 25bar: 0.1 ÷ 22.9bar
TRANSDUCER 10bar: 0.2 ÷ 8bar
TRANSDUCER 16bar: 0.2 ÷ 14bar
TRANSDUCER 25bar: 0.2 ÷ 23bar
TRANSDUCER 10bar: 0.1 ÷ 7.8bar
TRANSDUCER 16bar: 0.1 ÷ 13.8bar
TRANSDUCER 25bar: 0.1 ÷ 22.8bar
5. PROGRAMMING
12
5.1
31
PROBES SENSITIV.
1Okohm
IT IS USED TO SET
MANUALLY THE PROBES
SENSITIVITY VALUE
RANGE 0 ÷ 100kohm
PROBES SENSITIV.
1Okohm
BY PRESSING IT YOU RETURN
TO THE FIRST SETUP SCREEN;
SEE CHAPTER 5.7
PRESSING IT FOR MORE THAN
1s YOU GO OUT OF THE SETUP
AND THE PARAMETERS ARE
STORED IN THE MEMORY

5.6 Application 4-20mA meters
PROBE 4-20 mA
2.5 m
PROBE 4-20 mA
2.5 m
IT IS USED TO SET THE FULL
SCALE OF THE PROBE USED
MINIMUM LEVEL
0.50 m
MINIMUM LEVEL
0.50 m
IT IS USED TO SET THE WATER LEVEL
BELOW WHICH THE MOTHERBOARD
TURNS OFF THE MOTOR
MAXIMUM LEVEL
1.00 m
MAXIMUM LEVEL
1.00 m
RANGE 0.10 ÷ 24.95m
ALARM LEVEL
1.00 m
ALARM LEVEL
1.00 m
IT IS USED TO SET THE WATER
LEVEL ABOVE WHICH THE
MOTHERBOARD ENABLES
THE ALARM OUTPUT
RANGE 1.0 ÷ 25.0m RANGE 0.05 ÷ 24.9m
IT IS USED TO SET THE WATER LEVEL
ABOVE WHICH THE MOTHERBOARD
STARTS THE MOTOR
RANGE 0.15 ÷ 25m
5.1
5. PROGRAMMING
PRESSING IT FOR MORE THAN 1s
YOU GO OUT OF THE SETUP AND
THE PARAMETERS ARE STORED
IN THE MEMORY
PRESSED IT DISPLAYS THE
REMAINING PART OF THE
PARAMETERS SEE CHAPTER 5.5
32

ENGLISH
5.7 Advanced programming
MAXIMUM CURRENT
AUT. 16.5 A
MAXIMUM CURRENT
MAN. 16.5 A
IT IS USED TO SET THE
OVERLOAD MAXIMUM CURRENT
OF THE MOTOR
RANGE 0.5 ÷ 36.0A (SA687.xx)
CURRENT DELAY
4 s
CURRENT DELAY
4 s
IT IS USED TO SET THE DELAY
OF THE INTERVENTION FOR THE
PROTECTION OF THE CURRENT
RANGE 1 ÷ 8s
AUT. INDICATES THAT THE MAXIMUM
CURRENT VALUE HAS BEEN SET WITH
THE AUTO-LEARNING
MAN. INDICATES THAT THE
MAXIMUM CURRENT VALUE
HAS BEEN SET MANUALLY
RANGE 0.5 ÷ 18.0A (SA684.xx)
MINIMUM CURRENT
AUT. 9.9 A
MINIMUM CURRENT
MAN. 9.9 A
RANGE 0.5 ÷ 33.0A (SA687.xx)
RANGE 0.5 ÷ 15.0A (SA684.xx)
IT IS USED TO SET THE
MINIMUM CURRENT
OF THE MOTOR
MAN.INDICATES THAT THE
MINIMUM CURRENT VALUE
HAS BEEN SET MANUALLY
MINIMUM CURRENT
OFF
AUT. INDICATES THAT THE MINIMUM
CURRENT VALUE HAS BEEN SET
WITH THE AUTO-LEARNING,
EXCLUDING THE COSφ APPLICATION
5.1
5. PROGRAMMING
OFF EXCLUDES THE CONTROL
ON THE MINIMUM CURRENT
33
OFF EXCLUDES THE MAX
STARTS CONTROL
IT IS USED TO SET THE MAXIMUM
NUMBER OF STARTS PER HOUR
MAX STARTS PER
HOUR OFF
MAX STARTS PER
HOUR OFF
MAX STARTS PER
HOUR 10
MINIMUM CURRENT
RESET OFF
OFF EXCLUDES THE
MINIMUM CURRENT RESET
IT IS USED TO SET THE
RESET TIME ON THE
MINIMUM CURRENT
RANGE 1min ÷ 99h 59min
MINIMUM CURRENT
RESET OFF
MINIMUM CURRENT
RESET 0 h 5 m
N.B.: ABSENT ON
COS APPLICATIONφ
RANGE 1 ÷ 30
MOTOR TEST
OFF
MOTOR TEST
48h
MOTOR TEST
OFF
OFF EXCLUDES THE
MOTOR TEST
IT IS USED TO SET THE
DELAY BETWEEN EACH
ACTIVATION OF THE MOTOR TEST
RANGE 0FF - 24 - 48 - 72 - 96h

SUPPLY MAINS
WAITING OFF
OFF EXCLUDES THE
MAINS SUPPLY WAITING
SUPPLY MAINS
WAITING 1 min
IT IS USED TO SET THE
MAINS SUPPLY WAITING
RANGE 1 ÷ 30min
SUPPLY MAINS
WAITING OFF
MINIMUM VOLTAGE
207 V
MINIMUM VOLTAGE
207 V
IT IS USED TO SET THE
MINIMUM OPERATING VOLTAGE
OF THE MOTOR
RANGE 198 ÷ 220V (SA684.xx)
RANGE 340 ÷ 380V (SA687.xx)
MAXIMUM VOLTAGE
253 V
MAXIMUM VOLTAGE
253 V
RANGE 230 ÷ 253V (SA684.xx)
RANGE 400 ÷ 440V (SA687.xx)
MINIMUM VOLTAGE
OFF
MAXIMUM VOLTAGE
OFF
OFF EXCLUDES THE CONTROL
ON THE MINIMUM VOLTAGE
BY PRESSING IT YOU RETURN
TO THE FIRST SETUP SCREEN;
SEE CHAPTER 5.1
5. PROGRAMMING
34
PRESSING IT FOR MORE THAN
1s YOU GO OUT OF THE SETUP
AND THE PARAMETERS ARE
STORED IN THE MEMORY
OFF EXCLUDES THE CONTROL
ON THE MAXIMUM VOLTAGE
IT IS USED TO SET THE
MAXIMUM OPERATING VOLTAGE
OF THE MOTOR
ALARM DELAY
OFF
OFF EXCLUDES THE
ALARM DELAY
ALARM DELAY
OFF
ALARM DELAY
1 min
IT IS USED TO SET THE
DELAY ON THE ACTIVATION
OF THE ALARM OUTPUT
RANGE 1 ÷ 250min
MANUAL BUTTON
UNSTABLE
MANUAL BUTTON
UNSTABLE
UNSTABLE STARTS THE
MOTOR ONLY WHEN THE
MAN BUTTON IS PRESSED
MANUAL BUTTON
STABLE
STABLE STARTS THE MOTOR WITH
A PULSE ON THE MAN BUTTON;
STOPS THE MOTOR WITH A PULSE
ON THE RESET BUTTON

ENGLISH6. GENERAL FUNCTIONING OF THE CONTROL PANEL
6.1 General functioning
SETUP PREMI
PAG + MAN 10s
ON
THIS SCREEN IS DISPLAYED ONLY IF THE MAINS
SUPPLY WAITING FUNCTION IS ENABLED
IN THE SETUP MENU. TO EXCLUDE THE
WAITING TIME PRESS RESET
400 V 13.2A
Cf 0.80 0 h
MAINS WAIT. 1 m
RESET TO START
THE OPERATION SCREENS RELATING TO THE CHOSEN
APPLICATION ARE DISPLAYED BELOW
COSφ = SEE CHAPTER 6.2
CLEAN WATER = SEE CHAPTER 6.3
SEWAGE = SEE CHAPTER 6.4
4-20mA bar = SEE CHAPTER 6.5
4-20mA meters = SEE CHAPTER 6.6 }
6.2 Application cosφ
THE FOLLOWING SCREEN DISPLAYS:
- MEASURED VOLTAGE
- ABSORBED CURRENT
- COSφ DETECTED
- OPERATING HOURS OF THE MOTOR
AUTOMATIC MOTOR
Cf 0.80 13.2 A
STOP MOTOR
Cf 1.00 0.0 A
400 V 13.2 A
Cf 0.80 0h
IT IS USED TO START
THE MOTOR MANUALLY
EXTERNAL COMMAND
OFF
EXTERNAL COMMAND
ON
OFF: DISABLE MOTOR
ON: ENABLE MOTOR
6.1
IF THE MOTHERBOARD DETECTS A
DRY RUNNING CONDITION IT WILL
BE POSSIBLE TO DISPLAY A FOURTH SCREEN
WAITING FILLING
START 1 h 10 m
IT DISPLAYS THE REMAINING
WAITING FILLING TIME
It is used to scroll through the pages Pressed in MOTOR STOP status it starts the motor
in manual mode
Pressed it starts the motor in automatic mode
Pressed the motor goes in STOP function
Pressed in case of an alarm it resets it
35
IGNITION
CONTROL PANEL
ONLY IN STABLE MANUAL
BUTTON MODE

EXTERNAL COMMAND
ON
6. GENERAL FUNCTIONING OF THE CONTROL PANEL
6.3 Application clean water
400 V
13.2 A 0 h
THE FOLLOWING SCREEN DISPLAYS:
- MEASURED VOLTAGE
- ABSORBED CURRENT
- OPERATING HOURS OF THE MOTOR
AUTOMATIC MOTOR
13.2 A Oh
STOP MOTOR
0.0 A 0h
400 V
13.2 A 0h
6.4 Application sewage
400 V
13.2 A 0 h
AUTOMATIC MOTOR
13.2 A Oh
STOP MOTOR
0.0 A 0h
400 V
13.2 A 0h
MIN . OFF MAX1 OFF
ALL. ON
IS DISPLAYS THE STATUS OF THE INPUTS:
MIN: OFF G.MIN OPEN; ON G.MIN CLOSED
MAX1: OFF G.MAX1 OPEN; ON G.MAX1 CLOSED
ALL.: OFF G.ALAR OPEN; ON G.ALAR CLOSED
17
6.1
6.1
ONLY IN STABLE MANUAL
BUTTON MODE
EXTERNAL COMMAND
OFF
IF THE MOTHERBOARD DETECTS A
DRY RUNNING CONDITION IT WILL
BE POSSIBLE TO DISPLAY A FOURTH SCREEN
NO WATER
THIS SCREEN IS DISPLAYED WHEN
THE MINIMUM PROBE IS DISCOVERED
WAITING
FILLING
THIS SCREEN IS DISPLAYED WHEN THE
MINIMUM PROBE IS COVERED AND
THE MAXIMUM PROBE IS DISCOVERED
AFTER THE LACK OF WATER
36
OFF: DISABLE MOTOR
ON: ENABLE MOTOR
IT IS USED TO START
THE MOTOR MANUALLY
THE FOLLOWING SCREEN DISPLAYS:
- MEASURED VOLTAGE
- ABSORBED CURRENT
- OPERATING HOURS OF THE MOTOR
IT IS USED TO START
THE MOTOR MANUALLY
ONLY IN STABLE MANUAL
BUTTON MODE

ENGLISH6. GENERAL FUNCTIONING OF THE CONTROL PANEL
6.5 Application 4-20mA bar
400 V 13.2 A
4.5 bar 0 h
AUTOMATIC MOTOR
13.2 A Oh
STOP MOTOR
0.0 A 0h
400 V 13.2 A
4.5 bar 0h
SYSTEM PRESSURE
4.5 bar
IT DISPLAYS THE SYSTEM PRESSURE
DETECTED
6.6 Application 4-20mA meters
400 V 13.2 A
1.52 m 0 h
AUTOMATIC MOTOR
13.2 A Oh
STOP MOTOR
0.0 A 0h
400 V 13.2 A
1.52 m 0h
TANK LEVEL
1.52 m
IT DISPLAYS THE DETECTED
TANK LEVEL
6.1
6.1
NO WATER
WAITING
FILLING
ONLY IN STABLE MANUAL
BUTTON MODE
THE FOLLOWING SCREEN DISPLAYS:
- MEASURED VOLTAGE
- ABSORBED CURRENT
- SYSTEM PRESSURE
- OPERATING HOURS OF THE MOTOR
IT IS USED TO START
THE MOTOR MANUALLY
THIS SCREEN IS DISPLAYED WHEN THE
MINIMUM PROBE IS COVERED AND
THE MAXIMUM PROBE IS DISCOVERED
AFTER THE LACK OF WATER
THIS SCREEN IS DISPLAYED WHEN
THE MINIMUM PROBE IS DISCOVERED
IF THE MOTHERBOARD DETECTS A
DRY RUNNING CONDITION IT WILL
BE POSSIBLE TO DISPLAY A FOURTH SCREEN
ONLY IN STABLE MANUAL
BUTTON MODE
IT IS USED TO START
THE MOTOR MANUALLY
THE FOLLOWING SCREEN DISPLAYS:
- MEASURED VOLTAGE
- ABSORBED CURRENT
- TANK LEVEL IN METERS
- OPERATING HOURS OF THE MOTOR
37

38
7. MOTOR MAINTENANCE
7.1 Motor maintenance programming
7.2 Motor maintenance message
SETUP PRESS
PAGE + MAN 10s
IGNITION
CONTROL PANEL
+
ON
RANGE 1÷ 99999h
THIS SCREEN DISPLAYS
THE MAINTENANCE TIME RESET
THIS SCREEN DISPLAYS THE TIME ELAPSED
SINCE THE LAST MAINTENANCE
MOT. MAINTENANCE
SET 500h
MOT. MAINTENANCE
SET OFF
MOT. MAINTENANCE
SET OFF
MOT. MAINTENANCE
ENTER TO RESET
LAST MOTOR
MAINTENAN. 0h
LAST MOTOR
MAINTENAN. 500h
SCREEN
DESCRIPTION
PERFORM
MOTOR MAINTEN.
Exceeded the set time, this screen will be displayed during operation, indicating
to perform the motor maintenance
IT IS USED TO SET THE MOTOR MAINTENANCE
OFF EXCLUDES THE
MOTOR MAINTENANCE
PRESSING IT FOR MORE THAN 1s
YOU GO OUT OF THE MOTOR
MAINTENANCE PROGRAMMING
SETUP AND THE PARAMETERS ARE
STORED IN THE MEMORY

ENGLISH8. DATA LOGGER
8.1 Alarm data logger
SETUP PREMI
PAGE + MAN 10s +
ON
AL. 3 MAX. CURR.
17.5 A 20h
AL. 2 MIN. CURR.
9.5 A 15h
AL. 1 MAX. VOLT.
255V 10h
PRESSED FOR MORE THAN 1s, YOU
GO OUT OF THE DATA LOGGER
The alarm data logger is used to display the last 20 stored alarms in descending order.
The motherboard together with the alarm also records the motor operating hours in which it was
generated.
8.2 Event data logger
SETUP PREMI
PAGE + MAN 10s +
ON
EV. 12 MIN. CURR.
MAN. 8.2 A 30h
EV. 10 MAX. VOLT.
OFF 10h
- Maximum voltage
- Maximum motor starts per hour
- Minimum current
The event data logger is used to display the last 20 changes made in the setup relating to the
motor protections in descending order:
- Minimum voltage
- Maximum current
- Minimum cosφ
The motherboard together with the event also records the motor operating hours in which it was
generated.
EV. 11 MAX. CURR.
MAN. 20.2 A 25h
IGNITION
CONTROL PANEL
IGNITION
CONTROL PANEL
39
PRESSED FOR MORE THAN 1s, YOU
GO OUT OF THE DATA LOGGER

FREQUENT PROBLEMS CAUSES OPERATION
Application SEWAGE/CLEAN WATER:
FLOAT SWITCHES OFF status
with full tank
Application COS :φ
EXTERNAL COMMAND OFF
with empty tank
Ceck the functionality of the float switches
and replace if necessary
Possible failure of the float switch
Ceck the functionality of the float switches
and of the cable and replace if necessary
Possible failure of the float switches
or connection cable interrupted
Feed the control panel respecting
the input voltage
Set the switch on 1
Connect the flat cable from the motherboard
to the display
Switch set on 0
MAXIMUM CURRENT alarm
Maximum current set on the setup less
than that absorbed by the motor
Motor blocked or damaged
Application 4-20mA meters:
The displayed level
in meter is wrong
Clean carefully the piezoresistive probe
or replace if necessary
Possible obstruction or failure of the
piezoresistive probe 4-20mA
9. TROUBLESHOOTING AND PROPOSED SOLUTIONS
Application 4-20mA bar:
Pressure value in bar displayed
in the wrong display
Clean carefully the pressure transducer
or replace if necessary
Possible obstruction or failure of the
4-20mA pressure transducer
Display off
No supply
The flat cable inside the control panel
is not connected
Set manually the maximum current the 25%
more than the nominal value
Disconnect the motor and be sure
it is working properly
40
This manual suits for next models
1
Other SALUPO Control System manuals
Popular Control System manuals by other brands
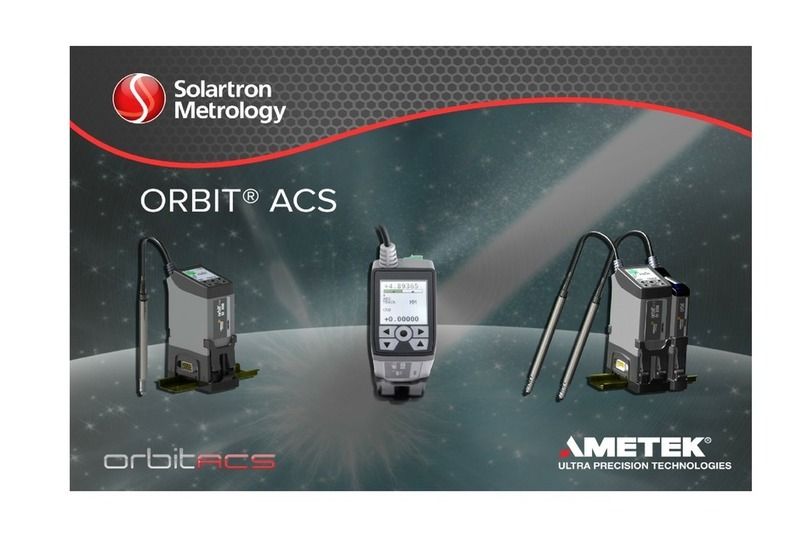
Solartron Metrology
Solartron Metrology AMETEK ORBIT ACS SI100 manual
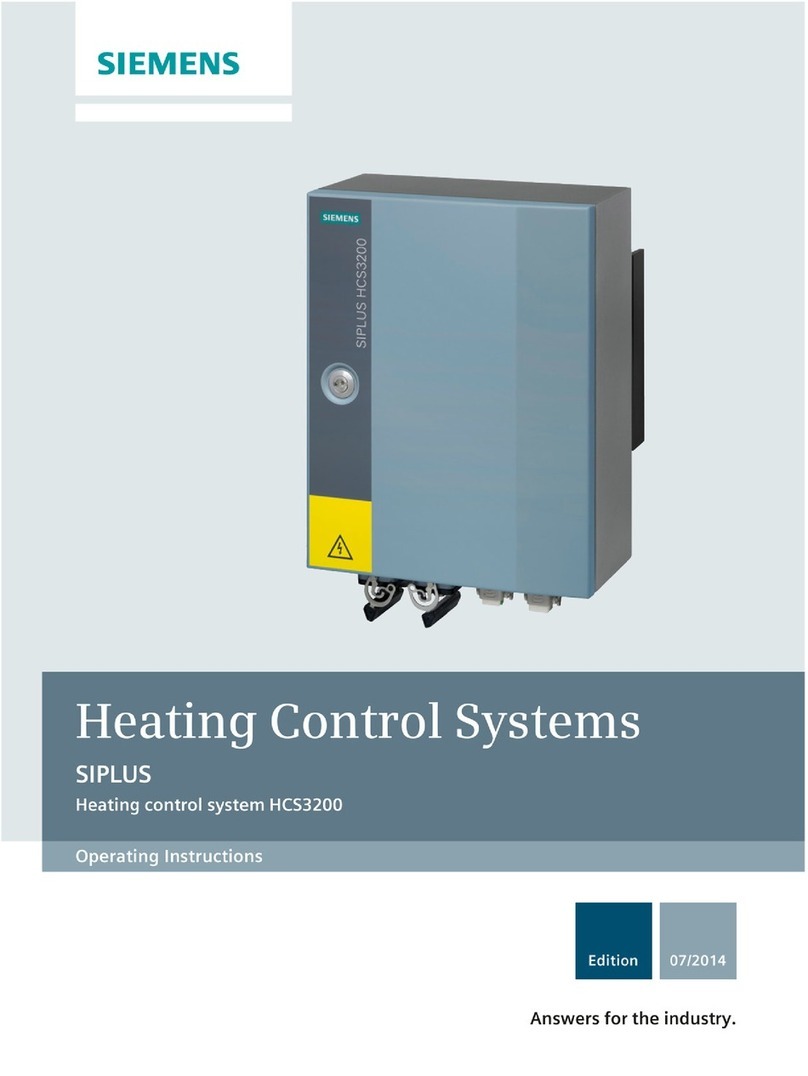
Siemens
Siemens SIPLUS HCS3200 operating instructions
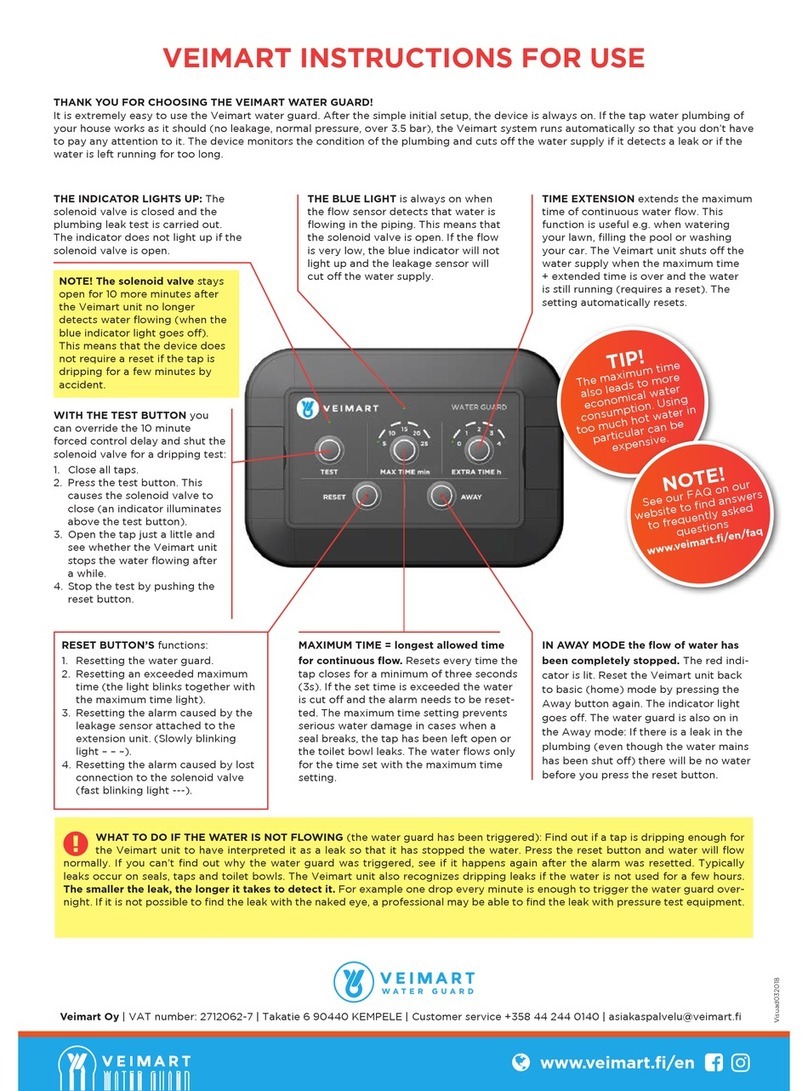
Veimart
Veimart VM-10 Instructions for use
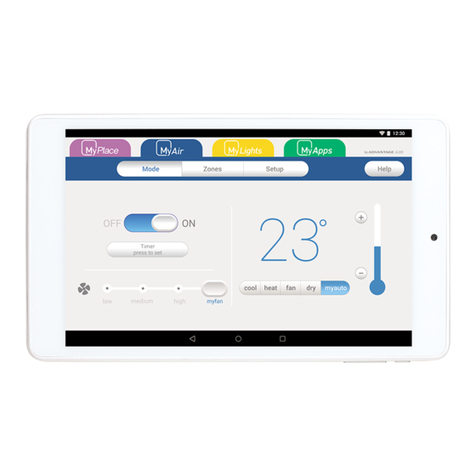
ADVANTAGE AIR
ADVANTAGE AIR MyAir user manual
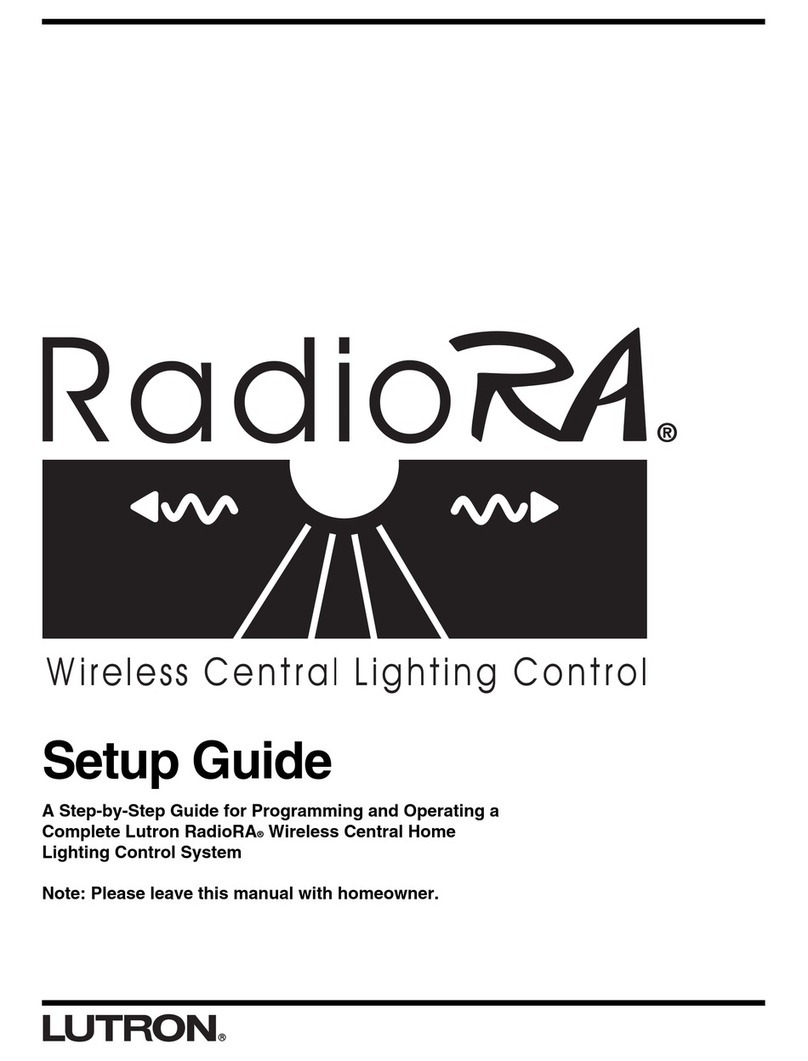
Lutron Electronics
Lutron Electronics RadioRA Setup guide
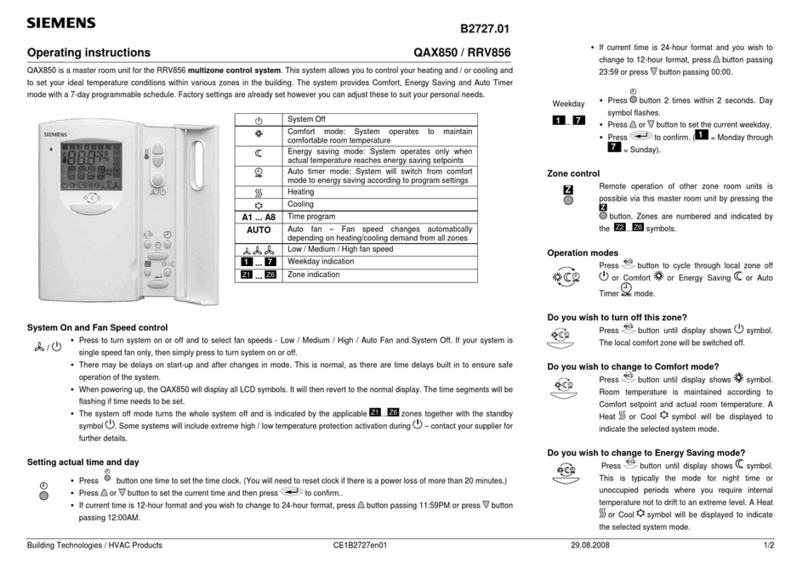
Siemens
Siemens QAX850 operating instructions