Scotchman FI-8510-20M User manual

You have downloaded a manual for our
Model FI-8510-20M Ironworker.
This manual does not include all of the
optional tooling for this machine.
If you would like a tooling manual,
please download our #40 Tooling Manual.
4295
4758
10mm ss
10mm ss
10mm ss
10mm ss 10mm ss 10mm ss
10mm ss
10mm ss
12mm
12mm
15273
025182
25180
25083
6 mm ss
25070
25070
10mm10mm
10mm
10mm
12mm
12mm
12mm
15381
25083
201610 201610
25078
113017 113017
15377
WARNING
SAFETY GLASSES REQUIRED WHEN
OPERATING OR OBSERVING THIS MACHINE
NEVER-
NEVER-
NEVER-
NEVER-
NEVER-
NEVER-
NEVER-
TO PREVENT SERIOUS BODILY INJURY
Operate, install tooling, service or adjust machine without
operator's manual and safety film.
Service machine with electrical power connected.
Operate any station without the respective strippers or
Operate machine with protective guards removed.
Place any part of your body under blade, punch or moving
Operate punch station without checking the punch to die
alignment and tightness.
Punch half holes, punch or shear unknown materials, side load
DO NOT REMOVE THIS SIGN FROM THIS MACHINE
REV. 0310
FOR MORE INFORMATION CONTACT SCOTCHMAN INDUSTRIES INC.
1-800-843-8844
003100
proper instructions and without reading and understanding the
hold-downs in place.
members.
(Check alignment and tightness daily.)
press brakes.
AT
SERIAL
SCOTCHMAN INDUSTRIES, INC.
PHILIP, SOUTH DAKOTA, U.S.A.
MADE IN U.S.A.
MODEL
FLA
HZ
PH
H.P. VOLT
BLADE LENGTH
PH. 605-859-2542
PSI
8510-20M
MACHINE CAPACITIES
SPEC. BASED ON MILD STEEL-65,000 PSI TENSILE
PUNCH
THROAT DEPTH RECT. NOTCHER
85 TONS
Ø27 THRU 25MM
Ø1-1/16 THRU 1"
10" - 254MM
76X127X12MM
3"w X 5"d X 1/2"t
#015380 1,05
FLAT SHEAR
25X300 - 19X508MM
1X12 - 3/4X 20"
BLADE LENGTH 20" - 508MM
PUNCH STROKE
3.45" - 87MM
ANGLE SHEAR
150X150X12MM
6"X6"X 1/2"
ROD SHEAR
Ø1-1/2" ROUND Ø38MM
1-1/4 SQUARE 32 SQUARE
FULLY INTEGRATED
BEYOND THESE GUARDS
INJURY DO NOT PLACE FINGERS
TO PREVENT SERIOUS BODILY
003105
WARNING
1210
GUARD FACE TO SHEAR EDGE
ADD 5-5/8" (143MM)
GUARD FACE TO SHEAR EDGE
ADD 4-1/4" (108MM)
11893Raw 11898 Assy.
230 Volts
19121
OFF
EATON 11856
ELECTRICAL HAZARD
Turn off power
and lock out
before servicing.
DANGER
3122 1213
15788
STOP
START
START
SHEAR
PUNCH
JOG
JOG PROBE
15600 Assy.
RUN

www.scotchman.com
MODEL
FI-8510-20M
IRONWORKER
SCOTCHMAN INDS. - 180 E US HWY 14 - PO BOX 850 - PHILIP, SD 57567 Call: 1-605-859-2542
SEPTEMBER 2021

PAGE 2
TABLE OF CONTENTS
SECTION DESCRIPTION PAGE #
1.0 INTRODUCTION 5
2.0 SAFETY PRECAUTIONS 6
2.1 WARRANTY 7
3.0 WARNING LABELS 8
4.0 INSTALLATION AND SET-UP 10-17
4.1 Physical Dimensions 10
4.2 Machine Moving Procedures 12
4.3 Physical Inspection 13
4.4 Electrical Requirements 14
4.5 Machine Start-Up 18
4.6 Machine Stroke Inspection and Adjustment 18
5.0 MAINTENANCE 20-23
5.1 Lubrication 20
5.2 Scheduled Maintenance 22
6.0 MACHINE OPERATION 24-42
6.1 Punch Operation 24
6.2 Bar Shear Operation 30
6.2A Hold Down Adjustment 32
6.2B Shear Blade Adjustment 33
6.3 Tooling Arm Adjustment 34
6.4 Angle Shear Operation 36
6.4A Angle Shear Blade Adjustment or Replacement 36
6.5 Rod Shear Operation 38
6.5A Rod Shear Blade Adjustment or Replacement 38

PAGE 3
TABLE OF CONTENTS
SECTION DESCRIPTION PAGE #
6.6 Rectangle Notcher Operation 40
6.6A Rectangle Notcher Blade Adjustment or Replacement 40
6.7 Jog Control 42
7.0 OPTIONAL TOOLS 42-67
7.1 Pipe Notcher 42
7.2 6 x 6 Ninety Degree Notcher 46
7.3 12 & 24 Inch Brakes 48
7.4 Angle Iron Brake 52
7.5 Channel Shear 54
7.6 Picket Fence Tool 58
7.7 Square Tube Shear 60
7.8 Optional Die Holders and Punch Retaining Nuts 62
7.8A Offset Die Holder For Flange Punching 62
7.8B 2-1/2 x 3 Inch Die Inserts 62
7.8C 6 x 6 Die Holder 62
7.8D #45 Punch Retaining Nut 62
7.8E Heavy Duty Split-Ring Retaining Nut 63
7.9 48 Inch Back Gauge 64
8.0 TROUBLE SHOOTING GUIDE 66-71
8.1 Electrical Trouble Shooting-Motor 66
8.2 Limit Switch Inspection Procedure 68
8.3 Control Valve Inspection 68
8.4 Hydraulics 69
8.5 Seal Replacement-Cylinder 70

PAGE 4
TABLE OF CONTENTS
SECTION DESCRIPTION PAGE #
9.0 PARTS LISTS 72-95
9.1 Tooling Arm Assembly 72
9.2 Drive Arm Assembly 74
9.3 Flat Bar Shear Assembly 76
9.4 6" Angle Shear Assembly 78
9.5 Rod Shear Assembly 80
9.6 Notcher Assembly 82
9.7 Upper Panel 84
9.8 Stripper Assembly 86
9.9 Sheet Metal & Cylinder 88
9.10 Power Unit 90
9.11 Punch Retaining Nuts 92
9.12 Electrical Unit 94
10.0 Supplement For Older Models 96-97
10.1 6 x 6 Angle Shear (Ser.# 1060 & Prior) 96

PAGE 5
1.0 INTRODUCTION
The Scotchman FI-8510-20M is a versatile, multi-purpose, shearing, punching and forming machine
engineered for trouble free operation.
The design of the machine combines simplicity of operation with smooth, full stroke control.
The ability of the operator to control the machine’s direction of movement at any point in the stroke,
(stop, jog or reverse), gives the Scotchman Ironworker a tremendous advantage over mechanical
ironworkers.
There is no chance of the Scotchman being "accidentally tripped".
The Hydraulic system operates at a maximum pressure of 2,700 PSI (185 BAR) and is protected from
overload by a relief valve.
The Scotchman FI-8510-20M is designed as a fully-integrated, tooled Ironworker.
On this model, the tools are an integral part of the machine and are designed for the user that wants the
advantage of five separate working stations without the necessity of tooling changes.
While this is a fully-integrated machine, Scotchman still offers many optional tools that are adaptable to
this model.
Some of the optional tools available are: a channel shear, pipe notcher and brake attachment, as well as a
variety of special tools.
If you have a special application, please contact your dealer or the factory.

PAGE 6
2.0 SAFETY PRECAUTIONS
1. The operators of this machine must be qualified and well trained in the operation of the machine.
The operators must be aware of the capacities of the machine and the proper use of the hold down
devices, strippers and guards provided with the machine.
2. All of the guards, adjustable restricters and awareness barriers must be installed on the machine
and kept in good working order. Promptly replace worn or damaged parts with authorized parts.
3. Never place any part of your body into or under any of the machine’s moving parts, strippers or
hold devices.
4. Wear the appropriate personal protective equipment. Safety glasses are required at all times,
whether operating, setting up or observing this machine in operation. Since heavy pieces of metal
with sharp edges can be processed on this machine, the operator should also wear steel-toed shoes
and tight fitting leather gloves.
5. Strictly comply with all warning labels and decals on the machine. Never remove any of the labels.
Replace worn or damaged labels promptly.
6. Always disconnect and lock out the power when performing maintenance work or setting up any
tooling on the machine. Follow the procedures outlined in the operator’s manual for setting up,
changing or aligning any tooling on this machine.
7. Never operate this machine with dull or damaged tooling. Replace worn punches, dies and blades
promptly.
8. Practice good housekeeping. Keep the area around the machine clear and well lit. Do not
obstruct the operator’s position by placing anything around the machine that would impede the
operator’s access to the machine.
9. Never modify this machine in any way without the written permission of the manufacturer.
10. Never leave this machine running unattended.
11. Always operate the punch station facing the station, standing. Never operate any of the work
stations from a sitting or kneeling position.
12. Set up a program of routine inspections and maintenance for this machine. Make all repairs and
adjustments in accordance with the manufacturer’s instructions.
13. A safety dvd was mailed to you or shipped with the machine. If you did not receive it, please
contact the factory or your local dealer immediately and one will be sent to you at no charge. If
this machine was purchased used, please contact the factory for a safety dvd.

PAGE 7
2.1 WARRANTY
Scotchman Industries, Inc. will, within three (3) years of the date of purchase, replace F.O.B. the factory
or refund the purchase price for any goods which are defective in materials or workmanship, provided
the buyer returns the warranty registration card within thirty (30) days of the purchase date and, at the
seller’s option, returns the defective goods freight and delivery prepaid to the seller, which shall be the
buyer’s sole and exclusive remedy for defective goods.
Hydraulic and electric components are subject to their respective manufacturer’s warranties.
This warranty does not apply to machines and/or components which have been altered, changed or
modified in any way or subjected to abuse and abnormal use, inadequate maintenance and lubrication or
subjected to use beyond the seller’s recommended capacities and specifications.
In no event shall the seller be liable for labor cost expended on such goods or consequential damages.
The seller shall not be liable to the purchaser or any other person for loss or damage directly or
indirectly arising from the use of the goods or from any other cause.
No officer, employee or agent of the seller is authorized to make any oral representations or warranty of
fitness or to waive any of the foregoing terms of sale and none shall be binding on the seller.
Any electrical changes made to the standard machine due to local electrical code variation must be paid
by purchaser.
As we constantly strive to improve our products, we reserve the right to make changes without
notification.

PAGE 8
3.0 WARNING LABELS
ITEM PART # DESCRIPTION
A 003110 PUNCH WARNING
B 003100 MAIN WARNING LABEL
C 003105 FINGERS BEYOND (SHEAR)
D 003120 DANGER: VOLTAGE
E 003140 FINGERS BEYOND (TOOL)
F 004349 NOTCHER NOTICE
G 015380 CAPACITY LABEL

PAGE 9
FIGURE 1

Page 10
4.0 INSTALLATION AND SET-UP
CAUTION: THIS SECTION DISCUSSES INSTALLATION AND SET-UP PROCEDURES.
PLEASE READ THOROUGHLY BEFORE OPERATING THIS MACHINE.
AFloor to Punch Ram 109.2
BFloor to Top of Die 37-1/4
C
D
E
F
G
H
I
Floor to Top of Bolster 79.4
Floor to Bar Shear 37-7/16
Floor to Notcher 37-3/8
Height 198.1
Length 66-1/4 168.3
Width 72.4
Floor to Top Of Shroud
Floor to Bottom Of Base 3 7.6
INCHES CM DESCRIPTION
ITEM
Floor to Rod Shear
J
K
L
M
N
O
Weight 4,550 LBS. 2,064 KG.
Punch Stroke 3.65 9.3
25-1/2
28-1/2
78
Floor to Angle Shear 48-5/16 122.7
47-11/16 121.1
Throat Depth 10 25.4
Floor to Bottom of Bolster 29-5/8 75.2
31-1/4
94.6
43
95.1
94.9
P
64.8
4.1 PHYSICAL DIMENSIONS

PAGE 11
FIGURE 2

PAGE 12
4.2 MACHINE MOVING PROCEDURES
CAUTION: BE SURE THAT ANY LIFTING DEVICE HAS ADEQUATE CAPACITY
BEFORE ATTEMPTING TO MOVE THIS MACHINE. THIS MODEL WEIGHS 4,500 LB.
(2,068 KG.). IT IS DESIGNED TO BE MOVED BY A FORKLIFT, ONLY. THERE ARE
FORKLIFT SLOTS DESIGNED INTO THE BASE OF THE MACHINE FOR THIS
PURPOSE.
SEE FIGURE 3 BELOW.
FIGURE 3

Page 13
Any damage to the machine during shipment should be reported to the delivery carrier immediately.
A damage report must be made so that a claim can be placed. The carrier is responsible for shipping
damage, but it is the customer.s responsibility to immediately report damages, external or internal.
After the machine has been located, remove the side shrouds and inspect the interior of the machine for
possible shipping damages.
CHECK SPECIFICALLY THE FOLLOWING ITEMS:
A. Stroke control handles and limit switches.
B. Pump and motor assembly.
C. Hydraulic hoses and fittings.
D. Starter box and control box.
E. Electrical connections.
F. Control valve.
G. A general inspection of machine shrouds, guards and awareness barriers.
H. Check the re-pack box for all accessory items ordered with the machine.
The reservoir is full of oil. The recommended oil is a lightweight, non-foaming, anti-wear, hydraulic oil
such as Mobil DTE-25, with a minimum ISO cleanliness code of 20/18/15, or equivalent.
The reservoir holds 13.5 U.S. gallons (51 liters).
4.3 PHYSICAL INSPECTIONS
CAUTION: DO NOT OVER FILL!

4.4 ELECTRICAL REQUIREMENTS
PAGE 14
CAUTION: TO PREVENT DAMAGE TO THE MOTOR AND DANGER TO THE OPERATOR,
ALL ELECTRICAL CONNECTIONS SHOULD BE MADE BY A LICENSED ELECTRICIAN.
POWER REQUIREMENTS
Motor frame 3PH=182T 1PH=184T
MOTOR VOLTAGE FULL LOAD CURRENT
(VAC) (AMPS)
208 14
230 12.6
380 7.7
460 6.3
575 5.1
230 (single phase) 24.5
Motor power rating: 5hp Speed 1,725 RPM
KVA power rating: 5.6 KVA Frequency 60 HZ
Starting Current: 210% Full Load
All machines are wired for three phase electrical power unless otherwise specified by customer. The
supply voltage should be (+ or -) 10% of the motor voltage rating, to insure satisfactory machine
performance. Check the motor data tag for full load current requirements.
The electrical diagram for the machine is inside the cover of the control box.
SEE DIAGRAMS IN FIGURES 4A THRU 4D
For electrical supply lines ten feet (3 m) or shorter, we recommend at least 12 and
preferably 10, gauge wire. For longer supply lines, use at least 10 gauge and preferably, 8 gauge.
We do not recommend supply lines longer than twenty five feet (7.5 m).

PN 011898 RATING TABLE
FI85 3PH
1 DISC
INCOMING SUPPLY
(BY CUSTOMER)
PROVIDE MAXIMUM
UPSTREAM PROTECTION
PER N.E.C. CODE 430-52
AND TABLE 430-152.
1M
L3
L2
L1
1OL T1
T3
T2 MTR
GND
SEE MOTOR TAG
FOR DETAILS
LINE VOLTAGE (3PH)
MAX. HP
MOTOR FLA
OVERLOAD
208
5
14
ZB32-24
230
5
12.6
ZB32-24
380
5
7.7
ZB32-10
460
5
6.3
ZB32-10
575
5
5.1
ZB32-10
1FU 2FU
FUSE REPLACEMENT
1FU & 2FU = FNQ-R-1-1/2
3FU = FNM-2
3FU
1T
SEE TRANSFORMER FOR
WIRING DATA
OPTIONAL WORK LIGHT AVAILABLE
(1T MUST BE 250VA MIN.)
(208V 1T MUST BE 350VA)
(BLK)
X1 L(WHT) X2
LED WORK LIGHT
(BLK) L
LASER LIGHT
1OL
97
95
98
4PB
96
E-STOP
1 2 1(1)
(2)
13
2
(3)
3
1M 14 A1
1PB
E-STOP
1 2
2PB
START
13 14
PUNCH
5
(OXO)
6
X1
START
1SS
SHEAR 1PL
G
1M
A2
(GRN/YEL)
X2
(WHT)
1FTS
4
2SS
JOG PROBE
RUN
56
(OXO)
(4)
(WHT) 10 (10)
(XOO)
(OOX)
1
(XOO)
2
3PB
4
JOG
3
3 4
(7)
(9)
(11)
7 8
(OOX)
SWITCH
PROBE
BLK
TERMINAL
BLOCK
GRN/YEL
SOCKET
PROBE
GRN/YEL
RED
1
(2)
BLK
3
(XO)
TERMINAL STRIP #
WIRE #
WIRE COLOR
COMPONENT TERMINAL #
NORMAL POSITION
OPTIONAL EQUIPMENT
COMPONENT
DRAWN BY:
CR - CONTROL RELAY
CVC - CONTROL VALVE COIL
DISC - DISCONNECT
FTS - FOOT SWITCH
FU - FUSE
LS - LIMIT SWITCH
M - MOTOR START RELAY
OL - OVERLOAD (THERMAL)
PB - PUSH BUTTON
PL - PILOT LIGHT
SS - SELECTOR SWITCH
T - TRANSFORMER
SCALE: PART NAME:
DATE:
RVT N/A FI85 3PH ELEC. SCHEMATIC
MATERIAL:REV:
8/1/18 C PER PART
PART NO:
SCOTCHMAN IND.
1
1
BROWN BROWN
12
11
WHT BLUE BLUE
13
(OOX) 11 12
1CR
A1 A2
3
9
4
10
(RED) (BLK) 5(5)
(OOX) 7
(XOO)
8
(8)
1 2
8
(6) 1LS/SHEAR
6(BLK)
(BLK)
7
(RED)
(RED)
2LS/PUNCH
(TOP)
GRAY X2
2CVC
9
BLACK
1CVC
1CR
43
31
21
44
22
32
011898-E1
(RED)
MALE
FEMALE
PAGE 15A
FIGURE 4A

PAGE 15B
FI85 230V 1PH
PN 011898 RATING TABLE
LINE VOLTAGE (1PH)
MAX. HP
MOTOR FLA
OVERLOAD
1 DISC
INCOMING SUPPLY
(BY CUSTOMER)
PROVIDE MAXIMUM
UPSTREAM PROTECTION
PER N.E.C. CODE 430-52
AND TABLE 430-152.
1M
L3
L2
L1
1OL T1
T3
T2 MTR
GND
SEE MOTOR TAG
FOR DETAILS
230
5
24.5
ZB32-24
1FU 2FU
FUSE REPLACEMENT
1FU & 2FU = FNQ-R-1-1/2
3FU = FNM-2
3FU
1T
SEE TRANSFORMER FOR
WIRING DATA
OPTIONAL WORK LIGHT AVAILABLE
(1T MUST BE 250VA)
(BLK)
X1 L(WHT) X2
LED WORK LIGHT
(BLK) L
LASER LIGHT
1OL
97
95
98
4PB
96
E-STOP
1 2 1(1)
(2)
13
2
(3)
3
1M 14 A1
1PB
E-STOP
1 2
2PB
START
13 14
PUNCH
5
(OXO)
6
X1
START
1SS
SHEAR 1PL
G
1M
A2
(GRN/YEL)
X2
(WHT)
1FTS
4
2SS
JOG PROBE
RUN
56
(OXO)
(4)
(WHT) 10 (10)
(XOO)
(OOX)
1
(XOO)
2
3PB
4
JOG
3
3 4
(7)
(9)
(11)
7 8
(OOX)
SWITCH
PROBE
BLK
TERMINAL
BLOCK
GRN/YEL
SOCKET
PROBE
GRN/YEL
RED
1
(2)
BLK
3
(XO)
TERMINAL STRIP #
WIRE #
WIRE COLOR
COMPONENT TERMINAL #
NORMAL POSITION
OPTIONAL EQUIPMENT
COMPONENT
DRAWN BY:
CR - CONTROL RELAY
CVC - CONTROL VALVE COIL
DISC - DISCONNECT
FTS - FOOT SWITCH
FU - FUSE
LS - LIMIT SWITCH
M - MOTOR START RELAY
OL - OVERLOAD (THERMAL)
PB - PUSH BUTTON
PL - PILOT LIGHT
SS - SELECTOR SWITCH
T - TRANSFORMER
SCALE: PART NAME:
DATE:
RVT N/A FI85 230V 1PH ELEC. SCHEMATIC
MATERIAL:REV:
8/1/18 C PER PART
PART NO:
SCOTCHMAN IND.
1
1
BROWN BROWN
12
11
WHT BLUE BLUE
13
(OOX) 11 12
1CR
A1 A2
3
9
4
10
(RED) (BLK) 5(5)
(OOX) 7
(XOO)
8
(8)
1 2
8
(6) 1LS/SHEAR
6(BLK)
(BLK)
7
(RED)
(RED)
2LS/PUNCH
(TOP)
GRAY X2
2CVC
9
BLACK
1CVC
1CR
43
31
21
44
22
32
011898-E1
(RED)
MALE
FEMALE
FIGURE 4B

Page 16 FIGURE 4C
3 PHASE
INCOMING POWER
GRD.
SET TO
MOTOR
FLA
1 PHASE
INCOMING POWER
GRD.
SET TO
MOTOR
FLA
JUMPER
TO MOTOR TO MOTOR
OVERLOAD
CONTACTOR CONTACTOR
OVERLOAD
T36T24T12
AH
RESET
TEST
A2
NC
22
14
NO
NONC
9796 98
95
_OL_
ZB32-32
2
6
A
4
8
OVERLOAD
L1 L2
A1
T1 T2 T3
A2
L3 13 NO
14 NO
1M
CONTACTOR
T36T24T12
AH
RESET
TEST
A2
NC
22
14
NO
NONC
9796 98
95
_OL_
ZB32-32
2
6
A
4
8
OVERLOAD
L1 L2
A1
T1 T2 T3
A2
L3 13 NO
14 NO
1M
CONTACTOR
L1 L2 L3
T1 T2 T3
DISCONNECT
L1 L2 L3
T1 T2 T3
DISCONNECT

Page 17
#4 #5 #6
#1 #7
LINE LINE
#2 #8 #3 #9
LINE
LOW VOLTAGE C0NNECTION
( 220-240 VOLT 3PH )
#6 #9#5 #8#4 #7
LINELINELINE
#1 #2 #3
HIGH VOLTAGE C0NNECTION
( 440-480 VOLT 3PH )
WITH WORK LIGHT
PRIMARY SIDE
WITHOUT WORK LIGHT
RED
GREEN
WHITE
X1
XF
X2
FUSE
550 460 380 230 208
H6
H5
H4
H3
H1
H2
250 KVA
H7
H7
H2 H3 H4 H5 H6
FUSE
FUSE
PRIMARY SIDE
WHITE GREEN
SECONDARY SIDE
RED
RED
240
380
400
415
440
460
480 575
600
H1-H2 H1-H3
XF-X2
120
130
110
115
120
85
91
100 110
FUSE FUSE
SECONDARY SIDE
150 KVA
All New Machines Now Have The 250 KVA Transformer as Standard Equipment.
From the Motor
208
220
230
500
550
H1-H4 H1-H5
XF-X4
XF-X3
125
95
99
#1 - #9 are Wires
EATON
CO250E6U
X4 X3 X2 X1 XF --
-- H5 H4 H3 H2 H1
1T
3FU
250 VA
FUSE
FIGURE 4D

1313
26306
201210201210
201210201210
203217
203217
203217
243101
026350 - Assy.
203212
1309
1302
243101
243101
026350 - SQUARE TUBE SHEAR
26500
026500 - HEAVY DUTY RETAINING NUT
(punch not included)
VISIT WWW.SCOTCHMAN.COM FOR MORE INFORMATION
OPTIONAL TOOLING IS AVAILABLE
Table of contents
Other Scotchman Lathe manuals
Popular Lathe manuals by other brands
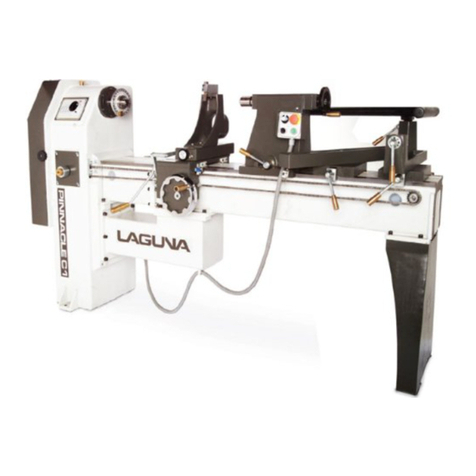
Laguna Tools
Laguna Tools MTP105 manual

Promac
Promac GH-2260ZX operating instructions
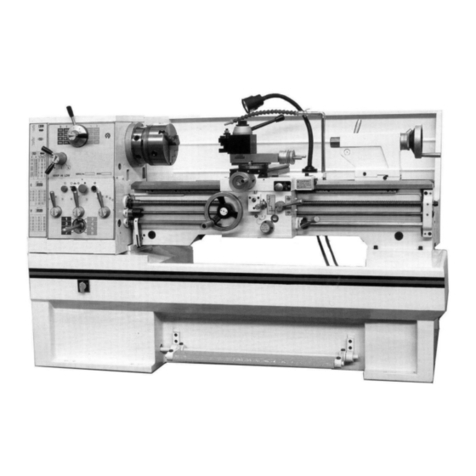
YANGZHOU SUPER MACHINE TOOL
YANGZHOU SUPER MACHINE TOOL CD6240 Instruction manual and parts list
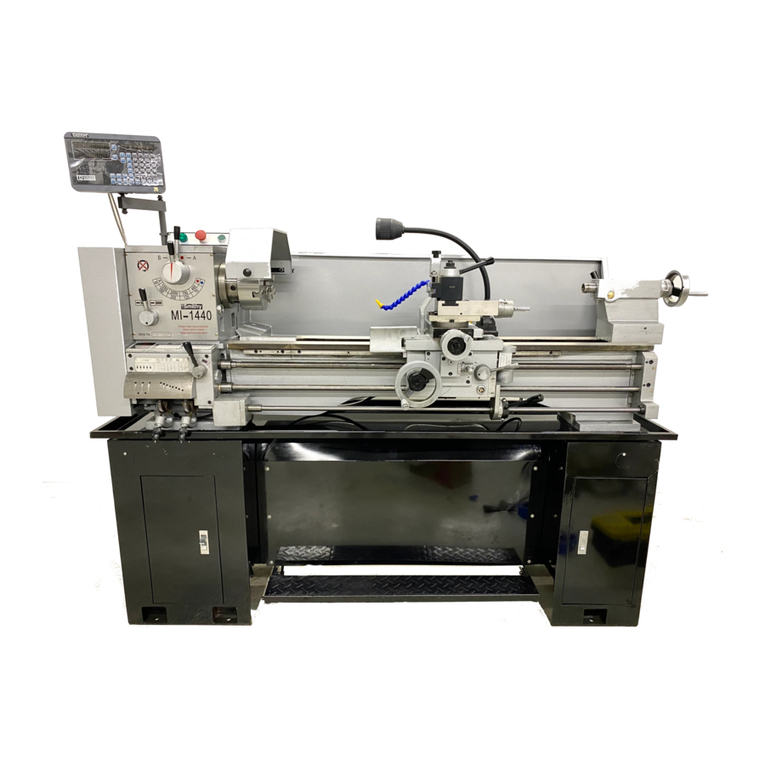
Smithy
Smithy MI-1440L Operator's manual
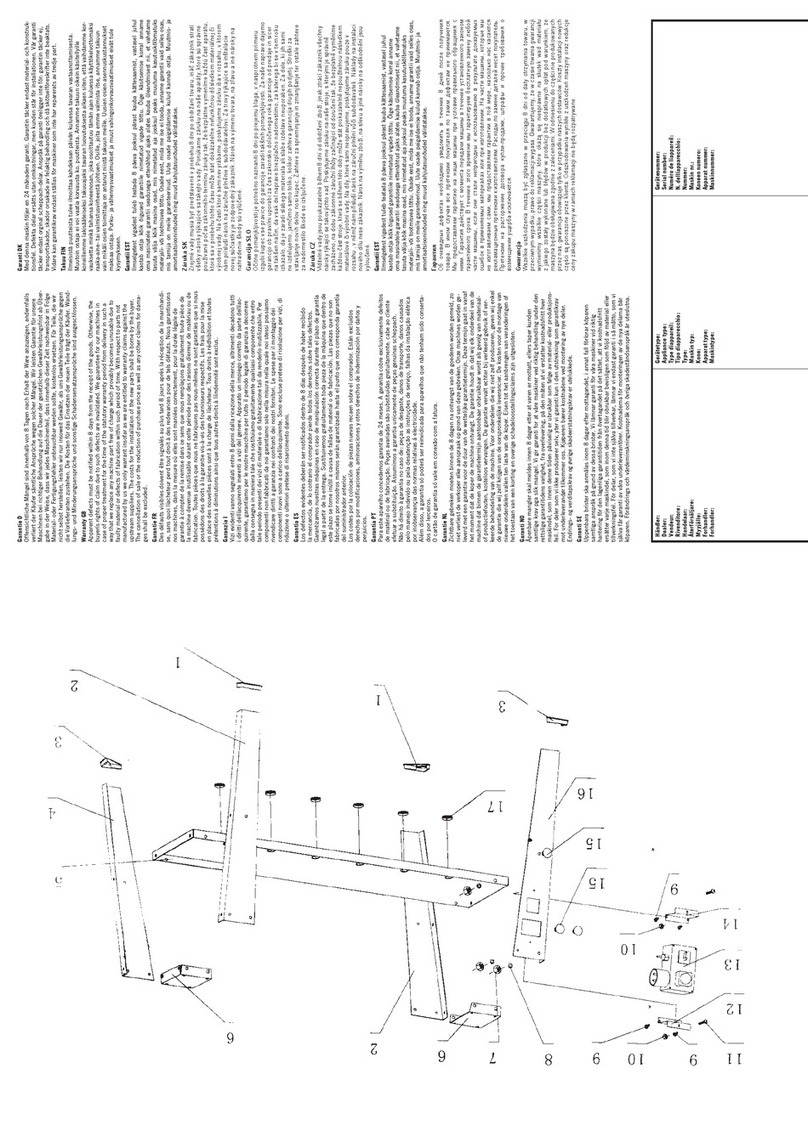
Scheppach
Scheppach Lata 5.0 Translation from the original instruction manual
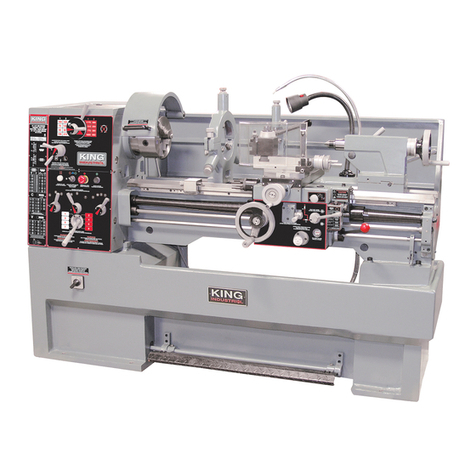
King Industrial
King Industrial TOOLROOM KC-1640ML instruction manual