Severn P Series Guide

Installation, Operation, Maintenance
Instructions for Severn Glocon
Piston Actuators –P Series
Typical Piston Actuator –List of Parts
Top and Side
Mount Handwheel
override options
shown above
General Inspection of parts
General inspection is for visual actuator condition only and a
test to confirm smooth movement of the piston in operation.
Advanced maintenance items:
Actuator ‘O’ ring seals, wiper ring and Piston rod guides
(Soft parts are available as an actuator repair kit)
Advanced Inspection –(to be carried out by trained /
experienced personnel only)
ACTUATOR ‘O’RING SEAL’S - Not re-useable
ACTUATOR SPRING –If damaged contact Severn Glocon
for advice on repair or whether replacement is needed
PISTON ROD GUIDES - Examine general condition; renew
if necessary
USE OF THIS MANUAL, LEGAL DIRECTIVES,
ENVIRONMENTAL AND OTHER SAFETY NOTICES
This manual to be read in conjunction with Severn Glocon
“Supplementary Installation, Erection, Maintenance and
Operating Procedures” document number SGG-IOM-5000,
DS610 and any other related O & M instructions relating to
any accessories fitted to the Control Valve. All notices,
warnings and guidance given in that manual are also
applicable to this document.
INTENDED USE
Reference is to be made to the Control Valve Specification
Sheet, Installation and Operation Instructions, nameplate to
check product is suitable for the intended use / application.
See Installation, Operation and Maintenance Instructions for
Severn Glocon Control and Choke valves SGG-IOM-5000-
M01-REV02 for information on the following (Latest Ed.’s):
a) MACHINERY DIRECTIVE INCORPORATED INTO A
MACHINE
b) ATEX DIRECTIVE
c) PRESSURE EQUIPMENT DIRECTIVE PED
d) ENVIROMENTAL and OTHER LEGISLATION & IPPC
DIRECTIVE
e) RETURNING PRODUCTS
DISPOSAL
Unless otherwise stated in the Instructions, this product is
recyclable and no ecological hazard is anticipated with its
disposal providing due care is taken
If any doubts exist, contact SEVERN GLOCON LTD
quoting the valve serial number
Safety: Always ensure safe working practices are followed:
Always isolate valve before maintenance.
Always use lockout methods to ensure safety
Caution: Do not put hands inside yoke area
Always use correct tools. Do not over tighten.
Do not use extension bars to force movement
Poison risk: Do not incinerate PTFE. Do not
smoke whilst handling PTFE.
Always read the manual. If any doubts exist,
contact SEVERN GLOCON LTD quoting the
valve serial number.
WARNING: When ordered, the actuator and or control valve
configuration and materials of construction are selected to
meet particular pressure, temperature, pressure drop and
controlled fluid conditions. Personal injury, property
damage, equipment damage, or leakage due to escaping
gas or bursting of pressure containing parts may result if the
actuator and or control valve or its ancillaries are over
pressured or installed where service conditions exceed the
actuator and control valve design limits. To avoid such injury
or damage, provide a relief valve for overpressure protection
as required by accepted industry or local codes and good
engineering practice. Do not apply other conditions to the
valve without written approval from Severn Glocon.
WARNING: Before performing any maintenance operation:
Isolate the actuator and or control valve from process
pressure. Relieve process pressure from both sides of the
control valve. Drain the process media from both sides of
the valve. If the control valve is to be removed from the line
decontaminate any process fluid remaining in the valve to
make safe. Disconnect and isolate any operating lines
providing air pressure, electric power, or a control signal to
the actuator. Vent the air pressure from the actuator. Be
sure that the actuator cannot suddenly open or close the
valve (Note by disconnecting the air and or power lines the
actuator will move the valve to its power failure position).
Ensure persons are a suitable distance from moving parts.
Use lock out procedures to be certain that the above
measures stay in effect whilst work is carried out on the
actuator or control valve.
Scope of this Manual - Installation - General
This manual includes installation, operating and
maintenance information for Severn Glocon P Series
actuators only. Please refer to separate manuals for

instructions covering the valve, positioner and any
accessories. Where the valve is operated by electric,
hydraulic or electro hydraulic actuation, follow the IOM
instructions provided by the actuator manufacturer.
Only persons qualified through training and or experience
should install, operate and maintain this product. In case of
questions about these instructions or the valves please
contact the nearest Severn Glocon office before proceeding.
Instructions in the following paragraphs describe the
installation procedures for the actuator. Instructions not
included are to be performed in accordance with standard
industry acceptable practises as may be required by local
codes, specifications and or regulations. Users should refer
to BS 6683 “Guide to installation and use of valves”.
Storage
Unless specifically specified by the contract, the actuator (or
valve and actuator) are packed for indoor storage at job site.
For short term storage the actuator or valve and actuator,
should be installed in a fire resistant weather tight and well
ventilated building. The equipment should be kept at a
temperature of –20F (-29deg.C) to +120F (48deg.C). The
area should be constructed and situated so that it will not be
subjected to flooding; the floor should be similarly level, firm,
protected and well drained. Actuators and valves should be
on pallets or shoring to permit air circulation.
For longer storage, a corrosion preventative should be
considered that is compatible with the process fluids.
Further advice should be sought from Severn Glocon.
Handling
Applicable codes regulations and industry practices must be
followed when handling or lifting valves. Care should be
exercised to protect instrumentation / ancillary equipment.
Severn Glocon lifting guidelines are available on request.
Installation
Make sure adequate overhead clearance exists when
installing the actuator. Minimum clearance is 150mm. It is
usual to use the actuator with a suitable valve positioner. If
this is the case, the air supply and instrument signal
connections must be connected as per the positioner
manufacturer’s instructions.
WARNING: Do not exceed the recommended air supply
pressure shown on the Severn Glocon specification sheet,
as injury to personnel or damage to equipment may occur.
The use of an air filter regulator on the air supply line is
recommended. Instrument quality air is required for
operation of the actuator and any ancillaries fitted.
The weight of the actuator valve assembly should be taken
into consideration when mounting on to a valve. Supports
may be required depending on the actuator orientation.
Actuator Removal and Fitting to Valve
Two types of fitting arrangement for actuators are possible.
Smaller actuators may be fitted by a half ring yoke design
method with either lock nut or stem clamp between stem
and actuator piston. Alternatively, all sizes of actuators may
be fitted by a bolted yoke and stem clamp design method.
IMPORTANT: See warnings on page 1 in regard to isolation
of items to be worked on and carry out safe isolation before
beginning work.
WARNING: Escaping air can cause personal injury, avoid
skin contact and wear eye protection. Take care to correctly
support any parts being lifted. Take care to remove any
linkage mechanisms before starting work to avoid damage.
Half Ring Yoke Design showing lock nut connection
(Actuator sizes
P25, 50 and 100)
Note: This design
may be fitted with
a stem clamp
instead of the lock
nut design. In this
case read relevant
sections of both
design options for
fitting
Bolted Yoke showing Stem Clamp Design
(All Actuator Sizes)
NOTE Yoke Fixings
and Gland Flange
Studs shown 90
degrees out of position
for clarity on Bolted
clamp design
Actuator Removal (Half ring fixing method).
Connect suitable slings to support the actuator weight. For
air fail actuators the valve plug/actuator stem should be
moved to approx. 50% open by means of air. This can be
achieved by using a temporary air line with a manually
controlled pressure regulator and connected to the lower air
port (spring close model) or the upper air port (spring open
model) in the actuator. With the valve in this position, the
plug locknut can be loosened, remove the yoke clamps and
spin the actuator off the valve plug. Caution; Do not allow
plug to rotate during unscrewing. When the actuator
disconnects from the plug, the plug may drop onto the seat
position; take care not to trap fingers. If the plug does not
drop, push the plug to the closed position. Remove the plug
lock nut, and gland flange. Push the actuator downwards
towards the valve body to allow removal of the two yoke
retaining half rings from the groove in the top of the valve
bonnet. The actuator can now be lifted clear of the valve
and all air vented from the actuator. Caution: This will cause
the actuator piston rod to move to the air fail position.
Actuator Fitting (setting the correct plug position)
Before fitting the actuator, extend the piston rod to the
maximum extended position and mark location on the yoke.
Connect suitable slings to support the actuator weight for
both air fail actions. For air fail close type lower the actuator
on to the valve body; during this operation loosely fit the
gland flange and plug lock nut. By rotating the actuator onto
the plug stem it will then be possible to fit the yoke retaining
half rings. Once these have been fitted rotate the actuator in
an anticlockwise direction until the half rings are a snug fit in
the yoke. The yoke clamps, the gland bolts and nuts can
now be fitted. Caution; During this process ensure the plug
is not driven hard into its seat or is allowed to rotate.
For air fail open type actuators use a temporary air line and
manual regulator as above to move the actuator down
slowly so as to be able to rotate the actuator onto the plug
stem. See prior caution notes. Relieve all air pressure and
disconnect. By screwing the actuator onto the plug it will be
possible to allow the yoke to be pushed down towards the
valve body and the yoke retaining half rings can be fitted.
Allow the actuator to rise after fitting to hold these rings in
place then fit the yoke clamps, gland bolts and nuts.

Setting the plug to its seating position.
With Actuator Piston Rod fully extended, (this can be seen
by the marks made earlier on the yoke) and with the plug
set fully on the seat, the actuator piston should extend to a
position short of the mark by approximately 1.5 - 3mm.
Adjust the plug to achieve this position by screwing the
actuator in or out. Do not rotate the plug. Move the actuator
up and down slowly to ensure smooth operation. Set the
plug lock nut. This position may need to be adjusted again
later depending upon the type of positioner when fitted.
Fully stroke the actuator to ensure smooth operation. NOTE:
When installing new or re-fitting the actuator, refer to valve
IOM detail on appropriate tightening of packing gland.
Actuator Removal (Bolted Stem Clamp fixing method)
Set the actuator just off its valve seat by use of a temporary
air line/regulator as above. Undo the clamp screws and nuts
to separate the actuator piston from the plug stem (the
piston may move up/down and in rare cases contact the
plug stem). The plug position may have to adjusted slightly
so as to allow the split clamp to release from its thread.
Air in the actuator can now be slowly released. Loosen the
gland bolts and gland flange. Loosen the yoke retaining cap
screws by approximately. 6mm to ensure spring force is fully
relaxed (actuator rocks easily). The actuator can now be
removed taking care not to damage the valve plug.
Actuator Fitting (setting the correct plug position to ensure
proper seating force is applied during normal operation.)
Fitting follows the reverse methodology of removal, but plug
should be set to its on seat position. Operate the actuator
piston down to its fully extended position (it should not hit
the top of the plug stem). Do not rotate the plug. The piston
should then be raised by approximately 6mm before fitting
the clamp. Adjust the stem position to ensure the threads
mesh fully and fit the other half of the clamp tightly. Fully
stroke the actuator to ensure smooth operation.
Pre-Operation
The actuator and control valve positioner must be set to
correctly close and seat the valve so as to not give rise to
premature trim degradation. If a manual handwheel override
is provided in the actuation system, ensure this is in the
disengaged or neutral position. Clean the actuator shaft of
any foreign matter. Always use correct tools including the
use of torque wrenches to assure bolts are not over
tightened during any checks carried out.
Operation
In operation, ensure that the actuator operates smoothly
and that there is no juddering or unusual motion. If the
actuator exhibits any strange behaviour, please contact your
nearest Severn Glocon representative immediately.
IMPORTANT: For all valve adjustments refer to relative IOM
instructions. If any doubts exist, contact SEVERN GLOCON
Maintenance
Actuator parts are subject to normal wear and tear and must
be inspected and replaced as necessary. Inspection and
maintenance frequency depends upon the severity and
importance of the service.
WARNING: The actuator may be spring loaded. Use care to
follow normal safety procedures when removing actuator
casings and end caps. When turning off the air supply the
actuator will move to its fail-safe position. Keep personnel
away from the moving parts of the valve and actuator during
this process to avoid personnel injury. The actuator may
move very quickly during this process.
Spare Parts
Whenever an actuator is disassembled, it is recommended
that all soft parts are replaced. These are consumable parts.
Troubleshooting
Jerking or sticky stem travel
Possible Cause
Solution
1.
Insufficient air supply
Check air supply and any filters for
blockage
2.
Unlubricated piston
cylinder wall
Lubricate the cylinder and ‘O’ ring
seals.
3.
Worn or damaged
piston rod guide
bushing
Check moving parts for damage.
Replace if worn
4.
Incorrectly located air
fail spring
Check actuator spring locations, re
fit if needed.
5.
Internal valve
problem
Check the valve. Repair as
required
High air consumption
1.
Leaks in the air
supply
Check air connections. Tighten
fittings and refit any leaking tube
lines.
2.
Positioner
Malfunction
Check and refer to positioner
manufacturer’s instructions
3.
Leaks through
actuator ‘O’ rings
Use actuator repair kit to replace
all ‘O’ rings and wiper rings
4.
Damaged Cylinder
Replace with New Cylinder
Actuator does not move to its fail safe position
1.
Air pressure is not
venting due to faulty
positioner / ancillaries
Check and refer to positioner or
ancillary manufacturer’s
instructions as needed
2.
Spring failure
Check and replace if needed
3.
Internal valve
problem
Check the valve, repair as
required.
AUXILIARY HANDWHEELS AND LIMIT STOPS
Top-mounted, Continuously Connected Handwheels
Fitted on
Actuators
Size P25,
50 and 100
Advanced Maintenance
The top-mounted, continuously connected hand-wheel is
totally, enclosed, so only checking for general condition is
required. However, disassembly may be necessary if the
mechanism fails. When reassembling the handwheel, be
sure to clean and lubricate the screw and drive nut with a
multi-purpose grease and replace ‘O’ rings with new.
IMPORTANT: After operation of the override it must be
returned to the neutral position for automatic operation
(shown by manual override shaft level with the bottom of the
viewing window in the hand-wheel end cover tube (6).
Operation
If a pneumatic failure occurs, or if manual control of the
valve is desired, the unit can be operated as follows:
1. Set the three-way bypass valve (located on the
pneumatic supply line to the positioner) to “Hand” to vent the
air pressure from the actuator. NOTE: a three-way valve is
installed in the supply line only when there is no lock-up
system or volume tank. On volume tank or lock-in place
systems, the bypass valve is located between the top and
bottom cylinder ports. However, on some pneumatic circuits
the single three-way bypass valve may be substituted by
two two-way manual valves. Consult the pneumatic circuit
supplied with the actuator documentation.
WARNING: By venting the air, the actuator will move to the
fail safe position, this may be fast. Please keep away from
moving parts including the positioner linkage to avoid injury.

2. To open the valve, turn the hand-wheel counter-clockwise
to retract the plug. To close the valve, turn the hand-wheel
clockwise to extend the plug.
4. To return the valve to automatic control, return the hand-
wheel nut to the ‘neutral’ as shown by the handwheel
position indicator and set the three-way bypass valve (see
previous NOTE) to ‘auto’. The neutral position is indicated
when the top of the screw aligns with the marked line on the
cap liner (see diagram).
5. Adjusting the hand-wheel nut to a position other than
neutral provides a limit open or close stop function
Declutchable Handwheels
Size P100,
and 200
Pin and
lever in auto
position
(Lever Up)
Advanced Maintenance
This is an enclosed unit. For long life, it is important to keep
a coating of multi-purpose grease on the acme threads and
engaging collets at all times. A grease point is provided and
a multi-purpose grease should be pumped into the unit
periodically. Oil can be applied to the hinge pins, the
operating lever and the bearings on handle mechanism.
WARNING: If the mechanism has been operated incorrectly
it is possible to strip the acme threads on the actuator piston
rod and replacement parts will be required.
Operation
If an air failure occurs, or if manual control of the valve is
desired, the handwheel override can be operated as follows:
1. Turn off the pneumatic supply. This is carried out by
operating the three-way bypass valve (located on the air
supply line to the positioner) to “Hand” to vent the air
pressure from the actuator. NOTE: three-way valves are
installed in the supply line only when there is no lock-up
system or volume tank. On volume tank or lock-in place
systems, the bypass valve(s) is located between the top and
bottom cylinder ports. However, on some pneumatic circuits
the single three-way bypass valve may be substituted by
two two-way manual valves. Consult the pneumatic circuit
supplied with the actuator documentation.
WARNING: Venting air will move actuator to the fail safe
position, this may be fast & personnel must keep away from
moving parts including the positioner linkage to avoid injury.
2. After isolating the pneumatic supply remove the operating
lever locking pin (1), from its hole beneath the operating
lever assembly (5). Do not lose this pin (it is normally held to
the body of the unit by a chain). It is now possible to move
the operating lever (5) down towards the valve body. This in
turn moves the internal engaging piston (2) and pushes the
split segments of a spring loaded operating nut (3), which
will engage onto the connecting rod (4) with its acme thread.
It may be required to rotate the hand-wheel (6) at the same
time to ease this process. Once the operating handle has
moved and the operating nut fully engaged on the acme
thread the locking pin (1) is used to hold the operating lever
in position by inserting into the lower of the two holes.
3. With the hand-wheel unit now fully engaged on the
actuator piston rod thread, rotating the hand-wheel
clockwise will close the valve and by rotating the hand-
wheel counter-clockwise, the valve will open.
4. To return to automatic control, using the hand-wheel
mechanism, firstly position the valve fully to the air fail
position.
WARNING: Control valves must only ever be put back into
automatic control mode once user has confirmed the valve
is fully in its Fail Safe mode position. Failure to do so can
cause damage to equipment and severe injury to personnel.
5. Pull out the operating lever locking pin (1) from its
locating hole above the operating lever assembly (5). To
declutch the hand-wheel assembly move the operating lever
(5) up away from the valve body. This moves the engaging
piston (2) away from the operating nut and allows operating
nut (3) springs to disengage operating nut from connecting
rod (4). It may be necessary to rotate the hand-wheel (6)
slightly to allow the acme threads to disengage. Confirm
disengagement by checking the handwheel moves freely.
WARNING: At this point, just in case there is still a load on
the actuating stem from the valve, meaning the actuator
piston rod will move to the no load position, it is advised to
keep personnel away from any moving parts.
6. When the acme thread is fully disengaged the operating
lever will be in its fully up position and the locking pin (1) is
used to hold the lever assembly in position by inserting this
locking pin in the upper of the two holes.
7. To return to automatic control, turn on pneumatic supply
by operating the three-way bypass valve (see previous
NOTE) to ‘auto’. This reconnects the air supply to the
positioner.
Disclaimer: Neither Severn Glocon Ltd, or any of its
affiliated entities assumes responsibility for the selection,
use or maintenance of any product. Responsibility for proper
selection, use, and maintenance of any product remains
solely with the purchaser and the end user. The contents of
this publication are presented for information purposes only,
and while every effort has been made to ensure their
accuracy, they are not to be construed as warranties or
guarantees, express or implied, regarding the products or
services described herein on their use or applicability. We
reserve the right to modify or improve the designs or
specifications of such products at any time without notice.
HEAD OFFICE: SEVERN GLOCON LTD,
Olympus Park, Quedgeley, Gloucester, GL2 4NF. UK.
Tel +44(0) 845 2232040
SEVERN GLOCON INDIA PVT LTD,
F96/97, SIPCOT Industrial Park, Irungattukkottai, Chennai,
602 05, INDIA, Tel +91(0)44 47104200
AFTERSALES & SERVICE: SEVERN UNIVAL LTD,
Heywoods Industrial Park, Birds Royd Lane, Brighouse, W
Yorkshire, HD6 1NA, UK. Tel +44(0) 845 6070710
www.severnglocon.com
Severn Glocon Manual Ref: SGG-IOM-ACT-M01-REV03
Date 27-02-2017
Popular Controllers manuals by other brands
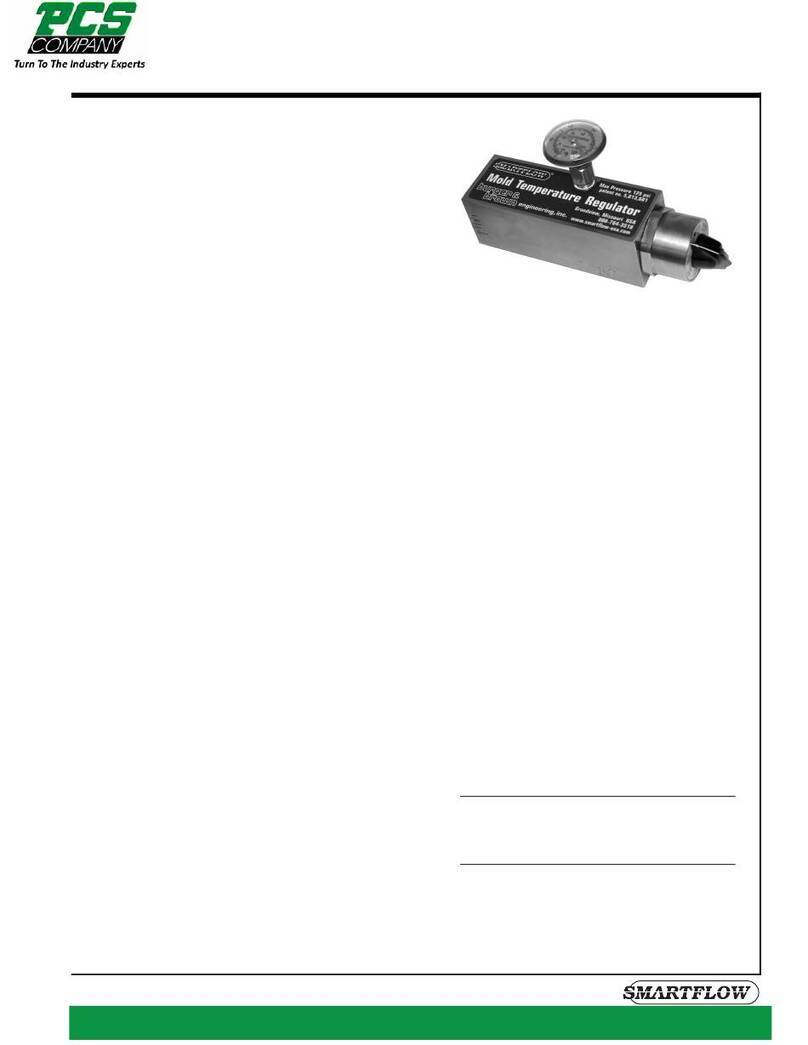
Burger & Brown
Burger & Brown SMARTFLOW WDT2-S3-P3 operating instructions
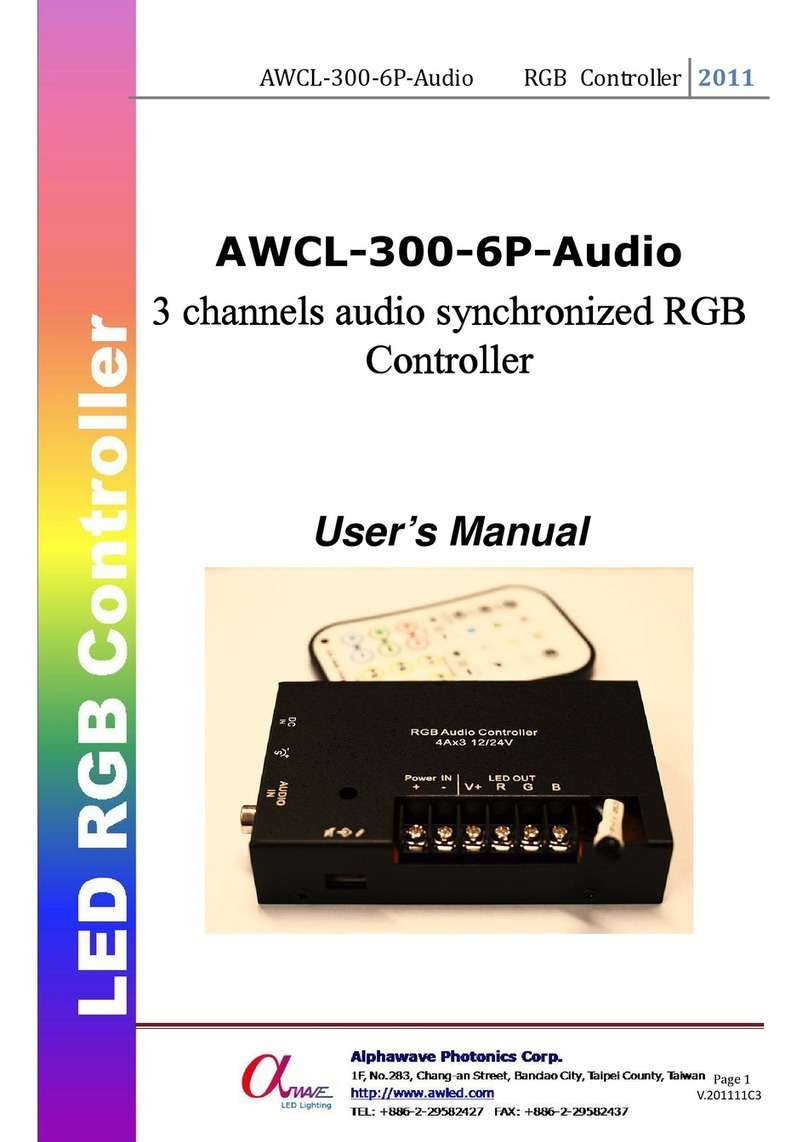
Alphawave Photonics
Alphawave Photonics AWCL-300-6P-Audio user manual
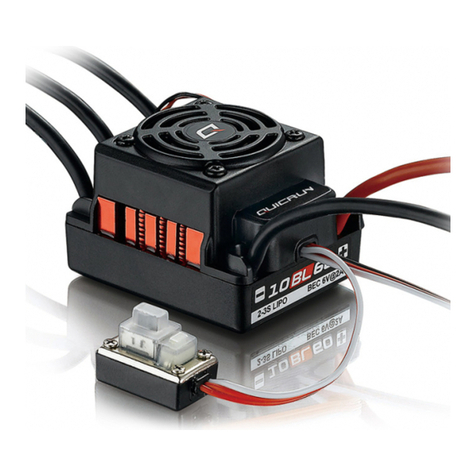
Hobby-Wing
Hobby-Wing Quicrun 16BL30 user manual
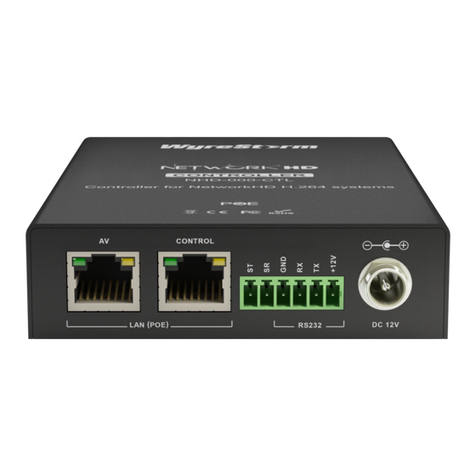
Wyrestorm
Wyrestorm NHD-000-CTL quick start guide

Oriental motor
Oriental motor aSTEP AZ Series user manual
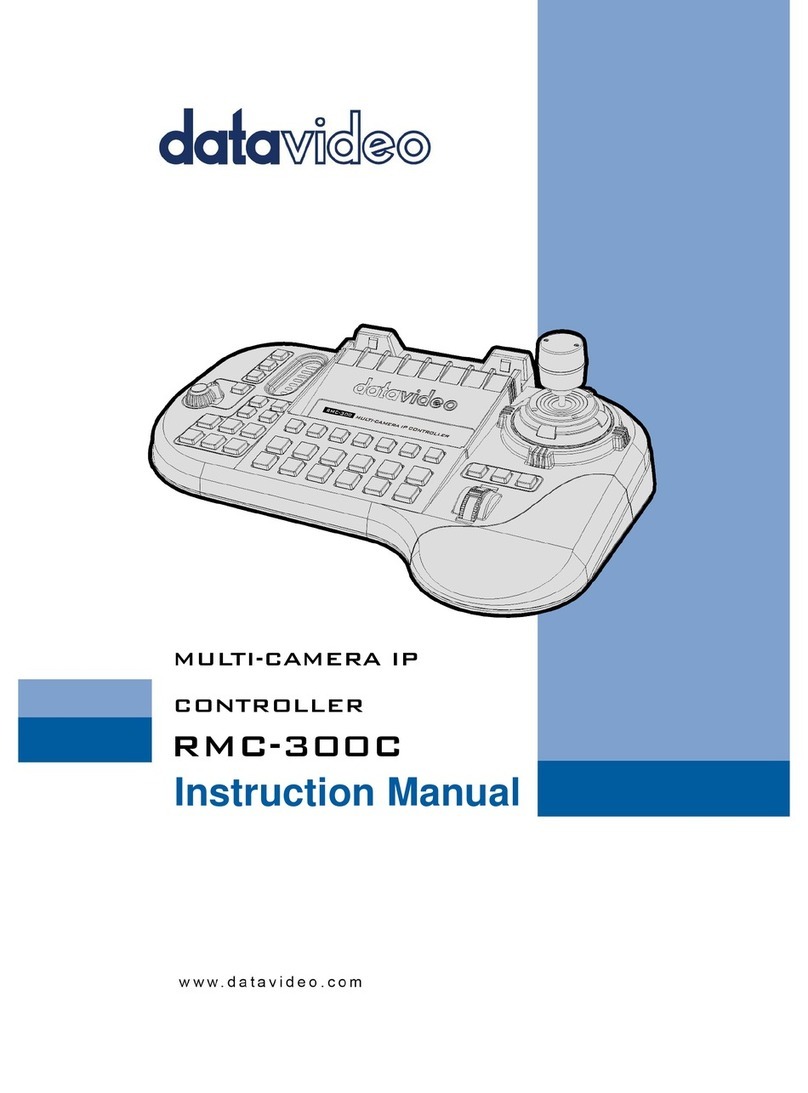
Data Video
Data Video RMC-300C instruction manual
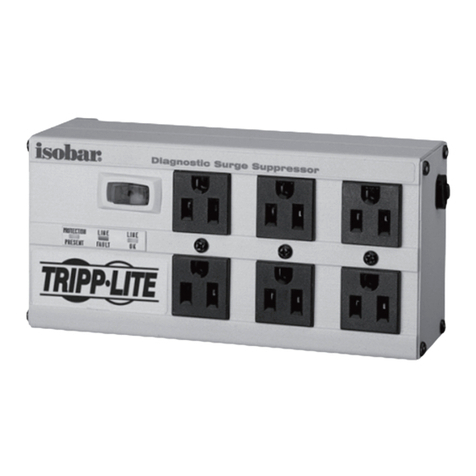
Tripp Lite
Tripp Lite LC-1200B owner's manual
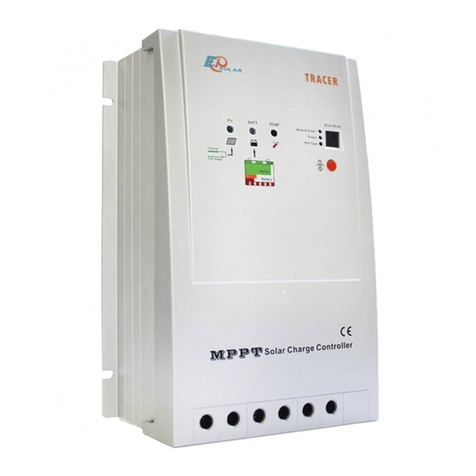
EP Solar
EP Solar Tracer-4210RN instruction manual
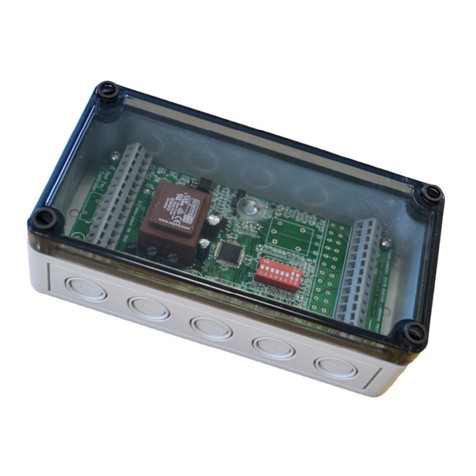
Ebmpapst
Ebmpapst CN1082 Operating and maintenance instructions
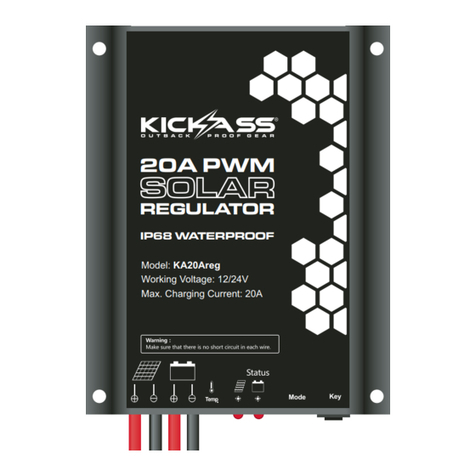
KICK ASS
KICK ASS KA20Areg quick start guide
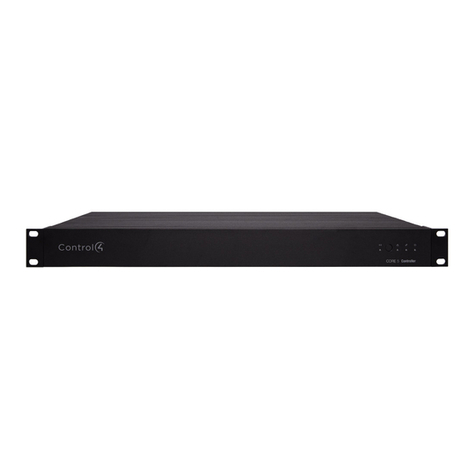
Contro l4
Contro l4 CORE-5 installation guide
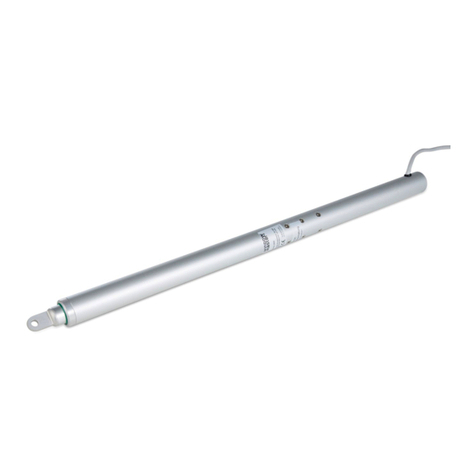
WindowMaster
WindowMaster WMS 409-n Installation instructions manual